Discover Cost-Saving Tips from Top Ball Valve Manufacturers (2025)
Introduction: Navigating the Global Market for ball valve manufacturer
In today’s competitive industrial landscape, sourcing high-quality ball valves can be a daunting task for international B2B buyers. With a myriad of manufacturers worldwide, understanding how to navigate the global market for ball valve manufacturers is crucial for ensuring operational efficiency and compliance with industry standards. This comprehensive guide addresses key challenges faced by buyers, offering insights into the various types of ball valves, their applications across different sectors, and the critical factors to consider when selecting suppliers.
Throughout this guide, we will explore essential topics such as how to effectively vet suppliers, the cost implications of different valve types, and the latest innovations in valve technology. By equipping buyers from regions like Africa, South America, the Middle East, and Europe—specifically countries like Saudi Arabia and Brazil—with actionable information, this resource aims to empower informed purchasing decisions.
Understanding the nuances of sourcing ball valves not only helps mitigate risks but also enhances the ability to negotiate better terms and foster long-term supplier relationships. As you delve into this guide, expect to gain valuable knowledge that can lead to significant cost savings and improved operational performance in your organization.
Understanding ball valve manufacturer Types and Variations
Type Name | Key Distinguishing Features | Primary B2B Applications | Brief Pros & Cons for Buyers |
---|---|---|---|
Floating Ball Valve | Ball is not fixed; it floats on the flow, sealing against the seat. | Water treatment, oil and gas, HVAC systems | Pros: Simple design, low cost. Cons: Limited pressure and temperature range. |
Trunnion Ball Valve | Ball is fixed and supported by trunnions, allowing for larger sizes. | Petrochemical, power generation, mining | Pros: Suitable for high pressure, larger sizes. Cons: Higher initial cost. |
V-Port Ball Valve | Features a V-shaped port for flow control and throttling. | Chemical processing, water distribution | Pros: Enhanced flow control capabilities. Cons: More complex design may require maintenance. |
Multi-Port Ball Valve | Allows flow in multiple directions through various ports. | Piping systems, gas distribution | Pros: Versatile application, space-saving. Cons: More expensive and complex. |
Electric Ball Valve | Integrates an electric actuator for automated control. | Automation systems, process control | Pros: Remote operation, precise control. Cons: Dependence on power supply, higher cost. |
What Are the Characteristics of Floating Ball Valves?
Floating ball valves are characterized by a ball that is not fixed but instead floats on the flow medium. This design allows the ball to move slightly, creating a tight seal against the valve seat when closed. They are widely used in applications such as water treatment and HVAC systems due to their simple design and lower manufacturing costs. When considering purchasing floating ball valves, buyers should evaluate the pressure and temperature limits, as these valves are not suitable for high-pressure applications.
How Do Trunnion Ball Valves Differ from Other Types?
Trunnion ball valves feature a fixed ball supported by trunnions, which provides stability and allows for larger valve sizes. This design makes them ideal for high-pressure and high-temperature applications, commonly found in petrochemical and power generation industries. While they offer advantages in durability and performance, the initial cost is generally higher compared to floating ball valves. Buyers should consider the specific requirements of their applications, including pressure ratings and size constraints.
What Are the Benefits of V-Port Ball Valves?
V-Port ball valves are designed with a V-shaped port that allows for better flow control and throttling capabilities. This makes them particularly suitable for applications in chemical processing and water distribution, where precise flow regulation is critical. While they provide enhanced control, the complexity of their design can lead to increased maintenance requirements. Buyers should assess whether their operational needs justify the potential for higher upkeep costs.
In What Scenarios Are Multi-Port Ball Valves Ideal?
Multi-port ball valves are designed to facilitate flow in multiple directions, making them highly versatile for piping systems and gas distribution. Their space-saving design can be beneficial in compact installations. However, they come at a higher price point and require a more complex installation process. Buyers should evaluate their system’s layout and flow requirements to determine if the benefits of multi-port valves align with their operational goals.
Why Choose Electric Ball Valves for Automation?
Electric ball valves integrate an electric actuator that allows for automated control, making them ideal for use in automation systems and process controls. They offer the advantage of remote operation and precise control over flow rates, which can enhance operational efficiency. However, these valves require a reliable power supply and can be more expensive than manual alternatives. When considering electric ball valves, buyers should weigh the benefits of automation against the costs and power dependency.
Related Video: Valves Explained – Control Valve Types (Gate Valve, Globe Valve, Ball Valve, Butterfly Valve, etc.)!
Key Industrial Applications of ball valve manufacturer
Industry/Sector | Specific Application of Ball Valve Manufacturer | Value/Benefit for the Business | Key Sourcing Considerations for this Application |
---|---|---|---|
Oil and Gas | Flow control in pipeline systems | Ensures safe and efficient transportation of hydrocarbons | Material compatibility, pressure ratings, and certifications for safety standards |
Water Treatment | Regulation of water flow in treatment plants | Enhances operational efficiency and reduces maintenance costs | Corrosion resistance, size specifications, and compliance with environmental regulations |
Chemical Processing | Isolation and control of chemical reactions | Minimizes leaks and enhances safety in hazardous environments | Chemical compatibility, temperature ratings, and valve automation options |
HVAC Systems | Control of air and fluid flow | Improves energy efficiency and system reliability | Size and pressure ratings, actuator compatibility, and installation requirements |
Food and Beverage | Hygiene and flow control in processing | Ensures product safety and meets industry standards | Sanitary design, material certifications, and compliance with food safety regulations |
How are Ball Valves Used in the Oil and Gas Sector?
In the oil and gas industry, ball valves are critical for flow control in pipeline systems. These valves are designed to handle high pressure and extreme temperatures, ensuring the safe and efficient transportation of hydrocarbons. For international buyers, particularly from regions like Africa and the Middle East, sourcing ball valves that meet specific material compatibility and safety certifications is crucial. This ensures that the valves can withstand harsh environments and comply with local regulations, reducing the risk of leaks and improving operational reliability.
What Role do Ball Valves Play in Water Treatment Facilities?
Ball valves are extensively used in water treatment facilities to regulate the flow of water through various processes, including filtration and disinfection. Their ability to provide tight seals helps enhance operational efficiency and reduce maintenance costs. For buyers in South America and Europe, it’s essential to consider the corrosion resistance of materials used in ball valves, especially in environments with high mineral content. Compliance with local environmental regulations also plays a significant role in sourcing decisions to ensure sustainable practices.
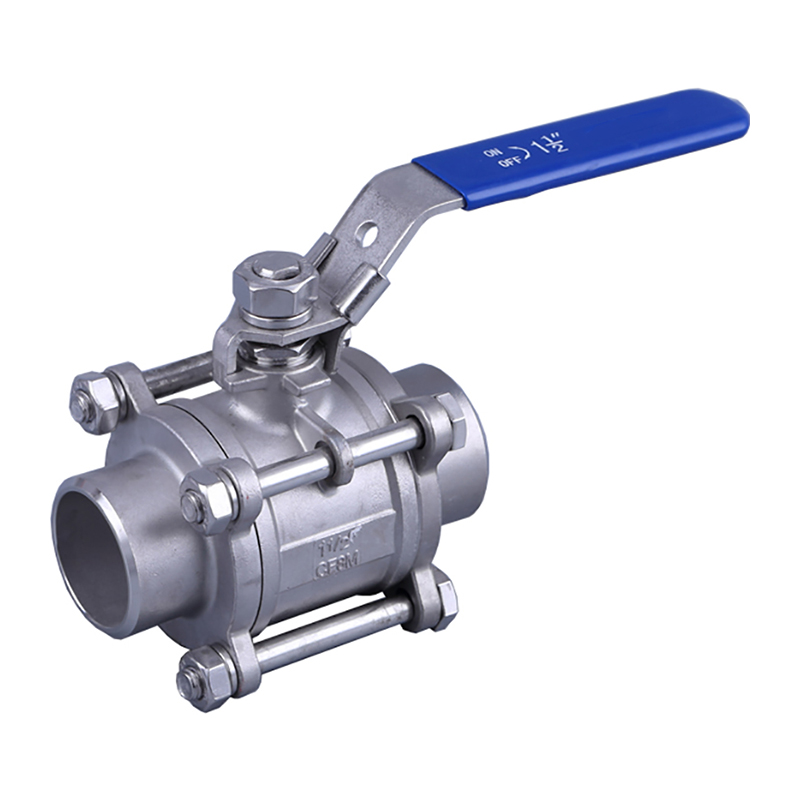
A stock image related to ball valve manufacturer.
How are Ball Valves Essential in Chemical Processing?
In chemical processing, ball valves are employed to isolate and control chemical reactions, minimizing the risk of leaks in hazardous environments. These valves must be made from materials compatible with the specific chemicals being processed to ensure safety and reliability. For international B2B buyers, particularly in Europe and the Middle East, understanding temperature ratings and valve automation options is vital for optimizing production efficiency and ensuring compliance with stringent safety standards.
Why are Ball Valves Important in HVAC Systems?
In HVAC systems, ball valves are used to control air and fluid flow, which significantly impacts energy efficiency and system reliability. They allow for precise flow regulation, which can lead to reduced operational costs. Buyers from Africa and South America should focus on sourcing valves that meet specific size and pressure ratings, as well as those compatible with various actuator systems to ensure seamless integration into existing HVAC setups.
How do Ball Valves Contribute to Food and Beverage Safety?
In the food and beverage industry, ball valves play a crucial role in maintaining hygiene and controlling flow during processing. They must meet stringent sanitary design requirements to ensure product safety and compliance with industry standards. For B2B buyers, particularly from Europe, it is essential to source ball valves with appropriate material certifications and compliance with food safety regulations. This focus on quality not only ensures safety but also enhances the overall efficiency of production processes.
Related Video: Trunnion Ball Valve
3 Common User Pain Points for ‘ball valve manufacturer’ & Their Solutions
Scenario 1: Sourcing Quality Ball Valves Amidst Global Supply Chain Disruptions
The Problem: In today’s global marketplace, B2B buyers, particularly in regions like Africa and South America, often face significant challenges when sourcing ball valves due to supply chain disruptions. Factors such as shipping delays, fluctuating material costs, and geopolitical tensions can lead to uncertainty in lead times and pricing. This can result in production delays, increased costs, and the potential for lost contracts, creating a ripple effect on overall business operations.
The Solution: To mitigate these challenges, international buyers should prioritize establishing relationships with multiple ball valve manufacturers to diversify their supply sources. Conducting thorough research to evaluate potential suppliers based on their reliability, production capacity, and geographic location can be beneficial. Additionally, buyers should consider local manufacturers or those with regional distribution centers to reduce lead times. Implementing a robust vendor management system can streamline communication and ensure that all suppliers are held to the same quality and delivery standards. Utilizing tools like demand forecasting and inventory management software can also help maintain optimal stock levels, reducing the risk of production stoppages.
Scenario 2: Understanding Technical Specifications for Ball Valves
The Problem: Many B2B buyers, especially those new to the industrial sector, struggle with understanding the technical specifications of ball valves. This includes aspects like pressure ratings, material compatibility, and valve sizes, which are critical to ensuring that the chosen product meets operational requirements. Misunderstandings can lead to selecting the wrong type of valve, resulting in failures, safety hazards, and costly rework.
The Solution: To overcome this issue, buyers should invest time in training and education about ball valve technology. This can involve attending industry webinars, workshops, or courses that focus on valve selection criteria and applications. Furthermore, collaborating closely with manufacturers during the specification phase can yield beneficial insights. Engaging in pre-purchase consultations where technical representatives can clarify specifications and provide tailored recommendations based on the buyer’s unique application can be invaluable. Additionally, creating a checklist of essential specifications to consider when evaluating options can streamline the decision-making process.
Scenario 3: Navigating Compliance and Regulatory Standards in Valve Manufacturing
The Problem: B2B buyers in regions like the Middle East and Europe often encounter stringent compliance and regulatory standards that govern the use of ball valves in various applications, such as oil and gas, water treatment, and pharmaceuticals. Navigating these regulations can be complex, and failure to comply can lead to legal repercussions, project delays, and damage to a company’s reputation.
The Solution: To effectively manage compliance issues, buyers should proactively familiarize themselves with local and international standards that apply to their industry, such as API, ANSI, and ISO certifications. Engaging with manufacturers who are well-versed in these regulations and who can provide documentation and certifications for their products is crucial. Buyers should also consider incorporating compliance checks into their procurement processes, ensuring that all products meet necessary standards before they are accepted. Building a compliance roadmap that outlines all relevant regulations and periodically reviewing this with legal or regulatory experts can help maintain alignment with evolving industry standards.
Strategic Material Selection Guide for ball valve manufacturer
When selecting materials for ball valves, manufacturers must consider various factors that affect performance, durability, and cost. Here, we analyze four common materials used in ball valve manufacturing: stainless steel, brass, PVC, and carbon steel. Each material offers unique properties and considerations that can significantly impact the end product’s suitability for specific applications.
What are the Key Properties of Stainless Steel for Ball Valves?
Stainless steel is a popular choice for ball valves due to its excellent corrosion resistance and high strength. It typically has a temperature rating of up to 150°C and can withstand high pressures, making it suitable for a wide range of applications, including oil and gas, chemical processing, and water treatment.
Pros & Cons: Stainless steel valves are durable and require minimal maintenance, which is a significant advantage in demanding environments. However, they can be more expensive than other materials, and their manufacturing complexity may lead to longer lead times.
Impact on Application: Stainless steel is compatible with various media, including corrosive fluids. This compatibility makes it a preferred choice in regions with stringent environmental regulations, such as Europe and parts of the Middle East.
How Does Brass Compare as a Material for Ball Valves?
Brass is another commonly used material for ball valves, known for its excellent machinability and moderate corrosion resistance. It generally has a temperature rating of up to 90°C and is suitable for low-pressure applications, such as water and gas distribution.
Pros & Cons: The main advantage of brass is its cost-effectiveness, making it an attractive option for budget-conscious projects. However, its susceptibility to dezincification in certain environments can limit its use in corrosive applications, particularly in tropical climates found in parts of Africa and South America.
Impact on Application: Brass valves are typically used in plumbing and HVAC systems. International buyers should be aware of local standards regarding lead content in brass, as compliance is increasingly important, especially in Europe.
What are the Benefits of Using PVC in Ball Valve Manufacturing?
PVC (Polyvinyl Chloride) is favored for its lightweight nature and resistance to corrosion and chemicals. It is suitable for applications involving water, chemicals, and wastewater, with a temperature rating of up to 60°C.
Pros & Cons: PVC ball valves are low-cost and easy to install, which can reduce overall project expenses. However, they are not suitable for high-pressure applications and can become brittle over time when exposed to UV light.
Impact on Application: PVC is widely used in irrigation and drainage systems, particularly in regions with abundant agricultural activities, such as parts of South America and Africa. Buyers should ensure that the PVC used meets local regulatory standards.
Why Choose Carbon Steel for Ball Valves?
Carbon steel offers high strength and durability, making it suitable for high-pressure applications. It typically has a temperature rating of up to 250°C and is often used in industrial settings.
Pros & Cons: The key advantage of carbon steel is its ability to handle high pressures and temperatures. However, it is prone to corrosion, requiring protective coatings or regular maintenance, which can increase long-term costs.
Impact on Application: Carbon steel is commonly used in oil and gas pipelines, making it a preferred choice in regions with significant energy production, such as the Middle East. Buyers should consider compliance with international standards, such as ASTM, to ensure product quality.
Summary Table of Material Selection for Ball Valve Manufacturing
Material | Typical Use Case for ball valve manufacturer | Key Advantage | Key Disadvantage/Limitation | Relative Cost (Low/Med/High) |
---|---|---|---|---|
Stainless Steel | Oil and gas, chemical processing | Excellent corrosion resistance | Higher cost and manufacturing complexity | High |
Brass | Plumbing, HVAC systems | Cost-effective | Susceptible to dezincification | Medium |
PVC | Irrigation, drainage systems | Lightweight and low-cost | Not suitable for high-pressure | Low |
Carbon Steel | Oil and gas pipelines | High strength for high pressures | Prone to corrosion, requires maintenance | Medium |
This strategic material selection guide provides international B2B buyers with essential insights into the properties, advantages, and limitations of various materials used in ball valve manufacturing. Understanding these factors can aid in making informed purchasing decisions tailored to specific application needs and regional compliance requirements.
In-depth Look: Manufacturing Processes and Quality Assurance for ball valve manufacturer
What Are the Key Stages in the Manufacturing Process of Ball Valves?
The manufacturing process for ball valves encompasses several critical stages that ensure the final product meets high standards of quality and performance. Understanding these stages is essential for B2B buyers, especially those from diverse regions such as Africa, South America, the Middle East, and Europe.
Material Preparation: How Is the Right Material Selected for Ball Valves?
The first step in the manufacturing process involves the careful selection and preparation of materials. Common materials used for ball valves include stainless steel, brass, and plastic, each chosen based on the application’s requirements, such as pressure, temperature, and medium compatibility.
Once selected, the materials undergo rigorous testing to ensure they meet specific mechanical and chemical properties. This often includes analyzing tensile strength, corrosion resistance, and hardness.
What Forming Techniques Are Used in Ball Valve Manufacturing?
After material preparation, the next phase is forming. This can include processes such as forging, machining, and casting.
- Forging: This technique enhances the material’s grain structure, resulting in increased strength and durability.
- Machining: Precision machining is employed to create the valve body and components, ensuring tight tolerances and smooth surfaces.
- Casting: For complex shapes, casting may be utilized, where molten metal is poured into molds.
Each technique has its advantages, and the choice depends on the specific design and performance requirements of the ball valve.
How Is the Assembly Process Conducted for Ball Valves?
Assembly is a critical phase where all components—such as the ball, seats, stem, and body—are brought together. The assembly process typically follows a systematic approach to maintain quality and ensure that each valve operates smoothly.
- Component Inspection: Each component undergoes an inspection before assembly to detect any defects.
- Assembly Techniques: Methods such as welding, bolting, or threading are used, depending on the valve design. High precision is crucial during this stage to avoid leaks and ensure functionality.
- Lubrication: Appropriate lubrication is applied to moving parts to enhance performance and longevity.
What Finishing Processes Are Essential for High-Quality Ball Valves?
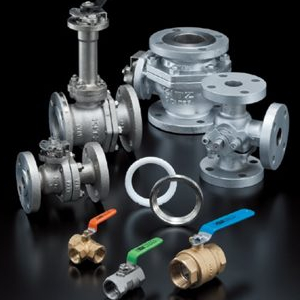
A stock image related to ball valve manufacturer.
Finishing processes include surface treatment, painting, and coating, which not only enhance the aesthetics of the ball valves but also improve their resistance to corrosion and wear. Common finishing techniques include:
- Electroplating: This process provides a protective layer that enhances corrosion resistance.
- Powder Coating: A durable finish that improves the valve’s appearance and resistance to environmental factors.
- Polishing: This step ensures a smooth surface finish, reducing friction and improving flow characteristics.
What Are the International Quality Assurance Standards for Ball Valves?
Quality assurance (QA) in the manufacturing of ball valves is paramount, particularly for international B2B transactions. Several international standards guide the QA processes:
- ISO 9001: This standard outlines a framework for quality management systems and is critical for ensuring consistent quality in manufacturing processes.
- API 6D: Specific to pipeline valves, this standard ensures that the ball valves meet stringent performance criteria.
- CE Marking: For products sold in Europe, CE marking signifies compliance with health, safety, and environmental protection standards.
What Are the Key Quality Control Checkpoints in Ball Valve Manufacturing?
Quality control (QC) is implemented at various checkpoints throughout the manufacturing process. Key QC stages include:
- Incoming Quality Control (IQC): This stage involves inspecting raw materials to ensure they meet specified standards before production begins.
- In-Process Quality Control (IPQC): Throughout the manufacturing process, regular inspections are conducted to ensure that each stage adheres to quality standards.
- Final Quality Control (FQC): Once assembly is complete, a comprehensive inspection is performed, including pressure tests and functional tests, to verify the valve’s integrity.
How Can B2B Buyers Verify Supplier Quality Control?
For international B2B buyers, especially those in Africa, South America, the Middle East, and Europe, verifying a supplier’s quality control measures is crucial. Here are some actionable steps:
- Conduct Supplier Audits: Regular audits help assess the supplier’s adherence to quality standards and manufacturing processes.
- Request Quality Reports: Suppliers should provide documentation of their quality control measures, including test results and compliance certificates.
- Third-Party Inspections: Engaging third-party inspection services can provide an unbiased assessment of the supplier’s manufacturing processes and quality control systems.
- Certifications Verification: Ensure that the supplier possesses relevant certifications, such as ISO and API, to validate their commitment to quality.
What Are the Challenges in Quality Control for International B2B Buyers?
International B2B buyers face unique challenges when dealing with quality control, including:
- Regulatory Differences: Varying standards across countries can complicate compliance and quality assurance processes.
- Communication Barriers: Language and cultural differences may hinder effective communication regarding quality expectations.
- Logistical Issues: Shipping delays or damage can impact the quality of products received.
To mitigate these challenges, B2B buyers should establish clear communication channels, understand the regulatory landscape, and consider local partnerships to facilitate smoother transactions.
Conclusion: Ensuring Quality in Ball Valve Manufacturing
In conclusion, understanding the manufacturing processes and quality assurance standards is essential for B2B buyers looking to procure ball valves. By focusing on material preparation, forming techniques, assembly, finishing processes, and robust quality control measures, buyers can ensure they source high-quality products that meet international standards. Implementing thorough verification processes will further enhance the reliability of suppliers and the quality of the valves purchased.
Practical Sourcing Guide: A Step-by-Step Checklist for ‘ball valve manufacturer’
The following is a practical sourcing guide designed for international B2B buyers looking to procure ball valves. This checklist will help streamline the process, ensuring that all critical factors are considered for successful procurement.
Step 1: Define Your Technical Specifications
Establishing clear technical specifications is essential for ensuring that the ball valves meet your operational requirements. Consider factors such as pressure ratings, size, material compatibility, and intended application. For example, if the valves are to be used in a corrosive environment, materials like stainless steel or specialized alloys may be necessary.
Step 2: Conduct Market Research to Identify Potential Suppliers
Researching the market helps you identify reputable ball valve manufacturers. Look for suppliers with a strong presence in your target regions, such as Africa, South America, the Middle East, and Europe. Utilize industry-specific directories, trade shows, and online platforms to create a list of potential suppliers.
Step 3: Verify Supplier Certifications and Compliance
Ensure that potential suppliers hold relevant certifications and comply with international standards, such as ISO 9001 for quality management and API standards for oil and gas applications. Certifications are indicators of a manufacturer’s commitment to quality and reliability. Additionally, check for compliance with local regulations in your purchasing region to avoid legal issues.
Step 4: Evaluate Supplier Experience and Reputation
Assess the experience and reputation of potential suppliers by reviewing case studies and client testimonials. Companies with a proven track record in your specific industry will likely understand your needs better. Additionally, inquire about their experience with similar projects to gauge their capability.
Step 5: Request Samples and Conduct Quality Testing
Before finalizing your order, request samples to evaluate the quality of the ball valves. Conduct rigorous testing to ensure they meet your technical specifications and performance standards. This step minimizes the risk of receiving subpar products that could lead to operational disruptions.
Step 6: Negotiate Terms and Conditions
Once you have selected a supplier, negotiate the terms and conditions of your purchase. Discuss pricing, payment terms, delivery schedules, and warranty provisions. Ensure that all agreements are documented in a contract to protect both parties and clarify expectations.
Step 7: Establish a Communication Plan
Effective communication is crucial throughout the procurement process. Set up regular check-ins with the supplier to monitor progress and address any issues that may arise. Establishing a clear communication plan helps ensure that both parties remain aligned on expectations and timelines.
By following these steps, international B2B buyers can effectively navigate the procurement of ball valves, ensuring they select the right manufacturer to meet their specific needs. Each step is designed to minimize risks and enhance the chances of successful sourcing.
Comprehensive Cost and Pricing Analysis for ball valve manufacturer Sourcing
What Are the Key Cost Components in Ball Valve Manufacturing?
When sourcing ball valves, understanding the cost structure is vital for international B2B buyers. The costs can be broadly categorized into several components:
-
Materials: The choice of materials significantly affects the price. Common materials include stainless steel, brass, and PVC. Higher-grade materials, while more expensive, offer better durability and corrosion resistance, which can be essential in specific applications.
-
Labor: Labor costs can vary widely depending on the region. For example, labor costs in Southeast Asia may be lower than those in Europe or North America. This variance can impact the overall pricing structure of the ball valves.
-
Manufacturing Overhead: This includes costs associated with factory operations, such as utilities, equipment maintenance, and administrative expenses. Efficient manufacturing processes can help reduce these overhead costs, which can be reflected in competitive pricing.
-
Tooling: Tooling costs are associated with the initial setup for manufacturing specific valve designs. Custom tooling can increase upfront costs but is often necessary for specialized applications.
-
Quality Control (QC): Ensuring that ball valves meet industry standards and customer specifications requires a robust QC process, which adds to the overall cost. Certifications such as ISO or API can influence both the cost and the perceived value of the product.
-
Logistics: Transportation and shipping costs can vary based on the distance from the manufacturer to the buyer, as well as the chosen shipping method. Incoterms can play a critical role in defining who bears these costs.
-
Margin: Manufacturers typically add a profit margin to cover their costs and ensure profitability. This margin can vary based on market competition and the perceived value of the product.
How Do Price Influencers Affect Ball Valve Sourcing?
Several factors can influence the pricing of ball valves:
-
Volume/MOQ (Minimum Order Quantity): Larger orders often result in lower per-unit costs due to economies of scale. Buyers should negotiate MOQs that align with their needs to optimize costs.
-
Specifications and Customization: Custom designs or features can increase costs. Buyers must clearly define their requirements to avoid unexpected charges.
-
Materials: The choice of materials directly impacts pricing. Buyers should assess the trade-off between cost and quality to ensure the selected material meets application requirements.
-
Quality and Certifications: Valves that meet higher quality standards or possess specific certifications may incur higher costs. However, these can lead to long-term savings through reduced failure rates and maintenance.
-
Supplier Factors: The reputation and reliability of the supplier can influence pricing. Established manufacturers may charge more due to their proven track record, but they may also offer better support and warranty options.
-
Incoterms: Understanding shipping terms is crucial. Incoterms dictate the responsibilities of buyers and sellers regarding shipping costs and risks, which can significantly impact total expenses.
What Are Effective Buyer Tips for Cost-Efficiency in Ball Valve Sourcing?
To maximize cost-efficiency when sourcing ball valves, consider the following strategies:
-
Negotiate Prices: Leverage your order volume and commitment to negotiate better pricing terms with suppliers. Building long-term relationships can also lead to more favorable terms.
-
Evaluate Total Cost of Ownership (TCO): Look beyond the initial purchase price. Consider maintenance, potential downtime, and replacement costs. A lower-priced valve may end up being more expensive in the long run if it requires frequent replacements.
-
Understand Pricing Nuances for International Buyers: Buyers from Africa, South America, the Middle East, and Europe should be aware of regional pricing trends and economic conditions that can affect costs. For instance, currency fluctuations can impact pricing, so securing contracts in stable currencies may mitigate this risk.
-
Leverage Local Suppliers: Whenever possible, sourcing from local manufacturers can reduce shipping costs and lead times. This is particularly beneficial for businesses operating in regions with developed manufacturing sectors.
-
Request Sample Valves: Before committing to large orders, request samples to assess quality. This helps in making informed decisions and avoids costly mistakes.
Final Thoughts on Ball Valve Pricing
While this analysis provides a framework for understanding the costs and pricing of ball valves, actual prices can vary widely based on numerous factors. It is essential for buyers to conduct thorough research and engage in detailed discussions with suppliers to obtain accurate pricing information tailored to their specific needs.
Alternatives Analysis: Comparing ball valve manufacturer With Other Solutions
Understanding Alternative Solutions to Ball Valve Manufacturers
In the industrial sector, selecting the right valve solution is crucial for operational efficiency and cost management. Ball valves are widely used due to their reliability and performance, but alternative technologies can also meet similar needs. This section will compare ball valve manufacturers with two viable alternatives: butterfly valves and gate valves. By analyzing these options, international B2B buyers can make informed decisions based on their specific requirements.
Comparison Aspect | Ball Valve Manufacturer | Butterfly Valve | Gate Valve |
---|---|---|---|
Performance | High flow efficiency; suitable for on/off control | Moderate flow efficiency; used in throttling | High flow efficiency; excellent for isolation |
Cost | Generally higher initial investment | Lower initial cost | Moderate initial cost |
Ease of Implementation | Requires skilled installation | Easier to install; less space needed | Requires skilled installation |
Maintenance | Low maintenance; durable materials | Moderate maintenance; seals may wear | Moderate maintenance; can become stuck |
Best Use Case | Ideal for quick shut-off in high-pressure applications | Suitable for large pipelines and low-pressure systems | Best for isolation in systems where flow is rarely changed |
What Are the Pros and Cons of Butterfly Valves?
Butterfly valves are a popular alternative due to their compact design and cost-effectiveness. They operate by rotating a disc to control flow, which allows for quick actuation and minimal pressure drop. However, while they are great for throttling applications, they may not perform as well as ball valves in high-pressure environments. Their sealing mechanism can wear over time, leading to potential leaks if not properly maintained.
How Do Gate Valves Compare?
Gate valves are designed primarily for on/off control, providing an unobstructed flow path when fully open. They are often used in applications where a tight seal is required. The advantage of gate valves is their ability to handle high flow rates and pressure; however, they require more space for installation compared to ball and butterfly valves. Maintenance can be moderate, as the gate can become stuck if not operated regularly, which might lead to operational delays.
Choosing the Right Valve Solution for Your Needs
When selecting between ball valves and their alternatives, B2B buyers should evaluate their specific operational requirements, including flow rates, pressure conditions, and installation constraints. Ball valves excel in high-pressure applications where quick shut-off is essential. In contrast, butterfly valves may be more suitable for larger pipelines with lower pressure, while gate valves are ideal for applications requiring infrequent flow adjustments. By considering these factors, buyers can select the valve solution that aligns with their operational goals and budget constraints.
Essential Technical Properties and Trade Terminology for ball valve manufacturer
What Are the Essential Technical Properties of Ball Valves for B2B Buyers?
Understanding the technical specifications of ball valves is crucial for B2B buyers, especially when sourcing for industries such as oil and gas, water treatment, and manufacturing. Here are some key properties to consider:
1. Material Grade
The material grade of a ball valve significantly influences its durability and corrosion resistance. Common materials include stainless steel, carbon steel, and brass. For instance, stainless steel (like ASTM A351 CF8M) is often preferred for its resistance to high temperatures and corrosive environments, making it ideal for chemical processing applications. Buyers should assess the compatibility of the material with the fluids being controlled to prevent premature failure.
2. Pressure Rating
Pressure rating, often measured in PSI (pounds per square inch), indicates the maximum pressure a valve can withstand. This specification is crucial for ensuring that the valve can handle the operational pressures of the system without leaking or failing. For example, a valve rated for 150 PSI may not be suitable for high-pressure applications in oil and gas sectors where pressures can exceed 500 PSI. Selecting the correct pressure rating ensures operational efficiency and safety.
3. Temperature Range
Ball valves operate within specific temperature ranges, usually defined in degrees Fahrenheit or Celsius. Understanding the temperature limits is vital, as extreme temperatures can affect the valve’s performance and lifespan. For example, valves made from plastic materials may degrade at high temperatures, while metal valves can withstand more extreme conditions. Buyers must match the valve’s temperature range with their operational environment to maintain system integrity.
4. End Connection Type
Ball valves come with various end connection types, including threaded, flanged, and welded. The choice of end connection impacts the ease of installation and the compatibility with existing piping systems. For instance, flanged connections are often used in larger pipelines due to their robust design, while threaded connections are common in smaller applications. Understanding the required connection type helps streamline installation and reduce costs.
5. Tolerance and Dimensions
Tolerance refers to the allowable variation in the valve’s dimensions, which is critical for ensuring proper fit and function within a system. Standard tolerances can affect how well the valve seals and operates under pressure. Buyers should ensure that the dimensions and tolerances meet industry standards to guarantee compatibility with their specific applications.
What Are Common Trade Terms Used in the Ball Valve Industry?
Familiarizing oneself with industry jargon is essential for effective communication and negotiation in the B2B sphere. Here are several key terms:
1. OEM (Original Equipment Manufacturer)
An OEM refers to a company that produces components that are used in another company’s end product. For ball valves, an OEM would manufacture the valves that are integrated into larger systems or products. Understanding OEM relationships can help buyers ensure they are sourcing high-quality components that meet industry standards.
2. MOQ (Minimum Order Quantity)
MOQ is the smallest quantity of a product that a supplier is willing to sell. This term is critical for budgeting and inventory management. For instance, if a manufacturer has an MOQ of 100 units for a specific ball valve, buyers must consider whether they can meet this requirement without overextending their resources.
3. RFQ (Request for Quotation)
An RFQ is a document sent to suppliers to solicit price quotes for specific products. In the context of ball valves, an RFQ helps buyers compare prices and specifications from different manufacturers, enabling informed purchasing decisions. Providing detailed specifications in an RFQ can lead to more accurate quotes.
4. Incoterms (International Commercial Terms)
Incoterms are international rules that define the responsibilities of buyers and sellers in international transactions. For ball valve purchases, understanding Incoterms like FOB (Free on Board) or CIF (Cost, Insurance, and Freight) is vital for clarifying shipping costs and responsibilities, which can significantly impact the total cost of acquisition.
5. Lead Time
Lead time refers to the time it takes from placing an order to receiving the product. This term is particularly important for B2B buyers in industries with tight project timelines. Knowing the lead time for ball valves can help in planning and ensuring that operations are not delayed due to waiting for essential components.
By grasping these technical properties and trade terms, international B2B buyers can make more informed decisions, ensuring that they select the right ball valves for their applications while navigating the complexities of global trade effectively.
Navigating Market Dynamics and Sourcing Trends in the ball valve manufacturer Sector
What Are the Key Market Dynamics and Trends in the Ball Valve Manufacturing Sector?
The ball valve manufacturing sector is experiencing significant growth, driven by several global factors. Increased industrialization in emerging markets, particularly in Africa and South America, is creating a higher demand for reliable fluid control systems. Additionally, the push towards automation and digital transformation in manufacturing processes is leading to the adoption of smart valves, which can be monitored and controlled remotely. These technological advancements not only enhance efficiency but also contribute to reducing operational costs, making them attractive for B2B buyers across various industries.
Emerging trends also include the integration of Industry 4.0 technologies, such as IoT and AI, into ball valve manufacturing. This shift allows manufacturers to optimize their production processes and improve product quality through real-time data analysis. International B2B buyers, particularly from regions like the Middle East and Europe, should consider suppliers who invest in these technologies to ensure they receive high-quality, innovative products. Furthermore, the focus on supply chain resilience has led buyers to seek local suppliers who can provide agility and quicker response times, particularly in the face of global disruptions.
How Is Sustainability Shaping the Sourcing Trends for Ball Valve Manufacturers?
Sustainability is becoming a cornerstone of sourcing strategies in the ball valve manufacturing sector. As environmental regulations tighten globally, manufacturers are increasingly held accountable for their environmental impact. This shift is prompting B2B buyers to prioritize suppliers who demonstrate a commitment to sustainable practices. Key considerations include the use of eco-friendly materials, energy-efficient manufacturing processes, and adherence to certifications such as ISO 14001 for environmental management.
Moreover, ethical sourcing has gained traction among international buyers. Ensuring that supply chains are free from labor exploitation and that materials are responsibly sourced is vital for maintaining corporate social responsibility (CSR) standards. Manufacturers are responding by adopting transparency in their supply chains, often providing documentation to prove their sustainability claims. B2B buyers should evaluate potential suppliers based on their sustainability certifications and track records in responsible sourcing to align with their own corporate values and consumer expectations.
What Is the Historical Context of Ball Valve Manufacturing and Its Relevance Today?
The ball valve has a storied history dating back to the early 20th century, initially designed to improve the efficiency of fluid flow in pipelines. Over the decades, advancements in materials and manufacturing techniques have significantly enhanced the performance and reliability of ball valves. Innovations such as the development of corrosion-resistant alloys and automated valve control systems have made these products essential in various industries, including oil and gas, water treatment, and chemical processing.
Understanding this historical context is crucial for B2B buyers, as it highlights the evolution of product standards and the importance of selecting manufacturers that have adapted to technological advancements. Buyers should seek out suppliers who not only understand the legacy of ball valve manufacturing but also demonstrate a commitment to innovation and quality assurance, ensuring that they remain competitive in today’s fast-paced market.
Frequently Asked Questions (FAQs) for B2B Buyers of ball valve manufacturer
-
How do I choose the right ball valve manufacturer for my needs?
Selecting the right ball valve manufacturer involves assessing several key factors. First, evaluate their industry experience and reputation within your specific sector. Look for manufacturers with certifications, such as ISO 9001, which indicate adherence to quality management standards. Additionally, consider their production capabilities, including the variety of materials used (e.g., stainless steel, brass) and customization options. Request samples to test product quality and ensure they can meet your delivery timelines. Finally, check reviews and testimonials from other international buyers to gauge reliability and service. -
What are the typical lead times for ball valve manufacturing and delivery?
Lead times for ball valve manufacturing can vary significantly based on order complexity and manufacturer capacity. Generally, standard orders may take anywhere from 4 to 12 weeks, while customized valves can extend this period to 16 weeks or more. Factors such as material availability, production schedules, and shipping logistics also play critical roles. For international buyers, it’s advisable to communicate your timeline expectations upfront and seek manufacturers who provide clear timelines and options for expedited processing. -
What are the minimum order quantities (MOQs) for ball valves?
Minimum order quantities (MOQs) for ball valves can vary by manufacturer and order type. Standard MOQs typically range from 100 to 500 units, depending on the valve size and specifications. Custom-designed valves may have higher MOQs due to the complexity of production. When sourcing from international manufacturers, inquire about their MOQ policies, as some may offer flexibility for first-time buyers or bulk orders. Understanding MOQs is essential for budgeting and inventory planning, especially for businesses in Africa, South America, and the Middle East. -
What payment terms should I expect when sourcing ball valves internationally?
Payment terms for international ball valve purchases can differ widely among manufacturers. Common terms include payment in advance, a 30% deposit with the balance due before shipment, or net 30/60 days after delivery. It’s crucial to negotiate terms that align with your cash flow and risk management strategies. Be wary of manufacturers requiring full payment upfront, especially if they lack a proven track record. Additionally, consider using secure payment methods such as letters of credit to protect your investment during international transactions. -
How can I ensure quality assurance when purchasing ball valves?
To ensure quality assurance when purchasing ball valves, start by selecting manufacturers that have robust quality control processes in place. Request documentation such as material certifications, inspection reports, and compliance with international standards like API 6D or ASME. Consider arranging for third-party inspections or audits before shipment to verify product quality. Establishing clear communication about your quality expectations and conducting regular follow-ups can also help maintain standards throughout the production process. -
What customization options are available for ball valves?
Many ball valve manufacturers offer a range of customization options to meet specific operational needs. Common customization includes variations in size, material, pressure ratings, and end connections (e.g., flanged, threaded). Additionally, you can request specific coatings for corrosion resistance or modifications for specific applications, such as high-temperature or cryogenic environments. When discussing customization, provide detailed specifications and consider requesting prototypes to ensure the final product meets your performance requirements. -
What logistics considerations should I keep in mind when importing ball valves?
When importing ball valves, logistics considerations are crucial to ensure timely and cost-effective delivery. First, evaluate shipping options, including air freight for urgent needs or sea freight for larger orders. Understand the customs regulations and duties applicable in your country, as these can significantly impact total costs. It’s advisable to work with logistics providers experienced in handling industrial equipment and to confirm that your manufacturer can provide necessary shipping documents. Proper planning can prevent delays and additional expenses. -
How do I vet a ball valve manufacturer before placing an order?
Vetting a ball valve manufacturer is essential for mitigating risks. Start by researching their industry reputation through online reviews and industry forums. Verify their certifications and compliance with international standards to ensure they maintain quality. Request references from previous clients, particularly those in similar markets or industries. Additionally, consider visiting their facility if possible, or use virtual meetings to assess their capabilities and professionalism. Establishing clear communication and responsiveness during this vetting process can also be indicative of their reliability as a supplier.
Important Disclaimer & Terms of Use
⚠️ Important Disclaimer
The information provided in this guide, including content regarding manufacturers, technical specifications, and market analysis, is for informational and educational purposes only. It does not constitute professional procurement advice, financial advice, or legal advice.
While we have made every effort to ensure the accuracy and timeliness of the information, we are not responsible for any errors, omissions, or outdated information. Market conditions, company details, and technical standards are subject to change.
B2B buyers must conduct their own independent and thorough due diligence before making any purchasing decisions. This includes contacting suppliers directly, verifying certifications, requesting samples, and seeking professional consultation. The risk of relying on any information in this guide is borne solely by the reader.
Strategic Sourcing Conclusion and Outlook for ball valve manufacturer
What Are the Key Takeaways for B2B Buyers in the Ball Valve Industry?
In conclusion, strategic sourcing in the ball valve manufacturing sector is essential for international B2B buyers aiming to enhance operational efficiency and ensure quality. By prioritizing suppliers who demonstrate a commitment to innovation, sustainability, and compliance with international standards, companies can mitigate risks and foster long-term partnerships. Buyers from Africa, South America, the Middle East, and Europe should focus on evaluating suppliers based on their technological capabilities, production flexibility, and responsiveness to market demands.
How Can International Buyers Prepare for Future Trends in Ball Valve Manufacturing?
Looking ahead, the ball valve industry is expected to evolve significantly, driven by advancements in technology and increasing regulatory demands. Buyers should remain vigilant about emerging trends such as automation in manufacturing processes and the integration of smart technologies into valve systems. This proactive approach will not only enhance procurement strategies but also position businesses to leverage new opportunities in various sectors, including oil and gas, water management, and industrial processes.
What Steps Should Buyers Take to Enhance Their Strategic Sourcing Efforts?
To capitalize on these insights, international buyers are encouraged to engage in continuous market research and supplier assessments. Establishing a robust network of reliable manufacturers will be crucial in navigating future challenges and ensuring a steady supply of high-quality ball valves. By taking these steps, businesses can secure their competitive edge and drive sustainable growth in a dynamic global marketplace.