Discover the Best Tissue Paper Supplier: Ultimate Buying Guide (2025)
Introduction: Navigating the Global Market for tissue paper supplier
Navigating the complexities of sourcing a reliable tissue paper supplier can be a daunting task for international B2B buyers, particularly in regions such as Africa, South America, the Middle East, and Europe. With fluctuating demand, varying quality standards, and diverse supplier capabilities, how can businesses ensure they choose the right partner? This guide provides a comprehensive overview of the tissue paper market, addressing the different types of tissue products available, their applications across various industries, and effective strategies for supplier vetting.
Buyers will gain insights into crucial factors such as pricing structures, quality assurance processes, and compliance with international standards. This guide aims to empower B2B buyers by equipping them with the knowledge necessary to make informed purchasing decisions that align with their business needs and local market conditions.
Whether you are in the UAE looking for eco-friendly tissue solutions, or in Germany seeking bulk supplies for hospitality services, understanding the intricacies of the tissue paper supply chain is essential. By navigating this guide, you will learn how to identify reputable suppliers, assess product quality, and negotiate favorable terms, ultimately ensuring that your business remains competitive in a globalized market.
Understanding tissue paper supplier Types and Variations
Type Name | Key Distinguishing Features | Primary B2B Applications | Brief Pros & Cons for Buyers |
---|---|---|---|
Standard Tissue Paper | Lightweight, absorbent, available in various colors | Retail packaging, gift wrapping | Pros: Cost-effective, versatile. Cons: Less durable, may not suit high-end applications. |
Recycled Tissue Paper | Made from post-consumer waste, eco-friendly | Eco-conscious brands, packaging | Pros: Sustainable, appeals to green consumers. Cons: May have lower quality and strength. |
Luxury Tissue Paper | Heavier weight, often printed or embossed, premium feel | High-end retail, special events | Pros: Enhances brand image, superior quality. Cons: Higher cost, may not be suitable for all applications. |
Colored Tissue Paper | Available in a wide range of colors, often used for aesthetics | Crafting, event decorations | Pros: Customizable, visually appealing. Cons: Limited durability compared to standard options. |
Food-Grade Tissue Paper | Safe for direct food contact, often bleached or unbleached | Food packaging, catering services | Pros: Compliant with safety standards, hygienic. Cons: Higher cost, limited aesthetic appeal. |
What Are the Characteristics of Standard Tissue Paper Suppliers?
Standard tissue paper suppliers offer lightweight and absorbent products that are widely available in various colors and sizes. This type of tissue paper is primarily used in retail packaging and gift wrapping, making it a staple for businesses looking for cost-effective solutions. When purchasing standard tissue paper, buyers should consider the weight and absorbency to ensure it meets their specific needs, particularly in applications where moisture absorption is critical.
How Does Recycled Tissue Paper Cater to Eco-Conscious Buyers?
Recycled tissue paper suppliers focus on sustainability by producing paper from post-consumer waste. This eco-friendly option is ideal for businesses that prioritize environmental responsibility, making it a popular choice for eco-conscious brands. Key purchasing considerations include the quality and strength of the paper, as recycled options may vary significantly. Buyers should also assess the supplier’s certifications to ensure compliance with environmental standards.
Why Choose Luxury Tissue Paper Suppliers for High-End Applications?
Luxury tissue paper suppliers provide products that are heavier in weight and often feature printed or embossed designs. This premium option is commonly used in high-end retail settings and special events, where branding and presentation are crucial. Buyers should evaluate the aesthetic appeal and quality of the tissue paper, as it can significantly enhance the customer experience. However, it is essential to weigh the higher cost against the potential benefits in brand perception.
What Benefits Does Colored Tissue Paper Offer for Crafting and Events?
Colored tissue paper suppliers provide a vibrant range of options that cater to crafting and event decoration needs. This type of tissue paper is highly customizable and visually appealing, making it a favorite among businesses in the creative sector. When selecting colored tissue paper, buyers should consider the intended use, as durability may be a concern for some applications. Additionally, assessing the supplier’s color consistency and availability can help ensure a successful project.
How Important Is Food-Grade Tissue Paper for Food Packaging?
Food-grade tissue paper suppliers specialize in products that are safe for direct contact with food, often available in both bleached and unbleached varieties. This type of tissue paper is critical for businesses in the food industry, including catering services and restaurants. Buyers must ensure that the tissue paper complies with safety standards, focusing on hygiene and quality. While food-grade options may come at a higher price point, the benefits of safety and compliance are invaluable in protecting consumer health.
Related Video: Tissue Paper production / manufacturing process
Key Industrial Applications of tissue paper supplier
Industry/Sector | Specific Application of Tissue Paper Supplier | Value/Benefit for the Business | Key Sourcing Considerations for this Application |
---|---|---|---|
Healthcare | Surgical and Hygiene Products | Ensures hygiene and prevents cross-contamination | Quality certifications, absorbency, and compliance with health standards |
Food Service | Napkins and Food Wrapping | Enhances customer experience and maintains cleanliness | Food safety certifications, material composition, and durability |
Hospitality | Guest Room Amenities | Improves guest satisfaction and brand image | Eco-friendliness, softness, and aesthetic appeal |
Retail and E-commerce | Packaging and Branding Solutions | Enhances product presentation and reduces damage | Customization options, print quality, and sustainability practices |
Personal Care Products | Facial Tissues and Wipes | Provides convenience and promotes hygiene | Skin compatibility, hypoallergenic properties, and packaging options |
How is Tissue Paper Used in Healthcare Settings?
In healthcare, tissue paper suppliers provide surgical and hygiene products that are critical for maintaining sanitary conditions. These products include surgical drapes, gowns, and wipes that help prevent cross-contamination during medical procedures. For international B2B buyers, especially from regions like Africa and the Middle East, sourcing tissue paper that meets stringent health regulations and certifications is essential. Buyers must prioritize absorbency and softness, ensuring comfort for patients while maintaining high hygiene standards.
What is the Role of Tissue Paper in Food Service?
In the food service industry, tissue paper is predominantly used for napkins and food wrapping, enhancing the overall dining experience. High-quality tissue paper helps absorb spills, keeps food items hygienic, and adds a touch of elegance to restaurant settings. For B2B buyers in South America and Europe, sourcing tissue paper with food safety certifications is crucial. Considerations should include the material’s durability and its ability to withstand moisture without disintegrating.
How Does Tissue Paper Enhance Hospitality Services?
In the hospitality sector, tissue paper suppliers play a vital role by providing guest room amenities such as facial tissues and toilet paper. These products significantly contribute to guest satisfaction and the establishment’s overall brand image. International buyers, particularly from Europe, should focus on eco-friendly options that align with sustainability trends. Factors like softness, aesthetic appeal, and packaging are also important, as they impact the guest’s experience and perception of the hotel.
Why is Tissue Paper Important for Retail and E-commerce?
In retail and e-commerce, tissue paper is often used for packaging and branding solutions, providing an added layer of protection for products during shipping. It enhances product presentation and minimizes damage, which is crucial for maintaining customer satisfaction. Buyers from diverse markets, including Africa and Europe, should consider customization options to reflect their brand identity. The print quality and sustainability practices of tissue paper suppliers are also vital, as consumers increasingly prefer eco-friendly products.
What Are the Key Considerations for Personal Care Products?
For personal care products, tissue paper is essential in the form of facial tissues and wipes, offering convenience and promoting hygiene. Suppliers must ensure their products are hypoallergenic and compatible with various skin types to cater to a broad consumer base. International buyers from regions like the Middle East should focus on packaging options that enhance usability and appeal to consumers’ preferences for high-quality personal care items.
Related Video: How Paper Is Made
3 Common User Pain Points for ’tissue paper supplier’ & Their Solutions
Scenario 1: Inconsistent Quality of Tissue Paper Products
The Problem: A B2B buyer in the hospitality industry, such as a hotel manager in the UAE, may face significant challenges when dealing with a tissue paper supplier that offers inconsistent quality. This inconsistency can manifest as variability in softness, absorbency, or strength, which directly impacts guest experience. For instance, if a hotel provides low-quality tissue in its restrooms or rooms, it can lead to negative reviews and affect the overall reputation of the establishment.
The Solution: To ensure consistent quality, buyers should establish clear specifications and standards with their tissue paper suppliers. This includes requesting product samples and conducting quality tests before placing large orders. Additionally, developing a strong relationship with suppliers who are transparent about their manufacturing processes can help. Buyers should also consider diversifying their supplier base to mitigate risks associated with dependency on a single source. Regular audits and feedback loops can further ensure that the products meet the established standards consistently.
Scenario 2: Supply Chain Disruptions Impacting Delivery Times
The Problem: International buyers, particularly from regions like South America, may encounter significant disruptions in their supply chain, leading to delays in receiving tissue paper shipments. This situation is exacerbated by global events such as pandemics or geopolitical tensions, which can cause unexpected supply shortages and logistical challenges. A buyer who operates a large retail chain might find themselves unable to restock essential products on time, resulting in lost sales and dissatisfied customers.
The Solution: To counteract supply chain disruptions, B2B buyers should implement a robust inventory management system that allows for real-time tracking of stock levels. Building strategic partnerships with multiple tissue paper suppliers can also provide flexibility and alternative options in case of disruptions. Additionally, buyers should discuss lead times and potential risks with their suppliers upfront, allowing for better planning. Establishing a buffer stock can provide a safety net during unexpected supply chain issues, ensuring that business operations can continue smoothly.
Scenario 3: Environmental Concerns and Sustainability Issues
The Problem: Many international B2B buyers, particularly in Europe, are increasingly concerned about the environmental impact of the products they source. Tissue paper, often made from virgin pulp, raises sustainability questions and can lead to reputational risks if suppliers do not adhere to eco-friendly practices. A buyer in the food service industry might struggle with sourcing tissue paper that aligns with their sustainability goals while also meeting customer expectations for quality.
The Solution: Buyers should prioritize suppliers that offer sustainable tissue paper options, such as products made from recycled materials or those certified by recognized environmental standards (e.g., FSC or PEFC). Engaging in open discussions with suppliers about their sourcing practices and sustainability initiatives can lead to better alignment with the buyer’s values. Additionally, considering the entire lifecycle of the product, including biodegradability and recyclability, is crucial. Buyers can also influence suppliers by demanding transparency in their practices, which may encourage them to adopt more sustainable operations. By making informed decisions, buyers can not only meet their sustainability goals but also appeal to environmentally conscious consumers.
Strategic Material Selection Guide for tissue paper supplier
When selecting materials for tissue paper production, international B2B buyers must consider various factors that influence product performance, cost, and compliance with regional standards. Here, we analyze four common materials used in tissue paper manufacturing, focusing on their properties, advantages, disadvantages, and specific considerations for buyers from Africa, South America, the Middle East, and Europe.
What Are the Key Properties of Virgin Pulp in Tissue Paper?
Virgin pulp is derived from fresh wood fibers and is the primary material used in high-quality tissue paper.
- Key Properties: Virgin pulp offers excellent absorbency, softness, and strength. It can withstand various temperatures and pressures during production without losing integrity.
- Pros & Cons: The main advantage of virgin pulp is its superior quality, leading to a more luxurious feel and better performance in absorbency. However, it comes with a higher cost due to sourcing and processing. Additionally, the manufacturing complexity can increase with the need for sustainable sourcing practices.
- Impact on Application: Virgin pulp is ideal for products requiring high absorbency, such as facial tissues and premium bathroom tissues.
- Specific Considerations: Buyers in regions like Germany and the UAE should ensure that the pulp is sourced from sustainably managed forests, complying with standards like FSC (Forest Stewardship Council) certification.
How Does Recycled Pulp Compare in Tissue Paper Production?
Recycled pulp is made from post-consumer paper products and is increasingly popular among environmentally conscious manufacturers.
- Key Properties: This material provides decent absorbency and softness, though it may not match the performance of virgin pulp.
- Pros & Cons: The primary advantage of recycled pulp is its cost-effectiveness and reduced environmental impact. However, it may have limitations in strength and absorbency, making it less suitable for high-end products.
- Impact on Application: Recycled pulp is often used in budget-friendly tissue products, such as napkins and low-cost bathroom tissue.
- Specific Considerations: Buyers in regions like South America may find recycled pulp aligns with local sustainability initiatives, but they should be aware of varying quality standards and certifications.
What Role Does Bamboo Pulp Play in Tissue Paper Manufacturing?
Bamboo pulp is an emerging alternative in the tissue paper market, known for its rapid growth and sustainability.
- Key Properties: Bamboo pulp is highly absorbent, soft, and possesses natural antibacterial properties, making it suitable for hygiene products.
- Pros & Cons: The key advantage is its eco-friendliness and renewability, as bamboo grows much faster than traditional trees. However, it can be more expensive and may require specialized processing techniques.
- Impact on Application: Bamboo pulp is particularly well-suited for premium tissue products aimed at health-conscious consumers.
- Specific Considerations: Buyers in the Middle East should evaluate the availability of bamboo pulp and ensure compliance with local regulations regarding sustainable sourcing.
Why Is Non-Woven Fabric Gaining Popularity in Tissue Paper Applications?
Non-woven fabrics are increasingly being used in tissue products, especially for industrial applications.
- Key Properties: These materials are created through a process that bonds fibers together, resulting in a strong, durable product that can be engineered for specific applications.
- Pros & Cons: The main advantage is their versatility and strength, making them suitable for heavy-duty applications. However, they may lack the softness and absorbency of traditional tissue products.
- Impact on Application: Non-woven fabrics are often used in industrial wipes and medical applications, where durability is essential.
- Specific Considerations: Buyers in Europe should ensure that non-woven products meet relevant health and safety standards, such as those outlined by DIN or EN regulations.
Summary Table of Material Selection for Tissue Paper Suppliers
Material | Typical Use Case for tissue paper supplier | Key Advantage | Key Disadvantage/Limitation | Relative Cost (Low/Med/High) |
---|---|---|---|---|
Virgin Pulp | Premium bathroom tissues, facial tissues | Superior softness and absorbency | Higher cost and sustainability concerns | High |
Recycled Pulp | Budget-friendly napkins, low-cost tissues | Cost-effective and eco-friendly | Limited strength and absorbency | Medium |
Bamboo Pulp | Premium hygiene products | Eco-friendly and antibacterial | Higher cost and processing complexity | High |
Non-Woven Fabric | Industrial wipes, medical applications | Strong and durable | Lacks softness and absorbency | Medium |
This strategic material selection guide provides a comprehensive overview for international B2B buyers in the tissue paper sector. By understanding the properties, advantages, and limitations of each material, buyers can make informed decisions that align with their business needs and regional compliance requirements.
In-depth Look: Manufacturing Processes and Quality Assurance for tissue paper supplier
What Are the Main Stages of Tissue Paper Manufacturing?
The manufacturing process of tissue paper involves several critical stages that ensure the final product meets the quality and performance expectations of B2B buyers. Here’s a detailed breakdown of the main stages involved:
1. Material Preparation
The first stage begins with the selection and preparation of raw materials, primarily recycled paper and virgin pulp. The choice between these materials often depends on the end-use of the tissue paper.
- Recycled Pulp: This is often sourced from post-consumer waste, making it an environmentally friendly option. The recycling process involves deinking and cleaning to remove contaminants.
- Virgin Pulp: Sourced from sustainably managed forests, this pulp is used for high-quality tissue products. It undergoes a refining process to enhance fiber quality.
Once the raw materials are selected, they are processed through a pulping machine that breaks down the fibers, creating a slurry.
2. Forming
After preparing the pulp, the next step is forming the tissue sheet. This is where the slurry is spread onto a moving screen or wire mesh to drain excess water, forming a continuous sheet.
- Wet-Laying Technique: In this traditional method, water is used to transport the pulp fibers onto the wire mesh. The fibers bond together as water is drained, forming a mat of tissue.
- Dry-Laying Technique: Increasingly popular due to its efficiency, this method uses a dry process to form sheets without excessive water, saving energy and reducing drying time.
Once formed, the wet sheet is pressed to remove additional moisture before it moves to the drying stage.
3. Assembly and Finishing
The dried tissue paper is then wound onto large rolls. This stage involves several sub-processes:
- Embossing: To improve softness and absorbency, the tissue is often embossed using patterned rollers.
- Perforating: This creates convenient tear lines, especially for consumer products.
- Cutting and Packaging: The large rolls are cut into smaller, manageable sizes that meet customer specifications, followed by packaging for distribution.
How Is Quality Assurance Implemented in Tissue Paper Manufacturing?
Quality assurance (QA) is integral to the tissue paper manufacturing process, ensuring that products meet international standards and customer expectations. Here are the key components of QA in this industry:
Relevant International Standards for Tissue Paper Suppliers
To maintain quality, tissue paper manufacturers often adhere to international standards, such as:
- ISO 9001: This is a widely recognized quality management standard that outlines criteria for an effective quality management system. It emphasizes consistent quality and customer satisfaction.
- CE Marking: For products sold in Europe, CE marking indicates compliance with health, safety, and environmental protection standards.
- API Certification: This certification is crucial for products intended for the medical sector, ensuring that the tissue products are safe and effective for use.
What Are the QC Checkpoints in Tissue Paper Manufacturing?
Quality control (QC) involves systematic checks at various stages of the manufacturing process:
- Incoming Quality Control (IQC): This step checks the quality of raw materials upon delivery. Manufacturers should verify that suppliers provide documentation proving compliance with quality standards.
- In-Process Quality Control (IPQC): Continuous monitoring during production ensures that the processes are stable and that the output meets quality specifications.
- Final Quality Control (FQC): After production, a final inspection is performed to check the finished product against predetermined standards.
What Testing Methods Are Commonly Used in Tissue Paper Quality Control?
Testing is an essential part of ensuring that tissue paper meets quality standards. Common testing methods include:
- Physical Testing: This involves measuring strength, absorbency, and thickness. For example, the burst strength test assesses how much pressure the tissue can withstand before failing.
- Chemical Testing: This checks for harmful substances, such as chlorine or formaldehyde, ensuring that the tissue is safe for use.
- Visual Inspection: Trained personnel inspect the tissue for defects like holes, discoloration, or inconsistencies in texture.
How Can B2B Buyers Verify Supplier Quality Control?
B2B buyers from regions such as Africa, South America, the Middle East, and Europe can take several steps to ensure their suppliers maintain robust quality control:
Conduct Supplier Audits
Regular audits are crucial for assessing a supplier’s compliance with quality standards. Buyers should request audits focusing on:
- Manufacturing Processes: Understanding how the supplier operates can reveal potential quality issues.
- Documentation: Ensure that the supplier maintains accurate records of their QA processes and testing results.
Review Quality Control Reports
Buyers should request detailed QC reports from suppliers, which should include:
- Testing Results: Documentation of various tests performed on the tissue paper.
- Non-Conformance Reports: Information on any products that did not meet quality standards and the actions taken.
Engage Third-Party Inspection Services
To ensure impartiality, engaging third-party inspectors can provide an objective assessment of the supplier’s quality control measures. These services can verify compliance with international standards and conduct random sampling of products.
What Are the QC and Certification Nuances for International B2B Buyers?
International B2B buyers must be aware of specific nuances related to quality control and certification:
- Cultural Differences: Understanding regional manufacturing practices and quality expectations can help buyers select suitable suppliers.
- Regulatory Requirements: Different regions may have varying regulations regarding the use of tissue products, especially in sectors like healthcare and food service. Buyers must ensure their suppliers comply with these regulations.
- Sustainability Standards: Increasingly, buyers are looking for suppliers who adhere to sustainability certifications, such as FSC (Forest Stewardship Council) or PEFC (Programme for the Endorsement of Forest Certification).
In conclusion, a comprehensive understanding of the manufacturing processes and quality assurance practices is essential for B2B buyers in the tissue paper industry. By focusing on these aspects, buyers can make informed decisions and build strong partnerships with reliable suppliers.
Practical Sourcing Guide: A Step-by-Step Checklist for ’tissue paper supplier’
Introduction
When sourcing tissue paper suppliers, international B2B buyers must navigate various factors to ensure they partner with a reliable and quality-focused supplier. This checklist serves as a practical guide to help you streamline your sourcing process and make informed decisions that align with your business needs and market expectations.
Step 1: Define Your Technical Specifications
Clearly outlining your technical specifications is essential before reaching out to potential suppliers. This includes determining the type of tissue paper you need (e.g., facial tissue, toilet paper, industrial wipes), along with the desired quality, thickness, and environmental certifications. By having specific requirements, you can filter suppliers effectively and ensure they can meet your production standards.
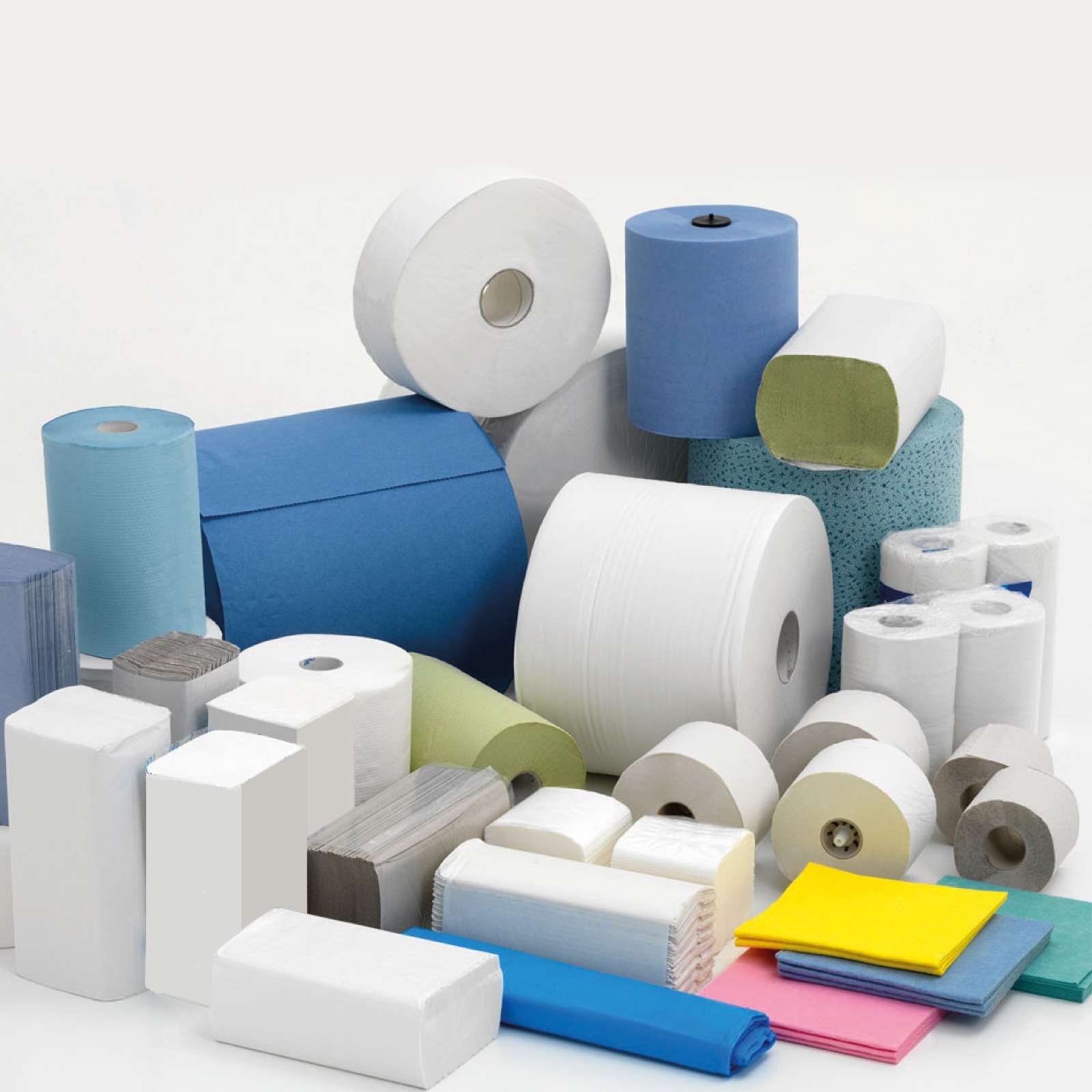
A stock image related to tissue paper supplier.
Step 2: Research Potential Suppliers
Conduct thorough research to identify potential tissue paper suppliers. Utilize online directories, trade fairs, and industry networks to compile a list of candidates. Focus on suppliers that have a strong presence in your target regions—Africa, South America, the Middle East, and Europe—as they will be more familiar with local market demands and regulations.
Step 3: Evaluate Supplier Capabilities and Experience
Before committing to a supplier, assess their capabilities and experience in the tissue paper sector. Look for:
– Production capacity: Ensure they can meet your order volumes consistently.
– Experience: Evaluate their years in the industry and portfolio of clients.
– Technology: Check if they utilize modern manufacturing techniques that align with your quality expectations.
Step 4: Verify Supplier Certifications
Certifications are a key indicator of a supplier’s commitment to quality and compliance. Verify that they hold relevant certifications such as ISO 9001 for quality management and FSC or PEFC for sustainable sourcing. These certifications not only enhance credibility but also assure you of their adherence to industry standards and environmental responsibility.
Step 5: Request Samples and Conduct Quality Checks
Always request product samples before finalizing any agreements. Assess the quality of the tissue paper, focusing on attributes such as softness, absorbency, and strength. If possible, conduct quality checks through third-party testing to validate that the product meets your specifications and industry standards.
Step 6: Understand Pricing Structures and Payment Terms
Discuss pricing structures and payment terms transparently with your shortlisted suppliers. Look for:
– Bulk pricing discounts: Ensure you understand how pricing may change with order volume.
– Payment terms: Negotiate terms that work for both parties, such as upfront deposits or payment upon delivery.
– Hidden costs: Be aware of any additional fees related to shipping, handling, or customs duties that could impact your overall budget.
Step 7: Establish Communication and Support Channels
Effective communication is crucial for a successful supplier relationship. Ensure that the supplier has dedicated support channels for addressing your inquiries or issues. Establishing a clear line of communication will facilitate smoother transactions and help resolve any potential challenges swiftly.
By following this checklist, international B2B buyers can enhance their sourcing strategy for tissue paper suppliers, ensuring they choose partners that align with their quality, sustainability, and operational requirements.
Comprehensive Cost and Pricing Analysis for tissue paper supplier Sourcing
What Are the Key Cost Components in Tissue Paper Supplier Pricing?
Understanding the cost structure of tissue paper suppliers is crucial for international B2B buyers. The primary cost components include:
-
Materials: The type of raw materials used, such as virgin pulp or recycled fibers, significantly affects the cost. High-quality materials generally lead to higher prices, but they can enhance product durability and user satisfaction.
-
Labor: Labor costs encompass wages for factory workers, supervisors, and quality control personnel. Regions with higher labor costs, like Western Europe, may see higher pricing compared to emerging markets in Africa and South America.
-
Manufacturing Overhead: This includes costs related to utilities, maintenance, and factory operations. Efficient manufacturing processes can help reduce overhead costs, allowing suppliers to offer more competitive pricing.
-
Tooling: Initial costs for machinery and equipment, as well as ongoing maintenance, play a role in pricing. Advanced machinery may incur higher initial costs but can increase production efficiency and product quality.
-
Quality Control (QC): Implementing stringent QC measures ensures product consistency and compliance with international standards. While this may add to costs, it can prevent issues that lead to returns and dissatisfaction.
-
Logistics: Shipping costs can vary dramatically based on the distance, mode of transport, and volume shipped. For international buyers, understanding logistics costs is essential, as they can significantly impact the total cost of ownership.
-
Margin: Suppliers typically add a profit margin to cover their operational expenses and to ensure sustainability. This margin varies by supplier and can be influenced by market demand and competition.
How Do Price Influencers Impact Tissue Paper Sourcing?
Several factors influence the pricing of tissue paper, which buyers should consider:
-
Volume/MOQ: Suppliers often provide better pricing for larger orders due to economies of scale. Understanding the minimum order quantities (MOQs) can help buyers negotiate better rates.
-
Specifications and Customization: Customized products, such as branded tissue or specific sizes, usually come at a premium. Buyers should weigh the added value of customization against the costs.
-
Material Quality and Certifications: Higher quality materials and certifications (like FSC or ISO) can increase costs but may be necessary for market competitiveness and compliance with local regulations.
-
Supplier Factors: The reputation and reliability of a supplier can impact pricing. Established suppliers may charge more for their brand and reliability, while emerging suppliers might offer lower prices to gain market share.
-
Incoterms: Understanding the shipping terms (like FOB, CIF) is critical as they define who bears the risk and costs during shipping. This knowledge can help buyers avoid unexpected expenses.
What Are the Best Buyer Tips for Cost-Efficient Tissue Paper Sourcing?
For international buyers, particularly from regions such as Africa, South America, the Middle East, and Europe, here are actionable tips:
-
Negotiate Wisely: Leverage your purchasing power, especially when ordering in bulk. Discuss payment terms and potential discounts for early payments to enhance your cost savings.
-
Focus on Total Cost of Ownership (TCO): Beyond the initial price, consider factors such as durability, shipping costs, and potential waste. A higher upfront cost may lead to lower long-term expenses.
-
Understand Pricing Nuances: Be aware that prices can fluctuate based on market conditions, currency exchange rates, and seasonal demand. Keeping an eye on these factors can help in making timely purchasing decisions.
-
Consider Local Suppliers: Sourcing from local suppliers can reduce logistics costs and lead times. It also supports local economies and may provide more flexibility in negotiations.
-
Request Samples: Before committing to large orders, request product samples to assess quality. This practice can prevent costly mistakes and ensure that you meet your customers’ expectations.
Disclaimer on Indicative Prices
Pricing in the tissue paper market can vary widely based on numerous factors. It is advisable to obtain quotes from multiple suppliers to ensure competitive pricing and to consider the latest market trends when making purchasing decisions.
Alternatives Analysis: Comparing tissue paper supplier With Other Solutions
Understanding Alternatives to Tissue Paper Suppliers
When considering tissue paper suppliers, it’s essential to evaluate various alternatives that can meet similar needs. These alternatives may offer different performance characteristics, cost structures, and application scenarios, allowing international B2B buyers, especially from Africa, South America, the Middle East, and Europe, to make informed decisions that align with their operational requirements and budgets.
Comparison of Tissue Paper Supplier and Alternatives
Comparison Aspect | Tissue Paper Supplier | Biodegradable Wipes | Reusable Cloths |
---|---|---|---|
Performance | Soft, absorbent, disposable | Soft, absorbent, single-use | Durable, absorbent, washable |
Cost | Moderate, variable by quality | Higher per unit cost | Lower long-term cost, initial investment needed |
Ease of Implementation | Simple procurement, widely available | Requires supplier education and marketing | Requires training and changing user habits |
Maintenance | Minimal, just disposal | Minimal, disposal after use | High, requires regular washing and drying |
Best Use Case | General hygiene, food service | Quick clean-ups, sensitive skin | Eco-friendly initiatives, heavy-duty cleaning |
Detailed Breakdown of Alternatives
What Are Biodegradable Wipes and Their Benefits?
Biodegradable wipes are made from plant-based materials that decompose more rapidly than traditional disposable products. They offer a similar performance to tissue paper but are marketed as more environmentally friendly. However, their higher per-unit cost can be a disadvantage for businesses with tight budgets. Moreover, while they are simple to implement, they may require additional education for staff and customers on proper disposal methods to ensure they decompose effectively.
How Do Reusable Cloths Compare?
Reusable cloths present a sustainable alternative, particularly appealing to organizations focused on reducing waste. They are durable and can handle heavy-duty cleaning tasks that tissue paper cannot. The initial investment in cloths can be offset by long-term savings, as they are washed and reused multiple times. However, the maintenance level is considerably higher, necessitating a change in operational habits, which may be challenging for some businesses. Additionally, training employees on effective cleaning protocols is vital to maximize their benefits.
Making the Right Choice for Your Business Needs
For international B2B buyers evaluating tissue paper suppliers and their alternatives, the decision should center around specific operational requirements and sustainability goals. If immediate disposability and convenience are paramount, traditional tissue paper may remain the best option. Conversely, if cost savings and environmental impact are priorities, exploring biodegradable wipes or reusable cloths could provide significant long-term benefits. Conducting a thorough needs assessment and considering the implications of each alternative will ensure that your choice aligns with your business strategy and customer expectations.
Essential Technical Properties and Trade Terminology for tissue paper supplier
What Are the Key Technical Properties of Tissue Paper for B2B Buyers?
When sourcing tissue paper, understanding its technical properties is crucial for ensuring quality and meeting specific business needs. Here are some essential specifications:
-
Material Grade
Tissue paper can be made from various materials, including virgin pulp, recycled paper, or a blend. The material grade affects softness, absorbency, and durability. For B2B buyers, selecting the right grade is important for product performance and customer satisfaction. -
Basis Weight
This refers to the weight of a ream (usually 500 sheets) of paper measured in grams per square meter (gsm). Higher basis weights typically indicate thicker, more durable tissue. Understanding this specification helps buyers assess the strength and quality of the tissue paper, making it easier to match their specific requirements. -
Tensile Strength
Tensile strength measures how much force the paper can withstand before breaking. This property is critical for tissue products that need to endure handling and usage. Buyers should prioritize high tensile strength for applications requiring durability, such as commercial use in restrooms or kitchens. -
Absorbency
Absorbency is the ability of tissue paper to soak up liquids, which is vital for products like napkins and towels. This property is often expressed in terms of absorbency rate or capacity. For B2B buyers, selecting tissue paper with adequate absorbency ensures effectiveness in cleaning and hygiene applications. -
Softness
Softness is a subjective but important property, especially for consumer-facing products. Tissue paper is often tested for softness through various methods, impacting user experience. Buyers should consider this property when sourcing products for personal care or hospitality sectors where comfort is essential.
Which Trade Terms Should B2B Buyers Understand When Dealing with Tissue Paper Suppliers?
Familiarity with industry terminology can streamline negotiations and enhance communication with suppliers. Here are some commonly used trade terms:
-
OEM (Original Equipment Manufacturer)
This term refers to companies that produce parts or equipment that may be marketed by another manufacturer. In tissue paper, OEM suppliers may create custom products for brands. Buyers should clarify OEM capabilities to ensure they receive tailored products. -
MOQ (Minimum Order Quantity)
MOQ is the smallest quantity of product that a supplier is willing to sell. Understanding MOQ is essential for buyers, as it affects inventory management and purchasing decisions. Negotiating favorable MOQs can lead to cost savings and better alignment with business needs. -
RFQ (Request for Quotation)
An RFQ is a formal process in which buyers ask suppliers to provide pricing and terms for specific products. Submitting a well-structured RFQ can help buyers receive competitive quotes and ensure all specifications are met. This practice is crucial for establishing clear expectations and pricing. -
Incoterms (International Commercial Terms)
Incoterms are a set of predefined international trade terms that clarify the responsibilities of buyers and sellers regarding shipping, insurance, and tariffs. Understanding these terms helps buyers mitigate risks and manage costs effectively in international transactions. -
Lead Time
Lead time refers to the time it takes from placing an order to receiving the goods. For B2B buyers, knowing the lead time is critical for planning inventory and ensuring timely availability of products. Buyers should discuss lead times with suppliers to align with their operational timelines.
By familiarizing themselves with these technical properties and trade terms, international B2B buyers can make informed decisions when sourcing tissue paper, ensuring they meet their operational and customer satisfaction goals.
Navigating Market Dynamics and Sourcing Trends in the tissue paper supplier Sector
What Are the Key Market Dynamics Affecting the Tissue Paper Supplier Sector?
The global tissue paper market is experiencing significant growth, driven by increasing demand for hygiene products and sustainable packaging solutions. As urbanization and disposable income rise in regions such as Africa, South America, the Middle East, and Europe, the consumption of tissue paper products—ranging from toilet paper to facial tissues—continues to expand. B2B buyers must stay informed about emerging technologies, such as automated manufacturing processes and digital supply chain management, which enhance efficiency and reduce costs. Furthermore, e-commerce has transformed sourcing strategies, allowing international buyers to access a broader range of suppliers and products, thereby fostering competitive pricing and innovation.
Key trends influencing the market include the shift towards eco-friendly materials, as consumers and businesses alike increasingly prioritize sustainability. The integration of smart technologies in manufacturing, such as IoT-enabled machinery, is also gaining traction, improving quality control and production speed. As a result, buyers from diverse regions should focus on suppliers who leverage these advancements to meet both quality and sustainability benchmarks.
How Are Sustainability and Ethical Sourcing Impacting Tissue Paper Suppliers?
Sustainability is no longer just a buzzword; it is a fundamental aspect of the tissue paper supply chain. The environmental impact of paper production, including deforestation and water usage, has prompted B2B buyers to seek suppliers who prioritize ethical sourcing practices. This includes the use of certified sustainable materials, such as FSC (Forest Stewardship Council) and PEFC (Programme for the Endorsement of Forest Certification) certified products, which ensure that the raw materials are sourced responsibly.
Moreover, the importance of transparent supply chains is gaining momentum. Buyers are increasingly looking for suppliers who can demonstrate compliance with environmental standards and provide traceability for their products. This not only helps mitigate risks associated with supply chain disruptions but also aligns with the values of environmentally conscious consumers. By prioritizing sustainability, B2B buyers can enhance their brand reputation and meet the growing demand for eco-friendly products.
What Is the Historical Context of the Tissue Paper Supplier Sector?
The tissue paper industry has evolved significantly over the past few decades. Initially, tissue products were primarily produced from virgin wood pulp, leading to concerns about environmental sustainability. However, the late 20th century marked a shift towards recycling and the use of alternative fibers, such as bamboo and recycled paper, as consumer awareness of environmental issues grew.
The introduction of advanced manufacturing technologies has also revolutionized the sector, allowing for higher quality and more efficient production processes. Today, the market is characterized by a blend of traditional and innovative practices, with suppliers increasingly adopting sustainable sourcing and production methods to meet the demands of international B2B buyers. Understanding this evolution is essential for making informed purchasing decisions that align with current market trends and sustainability goals.
Frequently Asked Questions (FAQs) for B2B Buyers of tissue paper supplier
-
How can I evaluate the credibility of a tissue paper supplier?
To assess the credibility of a tissue paper supplier, start by reviewing their business history, certifications, and client testimonials. Look for suppliers with a proven track record in international trade, especially in your region. Request samples to evaluate product quality and inquire about their production processes. Additionally, consider engaging in direct communication to gauge responsiveness and professionalism. Participating in industry trade shows or forums can also provide insights into the supplier’s reputation and reliability. -
What are the key factors to consider when selecting a tissue paper supplier?
When selecting a tissue paper supplier, focus on product quality, pricing, production capacity, and delivery timelines. Ensure the supplier can meet your specific needs regarding tissue types and customization options. It’s also vital to understand their compliance with international standards and regulations, especially if you’re sourcing from different countries. Lastly, assess their logistics capabilities to ensure they can deliver on time and manage any customs processes efficiently. -
What customization options are available when sourcing tissue paper?
Many tissue paper suppliers offer customization options, including size, thickness, and branding features such as printed logos. When discussing customization, clarify your specific requirements, such as color choices and packaging preferences. Some suppliers may also provide eco-friendly options if sustainability is a priority for your business. Make sure to request samples of customized products to evaluate quality before placing large orders. -
What is the typical minimum order quantity (MOQ) for tissue paper?
Minimum order quantities (MOQs) for tissue paper can vary significantly among suppliers, typically ranging from 1,000 to 10,000 units, depending on the product type and customization level. Suppliers may set higher MOQs for specialized products due to production costs. When negotiating, discuss your needs and see if the supplier is flexible with MOQs, particularly if you are starting with a smaller inventory. -
What payment terms should I expect when dealing with international tissue paper suppliers?
Payment terms for international transactions often vary, with common practices including upfront deposits (20-50%) and the balance due before shipment or upon delivery. Some suppliers may offer letters of credit or escrow services for larger orders to ensure security for both parties. It’s crucial to clarify payment methods, currency, and any potential fees associated with international transactions to avoid misunderstandings. -
How do I ensure quality assurance when sourcing tissue paper?
To ensure quality assurance, establish clear specifications and standards in your contract with the supplier. Request certifications and quality control processes that the supplier follows, such as ISO certifications. Conduct regular audits and quality checks, especially for large orders. Consider using third-party inspection services to verify product quality before shipment, which can mitigate risks and enhance your supply chain reliability.
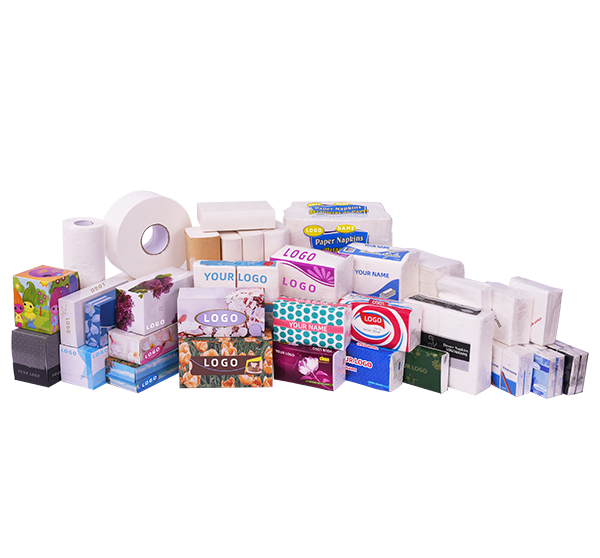
A stock image related to tissue paper supplier.
-
What logistics considerations should I keep in mind when importing tissue paper?
When importing tissue paper, pay attention to shipping methods, transit times, and customs regulations in both the exporting and importing countries. Choose a reliable logistics partner experienced in handling tissue paper shipments to manage the complexities of international transport. Ensure that all documentation, such as invoices, packing lists, and certificates of origin, is prepared accurately to avoid delays at customs. Additionally, consider the impact of tariffs and duties on your total cost. -
How can I effectively communicate my needs to a tissue paper supplier?
Effective communication is essential for successful supplier relationships. Be clear and concise about your requirements, including product specifications, order quantities, and delivery timelines. Use visual aids or samples to convey your expectations better. Establish regular communication channels, whether through emails, calls, or video meetings, to keep both parties aligned. Document all agreements and changes to ensure accountability and minimize misunderstandings.
Important Disclaimer & Terms of Use
⚠️ Important Disclaimer
The information provided in this guide, including content regarding manufacturers, technical specifications, and market analysis, is for informational and educational purposes only. It does not constitute professional procurement advice, financial advice, or legal advice.
While we have made every effort to ensure the accuracy and timeliness of the information, we are not responsible for any errors, omissions, or outdated information. Market conditions, company details, and technical standards are subject to change.
B2B buyers must conduct their own independent and thorough due diligence before making any purchasing decisions. This includes contacting suppliers directly, verifying certifications, requesting samples, and seeking professional consultation. The risk of relying on any information in this guide is borne solely by the reader.
Strategic Sourcing Conclusion and Outlook for tissue paper supplier
What Are the Key Takeaways for Strategic Sourcing of Tissue Paper?
In conclusion, strategic sourcing for tissue paper suppliers is not merely about cost savings; it encompasses a comprehensive approach that includes quality assessment, supplier reliability, and sustainability practices. By engaging in thorough market research, international B2B buyers from regions such as Africa, South America, the Middle East, and Europe can identify suppliers who meet their specific needs while fostering long-term partnerships. This process ensures that buyers can navigate the complexities of the tissue paper market, including fluctuations in raw material prices and evolving consumer preferences.
How Can International Buyers Benefit from Strategic Sourcing?
Investing time in strategic sourcing enhances not only the procurement process but also the overall supply chain efficiency. Buyers are encouraged to leverage technology and data analytics to monitor supplier performance and market trends, allowing for more informed decision-making. Furthermore, emphasizing sustainable sourcing can align businesses with global environmental goals, improving brand reputation and customer loyalty.
What Should International Buyers Do Next?
Looking ahead, international B2B buyers should act decisively by evaluating their current sourcing strategies and exploring new partnerships. Engaging with suppliers who prioritize innovation and sustainability will be crucial in the competitive tissue paper market. Now is the time to take proactive steps towards optimizing your supply chain, ensuring your business remains resilient and adaptable in an ever-changing landscape.