Discover Cost-Saving Benefits of Corner Desk Custom Solutions (2025)
Introduction: Navigating the Global Market for corner desk custom
In today’s dynamic business landscape, sourcing custom corner desks that maximize workspace efficiency can be a daunting challenge for international B2B buyers. The need for tailored solutions that fit specific office layouts and aesthetic preferences is paramount, yet navigating the myriad options available can lead to confusion and suboptimal purchasing decisions. This guide aims to demystify the process of acquiring custom corner desks by exploring various types, applications, and considerations that influence your choices.
From understanding the unique needs of different industries to evaluating supplier credibility and cost factors, this comprehensive resource provides actionable insights to empower buyers from Africa, South America, the Middle East, and Europe, including markets such as Brazil and Australia. By addressing common pain points and offering strategic advice, this guide enables decision-makers to confidently select corner desks that not only enhance functionality but also contribute to a cohesive and productive office environment.
Whether you’re an office manager looking to revamp your workspace or a procurement officer tasked with outfitting a new facility, this guide will equip you with the knowledge and tools necessary to make informed purchasing decisions that align with your organizational goals.
Understanding corner desk custom Types and Variations
Type Name | Key Distinguishing Features | Primary B2B Applications | Brief Pros & Cons for Buyers |
---|---|---|---|
L-Shaped Corner Desk | Utilizes two surfaces to create an L-shape, maximizing corner space. | Small offices, home offices, collaborative spaces. | Pros: Efficient use of space; provides ample workspace. Cons: May require more room; limited aesthetic options. |
U-Shaped Corner Desk | Features three surfaces, providing extensive workspace and storage. | Executive offices, design studios, project management teams. | Pros: Maximum workspace; enhances productivity. Cons: Takes up significant space; higher cost. |
Modular Corner Desk | Composed of interchangeable components for customization. | Startups, co-working spaces, flexible work environments. | Pros: Highly customizable; adaptable to changing needs. Cons: Initial setup can be complex; may require additional investment in components. |
Standing Corner Desk | Adjustable height options promote ergonomic working conditions. | Tech companies, creative agencies, health-focused workplaces. | Pros: Supports health and wellness; encourages movement. Cons: Potentially less stability at full height; may require additional investment for quality. |
Corner Desk with Storage | Integrated shelves and drawers for organization. | Administrative offices, accounting firms, legal practices. | Pros: Maximizes storage; keeps workspace organized. Cons: Can be bulkier; may limit legroom. |
What are the Characteristics of L-Shaped Corner Desks?
L-shaped corner desks are designed to fit snugly into the corner of an office, utilizing two surfaces to create an efficient workspace. They are particularly suitable for small offices where maximizing space is crucial. When purchasing, consider the desk size to ensure it fits comfortably in the designated area. Additionally, examine the materials used for durability, especially in high-traffic environments.
How Do U-Shaped Corner Desks Enhance Workspace?
U-shaped corner desks offer an expansive workspace with three surfaces, making them ideal for executive offices and creative studios. Their design allows for easy access to documents and tools from multiple angles, fostering collaboration among team members. B2B buyers should assess the desk’s footprint, ensuring it aligns with the office layout. Furthermore, consider the desk’s storage capabilities, as these can significantly impact workflow efficiency.
Why Choose Modular Corner Desks for Flexibility?
Modular corner desks are composed of interchangeable components that can be tailored to specific needs. This type of desk is particularly advantageous for startups and co-working spaces, where adaptability is essential. When selecting a modular desk, evaluate the compatibility of components and the ease of reconfiguration. Additionally, assess the quality of materials to ensure longevity as the workspace evolves.
What Benefits Do Standing Corner Desks Provide?
Standing corner desks feature adjustable height options, promoting ergonomic working conditions that can enhance employee health and productivity. They are increasingly favored in tech companies and health-focused workplaces. When considering a standing desk, buyers should prioritize stability and the quality of the height adjustment mechanism. Moreover, assess the desk’s surface area to ensure it meets workspace requirements without compromising comfort.
How Does Storage Impact Corner Desk Functionality?
Corner desks with integrated storage solutions, such as shelves and drawers, provide an organized workspace that is essential for administrative roles. These desks help maintain a clutter-free environment, which is beneficial for productivity. B2B buyers should evaluate the storage capacity and layout to ensure it meets their organizational needs. Additionally, consider the desk’s design to maintain a professional aesthetic while providing functionality.
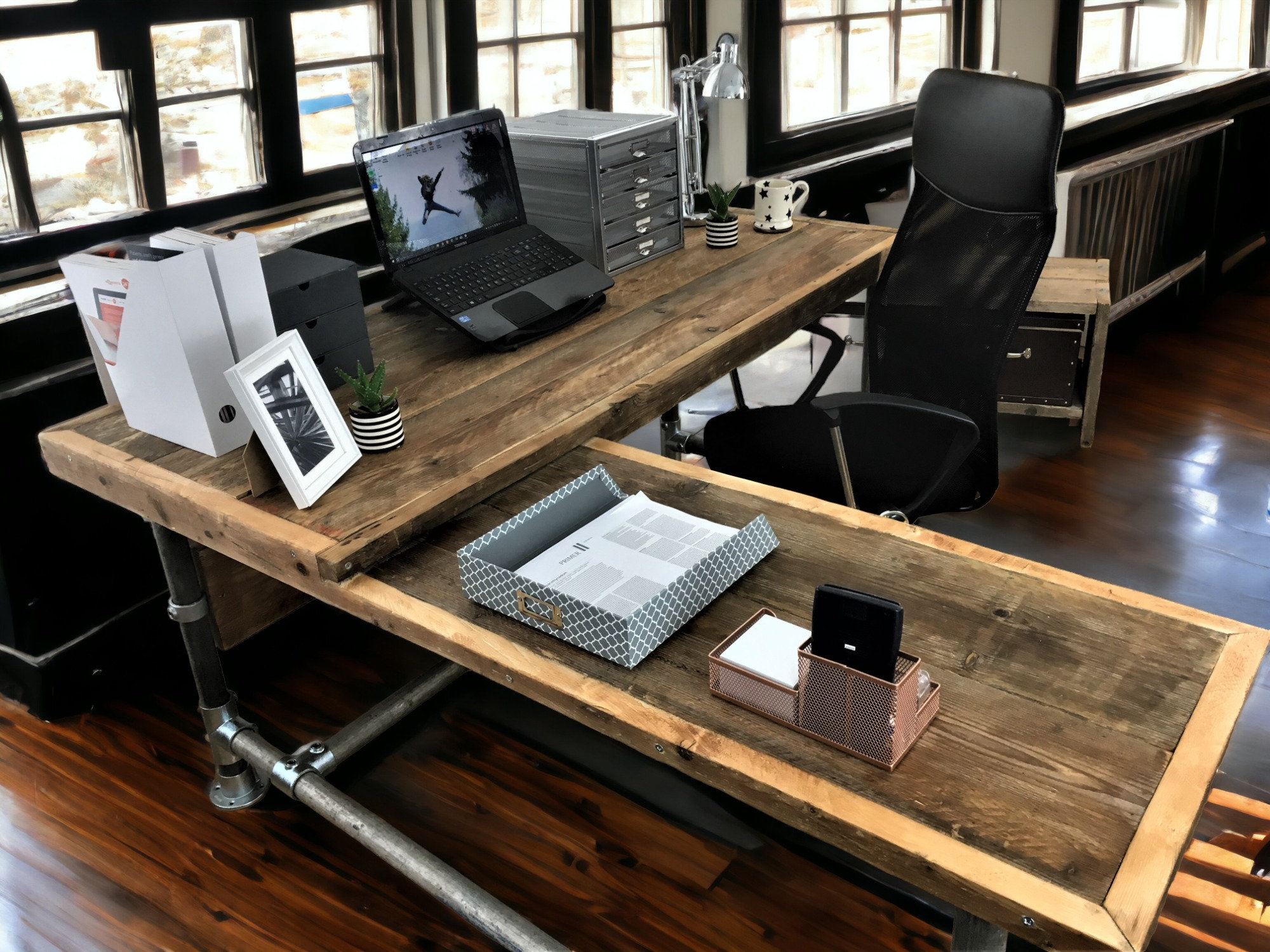
A stock image related to corner desk custom.
Related Video: How To Build a Giant Corner Desk – Woodworking
Key Industrial Applications of corner desk custom
Industry/Sector | Specific Application of corner desk custom | Value/Benefit for the Business | Key Sourcing Considerations for this Application |
---|---|---|---|
Corporate Offices | Ergonomic workstations for team collaboration | Enhances productivity and employee comfort | Material quality, customization options, delivery timelines |
Educational Institutions | Multi-functional study spaces for students | Promotes better learning environments and space utilization | Durability, design flexibility, compliance with safety standards |
Healthcare Facilities | Patient and staff interaction desks | Improves workflow efficiency and patient experience | Infection control materials, ergonomic design, ease of cleaning |
Creative Agencies | Customizable creative spaces for brainstorming sessions | Facilitates creativity and team engagement | Aesthetic appeal, modular designs, adaptability to space |
Retail and Showrooms | Interactive customer service desks | Enhances customer interaction and sales opportunities | Visual appeal, durability, integration with technology |
How are Corner Desks Customized for Corporate Offices?
In corporate offices, corner desks are tailored to create ergonomic workstations that foster collaboration among team members. These custom desks can incorporate features like adjustable height settings and integrated cable management systems, solving common issues related to workspace organization and employee comfort. International buyers from regions like Africa and Europe should consider the availability of sustainable materials and the ability to accommodate diverse office layouts when sourcing these desks.
What are the Benefits of Custom Corner Desks in Educational Institutions?
Educational institutions utilize custom corner desks to create multi-functional study spaces that cater to various learning styles. These desks can be designed to include storage solutions and collaborative spaces for group work, enhancing the overall learning environment. Buyers in South America and the Middle East should prioritize durability and compliance with educational safety standards to ensure long-term usability in high-traffic areas.
How Do Corner Desks Improve Efficiency in Healthcare Facilities?
In healthcare facilities, custom corner desks are essential for enhancing interaction between patients and staff. These desks can be designed to include features that support workflow efficiency, such as built-in storage for medical supplies and technology integration for electronic health records. Buyers in Europe and Africa must consider materials that support infection control and ergonomic designs that promote comfort for both staff and patients.
Why are Custom Corner Desks Important for Creative Agencies?
Creative agencies benefit from customizable corner desks that adapt to different brainstorming and project needs. These desks can be configured to facilitate group discussions and creative sessions, fostering an environment that encourages innovation. For international buyers, especially from regions like Brazil and Australia, it is crucial to focus on aesthetic appeal and modular designs that can be easily reconfigured as team dynamics change.
What Role Do Corner Desks Play in Retail and Showrooms?
In retail and showroom environments, custom corner desks serve as interactive customer service points, enhancing customer engagement and improving sales opportunities. These desks can be designed to integrate technology, such as point-of-sale systems, while maintaining visual appeal to attract customers. When sourcing for this application, businesses in the Middle East and South America should consider durability and the ability to seamlessly integrate with existing store layouts.
3 Common User Pain Points for ‘corner desk custom’ & Their Solutions
Scenario 1: Limited Space in Office Environments
The Problem: Many B2B buyers, especially in urban areas, are constrained by limited office space. Traditional desk setups often occupy unnecessary floor area, making it difficult to optimize available space. This is particularly challenging for companies that require collaborative work environments or need to accommodate remote employees who return to the office. The result is a cluttered workspace that hinders productivity and employee morale.
The Solution: Custom corner desks are an excellent solution for maximizing space efficiency. Buyers should consider working with manufacturers who specialize in tailored solutions. When sourcing a corner desk, opt for designs that integrate storage options like drawers or shelves, which can help in decluttering the workspace. Additionally, look for modular designs that allow for easy reconfiguration as your office needs evolve. Collaborate with your interior design team to ensure that the desk complements the overall office aesthetic while serving its functional purpose.
Scenario 2: Inconsistent Quality and Durability of Custom Desks
The Problem: One major concern for B2B buyers is the inconsistency in the quality and durability of custom corner desks. With many suppliers offering various materials and designs, it can be challenging to determine which options will stand the test of time. Buyers may end up investing in desks that do not meet their expectations, leading to frequent replacements and increased costs over time.
The Solution: To avoid quality issues, it is crucial to conduct thorough research before making a purchase. Buyers should prioritize suppliers with a solid reputation for quality craftsmanship and materials. Request samples or visit showrooms to assess the materials used in desk construction firsthand. Additionally, seek out manufacturers that offer warranties or guarantees on their products. This not only shows their confidence in their craftsmanship but also provides peace of mind for the buyer. Establishing a long-term relationship with a reliable supplier can also lead to better quality control and personalized service in the future.
Scenario 3: Navigating Customization Options and Features
The Problem: B2B buyers often find the customization process for corner desks overwhelming due to the myriad of options available. From material choices to ergonomic features, the decision-making process can become convoluted. This confusion can lead to choices that do not align with the company’s operational needs or employee preferences, ultimately resulting in dissatisfaction with the purchase.
The Solution: To streamline the customization process, buyers should create a detailed requirements document before approaching suppliers. This document should outline key features needed for the desks, such as size, material preferences, and ergonomic considerations. Involve employees in the decision-making process to gather insights on their needs and preferences. Furthermore, buyers should seek suppliers who offer virtual design consultations or interactive tools that allow them to visualize the desk in their space before finalizing the order. By clearly communicating needs and involving the end-users, companies can ensure that the final product not only meets their operational requirements but also enhances employee satisfaction and productivity.
Strategic Material Selection Guide for corner desk custom
When selecting materials for custom corner desks, international B2B buyers must consider various factors, including durability, cost, and suitability for specific applications. Here, we analyze four common materials: wood, metal, laminate, and glass. Each material has unique properties and implications for performance, manufacturing, and compliance with international standards.
What Are the Key Properties of Wood for Corner Desks?
Wood is a traditional choice for corner desks, known for its aesthetic appeal and structural integrity. Key properties include:
- Durability: Solid hardwoods like oak and maple offer high strength and resistance to wear.
- Temperature Sensitivity: Wood can expand or contract with temperature changes, which may affect joints and finishes.
- Environmental Impact: Sourced sustainably, wood can be an eco-friendly option.
Pros:
– Aesthetic versatility and warmth.
– Good structural performance.
– Can be refinished or repaired.
Cons:
– Higher cost for quality hardwoods.
– Vulnerable to moisture and pests.
– Requires regular maintenance.
How Does Metal Perform in Custom Corner Desk Applications?
Metal, particularly steel and aluminum, is increasingly popular for modern office furniture. Its properties include:
- Strength: High tensile strength makes metal desks durable and long-lasting.
- Corrosion Resistance: Stainless steel offers excellent resistance to rust and corrosion, while powder-coated finishes can enhance durability.
- Weight: Metal desks can be heavy, impacting shipping and installation.
Pros:
– High durability and low maintenance.
– Modern aesthetic appeal.
– Recyclable material.
Cons:
– Higher manufacturing complexity due to welding and finishing processes.
– Can be cold and uninviting compared to wood.
– Potential for scratches and dents.
Why Choose Laminate for Custom Corner Desks?
Laminate surfaces are engineered products made from layers of paper or plastic fused to a substrate. Their properties include:
- Cost-Effectiveness: Laminate is generally less expensive than solid wood or metal.
- Variety of Designs: Available in numerous colors and patterns, making it versatile for different office aesthetics.
- Moisture Resistance: Laminate surfaces are less susceptible to water damage compared to wood.
Pros:
– Affordable and easy to clean.
– Lightweight, making installation easier.
– Resistant to stains and scratches.
Cons:
– Less durable than solid wood or metal.
– Can chip or peel over time.
– Limited ability to repair surface damage.
What Are the Benefits and Limitations of Glass in Corner Desk Design?
Glass desks are often chosen for their sleek, modern look. Key properties include:
- Aesthetic Appeal: Glass offers a contemporary and elegant appearance.
- Weight: Glass can be heavy, necessitating sturdy support structures.
- Safety: Tempered glass is used to enhance safety and durability.
Pros:
– Provides a sense of openness and light.
– Easy to clean and maintain.
– Resistant to heat and moisture.
Cons:
– Vulnerable to scratches and fingerprints.
– Higher cost compared to laminate.
– Requires careful handling during transport and installation.
Considerations for International B2B Buyers
When selecting materials, buyers from Africa, South America, the Middle East, and Europe should consider local market preferences, compliance with international standards (such as ASTM, DIN, or JIS), and regional regulations regarding sustainability and environmental impact. Understanding these factors can significantly influence material selection and supplier relationships.
Summary Table of Material Selection for Corner Desks
Material | Typical Use Case for corner desk custom | Key Advantage | Key Disadvantage/Limitation | Relative Cost (Low/Med/High) |
---|---|---|---|---|
Wood | Executive offices and high-end environments | Aesthetic appeal and durability | Vulnerable to moisture and pests | High |
Metal | Modern offices and collaborative spaces | High durability and low maintenance | Higher manufacturing complexity | Medium |
Laminate | Budget-friendly workspaces | Cost-effective and variety of designs | Less durable than solid surfaces | Low |
Glass | Contemporary and minimalist designs | Sleek appearance and easy maintenance | Vulnerable to scratches and handling issues | Medium |
This analysis provides international B2B buyers with actionable insights into material selection for custom corner desks, helping them make informed decisions based on performance, cost, and suitability for their specific needs.
In-depth Look: Manufacturing Processes and Quality Assurance for corner desk custom
What are the Main Manufacturing Stages for Custom Corner Desks?
When it comes to producing custom corner desks, understanding the manufacturing process is crucial for international B2B buyers. The manufacturing process typically involves several key stages: material preparation, forming, assembly, and finishing. Each of these stages plays a vital role in ensuring that the final product meets quality and design specifications.
How is Material Prepared for Custom Corner Desks?
Material preparation is the first stage in the manufacturing process. This involves selecting the right materials, which may include various types of wood, metal, and laminate finishes. The choice of materials can significantly influence the desk’s durability, aesthetics, and cost.
-
Material Selection: Buyers should consider materials that are not only visually appealing but also durable and sustainable. For instance, solid wood offers longevity, while engineered wood can be more cost-effective.
-
Cutting and Sizing: Once materials are selected, they are cut to size using precision machinery. CNC (Computer Numerical Control) machines are commonly used to ensure high accuracy in dimensions, which is essential for custom designs.
What Techniques are Used in Forming Custom Corner Desks?
Forming is the next stage, where the prepared materials are shaped into the various components of the corner desk.
-
Joinery Techniques: Various joinery methods like dovetail, mortise and tenon, or dowel joints may be employed, depending on the design and structural requirements. Strong joinery not only enhances durability but also contributes to the desk’s aesthetic appeal.
-
Molding and Shaping: For desks with unique contours or designs, molding techniques are utilized. This can include bending wood or applying veneers for an elegant finish.
How is the Assembly of Custom Corner Desks Conducted?
The assembly stage is where the different components of the desk come together.
-
Assembly Line Setup: Depending on the volume of production, manufacturers may set up assembly lines to streamline the process. This can involve multiple stations where workers complete specific tasks, ensuring efficiency.
-
Quality Checks During Assembly: It is crucial to conduct quality checks at this stage to ensure that all components fit correctly and that the desk is structurally sound. Misalignment or defects can lead to significant issues later in the process.
What Finishing Techniques are Applied to Custom Corner Desks?
Finishing is the final stage of the manufacturing process and can greatly influence the product’s appearance and protection.
-
Surface Treatments: This includes sanding, staining, painting, or applying protective coatings. A high-quality finish not only enhances the desk’s appearance but also protects it from wear and tear.
-
Final Inspection: Before the desk is packaged, a thorough inspection is conducted to ensure that the finish meets the required standards and that there are no defects.
What International Quality Assurance Standards Should Buyers Know?
Quality assurance is a vital aspect of the manufacturing process for custom corner desks. International standards such as ISO 9001 ensure that manufacturers adhere to quality management principles.
-
ISO 9001 Certification: This certification indicates that a manufacturer has established a quality management system that is regularly audited. Buyers should inquire about this certification to ensure the manufacturer meets high-quality standards.
-
Industry-Specific Certifications: Depending on the market, additional certifications like CE (Conformité Européenne) for European markets or API (American Petroleum Institute) for specific industrial applications may be relevant. Understanding these certifications can help buyers gauge the quality and compliance of their suppliers.
What are the Key QC Checkpoints in the Manufacturing Process?
To ensure quality throughout the manufacturing process, several checkpoints are established.
-
Incoming Quality Control (IQC): This involves inspecting raw materials upon arrival to ensure they meet specifications before production begins.
-
In-Process Quality Control (IPQC): During the manufacturing stages, regular checks are performed to identify and address any issues early in the process.
-
Final Quality Control (FQC): This is the last line of defense before the product is shipped. FQC involves a comprehensive examination of the finished product to ensure it meets all quality standards.
How Can B2B Buyers Verify Supplier Quality Control?
B2B buyers must take proactive steps to verify the quality assurance processes of their suppliers. Here are some actionable methods:
-
Supplier Audits: Conducting regular audits of suppliers can provide insight into their quality control processes. This can include reviewing their certifications, quality management systems, and production processes.
-
Requesting Quality Reports: Buyers should ask for detailed quality reports that outline the results of inspections and tests conducted during the manufacturing process.
-
Third-Party Inspections: Engaging third-party inspection services can add an extra layer of assurance. These independent auditors can evaluate the manufacturing processes and ensure compliance with international standards.
What QC and Certification Nuances Should International Buyers Consider?
International B2B buyers, particularly from regions like Africa, South America, the Middle East, and Europe, should be aware of specific nuances in quality control and certification.
-
Regional Regulations: Different regions may have varying regulations regarding product safety and quality. Buyers should familiarize themselves with local standards to ensure compliance.
-
Cultural and Logistical Considerations: Understanding the cultural context and logistical challenges in international sourcing is essential. This includes recognizing potential language barriers and differing business practices.
-
Sustainability and Ethical Sourcing: Increasingly, buyers are focusing on sustainability and ethical sourcing. It is advisable to inquire about the environmental practices of suppliers and whether they align with global sustainability goals.
By paying close attention to the manufacturing processes and quality assurance measures, international B2B buyers can make informed decisions when sourcing custom corner desks. Ensuring that suppliers adhere to established quality standards and practices will ultimately lead to better products and stronger business relationships.
Practical Sourcing Guide: A Step-by-Step Checklist for ‘corner desk custom’
To successfully procure a custom corner desk, international B2B buyers must navigate a structured sourcing process. This guide provides a clear checklist designed to help you make informed decisions, ensuring that your investment meets both your functional needs and aesthetic expectations.
Step 1: Define Your Technical Specifications
Clearly outlining your technical specifications is the first crucial step in sourcing a custom corner desk. Consider dimensions, materials, and design features that align with your workspace needs. For example, if your office has limited space, you may need a desk that maximizes corner utilization while providing adequate storage options.
Step 2: Establish Your Budget
Setting a realistic budget is essential to avoid overspending. Understand the cost implications of various materials and customization options. Keep in mind that while cheaper options may save money upfront, investing in higher-quality materials can provide long-term durability and reduce replacement costs.
Step 3: Research Potential Suppliers
Conduct thorough research on suppliers who specialize in custom furniture. Look for companies with a strong reputation, positive reviews, and a portfolio showcasing their past work. It’s beneficial to check for suppliers who have experience serving clients in your region, as they may better understand local market trends and preferences.
Step 4: Request Samples and Prototypes
Before making a final decision, request samples or prototypes of the materials and finishes. This step is vital to assess the quality and craftsmanship of the products. Pay attention to the texture, color accuracy, and overall design to ensure it matches your expectations.
Step 5: Verify Supplier Certifications and Compliance
Ensure that potential suppliers adhere to industry standards and possess the necessary certifications. Compliance with safety regulations and environmental standards is crucial, especially when sourcing from different regions. For instance, ISO certifications can indicate a supplier’s commitment to quality management.
Step 6: Evaluate Supplier Capabilities
Assess the supplier’s capabilities to fulfill your order within your timeline. Inquire about their production capacity, lead times, and flexibility in accommodating changes. A supplier that can adapt to your needs and timelines can significantly enhance your procurement process.
Step 7: Establish Clear Communication Channels
Effective communication is key to a successful procurement process. Set clear expectations regarding design specifications, timelines, and delivery. Regular updates and feedback loops can help prevent misunderstandings and ensure that the final product aligns with your requirements.
By following these steps, international B2B buyers can streamline their sourcing process for custom corner desks, making informed decisions that align with their business objectives.
Comprehensive Cost and Pricing Analysis for corner desk custom Sourcing
What Are the Key Cost Components in Custom Corner Desk Sourcing?
When sourcing custom corner desks, international B2B buyers must understand the various cost components that contribute to the overall pricing. The primary cost components include:
-
Materials: The type and quality of materials significantly impact the cost. Solid wood, engineered wood, and metal finishes each come with different price points. Sustainable or certified materials may incur additional costs but can enhance marketability.
-
Labor: Labor costs can vary widely based on the region and the complexity of the design. Skilled craftsmanship, particularly in custom pieces, may demand higher wages, affecting the overall cost.
-
Manufacturing Overhead: This includes utilities, equipment maintenance, and facility costs. Efficient manufacturing processes can reduce overhead, thereby lowering prices.
-
Tooling: Custom designs often require specialized tooling, which can be a one-time investment that adds to the initial cost. Buyers should consider the amortization of these costs over larger order volumes.
-
Quality Control (QC): Implementing stringent QC measures ensures product reliability and durability but adds to labor and overhead costs. Buyers should weigh the importance of quality against cost savings.
-
Logistics: Shipping and transportation costs can vary based on distance, weight, and mode of transport. For international shipping, tariffs and customs duties may also apply.
-
Margin: Suppliers typically add a profit margin to cover their costs and risks. Understanding the margin expectations can aid in negotiations.
How Do Price Influencers Impact Custom Corner Desk Costs?
Several factors influence the pricing of custom corner desks, and understanding these can help buyers make informed decisions:
-
Volume and Minimum Order Quantity (MOQ): Larger orders often qualify for bulk pricing discounts. Buyers should negotiate MOQs that align with their purchasing capabilities to maximize savings.
-
Specifications and Customization: Highly customized designs may attract higher costs due to the additional labor and materials required. Clear specifications can help suppliers provide accurate quotes.
-
Material Quality and Certifications: Higher-quality materials and certifications (like FSC for wood) can increase costs. Buyers should assess whether the added expense aligns with their branding and customer expectations.
-
Supplier Factors: The supplier’s location, reputation, and production capabilities can affect pricing. Buyers should evaluate multiple suppliers to find the best balance of cost and quality.
-
Incoterms: Understanding Incoterms (International Commercial Terms) is crucial, as they define the responsibilities of buyers and sellers in shipping. Different terms can affect the total landed cost of the product.
What Are the Best Negotiation Strategies for B2B Buyers?
To optimize cost-efficiency when sourcing custom corner desks, buyers should consider the following tips:
-
Total Cost of Ownership (TCO): Rather than focusing solely on the initial price, consider the TCO, which includes maintenance, durability, and potential resale value. This perspective can justify higher upfront costs for better quality.
-
Leverage Relationships: Building long-term relationships with suppliers can lead to better pricing and terms. Regular communication and trust can facilitate more favorable negotiations.
-
Flexibility in Design: Offering flexibility in design can allow suppliers to suggest cost-saving alternatives without compromising on quality. This can lead to better pricing while still meeting buyer needs.
-
Request Multiple Quotes: Gathering quotes from various suppliers can provide a clearer picture of the market rate and leverage in negotiations. It’s also essential to ask for detailed breakdowns of costs to identify areas for negotiation.
-
Be Aware of Pricing Nuances: International buyers should be mindful of currency fluctuations, economic conditions, and regional market trends that may affect pricing. Understanding local market dynamics can enhance negotiation power.
Disclaimer on Indicative Prices
Please note that the prices discussed are indicative and can vary based on market conditions, supplier negotiations, and specific buyer requirements. It is advisable to conduct thorough research and obtain customized quotes from multiple suppliers before making purchasing decisions.
Alternatives Analysis: Comparing corner desk custom With Other Solutions
When considering office furniture solutions, particularly for creating efficient workspaces, it’s essential to analyze various alternatives to the ‘corner desk custom’. Each option offers unique benefits and challenges that could influence B2B purchasing decisions. Below, we explore how ‘corner desk custom’ compares with alternative solutions such as modular office furniture systems and standing desks.
Comparison Aspect | Corner Desk Custom | Modular Office Furniture Systems | Standing Desks |
---|---|---|---|
Performance | Highly functional; tailored for specific needs | Versatile; can adapt to various layouts | Encourages movement; can improve posture |
Cost | Higher initial investment due to customization | Moderate; costs vary based on components | Varies; typically moderate to high |
Ease of Implementation | Requires planning and design input | Generally easy; straightforward assembly | Simple to install, often requires minimal tools |
Maintenance | Low; durable materials reduce wear | Moderate; depends on quality of components | Low; minimal upkeep needed |
Best Use Case | Ideal for maximizing corner spaces in small offices | Suitable for dynamic work environments and collaborative spaces | Great for promoting health in sedentary jobs |
What Are the Advantages and Disadvantages of Modular Office Furniture Systems?

A stock image related to corner desk custom.
Modular office furniture systems are designed to be flexible and adaptable. They can be reconfigured to suit various needs, making them ideal for businesses that anticipate changes in team sizes or work processes. The primary advantages include versatility and ease of assembly, allowing businesses to create collaborative spaces quickly. However, they may not provide the same level of personalization as a corner desk custom, which can be a drawback for companies looking for specific designs or features tailored to their brand or operational needs.
Why Consider Standing Desks as an Alternative to Corner Desk Custom?
Standing desks have gained popularity due to their health benefits, such as reducing the risks associated with prolonged sitting. They promote movement and can be adjusted to accommodate different users, making them a good choice for shared workspaces. While they are often easy to install and require minimal maintenance, standing desks may not offer the same workspace optimization as a corner desk custom. They can also be less suitable for tasks requiring extensive paperwork or large monitors, which might lead to discomfort if not properly adjusted.
How Should B2B Buyers Choose the Right Solution for Their Needs?
In selecting the right office furniture solution, B2B buyers should consider their specific workspace requirements, budget constraints, and the nature of their business operations. A corner desk custom is ideal for maximizing corner spaces and creating a tailored work environment, especially in smaller offices. Conversely, modular systems offer flexibility and ease of reconfiguration for evolving work needs, while standing desks cater to health-conscious organizations aiming to enhance employee well-being. Ultimately, the choice should align with the company’s culture, workflow, and future growth plans. By evaluating these factors, buyers can make informed decisions that foster productivity and employee satisfaction.
Essential Technical Properties and Trade Terminology for corner desk custom
What Are the Essential Technical Properties for Custom Corner Desks?
When sourcing custom corner desks, international B2B buyers must consider several critical specifications. These specifications ensure that the furniture meets the specific needs of their workspace while maintaining quality and durability.
-
Material Grade
The material grade refers to the quality of the materials used in the desk’s construction. Common materials include solid wood, particle board, and metal. Higher-grade materials often provide better durability and aesthetics, making them suitable for long-term use in high-traffic environments. B2B buyers should ensure that the material grade aligns with their budget and the expected lifespan of the product. -
Dimensions and Tolerances
Accurate dimensions are crucial for fitting the desk within a specified space. Tolerances indicate the allowable variation in dimensions during manufacturing. For custom solutions, specifying precise dimensions and acceptable tolerances ensures that the desk will fit seamlessly into existing office layouts, avoiding costly modifications later. -
Load Capacity
Load capacity defines the maximum weight the desk can support without compromising structural integrity. This is particularly important for desks that will hold multiple monitors or heavy equipment. Buyers should assess their equipment needs and select a desk with an appropriate load capacity to avoid potential damages or safety issues. -
Finish Type
The finish type impacts both the appearance and maintenance of the desk. Options can include laminate, veneer, or paint. Each finish has different durability and aesthetic properties. Understanding the finish type helps buyers determine how the desk will blend with existing decor and how easily it can be cleaned or repaired. -
Assembly Requirements
Some custom corner desks may require assembly upon delivery, while others come pre-assembled. Knowing the assembly requirements can influence shipping costs and timelines. B2B buyers should consider their capacity for assembly and whether they need to factor in additional labor costs.
Which Trade Terms Are Important When Purchasing Custom Corner Desks?
Navigating the procurement of custom corner desks also involves understanding key industry terminology. Familiarity with these terms can streamline the purchasing process and clarify expectations between buyers and suppliers.
-
OEM (Original Equipment Manufacturer)
An OEM refers to a company that produces parts or equipment that may be marketed by another manufacturer. In the context of custom furniture, working with an OEM can ensure that buyers receive high-quality components that meet their specifications. -
MOQ (Minimum Order Quantity)
MOQ is the smallest number of units that a supplier is willing to sell. Understanding MOQ is crucial for B2B buyers, as it can impact inventory management and overall costs. Buyers should negotiate MOQs that align with their purchasing capabilities. -
RFQ (Request for Quotation)
An RFQ is a document sent to suppliers to request pricing and terms for specific products or services. Crafting a detailed RFQ can help buyers obtain accurate quotes and compare offers effectively, leading to better purchasing decisions. -
Incoterms (International Commercial Terms)
Incoterms are standardized trade terms that define the responsibilities of buyers and sellers in international transactions. Familiarity with these terms helps buyers understand shipping costs, risk management, and delivery responsibilities, ensuring that expectations are clear. -
Lead Time
Lead time refers to the period between placing an order and receiving the product. Understanding lead times helps buyers plan their procurement processes effectively, ensuring that they have the necessary furniture available when needed. -
Warranty
A warranty is a promise from the manufacturer regarding the quality and durability of the product. B2B buyers should inquire about warranty terms to safeguard their investment and ensure recourse in case of defects or damage.
By understanding both the technical properties and trade terminology associated with custom corner desks, international B2B buyers can make informed decisions that align with their operational needs and budget considerations.
Navigating Market Dynamics and Sourcing Trends in the corner desk custom Sector
What Are the Key Market Dynamics and Trends in the Custom Corner Desk Sector?
The custom corner desk market is experiencing significant growth driven by the rise in remote work and the emphasis on creating ergonomic workspaces. Businesses across Africa, South America, the Middle East, and Europe are increasingly investing in office furniture that optimizes space while enhancing productivity. The demand for personalization is shaping sourcing trends, with buyers seeking custom designs tailored to specific needs, such as size, functionality, and aesthetics. Emerging technologies like 3D printing and augmented reality (AR) are revolutionizing how products are designed and showcased, allowing B2B buyers to visualize and modify their selections in real-time.
Moreover, the integration of smart technology into office furniture is on the rise, as desks with built-in charging ports and connectivity options cater to the tech-savvy workforce. This trend is particularly relevant in markets like Brazil and Australia, where digital transformation in workplaces is accelerating. As international B2B buyers navigate these dynamics, they must also consider local market preferences and cultural nuances, which can significantly influence purchasing decisions.
How Is Sustainability Influencing Sourcing Decisions for Custom Corner Desks?
Sustainability has emerged as a critical factor in sourcing decisions for B2B buyers in the custom corner desk sector. With growing awareness of environmental issues, many companies are prioritizing eco-friendly materials and ethical supply chains. This shift is not only a response to consumer demand but also a regulatory push in various regions, including Europe and the Middle East, where sustainability regulations are tightening.
Buyers are increasingly looking for suppliers who offer ‘green’ certifications, such as Forest Stewardship Council (FSC) certification for wood products, which ensures that materials are sourced sustainably. Additionally, the use of recycled materials and low-VOC finishes is becoming more prevalent, appealing to environmentally-conscious businesses. By adopting sustainable practices, companies not only reduce their carbon footprint but also enhance their brand image, making them more attractive to clients and consumers who value corporate responsibility.
What Is the Evolution of the Custom Corner Desk Market?
The custom corner desk market has evolved significantly over the past few decades, shifting from traditional, mass-produced furniture to highly customizable options. In the early 2000s, the focus was primarily on functionality and affordability. However, as workplace design gained prominence, the demand for aesthetically pleasing and ergonomic furniture increased.
The introduction of online platforms in the late 2010s allowed buyers to easily access a wide range of designs, materials, and customization options. Today, the market is characterized by a fusion of technology and design, where B2B buyers can leverage digital tools for personalized solutions. This evolution reflects broader trends in workplace culture, emphasizing comfort, collaboration, and innovation in office environments.
International buyers must stay abreast of these changes to make informed sourcing decisions that align with their organizational goals and the expectations of their workforce.
Frequently Asked Questions (FAQs) for B2B Buyers of corner desk custom
-
How do I choose the right custom corner desk for my business needs?
Selecting the ideal custom corner desk involves assessing your specific requirements, including dimensions, materials, and design preferences. Consider the intended use—will it be for collaborative work or individual tasks? Evaluate the ergonomics and functionality, ensuring it accommodates your team’s workflow. Additionally, think about aesthetics; the desk should reflect your brand image while fitting seamlessly into your office decor. Lastly, request samples or prototypes from suppliers to verify quality before making a bulk purchase. -
What is the best material for a custom corner desk?
The best material for a custom corner desk depends on your business’s functional and aesthetic needs. Popular options include solid wood for durability and a classic look, laminate for easy maintenance and affordability, and metal for a modern industrial feel. Each material has its own benefits; for instance, wood offers warmth and longevity, while laminate can provide vibrant colors and patterns. When sourcing, consider the environmental impact of materials and opt for sustainable options when possible. -
What are the typical minimum order quantities (MOQs) for custom corner desks?
Minimum order quantities (MOQs) for custom corner desks can vary significantly between suppliers. Generally, MOQs can range from as low as 5 to as high as 100 units, depending on the complexity of customization and production capabilities. When negotiating with suppliers, inquire about flexibility in MOQs, especially if you are a smaller business or testing a new design. Some manufacturers may offer lower MOQs for first-time orders or specific promotional periods. -
How can I verify the reliability of a custom desk supplier?
To verify the reliability of a custom desk supplier, conduct thorough research. Start by checking reviews and testimonials from previous clients. Request references and follow up with past customers to gauge their satisfaction. Additionally, assess the supplier’s production capacity, certifications, and compliance with international quality standards. A visit to their manufacturing facility can also provide insight into their operational practices. Establishing open communication can further indicate their professionalism and willingness to address your concerns. -
What payment terms should I expect when sourcing custom corner desks internationally?
When sourcing custom corner desks internationally, payment terms can vary widely. Common practices include a deposit of 30-50% upfront, with the balance due upon shipment or delivery. Some suppliers may offer net payment terms, allowing payment within a specific period after receipt of goods. It’s essential to negotiate terms that suit your cash flow while ensuring the supplier is comfortable with the arrangement. Using secure payment methods and escrow services can also mitigate risks associated with international transactions.
- What quality assurance processes should I expect from suppliers?
Reputable suppliers should have established quality assurance (QA) processes to ensure the durability and functionality of custom corner desks. Expect regular inspections during production, including material checks, dimensions, and finishes. Request documentation of QA measures, such as certifications or test results. Additionally, inquire about post-production testing and the supplier’s policy on handling defects or issues. A reliable supplier will be transparent about their QA protocols and willing to accommodate your specific quality requirements.
-
What logistics considerations should I keep in mind when importing custom corner desks?
When importing custom corner desks, logistics play a crucial role in timely delivery and cost management. Consider shipping methods, such as sea freight for bulk orders or air freight for smaller shipments. Be aware of customs regulations and duties applicable to your region, as these can impact overall costs. Establish clear communication with your supplier regarding packaging to ensure protection during transit. Lastly, partner with a reliable freight forwarder who can navigate the complexities of international shipping and customs clearance. -
How can I ensure my custom corner desk meets local regulations and standards?
To ensure that your custom corner desk complies with local regulations and standards, familiarize yourself with the specific requirements in your region. This may include safety standards, environmental regulations, and ergonomic guidelines. Engage with suppliers who are knowledgeable about these standards and can provide relevant certifications. Before finalizing your order, request documentation proving compliance. Consulting with local authorities or industry experts can also provide insights into any additional requirements that must be met.
Important Disclaimer & Terms of Use
⚠️ Important Disclaimer
The information provided in this guide, including content regarding manufacturers, technical specifications, and market analysis, is for informational and educational purposes only. It does not constitute professional procurement advice, financial advice, or legal advice.
While we have made every effort to ensure the accuracy and timeliness of the information, we are not responsible for any errors, omissions, or outdated information. Market conditions, company details, and technical standards are subject to change.
B2B buyers must conduct their own independent and thorough due diligence before making any purchasing decisions. This includes contacting suppliers directly, verifying certifications, requesting samples, and seeking professional consultation. The risk of relying on any information in this guide is borne solely by the reader.
Strategic Sourcing Conclusion and Outlook for corner desk custom
Why is Strategic Sourcing Essential for Custom Corner Desks?
In the competitive landscape of B2B procurement, strategic sourcing for custom corner desks is not just beneficial but imperative. Buyers from Africa, South America, the Middle East, and Europe can maximize value by understanding their unique requirements and leveraging global suppliers’ capabilities. This involves assessing design specifications, material quality, and supplier reliability to ensure that the final product meets both functional and aesthetic needs.
What Are the Key Takeaways for International Buyers?
Key takeaways include the importance of establishing clear communication channels with suppliers, conducting thorough market research to identify potential partners, and considering local regulations and import duties that may affect costs. Moreover, fostering long-term relationships with manufacturers can lead to better pricing, quality assurance, and innovation in product design.
How Can Buyers Position Themselves for Future Success?
As the demand for ergonomic and space-efficient office solutions grows, international B2B buyers are encouraged to stay ahead of trends by incorporating flexibility into their sourcing strategies. Embracing sustainability and customization will not only enhance workspace functionality but also align with global market shifts toward environmentally responsible practices.
In conclusion, strategic sourcing is the cornerstone of successful procurement for custom corner desks. By proactively engaging with suppliers and adapting to evolving market demands, buyers can secure a competitive edge in their respective regions. Take action today by exploring diverse supplier networks and investing in solutions that cater to your unique business needs.