The Ultimate Guide to Electric Motor Manufacturer (2025)
Introduction: Navigating the Global Market for electric motor manufacturer
In today’s rapidly evolving industrial landscape, sourcing reliable electric motors can be a daunting challenge for international B2B buyers. With numerous manufacturers and a wide array of specifications to consider, finding the right electric motor manufacturer that meets both performance and budgetary requirements is crucial. This comprehensive guide serves as a valuable resource, addressing essential aspects such as the various types of electric motors available, their applications across different industries, and effective supplier vetting processes.
International buyers from Africa, South America, the Middle East, and Europe, including key markets like Turkey and Egypt, will find actionable insights that facilitate informed purchasing decisions. This guide not only outlines the critical factors influencing cost and performance but also provides strategies for evaluating potential suppliers based on quality, certification, and service support.
By navigating through this resource, you will gain a deeper understanding of the global electric motor market, empowering you to make strategic choices that enhance operational efficiency and drive business growth. Whether you’re looking for low-voltage motors for manufacturing or high-efficiency models for renewable energy applications, this guide equips you with the knowledge to succeed in your sourcing endeavors.
Understanding electric motor manufacturer Types and Variations
Type Name | Key Distinguishing Features | Primary B2B Applications | Brief Pros & Cons for Buyers |
---|---|---|---|
AC Induction Motors | Operate on alternating current; robust and reliable | Manufacturing, HVAC systems | Pros: Durable, low maintenance; Cons: Lower efficiency at low speeds. |
DC Brushless Motors | Use electronic commutation; high efficiency | Robotics, electric vehicles | Pros: High torque, quiet operation; Cons: Higher initial cost. |
Stepper Motors | Divide a full rotation into smaller steps | 3D printing, CNC machines | Pros: Precise control, good for positioning; Cons: Limited speed range. |
Synchronous Motors | Operate in sync with the supply frequency | Power generation, renewable energy | Pros: High efficiency, stable operation; Cons: More complex control systems. |
Permanent Magnet Motors | Use permanent magnets for high efficiency | Consumer electronics, appliances | Pros: Compact size, high power-to-weight ratio; Cons: Sensitive to temperature changes. |
What Are the Key Characteristics of AC Induction Motors?
AC Induction Motors are widely used in various industries due to their robustness and reliability. They operate using alternating current and are characterized by their simple construction, which minimizes maintenance needs. These motors are particularly suitable for applications in manufacturing and HVAC systems, where durability is essential. When purchasing, buyers should consider the motor’s efficiency at different speeds, as they can be less efficient at low speeds compared to other types.
How Do DC Brushless Motors Stand Out for B2B Applications?
DC Brushless Motors are known for their high efficiency and are commonly used in robotics and electric vehicles. They feature electronic commutation, eliminating the need for brushes and reducing wear. This type of motor provides high torque and operates quietly, making it ideal for applications requiring precision and low noise levels. Buyers should evaluate the initial investment cost against potential long-term savings in maintenance and energy efficiency.
Why Choose Stepper Motors for Precision Control?
Stepper Motors are unique in that they divide a full rotation into smaller, precise steps, making them ideal for applications that require accurate positioning, such as 3D printing and CNC machines. They provide excellent control over motion and are relatively easy to implement. However, buyers should be mindful of their speed limitations and ensure that the selected motor meets the specific speed and torque requirements of their application.
What Are the Advantages of Synchronous Motors in Power Generation?
Synchronous Motors operate in sync with the supply frequency, making them highly efficient and stable for applications such as power generation and renewable energy systems. These motors provide consistent performance and are capable of running at high efficiency under varying loads. B2B buyers must consider the complexity of the control systems required, as these motors may necessitate additional investment in technology for optimal operation.
How Do Permanent Magnet Motors Benefit Consumer Electronics?
Permanent Magnet Motors are recognized for their compact size and high power-to-weight ratio, making them suitable for consumer electronics and appliances. They utilize permanent magnets, which contribute to their high efficiency, especially in small applications. However, buyers should be aware that these motors can be sensitive to temperature changes, which may affect their performance in certain environments. Evaluating the application environment is crucial for ensuring long-term reliability.
Related Video: HOW ITS MADE: Tesla Electric Motor Manufacture
Key Industrial Applications of electric motor manufacturer
Industry/Sector | Specific Application of Electric Motor Manufacturer | Value/Benefit for the Business | Key Sourcing Considerations for this Application |
---|---|---|---|
Manufacturing | Conveyor Systems | Increases efficiency and productivity in material handling | Motor durability, energy efficiency, and control options |
Agriculture | Irrigation Pumps | Enhances water management and crop yield | Compatibility with local power supply and environmental conditions |
Mining | Crushing and Grinding Equipment | Improves operational efficiency and reduces downtime | Robustness under harsh conditions and maintenance support |
Transportation | Electric Vehicles | Reduces carbon footprint and operational costs | Battery compatibility and motor performance under various loads |
HVAC (Heating, Ventilation, and Air Conditioning) | Compressors and Fans | Enhances energy efficiency and comfort levels | Noise levels, energy efficiency ratings, and reliability |
How is Electric Motor Manufacturing Applied in Key Industries?
Manufacturing: Conveyor Systems
Electric motors are vital in manufacturing for powering conveyor systems that transport materials and products efficiently across production lines. By integrating high-performance electric motors, businesses can significantly enhance operational efficiency and productivity, minimizing manual labor and reducing the risk of workplace accidents. International buyers should prioritize sourcing motors that offer durability and energy efficiency, as these factors directly impact long-term operational costs and sustainability.
Agriculture: Irrigation Pumps
In the agricultural sector, electric motors are used to drive irrigation pumps, facilitating effective water management. This application is crucial for maximizing crop yield in regions with variable rainfall, particularly in Africa and South America. Buyers must consider motors that are compatible with local power supplies and can withstand environmental stresses such as dust and moisture, ensuring reliable performance in diverse conditions.
Mining: Crushing and Grinding Equipment
Electric motors are essential in mining operations, particularly for driving crushing and grinding equipment. These motors improve operational efficiency and reduce downtime, crucial for maintaining productivity in a highly competitive market. Buyers in the mining sector should focus on sourcing robust motors designed to operate in harsh environments, with strong support for maintenance and service to minimize operational disruptions.
Transportation: Electric Vehicles
The rise of electric vehicles (EVs) has made electric motors a cornerstone of the transportation industry. They contribute to a significant reduction in carbon emissions and lower operational costs compared to traditional combustion engines. B2B buyers, particularly in Europe and the Middle East, should consider compatibility with battery systems and the motor’s performance under various loads, ensuring optimal efficiency and range for their vehicles.
HVAC (Heating, Ventilation, and Air Conditioning): Compressors and Fans
Electric motors power compressors and fans in HVAC systems, playing a critical role in maintaining energy efficiency and comfort levels in residential and commercial buildings. Sourcing considerations include the motor’s noise levels, energy efficiency ratings, and overall reliability, as these elements directly affect customer satisfaction and operational costs. Buyers should seek manufacturers that offer motors tailored to specific HVAC applications, ensuring optimal performance in diverse environments.
Related Video: Electric Motor FACTORY – HOW IT’S MADE a Industrial Motor Assembly
3 Common User Pain Points for ‘electric motor manufacturer’ & Their Solutions
Scenario 1: Difficulty Sourcing High-Quality Electric Motors
The Problem:
B2B buyers in regions like Africa and South America often struggle to find reliable suppliers of high-quality electric motors. This challenge can stem from limited local manufacturing capabilities, leading to reliance on imports. Buyers may face issues such as inconsistent product quality, long lead times, and lack of transparency in the supply chain. These factors can significantly impact production schedules and operational efficiency, causing frustration and potential financial losses.
The Solution:
To effectively source high-quality electric motors, buyers should start by conducting thorough research on manufacturers. Look for suppliers with established reputations and verified certifications, such as ISO standards, which indicate adherence to international quality benchmarks. Utilizing platforms like Global Sources or Alibaba can help identify reputable manufacturers.
Engaging in direct communication with potential suppliers is crucial. Request product samples and ask for references from other businesses in your region that have successfully used the supplier’s products. Additionally, consider attending industry trade shows or exhibitions relevant to electric motors; this provides an opportunity to meet manufacturers face-to-face and assess their offerings firsthand.
Scenario 2: Navigating Complex Technical Specifications
The Problem:
B2B buyers often encounter challenges when trying to understand and specify the technical requirements for electric motors. This situation is particularly pronounced in sectors such as manufacturing and mining, where the motors must meet specific operational demands. Misunderstanding the necessary specifications can lead to purchasing the wrong type of motor, resulting in operational inefficiencies and increased costs.
The Solution:
To overcome this hurdle, buyers should invest time in understanding their specific application needs. Collaborating with engineers or technical experts within their organization can provide insights into the required specifications, such as torque, speed, and efficiency ratings.
When engaging with electric motor manufacturers, don’t hesitate to ask detailed questions regarding the technical aspects of the products. Request technical datasheets and product catalogs that outline performance metrics. Some manufacturers offer consultancy services to help buyers identify the most suitable products for their applications. Additionally, leveraging online resources and forums can provide clarity on common specifications and industry best practices.
Scenario 3: Managing After-Sales Support and Maintenance
The Problem:
Once electric motors are purchased and installed, B2B buyers often face challenges with after-sales support and maintenance. In regions like the Middle East and parts of Europe, where local support may be limited, buyers find it difficult to receive timely maintenance or repairs. This can lead to prolonged downtimes and increased operational costs, which can significantly affect profitability.
The Solution:
Buyers should prioritize manufacturers that offer robust after-sales support and service agreements. When evaluating potential suppliers, inquire about their warranty terms and the availability of local service centers. It’s advantageous to choose manufacturers that provide comprehensive training for staff on maintenance procedures.
Establishing a preventive maintenance schedule is also critical. Work with the supplier to develop a tailored maintenance plan that includes regular check-ups and servicing. This proactive approach can help identify issues before they escalate, ensuring that motors operate at peak efficiency. Furthermore, joining industry associations can provide access to resources and networks that facilitate better maintenance practices and support.
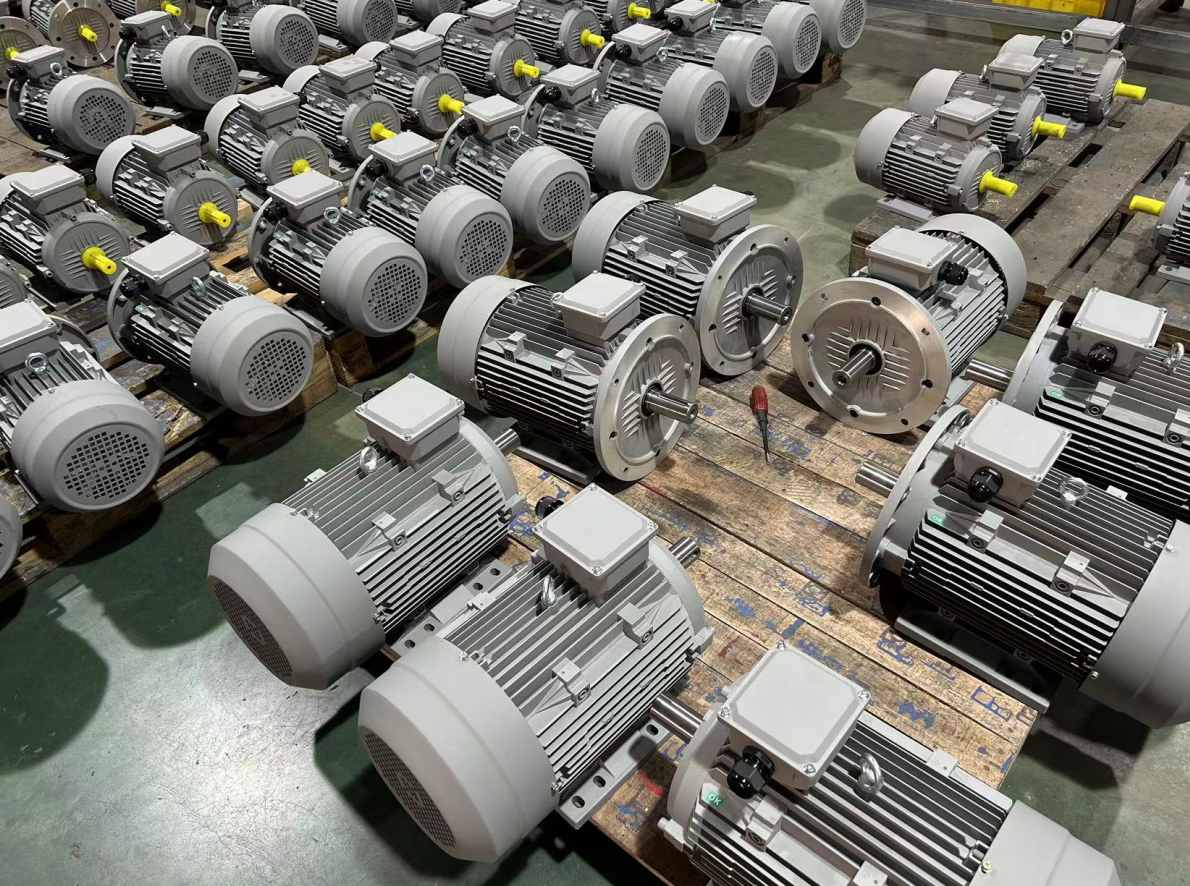
A stock image related to electric motor manufacturer.
Strategic Material Selection Guide for electric motor manufacturer
What Are the Key Materials Used in Electric Motor Manufacturing?
When selecting materials for electric motor manufacturing, it’s essential to consider the properties and suitability of each material for specific applications. Below, we analyze four common materials used in electric motors: copper, aluminum, steel, and plastic composites. Each material has distinct characteristics that can significantly influence the performance and cost-effectiveness of the final product.
How Does Copper Impact Electric Motor Performance?
Key Properties: Copper is renowned for its excellent electrical conductivity, thermal conductivity, and resistance to corrosion. It can withstand high temperatures and pressures, making it ideal for winding coils in motors.
Pros & Cons: The primary advantage of copper is its superior conductivity, which enhances motor efficiency. However, it is relatively expensive compared to other metals, and its weight can be a concern in applications where weight reduction is critical.
Impact on Application: Copper is particularly suitable for high-performance electric motors used in automotive and aerospace applications where efficiency is paramount. Its compatibility with various media is excellent, but care must be taken in corrosive environments.
Considerations for International Buyers: Buyers from Africa, South America, the Middle East, and Europe should be aware of compliance with international standards such as ASTM and DIN when sourcing copper. Additionally, fluctuations in copper prices can impact overall project budgets.
What Role Does Aluminum Play in Electric Motors?
Key Properties: Aluminum is lightweight, has good electrical conductivity, and offers excellent corrosion resistance. It typically has a lower melting point than copper, which can be advantageous in manufacturing processes.
Pros & Cons: The key advantage of aluminum is its lower cost and weight, making it a popular choice for applications where weight savings are critical. However, it has lower conductivity than copper, which may necessitate larger wire sizes to achieve similar performance.
Impact on Application: Aluminum is often used in electric motors for consumer appliances and automotive applications where weight and cost are significant factors. Its compatibility with various environments is generally good, although it may require protective coatings in harsh conditions.
Considerations for International Buyers: Buyers should consider the local availability of aluminum and its compliance with international standards. In regions like Turkey and Egypt, understanding local sourcing options can lead to cost savings.
Why is Steel a Common Choice in Electric Motor Manufacturing?
Key Properties: Steel is known for its strength, durability, and magnetic properties, making it an excellent choice for motor frames and cores. It can handle high mechanical stresses and is generally resistant to wear.
Pros & Cons: The primary advantage of steel is its robustness and ability to maintain structural integrity under load. However, it is heavier than aluminum and can be prone to corrosion if not properly treated.
Impact on Application: Steel is widely used in industrial electric motors where strength and durability are critical. Its magnetic properties enhance motor performance, but it may not be suitable for lightweight applications.
Considerations for International Buyers: Buyers should ensure that the steel used meets relevant standards, such as JIS or ASTM, particularly for applications in demanding environments. Understanding local regulations regarding material sourcing can also be beneficial.
How Do Plastic Composites Contribute to Electric Motor Design?
Key Properties: Plastic composites offer excellent resistance to corrosion and lightweight characteristics. They can be engineered to provide specific mechanical properties and thermal resistance.
Pros & Cons: The main advantage of plastic composites is their versatility and low weight, which can lead to significant energy savings in applications. However, they may not have the same strength or thermal conductivity as metals, which can limit their use in high-performance applications.
Impact on Application: Plastic composites are often used in housings and non-load-bearing components of electric motors. They are particularly effective in environments where corrosion is a concern, but they may not be suitable for high-heat applications.
Considerations for International Buyers: International buyers should evaluate the compatibility of plastic composites with local manufacturing processes and standards. Understanding the lifecycle and recyclability of these materials can also influence purchasing decisions.
Summary Table of Strategic Material Selection for Electric Motor Manufacturing
Material | Typical Use Case for Electric Motor Manufacturer | Key Advantage | Key Disadvantage/Limitation | Relative Cost (Low/Med/High) |
---|---|---|---|---|
Copper | Winding coils in high-performance motors | Superior electrical conductivity | High cost, heavy | High |
Aluminum | Lightweight motors in consumer appliances | Cost-effective, lightweight | Lower conductivity than copper | Medium |
Steel | Industrial motors requiring durability | Strong and durable | Heavier, prone to corrosion | Medium |
Plastic Composites | Housings and non-load-bearing components | Corrosion-resistant, lightweight | Limited strength and conductivity | Low |
This strategic material selection guide provides international B2B buyers with critical insights into the materials best suited for electric motor manufacturing, enabling informed decisions that align with their specific operational needs and regional considerations.
In-depth Look: Manufacturing Processes and Quality Assurance for electric motor manufacturer
What Are the Main Stages in the Manufacturing Process of Electric Motors?
The manufacturing process for electric motors is a multi-step procedure that ensures high performance and reliability. Each stage is crucial in producing a motor that meets the demands of various applications.
1. Material Preparation
The manufacturing process begins with the selection and preparation of materials. Common materials include silicon steel for the core, copper for windings, and various plastics for insulation. Quality of raw materials is paramount; using substandard materials can lead to motor inefficiencies and failures. B2B buyers should inquire about the supplier’s sourcing practices and the quality assurance of incoming materials.
2. Forming
During the forming stage, materials are shaped into components. This involves processes such as stamping, forging, and machining. For instance, the stator and rotor components are often stamped from sheets of silicon steel to improve magnetic properties. Advanced techniques like CNC machining enhance precision and reduce waste. Buyers should evaluate the technological capabilities of suppliers, as sophisticated machinery can significantly impact the quality and cost-effectiveness of the final product.
3. Assembly
Assembly is where the motor’s components come together. This stage typically involves winding the copper wire around the stator, inserting the rotor, and assembling the end bells. Effective assembly requires skilled labor and automated tools to ensure consistent quality. B2B buyers should assess whether the manufacturer employs skilled technicians and modern assembly techniques, as this can affect the motor’s durability and performance.
4. Finishing
Finishing processes include insulation, painting, and adding protective coatings. Insulation is critical to prevent electrical failures and ensure safety. Painting not only enhances aesthetics but also adds a layer of protection against environmental factors. It’s essential for buyers to confirm that suppliers adhere to industry standards for finishing processes to ensure long-lasting products.
How Do Quality Assurance Practices Impact Electric Motor Manufacturing?
Quality assurance (QA) is integral to the manufacturing process, ensuring that electric motors meet international standards and customer expectations.
Relevant International Standards for Electric Motor Manufacturing
International standards like ISO 9001 are vital for ensuring that manufacturing processes are consistently improved and products are reliable. In addition, certifications such as CE (Conformité Européenne) and API (American Petroleum Institute) are crucial for specific industries. B2B buyers should prioritize suppliers with these certifications, as they indicate adherence to quality standards and regulations.
What Are the Key Quality Control Checkpoints in Electric Motor Manufacturing?
Quality control (QC) involves several checkpoints throughout the manufacturing process to catch defects early. Key QC checkpoints include:
-
Incoming Quality Control (IQC): This ensures that raw materials meet specified standards before production begins. Buyers should verify how suppliers handle IQC and whether they document the inspection results.
-
In-Process Quality Control (IPQC): Conducted during manufacturing, IPQC checks for defects at various stages. Suppliers should provide data on IPQC methods and outcomes.
-
Final Quality Control (FQC): This is the last line of defense before products are shipped. FQC typically involves rigorous testing, including electrical and mechanical performance assessments. Buyers can request FQC reports to understand the reliability of the motors.
What Common Testing Methods Are Used in Electric Motor Quality Assurance?
Several testing methods are employed to ensure that electric motors perform as expected. These include:
-
Electrical Testing: This verifies insulation resistance, winding resistance, and inductance. It ensures that the motor operates efficiently and safely under load conditions.
-
Mechanical Testing: This includes vibration analysis and thermal imaging to detect potential issues such as misalignment or overheating.
-
Performance Testing: Motors are subjected to load tests to ensure they meet specified performance criteria. This is crucial for applications where reliability is non-negotiable.
B2B buyers should inquire about the specific testing protocols used by suppliers, as this can greatly affect motor performance and longevity.
How Can B2B Buyers Verify Supplier Quality Control?
Verifying a supplier’s quality control practices is essential for minimizing risks in the supply chain. Here are several strategies B2B buyers can employ:
-
Audits: Conducting on-site audits allows buyers to assess the manufacturing processes, quality control measures, and overall compliance with international standards. This firsthand observation can be invaluable.
-
Quality Reports: Suppliers should provide documentation of their quality control processes, including IQC, IPQC, and FQC results. These reports should detail any non-conformances and corrective actions taken.
-
Third-Party Inspections: Engaging third-party inspection services can provide an unbiased view of the supplier’s quality control practices. This is particularly useful for international transactions where distance may complicate direct oversight.
What Are the Quality Control Nuances for International B2B Buyers?
International B2B buyers, particularly from regions like Africa, South America, the Middle East, and Europe, face unique challenges in quality control. Differences in regulatory standards, cultural practices, and logistical issues can complicate the procurement process. Buyers should consider the following:
-
Regulatory Compliance: Understand the local regulations that may affect product quality and safety. This is especially important for products exported to or from regions with strict compliance laws.
-
Cultural Considerations: Building relationships with suppliers is crucial in many cultures. Establishing trust can facilitate better communication regarding quality expectations.
-
Logistics: Ensure that the chosen supplier has robust logistics capabilities to handle the complexities of international shipping, which can impact the timely delivery of quality products.
By thoroughly evaluating manufacturing processes and quality assurance practices, B2B buyers can make informed decisions, minimizing risks and ensuring they receive high-quality electric motors tailored to their specific needs.
Practical Sourcing Guide: A Step-by-Step Checklist for ‘electric motor manufacturer’
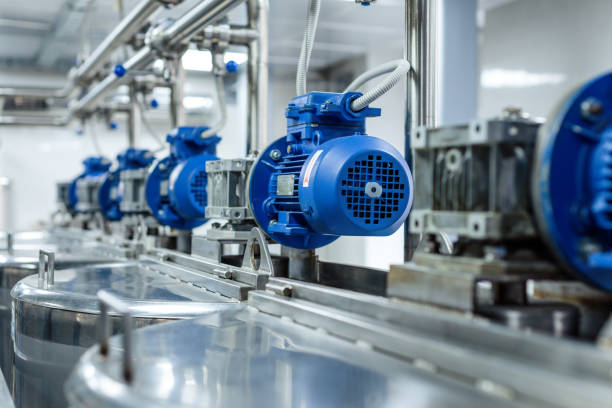
A stock image related to electric motor manufacturer.
The following checklist serves as a practical guide for international B2B buyers looking to procure electric motors. This step-by-step approach will ensure that you make informed decisions, minimize risks, and establish strong supplier relationships.
Step 1: Define Your Technical Specifications
Before starting your search for an electric motor manufacturer, it’s essential to clearly outline your technical requirements. Consider factors such as the type of motor (AC, DC, servo, etc.), power ratings, torque, speed, and environmental conditions.
– Why it’s important: Defining specifications helps you narrow down suppliers who can meet your exact needs, reducing the chances of costly mistakes later on.
Step 2: Research Market Trends and Suppliers
Conduct thorough research on the electric motor industry, focusing on market trends and potential suppliers. Utilize industry reports, trade publications, and online directories.
– What to look for: Pay attention to geographical trends, innovations, and the reputation of manufacturers in your target regions, such as Africa, South America, the Middle East, and Europe.
Step 3: Evaluate Potential Suppliers
Before committing to any supplier, it is crucial to vet them thoroughly. Request company profiles, case studies, and references from buyers in similar industries or regions.
– Key considerations: Look for suppliers who have experience in your specific application and can demonstrate a history of reliability and quality.
Step 4: ✅ Verify Supplier Certifications
Ensure that the manufacturers you are considering hold the necessary certifications, such as ISO 9001 for quality management and CE marking for European compliance.
– Why this matters: Certifications indicate that a supplier adheres to international quality standards, which is crucial for maintaining product integrity and safety.
Step 5: Request Samples or Prototypes
Once you have shortlisted potential suppliers, request samples or prototypes of the electric motors you are interested in. This step allows you to assess the quality and performance of the products firsthand.
– What to evaluate: Inspect the materials, construction, and functionality of the samples to ensure they meet your specifications.
Step 6: Negotiate Terms and Conditions
After selecting your preferred supplier, negotiate terms and conditions, including pricing, delivery timelines, payment terms, and warranties.
– Important aspects: Ensure that all agreements are documented to avoid misunderstandings and protect your interests.
Step 7: Establish a Communication Plan
Effective communication is vital for a successful partnership. Establish a clear plan for ongoing communication with your supplier, including regular updates and feedback mechanisms.
– Why this is essential: A strong communication channel fosters collaboration, helps resolve issues quickly, and builds a foundation for a long-term relationship.
By following this comprehensive checklist, international B2B buyers can confidently navigate the procurement process for electric motors, ensuring they select the right manufacturer for their specific needs.
Comprehensive Cost and Pricing Analysis for electric motor manufacturer Sourcing
What Are the Key Cost Components in Electric Motor Manufacturing?
When sourcing electric motors, understanding the cost structure is essential for effective budgeting and negotiations. The primary cost components include:
-
Materials: The quality and type of materials significantly influence the overall cost. High-grade metals, magnets, and insulation materials can enhance performance but increase costs.
-
Labor: Skilled labor is essential for manufacturing electric motors. Labor costs can vary based on geographical location, skill level, and local wage standards.
-
Manufacturing Overhead: This includes expenses related to utilities, maintenance, and factory operations. Efficient manufacturing processes can help lower overhead costs.
-
Tooling: Initial tooling costs can be substantial, particularly for custom designs. Consider these costs when evaluating quotes, as they can vary widely among suppliers.
-
Quality Control (QC): Investing in stringent quality control processes can lead to higher upfront costs but reduce long-term issues and warranty claims.
-
Logistics: Transportation and warehousing costs must be factored in, particularly for international shipments. The choice of logistics partner can affect both cost and delivery timelines.
-
Margin: Suppliers will typically add a profit margin to their costs. Understanding the typical margins in the electric motor industry can help buyers negotiate better deals.
How Do Price Influencers Impact Electric Motor Sourcing?
Several factors can influence the pricing of electric motors, and being aware of these can lead to more informed purchasing decisions:
-
Volume and Minimum Order Quantity (MOQ): Larger orders often qualify for discounts, which can significantly reduce per-unit costs. Always inquire about the MOQ and how it impacts pricing.
-
Specifications and Customization: Custom specifications can lead to increased costs due to additional engineering and production efforts. It’s important to balance customization needs with budget constraints.
-
Materials and Quality Certifications: Higher-quality materials and certifications (like ISO standards) often come at a premium. Assess whether these are necessary for your application to avoid unnecessary costs.
-
Supplier Factors: The reputation, location, and reliability of the supplier can affect pricing. Established suppliers may charge more but offer better quality and service.
-
Incoterms: Understanding the Incoterms (International Commercial Terms) used in your contract can impact logistics costs and responsibilities. Choose terms that align with your logistical capabilities and risk tolerance.
What Are Some Effective Buyer Tips for Negotiating Electric Motor Prices?
To maximize cost efficiency and value when sourcing electric motors, consider the following strategies:
-
Negotiate with Multiple Suppliers: Engaging multiple suppliers can create competition, leading to better pricing and terms. Presenting comparative quotes can strengthen your negotiating position.
-
Focus on Total Cost of Ownership (TCO): Evaluate the TCO rather than just the initial purchase price. Consider long-term factors such as energy efficiency, maintenance costs, and expected lifespan.
-
Understand Pricing Nuances: Familiarize yourself with the nuances of pricing in different regions. For instance, suppliers in Europe may have different pricing structures compared to those in Africa or South America.
-
Leverage Local Knowledge: Utilize local representatives or consultants who understand the market dynamics and can provide insights into fair pricing and reliable suppliers.
-
Stay Informed About Market Trends: Keep an eye on global material prices, labor costs, and technological advancements in electric motors. This knowledge can aid in timing your purchases to achieve the best prices.
Disclaimer on Indicative Prices
It is important to note that prices for electric motors can vary widely based on numerous factors including specifications, order quantities, and market conditions. Always request detailed quotes from multiple suppliers and conduct thorough due diligence to ensure you receive the best value for your investment.
Alternatives Analysis: Comparing electric motor manufacturer With Other Solutions
Understanding Alternatives in Electric Motor Solutions
When considering electric motor manufacturers, B2B buyers must explore alternative technologies that can fulfill similar functions. This analysis will compare electric motors to hydraulic systems and pneumatic actuators—two prevalent alternatives in various industrial applications. By evaluating performance, cost, ease of implementation, maintenance, and best use cases, buyers can make informed decisions tailored to their specific operational needs.
Comparison Table of Electric Motor Manufacturer and Alternatives
Comparison Aspect | Electric Motor Manufacturer | Hydraulic Systems | Pneumatic Actuators |
---|---|---|---|
Performance | High efficiency and torque | Excellent power-to-weight ratio | Quick response times |
Cost | Moderate initial investment | Higher setup and operational costs | Lower initial costs |
Ease of Implementation | Relatively easy installation | Complex piping and setup | Simple installation |
Maintenance | Low maintenance requirements | Regular maintenance needed | Moderate maintenance |
Best Use Case | Precision applications | Heavy lifting and torque tasks | Fast, repetitive tasks |
Detailed Breakdown of Alternatives
Hydraulic Systems
Hydraulic systems utilize fluid power to perform mechanical tasks, often found in heavy machinery and construction equipment. Pros include their ability to generate high force and torque, making them suitable for lifting and pushing heavy loads. However, the cons involve significant initial setup costs and the need for regular maintenance to prevent leaks and ensure system efficiency. For industries in Africa or the Middle East focusing on construction, hydraulic systems may be ideal despite their complexity.
Pneumatic Actuators
Pneumatic actuators operate using compressed air to produce movement, commonly used in assembly lines and packaging machinery. The advantages of pneumatic systems include their lower initial costs and relatively simple installation processes. They also offer quick response times, making them suitable for tasks requiring rapid actuation. However, their disadvantages include moderate maintenance needs and limitations in force compared to hydraulic systems. For buyers in South America focused on fast-paced production environments, pneumatic solutions can be a practical choice.
Conclusion: Choosing the Right Solution for Your Business Needs
Selecting the appropriate solution between electric motors, hydraulic systems, and pneumatic actuators depends on the specific requirements of your operations. B2B buyers must consider factors such as performance needs, budget constraints, and maintenance capabilities when making their decision. By carefully evaluating these alternatives, businesses can enhance their operational efficiency and ensure long-term success in their respective industries.
Essential Technical Properties and Trade Terminology for electric motor manufacturer
What Are the Essential Technical Properties of Electric Motors?
Understanding the technical properties of electric motors is crucial for international B2B buyers, particularly in regions such as Africa, South America, the Middle East, and Europe. Here are some key specifications to consider:
1. Material Grade
The material grade of components used in electric motors, such as copper for windings or steel for the rotor, directly influences performance and durability. High-grade materials typically lead to better conductivity and thermal resistance, enhancing efficiency and longevity. For B2B buyers, selecting motors made from superior materials can reduce maintenance costs and improve operational reliability.
2. Tolerance
Tolerance refers to the allowable variation in dimensions and specifications of motor components. In electric motors, precise tolerances are essential for ensuring proper fit and functionality. For instance, tighter tolerances in the rotor and stator can lead to reduced vibration and noise, enhancing performance. Buyers should prioritize manufacturers who adhere to stringent tolerance standards to guarantee the motor’s efficiency and lifespan.
3. Efficiency Rating
The efficiency rating, often expressed in terms of percentage, indicates how effectively an electric motor converts electrical energy into mechanical energy. Higher efficiency ratings result in lower energy consumption and operational costs. For international buyers, especially in energy-sensitive markets, selecting high-efficiency motors can lead to significant long-term savings and a reduced carbon footprint.
4. Insulation Class
The insulation class of an electric motor defines its ability to withstand temperature extremes without failure. Common classes include Class B (130°C) and Class F (155°C). Understanding the insulation class is vital for buyers operating in extreme environments, as it affects the motor’s longevity and reliability. Selecting the appropriate insulation class can prevent costly downtimes and repairs.
5. Operating Temperature Range
The operating temperature range specifies the conditions under which the motor can function optimally. Motors designed for high-temperature environments may require special cooling mechanisms or materials. Buyers must ensure that the motors they purchase are suited to their specific operational conditions to maintain efficiency and avoid overheating issues.
What Trade Terminology Should B2B Buyers Know When Purchasing Electric Motors?
Familiarity with industry-specific terminology can streamline the purchasing process and enhance negotiations. Here are some commonly used terms in the electric motor manufacturing sector:
1. OEM (Original Equipment Manufacturer)
An OEM is a company that produces parts or equipment that may be marketed by another manufacturer. In the electric motor industry, buyers often deal directly with OEMs for custom solutions tailored to their specific needs. Understanding OEM relationships can help buyers negotiate better terms and ensure product quality.
2. MOQ (Minimum Order Quantity)
MOQ refers to the smallest number of units a supplier is willing to sell. This concept is vital for B2B buyers who need to understand the supplier’s production capacity and cost-effectiveness. Negotiating the MOQ can impact inventory management and overall procurement costs.
3. RFQ (Request for Quotation)
An RFQ is a document sent to suppliers to solicit price quotes for specific quantities of goods or services. It is a critical step in the procurement process, allowing buyers to compare pricing and terms across different suppliers. Crafting a detailed RFQ can lead to better pricing and service agreements.
4. Incoterms (International Commercial Terms)
Incoterms are a set of predefined commercial terms published by the International Chamber of Commerce (ICC) that define the responsibilities of buyers and sellers in international transactions. Familiarity with Incoterms, such as FOB (Free on Board) or CIF (Cost, Insurance, and Freight), is essential for buyers to understand shipping costs, risks, and delivery responsibilities.
5. Lead Time
Lead time is the amount of time it takes from placing an order until it is received. In the electric motor industry, lead times can vary significantly based on customization and production schedules. Understanding lead times is crucial for buyers to plan their operations effectively and avoid delays in production.
By grasping these essential technical properties and trade terminologies, B2B buyers can make informed decisions, ensuring they select the right electric motors for their specific applications while optimizing costs and operational efficiency.
Navigating Market Dynamics and Sourcing Trends in the electric motor manufacturer Sector
What Are the Current Market Dynamics and Key Trends in the Electric Motor Manufacturing Sector?
The electric motor manufacturing sector is experiencing substantial growth driven by several global factors. Key among these are the increasing demand for energy efficiency, the shift towards renewable energy sources, and the expansion of electric vehicles (EVs). International B2B buyers, particularly from Africa, South America, the Middle East, and Europe, are increasingly influenced by technological advancements that enhance motor performance and efficiency. The rise of Industry 4.0 technologies, including the Internet of Things (IoT) and automation, is transforming production processes and driving demand for smart electric motors that offer predictive maintenance and real-time performance monitoring.
Emerging trends in sourcing include a focus on local suppliers to reduce lead times and transportation costs, especially in regions like Turkey and Egypt, where supply chain disruptions can significantly impact operations. Additionally, international buyers are adopting e-procurement platforms that streamline the sourcing process, enabling them to compare products and prices effectively. These platforms also facilitate access to a wider range of suppliers, fostering competition and innovation.
How Does Sustainability and Ethical Sourcing Impact the Electric Motor Manufacturing Sector?
Sustainability is becoming a crucial consideration for B2B buyers in the electric motor sector. The environmental impact of production processes and the materials used in manufacturing electric motors are under increasing scrutiny. Buyers are now prioritizing suppliers who demonstrate a commitment to reducing carbon footprints and implementing sustainable practices. This includes the use of eco-friendly materials and energy-efficient manufacturing processes that minimize waste and emissions.
Moreover, ethical sourcing is gaining traction as businesses recognize the importance of transparent supply chains. Buyers are increasingly seeking out suppliers that comply with environmental regulations and possess certifications like ISO 14001, which signifies a commitment to environmental management. Additionally, certifications related to ethical labor practices, such as Fair Trade, are becoming important for buyers who want to ensure that their supply chains are not only sustainable but also socially responsible.
What Has Been the Evolution of the Electric Motor Manufacturing Sector?
The electric motor manufacturing sector has a rich history dating back to the late 19th century when the first electric motors were developed. Initially, these motors were primarily used in industrial applications, but their versatility has led to widespread adoption across various sectors, including automotive, aerospace, and consumer electronics.
Over the decades, advancements in materials science and electrical engineering have significantly improved motor efficiency and performance. The introduction of brushless motors and advancements in control technologies have further revolutionized the sector, enabling applications in renewable energy systems, such as wind and solar power. Today, the sector is on the cusp of another transformation driven by the push for electrification and sustainability, making it essential for B2B buyers to stay informed about the latest innovations and sourcing strategies.
In conclusion, understanding the market dynamics and sourcing trends in the electric motor manufacturing sector is critical for international B2B buyers. By prioritizing sustainability and ethical sourcing, buyers can not only enhance their supply chain resilience but also align with the growing demand for environmentally responsible products.
Frequently Asked Questions (FAQs) for B2B Buyers of electric motor manufacturer
-
How do I choose the right electric motor manufacturer for my business needs?
Selecting the right electric motor manufacturer involves assessing several key factors. First, evaluate the manufacturer’s experience and expertise in your specific industry. Review their product range to ensure they offer motors that meet your technical specifications. Additionally, check for certifications like ISO 9001 to guarantee quality standards. Reading customer testimonials and case studies can provide insights into their reliability. Finally, consider their geographical location and logistics capabilities, especially if you are sourcing from Africa, South America, the Middle East, or Europe, to ensure timely delivery. -
What are the common customization options available for electric motors?
Many electric motor manufacturers offer a range of customization options to meet specific application requirements. These can include modifications to motor size, power ratings, efficiency levels, and mounting configurations. Additionally, you can request special features such as variable speed drives, specific insulation types for different environmental conditions, and tailored control systems. Discussing your needs with the manufacturer’s engineering team can help identify feasible customizations while ensuring compliance with industry standards and regulations. -
What minimum order quantities (MOQ) should I expect when sourcing electric motors?
Minimum order quantities can vary significantly among electric motor manufacturers. Typically, MOQs can range from a few units for standard products to hundreds for custom designs. It’s essential to clarify the MOQ with potential suppliers during the initial discussions, as this can impact your budget and inventory management. Some manufacturers may offer flexible terms for new customers or smaller businesses, so don’t hesitate to negotiate based on your specific needs and volume projections. -
What payment terms are standard when purchasing electric motors internationally?
Payment terms for international purchases of electric motors often include options like advance payment, letters of credit, or net 30/60/90 days after shipment. Standard practice typically requires some form of upfront payment, especially for custom orders. It’s advisable to discuss payment terms during the negotiation phase to align expectations and mitigate risks. Additionally, consider the implications of currency exchange rates and transaction fees, which can vary based on your region. -
How can I ensure quality assurance when sourcing electric motors from overseas?
To ensure quality assurance, request detailed documentation from the manufacturer, including certifications, test reports, and compliance with international standards like IEC or NEMA. You may also consider conducting factory audits or inspections prior to placing large orders. Engaging third-party inspection services can provide unbiased quality checks before shipment. Establishing clear quality specifications and performance benchmarks in your contract can further protect your interests. -
What logistics considerations should I keep in mind when importing electric motors?
When importing electric motors, logistics considerations include shipping methods, lead times, and customs regulations. Decide between air freight for faster delivery or sea freight for cost-effectiveness based on your urgency and budget. Ensure that the manufacturer can provide necessary shipping documents, such as a commercial invoice and bill of lading. Familiarize yourself with import duties and taxes in your country to avoid unexpected costs. Partnering with a reliable freight forwarder can help streamline the process and handle any customs clearance issues. -
How do I vet potential electric motor suppliers effectively?
Vetting potential suppliers involves a multi-step approach. Start by checking their business credentials, including years in operation, manufacturing capabilities, and client references. Utilize online platforms like LinkedIn or industry-specific forums to gather feedback from other buyers. Request product samples to assess quality firsthand and inquire about their warranty and support policies. Additionally, it’s beneficial to understand their supply chain practices and any potential impact on delivery times, especially for international transactions. -
What are the key industry standards and certifications to look for in electric motor manufacturers?
When sourcing electric motors, look for manufacturers that comply with key industry standards such as ISO 9001 for quality management, ISO 14001 for environmental management, and OHSAS 18001 for occupational health and safety. Additionally, check for compliance with specific product standards like IEC, NEMA, or UL, depending on your market requirements. These certifications not only ensure product quality but also demonstrate the manufacturer’s commitment to sustainable practices and regulatory compliance, which are increasingly important in today’s global market.
Important Disclaimer & Terms of Use
⚠️ Important Disclaimer
The information provided in this guide, including content regarding manufacturers, technical specifications, and market analysis, is for informational and educational purposes only. It does not constitute professional procurement advice, financial advice, or legal advice.
While we have made every effort to ensure the accuracy and timeliness of the information, we are not responsible for any errors, omissions, or outdated information. Market conditions, company details, and technical standards are subject to change.
B2B buyers must conduct their own independent and thorough due diligence before making any purchasing decisions. This includes contacting suppliers directly, verifying certifications, requesting samples, and seeking professional consultation. The risk of relying on any information in this guide is borne solely by the reader.
Strategic Sourcing Conclusion and Outlook for electric motor manufacturer
What Are the Key Takeaways for Strategic Sourcing in Electric Motor Manufacturing?
In the rapidly evolving landscape of electric motor manufacturing, strategic sourcing emerges as a critical element for international B2B buyers. By prioritizing suppliers that not only meet quality and compliance standards but also demonstrate sustainability practices, businesses can enhance their competitive edge. Understanding regional market dynamics—especially in Africa, South America, the Middle East, and Europe—can lead to more informed purchasing decisions that align with local economic conditions and regulatory requirements.
How Can B2B Buyers Prepare for Future Sourcing Challenges?
Looking ahead, B2B buyers must adopt a proactive approach to sourcing. This includes leveraging technology for better supply chain visibility, fostering strong relationships with suppliers, and being adaptable to changing market demands. Investing in partnerships that emphasize innovation will be key to navigating the complexities of global sourcing.
Why Is Now the Time to Enhance Your Sourcing Strategy?
As the demand for electric motors continues to rise, the opportunity to optimize sourcing strategies has never been greater. By focusing on strategic sourcing, companies can not only reduce costs but also improve product quality and delivery timelines. Now is the time for international B2B buyers to take action—evaluate your sourcing strategies and align them with the global trends shaping the electric motor industry. Embrace the future of manufacturing with confidence and foresight.