Discover Top Benefits from Leading USB Hub Manufacturers (2025)
Introduction: Navigating the Global Market for usb hub manufacturer
In the rapidly evolving landscape of technology, sourcing the right USB hub manufacturer can pose a significant challenge for international B2B buyers. With the increasing demand for connectivity solutions across diverse applications—from enhancing office productivity in Africa to supporting high-tech environments in Europe—understanding the intricacies of USB hubs is essential for informed purchasing decisions. This comprehensive guide delves into various aspects of USB hub manufacturing, including types, applications, supplier vetting processes, and cost considerations.
International buyers, particularly those from regions such as Africa, South America, the Middle East, and Europe (including Italy and the UK), will find valuable insights tailored to their unique market needs. We explore the importance of evaluating manufacturers based on quality, compliance with international standards, and their ability to provide tailored solutions that meet specific business requirements.
By equipping B2B buyers with the knowledge necessary to navigate the complexities of sourcing USB hubs, this guide empowers them to make strategic decisions that drive operational efficiency and enhance technological capabilities. Whether you’re looking to enhance your supply chain or seeking reliable partners for your business, understanding the global market for USB hubs is crucial for success in today’s interconnected world.
Understanding usb hub manufacturer Types and Variations
Type Name | Key Distinguishing Features | Primary B2B Applications | Brief Pros & Cons for Buyers |
---|---|---|---|
Powered USB Hubs | Includes external power supply for high-demand devices | Data centers, manufacturing | Pros: Supports multiple devices, stable power supply. Cons: Higher cost, requires additional space. |
Compact USB Hubs | Small, portable design for limited connections | Trade shows, mobile workstations | Pros: Lightweight, easy to transport. Cons: Limited ports, may not support high data transfer rates. |
Industrial USB Hubs | Rugged construction for harsh environments | Factories, outdoor events | Pros: Durable, weather-resistant. Cons: Bulkier, often more expensive. |
USB-C Hubs | Utilizes USB-C technology for faster data transfer | Modern office setups, tech startups | Pros: High-speed connectivity, versatile connections. Cons: Compatibility issues with older devices. |
Multi-port USB Hubs | Offers multiple USB ports in one unit | Offices, educational institutions | Pros: Cost-effective for multiple devices. Cons: Power distribution may be uneven, affecting performance. |
What Are the Characteristics of Powered USB Hubs?
Powered USB hubs are equipped with an external power supply, enabling them to support multiple high-demand devices simultaneously. This type is particularly suitable for environments like data centers and manufacturing, where numerous devices may need to be connected without sacrificing performance. When purchasing, buyers should consider the hub’s power output and the total number of devices it can support, ensuring it meets their specific operational requirements.
How Do Compact USB Hubs Fit Into B2B Applications?
Compact USB hubs are designed for portability, making them ideal for settings such as trade shows and mobile workstations. Their lightweight and small footprint allow for easy transport, but they typically offer fewer ports and may not support high-speed data transfers. B2B buyers should evaluate their need for mobility against the potential limitations in connectivity and performance.
What Makes Industrial USB Hubs Unique?
Industrial USB hubs are built to withstand harsh conditions, featuring rugged designs that are often weather-resistant. These hubs are essential in factories and outdoor events where durability is paramount. Buyers should assess the environmental conditions in which the hub will be used, as well as the number of connections required, to ensure they select a model that offers the necessary resilience.
Why Choose USB-C Hubs for Modern Work Environments?
USB-C hubs leverage the latest USB technology, providing faster data transfer rates and versatile connection options. They are particularly beneficial in modern office setups and tech startups that utilize cutting-edge devices. However, buyers must be aware of potential compatibility issues with older devices, making it crucial to evaluate their existing technology before investing.
How Do Multi-port USB Hubs Benefit B2B Buyers?
Multi-port USB hubs offer a cost-effective solution for connecting numerous devices in one unit, making them popular in offices and educational institutions. While they provide convenience, buyers should consider the power distribution capabilities of the hub, as uneven distribution can lead to performance issues. Understanding the total power requirements of connected devices will help ensure optimal functionality.
Related Video: USB Ports, Cables, Types, & Connectors
Key Industrial Applications of usb hub manufacturer
Industry/Sector | Specific Application of usb hub manufacturer | Value/Benefit for the Business | Key Sourcing Considerations for this Application |
---|---|---|---|
Healthcare | Connecting medical devices for data transfer | Enhances patient monitoring and data accuracy | Compliance with medical standards, reliability, and durability |
Manufacturing | Integrating machinery and control systems | Streamlines operations and improves productivity | Compatibility with existing systems, scalability, and support |
Education | Facilitating classroom technology integration | Enhances learning experiences through technology utilization | Multi-device support, ease of use, and educational software compatibility |
Retail | Point of Sale (POS) systems integration | Improves transaction efficiency and customer service | Security features, ease of integration with existing systems |
Telecommunications | Supporting network infrastructure and devices | Ensures reliable connectivity and data transmission | High-speed data transfer capabilities and robust performance |
How is USB Hub Manufacturing Applied in Healthcare?
In the healthcare sector, USB hubs are essential for connecting various medical devices, such as monitors, diagnostic equipment, and data entry systems. They facilitate seamless data transfer, improving patient monitoring and treatment accuracy. For international buyers in Africa, South America, the Middle East, and Europe, sourcing USB hubs must consider compliance with medical device standards, ensuring reliability and durability to withstand frequent use in clinical environments.
What Role Do USB Hubs Play in Manufacturing?
Manufacturing industries leverage USB hubs to integrate machinery and control systems, enabling efficient communication between devices. This integration streamlines operations, enhances productivity, and reduces downtime. Buyers should prioritize sourcing USB hubs that are compatible with existing systems and capable of scaling with future technological advancements, particularly in regions like Europe and the Middle East where industrial automation is rapidly evolving.
How Are USB Hubs Used in Education Settings?
In educational environments, USB hubs facilitate the integration of technology in classrooms, allowing multiple devices such as computers, projectors, and interactive boards to connect simultaneously. This enhances learning experiences by enabling the use of various educational software and multimedia resources. Buyers from diverse regions must consider multi-device support and ease of use to ensure that the technology is accessible to both educators and students.
Why Are USB Hubs Important for Retail Applications?
Retail environments utilize USB hubs to connect Point of Sale (POS) systems, barcode scanners, and payment terminals. This integration improves transaction efficiency and enhances customer service by enabling quick and reliable payment processing. When sourcing USB hubs, businesses should focus on security features and ease of integration with their existing systems to protect sensitive customer information and streamline operations.
How Do USB Hubs Support Telecommunications?
In the telecommunications sector, USB hubs support the connectivity of network infrastructure and devices, ensuring reliable data transmission and communication. This is crucial for maintaining service quality and operational efficiency. Buyers need to prioritize high-speed data transfer capabilities and robust performance when sourcing USB hubs, particularly in regions experiencing rapid technological growth and increasing connectivity demands.
Related Video: LABORATORY APPARATUS AND THEIR USES
3 Common User Pain Points for ‘usb hub manufacturer’ & Their Solutions
Scenario 1: Connectivity Issues with USB Hubs in Multi-Device Environments
The Problem:
B2B buyers, particularly in sectors that heavily rely on technology—such as IT, education, and healthcare—often face significant challenges with connectivity when using USB hubs. In environments where multiple devices are connected (e.g., printers, external hard drives, and cameras), it’s common to encounter issues like slow data transfer speeds or devices not being recognized. This can lead to workflow disruptions, missed deadlines, and ultimately, a negative impact on productivity.
The Solution:
To mitigate these connectivity issues, it’s crucial to choose a USB hub that supports the latest standards, such as USB 3.0 or USB 3.1. These standards offer faster data transfer speeds and better power delivery capabilities. When sourcing a USB hub manufacturer, inquire about the hub’s specifications regarding compatibility with your existing devices. Additionally, consider hubs that have dedicated power sources, which can provide adequate power to all connected devices, reducing the likelihood of connectivity failures. Testing the hub in a real-world scenario before full-scale deployment can also help identify potential issues early on.
Scenario 2: Inadequate Device Compatibility Across Different Operating Systems
The Problem:
International B2B buyers often encounter problems with device compatibility when sourcing USB hubs, especially in regions like Africa and South America, where diverse technology ecosystems exist. For example, a hub that works seamlessly with Windows devices might not be compatible with macOS or Linux systems, causing frustration and compatibility challenges within a mixed-OS environment.
The Solution:
To address compatibility issues, it is essential to collaborate with USB hub manufacturers who provide comprehensive compatibility documentation. Prioritize vendors that offer multi-platform support, ensuring their hubs can operate across various operating systems. Furthermore, consider investing in USB hubs that feature plug-and-play functionality, which minimizes installation headaches. Before finalizing your purchase, request trial units or demos to test the hubs with your specific devices and operating systems to ensure seamless integration.
Scenario 3: Uncertainty About Power Requirements and Performance
The Problem:
B2B buyers often struggle with understanding the power requirements for USB hubs, especially when connecting power-hungry devices such as external hard drives or high-definition webcams. Insufficient power can lead to performance degradation, devices not functioning correctly, or even hardware damage, creating a significant risk for businesses.
The Solution:
To prevent power-related issues, seek out USB hub manufacturers that clearly specify the power output of their products. Look for hubs that offer features like smart charging ports or built-in power adapters that can handle multiple devices simultaneously. When evaluating options, consider the total power consumption of all devices you plan to connect and ensure the hub can accommodate that load. Engaging in discussions with suppliers about your specific usage scenarios can help clarify power requirements and lead to better purchasing decisions. Additionally, investing in hubs that include LED indicators for power status can provide real-time feedback on device performance, further minimizing risks associated with inadequate power supply.
Strategic Material Selection Guide for usb hub manufacturer
What Are the Common Materials Used in USB Hub Manufacturing?
When selecting materials for USB hub manufacturing, it is essential to consider their properties, advantages, disadvantages, and how they align with international standards. Below is an analysis of four common materials used in the production of USB hubs.
1. ABS Plastic: A Versatile Choice for USB Hubs
Key Properties: ABS (Acrylonitrile Butadiene Styrene) is known for its high impact resistance and toughness. It has a temperature resistance of approximately 80°C and is relatively lightweight.
Pros & Cons: The main advantages of ABS include its cost-effectiveness and ease of manufacturing, which allows for complex shapes and designs. However, it has lower thermal stability compared to other materials, which may limit its use in high-temperature environments.
Impact on Application: ABS is suitable for general-purpose USB hubs, especially in consumer electronics. Its compatibility with various media types makes it a versatile choice.
Considerations for International Buyers: Buyers from regions like Africa and South America should ensure compliance with local safety standards, as ABS can emit harmful fumes when burned. In Europe, adherence to REACH regulations is crucial.
2. Aluminum: A Premium Material for Enhanced Performance
Key Properties: Aluminum is lightweight, has excellent corrosion resistance, and can withstand temperatures up to 150°C. Its thermal conductivity makes it ideal for heat dissipation.
Pros & Cons: The primary advantage of aluminum is its durability and aesthetic appeal, often resulting in a premium product. However, it is more expensive than plastics and can complicate manufacturing due to the need for specialized machining.
Impact on Application: Aluminum is ideal for high-performance USB hubs that require better thermal management, making it suitable for gaming and professional applications.
Considerations for International Buyers: Buyers in Europe and the Middle East should consider aluminum’s recyclability, which aligns with sustainability goals. Compliance with standards like ASTM B221 for aluminum extrusions is also important.
3. Polycarbonate: Strength and Transparency Combined
Key Properties: Polycarbonate is known for its high impact resistance and clarity. It can withstand temperatures up to 120°C and offers good dimensional stability.
Pros & Cons: Polycarbonate’s transparency allows for aesthetic designs and LED integration. However, it is more expensive than ABS and can be prone to scratching, which may affect its appearance over time.
Impact on Application: This material is ideal for USB hubs designed for public spaces or environments where visual appeal is essential, such as in retail.
Considerations for International Buyers: Compliance with safety standards is crucial, especially in Europe, where polycarbonate must meet specific fire safety regulations. Buyers should also consider the material’s environmental impact, as it is not biodegradable.
4. Steel: Robust and Reliable
Key Properties: Steel offers high strength and durability, withstanding extreme conditions and temperatures beyond 200°C. It is also resistant to corrosion when treated.
Pros & Cons: The key advantage of steel is its robustness, making it suitable for industrial applications. However, it is heavier and more expensive, which can increase shipping costs and complicate product design.
Impact on Application: Steel is ideal for rugged USB hubs used in harsh environments, such as factories or outdoor settings.
Considerations for International Buyers: Buyers should be aware of the compliance requirements for steel products, particularly regarding corrosion resistance standards in different regions, such as DIN in Europe.
Summary Table of Material Selection for USB Hub Manufacturing
Material | Typical Use Case for usb hub manufacturer | Key Advantage | Key Disadvantage/Limitation | Relative Cost (Low/Med/High) |
---|---|---|---|---|
ABS Plastic | General-purpose consumer electronics | Cost-effective and easy to mold | Lower thermal stability | Low |
Aluminum | High-performance gaming/professional hubs | Durable and excellent heat dissipation | Higher manufacturing complexity | High |
Polycarbonate | Retail and public space applications | Aesthetic appeal and transparency | Prone to scratching | Med |
Steel | Industrial and rugged environments | High strength and durability | Heavier and more expensive | High |
This strategic material selection guide provides insights for international B2B buyers, enabling them to make informed decisions based on material properties, application suitability, and compliance considerations.
In-depth Look: Manufacturing Processes and Quality Assurance for usb hub manufacturer
What Are the Main Stages in the Manufacturing Process of USB Hubs?
The manufacturing of USB hubs involves several critical stages that ensure the final product meets quality and performance standards. Below is a detailed breakdown of these stages:
1. Material Preparation
The initial stage involves sourcing high-quality materials, including PCBs (Printed Circuit Boards), connectors, and plastic casings. Suppliers should prioritize materials that meet international standards to ensure durability and performance. For example, using high-grade copper for wiring and flame-retardant plastics can significantly enhance product longevity.
2. Forming
During the forming stage, the materials are shaped into the required components. This involves processes like injection molding for plastic casings and etching for PCBs. Advanced techniques such as laser cutting may also be employed to achieve precise dimensions. Buyers should verify that manufacturers use CNC machines or automated processes to ensure consistent quality.
3. Assembly
The assembly stage is where all components come together. Skilled technicians or automated systems will place and solder the components onto the PCBs, ensuring that connections are secure. Automated optical inspection (AOI) is often used at this stage to identify defects early, thus preventing faulty products from progressing to the next stage.
4. Finishing
Finishing processes include applying protective coatings, branding, and packaging. This stage not only enhances the aesthetic appeal of the USB hubs but also provides additional protection against wear and tear. Manufacturers often employ environmental controls to ensure that finishing processes do not compromise product integrity.
How Is Quality Assurance Implemented in USB Hub Manufacturing?
Quality assurance (QA) is a fundamental aspect of USB hub manufacturing, ensuring that products meet both industry standards and customer expectations. Here are key components of the QA process:
International and Industry-Specific Standards
Manufacturers typically comply with various international standards, such as ISO 9001 for quality management systems and CE certification for safety and environmental standards. For USB hubs, the compliance with RoHS (Restriction of Hazardous Substances) is also essential, especially for B2B buyers in Europe.
What Are the Key Quality Control Checkpoints?
Effective quality control (QC) involves multiple checkpoints throughout the manufacturing process:
-
Incoming Quality Control (IQC): This stage checks raw materials upon arrival to ensure they meet specifications. Buyers should inquire about the supplier’s IQC processes and the criteria used for material acceptance.
-
In-Process Quality Control (IPQC): Continuous monitoring during the manufacturing process helps identify defects before they become systemic. Techniques such as statistical process control (SPC) can be employed to track production data in real-time.
-
Final Quality Control (FQC): Before products are shipped, they undergo rigorous testing to verify that they function as intended. Common tests include electrical performance assessments and thermal stability tests. B2B buyers should ask for detailed FQC reports as part of their supplier evaluation.
What Common Testing Methods Are Used in USB Hub Manufacturing?
Several testing methods are critical to ensuring the quality and reliability of USB hubs:
-
Electrical Testing: This includes checking the functionality of each port, ensuring data transfer rates meet USB specifications, and verifying the power supply.
-
Environmental Testing: USB hubs are often subjected to temperature cycling and humidity tests to ensure performance under various conditions. This is particularly important for buyers in regions with extreme climates.
-
Mechanical Testing: This assesses the physical durability of the hub, including stress tests for connectors and casing integrity.
How Can B2B Buyers Verify Supplier Quality Control?
For international B2B buyers, particularly those in Africa, South America, the Middle East, and Europe, verifying a supplier’s QC processes is vital to ensuring product reliability. Here are some strategies:
Conducting Supplier Audits
Regular audits allow buyers to assess the manufacturing processes and quality assurance systems in place. Buyers should consider establishing a checklist based on international standards and industry best practices during these audits.
Requesting Quality Reports
Suppliers should provide detailed reports on their QC processes, including IQC, IPQC, and FQC findings. These documents should outline any corrective actions taken in response to identified issues.
Utilizing Third-Party Inspection Services
Engaging third-party inspection services can provide an unbiased assessment of product quality before shipment. This is particularly useful for buyers who may not have the resources to conduct in-house inspections.
What Are the QC and Certification Nuances for International B2B Buyers?
When sourcing USB hubs from international manufacturers, buyers must be aware of the nuances in quality control and certification:
-
Understanding Local Regulations: Different regions have varying regulations regarding electronic devices. Buyers should ensure that their suppliers comply with local laws, particularly when importing products into their countries.
-
Certification Validity: Certifications like CE and RoHS should be up to date. Buyers should request copies of these certifications and verify their authenticity through the issuing bodies.
-
Cultural Considerations: Understanding the cultural context in which a manufacturer operates can impact communication and quality expectations. Buyers from Europe, for instance, may have different expectations compared to those in Africa or South America.
Conclusion
For international B2B buyers, a comprehensive understanding of the manufacturing processes and quality assurance practices of USB hub manufacturers is crucial. By focusing on the main manufacturing stages, quality control checkpoints, common testing methods, and verification strategies, buyers can make informed decisions that ensure they partner with reliable suppliers. This approach not only safeguards their investments but also enhances their product offerings in competitive markets.
Practical Sourcing Guide: A Step-by-Step Checklist for ‘usb hub manufacturer’
To assist international B2B buyers in procuring USB hubs from manufacturers, we have created a practical sourcing checklist. This guide outlines essential steps to streamline the procurement process, ensuring buyers make informed decisions.
Step 1: Define Your Technical Specifications
Before reaching out to manufacturers, clearly outline your technical requirements for the USB hubs. Consider factors such as the number of ports, USB standards (e.g., USB 2.0, USB 3.0), and additional features like power delivery or data transfer rates. By defining these specifications upfront, you ensure that you only engage with suppliers who can meet your specific needs, reducing time spent on unsuitable options.
Step 2: Research Potential Manufacturers
Conduct thorough research to identify potential USB hub manufacturers. Utilize online platforms, industry directories, and trade shows to gather information about companies. Look for manufacturers with a proven track record in producing high-quality USB hubs and check their client testimonials. This research will help you compile a shortlist of credible suppliers to approach.
Step 3: Verify Supplier Certifications
It’s crucial to verify that your selected manufacturers comply with relevant industry standards and certifications. Check for certifications like ISO 9001 for quality management and CE or FCC marks for safety compliance. Certifications not only indicate that the manufacturer adheres to quality standards but also assure you that their products are safe and reliable for your intended use.
Step 4: Request Samples for Testing
Once you have narrowed down your choices, request product samples from the manufacturers. This step allows you to evaluate the quality, performance, and compatibility of the USB hubs with your existing systems. Testing samples is essential to ensure that the products meet your technical specifications and function as expected in real-world applications.
Step 5: Inquire About Production Capabilities
Understanding a manufacturer’s production capabilities is vital for ensuring they can meet your demand. Inquire about their manufacturing capacity, lead times, and flexibility in production. This information will help you assess whether they can scale up production to meet your future needs, particularly if you anticipate growth or increased demand for USB hubs.
Step 6: Evaluate Pricing and Terms
Engage in discussions regarding pricing structures, payment terms, and shipping options. Compare quotes from multiple suppliers to identify competitive pricing while ensuring quality is not compromised. Additionally, clarify the terms of warranty and after-sales support, which can significantly impact your overall satisfaction with the purchase.
Step 7: Establish Communication and Support Channels
Finally, ensure there are clear lines of communication with the manufacturer. Effective communication is key to addressing any issues that may arise during production or after delivery. Establishing support channels will facilitate smoother transactions and foster a long-term relationship with the supplier, which is beneficial for future procurement needs.
By following this checklist, international B2B buyers from Africa, South America, the Middle East, and Europe can navigate the sourcing process for USB hubs more effectively, ensuring they partner with reliable manufacturers who meet their specific requirements.
Comprehensive Cost and Pricing Analysis for usb hub manufacturer Sourcing
What Are the Key Cost Components in USB Hub Manufacturing?
When sourcing USB hubs from manufacturers, understanding the cost structure is crucial for international B2B buyers. The primary cost components include:
-
Materials: The choice of materials significantly affects the cost. High-quality plastics, metals, and electronic components can drive up expenses. For instance, using premium-grade connectors enhances durability but increases material costs.
-
Labor: Labor costs vary by region and can influence the overall pricing. Countries with lower labor costs may offer competitive pricing, but it’s essential to ensure that quality is not compromised.
-
Manufacturing Overhead: This encompasses all indirect costs associated with production, such as utilities, facility maintenance, and equipment depreciation. Efficient manufacturing processes can help reduce overhead.
-
Tooling: Custom tooling for specific USB hub designs can be a significant upfront cost. Buyers should discuss these expenses with manufacturers to evaluate the impact on pricing.
-
Quality Control (QC): Ensuring the product meets industry standards often involves rigorous testing and quality assurance processes, which contribute to the overall cost.
-
Logistics: Shipping and handling costs can vary significantly based on the destination and chosen Incoterms. Buyers should consider these costs in their total budget.
-
Margin: Manufacturers will include a profit margin in their pricing, which can fluctuate based on market demand and competition.
How Do Price Influencers Affect USB Hub Sourcing?
Several factors can influence the price of USB hubs, making it essential for buyers to understand their implications:
-
Volume and Minimum Order Quantity (MOQ): Larger orders typically lead to lower per-unit costs due to economies of scale. Buyers should negotiate MOQs that align with their needs to optimize pricing.
-
Specifications and Customization: Custom features, such as unique designs or additional functionalities, can increase costs. Clearly defining specifications upfront can help manage expectations and pricing.
-
Material Quality and Certifications: High-quality materials and compliance with international certifications (e.g., CE, FCC) may raise costs but are crucial for product reliability and market acceptance.
-
Supplier Factors: The reputation and reliability of the supplier can affect pricing. Established manufacturers may charge more for their experience and service quality, while newer entrants might offer competitive rates.
-
Incoterms: The choice of shipping terms (e.g., FOB, CIF) can impact the total cost significantly. Understanding these terms helps buyers calculate landed costs more accurately.
What Are Effective Buyer Tips for Cost-Efficiency?
To achieve cost efficiency when sourcing USB hubs, international buyers can employ several strategies:
-
Negotiate Terms: Engaging in open discussions about pricing, payment terms, and delivery schedules can lead to more favorable conditions. Building a strong relationship with suppliers can also foster better negotiation outcomes.
-
Consider Total Cost of Ownership (TCO): Beyond the initial purchase price, buyers should assess factors such as durability, warranty, and maintenance costs. A higher upfront cost may be justified by lower long-term expenses.
-
Research Market Prices: Understanding the market landscape can provide insight into reasonable pricing. Buyers should compare quotes from multiple suppliers to ensure competitive pricing.
-
Stay Informed About Regional Variations: Prices can vary significantly between regions like Africa, South America, the Middle East, and Europe. Being aware of these differences can help buyers make informed decisions.
Disclaimer on Indicative Prices
It is essential to note that the prices for USB hubs can fluctuate based on market conditions, raw material costs, and supplier pricing strategies. Buyers should seek updated quotes and conduct thorough due diligence before finalizing any agreements to ensure they secure the best possible pricing.
Alternatives Analysis: Comparing usb hub manufacturer With Other Solutions
When considering the best solutions for enhancing connectivity in an office or workspace, B2B buyers often explore various alternatives to USB hubs. These alternatives can provide similar functionalities but may differ in performance, cost, and implementation. Understanding these options can help buyers make informed decisions that align with their specific requirements.
Comparison Aspect | Usb Hub Manufacturer | Alternative 1: Docking Station | Alternative 2: Wireless USB Adapters |
---|---|---|---|
Performance | High data transfer rates, typically USB 3.0 or higher | Superior performance with multiple ports and displays | Varies by device, often lower speeds than wired solutions |
Cost | Generally affordable | Higher initial investment, but offers more features | Moderate cost, depends on brand and range |
Ease of Implementation | Plug and play simplicity | Requires driver installation and configuration | Simple setup, but may require software updates |
Maintenance | Low maintenance required | Moderate maintenance for software updates | Low maintenance, but may need troubleshooting for connectivity issues |
Best Use Case | Ideal for basic connectivity needs | Best for professionals needing multiple connections | Suitable for mobile workforces or limited space environments |
What Are the Benefits and Drawbacks of Using Docking Stations as an Alternative to USB Hubs?
Docking stations provide a comprehensive solution for users who require multiple connections, such as monitors, USB devices, and power delivery. They are especially beneficial for professionals who frequently connect and disconnect laptops in a hybrid work environment. However, the higher cost and the need for specific drivers may deter some buyers. Maintenance can also be a concern, as software updates are necessary to ensure compatibility with new devices.
How Do Wireless USB Adapters Compare to Traditional USB Hubs?
Wireless USB adapters offer a unique advantage by eliminating the need for physical connections, which can be crucial in environments where mobility is key. They facilitate a cleaner workspace and allow for easier access to devices without the clutter of cables. However, they often provide lower data transfer speeds compared to wired solutions and may be less reliable in terms of connectivity, particularly in environments with many electronic devices. Buyers must weigh the convenience against potential performance trade-offs.
Conclusion: How to Choose the Right Connectivity Solution for Your Business?
Selecting the right solution depends on the specific needs of your business. If you require basic connectivity and affordability, USB hubs remain a solid choice. For users needing extensive connectivity options, docking stations may be the best fit, despite their higher cost. Conversely, if mobility and a clutter-free environment are priorities, wireless USB adapters could be the ideal solution. Assessing your organization’s requirements, budget, and the technical capabilities of your team will guide you to the most suitable option for enhancing connectivity in your operations.
Essential Technical Properties and Trade Terminology for usb hub manufacturer
What Are the Essential Technical Properties of USB Hubs for B2B Buyers?
When sourcing USB hubs, understanding their technical specifications is crucial for ensuring compatibility and performance. Here are some key properties to consider:
1. Material Grade
The material used in USB hubs often includes plastics like ABS (Acrylonitrile Butadiene Styrene) or polycarbonate, along with metals such as aluminum for the casing. The choice of material affects durability, heat resistance, and overall performance. For B2B buyers, selecting high-grade materials can prevent failures in demanding environments, thereby reducing warranty claims and enhancing customer satisfaction.
2. Power Output
USB hubs can have different power outputs, typically ranging from 5V to 20V depending on the USB standard (e.g., USB 2.0, 3.0, or 3.1). Understanding power output is vital, especially for buyers looking to charge multiple devices simultaneously. A hub with higher power output can support fast charging and reduce downtime for connected devices, making it a more efficient choice for businesses.
3. Data Transfer Rate
Data transfer rates can significantly impact productivity, especially in data-intensive environments. USB 2.0 offers a maximum speed of 480 Mbps, while USB 3.0 can reach up to 5 Gbps. For B2B buyers, selecting a hub with the appropriate data transfer rate ensures that large files can be moved quickly, which is essential for industries like media, design, and IT.
4. Number of Ports
The number of ports on a USB hub can vary widely, from a single port to upwards of 20. Depending on the specific use case, buyers should consider how many devices will be connected simultaneously. A hub with more ports can enhance workplace efficiency, allowing for better organization of multiple devices in a shared workspace.
5. Form Factor
The form factor, which can be desktop, wall-mounted, or portable, is another critical property. This affects where and how the hub can be used. For example, a portable hub may be ideal for sales teams that travel frequently, while a desktop model might better suit office settings. Understanding the required form factor helps buyers choose a product that fits their operational needs.
What Trade Terminology Should B2B Buyers Know When Purchasing USB Hubs?
Familiarizing yourself with industry jargon can significantly streamline the purchasing process. Here are some essential terms:
1. OEM (Original Equipment Manufacturer)
OEM refers to companies that produce products that are sold under another company’s brand name. For B2B buyers, working with OEMs can often lead to cost savings and customization options, as these manufacturers can tailor products to meet specific business requirements.
2. MOQ (Minimum Order Quantity)
MOQ is the smallest quantity of a product that a supplier is willing to sell. Understanding MOQ is crucial for B2B buyers to avoid overstocking or tying up capital in excess inventory. This term often influences purchasing decisions, especially for smaller companies or those with limited budgets.
3. RFQ (Request for Quotation)
An RFQ is a document sent to suppliers to solicit price quotes for specific products or services. For B2B buyers, issuing an RFQ can help compare pricing, terms, and conditions from multiple suppliers, ensuring the best deal.
4. Incoterms (International Commercial Terms)
Incoterms are internationally recognized rules that define the responsibilities of buyers and sellers in international transactions. Understanding these terms helps B2B buyers clarify shipping costs, risks, and logistics responsibilities, thus avoiding potential disputes.
5. Lead Time
Lead time refers to the time it takes from placing an order to receiving the product. For B2B buyers, understanding lead times is critical for planning inventory and ensuring that operations run smoothly without unexpected delays.
6. Certification Standards
Certification standards, such as CE (Conformité Européenne) or UL (Underwriters Laboratories), indicate that a product meets certain safety and quality criteria. For B2B buyers, ensuring that a USB hub has the necessary certifications can be crucial for compliance with local regulations and for the safety of end users.
By grasping these technical properties and trade terms, international B2B buyers can make more informed decisions when sourcing USB hubs, ultimately leading to better outcomes for their businesses.
Navigating Market Dynamics and Sourcing Trends in the usb hub manufacturer Sector
What Are the Current Market Dynamics and Key Trends in the USB Hub Manufacturer Sector?
The global market for USB hubs is witnessing significant growth, driven by the increasing demand for connectivity solutions across various sectors, including consumer electronics, automotive, and industrial applications. With the rise of remote work and digital transformation, businesses are seeking efficient ways to connect multiple devices seamlessly. This trend is particularly pronounced in regions like Africa and South America, where the adoption of technology is accelerating rapidly.
Emerging B2B tech trends include the integration of USB hubs with smart technologies such as IoT and AI, enhancing the functionality of devices through advanced data management and connectivity options. Moreover, the shift towards USB-C technology is reshaping sourcing strategies, as manufacturers focus on producing versatile hubs that support a range of devices. International buyers, especially from Europe (notably Italy and the UK), are increasingly prioritizing products that comply with the latest standards, ensuring compatibility and longevity.
In terms of market dynamics, competitive pricing and product differentiation remain crucial. Manufacturers are exploring innovative designs and enhanced features, such as fast charging capabilities and data transfer speeds, to capture market share. B2B buyers should monitor these trends closely to make informed sourcing decisions that align with technological advancements and consumer preferences.
How Is Sustainability and Ethical Sourcing Shaping the USB Hub Manufacturing Sector?
Sustainability is becoming a pivotal consideration in the USB hub manufacturing sector. International B2B buyers are increasingly aware of the environmental impact of their sourcing decisions, prompting manufacturers to adopt sustainable practices. This includes using eco-friendly materials, reducing waste during production, and implementing energy-efficient processes.
Ethical sourcing is equally important, as businesses seek to establish transparent supply chains that minimize harm to communities and the environment. Manufacturers are responding by obtaining certifications such as ISO 14001 for environmental management and Fair Trade for ethical labor practices. These certifications not only enhance brand reputation but also appeal to socially conscious consumers and businesses alike.
Furthermore, the incorporation of recycled materials in USB hub production is gaining traction. Buyers should prioritize manufacturers that demonstrate a commitment to sustainability and ethical sourcing, as this can lead to long-term partnerships and a positive brand image in their respective markets.
What Is the Brief Evolution of the USB Hub Manufacturing Sector?
The USB hub manufacturing sector has evolved significantly since the introduction of the Universal Serial Bus standard in the mid-1990s. Initially designed to simplify the connection of peripherals to computers, USB technology has undergone several iterations, with USB 2.0 and USB 3.0 providing increased data transfer rates and power delivery capabilities.
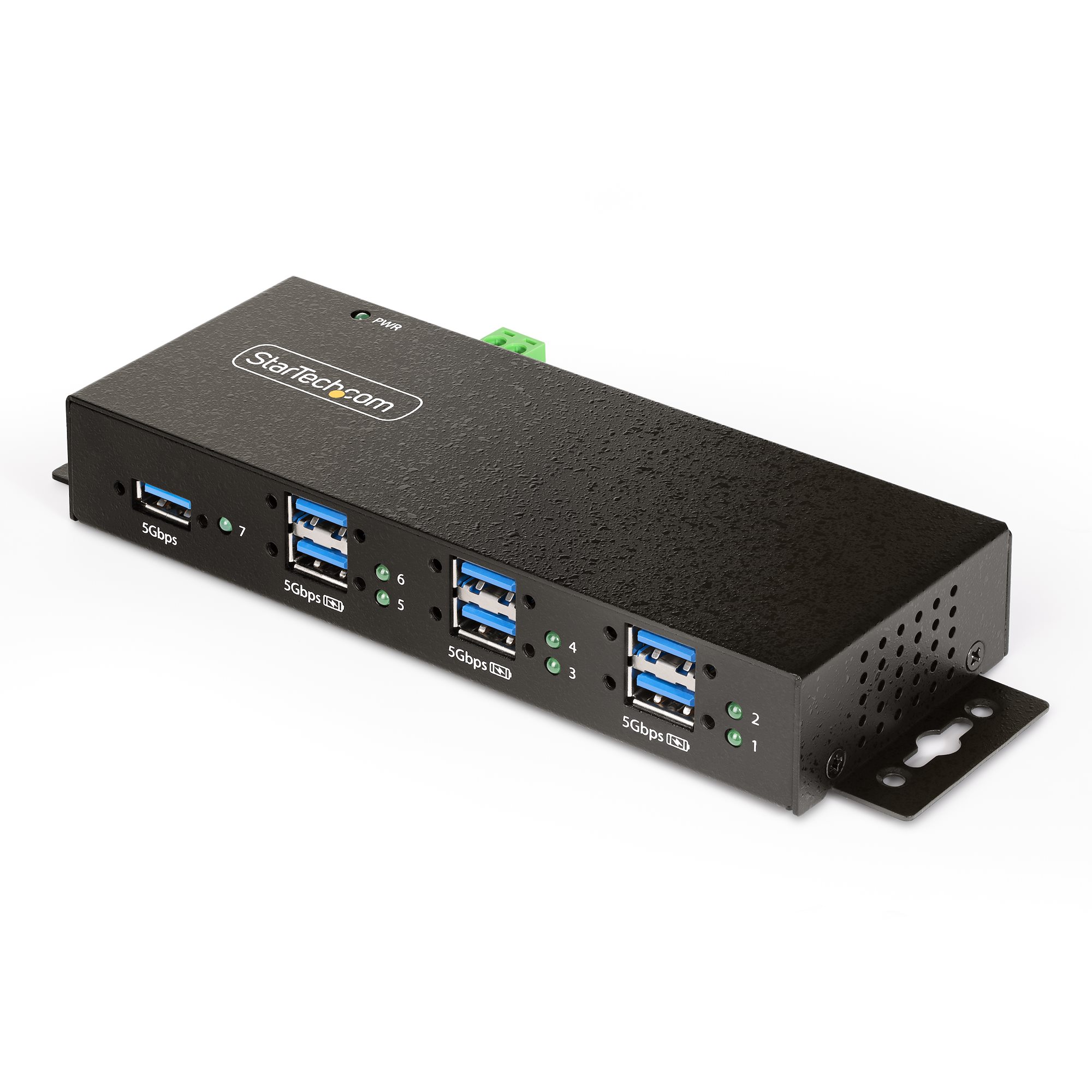
A stock image related to usb hub manufacturer.
The introduction of USB-C in recent years has further revolutionized the industry, offering a more versatile and user-friendly connection. This shift has led to the development of multi-port hubs that cater to the growing number of devices requiring connectivity, including laptops, smartphones, and gaming consoles.
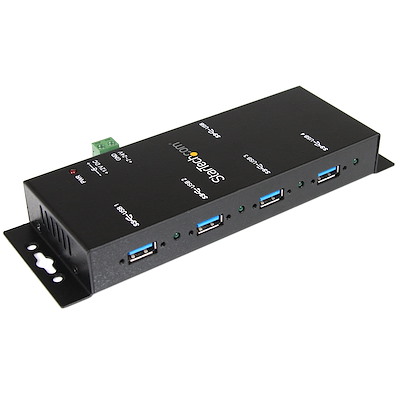
A stock image related to usb hub manufacturer.
As technology continues to advance, the USB hub sector is expected to further innovate, focusing on enhanced performance, compatibility, and sustainability. B2B buyers should keep abreast of these developments to ensure they are sourcing the most relevant and advanced products for their needs.
Frequently Asked Questions (FAQs) for B2B Buyers of usb hub manufacturer
-
How do I choose the right USB hub manufacturer for my business needs?
When selecting a USB hub manufacturer, consider factors such as the manufacturer’s reputation, certifications, and experience in the industry. Evaluate their product range to ensure they offer the specific types of USB hubs you require, such as powered or data transfer hubs. Additionally, request samples to assess product quality and reliability. Investigate their customer service and support capabilities, as effective communication can significantly impact your purchasing experience. -
What are the key quality assurance measures in USB hub manufacturing?
Quality assurance in USB hub manufacturing typically includes rigorous testing protocols, such as electrical performance tests, thermal testing, and compliance with international standards (e.g., CE, FCC). Manufacturers may implement ISO certifications to ensure consistent quality. Before finalizing a supplier, inquire about their quality control processes, including inspections at various production stages and final product testing to guarantee that the USB hubs meet your specifications and safety standards. -
What customization options are available when sourcing USB hubs?
Many USB hub manufacturers offer customization options to meet specific business needs. Customizations may include branding with your logo, different colors, varying port configurations, and tailored packaging. Some manufacturers may also provide options for specific functionalities, such as additional power ports or data transfer speeds. Discuss your requirements with potential suppliers to explore their customization capabilities and any associated costs. -
What are the minimum order quantities (MOQ) for USB hubs from manufacturers?
Minimum order quantities can vary significantly among USB hub manufacturers, often ranging from 100 to several thousand units. Factors influencing MOQ include the type of USB hub, customization requests, and the manufacturer’s production capacity. When evaluating suppliers, clarify their MOQ policies and explore opportunities for negotiating lower MOQs, especially if you are a new business or testing the market with a limited budget. -
How can I ensure timely delivery of USB hubs from international suppliers?
To ensure timely delivery from international suppliers, establish clear communication regarding lead times and shipping methods. Request a detailed timeline for production and shipping, considering potential delays such as customs clearance. Opt for manufacturers with reliable logistics partners and inquire about their experience in handling international shipments. Additionally, consider using Incoterms to clarify responsibilities for shipping and delivery between you and the supplier. -
What payment terms should I expect when sourcing USB hubs internationally?
Payment terms vary by manufacturer but typically include options such as advance payment, net 30/60/90 days, or letter of credit. Common practices involve a deposit (often 30%) before production and the balance upon completion or before shipping. Discuss payment options early in negotiations to ensure they align with your cash flow and financial management practices. Be cautious of manufacturers requesting full payment upfront, especially if they are new to you. -
How do I vet potential USB hub manufacturers for reliability?
Vetting potential USB hub manufacturers involves researching their business history, reading customer reviews, and checking references. Look for manufacturers with a strong track record of delivering quality products on time. Request certifications and compliance documents to confirm their adherence to industry standards. Conducting factory audits or visiting trade shows can also provide insights into their operations and capabilities, enhancing your confidence in their reliability. -
What are the common issues faced during the importation of USB hubs, and how can I mitigate them?
Common issues during the importation of USB hubs include customs delays, unexpected tariffs, and product compliance with local regulations. To mitigate these risks, ensure that your supplier provides all necessary documentation, including certificates of compliance. Research local import regulations and engage a customs broker to navigate the complexities of international shipping. Building a buffer in your timeline for potential delays can also help manage expectations and maintain your supply chain flow.
Important Disclaimer & Terms of Use
⚠️ Important Disclaimer
The information provided in this guide, including content regarding manufacturers, technical specifications, and market analysis, is for informational and educational purposes only. It does not constitute professional procurement advice, financial advice, or legal advice.
While we have made every effort to ensure the accuracy and timeliness of the information, we are not responsible for any errors, omissions, or outdated information. Market conditions, company details, and technical standards are subject to change.
B2B buyers must conduct their own independent and thorough due diligence before making any purchasing decisions. This includes contacting suppliers directly, verifying certifications, requesting samples, and seeking professional consultation. The risk of relying on any information in this guide is borne solely by the reader.
Strategic Sourcing Conclusion and Outlook for usb hub manufacturer
The landscape of USB hub manufacturing is evolving rapidly, driven by technological advancements and increasing demand from diverse markets. For international B2B buyers, particularly in regions such as Africa, South America, the Middle East, and Europe, strategic sourcing is essential. Key takeaways include the importance of evaluating supplier reliability, understanding regional compliance standards, and prioritizing quality and innovation in product offerings.
As connectivity needs grow, investing in USB hubs that offer enhanced functionality—such as fast data transfer rates and compatibility with various devices—will provide significant competitive advantages. Buyers should also consider suppliers that are responsive to market trends and capable of offering customized solutions.
Looking ahead, the demand for USB hubs is expected to surge, particularly as remote work and digitalization continue to shape business operations. International B2B buyers should act decisively to forge partnerships with reputable manufacturers that align with their strategic goals. By focusing on quality and innovation, businesses can ensure they are well-equipped to meet the future demands of a connected world. Embrace these opportunities and secure your supply chain today to stay ahead in this dynamic market.