Cut Costs with the Best Electrolysi Manufacturer Guide (2025)
Introduction: Navigating the Global Market for electrolysi manufacturer
In today’s rapidly evolving global market, sourcing the right electrolysi manufacturer can be a daunting challenge for international B2B buyers. With increasing demand for electrolyzers in various industries—ranging from renewable energy to water treatment—the stakes are higher than ever. Buyers from regions such as Africa, South America, the Middle East, and Europe face unique hurdles, including regional compliance standards, varying quality benchmarks, and fluctuating supply chain dynamics. This guide aims to demystify the complexities of the electrolysi manufacturing landscape, providing you with actionable insights to make informed purchasing decisions.
This comprehensive resource covers various aspects essential to understanding the electrolysi market, including different types of electrolyzers, their applications, and crucial supplier vetting processes. Additionally, it delves into cost considerations and potential return on investment, enabling buyers to evaluate options that align with their operational goals. By navigating through the intricacies of this guide, international B2B buyers will be empowered to identify reliable suppliers, negotiate better terms, and ultimately enhance their procurement strategies.
Whether you’re looking to invest in cutting-edge technology or seeking sustainable solutions, this guide is designed to equip you with the knowledge needed to thrive in the competitive landscape of electrolysi manufacturing.
Understanding electrolysi manufacturer Types and Variations
Type Name | Key Distinguishing Features | Primary B2B Applications | Brief Pros & Cons for Buyers |
---|---|---|---|
Alkaline Electrolyzers | Utilize alkaline solutions for electrolysis. | Hydrogen production, water treatment. | Pros: Cost-effective; Cons: Lower efficiency compared to PEM. |
Proton Exchange Membrane | Employ a solid polymer membrane for ion exchange. | Fuel cells, industrial hydrogen production. | Pros: High efficiency; Cons: Higher initial cost. |
Solid Oxide Electrolyzers | Operate at high temperatures for efficient reactions. | Energy storage, CO2 reduction. | Pros: High efficiency; Cons: Requires complex thermal management. |
Anion Exchange Membrane | Utilize anion exchange membranes for electrolysis. | Wastewater treatment, chemical synthesis. | Pros: Effective for specific applications; Cons: Limited material compatibility. |
Bipolar Plate Systems | Incorporate bipolar plates for multi-cell configurations. | Fuel cells, electrolytic cells in industries. | Pros: Compact design; Cons: Complexity in manufacturing. |
What are the Characteristics of Alkaline Electrolyzers?
Alkaline electrolyzers are among the most established technologies for electrolysis, utilizing alkaline solutions such as potassium hydroxide. They are primarily used in hydrogen production and water treatment applications. Their cost-effectiveness makes them an attractive option for businesses looking to minimize initial investments. However, buyers should consider that while they are reliable, alkaline electrolyzers tend to have lower efficiency compared to other technologies like PEM electrolyzers, which may affect long-term operational costs.
How Do Proton Exchange Membrane Electrolyzers Stand Out?
Proton Exchange Membrane (PEM) electrolyzers employ a solid polymer membrane that allows protons to pass through while being impermeable to gases. This technology is known for its high efficiency and fast response times, making it ideal for applications such as fuel cells and industrial hydrogen production. While the initial investment is higher than that of alkaline electrolyzers, the operational efficiency can lead to lower energy costs over time. Buyers should weigh the upfront costs against potential savings in energy efficiency.
What Makes Solid Oxide Electrolyzers Unique?
Solid Oxide Electrolyzers operate at elevated temperatures, enhancing the efficiency of the electrolysis process. They are particularly suited for energy storage solutions and carbon dioxide reduction applications. While they offer high efficiency, their requirement for complex thermal management systems can pose challenges in implementation. B2B buyers should consider the specific energy requirements and the potential for high-temperature applications when evaluating this technology.
What are the Applications of Anion Exchange Membrane Electrolyzers?
Anion Exchange Membrane (AEM) electrolyzers utilize specialized membranes that allow for anion transport. This technology is effective in wastewater treatment and chemical synthesis, where specific ion interactions are required. While they offer advantages in targeted applications, their material compatibility can be a limiting factor for some industries. Buyers should assess the compatibility of AEM technology with their specific chemical processes to ensure effective application.
Why Choose Bipolar Plate Systems for Electrolysis?
Bipolar Plate Systems are designed to accommodate multiple cells in a compact configuration, making them suitable for various industrial applications including fuel cells and electrolytic cells. Their compact design can lead to space savings in manufacturing facilities. However, the complexity of manufacturing these systems can result in higher production costs. Buyers should evaluate the balance between space efficiency and cost when considering this type of electrolyzer for their operations.
Related Video: Heat Pump Thermostat O, B, and C Terminal Variations Explained
Key Industrial Applications of electrolysi manufacturer
Industry/Sector | Specific Application of Electrolysis Manufacturer | Value/Benefit for the Business | Key Sourcing Considerations for this Application |
---|---|---|---|
Water Treatment | Production of chlorine and caustic soda for water purification | Enhances water quality and safety for consumption and industrial use | Quality of electrolytic cells, energy efficiency, compliance with local regulations |
Metal Production | Electrolytic refining of metals like copper and aluminum | Increases metal purity and reduces waste, optimizing production costs | Material sourcing, technology compatibility, delivery timelines |
Renewable Energy | Hydrogen production through water electrolysis | Supports clean energy initiatives and reduces carbon footprint | Electrolyzer efficiency, scalability, and operational costs |
Chemical Manufacturing | Synthesis of various chemicals through electrochemical processes | Streamlines production processes and enhances product quality | Raw material availability, technology support, and regulatory compliance |
Semiconductor Industry | Electroplating for component fabrication | Improves conductivity and durability of electronic components | Precision requirements, supplier reliability, and lead times |
How Is Electrolysis Used in Water Treatment, and What Are the Benefits?
In the water treatment industry, electrolytic processes are essential for producing chlorine and caustic soda, which are key in disinfecting and purifying water. By using electrolysis, companies can ensure a consistent supply of these chemicals, thus improving the safety and quality of water for both consumption and industrial applications. International buyers, especially from regions like Africa and the Middle East, should consider sourcing electrolytic cells that meet local regulatory standards and offer high energy efficiency to reduce operational costs.
What Role Does Electrolysis Play in Metal Production?
Electrolysis is critical in the metal production sector for refining metals such as copper and aluminum. This process enhances the purity of metals, which is vital for industries requiring high-quality materials, such as electronics and construction. B2B buyers should focus on the quality of the electrolytic refining technology and the compatibility of the equipment with existing production lines to optimize costs and minimize waste.
How Is Electrolysis Contributing to Renewable Energy Solutions?
In the renewable energy sector, electrolysis is a promising technology for producing hydrogen from water. This process plays a crucial role in supporting clean energy initiatives, helping businesses reduce their carbon footprint and transition to sustainable energy sources. Buyers from Europe and South America should prioritize sourcing highly efficient electrolyzers that can scale with their energy needs, while also considering operational costs and maintenance requirements.
What Are the Applications of Electrolysis in Chemical Manufacturing?
Electrolysis is widely used in chemical manufacturing for the synthesis of various chemicals, streamlining production processes and enhancing product quality. This method allows for more precise control over chemical reactions, resulting in fewer by-products and higher yields. B2B buyers should evaluate the availability of raw materials and the technology’s compliance with industry regulations to ensure a reliable supply chain.
How Does Electrolysis Improve Semiconductor Manufacturing?
In the semiconductor industry, electrolysis is used for electroplating components, which significantly enhances their conductivity and durability. This is crucial for the production of reliable electronic devices. International buyers should focus on the precision requirements of the electroplating process and the reliability of suppliers to ensure timely delivery of high-quality components.
Related Video: Electromagnets – Everyday Uses
3 Common User Pain Points for ‘electrolysi manufacturer’ & Their Solutions
Scenario 1: Difficulty in Identifying Quality Electrolysi Manufacturers
The Problem:
Many B2B buyers, especially from emerging markets in Africa and South America, face challenges in identifying reputable electrolysi manufacturers. The lack of reliable information and the prevalence of unverified suppliers can lead to significant risks, including poor product quality, delays in delivery, and financial losses. Buyers may find themselves overwhelmed with choices, often leading to decision paralysis or, worse, selecting a manufacturer that does not meet their needs.
The Solution:
To effectively source quality electrolysi manufacturers, B2B buyers should adopt a multi-faceted approach. First, leverage online platforms that specialize in industrial suppliers, such as Alibaba, ThomasNet, or global trade directories. Look for manufacturers with verified credentials, including certifications like ISO 9001, which indicate a commitment to quality management systems.
Next, consider reaching out to industry associations or trade organizations within your region or sector, as they often provide resources and lists of reputable manufacturers. Networking at industry conferences and trade shows can also yield valuable insights and personal recommendations from peers who have had direct experiences with manufacturers.
Finally, conducting thorough due diligence by requesting samples, checking references, and reviewing customer feedback can significantly mitigate risks. Establishing a clear set of criteria for evaluation—such as production capacity, technological capabilities, and adherence to safety standards—will further enhance the decision-making process.
Scenario 2: Navigating Complex Specifications and Compliance Issues
The Problem:
Electrolysi systems often require highly specific technical specifications and compliance with various international standards. B2B buyers may struggle to understand the intricate details of these requirements, which can lead to non-compliance, product recalls, or failures in application. This complexity is particularly pronounced for companies in the Middle East and Europe, where regulations are stringent and constantly evolving.
The Solution:
To navigate these complexities, B2B buyers should invest time in understanding the specific regulations and standards applicable to their market. Engage with local regulatory bodies or industry experts who can provide guidance on compliance requirements.
Working closely with manufacturers during the specification phase is critical. Clearly communicate your operational needs and seek their expertise in aligning product offerings with regulatory requirements. Manufacturers with a strong R&D department can often assist in customizing solutions that meet both your technical specifications and compliance standards.
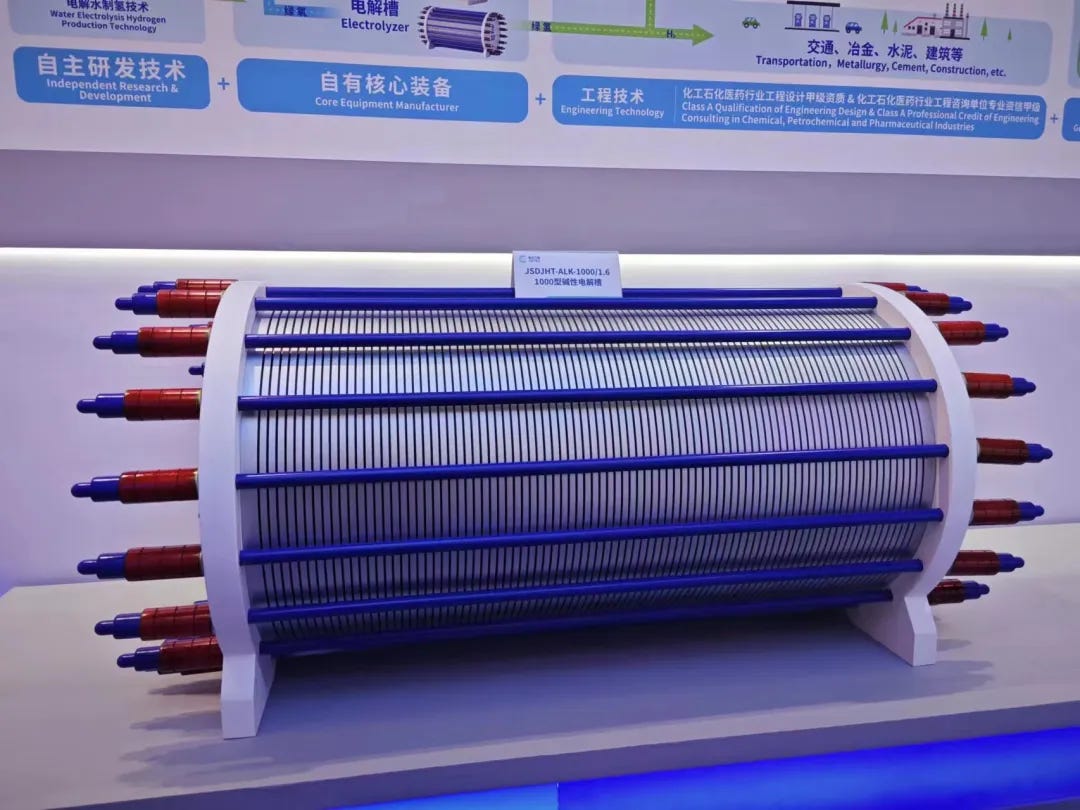
A stock image related to electrolysi manufacturer.
Additionally, consider collaborating with third-party consultants who specialize in regulatory compliance for electrolysi equipment. They can provide comprehensive assessments of your needs and help ensure that all aspects of your purchase are compliant, thereby reducing the risk of costly setbacks.
Scenario 3: High Operational Costs Due to Inefficiencies
The Problem:
A common pain point for B2B buyers in the electrolysi sector is the high operational costs stemming from inefficiencies in production processes. Buyers may find that the systems they purchase do not operate at optimal efficiency, leading to increased energy consumption and maintenance costs. This issue is particularly critical for businesses in Europe, where energy costs are rising and sustainability is becoming a priority.
The Solution:
To address operational inefficiencies, buyers should focus on investing in advanced electrolysi technologies that prioritize energy efficiency and automation. When evaluating manufacturers, look for those that emphasize energy-saving features in their systems, such as smart monitoring tools that optimize power consumption in real-time.
Conducting an energy audit of existing operations can also provide insights into inefficiencies and areas for improvement. Collaborate with manufacturers that offer training programs to ensure that your team understands how to operate the equipment effectively and maintain it properly.
Additionally, consider integrating predictive maintenance solutions offered by some manufacturers. These technologies utilize IoT sensors to monitor equipment performance, predicting failures before they occur and thereby reducing downtime and repair costs. By adopting these strategies, B2B buyers can significantly lower operational costs while enhancing the sustainability of their operations.
Strategic Material Selection Guide for electrolysi manufacturer
When selecting materials for electrolyzer manufacturing, international B2B buyers must consider various factors that affect performance, durability, and compliance with industry standards. Below, we analyze four common materials used in the production of electrolyzers, focusing on their properties, advantages, disadvantages, and implications for buyers in diverse regions such as Africa, South America, the Middle East, and Europe.
What are the Key Properties of Stainless Steel in Electrolyzer Manufacturing?
Stainless steel is a widely used material in electrolyzer manufacturing due to its excellent corrosion resistance and mechanical strength. It typically operates effectively under high temperatures and pressures, making it suitable for various electrolytic processes. The most common grades include 304 and 316, with 316 offering better resistance to chlorides, which is crucial in saline environments.
Pros and Cons:
– Pros: High durability, excellent corrosion resistance, and good mechanical properties.
– Cons: Higher cost compared to some alternatives and potential for pitting corrosion in aggressive environments.
Impact on Application:
Stainless steel is compatible with a wide range of electrolytic media, including alkaline and acidic solutions, making it versatile for different applications.
Considerations for International Buyers:
Buyers must ensure compliance with relevant standards such as ASTM A240 for stainless steel sheets and plates. Additionally, understanding local preferences for specific grades can aid in selection.
How Does Titanium Benefit Electrolyzer Performance?
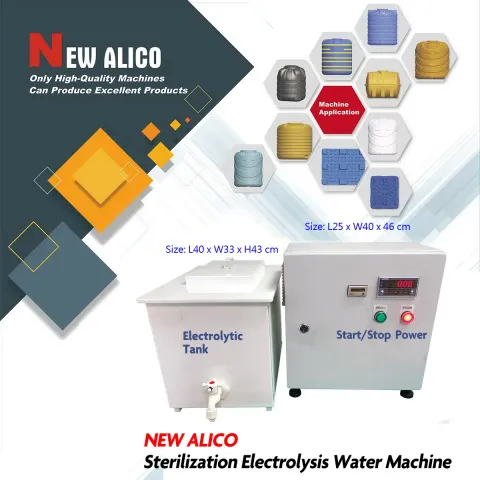
A stock image related to electrolysi manufacturer.
Titanium is another popular choice for electrolyzer components, particularly in environments that demand high corrosion resistance. It can withstand extreme conditions, including high temperatures and aggressive chemical environments.
Pros and Cons:
– Pros: Exceptional corrosion resistance, lightweight, and high strength-to-weight ratio.
– Cons: High manufacturing complexity and cost, which can affect overall project budgets.
Impact on Application:
Titanium is particularly effective in applications involving seawater or other saline solutions, where traditional metals may fail.
Considerations for International Buyers:
Buyers should be aware of the need for specialized welding techniques and the importance of adhering to standards like ASTM B265 for titanium plates.
What Role Does Graphite Play in Electrolyzer Design?
Graphite is often utilized in electrolyzer electrodes due to its excellent electrical conductivity and chemical stability. It can operate effectively at high temperatures and is resistant to many corrosive environments.
Pros and Cons:
– Pros: High electrical conductivity, good thermal stability, and cost-effectiveness.
– Cons: Brittle nature can lead to mechanical failure under stress and limited compatibility with certain electrolytic media.
Impact on Application:
Graphite is particularly well-suited for alkaline electrolyzers, where it can enhance efficiency and performance.
Considerations for International Buyers:
Understanding the specific grade of graphite suitable for the intended application is crucial, as well as compliance with standards such as ASTM D572 for carbon materials.
Why is Polymer Membrane Important in Electrolyzer Systems?
Polymer membranes, such as Nafion, are critical in proton exchange membrane (PEM) electrolyzers. These materials are designed to allow protons to pass while blocking gases, thus enhancing efficiency.
Pros and Cons:
– Pros: High ionic conductivity, lightweight, and flexible.
– Cons: Limited thermal stability and can be expensive compared to traditional materials.
Impact on Application:
Polymer membranes are essential for high-efficiency PEM electrolyzers, particularly in applications requiring rapid response times.
Considerations for International Buyers:
Buyers should evaluate the performance specifications of polymer membranes and ensure compliance with industry standards like ASTM D257 for electrical insulation properties.
Summary Table of Material Selection for Electrolyzer Manufacturing
Material | Typical Use Case for electrolysi manufacturer | Key Advantage | Key Disadvantage/Limitation | Relative Cost (Low/Med/High) |
---|---|---|---|---|
Stainless Steel | Structural components in electrolyzers | High durability and corrosion resistance | Higher cost and pitting corrosion risk | Medium |
Titanium | Electrodes in aggressive environments | Exceptional corrosion resistance | High manufacturing complexity | High |
Graphite | Electrodes in alkaline electrolyzers | High electrical conductivity | Brittle nature | Low |
Polymer Membrane | Core component in PEM electrolyzers | High ionic conductivity | Limited thermal stability | High |
This strategic material selection guide provides insights into the critical factors influencing material choice for electrolyzer manufacturing. By understanding these elements, international B2B buyers can make informed decisions that align with their operational needs and regulatory requirements.
In-depth Look: Manufacturing Processes and Quality Assurance for electrolysi manufacturer
What Are the Main Stages of Manufacturing for Electrolysis Equipment?
Manufacturing electrolyzers involves a series of meticulous processes to ensure high-quality production. The main stages include:
-
Material Preparation: This initial stage involves sourcing high-purity raw materials, such as electrodes and membranes. Suppliers should ensure that the materials meet specific industry standards. For instance, materials must be resistant to corrosion and capable of withstanding high operational temperatures. B2B buyers should inquire about the material specifications and certifications to confirm quality.
-
Forming: In this stage, the prepared materials are shaped into components necessary for the electrolyzer. Techniques like extrusion, casting, or machining are commonly employed. The choice of technique depends on the specific design and operational requirements of the electrolyzer. It is crucial for buyers to understand the forming methods used by suppliers, as these will affect the durability and efficiency of the final product.
-
Assembly: Once the components are formed, they are assembled into the final electrolyzer unit. This involves integrating various parts, such as the anode, cathode, and membranes, under controlled conditions to prevent contamination. Precision in assembly is vital, as any misalignment can lead to inefficiencies or failure during operation. Buyers should ask for documentation on assembly practices to ensure that suppliers adhere to stringent protocols.
-
Finishing: The final stage encompasses surface treatments and coatings to enhance the electrolyzer’s performance and longevity. Techniques like anodizing or applying protective coatings are common. Finishing processes not only improve the aesthetics but also protect against environmental factors. B2B buyers should verify the finishing processes utilized by the manufacturer to ensure they meet industry standards for durability.
How Is Quality Assurance Implemented in Electrolyzer Manufacturing?
Quality assurance (QA) is a critical component of manufacturing electrolyzers, ensuring that products meet international standards and customer expectations. Key aspects of QA include:
-
International Standards Compliance: Manufacturers often adhere to ISO 9001, which outlines quality management systems and processes. Compliance with this standard indicates that the manufacturer has established a systematic approach to quality control. Additionally, industry-specific certifications like CE (Conformité Européenne) and API (American Petroleum Institute) further validate the product’s reliability and safety. Buyers from regions like Africa and South America should prioritize suppliers with these certifications.
-
Quality Control Checkpoints: Effective quality control (QC) involves multiple checkpoints throughout the manufacturing process:
– Incoming Quality Control (IQC): This initial checkpoint verifies the quality of incoming materials before they enter production. Buyers should inquire about the criteria used for incoming inspections.
– In-Process Quality Control (IPQC): During manufacturing, IPQC ensures that processes are operating within specified parameters. This involves real-time monitoring and adjustments as needed.
– Final Quality Control (FQC): The final inspection checks the assembled units against predefined specifications. This step is crucial to ensure that the product performs as intended. -
Common Testing Methods: Manufacturers employ various testing methods to assess the quality of electrolyzers, including:
– Electrical Testing: Measuring voltage and current to ensure operational efficiency.
– Pressure Testing: Assessing the integrity of seals and joints to prevent leaks.
– Performance Testing: Evaluating the electrolyzer’s efficiency under operational conditions.
How Can B2B Buyers Verify Supplier Quality Control?
B2B buyers must conduct due diligence to verify the quality control practices of potential suppliers. Here are actionable steps:
-
Supplier Audits: Regular audits of suppliers can provide insight into their manufacturing processes and QC measures. Buyers should request audit reports or consider conducting their own assessments.
-
Quality Control Documentation: Suppliers should provide detailed documentation of their quality control processes, including test results and compliance certifications. This documentation should be readily available and transparent.
-
Third-Party Inspections: Engaging third-party inspection services can offer unbiased evaluations of the supplier’s QC processes. This is particularly beneficial for international buyers who may not be able to visit the manufacturing site.
-
References and Case Studies: Requesting references from previous clients or studying case studies can provide valuable insights into the supplier’s reliability and quality assurance practices. This is especially important for buyers in regions like Europe and the Middle East, where regulatory compliance is stringent.
What Are the Quality Control and Certification Nuances for International Buyers?
International B2B buyers must navigate various quality control and certification nuances when sourcing electrolyzers:
-
Cultural and Regulatory Differences: Different regions may have varying expectations regarding quality standards and certifications. Buyers from Africa and South America should familiarize themselves with local regulations and standards that may affect product acceptance.
-
Language Barriers: Language differences can pose challenges in understanding technical documentation and quality assurance practices. Buyers should seek suppliers who provide materials in a language they are comfortable with.
-
Supply Chain Transparency: Buyers should prioritize suppliers who are transparent about their supply chain and quality control processes. This transparency builds trust and ensures that the buyer is aware of potential risks and mitigations.
-
Post-Sale Support and Warranty: Understanding the supplier’s post-sale support and warranty policies is crucial for international buyers. This includes knowing how the supplier handles issues related to quality and performance after the sale.
By focusing on these manufacturing processes and quality assurance measures, B2B buyers can make informed decisions when selecting an electrolyzer manufacturer. Prioritizing suppliers who adhere to rigorous quality standards and transparent practices will enhance the reliability and efficiency of their operations.
Practical Sourcing Guide: A Step-by-Step Checklist for ‘electrolysi manufacturer’
In this practical sourcing guide, we provide a step-by-step checklist tailored for international B2B buyers looking to procure electrolysi manufacturing services. This guide aims to streamline the sourcing process, ensuring you make informed decisions while navigating the complexities of international procurement.
Step 1: Define Your Technical Specifications
Before initiating the sourcing process, it is essential to clearly outline your technical requirements. This includes the type of electrolysi technology you need, production capacity, and any specific material or design features. Having precise specifications helps you filter potential suppliers and ensures that the products meet your operational needs.
- Considerations:
- What are the unique challenges your application presents?
- Are there industry standards or regulations your supplier must comply with?
Step 2: Conduct Market Research for Suppliers
Next, you should conduct thorough market research to identify potential electrolysi manufacturers. Utilize industry reports, trade shows, and online platforms to gather a list of candidates. This initial research phase will provide insights into the capabilities and reputations of various suppliers.
- Research Sources:
- Trade associations and industry forums
- Online B2B marketplaces specific to your region, such as Alibaba or ThomasNet
Step 3: Evaluate Potential Suppliers
Before committing to any supplier, it’s crucial to vet them thoroughly. Request comprehensive company profiles, case studies, and references from previous clients in similar industries or regions. This helps you gauge their experience and reliability.
- Key Evaluation Criteria:
- Track record in delivering projects on time
- Quality control measures in place
Step 4: Verify Supplier Certifications
Ensure that your potential suppliers possess the necessary certifications and licenses. This step is vital as it reflects the manufacturer’s adherence to international quality standards and regulatory compliance.
- Common Certifications to Look For:
- ISO 9001 for quality management
- CE marking for compliance with EU regulations
Step 5: Request Samples and Prototypes
Once you’ve shortlisted suppliers, request samples or prototypes of their products. This allows you to evaluate the quality and performance of their offerings in real-world conditions, ensuring they align with your technical specifications.
- Sample Evaluation:
- Test for durability and efficiency
- Assess compatibility with your existing systems
Step 6: Negotiate Terms and Pricing
After verifying the quality of the products, the next step is to negotiate pricing and contract terms. This phase is crucial for establishing a mutually beneficial relationship. Be transparent about your budget and seek to understand the supplier’s pricing structure.
- Negotiation Tips:
- Inquire about bulk order discounts
- Discuss payment terms and lead times
Step 7: Establish a Clear Communication Channel
Finally, ensure that there is a clear line of communication established between your team and the supplier. This will facilitate smoother operations and allow for quick resolution of any issues that may arise during the procurement process.
- Communication Best Practices:
- Regular check-ins and updates
- Use project management tools for tracking progress
By following this checklist, international B2B buyers can systematically approach the sourcing of electrolysi manufacturers, ensuring that they select a partner who meets their technical and business needs.
Comprehensive Cost and Pricing Analysis for electrolysi manufacturer Sourcing
What Are the Key Cost Components in Electrolysis Manufacturing?
When sourcing from electrolysi manufacturers, understanding the comprehensive cost structure is crucial. The primary cost components include:
-
Materials: The cost of raw materials, such as metals and electrolytes, significantly impacts overall pricing. Prices can vary based on market fluctuations, availability, and quality standards.
-
Labor: Labor costs encompass wages for skilled workers involved in production, assembly, and maintenance. Regions with a high availability of skilled labor may offer competitive rates, while areas with labor shortages may see increased costs.
-
Manufacturing Overhead: This includes costs related to utilities, facility maintenance, and equipment depreciation. Efficient manufacturing processes can reduce overhead, thereby lowering overall production costs.
-
Tooling: Investment in specialized tools and machinery is a significant upfront cost. These costs can be amortized over time, making it essential to consider production volume when evaluating the impact on pricing.
-
Quality Control (QC): Ensuring product quality through rigorous testing and compliance with international standards can add to costs but is essential for maintaining market reputation and customer satisfaction.
-
Logistics: Transportation and handling of materials and finished products can be a substantial expense, particularly for international buyers. Choosing appropriate shipping methods and negotiating favorable freight terms can mitigate these costs.
-
Margin: Manufacturers typically include a profit margin in their pricing, which can vary based on their business model and market positioning.
How Do Price Influencers Affect Electrolysis Manufacturer Sourcing?
Several factors can influence pricing when sourcing from electrolysi manufacturers:
-
Volume and Minimum Order Quantity (MOQ): Higher order volumes often lead to better pricing. Manufacturers may offer discounts for larger orders, making it essential to evaluate your needs against MOQ requirements.
-
Specifications and Customization: Customized products often come at a premium. Clearly defining specifications can streamline production and potentially lower costs.
-
Materials and Quality Certifications: Sourcing high-quality materials that meet specific standards can drive up costs. Certifications such as ISO can also add to expenses but may enhance product credibility.
-
Supplier Factors: Supplier reputation, reliability, and production capacity can influence pricing. Established suppliers may charge more due to their track record, but their reliability can justify the cost.
-
Incoterms: Understanding Incoterms is crucial for determining who bears the costs and risks during shipping. Choosing the right Incoterm can significantly impact the total landed cost.
What Are the Best Negotiation Tips for B2B Buyers?
For international B2B buyers, particularly those from Africa, South America, the Middle East, and Europe, effective negotiation can lead to cost savings:
-
Conduct Market Research: Understanding the market landscape and competitor pricing can provide leverage during negotiations.
-
Clarify Your Needs: Clearly communicate your specifications and expectations to avoid misunderstandings that could lead to increased costs.
-
Explore Total Cost of Ownership (TCO): Evaluate not just the purchase price but also the long-term costs associated with maintenance, logistics, and potential downtime. This holistic view can guide better sourcing decisions.
-
Build Long-Term Relationships: Establishing a good relationship with suppliers can lead to better pricing and terms over time. Loyalty can often result in discounts and priority service.
-
Be Prepared for Cultural Differences: Understanding the cultural context of your supplier can improve communication and negotiation outcomes. Tailoring your approach based on local practices can foster goodwill and facilitate better deals.
Why Is It Important to Consider Pricing Nuances for International B2B Buyers?
Pricing for electrolysi manufacturing can vary significantly across regions due to economic factors, trade tariffs, and currency fluctuations. International buyers must remain vigilant about these nuances to avoid unexpected costs. Additionally, being aware of local regulations and compliance requirements can prevent costly delays and additional expenses.
Disclaimer on Indicative Prices
Please note that the prices discussed in this analysis are indicative and subject to change based on market conditions, supplier negotiations, and specific project requirements. It is advisable to obtain quotes directly from manufacturers for the most accurate and current pricing.
Alternatives Analysis: Comparing electrolysi manufacturer With Other Solutions
Understanding Alternatives to Electrolysis Manufacturing
When considering the procurement of electrolytic systems, international B2B buyers must evaluate various alternatives that may offer comparable benefits. In addition to traditional electrolysis manufacturers, several other technologies can achieve similar goals, such as hydrogen production or water treatment. This section provides a comparative analysis of electrolysis manufacturing against other viable solutions, enabling buyers to make informed decisions tailored to their operational needs.
Comparison Table of Electrolysis Manufacturer and Alternatives
Comparison Aspect | Electrolysis Manufacturer | Alternative 1: Steam Methane Reforming (SMR) | Alternative 2: Biomass Gasification |
---|---|---|---|
Performance | High efficiency in hydrogen production; suitable for large-scale applications | Moderate efficiency; well-established technology for hydrogen production | Variable efficiency; depends on feedstock quality |
Cost | Higher initial investment; lower operational costs in the long run | Lower initial costs; fluctuating operational costs due to natural gas prices | Moderate costs; dependent on biomass availability and processing |
Ease of Implementation | Requires specialized equipment and skilled personnel | Easier to implement; widely available technology | More complex setup; requires expertise in biomass processing |
Maintenance | Regular maintenance required; specialized service providers needed | Lower maintenance; proven technology with readily available parts | High maintenance; depends on the scale and complexity of the system |
Best Use Case | Ideal for large-scale hydrogen production and renewable energy applications | Best for industrial applications needing consistent hydrogen supply | Suitable for sustainable energy projects and waste management |
Detailed Breakdown of Alternatives
What is Steam Methane Reforming (SMR) and How Does It Compare?
Steam Methane Reforming (SMR) is a widely-used method for hydrogen production, primarily from natural gas. It offers a lower initial investment compared to electrolysis systems, making it an attractive option for many businesses. However, the operational costs can fluctuate due to the volatility of natural gas prices. While SMR is easier to implement and has a lower maintenance requirement, it is not as environmentally friendly as electrolysis, particularly when considering carbon emissions. Thus, while SMR may be suitable for immediate hydrogen needs, it may not align with long-term sustainability goals.
How Does Biomass Gasification Serve as an Alternative?
Biomass gasification converts organic materials into syngas, which can be further processed into hydrogen or other fuels. This method presents a sustainable approach to energy production, leveraging waste materials and reducing landfill dependency. The initial setup costs can be moderate, but the operational efficiency is highly dependent on the quality of the biomass feedstock. Additionally, biomass gasification systems can be complex and require specialized expertise, which can increase maintenance costs. This solution is ideal for organizations focused on sustainability and circular economy principles but may not be the best choice for those requiring consistent hydrogen production.
How to Choose the Right Solution for Your Needs
When selecting the appropriate technology for hydrogen production or similar applications, B2B buyers should consider several factors, including operational scale, cost constraints, and sustainability goals. Electrolysis manufacturers excel in efficiency and long-term operational savings, making them ideal for large-scale projects focused on renewable energy. However, alternatives like SMR and biomass gasification may offer viable options depending on immediate needs, budget, and environmental considerations. Ultimately, the right choice will depend on aligning the technology with the organization’s strategic objectives and operational capabilities.
Essential Technical Properties and Trade Terminology for electrolysi manufacturer
What Are the Essential Technical Properties for Electrolysis Manufacturers?
When engaging with electrolysi manufacturers, understanding critical technical properties is paramount for international B2B buyers. Here are some key specifications to consider:
1. Material Grade
The material grade of components used in electrolysis systems, such as electrodes and membranes, affects efficiency and durability. Common materials include titanium, nickel, and various alloys. Selecting the appropriate material ensures optimal performance, corrosion resistance, and longevity, which are crucial for reducing operational costs over time.
2. Tolerance Levels
Tolerance refers to the permissible limit of variation in physical dimensions or performance characteristics of the equipment. High precision is essential for components that interact closely, such as in cell stacks. Poor tolerance can lead to inefficiencies and increased wear, making it vital for buyers to specify their required tolerances clearly.
3. Current Density
Current density, measured in amperes per square meter (A/m²), indicates how much current is flowing through a given area of the electrode. It plays a critical role in determining the efficiency and output of the electrolysis process. Buyers should assess the manufacturer’s ability to meet specific current density requirements to optimize production rates.
4. Operating Temperature Range
The operating temperature range indicates the conditions under which the electrolysis equipment can function effectively. Equipment that operates at higher temperatures may enhance reaction rates but could also necessitate additional cooling systems. Understanding these limits helps buyers select suitable equipment for their environmental conditions.
5. Efficiency Ratings
Efficiency ratings refer to the effectiveness of an electrolysis system in converting electrical energy into chemical energy. High-efficiency systems can lead to lower energy costs and better overall performance. Buyers should inquire about the efficiency ratings of various models to make informed purchasing decisions.
6. Safety Certifications
Safety certifications ensure that the equipment meets international safety standards. These certifications are crucial for compliance with regulations in different regions, particularly for buyers from Africa, South America, the Middle East, and Europe. Understanding which certifications a manufacturer holds can mitigate risks associated with equipment operation.
What Are the Common Trade Terms Used in Electrolysis Manufacturing?
Familiarity with industry jargon is equally important for effective communication with manufacturers. Here are some essential terms:
1. OEM (Original Equipment Manufacturer)
An OEM is a company that produces components or equipment that may be marketed by another manufacturer. In the context of electrolysis, buyers may engage with OEMs to source specific parts tailored for their systems, ensuring compatibility and quality.
2. MOQ (Minimum Order Quantity)
MOQ refers to the smallest quantity of a product that a supplier is willing to sell. Understanding the MOQ is essential for buyers to avoid overcommitting financially while ensuring they meet their operational needs. Negotiating MOQs can lead to better pricing and inventory management.
3. RFQ (Request for Quotation)
An RFQ is a document sent to suppliers requesting pricing and terms for specific products or services. Buyers should prepare detailed RFQs that outline their technical specifications and requirements, enabling suppliers to provide accurate quotes and streamline the procurement process.
4. Incoterms
Incoterms (International Commercial Terms) define the responsibilities of buyers and sellers in international trade, covering aspects such as delivery, risk transfer, and shipping costs. Familiarity with Incoterms, such as FOB (Free On Board) or CIF (Cost Insurance and Freight), helps buyers negotiate better terms and understand their liabilities.
5. Lead Time
Lead time is the period between placing an order and receiving the product. Understanding lead times is critical for project planning and inventory management, especially for international buyers who may face longer shipping times.
6. Warranty Period
The warranty period indicates the duration for which a manufacturer guarantees the performance of their equipment. Knowing the warranty details can provide assurance regarding the reliability of the equipment and protect against unforeseen costs.
By grasping these technical properties and trade terms, international B2B buyers can navigate the complexities of purchasing from electrolysi manufacturers more effectively, ensuring they make informed decisions that align with their operational goals.
Navigating Market Dynamics and Sourcing Trends in the electrolysi manufacturer Sector
What Are the Key Market Dynamics and Trends Influencing Electrolysi Manufacturers?
The electrolysi manufacturer sector is experiencing significant transformation driven by various global factors. Key drivers include the increasing demand for clean energy solutions, the rise of electric vehicles (EVs), and the shift towards sustainable manufacturing processes. Countries in Africa and South America, rich in renewable resources, are becoming attractive markets for electrolytic solutions that facilitate the production of hydrogen and other clean fuels. In Europe and the Middle East, stringent regulations aimed at reducing carbon emissions are propelling investments in electrolytic technologies.
Emerging technologies such as advanced electrolyzers and digital monitoring systems are reshaping sourcing trends. B2B buyers are increasingly seeking suppliers that offer innovative solutions, including modular electrolyzers that can be easily scaled based on demand. The integration of IoT in electrolytic processes allows for real-time monitoring, enhancing operational efficiency and reducing downtime. Additionally, the trend towards local sourcing is gaining traction, as companies aim to mitigate supply chain disruptions caused by geopolitical tensions and the COVID-19 pandemic.
How Can Sustainability and Ethical Sourcing Impact Your Business in the Electrolysi Sector?
Sustainability is becoming a cornerstone for businesses within the electrolysi manufacturer sector. The environmental impact of electrolytic production processes is under scrutiny, prompting manufacturers to adopt greener practices. For international B2B buyers, understanding the importance of ethical supply chains is essential. This includes selecting suppliers that comply with environmental regulations and demonstrate a commitment to reducing their carbon footprint.
Buyers should look for suppliers who utilize green certifications and materials in their manufacturing processes. Certifications such as ISO 14001 (Environmental Management) and the use of recycled materials can serve as indicators of a supplier’s commitment to sustainability. By prioritizing ethical sourcing, companies can not only enhance their brand reputation but also attract environmentally conscious clients and comply with global sustainability initiatives. This strategic alignment can lead to long-term partnerships and increased market share in an evolving marketplace.
What Is the Historical Context of the Electrolysi Manufacturing Sector?
The electrolysi manufacturing sector has evolved significantly over the past few decades. Initially, electrolytic processes were primarily used in traditional industries such as metal refining and chemical production. However, with the advent of renewable energy technologies, particularly in the late 20th century, the focus shifted towards utilizing electrolysis for hydrogen production and energy storage solutions.
The 21st century has witnessed a surge in research and development, driven by the urgent need to transition to cleaner energy systems. Advances in materials science have led to the creation of more efficient electrolyzers, further propelling the industry forward. As global awareness of climate change grows, electrolysi manufacturers are now at the forefront of the energy transition, providing essential technologies that support the shift towards sustainable energy sources. This historical context is vital for B2B buyers who seek to understand the foundational changes shaping the current market landscape and influence future sourcing strategies.
Frequently Asked Questions (FAQs) for B2B Buyers of electrolysi manufacturer
-
1. How do I choose the right electrolysi manufacturer for my business needs?
Selecting the right electrolysi manufacturer involves assessing their industry experience, production capacity, and technological capabilities. It’s crucial to evaluate their certifications and compliance with international standards, as these often indicate product quality. Additionally, consider their customer service and support, especially for after-sales assistance. Request samples or prototypes to evaluate quality and functionality before making a commitment. Engaging with other clients or reading testimonials can also provide insights into their reliability and performance. -
2. What are the customization options available when sourcing from electrolysi manufacturers?
Many electrolysi manufacturers offer customization options to meet specific business requirements. These may include variations in size, materials, and design features tailored to your operational needs. It’s advisable to discuss your requirements upfront and inquire about the manufacturer’s flexibility in adapting their products. Additionally, ask about the lead time for custom orders, as this can affect your production schedule. Clear communication about your needs can lead to better outcomes in product specifications. -
3. What is the minimum order quantity (MOQ) for electrolysi products?
Minimum order quantities (MOQs) can vary significantly between manufacturers, often depending on the type of electrolysi product and the complexity of the order. Some manufacturers may have an MOQ as low as 10 units, while others might require hundreds. It’s essential to clarify the MOQ during initial discussions to ensure it aligns with your budget and inventory plans. Additionally, inquire if there are benefits for larger orders, such as discounts or improved lead times. -
4. How can I verify the reliability of an electrolysi manufacturer?
Verifying the reliability of an electrolysi manufacturer involves conducting thorough due diligence. Start by reviewing their business credentials, certifications, and production facilities, ideally through an on-site visit. Request references from previous clients and check online reviews or industry forums. Engaging third-party inspection services can also provide an unbiased assessment of their quality control processes. Ensuring they have a robust customer service framework can further enhance confidence in their reliability. -
5. What payment terms should I expect when dealing with electrolysi manufacturers?
Payment terms can vary widely among electrolysi manufacturers, influenced by factors such as order size and the manufacturer’s policies. Common terms include a deposit upfront (typically 30-50%) with the balance due upon delivery or before shipment. Some manufacturers may offer net terms, allowing payment within a specified period post-delivery. It’s crucial to discuss and negotiate payment terms early in the process to avoid misunderstandings and ensure they align with your cash flow management. -
6. How do I handle quality assurance when sourcing from electrolysi manufacturers?
Implementing a robust quality assurance process is essential when sourcing from electrolysi manufacturers. Establish clear quality standards and specifications before production begins. Request regular updates and samples during the manufacturing process to ensure compliance with your requirements. Consider third-party quality control inspections, especially for large orders, to mitigate risks. Additionally, review the manufacturer’s warranty and return policy to understand your options should any issues arise post-delivery. -
7. What logistics considerations should I keep in mind when importing electrolysi products?
Logistics play a crucial role in importing electrolysi products. Assess shipping options, including air freight versus sea freight, and understand associated costs and delivery timelines. Ensure that the manufacturer is well-versed in international shipping regulations and can provide necessary documentation, such as customs declarations and certificates of origin. Consider potential delays and plan for them in your supply chain. It might also be beneficial to work with a freight forwarder who can manage logistics and customs clearance on your behalf. -
8. How can I establish a long-term partnership with an electrolysi manufacturer?
Building a long-term partnership with an electrolysi manufacturer requires clear communication, mutual trust, and consistent quality expectations. Regularly engage with the manufacturer to provide feedback and discuss performance metrics. Establish joint goals for product development and innovation, which can foster collaboration. Additionally, consider negotiating favorable terms for future orders based on your relationship history. A commitment to transparency and responsiveness from both parties can create a strong, enduring partnership.
Important Disclaimer & Terms of Use
⚠️ Important Disclaimer
The information provided in this guide, including content regarding manufacturers, technical specifications, and market analysis, is for informational and educational purposes only. It does not constitute professional procurement advice, financial advice, or legal advice.
While we have made every effort to ensure the accuracy and timeliness of the information, we are not responsible for any errors, omissions, or outdated information. Market conditions, company details, and technical standards are subject to change.
B2B buyers must conduct their own independent and thorough due diligence before making any purchasing decisions. This includes contacting suppliers directly, verifying certifications, requesting samples, and seeking professional consultation. The risk of relying on any information in this guide is borne solely by the reader.
Strategic Sourcing Conclusion and Outlook for electrolysi manufacturer
What Are the Key Takeaways for B2B Buyers in Electrolysis Manufacturing?
In conclusion, strategic sourcing is crucial for international B2B buyers in the electrolysis manufacturing sector. By understanding market dynamics and leveraging supplier relationships, businesses can secure quality products while optimizing costs. Key takeaways include the importance of due diligence in supplier selection, the need for transparency in pricing structures, and the benefits of establishing long-term partnerships that foster innovation and reliability.
How Can B2B Buyers Navigate the Future of Electrolysis Manufacturing?
As the demand for sustainable energy solutions continues to rise, the outlook for electrolysis manufacturers remains robust. Buyers from Africa, South America, the Middle East, and Europe should focus on aligning their sourcing strategies with emerging technological advancements and sustainability goals. Engaging with suppliers who prioritize eco-friendly practices can not only enhance brand reputation but also drive competitive advantage.
What Should International Buyers Do Next?
Now is the time for international B2B buyers to take proactive steps towards refining their sourcing strategies in the electrolysis sector. Engage with manufacturers who demonstrate a commitment to innovation and sustainability, and explore opportunities for collaboration. By doing so, you position your business to thrive in an evolving market landscape, ensuring that you remain at the forefront of industry advancements.