Discover Top Gyro Manufacturers: Your Complete Sourcing Guide (2025)
Introduction: Navigating the Global Market for gyro manufacturer
In today’s dynamic global marketplace, sourcing high-quality gyro manufacturers poses a significant challenge for B2B buyers, particularly those operating in emerging markets such as Africa, South America, and the Middle East. Understanding the intricacies of gyro technology—used in various applications from aerospace to automotive and industrial machinery—can be daunting. This guide aims to simplify the process, providing insights into the types of gyros available, their specific applications, and essential considerations for supplier vetting and cost analysis.
With a comprehensive scope that covers everything from the latest technological advancements to practical tips for assessing supplier reliability, this resource equips international buyers with the knowledge needed to make informed purchasing decisions. By addressing critical questions such as, “What are the key factors to consider when choosing a gyro manufacturer?” and “How can I effectively evaluate the cost versus value of gyros?” the guide empowers businesses to navigate the complexities of the global gyro market confidently.
Particularly for buyers in Europe and regions like Australia and Indonesia, this guide highlights unique market trends and regional considerations that can impact sourcing strategies. In an environment where quality and reliability are paramount, having access to detailed insights and actionable strategies can make a substantial difference in securing the right partnerships and achieving operational excellence.
Understanding gyro manufacturer Types and Variations
Type Name | Key Distinguishing Features | Primary B2B Applications | Brief Pros & Cons for Buyers |
---|---|---|---|
Mechanical Gyroscopes | Utilizes spinning mass for orientation detection | Aerospace, Marine Navigation | Pros: Simple design, reliable. Cons: Bulky, sensitive to vibrations. |
Fiber Optic Gyroscopes | Employs light interference for precise measurements | Robotics, Aerospace, Automotive | Pros: High accuracy, compact. Cons: Expensive, sensitive to temperature changes. |
MEMS Gyroscopes | Miniaturized sensors using micro-electromechanical systems | Consumer Electronics, Drones, Smartphones | Pros: Cost-effective, lightweight. Cons: Lower precision than larger models. |
Ring Laser Gyroscopes | Uses laser beams for rotational measurement | Space Exploration, Military Applications | Pros: Extremely accurate, stable over time. Cons: High cost, complex installation. |
Vibrating Structure Gyroscopes | Measures angular rate via vibrating elements | Industrial Equipment, Automotive | Pros: Robust, good for harsh environments. Cons: Limited precision, larger size. |
What are the Characteristics and Suitability of Mechanical Gyroscopes?
Mechanical gyroscopes are traditional devices that leverage the principles of angular momentum. They feature a spinning rotor that remains stable in its orientation, making them ideal for applications in aerospace and marine navigation. B2B buyers should consider the simplicity and reliability of mechanical gyroscopes, especially for environments where vibration is minimal. However, their larger size and sensitivity to external vibrations can limit their application in more dynamic settings.
How Do Fiber Optic Gyroscopes Stand Out in Precision?
Fiber optic gyroscopes utilize the interference of light waves to detect rotation, offering exceptional accuracy. This technology is particularly suitable for high-stakes applications such as robotics, aerospace, and automotive sectors where precision is paramount. B2B buyers should weigh the benefits of high accuracy against the higher cost and sensitivity to temperature fluctuations, which can impact performance in varying environments.
What Makes MEMS Gyroscopes a Popular Choice for Consumer Electronics?
MEMS (Micro-Electro-Mechanical Systems) gyroscopes are compact sensors that have gained popularity in consumer electronics, drones, and smartphones. Their small size and cost-effectiveness make them ideal for mass production. However, while they are lightweight and affordable, B2B buyers must acknowledge that their precision may not match that of larger, more specialized gyroscopes. This makes them suitable for applications where space and budget are constraints, but accuracy is still important.
Why Choose Ring Laser Gyroscopes for High-Precision Applications?
Ring laser gyroscopes are designed for high-precision measurements, utilizing laser beams to detect rotation. They are predominantly used in space exploration and military applications where accuracy is critical. B2B buyers should consider the long-term stability and precision of these gyroscopes. However, their complexity and high cost may deter some businesses from investing, especially if simpler alternatives can meet their needs.
What are the Benefits and Limitations of Vibrating Structure Gyroscopes?
Vibrating structure gyroscopes measure angular rates through vibrating elements, making them robust for industrial applications. They excel in harsh environments, providing reliable performance in applications such as automotive systems. Buyers should appreciate their durability and resistance to environmental challenges, but must also consider their limitations in precision and size compared to other types of gyroscopes, which may affect their suitability for certain high-precision applications.
Related Video: How the Gyro Sensor Works
Key Industrial Applications of gyro manufacturer
Industry/Sector | Specific Application of gyro manufacturer | Value/Benefit for the Business | Key Sourcing Considerations for this Application |
---|---|---|---|
Aerospace & Defense | Attitude and Heading Reference Systems (AHRS) | Enhanced navigation accuracy and safety in aircraft operations. | Compliance with international standards and certifications. |
Automotive | Advanced Driver Assistance Systems (ADAS) | Improved vehicle safety and autonomous driving capabilities. | Integration with existing vehicle systems and software. |
Robotics & Automation | Motion Control in Robotics | Increased precision and efficiency in automated processes. | Compatibility with various robotic architectures and sensors. |
Marine Technology | Stabilization Systems for Vessels | Enhanced stability and safety in maritime operations. | Environmental resistance and robustness in harsh conditions. |
Industrial Equipment | Gyroscopic Sensors for Machinery | Improved operational efficiency and reduced downtime. | Durability and reliability under heavy operational loads. |
How is Gyro Technology Used in Aerospace & Defense?
In the aerospace and defense sector, gyro manufacturers supply Attitude and Heading Reference Systems (AHRS) that are critical for aircraft navigation. These systems provide precise orientation data, which is essential for maintaining flight stability and safety. International buyers must ensure that these gyros meet stringent aviation standards and certifications, as well as consider factors such as weight and power consumption to optimize performance in aircraft.
What Role Do Gyros Play in Automotive Applications?
Gyro technology is integral to Advanced Driver Assistance Systems (ADAS) in the automotive industry. These systems utilize gyroscopic sensors to detect vehicle orientation and movement, enabling features like lane-keeping assistance and automatic emergency braking. For B2B buyers, it’s crucial to source gyros that seamlessly integrate with existing vehicle technology, ensuring compatibility with various software platforms and compliance with safety regulations.
How Are Gyros Enhancing Robotics & Automation?
In robotics and automation, gyro manufacturers provide motion control systems that enhance the precision and efficiency of robotic movements. Gyroscopic sensors help robots maintain balance and orientation, which is vital in applications ranging from manufacturing to healthcare. Buyers should consider the compatibility of these gyros with different robotic architectures and ensure they can withstand the operational demands of specific tasks.
Why Are Gyros Important in Marine Technology?
Marine technology relies on stabilization systems equipped with gyroscopic sensors to maintain the balance and stability of vessels in turbulent waters. These systems significantly enhance safety and operational efficiency, particularly in commercial shipping and recreational boating. When sourcing gyros for marine applications, buyers must prioritize environmental resistance and robustness, as these devices must perform reliably in harsh marine conditions.
What Benefits Do Gyros Bring to Industrial Equipment?
In industrial settings, gyroscopic sensors are utilized to monitor and control the operation of heavy machinery. This technology improves operational efficiency by providing real-time data on machine orientation, which can prevent operational failures and reduce downtime. Buyers should focus on the durability and reliability of these gyros, ensuring they can withstand heavy loads and demanding operational environments.
Related Video: Two-axis gyro-stabilized platform based on INS (strapdown inertial navigation system) by Gyrolab
3 Common User Pain Points for ‘gyro manufacturer’ & Their Solutions
Scenario 1: Navigating Quality Assurance Challenges in Gyro Manufacturing
The Problem: B2B buyers often face the challenge of ensuring quality and reliability in gyro products. This issue is particularly pronounced when sourcing from international manufacturers, where differences in manufacturing standards and quality control practices can lead to inconsistent product performance. Buyers in regions like Africa and South America may find it especially difficult to ascertain the quality of gyros due to limited access to direct manufacturer audits or certifications. This uncertainty can lead to project delays, increased costs, and compromised operational efficiency.
The Solution: To mitigate these quality assurance concerns, buyers should prioritize sourcing from gyro manufacturers that have established international quality certifications, such as ISO 9001. It is crucial to conduct thorough due diligence by requesting detailed product specifications, quality assurance processes, and past performance metrics. Engaging in direct communication with manufacturers can also be beneficial; consider requesting sample products or conducting on-site visits to evaluate manufacturing processes firsthand. Additionally, utilizing third-party quality assurance services can provide an unbiased assessment of the manufacturer’s capabilities, ensuring that the gyros meet the required standards before bulk orders are placed.
Scenario 2: Managing Supply Chain Disruptions for Gyro Components
The Problem: Supply chain disruptions can pose significant challenges for B2B buyers, especially in industries reliant on precise components like gyros. Buyers from the Middle East and Europe may experience delays due to geopolitical issues, transportation bottlenecks, or raw material shortages. These disruptions can halt production lines, lead to inventory shortages, and ultimately affect customer satisfaction and business profitability.
The Solution: To address these supply chain issues, it is essential to establish a diversified sourcing strategy. This involves identifying multiple gyro manufacturers across different regions to mitigate risks associated with relying on a single supplier. Implementing a just-in-case inventory model rather than a just-in-time model can also provide a buffer against unforeseen disruptions. Buyers should maintain close relationships with their suppliers and continuously monitor their supply chain for potential vulnerabilities. Leveraging technology such as supply chain management software can help track inventory levels, forecast demand, and optimize logistics, thereby reducing the impact of disruptions on operations.
Scenario 3: Overcoming Technical Compatibility Issues with Gyro Systems
The Problem: Technical compatibility between gyro systems and existing equipment can be a significant pain point for B2B buyers. Companies in sectors like aerospace or automotive might struggle to integrate new gyro products with older systems, leading to functionality issues and increased costs for modifications. This is especially concerning for buyers in regions with rapidly evolving technology landscapes, such as Europe and South America, where innovation cycles are swift.
The Solution: To overcome compatibility issues, B2B buyers should engage in comprehensive needs assessments before making purchasing decisions. This involves not only understanding the specifications of the gyro systems but also evaluating the existing equipment and its capabilities. Collaboration with the gyro manufacturer during the design phase can facilitate custom solutions tailored to specific technical environments. Moreover, investing in modular gyro systems that allow for easier upgrades and compatibility with various platforms can provide long-term flexibility. Lastly, establishing a robust support system with the manufacturer for ongoing technical assistance can help address integration challenges effectively.
Strategic Material Selection Guide for gyro manufacturer
When selecting materials for gyroscope manufacturing, it’s crucial to consider not only the physical properties of the materials but also their compatibility with various applications and compliance with international standards. Here, we analyze four common materials used in gyro manufacturing: aluminum, stainless steel, titanium, and composite materials. Each material has distinct characteristics that can significantly impact performance, durability, and cost-effectiveness.
What Are the Key Properties of Aluminum in Gyro Manufacturing?
Aluminum is widely used in gyro manufacturing due to its lightweight nature and good strength-to-weight ratio. It typically exhibits excellent corrosion resistance, particularly when anodized, and can withstand moderate temperature ranges. The key properties that make aluminum suitable for gyroscopes include:
- Temperature Rating: Up to 150°C (302°F) for standard grades.
- Corrosion Resistance: Good, especially with protective coatings.
Pros and Cons of Aluminum: While aluminum is cost-effective and easy to machine, it can be less durable under extreme conditions compared to other metals. Its lower tensile strength may limit its use in high-stress applications.
How Does Stainless Steel Compare in Terms of Performance?
Stainless steel is another popular choice for gyro components due to its superior strength and corrosion resistance. It performs well under a wide range of temperatures and is less prone to deformation over time.
- Temperature Rating: Can withstand temperatures up to 800°C (1472°F).
- Corrosion Resistance: Excellent, especially in harsh environments.
Pros and Cons of Stainless Steel: The main advantage of stainless steel is its durability and resistance to wear. However, it is heavier and more expensive than aluminum, which may be a consideration for international buyers looking for lightweight solutions.
Why Is Titanium Considered a Premium Material for Gyros?
Titanium is recognized for its exceptional strength-to-weight ratio and outstanding corrosion resistance, making it ideal for high-performance gyroscopes, especially in aerospace and military applications.
- Temperature Rating: Up to 600°C (1112°F).
- Corrosion Resistance: Excellent, even in extreme environments.
Pros and Cons of Titanium: While titanium offers superior performance, it comes with a high cost and can be challenging to machine, which may increase manufacturing complexity. This makes it suitable for specialized applications where performance outweighs cost concerns.
What Role Do Composite Materials Play in Gyroscope Applications?
Composite materials, such as carbon fiber reinforced polymers, are increasingly being used in gyro manufacturing due to their lightweight and high-strength characteristics. They can be tailored to specific applications, providing flexibility in design.
- Temperature Rating: Generally up to 120°C (248°F) depending on the resin used.
- Corrosion Resistance: Excellent, particularly against chemical exposure.
Pros and Cons of Composites: The main advantage of composites is their lightweight nature and design flexibility. However, they can be more expensive and may require specialized manufacturing processes, which could be a barrier for some international buyers.
Summary Table of Material Selection for Gyro Manufacturing
Material | Typical Use Case for gyro manufacturer | Key Advantage | Key Disadvantage/Limitation | Relative Cost (Low/Med/High) |
---|---|---|---|---|
Aluminum | General-purpose gyroscopes | Lightweight and cost-effective | Lower strength under extreme loads | Low |
Stainless Steel | High-stress applications | Excellent durability and corrosion resistance | Heavier and more expensive | Medium |
Titanium | Aerospace and military applications | Superior strength-to-weight ratio | High cost and machining complexity | High |
Composite | Specialized lightweight gyroscopes | Design flexibility and lightweight | Higher cost and specialized manufacturing | Medium to High |
In summary, the choice of material for gyroscope manufacturing should align with the specific performance requirements of the application, cost considerations, and compliance with international standards. Buyers from diverse regions, including Africa, South America, the Middle East, and Europe, should evaluate these factors to ensure optimal performance and compliance with local regulations.
In-depth Look: Manufacturing Processes and Quality Assurance for gyro manufacturer
What Are the Main Stages of Gyro Manufacturing Processes?
The manufacturing process for gyroscopes involves several critical stages, each designed to ensure precision and reliability. Understanding these stages is vital for B2B buyers looking to evaluate potential suppliers.
Material Preparation: What Materials Are Used in Gyro Manufacturing?
Gyroscopes require high-quality materials to ensure their performance and durability. Common materials include:
- Metals: Aluminum and stainless steel are frequently used due to their strength-to-weight ratios.
- Plastics: Certain components may be made from high-performance plastics to reduce weight and cost.
- Glass: Optical gyros may utilize specialized glass for sensor components.
During material preparation, suppliers typically inspect incoming materials for compliance with specifications. This includes verifying the chemical composition and mechanical properties through tests such as tensile strength and hardness.
What Techniques Are Employed in Gyro Forming and Assembly?
The forming and assembly processes for gyroscopes involve precision engineering techniques, including:
- CNC Machining: Computer Numerical Control (CNC) machining is essential for creating complex geometries with high accuracy. It allows for the production of intricate parts that are critical to gyroscope functionality.
- Injection Molding: For plastic components, injection molding is a common technique. This method provides consistency and allows for high-volume production.
- Laser Cutting: This technique is often used for creating precise cuts in metal and plastic components, ensuring that parts fit together seamlessly.
Assembly is carried out in controlled environments to minimize contamination and ensure quality. Each component is carefully assembled, and alignment is verified using specialized tools.
How Is Finishing Achieved in Gyro Manufacturing?
Finishing processes enhance the performance and aesthetics of gyroscopes. Common finishing techniques include:
- Surface Treatments: Processes like anodizing or plating protect metal surfaces from corrosion and wear.
- Polishing: For optical components, polishing is crucial to achieve the necessary clarity and precision.
- Calibration: After assembly, gyroscopes undergo calibration to ensure accuracy. This involves adjusting the sensors and other components to meet specific performance standards.
What Quality Assurance Standards Are Relevant for Gyro Manufacturers?
Quality assurance (QA) is paramount in gyro manufacturing, especially for international B2B buyers. Several standards guide the QA processes:
- ISO 9001: This international standard specifies requirements for a quality management system (QMS). It emphasizes the importance of continual improvement and customer satisfaction.
- CE Marking: For products sold within the European Economic Area, CE marking indicates compliance with safety, health, and environmental protection standards.
- API Standards: For gyroscopes used in oil and gas applications, adherence to American Petroleum Institute (API) standards is critical.
What Are the Key Quality Control Checkpoints in Gyro Manufacturing?
Quality control (QC) is integrated throughout the manufacturing process, with specific checkpoints to ensure product integrity:
-
Incoming Quality Control (IQC): This initial phase involves inspecting raw materials and components before they enter the production process. It includes verifying supplier certifications and conducting physical inspections.
-
In-Process Quality Control (IPQC): During manufacturing, regular checks are performed to monitor processes and identify defects early. This can involve automated inspections using sensors or manual checks by trained personnel.
-
Final Quality Control (FQC): Once the gyroscopes are fully assembled, they undergo final inspections and testing. This includes performance testing under simulated operating conditions to verify functionality.
What Testing Methods Are Commonly Used in Gyro Quality Assurance?
Various testing methods are employed to ensure gyroscopes meet strict performance standards:
- Functional Testing: This involves checking the gyro’s response to rotational movement to ensure it meets specified performance criteria.
- Environmental Testing: Gyros may be subjected to extreme temperatures, humidity, and vibrations to assess their reliability in various conditions.
- Lifetime Testing: Accelerated life testing can simulate long-term use, helping to identify potential failures before products reach the market.
How Can B2B Buyers Verify Supplier Quality Control?
B2B buyers, particularly those from Africa, South America, the Middle East, and Europe, should take proactive steps to verify a supplier’s quality control processes:
-
Supplier Audits: Conducting on-site audits allows buyers to assess a supplier’s manufacturing practices, QA processes, and compliance with international standards.
-
Reviewing Quality Reports: Requesting detailed quality assurance reports, including inspection and testing results, can provide insights into a supplier’s commitment to quality.
-
Third-Party Inspections: Engaging independent third-party inspection services can provide an unbiased assessment of a supplier’s manufacturing and QC processes.
What Are the Quality Control Nuances for International B2B Buyers?
International buyers face unique challenges when it comes to quality control in gyro manufacturing. It is essential to understand:
-
Regulatory Differences: Different regions may have varying standards and regulations. Buyers must ensure that their suppliers comply with both local and international requirements.
-
Cultural Factors: Communication barriers and cultural differences can impact quality assurance practices. Establishing clear expectations and regular communication is critical for successful partnerships.
-
Logistics and Supply Chain Management: Understanding the logistics involved in international shipping, including how products are handled and stored, can affect quality. Implementing strict quality checks during transit can mitigate risks.
By comprehensively understanding these manufacturing processes and quality assurance measures, international B2B buyers can make informed decisions when selecting gyro manufacturers that align with their quality expectations and operational needs.
Practical Sourcing Guide: A Step-by-Step Checklist for ‘gyro manufacturer’
Introduction
This practical sourcing guide is designed for international B2B buyers seeking to procure gyro manufacturing services. By following this step-by-step checklist, you will be equipped with actionable insights to streamline your sourcing process, ensure quality, and establish reliable partnerships with suppliers across Africa, South America, the Middle East, and Europe.
Step 1: Define Your Technical Specifications
Clearly outlining your technical requirements is the foundation of successful sourcing. Identify the specific types of gyros you need, including dimensions, materials, and performance characteristics.
– Considerations: Different industries may require unique specifications, so ensure your requirements align with your application needs.
Step 2: Conduct Market Research for Suppliers
Thorough market research helps you identify potential suppliers with a solid reputation in gyro manufacturing. Look for companies that specialize in your required gyro types and understand your industry’s demands.
– Sources: Utilize industry directories, trade shows, and online platforms like Alibaba or ThomasNet to gather a list of potential suppliers.
Step 3: Evaluate Potential Suppliers
Before committing, it’s crucial to vet suppliers thoroughly. Request company profiles, case studies, and references from buyers in a similar industry or region.
– Key Elements to Check:
– Experience: Look for suppliers with a proven track record in gyro manufacturing.
– Client Feedback: Read reviews or testimonials to gauge satisfaction levels.
Step 4: Verify Supplier Certifications and Compliance
Ensure that your chosen suppliers comply with relevant industry standards and certifications. This step is vital for guaranteeing product quality and safety.
– Important Certifications:
– ISO 9001 for quality management systems.
– Industry-specific certifications that might be applicable based on your region or sector.
Step 5: Request Samples for Quality Assessment
Once you have shortlisted suppliers, request product samples to evaluate their quality firsthand. This allows you to assess the craftsmanship and ensure it meets your specifications.
– What to Look For:
– Material quality, precision in design, and overall performance of the gyros during testing.
Step 6: Negotiate Terms and Pricing
After selecting a supplier, engage in negotiations to establish favorable terms. Discuss pricing, payment terms, delivery timelines, and any after-sales support.
– Negotiation Tips:
– Be transparent about your budget but also emphasize the value of quality and reliability.
Step 7: Establish Clear Communication Channels
Effective communication is crucial throughout the sourcing process. Ensure that you have established clear channels for ongoing dialogue with your supplier.
– Best Practices:
– Use project management tools or regular check-in meetings to keep all parties aligned and address any issues promptly.
By following this checklist, you will be well-prepared to navigate the complexities of sourcing gyro manufacturing services, ensuring that you partner with reliable suppliers who meet your specific needs.

A stock image related to gyro manufacturer.
Comprehensive Cost and Pricing Analysis for gyro manufacturer Sourcing
What Are the Key Cost Components in Gyro Manufacturing?
Understanding the cost structure of gyro manufacturing is crucial for international B2B buyers. The primary cost components include:
-
Materials: The choice of materials significantly impacts costs. High-quality materials for gyroscopes, such as advanced alloys or composites, can increase initial expenses but may enhance performance and longevity.
-
Labor: Skilled labor is essential for precision manufacturing. Labor costs vary by region; countries with lower labor costs may offer competitive pricing but could compromise on quality.
-
Manufacturing Overhead: This includes costs related to factory operations, utilities, and maintenance. Efficient manufacturing processes can reduce overhead and improve overall pricing.
-
Tooling: Custom tooling can be a significant upfront investment. The complexity of the design and the required precision will influence tooling costs.
-
Quality Control (QC): Implementing rigorous QC processes is vital for ensuring product reliability. This can add to the costs but is essential for maintaining certifications and customer trust.
-
Logistics: Shipping and handling costs can vary based on the destination. Import duties and tariffs can also influence the total cost.
-
Margin: Manufacturers typically include a profit margin in their pricing. Understanding the market dynamics can help buyers negotiate better terms.
How Do Price Influencers Affect Gyro Manufacturing Costs?
Several factors can influence the pricing of gyroscopes:
-
Volume/MOQ (Minimum Order Quantity): Bulk purchases often lead to discounts. Buyers should evaluate their needs to maximize cost efficiency.
-
Specifications and Customization: Customized gyroscopes will generally cost more than standard models. Buyers should clarify their requirements upfront to avoid unexpected costs.
-
Materials: The choice of materials can significantly alter pricing. Higher-grade materials may offer better performance but at a premium price.
-
Quality and Certifications: Products that meet international quality standards or certifications may carry higher costs. However, these can be crucial for compliance and marketability.
-
Supplier Factors: The reputation and reliability of the supplier can impact pricing. Established suppliers may charge more but often offer better quality assurance.
-
Incoterms: Understanding shipping terms is essential for cost management. Different Incoterms can shift the burden of logistics costs and risks between buyer and seller.
What Negotiation Tips Can Help Buyers Achieve Cost-Efficiency?
To navigate the complex landscape of gyro sourcing, international buyers should consider the following strategies:
-
Research and Benchmarking: Conduct thorough market research to understand pricing trends and benchmarks. This can empower buyers during negotiations.
-
Leverage Relationships: Building long-term relationships with suppliers can lead to better terms and pricing. Trust often results in discounts and favorable conditions.
-
Negotiate on Volume: If possible, negotiate for lower prices based on volume commitments. Suppliers are often willing to offer discounts for larger orders.
-
Assess Total Cost of Ownership (TCO): Consider not just the purchase price but also the long-term costs associated with maintenance, reliability, and potential downtime. This holistic view can justify a higher initial investment.
-
Flexibility on Specifications: If certain specifications can be relaxed without compromising performance, this may lead to cost savings.
What Pricing Nuances Should International Buyers Be Aware Of?
International buyers, particularly those from Africa, South America, the Middle East, and Europe, should be aware of specific pricing nuances:
-
Currency Fluctuations: Exchange rates can impact costs significantly. Buyers should consider locking in prices when favorable rates are available.
-
Import Duties and Taxes: Understanding local import regulations and taxes is essential to calculate the final landed cost of products accurately.
-
Cultural Differences: Business practices vary by region. Understanding these nuances can facilitate smoother negotiations and partnerships.
Disclaimer on Indicative Prices
It is important to note that prices for gyroscopes can vary widely based on the factors outlined above. This analysis provides a framework for understanding potential costs but does not reflect specific pricing. Always seek detailed quotes from multiple suppliers to ensure the best value for your investment.
Alternatives Analysis: Comparing gyro manufacturer With Other Solutions
Exploring Alternatives to Gyro Manufacturers in B2B Applications
In the dynamic landscape of B2B procurement, international buyers often face the challenge of selecting the most suitable technology for their operational needs. While gyro manufacturers provide essential solutions for various industries, it’s crucial to explore alternative technologies that might offer comparable benefits. This section analyzes two viable alternatives to gyro manufacturers, focusing on performance, cost, ease of implementation, maintenance, and best use cases.
Comparison Table of Gyro Manufacturer and Alternatives
Comparison Aspect | Gyro Manufacturer | MEMS Sensors | Optical Motion Sensors |
---|---|---|---|
Performance | High precision and stability | Moderate precision, cost-effective | High sensitivity and range |
Cost | Generally higher | Lower initial costs | Mid-range costs |
Ease of Implementation | Moderate complexity | Easy integration | Moderate complexity |
Maintenance | Regular calibration needed | Low maintenance | Moderate maintenance |
Best Use Case | Aerospace, robotics | Consumer electronics, automotive | Virtual reality, gaming |
What Are the Advantages and Disadvantages of MEMS Sensors?
MEMS (Micro-Electro-Mechanical Systems) sensors present a compelling alternative to gyro manufacturers, especially for applications requiring compact size and low cost.
Pros:
– MEMS sensors are relatively inexpensive and easy to integrate into various systems, making them an attractive option for budget-conscious projects.
– They offer sufficient performance for many applications, especially in consumer electronics and automotive systems.
Cons:
– While MEMS sensors provide adequate precision, they may not match the high stability and accuracy of traditional gyro systems, particularly in demanding environments.
– They may require calibration in some cases, although this is often less frequent than with gyro systems.
How Do Optical Motion Sensors Compare?
Optical motion sensors utilize light to detect movement and position, offering a different approach to motion sensing.
Pros:
– These sensors are highly sensitive and can provide extensive range and accuracy, making them ideal for applications like virtual reality and gaming where precision is paramount.
– They can be less affected by environmental conditions compared to other technologies.
Cons:
– Optical motion sensors can be more complex to implement than MEMS sensors, requiring careful placement and setup to ensure optimal performance.
– They generally come at a moderate cost, which may be a consideration for budget-sensitive projects.
Making the Right Choice: How Should B2B Buyers Decide Between Gyro Manufacturers and Alternatives?
When evaluating alternatives to gyro manufacturers, B2B buyers should consider their specific operational requirements, budget constraints, and desired performance levels.
- Assess Application Needs: Identify the primary application and performance requirements. High-precision tasks may justify the investment in gyro technology, while less demanding applications could benefit from the cost savings of MEMS sensors.
- Evaluate Total Cost of Ownership: Consider not only initial purchase costs but also long-term maintenance and operational expenses. Lower-cost solutions may lead to higher maintenance costs over time.
- Future Scalability: Ensure that the chosen solution can scale with future business needs. Technologies that offer flexibility and adaptability may provide better long-term value.
By carefully analyzing these factors, international B2B buyers can make informed decisions that align with their strategic objectives and operational needs.
Essential Technical Properties and Trade Terminology for gyro manufacturer
What Are the Essential Technical Properties of Gyro Manufacturing?
When selecting a gyro manufacturer, understanding the technical properties that define the quality and performance of gyroscopic systems is crucial. Here are several key specifications that B2B buyers should consider:
-
Material Grade
– The materials used in gyro manufacturing can significantly impact durability and performance. Common materials include aluminum alloys for lightweight applications and stainless steel for corrosion resistance. For buyers, selecting the right material grade ensures that the gyro will withstand environmental stresses, thus reducing maintenance costs. -
Tolerance
– Tolerance refers to the allowable deviation from specified dimensions in the manufacturing process. High precision in tolerances is essential for gyros, as even minor deviations can lead to inaccuracies in navigation and positioning. Understanding tolerance levels helps buyers assess the manufacturer’s capability to meet their specific operational requirements. -
Weight and Size Specifications
– The weight and size of gyros are critical for applications in aerospace, marine, and automotive sectors, where space and weight constraints are common. Buyers must evaluate whether the manufacturer can produce gyros that fit their design criteria without compromising functionality. -
Power Consumption
– Gyros vary in their power consumption, which can affect overall system efficiency and operational costs. Understanding the power requirements allows buyers to select gyros that align with their energy management strategies, especially in battery-operated systems. -
Temperature Range
– The operational temperature range of a gyro indicates its suitability for various environments. Buyers must ensure that the gyros can function effectively under the temperature conditions relevant to their application, whether in extreme cold, heat, or varying climates.
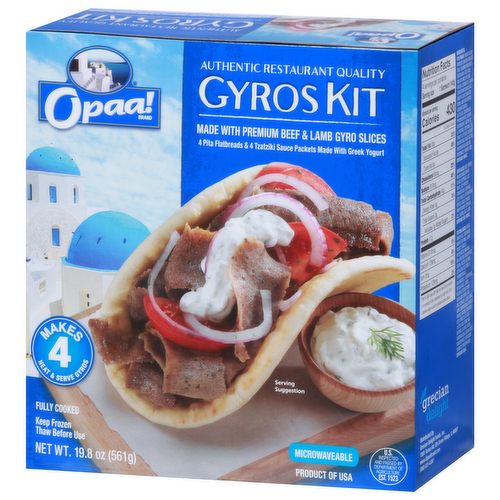
A stock image related to gyro manufacturer.
- Sensitivity and Drift Rate
– Sensitivity refers to the gyro’s ability to detect minute changes in motion, while drift rate indicates how much the gyro’s output changes over time without any movement. These specifications are vital for applications requiring high accuracy, such as in navigation systems. Buyers should inquire about these metrics to ensure optimal performance.
What Are Common Trade Terms Used in Gyro Manufacturing?
Familiarity with industry terminology can facilitate smoother negotiations and better understanding of the procurement process. Here are several essential trade terms:
-
OEM (Original Equipment Manufacturer)
– An OEM is a company that produces parts or equipment that may be marketed by another manufacturer. For buyers, working with OEMs can lead to better quality control and tailored solutions that meet specific needs. -
MOQ (Minimum Order Quantity)
– MOQ refers to the smallest quantity of a product that a supplier is willing to sell. Understanding MOQ is crucial for buyers to manage inventory costs effectively and ensure they meet their purchasing needs without overcommitting resources. -
RFQ (Request for Quotation)
– An RFQ is a document sent to suppliers requesting pricing information for specific products or services. Buyers should use RFQs to obtain competitive pricing and terms, ensuring they make informed purchasing decisions. -
Incoterms (International Commercial Terms)
– These are a set of predefined commercial terms published by the International Chamber of Commerce (ICC) that clarify the responsibilities of buyers and sellers in international trade. Familiarity with Incoterms helps buyers understand shipping costs, risks, and responsibilities, facilitating smoother transactions. -
Lead Time
– Lead time refers to the amount of time it takes from placing an order to receiving the goods. Understanding lead times is vital for buyers to manage project timelines and inventory levels effectively. -
Certification Standards
– Certifications such as ISO, CE, or AS9100 indicate that a manufacturer meets specific quality and safety standards. Buyers should seek manufacturers with relevant certifications to ensure product reliability and compliance with industry regulations.
By grasping these technical properties and trade terms, B2B buyers can make more informed decisions when sourcing gyros, ensuring that they select the right products for their specific applications and operational needs.
Navigating Market Dynamics and Sourcing Trends in the gyro manufacturer Sector
What Are the Key Market Dynamics and Trends in the Gyro Manufacturing Sector?
The gyro manufacturing sector is currently experiencing significant transformations driven by globalization and technological advancements. For international B2B buyers, particularly from Africa, South America, the Middle East, and Europe, understanding these dynamics is crucial for effective sourcing decisions.
A notable trend is the increasing demand for precision-engineered gyroscopes, particularly in aerospace, automotive, and consumer electronics. The rise of autonomous vehicles and drones has further amplified this need, leading to investments in advanced manufacturing techniques such as additive manufacturing and automation. Additionally, there is a growing emphasis on real-time data analytics and IoT integration, enabling manufacturers to enhance product performance and reliability.
Buyers should also be aware of the shifting supply chain dynamics. Geopolitical tensions and trade policies can impact sourcing strategies, making it essential for companies to diversify their supplier base and consider nearshoring options. This approach not only mitigates risks but also promotes stronger relationships with local suppliers, particularly in regions like Africa and South America, where emerging markets present untapped opportunities.
How Is Sustainability Influencing Sourcing Decisions in the Gyro Manufacturing Sector?
Sustainability is becoming a central pillar in the sourcing strategies of B2B buyers in the gyro manufacturing sector. The environmental impact of manufacturing processes is under scrutiny, prompting businesses to adopt more sustainable practices. This includes reducing carbon footprints through energy-efficient production methods and the use of renewable energy sources.
Moreover, ethical sourcing is gaining traction as buyers prioritize suppliers with transparent supply chains. Certifications such as ISO 14001 for environmental management and adherence to international labor standards are increasingly demanded. Buyers are encouraged to seek partnerships with manufacturers that demonstrate a commitment to sustainability, as this can enhance brand reputation and customer loyalty.
The use of eco-friendly materials is also on the rise. Manufacturers are exploring biodegradable or recyclable materials for packaging and components, reducing waste and contributing to a circular economy. By aligning sourcing practices with sustainability goals, B2B buyers not only fulfill regulatory requirements but also position themselves as leaders in corporate responsibility.
What Is the Historical Context of Gyro Manufacturing Relevant to Today’s B2B Buyers?
The evolution of gyro manufacturing dates back to the early 20th century, with the advent of mechanical gyroscopes primarily used in navigation systems. Over the decades, advancements in technology have transformed gyroscopes from simple mechanical devices to sophisticated electronic components. The introduction of microelectromechanical systems (MEMS) in the late 1990s marked a significant shift, allowing for the miniaturization of gyroscopes and expanding their applications.
This historical context is crucial for B2B buyers as it highlights the continuous innovation within the sector. Understanding the technological advancements that have shaped the industry can inform sourcing strategies, particularly when evaluating suppliers’ capabilities and product offerings. As the gyro manufacturing landscape evolves, staying abreast of historical trends can provide valuable insights into future developments and opportunities for collaboration.
Frequently Asked Questions (FAQs) for B2B Buyers of gyro manufacturer
-
How do I identify a reliable gyro manufacturer for my business?
To identify a reliable gyro manufacturer, start by researching potential suppliers online and reading customer reviews. Look for manufacturers with established reputations, certifications, and experience in your specific industry. Request references from other businesses that have sourced from them. Additionally, consider visiting the manufacturing facility if possible to assess their capabilities and quality control processes firsthand. -
What are the key factors to consider when sourcing gyro products internationally?
When sourcing gyro products internationally, consider factors such as product quality, supplier reliability, compliance with international standards, and shipping logistics. Evaluate the manufacturer’s production capacity, lead times, and Minimum Order Quantities (MOQs). Understanding the local market dynamics, tariffs, and customs regulations in both your region and the supplier’s country is also essential to ensure smooth transactions. -
What is the typical Minimum Order Quantity (MOQ) for gyro manufacturers?
Minimum Order Quantities (MOQs) can vary significantly among gyro manufacturers based on the type of product and the supplier’s policies. Typically, MOQs can range from 50 to several thousand units. It is crucial to discuss your specific needs with the manufacturer to negotiate terms that align with your budget and inventory management strategies, especially if you are a smaller business. -
How can I ensure quality assurance when sourcing gyros?
To ensure quality assurance when sourcing gyros, request detailed product specifications and quality control measures from the manufacturer. Implement a quality inspection process, which could include third-party inspections or audits before shipment. Additionally, consider requesting samples before placing a large order to verify the quality of the gyros meets your standards. -
What payment terms should I expect when dealing with gyro manufacturers?
Payment terms can vary widely among gyro manufacturers, but common practices include a deposit upfront (usually 30-50%) with the balance due before shipment. Some suppliers may offer payment upon delivery or extended credit terms for established relationships. Always negotiate favorable terms that protect your cash flow while ensuring the manufacturer has adequate security for the order. -
How do I handle logistics and shipping when sourcing gyros internationally?
Handling logistics and shipping involves coordinating with the manufacturer to determine shipping methods, timelines, and costs. Familiarize yourself with Incoterms (International Commercial Terms) to clarify responsibilities regarding shipping, insurance, and customs duties. Partnering with a reliable freight forwarder can streamline the logistics process and help navigate any potential challenges in customs clearance. -
What customization options are typically available from gyro manufacturers?
Many gyro manufacturers offer customization options, including adjustments in size, specifications, materials, and branding. When discussing your needs with potential suppliers, clearly outline your requirements and inquire about their capabilities for custom manufacturing. Ensure that any modifications align with your intended application and verify that they adhere to industry standards. -
How can I assess the financial stability of a gyro manufacturer?
Assessing the financial stability of a gyro manufacturer involves reviewing their business history, financial reports, and credit ratings. Look for manufacturers with a long-standing presence in the market and a track record of fulfilling orders. You can also request credit references from banks or other suppliers to gauge their financial reliability, ensuring they can sustain operations and deliver on your orders.
Important Disclaimer & Terms of Use
⚠️ Important Disclaimer
The information provided in this guide, including content regarding manufacturers, technical specifications, and market analysis, is for informational and educational purposes only. It does not constitute professional procurement advice, financial advice, or legal advice.
While we have made every effort to ensure the accuracy and timeliness of the information, we are not responsible for any errors, omissions, or outdated information. Market conditions, company details, and technical standards are subject to change.
B2B buyers must conduct their own independent and thorough due diligence before making any purchasing decisions. This includes contacting suppliers directly, verifying certifications, requesting samples, and seeking professional consultation. The risk of relying on any information in this guide is borne solely by the reader.
Strategic Sourcing Conclusion and Outlook for gyro manufacturer
As the global market for gyro manufacturers continues to evolve, strategic sourcing remains a vital component for international B2B buyers. By leveraging a comprehensive sourcing strategy, businesses can not only reduce costs but also enhance product quality and ensure timely delivery. Key takeaways include the importance of establishing strong supplier relationships, utilizing technology for efficient procurement processes, and diversifying supply chains to mitigate risks associated with geopolitical uncertainties.
International buyers from Africa, South America, the Middle East, and Europe should prioritize suppliers who demonstrate a commitment to quality and innovation. This approach not only secures a competitive edge but also fosters sustainability—an increasingly essential factor in global trade.
Looking ahead, the gyro manufacturing sector is poised for growth, driven by advancements in technology and rising demand across various industries. To capitalize on these opportunities, businesses are encouraged to engage in proactive sourcing strategies and explore partnerships that align with their long-term goals. By doing so, they can not only navigate the complexities of the market but also position themselves for success in a dynamic global landscape.