Find the Best Coaster Manufacturer: The Ultimate Guide (2025)
Introduction: Navigating the Global Market for coaster manufacturer
Navigating the global market for coaster manufacturing presents a unique set of challenges for international B2B buyers, particularly those from Africa, South America, the Middle East, and Europe. One of the key hurdles is sourcing reliable coaster manufacturers that align with specific operational needs, such as durability, design, and compliance with international standards. This guide aims to streamline your purchasing process by providing a comprehensive overview of various coaster types, their applications, and essential supplier vetting practices.
In this detailed guide, you will discover the critical factors influencing cost, the diversity of coaster types available in the market, and insights into emerging trends that can impact your sourcing decisions. By understanding the nuances of coaster manufacturing, buyers can make informed choices that enhance operational efficiency and reduce risks associated with procurement.
Whether you are in South Africa seeking local suppliers, or in the UAE looking to import high-quality coasters, this guide is tailored to empower your purchasing strategy. It equips you with the knowledge needed to identify the right manufacturers, negotiate effectively, and ensure that your investment yields the desired outcomes. With the right insights at your fingertips, navigating the complexities of the coaster manufacturing landscape will become a more manageable and rewarding endeavor.
Understanding coaster manufacturer Types and Variations
Type Name | Key Distinguishing Features | Primary B2B Applications | Brief Pros & Cons for Buyers |
---|---|---|---|
General Cargo Coasters | Designed for transporting bulk goods; large capacity | Freight shipping, import/export businesses | Pros: Versatile and cost-effective. Cons: May lack specialized features. |
Container Coasters | Equipped for containerized cargo; standard sizes | Global shipping, logistics companies | Pros: Efficient for intermodal transport. Cons: Requires specific handling equipment. |
Fishing Coasters | Built for fishing industries; includes onboard storage | Commercial fishing, seafood transportation | Pros: Tailored for fishing needs. Cons: Limited to specific sectors. |
Offshore Supply Vessels | Designed for offshore oil and gas operations | Energy sector, maritime logistics | Pros: Durable and suited for harsh conditions. Cons: Higher operational costs. |
Passenger Coasters | Designed for tourism and passenger transport | Cruise lines, tourist operations | Pros: Enhances customer experience. Cons: High initial investment. |
What Are the Key Features of General Cargo Coasters?
General cargo coasters are versatile vessels primarily designed for the transport of bulk goods. They typically have a large cargo capacity and can be used for various types of freight, making them ideal for businesses involved in import and export. When considering a general cargo coaster, B2B buyers should evaluate the vessel’s size, cargo hold configuration, and operational costs. These vessels are generally cost-effective but may lack specialized features that could be beneficial for specific cargo types.
How Do Container Coasters Enhance Shipping Efficiency?
Container coasters are specifically designed to carry standardized shipping containers, facilitating efficient intermodal transport. This type of coaster is essential for logistics companies and global shipping operations, allowing for seamless transfers between ships, trucks, and trains. Buyers should consider the vessel’s compatibility with existing logistics systems and the availability of handling equipment. While container coasters offer significant efficiency advantages, they may require specialized docks and handling capabilities, which can increase operational complexity.
What Are the Advantages of Fishing Coasters for the Seafood Industry?
Fishing coasters are tailored for the fishing industry, incorporating features such as onboard storage for catches and specialized equipment for handling seafood. These vessels are crucial for commercial fishing operations and seafood transportation. When purchasing a fishing coaster, buyers should assess the vessel’s storage capacity, fishing gear compatibility, and compliance with local regulations. While fishing coasters are highly specialized, their application is limited to the fishing sector, which can restrict versatility.
Why Are Offshore Supply Vessels Important for the Energy Sector?
Offshore supply vessels are designed to support oil and gas operations in marine environments. These vessels are built to withstand harsh conditions and typically feature robust cargo holds for equipment and supplies. They play a critical role in the energy sector, particularly for companies involved in offshore drilling and exploration. Buyers must evaluate the vessel’s durability, operational range, and ability to support specific offshore activities. However, the higher operational costs associated with these vessels can be a significant consideration for buyers.
How Do Passenger Coasters Contribute to Tourism?
Passenger coasters are designed to transport tourists and enhance the customer experience in maritime travel. They often feature amenities for comfort and entertainment, making them suitable for cruise lines and tourist operations. When considering a passenger coaster, B2B buyers should focus on passenger capacity, onboard facilities, and compliance with safety regulations. While passenger coasters can significantly improve service offerings, they typically involve a higher initial investment and ongoing maintenance costs.
Related Video: The 7 BEST Roller Coaster Manufacturers – Ranking the manufacturers Part 3
Key Industrial Applications of coaster manufacturer
Industry/Sector | Specific Application of coaster manufacturer | Value/Benefit for the Business | Key Sourcing Considerations for this Application |
---|---|---|---|
Shipping & Logistics | Construction of cargo coasters for short-distance transport | Enhanced operational efficiency and cost savings | Durability, load capacity, and compliance with maritime regulations |
Tourism & Leisure | Development of passenger ferries and excursion boats | Increased customer satisfaction and repeat business | Design adaptability, safety features, and aesthetic appeal |
Fishing Industry | Fishing coasters for sustainable seafood transportation | Improved freshness and reduced spoilage | Insulation properties, capacity, and ease of handling |
Renewable Energy | Coasters for transporting wind turbine components | Support for green energy initiatives and reduced carbon footprint | Weight distribution, customization options, and delivery timelines |
Construction & Infrastructure | Delivery of materials via coaster ships | Streamlined supply chain and reduced congestion | Compliance with local regulations, material specifications, and sourcing location |
How are Coaster Manufacturers Utilized in Shipping and Logistics?
In the shipping and logistics sector, coaster manufacturers provide vital solutions by constructing cargo coasters specifically designed for short-distance transport. These vessels enhance operational efficiency by enabling faster and more reliable deliveries, ultimately leading to significant cost savings. International buyers, particularly from regions like Africa and South America, should consider the durability and load capacity of the coasters, as well as compliance with local maritime regulations to ensure safe and effective operations.
What Role Do Coaster Manufacturers Play in Tourism and Leisure?
Coaster manufacturers are instrumental in the tourism and leisure industry by developing passenger ferries and excursion boats that cater to tourists. These vessels not only enhance customer satisfaction through comfortable and enjoyable experiences but also encourage repeat business. For international B2B buyers, especially from the Middle East and Europe, key considerations include design adaptability to fit various tourist attractions, safety features to ensure passenger security, and aesthetic appeal to attract visitors.
How are Coaster Manufacturers Beneficial to the Fishing Industry?
In the fishing industry, coaster manufacturers produce specialized fishing coasters designed for the sustainable transportation of seafood. These coasters play a crucial role in maintaining the freshness of fish and reducing spoilage during transit, thereby increasing profit margins for fishing companies. Buyers should focus on insulation properties and capacity, as well as the ease of handling these vessels, to maximize efficiency in their operations.
How Do Coaster Manufacturers Support Renewable Energy Initiatives?
Coaster manufacturers contribute significantly to the renewable energy sector by creating coasters that facilitate the transportation of wind turbine components. This application supports green energy initiatives by reducing the carbon footprint associated with transporting heavy equipment. International buyers must prioritize weight distribution and customization options when sourcing these coasters, ensuring that they meet the specific needs of their projects and adhere to delivery timelines.
What is the Importance of Coaster Manufacturers in Construction and Infrastructure?
In the construction and infrastructure sector, coaster manufacturers provide essential solutions for the delivery of materials via coaster ships. This application streamlines the supply chain and reduces congestion in busy ports, allowing for more efficient construction processes. Buyers should ensure compliance with local regulations, pay attention to material specifications, and consider sourcing locations to optimize their procurement strategy and enhance project timelines.
Related Video: Making a Roller Coaster in Desmos
3 Common User Pain Points for ‘coaster manufacturer’ & Their Solutions
Scenario 1: Navigating Supply Chain Disruptions in Coaster Manufacturing
The Problem: International B2B buyers, especially from regions like Africa and South America, often face significant supply chain disruptions when sourcing coasters. Factors such as political instability, fluctuating exchange rates, and shipping delays can lead to unexpected costs and project delays. This uncertainty can create a ripple effect, impacting inventory management and ultimately affecting customer satisfaction.
The Solution: To mitigate supply chain risks, buyers should establish strong relationships with multiple coaster manufacturers in different geographical locations. Diversifying suppliers can reduce dependency on a single source, providing alternatives in case of disruptions. Additionally, consider implementing a just-in-time inventory system that aligns with demand forecasts. Utilize technology to track shipments in real-time and maintain open communication channels with suppliers to stay informed about potential delays. Investing in a logistics partner with local expertise can also enhance the efficiency of your supply chain.
Scenario 2: Ensuring Quality Standards in Coaster Production
The Problem: Another common pain point for B2B buyers is ensuring that the coasters manufactured meet specific quality and safety standards. With varying regulations across regions, it can be challenging to ensure compliance without significant oversight. This issue can lead to costly recalls, reputational damage, and legal challenges.
The Solution: To address quality assurance, buyers should implement a robust supplier evaluation process. This process should include on-site audits, assessing the manufacturer’s facilities, and reviewing their quality control processes. Additionally, consider requesting certifications relevant to your market—such as ISO 9001 for quality management systems. Establishing a quality assurance agreement that outlines the expected standards and penalties for non-compliance can also safeguard your interests. Regularly engage with manufacturers through quality feedback sessions to cultivate a culture of continuous improvement.
Scenario 3: Managing Customization Requests for Coaster Designs
The Problem: International buyers often have unique requirements for coaster designs that reflect local cultures or brand identities. However, many coaster manufacturers may not be equipped to handle customized requests efficiently, leading to miscommunications and unsatisfactory products. This challenge can frustrate buyers who have specific timelines and budget constraints.
The Solution: To effectively manage customization requests, buyers should conduct thorough market research to identify coaster manufacturers that specialize in bespoke designs. Initiate a collaborative design process early, involving both your team and the manufacturer’s designers to ensure clear communication of requirements. Utilize design software that allows for visual mock-ups to facilitate discussions. Establish clear timelines and milestones for the design and production phases, and consider setting up a prototype stage before full-scale production. This approach not only reduces the risk of errors but also fosters a partnership mentality between buyer and manufacturer, leading to better overall results.
Strategic Material Selection Guide for coaster manufacturer
When selecting materials for coaster manufacturing, it is essential to consider various factors that influence product performance, durability, and cost. Below, we analyze four common materials used in the industry, highlighting their key properties, advantages, disadvantages, and specific considerations for international B2B buyers, particularly from Africa, South America, the Middle East, and Europe.
What are the Key Properties of Steel for Coaster Manufacturing?
Steel is a widely used material in coaster manufacturing due to its strength and durability. Key properties include high tensile strength, excellent fatigue resistance, and the ability to withstand high temperatures and pressures. Steel’s corrosion resistance can be enhanced through galvanization or coatings, making it suitable for various environments.
Pros: Steel is highly durable and can handle significant loads, making it ideal for structural components of coasters. It is also relatively cost-effective compared to other metals.
Cons: The primary drawback of steel is its susceptibility to corrosion if not properly treated, which may lead to increased maintenance costs. Additionally, the manufacturing process can be complex, requiring specialized equipment for cutting and welding.
Impact on Application: Steel is compatible with various media, including water and chemicals, provided it is appropriately treated for corrosion resistance.
Considerations for International Buyers: Compliance with international standards such as ASTM and DIN is crucial. Buyers should also consider local regulations regarding material sourcing and environmental impact.
How Does Aluminum Compare as a Material for Coaster Manufacturing?
Aluminum is another popular choice for coaster manufacturing, known for its lightweight and corrosion-resistant properties. It has a lower density than steel, which can reduce transportation costs and ease installation.
Pros: Aluminum’s lightweight nature makes it easier to handle and install, while its corrosion resistance minimizes maintenance needs. It also has good thermal conductivity.
Cons: Aluminum is generally more expensive than steel, and while it is strong, it may not support as heavy loads as steel. Its fatigue resistance is lower, which could affect long-term performance.
Impact on Application: Aluminum is suitable for environments where weight reduction is critical. However, its compatibility with certain chemicals should be evaluated based on the specific application.
Considerations for International Buyers: Buyers should ensure that the aluminum meets relevant standards such as JIS and ASTM. Additionally, understanding the local market for aluminum can help in negotiating better prices.
What are the Benefits and Limitations of Composite Materials in Coaster Manufacturing?
Composite materials, such as fiberglass-reinforced plastic (FRP), are increasingly used in coaster manufacturing due to their unique properties. Composites offer high strength-to-weight ratios and excellent resistance to environmental factors.
Pros: Composites are lightweight, corrosion-resistant, and can be molded into complex shapes, allowing for innovative designs. They also require minimal maintenance.
Cons: The primary limitation of composites is their higher initial cost compared to metals. Additionally, they may not have the same load-bearing capacity as steel or aluminum.
Impact on Application: Composites are ideal for applications where weight savings and corrosion resistance are critical, such as in coastal environments.
Considerations for International Buyers: Buyers should verify that composite materials comply with local and international standards. Additionally, the availability of skilled labor for installation may vary by region.
How Does Wood Fit into the Material Selection for Coaster Manufacturing?
Wood is a traditional material used in coaster manufacturing, particularly for aesthetic purposes and in specific types of coasters. Key properties include natural strength and flexibility, which can be advantageous in certain designs.
Pros: Wood is often more cost-effective than metals and can provide a unique aesthetic appeal. It is also relatively easy to work with and can be sourced sustainably.
Cons: Wood is susceptible to rot, pests, and environmental damage, which can lead to higher maintenance costs over time. Its strength is also variable, depending on the type of wood used.
Impact on Application: Wood is suitable for applications where aesthetics are prioritized, but its durability in harsh environments may be a concern.
Considerations for International Buyers: Buyers should ensure that the wood is sourced sustainably and meets local regulations. Understanding the market for treated versus untreated wood is also essential.
Summary Table of Material Selection for Coaster Manufacturing
Material | Typical Use Case for coaster manufacturer | Key Advantage | Key Disadvantage/Limitation | Relative Cost (Low/Med/High) |
---|---|---|---|---|
Steel | Structural components | High durability and load-bearing capacity | Susceptible to corrosion if untreated | Medium |
Aluminum | Lightweight structures | Lightweight and corrosion-resistant | Higher cost and lower load capacity | High |
Composite | Innovative designs | Lightweight and minimal maintenance | Higher initial cost and variable load capacity | High |
Wood | Aesthetic applications | Cost-effective and unique aesthetic appeal | Susceptible to rot and environmental damage | Low |
This strategic material selection guide provides international B2B buyers with crucial insights into the advantages and limitations of various materials in coaster manufacturing, helping them make informed purchasing decisions tailored to their specific regional needs and compliance requirements.
In-depth Look: Manufacturing Processes and Quality Assurance for coaster manufacturer
What Are the Main Stages of Manufacturing Processes for Coaster Manufacturers?
The manufacturing processes for coaster manufacturers involve several critical stages, each requiring precision and adherence to strict quality standards. Understanding these processes is essential for B2B buyers, particularly those in Africa, South America, the Middle East, and Europe, as it helps in selecting reliable suppliers.
1. Material Preparation: Selecting Quality Raw Materials
The first stage of manufacturing coasters begins with the selection of high-quality raw materials. Common materials include steel, aluminum, and composites, chosen for their durability and strength.
- Sourcing: B2B buyers should ensure that suppliers source materials from reputable vendors who can provide certifications of material properties.
- Pre-Treatment: Materials often undergo pre-treatment processes such as cleaning and coating to enhance performance and longevity. This step is crucial for preventing corrosion and ensuring the material’s integrity.
2. Forming: Advanced Techniques for Precision Shaping
The forming stage involves transforming raw materials into components through various techniques:
- Cutting and Bending: Techniques such as laser cutting and CNC machining are employed to achieve precise dimensions. Buyers should inquire about the technology used by manufacturers to ensure accuracy.
- Welding and Joining: Advanced welding techniques, including MIG and TIG welding, are used for assembling components. Understanding the welding methods can provide insights into the structural integrity of the final product.
3. Assembly: Integrating Components for Functionality
Once components are formed, they move to the assembly stage, where multiple parts are brought together:
- Sub-Assemblies: Components are often grouped into sub-assemblies before final assembly. This approach allows for easier quality checks and minimizes errors.
- Final Assembly: This stage includes integrating all sub-assemblies into the final product. It is essential that manufacturers follow systematic procedures to ensure all parts fit correctly and function as intended.
4. Finishing: Ensuring Aesthetic and Functional Quality
The finishing stage enhances both the appearance and durability of coasters:
- Surface Treatments: Processes such as powder coating or painting are applied to provide a protective layer and enhance aesthetics. Buyers should request information on the finishing techniques and materials used, as these can affect the product’s longevity.
- Inspection: Final inspections are conducted to ensure that the product meets design specifications and quality standards.
How Do Quality Assurance Processes Work in Coaster Manufacturing?
Quality assurance (QA) is a critical component in the manufacturing of coasters, ensuring that products meet both international and industry-specific standards.
International Standards: What Should Buyers Know?
Coaster manufacturers often comply with various international standards, including:
- ISO 9001: This standard focuses on quality management systems and is crucial for ensuring consistent product quality. B2B buyers should verify that their suppliers are ISO certified, as this indicates a commitment to quality.
- CE Marking: Essential for products sold within the European Economic Area, CE marking indicates compliance with health, safety, and environmental protection standards.
Industry-Specific Standards: What Are the Key Certifications?
In addition to general standards, coaster manufacturers may need to comply with industry-specific regulations such as:
- API Standards: For manufacturers supplying to the oil and gas sector, adherence to API standards ensures that products meet operational safety and performance requirements.
- Local Regulations: Understanding local regulations in regions like Africa or the Middle East can help buyers ensure that the products they purchase are compliant with regional laws.
What Are the Key Quality Control Checkpoints in Coaster Manufacturing?
Quality control (QC) checkpoints are vital in the manufacturing process, ensuring that defects are caught early. Here are the main QC checkpoints:
1. Incoming Quality Control (IQC)
IQC involves inspecting raw materials upon arrival. Manufacturers should have protocols in place to check the quality and specifications of materials before they enter the production line.
2. In-Process Quality Control (IPQC)
During production, IPQC involves continuous monitoring of the manufacturing process. Key aspects include:
- Process Monitoring: Regular checks on machinery and processes to ensure they operate within specified parameters.
- Random Sampling: Conducting random inspections of components during production to catch defects early.
3. Final Quality Control (FQC)
FQC occurs once production is completed and involves comprehensive testing of the final product. Common testing methods include:
- Functional Testing: Ensuring that the coaster operates correctly under load conditions.
- Durability Testing: Simulating operational stresses to evaluate long-term performance.
How Can B2B Buyers Verify Supplier Quality Control?
For international B2B buyers, verifying supplier quality control is essential to ensure they receive high-quality products.
1. Conducting Supplier Audits
Buyers should consider conducting audits of potential suppliers to assess their manufacturing processes and quality control measures. This can involve:
- On-Site Visits: Inspecting the manufacturing facility and observing processes in action.
- Documentation Review: Evaluating quality control documentation, including inspection reports and certificates.
2. Requesting Quality Reports
Suppliers should provide quality reports detailing inspection results, testing methods, and compliance with standards. Buyers should request these reports to understand the supplier’s commitment to quality.
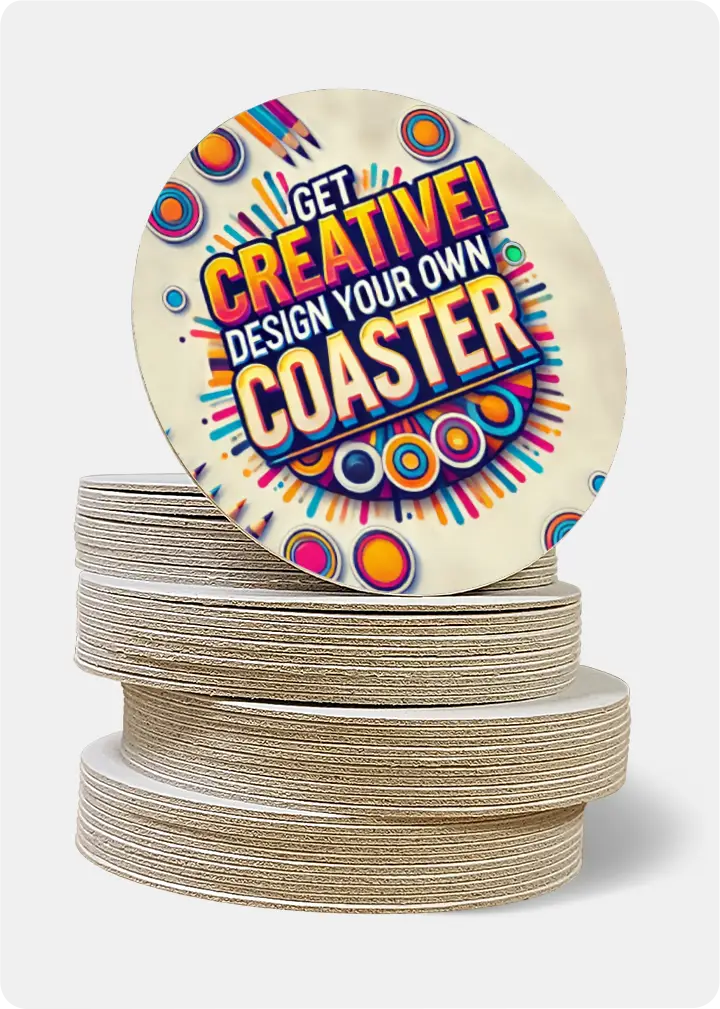
A stock image related to coaster manufacturer.
3. Engaging Third-Party Inspectors
Utilizing third-party inspection services can provide an unbiased assessment of the supplier’s quality control processes. These inspectors can conduct thorough evaluations and provide detailed reports that highlight any areas of concern.
What Nuances Should International B2B Buyers Consider for Quality Control?
When sourcing from manufacturers in different regions, B2B buyers should be aware of specific nuances:
- Cultural Differences: Understanding cultural attitudes towards quality and compliance can provide insights into supplier practices.
- Regulatory Variations: Different regions may have varying regulations that affect product quality. Buyers should familiarize themselves with local laws to ensure compliance.
- Communication Barriers: Effective communication is crucial in international transactions. Buyers should establish clear lines of communication with suppliers to address quality-related issues promptly.
By understanding the manufacturing processes and quality assurance measures, international B2B buyers can make informed decisions when selecting coaster manufacturers, ensuring they receive high-quality products that meet their specific needs.
Practical Sourcing Guide: A Step-by-Step Checklist for ‘coaster manufacturer’
When sourcing a coaster manufacturer, especially in diverse regions like Africa, South America, the Middle East, and Europe, it’s essential to follow a structured approach. This practical checklist will guide you through the necessary steps to ensure you find a reliable and high-quality supplier.
Step 1: Define Your Technical Specifications
Begin by clearly outlining your technical requirements for the coasters. This includes dimensions, materials, load capacity, and any specific design features.
– Why it matters: Precise specifications help avoid misunderstandings and ensure that the manufacturer can meet your production needs.
– What to look for: Check if the manufacturer has experience with similar products and can accommodate your specifications.
Step 2: Research Potential Suppliers
Conduct thorough research to identify potential coaster manufacturers. Use online directories, trade shows, and industry forums to compile a list of candidates.
– Why it matters: A wide pool of suppliers increases your chances of finding a manufacturer that fits your requirements and budget.
– What to look for: Focus on suppliers with a proven track record in producing coasters, particularly those with positive reviews from international buyers.
Step 3: Evaluate Supplier Certifications
Before moving forward, verify that potential suppliers hold relevant certifications, such as ISO 9001 or industry-specific standards.
– Why it matters: Certifications indicate that the manufacturer adheres to quality management practices, which can reduce the risk of defective products.
– What to look for: Ask for copies of certifications and check their validity with the issuing bodies.
Step 4: Request Samples
Always request product samples before making a large order. This allows you to assess the quality and craftsmanship of the coasters firsthand.
– Why it matters: Samples provide insight into the manufacturer’s capabilities and product quality.
– What to look for: Examine the materials, finish, and overall durability of the samples to ensure they meet your expectations.
Step 5: Assess Production Capacity and Lead Times
Inquire about the manufacturer’s production capacity and lead times for your order. Understanding these factors is crucial for planning your supply chain.
– Why it matters: Delays in production can disrupt your business operations and impact customer satisfaction.
– What to look for: Ensure the manufacturer can handle your order size and has a reliable timeline for delivery.
Step 6: Review Payment Terms and Conditions
Discuss payment terms and conditions before finalizing any agreements. Ensure that the terms are favorable and protect your interests.
– Why it matters: Clear payment terms can prevent misunderstandings and financial disputes later on.
– What to look for: Look for flexible payment options, including deposits and payment upon delivery, to mitigate risk.
Step 7: Establish Communication Channels
Effective communication is key to a successful partnership. Ensure that the manufacturer has a reliable communication system in place.
– Why it matters: Open lines of communication facilitate problem-solving and help maintain quality during production.
– What to look for: Check if the manufacturer is responsive and willing to provide updates throughout the production process.
By following these steps, international B2B buyers can effectively navigate the sourcing process for coaster manufacturers, ensuring a successful procurement experience.
Comprehensive Cost and Pricing Analysis for coaster manufacturer Sourcing
What Are the Key Cost Components in Coaster Manufacturing?
When sourcing from coaster manufacturers, understanding the cost structure is crucial for international B2B buyers. The primary cost components include:
-
Materials: The choice of materials significantly impacts costs. High-quality steel or aluminum, often used in coaster construction for durability, can vary greatly in price based on market fluctuations and supplier availability. Buyers should consider sourcing from local suppliers to reduce material costs.
-
Labor: Labor costs differ by region and manufacturing process. Countries with lower labor costs can offer competitive pricing, but this might come with trade-offs in quality or speed. Engage in discussions about labor practices to ensure ethical sourcing.
-
Manufacturing Overhead: This includes costs related to factory operation, utilities, and depreciation of equipment. Manufacturers with efficient operations can often pass savings onto buyers. Understanding the manufacturer’s operational efficiency can help in negotiations.
-
Tooling: Custom tooling can be a significant upfront cost, especially for specialized designs. Buyers should assess whether they can share tooling costs with other projects or negotiate for tooling included in the price for larger orders.
-
Quality Control (QC): Ensuring product quality through rigorous QC processes is vital. Manufacturers with established QC protocols may charge higher prices, but this can save buyers from costly defects and delays later on.
-
Logistics: Shipping costs can vary widely depending on the distance from the manufacturer, shipping mode (air vs. sea), and the complexity of the supply chain. For international buyers, understanding Incoterms is crucial to clarify who bears the cost at each stage of transport.
-
Margin: Finally, the manufacturer’s profit margin will affect the final price. This margin can vary based on market competition, perceived value, and the complexity of the product.
How Do Price Influencers Affect Coaster Manufacturing Costs?
Several factors can influence pricing in coaster manufacturing:
-
Volume and Minimum Order Quantity (MOQ): Larger orders typically result in lower per-unit costs due to economies of scale. Buyers should evaluate their purchasing strategies to optimize order sizes.
-
Specifications and Customization: Customized designs or specifications can significantly raise costs due to additional labor and materials required. Clear communication of requirements can help manage these costs.
-
Materials and Quality Certifications: Higher quality materials and certifications (such as ISO or CE) can increase costs but may also enhance the product’s longevity and marketability. Buyers should weigh the benefits against the additional costs.
-
Supplier Factors: The reputation and reliability of suppliers can affect pricing. Established suppliers may charge a premium for their proven track record, while less experienced manufacturers may offer lower prices but with higher risk.
-
Incoterms: Understanding the implications of different Incoterms (e.g., FOB, CIF) is essential. They determine who is responsible for shipping costs, insurance, and risks, affecting overall pricing.
What Are the Best Practices for Negotiating Prices with Coaster Manufacturers?
For international B2B buyers, especially from regions like Africa, South America, the Middle East, and Europe, effective negotiation can lead to significant cost savings. Here are some tips:
-
Research Market Prices: Familiarize yourself with current market rates for materials and labor to establish a baseline for negotiations.
-
Build Relationships: Establishing a rapport with suppliers can lead to better deals and improved service. Long-term relationships often yield better pricing structures.
-
Discuss Total Cost of Ownership (TCO): Highlight the importance of TCO in negotiations. A higher upfront cost may be justified if the product offers lower maintenance or operational costs over its lifecycle.
-
Be Transparent: Clearly communicate your budget constraints and volume requirements. This transparency can encourage manufacturers to offer tailored solutions that fit your financial parameters.
-
Evaluate All Costs: Consider not just the initial purchase price but also shipping, customs duties, and handling fees when assessing total costs.
Final Thoughts on Coaster Manufacturing Pricing
While costs can vary significantly based on multiple factors, understanding these components and influencers can empower international buyers to make informed sourcing decisions. Always consider obtaining multiple quotes and conducting thorough due diligence on potential suppliers to ensure the best value for your investment. Pricing is dynamic and can fluctuate based on market conditions, so stay informed and adaptable to secure the best deals.
Alternatives Analysis: Comparing coaster manufacturer With Other Solutions
When evaluating options for shipping and logistics solutions, international B2B buyers must consider various alternatives to traditional coaster manufacturers. Each alternative presents unique advantages and challenges that can impact operational efficiency and overall costs. Below, we will compare coaster manufacturers with two viable alternatives: container shipping and specialized freight services.
Comparison Aspect | Coaster Manufacturer | Container Shipping | Specialized Freight Services |
---|---|---|---|
Performance | Reliable for short-distance transport; limited cargo capacity | High capacity, suitable for long distances | Tailored solutions for specific cargo types |
Cost | Generally lower upfront costs, but higher per-unit transport costs | Competitive for bulk shipping; may incur port fees | Higher costs due to customization and speed |
Ease of Implementation | Simple setup; requires less infrastructure | Requires port facilities and logistics coordination | May require specialized equipment and logistics planning |
Maintenance | Moderate; involves regular inspections and repairs | Low; maintenance is primarily port-related | High; specialized equipment needs regular servicing |
Best Use Case | Short routes and smaller loads within regional markets | Global trade and large quantities of goods | Time-sensitive or high-value cargo requiring special handling |
What Are the Advantages and Disadvantages of Container Shipping?
Container shipping is a popular alternative that excels in transporting large volumes of goods over long distances. Its key benefits include significant cost savings per unit for bulk shipments and a well-established global network of ports. However, it may lack the flexibility needed for smaller shipments or regional deliveries, and shipping schedules can be inflexible, potentially delaying time-sensitive deliveries.
How Does Specialized Freight Services Compare?
Specialized freight services are tailored solutions designed for specific types of cargo, such as perishable goods or oversized items. The primary advantage of this approach is its ability to handle unique shipping requirements, ensuring that goods are transported safely and efficiently. However, this customization often comes at a premium price, and the complexity of logistics can make implementation more challenging compared to more straightforward solutions like coaster manufacturing or container shipping.
Conclusion: How Should B2B Buyers Choose the Right Shipping Solution?
When selecting the appropriate shipping solution, international B2B buyers should assess their specific needs, including cargo type, delivery timelines, and budget constraints. For businesses focused on regional transport with smaller loads, coaster manufacturers may offer a cost-effective solution. In contrast, companies engaged in global trade with large volumes may benefit from the efficiency of container shipping. Lastly, organizations requiring specialized handling for valuable or sensitive cargo might find that investing in specialized freight services aligns best with their operational requirements. By carefully evaluating these alternatives, buyers can make informed decisions that enhance their logistics strategies and overall business success.
Essential Technical Properties and Trade Terminology for coaster manufacturer
What Are the Key Technical Properties for Coaster Manufacturing?
When engaging with coaster manufacturers, understanding critical technical properties is essential for making informed purchasing decisions. Here are some key specifications:
-
Material Grade
– The material grade used in coaster construction significantly impacts durability and performance. Common materials include steel, aluminum, and composite materials, each offering unique properties such as corrosion resistance, weight, and strength. Selecting the right material is crucial for ensuring that the coaster meets operational requirements and local regulations. -
Tolerance Levels
– Tolerance levels refer to the allowable variation in dimensions and specifications during the manufacturing process. For coasters, maintaining tight tolerances is vital to ensure safety and performance. High tolerance levels can prevent operational issues, such as misalignment or structural failure, which could lead to costly repairs and safety concerns. -
Payload Capacity
– This specification defines the maximum weight a coaster can safely carry, including cargo and any additional weight from equipment or personnel. Knowing the payload capacity is essential for B2B buyers to ensure that the coaster can handle their specific operational needs without risking structural integrity or safety. -
Dimensions and Footprint
– The overall dimensions, including length, width, and height, are critical for determining how the coaster will fit into existing infrastructure. B2B buyers must consider these dimensions to ensure compatibility with ports, docks, or other facilities where the coaster will operate. -
Design and Stability Features
– Features such as hull shape, ballast systems, and stabilization mechanisms are essential for ensuring safe and efficient operation. A well-designed coaster minimizes rolling resistance and enhances stability in various sea conditions, which is crucial for operational efficiency and safety.
What Trade Terminology Should B2B Buyers Understand?
Navigating the coaster manufacturing industry requires familiarity with specific trade terms. Here are several key terms that international buyers should know:
-
OEM (Original Equipment Manufacturer)
– An OEM is a company that produces parts or equipment that may be marketed by another manufacturer. For coaster manufacturers, understanding OEM relationships can help buyers identify reliable suppliers and assess the quality of components used in coaster production. -
MOQ (Minimum Order Quantity)
– MOQ refers to the smallest quantity of a product that a supplier is willing to sell. Knowing the MOQ is essential for budgeting and inventory management, particularly for B2B buyers in regions like Africa or South America where demand may fluctuate. -
RFQ (Request for Quotation)
– An RFQ is a document sent to suppliers to request pricing and availability for specific products or services. It is a critical step in the procurement process, allowing buyers to compare offers and negotiate terms effectively. -
Incoterms (International Commercial Terms)
– Incoterms are a set of predefined commercial terms published by the International Chamber of Commerce (ICC) that define the responsibilities of buyers and sellers in international transactions. Familiarity with these terms helps B2B buyers understand shipping costs, risk management, and delivery obligations. -
Lead Time
– Lead time is the amount of time it takes from placing an order to receiving the product. Understanding lead times is crucial for B2B buyers to plan their operations and ensure that they have the necessary equipment available when needed.
By grasping these essential technical properties and trade terms, international B2B buyers can make more informed decisions when selecting coaster manufacturers, ensuring that their purchases align with operational needs and industry standards.
Navigating Market Dynamics and Sourcing Trends in the coaster manufacturer Sector
What Are the Current Market Dynamics and Key Trends in the Coaster Manufacturing Sector?
The coaster manufacturing sector is witnessing significant transformations driven by globalization, technological advancements, and changing consumer preferences. For international B2B buyers, especially from regions like Africa, South America, the Middle East, and Europe, understanding these dynamics is crucial for making informed sourcing decisions.
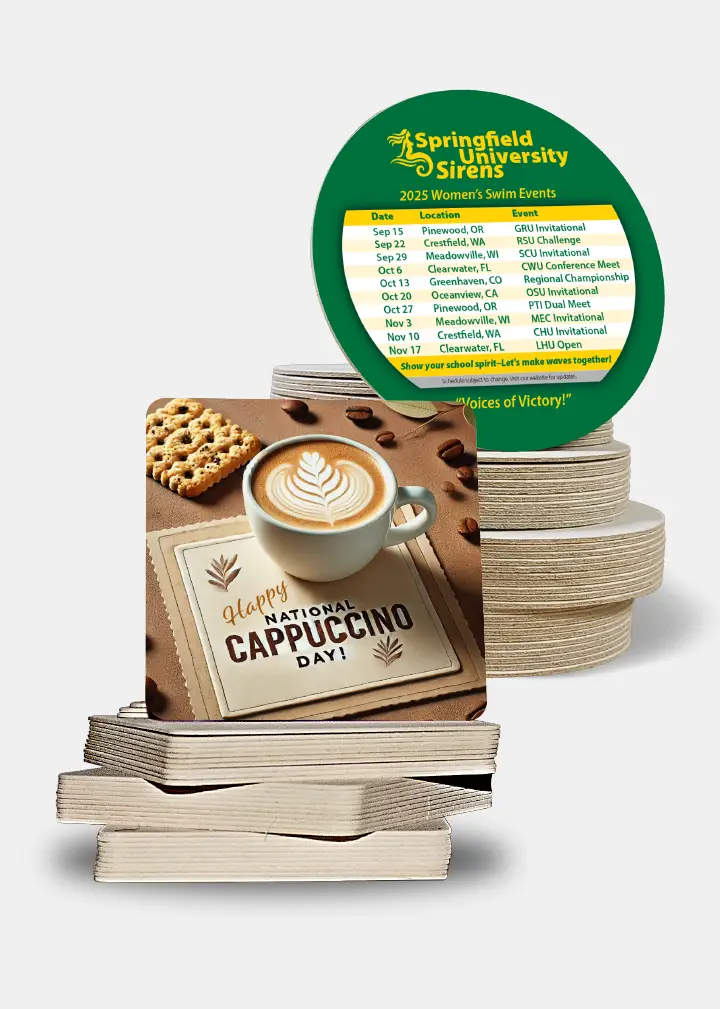
A stock image related to coaster manufacturer.
One key trend is the increasing adoption of automation and digital technologies in manufacturing processes. This shift not only enhances production efficiency but also reduces operational costs, making it more feasible for manufacturers to cater to diverse markets. Furthermore, the use of data analytics allows companies to optimize supply chain management and improve inventory control, providing a competitive edge.
Another emerging trend is the growing importance of customization. Buyers are increasingly seeking tailored coaster solutions that meet specific operational requirements, which necessitates manufacturers to be agile and responsive. This trend aligns with the broader consumer demand for personalized experiences, which is particularly pronounced in markets like South Africa and the UAE.
Additionally, sustainability has become a pivotal consideration. Manufacturers are under pressure to adopt eco-friendly materials and processes. This shift is not merely a regulatory compliance issue but also a response to consumer demand for sustainable practices. For buyers, sourcing from manufacturers that prioritize sustainability can enhance brand reputation and customer loyalty.
How Does Sustainability and Ethical Sourcing Impact the Coaster Manufacturing Sector?
Sustainability in the coaster manufacturing sector is not just a trend; it is becoming an integral part of business strategy. The environmental impact of manufacturing processes, including energy consumption and waste generation, is under scrutiny. Buyers are increasingly prioritizing suppliers who demonstrate a commitment to reducing their carbon footprint and implementing eco-friendly practices.
Ethical sourcing has gained prominence as well. This encompasses not only environmental considerations but also social responsibility within the supply chain. For B2B buyers, ensuring that their suppliers adhere to ethical labor practices is crucial. Certifications such as ISO 14001 for environmental management and Fair Trade certifications are becoming essential in evaluating potential suppliers.
Moreover, utilizing ‘green’ materials, such as recycled or sustainably sourced components, can significantly enhance the appeal of a manufacturer’s offerings. Buyers from regions like Europe, where sustainability standards are stringent, are particularly vigilant about these aspects. This not only aligns with regulatory requirements but also meets the growing consumer expectations for responsible sourcing.
What Is the Historical Context of Coaster Manufacturing Relevant to B2B Buyers?
The coaster manufacturing sector has evolved significantly since its inception. Initially, coasters were built primarily for local shipping needs, with limited designs and materials. Over the decades, advancements in engineering and materials science have transformed coaster designs, allowing for larger and more efficient vessels.
In the mid-20th century, the introduction of steel hulls and diesel engines marked a turning point, enhancing durability and operational capabilities. This evolution has made coasters more appealing to international B2B buyers, as they offer versatile solutions for various logistical challenges.
Today, the focus has shifted towards integrating modern technologies, such as automation and advanced navigation systems, which further enhance the operational efficiency of coasters. Understanding this historical context helps buyers appreciate the innovations that have shaped the current market and allows them to make more strategic sourcing decisions aligned with future trends.
In conclusion, navigating the coaster manufacturing sector requires a deep understanding of market dynamics, sustainability considerations, and historical developments. By staying informed, B2B buyers can align their sourcing strategies to leverage opportunities and address challenges in this evolving landscape.
Frequently Asked Questions (FAQs) for B2B Buyers of coaster manufacturer
-
How do I solve supply chain issues when sourcing coaster manufacturers?
To address supply chain issues, start by diversifying your supplier base. This reduces dependency on a single source and mitigates risks. Establish clear communication channels with manufacturers to ensure timely updates on production schedules and potential delays. Additionally, consider using local suppliers in Africa, South America, or the Middle East to minimize shipping times and costs. Implementing a robust logistics management system can also enhance visibility throughout the supply chain, enabling proactive issue resolution. -
What is the best approach for vetting international coaster manufacturers?
When vetting international coaster manufacturers, prioritize their reputation and experience in the industry. Request references from previous clients and conduct background checks on their business practices. Visit their facilities if possible, or use third-party inspection services to assess quality control processes. Evaluate their certifications and compliance with international safety standards, especially if you are importing into regions with strict regulations, such as Europe or the Middle East. -
How can I customize coaster designs to meet specific needs?
Customization options vary by manufacturer, so it’s essential to communicate your specific requirements clearly. Discuss design aspects, such as dimensions, materials, and branding elements, early in the negotiation process. Some manufacturers may offer design services or have a portfolio of customizable templates. Ensure that you receive prototypes or samples to evaluate before finalizing orders. Collaborating closely with the manufacturer will facilitate a smoother customization process. -
What are the typical minimum order quantities (MOQs) for coaster manufacturers?
Minimum order quantities can differ significantly among coaster manufacturers, influenced by factors like production capabilities and material costs. Generally, MOQs range from a few dozen to several hundred units. It’s advisable to discuss your needs with potential suppliers to negotiate MOQs that align with your business goals. Some manufacturers may be flexible, especially for first-time orders or trial runs. -
What payment terms should I expect when sourcing from coaster manufacturers?
Payment terms can vary widely based on the manufacturer’s policies and your relationship with them. Common practices include a deposit upfront (often 30-50%) and the balance upon delivery or before shipping. Some manufacturers may offer credit terms for established relationships. Always clarify payment methods accepted (such as bank transfers or letters of credit) and ensure that terms are documented in a formal contract to avoid disputes. -
How do quality assurance processes work in coaster manufacturing?
Quality assurance (QA) processes in coaster manufacturing typically involve several stages, including raw material inspection, in-process quality checks, and final product evaluation. Many manufacturers implement ISO standards or similar quality frameworks. It’s beneficial to inquire about their QA protocols and request documentation to verify compliance. Consider arranging for third-party inspections to ensure that products meet your quality expectations before shipment. -
What logistics considerations should I keep in mind when importing coasters?
When importing coasters, consider shipping methods, customs regulations, and potential tariffs. Choose a logistics partner experienced in international shipping to navigate these complexities. Ensure that all necessary documentation, such as invoices and certificates of origin, is prepared to facilitate smooth customs clearance. Additionally, factor in lead times for shipping, as delays can impact your supply chain and customer satisfaction. -
What are the benefits of working with a local coaster manufacturer?
Working with a local coaster manufacturer offers several advantages, including reduced shipping costs and shorter delivery times, which are critical for maintaining inventory levels. Local suppliers may also provide more personalized service and flexibility in order adjustments. Additionally, supporting local businesses can enhance your brand’s reputation in the community and strengthen relationships with stakeholders in your region. This is particularly relevant for businesses operating in Africa, South America, or the Middle East, where local partnerships can drive growth.
Important Disclaimer & Terms of Use
⚠️ Important Disclaimer
The information provided in this guide, including content regarding manufacturers, technical specifications, and market analysis, is for informational and educational purposes only. It does not constitute professional procurement advice, financial advice, or legal advice.
While we have made every effort to ensure the accuracy and timeliness of the information, we are not responsible for any errors, omissions, or outdated information. Market conditions, company details, and technical standards are subject to change.
B2B buyers must conduct their own independent and thorough due diligence before making any purchasing decisions. This includes contacting suppliers directly, verifying certifications, requesting samples, and seeking professional consultation. The risk of relying on any information in this guide is borne solely by the reader.
Strategic Sourcing Conclusion and Outlook for coaster manufacturer
What Are the Key Takeaways for Strategic Sourcing in Coaster Manufacturing?
In the evolving landscape of coaster manufacturing, strategic sourcing remains critical for international B2B buyers. Understanding the diverse market dynamics across regions such as Africa, South America, the Middle East, and Europe can lead to optimized procurement processes and improved supplier relationships. Buyers should prioritize partnerships with manufacturers that demonstrate reliability, innovation, and adherence to quality standards.
How Can B2B Buyers Leverage Strategic Sourcing for Competitive Advantage?
By adopting a strategic sourcing approach, companies can not only reduce costs but also enhance their supply chain resilience. Engaging with local manufacturers can yield significant benefits, including reduced lead times and improved logistics. Furthermore, aligning sourcing strategies with sustainability goals is increasingly vital as global markets trend towards eco-friendliness.
What is the Future Outlook for Coaster Manufacturing?
As we look ahead, the demand for coasters will likely continue to rise, driven by increasing global trade and the need for efficient cargo transport solutions. B2B buyers are encouraged to explore innovative technologies and sustainable practices in their sourcing strategies to stay ahead of the competition.
In conclusion, now is the opportune moment for international buyers, particularly from regions like South Africa and the UAE, to refine their sourcing strategies and invest in partnerships that promise long-term value and growth. Take action today to secure a competitive edge in the coaster manufacturing industry.