Discover Top Timer Manufacturers: Your Ultimate Sourcing Guide (2025)
Introduction: Navigating the Global Market for timer manufacturer
In an increasingly interconnected world, international B2B buyers face the challenge of sourcing reliable timer manufacturers that meet their specific needs. Whether you are looking for countdown timers for industrial applications or precision timing devices for consumer electronics, the complexity of navigating this global market can be daunting. This guide provides a comprehensive overview of the timer manufacturing landscape, covering various types of timers, their applications, and essential considerations for supplier vetting.
Buyers from Africa, South America, the Middle East, and Europe—countries such as Nigeria and Italy—will benefit from insights into cost structures, quality standards, and logistical challenges specific to their regions. By delving into these critical areas, this guide empowers you to make informed purchasing decisions that align with your business objectives.
Additionally, we explore the latest trends in timer technology and the importance of compliance with international standards. With a focus on actionable insights, this guide will help you identify the right suppliers, negotiate favorable terms, and ultimately enhance your operational efficiency through the effective use of timers in your business processes. Navigate the global market confidently and strategically, ensuring that your timer sourcing aligns with your overall business strategy.
Understanding timer manufacturer Types and Variations
Type Name | Key Distinguishing Features | Primary B2B Applications | Brief Pros & Cons for Buyers |
---|---|---|---|
Digital Timers | Accurate, easy-to-read displays; programmable settings | Manufacturing, laboratories, education | Pros: Precision, ease of use; Cons: May require power source. |
Mechanical Timers | Analog design; often wind-up or plug-in | Agriculture, food processing | Pros: No power needed; Cons: Less accurate, limited features. |
Online Countdown Timers | Web-based, accessible from any device; customizable alerts | Event planning, marketing campaigns | Pros: Flexibility, easy sharing; Cons: Dependent on internet access. |
Industrial Timers | Rugged design for harsh environments; often integrated with machinery | Production lines, HVAC systems | Pros: Durability, reliability; Cons: Higher cost, complex installation. |
Smart Timers | IoT-enabled; can be controlled via apps; data tracking | Smart homes, energy management | Pros: Automation, remote monitoring; Cons: Security concerns, initial setup complexity. |
What Are the Key Characteristics of Digital Timers for B2B Use?
Digital timers are characterized by their precise timekeeping capabilities and user-friendly interfaces. They often feature programmable settings that allow users to customize countdowns or intervals. In B2B contexts, these timers are widely used in manufacturing and laboratory settings where accuracy is critical. Buyers should consider the ease of programming and the display size, ensuring it meets the needs of their specific applications.
How Do Mechanical Timers Differ from Other Types?
Mechanical timers, often analog in design, operate without electricity, making them ideal for environments where power sources are limited. They are commonly used in agriculture and food processing, where simple timing tasks are required. While these timers are reliable and cost-effective, buyers should be aware of their limitations in precision and features compared to digital options.
Why Choose Online Countdown Timers for Business Applications?
Online countdown timers provide flexibility and accessibility, allowing users to set and share timers easily across various devices. They are particularly useful for event planning and marketing campaigns, where timing is crucial. However, businesses should ensure consistent internet access to utilize these tools effectively, as connectivity issues can hinder their functionality.
What Are the Benefits of Using Industrial Timers?
Industrial timers are designed to withstand harsh environments, making them suitable for production lines and HVAC systems. Their rugged construction ensures reliability in demanding settings. While they may come at a higher cost and require complex installation, the durability and long-term performance they offer can justify the investment for businesses focused on efficiency and productivity.
How Do Smart Timers Enhance B2B Operations?
Smart timers leverage IoT technology to provide advanced features like remote monitoring and automation. They are increasingly popular in smart homes and energy management systems. While they offer significant benefits in terms of convenience and data tracking, buyers must consider potential security risks and the complexity of initial setup when integrating these systems into their operations.
Related Video: Heat Pump Thermostat O, B, and C Terminal Variations Explained
Key Industrial Applications of timer manufacturer
Industry/Sector | Specific Application of Timer Manufacturer | Value/Benefit for the Business | Key Sourcing Considerations for this Application |
---|---|---|---|
Manufacturing | Automated Production Line Timing | Enhances operational efficiency and reduces downtime | Reliability, precision, and compatibility with existing systems |
Food & Beverage | Cooking and Baking Timers | Ensures product consistency and quality control | Accuracy, durability, and ease of use |
Healthcare | Medical Equipment Monitoring | Improves patient safety and compliance with regulations | Compliance with medical standards and reliability |
Agriculture | Irrigation Scheduling | Optimizes water usage and boosts crop yield | Weather-resistant features and energy efficiency |
Event Management | Countdown Timers for Events | Creates anticipation and enhances attendee experience | Visibility, sound options, and ease of setup |
How are Timers Used in Manufacturing for Enhanced Efficiency?
In the manufacturing sector, timer manufacturers provide solutions for automated production line timing. Timers help synchronize machinery operations, ensuring that each step in the production process occurs without unnecessary delays. This leads to enhanced operational efficiency and reduced downtime, which is crucial for businesses looking to maximize productivity. For international buyers, especially in regions like Africa and South America, sourcing timers that are reliable and precise is essential to avoid disruptions in production.
What Role Do Timers Play in the Food & Beverage Industry?
In the food and beverage industry, timers are vital for cooking and baking processes. They ensure that products are cooked for the right amount of time, maintaining consistency and quality. This is particularly important for businesses aiming to meet regulatory standards and consumer expectations. Buyers should consider the accuracy and durability of timers, as well as their ease of use, to ensure they can withstand the often demanding kitchen environment.
How Do Timers Enhance Patient Safety in Healthcare?
Timers play a crucial role in healthcare, particularly in the monitoring of medical equipment. They help track vital parameters, ensuring that readings are taken at the correct intervals, which is essential for patient safety. Compliance with healthcare regulations is paramount, and buyers in this sector must prioritize sourcing timers that meet stringent medical standards while maintaining reliability. This is particularly relevant for buyers in the Middle East and Europe, where regulations can be stringent.
How Can Timers Optimize Water Usage in Agriculture?
In agriculture, timers are used for irrigation scheduling, allowing farmers to optimize water usage and enhance crop yield. By automating watering schedules, farmers can ensure their crops receive the right amount of water at the right time, which is crucial in regions facing water scarcity. Buyers should look for timers with weather-resistant features and energy efficiency to ensure they are suitable for outdoor use, particularly in diverse climates across Africa and South America.
What Benefits Do Countdown Timers Offer in Event Management?
Countdown timers are essential tools in event management, creating anticipation and enhancing the attendee experience. They can be used for various events, from conferences to concerts, ensuring that schedules are adhered to and that audiences remain engaged. When sourcing countdown timers, buyers should consider visibility, sound options, and ease of setup, as these factors significantly impact the effectiveness of the timer in a live event setting. This is particularly relevant for event planners in Europe, where event experiences are increasingly competitive.
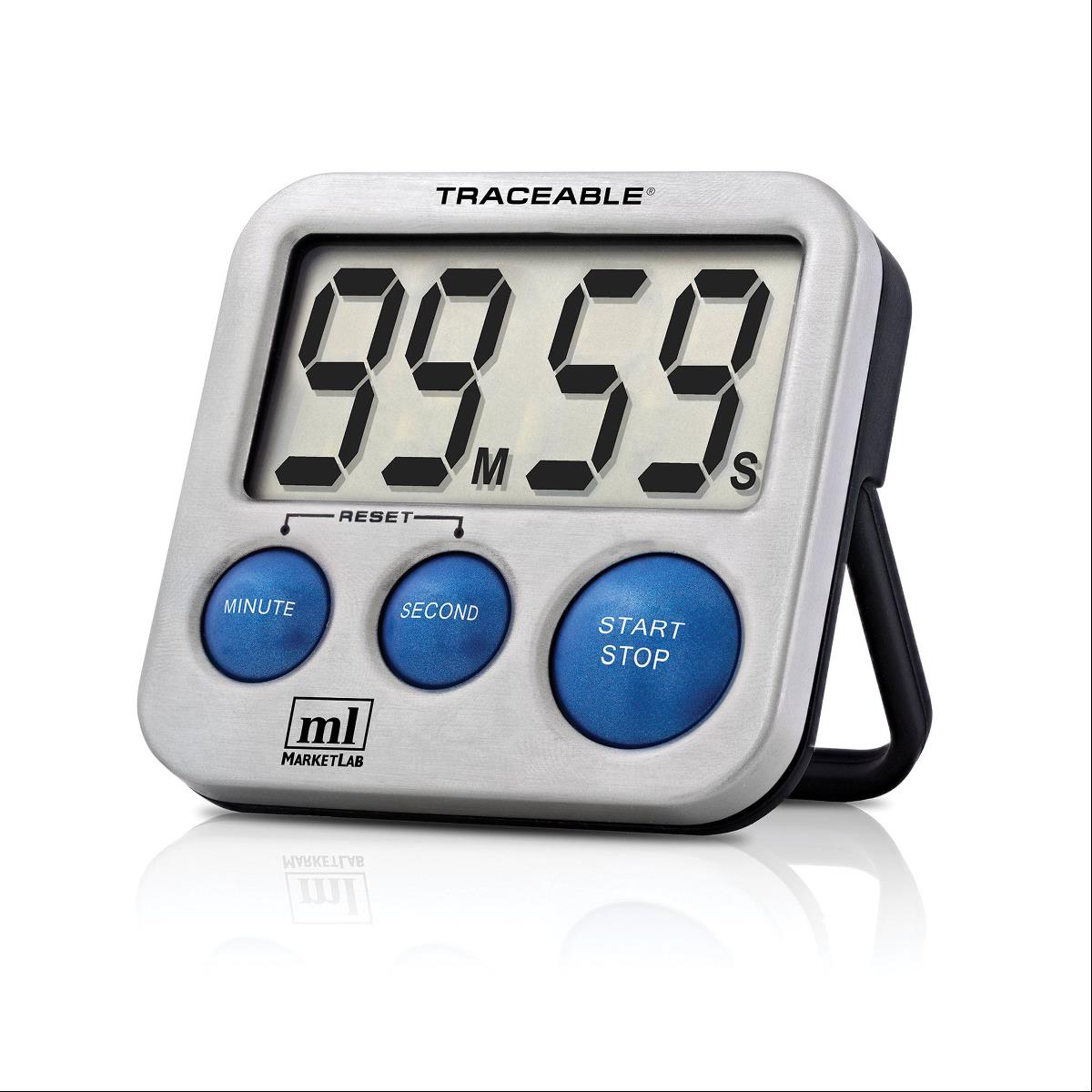
A stock image related to timer manufacturer.
Related Video: Types Of Flowmeters And Their Industrial Applications.
3 Common User Pain Points for ‘timer manufacturer’ & Their Solutions
Scenario 1: Sourcing Reliable Timer Manufacturers for Bulk Orders
The Problem: A procurement manager in South America faces the challenge of finding reliable timer manufacturers who can meet specific technical requirements while also delivering products in bulk. With limited local options and fluctuating international shipping costs, there’s a constant worry about product quality, delivery timelines, and potential communication barriers. This situation can lead to missed project deadlines and increased costs if the wrong supplier is chosen.
The Solution: To overcome this challenge, buyers should start by conducting thorough market research to identify reputable timer manufacturers with a proven track record. Utilize platforms such as Alibaba or global trade directories to locate suppliers that specialize in timers suited for your industry. Once potential manufacturers are identified, request detailed product specifications and past performance reviews from other clients. Establish a clear communication channel to discuss requirements and expectations. Conduct sample testing before committing to bulk orders to ensure that the timers meet your quality standards. Finally, negotiate terms that include penalties for late delivery, which can protect your business against potential delays.
Scenario 2: Ensuring Compatibility with Existing Systems
The Problem: A technology firm in Europe is integrating timers into its automation systems, but the selected timers are not compatible with existing protocols. This incompatibility can lead to system failures, increased downtime, and additional costs for redesigning the automation framework. The technical team is frustrated, as they need to find a solution quickly to avoid impacting project timelines.
The Solution: To prevent compatibility issues, it’s crucial for buyers to thoroughly assess the technical specifications of timers before purchase. Engage in pre-purchase consultations with manufacturers to discuss your existing systems and the specific functionalities required. Request documentation on compatibility with different protocols (such as MQTT, Modbus, or BACnet) and inquire about customizable options. If compatibility is uncertain, consider investing in a consultancy service that specializes in systems integration. They can help bridge the gap between your requirements and the manufacturer’s offerings, ensuring seamless integration and functionality.
Scenario 3: Managing Long-Term Support and Maintenance
The Problem: A manufacturing plant in Africa has installed timers for various processes, but as time progresses, the plant faces challenges with maintaining these devices. The original manufacturer provides limited support, leading to confusion about replacement parts and software updates. Without proper maintenance, the timers could malfunction, resulting in costly production downtime.
The Solution: To ensure long-term support and maintenance, buyers should prioritize manufacturers that offer comprehensive after-sales services. During the procurement process, inquire about warranty periods, availability of spare parts, and the manufacturer’s commitment to ongoing technical support. Consider establishing a service level agreement (SLA) that outlines response times for service requests and maintenance schedules. Additionally, training your in-house team on basic maintenance and troubleshooting can empower them to address minor issues without waiting for external support. Building a relationship with the manufacturer for ongoing communication can facilitate quick responses to future needs and ensure the longevity of the timers in use.
Strategic Material Selection Guide for timer manufacturer
What are the Key Materials Used in Timer Manufacturing?
When selecting materials for timer manufacturing, several factors must be considered, including performance, durability, cost, and compliance with international standards. Below, we analyze four common materials used in the production of timers, focusing on their properties, advantages, disadvantages, and specific considerations for international B2B buyers.
How Does Plastic Perform in Timer Manufacturing?
Key Properties: Plastics, such as polycarbonate and ABS, are lightweight, corrosion-resistant, and can withstand moderate temperatures. They are often rated for temperatures up to 100°C and provide good electrical insulation.
Pros & Cons: The primary advantage of using plastic is its low cost and ease of manufacturing, which allows for complex shapes and designs. However, plastics can be less durable than metals and may degrade under extreme conditions, such as high temperatures or exposure to UV light.
Impact on Application: Plastics are suitable for timers that are not exposed to harsh environments. However, they may not be ideal for applications requiring high-temperature resistance or exposure to chemicals.
Considerations for International Buyers: Buyers should ensure that the selected plastic meets local regulations and standards, such as ASTM or DIN specifications. Additionally, sourcing from suppliers with a good reputation for quality control is crucial.
What Role Does Metal Play in Timer Manufacturing?
Key Properties: Metals like aluminum and stainless steel are known for their strength and durability. They can withstand high temperatures and pressures, with ratings often exceeding 200°C for aluminum and 300°C for stainless steel.
Pros & Cons: The key advantage of metals is their robustness and resistance to wear and tear. However, they are typically more expensive than plastics and can complicate the manufacturing process due to the need for machining and finishing.
Impact on Application: Metal timers are ideal for industrial applications where durability and temperature resistance are critical. They are suitable for environments with high humidity or exposure to corrosive substances.
Considerations for International Buyers: Compliance with international standards is essential, especially for buyers in Europe and the Middle East, where regulations may be stricter. Understanding the specific grades of metals and their certifications is vital for ensuring product quality.
How Do Ceramics Enhance Timer Performance?
Key Properties: Ceramics are highly resistant to heat and corrosion, withstanding temperatures up to 1,000°C. They also exhibit excellent electrical insulation properties.
Pros & Cons: The major advantage of ceramics is their ability to function in extreme conditions without degrading. However, they are brittle and can be prone to cracking under stress, making them less suitable for high-impact applications.
Impact on Application: Ceramics are particularly beneficial in timers used in high-temperature environments, such as ovens or industrial furnaces. Their stability ensures accurate timing even in challenging conditions.
Considerations for International Buyers: Buyers should look for ceramics that comply with international standards, particularly in applications involving food safety or electronics. Understanding the specific properties of different ceramic materials is crucial for optimal performance.
What About Composite Materials in Timer Manufacturing?
Key Properties: Composite materials, such as fiberglass and carbon fiber, combine the benefits of plastics and metals. They offer high strength-to-weight ratios and can be engineered for specific performance characteristics.
Pros & Cons: The primary advantage of composites is their versatility and ability to be tailored for specific applications. However, they are often more expensive and may require specialized manufacturing techniques.
Impact on Application: Composites are suitable for timers that require both lightweight construction and durability, making them ideal for portable or high-performance devices.
Considerations for International Buyers: Buyers need to ensure that composite materials meet relevant safety and performance standards. The complexity of sourcing and manufacturing composites may also require closer collaboration with suppliers.
Summary of Material Selection for Timer Manufacturing
Material | Typical Use Case for Timer Manufacturer | Key Advantage | Key Disadvantage/Limitation | Relative Cost (Low/Med/High) |
---|---|---|---|---|
Plastic | Consumer timers, low-stress applications | Low cost, easy to mold | Less durable, temperature sensitive | Low |
Metal | Industrial timers, high-stress applications | High durability, excellent temperature resistance | Higher cost, complex manufacturing | High |
Ceramic | High-temperature applications, industrial use | Exceptional heat and corrosion resistance | Brittle, prone to cracking | Medium |
Composite | Lightweight, portable timers | High strength-to-weight ratio | Expensive, requires specialized processing | High |
This guide provides a comprehensive overview of the materials commonly used in timer manufacturing, equipping international B2B buyers with the insights needed to make informed decisions based on their specific applications and market requirements.
In-depth Look: Manufacturing Processes and Quality Assurance for timer manufacturer
What Are the Main Stages in the Manufacturing Process of Timers?
Manufacturing timers involves several key stages that ensure the final product meets quality and functionality standards. The main stages include:
-
Material Preparation: The first step in timer manufacturing is sourcing high-quality materials. This typically includes electronic components such as microcontrollers, resistors, capacitors, and casing materials. B2B buyers should inquire about the suppliers’ sourcing practices, ensuring they use reliable and certified materials to enhance product durability.
-
Forming: This stage involves shaping the materials into the desired form. Techniques can vary depending on the timer type. For instance, plastic parts may be injection molded, while metal components could be stamped or machined. Understanding the forming techniques used can help buyers assess the potential quality and performance of the timer.
-
Assembly: Once the components are prepared, they are assembled. This process can be manual or automated, depending on the manufacturer’s capabilities. Automated assembly often leads to higher precision and consistency. Buyers should look for manufacturers that utilize advanced assembly technologies to minimize errors and enhance efficiency.
-
Finishing: The final stage involves polishing, coating, or otherwise finishing the timer to improve aesthetics and protect against environmental factors. Common finishing methods include painting, anodizing, or applying protective films. The quality of the finishing process can significantly impact the timer’s durability and marketability.
How Is Quality Assurance Ensured During Timer Manufacturing?
Quality assurance (QA) is critical in the manufacturing of timers, ensuring that products meet both international and industry-specific standards. Key aspects of QA include:
-
International Standards Compliance: Most reputable timer manufacturers adhere to international quality standards such as ISO 9001, which focuses on quality management systems. Buyers should verify that potential suppliers have these certifications, as they indicate a commitment to maintaining high-quality processes.
-
Industry-Specific Certifications: Depending on the application, timers may require additional certifications like CE marking for European markets or API standards for industrial applications. These certifications ensure that the products comply with regional safety and quality regulations.
-
Quality Control Checkpoints: Effective quality control (QC) processes are implemented at various stages of manufacturing:
– Incoming Quality Control (IQC): This involves inspecting raw materials before they enter the production process. Suppliers should have documented procedures for this stage.
– In-Process Quality Control (IPQC): Ongoing checks during manufacturing help catch defects early. This may include visual inspections and functional testing of components.
– Final Quality Control (FQC): Before shipment, finished products undergo thorough testing to ensure they meet specifications. This may involve performance testing, durability tests, and compliance checks.
What Common Testing Methods Are Used in Timer Manufacturing?
Testing is a vital part of the QA process for timers. Common methods include:
- Functional Testing: This ensures the timer operates correctly under various conditions. For instance, timers may be tested for accuracy and response time.
- Environmental Testing: Timers should withstand different environmental conditions such as temperature fluctuations and humidity levels. Environmental testing simulates these conditions to ensure reliability.
- Electrical Testing: Assessing the electrical components for safety and performance is crucial. This includes checking for short circuits, grounding issues, and overall electrical integrity.
How Can B2B Buyers Verify Supplier Quality Control?
B2B buyers, particularly those from Africa, South America, the Middle East, and Europe, should take proactive steps to verify the quality control processes of timer manufacturers. Here are several methods:
-
Supplier Audits: Conducting on-site audits allows buyers to evaluate the manufacturing processes and QC systems in place. This provides insight into the supplier’s commitment to quality and adherence to standards.
-
Quality Reports: Requesting detailed quality reports can help buyers understand the supplier’s historical performance, including defect rates and corrective actions taken.
-
Third-Party Inspections: Engaging third-party inspection services can provide an unbiased assessment of the manufacturer’s quality control practices. These inspections can be scheduled at various stages of production, offering peace of mind to buyers.
What Are the Quality Control and Certification Nuances for International B2B Buyers?
International buyers must be aware of specific nuances related to quality control and certification, particularly when sourcing from diverse regions:
-
Cultural and Regulatory Differences: Understanding local regulations and cultural practices around quality can affect supplier reliability. For instance, some regions may have less stringent enforcement of quality standards, impacting product consistency.
-
Documentation Requirements: Buyers should ensure that suppliers provide adequate documentation for all certifications and quality checks. This is particularly important when importing products across borders, as customs may require proof of compliance.
-
Communication Channels: Establishing clear communication channels with suppliers can facilitate better quality management. B2B buyers should ensure they have direct access to quality assurance teams for timely updates and issue resolution.
By focusing on these aspects, B2B buyers can make informed decisions when selecting timer manufacturers, ensuring they receive high-quality products that meet their operational needs.
Practical Sourcing Guide: A Step-by-Step Checklist for ‘timer manufacturer’
The following step-by-step guide is designed to assist international B2B buyers, particularly from Africa, South America, the Middle East, and Europe, in sourcing timer manufacturers effectively. This checklist will help streamline your procurement process and ensure you find the right partner for your needs.
Step 1: Define Your Technical Specifications
Before initiating your search for a timer manufacturer, it’s essential to clearly outline your technical specifications. This includes understanding the type of timer you need (e.g., digital, mechanical, programmable) and the specific features that are critical for your application.
- Consider usage scenarios: Will the timer be used in industrial, commercial, or residential settings?
- Identify required certifications: Ensure compliance with local and international standards.
Step 2: Conduct Market Research
Engage in comprehensive market research to identify potential timer manufacturers that align with your specifications. Utilize online resources, industry reports, and trade publications to gather data on various suppliers.
- Leverage online platforms: Use B2B marketplaces like Alibaba or Global Sources to find reputable manufacturers.
- Check industry forums: Participate in discussions and ask for recommendations from industry peers.
Step 3: Evaluate Potential Suppliers
Before committing, it’s crucial to vet suppliers thoroughly. Request company profiles, case studies, and references from buyers in a similar industry or region. Don’t just rely on their website.
- Assess production capabilities: Ensure they can meet your volume requirements and delivery timelines.
- Inquire about quality assurance processes: Understand how they maintain product quality throughout the manufacturing process.
Step 4: Request Samples
Once you have shortlisted potential suppliers, request samples of their products. This step is vital for assessing the quality and functionality of the timers.
- Evaluate performance: Test the timers under real-world conditions to see if they meet your needs.
- Check for customization options: Determine if the supplier can tailor products to your specific requirements.
Step 5: Verify Supplier Certifications
Before finalizing your supplier, ensure they possess the necessary certifications. This is particularly important for compliance with safety and quality standards.
- Look for ISO certifications: Such certifications indicate adherence to international quality management standards.
- Confirm compliance with local regulations: This ensures that products can be sold and used in your target markets without legal issues.
Step 6: Negotiate Terms and Conditions
Effective negotiation can lead to better pricing and terms. Discuss payment terms, delivery schedules, and warranty policies to ensure both parties are aligned.
- Establish clear payment terms: Consider options like letters of credit or staggered payments based on milestones.
- Clarify warranty and return policies: This protects your investment and ensures you have recourse if the products do not meet expectations.
Step 7: Finalize Contractual Agreement
Once all terms are agreed upon, draft a comprehensive contract that outlines all aspects of the partnership. This should include pricing, delivery timelines, quality expectations, and penalty clauses for non-compliance.
- Include performance metrics: Specify KPIs that the supplier must meet to ensure accountability.
- Ensure legal review: Consult with legal experts to validate the contract’s terms before signing.
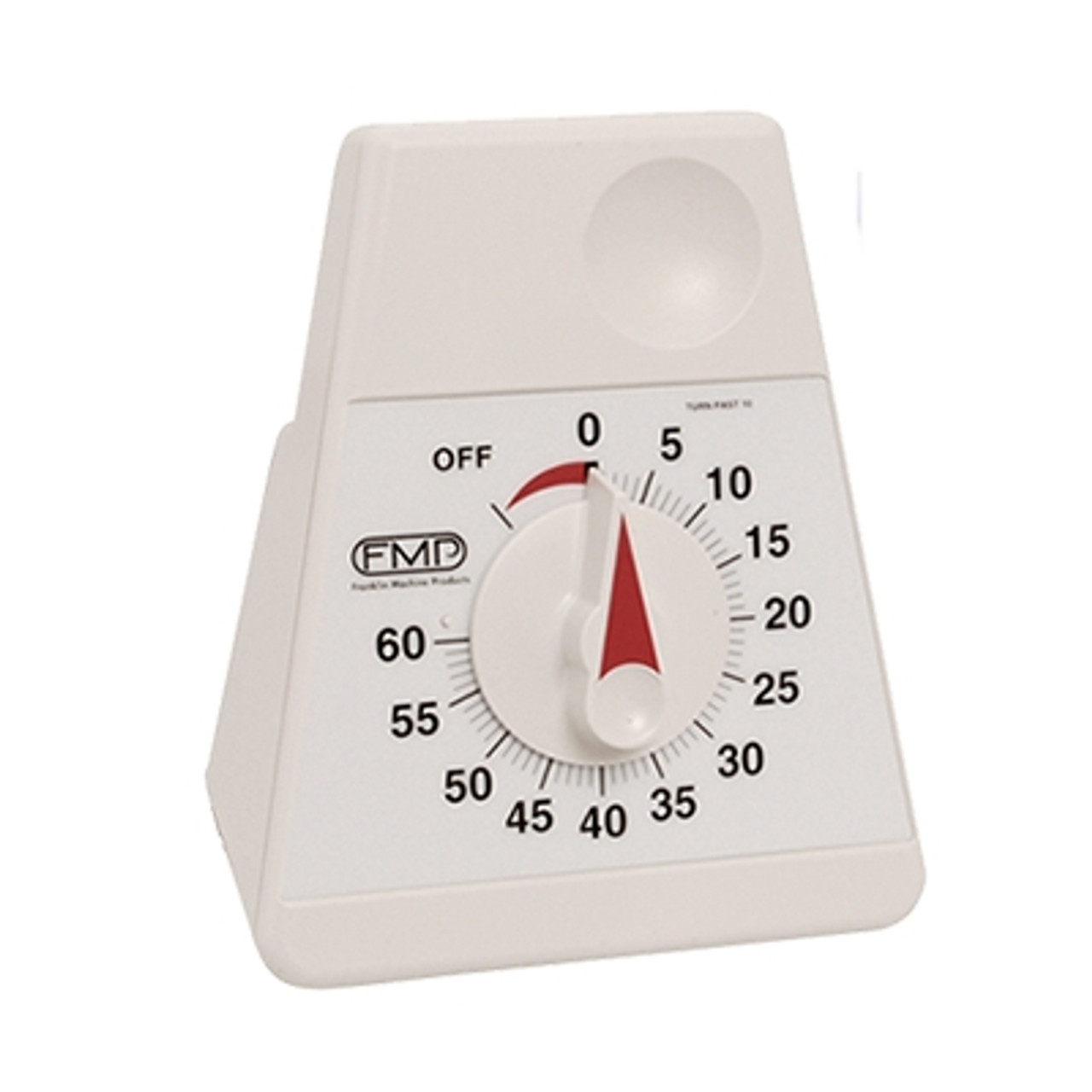
A stock image related to timer manufacturer.
By following this practical sourcing guide, you can navigate the complexities of procuring timers from manufacturers effectively, ensuring a successful partnership that meets your business needs.
Comprehensive Cost and Pricing Analysis for timer manufacturer Sourcing
What Are the Key Cost Components in Timer Manufacturing?
Understanding the cost structure of timer manufacturing is crucial for international B2B buyers looking to optimize their sourcing strategy. The main cost components include:
-
Materials: The type of materials used (e.g., plastics, metals, electronic components) significantly affects the overall cost. For high-quality timers, sourcing certified components can enhance product reliability but may increase material costs.
-
Labor: Labor costs vary greatly by region, with manufacturers in regions like Asia often offering lower labor rates compared to Europe or the Middle East. Understanding local wage rates and labor laws can help buyers gauge potential cost variations.
-
Manufacturing Overhead: This includes utilities, maintenance, and other indirect costs associated with the production process. Efficient factories may have lower overhead, allowing for more competitive pricing.
-
Tooling: The initial investment in tooling can be substantial, especially for customized timer designs. Buyers should inquire about tooling costs and how they impact the overall pricing structure.
-
Quality Control (QC): Ensuring quality through rigorous testing and certification processes adds to the cost but is essential for maintaining product standards. Buyers should consider the implications of QC on pricing and reliability.
-
Logistics: Shipping costs, insurance, and customs duties can vary significantly depending on the location of the supplier and the destination market. Understanding Incoterms is vital for managing these costs.
-
Margin: Manufacturers will typically include a profit margin in their pricing. This margin can vary based on competition, demand, and the perceived value of the product.
How Do Price Influencers Affect Timer Manufacturing Costs?
Several factors can influence the price of timers significantly, impacting international buyers:
-
Volume and Minimum Order Quantity (MOQ): Higher order volumes often lead to lower per-unit costs. Buyers should negotiate MOQs to optimize cost savings, especially when dealing with large-scale projects.
-
Specifications and Customization: Custom features or specifications can drive up costs. Clearly defining requirements upfront can help avoid unexpected price increases.
-
Material Choices: Opting for standard materials rather than specialized options can reduce costs. Buyers should evaluate whether premium materials are necessary for their applications.
-
Quality and Certifications: Timers that meet international quality standards (like ISO) may come at a higher price but can reduce the risk of failures and enhance brand reputation.
-
Supplier Factors: The reputation and reliability of suppliers can influence pricing. Established manufacturers may charge a premium for their track record of quality and service.
-
Incoterms: The choice of Incoterms can affect shipping costs and responsibilities. Understanding terms like FOB (Free on Board) and CIF (Cost Insurance and Freight) is crucial for accurate cost forecasting.
What Are Some Effective Buyer Tips for Cost Efficiency in Timer Sourcing?
To maximize cost efficiency while sourcing timers, international buyers should consider the following strategies:
-
Negotiate Terms: Don’t hesitate to negotiate pricing, MOQ, and payment terms. Suppliers may be willing to offer discounts for larger orders or long-term contracts.
-
Evaluate Total Cost of Ownership (TCO): Consider not just the purchase price but the long-term costs associated with maintenance, logistics, and potential product failures. This holistic view can lead to better purchasing decisions.
-
Research Supplier Backgrounds: Conduct due diligence on potential suppliers, focusing on their production capabilities, quality standards, and customer reviews. A reliable supplier can save costs associated with defects and delays.
-
Stay Informed About Market Trends: Keeping abreast of market conditions can provide leverage in negotiations. Awareness of fluctuations in material costs or labor rates can inform timing for orders.
-
Understand Regional Differences: Different regions may have varying cost structures. Buyers from Africa, South America, the Middle East, and Europe should consider these differences when selecting suppliers to ensure they are getting competitive pricing.
Disclaimer on Pricing
Prices mentioned in this analysis are indicative and subject to change based on market conditions, exchange rates, and specific buyer requirements. Always request updated quotes from suppliers to obtain accurate pricing for your sourcing needs.
Alternatives Analysis: Comparing timer manufacturer With Other Solutions
Exploring Alternatives to Timer Manufacturer Solutions
In the realm of time management tools, it’s essential to explore alternatives to traditional timer manufacturers. Various technologies and methodologies can fulfill similar functions while offering distinct advantages and disadvantages. This analysis will compare timer manufacturers with online timer solutions and smart device timers, providing actionable insights for international B2B buyers.
Comparison Table of Timer Solutions
Comparison Aspect | Timer Manufacturer | Online Timer Solutions | Smart Device Timers |
---|---|---|---|
Performance | High accuracy | Moderate accuracy | High accuracy |
Cost | Higher upfront cost | Free to low cost | Varies (medium to high) |
Ease of Implementation | Complex installation | Instant access online | User-friendly app setup |
Maintenance | Regular servicing needed | No maintenance required | Software updates needed |
Best Use Case | Industrial applications | Personal and small business | Smart home integration |
What Are the Advantages and Disadvantages of Online Timer Solutions?
Online timer solutions, such as those found on platforms like WebUhr.de, offer a cost-effective alternative. These solutions are typically free or low-cost and provide instant access without any installation requirements. Users can set timers for various durations and even share them with others. However, their performance may vary based on internet connectivity, and they may lack advanced features required for industrial applications. They are best suited for personal use or small businesses that need straightforward time management without complex setups.
How Do Smart Device Timers Compare?
Smart device timers, integrated into home automation systems, provide high accuracy and convenience. They can be controlled via mobile applications and offer features such as voice activation and remote access. This technology allows for seamless integration with other smart devices, enhancing overall functionality. However, the cost can vary significantly, depending on the brand and features. Additionally, users must stay updated with software updates to ensure optimal performance. Smart device timers are ideal for businesses looking to enhance efficiency through automation and smart technology.
Conclusion: How to Choose the Right Timer Solution for Your Business?
When selecting the right timer solution, B2B buyers should consider their specific needs, budget constraints, and the context in which the timer will be used. Timer manufacturers may be the best fit for industries requiring precision and reliability. In contrast, online timer solutions are perfect for cost-sensitive users seeking simplicity and ease of access. Smart device timers cater to organizations aiming to integrate time management into broader smart technology ecosystems. Each option has its unique strengths, and understanding these will enable buyers to make informed decisions tailored to their operational requirements.
Essential Technical Properties and Trade Terminology for timer manufacturer
What Are the Essential Technical Properties for Timer Manufacturers?
When sourcing timers for various applications, understanding the essential technical properties is crucial. Here are some key specifications that international B2B buyers should consider:
-
Material Grade
The material from which a timer is made significantly impacts its durability and performance. Common materials include plastic, metal, and silicone. For instance, high-grade plastics may offer better resistance to heat and moisture, making them suitable for outdoor applications. Buyers should consider the operational environment when selecting the appropriate material grade. -
Tolerance
Tolerance refers to the allowable deviation from a specified measurement. In timers, this is particularly important for accuracy. For example, a timer with a tolerance of ±1 second is more precise than one with ±5 seconds. Buyers need to assess the required accuracy based on the application, as higher tolerances often correlate with higher costs. -
Power Source
Timers can be powered by various sources, including batteries, AC power, or solar energy. The choice of power source affects operational costs and convenience. For instance, battery-operated timers are portable and easy to set up but may require frequent battery replacements. Understanding the power requirements helps in selecting the right model for specific use cases. -
Display Type
The display type—digital or analog—can influence usability and readability. Digital displays often provide clearer readings and are easier to read from a distance, while analog displays may be preferred for aesthetic reasons in certain applications. Buyers should consider the context in which the timer will be used to choose the most suitable display type. -
Programmable Features
Many modern timers come with programmable settings, allowing users to set multiple alarms or countdowns. This feature is valuable for businesses that need to manage various operations simultaneously. Buyers should evaluate how many programmable features are necessary to meet their operational needs.
What Trade Terminology Should B2B Buyers Know When Purchasing Timers?
Understanding industry jargon can greatly facilitate negotiations and purchasing processes. Here are some common terms that buyers should be familiar with:
-
OEM (Original Equipment Manufacturer)
An OEM refers to a company that produces parts or equipment that may be marketed by another manufacturer. When sourcing timers, buyers may deal directly with OEMs to obtain customized products tailored to their specifications. -
MOQ (Minimum Order Quantity)
MOQ indicates the smallest quantity of a product that a supplier is willing to sell. Understanding the MOQ is essential for budgeting and inventory management. Buyers should negotiate MOQs to align with their needs without overcommitting to excess inventory. -
RFQ (Request for Quotation)
An RFQ is a document sent to suppliers requesting pricing for specific products or services. This is a common practice in B2B transactions, allowing buyers to compare costs and ensure they are receiving competitive pricing.
-
Incoterms (International Commercial Terms)
Incoterms are a set of international rules that define the responsibilities of sellers and buyers in shipping contracts. Understanding these terms is vital for buyers to know who bears the cost and risk during transportation, ensuring smoother international transactions. -
Lead Time
Lead time refers to the time taken from placing an order to receiving the goods. It is a critical factor in supply chain management. Buyers should inquire about lead times to plan their inventory and production schedules effectively. -
Certification Standards
Certification standards indicate whether a product meets specific industry regulations or quality benchmarks. Common certifications for timers may include ISO standards or CE marking in Europe. Buyers should verify certifications to ensure compliance with local regulations and quality assurance.
By grasping these essential technical properties and industry terms, B2B buyers can make informed decisions when sourcing timers, leading to better procurement outcomes and enhanced operational efficiency.
Navigating Market Dynamics and Sourcing Trends in the timer manufacturer Sector
What are the Key Market Dynamics and Trends in the Timer Manufacturing Sector?
The timer manufacturing sector is experiencing significant growth driven by various global factors. One of the primary drivers is the increasing demand for precision timing in industrial applications, particularly in manufacturing and assembly lines. Technological advancements, such as the integration of IoT devices, are reshaping how timers are utilized, allowing for enhanced automation and real-time monitoring. International B2B buyers, especially from regions like Africa, South America, the Middle East, and Europe, should pay attention to these trends as they indicate a shift towards more sophisticated timer solutions that cater to specific industry needs.
Emerging sourcing trends also highlight a growing preference for digital and programmable timers over traditional mechanical options. As industries become more automated, the need for timers that can interface with other systems is paramount. This shift is particularly relevant for buyers in regions like Nigeria, where industrial growth is accelerating. Moreover, the rise of e-commerce platforms is transforming how businesses source timers, enabling them to access a broader range of suppliers and products than ever before. Buyers should leverage these platforms to negotiate better deals and explore innovative timer technologies.
How Does Sustainability Impact Sourcing Decisions in Timer Manufacturing?
Sustainability is becoming a critical consideration for B2B buyers in the timer manufacturing sector. The environmental impact of manufacturing processes and the materials used in timer production are under increased scrutiny. Buyers are encouraged to prioritize suppliers who demonstrate a commitment to sustainable practices, such as using eco-friendly materials and reducing waste in their production processes.
Ethical sourcing is equally essential, as businesses are increasingly held accountable for their supply chain practices. Buyers should seek suppliers with transparent supply chains and certifications that attest to their environmental and social responsibility, such as ISO 14001 for environmental management. Additionally, the adoption of “green” materials, such as recycled plastics or sustainably sourced metals, can enhance a company’s market appeal and compliance with global sustainability standards. By prioritizing sustainability and ethical sourcing, buyers can not only mitigate risks but also align with the growing consumer demand for environmentally responsible products.
What is the Historical Context of Timer Manufacturing Relevant to B2B Buyers?
The timer manufacturing industry has evolved significantly since its inception in the early 20th century. Initially focused on mechanical designs, the industry has transitioned to electronic and digital timers, reflecting broader technological advancements. The introduction of microcontrollers in the 1970s revolutionized timer capabilities, allowing for programmable functions and improved accuracy.
In recent years, the shift towards smart technology has further transformed the landscape. Timers are now integral components in smart homes and industrial automation, with applications ranging from simple countdowns to complex scheduling tasks integrated into larger systems. For B2B buyers, understanding this evolution is crucial as it informs the types of products available and the technological capabilities that can meet modern demands. Recognizing the historical context helps buyers make informed decisions about sourcing timers that align with their operational needs and technological aspirations.
Frequently Asked Questions (FAQs) for B2B Buyers of timer manufacturer
-
How do I choose the right timer manufacturer for my business needs?
Choosing the right timer manufacturer involves several key steps. Begin by identifying your specific requirements, such as the type of timers you need (digital, mechanical, programmable) and their intended applications. Research potential manufacturers by checking their reputation, experience, and production capabilities. Review client testimonials and case studies to gauge their reliability. Additionally, consider visiting their facilities if possible, or scheduling virtual meetings to discuss your needs and assess their customer service. -
What factors should I consider when vetting a timer supplier?
When vetting a timer supplier, focus on their certifications, quality control processes, and production capacity. Verify if they comply with international standards relevant to your region, such as ISO certifications. Assess their ability to meet your order quantities and delivery timelines. It’s also crucial to evaluate their communication practices and responsiveness to inquiries, as this can impact future collaborations. Lastly, inquire about their experience in dealing with businesses in your region to ensure cultural compatibility. -
What customization options are available for timers?
Many timer manufacturers offer customization options to meet specific business needs. Customizations can include branding (logo placement), functionality (preset timers, countdown features), and design (size, color, and display type). Some suppliers may also provide tailored programming for specific applications, such as industrial or educational uses. When discussing customization, clarify your requirements upfront and request samples to ensure the final product aligns with your expectations. -
What is the typical minimum order quantity (MOQ) for timer products?
The minimum order quantity (MOQ) for timer products varies by manufacturer and product type. Generally, MOQs can range from 100 to several thousand units, depending on the complexity and customization of the timers. For international buyers, negotiating MOQs can be possible, especially if you are willing to pay higher unit prices. It is advisable to discuss your specific needs with potential suppliers to find a suitable arrangement that meets both parties’ requirements. -
What payment terms should I expect when sourcing timers internationally?
Payment terms for international transactions can vary widely among manufacturers. Common terms include advance payment, partial payment before shipment, or net payment upon delivery. It’s essential to establish clear terms in your contract to avoid misunderstandings. Additionally, consider using secure payment methods like letters of credit or escrow services, which can protect both parties during the transaction. Always clarify the currency of payment and any additional fees that may apply. -
How do I ensure quality assurance when purchasing timers?
To ensure quality assurance when purchasing timers, request detailed product specifications and certifications from the manufacturer. Establish a quality control process that includes pre-shipment inspections and testing of samples. Some manufacturers may offer warranties or guarantees on their products, which can be a good indicator of their commitment to quality. Additionally, consider third-party quality assurance services, especially for larger orders, to verify that products meet your specifications before shipment. -
What logistics considerations should I be aware of when importing timers?
When importing timers, logistics considerations include shipping methods, customs regulations, and lead times. Decide between air freight for faster delivery or sea freight for cost-effectiveness. Familiarize yourself with import duties and taxes in your country, as these can significantly impact overall costs. Working with a reliable freight forwarder can help navigate these complexities and ensure that your products arrive on time and in good condition. Always track your shipments to address any issues promptly. -
How can I build a long-term relationship with my timer supplier?
Building a long-term relationship with your timer supplier involves consistent communication and mutual respect. Regularly provide feedback on product quality and service, which can help the manufacturer improve and adapt to your needs. Consider establishing a partnership approach, where both parties work collaboratively on product development and market strategies. Additionally, honoring payment terms and being transparent about your business needs can foster trust and encourage the supplier to prioritize your orders in the future.
Important Disclaimer & Terms of Use
⚠️ Important Disclaimer
The information provided in this guide, including content regarding manufacturers, technical specifications, and market analysis, is for informational and educational purposes only. It does not constitute professional procurement advice, financial advice, or legal advice.
While we have made every effort to ensure the accuracy and timeliness of the information, we are not responsible for any errors, omissions, or outdated information. Market conditions, company details, and technical standards are subject to change.
B2B buyers must conduct their own independent and thorough due diligence before making any purchasing decisions. This includes contacting suppliers directly, verifying certifications, requesting samples, and seeking professional consultation. The risk of relying on any information in this guide is borne solely by the reader.
Strategic Sourcing Conclusion and Outlook for timer manufacturer
In the competitive landscape of timer manufacturing, strategic sourcing emerges as a critical enabler for international B2B buyers. By prioritizing quality, reliability, and cost-effectiveness in supplier selection, businesses can secure a steady supply of high-performance timers tailored to their specific needs. Engaging with manufacturers that demonstrate a commitment to innovation and sustainability can enhance product offerings and improve brand reputation in diverse markets.
How Can International Buyers Leverage Strategic Sourcing for Timers?
For buyers in regions such as Africa, South America, the Middle East, and Europe, understanding local market dynamics and supplier capabilities is paramount. Establishing strong relationships with manufacturers not only facilitates better pricing but also fosters collaboration on product development and customization. This is particularly important in markets like Nigeria and Italy, where unique requirements and compliance standards may arise.
What’s Next for B2B Buyers in Timer Manufacturing?
As the demand for advanced timing solutions continues to grow, international buyers are encouraged to proactively engage with timer manufacturers. Explore partnerships that emphasize transparency, innovation, and efficiency. By doing so, businesses can not only enhance their operational capabilities but also position themselves as leaders in their respective markets. Embrace the future of sourcing; the right partnerships await.