Discover the Best Car Lift Supplier: Your Complete Guide (2025)
Introduction: Navigating the Global Market for car lift supplier
Navigating the global market for car lift suppliers presents unique challenges for international B2B buyers, particularly those from Africa, South America, the Middle East, and Europe. With the increasing demand for efficient vehicle maintenance solutions, sourcing high-quality car lifts that meet specific business needs can be daunting. This guide aims to simplify the process by providing insights into various types of car lifts, their applications across different industries, and essential factors to consider when selecting a supplier.
From understanding the nuances of hydraulic versus electric lifts to evaluating the latest safety standards and compliance requirements, this comprehensive guide equips buyers with the knowledge necessary for informed purchasing decisions. It delves into crucial topics such as supplier vetting processes, cost considerations, and maintenance requirements, ensuring that you can make choices that enhance operational efficiency and profitability.
By leveraging the insights in this guide, B2B buyers can navigate the complexities of the car lift market with confidence. Whether you are a small garage in South America looking to expand your service offerings or a large automotive service provider in Europe aiming to upgrade your equipment, this resource is designed to empower your decision-making process and help you find the right supplier for your specific needs.
Understanding car lift supplier Types and Variations
Type Name | Key Distinguishing Features | Primary B2B Applications | Brief Pros & Cons for Buyers |
---|---|---|---|
Two-Post Lifts | Simple design, low cost, suitable for light vehicles | Small garages, quick maintenance services | Pros: Cost-effective, easy to use. Cons: Limited height and weight capacity. |
Four-Post Lifts | Robust, can accommodate heavier vehicles, often has rolling jacks | Auto repair shops, vehicle storage facilities | Pros: Versatile for multiple vehicle types. Cons: Requires more space. |
Scissor Lifts | Compact design, ideal for tight spaces, vertical lifting | Tire shops, quick service centers | Pros: Space-saving, good for low ceilings. Cons: Limited access underneath vehicle. |
In-Ground Lifts | Permanent installation, high lifting capacity | Large workshops, commercial garages | Pros: Saves space, professional appearance. Cons: Higher installation costs. |
Portable Lifts | Lightweight, easy to transport, can be used in various locations | Mobile mechanics, roadside assistance | Pros: Flexibility and mobility. Cons: Generally lower weight capacity. |
What Are the Characteristics of Two-Post Lifts?
Two-post lifts are among the most commonly used car lifts in small garages and quick maintenance services. They feature a simple and efficient design that allows for easy access to the vehicle’s undercarriage. With a lower cost compared to other types, they are ideal for light vehicles, making them suitable for independent mechanics and small repair shops. However, they have limitations in height and weight capacity, which may restrict their use for larger vehicles.
How Do Four-Post Lifts Benefit B2B Operations?
Four-post lifts are known for their robustness and versatility, capable of handling heavier vehicles such as SUVs and trucks. They are particularly popular in auto repair shops and vehicle storage facilities due to their ability to support multiple vehicles simultaneously. While they offer a greater lifting capacity and stability, buyers should consider the space requirements for installation, as they take up more room than two-post lifts.
Why Choose Scissor Lifts for Limited Spaces?
Scissor lifts are an excellent choice for businesses with limited space or lower ceiling heights. Their compact design allows them to fit into tighter areas while providing vertical lifting capabilities. Ideal for tire shops and quick service centers, they enable easy access to vehicle components. However, the downside is that they offer limited access to the vehicle’s undercarriage, which can be a drawback for comprehensive repairs.
What Are the Advantages of In-Ground Lifts?
In-ground lifts provide a permanent solution for larger workshops and commercial garages. They offer high lifting capacities and a professional appearance, which can enhance the overall image of a business. These lifts save space by being installed below ground level, allowing for better workflow in busy environments. Nonetheless, the initial installation costs can be significant, making them a larger investment for B2B buyers.
How Do Portable Lifts Offer Flexibility?
Portable lifts are designed for mobility and convenience, making them suitable for mobile mechanics and roadside assistance. Their lightweight nature allows for easy transportation and setup in various locations. While they provide flexibility and can be used in different environments, they typically have lower weight capacities compared to fixed lifts, which can limit their application for heavier vehicles.
Related Video: Hydraulic Car Lift | Fully Automated Car Parking Lift | Car Lift | Smart Parking Solution 9445222331
Key Industrial Applications of car lift supplier
Industry/Sector | Specific Application of car lift supplier | Value/Benefit for the Business | Key Sourcing Considerations for this Application |
---|---|---|---|
Automotive Repair & Maintenance | Vehicle servicing and repairs using hydraulic lifts | Increased efficiency and safety in vehicle maintenance | Load capacity, lift height, durability, and service support |
Car Dealerships | Showroom display and vehicle inspections | Enhanced customer experience and streamlined operations | Space requirements, lift design, and ease of use |
Logistics & Warehousing | Loading and unloading vehicles in distribution centers | Improved logistics efficiency and reduced labor costs | Compatibility with various vehicle types and sizes |
Fleet Management | Routine maintenance for commercial vehicle fleets | Extended vehicle lifespan and reduced downtime | Reliability, maintenance needs, and warranty terms |
Car Auctions | Vehicle preparation and inspection before auctions | Faster turnover and better presentation of vehicles | Mobility, ease of setup, and safety features |
How Are Car Lifts Utilized in Automotive Repair & Maintenance?
In the automotive repair and maintenance sector, car lifts are essential tools for performing vehicle servicing and repairs. Hydraulic lifts allow mechanics to elevate vehicles safely, providing easy access to undercarriage components. This application solves the problem of limited access, improving efficiency and safety during maintenance tasks. International B2B buyers must consider load capacity, lift height, and durability when sourcing these lifts to ensure they meet the specific needs of their workshops.
What Role Do Car Lifts Play in Car Dealerships?
Car dealerships use car lifts to facilitate vehicle display and inspections, enhancing the overall customer experience. By elevating vehicles, dealerships can showcase features and allow customers to inspect undercarriage components. This practice not only improves the aesthetic appeal of the showroom but also streamlines operations during vehicle inspections. Buyers should prioritize space requirements, lift design, and ease of use when selecting lifts for dealership environments.
How Are Car Lifts Beneficial in Logistics & Warehousing?
In logistics and warehousing, car lifts are employed for loading and unloading vehicles in distribution centers. This application improves logistics efficiency by reducing the time and labor costs associated with manual handling. Car lifts enable quick access to cargo areas, streamlining the movement of goods. Buyers in this sector should consider compatibility with various vehicle types and sizes to ensure operational efficiency.
Why Are Car Lifts Important for Fleet Management?
Fleet management companies utilize car lifts for routine maintenance of commercial vehicle fleets. Regular use of lifts helps extend the lifespan of vehicles by facilitating timely maintenance checks and repairs. This proactive approach reduces vehicle downtime and enhances operational reliability. When sourcing car lifts, businesses should focus on reliability, maintenance needs, and warranty terms to ensure long-term value.
How Do Car Lifts Enhance Car Auction Processes?
Car lifts play a crucial role in preparing vehicles for auctions by enabling thorough inspections and detailing. Elevating vehicles allows auction houses to present cars in prime condition, speeding up turnover rates and improving sales potential. This application addresses the need for efficient vehicle preparation while enhancing the overall presentation. Buyers should look for lifts that offer mobility, ease of setup, and robust safety features to meet auction demands effectively.
Related Video: How to Install a 9000 LB 2 Post Lift
3 Common User Pain Points for ‘car lift supplier’ & Their Solutions
Scenario 1: Incompatibility with Existing Equipment
The Problem: Many B2B buyers in the automotive industry face significant challenges when sourcing car lifts due to compatibility issues with their existing workshop equipment. For instance, a buyer might invest in a state-of-the-art car lift only to discover that it does not align with their current hydraulic systems or space constraints. This oversight can lead to costly downtimes and additional expenses for retrofitting or replacement equipment, causing frustration and impacting overall productivity.
The Solution: To avoid compatibility issues, it’s crucial for buyers to conduct a thorough assessment of their existing equipment before engaging with a car lift supplier. Begin by documenting the specifications of your current setup, including hydraulic systems, space dimensions, and weight capacities. When discussing options with suppliers, share this information upfront to receive tailored recommendations. Additionally, request detailed product specifications and compatibility charts from suppliers to ensure that the new car lift will integrate seamlessly. Engaging a supplier who offers pre-installation consultations can also help identify potential issues early in the purchasing process.
Scenario 2: Limited After-Sales Support and Maintenance
The Problem: Another common pain point for B2B buyers is the lack of adequate after-sales support and maintenance services from car lift suppliers. After investing a significant amount of capital in car lifts, businesses often find themselves struggling with maintenance issues or needing repairs, only to discover that their supplier provides insufficient support. This can lead to prolonged equipment downtimes, which directly impacts service efficiency and revenue.
The Solution: To mitigate the risk of inadequate after-sales support, buyers should prioritize suppliers known for robust service agreements and customer support. Before finalizing a purchase, inquire about warranty terms, service packages, and the availability of spare parts. Look for suppliers that offer training for your staff on proper usage and maintenance of the equipment. Establishing a clear communication channel with the supplier for ongoing support can also ensure that you have quick access to assistance when needed. Additionally, consider suppliers that have a local presence or offer remote troubleshooting to minimize response times.
Scenario 3: Navigating Regulatory Compliance and Safety Standards
The Problem: International buyers, especially in regions like Africa and the Middle East, often face challenges in ensuring that the car lifts they purchase comply with local regulations and safety standards. This can lead to legal issues, fines, and potential hazards if the equipment fails to meet safety protocols. For example, a buyer may unknowingly invest in a car lift that does not adhere to local electrical or structural safety codes, putting their business at risk.
The Solution: To navigate regulatory compliance effectively, it’s essential for buyers to familiarize themselves with the relevant local regulations and standards pertaining to car lifts. This can be achieved by consulting local industry bodies or regulatory authorities before making a purchase. When engaging with suppliers, ask for certifications and compliance documents that demonstrate adherence to international and local safety standards. It’s also beneficial to seek suppliers with a proven track record in your region, as they are more likely to understand local requirements and provide products that meet these standards. Additionally, consider having a third-party inspection done on the equipment before installation to ensure it meets all safety criteria.
Strategic Material Selection Guide for car lift supplier
What are the Key Materials Used in Car Lifts?
When selecting materials for car lifts, international B2B buyers must consider various factors that influence performance, durability, and compliance with regional standards. Below, we analyze four common materials used in car lift manufacturing: steel, aluminum, composite materials, and high-density polyethylene (HDPE).
How Does Steel Perform as a Material for Car Lifts?
Key Properties: Steel is renowned for its high tensile strength and durability. It can withstand significant loads and is resistant to deformation under pressure. However, its performance can be affected by temperature changes, and it may corrode if not properly treated.
Pros & Cons: Steel’s primary advantage is its strength, making it suitable for heavy-duty applications. It is relatively cost-effective compared to other materials. However, steel is heavier, which can complicate manufacturing and installation. Additionally, it requires protective coatings to prevent rust, especially in humid or corrosive environments.
Impact on Application: Steel is compatible with various hydraulic fluids and can handle high-pressure applications. However, buyers must ensure that the steel used meets specific standards, such as ASTM A36 for structural steel.
Considerations for International Buyers: Buyers from regions like Africa and the Middle East should be aware of local corrosion risks and ensure that the steel is treated accordingly. Compliance with international standards such as ASTM or DIN is crucial, particularly in Europe.
What Are the Benefits of Using Aluminum in Car Lifts?
Key Properties: Aluminum is lightweight yet strong, offering good corrosion resistance. It has a lower tensile strength than steel but compensates with excellent weight-to-strength ratios.
Pros & Cons: The main advantage of aluminum is its lightweight nature, making it easier to handle and install. It is also resistant to corrosion, which is beneficial in humid climates. However, aluminum can be more expensive than steel, and its lower strength limits its use in extremely heavy applications.
Impact on Application: Aluminum is suitable for lighter vehicles and applications where weight reduction is critical. It can be used in hydraulic systems but may require specific considerations regarding fluid compatibility.
Considerations for International Buyers: Buyers in Europe may prefer aluminum due to its recyclability and environmental benefits. Understanding local regulations regarding aluminum sourcing and recycling can provide a competitive edge.
How Do Composite Materials Enhance Car Lift Performance?
Key Properties: Composite materials, often made from a combination of fibers and resins, offer excellent strength-to-weight ratios and are highly resistant to corrosion and environmental degradation.
Pros & Cons: Composites are lightweight and can be molded into complex shapes, allowing for innovative designs. However, they can be more costly and may require specialized manufacturing processes. Their strength can vary significantly based on the composite used.
Impact on Application: Composites are ideal for applications requiring high corrosion resistance and low weight. They may not be suitable for extremely heavy loads unless specifically engineered.
Considerations for International Buyers: Buyers should ensure that composite materials meet relevant standards, such as those set by ASTM or ISO. Understanding the local market’s acceptance of composite materials is essential, especially in regions with traditional preferences for metals.
What Role Does High-Density Polyethylene (HDPE) Play in Car Lift Design?
Key Properties: HDPE is a thermoplastic polymer known for its high impact resistance and low moisture absorption. It is lightweight and offers good chemical resistance.
Pros & Cons: The primary advantage of HDPE is its resistance to chemicals and moisture, making it suitable for various environments. However, it is not as strong as metals and may not be suitable for heavy-duty applications.
Impact on Application: HDPE can be used in non-structural components of car lifts, such as protective covers and guides. Its compatibility with various fluids makes it a versatile choice.
Considerations for International Buyers: Buyers must consider local regulations regarding plastics and their environmental impact. Ensuring compliance with standards such as REACH in Europe can enhance marketability.
Summary Table of Material Selection for Car Lifts
Material | Typical Use Case for Car Lift Supplier | Key Advantage | Key Disadvantage/Limitation | Relative Cost (Low/Med/High) |
---|---|---|---|---|
Steel | Heavy-duty car lifts | High strength and durability | Heavier, requires corrosion protection | Medium |
Aluminum | Lightweight car lifts | Lightweight and corrosion-resistant | More expensive, lower strength | High |
Composite Materials | Innovative designs for car lifts | Excellent strength-to-weight ratio | Higher cost, variable strength | High |
High-Density Polyethylene (HDPE) | Non-structural components | Chemical and moisture resistance | Not suitable for heavy loads | Low |
This guide provides a comprehensive overview of materials used in car lift manufacturing, emphasizing the importance of selecting the right material based on performance, cost, and compliance with international standards.
In-depth Look: Manufacturing Processes and Quality Assurance for car lift supplier
What Are the Main Stages of Manufacturing Processes for Car Lifts?
The manufacturing process of car lifts involves several critical stages, each contributing to the overall quality and reliability of the final product. Understanding these stages can help international B2B buyers make informed decisions when sourcing car lifts from suppliers.
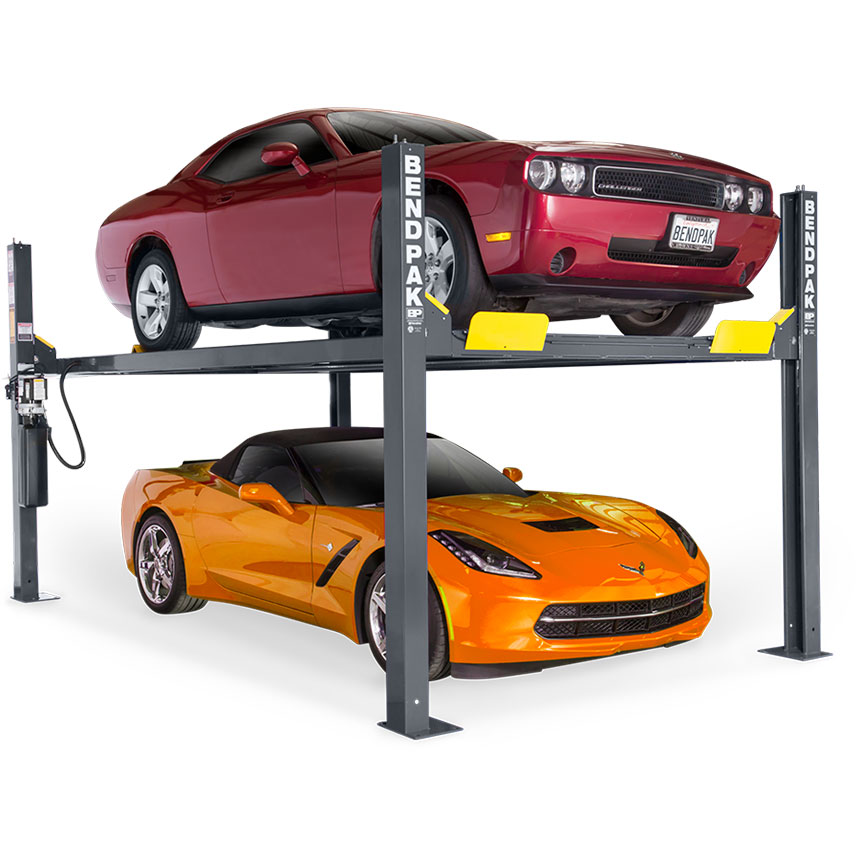
A stock image related to car lift supplier.
-
Material Preparation
The first stage of manufacturing involves selecting high-quality raw materials, typically steel or aluminum. Suppliers often use advanced techniques such as laser cutting and CNC machining to ensure precision in material dimensions. Buyers should verify that the materials used comply with international standards, which can significantly impact the strength and longevity of the lifts. -
Forming
In this stage, the prepared materials are shaped into components using processes like bending, stamping, and welding. Advanced robotics and automated machinery are commonly employed to enhance accuracy and speed. For buyers, it’s crucial to inquire about the technology used in this phase, as it often determines the structural integrity of the car lift. -
Assembly
After forming, the components are assembled into the final product. This process may include the installation of hydraulic systems, electrical wiring, and control systems. Suppliers who employ skilled labor along with automated assembly lines can ensure a high level of consistency. International buyers should seek suppliers that provide comprehensive assembly documentation, which can aid in maintenance and troubleshooting. -
Finishing
The finishing stage includes surface treatments such as powder coating or galvanizing, which protect against corrosion and wear. This stage is vital for durability, particularly in harsh environments common in regions like Africa and the Middle East. Buyers should request samples or specifications of the finishing processes to ensure they meet their environmental conditions.
How Is Quality Assurance Implemented in Car Lift Manufacturing?
Quality assurance (QA) is a pivotal aspect of car lift manufacturing, ensuring that products meet required standards throughout the production process. For B2B buyers, understanding the QA measures in place can enhance confidence in supplier capabilities.
-
International Standards and Certifications
Many car lift manufacturers adhere to international quality management standards such as ISO 9001, which emphasizes a systematic approach to managing quality. Additionally, industry-specific certifications like CE (Conformité Européenne) and API (American Petroleum Institute) may be applicable depending on the lift’s intended use. Buyers should check for these certifications as they signify compliance with safety and quality norms. -
Quality Control Checkpoints
Quality control (QC) in car lift manufacturing involves multiple checkpoints:
– Incoming Quality Control (IQC): This initial check assesses the quality of raw materials before production begins.
– In-Process Quality Control (IPQC): During manufacturing, periodic checks are performed to ensure components are being produced to specifications.
– Final Quality Control (FQC): After assembly, each lift undergoes a comprehensive inspection to verify functionality and safety before shipping. -
Common Testing Methods
Various testing methods are employed to assess the quality and safety of car lifts, including:
– Load Testing: Ensures that the lift can handle its rated capacity without failure.
– Hydraulic Testing: Verifies that hydraulic systems are leak-free and function correctly.
– Electrical Testing: Confirms that all electrical components meet safety standards and perform as intended.
How Can B2B Buyers Verify Supplier Quality Control?
For international B2B buyers, particularly those from Africa, South America, the Middle East, and Europe, verifying a supplier’s quality control processes is essential to mitigating risk and ensuring product reliability.
-
Conducting Supplier Audits
Regular audits of potential suppliers can provide insights into their manufacturing processes and quality control measures. Buyers should establish a checklist based on international standards and their specific requirements to evaluate the supplier’s capabilities effectively. -
Requesting Quality Control Reports
Suppliers should be able to provide detailed QC reports that document their testing processes, results, and any corrective actions taken. These documents can serve as a benchmark for quality assurance practices. -
Engaging Third-Party Inspection Services
Utilizing third-party inspection services can add an additional layer of assurance. These services can conduct unbiased assessments of the manufacturing process and final products, ensuring they meet the buyer’s standards and expectations.
What Are the Quality Control Nuances for International Buyers?
International B2B buyers face unique challenges when sourcing car lifts due to varying standards and regulations across regions. Understanding these nuances can help streamline the procurement process.
-
Regional Compliance Standards
Different regions may have distinct compliance standards that suppliers must meet. For instance, European buyers often prioritize CE certification, while buyers in the Middle East may focus on local safety regulations. It’s vital for buyers to communicate their specific compliance needs to suppliers upfront. -
Cultural and Communication Barriers
Cultural differences can affect how quality control processes are perceived and implemented. Buyers should be proactive in establishing clear communication channels with suppliers, ensuring that quality expectations are understood and met. -
Logistics and Transportation Considerations
The transportation of car lifts can introduce additional quality risks, such as damage during shipping. Buyers should discuss packaging and handling practices with suppliers to mitigate these risks and ensure the product arrives in optimal condition.
Conclusion
Understanding the manufacturing processes and quality assurance measures for car lifts is crucial for international B2B buyers. By focusing on material preparation, forming, assembly, and finishing, along with robust quality control practices, buyers can make informed decisions when selecting suppliers. Additionally, leveraging audits, quality reports, and third-party inspections will further ensure that the car lifts meet the necessary safety and quality standards, ultimately leading to successful partnerships and satisfied customers.
Practical Sourcing Guide: A Step-by-Step Checklist for ‘car lift supplier’
In the competitive landscape of automotive service equipment, sourcing a reliable car lift supplier is crucial for your business’s efficiency and safety. This guide provides a practical checklist to help international B2B buyers navigate the procurement process effectively, ensuring that you choose a supplier that meets your technical and business needs.
Step 1: Define Your Technical Specifications
Before reaching out to suppliers, clearly outline the technical requirements for the car lifts you need. Consider factors such as load capacity, lift height, and operational features (e.g., hydraulic vs. electric). Defining these specifications helps narrow down your options and ensures that you invest in equipment that aligns with your operational needs.
Step 2: Conduct Market Research
Investigate potential suppliers by gathering information about their market presence and product offerings. Utilize online platforms, industry reports, and trade shows to identify key players in the car lift manufacturing sector. Pay attention to reviews and testimonials from other businesses in your region, as they can provide valuable insights into supplier reliability and product performance.
Step 3: Verify Supplier Certifications
Ensure that potential suppliers hold necessary certifications and comply with international safety and quality standards, such as ISO 9001. Certifications demonstrate a commitment to quality and can reduce the risk of purchasing substandard equipment. Additionally, check if the supplier has any relevant local certifications, especially if you are sourcing from regions with specific regulatory requirements.
Step 4: Evaluate Supplier Experience
Assess the supplier’s experience in the industry by reviewing their track record and years of operation. A supplier with extensive experience is more likely to understand the unique challenges of different markets, such as those in Africa, South America, the Middle East, and Europe. Ask for case studies or examples of previous projects that highlight their expertise.
Step 5: Request Product Samples or Demonstrations
Before making a purchase, request product samples or live demonstrations of the car lifts. This step allows you to evaluate the equipment’s functionality, durability, and ease of use firsthand. Pay attention to features that enhance safety and efficiency, as these can significantly impact your operations.
Step 6: Inquire About After-Sales Support
A reliable supplier should offer comprehensive after-sales support, including installation, maintenance, and troubleshooting assistance. Inquire about the availability of spare parts and the response time for service requests. Good after-sales support ensures that your operations remain uninterrupted and helps build a long-term relationship with the supplier.
Step 7: Negotiate Terms and Pricing
Once you have shortlisted potential suppliers, engage in discussions about pricing, payment terms, and delivery schedules. Be clear about your budget and seek transparency in pricing to avoid hidden costs. Negotiating favorable terms can lead to significant savings and a more favorable long-term partnership.
Following this checklist will empower you to make informed decisions when sourcing car lift suppliers, ultimately contributing to your business’s operational success and growth.
Comprehensive Cost and Pricing Analysis for car lift supplier Sourcing
What Are the Key Cost Components in Car Lift Supplier Sourcing?
When sourcing car lifts, understanding the cost structure is essential for international B2B buyers. The primary cost components include:
-
Materials: The choice of materials significantly impacts the cost. For example, higher-grade steel or aluminum will increase the material costs but may enhance durability and performance.
-
Labor: Labor costs vary depending on the region and the complexity of the manufacturing process. Skilled labor may demand higher wages, influencing overall pricing.
-
Manufacturing Overhead: This includes expenses related to factory operations, such as utilities, rent, and salaries of non-production staff. Efficient overhead management can lead to more competitive pricing.
-
Tooling: Custom tooling for specialized car lifts can add to upfront costs. Understanding whether the supplier has existing tooling for your specifications can help manage expenses.
-
Quality Control (QC): Implementing stringent quality control measures ensures product reliability but may also add to the overall cost. Buyers should weigh the benefits of robust QC against their budget constraints.
-
Logistics: Shipping costs, including freight, insurance, and handling, can vary widely based on distance and shipping method. Incoterms will dictate who bears these costs, impacting total expenses.
-
Margin: Suppliers will typically include a profit margin in their pricing. Understanding the market standards for these margins can help in negotiating better deals.
How Do Price Influencers Affect Car Lift Pricing?
Several factors influence the pricing of car lifts, particularly for international buyers:
-
Volume and Minimum Order Quantity (MOQ): Larger orders often lead to lower per-unit costs. Understanding the supplier’s MOQ can help in planning purchases effectively.
-
Specifications and Customization: Customized car lifts tailored to specific needs can significantly increase costs. Buyers should clearly define their requirements to avoid unexpected expenses.
-
Material Quality and Certifications: Lifts that meet international safety standards or certifications (like CE in Europe) might command higher prices but provide peace of mind regarding safety and compliance.
-
Supplier Factors: The reputation, reliability, and location of the supplier can influence pricing. Suppliers with established track records may charge more due to perceived quality and service reliability.
-
Incoterms: The choice of Incoterms affects the total landed cost. Understanding terms like FOB (Free on Board) or CIF (Cost, Insurance, and Freight) is crucial to avoid hidden costs.
What Are the Best Buyer Tips for Sourcing Car Lifts?
To maximize cost-efficiency and ensure a successful procurement process, consider the following tips:
-
Negotiation Strategies: Always approach negotiations with a clear understanding of market prices and competitor offerings. Leverage volume commitments to negotiate better terms.
-
Total Cost of Ownership (TCO): Assess the TCO, which includes initial purchase price, maintenance, operational costs, and potential resale value. A cheaper upfront cost may lead to higher long-term expenses if quality is compromised.
-
Pricing Nuances for International Buyers: Be aware of currency fluctuations and potential tariffs that can affect pricing. Establishing contracts in stable currencies can mitigate risks.
-
Research and References: Always conduct thorough research on potential suppliers, including checking references and customer reviews. This due diligence can prevent costly mistakes and ensure you are sourcing from reputable suppliers.
Conclusion
Understanding the cost structure and pricing influencers in sourcing car lifts is crucial for international B2B buyers. By considering the various components, negotiating effectively, and focusing on total cost of ownership, businesses can make informed decisions that align with their operational needs and budget constraints. Remember that prices can fluctuate based on market conditions, so always seek indicative pricing and be prepared for adjustments.
Alternatives Analysis: Comparing car lift supplier With Other Solutions
When evaluating solutions for vehicle maintenance and servicing, businesses often consider various alternatives to traditional car lifts. Each option comes with its own set of advantages and disadvantages, making it essential for international B2B buyers to understand their choices. This section compares the conventional car lift supplier against two notable alternatives: portable car ramps and hydraulic jacks.
Comparison Aspect | Car Lift Supplier | Portable Car Ramps | Hydraulic Jacks |
---|---|---|---|
Performance | High stability and weight capacity | Limited to lighter vehicles | Good for quick lifts but not stable |
Cost | Higher initial investment | Low-cost option | Moderate cost, varies by model |
Ease of Implementation | Requires installation and space | Easy to use and store | Requires minimal setup |
Maintenance | Regular service needed | Low maintenance | Requires occasional checks |
Best Use Case | Professional garages and workshops | Home mechanics and light-duty tasks | Emergency situations or low-volume shops |
What are the Advantages and Disadvantages of Using Portable Car Ramps?
Portable car ramps offer a lightweight and affordable solution for lifting vehicles. They are particularly advantageous for home mechanics who may not require a permanent installation. The ease of use and storage makes them appealing, especially for small garages or personal use. However, their performance is limited to lighter vehicles, and they lack the stability and height adjustments that a car lift can provide. This can pose safety risks if used improperly.
How Do Hydraulic Jacks Compare to Car Lift Suppliers?
Hydraulic jacks are another alternative that provides a flexible lifting solution, especially in emergency situations. They are generally more affordable than car lifts and easy to transport, making them suitable for mobile mechanics. However, hydraulic jacks require careful handling and do not offer the same stability as a car lift. Their lifting capacity is usually lower, and they are not ideal for extensive vehicle servicing, where more stable solutions are necessary.
How Can B2B Buyers Choose the Right Vehicle Lifting Solution?
When selecting the right vehicle lifting solution, B2B buyers should assess their specific needs, including the types of vehicles serviced, frequency of use, and available space. For businesses that require heavy-duty lifting and frequent vehicle servicing, investing in a car lift supplier may be justified despite the higher initial cost. Alternatively, if the primary need is for occasional use or lighter vehicles, portable ramps or hydraulic jacks may offer a more cost-effective and flexible solution.
In summary, understanding the strengths and limitations of each alternative allows international buyers to make informed decisions that align with their operational needs and budget constraints. Evaluating performance, cost, ease of implementation, maintenance, and the best use case will guide buyers toward the most suitable solution for their vehicle maintenance requirements.
Essential Technical Properties and Trade Terminology for car lift supplier
What Are the Essential Technical Properties of Car Lifts?
When purchasing car lifts, international B2B buyers should be aware of several critical specifications that directly impact performance, safety, and reliability. Here are some essential technical properties to consider:
1. Load Capacity
Load capacity refers to the maximum weight a car lift can safely handle. Typical capacities range from 3,000 to 30,000 pounds. Understanding load capacity is vital for ensuring that the lift can accommodate the vehicles in your service operation, especially when dealing with heavy-duty trucks or specialized vehicles.
2. Material Grade
Material grade indicates the quality and strength of the materials used in the construction of the car lift. Common materials include high-strength steel and aluminum alloys. Opting for higher-grade materials enhances durability and longevity, which can lead to lower maintenance costs over time.
3. Lifting Height
Lifting height is the maximum vertical distance a lift can raise a vehicle. This specification is crucial for mechanics and technicians who need sufficient space to work underneath vehicles. A typical range is between 50 inches to 72 inches, but higher models are available for specific applications.
4. Tolerance
Tolerance refers to the allowable deviation from a specified value in the lift’s construction and operation. For example, the precision in how a lift aligns with the vehicle’s chassis is critical for safety and performance. Tighter tolerances generally result in better performance and less wear over time.
5. Power Source
Car lifts can be powered by hydraulic systems, electric motors, or pneumatic systems. Understanding the power source is essential for compatibility with your workshop’s infrastructure and for evaluating energy efficiency. Hydraulic lifts, for instance, are known for their robustness and smooth operation.
6. Safety Features
Safety features include automatic locking systems, emergency stop buttons, and overload protection. These elements are non-negotiable when considering the safety of your workforce and the vehicles being serviced. Investing in lifts with advanced safety features can minimize risks and ensure compliance with industry regulations.
What Are Common Trade Terms Used in the Car Lift Industry?
Familiarizing yourself with industry jargon is crucial for effective communication with suppliers and understanding the procurement process. Here are some commonly used terms in the car lift supply sector:
1. OEM (Original Equipment Manufacturer)
An OEM refers to a company that produces parts and equipment that may be marketed by another manufacturer. When sourcing car lifts, knowing whether a supplier is an OEM can affect quality assurance and warranty considerations.
2. MOQ (Minimum Order Quantity)
MOQ represents the smallest number of units a supplier is willing to sell. Understanding the MOQ helps buyers plan their inventory and manage cash flow effectively. For smaller businesses, negotiating lower MOQs can be beneficial.
3. RFQ (Request for Quotation)
An RFQ is a formal process in which buyers request price quotes from suppliers. This step is essential for comparing costs and negotiating terms. A well-structured RFQ can lead to better pricing and improved supplier relationships.
4. Incoterms (International Commercial Terms)
Incoterms are standardized trade terms that define the responsibilities of buyers and sellers in international transactions. Familiarity with Incoterms helps in understanding shipping costs, risk allocation, and delivery responsibilities.
5. Lead Time
Lead time is the duration from placing an order to the delivery of the product. It is crucial for planning and inventory management. Knowing the lead time can help businesses schedule operations and meet customer demands effectively.
6. Warranty Period
The warranty period is the time frame during which the supplier guarantees the product against defects. Understanding warranty terms is vital for assessing long-term costs and ensuring that you are covered for potential repairs or replacements.
By understanding these technical specifications and trade terminologies, international B2B buyers can make informed decisions when sourcing car lifts, ultimately enhancing operational efficiency and safety in their businesses.
Navigating Market Dynamics and Sourcing Trends in the car lift supplier Sector
What Are the Current Market Dynamics and Key Trends in the Car Lift Supplier Sector?
The car lift supplier sector is experiencing significant growth driven by several global factors. Increased vehicle ownership, particularly in emerging markets in Africa and South America, is creating a heightened demand for efficient and reliable car lifting solutions. Additionally, the rise in e-commerce and online vehicle sales is propelling the need for automotive services, including maintenance and repair, thereby boosting the demand for car lifts.
Emerging B2B technologies are reshaping the sourcing landscape. Advanced manufacturing processes, such as 3D printing, allow suppliers to create customized lifting solutions tailored to specific regional demands. Moreover, the integration of IoT (Internet of Things) technology in car lifts is enabling predictive maintenance, reducing downtime, and enhancing operational efficiency. For international buyers, particularly in Europe and the Middle East, this technological advancement presents opportunities to source more intelligent, user-friendly products.
Market dynamics are also influenced by regulatory changes and safety standards. In regions like Europe, stringent regulations regarding vehicle safety and maintenance are pushing buyers to invest in high-quality, compliant car lifting equipment. For B2B buyers, understanding these market trends is crucial for making informed sourcing decisions that align with their operational needs and regional compliance requirements.
How Is Sustainability and Ethical Sourcing Impacting the Car Lift Supplier Sector?
Sustainability is becoming a central concern for international B2B buyers in the car lift sector. The environmental impact of manufacturing and disposing of car lifts is prompting companies to prioritize sustainable practices. Buyers are increasingly looking for suppliers that demonstrate commitment to reducing carbon footprints through energy-efficient production processes and the use of recyclable materials.
Ethical sourcing is also gaining traction, with a focus on supply chain transparency. Buyers are urged to engage with suppliers who adhere to fair labor practices and environmental regulations. Certifications such as ISO 14001 (Environmental Management) and LEED (Leadership in Energy and Environmental Design) are indicators of a supplier’s commitment to sustainability. By prioritizing suppliers with these certifications, B2B buyers can not only ensure compliance but also enhance their corporate social responsibility profiles.
Furthermore, the trend towards green materials in manufacturing car lifts is becoming prevalent. Suppliers are exploring alternatives to traditional steel and plastics, such as aluminum and composite materials, which offer lower environmental impacts. For buyers, sourcing from suppliers who embrace these innovations can lead to cost savings and improved market positioning.
What Is the Brief Evolution of the Car Lift Supplier Sector?
The car lift supplier sector has evolved significantly over the past few decades, transitioning from basic hydraulic lifts to advanced, technology-driven solutions. Initially, car lifts were primarily mechanical and hydraulic systems designed for simple vehicle maintenance tasks. However, with advancements in technology, the introduction of electric and portable lifts has revolutionized the market.
In the 2000s, the integration of electronics and automation into car lifts allowed for greater precision and efficiency, catering to the increasing complexity of modern vehicles. Today, the focus has shifted to smart lifts equipped with IoT capabilities, enabling predictive maintenance and real-time monitoring. This evolution reflects the broader trends in the automotive industry, where technology and sustainability are at the forefront of innovation. For international B2B buyers, understanding this evolution can aid in identifying suppliers that align with future trends and technological advancements.
Frequently Asked Questions (FAQs) for B2B Buyers of car lift supplier
-
How do I choose the right car lift supplier for my business?
When selecting a car lift supplier, evaluate their industry experience, product range, and customer reviews. Request samples or demonstrations to assess quality. It’s also vital to check if they comply with international safety standards and regulations, as this ensures reliability and durability. Lastly, consider their communication responsiveness and after-sales support, which are crucial for a long-term partnership. -
What are the key features to look for in a car lift?
Important features to consider include lifting capacity, safety mechanisms (like automatic locks), ease of use, and warranty terms. Hydraulic vs. electric lifts should be compared based on your workshop’s needs. Additionally, consider the lift’s footprint and whether it can accommodate various vehicle sizes, especially if you’re dealing with diverse automotive models. -
What customization options are typically available from car lift suppliers?
Many car lift suppliers offer customization options such as height adjustments, color choices, and additional safety features. You may also request specific configurations based on the types of vehicles you service. Ensure the supplier has experience with custom requests and can deliver within your timeline without compromising on quality. -
What is the minimum order quantity (MOQ) for car lifts?
MOQs can vary widely among suppliers, often ranging from one unit for smaller suppliers to larger quantities for major manufacturers. It’s advisable to discuss your specific needs with potential suppliers to negotiate favorable terms, especially if you are a new business or looking to test the market with a smaller initial investment. -
What payment terms should I expect when sourcing car lifts internationally?
Payment terms can differ significantly based on the supplier’s policies and the buyer’s location. Common terms include a deposit upfront (usually 30% to 50%), with the balance paid before shipping or upon delivery. Ensure you clarify any additional costs such as shipping, customs duties, and taxes to avoid surprises. -
How can I ensure the quality of car lifts from international suppliers?
Conduct thorough due diligence by requesting product certifications and quality assurance documentation. It’s beneficial to visit the supplier’s manufacturing facility if possible, or to engage third-party inspection services. Additionally, consider sourcing samples or trial units to assess quality before committing to larger orders. -
What logistics considerations should I keep in mind when importing car lifts?
Logistics play a critical role in importing car lifts, including shipping methods, lead times, and customs clearance. Choose a freight forwarder experienced in heavy equipment to navigate these complexities. Additionally, ensure all necessary import documentation is prepared to facilitate smooth customs procedures. -
How do I handle after-sales service and support with my car lift supplier?
Establish clear communication channels for after-sales service before finalizing your order. Inquire about warranty conditions, parts availability, and response times for service requests. A reliable supplier will provide comprehensive support, including installation guidance and troubleshooting assistance, ensuring your operations run smoothly.
Important Disclaimer & Terms of Use
⚠️ Important Disclaimer
The information provided in this guide, including content regarding manufacturers, technical specifications, and market analysis, is for informational and educational purposes only. It does not constitute professional procurement advice, financial advice, or legal advice.
While we have made every effort to ensure the accuracy and timeliness of the information, we are not responsible for any errors, omissions, or outdated information. Market conditions, company details, and technical standards are subject to change.
B2B buyers must conduct their own independent and thorough due diligence before making any purchasing decisions. This includes contacting suppliers directly, verifying certifications, requesting samples, and seeking professional consultation. The risk of relying on any information in this guide is borne solely by the reader.
Strategic Sourcing Conclusion and Outlook for car lift supplier
In conclusion, strategic sourcing is crucial for international B2B buyers in the car lift industry, particularly those from Africa, South America, the Middle East, and Europe. By leveraging a global supplier network, companies can not only optimize costs but also enhance quality and innovation in their product offerings. Key takeaways include the importance of thorough market research to identify reputable suppliers, the necessity of evaluating total cost of ownership rather than just initial pricing, and the value of establishing long-term relationships to ensure reliable supply chains.
As the automotive industry continues to evolve, staying ahead of trends such as electric vehicle support and automation in service stations will be essential. International buyers should actively seek partnerships with suppliers who demonstrate a commitment to sustainability and technological advancement.
Looking ahead, the potential for growth in the car lift market remains robust, driven by increasing demand for efficient automotive service solutions. Now is the time for B2B buyers to take action: assess your sourcing strategies, engage with innovative suppliers, and position your business for future success in this dynamic market.