Discover GMC Sierra 1500 Custom: The Ultimate Buyer’s Guide (2025)
Introduction: Navigating the Global Market for gmc sierra 1500 custom
In today’s competitive landscape, sourcing the right GMC Sierra 1500 custom vehicles can be a complex endeavor for international B2B buyers, especially those operating in diverse markets like Africa, South America, the Middle East, and Europe. With a myriad of options available, understanding the specifications, customizations, and suitable applications of the GMC Sierra 1500 is crucial for making informed purchasing decisions. This guide aims to demystify the process, providing insights into various types of customizations available, their applications across different industries, and how to effectively vet suppliers to ensure quality and reliability.
Buyers will benefit from a thorough exploration of cost factors associated with the GMC Sierra 1500 custom, including hidden costs that might affect the overall budget. Additionally, we will delve into regional considerations, helping buyers navigate market trends and regulatory environments specific to their locations, such as Mexico or the UK. By equipping B2B buyers with actionable knowledge about sourcing strategies, quality assessment, and potential pitfalls, this guide empowers businesses to optimize their procurement processes. Ultimately, the goal is to enhance buyer confidence and ensure that every investment in a GMC Sierra 1500 custom aligns with strategic business objectives and operational needs.
Understanding gmc sierra 1500 custom Types and Variations
Type Name | Key Distinguishing Features | Primary B2B Applications | Brief Pros & Cons for Buyers |
---|---|---|---|
GMC Sierra 1500 SLT | Premium leather interior, advanced tech features | Fleet management, luxury transport | Pros: High comfort, good resale value. Cons: Higher initial cost. |
GMC Sierra 1500 AT4 | Off-road capabilities, rugged design | Construction, outdoor services | Pros: Excellent off-road performance. Cons: Less fuel-efficient. |
GMC Sierra 1500 Work Truck | Basic features, durable construction | Heavy-duty tasks, tradesmen | Pros: Cost-effective, easy maintenance. Cons: Limited comfort and features. |
GMC Sierra 1500 Denali | High-end finishes, advanced safety features | Executive transport, premium services | Pros: Luxurious, top-tier technology. Cons: Higher operational costs. |
GMC Sierra 1500 Elevation | Sporty appearance, customizable features | Marketing, event logistics | Pros: Attractive design, versatile. Cons: May lack some luxury features. |
What are the Key Features of the GMC Sierra 1500 SLT?
The GMC Sierra 1500 SLT stands out with its premium leather interior and advanced technology, including a high-definition touchscreen and navigation system. This model is particularly suited for businesses that require a vehicle that combines comfort with functionality, such as fleet management or luxury transport services. When considering the SLT, businesses should weigh its higher initial cost against its potential for high resale value and driver satisfaction.
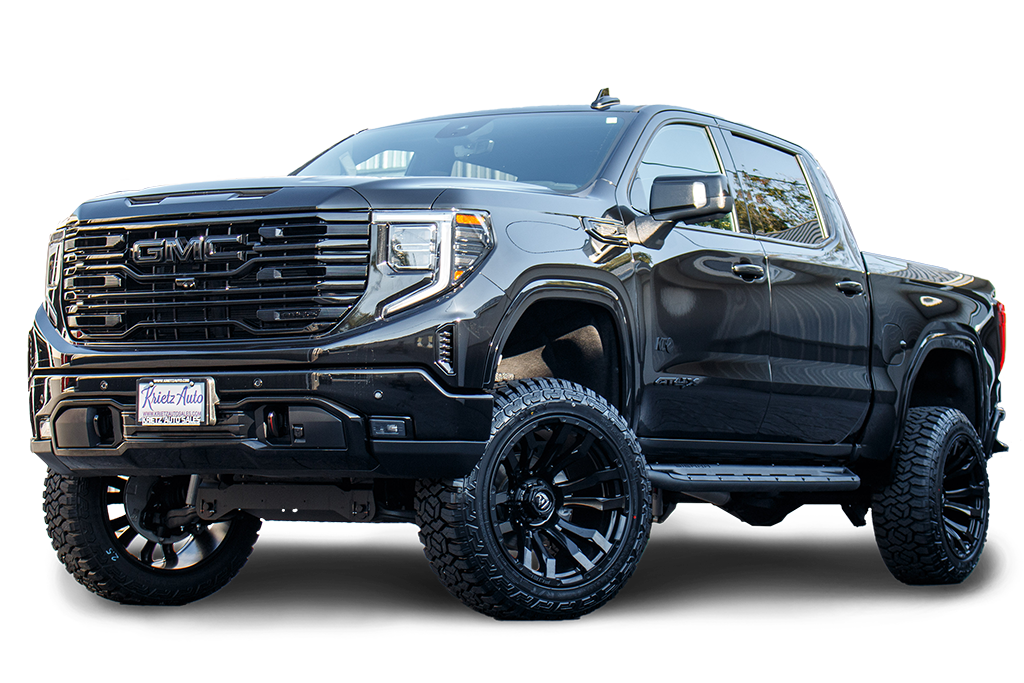
A stock image related to gmc sierra 1500 custom.
How Does the GMC Sierra 1500 AT4 Cater to Off-Road Needs?
Designed for off-road enthusiasts, the GMC Sierra 1500 AT4 features a rugged exterior and enhanced suspension for superior handling on rough terrain. This model is ideal for construction companies and outdoor service providers that need a reliable vehicle capable of navigating challenging environments. Buyers should consider the AT4’s fuel efficiency, which may be lower due to its off-road capabilities, against its performance advantages.
Why Choose the GMC Sierra 1500 Work Truck for Heavy-Duty Tasks?
The GMC Sierra 1500 Work Truck is built for durability and practicality, with a focus on essential features rather than luxury. It is well-suited for tradespeople and businesses that prioritize cost-effectiveness and ease of maintenance. While it may lack some comfort and advanced features, its straightforward design makes it a reliable choice for heavy-duty applications.
What Makes the GMC Sierra 1500 Denali a Premium Choice?
The GMC Sierra 1500 Denali is the epitome of luxury in the pickup truck segment, featuring high-end finishes and cutting-edge safety technologies. It is perfect for businesses that require an executive transport solution or premium service offerings. However, potential buyers should be aware of the higher operational costs associated with this model, which may impact overall budget considerations.
How Does the GMC Sierra 1500 Elevation Stand Out in Customization?
With its sporty appearance and customizable features, the GMC Sierra 1500 Elevation appeals to businesses looking for a visually striking vehicle. This model is particularly effective in marketing and event logistics, where presentation is key. While it offers versatility, buyers should note that it may not include some of the luxury features found in higher-end models, which could influence their decision based on specific business needs.
Related Video: Our FIRST Custom 2022 GMC Sierra 1500 AT4 Truck
Key Industrial Applications of gmc sierra 1500 custom
Industry/Sector | Specific Application of gmc sierra 1500 custom | Value/Benefit for the Business | Key Sourcing Considerations for this Application |
---|---|---|---|
Construction | Heavy-duty material transportation | Enhances productivity by facilitating quick transport of materials and tools to job sites. | Consider payload capacity, durability, and off-road capabilities for rough terrain. |
Agriculture | Farm equipment towing | Increases operational efficiency by towing heavy farm equipment and trailers. | Evaluate towing capacity, engine performance, and compatibility with agricultural implements. |
Logistics and Delivery | Last-mile delivery vehicle | Improves delivery speed and reliability in urban and rural settings. | Assess cargo space, fuel efficiency, and urban maneuverability. |
Mining | Off-road transport for equipment | Provides robust transport solutions in challenging terrains for mining operations. | Focus on durability, off-road capabilities, and maintenance support. |
Oil and Gas | Equipment transport to remote sites | Ensures timely delivery of equipment to remote drilling and exploration locations. | Look for fuel efficiency, cargo capacity, and ruggedness for harsh environments. |
How is the GMC Sierra 1500 Custom Used in the Construction Industry?
In the construction sector, the GMC Sierra 1500 Custom is primarily utilized for transporting heavy-duty materials, tools, and equipment to various job sites. Its robust build and high payload capacity make it an ideal choice for contractors looking to enhance productivity. Buyers from Africa, South America, the Middle East, and Europe should consider the truck’s durability and off-road capabilities, especially when navigating rough terrains common in construction projects. This vehicle significantly reduces downtime by ensuring that essential materials are readily available on-site.
What Role Does the GMC Sierra 1500 Custom Play in Agriculture?
The GMC Sierra 1500 Custom serves as a vital asset in the agricultural industry, particularly for towing farm equipment and trailers. Its impressive towing capacity allows farmers to transport heavy machinery, such as plows and harvesters, efficiently between fields. For international buyers, especially in regions with expansive agricultural landscapes like South America and Africa, it is crucial to evaluate the truck’s engine performance and compatibility with various agricultural implements to ensure seamless operations throughout the farming season.
How Does the GMC Sierra 1500 Custom Enhance Logistics and Delivery Operations?
In logistics and delivery, the GMC Sierra 1500 Custom is an effective last-mile delivery vehicle. Its spacious cargo area is designed to accommodate a variety of goods, making it ideal for both urban and rural delivery routes. International B2B buyers should focus on the vehicle’s fuel efficiency and urban maneuverability, which can significantly impact operational costs and delivery times. This capability is particularly beneficial for businesses looking to optimize their supply chain management in diverse geographical locations.
What Are the Benefits of Using the GMC Sierra 1500 Custom in Mining?
The mining industry requires reliable transport solutions for moving equipment across challenging terrains. The GMC Sierra 1500 Custom excels in this area, providing robust off-road capabilities essential for navigating rough and uneven landscapes. Buyers in the Middle East and Africa, where mining operations are prevalent, should prioritize the truck’s durability and maintenance support to ensure continuous operation and minimize downtime in remote locations.
How is the GMC Sierra 1500 Custom Beneficial for Oil and Gas Operations?
In the oil and gas sector, the GMC Sierra 1500 Custom is utilized for transporting equipment to remote drilling and exploration sites. Its rugged construction and substantial cargo capacity ensure that essential tools and machinery reach their destinations on time, which is critical in this fast-paced industry. International buyers should consider the vehicle’s fuel efficiency and overall performance in harsh environments, as these factors can greatly influence operational success and cost-effectiveness in oil and gas projects.
Related Video: Giving a Custom 2022 GMC Sierra 1500 AT4 Truck a FULL Chrome Delete
3 Common User Pain Points for ‘gmc sierra 1500 custom’ & Their Solutions
Scenario 1: Customization Complexity for Diverse Markets
The Problem: B2B buyers from regions like Africa and South America often struggle with the complexity of customizing the GMC Sierra 1500 to meet local regulations and preferences. Each country has its own vehicle standards, which can include specific emissions requirements, safety features, and even aesthetic preferences that might not align with standard models. This can lead to frustration when trying to source the right configuration that complies with local laws while also appealing to the target market.
The Solution: To effectively navigate this challenge, B2B buyers should engage with local automotive regulatory bodies early in the purchasing process to understand the specific requirements that the GMC Sierra 1500 must meet in their market. It’s advisable to partner with local dealerships or automotive consultants who specialize in import regulations. Additionally, buyers can take advantage of GMC’s customizable options by utilizing online configurators to create a vehicle specification that fits both the regulatory framework and market expectations. By thoroughly researching and planning for customization options, buyers can reduce delays and ensure compliance, ultimately leading to a smoother procurement process.
Scenario 2: Supply Chain Disruptions Impacting Delivery
The Problem: Buyers in Europe and the Middle East may encounter significant delays in the delivery of the GMC Sierra 1500 due to ongoing supply chain disruptions. These disruptions can stem from global events, such as geopolitical tensions or pandemics, which can affect the availability of parts and manufacturing capabilities. Such delays can impede business operations, especially for companies relying on the Sierra for logistics or transportation services.
The Solution: To mitigate the impact of supply chain disruptions, B2B buyers should adopt a proactive approach by establishing relationships with multiple suppliers and logistics partners. Diversifying sources for parts and employing alternative shipping methods can help alleviate delays. Additionally, staying informed about global supply chain trends and collaborating closely with GMC’s customer service can provide insights into expected delivery timelines and alternative options. Buyers should also consider pre-ordering vehicles and parts to buffer against future disruptions, ensuring they have the necessary resources when needed.
Scenario 3: Maintenance and Service Support Challenges
The Problem: International buyers often face challenges in obtaining adequate maintenance and service support for the GMC Sierra 1500, especially in remote or less-developed regions. Lack of trained technicians and parts availability can lead to extended downtimes, negatively impacting the operational efficiency of businesses that depend on these vehicles.
The Solution: To address maintenance and service support issues, buyers should prioritize establishing partnerships with reputable local service providers who have experience with GMC vehicles. It’s crucial to conduct due diligence when selecting these partners to ensure they can meet service standards. Buyers can also invest in training local technicians on GMC vehicle maintenance to create a reliable support network. Additionally, sourcing spare parts in advance and maintaining an inventory can help minimize downtime. By developing a robust maintenance plan that includes regular servicing schedules and local support agreements, buyers can enhance vehicle longevity and operational reliability.
Strategic Material Selection Guide for gmc sierra 1500 custom
What Are the Key Materials Used in the GMC Sierra 1500 Custom?
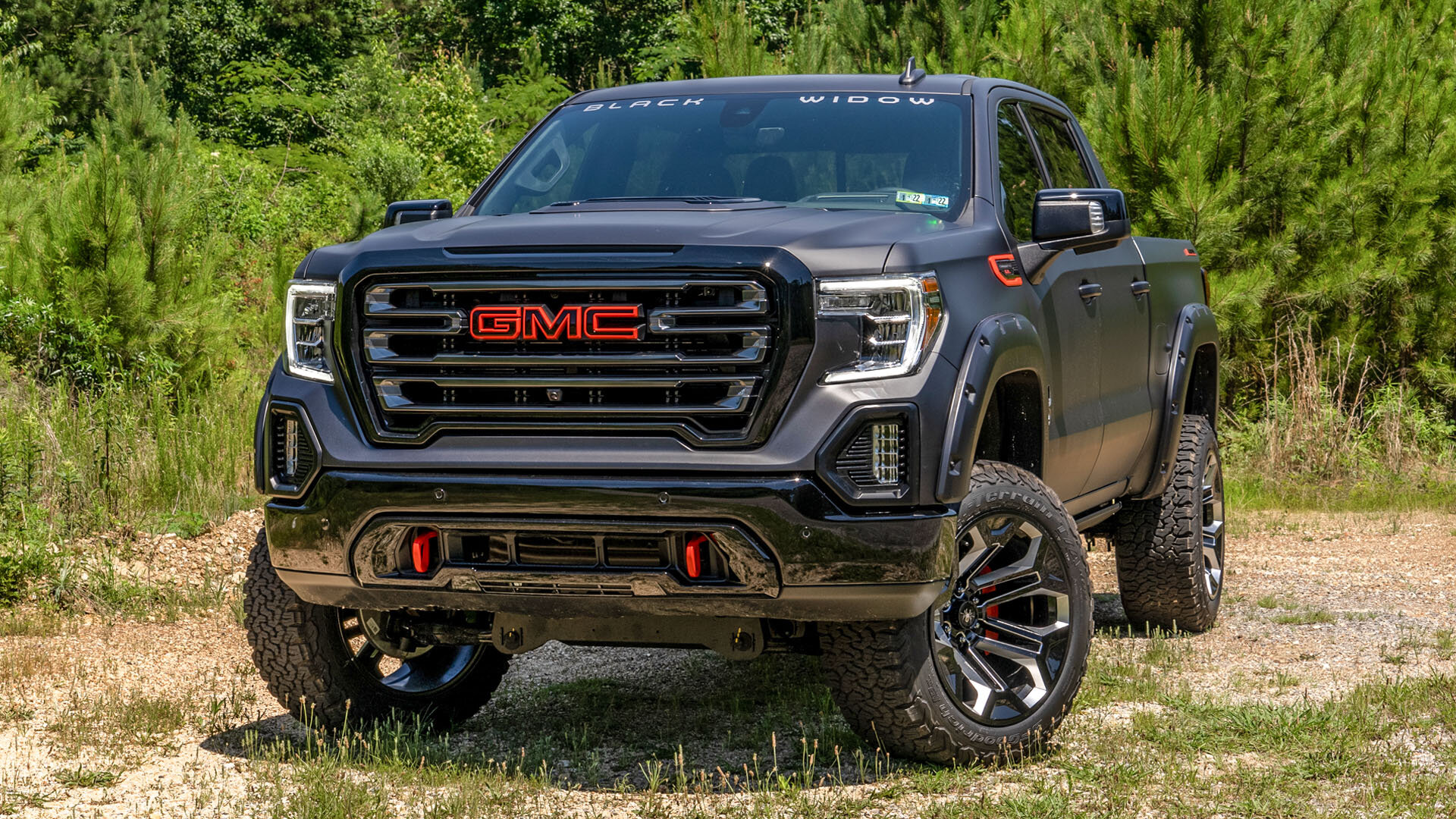
A stock image related to gmc sierra 1500 custom.
When selecting materials for the GMC Sierra 1500 Custom, it’s essential to consider their properties, advantages, disadvantages, and compliance with international standards. Here, we analyze four common materials used in the construction of this vehicle, focusing on their implications for B2B buyers in Africa, South America, the Middle East, and Europe.
How Does Aluminum Impact the Performance of the GMC Sierra 1500 Custom?
Key Properties: Aluminum is lightweight, with excellent corrosion resistance and thermal conductivity. It can withstand significant temperature variations, making it suitable for various climates.
Pros & Cons: The primary advantage of aluminum is its low weight, which enhances fuel efficiency and handling. However, it can be more expensive than steel and may require specialized manufacturing processes, which can increase production costs.
Impact on Application: Aluminum’s lightweight nature improves the overall performance of the GMC Sierra 1500 Custom, especially in towing and payload capacities. It is compatible with various media and applications, making it versatile.
Considerations for International Buyers: Compliance with standards such as ASTM B221 for aluminum extrusions is crucial. Buyers should also consider the availability of aluminum in their region, as sourcing can vary significantly.
What Role Does Steel Play in the GMC Sierra 1500 Custom?
Key Properties: Steel offers high tensile strength and durability, making it an ideal choice for structural components. It has excellent fatigue resistance and can handle high-pressure applications.
Pros & Cons: The main advantage of steel is its strength and affordability. However, it is heavier than aluminum, which can negatively affect fuel efficiency. Additionally, steel is prone to corrosion unless properly treated.
Impact on Application: Steel components are critical for the chassis and frame of the GMC Sierra 1500 Custom, providing stability and safety. Its compatibility with various media is generally high, but corrosion resistance must be managed through coatings.
Considerations for International Buyers: Buyers should ensure compliance with standards such as ASTM A36 for structural steel. The availability of treated steel options is also a factor, especially in regions with high humidity or salt exposure.
How Does Composite Material Enhance the GMC Sierra 1500 Custom?
Key Properties: Composites are lightweight and can be engineered for specific performance characteristics, including impact resistance and thermal insulation.
Pros & Cons: Composites offer excellent strength-to-weight ratios and can be molded into complex shapes, allowing for design flexibility. However, they can be more costly and may require specialized manufacturing techniques.
Impact on Application: Composites are often used in non-structural components, such as body panels and interior fittings, where weight savings are essential. Their compatibility with various media is generally good, but they may not withstand extreme temperatures.
Considerations for International Buyers: Compliance with standards like ASTM D638 for tensile properties is important. B2B buyers should also consider the availability of composite materials in their region, as sourcing can be limited.
What Are the Benefits of Using Plastics in the GMC Sierra 1500 Custom?
Key Properties: Plastics are lightweight, corrosion-resistant, and can be produced in various colors and textures. They also provide good thermal and electrical insulation.
Pros & Cons: The main advantage of plastics is their versatility and low cost. However, they may not offer the same strength as metals and can degrade under UV exposure unless treated.
Impact on Application: Plastics are commonly used for interior components, such as dashboards and panels, where weight reduction and design flexibility are advantageous. Their compatibility with various media is generally satisfactory, but care should be taken regarding temperature limits.
Considerations for International Buyers: Compliance with standards such as ASTM D790 for flexural properties is essential. Buyers should also consider the recycling and disposal regulations in their regions, as these can affect the long-term viability of plastic components.
Summary Table of Material Selection for GMC Sierra 1500 Custom
Material | Typical Use Case for GMC Sierra 1500 Custom | Key Advantage | Key Disadvantage/Limitation | Relative Cost (Low/Med/High) |
---|---|---|---|---|
Aluminum | Body panels, structural components | Lightweight, corrosion-resistant | Higher cost, manufacturing complexity | High |
Steel | Chassis, frame components | Strong, cost-effective | Heavier, prone to corrosion | Medium |
Composite | Body panels, interior fittings | Design flexibility, lightweight | Higher cost, limited temperature resistance | High |
Plastic | Interior components, dashboards | Versatile, low cost | Lower strength, UV degradation risk | Low |
This comprehensive analysis provides international B2B buyers with actionable insights into material selection for the GMC Sierra 1500 Custom, enabling informed decision-making based on performance, cost, and compliance considerations.
In-depth Look: Manufacturing Processes and Quality Assurance for gmc sierra 1500 custom
What Are the Key Stages in the Manufacturing Process of the GMC Sierra 1500 Custom?
The manufacturing process for the GMC Sierra 1500 Custom involves several critical stages, each designed to ensure high-quality production. Understanding these stages can help international B2B buyers assess the quality and reliability of their suppliers.
Material Preparation
The first step in the manufacturing process is material preparation. This involves sourcing high-quality raw materials such as steel, aluminum, and composites. Suppliers must adhere to strict specifications to ensure that the materials meet the necessary strength and durability standards required for the GMC Sierra 1500. The selection of materials is crucial as it directly impacts the vehicle’s performance and longevity.
Forming Techniques
Once the materials are prepared, the next stage is forming. This process includes cutting, stamping, and shaping the materials into specific components. Advanced techniques such as hydroforming and robotic welding are often employed to enhance precision and reduce waste. For example, hydroforming allows for complex shapes to be formed from a single piece of metal, improving structural integrity.
Assembly Line Operations
The assembly stage is where all individual components come together to create the finished vehicle. This process is typically conducted on a moving assembly line, which enhances efficiency. Skilled labor is crucial here, as workers must ensure that each component is fitted correctly. Automated systems are also used extensively, ensuring that each vehicle meets stringent quality standards. During assembly, various checks are performed to catch any discrepancies early in the process.
Finishing Processes
After assembly, the GMC Sierra 1500 undergoes finishing processes, which include painting, interior installation, and quality inspections. The painting process often involves several layers, including primer, base coat, and clear coat, to ensure a durable and aesthetically pleasing finish. Quality assurance during the finishing stage is paramount, as it directly influences customer satisfaction and brand reputation.
How Is Quality Assurance Implemented in the GMC Sierra 1500 Manufacturing Process?
Quality assurance (QA) is integral to the manufacturing of the GMC Sierra 1500 Custom. It ensures that every vehicle produced meets both international standards and customer expectations.
What International Standards Govern Quality Assurance?
Several international standards guide quality assurance in automotive manufacturing, including ISO 9001, which focuses on quality management systems. Compliance with ISO standards helps manufacturers maintain a consistent level of quality and safety across their production processes. Additionally, industry-specific certifications like CE and API are crucial for compliance, especially for vehicles intended for the European market.
What Are the Key Quality Control Checkpoints?
Quality control (QC) checkpoints are critical throughout the manufacturing process. These typically include:
- Incoming Quality Control (IQC): This involves inspecting raw materials upon arrival to ensure they meet specified quality standards.
- In-Process Quality Control (IPQC): Conducted during the manufacturing process, IPQC checks are vital for identifying defects early and preventing them from progressing to the next stage.
- Final Quality Control (FQC): This final inspection occurs after assembly and before the vehicle leaves the factory. It includes comprehensive testing of all systems and components.
What Testing Methods Are Commonly Used in the GMC Sierra 1500 Quality Assurance Process?
Quality assurance testing methods are crucial for ensuring that the GMC Sierra 1500 meets performance and safety standards. Common testing methods include:
- Durability Testing: This involves subjecting the vehicle to extreme conditions to assess its performance under stress.
- Crash Testing: Conducted to evaluate the safety features of the vehicle, ensuring compliance with safety regulations.
- Emissions Testing: This ensures that the vehicle meets environmental standards, particularly important for markets in Europe and North America.
How Can B2B Buyers Verify Supplier Quality Control?
For international B2B buyers, verifying the quality control processes of suppliers is essential for ensuring product reliability. Here are several strategies to consider:
- Supplier Audits: Conducting regular audits of suppliers can provide insights into their manufacturing processes and quality assurance measures. This can include reviewing their adherence to international standards and internal quality protocols.
- Quality Reports: Requesting detailed quality reports from suppliers can help assess their performance over time. These reports should include data on defect rates, compliance with standards, and results from testing.
- Third-Party Inspections: Engaging third-party inspection services can offer an unbiased evaluation of a supplier’s manufacturing and quality control processes. This is particularly important for buyers in regions like Africa and South America, where local regulations may differ.
What Are the Quality Control and Certification Nuances for International B2B Buyers?
Navigating the nuances of quality control and certification is essential for international B2B buyers, particularly those from diverse regions like Africa, South America, the Middle East, and Europe. Understanding local regulations and standards is crucial to ensure compliance. For instance, different countries may have varying safety and emissions standards that a vehicle must meet before it can be sold in those markets.
Furthermore, recognizing the importance of certifications such as ISO, CE, and others can help buyers make informed decisions when selecting suppliers. Engaging with suppliers who have robust QA processes and certifications can significantly reduce risks associated with product quality and compliance.
Conclusion
In-depth knowledge of the manufacturing processes and quality assurance measures for the GMC Sierra 1500 Custom is vital for international B2B buyers. By understanding each stage of production and the associated quality control processes, buyers can make informed decisions when selecting suppliers, ensuring they meet the necessary standards for performance, safety, and environmental compliance.
Practical Sourcing Guide: A Step-by-Step Checklist for ‘gmc sierra 1500 custom’
To successfully procure a GMC Sierra 1500 Custom, especially in the context of international B2B transactions, it is essential to follow a structured approach. This checklist will guide you through the critical steps necessary to ensure a smooth sourcing process.
Step 1: Define Your Technical Specifications
Clearly outline the specific requirements for the GMC Sierra 1500 Custom you intend to procure. This includes details such as engine type, towing capacity, custom features, and desired accessories. Defining these specifications helps streamline the sourcing process and ensures that suppliers can meet your exact needs.
- Consider regional regulations: Ensure that the specifications comply with the automotive regulations in your target market.
- Account for customization needs: Be explicit about any customizations to avoid misunderstandings later.
Step 2: Research Potential Suppliers
Conduct thorough research to identify reputable suppliers who specialize in the GMC Sierra 1500 Custom. Utilize online platforms, automotive forums, and trade directories to compile a list of potential vendors.
- Look for established suppliers: Focus on companies with a proven track record and positive customer reviews.
- Assess their industry experience: Suppliers with experience in your region or sector may better understand your specific requirements.
Step 3: Evaluate Supplier Certifications
Verify that potential suppliers hold relevant certifications and licenses. This is crucial for ensuring compliance with industry standards and regulations.
- Check for ISO certifications: These can indicate a commitment to quality and continuous improvement.
- Confirm local compliance: Ensure that the supplier adheres to the automotive regulations specific to your region.
Step 4: Request and Review Quotes
Once you have shortlisted suppliers, request detailed quotes for the GMC Sierra 1500 Custom. A well-structured quote should include pricing, delivery times, payment terms, and warranty information.
- Compare multiple quotes: This will help you gauge the market rate and identify the best value.
- Look beyond price: Consider the total cost of ownership, including potential maintenance and after-sales service.
Step 5: Conduct Site Visits or Virtual Inspections
If feasible, arrange site visits to the supplier’s facility or conduct virtual inspections to assess their production capabilities and quality control processes.
- Observe production practices: Ensure that the supplier follows industry best practices in manufacturing and quality assurance.
- Meet key personnel: Building relationships with the supplier’s team can enhance collaboration and communication.
Step 6: Negotiate Terms and Conditions
Before finalizing the deal, engage in negotiations to establish favorable terms and conditions that protect your interests.
- Discuss payment terms: Ensure that the payment structure aligns with your cash flow needs.
- Clarify delivery schedules: Agree on realistic timelines that accommodate any potential delays.
Step 7: Finalize the Agreement
Once negotiations are complete, draft a comprehensive contract that outlines all agreed-upon terms, including specifications, pricing, delivery, and warranties.
- Include a dispute resolution clause: This can help mitigate risks and provide a clear process for addressing potential issues.
- Ensure legal compliance: Consult with legal experts to ensure that the agreement adheres to local and international laws.
By following these steps, international B2B buyers can effectively navigate the complexities of procuring a GMC Sierra 1500 Custom, ensuring a successful transaction that meets their specific requirements.
Comprehensive Cost and Pricing Analysis for gmc sierra 1500 custom Sourcing
What Are the Key Cost Components in Sourcing a GMC Sierra 1500 Custom?
When sourcing a GMC Sierra 1500 Custom, understanding the cost structure is critical for international B2B buyers. The primary cost components include:
-
Materials: The choice of materials significantly impacts the overall cost. High-quality steel, aluminum, and specialized components for customization can increase expenses. Buyers should evaluate local suppliers to reduce costs related to material procurement.
-
Labor: Labor costs vary by region. For instance, labor in South America may be less expensive than in Europe, but it’s essential to consider skill levels and labor regulations. Skilled labor for customization can drive up costs.
-
Manufacturing Overhead: This encompasses all costs not directly tied to production, such as utilities, rent, and administrative expenses. Understanding the manufacturing environment in the supplier’s country can help buyers assess the overhead costs.
-
Tooling: Custom projects often require specialized tooling, which can be a significant upfront investment. Buyers should inquire about tooling costs and how they are amortized over production volumes.
-
Quality Control (QC): Ensuring the GMC Sierra meets international standards necessitates robust QC processes. Buyers should factor in QC costs to avoid potential issues related to compliance and warranty claims.
-
Logistics: Transportation costs can fluctuate based on the distance between the supplier and the buyer’s location, as well as the chosen shipping method. Understanding Incoterms is crucial in determining who bears these costs.
-
Margin: Suppliers will include a margin on top of their costs. This margin can vary based on market competition and the perceived value of the customizations offered.
How Do Price Influencers Affect the Sourcing of GMC Sierra 1500 Custom?
Several factors influence the pricing of a GMC Sierra 1500 Custom:
-
Volume/MOQ (Minimum Order Quantity): Higher order volumes often lead to lower per-unit costs due to economies of scale. International buyers should consider combining orders with other businesses to meet MOQ requirements.
-
Specifications and Customization: Custom features increase complexity and costs. Buyers should clearly define specifications to avoid scope creep, which can lead to unexpected expenses.
-
Materials and Quality Certifications: The choice of materials not only affects cost but also quality. Certifications like ISO can add to the price but are essential for ensuring compliance with international standards.
-
Supplier Factors: The supplier’s reputation, experience, and location play a significant role in pricing. Established suppliers may charge a premium, but they often provide higher reliability and quality assurance.
-
Incoterms: Understanding terms like FOB (Free on Board) or CIF (Cost, Insurance, and Freight) can help buyers clarify who is responsible for various costs, affecting the overall pricing.
What Are the Best Buyer Tips for Sourcing GMC Sierra 1500 Custom?
International B2B buyers should consider several strategies to maximize cost efficiency:
-
Negotiation Strategies: Engaging in open discussions about pricing can lead to favorable terms. Don’t hesitate to negotiate based on volume, long-term contracts, or bundled services.
-
Total Cost of Ownership (TCO): Evaluate not only the purchase price but also maintenance, operational costs, and potential resale value. A lower initial price may lead to higher TCO if quality is compromised.
-
Understanding Pricing Nuances: Different regions have varying pricing structures due to local economies, labor costs, and material availability. Buyers from Africa, South America, the Middle East, and Europe should conduct market research to understand these nuances.
-
Seek Multiple Quotes: Obtain quotes from various suppliers to compare costs and services. This can help identify competitive pricing and ensure that you are not overpaying.
Conclusion
While sourcing a GMC Sierra 1500 Custom, international B2B buyers must navigate a complex landscape of costs and pricing influences. By understanding the cost components, price influencers, and employing strategic buyer tips, businesses can make informed decisions that align with their budgetary constraints and quality expectations. Always remember that indicative prices can vary significantly, so thorough research and due diligence are essential.
Alternatives Analysis: Comparing gmc sierra 1500 custom With Other Solutions
Understanding Alternatives for the GMC Sierra 1500 Custom
When considering the GMC Sierra 1500 Custom, it’s essential for international B2B buyers to explore alternative solutions that might better suit their operational needs. This comparison will focus on two viable alternatives: the Ford F-150 and the Ram 1500. Each of these trucks offers unique features and specifications that can meet different business requirements, particularly in diverse markets such as Africa, South America, the Middle East, and Europe.
Comparison Table of GMC Sierra 1500 Custom and Alternatives
Comparison Aspect | GMC Sierra 1500 Custom | Ford F-150 | Ram 1500 |
---|---|---|---|
Performance | 355 hp, V8 engine | Up to 450 hp, EcoBoost | 395 hp, V8 engine |
Cost | Starting at $36,000 | Starting at $34,000 | Starting at $32,000 |
Ease of Implementation | Moderate | Easy with extensive support | Moderate |
Maintenance | Average cost | Average cost | Slightly higher cost |
Best Use Case | Versatile, daily use | Heavy-duty, off-road | Luxury, comfort-oriented |
In-Depth Analysis of Alternatives
Ford F-150: What Are Its Strengths and Weaknesses?
The Ford F-150 is renowned for its robust performance and is often regarded as one of the best-selling trucks in the U.S. market. It offers a powerful EcoBoost engine option that provides exceptional towing capacity, making it ideal for businesses that require heavy hauling capabilities. The F-150’s extensive dealer network ensures easy access to parts and service, facilitating smoother operations. However, buyers should consider the slightly higher initial cost compared to the Sierra 1500 and the potential for higher fuel consumption in heavier configurations.
Ram 1500: How Does It Stand Out?
The Ram 1500 is often praised for its luxurious interior and smooth ride quality, setting it apart from competitors. It features advanced technology options, including an impressive infotainment system that enhances driver comfort and connectivity. This model is particularly suited for businesses that prioritize employee comfort during long hauls. However, the Ram 1500 may come with higher maintenance costs, and its performance may not match the heavy-duty capabilities of the GMC Sierra 1500 or Ford F-150 in certain scenarios.
Making the Right Choice: What Should Buyers Consider?
For international B2B buyers, selecting the right truck involves understanding both the operational needs and the specific market conditions they operate within. The GMC Sierra 1500 Custom offers a well-rounded option for various tasks, but alternatives like the Ford F-150 and Ram 1500 can provide unique advantages depending on the buyer’s priorities—be it performance, comfort, or cost efficiency. It’s crucial to evaluate factors such as load capacity, dealer support, and maintenance costs when making a decision. Ultimately, the best choice will align with the specific requirements and challenges faced by the business in its respective market.
Essential Technical Properties and Trade Terminology for gmc sierra 1500 custom
What are the Essential Technical Properties of the GMC Sierra 1500 Custom?
When considering the GMC Sierra 1500 Custom for international procurement, understanding its technical specifications is crucial. Here are some key properties that are often evaluated:
-
Towing Capacity
The GMC Sierra 1500 Custom boasts a towing capacity that can reach up to 12,200 pounds, depending on the engine choice. This property is vital for businesses that require transportation of heavy equipment or goods. A higher towing capacity translates to improved logistics and operational efficiency. -
Payload Capacity
With a payload capacity of approximately 2,200 pounds, this vehicle is designed to handle substantial loads. For B2B buyers, this means reduced trips and lower transportation costs, which is essential for businesses aiming to maximize productivity. -
Engine Options and Performance
The Sierra 1500 offers multiple engine configurations, including a 2.7L turbocharged four-cylinder and a 5.3L V8. Each engine option provides different performance metrics like horsepower and fuel efficiency. B2B buyers should assess which engine aligns with their operational needs, balancing power requirements with fuel economy. -
Material Composition
The truck’s body is constructed using high-strength steel and aluminum, enhancing durability while reducing weight. Understanding material grades is crucial for procurement specialists looking to ensure longevity and lower maintenance costs in their fleet. -
Safety Ratings
The Sierra 1500 is equipped with advanced safety features, earning high ratings from safety organizations. For businesses, investing in vehicles with superior safety ratings can lead to reduced insurance costs and lower liability risks.
What Trade Terms Should B2B Buyers Know When Purchasing the GMC Sierra 1500 Custom?
In addition to technical specifications, familiarizing yourself with industry terminology can streamline the purchasing process. Here are some common trade terms:
-
OEM (Original Equipment Manufacturer)
OEM refers to the original manufacturer of the vehicle parts. For B2B buyers, understanding OEM parts is crucial for ensuring compatibility and quality in replacements or repairs, which can affect the overall operational efficiency of the fleet. -
MOQ (Minimum Order Quantity)
This term indicates the smallest quantity of a product that a supplier is willing to sell. Knowing the MOQ is essential for budgeting and inventory management, particularly for companies looking to acquire multiple units of the GMC Sierra 1500 Custom. -
RFQ (Request for Quotation)
An RFQ is a document sent to suppliers requesting pricing information for specific products. For international buyers, utilizing an RFQ can help in comparing prices and securing the best deal, which is vital in competitive markets. -
Incoterms (International Commercial Terms)
These are standardized shipping terms that define the responsibilities of buyers and sellers. Familiarity with Incoterms helps businesses understand who is liable for transportation costs and risks, which can significantly impact the total cost of ownership. -
Lead Time
Lead time refers to the time taken from placing an order to delivery. Understanding lead times is essential for procurement planning, especially in industries where time-sensitive deliveries are crucial. -
Warranty Period
The warranty period defines the time frame during which the manufacturer will cover repairs or replacements. For B2B buyers, a robust warranty can mitigate risks and reduce long-term maintenance costs.
By comprehending these technical properties and trade terms, international B2B buyers can make informed decisions when acquiring the GMC Sierra 1500 Custom, ensuring that their investments align with their operational requirements and strategic goals.
Navigating Market Dynamics and Sourcing Trends in the gmc sierra 1500 custom Sector
What Are the Key Market Dynamics Affecting the GMC Sierra 1500 Custom Sector?
The GMC Sierra 1500 Custom sector is influenced by several global drivers that shape market dynamics for international B2B buyers. Increasing demand for pickup trucks, particularly in emerging markets in Africa and South America, is a significant trend. These regions are witnessing a surge in urbanization and infrastructure development, leading to a higher demand for versatile vehicles like the Sierra 1500. Moreover, the rise of e-commerce and logistics services is propelling the need for durable and reliable transportation options.
B2B tech trends are also transforming sourcing strategies. The integration of advanced technologies such as IoT and AI in vehicle manufacturing is enhancing operational efficiencies and product quality. Buyers are increasingly looking for suppliers who adopt these innovations, as they lead to improved supply chain visibility and reduced lead times. Furthermore, the ongoing shift towards digital procurement platforms allows international buyers to streamline their sourcing processes, compare suppliers more effectively, and make data-driven decisions.
In Europe, sustainability regulations are becoming more stringent, which affects sourcing dynamics. Buyers must consider suppliers’ compliance with environmental standards and certifications, as these factors can impact market access and brand reputation. The competition among manufacturers is intensifying, and those who can demonstrate a commitment to innovation and sustainability will have a distinct advantage in the market.
How Is Sustainability Shaping Sourcing in the GMC Sierra 1500 Custom Market?
Sustainability is a critical consideration for B2B buyers in the GMC Sierra 1500 Custom market. The environmental impact of vehicle manufacturing is under scrutiny, prompting companies to adopt more sustainable practices. This includes sourcing materials that are environmentally friendly and ensuring that production processes minimize waste and emissions.
Ethical sourcing is becoming increasingly important, as consumers and businesses alike are prioritizing companies that demonstrate social responsibility. Buyers should look for suppliers who can provide transparency in their supply chains, showcasing their commitment to ethical labor practices and environmental stewardship. Certifications such as ISO 14001 for environmental management systems or certifications from organizations like the Forest Stewardship Council (FSC) can provide assurance that suppliers adhere to recognized sustainability standards.
Incorporating ‘green’ materials into the GMC Sierra 1500 Custom, such as recycled metals and sustainably sourced plastics, is not only beneficial for the environment but can also enhance brand reputation. Buyers should engage with suppliers who prioritize these materials in their offerings, as this aligns with the growing demand for sustainable products in global markets.
What Is the Historical Context of the GMC Sierra 1500 Custom’s Development?
The GMC Sierra 1500 Custom has evolved significantly since its introduction, adapting to changing consumer preferences and market demands. Originally launched as a workhorse truck in the mid-1990s, it has transformed into a versatile vehicle that combines utility with luxury features. This evolution reflects broader trends in the automotive industry, where consumer expectations have shifted towards multifunctional vehicles that cater to both work and leisure.
The introduction of custom options has allowed buyers to tailor the Sierra 1500 to their specific needs, enhancing its appeal in various markets. This flexibility has been particularly advantageous for international B2B buyers who require vehicles that can serve multiple purposes, from transporting goods to accommodating business needs. As the market continues to evolve, ongoing innovation in design, technology, and sustainability will shape the future of the GMC Sierra 1500 Custom, making it a compelling choice for B2B buyers across diverse regions.
Frequently Asked Questions (FAQs) for B2B Buyers of gmc sierra 1500 custom
-
How can I evaluate the reliability of a GMC Sierra 1500 custom supplier?
To assess the reliability of a GMC Sierra 1500 custom supplier, begin by reviewing their certifications and industry experience. Look for suppliers with a proven track record in exporting vehicles to your region. Request references from previous clients and check online reviews or forums to gauge their reputation. Additionally, consider visiting the supplier’s facility if possible, as this will give you firsthand insight into their operations and quality control processes. -
What are the key customization options available for the GMC Sierra 1500?
The GMC Sierra 1500 offers a wide range of customization options, including engine types, trim levels, and interior features. Buyers can choose from various bed lengths, cab configurations, and towing packages. Furthermore, options for advanced technology packages, safety features, and exterior finishes allow businesses to tailor the vehicle to their specific needs. Engaging directly with suppliers about your requirements can help clarify available options and any associated costs. -
What is the typical Minimum Order Quantity (MOQ) for GMC Sierra 1500 custom vehicles?
The Minimum Order Quantity (MOQ) for GMC Sierra 1500 custom vehicles can vary significantly depending on the supplier and customization level. Generally, it ranges from one vehicle for smaller suppliers to ten or more for larger manufacturers. Always inquire with potential suppliers about their specific MOQ policies, as negotiating terms may be possible, especially if you are planning future orders.
-
What payment terms should I expect when purchasing GMC Sierra 1500 custom vehicles?
Payment terms for purchasing GMC Sierra 1500 custom vehicles typically involve a deposit followed by the balance paid upon delivery. Standard practices may include a 20-30% upfront payment with the remaining balance due before shipment. Some suppliers may offer financing options or letter of credit arrangements. Always clarify payment terms upfront to avoid misunderstandings and ensure your budget aligns with supplier requirements. -
How can I ensure quality assurance for my GMC Sierra 1500 custom order?
To ensure quality assurance for your GMC Sierra 1500 custom order, it’s crucial to establish clear specifications and expectations with your supplier from the outset. Request detailed documentation, including build sheets and quality control checklists, to confirm that the vehicle meets your requirements. Additionally, consider arranging for third-party inspections during manufacturing and before shipment to verify compliance with quality standards. -
What logistics considerations should I keep in mind when importing GMC Sierra 1500 vehicles?
When importing GMC Sierra 1500 vehicles, logistics considerations include shipping methods, customs clearance, and delivery timelines. Determine whether you will use air or sea freight based on your budget and urgency. Familiarize yourself with the customs regulations and tariffs in your country to avoid delays. Working with a logistics partner who has experience in automotive imports can streamline the process and mitigate potential issues.
-
What are the potential challenges when sourcing GMC Sierra 1500 custom from international suppliers?
Sourcing GMC Sierra 1500 custom from international suppliers may present challenges such as language barriers, cultural differences, and differing business practices. Additionally, ensuring compliance with your local regulations and understanding import duties can complicate the process. To mitigate these challenges, thorough research and establishing strong communication channels with suppliers are essential. Engaging a local intermediary familiar with the market can also provide valuable insights. -
How does warranty and after-sales support work for international buyers of GMC Sierra 1500?
Warranty and after-sales support for international buyers of GMC Sierra 1500 vehicles can vary by supplier. Typically, manufacturers offer a limited warranty covering defects and repairs for a specified period or mileage. However, international buyers should confirm whether warranty services are available locally or if they need to return the vehicle to the supplier. It’s advisable to discuss after-sales support options, including parts availability and service agreements, to ensure you have access to necessary support post-purchase.
Important Disclaimer & Terms of Use
⚠️ Important Disclaimer
The information provided in this guide, including content regarding manufacturers, technical specifications, and market analysis, is for informational and educational purposes only. It does not constitute professional procurement advice, financial advice, or legal advice.
While we have made every effort to ensure the accuracy and timeliness of the information, we are not responsible for any errors, omissions, or outdated information. Market conditions, company details, and technical standards are subject to change.
B2B buyers must conduct their own independent and thorough due diligence before making any purchasing decisions. This includes contacting suppliers directly, verifying certifications, requesting samples, and seeking professional consultation. The risk of relying on any information in this guide is borne solely by the reader.
Strategic Sourcing Conclusion and Outlook for gmc sierra 1500 custom
In the dynamic landscape of international B2B sourcing, the GMC Sierra 1500 Custom stands out as a versatile option for businesses seeking reliability and performance. Key takeaways for buyers include the importance of aligning sourcing strategies with the specific needs of their operations. By leveraging the Sierra’s customization capabilities, businesses can enhance their fleet’s functionality, ensuring that they are well-equipped to meet diverse demands across various industries.
Strategic sourcing is not merely about cost savings; it is about creating long-term value through partnerships with trusted suppliers. For international buyers, particularly from Africa, South America, the Middle East, and Europe, understanding local market conditions and regulatory frameworks is essential. This knowledge enables buyers to negotiate better terms and optimize their supply chains effectively.
Looking ahead, the demand for customizable, durable vehicles like the GMC Sierra 1500 is expected to rise. By proactively engaging with manufacturers and exploring innovative financing options, international B2B buyers can position themselves advantageously in a competitive marketplace. Now is the time to take action—invest in strategic sourcing and ensure your business is ready to capitalize on the opportunities that lie ahead.