Discover Top Flask Manufacturers: Save Costs & Improve Quality (2025)
Introduction: Navigating the Global Market for flask manufacturer
Navigating the global market for flask manufacturers presents a unique set of challenges for international B2B buyers, particularly those sourcing from diverse regions such as Africa, South America, the Middle East, and Europe. The complexity of finding reliable suppliers, understanding regional manufacturing standards, and ensuring quality control can be daunting. This guide aims to simplify this process by providing a comprehensive overview of the flask manufacturing landscape, including types of flasks, their various applications, and essential tips for vetting suppliers effectively.
In this guide, you will discover the different materials used in flask production, from stainless steel to glass, and the implications of each for durability and functionality. We will also delve into the specific applications of flasks in various industries, such as food and beverage, healthcare, and education, allowing you to align your sourcing strategies with market needs. Furthermore, we will provide insights into cost factors, enabling you to make informed budgetary decisions.
By the end of this guide, you will be equipped with the knowledge and tools necessary to navigate the complexities of the global flask market confidently. Whether you’re a buyer in Italy looking for sustainable options or a procurement manager in South Africa seeking competitive pricing, this resource will empower you to make well-informed purchasing decisions that meet your organizational requirements.
Understanding flask manufacturer Types and Variations
Type Name | Key Distinguishing Features | Primary B2B Applications | Brief Pros & Cons for Buyers |
---|---|---|---|
Custom Flask Manufacturers | Tailored designs, materials, and sizes. | Promotional products, corporate gifts, branding. | Pros: Unique branding opportunities. Cons: Higher costs. |
Mass Production Flask Manufacturers | Standardized designs, high volume output. | Retail, bulk orders, general consumer use. | Pros: Cost-effective, quick delivery. Cons: Limited customization. |
Eco-Friendly Flask Manufacturers | Sustainable materials, eco-conscious designs. | Health and wellness, environmentally-focused brands. | Pros: Appeals to green consumers. Cons: Potentially higher prices. |
Specialty Flask Manufacturers | Niche designs (e.g., vacuum-insulated, sports). | Outdoor activities, specialized markets. | Pros: High functionality and performance. Cons: May not be widely available. |
Luxury Flask Manufacturers | Premium materials, high-end craftsmanship. | Gifting, luxury branding, upscale markets. | Pros: Prestige and quality. Cons: High price point. |
What Are the Characteristics of Custom Flask Manufacturers?
Custom flask manufacturers specialize in producing flasks tailored to specific client requirements, including unique designs, materials, and sizes. These manufacturers are particularly suitable for businesses looking to create promotional products or corporate gifts that stand out. When considering a purchase, B2B buyers should assess the manufacturer’s design capabilities and minimum order quantities, as customization may lead to longer lead times and higher costs.
How Do Mass Production Flask Manufacturers Operate?
Mass production flask manufacturers focus on creating standardized designs at scale, enabling them to fulfill large orders quickly and efficiently. This type of manufacturer is ideal for businesses needing bulk purchases for retail or general consumer applications. Buyers should evaluate the pricing structure and lead times, as well as the quality of materials used, to ensure the flasks meet their market standards while remaining cost-effective.
Why Choose Eco-Friendly Flask Manufacturers?
Eco-friendly flask manufacturers produce products using sustainable materials and environmentally conscious practices. These manufacturers appeal to businesses in health and wellness sectors or those targeting eco-conscious consumers. When purchasing from eco-friendly manufacturers, B2B buyers should consider the certifications of materials used and the overall environmental impact of the production process, as these factors can enhance brand reputation.
What Makes Specialty Flask Manufacturers Unique?
Specialty flask manufacturers create niche products, such as vacuum-insulated flasks or those designed for specific outdoor activities. These flasks are often highly functional and cater to specialized markets. Buyers should focus on the specific features offered, such as insulation capabilities or durability, and assess how well these align with their target audience’s needs. Availability may vary, so establishing a reliable supply chain is crucial.
How Do Luxury Flask Manufacturers Stand Out?
Luxury flask manufacturers emphasize premium materials and high-end craftsmanship, targeting upscale markets and gifting opportunities. These manufacturers are suitable for brands looking to convey prestige and quality. B2B buyers must consider the price point and the potential return on investment when purchasing luxury items, as they often require a higher upfront cost but can enhance brand image and customer loyalty significantly.
Related Video: Steel bottle flask manufacturing process – Sun Glory
Key Industrial Applications of flask manufacturer
Industry/Sector | Specific Application of flask manufacturer | Value/Benefit for the Business | Key Sourcing Considerations for this Application |
---|---|---|---|
Pharmaceutical Industry | Production of laboratory flasks for drug formulation | Ensures accurate and reproducible results in drug testing | Quality certifications (ISO, GMP), material compatibility, and delivery timelines |
Food and Beverage Sector | Manufacturing of flasks for beverage storage and transport | Maintains product integrity and extends shelf life | Food safety standards, material certifications, and custom designs |
Chemical Processing | Use of flasks for chemical reactions and storage | Enhances safety and efficiency in chemical handling | Chemical resistance, temperature tolerance, and bulk purchasing agreements |
Research and Development | Development of specialized flasks for scientific experiments | Supports innovation and research accuracy | Customization options, technical support, and rapid prototyping capabilities |
Environmental Testing | Production of flasks for sampling and testing pollutants | Aids in compliance with environmental regulations | Certification for environmental standards, durability, and ease of use |
How is Flask Manufacturing Applied in the Pharmaceutical Industry?
In the pharmaceutical industry, flasks are crucial for drug formulation and testing. They are used to mix, store, and analyze compounds under controlled conditions. The accuracy of drug testing directly influences the safety and efficacy of pharmaceuticals, making high-quality flasks essential. International buyers, particularly from regions with stringent regulations like Europe, must ensure that manufacturers provide flasks that meet quality certifications such as ISO and GMP. Additionally, compatibility with various chemical agents is a critical factor to consider.
What Role Do Flasks Play in the Food and Beverage Sector?
In the food and beverage sector, flasks are employed for both storage and transportation of liquids. They help maintain product integrity by preventing contamination and extending shelf life. For businesses in Africa and South America, where logistics can be challenging, sourcing flasks that comply with food safety standards is paramount. Buyers should look for manufacturers that offer certifications for materials used, ensuring they are safe for food contact, and consider custom designs to meet specific branding needs.
How Are Flasks Utilized in Chemical Processing?
Flasks in chemical processing serve as essential tools for conducting reactions and storing chemicals. They are designed to withstand various chemical interactions, enhancing safety and efficiency in handling hazardous materials. B2B buyers from the Middle East and Europe must prioritize sourcing flasks that offer high chemical resistance and temperature tolerance. Long-term contracts with manufacturers can facilitate bulk purchasing, ensuring consistent supply and cost-effectiveness.
Why Are Flasks Important for Research and Development?
In research and development, specialized flasks support scientific experiments by providing controlled environments for reactions and analyses. They enable researchers to innovate and achieve accurate results, which are vital for advancements in various fields. Buyers in Europe and Africa should seek manufacturers that offer customization options, allowing for tailored solutions that meet specific research needs. Technical support and rapid prototyping capabilities are additional factors that enhance the sourcing process.
How Do Flasks Support Environmental Testing?
Flasks are pivotal in environmental testing, particularly for sampling and analyzing pollutants in various ecosystems. They help ensure compliance with environmental regulations by providing reliable and accurate testing methods. International buyers in sectors focused on sustainability must ensure that the flasks they procure are certified for environmental standards. Durability and ease of use are also critical considerations, particularly when dealing with diverse and challenging testing environments.
Related Video: Types Of Flowmeters And Their Industrial Applications.
3 Common User Pain Points for ‘flask manufacturer’ & Their Solutions
Scenario 1: Navigating Quality Assurance in Flask Manufacturing
The Problem: One of the most significant challenges for B2B buyers sourcing flasks is ensuring consistent quality. Many manufacturers may not adhere to the same standards, leading to discrepancies in product performance, safety, and durability. For buyers, particularly those in sectors such as pharmaceuticals or food and beverage, the stakes are high. A subpar flask can compromise product integrity, result in compliance issues, and ultimately harm brand reputation.
The Solution: To navigate this issue, buyers should implement a robust quality assurance process when selecting a flask manufacturer. Start by requesting samples and performing rigorous testing to evaluate the material properties and overall performance of the flasks. Establish clear specifications and standards, and communicate these expectations with the manufacturer upfront. Additionally, consider conducting regular audits or site visits to the manufacturing facility to ensure compliance with quality standards. Collaborating with manufacturers who are ISO certified or who follow established industry guidelines can further mitigate risks associated with quality.
Scenario 2: Managing Lead Times and Delivery Schedules
The Problem: In the fast-paced world of B2B commerce, delays in production and delivery can severely disrupt operations. Buyers often face the frustration of manufacturers that fail to meet lead times, which can result from various factors including supply chain disruptions, inefficient production processes, or miscommunication. Such delays can hinder product launches and lead to lost sales opportunities, especially in regions with high demand like Africa and Europe.
The Solution: To address lead time challenges, buyers should prioritize establishing a transparent communication channel with their flask manufacturers. Engage in discussions about production timelines during the initial negotiation phase and set clear deadlines. Implementing a just-in-time inventory approach can also help manage stock levels and minimize the impact of potential delays. Additionally, consider building relationships with multiple manufacturers or suppliers to create a backup plan. This strategy allows for flexibility and ensures that if one manufacturer cannot meet a deadline, another can step in.
Scenario 3: Overcoming Customization Limitations
The Problem: Many B2B buyers require customized flasks to meet specific branding or functional needs. However, manufacturers often have limitations regarding customization options, whether it be in terms of materials, sizes, or printing capabilities. This can lead to frustration for buyers who wish to differentiate their products in a competitive marketplace, especially in diverse regions such as South America and the Middle East where unique designs may be necessary to appeal to local consumers.
The Solution: To successfully navigate customization limitations, buyers should conduct thorough research to identify manufacturers that specialize in bespoke solutions. When approaching a manufacturer, clearly articulate your customization requirements and inquire about their capabilities. It can be beneficial to collaborate with manufacturers who have experience in your industry, as they may offer more tailored solutions. Establishing a partnership approach can foster innovation and encourage manufacturers to expand their customization options to meet your needs. Additionally, consider leveraging technology like 3D modeling to visualize your custom designs before production, ensuring that the end product aligns with your expectations.
Strategic Material Selection Guide for flask manufacturer
When selecting materials for flask manufacturing, it is essential to understand the properties, advantages, and limitations of various materials. This knowledge helps international B2B buyers make informed decisions, especially in diverse markets such as Africa, South America, the Middle East, and Europe. Here, we analyze four common materials used in flask manufacturing: stainless steel, glass, plastic, and aluminum.
What Are the Key Properties of Stainless Steel for Flask Manufacturing?
Stainless steel is renowned for its excellent mechanical properties, including high tensile strength and resistance to corrosion. It typically withstands temperatures ranging from -200°C to 800°C, making it suitable for a wide range of applications. The most common grades used in flask manufacturing are 304 and 316, with 316 offering superior corrosion resistance, particularly against chlorides.
Pros and Cons of Stainless Steel:
– Pros: Durability and longevity are significant advantages, as stainless steel flasks can endure harsh environments without degrading. They are also easy to clean and maintain.
– Cons: The initial manufacturing cost is relatively high compared to other materials, and the complexity of the production process can lead to longer lead times.
Impact on Application: Stainless steel flasks are ideal for both hot and cold liquids, making them versatile for various industries, including food and beverage, pharmaceuticals, and chemicals.
Considerations for International Buyers: Compliance with international standards such as ASTM and DIN is crucial. Buyers from Europe, particularly Italy and Germany, may prioritize materials that meet stringent quality certifications.
How Does Glass Perform as a Flask Material?
Glass is a classic choice for flasks, particularly in laboratory settings. It is chemically inert, meaning it does not react with most substances, which is vital for applications involving sensitive chemicals.
Pros and Cons of Glass:
– Pros: Glass flasks offer excellent clarity, allowing for easy monitoring of contents. They are also recyclable, which appeals to environmentally conscious buyers.
– Cons: Fragility is a major drawback, as glass can break easily under impact or thermal shock. Additionally, glass flasks can be heavier than their metal or plastic counterparts.
Impact on Application: Glass is suitable for storing acids, bases, and other reactive substances, making it popular in laboratories and pharmaceutical industries.
Considerations for International Buyers: Buyers should ensure that glass products comply with safety regulations, especially in regions with strict packaging and transportation laws.
What Are the Advantages of Using Plastic in Flask Manufacturing?
Plastic, particularly high-density polyethylene (HDPE) and polypropylene (PP), is increasingly popular in flask manufacturing due to its lightweight and cost-effective nature. These materials are resistant to many chemicals and can withstand moderate temperatures.
Pros and Cons of Plastic:
– Pros: The lightweight nature of plastic makes it easy to transport, and the lower cost can be a significant advantage for bulk purchases. Additionally, plastics can be molded into complex shapes.
– Cons: Plastics may not withstand high temperatures as effectively as metals or glass and can be prone to scratching and wear over time.
Impact on Application: Plastic flasks are suitable for non-reactive liquids and are widely used in the food and beverage industry, as well as in consumer products.
Considerations for International Buyers: Compliance with food safety standards, such as FDA regulations in the U.S. or EFSA in Europe, is essential for buyers in these regions.
Why Choose Aluminum for Flask Manufacturing?
Aluminum is another viable option for flask manufacturing, known for its lightweight and excellent thermal conductivity. It is often anodized to enhance corrosion resistance and durability.
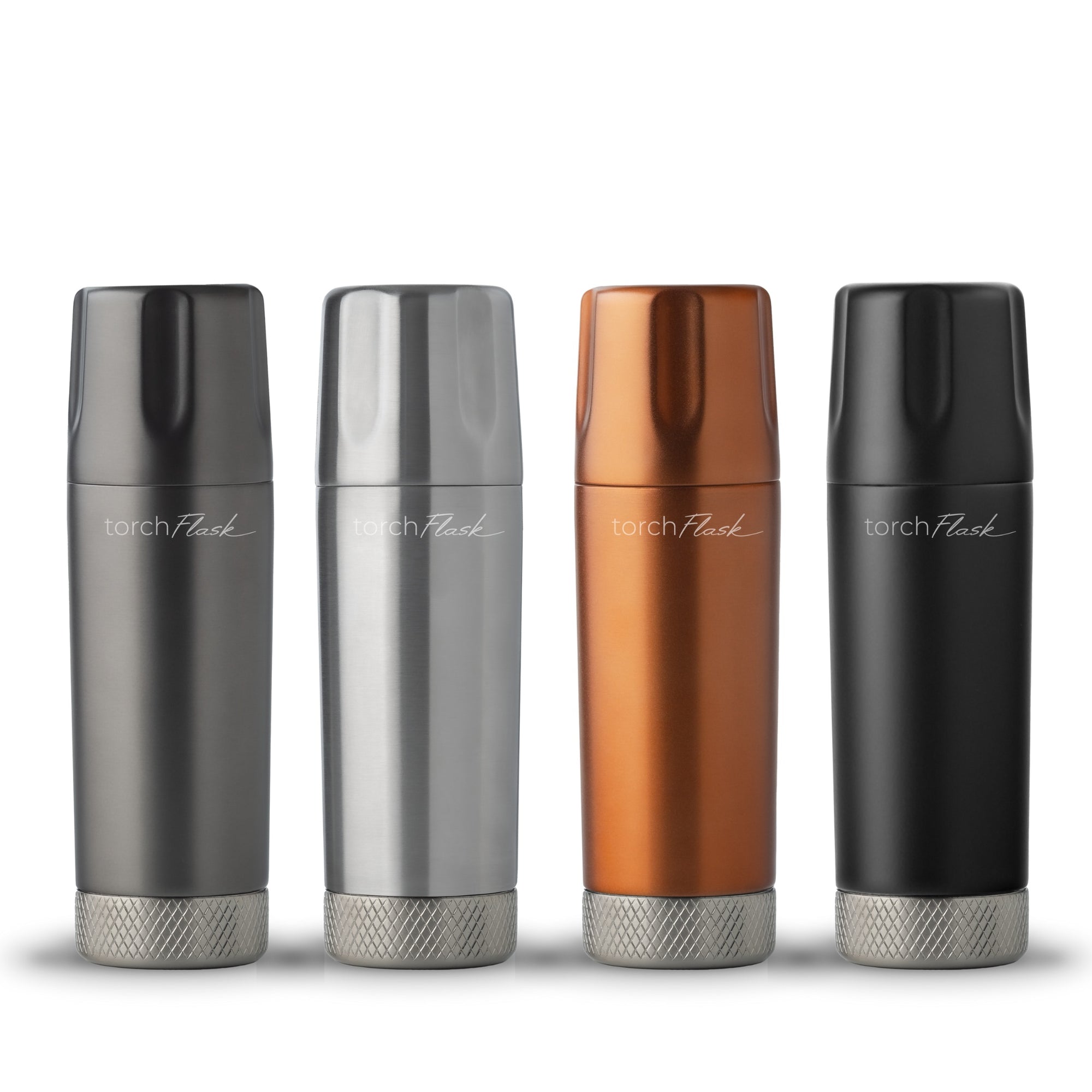
A stock image related to flask manufacturer.
Pros and Cons of Aluminum:
– Pros: Aluminum flasks are lightweight and can be produced at a lower cost than stainless steel. They also offer good thermal insulation when designed with double-wall construction.
– Cons: Aluminum is more susceptible to corrosion than stainless steel, especially if the anodization layer is compromised. It may also impart a metallic taste to certain liquids.
Impact on Application: Aluminum flasks are commonly used for beverages and are popular among outdoor enthusiasts for their portability.
Considerations for International Buyers: Buyers should be aware of the anodization process and ensure that products meet relevant international standards, especially in regions with high-quality expectations.
Summary Table of Material Selection for Flask Manufacturing
Material | Typical Use Case for flask manufacturer | Key Advantage | Key Disadvantage/Limitation | Relative Cost (Low/Med/High) |
---|---|---|---|---|
Stainless Steel | Food & beverage, chemicals | High durability and corrosion resistance | Higher manufacturing cost | High |
Glass | Laboratory, pharmaceuticals | Chemically inert and recyclable | Fragile and heavy | Medium |
Plastic | Food & beverage, consumer products | Lightweight and cost-effective | Limited temperature resistance | Low |
Aluminum | Beverages, outdoor applications | Lightweight and good thermal conductivity | Susceptible to corrosion | Medium |
This guide provides a comprehensive overview of material selection for flask manufacturing, enabling B2B buyers to make informed decisions based on their specific needs and regional considerations.
In-depth Look: Manufacturing Processes and Quality Assurance for flask manufacturer
What Are the Key Stages in the Manufacturing Process for Flasks?
The manufacturing process for flasks involves several critical stages, each essential for ensuring the final product meets quality and performance standards. Here are the main stages typically involved:
Material Preparation: How Is Raw Material Selected and Processed?
The first step in flask manufacturing is the selection and preparation of materials. Common materials used include stainless steel, glass, and high-grade plastics. Each material is chosen based on the flask’s intended use—whether for beverages, laboratory applications, or outdoor activities.
Once selected, the raw materials undergo preparation, which may include cutting, cleaning, and treating to enhance their properties. For instance, stainless steel flasks are often treated to resist corrosion and improve durability. This preparation is vital as it sets the foundation for the quality of the finished product.
What Techniques Are Used in Forming Flasks?
Forming is the next crucial stage, where the prepared materials are shaped into the flask’s desired form. Various techniques are employed based on the type of flask being manufactured:
-
Metal Stamping and Deep Drawing: For stainless steel flasks, metal stamping is commonly used, followed by deep drawing to achieve the desired shape. This method is efficient and can produce high volumes of consistent products.
-
Blow Molding: For plastic flasks, blow molding is a prevalent technique. This process involves inflating a heated plastic tube into a mold, allowing for complex shapes and lightweight designs.
-
Glass Blowing: In the case of glass flasks, traditional glass blowing techniques may be used, requiring skilled artisans to ensure uniform thickness and quality.
Each of these techniques has its own advantages, and the choice often depends on the specific requirements of the flask, such as insulation properties or aesthetic design.
How Is Assembly Conducted in Flask Manufacturing?
After forming, the next step is assembly, which involves bringing together various components of the flask. This stage may include attaching lids, seals, or insulation layers, depending on the flask’s design.
Quality assurance during assembly is critical; manufacturers often employ automated systems for precision and efficiency. Manual assembly may also be used for more intricate designs, ensuring that each component fits perfectly and functions as intended.
What Finishing Processes Are Applied to Flasks?
Finishing processes add the final touches to the flasks, enhancing both aesthetics and functionality. Common finishing techniques include:
-
Polishing: For metal flasks, polishing is essential to achieve a smooth, reflective surface that is both visually appealing and easy to clean.
-
Coating: Applying coatings can improve resistance to scratches and corrosion. For instance, powder coating is popular in outdoor flasks to provide a durable finish.
-
Printing and Labeling: Many flasks feature branding or decorative elements, which are applied using screen printing or laser engraving.
These finishing processes not only enhance the product’s appearance but also its usability and longevity.
What Quality Assurance Standards Should B2B Buyers Consider?
Quality assurance is a fundamental aspect of flask manufacturing, ensuring that products meet international and industry-specific standards. For B2B buyers, understanding these standards is crucial for making informed purchasing decisions.
What Are the Relevant International Standards for Flask Manufacturing?
-
ISO 9001: This international standard focuses on quality management systems and is applicable to any organization, including flask manufacturers. It emphasizes customer satisfaction and continuous improvement, ensuring that the manufacturer maintains high-quality production practices.
-
CE Marking: For flasks sold in Europe, CE marking indicates compliance with EU safety, health, and environmental protection standards. This is particularly important for flasks used in food and beverage applications.
-
API Standards: For flasks used in pharmaceutical or laboratory settings, adherence to American Petroleum Institute (API) standards is essential. These standards ensure that the products are safe and effective for use in critical applications.
What Are the Key QC Checkpoints in Flask Manufacturing?
Quality control (QC) involves several checkpoints throughout the manufacturing process to ensure that each flask meets established standards. The main QC checkpoints include:
-
Incoming Quality Control (IQC): This initial checkpoint assesses the quality of raw materials before they enter the production line. Materials that do not meet specifications are rejected to prevent defects in the final product.
-
In-Process Quality Control (IPQC): During the manufacturing process, IPQC involves regular inspections at various stages, such as after forming and assembly. This helps identify and rectify issues in real-time, ensuring that defects are minimized.
-
Final Quality Control (FQC): The final inspection occurs before the flasks are packaged and shipped. FQC checks for overall appearance, functionality, and adherence to specifications, ensuring that only products meeting quality standards reach the market.
How Can B2B Buyers Verify Supplier Quality Control?
B2B buyers must take proactive steps to verify the quality control measures of their suppliers. Here are some effective strategies:
-
Conduct Audits: Regular audits of the manufacturing facilities can provide insights into the supplier’s quality control processes. Audits should assess compliance with international standards and evaluate the effectiveness of their QC checkpoints.
-
Request Quality Reports: Suppliers should provide documentation of their quality control processes, including results from IQC, IPQC, and FQC. These reports can help buyers assess whether the supplier maintains high standards throughout production.
-
Engage Third-Party Inspectors: Hiring independent third-party inspectors can provide an unbiased assessment of the supplier’s manufacturing practices and quality control. This is especially important for international transactions where direct oversight may be challenging.
What Are the QC and Certification Nuances for International B2B Buyers?
International buyers, particularly from regions like Africa, South America, the Middle East, and Europe, should be aware of specific nuances related to QC and certification:
-
Cultural and Regulatory Differences: Different regions may have varying standards and regulations for manufacturing and quality assurance. Buyers must understand these differences to ensure compliance and prevent issues during importation.
-
Documentation and Certification Requirements: Importing flasks may require specific documentation, including compliance certificates and customs declarations. Buyers should ensure that their suppliers can provide all necessary documentation to facilitate a smooth import process.
-
Logistical Considerations: International shipping may introduce additional risks, such as damage during transit. Therefore, selecting suppliers with robust packaging and handling processes is crucial to maintaining product integrity.
By understanding these manufacturing processes and quality assurance practices, international B2B buyers can make informed decisions, ensuring they partner with reliable flask manufacturers that meet their quality and performance expectations.
Practical Sourcing Guide: A Step-by-Step Checklist for ‘flask manufacturer’
In the competitive landscape of international B2B sourcing, particularly for flask manufacturers, it is essential for buyers to navigate the process meticulously. This guide provides a structured checklist to streamline your procurement journey, ensuring you select the right supplier for your business needs.
Step 1: Define Your Technical Specifications
Clearly outline the specifications of the flasks you need, including materials, sizes, design features, and any regulatory compliance requirements specific to your market. This step is crucial as it sets the foundation for your sourcing process. A well-defined specification helps in communicating your requirements to potential suppliers and ensures they can meet your needs effectively.
Step 2: Conduct Market Research
Research the global market for flask manufacturers, focusing on regions that align with your sourcing strategy, such as Africa, South America, the Middle East, and Europe. Look for manufacturers that specialize in your required flask type and have a proven track record. This will help you identify key players and emerging suppliers who can meet your quality and pricing expectations.
Step 3: Evaluate Potential Suppliers
Before committing, it’s crucial to vet suppliers thoroughly. Request company profiles, case studies, and references from buyers in similar industries or regions. Assess their production capabilities, quality control measures, and experience with international shipping. Don’t just rely on their website; consider visiting their facilities or conducting virtual audits if feasible.
Step 4: Verify Supplier Certifications
Ensure that your selected suppliers possess the necessary certifications for quality and safety, such as ISO 9001 for quality management and relevant industry-specific certifications. Certifications not only demonstrate compliance with international standards but also provide assurance regarding the quality of the products you will receive.
Step 5: Request Samples for Testing
Always request samples before placing a large order. This allows you to assess the quality, design, and functionality of the flasks firsthand. Testing samples against your specifications will help confirm that the supplier can deliver products that meet your expectations, ultimately reducing the risk of unsatisfactory orders.
Step 6: Negotiate Terms and Pricing
Once you have identified a suitable supplier, engage in negotiations regarding pricing, payment terms, lead times, and shipping arrangements. Be clear about your budget and ensure that all terms are documented. This step is vital for establishing a mutually beneficial relationship and avoiding misunderstandings later on.
Step 7: Establish a Communication Plan
Effective communication is key to a successful partnership. Establish a clear communication plan with your supplier, outlining preferred methods of contact, frequency of updates, and key points of contact on both sides. This ensures that both parties are aligned throughout the sourcing process and can address any issues promptly.
By following this checklist, international B2B buyers can approach the procurement of flask manufacturing with confidence, ensuring they choose a supplier that meets their specific needs while fostering a productive business relationship.
Comprehensive Cost and Pricing Analysis for flask manufacturer Sourcing
What Are the Key Cost Components for Flask Manufacturing?
When sourcing flasks from manufacturers, understanding the cost structure is crucial for making informed purchasing decisions. The primary cost components include:
-
Materials: The type of materials used (e.g., stainless steel, glass, plastic) significantly affects the overall cost. High-quality materials often come at a premium but can enhance the durability and aesthetic appeal of the product.
-
Labor: Labor costs vary by region and the complexity of the manufacturing process. In countries with higher labor costs, such as Germany and Italy, manufacturers may employ more skilled labor, which can lead to better quality but higher prices.
-
Manufacturing Overhead: This encompasses indirect costs such as utilities, rent, and administrative expenses associated with production. These costs can vary greatly depending on the manufacturer’s location and operational efficiency.
-
Tooling: Initial setup costs for molds and machinery can be significant, especially for custom flasks. Buyers should consider these costs when assessing the total price, particularly for low-volume orders.
-
Quality Control (QC): Implementing rigorous QC processes incurs additional costs but is essential for ensuring product reliability and compliance with international standards. This is particularly important for buyers in regulated markets.
-
Logistics: Transportation costs can fluctuate based on distance, shipping methods, and fuel prices. Understanding the logistics involved in moving products from the manufacturer to the buyer’s location is essential for accurate cost estimation.
-
Margin: Manufacturer profit margins vary and can be influenced by market demand, competition, and the perceived value of the product. Buyers should be aware of these margins to better negotiate prices.
How Do Price Influencers Impact Flask Manufacturing Costs?
Several factors influence the pricing of flasks, making it essential for international B2B buyers to consider these when sourcing:
-
Volume and Minimum Order Quantity (MOQ): Larger orders typically reduce the per-unit cost. Buyers should negotiate MOQs that align with their needs to maximize cost efficiency.
-
Specifications and Customization: Customized designs or specific features (e.g., insulation, size) can increase costs. Buyers must balance the need for customization with budget constraints.
-
Quality and Certifications: Flasks that meet international quality standards or carry certifications (e.g., ISO, FDA) may have higher costs due to the added compliance efforts. Buyers should assess whether these certifications are necessary for their market.
-
Supplier Factors: The reputation and reliability of the supplier can impact pricing. Established suppliers may charge a premium for their experience and quality assurance, while newer suppliers might offer lower prices to gain market share.
-
Incoterms: Understanding shipping terms (Incoterms) is crucial for calculating the total cost. For example, FOB (Free on Board) means the buyer takes on shipping costs once the goods are loaded onto the vessel, while DDP (Delivered Duty Paid) includes all costs until the goods reach the buyer.
What Are Essential Buyer Tips for Cost-Efficient Flask Sourcing?
International B2B buyers, especially from Africa, South America, the Middle East, and Europe, should consider the following strategies to ensure cost-effective sourcing:
-
Negotiate Prices: Always engage in negotiations. Suppliers may have flexibility in pricing, especially for larger orders or long-term partnerships.
-
Evaluate Total Cost of Ownership (TCO): Consider all associated costs, including shipping, duties, and potential after-sales service. A lower initial price may lead to higher long-term costs if quality is compromised.
-
Understand Pricing Nuances: Be aware of regional pricing trends and economic conditions that may affect costs. For instance, fluctuations in currency exchange rates can impact the overall expense for buyers from Europe sourcing from Asia.
-
Build Relationships with Suppliers: Developing strong relationships can lead to better pricing and terms over time. Trust and communication often yield favorable outcomes in negotiations.
-
Stay Informed: Keep up with industry trends and market changes. Understanding the competitive landscape can provide leverage when discussing pricing with suppliers.
Conclusion
In summary, a comprehensive understanding of cost components, price influencers, and strategic negotiation can empower B2B buyers in their sourcing decisions for flasks. By considering these factors, buyers can optimize their procurement processes and achieve better pricing outcomes tailored to their specific needs.
Alternatives Analysis: Comparing flask manufacturer With Other Solutions
Understanding the Importance of Alternative Solutions
In the competitive landscape of international B2B transactions, particularly for buyers in regions such as Africa, South America, the Middle East, and Europe, exploring alternatives to a traditional flask manufacturer can be crucial. Buyers must evaluate various solutions that can meet their operational needs, enhance efficiency, and potentially reduce costs. This section compares the traditional flask manufacturing process with two viable alternatives: 3D Printing and Injection Molding.
Comparison Table of Flask Manufacturing Alternatives
Comparison Aspect | Flask Manufacturer | 3D Printing | Injection Molding |
---|---|---|---|
Performance | High-quality, durable flasks | Customizable, rapid prototyping | High volume production |
Cost | Moderate initial investment | Low initial investment, high per-unit cost | High upfront costs, lower per-unit cost |
Ease of Implementation | Requires established processes | Easy to implement, requires design software | Complex setup, requires molds |
Maintenance | Regular maintenance needed | Minimal maintenance | Maintenance of molds needed |
Best Use Case | Bulk production of standard flasks | Small batches, custom designs | Large-scale production |
In-Depth Analysis of Alternatives
What are the advantages and disadvantages of 3D Printing as an alternative?
3D printing presents a modern approach to flask production, offering significant customization capabilities. It allows for rapid prototyping, making it an excellent option for businesses needing unique designs or small batches. The initial investment is relatively low compared to traditional manufacturing methods, but the per-unit cost can be higher, especially for larger quantities. Additionally, 3D printing requires design software and expertise, which can be a barrier for some companies. Its minimal maintenance requirements make it attractive for firms looking to reduce operational downtime.
How does Injection Molding compare to flask manufacturing?
Injection molding is a well-established method that excels in high-volume production scenarios. Once the molds are created, the cost per unit drops significantly, making it economically viable for large orders. However, the initial investment in molds can be substantial, which may deter smaller businesses or those with fluctuating demand. The setup process is complex and requires precision, but once operational, it offers consistent quality and efficiency. Maintenance of the molds is necessary to ensure longevity and performance, which could add to operational overhead.
Conclusion: Which Solution Should International B2B Buyers Choose?
Choosing the right solution for flask production depends largely on your specific operational needs, budget constraints, and production volume. If your business requires high customization with lower initial investment, 3D printing may be the most suitable option. Conversely, if you expect to produce large quantities consistently, injection molding could provide the best long-term cost efficiency despite its higher upfront costs. Evaluating these alternatives in the context of your operational goals will enable you to make an informed decision that aligns with your business strategy.
Essential Technical Properties and Trade Terminology for flask manufacturer
What Are the Essential Technical Properties for Flask Manufacturing?
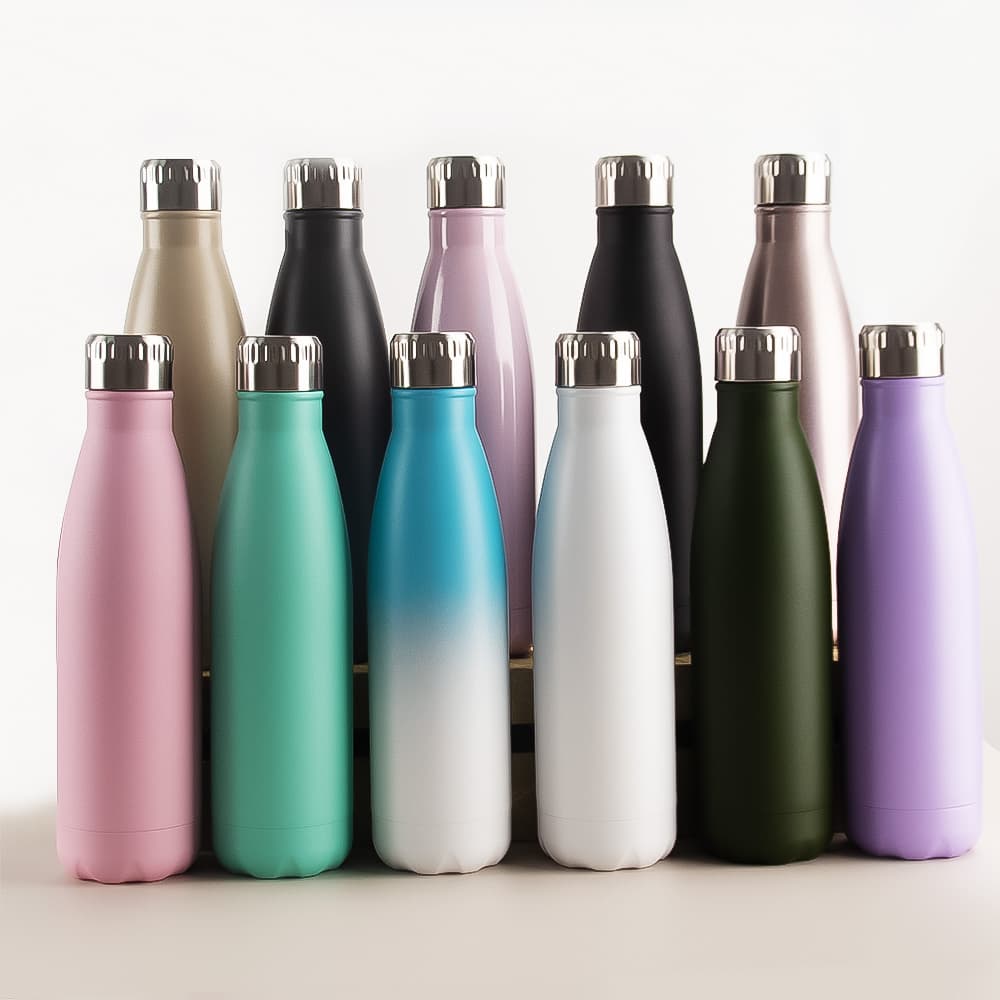
A stock image related to flask manufacturer.
In the competitive landscape of flask manufacturing, understanding the critical technical properties can significantly influence purchasing decisions. Here are some key specifications that B2B buyers should consider:
1. Material Grade
The material grade refers to the quality and composition of the raw materials used in flask production. Common materials include stainless steel, glass, and plastic. Each material has unique properties affecting durability, heat resistance, and chemical compatibility. For instance, stainless steel flasks are preferred for their corrosion resistance and longevity, making them ideal for industries that require reliable performance in harsh environments.
2. Tolerance
Tolerance defines the permissible limits of variation in a physical dimension. In flask manufacturing, maintaining tight tolerances is crucial for ensuring that components fit together correctly, thereby preventing leaks and enhancing user safety. Buyers should look for manufacturers who can meet specific tolerance requirements, as this can affect the functionality and reliability of the final product.
3. Capacity
Capacity indicates the volume of liquid the flask can hold, typically measured in liters or ounces. This property is vital for buyers who need flasks for specific applications, such as medical use or food service. Understanding the required capacity helps in selecting the right product for the intended use, ensuring efficiency and customer satisfaction.
4. Temperature Resistance
Temperature resistance refers to a flask’s ability to withstand extreme heat or cold without losing structural integrity. This property is particularly important for applications in laboratory settings or outdoor use. B2B buyers should inquire about temperature ranges to ensure the selected flasks can handle their operational demands.
5. Surface Finish
The surface finish of a flask affects not only its aesthetic appeal but also its functionality. A smooth finish can enhance cleaning efficiency and reduce contamination risks, while a textured finish may improve grip. Buyers should consider the intended use and choose a surface finish that aligns with their operational requirements.
What Are Common Trade Terms in Flask Manufacturing?
Understanding industry jargon is essential for effective communication and negotiation in the flask manufacturing sector. Here are some common terms that B2B buyers should familiarize themselves with:
1. OEM (Original Equipment Manufacturer)
OEM refers to a company that produces parts or equipment that may be marketed by another manufacturer. In the context of flask manufacturing, an OEM may provide custom-designed flasks for other brands. Buyers should consider OEM partnerships for tailored solutions that meet specific needs.
2. MOQ (Minimum Order Quantity)
MOQ is the smallest quantity of product that a supplier is willing to sell. This term is crucial for B2B buyers as it influences inventory management and budgeting. Understanding MOQ helps in planning purchases and negotiating better terms with manufacturers.
3. RFQ (Request for Quotation)
An RFQ is a document used to invite suppliers to submit price quotations for specific products or services. When dealing with flask manufacturers, issuing an RFQ can help buyers gather competitive pricing and terms, enabling informed decision-making.
4. Incoterms (International Commercial Terms)
Incoterms are a set of international rules that define the responsibilities of buyers and sellers in international transactions. Familiarity with these terms is essential for B2B buyers in understanding shipping costs, risks, and responsibilities associated with flask procurement.
5. Lead Time
Lead time is the duration from the placement of an order to the delivery of the product. In flask manufacturing, knowing the lead time helps buyers manage their supply chain effectively. It is vital to align production schedules with demand forecasts to ensure timely availability of flasks.
By understanding these essential technical properties and industry terms, international B2B buyers can make informed decisions that optimize their purchasing strategies and enhance operational efficiency.
Navigating Market Dynamics and Sourcing Trends in the flask manufacturer Sector
What Are the Key Market Dynamics and Trends in the Flask Manufacturing Sector?
The global flask manufacturing sector is experiencing significant growth, driven by increasing demand across various industries including pharmaceuticals, food and beverage, and personal care. The rise in environmental awareness is also reshaping market dynamics, with a growing preference for sustainable products. International B2B buyers, particularly from Africa, South America, the Middle East, and Europe, are increasingly seeking suppliers who can provide high-quality flasks that meet both functional and environmental standards.
Emerging technologies are transforming sourcing practices. Automation and digital tools are streamlining supply chain management, enhancing transparency, and enabling real-time tracking of products. Additionally, advancements in materials science have led to the development of innovative flask designs that improve insulation and durability. Buyers are encouraged to adopt a proactive approach, utilizing data analytics to forecast demand and optimize inventory levels, which can significantly reduce costs.
Furthermore, regulatory frameworks are evolving, particularly in regions such as the EU, where stringent regulations govern materials used in manufacturing. This necessitates a thorough understanding of compliance requirements among international buyers to avoid potential disruptions in sourcing. As a result, the ability to adapt to these changes while ensuring quality and compliance will be critical for B2B buyers in the flask manufacturing sector.
How Important Is Sustainability and Ethical Sourcing in the Flask Manufacturing Industry?
Sustainability has become a cornerstone of modern manufacturing, especially in the flask sector. The environmental impact of production processes and materials used is under scrutiny, prompting buyers to prioritize ethical sourcing practices. This includes selecting suppliers who employ sustainable manufacturing methods, minimize waste, and utilize eco-friendly materials.
The importance of ethical supply chains cannot be overstated. Buyers are increasingly looking for certifications that verify a supplier’s commitment to sustainable practices, such as ISO 14001 for environmental management or certifications related to recycled materials. These certifications not only enhance a company’s reputation but also align with the growing consumer demand for transparency and accountability.
In addition, the use of biodegradable or recyclable materials in flask manufacturing is gaining traction. Buyers should consider partnerships with manufacturers who are pioneering the use of such materials, as this can lead to a competitive advantage in the marketplace. By integrating sustainability into their sourcing strategies, B2B buyers can not only reduce their environmental footprint but also meet the expectations of an increasingly eco-conscious consumer base.
What Is the Historical Evolution of the Flask Manufacturing Sector?
The flask manufacturing sector has evolved significantly over the past few decades. Initially dominated by glass and metal materials, the industry has diversified with the introduction of various plastics and composite materials. This evolution has been driven by technological advancements and changing consumer preferences for lightweight, durable, and insulated products.
In the early 2000s, the introduction of vacuum insulation technology revolutionized the way flasks retain temperature, making them popular among outdoor enthusiasts and professionals alike. As global awareness of environmental issues has grown, manufacturers have increasingly focused on sustainable practices, transitioning towards materials that minimize ecological impact.
This historical context is essential for B2B buyers as it highlights the importance of innovation and adaptability in selecting suppliers. Understanding the evolution of materials and technologies can inform purchasing decisions, ensuring that buyers align with manufacturers who are committed to quality, sustainability, and meeting the demands of modern consumers.
Frequently Asked Questions (FAQs) for B2B Buyers of flask manufacturer
-
How can I determine the quality of a flask manufacturer?
To assess the quality of a flask manufacturer, start by reviewing their certifications and compliance with international standards such as ISO. Request samples to evaluate the craftsmanship, material quality, and durability. Additionally, check for customer reviews and testimonials to gauge reliability. Engaging in direct communication with the manufacturer can also provide insights into their production processes and quality assurance measures. -
What customization options are available when sourcing flasks?
Many flask manufacturers offer a range of customization options, including size, material, color, and branding features such as logos or unique designs. It’s essential to discuss your specific requirements early in the sourcing process. Ask the manufacturer about their capabilities for custom molds or finishes to ensure they can meet your expectations and timelines. -
What is the minimum order quantity (MOQ) for flask manufacturing?
The MOQ can vary significantly among manufacturers based on their production capabilities and product type. Typically, MOQs range from 100 to 1,000 units. For smaller businesses or startups, some manufacturers may offer lower MOQs but at a higher per-unit cost. Always clarify the MOQ before placing an order to avoid unexpected costs. -
What payment terms should I expect when sourcing flasks internationally?
Payment terms can vary widely depending on the manufacturer and your negotiation. Common terms include a deposit (usually 30-50%) upfront, with the balance due upon shipment or delivery. Some manufacturers may also offer letters of credit or other financing options. Ensure you have a clear agreement in writing to avoid any disputes later. -
How do I conduct due diligence on a flask manufacturer?
Conducting due diligence involves researching the manufacturer’s history, production capacity, and reputation. Look for reviews on platforms like Alibaba or Trustpilot, and request references from previous clients. Additionally, consider visiting the manufacturing facility if possible, or use third-party inspection services to verify their operations and quality control processes. -
What logistics considerations should I keep in mind when importing flasks?
When importing flasks, consider factors such as shipping costs, customs duties, and delivery timelines. Work with a freight forwarder to navigate international shipping regulations and ensure timely delivery. It’s also crucial to understand the Incoterms (International Commercial Terms) that define the responsibilities of buyers and sellers in the shipping process.
-
How can I ensure quality assurance during flask production?
To ensure quality assurance, establish a clear set of quality standards before production begins. Regularly communicate with the manufacturer throughout the production process, and consider conducting in-line inspections. Request a final inspection before shipment to catch any defects or issues, ensuring the product meets your specifications. -
What are the common materials used in flask manufacturing?
Flasks are typically made from stainless steel, glass, or plastic, each offering different benefits. Stainless steel is favored for its durability and insulation properties, making it ideal for hot or cold beverages. Glass provides a clean taste but can be fragile, while plastic is lightweight and versatile but may not be suitable for all liquids. Choose the material based on your specific use case and market demands.
Important Disclaimer & Terms of Use
⚠️ Important Disclaimer
The information provided in this guide, including content regarding manufacturers, technical specifications, and market analysis, is for informational and educational purposes only. It does not constitute professional procurement advice, financial advice, or legal advice.
While we have made every effort to ensure the accuracy and timeliness of the information, we are not responsible for any errors, omissions, or outdated information. Market conditions, company details, and technical standards are subject to change.
B2B buyers must conduct their own independent and thorough due diligence before making any purchasing decisions. This includes contacting suppliers directly, verifying certifications, requesting samples, and seeking professional consultation. The risk of relying on any information in this guide is borne solely by the reader.
Strategic Sourcing Conclusion and Outlook for flask manufacturer
In the dynamic landscape of global sourcing for flask manufacturers, strategic sourcing emerges as a critical component for success. By prioritizing quality, reliability, and cost-effectiveness, international B2B buyers—especially from Africa, South America, the Middle East, and Europe—can secure partnerships that enhance their operational efficiencies and competitive edge.
How Can Strategic Sourcing Enhance Your Supply Chain?
Investing in strategic sourcing enables buyers to build a diversified supplier base, ensuring access to innovative products and mitigating risks associated with supply disruptions. This approach not only fosters stronger relationships with manufacturers but also aligns procurement strategies with broader business goals, facilitating long-term growth.
What Does the Future Hold for Flask Manufacturers?
As market demands evolve, the future of flask manufacturing is poised for transformation. Trends such as sustainability and customization will shape production processes, compelling manufacturers to adapt swiftly. B2B buyers are encouraged to stay ahead of these trends by leveraging data-driven insights and fostering collaborative partnerships.
In conclusion, embracing strategic sourcing is not just a procurement tactic; it is a pathway to building resilient supply chains. International buyers are urged to take proactive steps now, exploring diverse sourcing options and engaging with manufacturers who prioritize innovation and sustainability. By doing so, they position themselves for success in an increasingly competitive marketplace.