Unlock Quality & Cost Savings: The Sleeve Manufacturer Guide (2025)
Introduction: Navigating the Global Market for sleeve manufacturer
In the dynamic landscape of global commerce, sourcing reliable sleeve manufacturers presents a unique challenge for B2B buyers, especially those operating in diverse markets such as Africa, South America, the Middle East, and Europe. The demand for high-quality sleeves—ranging from protective packaging to functional components in various industries—requires a nuanced understanding of supplier capabilities, production standards, and market trends. This comprehensive guide addresses these complexities by offering insights into the types of sleeves available, their applications across different sectors, and essential criteria for vetting suppliers.
Navigating the myriad of options and potential pitfalls in the sleeve manufacturing market can be daunting. This guide not only outlines the specific factors to consider when selecting suppliers but also delves into cost considerations, quality assurance practices, and logistical aspects of international procurement. For buyers in regions like Germany and Mexico, understanding local and global market dynamics is crucial for making informed purchasing decisions.
Empowering international B2B buyers with actionable insights, this guide serves as a vital resource for optimizing sourcing strategies and ensuring successful partnerships with sleeve manufacturers. By arming buyers with knowledge and tools, it enhances their ability to negotiate effectively, maintain quality standards, and ultimately drive their business growth in a competitive global market.
Understanding sleeve manufacturer Types and Variations
Type Name | Key Distinguishing Features | Primary B2B Applications | Brief Pros & Cons for Buyers |
---|---|---|---|
Custom Sleeve Manufacturers | Tailored designs based on specific client needs | Packaging, Automotive, Electronics | Pros: Unique solutions; precise fit. Cons: Higher costs; longer lead times. |
Standard Sleeve Manufacturers | Pre-defined sizes and designs available off-the-shelf | Retail, Food & Beverage, Consumer Goods | Pros: Quick delivery; lower costs. Cons: Limited customization options. |
Eco-Friendly Sleeve Manufacturers | Use of sustainable materials and processes | Food Packaging, Cosmetics, Apparel | Pros: Environmentally responsible; appealing to eco-conscious brands. Cons: May have higher production costs. |
High-Volume Sleeve Manufacturers | Focus on mass production for large orders | Industrial, Automotive, Electronics | Pros: Cost-effective for bulk orders; efficient production. Cons: Less flexibility in design changes. |
Specialized Sleeve Manufacturers | Expertise in niche applications (e.g., medical) | Medical Devices, Pharmaceuticals | Pros: High-quality standards; industry-specific knowledge. Cons: Potentially higher prices for specialized services. |
What are the Characteristics of Custom Sleeve Manufacturers?
Custom sleeve manufacturers specialize in creating tailored solutions that meet specific client requirements. These manufacturers are ideal for businesses that require unique designs or specifications that cannot be met by standard products. When purchasing from custom manufacturers, B2B buyers should consider the design process, lead times, and potential costs associated with customization. This option is particularly suitable for industries like automotive and electronics where precision is critical.
How Do Standard Sleeve Manufacturers Operate?
Standard sleeve manufacturers offer a range of pre-defined sizes and designs that are readily available for quick distribution. This model is beneficial for companies looking for cost-effective solutions without the need for customization. B2B buyers often choose this option for sectors such as retail and food and beverage, where speed of delivery and budget constraints are significant factors. While standard sleeves can be less expensive, they may not meet specific branding or functional needs.
Why Choose Eco-Friendly Sleeve Manufacturers?
Eco-friendly sleeve manufacturers focus on sustainable practices and materials, appealing to businesses that prioritize environmental responsibility. These manufacturers are increasingly popular in industries such as food packaging and cosmetics, where consumers are becoming more eco-conscious. When considering eco-friendly options, B2B buyers should evaluate the availability of materials, production costs, and the overall impact on branding. While these sleeves may be more expensive, they can enhance a brand’s reputation and customer loyalty.
What are the Benefits of High-Volume Sleeve Manufacturers?
High-volume sleeve manufacturers are designed for businesses that require mass production of sleeves for large orders. This type of manufacturer is often found in industrial and automotive sectors where cost efficiency and production speed are paramount. Buyers should assess the scalability of production, pricing structures for bulk orders, and the manufacturer’s ability to handle large-scale projects. While this option is cost-effective, it may limit the flexibility for design changes during production.
What Sets Specialized Sleeve Manufacturers Apart?
Specialized sleeve manufacturers cater to niche markets, such as medical devices or pharmaceuticals, where compliance with strict regulations and high-quality standards are essential. These manufacturers provide tailored solutions that address specific industry needs. B2B buyers should carefully evaluate the manufacturer’s expertise, certifications, and ability to meet regulatory requirements. Although prices may be higher due to specialization, the quality and reliability of these products often justify the investment.
Related Video: Variations In Construction Projects Explained
Key Industrial Applications of sleeve manufacturer
Industry/Sector | Specific Application of Sleeve Manufacturer | Value/Benefit for the Business | Key Sourcing Considerations for this Application |
---|---|---|---|
Automotive | Protective sleeves for wiring harnesses | Enhances safety and durability of electrical systems | Material quality, temperature resistance, and compliance with automotive standards |
Oil & Gas | Insulation sleeves for pipes and cables | Reduces heat loss and improves energy efficiency | Ability to withstand harsh environments and certifications for safety standards |
Food Processing | Sleeves for machinery and conveyor systems | Ensures hygiene and prevents contamination | Compliance with food safety regulations and easy cleaning features |
Electronics | Thermal sleeves for electronic components | Protects sensitive parts from heat damage | Thermal conductivity, material compatibility, and reliability under varying conditions |
Aerospace | Fire-resistant sleeves for wiring and hoses | Increases safety in high-risk environments | Certifications for fire resistance and weight constraints for aerospace applications |
How Are Sleeve Manufacturers Used in the Automotive Industry?
In the automotive sector, sleeve manufacturers provide protective sleeves for wiring harnesses. These sleeves are crucial for safeguarding electrical systems from abrasion, moisture, and thermal damage. For international B2B buyers, particularly from regions like Europe and South America, sourcing high-quality materials that meet stringent automotive standards is essential. Buyers should consider the sleeve’s temperature resistance and compliance with automotive regulations to ensure reliability and safety in vehicle operation.
What Role Do Sleeves Play in the Oil & Gas Industry?
In the oil and gas industry, insulation sleeves are utilized for pipes and cables to minimize heat loss and enhance energy efficiency. These sleeves are designed to withstand extreme temperatures and corrosive environments, making them vital for operational integrity. Buyers from Africa and the Middle East should prioritize sourcing materials that offer high durability and compliance with industry safety standards. Additionally, understanding the environmental conditions of the installation site is critical for selecting the appropriate sleeve type.
How Are Sleeves Ensuring Hygiene in Food Processing?
Sleeves in the food processing industry are employed to cover machinery and conveyor systems, ensuring hygiene and preventing contamination. These sleeves are typically made from materials that are easy to clean and resistant to various food substances. For B2B buyers in Europe and South America, it is crucial to source sleeves that comply with food safety regulations, ensuring that they do not introduce any contaminants into the food supply. Buyers should also look for features that facilitate easy maintenance and cleaning.
What Benefits Do Thermal Sleeves Provide in Electronics?
In the electronics sector, thermal sleeves are used to protect sensitive components from heat damage. These sleeves are designed to offer excellent thermal conductivity and insulation, ensuring that electronic devices operate efficiently without overheating. International buyers, particularly from Europe and the Middle East, should focus on sourcing sleeves that meet specific thermal performance criteria and are compatible with various electronic materials. Reliability and long-term performance are key considerations for ensuring device longevity.
Why Are Fire-Resistant Sleeves Essential in Aerospace?
Fire-resistant sleeves are critical in the aerospace industry for protecting wiring and hoses from potential fire hazards. These sleeves enhance safety in high-risk environments, ensuring that aircraft systems remain operational during emergencies. For B2B buyers, especially in Europe, it is vital to source sleeves that have the necessary fire resistance certifications and meet weight constraints. Understanding the regulatory landscape and ensuring compliance with aerospace safety standards are essential for successful procurement in this sector.
Related Video: What are all the Laboratory Apparatus and their uses?
3 Common User Pain Points for ‘sleeve manufacturer’ & Their Solutions
Scenario 1: Inconsistent Quality Across Suppliers
The Problem:
B2B buyers often encounter significant challenges when sourcing sleeves from multiple manufacturers. Discrepancies in quality can lead to production delays, increased costs, and ultimately, dissatisfied customers. For instance, a manufacturer in Europe might receive a batch of sleeves that do not meet specified thickness or durability standards, whereas a similar order from an African supplier may vary significantly in both material and finish. This inconsistency not only disrupts the supply chain but also complicates inventory management and quality control processes.
The Solution:
To overcome quality inconsistencies, buyers should prioritize establishing clear and detailed specifications before engaging with sleeve manufacturers. This includes defining material types, dimensions, tolerances, and performance criteria. Additionally, conducting thorough research to identify reputable suppliers with established quality assurance processes is essential. Buyers can leverage third-party certification bodies or industry standards (like ISO) to validate supplier credibility. Regular quality audits and sample testing should be implemented to ensure compliance with set standards before mass production. Establishing long-term relationships with a select few manufacturers rather than spreading orders across multiple suppliers can also help maintain consistent quality and simplify logistics.
Scenario 2: Delays in Production and Delivery Timelines
The Problem:
Timely delivery is crucial in the B2B landscape, especially when manufacturing schedules are tight. A common pain point for buyers is experiencing delays in production and shipping from sleeve manufacturers. For example, a company in South America may plan a product launch that depends on receiving sleeves on a specific date, only to find that their supplier has underestimated production time or faced unforeseen shipping issues. Such delays can lead to missed deadlines, increased costs, and lost revenue opportunities.
The Solution:
To mitigate risks related to production delays, buyers should adopt a proactive approach to communication and planning. Establishing a clear timeline for production and delivery at the outset of the order process is vital. Buyers should also implement buffer periods in their project timelines to account for potential delays. Engaging in regular communication with the manufacturer throughout the production process can help identify issues early on. Additionally, buyers should consider diversifying their supplier base to include multiple manufacturers that can fulfill orders, which provides flexibility in case one supplier faces challenges. Utilizing local suppliers where feasible can also reduce shipping times and complexities.
Scenario 3: Difficulty in Customization and Design Changes
The Problem:
In many cases, B2B buyers may require customized sleeves that cater to specific project needs or branding requirements. However, not all manufacturers are equipped to handle customization efficiently. This can lead to frustration when trying to communicate design changes or when the manufacturer is unable to meet unique specifications. For instance, a European company may want to incorporate a unique branding element or a special coating, but the sleeve manufacturer in question lacks the necessary technology or expertise.
The Solution:
To address challenges related to customization, buyers should conduct thorough assessments of potential sleeve manufacturers’ capabilities before placing orders. This includes evaluating their equipment, technology, and expertise in handling custom orders. Engaging in early discussions about design specifications, including providing visual aids or prototypes, can significantly enhance communication and alignment. Buyers should also inquire about the manufacturer’s past experience with similar custom projects and request case studies or samples to ensure their capabilities meet expectations. Establishing a collaborative relationship where feedback is encouraged can facilitate smoother design iterations and adjustments, ultimately leading to satisfactory outcomes.
Strategic Material Selection Guide for sleeve manufacturer
What Are the Key Materials Used in Sleeve Manufacturing?
When selecting materials for sleeve manufacturing, international B2B buyers must consider various factors such as performance properties, cost, and suitability for specific applications. Here, we analyze four common materials used in sleeve manufacturing: rubber, silicone, PVC, and metal. Each material has distinct properties, advantages, and limitations that can significantly impact the performance of the final product.
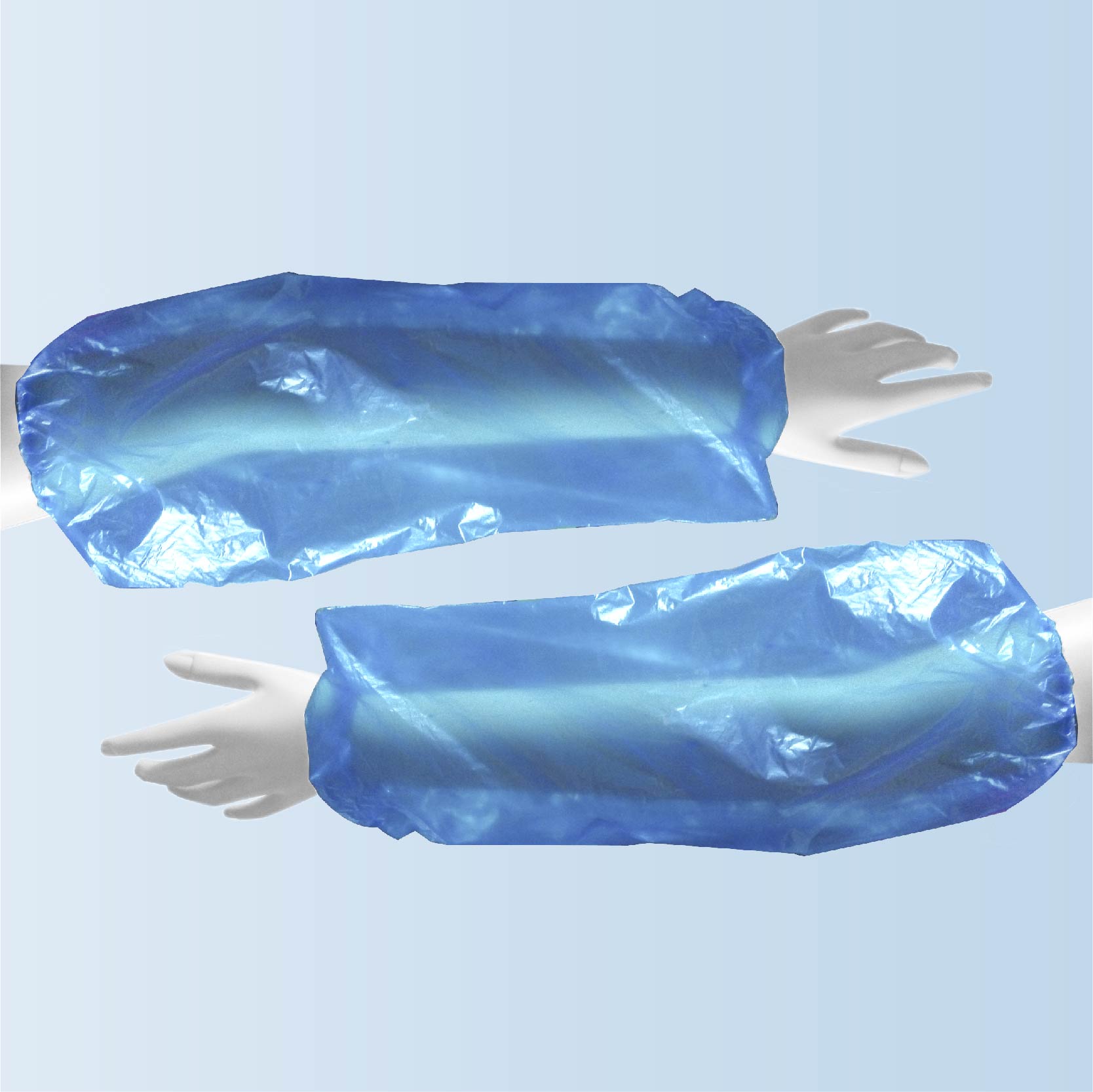
A stock image related to sleeve manufacturer.
How Does Rubber Perform in Sleeve Applications?
Rubber is a versatile material known for its excellent elasticity and durability. It typically has a high-temperature rating, allowing it to withstand moderate heat and pressure, making it suitable for applications in automotive and industrial sectors. Rubber sleeves provide good corrosion resistance, particularly against oils and solvents.
Pros: Rubber sleeves are generally cost-effective and easy to manufacture, making them a popular choice for mass production. They also offer excellent sealing capabilities.
Cons: However, rubber can degrade over time when exposed to UV light and extreme temperatures, limiting its lifespan in outdoor applications. Additionally, it may not be suitable for applications involving strong acids or bases.
Considerations for International Buyers: Buyers should ensure compliance with international standards such as ASTM D2000 for rubber materials. Countries like Germany and Mexico often have specific regulations regarding the use of rubber in industrial applications.
What Benefits Does Silicone Offer for Sleeve Manufacturing?
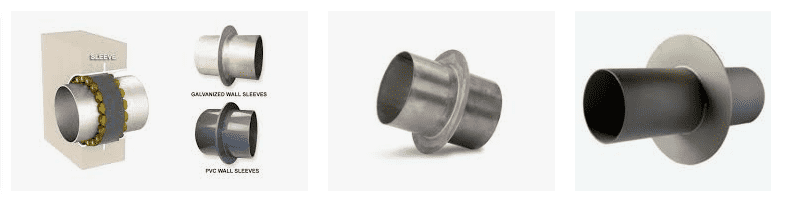
A stock image related to sleeve manufacturer.
Silicone is increasingly popular in sleeve manufacturing due to its superior thermal stability and flexibility. It can withstand extreme temperatures, from -60°C to 200°C, making it ideal for high-temperature applications in the automotive and aerospace industries. Silicone also exhibits excellent resistance to UV light and ozone, enhancing its longevity.
Pros: The primary advantage of silicone is its ability to maintain its properties over a wide temperature range, ensuring consistent performance. It is also non-toxic and suitable for food-grade applications.
Cons: On the downside, silicone can be more expensive than rubber and may require more complex manufacturing processes. Its lower tensile strength compared to rubber can also limit its use in high-stress applications.
Considerations for International Buyers: Buyers should look for silicone materials that comply with FDA regulations for food contact applications. Additionally, understanding local certifications in regions like Africa and the Middle East can be crucial for market entry.
Why Choose PVC for Sleeve Manufacturing?
Polyvinyl Chloride (PVC) is a widely used thermoplastic material known for its durability and chemical resistance. PVC sleeves are often employed in plumbing and electrical applications due to their excellent insulation properties and resistance to corrosion.
Pros: PVC is cost-effective and easy to mold, making it suitable for a variety of applications. Its resistance to chemicals and moisture makes it ideal for outdoor use.
Cons: However, PVC has a lower temperature tolerance compared to rubber and silicone, which may limit its use in high-temperature environments. It is also less flexible, which can be a disadvantage in applications requiring a high degree of movement.
Considerations for International Buyers: Buyers should verify compliance with local standards such as DIN 4066 in Europe for PVC products. Understanding the environmental regulations regarding PVC use in countries like South Africa is also essential.
What Are the Advantages of Using Metal in Sleeve Manufacturing?
Metal sleeves, often made from stainless steel or aluminum, are known for their strength and durability. They are commonly used in high-pressure applications, such as hydraulic systems, where both temperature and pressure ratings are critical.
Pros: Metal sleeves provide excellent resistance to wear and tear, making them suitable for demanding environments. They also offer superior mechanical strength and can be used in applications requiring high reliability.
Cons: The primary disadvantage of metal sleeves is their higher cost and complexity in manufacturing. They can also be heavier than other materials, which may not be suitable for all applications.
Considerations for International Buyers: Buyers must ensure compliance with relevant standards such as ASTM A269 for stainless steel. In Europe, adherence to EN standards is also critical for market acceptance.
Summary Table of Material Selection for Sleeve Manufacturing
Material | Typical Use Case for sleeve manufacturer | Key Advantage | Key Disadvantage/Limitation | Relative Cost (Low/Med/High) |
---|---|---|---|---|
Rubber | Automotive and industrial applications | Cost-effective and good sealing | Degrades under UV and extreme heat | Low |
Silicone | High-temperature and food-grade applications | Excellent thermal stability | More expensive and complex to manufacture | High |
PVC | Plumbing and electrical applications | Cost-effective and moisture-resistant | Lower temperature tolerance | Med |
Metal | High-pressure hydraulic systems | Superior mechanical strength | Higher cost and heavier weight | High |
This strategic material selection guide provides international B2B buyers with essential insights into choosing the right materials for sleeve manufacturing, considering performance, cost, and compliance with regional standards.
In-depth Look: Manufacturing Processes and Quality Assurance for sleeve manufacturer
What Are the Main Stages in the Manufacturing Process of Sleeves?
The manufacturing process for sleeves involves several key stages, each critical to ensuring the final product meets quality standards and customer specifications. Understanding these stages can help international B2B buyers assess the capabilities of potential suppliers.
Material Preparation: What Materials Are Typically Used?
The first step in sleeve manufacturing is material preparation. Common materials include various grades of plastics, metals, and textiles, depending on the intended application of the sleeve. For instance, high-density polyethylene (HDPE) is often used for industrial sleeves due to its durability, while elastomers may be chosen for applications requiring flexibility.
Before processing, materials must be inspected for quality and suitability. This includes checking for contaminants and verifying that the material meets specified standards. B2B buyers should inquire about the sourcing of materials and whether suppliers provide certificates of compliance.
Forming: How Are Sleeves Shaped and Molded?
Once the materials are prepared, the next step is forming. This stage typically involves techniques such as extrusion, injection molding, or die-cutting, depending on the material and design specifications.
- Extrusion: Commonly used for thermoplastic sleeves, where material is heated and forced through a die to create a continuous profile.
- Injection Molding: Suitable for creating complex shapes, where molten material is injected into a mold.
- Die-Cutting: Used for textile sleeves, where sheets of fabric are cut into desired shapes.
Each method has its pros and cons, influencing production speed, cost, and design flexibility. Buyers should assess the capabilities of suppliers in these forming techniques, as this can affect lead times and pricing.
Assembly: How Are Sleeves Constructed?
In the assembly stage, sleeves may undergo additional processes such as stitching, welding, or bonding, depending on their design. This stage is crucial for ensuring that components fit together correctly and meet durability requirements.
For instance, if sleeves are intended for high-pressure applications, welding techniques may be employed to ensure that joints can withstand stress. Buyers should inquire about the assembly methods used and how they align with industry standards.
Finishing: What Final Treatments Are Applied?
The final stage in sleeve manufacturing is finishing, which may include surface treatments, coatings, or additional inspections. This stage is essential for enhancing the sleeve’s performance and aesthetic appeal.
Common finishing processes include:
– Coating: To improve chemical resistance or provide a specific color.
– Surface Texturing: For grip or aesthetic purposes.
– Quality Inspections: Ensuring the product meets specifications and is free from defects.
Buyers should ensure that suppliers have a defined finishing process and that they can provide evidence of compliance with applicable industry standards.
What Quality Assurance Practices Are Essential for Sleeve Manufacturers?
Quality assurance (QA) is integral to the manufacturing process, ensuring that products meet required specifications and standards. B2B buyers should understand the QA practices employed by suppliers to mitigate risks associated with product defects.
Which International Standards Should Sleeve Manufacturers Comply With?
Compliance with international standards is crucial for ensuring quality. The most relevant standards for sleeve manufacturers include:
- ISO 9001: A globally recognized standard for quality management systems, ensuring consistent product quality and customer satisfaction.
- CE Marking: Indicates compliance with European health, safety, and environmental protection standards, essential for products sold within the EU.
- API Standards: Relevant for sleeves used in the oil and gas industry, ensuring products meet industry-specific requirements.
Buyers should verify that suppliers hold current certifications and understand the implications of these standards in their respective markets.
What Are the Key Quality Control Checkpoints?
Quality control (QC) involves several checkpoints throughout the manufacturing process to ensure product integrity:
- Incoming Quality Control (IQC): Inspecting raw materials upon arrival to ensure they meet specifications.
- In-Process Quality Control (IPQC): Monitoring production processes to catch defects early.
- Final Quality Control (FQC): Conducting thorough inspections of finished products before shipment.
Understanding these checkpoints allows buyers to assess the effectiveness of a supplier’s QC processes.
How Can B2B Buyers Verify Supplier Quality Control?
Verifying the quality control measures of a sleeve manufacturer is vital for international buyers. Here are some actionable steps:
What Audits and Reports Should Buyers Request?
Buyers should request access to quality control reports and audit findings. This includes:
- Internal Audit Reports: To understand the supplier’s self-assessment processes.
- Third-Party Audit Reports: Conducted by recognized certification bodies, providing an unbiased evaluation of the supplier’s quality systems.
How Can Third-Party Inspections Ensure Compliance?
Engaging third-party inspection services can provide additional assurance of quality. These services can perform random checks at various production stages, verifying compliance with industry standards and specifications.
Buyers should inquire whether suppliers are open to third-party inspections and how frequently they utilize these services.
What Are the Quality Control Nuances for International B2B Buyers?
For buyers in regions such as Africa, South America, the Middle East, and Europe, understanding regional regulations and quality expectations is crucial.
- Cultural Considerations: Different regions may have varying expectations regarding product quality and customer service. Buyers should ensure that suppliers are aware of and can meet these expectations.
- Logistical Challenges: International shipping can impact quality, so it’s essential to understand how suppliers package and transport products to prevent damage.
By being informed about these nuances, B2B buyers can make more educated decisions and foster successful supplier relationships.
Conclusion: How to Ensure Quality in Sleeve Manufacturing
In conclusion, understanding the manufacturing processes and quality assurance practices of sleeve manufacturers is essential for international B2B buyers. By focusing on material preparation, forming, assembly, and finishing stages, as well as verifying compliance with international standards, buyers can ensure they select suppliers capable of delivering high-quality products that meet their specific needs.
Practical Sourcing Guide: A Step-by-Step Checklist for ‘sleeve manufacturer’
Introduction
In the competitive landscape of international B2B sourcing, finding the right sleeve manufacturer is critical for ensuring product quality and supply chain efficiency. This guide provides a step-by-step checklist designed for international buyers from regions such as Africa, South America, the Middle East, and Europe. By following these actionable steps, you can streamline your sourcing process and make informed decisions.
Step 1: Define Your Technical Specifications
Clearly outlining your technical specifications is essential for effective communication with potential manufacturers. Consider the materials, dimensions, and any specific design features you require. This clarity not only helps in obtaining accurate quotes but also ensures that the manufacturer understands your needs.
- Material Requirements: Specify if you need eco-friendly or specific performance materials.
- Size and Dimensions: Provide exact measurements to avoid miscommunication.
Step 2: Research Potential Manufacturers
Conduct thorough research to identify potential sleeve manufacturers that fit your requirements. Utilize online directories, trade shows, and industry contacts to compile a list of suppliers.
- Industry Reputation: Look for reviews and testimonials from previous clients.
- Geographic Considerations: Factor in shipping costs and lead times based on the manufacturer’s location.
Step 3: Evaluate Potential Suppliers
Before committing, it’s crucial to vet suppliers thoroughly. Request company profiles, case studies, and references from buyers in a similar industry or region. Don’t just rely on their website.
- Quality Certifications: Ensure they have relevant certifications (e.g., ISO 9001) that demonstrate their commitment to quality.
- Production Capabilities: Confirm they can meet your volume needs and deadlines.
Step 4: Request Samples
Requesting samples is a vital step to verify the quality of the manufacturer’s products. This allows you to assess their craftsmanship, material quality, and adherence to your specifications before placing a large order.
- Prototype Evaluation: Test the samples in real-world conditions to gauge performance.
- Feedback Loop: Use the samples to gather feedback from your team or stakeholders.
Step 5: Negotiate Terms and Pricing
Once you’ve shortlisted potential manufacturers, engage in negotiations regarding pricing, payment terms, and delivery schedules. This step is crucial for establishing a mutually beneficial relationship.
- Volume Discounts: Inquire about pricing breaks for larger orders.
- Payment Security: Consider using secure payment methods to protect your investment.
Step 6: Verify Compliance and Ethical Standards
Ensuring that your chosen manufacturer adheres to ethical labor practices and complies with international regulations is vital for brand integrity. Conduct due diligence to avoid potential reputational risks.
- Social Compliance Audits: Request documentation of their labor practices.
- Sustainability Practices: Assess their environmental impact and commitment to sustainable production methods.
Step 7: Establish Communication Channels
Effective communication is key to successful sourcing. Establish clear channels of communication with your chosen manufacturer to facilitate ongoing dialogue throughout the production process.
- Regular Updates: Set expectations for regular progress updates and feedback sessions.
- Cultural Sensitivity: Be aware of cultural differences that may impact communication styles.
By following this comprehensive checklist, international B2B buyers can effectively navigate the complexities of sourcing sleeve manufacturers, ensuring quality and reliability in their supply chain.
Comprehensive Cost and Pricing Analysis for sleeve manufacturer Sourcing
When sourcing sleeves from manufacturers, understanding the cost structure is critical for international B2B buyers. This analysis highlights the various components that contribute to pricing, as well as the factors influencing costs and actionable tips for effective sourcing.
What Are the Key Cost Components in Sleeve Manufacturing?
-
Materials: The choice of materials significantly affects the final price. Common materials for sleeves include polyethylene, polyester, and other polymers. Prices fluctuate based on market demand and availability. Buyers should consider sourcing materials that balance quality and cost-effectiveness.
-
Labor Costs: Labor costs vary by region, influenced by local wage standards and skill levels. In countries like Germany or the UAE, labor may be more expensive compared to South American countries. Understanding the local labor market can provide insights into potential cost savings.
-
Manufacturing Overhead: This includes expenses related to utilities, rent, and equipment maintenance. Overhead can vary significantly based on the manufacturer’s location and operational efficiency. Buyers should inquire about how overhead is calculated and included in the pricing.
-
Tooling Costs: If custom molds or tooling are required for specific sleeve designs, this can lead to higher initial costs. Tooling costs are often amortized over production runs, so larger orders can mitigate these expenses.
-
Quality Control (QC): Implementing stringent QC processes ensures product reliability but can add to costs. Manufacturers that invest in quality assurance may charge more, but this can lead to long-term savings by reducing returns and defects.
-
Logistics: Shipping and handling are crucial, especially for international buyers. Costs can vary based on the shipping method, distance, and volume. Understanding Incoterms (International Commercial Terms) is essential to clarify who bears the costs and risks during transportation.
-
Profit Margin: Manufacturers will typically add a profit margin to cover their costs and ensure sustainability. This margin can vary widely depending on the manufacturer’s market position and the competitive landscape.
How Do Price Influencers Affect Sleeve Manufacturing Costs?
-
Volume and Minimum Order Quantities (MOQs): Larger orders often lead to lower per-unit costs due to economies of scale. Conversely, smaller orders may attract higher prices. Negotiating MOQs can be advantageous for buyers looking to minimize costs.
-
Specifications and Customization: Custom designs or specific performance specifications can increase costs. Buyers should clearly communicate their needs to avoid unexpected expenses.
-
Material Quality and Certifications: Higher quality materials and certifications (like ISO standards) usually come with a price premium. Buyers in industries with stringent quality requirements should factor these costs into their budgets.
-
Supplier Factors: Established suppliers with a good reputation may charge more due to their reliability and quality assurance practices. However, they can also reduce risks associated with sourcing.
What Are the Best Practices for Negotiating Sleeve Prices?
-
Conduct a Total Cost of Ownership (TCO) Analysis: Assess not just the initial purchase price but also the long-term costs, including shipping, maintenance, and potential defects. This comprehensive view can help in making informed decisions.
-
Be Transparent About Requirements: Clearly outline your specifications and expectations to avoid miscommunication that could lead to increased costs.
-
Leverage Relationships: Building strong relationships with suppliers can lead to better pricing and terms. Regular communication and feedback can foster trust and collaboration.
-
Stay Informed About Market Trends: Understanding market conditions, such as material price fluctuations or geopolitical factors affecting supply chains, can provide leverage during negotiations.
-
Request Multiple Quotes: Comparing prices from different manufacturers can highlight competitive pricing and help in negotiations.
Conclusion
Sourcing sleeves involves navigating a complex cost structure and numerous influencing factors. By understanding these elements, international B2B buyers from Africa, South America, the Middle East, and Europe can make informed sourcing decisions, negotiate effectively, and ultimately achieve a favorable balance between cost and quality. Always remember that indicative prices can vary based on market conditions and specific supplier circumstances, so continuous engagement and assessment are vital.
Alternatives Analysis: Comparing sleeve manufacturer With Other Solutions
When considering the procurement of sleeve manufacturing solutions, it’s essential for international B2B buyers to evaluate not only the sleeve manufacturer itself but also viable alternative solutions. This analysis helps in determining the best fit for specific business needs, budget constraints, and operational capabilities.
Comparison Aspect | Sleeve Manufacturer | Alternative 1: Shrink Sleeving Technology | Alternative 2: Rigid Packaging Solutions |
---|---|---|---|
Performance | High durability and flexibility; customizable designs for various products | Good for temperature-sensitive products; adapts well to different shapes | Offers robust protection; limited flexibility in design |
Cost | Moderate initial investment with potential for high return on investment | Generally lower upfront costs; requires specialized equipment | Higher production costs due to materials and machinery |
Ease of Implementation | Requires trained personnel for setup and operation | Easier to implement; often requires minimal training | Complex setup; may require significant workforce training |
Maintenance | Moderate maintenance; regular checks needed to ensure quality | Low maintenance; less wear and tear on equipment | High maintenance costs due to machinery and material handling |
Best Use Case | Ideal for products needing custom branding and protection | Suitable for high-volume, temperature-sensitive items | Best for heavy-duty products requiring maximum protection |
What Are the Advantages and Disadvantages of Shrink Sleeving Technology?
Shrink sleeving technology provides a compelling alternative to traditional sleeve manufacturing. Its primary advantage lies in cost-effectiveness and adaptability. This method is especially useful for businesses looking to package temperature-sensitive products, such as food and beverages, where the shrinkable film conforms to the product’s shape, providing a snug fit. However, this technology may not offer the same level of durability or customization as traditional sleeve manufacturing, potentially limiting branding opportunities.
How Does Rigid Packaging Solutions Compare?
Rigid packaging solutions present a strong alternative, particularly for industries requiring enhanced protection for their products, such as electronics or fragile items. These solutions provide robust structural integrity and can withstand significant external pressure, making them ideal for shipping and storage. The downside is that rigid packaging can come with higher costs and less flexibility in design, which may not suit all businesses looking for unique branding options or lightweight solutions.
How Should B2B Buyers Choose the Right Solution?
Selecting the right packaging solution ultimately depends on the specific needs of your business. Consider factors such as the type of product being packaged, budget constraints, and the desired level of customization. For products that require a high degree of protection and durability, a sleeve manufacturer may be the best choice. However, if cost and ease of implementation are primary concerns, shrink sleeving technology might be more appropriate. Rigid packaging should be considered when maximum product protection is necessary, especially in sectors like electronics or glassware.
In summary, conducting a thorough alternatives analysis empowers B2B buyers to make informed decisions that align with their operational goals and customer expectations. By understanding the strengths and weaknesses of each option, businesses can optimize their packaging strategies to enhance product presentation, safety, and overall market competitiveness.
Essential Technical Properties and Trade Terminology for sleeve manufacturer
What Are the Key Technical Properties of Sleeves in Manufacturing?
When sourcing sleeves for industrial applications, understanding their technical properties is crucial for ensuring compatibility and performance. Here are some essential specifications to consider:
1. Material Grade
The material used in sleeve manufacturing significantly impacts its durability and performance. Common materials include rubber, plastic, and metal. For instance, rubber sleeves are often used in applications requiring flexibility and vibration dampening, while metal sleeves are preferred for high-strength applications. Selecting the appropriate material grade ensures that the sleeves meet the specific demands of your operations.
2. Tolerance
Tolerance refers to the permissible limit of variation in a physical dimension. In sleeve manufacturing, tight tolerances are often necessary to ensure proper fit and function. For example, a sleeve with a tolerance of ±0.01 mm is more precise than one with ±0.05 mm. Understanding tolerance specifications is essential for ensuring that the sleeves will function correctly in their intended applications, minimizing the risk of operational failures.
3. Temperature Resistance
Temperature resistance indicates how well a sleeve can withstand extreme temperatures without degrading. This property is particularly important in industries such as automotive and aerospace, where components may be exposed to high heat or cold. Selecting sleeves with appropriate temperature ratings can prevent premature wear and failure, ensuring reliability in critical applications.
4. Chemical Resistance
In many industrial environments, sleeves may come into contact with various chemicals, oils, and solvents. Chemical resistance is a crucial property that determines how well a sleeve can withstand corrosive substances. For example, sleeves made from fluoropolymer materials offer excellent chemical resistance, making them suitable for harsh environments. Assessing chemical compatibility is vital to prevent material degradation and ensure long-term performance.
5. Tensile Strength
Tensile strength measures how much force a material can withstand while being stretched or pulled before breaking. For sleeves, high tensile strength is essential, particularly in applications where they are subject to tension or pressure. Choosing sleeves with adequate tensile strength ensures they can perform effectively under load without failure.
What Are Common Trade Terms in Sleeve Manufacturing?
Familiarity with industry-specific terminology can streamline communication with suppliers and enhance the procurement process. Here are some key terms to know:
1. OEM (Original Equipment Manufacturer)
OEM refers to companies that produce parts or equipment that may be marketed by another manufacturer. In sleeve manufacturing, an OEM might create custom sleeves for a specific client, ensuring that the product meets precise specifications and branding requirements. Understanding OEM relationships can lead to more tailored solutions and better quality control.
2. MOQ (Minimum Order Quantity)
MOQ indicates the smallest quantity of a product that a supplier is willing to sell. In sleeve manufacturing, MOQs can vary based on material and design complexity. Being aware of MOQs helps buyers plan their inventory and budget, ensuring they meet supplier requirements while avoiding excess stock.
3. RFQ (Request for Quotation)
An RFQ is a formal process where buyers request price quotes from suppliers for specific products. In the context of sleeve manufacturing, submitting an RFQ allows buyers to compare pricing, specifications, and delivery timelines from multiple manufacturers, facilitating informed purchasing decisions.
4. Incoterms (International Commercial Terms)
Incoterms are a set of rules that define the responsibilities of buyers and sellers in international transactions. They clarify who is responsible for shipping costs, insurance, and risks during transport. Understanding Incoterms is vital for international B2B buyers to negotiate terms effectively and avoid misunderstandings in shipping logistics.
5. Lead Time
Lead time refers to the amount of time it takes for a supplier to fulfill an order after it has been placed. In sleeve manufacturing, lead times can vary based on production capacity and material availability. Knowing lead times is essential for effective supply chain management, allowing buyers to plan their operations accordingly.
Understanding these technical properties and trade terms empowers international B2B buyers, particularly from regions like Africa, South America, the Middle East, and Europe, to make informed decisions when sourcing sleeves, ensuring quality and operational efficiency.
Navigating Market Dynamics and Sourcing Trends in the sleeve manufacturer Sector
What Are the Current Market Dynamics and Sourcing Trends in the Sleeve Manufacturing Sector?
The sleeve manufacturing sector is experiencing significant growth, driven by various global factors. One of the primary drivers is the increasing demand for customized packaging solutions across diverse industries, including food and beverage, pharmaceuticals, and consumer goods. The rise of e-commerce has further accelerated this trend, as brands seek to enhance their product presentation and ensure safe delivery. International B2B buyers from regions like Africa, South America, the Middle East, and Europe, particularly Germany and Mexico, are increasingly seeking innovative suppliers who can provide flexible, high-quality sleeve solutions.
Emerging technologies play a crucial role in shaping sourcing trends. The integration of automation and digital tools in manufacturing processes enhances efficiency, reduces lead times, and lowers production costs. For instance, advanced printing technologies allow for intricate designs and rapid prototyping, enabling manufacturers to respond swiftly to market demands. Moreover, the adoption of data analytics helps businesses understand consumer behavior and optimize inventory management, making it easier for buyers to manage their supply chains effectively.
As international buyers navigate these market dynamics, understanding regional preferences and compliance regulations becomes essential. For example, European buyers may prioritize suppliers who adhere to stringent environmental standards, while buyers in emerging markets may focus on cost-effectiveness and scalability. By aligning sourcing strategies with these dynamics, B2B buyers can position themselves for success in the sleeve manufacturing sector.
How Important Is Sustainability and Ethical Sourcing in the Sleeve Manufacturing Industry?
Sustainability has become a pivotal concern in the sleeve manufacturing sector, reflecting the growing demand for environmentally friendly products. International B2B buyers are increasingly prioritizing suppliers who demonstrate a commitment to reducing their environmental footprint. This includes using sustainable materials, such as biodegradable plastics and recycled content, which not only meet regulatory standards but also appeal to eco-conscious consumers.
The importance of ethical sourcing cannot be overstated. B2B buyers must ensure that their suppliers maintain fair labor practices and uphold human rights throughout the supply chain. This is particularly relevant in regions where labor regulations may be less stringent. Buyers should seek suppliers who possess recognized ‘green’ certifications, such as FSC (Forest Stewardship Council) for paper products or ISO 14001 for environmental management systems. These certifications provide assurance that the materials used in sleeves are sourced responsibly and sustainably.
Investing in sustainable and ethical sourcing not only enhances brand reputation but also mitigates risks associated with supply chain disruptions and regulatory compliance. As consumers increasingly favor brands that prioritize sustainability, B2B buyers who align with these values can gain a competitive advantage in the sleeve manufacturing market.
What Has Been the Evolution of Sleeve Manufacturing in the B2B Context?
The sleeve manufacturing industry has evolved significantly over the past few decades, transitioning from traditional production methods to more sophisticated, technology-driven processes. Initially, sleeve production relied heavily on manual labor and basic machinery, resulting in longer lead times and limited customization options. However, the advent of digital printing technology and advanced manufacturing techniques has revolutionized the sector.
Today, manufacturers can produce sleeves with intricate designs and varying sizes, catering to the specific needs of different industries. The rise of e-commerce has further fueled this evolution, as brands require packaging solutions that not only protect their products but also enhance their marketability. This shift has encouraged manufacturers to invest in research and development to innovate and stay competitive.
As the industry continues to evolve, international B2B buyers are presented with new opportunities to partner with forward-thinking manufacturers who can provide tailored solutions that meet the demands of a dynamic marketplace. Understanding this evolution helps buyers make informed decisions when sourcing sleeve products, ensuring they align with current trends and future developments.
Frequently Asked Questions (FAQs) for B2B Buyers of sleeve manufacturer
-
How do I choose the right sleeve manufacturer for my business needs?
Selecting the right sleeve manufacturer involves evaluating several factors. Start by assessing their production capabilities and the materials they use. Look for manufacturers that specialize in your specific sleeve type (e.g., thermal, heat-shrink, etc.) and have experience in your industry. Request samples to evaluate quality, and check references or reviews from other clients. Finally, ensure they have the capacity to meet your volume requirements and can accommodate customization requests. -
What are the typical minimum order quantities (MOQs) for sleeve manufacturers?
Minimum order quantities can vary significantly among sleeve manufacturers based on their production capabilities and the type of sleeve you need. Generally, MOQs can range from as low as 500 to several thousand units. For specialized or custom designs, MOQs may be higher. Always confirm the MOQ with potential suppliers and consider negotiating if you are looking to place a smaller initial order. -
What payment terms should I expect when sourcing sleeves internationally?
Payment terms can vary based on the manufacturer and your negotiation. Common terms include a 30% deposit upfront, with the remaining 70% due before shipping. Some manufacturers may offer net 30 or net 60 terms after delivery. It’s crucial to discuss payment methods (e.g., wire transfer, letter of credit) and ensure you understand any fees associated with international transactions. -
How can I ensure quality assurance from my sleeve manufacturer?
To ensure quality assurance, first, check if the manufacturer is certified under relevant quality standards, such as ISO 9001. Request detailed quality control processes, including inspection methods and testing procedures. It’s also beneficial to conduct on-site audits or hire third-party inspectors to verify the production quality. Establish clear communication regarding your quality expectations and include them in your contract. -
What customization options are typically available for sleeve products?
Many sleeve manufacturers offer a range of customization options, including size, material, color, and printing. You can request specific features such as logos, barcodes, or unique designs to meet your branding needs. Discuss your requirements upfront and request samples of customized products to ensure the manufacturer can deliver to your specifications. -
How do logistics and shipping work when sourcing sleeves internationally?
Logistics and shipping depend on the agreement with your manufacturer. Most suppliers will handle shipping arrangements, but it’s essential to clarify who bears the shipping costs and responsibilities. Common shipping methods include air freight for speed or sea freight for cost-effectiveness. Ensure you understand customs regulations and duties in your country, as these can affect delivery times and overall costs. -
What are the common challenges in sourcing sleeves from international manufacturers?
Sourcing sleeves internationally can present challenges such as language barriers, cultural differences, and varying quality standards. Additionally, time zone differences may complicate communication. Delays in shipping and customs clearance can also occur. To mitigate these challenges, establish clear communication, set realistic timelines, and consider working with local intermediaries or agents familiar with the region. -
How do I assess the reliability of a sleeve manufacturer before placing an order?
Assessing the reliability of a sleeve manufacturer involves conducting thorough due diligence. Start by reviewing their company history, client testimonials, and case studies. Request references from current or past clients, and check their financial stability through credit reports. Additionally, consider visiting their facility if possible or conducting a virtual tour. Reliable manufacturers should be transparent about their processes and willing to provide comprehensive documentation regarding their capabilities.
Important Disclaimer & Terms of Use
⚠️ Important Disclaimer
The information provided in this guide, including content regarding manufacturers, technical specifications, and market analysis, is for informational and educational purposes only. It does not constitute professional procurement advice, financial advice, or legal advice.
While we have made every effort to ensure the accuracy and timeliness of the information, we are not responsible for any errors, omissions, or outdated information. Market conditions, company details, and technical standards are subject to change.
B2B buyers must conduct their own independent and thorough due diligence before making any purchasing decisions. This includes contacting suppliers directly, verifying certifications, requesting samples, and seeking professional consultation. The risk of relying on any information in this guide is borne solely by the reader.
Strategic Sourcing Conclusion and Outlook for sleeve manufacturer
What Are the Key Takeaways for B2B Buyers in Sleeve Manufacturing?
In the evolving landscape of sleeve manufacturing, strategic sourcing emerges as a critical component for international B2B buyers. By focusing on reliable suppliers, businesses can ensure consistent quality and timely delivery, which are vital for maintaining competitive advantage. Understanding regional market dynamics in Africa, South America, the Middle East, and Europe allows buyers to tailor their sourcing strategies effectively, leveraging local strengths and mitigating risks.
How Can Strategic Sourcing Enhance Your Supply Chain?
Investing time in strategic sourcing not only optimizes costs but also fosters innovation through collaboration with manufacturers who are committed to sustainability and technological advancements. This is particularly relevant as global supply chains face disruptions; having a diverse pool of suppliers can enhance resilience and adaptability.
What Should B2B Buyers Do Next?
As you move forward, consider evaluating your current sourcing strategies and exploring partnerships with manufacturers that align with your sustainability goals. Engage in discussions with potential suppliers to understand their capabilities and commitment to quality. By doing so, you position your business for long-term success in a competitive market.
Embrace the future of sleeve manufacturing by making informed decisions today. Your proactive approach can lead to significant benefits, ensuring that your supply chain is not only efficient but also robust against future challenges.