Unlock Savings: The Ultimate Bus Bar Supplier Guide (2025)
Introduction: Navigating the Global Market for bus bar supplier
Navigating the complexities of sourcing reliable bus bar suppliers can pose significant challenges for international B2B buyers, particularly those operating in diverse markets across Africa, South America, the Middle East, and Europe, including countries like Argentina and Turkey. As industries increasingly rely on efficient power distribution systems, understanding the intricacies of bus bars—such as their types, applications, and material specifications—becomes critical for making informed purchasing decisions. This guide aims to demystify the global market for bus bar suppliers by providing comprehensive insights into various product categories, from copper and aluminum bus bars to insulated and uninsulated options.
Throughout this guide, we will explore essential aspects of the procurement process, including supplier vetting criteria, cost considerations, and the implications of regional regulations and standards. By equipping B2B buyers with actionable knowledge, we empower them to navigate the supplier landscape with confidence, ensuring they select partners that align with their operational needs and compliance requirements. Whether you are sourcing for industrial applications or commercial projects, this guide serves as a valuable resource to enhance your procurement strategy and drive successful outcomes in the global marketplace.
Understanding bus bar supplier Types and Variations
Type Name | Key Distinguishing Features | Primary B2B Applications | Brief Pros & Cons for Buyers |
---|---|---|---|
Copper Bus Bars | High conductivity, corrosion-resistant coating | Power distribution, industrial use | Pros: Excellent conductivity, durable. Cons: Higher cost compared to aluminum. |
Aluminum Bus Bars | Lightweight, lower cost | Renewable energy, commercial sectors | Pros: Cost-effective, lightweight. Cons: Lower conductivity than copper. |
Insulated Bus Bars | Protective coating, reduces short-circuit risks | Electrical panels, transformers | Pros: Enhanced safety, reduced maintenance. Cons: More complex installation. |
Flexible Bus Bars | Bendable design, easy installation | Mobile equipment, temporary setups | Pros: Versatile, easy to install. Cons: Lower current capacity than rigid bars. |
Bus Bar Assemblies | Pre-assembled units, includes connectors | Data centers, large facilities | Pros: Quick installation, reduced labor costs. Cons: Limited customization. |
What Are the Characteristics of Copper Bus Bars and Their B2B Suitability?
Copper bus bars are known for their superior electrical conductivity and durability, making them ideal for high-performance applications. They are often used in power distribution systems and industrial settings where reliability is paramount. When purchasing copper bus bars, buyers should consider the cost versus the long-term benefits of lower resistance and maintenance requirements, especially in environments prone to corrosion.
How Do Aluminum Bus Bars Compare in Cost and Applications?
Aluminum bus bars offer a cost-effective alternative to copper, making them suitable for applications in renewable energy and commercial sectors. Their lightweight nature facilitates easier handling and installation, which can be a significant advantage in large projects. However, buyers must evaluate the trade-off between lower conductivity and the overall project budget, particularly in high-current applications.
What Are the Benefits of Using Insulated Bus Bars?
Insulated bus bars come with protective coatings that enhance safety by reducing the risk of short circuits. They are particularly useful in electrical panels and transformers where safety and reliability are critical. Buyers should assess the installation requirements and maintenance implications, as insulated bus bars may require more complex setups but ultimately lead to lower long-term risks.
Why Choose Flexible Bus Bars for Mobile Applications?
Flexible bus bars are designed for easy installation and adaptability, making them ideal for mobile equipment and temporary setups. Their bendable design allows for quick adjustments in tight spaces. However, buyers should be aware that flexible bus bars typically have lower current capacities compared to rigid bars, which may limit their application in high-demand environments.
What Advantages Do Bus Bar Assemblies Offer to Large Facilities?
Bus bar assemblies provide a comprehensive solution for large facilities, including data centers. They come pre-assembled with connectors, allowing for quicker installation and reduced labor costs. However, buyers need to consider the limited customization options available with these assemblies, which may not fit all unique system requirements.
Related Video: Variations In Construction Projects Explained
Key Industrial Applications of bus bar supplier
Industry/Sector | Specific Application of bus bar supplier | Value/Benefit for the Business | Key Sourcing Considerations for this Application |
---|---|---|---|
Power Generation | Power distribution in renewable energy plants | Efficient energy transfer and reduced energy losses | Compliance with local regulations and standards, scalability |
Manufacturing | Electrical distribution in industrial machinery | Enhanced reliability and reduced downtime | Customization options, material quality, and certifications |
Transportation | Power supply systems in electric vehicles | Improved performance and safety | Weight considerations, thermal management capabilities |
Data Centers | Power management in data centers and server farms | Increased uptime and operational efficiency | High current capacity, thermal performance, and redundancy |
Construction | Electrical infrastructure in commercial buildings | Safety and efficiency in electrical installations | Local supplier partnerships, installation support, and warranties |
How Are Bus Bars Used in Power Generation?
In the power generation sector, bus bars are essential for efficient power distribution, particularly in renewable energy plants such as solar or wind farms. They facilitate the transfer of high currents from generators to transformers, minimizing energy losses. International buyers, especially from regions like Africa and South America, should consider sourcing bus bars that comply with local regulations and standards, ensuring they can handle the required current loads while being scalable for future expansions.
What Role Do Bus Bars Play in Manufacturing?
In manufacturing, bus bars are critical for the electrical distribution in industrial machinery, ensuring a reliable power supply. They help minimize downtime by providing a robust connection between power sources and equipment. When sourcing bus bars, manufacturers should prioritize customization options to fit specific machinery requirements and ensure the materials meet industry standards for quality and safety certifications. This is particularly vital for buyers in Europe and the Middle East, where compliance with stringent regulations is mandatory.
How Are Bus Bars Beneficial in Transportation?
Bus bars are increasingly used in electric vehicles (EVs) to manage power supply systems effectively. They improve performance by reducing resistance and enhancing safety through better thermal management. For international buyers, especially in regions like Turkey and Argentina, weight considerations are crucial, as the bus bars must be lightweight yet capable of handling high currents. Additionally, sourcing suppliers with proven thermal management capabilities can significantly enhance the performance and safety of EV systems.
Why Are Bus Bars Important in Data Centers?
In data centers, bus bars play a pivotal role in power management and distribution, ensuring high reliability and efficiency. They are designed to handle high current loads, which is essential for maintaining uptime and operational efficiency. For B2B buyers from Europe and the Middle East, focusing on bus bars with high current capacity and excellent thermal performance is critical. Additionally, considering options for redundancy can further enhance the reliability of power supply in mission-critical environments.
How Do Bus Bars Contribute to Construction Projects?
In the construction industry, bus bars are utilized for electrical infrastructure in commercial buildings, providing a safe and efficient means of distributing electricity. They help streamline electrical installations, reducing complexity and installation time. Buyers should consider establishing partnerships with local suppliers for better support and warranty options, ensuring they have access to installation assistance and service. This approach is particularly beneficial for projects in developing regions like Africa and South America, where local expertise can greatly enhance project success.
Related Video: HOW ITS MADE: Stainless bar and billet
3 Common User Pain Points for ‘bus bar supplier’ & Their Solutions
Scenario 1: Sourcing Quality Bus Bars in Emerging Markets
The Problem: International B2B buyers, particularly from Africa and South America, often face significant challenges in sourcing high-quality bus bars. The lack of reliable suppliers and fluctuating material standards can lead to subpar products that do not meet safety or operational requirements. Buyers may also struggle to find suppliers who understand the specific needs of their industries, such as energy distribution or manufacturing.
The Solution: To effectively source quality bus bars, buyers should start by conducting thorough market research to identify reputable suppliers with a track record of quality assurance. Engaging with local industry associations can provide valuable insights and recommendations. Additionally, requesting samples and certifications, such as ISO 9001 or relevant local standards, can help verify the quality of the bus bars. Establishing a clear set of specifications tailored to your operational needs will also ensure that you select a supplier that can meet your unique requirements. Finally, consider forming long-term partnerships with suppliers who demonstrate reliability, as this can lead to better pricing and priority service.
Scenario 2: Managing Delivery Delays for Bus Bar Orders
The Problem: One of the most frustrating pain points for B2B buyers is dealing with delivery delays. This issue can arise from logistical challenges, customs clearance in international shipping, or supplier mismanagement. Such delays can disrupt project timelines, lead to increased costs, and damage business relationships.
The Solution: To mitigate delivery delays, buyers should implement a robust supply chain management strategy. Start by setting clear timelines and deadlines in your agreements with suppliers. Regular communication is key; maintain ongoing dialogue about order status and expected delivery dates. Utilizing technology, such as supply chain management software, can provide real-time tracking of shipments and alert you to potential delays. Additionally, consider sourcing from multiple suppliers to diversify risk. This strategy not only ensures continuity in supply but also provides leverage in negotiations regarding delivery commitments.
Scenario 3: Understanding Technical Specifications of Bus Bars
The Problem: Many international B2B buyers find it challenging to navigate the technical specifications of bus bars, such as current ratings, material compatibility, and installation requirements. This lack of understanding can lead to incorrect purchases, resulting in safety hazards and increased operational costs.
The Solution: To enhance understanding of bus bar specifications, buyers should invest in training and education. Participating in workshops or webinars focused on electrical components can provide valuable insights into the technical aspects of bus bars. Buyers should also consult with engineers or technical advisors who can clarify specifications and assist in selecting the right products. When engaging with suppliers, ask for detailed product data sheets and clarification on performance metrics. Additionally, consider creating a checklist of required specifications that align with your operational needs, which can serve as a reference during the purchasing process. By taking these proactive steps, buyers can ensure they make informed decisions that align with their technical requirements.
Strategic Material Selection Guide for bus bar supplier
What Are the Common Materials Used in Bus Bar Manufacturing?
When selecting materials for bus bars, several factors come into play, including electrical conductivity, thermal management, and environmental resistance. The following materials are commonly used in the manufacturing of bus bars, each with unique properties that make them suitable for different applications.
How Does Copper Perform as a Bus Bar Material?
Key Properties: Copper is renowned for its excellent electrical conductivity, with a conductivity rating of approximately 59 S/m. It also exhibits good thermal conductivity, making it effective in dissipating heat. Copper can withstand high temperatures, typically rated up to 200°C.
Pros & Cons: The main advantage of copper is its superior conductivity, which allows for smaller bus bar designs without compromising performance. However, copper is relatively expensive compared to other materials, and it is prone to corrosion, particularly in humid environments. This necessitates protective coatings or treatments, adding to manufacturing complexity.
Impact on Application: Copper bus bars are ideal for high-current applications in power distribution systems and renewable energy installations. However, they may not be suitable for environments with high corrosion potential unless adequately protected.
Considerations for International Buyers: Compliance with standards such as ASTM B187 and IEC 61238 is crucial. Buyers from regions like Africa and South America should also consider local climate conditions that may affect copper’s longevity.
What Role Does Aluminum Play in Bus Bar Applications?
Key Properties: Aluminum has a conductivity rating of about 37 S/m, which is lower than copper but still sufficient for many applications. It is lightweight and has good corrosion resistance, particularly when anodized.
Pros & Cons: The primary advantage of aluminum is its lower cost and weight, making it easier to handle and install. However, its lower conductivity means that larger cross-sections are required to achieve the same performance as copper, which can offset some of the weight savings. Additionally, aluminum can be more susceptible to mechanical stress and fatigue.
Impact on Application: Aluminum bus bars are often used in medium-voltage applications and in environments where weight is a critical factor. They are particularly suitable for overhead power lines and renewable energy systems.
Considerations for International Buyers: Compliance with standards such as ASTM B231 and DIN 48201 is important. Buyers in Europe and the Middle East may prefer aluminum for its lightweight properties, especially in applications where transport costs are a concern.
How Does Stainless Steel Compare as a Bus Bar Material?
Key Properties: Stainless steel offers moderate electrical conductivity (around 1.5 S/m) and excellent corrosion resistance, especially in harsh environments. It can withstand high temperatures, typically rated up to 800°C.
Pros & Cons: The significant advantage of stainless steel is its durability and resistance to corrosion, making it suitable for outdoor applications. However, its lower conductivity means that it is less efficient than copper or aluminum, requiring larger dimensions for the same electrical performance.
Impact on Application: Stainless steel bus bars are often used in industrial applications where exposure to corrosive substances is a concern. They are also suitable for environments with extreme temperatures.
Considerations for International Buyers: Buyers should ensure compliance with ASTM A276 and JIS G4303 standards. In regions like Turkey and the Middle East, where environmental conditions can be harsh, stainless steel may be preferred.
What Are the Benefits of Using Brass for Bus Bars?
Key Properties: Brass, an alloy of copper and zinc, has a conductivity rating of approximately 28 S/m. It offers good corrosion resistance and can withstand moderate temperatures.
Pros & Cons: The main advantage of brass is its excellent machinability and aesthetic appeal. However, its lower conductivity compared to copper and aluminum makes it less suitable for high-current applications. Additionally, brass can be more expensive due to its alloying elements.
Impact on Application: Brass bus bars are typically used in low-voltage applications and where aesthetic considerations are important, such as in decorative electrical fittings.
Considerations for International Buyers: Compliance with standards like ASTM B16 and DIN 17660 is essential. Buyers in Europe may appreciate brass for its decorative qualities, while those in Africa and South America may focus more on cost-effectiveness.
Summary Table of Bus Bar Materials
Material | Typical Use Case for bus bar supplier | Key Advantage | Key Disadvantage/Limitation | Relative Cost (Low/Med/High) |
---|---|---|---|---|
Copper | High-current applications | Superior electrical conductivity | Expensive and prone to corrosion | High |
Aluminum | Medium-voltage applications | Lightweight and cost-effective | Lower conductivity than copper | Medium |
Stainless Steel | Industrial applications | Excellent corrosion resistance | Lower conductivity | Medium |
Brass | Low-voltage and decorative fittings | Good machinability and aesthetic appeal | Lower conductivity and higher cost | Medium |
This guide provides a comprehensive understanding of the materials available for bus bars, enabling international B2B buyers to make informed decisions based on their specific application needs and regional considerations.
In-depth Look: Manufacturing Processes and Quality Assurance for bus bar supplier
What Are the Main Stages of Manufacturing Processes for Bus Bars?
The manufacturing process for bus bars involves several critical stages, each designed to ensure the final product meets the required specifications for quality and performance. Understanding these stages can help international B2B buyers assess potential suppliers effectively.
1. Material Preparation: What Materials Are Used in Bus Bar Production?
The first step in the manufacturing process is material preparation, where raw materials such as copper, aluminum, or their alloys are sourced. These materials are selected based on their electrical conductivity, mechanical strength, and resistance to corrosion. For buyers in regions like Africa and South America, it is essential to verify that suppliers use high-quality materials that comply with international standards.
2. Forming: How Are Bus Bars Shaped?
Once the materials are prepared, the next stage is forming, where the raw materials are shaped into bus bars. This can be achieved through various techniques such as extrusion, bending, or stamping. Extrusion is particularly common as it allows for continuous lengths of bus bars, which can then be cut to specific sizes. For B2B buyers, understanding the forming techniques used can provide insights into the durability and performance of the final product.
3. Assembly: What Does the Assembly Process Involve?
Following the forming stage, the bus bars undergo an assembly process where they may be integrated with other components, such as insulators and connectors. This stage is crucial for ensuring that the bus bars function correctly within electrical systems. Buyers should inquire about the assembly methods employed by suppliers, as precision in this step is vital for the reliability of the bus bars in their applications.
4. Finishing: How Are Bus Bars Prepared for Use?
The final stage of manufacturing is finishing, which includes processes such as surface treatment, coating, and labeling. Surface treatments can enhance corrosion resistance and improve conductivity, while coatings can provide additional insulation. Buyers should look for suppliers who implement finishing processes that comply with industry standards to ensure longevity and effectiveness in various environments.
What Quality Assurance Practices Should B2B Buyers Expect from Bus Bar Suppliers?
Quality assurance (QA) is a critical aspect of the manufacturing process for bus bars. B2B buyers should be aware of the relevant international standards and industry-specific certifications that ensure product quality.
1. Which International Standards Are Important for Bus Bar Manufacturing?
International standards such as ISO 9001 play a vital role in ensuring that suppliers maintain a quality management system (QMS) that meets customer and regulatory requirements. Additionally, certifications like CE (Conformité Européenne) and API (American Petroleum Institute) may be relevant depending on the application of the bus bars. Buyers should request proof of these certifications to validate a supplier’s commitment to quality.
2. What Are the Key Quality Control Checkpoints in Bus Bar Manufacturing?
Quality control (QC) checkpoints are integral to the manufacturing process. These typically include:
- Incoming Quality Control (IQC): Inspection of raw materials upon arrival to ensure they meet specified standards.
- In-Process Quality Control (IPQC): Continuous monitoring during the manufacturing process to detect defects early.
- Final Quality Control (FQC): A comprehensive inspection of the finished bus bars before they are shipped.
Understanding these checkpoints can help buyers assess the reliability of potential suppliers.
3. What Common Testing Methods Are Used for Bus Bars?
Various testing methods are employed to ensure the quality and performance of bus bars. Common tests include:
- Electrical Testing: To measure conductivity and insulation resistance.
- Mechanical Testing: To assess tensile strength and flexibility.
- Thermal Testing: To evaluate performance under temperature fluctuations.
Buyers should inquire about the specific testing methods used by suppliers to ensure compliance with industry standards.
How Can B2B Buyers Verify Supplier Quality Assurance?
Verifying the quality assurance practices of bus bar suppliers is crucial for B2B buyers, especially in international markets.
1. What Are the Best Practices for Conducting Supplier Audits?
Conducting supplier audits is one of the most effective ways to verify quality assurance practices. Buyers should establish a clear audit process that includes:
- On-site Visits: Assessing the manufacturing facilities and observing the production processes.
- Documentation Review: Evaluating quality management documents, including QC reports and test results.
- Interviews: Discussing QA practices with key personnel involved in the manufacturing process.
2. How Important Are Quality Reports and Third-Party Inspections?
Quality reports provide insight into a supplier’s performance and adherence to standards. B2B buyers should request recent quality reports and consider engaging third-party inspection services to conduct independent evaluations. This adds an extra layer of assurance regarding the supplier’s compliance with international quality standards.
3. What Nuances Should International Buyers Consider Regarding Quality Certification?
International buyers, particularly from regions like Africa, South America, the Middle East, and Europe, should be aware of the nuances in quality certification. Certifications may vary by region and industry, so it is essential to ensure that the supplier’s certifications are recognized in the buyer’s local market. Additionally, understanding the local regulatory environment can help buyers make informed decisions when selecting suppliers.
Conclusion
B2B buyers in the international market must have a comprehensive understanding of the manufacturing processes and quality assurance practices involved in bus bar production. By focusing on material preparation, forming, assembly, and finishing stages, as well as emphasizing the importance of quality control, buyers can make informed decisions when selecting suppliers. Verifying quality through audits, reports, and third-party inspections will further ensure that the bus bars meet the necessary standards for their applications.
Practical Sourcing Guide: A Step-by-Step Checklist for ‘bus bar supplier’
The following guide serves as a practical checklist for international B2B buyers seeking to procure bus bars from reliable suppliers. This step-by-step approach will help streamline your sourcing process, ensuring you make informed decisions that align with your business needs.
Step 1: Define Your Technical Specifications
Start by clearly outlining the technical specifications required for your bus bars. This includes dimensions, materials, current ratings, and environmental conditions they need to withstand. Having detailed specifications helps potential suppliers understand your needs and provides a basis for comparison.
- Considerations:
- Determine if you need standard or custom designs.
- Specify any industry standards or certifications that must be met.
Step 2: Conduct Market Research for Potential Suppliers
Investigate the market to identify potential bus bar suppliers. Utilize online platforms, trade shows, and industry publications to compile a list of companies with a strong reputation.
- Action Points:
- Look for suppliers with extensive experience in your specific industry.
- Check reviews and testimonials from other B2B buyers, especially those within your geographical region, such as Africa, South America, or Europe.
Step 3: Evaluate Supplier Capabilities and Compliance
Before committing to a supplier, assess their manufacturing capabilities and compliance with relevant industry standards. This is crucial to ensure that they can meet your quality and delivery requirements.
- Verification Steps:
- Request copies of certifications (ISO, IEC, etc.) to ensure they adhere to industry norms.
- Inquire about their production capacity and lead times to align with your project schedules.
Step 4: Request Quotes and Compare Pricing
Once you have a shortlist of potential suppliers, request detailed quotes from each. This should include pricing, delivery times, and payment terms.
- Comparison Tips:
- Look beyond just the price; consider the total cost of ownership including shipping, duties, and potential import taxes.
- Evaluate the payment terms offered, as favorable conditions can significantly impact your cash flow.
Step 5: Check References and Past Performance
To gain confidence in your chosen supplier, request references from their previous clients. This step is essential for understanding their reliability and service quality.
- What to Ask:
- Inquire about the supplier’s ability to meet deadlines and handle issues that arise during the procurement process.
- Ask if the references would consider working with the supplier again.
Step 6: Assess Post-Sale Support and Warranty Options
Ensure that the supplier provides adequate post-sale support and warranty options. This is vital for long-term relationships and operational reliability.
- Key Considerations:
- Clarify the warranty terms to understand coverage for defects or performance issues.
- Evaluate the supplier’s responsiveness to inquiries and support requests post-purchase.
Step 7: Finalize Contract Terms and Conditions
Once you have selected a supplier, finalize the contract, ensuring that all terms and conditions are clearly defined. This includes delivery schedules, payment terms, and penalties for non-compliance.
- Contract Checklist:
- Ensure that the agreement includes clauses for dispute resolution and quality assurance.
- Verify that all agreed-upon specifications are documented in the contract to prevent misunderstandings.
By following this checklist, you can effectively navigate the complexities of sourcing bus bars, ensuring that you partner with a supplier that meets your technical and business requirements.
Comprehensive Cost and Pricing Analysis for bus bar supplier Sourcing
What Are the Key Cost Components in Bus Bar Supplier Sourcing?
When sourcing bus bars, understanding the cost structure is crucial for effective budgeting and negotiation. The primary components of cost include:
-
Materials: This is often the largest expense, encompassing copper or aluminum used in the bus bars, along with any insulating materials. The price can fluctuate based on global commodity markets.
-
Labor: Labor costs include wages for skilled workers involved in the manufacturing process. In regions like Africa and South America, labor may be less expensive, but the skill level and productivity can vary significantly.
-
Manufacturing Overhead: This covers the indirect costs associated with production, such as utilities, facility maintenance, and equipment depreciation. Efficient manufacturing processes can help minimize these costs.
-
Tooling: Initial investments in tooling can be substantial, especially for custom bus bar designs. Buyers should consider whether the supplier has the capability to minimize tooling costs through standardization.
-
Quality Control (QC): Robust QC processes ensure that the bus bars meet industry standards and specifications. This may add to the overall cost but is essential for avoiding costly rejections and ensuring reliability.
-
Logistics: Transportation and shipping costs can vary dramatically based on distance, shipping method, and international tariffs. Incoterms play a significant role in defining who bears these costs.
-
Margin: Finally, the supplier’s profit margin will influence the final price. Understanding the typical margins in the bus bar market can help buyers assess whether a quote is competitive.
How Do Price Influencers Affect Bus Bar Sourcing?
Several factors can influence the pricing of bus bars, particularly for international B2B buyers:
-
Volume and Minimum Order Quantity (MOQ): Suppliers often offer better pricing on larger orders. Buyers should assess their needs and consider consolidating orders to meet MOQ requirements.
-
Specifications and Customization: Custom designs or specialized specifications can significantly increase costs. Buyers should clearly define their requirements to avoid unnecessary expenditures.
-
Materials and Quality Certifications: The choice of materials can affect both cost and quality. Suppliers with quality certifications (like ISO) may charge a premium, but this often translates to better performance and reliability.
-
Supplier Factors: The supplier’s reputation, location, and operational efficiency can all impact pricing. Established suppliers with a history of reliability may command higher prices, but they also provide peace of mind.
-
Incoterms: Understanding Incoterms is essential for international transactions. They define the responsibilities of buyers and sellers in terms of shipping costs, risks, and insurance, which can affect the total cost of ownership.
What Are Essential Buyer Tips for Cost-Efficiency in Bus Bar Sourcing?
To maximize cost-efficiency when sourcing bus bars, international buyers should consider the following strategies:
-
Negotiation: Engage in discussions with suppliers to explore potential discounts for bulk orders or long-term contracts. Building a relationship can lead to better pricing and terms.
-
Total Cost of Ownership (TCO): Assess the total cost of ownership rather than just the initial purchase price. Consider factors like maintenance, lifespan, and energy efficiency of the bus bars.
-
Pricing Nuances for International Buyers: Be aware of currency fluctuations, import tariffs, and potential delays in shipping. These factors can add to the overall cost and should be factored into decision-making.
-
Research and Compare Suppliers: Conduct thorough market research to compare prices and offerings from multiple suppliers. This can reveal competitive pricing and help identify the best value.
Disclaimer for Indicative Prices
It is important to note that prices for bus bars can vary significantly based on market conditions, location, and specific supplier agreements. Buyers should seek personalized quotes from suppliers to obtain accurate pricing tailored to their unique requirements.
Alternatives Analysis: Comparing bus bar supplier With Other Solutions
When exploring the best electrical distribution solutions, understanding the alternatives to bus bars is essential for making informed procurement decisions. Bus bars are commonly used for their efficiency in power distribution, but there are other technologies and methods that could meet specific needs depending on the application, budget, and operational requirements. This section compares bus bars to two viable alternatives: cable distribution systems and power distribution units (PDUs).
Comparison Aspect | Bus Bar Supplier | Cable Distribution System | Power Distribution Unit (PDU) |
---|---|---|---|
Performance | High current capacity; low voltage drop | Variable performance based on cable type and length | Effective for localized power distribution; can handle varying loads |
Cost | Moderate initial cost; lower long-term costs due to efficiency | Lower initial costs; potential higher long-term costs due to maintenance | Higher upfront costs; potential savings through energy efficiency |
Ease of Implementation | Requires careful design and installation | Easier installation; flexible routing options | Simple to implement in existing setups; modular designs available |
Maintenance | Low maintenance; durable materials | Regular checks needed; potential for wear and tear | Requires regular monitoring; proactive maintenance necessary |
Best Use Case | Large-scale applications; industrial settings | Residential or small commercial setups | Data centers; environments requiring flexible power management |
What Are the Pros and Cons of Cable Distribution Systems Compared to Bus Bars?
Cable Distribution Systems are flexible and can be adapted to various installation environments. They are generally cheaper to install, particularly for small-scale applications. However, their performance can vary significantly based on the cable type and installation method. Longer cable runs can lead to increased voltage drops, which can impact efficiency. Maintenance is also more frequent, as wear and tear can lead to outages if not managed properly.
How Do Power Distribution Units (PDUs) Stack Up Against Bus Bars?
Power Distribution Units (PDUs) are ideal for environments like data centers where power needs to be distributed to multiple devices. PDUs can offer features such as surge protection and monitoring capabilities, making them valuable for sensitive equipment. However, they typically come with a higher upfront cost than bus bars. While PDUs are easy to implement, they require regular monitoring and maintenance to ensure they are operating efficiently.
How Can B2B Buyers Choose the Right Solution for Their Needs?
Choosing between a bus bar supplier, cable distribution systems, or PDUs requires a thorough assessment of your specific operational needs. Consider the scale of your application, the initial and long-term costs, and the maintenance capabilities you can support. For large industrial applications where efficiency and reliability are paramount, bus bars may be the best choice. In contrast, smaller setups or those requiring flexibility might benefit from cable distribution systems, while PDUs are suited for environments with high-density power requirements and the need for granular monitoring. Always align your choice with both current needs and future scalability to ensure a sustainable investment.
Essential Technical Properties and Trade Terminology for bus bar supplier
What Are the Key Technical Properties of Bus Bars That B2B Buyers Should Know?
When sourcing bus bars for electrical distribution systems, understanding their technical specifications is crucial. Here are some essential properties that influence performance and reliability:
1. Material Grade
Bus bars are typically made from copper or aluminum. Copper offers superior conductivity and is more durable, while aluminum is lighter and more cost-effective. Selecting the appropriate material grade is vital for ensuring efficient power distribution and minimizing energy losses.
2. Cross-Sectional Area
The cross-sectional area of a bus bar directly affects its current-carrying capacity. A larger cross-section can handle higher currents but may also increase costs and weight. For B2B buyers, matching the bus bar’s cross-sectional area to the application’s specific current requirements is essential for safety and efficiency.
3. Tolerance Levels
Tolerance refers to the permissible deviation from specified dimensions. High precision in manufacturing tolerances ensures better connections and reduces the risk of overheating or electrical failures. Buyers should inquire about the tolerance levels offered by suppliers to ensure compatibility with their systems.
4. Temperature Rating
The temperature rating indicates the maximum operating temperature a bus bar can withstand without compromising its integrity. This property is crucial for applications in environments with fluctuating temperatures. B2B buyers must ensure that the bus bar’s temperature rating aligns with their operational conditions to prevent premature failure.
5. Surface Treatment
Surface treatments such as tin plating or anodizing can enhance corrosion resistance and improve conductivity. Understanding the surface treatment options available can help buyers choose the best bus bar for environments prone to moisture or other corrosive elements.
What Trade Terminology Should B2B Buyers Understand When Sourcing Bus Bars?
Familiarity with industry terminology can streamline the procurement process and enhance communication with suppliers. Here are key terms that every B2B buyer should know:
1. OEM (Original Equipment Manufacturer)
An OEM refers to a company that produces parts and equipment that may be marketed by another manufacturer. When dealing with bus bar suppliers, understanding OEM specifications ensures that the products will integrate seamlessly into existing systems.
2. MOQ (Minimum Order Quantity)
MOQ is the smallest number of units that a supplier is willing to sell. Knowing the MOQ is critical for B2B buyers to manage their inventory effectively and avoid overstocking or underordering.
3. RFQ (Request for Quotation)
An RFQ is a document issued by a buyer to request pricing and terms from suppliers for specific products. Crafting a detailed RFQ helps ensure that suppliers provide accurate and competitive quotes, ultimately aiding in budget planning and supplier selection.
4. Incoterms (International Commercial Terms)
Incoterms are a set of international rules that define the responsibilities of buyers and sellers in international transactions. Familiarity with Incoterms helps B2B buyers understand shipping logistics, including who is responsible for shipping costs, insurance, and the risk of loss during transit.
5. Lead Time
Lead time refers to the time taken from placing an order to its delivery. Understanding lead times is vital for B2B buyers, as it affects project timelines and inventory management. Buyers should communicate clearly with suppliers about expected lead times to ensure timely project execution.
Conclusion
By grasping these technical properties and trade terminologies, international B2B buyers can make informed decisions when sourcing bus bars. This knowledge not only facilitates better supplier communication but also enhances the overall efficiency of electrical systems, ultimately contributing to project success.
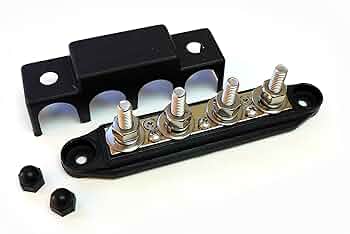
A stock image related to bus bar supplier.
Navigating Market Dynamics and Sourcing Trends in the bus bar supplier Sector
What are the Key Market Trends Affecting the Bus Bar Supplier Sector?
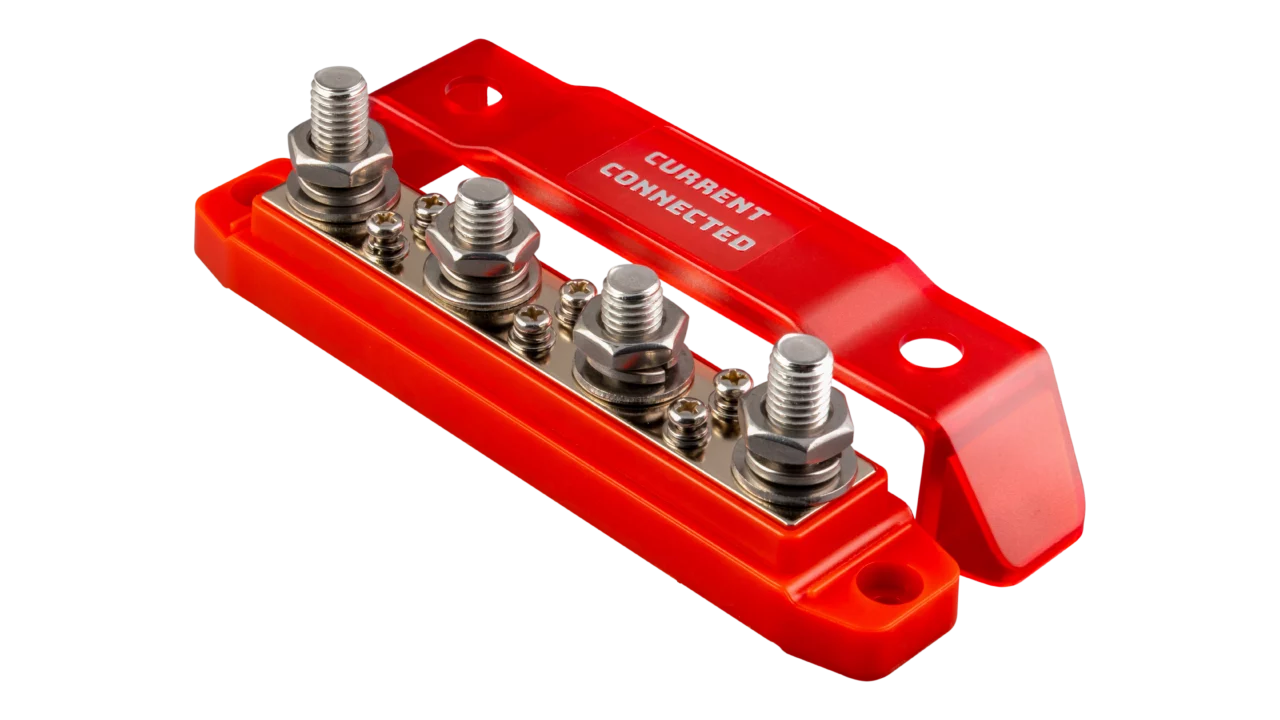
A stock image related to bus bar supplier.
The bus bar supplier sector is currently influenced by several global drivers, including the rapid expansion of renewable energy sources, urbanization, and the growing demand for efficient electrical distribution systems. As nations strive to meet their energy needs sustainably, the shift towards solar and wind power is driving the need for effective power management solutions. This trend is particularly relevant for international B2B buyers in regions like Africa and South America, where energy infrastructure is still developing.
In terms of technology, the integration of smart grids and IoT (Internet of Things) is transforming how bus bars are utilized in energy distribution. Suppliers are increasingly adopting digital solutions that enhance monitoring and management, allowing for predictive maintenance and operational efficiency. As a result, buyers are encouraged to seek suppliers who are at the forefront of these technological advancements to ensure they are equipped with the best solutions available.
Moreover, market dynamics are shifting due to geopolitical factors and trade agreements, especially for buyers in Europe and the Middle East. Tariffs and regulations can significantly impact sourcing strategies, making it essential for buyers to stay informed about the latest trade policies affecting their supply chains. Understanding local market conditions and regional suppliers can provide B2B buyers with a competitive edge in sourcing high-quality bus bar solutions.
How Can Sustainability and Ethical Sourcing Impact Your Bus Bar Supply Chain?
Sustainability is becoming a pivotal consideration in the sourcing strategies of international B2B buyers. The environmental impact of materials and manufacturing processes used in bus bar production is under scrutiny, with increasing pressure from consumers and regulators alike. Buyers are encouraged to evaluate the carbon footprint of their suppliers and consider those who implement sustainable practices throughout their supply chain.
Ethical sourcing is equally important, as it ensures that suppliers adhere to fair labor practices and contribute positively to their communities. Certifications such as ISO 14001 for environmental management and Fair Trade certification can serve as indicators of a supplier’s commitment to sustainability and ethical practices. By prioritizing suppliers with these certifications, buyers can enhance their brand reputation and appeal to a growing segment of eco-conscious consumers.
Additionally, exploring alternative materials—such as recycled metals or eco-friendly insulating materials—can further reduce environmental impact. This shift not only helps in compliance with regulations but also positions companies as leaders in sustainable practices within their industry.
What is the Evolution of Bus Bar Technology and Its Relevance for B2B Buyers?
The evolution of bus bar technology dates back to the early 20th century when the need for efficient electrical distribution became paramount with the growth of urban centers. Initially, bus bars were simple copper or aluminum bars used to connect multiple circuits within electrical distribution systems. However, advancements in material science and electrical engineering have led to the development of more sophisticated bus bar systems that offer improved conductivity, thermal management, and modularity.
In recent years, innovations such as insulated bus bars and busway systems have gained traction, offering enhanced safety and flexibility in installation. These developments are particularly relevant for B2B buyers as they seek to implement solutions that not only meet current operational demands but also adapt to future needs. Understanding the historical context of bus bar technology allows buyers to make informed decisions when selecting suppliers and products that align with their long-term strategic goals.
By leveraging insights from market dynamics, sustainability considerations, and the evolution of technology, international B2B buyers can navigate the complexities of the bus bar supplier sector more effectively.
Frequently Asked Questions (FAQs) for B2B Buyers of bus bar supplier
-
How do I select the right bus bar supplier for my business needs?
Selecting the right bus bar supplier involves assessing several key factors. Start by evaluating their industry experience and reputation. Look for suppliers who specialize in your specific type of bus bar, whether it’s copper or aluminum, and who can demonstrate compliance with international standards such as IEC or UL. Request samples to gauge quality, and consider their ability to provide customization options that fit your project requirements. Finally, assess their customer service responsiveness and ability to meet deadlines. -
What are the benefits of customizing bus bars for my project?
Customizing bus bars can significantly enhance your project’s efficiency and performance. Tailored designs can optimize space and reduce weight, which is crucial in applications where every kilogram counts. Additionally, customized bus bars allow for specific electrical requirements, improving conductivity and thermal management. By working closely with your supplier, you can ensure that the bus bars meet your unique technical specifications, leading to better overall system reliability. -
What is the minimum order quantity (MOQ) for bus bars from suppliers?
The minimum order quantity (MOQ) for bus bars varies significantly among suppliers and can depend on factors like material type, complexity of design, and production capabilities. Generally, MOQs can range from a few hundred to several thousand units. When sourcing, inquire about the MOQ upfront to ensure it aligns with your project’s scale. Some suppliers may offer flexible options for smaller orders or prototypes, which can be beneficial for testing before committing to larger quantities.
-
What payment terms should I expect when sourcing bus bars internationally?
Payment terms for international bus bar suppliers typically include options such as advance payment, letter of credit, or payment upon delivery. It’s essential to discuss and negotiate these terms before finalizing your order. Most suppliers will require a deposit, usually around 30%, with the balance payable upon shipment or delivery. Understanding the supplier’s preferred payment methods and currency can also help avoid unexpected fees and facilitate smoother transactions. -
How do I ensure quality assurance when purchasing bus bars?
To ensure quality assurance when purchasing bus bars, request detailed documentation regarding the supplier’s quality control processes. This includes certifications from recognized standards bodies, such as ISO 9001. Additionally, ask for inspection reports and test results for the specific bus bars you are ordering. If possible, arrange for third-party inspections or audits to verify compliance with your quality requirements before shipment. -
What logistics considerations should I keep in mind when importing bus bars?
Logistics play a crucial role in the successful importation of bus bars. Consider the shipping methods available, which may include air freight for faster delivery or sea freight for larger quantities. Factor in customs regulations and duties applicable in your country, as these can significantly affect overall costs. Establishing a reliable logistics partner familiar with international shipping of electrical components can streamline the process and help avoid delays. -
How can I assess the reliability of a bus bar supplier?
Assessing a bus bar supplier’s reliability can be accomplished through several methods. Begin by reviewing customer testimonials and case studies, which provide insight into their track record. Additionally, check for industry certifications and memberships in relevant trade organizations. Engaging in direct communication with the supplier can also help gauge their responsiveness and willingness to address your concerns. Lastly, consider conducting a site visit if feasible, to observe their manufacturing processes firsthand. -
What are the common applications for bus bars in various industries?
Bus bars are integral in various industries, including energy, transportation, and manufacturing. In the energy sector, they facilitate power distribution in substations and solar power plants. In transportation, they are used in electric and hybrid vehicles to manage high-voltage systems efficiently. Furthermore, manufacturing facilities utilize bus bars for power distribution in machinery and equipment. Understanding the specific applications relevant to your industry can help in sourcing the appropriate bus bars for your projects.
Important Disclaimer & Terms of Use
⚠️ Important Disclaimer
The information provided in this guide, including content regarding manufacturers, technical specifications, and market analysis, is for informational and educational purposes only. It does not constitute professional procurement advice, financial advice, or legal advice.
While we have made every effort to ensure the accuracy and timeliness of the information, we are not responsible for any errors, omissions, or outdated information. Market conditions, company details, and technical standards are subject to change.
B2B buyers must conduct their own independent and thorough due diligence before making any purchasing decisions. This includes contacting suppliers directly, verifying certifications, requesting samples, and seeking professional consultation. The risk of relying on any information in this guide is borne solely by the reader.
Strategic Sourcing Conclusion and Outlook for bus bar supplier
In conclusion, the strategic sourcing of bus bars presents significant opportunities for international B2B buyers, especially those located in Africa, South America, the Middle East, and Europe. By understanding the diverse market dynamics and leveraging competitive pricing, buyers can optimize their procurement processes. The emphasis on quality, reliability, and sustainability in sourcing practices not only ensures compliance with regional standards but also fosters long-term partnerships with suppliers.
Why Is Strategic Sourcing Essential for B2B Buyers?
Strategic sourcing empowers businesses to make informed decisions that align with their operational goals. It minimizes risks associated with supply chain disruptions, enhances cost efficiency, and drives innovation through collaborative supplier relationships. For buyers in emerging markets, this approach is crucial in navigating fluctuating economic conditions and accessing high-quality products that meet their specifications.
What Does the Future Hold for Bus Bar Supply Chains?
Looking ahead, the global demand for advanced electrical solutions, driven by renewable energy initiatives and urban infrastructure projects, is expected to rise. B2B buyers should remain proactive in identifying and engaging with reliable bus bar suppliers to stay ahead of market trends. By prioritizing strategic sourcing, businesses can not only enhance their operational efficiency but also contribute to sustainable development goals.
Engage with potential suppliers today to explore innovative solutions that can propel your business forward in this evolving landscape.