Maximize Workspace Efficiency: L Shaped Desk Custom Guide (2025)
Introduction: Navigating the Global Market for l shaped desk custom
In the fast-evolving landscape of office furniture, sourcing custom l-shaped desks has become a pivotal challenge for international B2B buyers. These versatile workstations not only optimize space but also enhance productivity, making them an essential component in modern work environments. However, navigating the complexities of global suppliers, varying material qualities, and regional preferences can be daunting. This guide aims to demystify the process, providing a thorough exploration of the different types of l-shaped desks available, their various applications, and the critical factors to consider when selecting suppliers.
International buyers from Africa, South America, the Middle East, and Europe will find this resource invaluable. It covers essential topics such as effective supplier vetting processes, cost analysis, and the latest trends in ergonomic design. By equipping you with actionable insights and industry best practices, this guide empowers you to make informed purchasing decisions that align with your business needs and local market conditions.
Whether you are looking to furnish a new office or upgrade your existing workspace, understanding the global market for custom l-shaped desks can significantly impact your operational efficiency and employee satisfaction. Prepare to navigate this intricate market with confidence, ensuring that your investment in office furniture yields both aesthetic appeal and functional benefits.
Understanding l shaped desk custom Types and Variations
Type Name | Key Distinguishing Features | Primary B2B Applications | Brief Pros & Cons for Buyers |
---|---|---|---|
Executive L-Shaped Desk | High-end materials, ergonomic design, often with built-in storage | Executive offices, high-profile meetings | Pros: Enhances professionalism, offers comfort. Cons: Higher cost, may not fit all budgets. |
Corner L-Shaped Desk | Compact design, optimized for corner spaces, often modular | Small offices, home offices | Pros: Space-saving, versatile. Cons: Limited workspace, may lack storage options. |
Standing L-Shaped Desk | Adjustable height, promotes active working, often with cable management | Tech companies, collaborative spaces | Pros: Health benefits, modern design. Cons: Higher price point, requires adjustment period. |
Customizable L-Shaped Desk | Tailored materials, sizes, and colors to meet specific needs | Design firms, creative studios | Pros: Unique branding, fits specific space. Cons: Longer lead times, potentially higher costs. |
L-Shaped Desk with Storage | Integrated cabinets and drawers, focused on organization | Administrative offices, libraries | Pros: Maximizes space efficiency, organized workspace. Cons: Can be bulky, limits flexibility. |
What Are the Characteristics of Executive L-Shaped Desks?
Executive L-shaped desks are characterized by their high-end materials, ergonomic designs, and often include built-in storage solutions. Typically made from solid wood or premium laminates, these desks convey professionalism and are designed to enhance comfort during long working hours. B2B buyers should consider the prestige factor these desks bring to executive offices and high-profile meetings, although the higher cost may be a barrier for some organizations.
How Do Corner L-Shaped Desks Optimize Space?
Corner L-shaped desks are designed to fit snugly into corner spaces, making them ideal for small offices or home environments. Their compact design often allows for modular configurations, enabling businesses to adapt the workspace as needed. Buyers should weigh the space-saving benefits against the potential limitations in workspace and storage, as these desks may not offer as much surface area for documents and equipment.
Why Choose Standing L-Shaped Desks for Modern Workspaces?
Standing L-shaped desks are becoming increasingly popular in tech companies and collaborative workspaces due to their adjustable height features. These desks promote active working and can often include integrated cable management systems to maintain a clean appearance. While they offer significant health benefits and a modern aesthetic, buyers should be prepared for a potentially higher price point and an adjustment period for employees transitioning to standing work.
What Are the Advantages of Customizable L-Shaped Desks?
Customizable L-shaped desks allow businesses to tailor the materials, sizes, and colors to meet specific needs, making them particularly appealing to design firms and creative studios. This bespoke approach can enhance brand identity and ensure the desk fits perfectly within the designated workspace. However, buyers should consider the longer lead times and potentially higher costs associated with customization.
How Do L-Shaped Desks with Storage Improve Workspace Organization?
L-shaped desks with integrated storage solutions, such as cabinets and drawers, focus on maximizing organizational efficiency. They are particularly suitable for administrative offices and libraries, where keeping materials organized is essential. While these desks provide a structured workspace, buyers should be aware that they can be bulkier and may limit flexibility in rearranging the office layout.
Related Video: Custom L-Shaped Desk | IKEA Hack – MICKE Drawer | Easy Project #3
Key Industrial Applications of l shaped desk custom
Industry/Sector | Specific Application of l shaped desk custom | Value/Benefit for the Business | Key Sourcing Considerations for this Application |
---|---|---|---|
Corporate Offices | Executive suites and collaborative workspaces | Enhances productivity through efficient space utilization | Customization options, ergonomic design, durability |
Education | Faculty offices and administrative areas | Supports diverse work styles and collaborative projects | Compliance with educational standards, aesthetic appeal |
Healthcare | Patient consultation rooms and administrative offices | Facilitates better patient interaction and workflow | Hygiene materials, adjustable features, space optimization |
IT and Tech Companies | Development and project management hubs | Promotes teamwork and creativity in project execution | Cable management solutions, tech integration, scalability |
Creative Agencies | Design studios and brainstorming areas | Fosters innovation and enhances team collaboration | Aesthetic customization, flexible layouts, mobility options |
How Are L Shaped Desks Custom Used in Corporate Offices?
In corporate offices, custom L-shaped desks are frequently employed in executive suites and collaborative workspaces. These desks maximize the use of available space, allowing for efficient organization of documents and technology. They address common issues such as clutter and inadequate workspace by providing ample surface area for multiple tasks. International buyers should consider customization options to fit their unique branding requirements and ergonomic designs that promote employee well-being.
What Role Do L Shaped Desks Custom Play in Education?
In the education sector, L-shaped desks are utilized in faculty offices and administrative areas to support various work styles and collaborative projects. These desks enable educators to effectively manage their tasks while fostering a conducive environment for meetings and discussions. Buyers from educational institutions should focus on compliance with educational standards and aesthetic appeal to create inspiring spaces that motivate both staff and students.
How Are L Shaped Desks Custom Beneficial in Healthcare Settings?
In healthcare, custom L-shaped desks serve critical roles in patient consultation rooms and administrative offices. They enhance the workflow by facilitating better interaction between healthcare providers and patients, thus improving overall service quality. For international buyers in this sector, sourcing desks made from hygiene-friendly materials and those with adjustable features can provide significant advantages in maintaining a clean and functional environment.
Why Are L Shaped Desks Custom Important for IT and Tech Companies?
IT and tech companies often use custom L-shaped desks in development and project management hubs to promote teamwork and creativity. These desks are designed to accommodate various technology setups, enhancing productivity during project execution. Buyers should prioritize features such as cable management solutions and tech integration capabilities to ensure that workspaces remain organized and efficient as projects evolve.
How Do Creative Agencies Benefit from Custom L Shaped Desks?
Creative agencies leverage custom L-shaped desks in design studios and brainstorming areas to foster innovation and enhance team collaboration. The flexibility of these desks allows for dynamic arrangements that can adapt to different project needs. Buyers in this sector should consider aesthetic customization and mobility options to create inspiring environments that encourage creativity and teamwork among staff.
Related Video: DIY L-Shaped Desk – With Burnt Wood Finish
3 Common User Pain Points for ‘l shaped desk custom’ & Their Solutions
Scenario 1: Inadequate Space Optimization in Small Offices
The Problem:
For many B2B buyers, especially those operating in urban centers of Africa and Europe, office space is often at a premium. Companies may find that standard desk sizes do not fit well within their available square footage, leading to cluttered workspaces and decreased productivity. The challenge becomes even more pronounced when multiple employees share a confined area. Custom L-shaped desks could offer a solution, but buyers often struggle to visualize how these pieces will integrate into their existing layouts.
The Solution:
To effectively utilize space, B2B buyers should start by conducting a detailed office layout assessment. This involves measuring available spaces and identifying potential configurations for L-shaped desks. When sourcing custom desks, prioritize suppliers who offer design consultations or digital visualization tools. These resources can help create a 3D model of the proposed setup, allowing businesses to see how the desks will fit with existing furniture. Additionally, consider desks with built-in storage solutions to maximize vertical space, thereby keeping the work area organized and functional. This approach not only enhances productivity but also ensures that the workspace remains aesthetically pleasing.
Scenario 2: Inconsistent Quality in Custom Furniture Orders
The Problem:
International buyers, particularly from regions like South America and the Middle East, often face challenges regarding the quality of custom L-shaped desks. Variability in material quality and craftsmanship can lead to discrepancies between what is ordered and what is received. This inconsistency can result in costly returns, wasted time, and ultimately, frustration for procurement teams tasked with furnishing office spaces.
The Solution:
To mitigate quality issues, it is crucial for buyers to establish clear specifications before placing orders. This includes selecting specific materials, finishes, and even hardware for the desks. Furthermore, engaging with reputable manufacturers who provide samples or prototypes can help ensure that the final product meets expectations. Building strong relationships with suppliers based on transparent communication about quality standards can also foster accountability. Finally, consider leveraging third-party quality assurance services, especially for larger orders, to perform inspections before shipment. This proactive approach can help eliminate potential quality concerns and ensure a smoother procurement process.
Scenario 3: Limited Customization Options Leading to Employee Discontent
The Problem:
As companies strive to enhance employee satisfaction and productivity, the need for customizable workspaces has become increasingly important. However, many B2B buyers encounter limitations in customization options when sourcing L-shaped desks. This can lead to a one-size-fits-all approach that fails to meet the diverse needs of employees, resulting in discomfort and decreased morale.
The Solution:
Buyers should seek suppliers that offer a wide range of customization options, allowing them to tailor L-shaped desks to individual employee preferences. This includes adjustable height features, modular components, and various finishes. Conducting employee surveys or focus groups can provide valuable insights into what features are most desired, ensuring that the final products cater to user needs. Additionally, consider incorporating ergonomic designs that promote health and well-being, such as desks that allow for both sitting and standing positions. By investing in customizable solutions, companies can foster a more engaged workforce while enhancing overall productivity.
Strategic Material Selection Guide for l shaped desk custom
When selecting materials for custom L-shaped desks, international B2B buyers must consider various factors that influence performance, durability, and cost-effectiveness. Below, we analyze four common materials used in the construction of L-shaped desks, focusing on their properties, advantages and disadvantages, and specific considerations relevant to buyers from Africa, South America, the Middle East, and Europe.
What Are the Key Properties of Solid Wood for Custom L-shaped Desks?
Solid wood is a traditional choice for furniture, known for its aesthetic appeal and durability. Key properties include high strength and resistance to wear, making it suitable for high-traffic office environments. Solid wood can withstand a range of temperatures and pressures, although it may be susceptible to warping in humid conditions.
Pros and Cons:
– Pros: Offers a classic look, excellent durability, and can be refinished. It also provides good insulation against temperature changes.
– Cons: Higher cost compared to synthetic materials and requires more complex manufacturing processes. It may not be suitable for environments with extreme humidity.
Impact on Application:
Solid wood desks are ideal for executive offices and high-end workspaces. However, buyers must ensure that the wood is sourced sustainably to comply with international standards, such as the Forest Stewardship Council (FSC) certification.
How Does Metal Compare as a Material for Custom L-shaped Desks?
Metal, particularly steel and aluminum, is increasingly popular for modern office furniture. It boasts excellent strength and durability, with high corrosion resistance, making it suitable for various climates.
Pros and Cons:
– Pros: Highly durable, resistant to corrosion, and often more cost-effective than solid wood. Metal desks can also be designed to be lightweight yet sturdy.
– Cons: Can be prone to scratches and dents, and may not provide the warmth that wood does. Manufacturing complexity can increase with custom designs.
Impact on Application:
Metal desks are well-suited for industrial-style offices and workspaces requiring robust furniture. International buyers should consider compliance with standards such as ASTM for material quality and safety.
What Are the Benefits of Using Laminates for Custom L-shaped Desks?
Laminates are a popular choice for custom desks due to their versatility and cost-effectiveness. They consist of a core material (often particleboard) covered with a decorative layer, offering a wide range of colors and finishes.
Pros and Cons:
– Pros: Cost-effective, easy to clean, and available in numerous designs. They are also resistant to scratches and stains.
– Cons: Less durable than solid wood or metal and can be damaged by heat or moisture. The underlying particleboard may not withstand heavy loads over time.
Impact on Application:
Laminates are suitable for budget-conscious buyers looking for aesthetic appeal without compromising too much on durability. Buyers should consider local standards for particleboard emissions, such as CARB in the U.S. or E1 in Europe.
Why Choose Engineered Wood for Custom L-shaped Desks?
Engineered wood, such as MDF or plywood, combines the aesthetic qualities of wood with enhanced durability. It is manufactured from wood fibers bonded together under heat and pressure, resulting in a stable product.
Pros and Cons:
– Pros: More environmentally friendly than solid wood, as it utilizes wood waste. It is also less prone to warping and is generally more affordable.
– Cons: May not have the same aesthetic appeal as solid wood and can be less durable under heavy loads.
Impact on Application:
Engineered wood desks are ideal for modern offices and are often used in modular furniture systems. Buyers should verify compliance with local regulations regarding formaldehyde emissions, especially in regions with strict environmental laws.
Summary Table of Material Selection for Custom L-shaped Desks
Material | Typical Use Case for l shaped desk custom | Key Advantage | Key Disadvantage/Limitation | Relative Cost (Low/Med/High) |
---|---|---|---|---|
Solid Wood | Executive offices, high-end workspaces | Classic aesthetic and durability | Higher cost and humidity sensitivity | High |
Metal | Industrial-style offices | Excellent strength and corrosion resistance | Prone to scratches and dents | Medium |
Laminates | Budget-friendly offices | Cost-effective and easy to clean | Less durable and heat-sensitive | Low |
Engineered Wood | Modular furniture systems | Environmentally friendly and stable | Aesthetic appeal may be lacking | Medium |
By understanding the properties, advantages, and limitations of these materials, international B2B buyers can make informed decisions that align with their specific needs and compliance requirements.
In-depth Look: Manufacturing Processes and Quality Assurance for l shaped desk custom
What Are the Key Stages in the Manufacturing Process of Custom L-Shaped Desks?
The manufacturing process for custom L-shaped desks involves several critical stages, each contributing to the overall quality and functionality of the product. Understanding these stages can help B2B buyers evaluate suppliers effectively.
1. Material Preparation
The first step in manufacturing custom L-shaped desks is material preparation. High-quality raw materials, typically wood, metal, or composite materials, are selected based on design specifications and durability requirements. Suppliers often use sustainable wood sources to appeal to environmentally conscious buyers.
Before processing, materials undergo thorough inspection to ensure they meet required specifications. This stage may include cutting lumber to size, treating wood for pest resistance, or sourcing pre-fabricated components like metal legs or hardware.
2. Forming
Once materials are prepared, the next step is forming. This involves shaping the materials into the desired components of the desk. For wood, this may include techniques such as milling, routing, and sanding to achieve precise dimensions and smooth finishes.
For metal components, processes like bending, welding, or laser cutting are employed. Advanced technology, such as CNC machines, can enhance precision and reduce waste, leading to more cost-effective production. Buyers should inquire about the technology used and the expertise of the workforce to ensure high-quality outcomes.
3. Assembly
After forming, the components are assembled. This stage can vary significantly based on the design complexity of the L-shaped desk. Assembly may involve joining the desktop to the legs, attaching drawers, and ensuring all mechanical components function correctly.
Quality during assembly is critical; misalignment can lead to stability issues. Thus, manufacturers often implement jigs and fixtures to maintain consistency. B2B buyers should confirm that suppliers utilize skilled labor and quality tools during this process.
4. Finishing
The final manufacturing stage is finishing, which involves applying stains, paints, or protective coatings to enhance appearance and durability. This stage is essential for providing a polished look and protecting the desk from wear and tear.
Different finishing techniques, such as spray finishing or hand polishing, can impact the final product’s quality. Buyers should inquire about the types of finishes available and any associated environmental considerations, such as the use of low-VOC materials.
How Is Quality Assurance Implemented in Custom Desk Manufacturing?
Quality assurance (QA) is integral to the manufacturing process, ensuring that custom L-shaped desks meet both buyer specifications and international standards. A robust QA program typically involves multiple checkpoints throughout the production cycle.
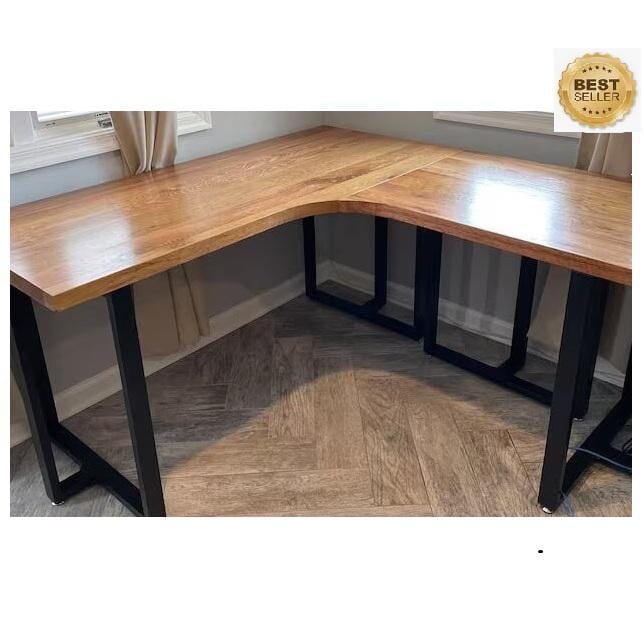
A stock image related to l shaped desk custom.
1. Understanding International Quality Standards
For B2B buyers, it is crucial to understand relevant international quality standards. The ISO 9001 certification is a key indicator of a manufacturer’s commitment to quality management systems. This standard emphasizes customer satisfaction and continuous improvement, making it a valuable benchmark for buyers.
Additionally, industry-specific certifications, such as CE marking for safety in Europe or API standards for durability, can further assure buyers of a product’s quality. Buyers should request documentation of these certifications during supplier evaluation.
2. What Are the Key Quality Control Checkpoints?
Quality control (QC) can be broken down into several critical checkpoints:
-
Incoming Quality Control (IQC): This stage occurs before materials enter the production process. Suppliers must inspect raw materials for defects and compliance with specifications.
-
In-Process Quality Control (IPQC): During manufacturing, ongoing inspections help identify issues early. This may involve measuring dimensions, checking assembly accuracy, and testing the functionality of moving parts.
-
Final Quality Control (FQC): The final inspection occurs after assembly and finishing. This stage ensures that the product meets all specifications and is free from defects before shipping.
Buyers should seek suppliers who have a robust QC process in place, including documented procedures and trained personnel.
3. What Common Testing Methods Are Used?
Testing methods vary by component but often include:
- Dimensional Inspection: Verifying that all parts meet specified dimensions.
- Load Testing: Ensuring that the desk can support the intended weight.
- Durability Testing: Subjecting the desk to wear and tear to assess long-term performance.
- Finish Testing: Checking for consistency in color and texture, as well as resistance to scratching or moisture.
Understanding these methods can help buyers assess the thoroughness of a supplier’s QC practices.
How Can B2B Buyers Verify Supplier Quality Control?
Verification of a supplier’s QC practices is essential for international B2B buyers. Here are some actionable strategies:
1. Conducting Supplier Audits
Regular audits can provide insights into a supplier’s manufacturing processes and quality control measures. Buyers can either conduct these audits themselves or hire third-party inspection agencies to ensure unbiased evaluations.
Audits should focus on production practices, employee training, and adherence to quality standards.
2. Requesting Quality Reports
B2B buyers should ask for detailed quality reports, which include metrics on defect rates, inspection results, and corrective actions taken. These reports can provide clarity on the supplier’s commitment to quality.
3. Utilizing Third-Party Inspections
Engaging third-party inspection services can further validate the quality of products before shipment. These services can conduct inspections at various stages of production, ensuring that the desks meet international standards and buyer specifications.
What Are the Quality Control Nuances for International Buyers?
For B2B buyers from Africa, South America, the Middle East, and Europe, navigating the nuances of QC can be complex. Here are some considerations:
-
Cultural Differences: Understanding local manufacturing practices and quality perceptions can aid in establishing effective communication with suppliers.
-
Regulatory Compliance: Buyers should be aware of any local regulations that may impact product specifications, such as safety standards in the UAE or environmental regulations in Europe.
-
Logistics and Supply Chain Considerations: Quality can also be affected by logistics. Buyers should evaluate how suppliers manage their supply chain to ensure consistent quality from raw material sourcing to final delivery.
By taking these factors into account, international B2B buyers can make informed decisions and establish long-term partnerships with reliable suppliers of custom L-shaped desks.
Practical Sourcing Guide: A Step-by-Step Checklist for ‘l shaped desk custom’
This guide serves as a practical checklist for B2B buyers seeking to procure custom L-shaped desks. A well-structured approach can ensure that you select the right product that meets your needs while also ensuring compliance with regional standards and supplier reliability. Below are the essential steps to streamline your sourcing process.
Step 1: Define Your Technical Specifications
Before you start sourcing, clearly outline the specifications of the L-shaped desk you require. Consider dimensions, materials, and design features, such as adjustable height or integrated storage solutions.
– Why it’s important: A well-defined specification helps in communicating your needs to potential suppliers and ensures that you receive accurate quotes.
– What to look for: Include details like weight capacity, color options, and any ergonomic requirements.
Step 2: Conduct Market Research
Research the market to identify potential suppliers and current trends in L-shaped desk designs. Utilize online platforms, industry forums, and trade shows to gather insights.
– Why it’s important: Understanding market dynamics allows you to identify reputable suppliers and innovative products that meet your needs.
– What to look for: Pay attention to regional preferences and compliance with local regulations, especially in your target markets.
Step 3: Evaluate Potential Suppliers
Before committing to a supplier, perform a thorough evaluation. Request detailed company profiles, check their history, and ask for references from other B2B clients.
– Why it’s important: Vetting suppliers minimizes risks related to product quality and delivery timelines.
– What to look for: Look for suppliers with experience in your specific industry and positive feedback from other buyers.
Step 4: Request Samples and Prototypes
Always request samples or prototypes of the desks you are considering. This step allows you to assess the quality and craftsmanship firsthand.
– Why it’s important: Evaluating a physical product can reveal nuances that images or descriptions may not convey.
– What to look for: Check the materials used, finish quality, and overall durability of the desk.
Step 5: Verify Compliance and Certifications
Ensure that the suppliers meet all necessary industry standards and certifications relevant to your region. This includes safety standards and environmental certifications.
– Why it’s important: Compliance not only protects your business from legal issues but also enhances your brand’s reputation.
– What to look for: Certifications like ISO, ANSI/BIFMA, or local certifications pertinent to your market.
Step 6: Negotiate Terms and Pricing
Once you have selected potential suppliers, enter negotiations regarding pricing, payment terms, and delivery schedules. Clearly outline expectations in the contract.
– Why it’s important: Effective negotiation can lead to cost savings and better terms, which are crucial for your business’s bottom line.
– What to look for: Ensure transparency in pricing to avoid hidden costs and understand payment structures that fit your cash flow.
Step 7: Plan for Logistics and Delivery
Develop a logistics plan that addresses how the desks will be shipped, delivered, and assembled at your location.
– Why it’s important: A clear logistics strategy reduces potential delays and ensures a smooth transition from supplier to your business.
– What to look for: Consider lead times, shipping methods, and assembly services offered by the supplier.
Following these steps will empower you to make informed decisions in your sourcing process for custom L-shaped desks, ensuring a successful procurement experience tailored to your business needs.
Comprehensive Cost and Pricing Analysis for l shaped desk custom Sourcing
What Are the Key Cost Components for Custom L-Shaped Desks?
When sourcing custom L-shaped desks, understanding the cost structure is essential for B2B buyers. The primary cost components include:
-
Materials: The choice of materials significantly impacts cost. Common options include MDF, particle board, solid wood, and metal. High-quality materials may increase the initial cost but can lead to better durability and customer satisfaction.
-
Labor: Labor costs vary by region and can be influenced by local wage standards. Skilled labor is often required for custom designs, which can elevate the overall price.
-
Manufacturing Overhead: This includes costs associated with running the production facility, such as utilities, equipment maintenance, and administrative expenses. Efficient factories may offer lower overhead costs, translating to better pricing for buyers.
-
Tooling: Custom designs often require specialized tooling, which can be a significant upfront investment. Buyers should inquire whether tooling costs are included in the quoted price or charged separately.
-
Quality Control (QC): Implementing robust QC processes ensures that the products meet the required specifications and quality standards. While this may add to costs, it can prevent costly returns and dissatisfaction later.
-
Logistics: Shipping and handling costs can vary widely based on distance, weight, and volume. Understanding Incoterms is vital as they define who is responsible for shipping costs, insurance, and risk.
-
Margin: Suppliers typically add a profit margin to cover their expenses and risks. This margin can fluctuate based on market demand and competition.
How Do Price Influencers Affect Custom L-Shaped Desk Sourcing?
Several factors can influence the pricing of custom L-shaped desks:
-
Volume/MOQ (Minimum Order Quantity): Larger orders often result in lower per-unit costs due to economies of scale. Buyers should negotiate volume discounts when possible.
-
Specifications and Customization: Unique designs or features can increase costs. Buyers should clearly define their specifications to avoid unexpected charges.
-
Materials Quality and Certifications: Premium materials and certifications (like ISO or environmental standards) can elevate costs but may also enhance the product’s marketability and longevity.
-
Supplier Factors: The reputation and reliability of the supplier can influence pricing. Established suppliers with a track record of quality may charge more but offer peace of mind regarding product delivery and consistency.
-
Incoterms: Understanding the agreed Incoterms is crucial for pricing. They dictate the responsibilities of buyers and sellers in the shipping process, impacting overall costs.
What Buyer Tips Can Help in Negotiating Custom Desk Prices?
For international B2B buyers, particularly from regions like Africa, South America, the Middle East, and Europe, the following tips can enhance cost-efficiency:
-
Negotiate Wisely: Don’t hesitate to negotiate prices, especially if you’re ordering in bulk. Suppliers may have wiggle room, particularly if they want to build a long-term relationship.
-
Evaluate Total Cost of Ownership (TCO): Look beyond the initial purchase price. Consider factors such as maintenance, durability, and resale value. A higher upfront cost may lead to lower long-term expenses.
-
Understand Pricing Nuances: Be aware of currency fluctuations, tariffs, and import duties that may affect the final price. Staying informed about these factors can help in budgeting accurately.
-
Request Detailed Quotes: Ensure that quotes include all cost components to avoid surprises later. A detailed quote allows for better comparisons between suppliers.
-
Leverage Local Insights: If sourcing from regions like the UAE or Indonesia, local market knowledge can provide leverage in negotiations. Understanding regional pricing trends can help secure better deals.
Disclaimer on Indicative Prices
Prices for custom L-shaped desks can vary significantly based on the aforementioned factors. It is advisable for buyers to obtain multiple quotes and conduct thorough market research to ensure they are getting the best deal possible. Always consult with suppliers for the most accurate and up-to-date pricing information tailored to specific requirements.
Alternatives Analysis: Comparing l shaped desk custom With Other Solutions
Understanding Alternatives in Office Furniture Solutions
When considering office furniture, particularly for collaborative and individual workspaces, the choice of desk can significantly impact productivity and employee satisfaction. Among the popular options, the custom L-shaped desk stands out for its versatility and functionality. However, it is essential for B2B buyers to evaluate alternative solutions that may better meet their specific needs or budget constraints. This analysis compares the custom L-shaped desk with two viable alternatives: the modular workstation and the traditional rectangular desk.
Comparison Table: L Shaped Desk Custom vs. Alternatives
Comparison Aspect | L Shaped Desk Custom | Modular Workstation | Traditional Rectangular Desk |
---|---|---|---|
Performance | High adaptability for space and use | Flexible layout for team dynamics | Standardized use, limited flexibility |
Cost | Higher initial investment | Mid-range pricing | Lower cost, widely available |
Ease of Implementation | Requires planning and customization | Easy to assemble and reconfigure | Quick setup, minimal tools needed |
Maintenance | Moderate upkeep, depending on materials | Low maintenance, durable materials | Low maintenance, but may lack durability |
Best Use Case | Ideal for dedicated office spaces or executive suites | Suitable for dynamic teams and collaborative environments | Good for smaller or traditional office setups |
What are the Pros and Cons of Modular Workstations?
Modular workstations offer a flexible alternative to the custom L-shaped desk. These desks can be reconfigured to suit various team setups and workflows, making them ideal for companies that frequently change their office layout or need to accommodate different project teams. The primary advantage of modular workstations lies in their ease of assembly and disassembly, allowing businesses to adapt quickly without significant downtime. However, while they offer versatility, the design may not provide the same level of personal space and privacy as a custom L-shaped desk, which could affect concentration in quieter work environments.
What are the Benefits and Drawbacks of Traditional Rectangular Desks?
Traditional rectangular desks are a staple in many office environments due to their affordability and straightforward design. They are widely available and can be easily sourced in bulk, making them a cost-effective choice for startups or businesses looking to furnish an entire office quickly. The simplicity of traditional desks also means they require minimal maintenance. However, they lack the space optimization and collaborative potential of L-shaped desks, which can hinder productivity in open-plan offices where teamwork and communication are essential.
How to Choose the Right Office Desk Solution for Your Business?
Selecting the right desk solution is crucial for optimizing office space and enhancing employee productivity. B2B buyers should assess their specific needs, such as the size of their office, the nature of their work (individual vs. collaborative), and budget constraints. For businesses focused on creating a dynamic, collaborative environment, modular workstations may provide the flexibility needed. Conversely, if the goal is to establish a more traditional office setup with dedicated workspaces, a custom L-shaped desk could be the better choice. Ultimately, understanding the unique requirements of your team and the functionality each desk type provides will guide you toward making an informed decision.
Essential Technical Properties and Trade Terminology for l shaped desk custom
When considering the procurement of custom L-shaped desks, understanding the essential technical properties and industry terminology is crucial for B2B buyers. Here’s a detailed look at the specifications and terminology that will enhance your purchasing decisions.
What Are the Key Technical Specifications for Custom L-Shaped Desks?
-
Material Grade
– The material grade refers to the quality and type of materials used in the desk’s construction, such as solid wood, particle board, or metal. Higher-grade materials typically offer better durability and aesthetic appeal. For B2B buyers, selecting the right material is essential for ensuring the longevity and functionality of the desk, especially in high-traffic office environments. -
Dimensions and Tolerance
– The dimensions of an L-shaped desk include its length, width, and height, which should be tailored to fit the intended workspace. Tolerance indicates the permissible limits of variation in these dimensions. Precise tolerances are critical in ensuring that the desk fits seamlessly into the designated area and meets ergonomic standards, ultimately impacting employee comfort and productivity. -
Weight Capacity
– This specification indicates how much weight the desk can support without compromising its structural integrity. For B2B buyers, understanding weight capacity is vital, particularly for setups that include multiple monitors or heavy equipment. Ensuring the desk can handle the intended load will prevent potential damage and enhance user satisfaction. -
Finish and Surface Treatment
– The finish refers to the final coating applied to the desk’s surface, which can affect its appearance, durability, and resistance to scratches or stains. Different finishes, such as laminate, veneer, or high-gloss, can cater to varying aesthetic preferences and functional needs. For B2B buyers, selecting the appropriate finish is crucial for maintaining the desk’s appearance over time and aligning it with brand identity. -
Modularity and Customization Options
– Modularity refers to the ability to customize or modify the desk configuration based on changing needs. This is particularly important for growing businesses that may require flexible office solutions. Understanding the customization options available can help buyers create a workspace that adapts to their evolving requirements.
What Are Common Trade Terms Used in the Custom Desk Industry?
-
OEM (Original Equipment Manufacturer)
– An OEM refers to a company that produces parts or equipment that may be marketed by another manufacturer. For buyers, working with OEMs can ensure that the products meet specific quality standards and can be customized to their needs. -
MOQ (Minimum Order Quantity)
– MOQ is the smallest quantity of a product that a supplier is willing to sell. This term is crucial for B2B buyers as it directly impacts procurement strategies and inventory management. Understanding MOQ can help buyers negotiate better terms and minimize excess stock. -
RFQ (Request for Quotation)
– An RFQ is a document used to solicit price quotes from suppliers for specific products or services. This process is essential for B2B buyers looking to compare pricing and terms from multiple suppliers, ensuring they make informed purchasing decisions. -
Incoterms (International Commercial Terms)
– Incoterms define the responsibilities of buyers and sellers in international transactions, including who is responsible for shipping, insurance, and tariffs. Familiarity with these terms is vital for B2B buyers, as they help clarify costs and risks associated with international procurement. -
Lead Time
– Lead time refers to the amount of time it takes from placing an order to receiving the product. For B2B buyers, understanding lead times is essential for planning and ensuring that office setups are completed in a timely manner, particularly during expansions or relocations.
By comprehensively understanding these technical properties and trade terms, B2B buyers can make informed decisions that enhance their procurement processes and ensure that the custom L-shaped desks meet their organizational needs.
Navigating Market Dynamics and Sourcing Trends in the l shaped desk custom Sector
What Are the Current Market Dynamics and Key Trends in the L Shaped Desk Custom Sector?
The global market for custom L-shaped desks is witnessing significant growth driven by the increasing demand for ergonomic office solutions and the rise of remote work. As businesses adapt to hybrid work models, the need for versatile and space-efficient furniture has surged. International B2B buyers, particularly from regions such as Africa, South America, the Middle East, and Europe, are focusing on sourcing desks that combine functionality with aesthetic appeal. Key trends include the integration of smart technology into office furniture, such as built-in charging ports and adjustable height features, catering to the evolving needs of modern workplaces.
Moreover, customization options are becoming paramount, allowing businesses to tailor products to their specific needs, whether in terms of size, color, or additional features. As international buyers navigate these trends, understanding local preferences and cultural nuances is crucial. For instance, in the Middle East, opulent designs may resonate more, while minimalist styles might be preferred in Scandinavian countries. Additionally, the rise of e-commerce platforms is facilitating easier access to international suppliers, enabling B2B buyers to compare prices and quality effectively.
How Is Sustainability and Ethical Sourcing Reshaping the L Shaped Desk Custom Market?
Sustainability has emerged as a vital consideration for B2B buyers in the custom furniture sector. The environmental impact of manufacturing processes, particularly in the use of wood and plastics, has prompted companies to seek suppliers who adhere to sustainable practices. This includes the use of certified sustainable materials, such as FSC-certified wood, which ensures that timber is sourced from responsibly managed forests.
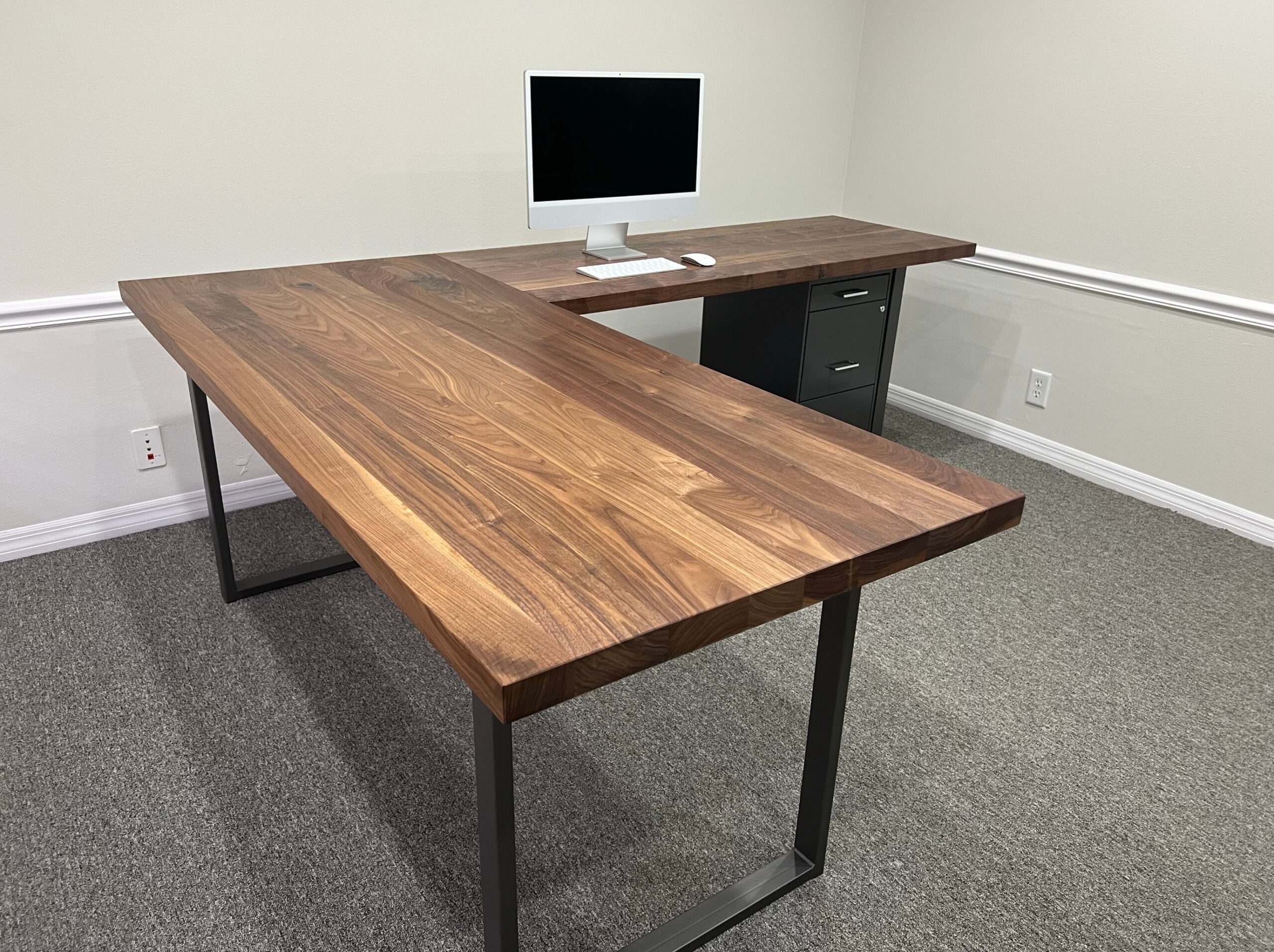
A stock image related to l shaped desk custom.
Ethical sourcing extends beyond materials; it encompasses fair labor practices and transparency in the supply chain. Buyers from Africa and South America, for instance, are increasingly aware of the importance of supporting local economies and minimizing their carbon footprint. Certifications such as LEED (Leadership in Energy and Environmental Design) or GreenGuard are becoming essential for businesses looking to enhance their reputation and comply with environmental regulations. By prioritizing sustainability, B2B buyers not only meet consumer demand for eco-friendly products but also position themselves as responsible corporate citizens in a competitive marketplace.
How Has the Custom L Shaped Desk Market Evolved Over Time?
The evolution of the custom L-shaped desk market can be traced back to the changing dynamics of workspaces. Initially, office furniture focused primarily on functionality, but over the years, design aesthetics and employee well-being have taken center stage. The shift toward open office layouts and collaborative spaces has led to the demand for adaptable furniture solutions, including L-shaped desks that maximize corner spaces while providing ample working area.
As technology advanced, so did the integration of smart features in office furniture, reflecting the increasing importance of tech-savvy work environments. Furthermore, the COVID-19 pandemic accelerated the trend towards remote work, prompting manufacturers to innovate and offer solutions that cater to home offices. Today, the market is characterized by a blend of traditional craftsmanship and modern technology, allowing buyers to invest in furniture that meets both practical and aesthetic needs. Understanding this evolution helps B2B buyers make informed decisions when sourcing custom L-shaped desks, ensuring they select products that align with contemporary work trends.
Frequently Asked Questions (FAQs) for B2B Buyers of l shaped desk custom
-
How do I choose the right supplier for custom L-shaped desks?
Selecting the right supplier for custom L-shaped desks involves thorough research and vetting. Start by assessing potential suppliers’ experience and expertise in manufacturing office furniture. Look for verified reviews, case studies, and references from other B2B clients, particularly those in your region (Africa, South America, the Middle East, or Europe). It’s also beneficial to request samples or prototypes to evaluate quality. Engaging in direct communication can provide insights into their customer service and responsiveness, which are crucial for a successful partnership. -
What is the typical minimum order quantity (MOQ) for custom L-shaped desks?
The MOQ for custom L-shaped desks can vary widely depending on the supplier and the complexity of the customization. Generally, it ranges from 10 to 50 units, but some manufacturers may accommodate lower quantities for first-time buyers or pilot projects. Always clarify the MOQ before entering negotiations to avoid misunderstandings. If your order is below the MOQ, consider asking about flexibility or potential bulk purchasing options for future orders. -
What are the common payment terms for international B2B transactions involving custom L-shaped desks?
Payment terms in international B2B transactions typically include a deposit upfront (often 30-50%) with the balance paid upon completion or delivery. Some suppliers may offer credit terms, but this is usually reserved for established clients. It’s essential to discuss and agree on payment methods that are secure and convenient for both parties, such as wire transfers, letters of credit, or escrow services. Always ensure that payment terms are documented in your contract to prevent disputes. -
How can I ensure the quality of custom L-shaped desks before shipment?
To guarantee quality before shipment, implement a thorough quality assurance (QA) process. Request detailed product specifications and prototypes before mass production. Most suppliers should be willing to conduct a pre-shipment inspection, either through third-party services or your own representative. Additionally, establish clear quality standards and expectations in your contract. Regular communication during the manufacturing process can also help identify and resolve potential issues early. -
What factors should I consider when customizing L-shaped desks for my business?
When customizing L-shaped desks, consider factors such as ergonomic design, material quality, functionality, and aesthetics. Ergonomics are vital for employee comfort and productivity, so ensure that the desk dimensions suit your workforce’s needs. Select durable materials that align with your brand’s image. Functionality, such as integrated cable management and storage solutions, can enhance usability. Lastly, aesthetic elements should reflect your brand identity while appealing to your target market. -
What logistics considerations should I be aware of when importing custom L-shaped desks?
Logistics for importing custom L-shaped desks include understanding shipping options, customs regulations, and potential tariffs. Choose between air freight for faster delivery or sea freight for cost-effectiveness, considering the urgency of your needs. Research import regulations specific to your country, as compliance is essential to avoid delays. Additionally, factor in potential duties and taxes that may apply upon entry. Working with a logistics partner experienced in international trade can streamline the process. -
How do I handle potential delays in the delivery of custom L-shaped desks?
Handling delivery delays involves proactive communication and contingency planning. Maintain regular contact with your supplier to receive updates on production and shipping timelines. If delays occur, discuss alternative solutions, such as expedited shipping or partial shipments. It’s also wise to have a buffer in your project timeline to accommodate unforeseen delays. Establishing a clear contract with defined timelines and penalties for non-compliance can help mitigate risks. -
What are the benefits of sourcing custom L-shaped desks from international suppliers?
Sourcing custom L-shaped desks from international suppliers can provide several advantages, including access to diverse designs, competitive pricing, and high-quality materials. International suppliers often have specialized expertise that can lead to innovative solutions tailored to your needs. Additionally, leveraging global supply chains can yield cost savings, especially if you are sourcing from regions known for manufacturing efficiency. However, ensure that you conduct due diligence to mitigate risks associated with international trade, such as compliance and quality control.
Important Disclaimer & Terms of Use
⚠️ Important Disclaimer
The information provided in this guide, including content regarding manufacturers, technical specifications, and market analysis, is for informational and educational purposes only. It does not constitute professional procurement advice, financial advice, or legal advice.
While we have made every effort to ensure the accuracy and timeliness of the information, we are not responsible for any errors, omissions, or outdated information. Market conditions, company details, and technical standards are subject to change.
B2B buyers must conduct their own independent and thorough due diligence before making any purchasing decisions. This includes contacting suppliers directly, verifying certifications, requesting samples, and seeking professional consultation. The risk of relying on any information in this guide is borne solely by the reader.
Strategic Sourcing Conclusion and Outlook for l shaped desk custom
In the evolving landscape of office furniture, particularly for custom L-shaped desks, strategic sourcing is paramount for international B2B buyers. By understanding regional preferences and aligning with reliable suppliers, businesses can enhance workspace efficiency while accommodating unique design requirements. Key takeaways emphasize the importance of assessing supplier capabilities, leveraging local market insights, and ensuring compliance with international standards.
How can strategic sourcing improve your procurement of custom L-shaped desks? By adopting a proactive sourcing strategy, buyers can mitigate risks associated with supply chain disruptions and fluctuating costs. Establishing long-term partnerships with manufacturers from diverse regions—such as Africa, South America, the Middle East, and Europe—can provide competitive advantages in terms of pricing and product innovation.
As we look ahead, the demand for customizable office solutions will only grow. Now is the time for international B2B buyers to explore innovative sourcing strategies that not only meet current needs but also anticipate future trends. By investing in custom L-shaped desks that reflect both functionality and aesthetics, businesses can create work environments that foster productivity and well-being. Engage with trusted suppliers today to secure the best options for your organization’s needs.