Discover Top Handle Grip Manufacturers: Your Sourcing Guide (2025)
Introduction: Navigating the Global Market for handle grip manufacturer
In today’s competitive landscape, international B2B buyers face the pressing challenge of sourcing high-quality handle grips that meet diverse application needs—from industrial machinery to consumer products. As a handle grip manufacturer, understanding the complexities of sourcing and procurement is crucial. This guide offers a comprehensive overview of the handle grip market, detailing various types, applications, and essential factors to consider when selecting suppliers. From evaluating material durability to understanding ergonomic design, we aim to equip buyers with the knowledge they need to make informed purchasing decisions.
Whether you are based in Africa, South America, the Middle East, or Europe, this guide addresses the unique challenges each region faces in the global marketplace. We explore critical aspects such as supplier vetting processes, cost considerations, and trends impacting the handle grip industry. By providing actionable insights and best practices, we empower B2B buyers to navigate the complexities of sourcing effectively.
With an authoritative and solution-oriented approach, this guide serves as a valuable resource for businesses looking to enhance their product offerings and ensure quality in their supply chains. As you delve into the sections that follow, expect to gain a deeper understanding of how to strategically approach your handle grip sourcing needs, ultimately leading to improved product performance and customer satisfaction.
Understanding handle grip manufacturer Types and Variations
Type Name | Key Distinguishing Features | Primary B2B Applications | Brief Pros & Cons for Buyers |
---|---|---|---|
Rubber Handle Grips | Made from durable, slip-resistant rubber; often ergonomically designed. | Hand tools, sporting equipment, machinery. | Pros: Excellent grip, shock absorption. Cons: May wear out faster in extreme conditions. |
Plastic Handle Grips | Lightweight, cost-effective, and available in various colors and designs. | Household tools, kitchen appliances. | Pros: Affordable, customizable. Cons: Less durable than rubber or metal options. |
Metal Handle Grips | High strength and longevity; often used in heavy-duty applications. | Industrial machinery, automotive tools. | Pros: Extremely durable, resistant to wear. Cons: Heavier, may be more expensive. |
Foam Handle Grips | Soft, cushioned surface for comfort; often used in consumer products. | Fitness equipment, kitchen utensils. | Pros: Comfortable to use, lightweight. Cons: Can degrade over time with moisture. |
Composite Handle Grips | Combination of materials for enhanced performance; often lightweight yet strong. | Aerospace, high-performance tools. | Pros: Balanced properties, innovative designs. Cons: Higher cost, may require specialized manufacturing. |
What Are Rubber Handle Grips and Their B2B Suitability?
Rubber handle grips are widely recognized for their slip-resistant properties and ergonomic designs. These grips provide excellent shock absorption, making them suitable for hand tools, sporting equipment, and machinery. B2B buyers should consider the durability of rubber grips, especially in environments with high wear and tear. While they offer superior grip and comfort, potential buyers should be aware of their lifespan in extreme conditions, which may necessitate more frequent replacements.
How Do Plastic Handle Grips Compare in the Market?
Plastic handle grips are known for their lightweight nature and cost-effectiveness, appealing to budget-conscious buyers. They are available in various colors and designs, allowing for customization in household tools and kitchen appliances. While they are affordable and versatile, buyers must weigh their lower durability compared to rubber or metal grips. For companies looking for a balance between cost and functionality, plastic grips can be a suitable choice.
What Advantages Do Metal Handle Grips Offer for Heavy-Duty Use?
Metal handle grips are ideal for heavy-duty applications due to their high strength and longevity. They are commonly used in industrial machinery and automotive tools, where durability is paramount. Buyers should appreciate the resistance of metal grips to wear and tear, making them a long-term investment. However, the added weight and potentially higher cost may deter some buyers who prioritize lightweight solutions.
Why Choose Foam Handle Grips for Comfort?
Foam handle grips are designed for comfort, featuring a soft, cushioned surface that makes them popular in fitness equipment and kitchen utensils. These grips are lightweight and provide a pleasant tactile experience for users. However, B2B buyers should consider the potential degradation of foam grips over time, especially in humid conditions. Companies prioritizing user comfort in their products may find foam grips an attractive option.
What Are the Benefits of Composite Handle Grips?
Composite handle grips utilize a combination of materials to achieve enhanced performance characteristics. They are often lightweight yet strong, making them suitable for high-performance applications in aerospace and specialized tools. While these grips can offer balanced properties and innovative designs, buyers should be prepared for higher costs and the possibility of requiring specialized manufacturing processes. For businesses focused on advanced technology and performance, composite grips are a compelling choice.
Related Video: Variations In Construction Projects Explained
Key Industrial Applications of handle grip manufacturer
Industry/Sector | Specific Application of handle grip manufacturer | Value/Benefit for the Business | Key Sourcing Considerations for this Application |
---|---|---|---|
Automotive | Steering wheel grips | Enhanced driver comfort and control | Material durability and ergonomic design |
Consumer Electronics | Handheld device grips | Improved user experience and functionality | Customization options and grip texture |
Industrial Equipment | Machinery handles | Increased safety and operational efficiency | Compliance with safety standards and load ratings |
Healthcare | Medical equipment grips | Better handling and hygiene for users | Antimicrobial materials and easy-to-clean designs |
Sports and Recreation | Sports equipment grips | Enhanced performance and user comfort | Weight considerations and material flexibility |
How Are Handle Grip Manufacturers Used in the Automotive Industry?
In the automotive sector, handle grip manufacturers produce steering wheel grips that significantly enhance driver comfort and control. These grips are designed to reduce slippage and improve the tactile feedback of the steering wheel, which is crucial for safe driving. For international buyers, especially in regions like Africa and South America, sourcing grips that comply with local safety regulations and climate conditions is essential. Additionally, buyers should consider the durability of materials used, as they must withstand varying temperatures and wear over time.
What Are the Applications of Handle Grips in Consumer Electronics?
Handle grips in consumer electronics, particularly for handheld devices, enhance user experience by providing better grip and control. These grips can be customized for various devices, ensuring that users can operate gadgets comfortably during prolonged use. For B2B buyers in Europe and the Middle East, sourcing grips that allow for personalization—such as color and texture—can be a deciding factor in product differentiation. It is important to ensure that the materials used are lightweight yet durable, as this can impact the overall usability of the device.
How Do Handle Grips Contribute to Industrial Equipment Safety?
In industrial settings, handle grips for machinery are critical for ensuring operator safety and efficiency. These grips are designed to provide a secure hold, reducing the risk of accidents caused by slipping or loss of control during operation. Buyers, particularly from regions with stringent safety regulations, must prioritize sourcing grips that meet industry standards for load ratings and material resilience. Additionally, considering ergonomic designs can help in minimizing worker fatigue, thereby improving productivity.
What Role Do Handle Grips Play in Healthcare Equipment?
In the healthcare industry, handle grip manufacturers supply grips for medical equipment that enhance handling and hygiene. Grips that are designed with antimicrobial materials help in maintaining hygiene standards, which is paramount in healthcare settings. For international buyers, especially in regions with diverse healthcare regulations, it is crucial to source grips that comply with local health standards. Furthermore, ease of cleaning and maintenance is a significant consideration, as it directly impacts the safety and usability of medical devices.
How Are Handle Grips Utilized in Sports and Recreation?
In the sports and recreation sector, handle grips are essential for enhancing performance and user comfort in various equipment such as tennis rackets and golf clubs. These grips provide better control and reduce the risk of injury during use. B2B buyers should consider sourcing grips that are lightweight yet provide adequate cushioning and support. Additionally, understanding the specific performance needs of athletes in different regions can help in selecting the right materials and designs that cater to local preferences and conditions.
3 Common User Pain Points for ‘handle grip manufacturer’ & Their Solutions
Scenario 1: Difficulty in Sourcing High-Quality Handle Grips
The Problem: One of the primary challenges faced by B2B buyers in Africa and South America is the inconsistent quality of handle grips from various manufacturers. Buyers often struggle with suppliers who fail to meet quality standards, leading to product recalls, increased costs, and a tarnished brand reputation. This situation becomes particularly dire when manufacturers do not adhere to international quality certifications, which are crucial for ensuring safety and durability.
The Solution: To navigate this challenge, buyers should prioritize sourcing from manufacturers who have verifiable quality control processes in place. Conduct thorough research on potential suppliers, focusing on their certifications (such as ISO 9001) and customer reviews. Consider initiating a pilot order to evaluate the quality of the handle grips before committing to larger quantities. Establish clear specifications and quality benchmarks in your contracts to ensure that the manufacturer understands your expectations. Regular communication and scheduled quality inspections during the production process can further mitigate risks associated with poor quality.
Scenario 2: Complex Customization Requirements
The Problem: Many buyers, especially in Europe and the Middle East, require customized handle grips that align with specific product designs and ergonomics. This need for customization often leads to complications in the manufacturing process, resulting in delays and increased costs. Furthermore, lack of communication about design expectations can lead to products that do not meet the intended specifications.
The Solution: To effectively manage customization needs, establish a detailed design brief that outlines all specifications, including materials, dimensions, and intended use cases. Collaborate closely with the handle grip manufacturer during the design phase to ensure that all elements are achievable within their production capabilities. Utilize 3D modeling or prototypes to visualize the end product and make necessary adjustments before mass production. Regular check-ins and updates during the manufacturing process can help ensure that the product remains on track and meets the desired customization requirements.
Scenario 3: Navigating Import Regulations and Duties
The Problem: B2B buyers across Africa and South America frequently encounter complex import regulations and duties that can significantly affect the overall cost and timing of acquiring handle grips. These challenges can lead to unexpected delays in delivery and increased operational costs, complicating inventory management and production schedules.
The Solution: To mitigate issues related to import regulations, buyers should conduct thorough research on the specific import policies of their countries. Engage with logistics providers who have expertise in international shipping and can offer insights into customs regulations, tariffs, and documentation requirements. Consider working with manufacturers who can assist with export compliance and provide necessary documentation for smooth customs clearance. Additionally, developing a strong relationship with a customs broker can facilitate faster processing and help navigate potential hurdles. By planning ahead and ensuring compliance with regulations, buyers can avoid costly delays and maintain a steady flow of inventory.
Strategic Material Selection Guide for handle grip manufacturer
When selecting materials for handle grips, manufacturers must consider various factors that affect performance, durability, and compliance with international standards. Below is an analysis of four common materials used in handle grip manufacturing, focusing on their properties, advantages, disadvantages, and implications for international B2B buyers.
What Are the Key Properties of Rubber for Handle Grips?
Rubber is a popular choice for handle grips due to its excellent flexibility and grip. It typically offers a temperature rating of -40°C to 100°C and is resistant to abrasion and certain chemicals. The inherent elasticity of rubber allows it to absorb shock and provide a comfortable grip.
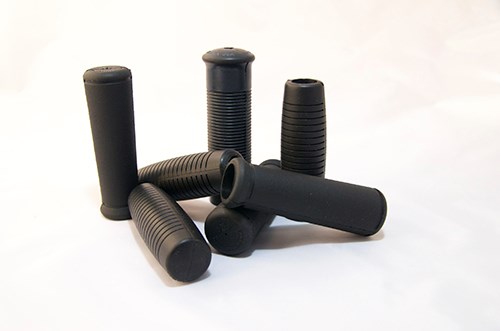
A stock image related to handle grip manufacturer.
Pros & Cons:
Rubber grips are durable and provide a non-slip surface, making them suitable for various applications, including tools and sporting equipment. However, they can degrade over time when exposed to UV light and extreme temperatures, leading to a shorter lifespan compared to other materials. Additionally, the manufacturing process can be complex, impacting production costs.
Impact on Application:
Rubber grips are ideal for applications requiring a firm hold, especially in wet or oily conditions. However, they may not be suitable for high-temperature environments where degradation could occur.
Considerations for International Buyers:
Buyers from regions like Africa and South America should ensure compliance with local standards for rubber products, such as ASTM D2000 or ISO 37, to guarantee quality and safety.
How Does Plastic Compare as a Material for Handle Grips?
Plastic, particularly thermoplastics like polypropylene and polycarbonate, is widely used for handle grips due to its versatility and cost-effectiveness. These materials can withstand temperatures ranging from -20°C to 80°C, depending on the specific type of plastic.
Pros & Cons:
Plastic grips are lightweight, resistant to moisture, and can be produced in various colors and textures, enhancing aesthetic appeal. However, they may not offer the same level of grip as rubber and can become brittle over time, especially when exposed to UV light.
Impact on Application:
Plastic grips are suitable for a wide range of applications, including consumer goods and industrial tools. However, they may not perform well in high-stress environments where durability is a concern.
Considerations for International Buyers:
Buyers in Europe, particularly Germany, should be aware of compliance with EU regulations regarding plastic materials, such as REACH and RoHS, to ensure environmental safety and product quality.
What Are the Advantages of Metal for Handle Grips?
Metal grips, often made from aluminum or stainless steel, are known for their strength and durability. They can withstand high temperatures and pressures, making them suitable for heavy-duty applications.
Pros & Cons:
Metal grips are highly durable and resistant to corrosion, providing a long lifespan. However, they can be heavier than other materials, which may not be suitable for all applications. Additionally, the manufacturing process can be more expensive due to machining and finishing requirements.
Impact on Application:
Metal grips are ideal for tools and equipment used in industrial settings, where strength and durability are paramount. However, they may not provide the same level of comfort as rubber or plastic grips.
Considerations for International Buyers:
Buyers in the Middle East should consider compliance with international standards such as ASTM A240 for stainless steel to ensure quality and performance.
How Does Foam Material Enhance Handle Grip Performance?
Foam materials, particularly EVA (ethylene-vinyl acetate) and polyurethane, are increasingly popular for handle grips due to their lightweight and cushioning properties. These materials typically have a temperature tolerance of -30°C to 70°C.
Pros & Cons:
Foam grips provide excellent comfort and shock absorption, making them ideal for prolonged use. However, they can be less durable than rubber or metal and may compress over time, affecting performance.
Impact on Application:
Foam grips are commonly used in sporting equipment and consumer products where comfort is a priority. However, they may not be suitable for industrial applications where durability is critical.
Considerations for International Buyers:
Buyers from regions such as Europe should ensure that foam materials comply with safety standards, such as EN 71 for toys, to avoid potential hazards.
Summary Table of Material Selection for Handle Grips
Material | Typical Use Case for Handle Grip Manufacturer | Key Advantage | Key Disadvantage/Limitation | Relative Cost (Low/Med/High) |
---|---|---|---|---|
Rubber | Tools, Sporting Equipment | Excellent grip and shock absorption | Degrades under UV exposure | Medium |
Plastic | Consumer Goods, Industrial Tools | Lightweight and cost-effective | Can become brittle over time | Low |
Metal | Heavy-Duty Tools, Industrial Equipment | High durability and corrosion resistance | Heavier and more expensive to manufacture | High |
Foam | Sporting Equipment, Consumer Products | Comfortable and shock-absorbing | Less durable, compresses over time | Medium |
This analysis provides a comprehensive overview of the materials available for handle grips, helping international B2B buyers make informed decisions based on their specific application needs and regional compliance requirements.
In-depth Look: Manufacturing Processes and Quality Assurance for handle grip manufacturer
What Are the Key Stages in the Manufacturing Process of Handle Grips?
Manufacturing handle grips involves several critical stages that ensure both quality and functionality. Understanding these stages helps B2B buyers from regions such as Africa, South America, the Middle East, and Europe (including Germany and Indonesia) to evaluate suppliers effectively.
1. Material Preparation
The first step in the manufacturing process is selecting and preparing the materials. Common materials used for handle grips include rubber, plastic, and foam, chosen for their durability and comfort. During this stage, suppliers typically conduct material tests to ensure they meet industry standards and specifications. Buyers should inquire about the origin and quality of these materials, as they directly influence the final product’s performance.
2. Forming Techniques
Once materials are prepared, the next stage involves forming the handle grips. This can be achieved through various techniques, including:
- Injection Molding: This is a popular method where molten material is injected into a mold to create the desired shape. It is efficient for producing large quantities with consistent quality.
- Compression Molding: Suitable for rubber grips, this technique involves placing material into a heated mold where it is compressed to form the grip.
- Extrusion: Used for creating continuous lengths of grips, typically made from thermoplastic materials.
Buyers should assess the forming techniques used by suppliers, as they impact the product’s quality and cost-effectiveness.
3. Assembly Processes
After forming, the grips often require assembly with other components, such as internal structures or attachments. This stage may involve:
- Adhesive Bonding: Using adhesives to attach different parts securely.
- Mechanical Fastening: Employing screws, clips, or other fasteners to hold components together.
B2B buyers should inquire about the assembly methods, as they can affect the grip’s durability and functionality.
4. Finishing Touches
Finishing processes enhance the grip’s aesthetic and functional qualities. Common finishing techniques include:
- Surface Treatment: This may involve sanding, polishing, or applying coatings to improve grip texture and appearance.
- Printing and Branding: Adding logos or branding elements through techniques like pad printing or screen printing.
Understanding these finishing processes is essential for buyers looking for specific aesthetic qualities or branding options.
How Is Quality Assurance Implemented in Handle Grip Manufacturing?
Quality assurance (QA) is crucial in ensuring that handle grips meet international standards and customer expectations. Buyers should be familiar with the QA processes used by manufacturers.
Relevant International Standards
Manufacturers often adhere to international quality standards such as ISO 9001, which focuses on quality management systems. Additionally, industry-specific certifications like CE (Conformité Européenne) and API (American Petroleum Institute) may apply, particularly for grips used in specialized applications.
B2B buyers should ask suppliers about their compliance with these standards, as they indicate a commitment to quality and safety.
Key Quality Control Checkpoints
Quality control (QC) involves several checkpoints throughout the manufacturing process:
- Incoming Quality Control (IQC): Inspecting raw materials upon arrival to ensure they meet specifications.
- In-Process Quality Control (IPQC): Conducting inspections during manufacturing to identify defects early.
- Final Quality Control (FQC): Performing thorough inspections before products are packaged and shipped.
These checkpoints help maintain product quality at each stage of production. Buyers should inquire about the frequency and methods of these inspections.
What Testing Methods Are Commonly Used for Handle Grips?
Various testing methods are employed to ensure handle grips meet performance and safety standards. Some common testing methods include:
- Durability Testing: Assessing how well grips withstand wear and tear over time.
- Grip Strength Testing: Measuring how effectively a grip performs under load.
- Environmental Testing: Evaluating how grips perform under different temperature and humidity conditions.
Buyers should request information on testing protocols and results, as this data provides insight into product reliability.
How Can B2B Buyers Verify Supplier Quality Control?
B2B buyers can take several steps to verify the quality control processes of potential suppliers:
- Conduct Supplier Audits: Performing on-site audits allows buyers to assess manufacturing practices and QA processes firsthand.
- Request Quality Reports: Suppliers should provide detailed reports on quality control measures, including inspection results and compliance certifications.
- Engage Third-Party Inspectors: Utilizing independent inspection services can offer an unbiased evaluation of the supplier’s quality assurance processes.
By taking these steps, buyers can significantly reduce the risk of quality issues in their supply chain.
What Are the QC and Certification Nuances for International Buyers?
International buyers, particularly from diverse regions like Africa, South America, the Middle East, and Europe, should be aware of specific nuances in quality control and certification:
- Understanding Regional Standards: Different regions may have unique certification requirements. For example, products sold in the European market may need CE marking, while those in the Middle East might require compliance with local regulations.
- Language and Documentation: Ensure that all quality documentation is available in a language that is understandable to the buyer. This helps in verifying compliance and understanding product specifications.
- Cultural Considerations: Cultural differences may affect communication and expectations around quality. Establishing clear agreements and understanding local practices can enhance supplier relationships.
By being informed about these nuances, international B2B buyers can make better purchasing decisions and foster stronger partnerships with handle grip manufacturers.
Practical Sourcing Guide: A Step-by-Step Checklist for ‘handle grip manufacturer’
This guide aims to provide international B2B buyers with a clear and actionable checklist for sourcing handle grip manufacturers. By following these steps, buyers can ensure they select the right supplier to meet their specific needs, particularly when sourcing from regions such as Africa, South America, the Middle East, and Europe.
Step 1: Define Your Technical Specifications
Before beginning the sourcing process, it’s essential to clearly outline your technical specifications for the handle grips. This includes the materials, dimensions, design requirements, and any industry standards that must be met. A well-defined specification helps streamline communication with potential suppliers and ensures that they can meet your requirements effectively.
- Materials: Consider whether you need rubber, plastic, or composite materials.
- Dimensions: Specify the length, width, and grip texture.
Step 2: Conduct Market Research
Understanding the market landscape is vital to identifying potential manufacturers. Research suppliers based on their reputation, experience, and product offerings in the handle grip sector. This information can be gathered from industry reports, trade shows, and online platforms.
- Industry Reports: Use resources like IBISWorld or Statista for market insights.
- Trade Shows: Attend relevant exhibitions to meet manufacturers and evaluate their products.
Step 3: Evaluate Potential Suppliers
Once you have a list of potential manufacturers, it’s crucial to vet them thoroughly. Request company profiles, case studies, and references from buyers in a similar industry or region. This step is essential to ensure reliability and quality.
- Company Profiles: Look for information on their production capacity and quality control processes.
- References: Ask for testimonials from previous clients to gauge satisfaction levels.
Step 4: Verify Supplier Certifications
Ensure that the manufacturers you are considering possess the necessary certifications, such as ISO 9001 for quality management systems or specific industry-related certifications. This verification is critical to ensure that the manufacturer adheres to international quality standards.
- Quality Certifications: Check for compliance with safety regulations relevant to your industry.
- Environmental Standards: Consider certifications like ISO 14001 if sustainability is a priority for your business.
Step 5: Request Samples and Prototypes
Before placing a large order, request samples or prototypes of the handle grips. This step allows you to assess the quality, comfort, and functionality of the grips firsthand. It’s an important risk mitigation strategy to ensure the product meets your expectations.
- Testing: Evaluate the sample for durability and usability.
- Feedback: Share samples with potential end-users to gather their input.
Step 6: Negotiate Terms and Conditions
Once you are satisfied with a supplier’s capabilities, it’s time to discuss and negotiate terms and conditions. This includes pricing, payment terms, delivery schedules, and warranty policies. Clear agreements will help prevent misunderstandings later in the procurement process.
- Pricing: Ensure that the pricing structure is transparent and competitive.
- Delivery: Discuss lead times and shipping arrangements to avoid delays.
Step 7: Establish a Communication Plan
Effective communication is key to a successful sourcing relationship. Establish a clear communication plan that includes regular check-ins and updates throughout the manufacturing process. This ensures that any issues are promptly addressed and that you remain informed.
- Regular Updates: Set a schedule for updates during the production phase.
- Point of Contact: Designate a specific contact person for both parties to streamline communication.
By following this practical sourcing guide, international B2B buyers can confidently navigate the process of procuring handle grips, ensuring they partner with a manufacturer that aligns with their needs and standards.
Comprehensive Cost and Pricing Analysis for handle grip manufacturer Sourcing
What Are the Key Cost Components in Handle Grip Manufacturing?
When sourcing handle grips, understanding the cost structure is crucial for international B2B buyers. The primary cost components include:
-
Materials: The choice of materials (e.g., rubber, plastic, or metal) significantly affects the overall cost. High-quality materials may increase initial expenditure but lead to better durability and performance.
-
Labor: Labor costs vary by region, influenced by local wage standards and skill levels. For instance, sourcing from countries with lower labor costs can reduce expenses, but it may come at the expense of quality.
-
Manufacturing Overhead: This includes indirect costs like utilities, rent, and administrative expenses. Manufacturers with efficient operations may offer better pricing.
-
Tooling: Custom tooling can be a substantial upfront cost, particularly for specialized grips. Buyers should consider whether the tooling costs will be absorbed into the product price or charged separately.
-
Quality Control (QC): Investing in robust QC processes ensures product reliability and compliance with international standards, which can add to overall costs but also mitigate risks related to product recalls or failures.
-
Logistics: Shipping costs, including freight and insurance, can fluctuate based on the shipping method and distance. Understanding Incoterms (International Commercial Terms) can help buyers clarify who bears these costs.
-
Margin: Manufacturer margins can vary widely based on brand reputation, market demand, and competitive landscape. Buyers should be aware of these margins when negotiating prices.
How Do Price Influencers Impact Handle Grip Manufacturing Costs?
Several factors influence the pricing of handle grips, and understanding these can aid buyers in making informed decisions:
-
Volume and Minimum Order Quantity (MOQ): Higher order volumes typically lead to lower unit prices. Buyers should negotiate MOQs to optimize costs without overcommitting.
-
Specifications and Customization: Custom designs or specifications can increase costs due to additional tooling and material requirements. Buyers should weigh the benefits of customization against potential cost increases.
-
Material Quality and Certifications: Premium materials and compliance with certifications (e.g., ISO, CE) can raise costs. However, they often enhance product longevity and marketability.
-
Supplier Factors: The supplier’s reputation, reliability, and production capabilities can impact pricing. Established suppliers may charge a premium but offer better quality assurance.
-
Incoterms: Different Incoterms can shift costs and responsibilities between buyers and sellers. Understanding these terms is crucial for budgeting accurately.
What Are Effective Buyer Tips for Negotiating Handle Grip Prices?
International B2B buyers can leverage several strategies to achieve cost-efficient sourcing:
-
Negotiate with Multiple Suppliers: Engaging with several manufacturers can create competitive tension, leading to better pricing and terms. Always request quotations from multiple suppliers to compare offers effectively.
-
Evaluate Total Cost of Ownership (TCO): Consider not just the purchase price but also shipping, maintenance, and potential disposal costs. TCO analysis helps in making more informed sourcing decisions.
-
Focus on Cost Efficiency: Look for ways to optimize costs without sacrificing quality. This can include bulk purchasing or exploring alternative materials that meet specifications but are more affordable.
-
Understand Pricing Nuances in Different Markets: Pricing structures can vary significantly across regions. For example, buyers from Africa may encounter different logistics challenges compared to those in Europe, influencing overall costs.
-
Be Prepared to Walk Away: If a deal does not meet your cost expectations, be willing to explore other options. This mindset can empower negotiations and lead to more favorable outcomes.
Disclaimer on Indicative Prices
Prices for handle grips can fluctuate based on market conditions, material availability, and other economic factors. It is recommended to conduct thorough market research and consult with multiple suppliers to obtain accurate pricing tailored to your specific requirements.
Alternatives Analysis: Comparing handle grip manufacturer With Other Solutions
In the realm of handle grips, international B2B buyers have several options to consider when evaluating solutions. While a handle grip manufacturer provides specialized products, alternatives may offer different advantages depending on the specific needs of the business. This section will explore various alternatives, helping buyers make informed decisions.
Comparison Aspect | Handle Grip Manufacturer | Alternative 1: Foam Grips | Alternative 2: Rubber Coatings |
---|---|---|---|
Performance | High durability and comfort, designed for specific applications | Moderate durability, good shock absorption | High durability, excellent grip in wet conditions |
Cost | Moderate to high, depending on customization | Low to moderate, cost-effective for mass production | Moderate, varies based on thickness and application |
Ease of Implementation | Requires specific manufacturing processes and lead times | Easy to apply, often available in bulk | Requires application expertise, may involve curing time |
Maintenance | Low, designed for long-term use | Low, but may wear out faster than grips | Low, but surface may degrade over time |
Best Use Case | Specialized applications where precision and comfort are crucial | General-purpose applications, consumer goods | Environments requiring superior grip, such as in outdoor tools |
What Are Foam Grips and Their Advantages?
Foam grips are soft, lightweight alternatives commonly found in consumer products such as sports equipment and hand tools. They offer moderate durability and excellent shock absorption, making them comfortable for prolonged use. However, foam grips may wear out faster compared to traditional handle grips, especially in high-use environments. Their low cost makes them an attractive option for businesses looking for budget-friendly solutions. However, they may not provide the same level of precision or comfort as grips manufactured specifically for certain applications.
How Do Rubber Coatings Compare?
Rubber coatings are another alternative that provides a high level of durability and excellent grip, especially in wet conditions. They can be applied to various surfaces, enhancing the grip of tools and equipment. The application of rubber coatings, however, may require specialized knowledge and can involve curing time, which might delay production. While they are moderately priced, the cost can vary significantly based on the thickness and type of rubber used. Rubber coatings are ideal for environments where grip is paramount, such as in outdoor tools or industrial applications.
How to Choose the Right Solution for Your Business Needs?
When selecting between a handle grip manufacturer and alternative solutions, B2B buyers should consider their specific use case, budget constraints, and the importance of performance characteristics such as durability and comfort. If the application requires a specialized grip tailored to particular ergonomic needs, investing in a handle grip manufacturer may be worthwhile. On the other hand, if cost-efficiency is a priority and the application is less demanding, alternatives like foam grips or rubber coatings may provide satisfactory results.
In conclusion, understanding the nuances of each option allows buyers from Africa, South America, the Middle East, and Europe to make informed decisions that align with their business objectives. Whether prioritizing performance, cost, or ease of implementation, assessing the specific requirements of each application will guide the choice of the most suitable handle grip solution.
Essential Technical Properties and Trade Terminology for handle grip manufacturer
What Are the Key Technical Properties for Handle Grip Manufacturing?
When sourcing handle grips for various applications, international B2B buyers must consider several critical technical properties that directly influence product performance, cost, and suitability for specific markets. Here are some essential specifications:
-
Material Grade
– The choice of material is paramount. Common materials include rubber, thermoplastics, and metals, each offering different durability, flexibility, and tactile properties. For instance, rubber grips provide superior comfort and slip resistance, making them ideal for handheld tools. Selecting the right material not only affects the product’s longevity but also impacts its compliance with regional safety standards. -
Tolerance Levels
– Tolerance refers to the allowable variation in dimensions during manufacturing. Precision is crucial, especially for components that need to fit together seamlessly. High tolerance levels ensure that handle grips fit securely onto tools or machinery, reducing the risk of defects and enhancing user safety. Buyers should inquire about the manufacturer’s capability to maintain specified tolerances to ensure quality control. -
Surface Texture
– The surface finish of handle grips can greatly influence user experience. Textured surfaces enhance grip and control, particularly in wet or slippery conditions. Buyers should consider the intended use of the handle grips and request samples to evaluate the surface texture against their specific requirements. -
Temperature Resistance
– Depending on the application, handle grips may need to withstand extreme temperatures. Materials with high temperature resistance are essential for applications in industrial settings or outdoor tools that face varying weather conditions. Understanding the thermal properties of materials helps buyers select grips that will perform reliably over time. -
Colorfastness
– Especially important for consumer-facing products, colorfastness refers to the ability of the material to maintain its color under exposure to light and washing. This property is vital for aesthetic consistency and product longevity, particularly in regions with high UV exposure. Buyers should verify that the manufacturer uses UV-stable materials if color retention is a priority.
What Are Common Trade Terminology and Jargon Used in Handle Grip Manufacturing?
Understanding industry jargon is crucial for effective communication and negotiation in the B2B landscape. Here are some common terms that buyers should familiarize themselves with:
-
OEM (Original Equipment Manufacturer)
– An OEM refers to a company that produces parts or equipment that may be marketed by another manufacturer. For handle grips, this means sourcing grips made by a specialized manufacturer to be used in a larger product. Knowing about OEM relationships helps buyers understand the supply chain and potential for customization. -
MOQ (Minimum Order Quantity)
– MOQ is the smallest number of units a supplier is willing to sell. This term is critical for budget-conscious buyers, as it can affect initial investment and inventory management. Buyers should negotiate MOQ to align with their production schedules and demand forecasts. -
RFQ (Request for Quotation)
– An RFQ is a document sent to suppliers to request pricing and terms for specific products or services. For handle grips, submitting an RFQ allows buyers to compare offers from different manufacturers, ensuring they obtain the best value. -
Incoterms (International Commercial Terms)
– Incoterms define the responsibilities of buyers and sellers in international shipping. Terms like FOB (Free on Board) and CIF (Cost, Insurance, and Freight) dictate who bears the cost and risk at various points in the shipping process. Understanding Incoterms helps buyers anticipate shipping costs and legal responsibilities. -
Lead Time
– Lead time refers to the time taken from placing an order to delivery. In the handle grip industry, understanding lead times is essential for project planning and inventory management. Buyers should ensure they have clear communication with manufacturers regarding expected lead times to avoid production delays.
By grasping these technical properties and trade terms, international B2B buyers can make informed decisions when sourcing handle grips, ultimately enhancing their product offerings and market competitiveness.
Navigating Market Dynamics and Sourcing Trends in the handle grip manufacturer Sector
What Are the Current Market Dynamics and Key Trends in the Handle Grip Manufacturing Sector?
The handle grip manufacturing sector is influenced by several global drivers, including technological advancements and shifting consumer preferences. International B2B buyers, particularly from regions like Africa, South America, the Middle East, and Europe, are increasingly looking for innovative solutions that enhance product usability and ergonomics. Key trends include the integration of smart technology into handle grips, such as sensors that provide feedback on grip strength and pressure, appealing particularly to industries like sports equipment and medical devices.
Moreover, the rise of e-commerce platforms has transformed sourcing strategies. Buyers can now access a wider range of suppliers globally, allowing for better price comparisons and product selections. Digital tools like AI-driven analytics are also helping manufacturers forecast demand and manage inventory more effectively, thus streamlining operations. This trend is crucial for international buyers seeking to minimize lead times and costs.
Additionally, sustainability is becoming a significant factor in purchasing decisions. More buyers are demanding eco-friendly materials and production methods, which is reshaping the supply chain dynamics. Manufacturers that prioritize sustainable practices not only appeal to conscientious buyers but also mitigate risks associated with environmental regulations.
How Does Sustainability Impact Sourcing Decisions in the Handle Grip Manufacturing Sector?
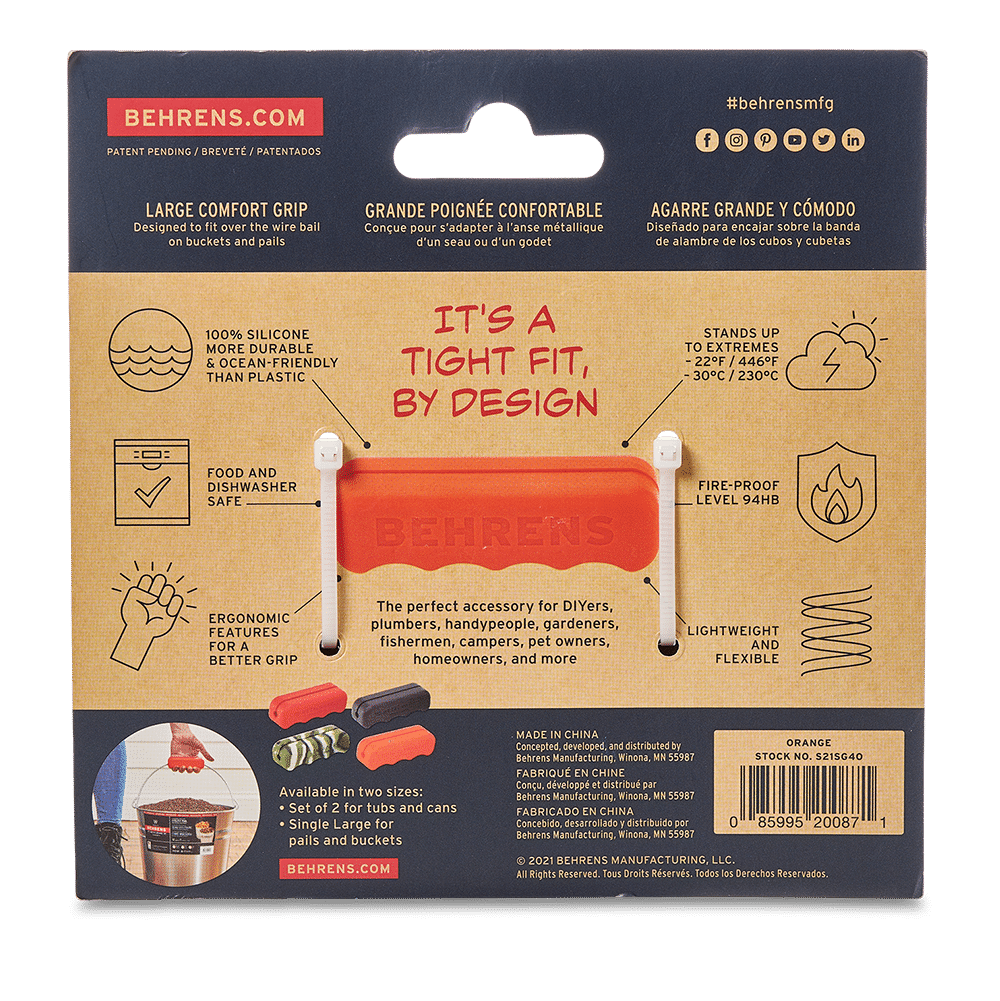
A stock image related to handle grip manufacturer.
Sustainability and ethical sourcing are pivotal in today’s B2B landscape, particularly for handle grip manufacturers. The environmental impact of production processes has come under scrutiny, prompting buyers to seek suppliers who adhere to sustainable practices. This includes using biodegradable materials, reducing waste during manufacturing, and ensuring that production processes have minimal carbon footprints.
Furthermore, ethical supply chains are becoming a critical component of procurement strategies. Buyers are increasingly considering suppliers’ labor practices and sourcing ethics, which can influence their brand reputation and consumer trust. Certifications such as ISO 14001 (Environmental Management) and Fair Trade can significantly enhance a manufacturer’s appeal to international buyers.
In terms of materials, the trend towards using recycled plastics and sustainably sourced natural materials is gaining traction. Manufacturers that invest in ‘green’ certifications not only position themselves favorably in the market but also align with the values of a growing segment of environmentally-conscious consumers. This shift not only helps in meeting regulatory demands but also opens up new market opportunities, particularly in regions with stringent environmental policies.
What is the Evolution of the Handle Grip Manufacturing Sector?
The handle grip manufacturing sector has undergone significant evolution over the decades, influenced by advancements in materials science and changing consumer needs. Initially dominated by simple rubber and plastic designs, the sector has now embraced a variety of materials, including advanced composites and soft-touch polymers that enhance user experience and comfort.
In recent years, the focus has shifted towards ergonomic designs that cater to specific user demographics, such as the aging population or individuals with disabilities. This evolution reflects a broader trend towards inclusivity and accessibility in product design, which is increasingly becoming a requirement rather than an option for manufacturers.
Furthermore, the integration of technology into product design, such as grips that monitor health metrics or provide adaptive support, showcases the sector’s responsiveness to emerging trends and consumer demands. As international buyers navigate this evolving landscape, understanding these historical shifts can provide critical insights into sourcing strategies and supplier evaluations.
Frequently Asked Questions (FAQs) for B2B Buyers of handle grip manufacturer
-
How do I choose the right handle grip manufacturer for my business needs?
Selecting the right handle grip manufacturer involves assessing their experience, production capabilities, and quality assurance processes. Look for manufacturers with a proven track record in your industry and positive client testimonials. It’s also essential to evaluate their ability to customize products according to your specifications. Request samples to assess the quality of their grips and ensure they meet your ergonomic and functional requirements. Establishing clear communication and understanding their lead times and minimum order quantities (MOQ) is vital for a successful partnership. -
What factors should I consider when vetting a handle grip supplier?
When vetting a handle grip supplier, consider their certifications, such as ISO 9001, which indicate adherence to quality management standards. Check their production processes and technology to ensure they can meet your specifications. Ask about their supply chain reliability and previous client references. Additionally, review their terms of service, including payment options and return policies. Conducting an on-site visit, if feasible, can provide deeper insights into their operations and quality control practices. -
What is the minimum order quantity (MOQ) for handle grips?
The minimum order quantity (MOQ) for handle grips varies by manufacturer and can range from a few hundred to several thousand units. Factors influencing MOQ include production capacity, material costs, and customization requirements. It is advisable to discuss your projected demand with potential suppliers to negotiate favorable terms. Keep in mind that higher order quantities may reduce the per-unit cost, so consider your budget and inventory needs when making a decision. -
What payment terms should I expect when sourcing handle grips?
Payment terms for handle grip orders typically include a deposit upfront, followed by the balance upon completion or prior to shipment. Common arrangements involve a 30% deposit and 70% upon delivery. Some suppliers may offer more flexible terms based on your relationship and order size. Always clarify payment methods accepted, such as bank transfers or letters of credit, and ensure that you understand any potential currency exchange implications, especially when dealing with international suppliers. -
How can I ensure the quality of handle grips from manufacturers?
To ensure quality, request samples before placing a bulk order. Verify that the manufacturer follows stringent quality control processes, such as inspections during production and pre-shipment checks. Discuss their compliance with international standards and certifications relevant to your market. Consider implementing a third-party quality assurance service to conduct inspections and audits of the manufacturing facility, ensuring that the products meet your quality expectations before they are shipped. -
What logistics considerations should I be aware of when importing handle grips?
Logistics considerations include shipping methods, customs regulations, and lead times. Determine whether air freight or sea freight best suits your needs based on urgency and budget. Understand the import duties and taxes applicable in your country to avoid unexpected costs. Establish clear communication with your supplier regarding shipping schedules and tracking. It’s also advisable to work with a reputable freight forwarder to navigate the complexities of international shipping and customs clearance. -
Can handle grips be customized to meet specific requirements?
Yes, many handle grip manufacturers offer customization options, allowing you to tailor grips to your specific needs. This can include variations in size, material, color, and ergonomic design. When discussing customization, provide detailed specifications and consider any necessary prototypes to ensure the final product meets your expectations. Be aware that customized orders may have higher MOQs and longer lead times, so plan accordingly. -
What are the best practices for establishing long-term relationships with handle grip suppliers?
To foster long-term relationships with handle grip suppliers, prioritize open communication and transparency. Provide feedback on product quality and service to help them improve. Regularly review your order patterns and discuss future needs to ensure they can meet your demands. Consider establishing contracts that outline expectations for quality, delivery, and pricing. Building trust through consistent orders and timely payments can lead to better terms and collaboration opportunities in the future.
Important Disclaimer & Terms of Use
⚠️ Important Disclaimer
The information provided in this guide, including content regarding manufacturers, technical specifications, and market analysis, is for informational and educational purposes only. It does not constitute professional procurement advice, financial advice, or legal advice.
While we have made every effort to ensure the accuracy and timeliness of the information, we are not responsible for any errors, omissions, or outdated information. Market conditions, company details, and technical standards are subject to change.
B2B buyers must conduct their own independent and thorough due diligence before making any purchasing decisions. This includes contacting suppliers directly, verifying certifications, requesting samples, and seeking professional consultation. The risk of relying on any information in this guide is borne solely by the reader.
Strategic Sourcing Conclusion and Outlook for handle grip manufacturer
What Are the Key Takeaways for B2B Buyers in Handle Grip Manufacturing?
In conclusion, strategic sourcing for handle grip manufacturers presents a wealth of opportunities for international B2B buyers, especially from Africa, South America, the Middle East, and Europe. By focusing on quality, cost-effectiveness, and supplier reliability, buyers can enhance their procurement strategies. It’s crucial to evaluate suppliers not just on price but also on their ability to meet compliance standards, deliver timely, and innovate in product design.
How Can Buyers Leverage Strategic Sourcing for Competitive Advantage?
The value of strategic sourcing extends beyond mere cost savings; it fosters long-term partnerships that can lead to better service and improved product offerings. Engaging with manufacturers who understand local market needs can significantly boost product adaptability and customer satisfaction.
What Should B2B Buyers Do Next?
As we look towards the future, international buyers are encouraged to explore emerging markets and technologies that can elevate their sourcing strategies. By being proactive in supplier engagement and market research, companies can position themselves ahead of the competition. Embrace the evolution of the handle grip manufacturing landscape, and seize the opportunity to enhance your supply chain efficiency and product quality today.