Save Costs with PCB Manufacturing: The Ultimate Guide China (2025)
Introduction: Navigating the Global Market for pcb manufacturing china
In today’s interconnected world, sourcing high-quality printed circuit boards (PCBs) from China presents a significant opportunity for international B2B buyers looking to enhance their product offerings. However, navigating the complexities of PCB manufacturing in China can be daunting, especially for companies in Africa, South America, the Middle East, and Europe, including key markets like Germany and Spain. With varying standards, supplier reliability, and evolving market dynamics, making informed purchasing decisions is essential to avoid costly pitfalls.
This comprehensive guide delves into the intricate landscape of PCB manufacturing in China, exploring various types of PCBs and their applications across industries. We will provide actionable insights on how to effectively vet suppliers, understand cost structures, and identify potential risks associated with international procurement. By addressing critical questions, such as “What should I consider when selecting a PCB manufacturer in China?” and “How can I assess the quality of PCBs from Chinese suppliers?”, this guide equips buyers with the knowledge needed to navigate the global market confidently.
As you embark on this journey, our aim is to empower you with the tools and information necessary to make strategic, informed decisions that align with your business goals. From understanding the nuances of production processes to establishing robust supply chain partnerships, this guide is your roadmap to successfully sourcing PCBs from China and leveraging their advantages for your business growth.
Understanding pcb manufacturing china Types and Variations
Type Name | Key Distinguishing Features | Primary B2B Applications | Brief Pros & Cons for Buyers |
---|---|---|---|
Rigid PCBs | Solid substrate, commonly made of FR-4 material | Consumer electronics, automotive | Pros: Cost-effective, reliable; Cons: Limited flexibility in design. |
Flexible PCBs | Thin, bendable, and lightweight | Wearable devices, medical equipment | Pros: High adaptability; Cons: Higher manufacturing costs. |
Rigid-Flex PCBs | Combination of rigid and flexible sections | Aerospace, military, high-end electronics | Pros: Space-saving, versatile; Cons: Complex manufacturing process. |
Multi-layer PCBs | More than two layers, complex circuitry | High-frequency devices, telecom | Pros: Compact design, enhanced performance; Cons: Longer lead times. |
High-Frequency PCBs | Designed for high-speed signals, specific materials | RF applications, satellite technology | Pros: Optimized for performance; Cons: Specialized materials increase costs. |
What are Rigid PCBs and Their Key Applications?
Rigid PCBs are the most common type of printed circuit boards, primarily made from materials like FR-4. They are characterized by their solid structure, making them ideal for applications where durability and reliability are essential. B2B buyers in sectors like consumer electronics and automotive will find rigid PCBs suitable due to their cost-effectiveness and proven performance. However, the limited design flexibility can be a drawback for innovative projects requiring intricate layouts.
How Do Flexible PCBs Meet Modern Design Needs?
Flexible PCBs are designed to be thin, lightweight, and bendable, making them perfect for applications in wearable technology and medical devices. Their adaptability allows them to fit into unconventional shapes and spaces, which is increasingly important in modern device design. While they offer significant advantages in terms of flexibility, B2B buyers should consider the higher manufacturing costs associated with flexible PCBs, especially for large-scale production.
What Advantages Do Rigid-Flex PCBs Offer?
Rigid-flex PCBs combine the benefits of both rigid and flexible PCBs, allowing for innovative designs that save space and weight. These boards are particularly valuable in industries like aerospace and military, where performance and compactness are critical. However, the complexity of their manufacturing process can lead to increased costs and longer lead times, which B2B buyers should factor into their procurement strategies.
Why Choose Multi-layer PCBs for Complex Applications?
Multi-layer PCBs feature more than two layers of circuitry, enabling complex designs that are crucial for high-frequency devices and telecommunications. They allow for compact and efficient layouts, making them ideal for applications where space is at a premium. However, the increased complexity can lead to longer lead times, which is an essential consideration for B2B buyers needing timely delivery for production schedules.
What are the Specific Needs for High-Frequency PCBs?
High-frequency PCBs are engineered to handle high-speed signals, utilizing specialized materials to minimize signal loss and distortion. They are essential in RF applications and satellite technology, where performance is paramount. While these boards offer optimized functionality, the use of specialized materials can significantly raise costs. B2B buyers must weigh the benefits of enhanced performance against the potential budget implications when considering high-frequency PCBs for their projects.
Related Video: PCB Manufacture and PCB Assembly inside PCB Factory China – PCBWay
Key Industrial Applications of pcb manufacturing china
Industry/Sector | Specific Application of PCB Manufacturing China | Value/Benefit for the Business | Key Sourcing Considerations for this Application |
---|---|---|---|
Electronics | Consumer Electronics (Smartphones, Tablets) | High-volume production with cost efficiency | Quality certifications, lead times, and minimum order quantities |
Automotive | Advanced Driver-Assistance Systems (ADAS) | Enhanced safety features and improved reliability | Compliance with automotive standards and testing protocols |
Medical Devices | Diagnostic Equipment (MRI, Ultrasound) | Precision and reliability in critical applications | Regulatory compliance (ISO, CE marking) and material sourcing |
Telecommunications | Network Infrastructure (5G Equipment) | Scalability and performance optimization | Customization options and technical support availability |
Industrial Automation | Control Systems for Manufacturing Equipment | Increased efficiency and reduced downtime | Long-term partnerships and after-sales service support |
How is PCB Manufacturing China Used in Consumer Electronics?
In the consumer electronics sector, PCB manufacturing in China plays a pivotal role in the production of devices like smartphones and tablets. Manufacturers benefit from China’s advanced technology and high-volume production capabilities, allowing them to meet global demand efficiently. International buyers, particularly from Europe and Africa, should prioritize suppliers with strong quality assurance processes to ensure product reliability and compliance with international standards.
What Are the Applications of PCB Manufacturing in Automotive?
In the automotive industry, PCBs are crucial for advanced driver-assistance systems (ADAS). These systems enhance vehicle safety through features like lane-keeping assistance and collision detection. B2B buyers from South America and the Middle East should focus on sourcing PCBs that meet stringent automotive standards and testing protocols, as reliability is paramount in this sector. Ensuring that manufacturers have experience in automotive applications can significantly mitigate risks.
How Does PCB Manufacturing Impact Medical Devices?
PCB manufacturing in China is essential for medical devices, particularly diagnostic equipment such as MRI and ultrasound machines. The precision required in these devices means that manufacturers must adhere to strict regulatory compliance, including ISO and CE marking. International buyers, especially from Europe, must ensure that their suppliers have a proven track record in medical applications, as the stakes are high when it comes to patient safety and device efficacy.
What Are the Key Uses of PCB Manufacturing in Telecommunications?
In the telecommunications sector, PCBs are integral to the infrastructure that supports 5G technology. The need for high-performance and scalable solutions drives demand for PCBs that can handle increased data loads. Buyers from Africa and the Middle East should consider suppliers that offer customization options and robust technical support, as these factors can significantly impact the performance and longevity of telecommunications equipment.
How is PCB Manufacturing Used in Industrial Automation?
Industrial automation relies heavily on PCBs for control systems in manufacturing equipment. These PCBs help improve operational efficiency and reduce downtime, which is critical for businesses looking to optimize productivity. B2B buyers should seek long-term partnerships with PCB manufacturers who can provide comprehensive after-sales service support and are capable of adapting to evolving technology trends in automation.
Related Video: How PCB is Made in China – PCBWay – Factory Tour
3 Common User Pain Points for ‘pcb manufacturing china’ & Their Solutions
Scenario 1: Navigating Quality Assurance Challenges in PCB Manufacturing
The Problem: One of the primary concerns for B2B buyers sourcing PCBs from China is the inconsistency in quality. Many international buyers have encountered subpar products that don’t meet their specifications or industry standards. This inconsistency can lead to significant delays in production schedules, increased costs due to rework, and ultimately, damage to their brand reputation. Buyers often feel overwhelmed by the lack of reliable quality assurance processes and fear that their suppliers may not adhere to the same rigorous standards expected in their own markets, particularly in highly regulated regions like Europe.
The Solution: To effectively navigate quality assurance challenges, B2B buyers should implement a robust vendor qualification process. This includes conducting thorough due diligence on potential suppliers, which should involve reviewing their certifications (such as ISO 9001), quality control processes, and past performance records. Additionally, establishing clear and detailed specifications upfront is crucial. Buyers should use quality management tools like the Failure Mode and Effects Analysis (FMEA) to identify potential risks in the manufacturing process and set up regular audits or third-party inspections to monitor compliance. Finally, forming a collaborative relationship with the supplier can foster open communication, allowing for immediate feedback and adjustments to be made during the production process.
Scenario 2: Overcoming Communication Barriers in International Procurement
The Problem: Language and cultural differences can significantly impede effective communication between B2B buyers and Chinese PCB manufacturers. Misunderstandings can arise regarding product specifications, timelines, and pricing, often leading to costly mistakes and frustration. Buyers from Africa, South America, and Europe may find it difficult to articulate their requirements or gauge the manufacturer’s capabilities, which can result in delays and compromised product quality.
The Solution: To overcome communication barriers, B2B buyers should consider employing a local intermediary or sourcing agent who understands both the Chinese manufacturing landscape and the buyer’s local market. This agent can facilitate clearer communication, ensuring that both parties have a mutual understanding of expectations and deliverables. Furthermore, investing in a comprehensive project management tool that includes visual aids, such as diagrams and prototypes, can help bridge the gap in understanding. Using simple language and avoiding jargon in emails and documentation can also enhance clarity. Finally, regular video conferences can provide a platform for real-time discussions, allowing for immediate clarification of any issues that arise.
Scenario 3: Managing Lead Time and Supply Chain Delays
The Problem: International B2B buyers often face significant lead time challenges when sourcing PCBs from China. The complexities of global supply chains, compounded by factors like logistics delays, customs clearance, and geopolitical tensions, can lead to unexpected disruptions. Buyers may find themselves in situations where they cannot meet their production schedules, resulting in lost revenue and strained customer relationships.
The Solution: To effectively manage lead times and minimize supply chain disruptions, B2B buyers should adopt a proactive supply chain management strategy. This includes building strong relationships with multiple suppliers to diversify risk and ensure flexibility. Implementing Just-In-Time (JIT) inventory practices can help align production schedules with actual demand, reducing the pressure on supply chains. Buyers should also stay informed about global shipping trends and potential disruptions by subscribing to logistics and supply chain updates. Lastly, establishing buffer stock for critical components can provide a safety net, allowing for continued production even in the face of unforeseen delays. By planning ahead and maintaining open lines of communication with suppliers regarding any changes in lead time, buyers can better navigate the complexities of PCB manufacturing in China.
Strategic Material Selection Guide for pcb manufacturing china
In the realm of PCB manufacturing in China, the choice of materials is crucial for ensuring product performance and meeting specific application requirements. Here, we analyze several common materials used in PCB production, focusing on their properties, advantages, disadvantages, and considerations for international B2B buyers, particularly from Africa, South America, the Middle East, and Europe.
What Are the Key Properties of FR-4 in PCB Manufacturing?
FR-4 is one of the most widely used materials in PCB manufacturing. It is a composite of woven glass fabric and epoxy resin, providing excellent electrical insulation and mechanical strength.
- Key Properties: FR-4 exhibits a high glass transition temperature (Tg), typically around 130-180°C, making it suitable for applications requiring thermal stability. It also has good moisture resistance and low dielectric loss.
- Pros & Cons: The durability of FR-4 is notable, but it can be more expensive than other materials. Manufacturing complexity is moderate, and it is suitable for a wide range of applications, from consumer electronics to industrial devices. However, it is not ideal for high-frequency applications due to signal integrity issues.
- Impact on Application: FR-4 is compatible with various media, but it may not perform well in extreme environmental conditions.
- Considerations for International Buyers: Compliance with standards such as IPC-4101 and UL 94 is essential. Buyers from regions like Europe may also need to consider RoHS compliance.
How Does Polyimide Compare for High-Performance PCBs?
Polyimide is favored for applications requiring high thermal resistance and flexibility, making it suitable for flexible PCBs.
- Key Properties: Polyimide can withstand temperatures up to 300°C, which is beneficial for high-temperature applications. It also provides excellent chemical resistance and mechanical properties.
- Pros & Cons: The key advantage of polyimide is its thermal stability and flexibility, which is essential for applications like aerospace and automotive. However, it is generally more expensive and can complicate the manufacturing process due to its sensitivity to moisture.
- Impact on Application: Polyimide is highly compatible with aggressive media, making it ideal for harsh environments.
- Considerations for International Buyers: Buyers should ensure that polyimide materials meet international standards such as ASTM D-3039 for tensile properties and JIS C 6481 for flexible circuits.
What Are the Benefits of Using Aluminum PCBs?
Aluminum PCBs are increasingly popular due to their excellent thermal conductivity, making them suitable for LED applications.
- Key Properties: Aluminum PCBs can dissipate heat effectively, which is critical for maintaining the performance and longevity of electronic components.
- Pros & Cons: The primary advantage is their thermal management capability, which enhances product reliability. However, they can be more expensive to manufacture and may require specialized processes.
- Impact on Application: Aluminum PCBs are particularly effective in applications where heat dissipation is critical, such as in lighting and power electronics.
- Considerations for International Buyers: Compliance with thermal management standards and ensuring that the aluminum used meets specific alloy requirements is crucial for buyers, especially in regions with stringent regulations.
Why Consider CEM-1 for Cost-Effective Solutions?
CEM-1 is a cost-effective alternative to FR-4, often used in lower-end applications.
- Key Properties: CEM-1 consists of a paper-based substrate with a single layer of copper, offering decent electrical insulation and mechanical strength.
- Pros & Cons: The main advantage is its low cost, making it suitable for budget-sensitive projects. However, it has lower thermal and moisture resistance compared to FR-4 and is not suitable for high-frequency applications.
- Impact on Application: CEM-1 is best suited for simple applications where performance is not critical.
- Considerations for International Buyers: Buyers should be aware of the trade-offs in performance and ensure that the material meets basic compliance standards relevant to their region.
Summary Table of Materials for PCB Manufacturing in China
Material | Typical Use Case for pcb manufacturing china | Key Advantage | Key Disadvantage/Limitation | Relative Cost (Low/Med/High) |
---|---|---|---|---|
FR-4 | Consumer electronics, industrial devices | Excellent electrical insulation | Not suitable for high-frequency use | Medium |
Polyimide | Aerospace, automotive, flexible circuits | High thermal resistance | More expensive, complex to manufacture | High |
Aluminum | LED applications, power electronics | Superior thermal conductivity | Higher manufacturing costs | Medium to High |
CEM-1 | Budget-sensitive electronic products | Cost-effective | Lower thermal/moisture resistance | Low |
This strategic material selection guide provides essential insights for international B2B buyers looking to navigate the complexities of PCB manufacturing in China. By understanding the properties, advantages, and limitations of each material, buyers can make informed decisions that align with their specific application needs and compliance requirements.
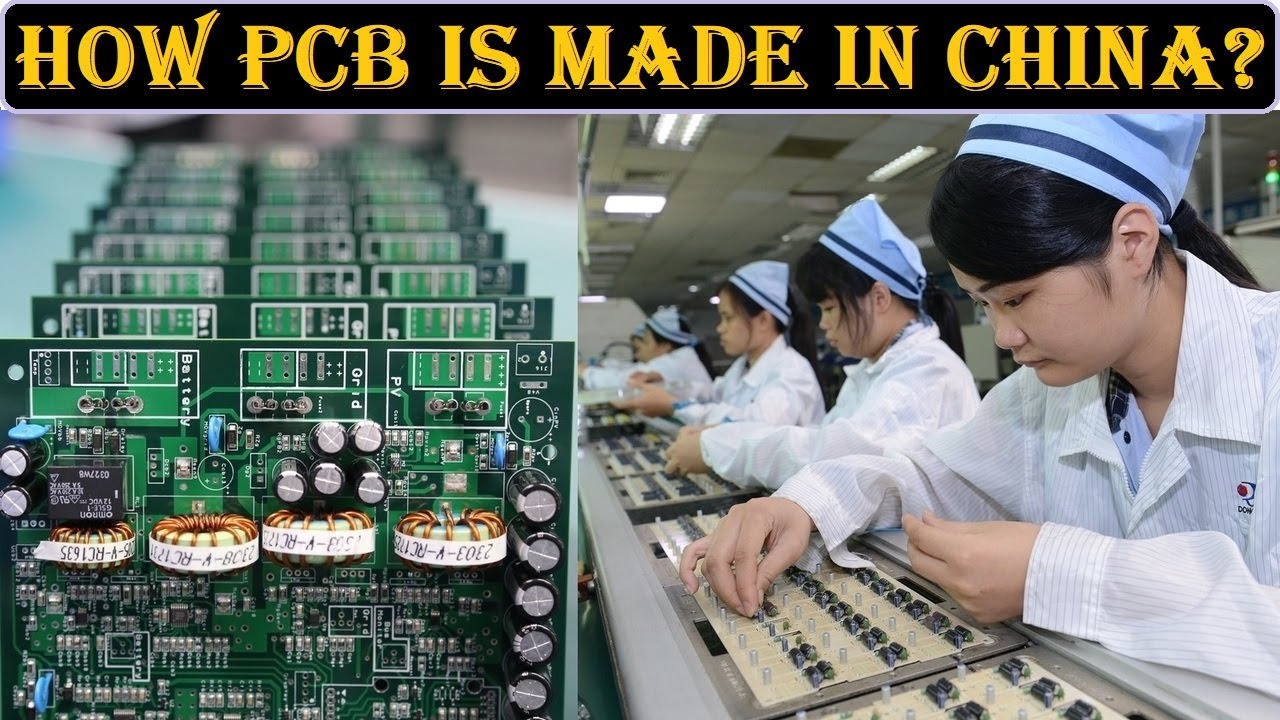
A stock image related to pcb manufacturing china.
In-depth Look: Manufacturing Processes and Quality Assurance for pcb manufacturing china
What Are the Main Stages of PCB Manufacturing in China?
The manufacturing process for printed circuit boards (PCBs) in China is characterized by a series of well-defined stages, each critical to ensuring the final product meets stringent quality standards. Understanding these stages can help international B2B buyers make informed decisions when sourcing PCBs from Chinese manufacturers.
1. Material Preparation
The first stage involves the selection and preparation of raw materials. High-quality substrates, such as FR-4 or polyimide, are essential for durability and performance. Manufacturers typically ensure that materials are sourced from reputable suppliers who comply with international standards. This stage also includes the preparation of copper foils, laminates, and other components, which are essential for the board’s functionality.
2. Forming
In this stage, the prepared materials are processed to create the PCB layout. This involves several techniques, including:
- Photolithography: A process that transfers circuit patterns onto the substrate using light-sensitive chemicals.
- Etching: Removing unwanted copper to form the desired circuit pathways.
- Drilling: Creating holes for component placement and interconnections.
These techniques are critical as they directly affect the accuracy and reliability of the final product.
3. Assembly
Once the PCB is formed, the assembly stage begins. This involves placing electronic components onto the board, which can be done using several methods, such as:
- Surface Mount Technology (SMT): Components are mounted directly onto the surface of the PCB, allowing for higher density and smaller designs.
- Through-Hole Technology (THT): Components are inserted into pre-drilled holes and soldered from the opposite side.
The choice of assembly technique often depends on the specific requirements of the project, including size constraints and performance specifications.
4. Finishing
The final stage of PCB manufacturing is finishing, which includes several processes aimed at enhancing the board’s durability and performance. This can involve:
- Solder Mask Application: A protective layer that prevents oxidation and solder bridging.
- Surface Finish: Various finishes, such as HASL (Hot Air Solder Leveling) or ENIG (Electroless Nickel Immersion Gold), can be applied to improve solderability and protect the exposed copper.
These finishing touches are vital for ensuring that the PCB can withstand environmental stress and maintain optimal performance over time.
How Is Quality Assurance Implemented in PCB Manufacturing?
Quality assurance (QA) is a cornerstone of PCB manufacturing in China, ensuring that products meet both international and industry-specific standards. This process encompasses multiple checkpoints and testing methods that B2B buyers should be aware of.
International Standards: Which Ones Matter for PCB Quality?
Chinese PCB manufacturers often adhere to various international standards, which can provide assurance of quality. Key standards include:
- ISO 9001: A widely recognized quality management system standard that ensures consistent quality and continuous improvement.
- IPC Standards: These include IPC-A-600 for acceptability of printed boards and IPC-2221 for generic design standards.
Compliance with these standards indicates a commitment to maintaining high-quality manufacturing processes.
What Are the Key Quality Control Checkpoints?
Quality control (QC) in PCB manufacturing typically includes several checkpoints throughout the production process:
- Incoming Quality Control (IQC): This initial step involves inspecting raw materials and components upon arrival to ensure they meet specified standards.
- In-Process Quality Control (IPQC): During the manufacturing process, random samples are tested to identify any deviations from quality standards.
- Final Quality Control (FQC): The completed PCBs undergo rigorous testing to verify their functionality and reliability before shipping.
These checkpoints help to catch potential issues early and ensure that only high-quality products reach the customer.
What Common Testing Methods Are Used in PCB Quality Assurance?
Manufacturers employ various testing methods to ensure PCBs perform as expected. Some common testing techniques include:
- Electrical Testing: Verifying the electrical integrity of the PCB through methods like Automated Optical Inspection (AOI) and flying probe testing.
- Thermal Cycling: Subjecting PCBs to extreme temperature variations to assess their durability and performance under stress.
- X-Ray Inspection: Used for inspecting solder joints and hidden components, ensuring that every part of the assembly meets quality standards.
Understanding these testing methods can help international buyers gauge the reliability of their suppliers’ quality assurance processes.
How Can B2B Buyers Verify Supplier Quality Control?
When sourcing PCBs from China, B2B buyers must adopt strategies to verify the quality control measures of potential suppliers. Here are several actionable steps:
- Conduct Audits: Regular audits of manufacturing facilities can provide insights into the operational processes and adherence to quality standards.
- Request Quality Reports: Ask suppliers for their quality control documentation, including test results and certifications. This transparency can help build trust.
- Engage Third-Party Inspectors: Hiring independent inspection services can offer an unbiased assessment of the manufacturing processes and final products.
What Are the Quality Certification Nuances for International B2B Buyers?
For B2B buyers from Africa, South America, the Middle East, and Europe, understanding the nuances of quality certification is essential. Buyers should be aware that:
- Regional Differences: Some certifications may hold more weight in specific regions. For example, CE marking is crucial for products sold in the European Union.
- Local Regulations: Familiarize yourself with local regulations that may apply to PCBs in your region, as compliance can affect product acceptance and marketability.
By being proactive in these areas, international buyers can better ensure that their PCB sourcing decisions align with their quality expectations and regulatory requirements.
Practical Sourcing Guide: A Step-by-Step Checklist for ‘pcb manufacturing china’
Introduction
Navigating the complexities of PCB manufacturing in China can be daunting for international B2B buyers, particularly those from Africa, South America, the Middle East, and Europe. This step-by-step checklist is designed to streamline your sourcing process, ensuring you make informed decisions that align with your technical requirements and business goals.
1. Define Your Technical Specifications
Before initiating contact with suppliers, clearly outline your technical specifications. This includes details such as the type of PCB (single-sided, double-sided, or multilayer), materials (FR-4, aluminum, etc.), layer count, and any specific performance requirements. A well-defined specification helps prevent misunderstandings and ensures that suppliers can meet your needs effectively.
2. Research and Shortlist Potential Suppliers
Conduct thorough research to identify potential PCB manufacturers in China. Utilize platforms like Alibaba, Global Sources, and industry-specific directories. Look for suppliers with a solid reputation, positive reviews, and relevant experience in your specific industry. Shortlisting 3-5 suppliers will give you a manageable pool for further evaluation.
3. ✅ Verify Supplier Certifications
Ensure that your shortlisted suppliers possess the necessary certifications, such as ISO 9001 for quality management and IPC standards for PCB manufacturing. Certifications indicate that the supplier adheres to industry best practices and quality controls. Request copies of these certifications and check for their validity, as this can significantly mitigate risks associated with quality assurance.
4. Evaluate Supplier Capabilities and Experience
Assess the manufacturing capabilities and experience of each supplier. Inquire about their production capacity, lead times, and the technology they use. It’s also beneficial to ask for case studies or examples of previous work relevant to your industry. This evaluation will help you gauge whether the supplier can meet your volume and complexity requirements.
5. Request Samples for Testing
Once you have narrowed down your choices, request samples of PCBs that match your specifications. Testing these samples is crucial to ensure that the quality, performance, and durability meet your standards. Evaluate aspects such as solderability, thermal performance, and electrical integrity. This step acts as a critical quality control measure before placing a larger order.
6. Negotiate Terms and Pricing Transparently
Engage in transparent negotiations regarding pricing, payment terms, and delivery schedules. Be clear about your budget constraints and expectations for quality. Consider discussing bulk order discounts or long-term partnership agreements, as this can lead to more favorable terms. Always get everything in writing to avoid misunderstandings later.
7. Establish Communication Channels
Effective communication is key to a successful sourcing experience. Establish clear communication channels with your chosen supplier, including preferred methods (email, phone, video calls) and time zones. Regular updates on the production process and any issues that arise will help maintain a positive working relationship and ensure project timelines are met.
By following this checklist, international B2B buyers can enhance their sourcing strategy for PCB manufacturing in China, ultimately leading to better quality products and successful partnerships.
Comprehensive Cost and Pricing Analysis for pcb manufacturing china Sourcing
What Are the Key Cost Components in PCB Manufacturing Sourcing from China?
When sourcing PCB manufacturing from China, understanding the cost structure is vital for international B2B buyers. The primary cost components include:
-
Materials: The choice of raw materials significantly impacts the overall cost. High-quality laminates, copper foils, and solder masks can vary in price. Buyers should consider the specifications needed for their application, as this can lead to variations in material costs.
-
Labor: Labor costs in China are generally lower compared to many Western countries, but they can vary by region and skill level. Specialized labor for complex PCB designs or high-volume production may command higher wages.
-
Manufacturing Overhead: This encompasses costs related to utilities, facility maintenance, and equipment depreciation. Efficient manufacturing processes can help mitigate these expenses, but buyers should inquire about the supplier’s operational efficiencies.
-
Tooling: Initial tooling costs can be substantial, especially for custom designs. However, these costs are often amortized over larger production runs. Understanding the tooling requirements upfront is crucial for accurate pricing.
-
Quality Control (QC): Implementing stringent QC measures ensures product reliability but adds to the cost. Buyers should assess the supplier’s QC protocols and certifications to align with their quality expectations.
-
Logistics: Shipping costs can vary significantly based on the chosen Incoterms, shipping method, and destination. For buyers from Africa, South America, the Middle East, and Europe, understanding these logistics is crucial to avoid unexpected expenses.
-
Margin: Supplier margins can differ based on their reputation, capabilities, and market conditions. A well-established supplier may charge a premium, but they might also provide superior service and reliability.
How Do Price Influencers Impact PCB Manufacturing Costs?
Several factors influence the pricing of PCBs from Chinese manufacturers:
-
Volume and Minimum Order Quantity (MOQ): Larger orders often lead to lower per-unit costs. Understanding the supplier’s MOQ can help buyers negotiate better pricing structures.
-
Specifications and Customization: Customized PCBs typically incur higher costs due to the complexity of design and production. Buyers should weigh the need for custom features against potential cost increases.
-
Material Quality and Certifications: Higher-quality materials and certifications (e.g., ISO, UL) can drive up costs but are often necessary for compliance in specific industries. Buyers should balance quality with their budget constraints.
-
Supplier Factors: The reputation and reliability of the supplier can influence pricing. Established suppliers may charge more but often provide better service and product consistency.
-
Incoterms: The choice of Incoterms affects the total cost of ownership. Terms such as FOB (Free on Board) or CIF (Cost, Insurance, and Freight) can shift costs between the buyer and seller, impacting the final pricing.
What Are the Best Negotiation Strategies for B2B Buyers?
For international B2B buyers, particularly those from Africa, South America, the Middle East, and Europe, effective negotiation can yield significant cost savings:
-
Understand Total Cost of Ownership (TCO): Consider all costs associated with procurement, including shipping, tariffs, and potential delays. This holistic view allows for better negotiation on price and terms.
-
Leverage Volume Discounts: If feasible, consolidate orders to meet MOQs or negotiate for bulk discounts. Suppliers may be more willing to offer lower prices for larger commitments.
-
Build Relationships with Suppliers: Establishing a long-term partnership can lead to better pricing and service. Regular communication and feedback can help foster a collaborative environment.
-
Request Transparent Pricing: Ask suppliers for a breakdown of costs. Understanding how each component contributes to the final price can reveal areas for negotiation and potential cost reductions.
-
Be Aware of Regional Factors: Different regions may have varying cost structures and supplier capabilities. Buyers should research these factors to ensure they are negotiating from an informed position.
Conclusion: What Should Buyers Keep in Mind?
While sourcing PCBs from China can offer significant cost advantages, it is crucial for buyers to understand the comprehensive cost structure and pricing nuances. By focusing on key cost components, price influencers, and effective negotiation strategies, international B2B buyers can optimize their sourcing decisions. Always remember to request indicative prices from suppliers as these can fluctuate based on market conditions and specific project requirements.
Alternatives Analysis: Comparing pcb manufacturing china With Other Solutions
In the competitive landscape of PCB manufacturing, international B2B buyers are increasingly seeking alternatives to traditional sourcing methods, particularly from China. Understanding these alternatives can provide valuable insights for companies in Africa, South America, the Middle East, and Europe. This analysis will compare PCB manufacturing in China with two viable alternatives: domestic manufacturing in Europe and outsourcing to emerging markets in Southeast Asia.
Comparison Table
Comparison Aspect | Pcb Manufacturing China | Domestic Manufacturing (Europe) | Outsourcing to Southeast Asia |
---|---|---|---|
Performance | High-quality standards, advanced technology | Consistent quality, shorter lead times | Variable quality, depends on supplier |
Cost | Generally lower costs due to economies of scale | Higher labor and production costs | Competitive pricing, but variable due to logistics |
Ease of Implementation | Established supply chains, but complex regulations | Streamlined processes, fewer regulatory hurdles | Complex logistics and customs processes |
Maintenance | Good support, but time zone differences can affect communication | Local support, easier to manage | Support varies widely, may require on-site visits |
Best Use Case | High-volume production, cost-sensitive projects | High-quality, low-volume needs, rapid prototyping | Cost-effective solutions for medium-volume projects |
What Are the Pros and Cons of Domestic Manufacturing in Europe?
Domestic manufacturing in Europe offers several advantages. It typically ensures consistent quality due to stringent regulations and standards. Additionally, lead times are often shorter, which is crucial for businesses that require rapid turnarounds. However, the downside is higher production costs, which may not be feasible for all projects, especially those with budget constraints. Companies targeting high-quality, low-volume needs or rapid prototyping should consider this alternative.
How Does Outsourcing to Southeast Asia Compare?
Outsourcing to Southeast Asia can be a cost-effective solution for medium-volume projects. Countries like Vietnam, Thailand, and Malaysia have developed robust manufacturing capabilities, often at lower costs than China. However, the quality can be variable, depending on the supplier’s capabilities. Logistics can also become complicated, with potential delays at customs. This option is best for businesses that are flexible with quality and timeline and are looking to optimize costs without sacrificing too much on performance.
Conclusion: How Should B2B Buyers Choose the Right PCB Manufacturing Solution?
When deciding between PCB manufacturing in China and its alternatives, B2B buyers must evaluate their specific needs carefully. Consider factors such as the required production volume, budget constraints, desired quality, and turnaround times. For high-volume and cost-sensitive projects, China remains a strong contender. However, for projects requiring rapid prototyping or high-quality standards, domestic manufacturing in Europe may be more suitable. Conversely, if cost savings are the primary concern and flexibility in quality is acceptable, outsourcing to Southeast Asia could be the right choice. Ultimately, the decision should align with the company’s strategic goals and operational requirements.
Essential Technical Properties and Trade Terminology for pcb manufacturing china
What Are the Key Technical Properties in PCB Manufacturing?
Understanding the technical properties of printed circuit boards (PCBs) is crucial for international B2B buyers, especially those sourcing from China. Here are some essential specifications to consider:
1. Material Grade: Why Does It Matter?
The choice of material grade significantly impacts a PCB’s performance and reliability. Common materials include FR-4, which is flame-retardant and offers good mechanical strength, and Rogers materials, known for their high-frequency capabilities. Selecting the appropriate material is vital for ensuring that the PCB meets specific application requirements, such as thermal management and signal integrity.
2. Tolerance: How Does It Affect Your PCB Quality?
Tolerance refers to the acceptable limits of variation in the dimensions of the PCB features. Standard tolerances for PCB manufacturing can range from ±0.1mm to ±0.5mm. A tighter tolerance typically translates to a higher manufacturing cost but ensures that the PCB fits precisely within the intended electronic assembly, reducing the risk of malfunction or performance issues.
3. Layer Count: What Is Its Impact on Design Complexity?
The layer count indicates the number of conductive layers in a PCB. Simple designs may only require a two-layer board, while more complex applications can necessitate multi-layer boards (up to 20 layers or more). Understanding the required layer count is essential for B2B buyers as it affects both the cost and the complexity of the manufacturing process.
4. Surface Finish: Which Options Should You Consider?
The surface finish of a PCB affects its solderability and overall performance. Common finishes include HASL (Hot Air Solder Leveling), ENIG (Electroless Nickel Immersion Gold), and OSP (Organic Solderability Preservative). Each has its pros and cons regarding cost, longevity, and suitability for specific applications. Selecting the right surface finish can enhance the reliability of the PCB in real-world applications.
5. Vias: What Are the Different Types and Their Uses?
Vias are conductive pathways that connect different layers of a PCB. The types of vias—such as through-hole, blind, or buried vias—play a critical role in the design and functionality of the PCB. Understanding the different types of vias and their applications can help buyers optimize their designs for performance and manufacturability.
What Are Common Trade Terms in PCB Manufacturing?
Familiarity with industry terminology is essential for effective communication with suppliers and understanding quotes. Here are some common terms that international B2B buyers should know:
1. OEM: What Does It Mean for Your Sourcing Strategy?
OEM stands for Original Equipment Manufacturer. In the PCB context, it refers to companies that design and manufacture products for other brands. Understanding OEM relationships can help buyers identify reliable manufacturers that adhere to quality standards.
2. MOQ: How Does It Impact Your Orders?
MOQ, or Minimum Order Quantity, is the smallest quantity a supplier is willing to sell. This term is crucial for B2B buyers as it influences budgeting and inventory management. Understanding the MOQ can help buyers avoid excess costs and ensure they have enough stock to meet demand.
3. RFQ: What Is Its Role in the Sourcing Process?
RFQ stands for Request for Quotation. It is a formal process where buyers request pricing and terms from suppliers. An effective RFQ can streamline the procurement process and ensure that buyers receive competitive quotes tailored to their specifications.
4. Incoterms: Why Are They Important for International Trade?
Incoterms are international commercial terms that define the responsibilities of buyers and sellers in a transaction. Familiarity with Incoterms like FOB (Free on Board) or CIF (Cost, Insurance, and Freight) is essential for understanding shipping costs, risk, and delivery timelines, especially for international transactions.
5. DFM: How Does Design for Manufacturing Affect Costs?
DFM, or Design for Manufacturing, refers to the process of designing PCBs to optimize manufacturability. By considering manufacturability during the design phase, buyers can reduce production costs and avoid potential issues during assembly, leading to a more efficient supply chain.
By grasping these technical properties and trade terms, international B2B buyers can make informed decisions when sourcing PCBs from China, ensuring quality, compliance, and cost-effectiveness.
Navigating Market Dynamics and Sourcing Trends in the pcb manufacturing china Sector
What Are the Current Market Dynamics Influencing PCB Manufacturing in China?
The PCB manufacturing sector in China is experiencing significant shifts driven by global technological advancements and changing buyer preferences. Key factors such as the rapid growth of the Internet of Things (IoT), advancements in electric vehicle technology, and the expansion of 5G networks are propelling the demand for high-quality PCBs. International B2B buyers, especially those from Africa, South America, the Middle East, and Europe, need to be aware that the Chinese market is increasingly focusing on automation and smart manufacturing processes to enhance efficiency and reduce lead times.
Moreover, the geopolitical landscape is influencing sourcing strategies, with companies looking to diversify their supply chains to mitigate risks associated with trade tensions and tariffs. For buyers from regions like Germany and Spain, this presents an opportunity to negotiate better terms and establish partnerships with manufacturers that have robust export capabilities. Emerging technologies such as AI and machine learning are being integrated into production processes, enabling manufacturers to optimize quality control and reduce waste, thus providing a competitive edge in the global market.
How Are Sustainability and Ethical Sourcing Shaping PCB Manufacturing in China?
Sustainability is becoming an essential consideration for B2B buyers in the PCB manufacturing sector. The environmental impact of traditional manufacturing processes has prompted a shift towards greener alternatives. International buyers are increasingly looking for suppliers that prioritize sustainable practices, such as using eco-friendly materials and processes that minimize waste and energy consumption.
Ethical sourcing is another critical aspect that buyers must consider. The importance of maintaining transparent supply chains cannot be overstated; it not only enhances brand reputation but also meets the growing consumer demand for socially responsible products. Certifications such as ISO 14001 for environmental management and RoHS compliance for hazardous substances are becoming benchmarks for assessing suppliers in the PCB manufacturing sector. Buyers should prioritize partnerships with manufacturers who have demonstrated commitment to sustainability and ethical practices, as this can significantly enhance their own brand image and marketability.
What Is the Historical Context of PCB Manufacturing in China?
The evolution of PCB manufacturing in China dates back to the 1970s when the country began to embrace technology and foreign investment. Initially, the focus was on low-cost production, which attracted numerous international companies seeking to reduce costs. Over the decades, China has transformed into a global leader in PCB manufacturing, driven by significant investments in technology and infrastructure. The shift towards high-tech, high-quality production has positioned China as a crucial player in the global supply chain, especially for industries like consumer electronics, automotive, and telecommunications.
This historical perspective is vital for B2B buyers to understand the competitive landscape and the ongoing changes that could impact their sourcing strategies. As the market continues to evolve, international buyers must stay informed about the latest trends and technologies in PCB manufacturing to make well-informed sourcing decisions.
Frequently Asked Questions (FAQs) for B2B Buyers of pcb manufacturing china
-
How do I choose the right PCB manufacturer in China?
Selecting the right PCB manufacturer involves several critical steps. First, assess their industry experience and expertise, particularly in your specific sector. Look for certifications like ISO 9001, which indicate quality management systems are in place. Evaluate their production capabilities, including technology and equipment used, to ensure they can meet your volume and complexity requirements. Don’t hesitate to request samples to gauge quality before committing to a large order. Finally, consider their communication skills and responsiveness, which are vital for successful collaboration. -
What are the common minimum order quantities (MOQ) for PCB manufacturing in China?
Minimum order quantities (MOQs) can vary significantly among PCB manufacturers in China. Typically, the MOQ ranges from 5 to 100 pieces, depending on factors such as the complexity of the design, materials used, and the manufacturer’s capacity. For specialized or low-volume orders, some manufacturers may accommodate smaller MOQs but may charge higher unit prices. It’s advisable to discuss your specific needs upfront to negotiate favorable terms and find a supplier willing to work with your desired quantity. -
What payment terms should I expect when sourcing PCBs from China?
Payment terms for PCB manufacturing can vary, but common practices include a 30% deposit upfront and the remaining 70% before shipment. Some manufacturers may offer more flexible terms for long-term clients or larger orders. It’s important to clarify the payment methods accepted, which typically include wire transfers, PayPal, or letter of credit. Ensure that all payment terms are documented in your purchase agreement to avoid any misunderstandings down the line. -
How do I ensure quality assurance when sourcing PCBs from China?
To guarantee quality assurance, start by requesting detailed documentation of the manufacturer’s quality control processes. Look for certifications like IPC-A-600 and IPC-A-610, which indicate adherence to industry standards. Consider conducting an on-site audit or hiring a third-party inspection service to evaluate the production facilities and processes. Additionally, establish a clear communication channel for addressing quality issues and set up inspection checkpoints throughout the production cycle to catch any defects early. -
What customization options are available for PCBs in China?
Many PCB manufacturers in China offer extensive customization options to meet specific project needs. These can include variations in board thickness, material types (e.g., FR-4, Rogers), surface finishes (like ENIG or HASL), and layer counts. Additionally, manufacturers can accommodate unique design features such as blind/buried vias, specific solder mask colors, or custom silkscreen printing. Discuss your design requirements with potential suppliers early in the process to explore the range of options available. -
What logistics considerations should I keep in mind when importing PCBs from China?
Logistics play a crucial role in the PCB sourcing process. Consider the shipping methods (air freight vs. sea freight) based on your budget and timeline. Ensure you understand the customs regulations in your country, as well as any tariffs or duties that may apply to your import. It’s also wise to work with a reliable freight forwarder who can help navigate the complexities of international shipping and provide updates on your shipment’s status. -
How do I evaluate the reliability of a PCB supplier in China?
Evaluating a PCB supplier’s reliability involves thorough research and due diligence. Start by checking their online reputation through reviews and testimonials from other international clients. Request references and case studies that demonstrate their capabilities and successful project completions. Additionally, look into their production capacity and lead times, as a reliable supplier should meet deadlines consistently. Consider establishing a trial order to test their service and quality before committing to larger contracts. -
What are the potential risks of sourcing PCBs from China, and how can I mitigate them?
Sourcing PCBs from China carries risks such as quality inconsistencies, communication barriers, and potential delays in shipping. To mitigate these risks, conduct comprehensive supplier vetting, including audits and reference checks. Use clear contracts that outline quality expectations, timelines, and penalties for non-compliance. Establish regular communication and updates throughout the production process to address any issues promptly. Additionally, consider purchasing insurance for your shipment to protect against loss or damage during transit.
Important Disclaimer & Terms of Use
⚠️ Important Disclaimer
The information provided in this guide, including content regarding manufacturers, technical specifications, and market analysis, is for informational and educational purposes only. It does not constitute professional procurement advice, financial advice, or legal advice.
While we have made every effort to ensure the accuracy and timeliness of the information, we are not responsible for any errors, omissions, or outdated information. Market conditions, company details, and technical standards are subject to change.
B2B buyers must conduct their own independent and thorough due diligence before making any purchasing decisions. This includes contacting suppliers directly, verifying certifications, requesting samples, and seeking professional consultation. The risk of relying on any information in this guide is borne solely by the reader.
Strategic Sourcing Conclusion and Outlook for pcb manufacturing china
In today’s competitive landscape, strategic sourcing from China for PCB manufacturing presents significant advantages for international B2B buyers. By leveraging China’s robust supply chain, advanced technology, and cost efficiencies, companies can enhance their product offerings while maintaining profitability. Key takeaways include the importance of establishing strong relationships with suppliers, understanding regional market dynamics, and ensuring compliance with international standards.
What are the future trends in PCB manufacturing from China? As the industry evolves, we can expect innovations in materials and processes, particularly in response to the growing demand for environmentally sustainable practices. Buyers should remain vigilant and adaptable, embracing new technologies such as automation and smart manufacturing to stay ahead.
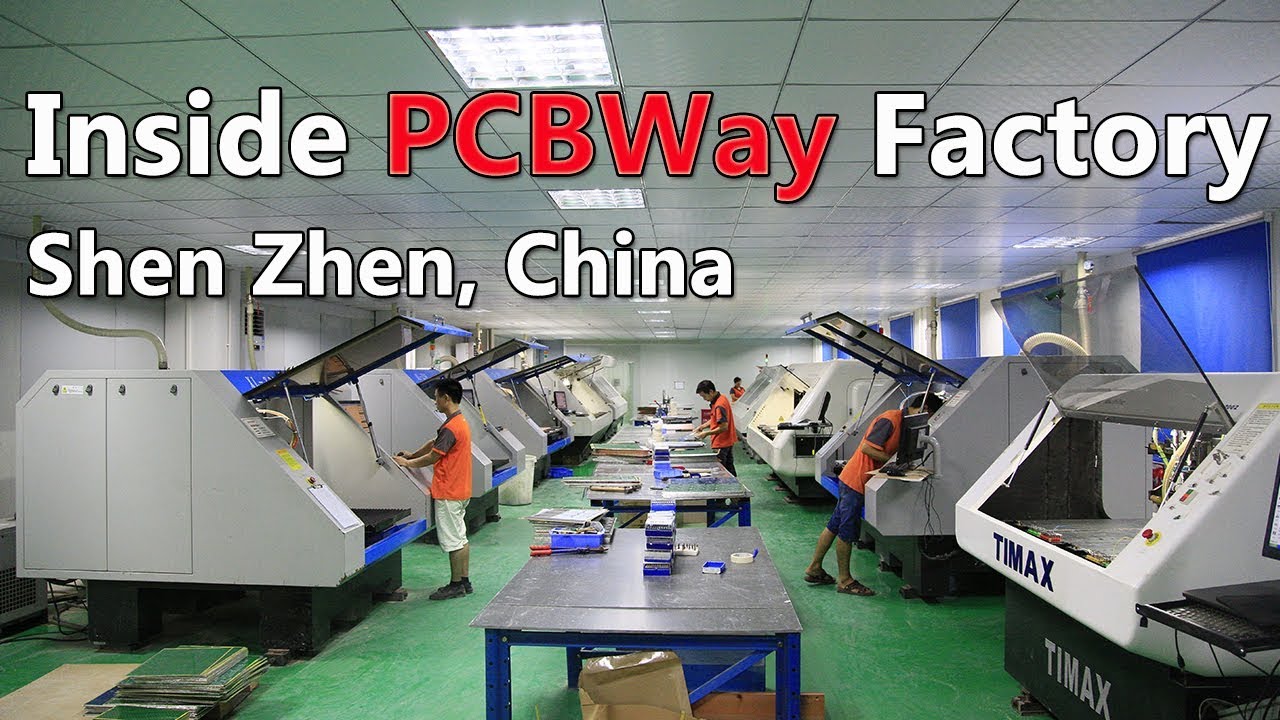
A stock image related to pcb manufacturing china.
For B2B buyers in Africa, South America, the Middle East, and Europe, now is the time to engage with Chinese manufacturers strategically. By conducting thorough due diligence and fostering partnerships, you can secure a competitive edge in your market. Take proactive steps today to explore how sourcing PCBs from China can align with your business goals and drive future growth. Embrace the opportunities that lie ahead, and position your company for success in the global marketplace.