Discover Top Benefits of an Auto Spare Parts Supplier (2025)
Introduction: Navigating the Global Market for auto spare parts supplier
Navigating the global market for auto spare parts suppliers can be a daunting task for international B2B buyers. The automotive industry is rapidly evolving, and sourcing reliable components that meet both quality and compliance standards has never been more critical. This guide aims to provide comprehensive insights into the world of auto spare parts suppliers, focusing on key challenges such as supplier vetting, cost considerations, and types of components available.
In the following sections, we will explore various categories of auto spare parts, from OEM to aftermarket options, and delve into their applications across different markets. Buyers will learn how to effectively assess suppliers, ensuring they partner with reputable companies that adhere to international standards. Additionally, we will discuss pricing strategies and negotiation tactics tailored for buyers from regions such as Africa, South America, the Middle East, and Europe, including specific insights for markets like the UAE and Poland.
This guide empowers B2B buyers to make informed purchasing decisions, mitigating risks associated with sourcing auto spare parts. By equipping readers with actionable insights and industry best practices, we aim to simplify the procurement process and enhance the overall efficiency of their supply chains. Whether you are a seasoned buyer or new to the automotive sector, understanding the dynamics of the global auto spare parts market is essential for achieving business success.
Understanding auto spare parts supplier Types and Variations
Type Name | Key Distinguishing Features | Primary B2B Applications | Brief Pros & Cons for Buyers |
---|---|---|---|
OEM Suppliers | Original Equipment Manufacturer; provides parts made to manufacturer specifications. | Vehicle assembly, repairs, and maintenance | Pros: High quality, guaranteed fit; Cons: Higher costs, limited options. |
Aftermarket Suppliers | Offers parts that are compatible with OEM standards but are not made by the original manufacturer. | Vehicle repairs, upgrades, and modifications | Pros: Cost-effective, diverse options; Cons: Variable quality, potential compatibility issues. |
Wholesale Distributors | Large-scale suppliers that sell bulk quantities of auto parts to retailers or repair shops. | Retail, fleet maintenance, and service centers | Pros: Lower prices per unit, wide selection; Cons: Minimum order requirements, less personalized service. |
Specialty Suppliers | Focus on specific types of parts (e.g., performance parts, vintage parts). | Niche markets, customization, and restoration projects | Pros: Expert knowledge, tailored solutions; Cons: Limited inventory, potentially higher prices. |
Online Marketplaces | Platforms that connect buyers with various suppliers, often featuring user reviews and ratings. | General purchase, research, and comparison shopping | Pros: Convenience, competitive pricing; Cons: Risk of counterfeit products, variable shipping times. |
What Are the Key Characteristics of OEM Suppliers?
OEM suppliers are known for providing parts that are made specifically for a particular vehicle brand, ensuring high quality and a perfect fit. These suppliers often have contracts with vehicle manufacturers, which means their parts meet strict industry standards. For B2B buyers, especially those in Africa and South America, purchasing from OEM suppliers can guarantee the reliability and longevity of the parts used in vehicle assembly or repairs. However, they may come at a premium price, and buyers should consider their budget and the importance of quality in their purchasing decisions.
How Do Aftermarket Suppliers Differ from OEM Suppliers?
Aftermarket suppliers provide parts that are designed to be compatible with OEM specifications but are produced by third-party manufacturers. This type of supplier is popular among businesses looking for cost-effective solutions without compromising on quality. They offer a wider range of options, making them suitable for various applications, including repairs and vehicle upgrades. However, B2B buyers should be cautious about the variable quality of aftermarket parts and ensure they are purchasing from reputable suppliers to avoid compatibility issues.
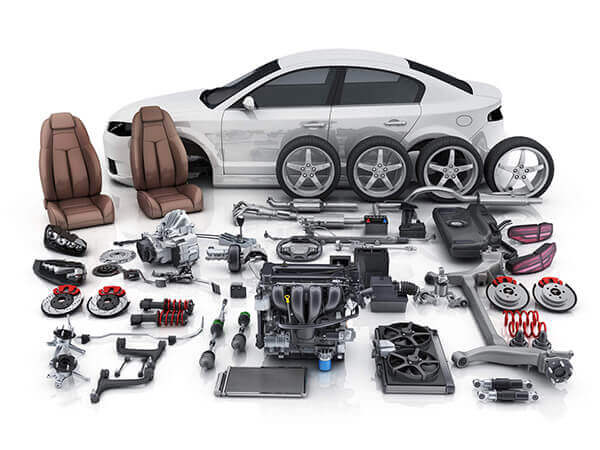
A stock image related to auto spare parts supplier.
What Advantages Do Wholesale Distributors Offer B2B Buyers?
Wholesale distributors play a crucial role in the auto spare parts supply chain by offering bulk quantities at reduced prices. They serve as intermediaries between manufacturers and retailers or repair shops, providing a wide selection of parts. This model is particularly beneficial for businesses with high-volume needs, such as fleet maintenance operations. However, buyers should be aware of minimum order quantities that can affect cash flow and may find the service less personalized compared to smaller suppliers.
Why Should Businesses Consider Specialty Suppliers?
Specialty suppliers focus on specific niches within the auto spare parts market, such as performance enhancements or rare vintage components. These suppliers often possess in-depth knowledge and expertise, making them ideal for businesses looking for customized solutions or restoration projects. While they provide unique products, B2B buyers should evaluate their inventory and pricing, as specialty parts can sometimes be more expensive and less readily available than standard options.
How Do Online Marketplaces Enhance the Purchasing Process for B2B Buyers?
Online marketplaces have revolutionized how B2B buyers acquire auto spare parts by offering a platform where multiple suppliers can list their products. This convenience allows buyers to compare prices, read reviews, and make informed purchasing decisions from the comfort of their offices. However, the risk of counterfeit products and inconsistent shipping times can be drawbacks. Buyers should prioritize established platforms and verify supplier credibility to mitigate these risks while enjoying the benefits of competitive pricing and vast selection.
Related Video: Functions and Classification of Spare Parts Management
Key Industrial Applications of auto spare parts supplier
Industry/Sector | Specific Application of auto spare parts supplier | Value/Benefit for the Business | Key Sourcing Considerations for this Application |
---|---|---|---|
Automotive Manufacturing | Sourcing of OEM parts for assembly lines | Ensures quality and compliance with standards | Supplier certifications, lead times, and pricing |
Fleet Management | Replacement parts for vehicle maintenance | Reduces downtime and maintenance costs | Bulk purchasing options, warranty terms, and delivery times |
Logistics and Transportation | Spare parts for trucks and delivery vehicles | Enhances operational efficiency and reliability | Availability of parts, compatibility, and service support |
Automotive Repair Services | Aftermarket parts for repair shops | Increases customer satisfaction and loyalty | Quality assurance, return policies, and supplier reputation |
Export and Import Businesses | Spare parts for re-export to local markets | Capitalizes on demand in emerging markets | Compliance with local regulations, shipping logistics, and tariffs |
How Are Auto Spare Parts Suppliers Used in Automotive Manufacturing?
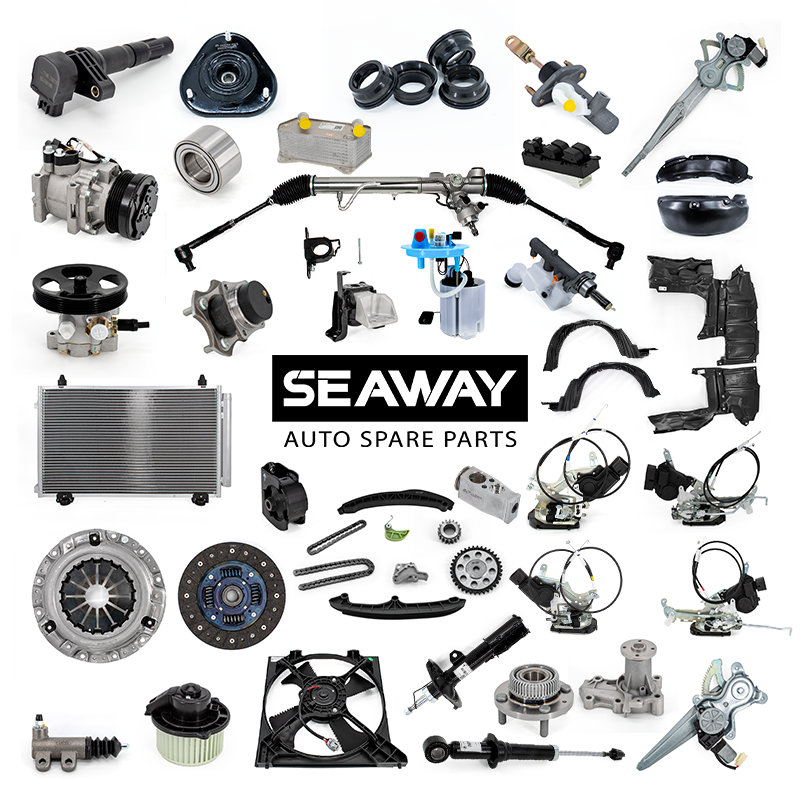
A stock image related to auto spare parts supplier.
In the automotive manufacturing sector, auto spare parts suppliers play a crucial role in sourcing Original Equipment Manufacturer (OEM) parts for assembly lines. These suppliers ensure that the components meet rigorous quality standards and regulatory compliance, which is vital for manufacturers aiming to maintain brand integrity and safety. International buyers, particularly from regions like Africa and South America, must prioritize suppliers with proper certifications and a proven track record in timely deliveries to avoid production delays.
What Are the Benefits of Using Spare Parts in Fleet Management?
For fleet management companies, auto spare parts suppliers provide essential replacement parts that facilitate timely vehicle maintenance. By sourcing high-quality parts, businesses can significantly reduce vehicle downtime, leading to lower maintenance costs and improved operational efficiency. B2B buyers in the Middle East and Europe should focus on suppliers that offer bulk purchasing options and favorable warranty terms, ensuring long-term partnerships that benefit their operational needs.
How Do Spare Parts Impact Logistics and Transportation?
In the logistics and transportation industry, auto spare parts suppliers are vital for maintaining trucks and delivery vehicles. Reliable access to spare parts enhances the efficiency and reliability of transport operations, allowing companies to meet delivery deadlines consistently. Buyers from Europe and Africa should consider the availability of parts and compatibility with their existing fleet when sourcing, as these factors directly affect operational success.
Why Are Spare Parts Important for Automotive Repair Services?
Auto spare parts suppliers are indispensable for automotive repair services, providing aftermarket parts that help shops deliver quality repairs to customers. By ensuring a steady supply of high-quality parts, repair services can enhance customer satisfaction and loyalty, fostering repeat business. Buyers in South America and the Middle East should investigate suppliers’ quality assurance practices and return policies to ensure they can maintain service excellence.
What Should Export and Import Businesses Consider When Sourcing Spare Parts?
For export and import businesses, auto spare parts suppliers are essential for re-exporting to local markets, especially in regions with high demand for specific vehicle types. Sourcing from reliable suppliers allows businesses to capitalize on emerging market trends effectively. International buyers must be aware of compliance with local regulations, shipping logistics, and potential tariffs to optimize their sourcing strategies and minimize costs.
Related Video: Online free car parts catalog & diagrams ! How to use it
3 Common User Pain Points for ‘auto spare parts supplier’ & Their Solutions
Scenario 1: Difficulty in Sourcing Quality Spare Parts
The Problem:
B2B buyers in regions such as Africa and South America often struggle with sourcing quality auto spare parts. Many suppliers provide low-quality products that do not meet industry standards, leading to frequent breakdowns and increased maintenance costs. This problem is exacerbated by a lack of clear product specifications and limited access to reliable supplier reviews. As a result, buyers are left uncertain about which suppliers to trust, causing delays in procurement and potential loss of business.
The Solution:
To effectively source quality auto spare parts, buyers should start by conducting thorough research on potential suppliers. Utilize platforms that provide verified reviews and ratings from other businesses. Establish a clear set of specifications for the parts needed, including OEM standards, to ensure that suppliers understand the quality required. Additionally, consider forming relationships with suppliers who can provide product samples or trial orders. This allows for testing the parts’ compatibility and quality before committing to larger orders. Engaging in industry forums or networking events can also help buyers connect with reputable suppliers who have a proven track record.
Scenario 2: Navigating Complex Customs Regulations
The Problem:
Importing auto spare parts can be a daunting task for B2B buyers, especially in the Middle East and Africa, where customs regulations can be complex and vary significantly by country. Delays in shipping due to customs clearance can disrupt operations and lead to financial losses. Buyers may also face unexpected tariffs and taxes that were not accounted for in the initial procurement cost, complicating budgeting and financial planning.
The Solution:
To navigate complex customs regulations effectively, B2B buyers should invest time in understanding the specific import regulations of their country. This includes researching any tariffs, taxes, and documentation required for importing auto spare parts. Engaging a customs broker or a logistics expert with experience in automotive parts can simplify this process, ensuring that all paperwork is correctly filled out and submitted. Additionally, establishing clear communication with suppliers regarding shipping methods and documentation can prevent delays. It is also beneficial to stay updated on changes in trade agreements or regulations that could impact costs and import procedures.
Scenario 3: Uncertainty in After-Sales Support and Warranty
The Problem:
After-sales support and warranty issues are common pain points for B2B buyers sourcing auto spare parts. Inconsistent warranty terms and lack of reliable customer service from suppliers can lead to uncertainty, especially when parts fail soon after installation. This not only affects operational efficiency but also erodes trust in the supplier, making buyers hesitant to place future orders.
The Solution:
To mitigate concerns regarding after-sales support, buyers should prioritize suppliers who offer clear and comprehensive warranty terms. Before finalizing orders, request detailed documentation on warranty coverage, including conditions, duration, and the process for claiming warranty services. It’s also advisable to inquire about the supplier’s customer service availability and responsiveness. Establishing a direct line of communication with a dedicated account manager can enhance the support experience. Buyers should consider suppliers who have a solid reputation for after-sales service, as evidenced by testimonials or case studies from other businesses. Regular follow-ups with suppliers post-purchase can also help ensure that any issues are addressed promptly, fostering a stronger business relationship.
Strategic Material Selection Guide for auto spare parts supplier
What Are the Key Materials Used in Auto Spare Parts?
When selecting materials for auto spare parts, international B2B buyers must consider various factors, including performance, cost, and regional standards. Below, we analyze four commonly used materials: steel, aluminum, plastic, and rubber. Each material has distinct properties, advantages, and limitations that can significantly impact the final product’s performance and suitability.
How Does Steel Perform as a Material for Auto Spare Parts?
Key Properties: Steel is known for its high tensile strength and durability, making it suitable for high-stress applications. It typically withstands high temperatures and pressures, with corrosion resistance varying based on the specific alloy used.
Pros & Cons: The primary advantage of steel is its strength and durability, which translates to longer-lasting parts. However, it can be heavier than alternatives, which may affect fuel efficiency in vehicles. Additionally, manufacturing complexity can increase with high-grade steel types.
Impact on Application: Steel is commonly used for structural components like frames and suspension parts due to its robustness. However, it may not be suitable for components exposed to corrosive environments unless treated or alloyed appropriately.
Considerations for International Buyers: Buyers from regions like Europe and the Middle East should ensure compliance with standards such as ASTM or DIN for steel grades. In Africa and South America, sourcing from local suppliers who can provide certified materials may also be crucial to reduce lead times.
What Are the Advantages of Aluminum in Auto Spare Parts?
Key Properties: Aluminum is lightweight and has excellent corrosion resistance, making it ideal for parts that require reduced weight without sacrificing strength. It typically performs well in a variety of temperatures.
Pros & Cons: The main advantage of aluminum is its weight-saving potential, which can enhance vehicle performance and fuel efficiency. However, aluminum parts can be more expensive and may require specialized manufacturing processes, such as welding or casting.
Impact on Application: Aluminum is often used for engine components, wheels, and body panels. Its compatibility with various media makes it versatile, but care must be taken to avoid galvanic corrosion when paired with dissimilar metals.
Considerations for International Buyers: Buyers in Europe may prefer aluminum due to stringent fuel efficiency regulations. Compliance with international standards such as JIS for aluminum alloys is essential for maintaining quality and performance.
How Do Plastics Fit into the Auto Spare Parts Landscape?
Key Properties: Plastics are known for their lightweight, moldability, and resistance to corrosion and chemicals. They can be engineered for specific applications, offering varying degrees of strength and flexibility.
Pros & Cons: The primary advantage of plastics is their low cost and ease of manufacturing, allowing for complex shapes and designs. However, they may not offer the same level of durability as metals, especially under extreme conditions.
Impact on Application: Plastics are commonly used in interior components, dashboards, and non-structural parts. They are also suitable for applications requiring chemical resistance, such as fuel tanks.
Considerations for International Buyers: Buyers from regions like South America and Africa should focus on sourcing plastics that meet local environmental regulations. Understanding material certifications and standards is vital for ensuring product quality.
What Role Does Rubber Play in Auto Spare Parts?
Key Properties: Rubber is flexible, resilient, and has excellent vibration-damping properties. It can withstand a range of temperatures and is often used in sealing applications.
Pros & Cons: The main advantage of rubber is its ability to absorb shocks and vibrations, enhancing comfort in vehicles. However, it can degrade over time due to exposure to UV light and ozone, limiting its lifespan.
Impact on Application: Rubber is widely used in seals, gaskets, and tires. Its compatibility with various media makes it suitable for applications involving fluids, but buyers must consider the specific rubber type for different environments.
Considerations for International Buyers: Buyers in the Middle East should be aware of the effects of extreme temperatures on rubber performance. Compliance with local standards and certifications is essential to ensure quality and safety.
Summary Table of Material Selection for Auto Spare Parts
Material | Typical Use Case for auto spare parts supplier | Key Advantage | Key Disadvantage/Limitation | Relative Cost (Low/Med/High) |
---|---|---|---|---|
Steel | Structural components (frames, suspension) | High strength and durability | Heavier than alternatives, complex manufacturing | Medium |
Aluminum | Engine components, wheels, body panels | Lightweight, excellent corrosion resistance | Higher cost, specialized manufacturing required | High |
Plastic | Interior components, dashboards | Low cost, easy to mold | Less durable than metals, may degrade | Low |
Rubber | Seals, gaskets, tires | Excellent vibration damping | Can degrade over time, limited lifespan | Medium |
This comprehensive analysis provides international B2B buyers with actionable insights into material selection for auto spare parts, ensuring informed decisions that align with both performance and regional standards.
In-depth Look: Manufacturing Processes and Quality Assurance for auto spare parts supplier
What Are the Main Stages in the Manufacturing Processes for Auto Spare Parts?
Understanding the manufacturing processes of auto spare parts is crucial for B2B buyers seeking quality and reliability. The production of these components typically involves four main stages: material preparation, forming, assembly, and finishing.
-
Material Preparation: This initial stage involves selecting the right materials based on the specifications required for the spare parts. Common materials include metals like steel and aluminum, plastics, and composites. Suppliers must ensure that raw materials meet industry standards to avoid defects during production.
-
Forming: In this stage, the prepared materials undergo various processes such as casting, forging, stamping, or machining. Techniques like CNC machining are prevalent for precision parts, while die casting is often used for complex shapes. Each method has its own advantages and is chosen based on the part’s design requirements and production volume.
-
Assembly: After forming, parts are assembled to create the final product. This can involve manual labor or automated processes, depending on the complexity and scale of production. Quality control checks are essential at this stage to ensure that all components fit together correctly.
-
Finishing: The final stage involves surface treatments such as painting, coating, or polishing. These processes enhance the durability and aesthetic appeal of the parts. It is also the last opportunity to inspect for any defects before the parts are packaged and shipped.
Which Quality Assurance Standards Are Relevant for Auto Spare Parts Suppliers?
Quality assurance is a critical aspect of the manufacturing process, particularly for international B2B buyers who require consistent quality across different suppliers. Several international and industry-specific standards are important:
-
ISO 9001: This is a widely recognized quality management standard that outlines requirements for a quality management system (QMS). Suppliers certified to ISO 9001 demonstrate their commitment to quality and customer satisfaction.
-
CE Marking: For products sold in the European Economic Area (EEA), CE marking indicates conformity with health, safety, and environmental protection standards. It is essential for suppliers targeting European markets.
-
API Standards: For spare parts used in the oil and gas industry, the American Petroleum Institute (API) sets standards that ensure the performance and reliability of components.
What Are the Key Quality Control Checkpoints in Manufacturing?
Implementing robust quality control (QC) checkpoints throughout the manufacturing process helps ensure that defects are identified and addressed early. The typical QC checkpoints include:
-
Incoming Quality Control (IQC): This involves inspecting raw materials upon arrival at the facility. Suppliers conduct tests to verify that materials meet specified standards before they enter the production line.
-
In-Process Quality Control (IPQC): Throughout the manufacturing process, inspections are performed to monitor production parameters and ensure that the parts are being produced according to specifications. This can include dimensional checks and functional tests.
-
Final Quality Control (FQC): Before packaging and shipping, a final inspection is conducted to confirm that the finished product meets all quality standards. This may include visual inspections, functional tests, and performance evaluations.
What Common Testing Methods Are Used in Quality Assurance?
B2B buyers should be aware of the various testing methods employed by auto spare parts suppliers to ensure product quality:
-
Dimensional Inspection: This method verifies that the dimensions of the parts meet the specified tolerances using tools such as calipers and micrometers.
-
Material Testing: Suppliers conduct tests like tensile strength, hardness, and fatigue tests to confirm that the materials used can withstand operational stresses.
-
Functional Testing: This involves simulating the operating conditions of the parts to ensure they perform as expected in real-world applications.
-
Non-Destructive Testing (NDT): Techniques such as ultrasonic testing, X-ray, and magnetic particle inspection are used to detect defects without damaging the parts.
How Can B2B Buyers Verify Supplier Quality Control?
For international B2B buyers, verifying the quality control measures of potential suppliers is essential to mitigate risks associated with product defects. Here are several methods to do so:
-
Supplier Audits: Conducting audits of suppliers’ manufacturing facilities can provide insights into their quality control processes. Audits allow buyers to assess compliance with international standards and identify areas for improvement.
-
Quality Reports: Requesting detailed quality reports from suppliers can help buyers understand the QC measures in place and the results of recent inspections and tests.
-
Third-Party Inspections: Engaging third-party inspection services can offer an unbiased evaluation of the supplier’s quality processes and product reliability. This is particularly useful for buyers in regions where they cannot easily conduct on-site visits.
What Are the Quality Control Nuances for International B2B Buyers?
Navigating the complexities of quality control can be particularly challenging for international B2B buyers. Here are some nuances to consider:
-
Cultural Differences: Different regions may have varying attitudes toward quality and compliance. Understanding local practices and expectations is essential for effective communication and negotiation.
-
Regulatory Compliance: Buyers must ensure that their suppliers comply with local regulations and standards, which can vary significantly between regions such as Africa, South America, the Middle East, and Europe.
-
Supply Chain Transparency: Increasingly, buyers are demanding greater transparency in the supply chain. Suppliers should provide documentation and traceability for all materials and processes used in production.
By understanding these aspects of manufacturing processes and quality assurance, international B2B buyers can make informed decisions when selecting auto spare parts suppliers, ensuring they receive products that meet their quality and performance expectations.
Practical Sourcing Guide: A Step-by-Step Checklist for ‘auto spare parts supplier’
In the rapidly evolving automotive industry, sourcing auto spare parts from reliable suppliers is crucial for maintaining operational efficiency and ensuring product quality. This checklist provides international B2B buyers, especially from Africa, South America, the Middle East, and Europe, with a structured approach to finding the right auto spare parts supplier.
Step 1: Define Your Technical Specifications
Begin by clearly outlining the technical specifications of the auto spare parts you need. This includes dimensions, materials, compliance standards, and performance criteria. Having precise specifications helps in communicating your requirements to potential suppliers and ensures that you receive products that meet your quality and compatibility standards.
- Considerations:
- Identify the specific models and brands of vehicles for which you require parts.
- Gather data on existing parts to assess compatibility and performance expectations.
Step 2: Conduct Market Research for Potential Suppliers
Research the market to identify potential suppliers that specialize in auto spare parts. Utilize online platforms, industry forums, and trade shows to gather a list of candidates.
- Why It’s Important:
- A broad list of suppliers provides options and competitive pricing.
- Industry forums and trade shows can offer insights into supplier reputation and product quality.
Step 3: Verify Supplier Certifications
Before proceeding with any supplier, verify their certifications and compliance with international quality standards, such as ISO 9001. This is essential to ensure that the supplier adheres to quality management practices.
- Action Items:
- Request copies of relevant certifications.
- Check for compliance with local regulations in your purchasing region.
Step 4: Evaluate Supplier Reputation and Experience
Assess the reputation and experience of potential suppliers. Look for reviews, testimonials, and case studies from other businesses in your industry.
- Key Points:
- A supplier with a proven track record is likely to provide reliable products and services.
- Engage with other buyers to get firsthand accounts of their experiences with the supplier.
Step 5: Request Samples and Product Specifications
Before making a bulk purchase, request samples of the auto spare parts. This allows you to evaluate the quality and compatibility of the parts with your requirements.
- Why This Matters:
- Testing samples helps mitigate risks associated with quality issues.
- It also provides an opportunity to assess the supplier’s responsiveness and customer service.
Step 6: Negotiate Terms and Conditions
Once you have selected a supplier, negotiate the terms and conditions of the purchase. This includes pricing, payment terms, delivery schedules, and warranty policies.
- Considerations:
- Aim for clear communication to avoid misunderstandings.
- Ensure that all agreements are documented to protect your interests.
Step 7: Establish a Long-Term Relationship
Consider establishing a long-term relationship with your chosen supplier. Building a strategic partnership can lead to better pricing, priority service, and collaborative innovation.
- Benefits:
- Long-term relationships can enhance supply chain stability.
- Suppliers are more likely to prioritize your needs and offer tailored solutions.
By following this checklist, B2B buyers can streamline their sourcing process for auto spare parts, ensuring that they choose suppliers who meet their technical, quality, and service requirements effectively.
Comprehensive Cost and Pricing Analysis for auto spare parts supplier Sourcing
What Are the Key Cost Components in Auto Spare Parts Supplier Sourcing?
When sourcing auto spare parts, understanding the cost structure is crucial for international B2B buyers. The primary components of cost include:
- Materials: The choice of raw materials significantly affects the cost. For instance, high-quality steel or specialized polymers may increase the expense but offer better durability and performance.
- Labor: Labor costs vary by region and can impact overall pricing. In countries with higher wages, such as those in Europe, labor-intensive processes may lead to increased costs.
- Manufacturing Overhead: This encompasses all indirect costs associated with production, including utilities and facility costs. Efficient production processes can help minimize these overheads.
- Tooling: Initial tooling costs can be substantial, especially for custom parts. Buyers should consider whether the supplier can absorb these costs or if they will be passed on.
- Quality Control (QC): Effective QC processes ensure that parts meet specifications, but they add to the overall cost. Buyers should weigh the importance of quality against the potential cost savings.
- Logistics: Shipping and handling expenses vary widely depending on distance, mode of transport, and shipping frequency. Buyers should explore options to optimize logistics costs.
- Margin: Suppliers typically include a profit margin in their pricing. Understanding industry standards for margins can help buyers negotiate better deals.
How Do Price Influencers Affect Auto Spare Parts Costs?
Several factors influence the pricing of auto spare parts, particularly for international transactions:
- Volume and Minimum Order Quantity (MOQ): Larger orders often qualify for discounts, making it essential for buyers to assess their purchasing needs and negotiate favorable MOQs.
- Specifications and Customization: Customized parts can incur additional costs due to the need for specialized manufacturing processes. Buyers should clearly define their requirements to avoid unexpected charges.
- Materials and Quality Certifications: Parts made from premium materials or with specific certifications (like ISO or IATF) may command higher prices. Buyers should evaluate whether these certifications align with their quality standards and customer expectations.
- Supplier Factors: The reputation and reliability of the supplier can affect pricing. Established suppliers may charge a premium for their experience and service quality.
- Incoterms: Understanding Incoterms is vital for international buyers, as they dictate shipping responsibilities and costs. Choosing the right terms can lead to significant savings.
What Are the Best Negotiation Strategies for International Buyers?
Effective negotiation is key to achieving cost-efficiency in auto spare parts sourcing:
- Research and Benchmarking: Before negotiations, research market prices and benchmark against competitors. This knowledge empowers buyers to negotiate confidently.
- Focus on Total Cost of Ownership (TCO): Consider all costs associated with a part, including maintenance and logistics, rather than just the purchase price. This holistic view helps in evaluating suppliers.
- Flexibility in Specifications: If possible, be open to alternative materials or designs that may lower costs. Flexibility can lead to substantial savings.
- Build Long-Term Relationships: Establishing a strong relationship with suppliers can lead to better pricing, priority service, and exclusive deals in the long run.
What Should Buyers Keep in Mind Regarding Pricing Nuances?
International B2B buyers, particularly from regions like Africa, South America, the Middle East, and Europe, should be aware of specific pricing nuances:
- Currency Fluctuations: Be mindful of exchange rates when negotiating prices in different currencies, as fluctuations can impact overall costs.
- Import Duties and Taxes: Understand the import regulations and potential duties in your country, as these can significantly add to the total cost of procurement.
- Cultural Differences: Negotiation styles can vary across cultures. Familiarizing yourself with local business etiquette can facilitate smoother negotiations.
Disclaimer on Indicative Prices
Prices for auto spare parts can vary widely based on the factors discussed above. It’s essential to seek detailed quotes from multiple suppliers and to consider all cost components when making sourcing decisions.
Alternatives Analysis: Comparing auto spare parts supplier With Other Solutions
When considering the procurement of auto spare parts, B2B buyers are often faced with various alternatives that promise similar outcomes. Understanding these alternatives is crucial for making an informed decision that aligns with your business needs. Below, we explore how auto spare parts suppliers compare against other viable solutions, focusing on performance, cost, ease of implementation, maintenance, and best use cases.
Comparison Aspect | Auto Spare Parts Supplier | Alternative 1: OEM Parts | Alternative 2: Aftermarket Parts |
---|---|---|---|
Performance | High quality, OEM standards | Top-tier performance, designed for specific vehicles | Variable quality, may not meet OEM standards |
Cost | Moderate to high | Higher upfront costs | Lower costs, potential for savings |
Ease of Implementation | Streamlined supply chain | Requires OEM relationships | Widely available, easier to source |
Maintenance | Often includes warranties | Comprehensive support from manufacturers | Limited warranties, variable support |
Best Use Case | Fleet management, long-term reliability | New vehicle repairs, critical components | Budget-conscious repairs, older vehicles |
What are the Benefits and Drawbacks of Using OEM Parts?
OEM Parts (Original Equipment Manufacturer) are designed and manufactured by the vehicle’s original producer. They offer the highest level of quality and assurance, making them ideal for critical repairs, especially in new vehicles. However, they often come with a higher price tag and require established relationships with manufacturers, which can complicate the procurement process. For businesses focused on quality and reliability, OEM parts are a sound investment, but budget constraints might limit their viability.
How Do Aftermarket Parts Compare in Terms of Cost and Availability?
Aftermarket Parts are produced by third-party manufacturers and tend to be more affordable than OEM parts. They are widely available and can be sourced easily, making them an attractive option for budget-conscious buyers or those servicing older vehicles. However, the quality of aftermarket parts can be inconsistent, and some may not meet OEM specifications. This can lead to potential reliability issues down the line, making them less suitable for critical repairs.
How Do Auto Spare Parts Suppliers Stand Out?
Auto Spare Parts Suppliers provide a balance between OEM and aftermarket options. They often offer a comprehensive range of products, allowing buyers to select parts that meet their specific quality and budget requirements. Additionally, many suppliers provide warranties and support, which can enhance peace of mind. The streamlined supply chain and established relationships with manufacturers also mean that buyers can expect timely deliveries and reliability in their procurement process.
Making the Right Choice: Which Solution Should You Choose?
When deciding between auto spare parts suppliers, OEM parts, and aftermarket parts, B2B buyers should consider their specific needs, such as the importance of quality, budget constraints, and the types of vehicles being serviced. For businesses operating fleets or requiring high reliability, investing in an auto spare parts supplier or OEM parts may be the best option. Conversely, if cost savings are a priority and quality is less critical, aftermarket parts could serve as a viable solution. Ultimately, a thorough analysis of the advantages and limitations of each option will guide buyers toward the best choice for their operations.
Essential Technical Properties and Trade Terminology for auto spare parts supplier
What Are the Key Technical Properties of Auto Spare Parts?
When sourcing auto spare parts, international B2B buyers must understand several critical technical specifications that influence the quality, compatibility, and performance of the components. Here are some essential properties to consider:
-
Material Grade
– Definition: Material grade indicates the type of material used in the manufacturing of the spare part, such as steel, aluminum, or plastic.
– Importance: The material grade affects durability, weight, and resistance to wear and corrosion. For instance, high-grade steel components are preferable for parts exposed to high stress, ensuring longevity and reliability. -
Tolerance Levels
– Definition: Tolerance refers to the permissible limit of variation in a physical dimension of the spare part.
– Importance: Precise tolerances are crucial for ensuring that parts fit together correctly, which is essential for the functionality of the vehicle. Inaccurate tolerances can lead to mechanical failures, increased wear, or safety hazards. -
Finish Type
– Definition: Finish type describes the surface treatment applied to a part, such as anodizing, painting, or plating.
– Importance: The finish affects not only the aesthetic appeal but also the performance and durability of the part. For example, a corrosion-resistant finish is vital for parts exposed to moisture, particularly in humid regions. -
Performance Ratings
– Definition: Performance ratings often refer to metrics such as load capacity, temperature resistance, and lifespan.
– Importance: These ratings help buyers assess whether a part can withstand the operational demands of specific applications. For instance, high-temperature performance ratings are critical for engine components. -
Compatibility Standards
– Definition: Compatibility standards outline the specifications a part must meet to be suitable for particular vehicle makes and models.
– Importance: Ensuring compatibility prevents costly errors and returns. Parts that do not meet OEM specifications may lead to performance issues or warranty problems.
What Are Common Trade Terms Used in the Auto Spare Parts Industry?
Understanding industry jargon is essential for effective communication and negotiation in the auto spare parts market. Here are some common trade terms:
-
OEM (Original Equipment Manufacturer)
– Definition: OEM refers to companies that produce parts that are used in the original assembly of vehicles.
– Importance: Buying OEM parts often guarantees quality and compatibility, which is critical for maintaining vehicle performance and safety. -
MOQ (Minimum Order Quantity)
– Definition: MOQ is the smallest quantity of an item that a supplier is willing to sell.
– Importance: Knowing the MOQ helps buyers assess the feasibility of orders, especially for smaller businesses or new market entrants. -
RFQ (Request for Quotation)
– Definition: An RFQ is a formal document sent to suppliers to request pricing for specific products or services.
– Importance: Issuing an RFQ enables buyers to compare prices and terms from multiple suppliers, facilitating better purchasing decisions. -
Incoterms (International Commercial Terms)
– Definition: Incoterms are a series of pre-defined commercial terms published by the International Chamber of Commerce (ICC) that clarify the responsibilities of buyers and sellers.
– Importance: Understanding Incoterms is vital for international trade as they determine who bears the risk and cost for shipping, insurance, and duties, thus influencing overall pricing strategies. -
Lead Time
– Definition: Lead time is the amount of time between placing an order and receiving the goods.
– Importance: Knowledge of lead time is crucial for inventory management and planning, helping businesses avoid stockouts or excess inventory. -
Certification Standards
– Definition: Certification standards refer to the official recognition that a product meets specific industry requirements.
– Importance: Certifications ensure compliance with safety, environmental, and performance standards, providing assurance to buyers regarding the quality of the parts they procure.
By familiarizing themselves with these technical properties and trade terms, international B2B buyers can make informed decisions when sourcing auto spare parts, ultimately enhancing their procurement strategies and operational efficiencies.
Navigating Market Dynamics and Sourcing Trends in the auto spare parts supplier Sector
What Are the Key Market Dynamics in the Auto Spare Parts Supplier Sector?
The global auto spare parts supplier market is driven by several key factors, including increasing vehicle ownership, the rise of e-commerce, and advancements in technology. As the automotive industry continues to grow, particularly in regions like Africa, South America, the Middle East, and Europe, international B2B buyers must stay informed about current and emerging trends. The shift towards digital platforms has revolutionized sourcing, enabling buyers to access a wider range of products and suppliers at competitive prices. Technologies such as artificial intelligence and machine learning are being leveraged for inventory management and demand forecasting, improving operational efficiencies.
Furthermore, the trend towards localization is gaining traction as buyers look to mitigate risks associated with global supply chains. This shift is particularly relevant for regions like the UAE, where companies are exploring partnerships with local suppliers to enhance supply chain resilience. Additionally, emerging markets are witnessing a surge in aftermarket services, as vehicle owners increasingly seek cost-effective alternatives to OEM parts. This presents a significant opportunity for B2B buyers to diversify their sourcing strategies and tap into the growing demand for high-quality spare parts.
How Does Sustainability Impact Sourcing Trends in the Auto Spare Parts Sector?
Sustainability and ethical sourcing have become paramount in the auto spare parts supplier sector. The environmental impact of automotive production is substantial, prompting buyers to prioritize suppliers that adhere to sustainable practices. This includes sourcing materials that are recycled or derived from renewable sources, which can significantly reduce the carbon footprint associated with spare parts manufacturing.
Moreover, the importance of ethical supply chains cannot be overstated. International buyers are increasingly scrutinizing their suppliers for compliance with labor standards and environmental regulations. Certifications such as ISO 14001 (Environmental Management) and ISO 9001 (Quality Management) are becoming essential for suppliers aiming to establish credibility in the market. By choosing suppliers with these certifications, B2B buyers can ensure that their sourcing practices align with sustainability goals, thereby enhancing their brand reputation and appeal to environmentally-conscious consumers.
What Is the Historical Context of the Auto Spare Parts Supplier Industry?
The auto spare parts supplier industry has evolved significantly over the past few decades. Initially dominated by local manufacturers, the sector has witnessed a dramatic shift towards globalization. The advent of e-commerce platforms has further accelerated this trend, allowing suppliers from various regions to compete in the global marketplace. This evolution has not only expanded the options available to B2B buyers but also introduced complexities in managing international supply chains.
As the industry continues to adapt to changing consumer preferences and technological advancements, international buyers must navigate these dynamics effectively. By understanding the historical context, buyers can better appreciate the factors influencing current market trends and make informed sourcing decisions that align with their business objectives.
Frequently Asked Questions (FAQs) for B2B Buyers of auto spare parts supplier
-
How do I solve supply chain disruptions when sourcing auto spare parts?
Supply chain disruptions can significantly impact your ability to source auto spare parts. To mitigate these risks, establish strong relationships with multiple suppliers across different regions, ensuring a diverse supply base. Implementing a robust inventory management system can help you anticipate shortages and maintain optimal stock levels. Additionally, consider utilizing technology for real-time tracking of shipments and logistics to quickly identify and address potential delays. Finally, always have contingency plans in place to switch suppliers or alter sourcing strategies when necessary. -
What is the best strategy for vetting auto spare parts suppliers?
The best strategy for vetting auto spare parts suppliers involves a multi-faceted approach. Start by researching the supplier’s reputation through industry forums, reviews, and references from other B2B buyers. Assess their certifications and compliance with international quality standards. Conduct on-site visits if possible to evaluate their facilities and production processes. Additionally, request samples to test the quality of their parts. Finally, analyze their financial stability and ability to meet your specific needs regarding volume, customization, and lead times. -
What should I consider when negotiating payment terms with international suppliers?
When negotiating payment terms with international suppliers, consider factors such as currency fluctuations, payment methods, and the supplier’s financial policies. Aim for terms that balance risk and cash flow, such as a mix of upfront payments and payment upon delivery or after inspection. Be clear about any additional fees, such as transaction costs or import duties. It’s also essential to understand the implications of international trade regulations that might affect payment timelines. Finally, consider using escrow services for larger transactions to ensure security for both parties. -
How can I ensure the quality of auto spare parts sourced internationally?
To ensure the quality of auto spare parts sourced internationally, implement a comprehensive quality assurance (QA) process. This includes requiring suppliers to provide certificates of authenticity and quality control documentation. Conduct regular audits and inspections, either in-person or through third-party services. Utilize testing protocols to verify the performance and durability of parts before full-scale orders. Establish clear return policies for defective parts and maintain open communication with your suppliers regarding quality expectations. -
What are the minimum order quantities (MOQ) I should expect from auto spare parts suppliers?
Minimum order quantities (MOQ) can vary significantly among auto spare parts suppliers based on their production capabilities and market focus. Generally, larger suppliers may have higher MOQs, while smaller or niche suppliers might be more flexible. When discussing MOQs, consider your inventory needs and potential for future orders. It’s beneficial to negotiate MOQs that align with your business model, ensuring you can maintain adequate stock without incurring excessive costs. Always clarify if there are different MOQs for custom parts versus standard components. -
How do I handle customs and logistics when importing auto spare parts?
Handling customs and logistics when importing auto spare parts requires thorough planning and understanding of international trade regulations. Ensure that you have all necessary documentation, such as commercial invoices, packing lists, and certificates of origin. Engage a reliable freight forwarder familiar with customs procedures in both the exporting and importing countries. It’s crucial to stay informed about tariffs, duties, and any trade agreements that might affect your shipments. Additionally, consider insurance for your shipments to protect against loss or damage during transit. -
What are the key factors to consider for supplier customization of auto spare parts?
When seeking supplier customization of auto spare parts, key factors include the supplier’s technical capabilities and willingness to accommodate specific requests. Discuss your requirements in detail, including design specifications, material preferences, and production timelines. Ensure the supplier has the necessary equipment and expertise to meet your customization needs. Also, consider the impact of customization on pricing and lead times, as bespoke parts may involve higher costs and longer production periods. Establish clear communication channels to facilitate collaboration throughout the customization process. -
How can I evaluate the reliability of an auto spare parts supplier?
Evaluating the reliability of an auto spare parts supplier involves assessing several key indicators. Begin by reviewing their track record in delivering orders on time and in full. Request references from other clients, particularly those in your industry, to gauge satisfaction levels. Analyze their communication practices and responsiveness to inquiries, as effective communication is vital for a reliable partnership. Additionally, consider their financial stability and market presence, as established suppliers are often more dependable. Finally, look for certifications and awards that reflect their commitment to quality and service.
Important Disclaimer & Terms of Use
⚠️ Important Disclaimer
The information provided in this guide, including content regarding manufacturers, technical specifications, and market analysis, is for informational and educational purposes only. It does not constitute professional procurement advice, financial advice, or legal advice.
While we have made every effort to ensure the accuracy and timeliness of the information, we are not responsible for any errors, omissions, or outdated information. Market conditions, company details, and technical standards are subject to change.
B2B buyers must conduct their own independent and thorough due diligence before making any purchasing decisions. This includes contacting suppliers directly, verifying certifications, requesting samples, and seeking professional consultation. The risk of relying on any information in this guide is borne solely by the reader.
Strategic Sourcing Conclusion and Outlook for auto spare parts supplier
What Are the Key Takeaways for B2B Buyers in Auto Spare Parts Sourcing?
In today’s global marketplace, strategic sourcing of auto spare parts is paramount for international B2B buyers, especially those from Africa, South America, the Middle East, and Europe. Prioritizing reliable suppliers, understanding local regulations, and leveraging technology can enhance procurement efficiency. Buyers should focus on building long-term partnerships with suppliers who demonstrate a commitment to quality, transparency, and innovation. Additionally, staying informed about market trends and consumer demands will aid in making well-informed purchasing decisions.
How Can Buyers Position Themselves for Future Success?
As the automotive industry continues to evolve with advancements in electric vehicles and smart technologies, buyers must be agile and forward-thinking. Embracing data analytics can provide insights into market dynamics and supplier performance, enabling more strategic sourcing decisions. Furthermore, participating in industry forums and networking events can facilitate valuable connections and knowledge sharing among peers.
What Is the Call to Action for International B2B Buyers?
In conclusion, international B2B buyers are encouraged to adopt a proactive approach to sourcing auto spare parts. By investing in strategic relationships and utilizing modern tools, buyers can secure a competitive advantage. Engage with suppliers who align with your business goals and foster partnerships that will drive mutual growth. The future is bright for those willing to adapt and innovate in the dynamic landscape of automotive parts sourcing.