Unlock Efficiency: The Ultimate Box Truck Custom Guide (2025)
Introduction: Navigating the Global Market for box truck custom
In today’s rapidly evolving logistics landscape, sourcing customized box trucks presents a unique challenge for international B2B buyers. The demand for tailored transportation solutions is growing, particularly in emerging markets across Africa, South America, the Middle East, and Europe. This guide on box truck customization provides a comprehensive overview of the various types of box trucks available, their specific applications, and the critical factors to consider when selecting the right solution for your business needs.
Navigating the global market for custom box trucks involves understanding supplier vetting processes, cost considerations, and regional regulations. This guide is designed to empower international B2B buyers with actionable insights that enhance informed purchasing decisions. By delving into the intricacies of box truck customization, you will gain knowledge about the latest trends and innovations, ensuring that your logistics operations remain competitive and efficient.
Whether you are looking to expand your fleet or optimize your existing logistics network, this guide serves as an essential resource. It equips you with the necessary tools to evaluate suppliers, compare costs, and ultimately select the most suitable box truck solutions that align with your operational goals. Embrace the opportunity to streamline your supply chain and improve your delivery capabilities with custom box trucks tailored to your specific requirements.
Understanding box truck custom Types and Variations
Type Name | Key Distinguishing Features | Primary B2B Applications | Brief Pros & Cons for Buyers |
---|---|---|---|
Standard Box Truck | Enclosed cargo area, flatbed, various sizes | General freight, moving services | Pros: Versatile, cost-effective. Cons: Limited customization. |
Refrigerated Box Truck | Insulated cargo area with refrigeration units | Food transport, pharmaceuticals | Pros: Maintains temperature, suitable for perishables. Cons: Higher maintenance costs. |
Liftgate Box Truck | Equipped with hydraulic liftgate | Delivery of heavy items, equipment rental | Pros: Facilitates loading/unloading, saves labor. Cons: Added weight, potential mechanical issues. |
Cargo Van Box Truck | Smaller size, often with side doors | Urban deliveries, small business use | Pros: Maneuverable, fuel-efficient. Cons: Limited cargo capacity. |
Custom-Fit Box Truck | Tailored specifications, specialized features | Niche markets, specialized deliveries | Pros: Meets specific business needs. Cons: Higher upfront cost, longer lead times. |
What are the Characteristics of Standard Box Trucks?
Standard box trucks are versatile vehicles designed for transporting various goods. They feature an enclosed cargo area, which protects items from the elements, and come in different sizes to accommodate various load capacities. Their primary applications include general freight transport and moving services, making them popular among logistics companies. When purchasing, buyers should consider the truck’s size, payload capacity, and any additional features that can enhance operational efficiency.
How Do Refrigerated Box Trucks Support B2B Needs?
Refrigerated box trucks are specifically designed to transport temperature-sensitive products. These trucks have insulated cargo areas equipped with refrigeration units, making them ideal for transporting food, pharmaceuticals, and other perishable goods. Businesses in the food service and healthcare sectors should prioritize these vehicles to ensure product integrity during transit. Buyers should evaluate the refrigeration system’s efficiency, maintenance requirements, and compliance with health regulations when considering this type of truck.
What are the Benefits of Liftgate Box Trucks?
Liftgate box trucks come equipped with hydraulic liftgates that facilitate the loading and unloading of heavy items. This feature is particularly beneficial for businesses involved in delivering bulky goods or equipment rentals. By reducing the need for manual labor, these trucks enhance operational efficiency. Buyers should assess the liftgate’s weight capacity, durability, and potential maintenance issues when exploring this option.
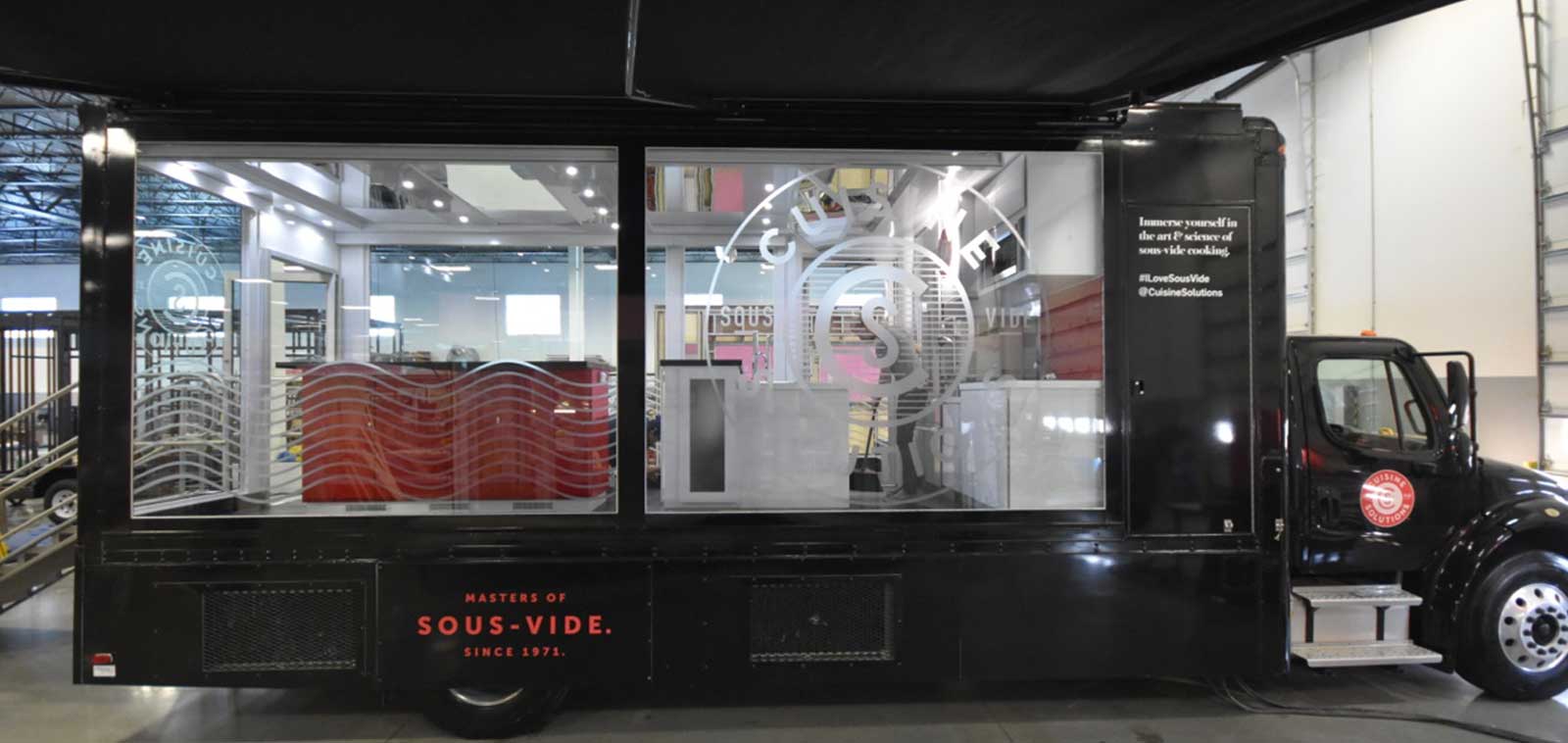
A stock image related to box truck custom.
Why Choose Cargo Van Box Trucks for Urban Deliveries?
Cargo van box trucks are smaller and often feature side doors for easier access in urban environments. They are ideal for businesses that require quick and efficient deliveries in congested city areas. Their maneuverability and fuel efficiency make them a cost-effective choice for small businesses. However, buyers should be mindful of their limited cargo capacity and ensure that the vehicle meets their specific delivery needs.
How Can Custom-Fit Box Trucks Enhance Specialized Business Operations?
Custom-fit box trucks are tailored to meet the unique requirements of specific businesses, incorporating specialized features such as shelving, partitions, or advanced technology. These trucks cater to niche markets and specialized delivery services, offering businesses the flexibility to operate efficiently. However, they come with a higher upfront cost and longer lead times, so buyers must carefully evaluate their specific needs and budget constraints before investing in a custom solution.
Related Video: 2017 FREIGHTLINER M2 112 BOLT CUSTOM SLEEPER TRUCK TOUR
Key Industrial Applications of box truck custom
Industry/Sector | Specific Application of box truck custom | Value/Benefit for the Business | Key Sourcing Considerations for this Application |
---|---|---|---|
Logistics and Transportation | Customized delivery services for e-commerce | Enhanced delivery efficiency and customer satisfaction | Consider load capacity, fuel efficiency, and route optimization features. |
Construction | On-site material transport and storage | Streamlined project management and reduced downtime | Assess durability, payload capacity, and weather resistance. |
Food and Beverage | Mobile catering and food delivery | Improved service reach and freshness of products | Evaluate temperature control systems and hygiene compliance. |
Healthcare | Patient transport and medical equipment delivery | Timely access to critical services and equipment | Ensure compliance with health regulations and specialized storage needs. |
Retail | Pop-up shops and mobile retail solutions | Increased market reach and customer engagement | Focus on branding opportunities and modular design options. |
How is Box Truck Custom Used in Logistics and Transportation?
In the logistics and transportation sector, box trucks are customized to facilitate efficient e-commerce deliveries. These vehicles can be tailored with specialized shelving, loading ramps, and secure storage options to accommodate varying product sizes. The primary challenge addressed is the need for timely deliveries while maintaining package integrity. International B2B buyers should focus on sourcing trucks that offer optimal load capacities and fuel efficiency, as these factors can significantly impact operational costs and service reliability.
What Role Does Box Truck Custom Play in Construction?
In construction, box trucks serve as essential tools for transporting materials and equipment directly to job sites. Customization may include reinforced interiors for heavy loads and secure storage compartments for tools. This application solves the issue of material loss and project delays caused by inefficient transport. Buyers from regions like Africa and South America should prioritize trucks that meet local road regulations and can withstand rugged terrains, ensuring reliability in diverse environments.
How is Box Truck Custom Beneficial for Food and Beverage Delivery?
Box trucks are increasingly employed in the food and beverage industry for mobile catering and delivery services. Custom features such as refrigeration units and insulated compartments ensure the freshness and safety of products during transport. This application addresses the critical need for maintaining food quality while expanding service areas. Buyers should consider sourcing trucks with advanced temperature control systems and compliance with health regulations, especially in regions with varying climate conditions.
In What Ways Does Box Truck Custom Support Healthcare Services?
In the healthcare sector, box trucks are customized for the transport of patients and medical equipment. Features may include specialized seating for patient comfort and secure storage for sensitive medical devices. The challenge of ensuring timely access to healthcare services is mitigated by these tailored solutions. Buyers should ensure that the trucks comply with health regulations and incorporate necessary safety features, particularly in regions where healthcare logistics can be complex.
How Can Retail Benefit from Custom Box Trucks?
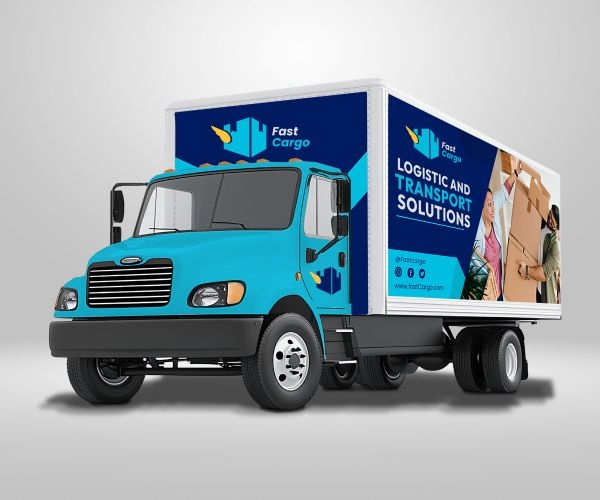
A stock image related to box truck custom.
Retail businesses utilize customized box trucks for pop-up shops and mobile retail solutions, allowing them to engage customers in various locations. Custom designs can include branding opportunities and flexible layouts that adapt to different sales environments. This application addresses the need for increased market reach while enhancing customer interaction. B2B buyers should focus on sourcing trucks that offer modular designs, enabling quick reconfiguration for different retail scenarios.
Related Video: Warnerwoods Company uses a perpetual Inventory System
3 Common User Pain Points for ‘box truck custom’ & Their Solutions
Scenario 1: Navigating Customization Complexity in Box Trucks
The Problem:
B2B buyers often face the challenge of navigating the complexity of customization options for box trucks. With various configurations available, including different sizes, shelving options, and specialized equipment, it can be overwhelming to determine which combination best suits their operational needs. This confusion can lead to purchasing the wrong vehicle, resulting in wasted resources and operational inefficiencies.
The Solution:
To address this issue, buyers should start by conducting a thorough needs assessment of their logistics and operational requirements. Collaborate with your team to list the specific items that will be transported, their dimensions, and the frequency of deliveries. Once you have a clear understanding of your needs, engage with a manufacturer or dealer that specializes in box truck customization. Ask for case studies or examples of similar businesses to guide your choices. Additionally, consider utilizing software tools that allow for virtual customization, enabling you to visualize the end product before making a decision. This proactive approach minimizes the risk of costly errors and ensures that the box truck fits your operational profile perfectly.
Scenario 2: Overcoming Delivery Delays in Custom Orders
The Problem:
Another common pain point for B2B buyers is the potential for delivery delays when ordering custom box trucks. Manufacturing lead times can vary significantly based on the complexity of the customization and the supplier’s capacity, which may disrupt planned operations or logistics schedules. Such delays can result in financial losses, especially for businesses reliant on timely deliveries to clients.
The Solution:
To mitigate delivery delays, it is crucial to establish clear communication with your supplier from the outset. Inquire about the average lead times for specific customizations and request a detailed timeline for your order. Consider setting milestones for updates throughout the production process, allowing you to monitor progress and address any issues promptly. Furthermore, it may be beneficial to maintain a strong relationship with multiple suppliers to diversify your options and ensure availability. Building a buffer in your logistics planning can also provide flexibility in case of unforeseen delays. By proactively managing timelines and supplier communications, you can better align your operations with delivery schedules.
Scenario 3: Ensuring Compliance with Local Regulations
The Problem:
Compliance with local regulations regarding vehicle specifications can be a significant hurdle for B2B buyers of custom box trucks. Different regions may have specific requirements regarding weight limits, emissions standards, and safety features. Failure to adhere to these regulations can result in hefty fines and operational disruptions.
The Solution:
To ensure compliance, start by researching the specific regulations that apply to your region or target market. Consult with local transportation authorities or industry bodies to obtain the most accurate and up-to-date information. When engaging with manufacturers, explicitly discuss your compliance requirements to ensure they can meet local regulations during the customization process. Additionally, consider working with a logistics consultant who specializes in regulatory compliance to guide you through the complexities of vehicle specifications. This approach will not only help you avoid penalties but also enhance your company’s reputation as a responsible operator in your industry.
Strategic Material Selection Guide for box truck custom
What Are the Key Materials for Custom Box Trucks?
When selecting materials for custom box trucks, it’s essential to consider their properties, advantages, and limitations. The choice of material impacts durability, cost, and suitability for specific applications. Below, we analyze four common materials used in the construction of custom box trucks: aluminum, steel, fiberglass, and composite materials.
How Does Aluminum Perform in Custom Box Truck Construction?
Key Properties:
Aluminum is lightweight, corrosion-resistant, and has a high strength-to-weight ratio. It can withstand temperatures ranging from -50°C to 150°C, making it suitable for various climates.
Pros & Cons:
The primary advantage of aluminum is its lightweight nature, which enhances fuel efficiency and payload capacity. However, it can be more expensive than steel and is less durable under heavy impact, making it less suitable for high-stress applications.
Impact on Application:
Aluminum is ideal for transporting goods that require a lightweight solution without sacrificing strength, such as electronics or perishable items.
Considerations for International Buyers:
Buyers from regions like Africa and South America should ensure compliance with local regulations regarding aluminum use in transportation. Standards such as ASTM B209 for aluminum sheet and plate may apply.
What Are the Benefits of Using Steel in Box Truck Customization?
Key Properties:
Steel offers excellent tensile strength and can handle high-pressure applications. It is less prone to deformation under heavy loads and has a temperature tolerance of -40°C to 200°C.
Pros & Cons:
The main advantage of steel is its durability and resistance to wear and tear. However, it is heavier than aluminum, which can reduce fuel efficiency and increase operational costs. Additionally, steel is prone to rust if not properly treated.
Impact on Application:
Steel is suitable for heavy-duty applications, such as transporting construction materials or machinery. Its robustness makes it a preferred choice for industries requiring high durability.
Considerations for International Buyers:
Compliance with standards such as ASTM A36 for structural steel is crucial. Buyers should also consider the availability of galvanized options to mitigate corrosion, especially in humid climates.
Why Choose Fiberglass for Custom Box Trucks?
Key Properties:
Fiberglass is lightweight, non-corrosive, and offers good thermal insulation. It can withstand temperatures from -20°C to 80°C.
Pros & Cons:
Fiberglass is resistant to rust and corrosion, making it ideal for environments with moisture. However, it can be more expensive than steel and aluminum and may not be as strong under heavy loads.
Impact on Application:
This material is excellent for transporting sensitive items that require temperature control, such as pharmaceuticals or food products.
Considerations for International Buyers:
Buyers should ensure compliance with local standards for fiberglass construction, such as ASTM D638 for tensile properties. Understanding the local market for fiberglass suppliers is also essential, particularly in regions like Europe and the Middle East.
What Advantages Do Composite Materials Offer for Box Truck Customization?
Key Properties:
Composite materials combine various materials to enhance performance. They typically offer high strength, low weight, and resistance to corrosion and chemicals.
Pros & Cons:
The primary advantage of composites is their versatility and ability to be tailored for specific applications. However, they can be costly and may require specialized manufacturing processes.
Impact on Application:
Composites are ideal for specialized applications, such as transporting hazardous materials or in environments where weight reduction is critical.
Considerations for International Buyers:
Compliance with international standards like ISO 9001 for quality management is vital. Buyers should also be aware of the potential for higher costs and longer lead times associated with composite materials.
Summary Table of Material Selection for Box Truck Custom
Material | Typical Use Case for Box Truck Custom | Key Advantage | Key Disadvantage/Limitation | Relative Cost (Low/Med/High) |
---|---|---|---|---|
Aluminum | Lightweight cargo transport | High strength-to-weight ratio | Higher cost and lower impact resistance | Medium |
Steel | Heavy-duty applications | Excellent durability and wear resistance | Heavier weight and potential for rust | Low |
Fiberglass | Temperature-sensitive goods | Corrosion-resistant and good insulation | Higher cost and lower load-bearing capacity | High |
Composite | Specialized hazardous material transport | Tailored performance and low weight | High cost and complex manufacturing | High |
This strategic material selection guide provides international B2B buyers with critical insights into the properties, advantages, and considerations for each material, enabling informed decisions for custom box truck construction.
In-depth Look: Manufacturing Processes and Quality Assurance for box truck custom
What Are the Main Manufacturing Stages for Custom Box Trucks?
Manufacturing custom box trucks involves a series of critical stages, each designed to ensure the vehicle meets specific requirements and quality standards. Understanding these stages helps international B2B buyers make informed decisions when sourcing from suppliers.
-
Material Preparation: The first step involves selecting high-quality materials suitable for the truck’s structure and functionality. Common materials include steel for the frame, aluminum for lightweight components, and specialized plastics for interior fittings. Suppliers must ensure that all materials comply with international standards to guarantee durability and performance.
-
Forming Processes: This stage encompasses various techniques such as stamping, welding, and bending. Stamping is used to create body panels, while welding is essential for assembling the frame. Advanced technologies like laser cutting and CNC machining may also be employed for precision. Each technique must be carefully monitored to maintain tolerances and ensure a robust build.
-
Assembly: During the assembly phase, components such as the chassis, engine, and box body are integrated. Skilled labor is crucial here, as the quality of assembly directly impacts the vehicle’s performance. Automated assembly lines can enhance efficiency, but manual inspection remains vital to catch any discrepancies.
-
Finishing: The final stage includes painting, coating, and detailing. A high-quality finish not only improves aesthetics but also provides protection against the elements. This stage often involves multiple quality checks to ensure consistency and adherence to specifications.
How Do Quality Assurance Practices Ensure High Standards in Box Truck Manufacturing?
Quality assurance (QA) is paramount in the manufacturing of custom box trucks, ensuring that each vehicle meets industry standards and client specifications. Here’s how QA practices are integrated into the manufacturing process:
-
Adherence to International Standards: Many manufacturers comply with ISO 9001, which sets criteria for a quality management system. This certification ensures that suppliers consistently provide products that meet customer and regulatory requirements. Additional certifications like CE marking for European markets and API standards for specific industries may also apply.
-
Key Quality Control Checkpoints: Implementing checkpoints throughout the manufacturing process is essential for identifying defects early. Common checkpoints include:
– Incoming Quality Control (IQC): Inspects materials upon arrival to ensure they meet predefined standards.
– In-Process Quality Control (IPQC): Conducts inspections during the manufacturing process to catch issues as they arise.
– Final Quality Control (FQC): Evaluates the completed box truck against specifications before delivery. -
Common Testing Methods: Various testing methods are employed to verify the integrity and performance of the box trucks. These may include:
– Static and dynamic load testing to assess structural integrity.
– Leak tests for water-tightness in the box body.
– Road testing to evaluate performance under real-world conditions.
How Can B2B Buyers Verify Supplier Quality Control?
For international B2B buyers, especially those from diverse regions like Africa, South America, the Middle East, and Europe, verifying supplier quality control is crucial. Here are actionable steps to ensure suppliers meet high standards:
-
Conducting Audits: Regular audits of the manufacturing facility can provide insights into the supplier’s adherence to quality standards. Buyers should request audit reports and ensure they include checks on compliance with ISO standards and any relevant industry certifications.
-
Reviewing Quality Reports: Suppliers should provide detailed quality reports that outline testing results, defect rates, and corrective actions taken. This transparency is key to understanding the supplier’s commitment to quality.
-
Third-Party Inspections: Engaging third-party inspection agencies can add an extra layer of assurance. These agencies can conduct unbiased inspections at various stages of production, ensuring that the supplier adheres to the agreed-upon quality standards.
What Are the Quality Control Nuances for International Buyers?
International B2B buyers must navigate various quality control nuances when sourcing custom box trucks. Understanding these factors can significantly influence sourcing decisions:
-
Cultural and Regulatory Differences: Quality standards can vary significantly across regions. Buyers should familiarize themselves with local regulations and standards in their target markets to ensure compliance. For instance, European buyers must consider EU regulations, while Middle Eastern buyers may need to adhere to Gulf Standards.
-
Communication Barriers: Clear communication is vital for ensuring that specifications are understood and met. Buyers should establish a robust communication plan with suppliers to address any potential misunderstandings early in the manufacturing process.
-
Logistical Challenges: The transportation of custom box trucks can present challenges related to quality assurance. Buyers should consider how transportation methods could impact the vehicle’s condition upon arrival and ensure that suppliers employ proper handling and shipping practices.
-
Post-Delivery Support: Quality assurance doesn’t end with delivery. B2B buyers should inquire about post-delivery support, including warranties, service options, and availability of spare parts, to ensure ongoing quality management after the sale.
Conclusion
A comprehensive understanding of the manufacturing processes and quality assurance practices for custom box trucks is essential for international B2B buyers. By focusing on key manufacturing stages, implementing rigorous quality control measures, and verifying supplier practices, buyers can ensure they source high-quality vehicles that meet their operational needs. Investing time in these areas can lead to significant long-term benefits, including improved performance, reduced maintenance costs, and enhanced customer satisfaction.
Practical Sourcing Guide: A Step-by-Step Checklist for ‘box truck custom’
Introduction
Navigating the procurement process for custom box trucks can be complex, especially for international B2B buyers. This checklist is designed to provide a clear and actionable roadmap to ensure you make informed decisions that align with your business needs. From defining specifications to selecting the right suppliers, each step is crucial for a successful sourcing experience.
Step 1: Define Your Technical Specifications
Understanding the specific requirements for your custom box truck is essential. This includes dimensions, weight capacity, engine type, and any specialized features like refrigeration or branding options. Clearly defined specifications help streamline communications with suppliers and ensure that the end product meets your operational needs.
- Consider your industry: Different industries may require unique features. For example, food transport might need refrigeration, while construction might prioritize durability.
- Document everything: Create a detailed specification sheet to share with potential suppliers.
Step 2: Research Potential Suppliers
A thorough research process will help you identify reputable suppliers capable of delivering quality custom box trucks. Investigate their track record, product offerings, and client testimonials.
- Use multiple sources: Check online directories, industry forums, and trade shows to gather information.
- Look for local suppliers: Especially for buyers in Africa, South America, and the Middle East, local suppliers may offer better support and understanding of regional regulations.
Step 3: Evaluate Supplier Certifications
Before proceeding, verify that potential suppliers possess the necessary certifications and licenses. This ensures compliance with international standards and local regulations, which can vary significantly across regions.
- Check quality certifications: Look for ISO certifications or industry-specific endorsements.
- Confirm manufacturing capabilities: Ensure they have the technology and workforce to meet your specifications.
Step 4: Request Detailed Quotations
Once you have shortlisted potential suppliers, request detailed quotations that outline the cost, delivery times, and payment terms. This is crucial for budgeting and financial planning.
- Compare apples to apples: Ensure that all quotes are based on the same specifications to accurately compare costs.
- Clarify payment terms: Understand whether upfront payments, milestones, or post-delivery payments are required.
Step 5: Conduct Factory Visits or Virtual Tours
If feasible, arrange factory visits or virtual tours to assess the supplier’s production capabilities and quality control processes. This step can provide invaluable insights into their operational standards and commitment to quality.
- Observe the production process: Look for adherence to safety protocols and quality assurance measures.
- Meet the team: Engaging with the manufacturing team can foster better communication and collaboration.
Step 6: Negotiate Terms and Conditions
Once you’ve identified a preferred supplier, it’s time to negotiate terms. This includes pricing, lead times, warranties, and after-sales support. Strong negotiations can lead to better deals and ensure long-term satisfaction.
- Be clear about your needs: Communicate your expectations regarding delivery timelines and service levels.
- Consider long-term partnerships: Building a relationship with your supplier can yield benefits in future transactions.
Step 7: Finalize the Contract
Before signing any agreements, ensure that all terms are clearly defined and understood by both parties. A well-structured contract protects your interests and outlines the responsibilities of each party.
- Include performance metrics: Specify quality standards, delivery schedules, and penalties for non-compliance.
- Consult a legal expert: If possible, have a legal professional review the contract to avoid potential issues.
Following this step-by-step checklist will enhance your sourcing process for custom box trucks, helping you make informed decisions that align with your business objectives.
Comprehensive Cost and Pricing Analysis for box truck custom Sourcing
What Are the Key Cost Components in Box Truck Custom Sourcing?
When sourcing custom box trucks, understanding the cost structure is paramount for international B2B buyers. The primary cost components include:
-
Materials: The choice of materials significantly impacts cost. High-quality steel, aluminum, or composite materials may be more expensive but offer durability and longevity, which can be crucial for transporting goods across diverse terrains.
-
Labor: Labor costs vary by region. Countries with lower labor costs may provide a price advantage, but it’s essential to consider the skill level and experience of the workforce, which can influence the quality of the final product.
-
Manufacturing Overhead: This includes costs related to utilities, facility maintenance, and administrative expenses. Efficient manufacturing processes can help reduce overhead costs, providing savings that can be passed on to buyers.
-
Tooling: Custom designs often require specialized tooling. The initial investment in tooling can be high, but it’s a one-time cost that can be amortized over large production runs.
-
Quality Control (QC): Implementing rigorous QC processes ensures that the box trucks meet international standards. While this adds to the upfront costs, it can prevent costly recalls or repairs in the future.
-
Logistics: Shipping costs must be factored into the total price. This includes freight forwarding, customs duties, and insurance, which can vary significantly depending on the destination and Incoterms used.
-
Margin: Suppliers typically add a profit margin to cover their risks and operational costs. Understanding the average margin in the industry can help in negotiations.
How Do Price Influencers Affect Box Truck Custom Costs?
Several factors can influence the pricing of custom box trucks:
-
Volume and Minimum Order Quantity (MOQ): Larger orders generally reduce the per-unit cost due to economies of scale. Establishing a long-term relationship with suppliers can also lead to better pricing.
-
Specifications and Customization: The complexity of specifications directly impacts costs. Highly customized trucks may require more specialized materials and labor, increasing the overall price.
-
Materials and Quality Certifications: Sourcing certified materials may lead to higher costs, but it often ensures compliance with safety and regulatory standards, which is crucial for international operations.
-
Supplier Factors: The reputation and reliability of the supplier can affect pricing. Established suppliers with proven track records may command higher prices but offer better quality assurance and support.
-
Incoterms: The chosen Incoterms can significantly influence logistics costs and responsibilities. Understanding the implications of terms like FOB (Free on Board) or CIF (Cost, Insurance, and Freight) is vital for accurate cost estimation.
What Tips Can Help International B2B Buyers Negotiate Better Prices?
-
Negotiate Effectively: Always approach negotiations with a clear understanding of your needs and budget. Leveraging multiple supplier quotes can provide negotiating power.
-
Focus on Cost-Efficiency: Look beyond the initial price. Consider the Total Cost of Ownership (TCO), which includes maintenance, fuel efficiency, and resale value, to assess the overall value.
-
Understand Pricing Nuances: Be aware of regional market conditions that may affect pricing. For instance, fluctuations in currency exchange rates can impact costs for buyers from Africa or South America.
-
Build Relationships: Establishing long-term relationships with suppliers can lead to better terms and preferential pricing over time.
-
Stay Informed on Market Trends: Keeping abreast of industry trends and economic conditions can provide insights into when to purchase and how to negotiate effectively.
Disclaimer on Indicative Prices
Prices for custom box trucks are highly variable based on the factors discussed above. Buyers are encouraged to conduct thorough market research and obtain multiple quotes before making purchasing decisions. This approach not only aids in understanding the market better but also helps in striking the most advantageous deals.
Alternatives Analysis: Comparing box truck custom With Other Solutions
When considering logistics and transportation solutions, it’s essential for international B2B buyers to evaluate various alternatives alongside the ‘box truck custom’. This section will provide a comparative analysis of box truck custom against two viable alternatives: cargo vans and freight trailers. Each option has distinct characteristics that may suit different operational needs.
Comparison Table of Box Truck Custom and Alternatives
Comparison Aspect | Box Truck Custom | Cargo Van | Freight Trailer |
---|---|---|---|
Performance | High load capacity | Moderate load capacity | Very high load capacity |
Cost | Moderate initial investment | Lower initial investment | Higher initial investment |
Ease of Implementation | Requires customization | Quick setup | Longer setup time |
Maintenance | Moderate upkeep | Lower maintenance costs | Higher maintenance costs |
Best Use Case | Urban deliveries | Small to medium deliveries | Long-distance transport |
What Are the Pros and Cons of Using Cargo Vans as an Alternative?
Cargo vans are versatile vehicles that offer a good balance between load capacity and maneuverability. One of their main advantages is their lower initial investment compared to box trucks, making them an appealing option for businesses with budget constraints. They also require less maintenance, which can lead to lower operational costs over time. However, their load capacity is limited, which may not be sufficient for larger shipments. Additionally, their smaller size can be a disadvantage in urban areas with heavy traffic, where larger trucks may have more space to operate.
How Do Freight Trailers Compare to Box Truck Custom?
Freight trailers are designed for heavy-duty transport, offering a significantly higher load capacity than box trucks. This makes them ideal for businesses that need to transport large quantities of goods over long distances. However, the higher initial investment and maintenance costs can be a drawback, especially for smaller businesses. Additionally, freight trailers typically require a specific vehicle for towing, which can complicate logistics and increase costs. The setup time for freight trailers is also longer, as they often need to be connected to a tractor unit, making them less suitable for quick urban deliveries.
How Can B2B Buyers Choose the Right Solution for Their Needs?
When selecting the right transportation solution, B2B buyers should consider several factors, including their specific operational requirements, budget, and the nature of the goods being transported. For businesses focused on urban deliveries with moderate load requirements, a box truck custom may provide the ideal balance of performance and cost. In contrast, if budget constraints are a priority and the load is manageable, cargo vans could be a more economical choice. On the other hand, for companies dealing with high-volume shipments over long distances, investing in freight trailers may ultimately be more efficient despite the higher costs. By thoroughly analyzing these factors, buyers can make informed decisions that align with their logistical needs.
Essential Technical Properties and Trade Terminology for box truck custom
What Are the Key Technical Properties of Box Truck Customization?
When considering box truck customization, understanding the technical properties is essential for B2B buyers. Here are critical specifications that play a pivotal role in the selection process:
-
Material Grade
The material grade refers to the quality of the materials used in the construction of the box truck. Common materials include aluminum, steel, and fiberglass. The choice of material affects durability, weight, and cost. For instance, aluminum is lightweight and resistant to corrosion, making it ideal for maximizing payload capacity, while steel offers strength and resilience for heavy-duty applications. -
Load Capacity
Load capacity is the maximum weight a box truck can carry safely. This specification is crucial for buyers who need to transport heavy goods. Understanding the load capacity ensures compliance with local regulations and helps prevent overloading, which can lead to accidents or damage to the vehicle. -
Dimensions and Tolerance
The dimensions of the box truck, including length, width, and height, must meet specific requirements for loading and unloading goods. Tolerance refers to the allowable variation in these dimensions. Accurate dimensions and tolerances are vital for ensuring that the truck fits into loading docks and adheres to international shipping standards. -
Thermal Insulation
For businesses transporting temperature-sensitive products, thermal insulation is a critical property. Insulated box trucks help maintain the required temperature for perishable goods, thus ensuring product integrity during transit. Buyers should evaluate the R-value (thermal resistance) of the insulation material to ensure it meets their needs. -
Chassis Configuration
The chassis configuration includes the type of chassis used, such as single or dual rear axle, which affects handling and weight distribution. Understanding chassis options is vital for buyers looking for specific performance characteristics, especially for off-road or urban environments. -
Safety Features
Safety features such as anti-lock braking systems (ABS), stability control, and reinforced structures are essential for protecting both the driver and cargo. Buyers should prioritize these features to minimize risks associated with transporting goods.
What Common Trade Terms Should B2B Buyers Know?
In addition to understanding technical properties, familiarity with industry terminology is critical for navigating the box truck customization market. Here are some common terms:
-
OEM (Original Equipment Manufacturer)
OEM refers to the company that originally manufactured the components of a vehicle. In box truck customization, buyers often seek OEM parts for reliability and compatibility, ensuring that the customizations meet original specifications. -
MOQ (Minimum Order Quantity)
MOQ is the smallest number of units a supplier is willing to sell. For B2B buyers, understanding MOQ is essential for budgeting and inventory management. It can also indicate the supplier’s capability and willingness to serve smaller businesses or niche markets. -
RFQ (Request for Quotation)
An RFQ is a document sent to suppliers requesting pricing and terms for specific products or services. For international buyers, issuing an RFQ can facilitate competitive pricing and ensure that all potential suppliers are evaluated based on the same criteria. -
Incoterms (International Commercial Terms)
Incoterms are a set of predefined international trade terms that clarify the responsibilities of buyers and sellers regarding shipping costs, risk, and delivery. Familiarity with these terms is crucial for B2B buyers engaged in international transactions to avoid misunderstandings and ensure smooth logistics. -
Lead Time
Lead time refers to the amount of time it takes from placing an order to receiving it. Understanding lead times is critical for B2B buyers who need to plan their inventory and production schedules accordingly. -
Customization Options
This term encompasses the various alterations and enhancements available for box trucks, including size, interior layout, and specialized equipment. Buyers should assess their specific needs and communicate these clearly to suppliers to ensure that the final product meets their operational requirements.
Understanding these technical properties and trade terms will empower international B2B buyers to make informed decisions when customizing box trucks, ensuring that they select the right specifications and navigate the procurement process smoothly.
Navigating Market Dynamics and Sourcing Trends in the box truck custom Sector
What Are the Key Market Trends Influencing the Box Truck Custom Sector?
The global box truck custom sector is experiencing a transformative shift driven by various market dynamics and technological advancements. One of the primary drivers is the increasing demand for last-mile delivery solutions, particularly in urban areas across Africa, South America, the Middle East, and Europe. The rise of e-commerce has accelerated the need for customized vehicles that can navigate narrow streets and tight spaces while maximizing cargo capacity.
Emerging technologies, such as telematics and fleet management software, are enhancing operational efficiency for businesses in this sector. These technologies enable real-time tracking, predictive maintenance, and optimized routing, significantly reducing operational costs and improving service delivery. Additionally, the integration of electric and hybrid powertrains is gaining momentum as companies seek to lower their carbon footprints and comply with stringent environmental regulations.
International B2B buyers must also consider the impact of geopolitical factors, such as trade agreements and tariffs, which can influence sourcing strategies. For instance, buyers from the Middle East may benefit from favorable trade terms with European manufacturers, while South American buyers may need to navigate complex import regulations. Understanding these dynamics is crucial for making informed procurement decisions.
How Is Sustainability Shaping Sourcing Practices in the Box Truck Custom Sector?
Sustainability is increasingly becoming a pivotal concern for businesses sourcing box trucks. The environmental impact of traditional manufacturing processes and the logistics involved in transporting heavy vehicles has prompted many buyers to prioritize ethical sourcing. This shift is evident in the growing demand for ‘green’ certifications and materials.
B2B buyers should seek suppliers that utilize sustainable materials, such as recycled steel and eco-friendly composites, in their box truck manufacturing processes. Certifications like ISO 14001, which focuses on effective environmental management systems, are becoming essential for suppliers aiming to demonstrate their commitment to sustainability. Furthermore, many manufacturers are adopting life cycle assessment (LCA) methodologies to evaluate the environmental impact of their products from production to disposal.
By prioritizing sustainability in their sourcing strategies, international buyers not only contribute to environmental conservation but also enhance their brand reputation. As consumers increasingly favor companies with strong sustainability credentials, B2B buyers can leverage ethical sourcing as a competitive advantage in the marketplace.
What Is the Historical Context of the Box Truck Custom Sector?
The box truck custom sector has evolved significantly over the decades, adapting to changing consumer needs and technological advancements. Initially, box trucks were primarily used for freight and industrial applications. However, as urbanization intensified and e-commerce began to flourish in the late 20th century, the demand for versatile and customizable box trucks grew.
The integration of advanced manufacturing techniques, such as computer-aided design (CAD) and 3D printing, has revolutionized the customization process. Today, buyers can specify their requirements in detail, from the size and shape of the cargo area to the inclusion of specialized features like refrigeration units or branding options. This evolution reflects a broader trend towards personalization in the B2B sector, where tailored solutions are increasingly viewed as essential for competitive differentiation.
Understanding this historical context helps international buyers appreciate the advancements that have shaped the box truck custom sector and underscores the importance of staying abreast of emerging trends and technologies.
Frequently Asked Questions (FAQs) for B2B Buyers of box truck custom
-
How do I ensure the quality of custom box trucks from international suppliers?
To ensure quality, conduct thorough research on potential suppliers. Request samples or visit manufacturing facilities if possible. Verify certifications and compliance with international standards, such as ISO or local regulations. Utilize third-party inspection services to assess production quality before shipment. Building a strong relationship with suppliers can also facilitate better quality control and responsiveness to your specifications. -
What are the best practices for vetting suppliers of custom box trucks?
Begin by checking the supplier’s reputation through reviews, testimonials, and industry references. Evaluate their production capabilities, experience, and financial stability. Request detailed information about their customization options, lead times, and previous projects. Consider using platforms like Alibaba or Global Sources, which often provide buyer protection and verification services to help ensure you’re working with legitimate suppliers. -
What customization options are available for box trucks?
Customization options for box trucks can include body dimensions, load capacity, interior fittings, and exterior finishes. Buyers can also specify features like refrigeration units, shelving systems, or specialized loading ramps. Discuss your specific needs with suppliers to understand the extent of customization available and ensure that the final product meets your operational requirements. -
What is the minimum order quantity (MOQ) for custom box trucks?
The MOQ for custom box trucks varies by supplier and the complexity of the customization. Generally, larger orders can result in lower per-unit costs. It’s advisable to negotiate MOQs based on your needs, especially if you’re a smaller business or just starting. Some suppliers may offer lower MOQs for first-time orders or sample units to establish a business relationship. -
What payment terms should I expect when sourcing custom box trucks internationally?
Payment terms can vary significantly among suppliers but typically include options such as a deposit upfront (often 30-50%), with the balance due before shipment or upon delivery. Some suppliers may offer financing or installment options. Ensure that payment methods are secure, such as using letters of credit or escrow services, which provide protection against fraud. -
How do I manage logistics and shipping for custom box trucks?
Managing logistics involves coordinating with your supplier to understand shipping options, costs, and timelines. Consider hiring a freight forwarder who specializes in international shipping to handle customs clearance and logistics efficiently. Ensure that shipping insurance is in place to protect against potential damages during transit. Plan for potential delays by factoring in customs processing times and local regulations. -
What are the common challenges in sourcing custom box trucks internationally?
Common challenges include language barriers, differing regulations, and cultural differences in business practices. Additionally, logistics can be complex, with potential delays in shipping and customs. To mitigate these risks, establish clear communication with suppliers, utilize legal contracts to outline terms, and consider engaging local consultants who understand the market dynamics of your target region. -
How can I ensure compliance with local regulations for custom box trucks?
Compliance with local regulations is crucial for the successful operation of your box trucks. Research the specific regulations in your country or region, which may include safety standards, emissions requirements, and licensing. Work closely with your supplier to ensure that the trucks meet these standards, and consider consulting with local regulatory bodies or legal experts to navigate complex compliance issues effectively.
Important Disclaimer & Terms of Use
⚠️ Important Disclaimer
The information provided in this guide, including content regarding manufacturers, technical specifications, and market analysis, is for informational and educational purposes only. It does not constitute professional procurement advice, financial advice, or legal advice.
While we have made every effort to ensure the accuracy and timeliness of the information, we are not responsible for any errors, omissions, or outdated information. Market conditions, company details, and technical standards are subject to change.
B2B buyers must conduct their own independent and thorough due diligence before making any purchasing decisions. This includes contacting suppliers directly, verifying certifications, requesting samples, and seeking professional consultation. The risk of relying on any information in this guide is borne solely by the reader.
Strategic Sourcing Conclusion and Outlook for box truck custom
What Are the Key Takeaways for International B2B Buyers of Custom Box Trucks?
In conclusion, strategic sourcing plays a pivotal role in the acquisition of custom box trucks, especially for international buyers from Africa, South America, the Middle East, and Europe. By establishing long-term partnerships with reliable suppliers, buyers can secure better pricing, quality, and delivery timelines. Understanding local regulations and market dynamics is essential for navigating complexities and ensuring compliance.
How Can B2B Buyers Position Themselves for Future Success?
As the demand for customized transportation solutions grows, international buyers should leverage technology and data analytics to optimize their sourcing processes. Embracing sustainable practices in sourcing can also enhance brand reputation and meet the increasing consumer demand for eco-friendly solutions.
What Steps Should You Take Next?
Moving forward, we encourage B2B buyers to actively engage with suppliers, participate in trade shows, and utilize digital platforms for sourcing. By staying informed about market trends and innovations, you can make informed decisions that will position your business for success in an ever-evolving landscape. Take the initiative today to explore new opportunities in the custom box truck market and drive your business forward.