Discover Top Benefits of Sourcing a Converter Manufacturer (2025)
Introduction: Navigating the Global Market for converter manufacturer
In today’s rapidly evolving global market, sourcing high-quality converter manufacturers poses significant challenges for international B2B buyers. Whether you’re based in Africa, South America, the Middle East, or Europe, understanding the nuances of converter technology is crucial for making informed purchasing decisions. This comprehensive guide offers insights into various types of converters, their applications across industries, and essential factors to consider when vetting suppliers.
From power converters to signal converters, each type serves a unique purpose and comes with its own set of specifications and standards. Navigating these complexities requires not only a grasp of technical details but also an understanding of market dynamics, pricing strategies, and supplier reliability. This guide empowers B2B buyers by equipping them with the knowledge necessary to evaluate potential suppliers effectively, ensuring you choose the right converter solutions that align with your business needs.
Additionally, we delve into cost considerations and potential pitfalls to avoid, enhancing your ability to negotiate favorable terms. By leveraging the actionable insights provided, you can mitigate risks and make strategic choices that drive efficiency and profitability in your operations. Ultimately, this guide serves as a valuable resource for international buyers looking to thrive in the competitive landscape of converter manufacturing.
Understanding converter manufacturer Types and Variations
Type Name | Key Distinguishing Features | Primary B2B Applications | Brief Pros & Cons for Buyers |
---|---|---|---|
AC-DC Converter Manufacturers | Convert alternating current (AC) to direct current (DC); widely used in electronics. | Power supplies for electronic devices, battery chargers. | Pros: Essential for powering DC devices; reliable. Cons: Limited to specific applications; may require additional components for full systems. |
DC-DC Converter Manufacturers | Transform one DC voltage level to another; high efficiency in power conversion. | Renewable energy systems, electric vehicles, portable electronics. | Pros: Versatile for various voltage needs; compact design. Cons: Complexity in design; can be costly depending on specifications. |
DC-AC Inverter Manufacturers | Convert DC back to AC; crucial for renewable energy systems and UPS. | Solar energy systems, uninterruptible power supplies (UPS). | Pros: Enables use of solar energy in homes; essential for backup power. Cons: Efficiency can vary; may require maintenance. |
Bidirectional Converter Manufacturers | Allow energy flow in both directions; suitable for energy storage systems. | Electric vehicles, grid-tied battery systems. | Pros: Enhances energy flexibility; supports renewable integration. Cons: Higher initial costs; complex technology. |
Custom Converter Manufacturers | Tailor-made solutions for specific industry needs; can integrate various technologies. | Specialized industrial applications, aerospace, and defense. | Pros: Perfect fit for unique requirements; optimized performance. Cons: Longer lead times; potentially higher costs. |
What Are AC-DC Converter Manufacturers and Their B2B Relevance?
AC-DC converter manufacturers specialize in devices that convert alternating current (AC) into direct current (DC). These converters are essential for powering devices that require a stable DC supply, such as computers and battery chargers. When considering an AC-DC converter, B2B buyers should evaluate the converter’s efficiency, output voltage stability, and compatibility with existing systems to ensure seamless integration into their operations.
How Do DC-DC Converter Manufacturers Operate in Various Industries?
DC-DC converter manufacturers produce devices that change one DC voltage level to another. They are particularly valuable in sectors like renewable energy, where they optimize battery charging and discharging processes. Buyers should assess factors such as efficiency ratings, size, and output specifications when selecting a DC-DC converter, as these elements can significantly impact the performance of their applications.
What Role Do DC-AC Inverter Manufacturers Play in Power Systems?
DC-AC inverter manufacturers create devices that convert DC power back to AC, which is vital for solar energy systems and uninterruptible power supplies (UPS). These inverters allow renewable energy to be utilized effectively in residential and commercial settings. B2B buyers need to consider the inverter’s efficiency, capacity, and reliability, especially in critical applications where power continuity is crucial.
Why Are Bidirectional Converter Manufacturers Important for Energy Storage?
Bidirectional converter manufacturers focus on devices that facilitate energy flow in both directions, making them ideal for applications like electric vehicles and grid-tied battery systems. These converters enhance flexibility in energy management. When selecting a bidirectional converter, B2B buyers should consider factors such as power ratings, control systems, and integration capabilities with existing infrastructure.
How Do Custom Converter Manufacturers Address Unique Industry Needs?
Custom converter manufacturers offer tailored solutions to meet specific industry requirements, such as those found in aerospace or specialized industrial applications. These bespoke devices can integrate various technologies to optimize performance. B2B buyers should weigh the benefits of customization against potential longer lead times and higher costs, ensuring that the solution aligns with their operational goals and budget constraints.
Related Video: EXEDY Tech – Torque Converter Function Explained
Key Industrial Applications of converter manufacturer
Industry/Sector | Specific Application of converter manufacturer | Value/Benefit for the Business | Key Sourcing Considerations for this Application |
---|---|---|---|
Renewable Energy | Inverters for solar power systems | Maximizes energy conversion efficiency and reliability | Compliance with local regulations and certifications |
Transportation | Electric vehicle (EV) charging stations | Supports sustainable transport and reduces carbon footprint | Compatibility with various EV models and standards |
Industrial Automation | Power converters for machinery | Enhances operational efficiency and reduces downtime | Customization options for specific machinery needs |
Telecommunications | DC-DC converters for communication systems | Ensures stable power supply for critical infrastructure | Reliability in extreme environments and conditions |
Mining and Metals | Converters for heavy machinery | Improves energy efficiency and reduces operational costs | Rugged design to withstand harsh conditions |
How Are Converters Used in Renewable Energy Applications?
In the renewable energy sector, particularly in solar power, converter manufacturers produce inverters that convert direct current (DC) generated by solar panels into alternating current (AC) for use in homes and businesses. This conversion is critical for maximizing energy efficiency and ensuring reliable energy supply. International buyers should consider compliance with local energy regulations and certifications to ensure the inverters meet safety and efficiency standards.
What Role Do Converters Play in Transportation?
Converters are essential in the transportation industry, especially for electric vehicle (EV) charging stations. They facilitate the conversion of AC from the grid to DC required by EV batteries. By investing in high-quality converters, businesses can support sustainable transport initiatives and reduce their carbon footprint. When sourcing, buyers must ensure compatibility with various EV models and adhere to international charging standards.
How Do Converters Enhance Industrial Automation?
In industrial automation, power converters are utilized to manage the voltage and current supplied to machinery. This ensures optimal performance and enhances operational efficiency while minimizing downtime. For international buyers, it is crucial to consider customization options that cater to specific machinery requirements, as well as the overall energy efficiency of the converters to lower operational costs.
Why Are Converters Important in Telecommunications?
DC-DC converters are vital in telecommunications, providing stable power supply to communication systems, which is crucial for maintaining connectivity. These converters must operate reliably under extreme conditions, making sourcing from reputable manufacturers essential. Buyers should evaluate the reliability and performance of converters to ensure they can withstand the demanding environments of telecommunications infrastructure.
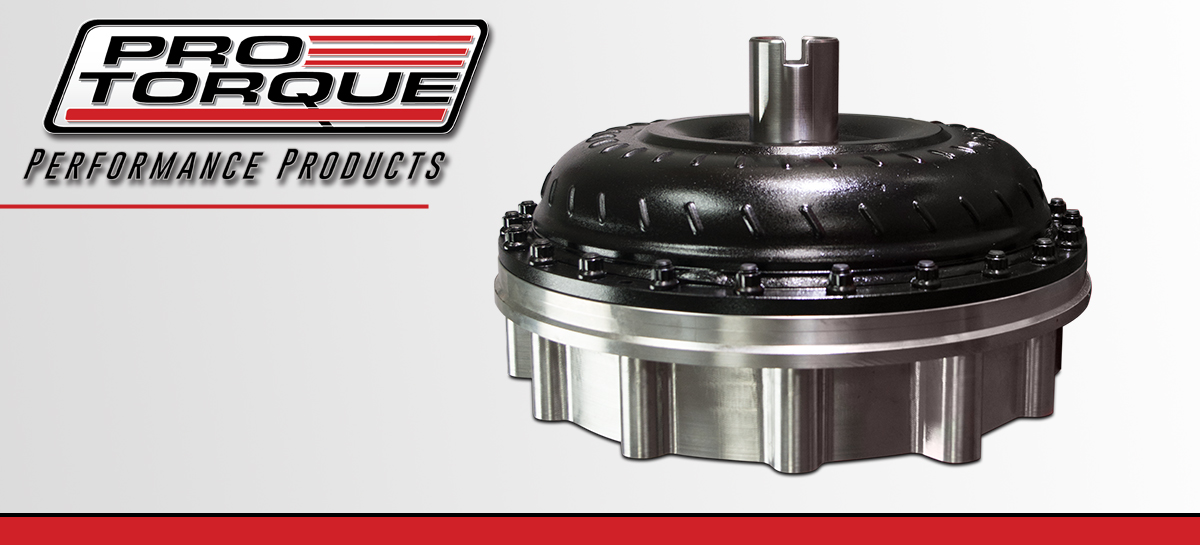
A stock image related to converter manufacturer.
How Do Converters Benefit the Mining and Metals Sector?
In the mining and metals industry, converters are used in heavy machinery to optimize energy consumption and improve efficiency. By implementing energy-efficient converters, mining operations can significantly reduce operational costs and enhance productivity. Buyers in this sector should prioritize sourcing rugged designs that can endure harsh mining conditions, ensuring longevity and reliability in their equipment.
3 Common User Pain Points for ‘converter manufacturer’ & Their Solutions
Scenario 1: Navigating Compatibility Issues with Legacy Systems
The Problem: Many B2B buyers in industries such as manufacturing and energy face the challenge of integrating new converters with existing legacy systems. These systems often use outdated technology that may not support modern converter specifications, leading to costly downtimes and disruptions. For instance, a buyer in South Africa might discover that the converters they purchased are incompatible with their machinery, resulting in project delays and financial losses.
The Solution: To mitigate compatibility issues, buyers should conduct thorough compatibility assessments before purchasing converters. This involves collaborating closely with the converter manufacturer to understand the specifications and capabilities of both the new converters and existing equipment. It’s essential to request detailed technical documentation and to engage in testing phases where possible. Buyers can also seek converters that offer modular designs or backward compatibility features, which can facilitate smoother integration. Additionally, investing in training for staff on how to implement new technology can ensure a more seamless transition.
Scenario 2: Understanding Performance Specifications and Standards
The Problem: International buyers often struggle to understand the various performance specifications and standards applicable to converters in their region. For instance, a buyer from Europe may find it challenging to navigate the differences between IEC standards and local regulations, which can lead to compliance issues and potential penalties. This lack of clarity can also result in selecting converters that do not meet operational needs, ultimately affecting productivity.
The Solution: Buyers should prioritize working with converter manufacturers who are transparent about their adherence to international and local standards. Engaging with manufacturers that provide educational resources, such as webinars or detailed guides on performance specifications, can empower buyers to make informed decisions. Additionally, buyers should consider forming partnerships with local industry associations or regulatory bodies that can offer guidance on compliance requirements. This proactive approach not only ensures adherence to standards but also enhances operational efficiency.
Scenario 3: Managing Supply Chain Disruptions
The Problem: Supply chain disruptions have become increasingly common, impacting the availability of converters and leading to extended lead times. For buyers in regions such as South America or the Middle East, the challenge is exacerbated by geopolitical factors and logistical hurdles. This can result in delayed projects, increased costs, and potential loss of competitive advantage.
The Solution: To effectively manage supply chain risks, buyers should diversify their supplier base to reduce dependency on a single manufacturer or region. Establishing relationships with multiple converter manufacturers across different geographical areas can provide flexibility and assurance of supply during disruptions. Buyers should also implement just-in-time inventory strategies and maintain close communication with suppliers regarding lead times and potential delays. Additionally, investing in supply chain management software can help buyers forecast demand more accurately and streamline procurement processes, ensuring that they remain agile in a volatile market.
Strategic Material Selection Guide for converter manufacturer
When selecting materials for converters, manufacturers must consider various properties and how they align with the specific requirements of their applications. Here’s an analysis of four common materials used in converter manufacturing, focusing on their key properties, advantages, disadvantages, and implications for international B2B buyers.
What Are the Key Properties of Stainless Steel in Converter Manufacturing?
Stainless steel is renowned for its excellent corrosion resistance and high-temperature tolerance, making it a popular choice for converters. Its ability to withstand a wide range of temperatures and pressures is vital for applications in industries such as oil and gas, chemical processing, and food production. Stainless steel typically has a temperature rating of up to 1,500°F (815°C) and can handle pressures exceeding 10,000 psi, depending on the grade.
Pros: The primary advantages of stainless steel include its durability, strength, and resistance to oxidation and corrosion. It is also relatively easy to fabricate and weld, which simplifies manufacturing processes.
Cons: However, stainless steel can be more expensive than other materials, and its manufacturing complexity may increase costs. Additionally, certain grades may not be suitable for specific media, such as highly acidic or alkaline substances.
Impact on Application: In converters, stainless steel is often used for components that require high strength and corrosion resistance, particularly when handling aggressive media.
How Does Aluminum Compare as a Material for Converters?
Aluminum is another commonly used material in converter manufacturing, particularly in applications where weight reduction is essential. Aluminum’s lightweight nature, combined with good corrosion resistance, makes it ideal for automotive and aerospace applications.
Pros: The key advantages of aluminum include its low weight, which can lead to energy savings in transport and installation, and its excellent thermal conductivity. It is also more cost-effective than stainless steel.
Cons: On the downside, aluminum has a lower temperature tolerance (typically around 1,200°F or 650°C) and pressure rating compared to stainless steel. It can also be less durable, particularly in harsh environments.
Impact on Application: Aluminum is suitable for converters that operate under moderate conditions and where weight is a critical factor. However, it may not be ideal for high-pressure or high-temperature applications.
What Are the Benefits and Limitations of Carbon Steel?
Carbon steel is widely used in converter manufacturing due to its strength and affordability. It is particularly effective in applications requiring high tensile strength and durability.
Pros: Carbon steel offers excellent mechanical properties and is relatively inexpensive, making it a cost-effective choice for many applications. It can withstand high pressures and is easy to machine.
Cons: However, carbon steel is prone to corrosion, which can limit its use in certain environments without protective coatings. Its performance can also degrade at elevated temperatures.
Impact on Application: Carbon steel is commonly used in converters for applications such as water and steam services, where the media is not corrosive. Buyers should consider the need for protective coatings to enhance longevity.
Why Is Plastic a Viable Option for Some Converter Applications?
Plastics, particularly high-performance polymers, are increasingly being used in converter manufacturing, especially for applications involving corrosive substances or where weight is a concern.
Pros: The main advantages of plastic materials include their excellent chemical resistance, lightweight nature, and lower cost compared to metals. They can also be molded into complex shapes, which can simplify manufacturing.
Cons: The limitations of plastics include lower temperature and pressure ratings compared to metals. They may not be suitable for high-stress applications or environments with extreme temperatures.
Impact on Application: Plastics are ideal for converters in chemical processing where corrosive media is handled, but manufacturers must ensure compatibility with the specific chemicals involved.
Summary Table of Material Selection for Converter Manufacturing
Material | Typical Use Case for Converter Manufacturer | Key Advantage | Key Disadvantage/Limitation | Relative Cost (Low/Med/High) |
---|---|---|---|---|
Stainless Steel | High-pressure chemical converters | Excellent corrosion resistance | Higher cost and complexity | High |
Aluminum | Automotive and aerospace converters | Lightweight and cost-effective | Lower temperature tolerance | Medium |
Carbon Steel | Water and steam service converters | High strength and low cost | Prone to corrosion | Low |
Plastic | Chemical processing converters | Excellent chemical resistance | Lower temperature and pressure limits | Medium |
This guide provides a comprehensive overview of material options for converter manufacturers, helping international B2B buyers make informed decisions based on performance needs, cost considerations, and application suitability.
In-depth Look: Manufacturing Processes and Quality Assurance for converter manufacturer
What Are the Key Stages in the Manufacturing Process of Converters?
Manufacturing converters involves several critical stages that ensure the final product meets the necessary specifications and quality standards. The primary stages include:
-
Material Preparation: This initial stage involves selecting high-quality raw materials, such as metals and plastics, that meet the specifications for electrical conductivity, thermal resistance, and durability. Suppliers should be able to provide material certifications, which B2B buyers can verify to ensure compliance with international standards.
-
Forming: After material preparation, the forming stage shapes the raw materials into the desired components. Techniques such as stamping, extrusion, and casting are commonly used. Advanced methods like CNC machining can also be employed for precision components. Buyers should inquire about the machinery and technologies used, as well as the experience of the workforce involved in this stage.
-
Assembly: In the assembly phase, the formed components are brought together. This may involve soldering, welding, or using adhesives, depending on the converter type. Automated assembly lines are increasingly common, improving efficiency and consistency. Buyers should assess the manufacturer’s assembly capabilities and the skill level of their technicians.
-
Finishing: The final stage encompasses surface treatments, such as coating, plating, or anodizing, which enhance the product’s performance and longevity. This stage is vital for converters that will be exposed to harsh environments. B2B buyers should request information on the finishing processes and materials used to ensure they meet specific environmental and operational requirements.
How Is Quality Assurance Integrated into the Manufacturing Process?
Quality assurance (QA) is essential in the converter manufacturing process to ensure that products meet industry standards and customer expectations. Here are some key aspects of QA:
-
International Standards Compliance: Many converter manufacturers adhere to ISO 9001, a widely recognized standard for quality management systems. This certification indicates that the manufacturer has established processes for quality control and continuous improvement. B2B buyers should seek suppliers with these certifications, as they demonstrate a commitment to quality.
-
Industry-Specific Certifications: Depending on the application, converters may also require certifications such as CE marking for European markets or API standards for the oil and gas industry. Buyers should verify that manufacturers possess the necessary certifications for their specific sector.
-
Quality Control Checkpoints: Effective quality control involves several checkpoints throughout the manufacturing process:
– Incoming Quality Control (IQC): This stage involves inspecting raw materials upon receipt to ensure they meet specifications.
– In-Process Quality Control (IPQC): During production, various tests and inspections are conducted to monitor product quality at different stages.
– Final Quality Control (FQC): Before shipping, finished products undergo rigorous testing to ensure they meet all specifications and standards. -
Common Testing Methods: Various testing methods are employed to verify product quality, including:
– Electrical Testing: Ensures that converters function correctly under operational conditions.
– Mechanical Testing: Assesses the physical properties and durability of the materials used.
– Environmental Testing: Simulates real-world conditions to ensure reliability over time.
How Can B2B Buyers Verify a Supplier’s Quality Control Practices?
B2B buyers must perform due diligence to ensure that their suppliers uphold stringent quality control practices. Here are some actionable steps:
-
Supplier Audits: Conducting audits of potential suppliers can provide insights into their manufacturing processes and quality assurance systems. Buyers should look for comprehensive audits that evaluate compliance with international standards and internal QA protocols.
-
Requesting Quality Reports: Suppliers should be willing to share quality control reports that detail their inspection and testing results. These reports should outline failure rates, corrective actions taken, and overall performance metrics.
-
Third-Party Inspections: Engaging third-party inspection services can offer an unbiased assessment of a supplier’s manufacturing capabilities and quality assurance practices. This step is particularly valuable for buyers in regions with less transparency in manufacturing processes.
-
References and Reviews: Buyers should seek references from other businesses that have worked with the supplier. Reviews can provide insights into the supplier’s reliability, product quality, and customer service.
What Are the Quality Control Nuances for International B2B Buyers?
International B2B buyers, particularly those from Africa, South America, the Middle East, and Europe, should be aware of specific nuances in quality control:
-
Cultural and Regional Differences: Quality expectations may vary by region, so it’s essential to understand the specific standards and practices prevalent in your target market. For instance, European standards may be more stringent compared to those in other regions.
-
Import Regulations: Each region has its regulations regarding imported goods. B2B buyers must ensure that converters meet local compliance requirements, including safety and environmental regulations.
-
Language Barriers: Communication can be a challenge when dealing with international suppliers. It is advisable to have clear documentation and contracts in the buyer’s preferred language, ensuring that all quality expectations are understood.
-
Logistics and Supply Chain Management: International shipping can introduce challenges in maintaining quality. Buyers should work with suppliers who have robust logistics processes to ensure that products are not damaged during transport.
By understanding these manufacturing processes and quality assurance practices, B2B buyers can make informed decisions when selecting converter manufacturers, ensuring that they receive high-quality products that meet their operational needs.
Practical Sourcing Guide: A Step-by-Step Checklist for ‘converter manufacturer’
Introduction
When sourcing converters for your business, it’s essential to follow a structured approach to ensure that you partner with the right manufacturer. This checklist is designed to guide international B2B buyers, particularly from Africa, South America, the Middle East, and Europe, through the critical steps of the procurement process. By adhering to these steps, you can mitigate risks, enhance quality, and optimize your supply chain.
Step 1: Define Your Technical Specifications
Before reaching out to potential suppliers, clearly outline your technical requirements. This includes voltage levels, output types, efficiency ratings, and any specific certifications needed for your industry.
- Why it matters: Clear specifications help prevent misunderstandings and ensure that the products meet your operational needs.
- What to look for: Ensure that your specifications are aligned with industry standards relevant to your region.
Step 2: Conduct Market Research on Suppliers
Research potential converter manufacturers to understand their market presence, reputation, and areas of expertise. Utilize online platforms, industry publications, and trade shows to gather information.
- Why it matters: A well-researched supplier list can save you time and resources in the long run.
- What to look for: Focus on suppliers with a proven track record in your specific industry or application.
Step 3: Evaluate Potential Suppliers
Before committing, it’s crucial to vet suppliers thoroughly. Request company profiles, case studies, and references from buyers in a similar industry or region.
- Why it matters: Evaluating suppliers helps you identify those who can deliver quality and reliability.
- What to look for: Check for client testimonials, industry recognition, and any red flags in their business history.
Step 4: Verify Supplier Certifications
Ensure that potential manufacturers hold the necessary certifications relevant to your industry, such as ISO, CE, or UL certifications.
- Why it matters: Certifications indicate that the manufacturer adheres to specific quality and safety standards, which is crucial for compliance.
- What to look for: Verify the authenticity of these certifications through official channels or regulatory bodies.
Step 5: Request Samples for Testing
Before finalizing your order, request samples of the converters you are considering. This allows you to evaluate their performance and compatibility with your systems.
- Why it matters: Testing samples helps you assess quality and functionality firsthand.
- What to look for: Pay attention to the converters’ efficiency, durability, and any specific features that may impact your application.
Step 6: Negotiate Terms and Pricing
Once you have identified a preferred supplier, engage in negotiations to discuss pricing, payment terms, delivery schedules, and after-sales support.
- Why it matters: Effective negotiation can lead to better pricing and terms that align with your budget and operational timelines.
- What to look for: Ensure that all terms are documented clearly to avoid disputes later.
Step 7: Establish a Communication Plan
Set up a communication plan with your chosen supplier to ensure that both parties are aligned throughout the procurement process.
- Why it matters: Regular communication fosters transparency and helps address any issues promptly.
- What to look for: Define points of contact, preferred communication channels, and frequency of updates.
By following this checklist, international B2B buyers can streamline their sourcing process and secure reliable partnerships with converter manufacturers, ultimately enhancing their operational efficiencies and product quality.
Comprehensive Cost and Pricing Analysis for converter manufacturer Sourcing
What Are the Key Cost Components in Converter Manufacturing?
When sourcing converters, understanding the cost structure is essential for international B2B buyers. The primary cost components include:
-
Materials: The cost of raw materials, such as metals, plastics, and electronic components, can vary significantly based on market fluctuations and supplier location. Buyers should consider sourcing materials locally to reduce costs and lead times.
-
Labor: Labor costs can differ based on geographic location, skill level, and labor laws. In regions like Africa and South America, labor may be more cost-effective, while Europe may present higher labor costs due to stringent labor regulations.
-
Manufacturing Overhead: This includes utilities, facility maintenance, and administrative costs. Understanding the overhead can help buyers gauge the overall cost efficiency of a supplier.
-
Tooling: Initial tooling costs can be significant, especially for custom designs. Buyers should inquire about these costs upfront, as they can influence the total pricing structure.
-
Quality Control (QC): Ensuring product quality through rigorous QC processes adds to the cost. Suppliers with higher QC standards may charge more but provide better reliability and compliance with international standards.
-
Logistics: Transportation costs, including shipping and customs fees, can vary widely depending on the supplier’s location and chosen shipping method. Incoterms will play a crucial role in determining who bears these costs.
-
Margin: The profit margin set by the manufacturer will significantly impact the final price. Buyers should be aware of typical industry margins to identify reasonable pricing.
How Do Price Influencers Affect Converter Manufacturing Costs?
Several factors influence the pricing of converters, including:
-
Volume and Minimum Order Quantity (MOQ): Suppliers often offer discounts for larger orders. Understanding the MOQ can help buyers negotiate better terms.
-
Specifications and Customization: Custom designs and specifications can increase costs. Buyers should assess whether standard products meet their needs to avoid unnecessary expenses.
-
Materials and Quality Certifications: The choice of materials and the presence of quality certifications (e.g., ISO) can significantly impact price. Higher quality often comes at a premium but can reduce long-term costs associated with failures or defects.
-
Supplier Factors: Relationship with suppliers, their reputation, and their production capabilities can influence pricing. Established suppliers may charge more but often provide better reliability and service.
-
Incoterms: Understanding Incoterms (International Commercial Terms) is crucial for determining responsibility for shipping costs and risks. This can affect the overall pricing structure and should be clearly defined in contracts.
What Are the Best Negotiation Strategies for International B2B Buyers?
For buyers from regions such as Africa, South America, the Middle East, and Europe, here are actionable tips for effective negotiation and cost management:
-
Conduct Market Research: Understand market prices for converters in your region to ensure competitive offers from suppliers.
-
Leverage Total Cost of Ownership (TCO): Emphasize the importance of TCO in negotiations. This includes not just the purchase price but also maintenance, operational costs, and potential downtime costs.
-
Build Long-Term Relationships: Establishing a reliable partnership with suppliers can lead to better pricing, priority service, and flexibility in future orders.
-
Be Transparent About Your Needs: Clearly communicate your requirements and constraints, such as budget limits and timelines. This can help suppliers tailor their offers more effectively.
-
Consider Currency Risks: For international transactions, fluctuations in currency exchange rates can affect overall costs. Consider locking in prices or using contracts that mitigate these risks.
What Should International B2B Buyers Keep in Mind Regarding Pricing Nuances?
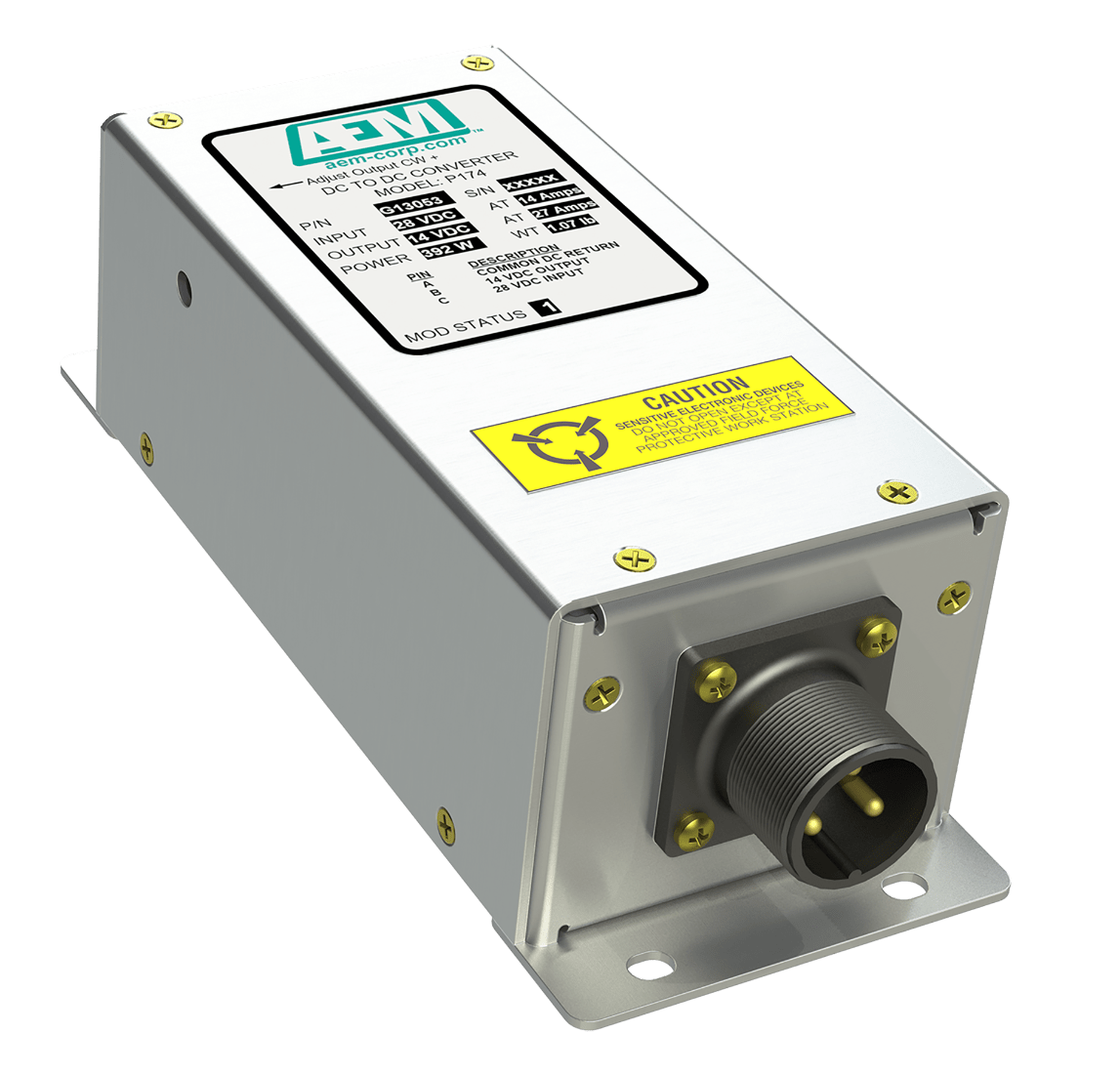
A stock image related to converter manufacturer.
Buyers should remain cautious about indicative prices. Pricing in converter manufacturing can vary widely based on the factors discussed above. Always seek detailed quotes and breakdowns from suppliers to understand the cost structure fully. Additionally, consider the potential for price adjustments based on changing market conditions or increased demand.
By understanding these elements, international B2B buyers can make informed decisions, ensuring they secure the best possible pricing for their converter sourcing needs while maintaining quality and reliability.
Alternatives Analysis: Comparing converter manufacturer With Other Solutions
Understanding the Importance of Evaluating Alternatives for Converter Solutions
When sourcing solutions for converting energy or signals, it is essential for international B2B buyers to evaluate various options available in the market. This evaluation not only helps in identifying the most suitable technology but also ensures that organizations can optimize performance while managing costs effectively. In this section, we will compare the traditional converter manufacturer with two viable alternatives: Digital Signal Processing (DSP) and Power Electronics Solutions.
Comparison Table of Converter Manufacturer and Alternatives
Comparison Aspect | Converter Manufacturer | Digital Signal Processing (DSP) | Power Electronics Solutions |
---|---|---|---|
Performance | High efficiency, reliable | Variable performance based on configuration | Excellent for high power applications |
Cost | Moderate to high initial investment | Lower initial cost, but may require extensive programming | High upfront cost but long-term savings |
Ease of Implementation | Requires specialized skills | Moderate, depending on application complexity | Complex, often needing integration with existing systems |
Maintenance | Regular maintenance needed | Low maintenance after initial setup | Moderate maintenance with periodic checks |
Best Use Case | General conversion tasks | Signal processing in telecommunications | Industrial power management |
In-Depth Analysis of Alternatives
What are the advantages and disadvantages of Digital Signal Processing (DSP)?
Digital Signal Processing (DSP) offers a flexible and cost-effective alternative to traditional converter manufacturers. One of its key advantages is the ability to adapt to various applications, particularly in telecommunications and audio processing. This adaptability can lead to lower initial costs compared to hardware-centric solutions. However, the performance of DSP is highly dependent on the configuration and the expertise of the personnel involved. While it can be efficient for specific tasks, it may not provide the same level of reliability and efficiency as a dedicated converter in all scenarios. Additionally, the need for ongoing programming and updates can increase operational complexity.
How do Power Electronics Solutions compare to converter manufacturers?
Power Electronics Solutions are designed for high-power applications and can efficiently handle large energy conversions, making them ideal for industrial settings. Their robustness and efficiency in managing power loads are significant advantages. However, the initial investment can be substantial, and their complexity often requires specialized knowledge for integration with existing systems. While they can provide long-term savings through energy efficiency, the upfront costs and maintenance requirements can be a barrier for smaller businesses or those with limited budgets.
Conclusion: How to Choose the Right Solution for Your Needs
Selecting the right solution for converting energy or signals is crucial for optimizing operational efficiency and cost management. B2B buyers should assess their specific needs, considering factors such as performance requirements, budget constraints, and the complexity of implementation and maintenance. While converter manufacturers may provide high reliability and efficiency, alternatives like DSP and Power Electronics Solutions offer distinct advantages that may be more suitable depending on the use case. Evaluating these options through a careful analysis of their strengths and weaknesses will empower businesses to make informed decisions that align with their operational goals and market demands.
Essential Technical Properties and Trade Terminology for converter manufacturer
What Are the Essential Technical Properties for Converter Manufacturing?
When engaging with converter manufacturers, understanding the technical properties of products is crucial for making informed purchasing decisions. Below are several key specifications that B2B buyers should consider:
-
Material Grade
The material grade of a converter plays a vital role in determining its durability, efficiency, and compatibility with specific applications. Common materials used include aluminum, stainless steel, and various alloys. Selecting the appropriate material can significantly affect the converter’s performance, especially in harsh environments. -
Tolerance
Tolerance refers to the allowable deviation from a specified dimension in the manufacturing process. In converter manufacturing, tight tolerances are essential to ensure optimal fit and function within the application. For B2B buyers, understanding tolerance specifications helps to minimize operational issues and potential rework costs. -
Power Rating
This specification indicates the maximum amount of power that a converter can handle without failure. It is critical for buyers to match the power rating of the converter with their application requirements to ensure safety and reliability. Overloading a converter can lead to overheating and damage, resulting in costly downtime. -
Efficiency Rating
Efficiency ratings indicate how effectively a converter transforms input power to output power, often expressed as a percentage. Higher efficiency means less energy loss, which is particularly important for companies aiming to reduce operational costs and environmental impact. Buyers should prioritize converters with high efficiency ratings for long-term savings. -
Thermal Management
The ability of a converter to dissipate heat is vital for maintaining performance and longevity. Specifications related to thermal management, such as maximum operating temperature and cooling methods, should be clearly understood. For B2B buyers, selecting converters with robust thermal management can enhance reliability and reduce the risk of failure.
What Common Trade Terms Should B2B Buyers Know in Converter Manufacturing?
Familiarity with industry terminology helps streamline communication and negotiation processes. Below are common trade terms relevant to converter manufacturing:
-
OEM (Original Equipment Manufacturer)
An OEM refers to a company that produces parts or equipment that may be marketed by another manufacturer. In the context of converters, knowing the OEM is crucial as it often influences product quality and reliability. Buyers should ensure that they are sourcing from reputable OEMs to guarantee product integrity. -
MOQ (Minimum Order Quantity)
MOQ specifies the smallest quantity of a product that a supplier is willing to sell. Understanding MOQ is essential for budget planning and inventory management. B2B buyers should negotiate MOQs that align with their operational needs to avoid excess inventory costs or supply shortages. -
RFQ (Request for Quotation)
An RFQ is a document sent to suppliers requesting a quote for specific products or services. This process helps buyers compare prices and terms from different manufacturers. Crafting a detailed RFQ can lead to better pricing and terms, ensuring that buyers receive the best value. -
Incoterms (International Commercial Terms)
Incoterms are a set of rules that define the responsibilities of buyers and sellers in international transactions. They clarify who is responsible for shipping, insurance, and tariffs. For B2B buyers, understanding Incoterms is vital for managing logistics and costs effectively. -
Lead Time
Lead time refers to the time taken from placing an order to the delivery of the product. Knowing the lead time helps buyers plan their operations and manage inventory effectively. It is advisable to discuss lead times during negotiations to ensure alignment with project timelines.
By understanding these essential technical properties and trade terminologies, B2B buyers can make more informed decisions when sourcing converters, ultimately leading to better product selection and successful partnerships.
Navigating Market Dynamics and Sourcing Trends in the converter manufacturer Sector
What Are the Current Market Dynamics and Key Trends in the Converter Manufacturer Sector?
The converter manufacturing sector is witnessing significant transformation driven by technological advancements and shifting consumer demands. Key global drivers include the increasing demand for energy-efficient solutions and the growing emphasis on automation across industries. For international B2B buyers, particularly in regions like Africa, South America, the Middle East, and Europe, understanding these dynamics is crucial for making informed sourcing decisions.
Emerging B2B technology trends include the integration of IoT (Internet of Things) and AI (Artificial Intelligence) within converter systems, enabling predictive maintenance and enhanced operational efficiency. This trend is particularly relevant for buyers in sectors such as renewable energy and automotive, where efficiency can lead to substantial cost savings and improved performance. Moreover, the rise of digital marketplaces and e-commerce platforms is simplifying procurement processes, allowing buyers from diverse regions to access a wider range of products and suppliers.
Market dynamics also reflect increasing competition among manufacturers, which is pushing for innovation and improved product quality. Buyers should consider suppliers that are not only price-competitive but also offer advanced solutions that can adapt to changing market needs. Collaborating with local distributors can also enhance supply chain resilience, particularly for buyers in emerging markets where logistics can be challenging.
How Important Is Sustainability and Ethical Sourcing in the Converter Manufacturing Sector?
Sustainability is becoming a central theme in the converter manufacturing sector, driven by both regulatory pressures and consumer preferences. For B2B buyers, understanding the environmental impact of their sourcing decisions is crucial. Manufacturers that prioritize sustainability often implement eco-friendly practices throughout their supply chains, from sourcing raw materials to production processes.
Ethical sourcing is equally important, as buyers are increasingly scrutinizing supply chains for compliance with labor standards and environmental regulations. Certifications such as ISO 14001 (Environmental Management) and ISO 45001 (Occupational Health and Safety) are indicators of a manufacturer’s commitment to sustainable practices. Buyers should seek suppliers who can demonstrate these certifications, as they not only mitigate risks but also enhance brand reputation.
Moreover, the use of ‘green’ materials, such as recyclable metals and non-toxic coatings, is gaining traction. These materials not only reduce environmental impact but also appeal to a growing market segment that values sustainability. B2B buyers should prioritize suppliers that offer transparent information about their sourcing practices and material compositions, as this can inform better purchasing decisions and align with corporate sustainability goals.
What Is the Brief Evolution of the Converter Manufacturing Sector?
The converter manufacturing sector has evolved significantly over the past few decades. Initially focused on basic power conversion applications, the industry has transformed in response to rapid technological advancements and increasing energy demands. The introduction of digital technologies and smart systems has revolutionized converter design and functionality, enabling more efficient and compact solutions.
Today, converter manufacturers are not only tasked with meeting traditional power conversion needs but also adapting to the complexities of renewable energy integration and electric vehicle charging infrastructure. This evolution has opened new opportunities for international B2B buyers, who can leverage innovative solutions to enhance operational efficiencies and reduce energy costs. Understanding this historical context is essential for buyers looking to navigate the increasingly competitive landscape of the converter manufacturing sector.
Frequently Asked Questions (FAQs) for B2B Buyers of converter manufacturer
-
How do I ensure quality when sourcing converters from international manufacturers?
To ensure quality when sourcing converters, start by conducting thorough research on potential manufacturers. Look for certifications such as ISO 9001, which indicates adherence to quality management systems. Request samples to evaluate product performance and reliability. Additionally, consider visiting the manufacturing facility if feasible, or utilize third-party inspection services to verify quality before shipment. Establish clear quality assurance agreements that outline specifications and testing procedures to protect your investment. -
What are the key factors to consider when choosing a converter manufacturer?
Key factors include the manufacturer’s experience in the industry, production capabilities, and technological expertise. Evaluate their reputation by reading customer reviews and case studies. Assess their ability to meet your specific needs, including customization options and minimum order quantities (MOQs). Also, consider their logistics capabilities, lead times, and after-sales support, as these can significantly impact your supply chain efficiency and overall satisfaction. -
What is the minimum order quantity (MOQ) for converters, and how does it vary by manufacturer?
The MOQ for converters can vary significantly based on the manufacturer, product type, and complexity of the customization. Some manufacturers may have an MOQ as low as 50 units for standard products, while custom designs might require higher minimums, ranging from 100 to 1,000 units. Always inquire about MOQs upfront, as negotiating smaller quantities may be possible, especially if you are testing the market or establishing a long-term partnership. -
How can I customize converters to fit my specific needs?
Customizing converters typically involves discussing your technical requirements with the manufacturer. Provide detailed specifications, including voltage, current ratings, and environmental conditions. Many manufacturers offer tailored solutions, such as different form factors, power outputs, or additional features. Collaborate closely during the design phase to ensure that the final product meets your expectations. Additionally, request prototypes to test functionality before full-scale production. -
What payment terms should I expect when working with international converter manufacturers?
Payment terms can vary widely among international manufacturers. Common practices include a deposit (usually 30% to 50%) upfront, with the balance paid before or upon delivery. Some manufacturers might offer favorable terms based on your order size or business relationship. It’s essential to clarify payment methods accepted (e.g., wire transfer, letter of credit) and ensure they are secure and reliable. Always document terms in a formal contract to avoid disputes. -
What logistics considerations should I be aware of when importing converters?
When importing converters, consider shipping methods (air vs. sea), costs, and delivery times. Understand the customs regulations of your country, including tariffs and taxes applicable to electrical equipment. Work with a reliable freight forwarder to navigate logistics challenges and ensure timely delivery. Additionally, factor in lead times for manufacturing and shipping to avoid disruptions in your supply chain. -
How do I verify the credibility of a converter manufacturer?
To verify a manufacturer’s credibility, start by checking their business registration and industry certifications. Request references from previous clients and conduct background checks. Utilize platforms like LinkedIn to see endorsements and recommendations. Attend industry trade shows to meet manufacturers in person and assess their operations. Engaging in small test orders can also help gauge reliability before committing to larger contracts. -
What quality assurance practices should converter manufacturers follow?
Quality assurance practices in converter manufacturing should include regular inspections throughout the production process, adherence to international standards (like IEC and UL), and comprehensive testing of final products. Manufacturers should implement a robust quality management system that includes documentation of procedures, staff training, and continuous improvement initiatives. Requesting access to these practices during the vetting process can provide confidence in the manufacturer’s commitment to delivering high-quality products.
Important Disclaimer & Terms of Use
⚠️ Important Disclaimer
The information provided in this guide, including content regarding manufacturers, technical specifications, and market analysis, is for informational and educational purposes only. It does not constitute professional procurement advice, financial advice, or legal advice.
While we have made every effort to ensure the accuracy and timeliness of the information, we are not responsible for any errors, omissions, or outdated information. Market conditions, company details, and technical standards are subject to change.
B2B buyers must conduct their own independent and thorough due diligence before making any purchasing decisions. This includes contacting suppliers directly, verifying certifications, requesting samples, and seeking professional consultation. The risk of relying on any information in this guide is borne solely by the reader.
Strategic Sourcing Conclusion and Outlook for converter manufacturer
In the ever-evolving landscape of converter manufacturing, strategic sourcing remains a cornerstone for achieving operational excellence and competitive advantage. By leveraging global supplier networks, particularly in regions such as Africa, South America, the Middle East, and Europe, businesses can enhance their procurement processes and optimize cost efficiencies. Understanding local market dynamics and regulatory environments is crucial for identifying reliable partners who can deliver quality products tailored to specific needs.
What Are the Key Benefits of Strategic Sourcing for International B2B Buyers?
International buyers benefit from a comprehensive sourcing strategy that encompasses risk management, quality assurance, and sustainable practices. Engaging with manufacturers who prioritize innovation and flexibility ensures that your supply chain remains resilient against market fluctuations and technological advancements.
As we look ahead, the demand for advanced converter solutions will only intensify, driven by emerging technologies and increasing sustainability mandates. Now is the time for B2B buyers to assess their sourcing strategies critically and engage with manufacturers who are poised to meet future challenges. Embrace this opportunity to strengthen your supply chain by prioritizing strategic sourcing partnerships that can propel your business forward in the competitive global market.