Unlock Efficiency: The Ultimate 3D Printer Custom Guide (2025)
Introduction: Navigating the Global Market for 3d printer custom
Navigating the global market for 3D printer custom solutions can be a daunting task for international B2B buyers, especially when balancing factors like quality, cost, and supplier reliability. As industries increasingly adopt 3D printing technology for rapid prototyping and custom manufacturing, sourcing the right equipment becomes critical for maintaining competitive advantage. This guide delves into the multifaceted world of custom 3D printers, covering essential topics such as types of printers, applications across various sectors, effective supplier vetting strategies, and cost considerations.
By equipping buyers with actionable insights, this comprehensive resource empowers decision-makers from Africa, South America, the Middle East, and Europe—such as those in Thailand and the UK—to make informed purchasing decisions. Understanding the nuances of the 3D printing landscape not only enhances sourcing capabilities but also mitigates risks associated with vendor selection and product quality.
As you progress through this guide, you will uncover the best practices for identifying suitable suppliers, negotiating terms, and evaluating the total cost of ownership. With the right knowledge, you can confidently navigate the complexities of the 3D printing market and leverage its potential to drive innovation and efficiency in your business operations.
Understanding 3d printer custom Types and Variations
Type Name | Key Distinguishing Features | Primary B2B Applications | Brief Pros & Cons for Buyers |
---|---|---|---|
Fused Deposition Modeling (FDM) | Utilizes thermoplastic filaments; layer-by-layer construction | Prototyping, manufacturing tools, small parts | Pros: Cost-effective, easy to use. Cons: Limited material properties, slower than other methods. |
Stereolithography (SLA) | Uses UV light to cure resin; high-resolution prints | Medical devices, jewelry, detailed prototypes | Pros: High detail and smooth finish. Cons: More expensive materials, post-processing required. |
Selective Laser Sintering (SLS) | Uses lasers to fuse powdered materials; no support structures needed | Aerospace, automotive, complex geometries | Pros: Strong, functional parts; versatile materials. Cons: Higher initial costs, requires specialized knowledge. |
Digital Light Processing (DLP) | Projects light to cure resin; faster than SLA | Rapid prototyping, dental applications | Pros: Speed and detail; less post-processing. Cons: Limited material options, resin costs. |
Multi Jet Fusion (MJF) | Uses inkjet technology to apply agents on powder; high-speed production | Production parts, tooling, functional prototypes | Pros: High strength and detail; faster production. Cons: Expensive setup, limited material variety. |
What are the Key Characteristics of Fused Deposition Modeling (FDM)?
Fused Deposition Modeling (FDM) is one of the most popular 3D printing technologies, primarily due to its affordability and ease of use. It works by extruding thermoplastic filaments through a heated nozzle, which lays down layers in a controlled manner. FDM is particularly suitable for creating prototypes, manufacturing tools, and small parts. B2B buyers should consider the range of materials available, as well as the mechanical properties required for their applications, when choosing FDM printers.
How Does Stereolithography (SLA) Stand Out in 3D Printing?
Stereolithography (SLA) is renowned for its precision and ability to produce high-resolution prints with smooth surfaces. This technology employs UV light to cure liquid resin layer by layer, making it ideal for detailed applications such as medical devices, jewelry, and intricate prototypes. For B2B buyers, the key considerations include the cost of resin and the need for post-processing, which can add to the overall production time and expense.
What Makes Selective Laser Sintering (SLS) a Preferred Choice?
Selective Laser Sintering (SLS) uses a laser to fuse powdered materials, allowing for complex geometries without the need for support structures. This method is particularly useful in industries like aerospace and automotive, where strength and functionality are crucial. B2B buyers should weigh the higher initial costs and the expertise required to operate SLS printers against the benefits of producing strong, durable parts that can withstand rigorous testing.
Why Choose Digital Light Processing (DLP) for Rapid Prototyping?
Digital Light Processing (DLP) technology is recognized for its rapid production capabilities, as it uses a digital light projector to cure resin. This method is particularly beneficial for applications requiring high detail, such as dental models and rapid prototyping. Buyers should consider the trade-off between speed and material options, as DLP may have a limited selection of resins compared to other technologies.
How Does Multi Jet Fusion (MJF) Enhance Production Efficiency?
Multi Jet Fusion (MJF) is a cutting-edge technology that combines inkjet printing with powder bed fusion to create parts quickly and efficiently. MJF is ideal for producing functional prototypes and production parts in industries where strength and detail are essential. B2B buyers need to consider the initial setup costs and the limited range of materials available, but the benefits of speed and part quality often justify the investment.
Related Video: Bambu Studio | Adding and Removing Custom Supports
Key Industrial Applications of 3d printer custom
Industry/Sector | Specific Application of 3D Printer Custom | Value/Benefit for the Business | Key Sourcing Considerations for this Application |
---|---|---|---|
Aerospace | Custom tooling and prototypes for aircraft components | Reduced lead times and costs for custom parts | Material certifications, precision requirements |
Automotive | Production of lightweight, customized vehicle parts | Enhanced performance and fuel efficiency | Compatibility with existing systems, durability |
Medical Devices | Creation of patient-specific implants and surgical tools | Improved patient outcomes and reduced surgery times | Biocompatibility, regulatory compliance |
Consumer Electronics | Custom enclosures and parts for electronic devices | Faster product development and market entry | Design flexibility, material properties |
Construction | 3D-printed molds for concrete structures | Cost savings and faster construction timelines | Material strength, environmental considerations |
How is 3D Printer Custom Used in Aerospace?
In the aerospace industry, custom 3D printing is utilized for creating specialized tooling and prototypes of aircraft components. This technology enables manufacturers to produce lightweight and complex geometries that are often impossible to achieve with traditional manufacturing methods. The primary benefit is a significant reduction in lead times and costs associated with custom parts, allowing for rapid prototyping and iteration. International B2B buyers should focus on sourcing materials that meet stringent industry certifications and ensure the precision required for aerospace applications.
What are the Benefits of 3D Printing in Automotive Applications?
The automotive sector employs 3D printer custom technology for the production of lightweight, customized vehicle parts. This innovation leads to enhanced performance and fuel efficiency, as manufacturers can design components that are specifically tailored to their vehicles’ needs. Buyers in this sector must consider the compatibility of 3D-printed parts with existing systems and ensure the durability of materials used, as automotive applications often face rigorous conditions.
How is 3D Printing Revolutionizing Medical Devices?
3D printing is transforming the medical device industry by enabling the creation of patient-specific implants and surgical tools. This customization leads to improved patient outcomes, as devices can be tailored to the unique anatomy of individual patients, reducing surgery times and enhancing recovery. For international B2B buyers, it is crucial to ensure that materials used are biocompatible and comply with local regulatory standards to avoid complications in the supply chain.
How Does 3D Printing Impact Consumer Electronics?
In the consumer electronics industry, custom 3D printing is used for creating bespoke enclosures and parts for electronic devices. This capability allows companies to accelerate product development cycles and get to market faster with unique offerings. Buyers should prioritize design flexibility and the specific material properties required for electronic applications to ensure optimal performance and durability of the final products.
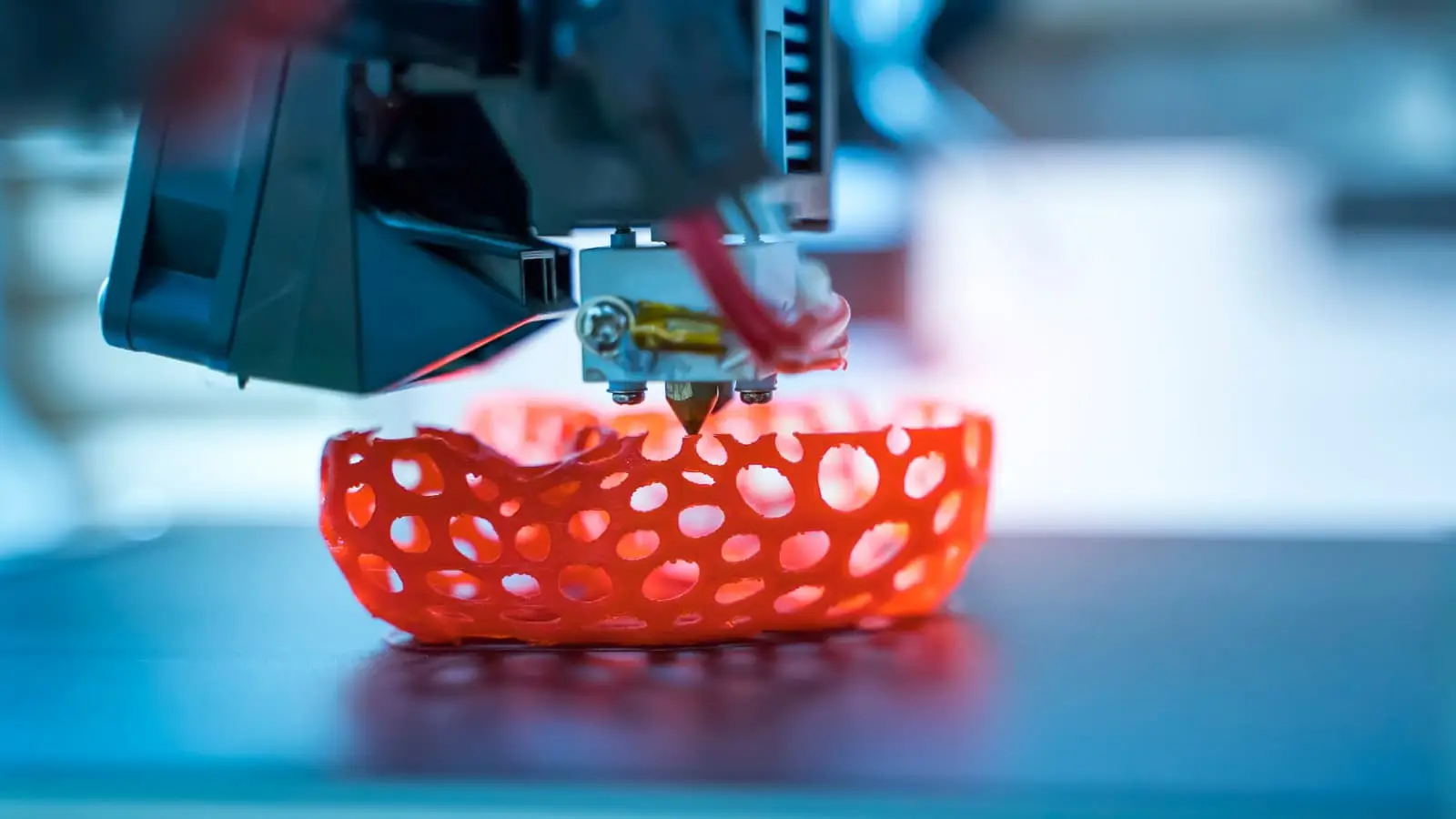
A stock image related to 3d printer custom.
What Role Does 3D Printing Play in Construction?
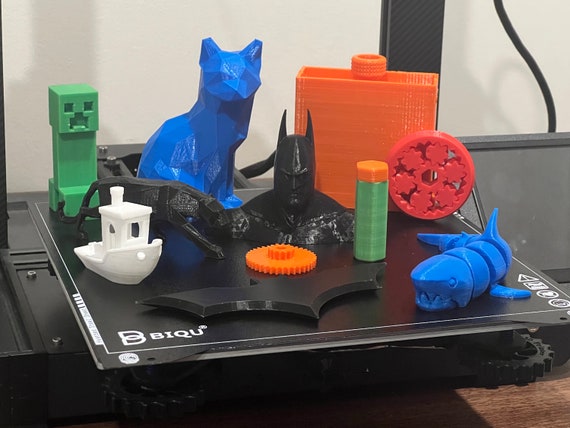
A stock image related to 3d printer custom.
3D printer custom technology is increasingly applied in the construction industry for producing molds used in concrete structures. This application leads to significant cost savings and faster timelines, as traditional mold-making processes can be time-consuming and labor-intensive. When sourcing for this application, buyers should consider material strength and environmental factors, as these elements can greatly influence the sustainability and longevity of construction projects.
Related Video: Introducing The Markforged Metal X 3D Printer | The Complete Metal 3D Printing Solution
3 Common User Pain Points for ‘3d printer custom’ & Their Solutions
Scenario 1: Difficulty in Achieving Design Precision with Custom 3D Printing
The Problem:
B2B buyers often encounter challenges with achieving the exact design specifications required for their projects. This is particularly true in industries such as aerospace, automotive, and medical, where precision is non-negotiable. Buyers may receive prototypes or final products that deviate from the intended design due to limitations in the 3D printing technology used or the material properties. This not only leads to wasted resources but also delays in project timelines and increased costs.
The Solution:
To overcome design precision issues, B2B buyers should prioritize selecting a 3D printing service provider that specializes in high-resolution printing technologies, such as SLA (Stereolithography) or SLS (Selective Laser Sintering). These technologies offer superior detail and can handle intricate designs more effectively than standard FDM (Fused Deposition Modeling) printers. Furthermore, buyers should ensure they provide comprehensive design specifications, including tolerances, material requirements, and intended use cases. Engaging in a collaborative design review process with the provider can also help identify potential pitfalls early on, allowing for adjustments before the printing process begins.
Scenario 2: Inadequate Material Options for Custom 3D Printing
The Problem:
Another common pain point for international B2B buyers is the limited range of materials available for custom 3D printing. Different industries require specific material characteristics, such as durability, flexibility, heat resistance, or biocompatibility. When suppliers offer only a narrow selection, it can result in either subpar products or the need to seek out multiple vendors, complicating supply chains and increasing costs.
The Solution:
To address material limitations, buyers should conduct thorough research on suppliers that provide a broad spectrum of materials, including metals, thermoplastics, ceramics, and bio-materials. Engaging with suppliers that have partnerships with material manufacturers can also enhance the range of options available. It’s essential to inquire about the properties of each material and request sample prints to assess their suitability for specific applications. Additionally, buyers can consider investing in post-processing services, such as coating or treatment, to enhance the performance characteristics of the printed parts, thereby expanding the functional capabilities of their products.
Scenario 3: Lack of Expertise in 3D Printing Technology
The Problem:
A significant challenge faced by many B2B buyers, especially those entering the 3D printing space for the first time, is the lack of in-house expertise related to the technology. This gap can lead to suboptimal usage of 3D printing capabilities, resulting in inefficiencies, increased costs, and misalignment with business objectives. Buyers may struggle with selecting the right technology, material, and processes, which can ultimately affect product quality and time-to-market.
The Solution:
To bridge the expertise gap, buyers should consider partnering with experienced 3D printing consultants or providers that offer advisory services. These experts can guide organizations through the complexities of 3D printing, from design optimization to material selection and production processes. Additionally, investing in training programs for staff can enhance in-house capabilities, ensuring that the team is well-equipped to leverage 3D printing effectively. Buyers should also take advantage of online resources, webinars, and industry forums to stay informed about the latest advancements and best practices in 3D printing. This proactive approach not only improves product outcomes but also fosters innovation within the organization.
Strategic Material Selection Guide for 3d printer custom
What Are the Key Properties of Common 3D Printing Materials?
When selecting materials for custom 3D printing, it is crucial to understand the properties that affect product performance. Here, we analyze four common materials used in 3D printing: PLA, ABS, PETG, and Nylon. Each material has unique characteristics that make it suitable for specific applications.
How Does PLA Perform in 3D Printing?
Polylactic Acid (PLA) is a biodegradable thermoplastic derived from renewable resources like corn starch. It is known for its ease of use and excellent print quality.
- Key Properties: PLA has a lower melting temperature (around 180-220°C) and is not very heat-resistant. It exhibits good tensile strength but can be brittle under stress.
- Pros & Cons: The advantages of PLA include its low cost, minimal warping, and vibrant color options. However, it has limited durability and is not suitable for high-temperature applications.
- Impact on Application: PLA is ideal for prototyping and decorative items but may not withstand harsh environmental conditions.
- Considerations for International Buyers: Buyers should ensure compliance with local environmental regulations, as PLA is biodegradable. Familiarity with standards like ASTM D6400 can be advantageous.
What Are the Advantages and Disadvantages of ABS?
Acrylonitrile Butadiene Styrene (ABS) is a widely used thermoplastic known for its toughness and impact resistance.
- Key Properties: ABS has a higher melting point (around 220-260°C) and is more heat-resistant than PLA. It also offers good chemical resistance.
- Pros & Cons: The material is durable and suitable for functional parts. However, it can warp during printing and requires a heated bed for optimal results, increasing manufacturing complexity.
- Impact on Application: ABS is commonly used for automotive parts and consumer goods due to its strength and resilience.
- Considerations for International Buyers: Compliance with standards such as ASTM D3965 is essential, particularly in industries like automotive. Buyers should also consider the availability of heated print beds in their region.
Why Is PETG Gaining Popularity in 3D Printing?
Polyethylene Terephthalate Glycol (PETG) is a modified version of PET, known for its excellent clarity and strength.
- Key Properties: PETG has a melting temperature similar to ABS (around 230-250°C) and offers good chemical resistance and flexibility.
- Pros & Cons: PETG is less prone to warping compared to ABS and is easier to print than Nylon. However, it can be more expensive and has a lower temperature resistance than ABS.
- Impact on Application: PETG is suitable for applications requiring transparency and toughness, such as packaging and medical devices.
- Considerations for International Buyers: Buyers should check for compliance with food safety standards, especially when used for packaging. Familiarity with standards like FDA regulations can be beneficial.
What Makes Nylon a Unique Choice for 3D Printing?
Nylon is a versatile material known for its strength and flexibility.
- Key Properties: Nylon has a high melting point (around 240-260°C) and excellent wear resistance, making it suitable for functional parts.
- Pros & Cons: Its flexibility and durability are significant advantages, but Nylon can be challenging to print due to its tendency to absorb moisture, which can lead to warping.
- Impact on Application: Nylon is commonly used in applications that require high strength and flexibility, such as gears and mechanical parts.
- Considerations for International Buyers: Buyers should be aware of the need for moisture control during storage and printing. Compliance with standards like ISO 9001 can enhance product quality assurance.
Summary Table of Material Properties
Material | Typical Use Case for 3D Printer Custom | Key Advantage | Key Disadvantage/Limitation | Relative Cost (Low/Med/High) |
---|---|---|---|---|
PLA | Prototyping, decorative items | Easy to print, low warping | Brittle, low heat resistance | Low |
ABS | Automotive parts, consumer goods | Tough, impact-resistant | Warping, requires heated bed | Medium |
PETG | Packaging, medical devices | Clarity, chemical resistance | More expensive, lower heat resistance | Medium |
Nylon | Gears, mechanical parts | High strength, flexibility | Moisture absorption, printing difficulty | High |
This strategic material selection guide provides international B2B buyers with essential insights into common 3D printing materials, helping them make informed decisions based on their specific needs and compliance requirements.
In-depth Look: Manufacturing Processes and Quality Assurance for 3d printer custom
What Are the Key Stages in the Manufacturing Process of Custom 3D Printers?
When considering the manufacturing processes for custom 3D printers, B2B buyers must understand the distinct stages involved. These stages include material preparation, forming, assembly, and finishing.
-
Material Preparation
– This initial stage involves selecting and preparing the raw materials used in 3D printing, such as thermoplastics, metals, or ceramics. The choice of material is crucial as it impacts the durability and functionality of the final product.
– Techniques such as granulation or powder sizing may be employed to ensure that materials meet specific size and consistency requirements. For instance, in powder bed fusion methods, the particle size of the powder affects the print resolution and mechanical properties of the printed part. -
Forming
– The forming stage involves the actual 3D printing process, where the prepared materials are transformed into the desired shape. Techniques vary widely depending on the technology being used, including Fused Deposition Modeling (FDM), Stereolithography (SLA), and Selective Laser Sintering (SLS).
– Each technique has its strengths and weaknesses. For example, SLA provides high-resolution prints with smooth finishes but is often limited in material choices compared to FDM. -
Assembly
– After forming, parts may require assembly, especially for complex designs that are printed in multiple segments. This process can involve various methods such as adhesive bonding, mechanical fastening, or welding.
– For international buyers, understanding the assembly techniques used is crucial, as it can affect the final product’s performance and reliability. -
Finishing
– The finishing stage enhances the appearance and functionality of the printed parts. This could involve sanding, painting, or applying protective coatings.
– Finishing techniques can greatly affect the aesthetic appeal and durability of the product, making it important for buyers to inquire about the options available.
How is Quality Assurance Implemented in Custom 3D Printer Manufacturing?
Quality assurance (QA) is a critical aspect of the manufacturing process, ensuring that products meet specified standards and customer expectations. In the context of custom 3D printers, QA involves several international standards and checkpoints.
-
What Are the Relevant International Standards for 3D Printer Quality Assurance?
– ISO 9001: This widely recognized standard outlines the criteria for a quality management system. It emphasizes customer satisfaction and the continuous improvement of processes, making it essential for manufacturers aiming to build trust with international B2B buyers.
– CE Marking: For products sold in the European market, CE marking indicates compliance with health, safety, and environmental protection standards. Understanding these certifications is essential for buyers in Europe, as it affects market access.
– API Standards: For industries like aerospace and medical, adherence to API standards ensures that components meet rigorous safety and performance criteria. -
What Are the Key Quality Control Checkpoints in the Manufacturing Process?
– Incoming Quality Control (IQC): This initial checkpoint involves inspecting raw materials before they enter the production line. Ensuring that materials meet specified standards prevents defects in the final product.
– In-Process Quality Control (IPQC): During manufacturing, regular inspections are conducted to monitor the process and identify potential issues early. This proactive approach can save costs associated with rework and scrap.
– Final Quality Control (FQC): Once production is complete, final inspections and testing are conducted to verify that the finished product meets all specifications. This may include functional testing, dimensional checks, and surface quality assessments. -
What Testing Methods Are Commonly Used in the QA Process?
– Common testing methods include tensile testing, impact testing, and thermal analysis. These tests assess the mechanical properties of materials and components, ensuring they perform as intended in real-world applications.
– Non-destructive testing (NDT) techniques, such as ultrasonic or X-ray testing, may also be employed to detect internal flaws without damaging the components.
How Can B2B Buyers Verify Supplier Quality Control Processes?
For B2B buyers, particularly those from Africa, South America, the Middle East, and Europe, verifying the quality control processes of potential suppliers is crucial.
-
Conducting Supplier Audits
– Regular audits allow buyers to assess the supplier’s manufacturing processes, quality control measures, and compliance with international standards. This firsthand evaluation can provide insights into the supplier’s capabilities and commitment to quality. -
Requesting Quality Reports
– Buyers should ask for detailed quality reports, including results from IQC, IPQC, and FQC processes. These documents can provide transparency into the supplier’s quality assurance practices and help identify any recurring issues. -
Engaging Third-Party Inspectors
– Utilizing third-party inspection services can offer an unbiased assessment of the supplier’s quality control processes. These inspectors can verify compliance with standards and provide additional assurance regarding product quality.
What Are the Quality Control and Certification Nuances for International B2B Buyers?
International B2B buyers must navigate various quality control and certification nuances to ensure compliance and product reliability.
-
Understanding Regional Standards
– Different regions may have specific regulations that impact product compliance. For example, buyers in Europe may need to focus on CE marking, while those in the Middle East might prioritize compliance with local health and safety regulations. -
Cultural and Communication Considerations
– Effective communication with suppliers is essential to ensure that quality expectations are clearly understood. Cultural differences may influence how quality is perceived and addressed, making it important for buyers to establish clear lines of communication. -
Building Long-Term Relationships
– Establishing long-term relationships with suppliers can lead to improved quality assurance practices over time. By fostering collaboration and open dialogue, buyers can work with suppliers to enhance product quality and reliability.
By understanding the intricacies of manufacturing processes and quality assurance, B2B buyers can make informed decisions when sourcing custom 3D printers, ultimately leading to better business outcomes.
Practical Sourcing Guide: A Step-by-Step Checklist for ‘3d printer custom’
The following practical sourcing guide is designed for international B2B buyers interested in procuring custom 3D printers. This checklist will help you navigate the complexities of sourcing, ensuring you make informed decisions that align with your business needs.
Step 1: Define Your Technical Specifications
Clearly articulate your requirements. Understanding the specific features and capabilities you need from a custom 3D printer is essential for successful procurement. Consider factors such as build volume, material compatibility, and printing speed. This will not only streamline your search but also help suppliers provide relevant solutions tailored to your needs.
Step 2: Research Market Trends and Technologies
Stay informed about the latest advancements. The 3D printing industry is rapidly evolving, with new technologies and materials emerging frequently. Researching current trends helps you identify which innovations may benefit your operations and gives you leverage when negotiating with suppliers. Look for insights in industry reports, webinars, and trade publications.
Step 3: Evaluate Potential Suppliers
Conduct thorough due diligence. Vetting suppliers is a critical step to ensure reliability and quality. Request detailed company profiles, case studies, and references from existing clients in your sector. Assess their experience with similar projects and their ability to meet your technical specifications.
- Check certifications: Ensure suppliers comply with industry standards and regulations relevant to your market.
- Review their portfolio: A robust portfolio can indicate a supplier’s capability and reliability.
Step 4: Request Proposals and Quotes
Solicit detailed proposals from shortlisted suppliers. When requesting quotes, provide your technical specifications to ensure you receive comparable proposals. Analyze the pricing structure, payment terms, and delivery timelines. This step is vital for understanding the cost implications and potential return on investment.
Step 5: Assess After-Sales Support and Warranty
Consider the long-term relationship with the supplier. After-sales support can significantly affect your operational efficiency. Inquire about the warranty period, support services, and availability of spare parts. A supplier that offers comprehensive support can save you time and money in the long run.
Step 6: Negotiate Terms and Conditions
Engage in discussions to finalize the deal. Once you have selected a supplier, negotiate terms that suit both parties. Focus on price, payment schedules, delivery timelines, and service levels. Ensure all agreements are documented to prevent misunderstandings later.
Step 7: Confirm Compliance with Local Regulations
Ensure adherence to legal requirements. Depending on your location, various regulations may apply to the import and use of 3D printers. Verify that your chosen supplier complies with these regulations to avoid legal complications and ensure smooth operations in your region.
By following this checklist, you can enhance your sourcing strategy for custom 3D printers, ensuring that you select a supplier who meets your business requirements and helps you stay competitive in your industry.
Comprehensive Cost and Pricing Analysis for 3d printer custom Sourcing
What Are the Key Cost Components in 3D Printer Custom Sourcing?
When sourcing custom 3D printers, understanding the cost structure is essential for effective budgeting and negotiation. The primary cost components include:
-
Materials: The choice of filament or resin significantly impacts cost. High-quality materials may come at a premium but can enhance the final product’s durability and performance. Common materials used in 3D printing include PLA, ABS, and specialty materials like nylon or metal-infused filaments.
-
Labor: Labor costs can vary based on geographic location and the complexity of the design. Skilled labor for setup, operation, and maintenance may be more expensive, particularly in regions with high wage standards.
-
Manufacturing Overhead: This includes indirect costs such as utilities, equipment maintenance, and facility costs. Companies may allocate a percentage of these costs to each project, affecting the overall pricing.
-
Tooling: Custom tooling may be required for specific designs, adding to initial costs. This is particularly relevant for large orders where molds or specialized equipment are necessary.
-
Quality Control (QC): Ensuring that the produced parts meet specified standards requires investment in quality control measures, which can include inspections and testing. This is crucial for industries where precision is paramount.
-
Logistics: Shipping and handling costs can vary widely based on distance, mode of transport, and the size of the shipment. Import duties and taxes must also be considered, especially for international transactions.
-
Margin: Suppliers will include a profit margin, which can vary based on competition, market demand, and the supplier’s operational efficiency.
How Do Price Influencers Affect Custom 3D Printer Costs?
Several factors can influence the pricing of custom 3D printers:
-
Volume and Minimum Order Quantity (MOQ): Higher order volumes often lead to lower unit prices due to economies of scale. Negotiating MOQs can be beneficial for smaller businesses looking to minimize upfront costs.
-
Specifications and Customization: More complex designs and custom specifications typically increase costs. Buyers should clearly outline requirements to avoid unexpected expenses.
-
Material Quality and Certifications: Premium materials and certified products (like those meeting ISO standards) can add to the cost but may be necessary for compliance in certain industries.
-
Supplier Factors: The reputation and reliability of the supplier can affect pricing. Established suppliers may charge more due to their experience and quality assurance.
-
Incoterms: Understanding shipping terms (e.g., FOB, CIF) is vital for calculating total costs. These terms dictate responsibility for shipping costs, insurance, and risk, impacting the overall expenditure.
What Are Effective Buyer Tips for Negotiating 3D Printer Costs?
International B2B buyers, especially from Africa, South America, the Middle East, and Europe, should consider the following strategies:
-
Negotiate Terms: Always negotiate payment terms and conditions. Consider discussing longer payment periods or discounts for upfront payments to improve cash flow.
-
Focus on Cost-Efficiency: Evaluate the total cost of ownership (TCO) rather than just the purchase price. Consider long-term costs associated with maintenance, materials, and energy consumption.
-
Understand Pricing Nuances: Be aware of regional pricing differences and how factors like local demand and currency fluctuations can affect costs. Leverage this knowledge in negotiations.
-
Request Samples: Before committing to large orders, request samples to evaluate quality. This can prevent costly mistakes and ensure that the final product meets expectations.
-
Build Relationships: Developing long-term relationships with suppliers can lead to better pricing and terms over time. Regular communication and feedback can foster trust and collaboration.
Disclaimer on Pricing
It is important to note that pricing for custom 3D printers can fluctuate based on market conditions, material availability, and individual supplier pricing strategies. Therefore, always seek updated quotes and conduct thorough market research before making purchasing decisions.
Alternatives Analysis: Comparing 3d printer custom With Other Solutions
When considering the implementation of a 3D printer custom, it’s crucial for B2B buyers to evaluate other viable solutions that can achieve similar outcomes. This analysis aims to highlight alternatives, allowing businesses to make informed decisions based on their unique operational needs and constraints.
Comparison Table of 3D Printer Custom and Alternatives
Comparison Aspect | 3D Printer Custom | CNC Machining | Injection Molding |
---|---|---|---|
Performance | High precision and flexibility in design | Excellent precision for complex parts | High-volume production efficiency |
Cost | Moderate initial investment with variable material costs | High setup cost, economical for large runs | High upfront costs, cost-effective for mass production |
Ease of Implementation | Requires skilled personnel for operation | Requires specialized training and setup | Complex molds necessitate significant planning |
Maintenance | Regular calibration and upkeep needed | Low maintenance but requires skilled technicians | Maintenance on molds can be costly and time-consuming |
Best Use Case | Prototyping, custom parts, low-volume production | High precision parts in medium to large volumes | Mass production of identical parts |
What Are the Advantages and Disadvantages of CNC Machining?
CNC (Computer Numerical Control) machining is a subtractive manufacturing process that is ideal for producing highly precise components. One of its significant advantages is the ability to handle a variety of materials, including metals and plastics, with exceptional accuracy. However, the initial setup costs can be prohibitive for small businesses, and the process can be inefficient for low-volume production runs. CNC machining is best suited for medium to large-scale production where precision is paramount.
How Does Injection Molding Compare to 3D Printer Custom?
Injection molding is a manufacturing process that involves injecting molten material into a mold to create parts. This method is highly efficient for mass production, resulting in lower per-unit costs when producing large quantities. However, it requires significant upfront investment in mold creation, which can be a barrier for smaller businesses or those testing new products. Injection molding is ideal for high-volume production of identical components but lacks the flexibility of 3D printing, especially for custom or rapidly changing designs.
Conclusion: How to Choose the Right Solution for Your Needs?
Selecting the most suitable manufacturing solution depends on several factors, including production volume, desired precision, budget constraints, and the specific application of the parts being produced. For businesses focused on rapid prototyping and customization, 3D printer custom offers unmatched flexibility and precision. Conversely, for high-volume production with strict tolerances, CNC machining or injection molding may be more appropriate. B2B buyers should carefully assess their operational requirements and long-term production goals to determine the best fit for their needs.
Essential Technical Properties and Trade Terminology for 3d printer custom
What Are the Essential Technical Properties of Custom 3D Printers?
When considering the procurement of custom 3D printers, understanding key technical specifications is crucial for B2B buyers. Here are some essential properties to evaluate:
1. Material Grade: Why Is It Important?
Material grade refers to the quality and type of materials used in the 3D printing process. Different grades offer varying mechanical properties, such as strength, flexibility, and thermal resistance. For industries like aerospace and automotive, selecting the right material grade is vital to ensure the durability and performance of end products. Buyers should inquire about available materials and their respective grades to match their specific application needs.
2. Tolerance: How Does It Impact Production?
Tolerance defines the allowable deviation from a specified dimension in the printed part. In B2B applications, maintaining tight tolerances (usually expressed in millimeters or microns) is critical for parts that must fit precisely within assemblies. Poor tolerance can lead to assembly issues or product failures, making it essential for buyers to understand the tolerance capabilities of a printer before making a purchase.
3. Build Volume: What Are the Size Limitations?
Build volume indicates the maximum dimensions a 3D printer can accommodate during the printing process. For businesses requiring large-scale prototypes or components, knowing the build volume is essential to ensure that the printer can meet production needs. Buyers should consider both the height and width of the build area when evaluating options.
4. Print Speed: How Does It Affect Efficiency?
Print speed is a measure of how quickly a 3D printer can produce an object, often expressed in millimeters per second (mm/s). In competitive markets, faster print speeds can significantly reduce time-to-market. Buyers should assess their project timelines and production requirements to select a printer that aligns with their operational efficiency goals.
5. Layer Height: What Is Its Role in Quality?
Layer height determines the thickness of each layer deposited during the printing process. A smaller layer height can produce finer details and smoother surfaces, making it ideal for intricate designs. Conversely, a larger layer height can accelerate production but may compromise the finish quality. Understanding the implications of layer height helps buyers choose a printer that meets their quality standards.
What Are Common Trade Terms in the 3D Printing Industry?
Familiarity with industry jargon is essential for effective communication and negotiation. Here are several common terms that buyers should know:
1. OEM (Original Equipment Manufacturer): What Does It Mean?
OEM refers to a company that produces parts or equipment that may be marketed by another manufacturer. In the context of 3D printing, OEMs might offer custom printers tailored to specific industry needs. Understanding the OEM landscape can help buyers find reliable suppliers for their projects.
2. MOQ (Minimum Order Quantity): Why Is It Relevant?
MOQ indicates the smallest quantity of products that a supplier is willing to sell. This term is crucial for B2B buyers who need to assess whether they can meet the minimum requirements set by manufacturers, which can affect pricing and inventory management.
3. RFQ (Request for Quotation): How to Use It Effectively?
An RFQ is a document used by buyers to solicit price quotes from suppliers for specific products or services. For 3D printing, submitting an RFQ can help businesses receive tailored offers based on their project specifications, enabling informed decision-making.
4. Incoterms: What Are Their Implications?
Incoterms (International Commercial Terms) define the responsibilities of buyers and sellers in international trade. Understanding these terms is vital for B2B buyers, as they clarify who is responsible for shipping, insurance, and tariffs, ultimately affecting overall project costs.
By grasping these technical properties and trade terms, international B2B buyers can make informed decisions when investing in custom 3D printing solutions, ensuring alignment with their operational needs and market demands.
Navigating Market Dynamics and Sourcing Trends in the 3d printer custom Sector
What Are the Current Market Dynamics and Key Trends in the 3D Printer Custom Sector?
The global market for custom 3D printing is experiencing significant growth, driven by advancements in technology and increasing demand across various industries. Key factors influencing this market include the rise of additive manufacturing, which allows for complex designs that traditional manufacturing methods cannot achieve. B2B buyers from Africa, South America, the Middle East, and Europe are particularly interested in how these technologies can enhance product customization and reduce lead times.
Emerging trends include the integration of artificial intelligence and machine learning in design processes, enabling better optimization of 3D models and materials. Additionally, the shift towards decentralized manufacturing is making it easier for international buyers to source products locally, minimizing shipping costs and lead times. Another notable trend is the rise of Industry 4.0, where smart factories leverage IoT devices to streamline production and enhance supply chain transparency.
Understanding these dynamics is crucial for B2B buyers who are looking to remain competitive. By staying informed about these trends, companies can better align their sourcing strategies to leverage the benefits of advanced 3D printing technologies.
How Can Sustainability and Ethical Sourcing Impact B2B in the 3D Printer Custom Sector?
Sustainability has become a pivotal consideration in the B2B landscape, particularly in the custom 3D printing sector. The environmental impact of traditional manufacturing processes has prompted buyers to seek more sustainable alternatives. This includes the use of biodegradable or recyclable materials in 3D printing, which not only reduces waste but also aligns with the growing consumer preference for eco-friendly products.
Moreover, the importance of ethical supply chains cannot be overstated. B2B buyers are increasingly scrutinizing their suppliers to ensure compliance with ethical standards, including fair labor practices and environmental responsibility. Certifications such as ISO 14001 for environmental management and various ‘green’ labels for materials are becoming essential in supplier evaluations.
By prioritizing sustainability and ethical sourcing, businesses can not only improve their brand image but also meet regulatory requirements and consumer expectations. This proactive approach can lead to long-term cost savings and foster stronger relationships with suppliers and customers alike.
What Is the Brief Evolution of the 3D Printer Custom Sector Relevant for B2B Buyers?
The evolution of the custom 3D printer sector has been marked by significant technological advancements since the 1980s, when the first 3D printing technologies were developed. Initially limited to prototyping, the applications of 3D printing have expanded dramatically, now encompassing industries such as aerospace, automotive, healthcare, and consumer goods.
The introduction of more affordable 3D printers and the development of diverse materials have enabled small and medium-sized enterprises (SMEs) to adopt these technologies. This democratization of 3D printing has resulted in a proliferation of custom products available to B2B buyers, allowing for increased innovation and customization options.
As the technology continues to mature, the focus is shifting towards greater integration with digital processes and sustainability, making it essential for B2B buyers to understand these trends to remain competitive in the evolving marketplace.
Frequently Asked Questions (FAQs) for B2B Buyers of 3d printer custom
-
How do I ensure the quality of custom 3D printers from international suppliers?
To ensure quality, start by researching suppliers thoroughly. Check for certifications like ISO or industry-specific standards. Request samples or prototypes to evaluate performance and quality. Additionally, consider visiting the supplier’s facility if possible, or use third-party inspection services to conduct quality checks before shipment. Establish clear quality assurance protocols in your contract, detailing acceptable quality levels and testing methods. -
What factors should I consider when selecting a custom 3D printer supplier?
When selecting a supplier, consider their experience, reputation, and customer reviews. Evaluate their technological capabilities and the range of materials they can work with. Communication is crucial; ensure they can understand your requirements and provide timely updates. Additionally, assess their compliance with international trade regulations and their ability to provide after-sales support and training. -
What are the typical minimum order quantities (MOQ) for custom 3D printers?
Minimum order quantities can vary significantly based on the supplier and the complexity of the customizations required. Typically, MOQs for 3D printers can range from one unit for very specialized or unique designs to several dozen for more standard models. Discuss your needs with potential suppliers to negotiate favorable terms, especially if you are testing the market or are a new buyer. -
What payment terms should I negotiate when purchasing custom 3D printers?
When negotiating payment terms, aim for a balance that protects both parties. Common terms include a deposit upfront (often 30-50%) with the balance due upon delivery or after inspection. Consider using escrow services for larger transactions to ensure security. Be clear about the currency used, any potential taxes, and the implications of international exchange rates. -
How can I manage logistics when importing custom 3D printers?
To manage logistics effectively, work closely with your supplier to understand shipping options and lead times. Choose a reliable freight forwarder familiar with international shipping regulations. Ensure that all customs paperwork is prepared in advance to avoid delays. Additionally, consider insurance for your shipment to protect against potential loss or damage during transit. -
What are the most common customization options available for 3D printers?
Customization options for 3D printers typically include modifications to size, material compatibility, and added features like dual extrusion or enhanced print speeds. Some suppliers also offer software customizations or tailored user interfaces. Discuss your specific requirements with the supplier to explore all available options and ensure the final product meets your operational needs. -
How do I assess the reliability of a 3D printer manufacturer?
To assess reliability, research the manufacturer’s track record by looking for client testimonials and case studies. Analyze their years in business and any industry awards or recognitions they have received. Engage in conversations with other businesses that have sourced from them to get firsthand accounts of their experiences. A reliable manufacturer should also offer warranties and robust customer support. -
What are the best practices for collaborating with suppliers on custom 3D printer designs?
Effective collaboration begins with clear communication of your design requirements and expectations. Utilize collaborative tools for sharing designs and feedback, and establish regular check-ins to monitor progress. Provide comprehensive specifications and be open to suggestions from the supplier based on their expertise. Document all agreements and changes to prevent misunderstandings, ensuring a smooth design and production process.
Important Disclaimer & Terms of Use
⚠️ Important Disclaimer
The information provided in this guide, including content regarding manufacturers, technical specifications, and market analysis, is for informational and educational purposes only. It does not constitute professional procurement advice, financial advice, or legal advice.
While we have made every effort to ensure the accuracy and timeliness of the information, we are not responsible for any errors, omissions, or outdated information. Market conditions, company details, and technical standards are subject to change.
B2B buyers must conduct their own independent and thorough due diligence before making any purchasing decisions. This includes contacting suppliers directly, verifying certifications, requesting samples, and seeking professional consultation. The risk of relying on any information in this guide is borne solely by the reader.
Strategic Sourcing Conclusion and Outlook for 3d printer custom
In the evolving landscape of 3D printing, strategic sourcing emerges as a pivotal factor for international B2B buyers seeking customized solutions. By leveraging strategic sourcing, businesses can optimize their supply chains, reduce costs, and enhance product innovation. Key takeaways include the importance of assessing supplier capabilities, understanding regional market dynamics, and fostering relationships that align with long-term business goals.
What role does collaboration play in successful strategic sourcing? Collaborative partnerships not only yield better pricing and quality but also facilitate access to cutting-edge technologies and trends. Buyers from Africa, South America, the Middle East, and Europe should prioritize suppliers who demonstrate a commitment to sustainability and adaptability, ensuring that they remain competitive in a rapidly changing market.
Looking forward, the future of 3D printing customization holds immense potential. As technology advances, so too will the opportunities for businesses to integrate innovative solutions into their operations. Engage proactively with suppliers who are ready to navigate this transformation, and position your organization at the forefront of the 3D printing revolution. Embrace strategic sourcing as a pathway to unlock new possibilities and drive growth in your business.