Unlock Savings: The Ultimate Composite Panel China Guide (2025)
Introduction: Navigating the Global Market for composite panel china
Navigating the complexities of sourcing composite panels from China can pose significant challenges for international B2B buyers. With a vast array of products available, understanding the differences between types, applications, and quality standards is crucial. This guide comprehensively explores the various types of composite panels—such as aluminum composite panels, fiberglass reinforced panels, and more—detailing their applications across industries like construction, automotive, and aerospace. Additionally, we will cover essential aspects of supplier vetting, including certifications, production capabilities, and reliability, ensuring that you partner with the best manufacturers to meet your specific needs.
For buyers in Africa, South America, the Middle East, and Europe, particularly in countries like Germany and Spain, making informed purchasing decisions can lead to significant cost savings and enhanced product performance. This guide empowers you with actionable insights, addressing key considerations such as pricing strategies, shipping logistics, and market trends. By equipping you with the knowledge to navigate the global market effectively, we aim to streamline your sourcing process, reduce risks, and ultimately enhance your competitive edge in the marketplace. Whether you are looking to expand your product offerings or enhance your supply chain efficiency, this guide is your comprehensive resource for successfully sourcing composite panels from China.
Understanding composite panel china Types and Variations
Type Name | Key Distinguishing Features | Primary B2B Applications | Brief Pros & Cons for Buyers |
---|---|---|---|
Aluminum Composite Panels (ACP) | Lightweight, durable, and corrosion-resistant | Building facades, signage, interior design | Pros: Aesthetic appeal, easy to maintain; Cons: Can be more expensive than alternatives. |
Glass Fiber Reinforced Polymer (GFRP) | High strength-to-weight ratio, excellent corrosion resistance | Marine, automotive, and construction sectors | Pros: Lightweight, strong; Cons: Limited heat resistance. |
Polyurethane Composite Panels | High insulation properties, energy-efficient | Refrigeration, cold storage, and construction | Pros: Excellent thermal insulation; Cons: Vulnerable to UV degradation. |
Cement Composite Panels | Fire-resistant, robust, and moisture-resistant | Exterior walls, roofing, and flooring | Pros: Durable, low maintenance; Cons: Heavier, may require specialized installation. |
Wood Plastic Composite Panels | Made from recycled materials, eco-friendly | Decking, outdoor furniture, and flooring | Pros: Sustainable, aesthetic versatility; Cons: Susceptible to moisture and warping. |
What are the Characteristics of Aluminum Composite Panels (ACP)?
Aluminum Composite Panels (ACP) are composed of two thin layers of aluminum enclosing a non-aluminum core, providing a lightweight yet durable solution. They are particularly suitable for exterior applications such as building facades and signage due to their aesthetic appeal and ability to withstand weather conditions. B2B buyers should consider factors such as design flexibility, color options, and the panel’s fire rating when making purchasing decisions. While they offer a modern look, the cost may be higher compared to traditional cladding materials.
Why Choose Glass Fiber Reinforced Polymer (GFRP)?
Glass Fiber Reinforced Polymer (GFRP) is an advanced composite that combines glass fibers with a polymer matrix, offering exceptional strength and lightweight characteristics. This material is ideal for applications in marine, automotive, and construction sectors where weight reduction without sacrificing strength is crucial. When purchasing GFRP, buyers should evaluate the specific reinforcement types and resin formulations to ensure they meet application requirements. However, it’s important to note that GFRP may not perform well in high-temperature environments, limiting its use in some applications.
What are the Benefits of Polyurethane Composite Panels?
Polyurethane Composite Panels are known for their superior thermal insulation properties, making them a popular choice in refrigeration and cold storage applications. They consist of a rigid core sandwiched between two outer layers, ensuring energy efficiency. B2B buyers should assess the panel thickness, insulation values, and potential UV degradation when considering these panels for their projects. While they provide excellent insulation, their susceptibility to UV damage can be a drawback, necessitating protective coatings in certain environments.
How Do Cement Composite Panels Stand Out?
Cement Composite Panels are engineered for high durability and fire resistance, making them suitable for exterior walls and roofing. These panels resist moisture, mold, and pests, offering a long-lasting solution for construction projects. Buyers should consider the weight of these panels, as their heavier nature may require specialized installation techniques. While cement composites are robust and low maintenance, their weight can be a disadvantage in applications where lighter materials are preferred.
What Makes Wood Plastic Composite Panels Eco-Friendly?
Wood Plastic Composite Panels are crafted from a blend of recycled wood fibers and plastic, creating a sustainable option for decking and outdoor furniture. These panels provide aesthetic versatility and are often chosen for their eco-friendly attributes. B2B buyers should evaluate the durability against moisture and potential warping, particularly in outdoor settings. While they offer sustainability and visual appeal, their performance in wet conditions can be a concern, making proper maintenance essential for longevity.
Related Video: Understanding Honeycomb Panel and Honeycomb Composite Structures
Key Industrial Applications of composite panel china
Industry/Sector | Specific Application of composite panel china | Value/Benefit for the Business | Key Sourcing Considerations for this Application |
---|---|---|---|
Construction | Wall and Ceiling Panels for Commercial Buildings | Lightweight, durable, and energy-efficient materials | Compliance with local building codes and fire standards |
Automotive | Interior Panels for Vehicles | Reduced weight leading to improved fuel efficiency | Material compatibility with existing vehicle designs |
Aerospace | Aircraft Cabin Interiors | High strength-to-weight ratio and resistance to corrosion | Certification standards for aviation materials |
Marine | Boat Hulls and Decks | Enhanced durability and resistance to water damage | Supplier reliability and performance in harsh environments |
Furniture | Decorative Panels for High-End Furniture | Aesthetic appeal combined with durability | Customization options and design flexibility |
How Are Composite Panels Used in the Construction Industry?
In the construction sector, composite panels from China are utilized for wall and ceiling applications in commercial buildings. These panels are favored for their lightweight nature, which reduces structural load, and their superior insulation properties, enhancing energy efficiency. International buyers, particularly from regions like Africa and the Middle East, must ensure compliance with local building codes and fire safety standards to mitigate risks associated with flammability and durability.
What Role Do Composite Panels Play in Automotive Applications?
In the automotive industry, composite panels are increasingly used for interior vehicle components. They provide significant weight savings, which directly translates to improved fuel efficiency and lower emissions. For B2B buyers in Europe, such as Germany and Spain, it is crucial to consider material compatibility with existing designs and ensure that the panels meet stringent safety and environmental regulations.
Why Are Composite Panels Important for Aerospace?
Composite panels are essential in the aerospace industry, particularly for aircraft cabin interiors. Their high strength-to-weight ratio allows for lighter aircraft, which enhances fuel efficiency and performance. Buyers in this sector must focus on sourcing materials that meet specific certification standards, as aviation materials are subject to rigorous testing for safety and reliability.
How Are Composite Panels Beneficial in Marine Applications?
In the marine industry, composite panels are used for boat hulls and decks, offering exceptional resistance to water damage and corrosion. This durability is vital for maintaining the integrity and longevity of marine vessels. Buyers should prioritize suppliers that demonstrate reliability and performance in harsh marine environments, ensuring that the panels can withstand the demanding conditions of the sea.
What Are the Advantages of Composite Panels in Furniture Design?
Composite panels are widely used in the furniture industry, particularly for high-end decorative applications. They provide an aesthetic appeal while maintaining durability, making them ideal for luxury furniture design. International buyers should seek out customization options that allow for unique designs and finishes, ensuring that the panels align with their brand identity and market trends.
Related Video: ECONECT-Z™ Aluminum Composite Material Panel System
3 Common User Pain Points for ‘composite panel china’ & Their Solutions
Scenario 1: Sourcing Quality Composite Panels from China
The Problem: International B2B buyers often face significant challenges when sourcing composite panels from China, particularly in ensuring product quality and compliance with international standards. This is exacerbated by language barriers, differences in business practices, and the sheer number of manufacturers available. Buyers may receive samples that seem satisfactory, only to discover upon delivery that the panels do not meet their specifications or quality expectations, leading to costly delays and rework in their projects.
The Solution: To overcome these challenges, buyers should implement a structured sourcing strategy. Begin by conducting thorough research to identify reputable manufacturers with a proven track record in producing composite panels. Utilize platforms like Alibaba or Global Sources, but prioritize suppliers with verified ratings and positive reviews. Request certifications and compliance documents that prove adherence to international quality standards, such as ISO 9001. Establish clear communication channels and consider hiring a local agent or consultant who can bridge the gap between cultures and ensure that your specifications are accurately conveyed. Additionally, arranging for third-party inspections at various stages of production can provide peace of mind and ensure that the final product meets your expectations.
Scenario 2: Understanding Technical Specifications for Composite Panels
The Problem: Many B2B buyers may not fully understand the technical specifications associated with composite panels, leading to difficulties in selecting the right product for their specific applications. For example, factors like thermal insulation, fire resistance, and load-bearing capacity are critical but can be misunderstood or overlooked. This lack of knowledge can result in purchasing panels that are either inadequate for the intended use or overly specialized, causing unnecessary costs.
The Solution: To address this knowledge gap, buyers should invest time in understanding the key properties and applications of composite panels. Engage with manufacturers to obtain detailed product datasheets that explain the technical specifications in layman’s terms. Attend industry trade shows or webinars that focus on composite materials, which can provide valuable insights into the latest advancements and best practices. Collaborate with engineers or consultants who specialize in material science to assess your project requirements accurately. By gaining a clear understanding of the necessary specifications, buyers can make informed decisions and avoid costly mistakes in their projects.
Scenario 3: Managing Supply Chain Disruptions When Importing Composite Panels
The Problem: Supply chain disruptions can significantly impact the timely delivery of composite panels from China, especially in a global market affected by various factors such as geopolitical tensions, pandemics, or transportation issues. B2B buyers may experience unexpected delays, leading to project timelines being extended and increased costs due to penalties or expedited shipping.
The Solution: To mitigate the risks associated with supply chain disruptions, buyers should develop a robust supply chain strategy that includes diversifying their supplier base. Instead of relying solely on one manufacturer, consider sourcing from multiple suppliers within China or even exploring manufacturers in other countries. Establishing strong relationships with logistics providers can also provide flexibility in shipping options. Implementing just-in-time (JIT) inventory practices can help manage stock levels more effectively, reducing the impact of delays. Additionally, maintain open lines of communication with your suppliers to receive timely updates about potential issues, allowing you to proactively adjust your project plans as needed. By taking these steps, B2B buyers can enhance their resilience against supply chain disruptions and ensure a more reliable procurement process.
Strategic Material Selection Guide for composite panel china
What Are the Key Materials Used in Composite Panels in China?
When selecting composite panels for various applications, understanding the materials used is crucial for international B2B buyers. This section analyzes four common materials used in composite panels manufactured in China, focusing on their properties, advantages, limitations, and considerations for buyers from Africa, South America, the Middle East, and Europe.
Which Materials Are Commonly Used in Composite Panels?
1. Polyester Resin with Glass Fiber Reinforcement
Key Properties: Polyester resin combined with glass fiber offers excellent strength-to-weight ratios, temperature resistance up to 80°C, and good corrosion resistance. This combination is particularly effective in applications requiring lightweight yet strong materials.
Pros & Cons: The durability of this composite is high, making it suitable for various environments. However, it can be more expensive than traditional materials like wood or metal. Manufacturing complexity is moderate, as it requires careful handling of resins and fibers during the curing process.
Impact on Application: This material is ideal for applications in the automotive and marine industries, where weight reduction is critical. It is also compatible with various media, including water and chemicals, making it versatile for different environments.
Considerations for International Buyers: Buyers should ensure compliance with international standards such as ASTM D638 for tensile properties and DIN EN 1452 for piping systems. Understanding local regulations regarding material safety and environmental impact is also essential.
2. Aluminum Composite Material (ACM)
Key Properties: ACM consists of two thin layers of aluminum enclosing a non-aluminum core, providing excellent rigidity, weather resistance, and fire resistance. It can withstand temperatures up to 100°C and offers good insulation properties.
Pros & Cons: One of the main advantages of ACM is its aesthetic appeal and versatility in design, making it popular in architectural applications. However, the cost can be high, and the manufacturing process is more complex due to the need for precise cutting and finishing.
Impact on Application: ACM is commonly used in building facades, signage, and interior applications. Its compatibility with various environmental conditions makes it suitable for both indoor and outdoor use.
Considerations for International Buyers: Buyers should pay attention to compliance with fire safety standards such as EN 13501-1 in Europe. Understanding the local market’s preferences for aesthetics and durability can also influence purchasing decisions.
3. Wood Plastic Composite (WPC)
Key Properties: WPC combines wood fibers with thermoplastics, offering natural aesthetics while being resistant to moisture, rot, and insects. It typically performs well in temperature ranges from -30°C to 60°C.
Pros & Cons: WPC is environmentally friendly and provides a sustainable alternative to traditional wood. However, it may have lower structural strength compared to other composites and can be more expensive than conventional wood.
Impact on Application: This material is widely used in outdoor decking, fencing, and furniture. Its resistance to environmental factors makes it suitable for applications exposed to moisture and UV light.
Considerations for International Buyers: Buyers should verify compliance with environmental standards and certifications such as FSC (Forest Stewardship Council) for sustainable sourcing. Knowing the local preferences for aesthetics and performance can guide material selection.
4. Carbon Fiber Reinforced Polymer (CFRP)
Key Properties: CFRP is known for its exceptional strength-to-weight ratio and stiffness, with temperature resistance exceeding 120°C. It is also highly resistant to corrosion and fatigue.
Pros & Cons: The primary advantage of CFRP is its lightweight and high-performance characteristics, making it ideal for high-tech applications. However, it is one of the most expensive composite materials and requires specialized manufacturing techniques, which can complicate production.
Impact on Application: CFRP is commonly used in aerospace, automotive, and high-performance sporting goods. Its compatibility with demanding environments makes it suitable for applications requiring advanced material properties.
Considerations for International Buyers: Buyers must consider compliance with industry-specific standards such as JIS (Japanese Industrial Standards) for aerospace applications. Understanding the cost implications and availability of CFRP in local markets is essential for budget planning.
Summary Table of Composite Panel Materials
Material | Typical Use Case for composite panel china | Key Advantage | Key Disadvantage/Limitation | Relative Cost (Low/Med/High) |
---|---|---|---|---|
Polyester Resin with Glass Fiber | Automotive and marine applications | Excellent strength-to-weight ratio | Higher cost than traditional materials | Medium |
Aluminum Composite Material (ACM) | Building facades and signage | Aesthetic appeal and versatility | Higher manufacturing complexity | High |
Wood Plastic Composite (WPC) | Outdoor decking and furniture | Environmentally friendly | Lower structural strength | Medium |
Carbon Fiber Reinforced Polymer (CFRP) | Aerospace and high-performance applications | Exceptional strength-to-weight ratio | High cost and specialized manufacturing | High |
This analysis provides a comprehensive overview of the materials used in composite panels, allowing international B2B buyers to make informed decisions based on their specific needs and market conditions.
In-depth Look: Manufacturing Processes and Quality Assurance for composite panel china
What Are the Key Stages in the Manufacturing Process of Composite Panels in China?
The manufacturing of composite panels in China is a multi-step process that combines various materials to achieve desirable properties such as strength, durability, and lightweight characteristics. Understanding these stages can help international B2B buyers make informed decisions when sourcing from Chinese manufacturers.
1. Material Preparation: How Are Raw Materials Selected and Processed?
The first stage involves careful selection and preparation of raw materials, which typically include a polymer matrix and reinforcement materials like glass or carbon fibers. The polymer matrix serves as a binder, while the reinforcement provides the necessary strength. Manufacturers often choose polyester or epoxy resins for their favorable mechanical properties.
Once selected, these materials undergo several pre-processing steps, including cutting, drying, and sometimes treating the fibers to enhance bonding with the matrix. Ensuring the quality of these raw materials is crucial, as it directly impacts the final product’s performance.
2. Forming: What Techniques Are Used to Shape Composite Panels?
The forming stage is critical in defining the structural integrity and aesthetics of composite panels. Common techniques employed include:
-
Hand Lay-Up: In this manual method, layers of reinforcement are placed into a mold, followed by the application of resin. It allows for customization but can be labor-intensive.
-
Vacuum Infusion: This technique uses vacuum pressure to draw resin into the dry reinforcement materials. It offers better resin distribution and reduces the risk of air bubbles, resulting in a stronger panel.
-
Compression Molding: Suitable for high-volume production, this method involves placing a pre-measured amount of composite material into a heated mold, where pressure and heat cure the material quickly.
These forming techniques not only affect the performance but also the cost and lead time of production. Buyers should inquire about the techniques used and their implications for the final product.
3. Assembly: How Are Composite Panels Joined or Enhanced?
After forming, composite panels may require assembly with other components or additional enhancements. This could involve bonding different panels together or integrating features like insulation or surface coatings. Adhesive bonding is a common method, especially for complex geometries where mechanical fastening may not be feasible.
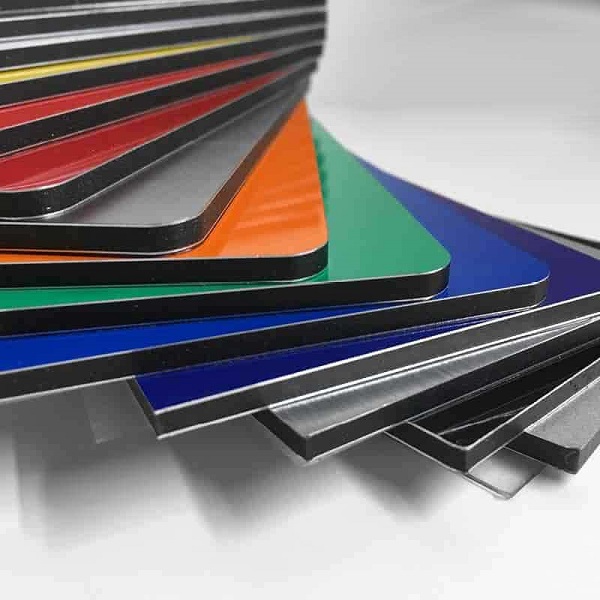
A stock image related to composite panel china.
Understanding the assembly process is vital for buyers who need to ensure that the final product meets specific application requirements, such as thermal resistance or moisture protection.
4. Finishing: What Processes Ensure Aesthetic and Functional Quality?
The finishing stage focuses on both the aesthetic and functional aspects of composite panels. This may involve sanding, painting, or applying protective coatings. Finishing not only enhances the visual appeal but also contributes to the durability and resistance of the panels to environmental factors.
Buyers should consider the finishing options available and how they align with their specific needs, such as color matching or surface texture.
How Is Quality Assurance Implemented in Composite Panel Manufacturing?
Quality assurance (QA) is a critical aspect of composite panel manufacturing that ensures the final product meets international standards and buyer specifications.
Relevant International Standards: What Certifications Should Buyers Look For?
International standards such as ISO 9001 play a significant role in ensuring consistent quality management systems among manufacturers. Additionally, industry-specific certifications like CE (Conformité Européenne) for European markets and API (American Petroleum Institute) certifications for oil and gas applications may be required depending on the intended use of the composite panels.
B2B buyers should verify that suppliers possess these certifications, as they demonstrate compliance with recognized quality benchmarks.
Key Quality Control Checkpoints: What Are the Main Stages of QC?
Quality control in composite panel manufacturing typically includes several key checkpoints:
-
Incoming Quality Control (IQC): This initial inspection verifies the quality of raw materials before production begins. It ensures that materials meet specified standards and reduces the risk of defects in the final product.
-
In-Process Quality Control (IPQC): During manufacturing, periodic inspections are conducted to monitor the processes and identify any deviations from established protocols. This may include checking the curing process or monitoring temperature and pressure during forming.
-
Final Quality Control (FQC): After production, a comprehensive inspection of the finished panels is carried out. This includes dimensional checks, visual inspections, and functional testing to ensure the panels meet all specifications.
What Testing Methods Are Commonly Used in Composite Panel Quality Control?
Several testing methods are employed to evaluate the performance and durability of composite panels:
-
Mechanical Testing: This includes tensile, compression, and flexural tests to measure the strength and stiffness of the panels.
-
Thermal Testing: Conducted to assess the material’s resistance to heat and its thermal stability under various conditions.
-
Environmental Testing: Simulates exposure to different environmental conditions (e.g., moisture, UV light) to evaluate long-term durability.
B2B buyers should request detailed testing reports from manufacturers to understand the performance characteristics of the composite panels.
How Can B2B Buyers Verify Supplier Quality Control Processes?
Verification of a supplier’s quality control processes is essential for B2B buyers, particularly when sourcing internationally. Here are several strategies:
-
Audits: Conducting on-site audits allows buyers to assess the manufacturing environment, quality control processes, and adherence to standards firsthand.
-
Documentation: Requesting quality control documentation, including IQC, IPQC, and FQC reports, can provide insights into the supplier’s commitment to quality.
-
Third-Party Inspections: Engaging third-party inspection services can offer an unbiased evaluation of the manufacturing processes and product quality, adding an extra layer of assurance.
What Are the Nuances of Quality Control for International B2B Buyers?
For international B2B buyers, particularly those from Africa, South America, the Middle East, and Europe, understanding regional compliance requirements is crucial. Different markets may have specific regulations or standards that composite panels must meet, impacting the manufacturing process and quality assurance practices.
Buyers should be proactive in communicating their specific requirements to suppliers and may need to engage legal or compliance experts to navigate the complexities of international trade.
In conclusion, understanding the manufacturing processes and quality assurance practices in the production of composite panels in China can empower B2B buyers to make informed decisions. By focusing on the key stages of manufacturing, relevant quality standards, testing methods, and verification strategies, buyers can ensure they source high-quality products that meet their specific needs.
Practical Sourcing Guide: A Step-by-Step Checklist for ‘composite panel china’
In the rapidly evolving market for composite panels, particularly from China, international B2B buyers must navigate a complex landscape to ensure they make informed and effective purchasing decisions. This guide provides a step-by-step checklist designed to assist buyers in sourcing high-quality composite panels that meet their specific needs.
Step 1: Define Your Technical Specifications
Before engaging suppliers, clarify your requirements for composite panels. This includes determining dimensions, material types (e.g., aluminum, fiberglass), weight restrictions, and performance characteristics such as fire resistance or thermal insulation. Clear specifications help suppliers provide accurate quotes and ensure the products align with your project needs.
Step 2: Research the Market Landscape
Conduct thorough market research to understand the current trends, pricing, and competition for composite panels in China. Look for reports and articles that highlight leading manufacturers and emerging technologies. This knowledge will enable you to make better comparisons and recognize reputable suppliers.
Step 3: Identify Potential Suppliers
Compile a list of potential suppliers based on your research. Use online platforms, trade shows, and industry networks to find manufacturers specializing in composite panels. Aim to identify suppliers with a proven track record, particularly those with experience in exporting to your region.
Step 4: Verify Supplier Certifications and Compliance
Ensure that potential suppliers hold relevant certifications, such as ISO 9001 for quality management systems and environmental standards like ISO 14001. Compliance with international standards indicates a commitment to quality and sustainability. Additionally, check for product certifications specific to your industry needs (e.g., fire safety ratings).
Step 5: Request Samples for Evaluation
Before making a bulk purchase, request samples of the composite panels to assess their quality. Examine the materials for durability, finish, and compliance with your specifications. Testing samples can help you avoid costly mistakes and ensure that the products meet your expectations.
Step 6: Assess Pricing and Payment Terms
Once you have shortlisted suppliers, evaluate their pricing structures and payment terms. Consider the total cost of ownership, including shipping and potential tariffs, rather than just the upfront price. Discuss payment options that can safeguard your investment, such as letters of credit or escrow services.
Step 7: Establish Clear Communication Channels
Maintain open and clear communication with your chosen supplier throughout the sourcing process. Establishing dedicated points of contact ensures that any questions or concerns are addressed promptly. Effective communication is crucial for managing timelines, quality control, and resolving issues that may arise during production or shipping.
By following these steps, international B2B buyers can effectively source composite panels from China, ensuring that they select the right suppliers and products for their specific needs while minimizing risks.
Comprehensive Cost and Pricing Analysis for composite panel china Sourcing
What Are the Key Cost Components for Sourcing Composite Panels from China?
When sourcing composite panels from China, understanding the cost structure is essential for making informed purchasing decisions. The primary cost components include:
-
Materials: The raw materials used in composite panels can significantly impact the overall cost. Common materials include polymers, glass fibers, and additives. Prices can fluctuate based on market conditions and availability.
-
Labor: Labor costs in China tend to be lower than in many Western countries, but they vary by region and skill level. Skilled labor for manufacturing composite panels may command higher wages, which can influence pricing.
-
Manufacturing Overhead: This includes the costs associated with running the production facility, such as utilities, maintenance, and administrative expenses. Efficient factories may have lower overhead, translating to better pricing for buyers.
-
Tooling: The initial investment in molds and tools required for production can be significant, especially for customized panels. Tooling costs are typically amortized over the production volume, so larger orders can reduce the per-unit cost.
-
Quality Control (QC): Ensuring product quality can add to costs, especially if third-party inspection services are employed. Buyers should consider the level of QC necessary for their applications, as this can affect overall pricing.
-
Logistics: Shipping costs are a crucial component, particularly for international buyers. Factors include freight charges, insurance, customs duties, and other transportation fees. Efficient logistics management can help mitigate these costs.
-
Margin: Suppliers will typically include a profit margin in their pricing. Understanding the market dynamics can help buyers negotiate better terms.
How Do Price Influencers Affect the Cost of Composite Panels?
Several factors influence the pricing of composite panels, including:
-
Volume/MOQ: Minimum order quantities (MOQ) can affect pricing. Larger orders often lead to lower per-unit costs, as they allow suppliers to spread fixed costs over more units.
-
Specifications and Customization: Custom specifications can drive up costs due to the need for specialized materials or manufacturing processes. Buyers should clearly define their requirements to avoid unexpected price increases.
-
Materials: The choice of materials significantly affects pricing. High-performance materials, while offering better durability and strength, will cost more than standard options.
-
Quality and Certifications: Panels that meet specific industry standards or certifications (e.g., ISO, ASTM) may carry a premium. Buyers should assess the necessity of certifications based on their application.
-
Supplier Factors: The supplier’s reputation, reliability, and production capabilities can influence pricing. Established suppliers with a proven track record may charge more but can offer better quality assurance.
-
Incoterms: The agreed Incoterms (International Commercial Terms) can significantly affect total costs. Terms like FOB (Free on Board) or CIF (Cost, Insurance, and Freight) determine who bears costs and risks at various stages of shipping.
What Are the Best Buyer Tips for Cost-Efficiency in Composite Panel Sourcing?
For international buyers, particularly from regions such as Africa, South America, the Middle East, and Europe, here are some actionable tips:
-
Negotiate Effectively: Engage suppliers in negotiations to achieve better pricing. Understanding the cost structure can provide leverage in discussions.
-
Consider Total Cost of Ownership (TCO): Evaluate not just the purchase price but also logistics, maintenance, and potential waste costs. A lower initial price may lead to higher long-term expenses.
-
Be Aware of Pricing Nuances: Different regions may have varying pricing structures due to local economic conditions, tariffs, and regulations. Research local market conditions to better understand pricing dynamics.
-
Build Relationships with Suppliers: Establishing long-term partnerships can lead to better pricing, improved service, and priority access to materials, especially in fluctuating markets.
-
Stay Informed About Market Trends: Keep abreast of trends in material costs and global supply chain issues. This knowledge can help in making timely purchasing decisions and anticipating price changes.
Disclaimer on Indicative Prices
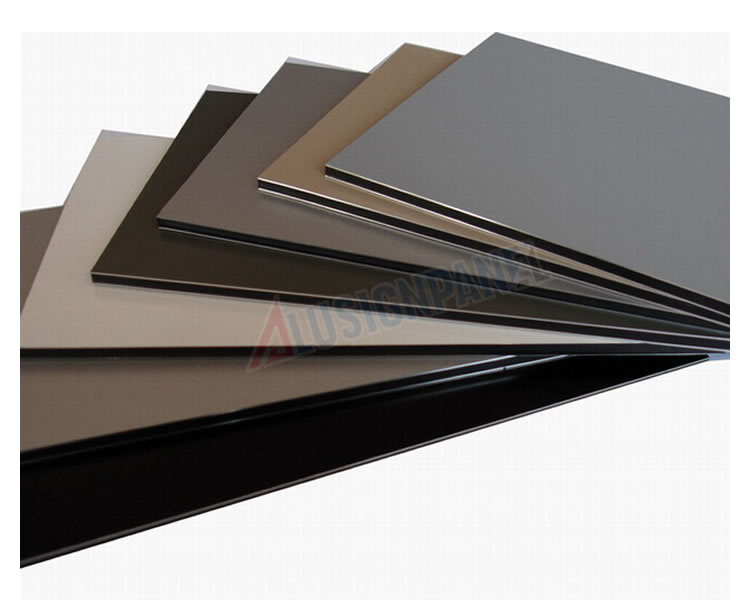
A stock image related to composite panel china.
Prices for composite panels can vary widely based on numerous factors. Buyers should conduct thorough market research and obtain multiple quotes to ensure they are receiving a competitive offer. Always consider the specific context of your needs and the supplier’s capabilities when evaluating pricing.
Alternatives Analysis: Comparing composite panel china With Other Solutions
When considering the procurement of materials for construction or manufacturing, international B2B buyers often face a myriad of options. One popular choice is composite panels from China, known for their strength and lightweight properties. However, it is vital to evaluate alternative solutions to ensure the best fit for specific project requirements. Below, we compare ‘Composite Panel China’ with two viable alternatives: Aluminum Composite Panels (ACP) and Plywood.
Comparison Aspect | Composite Panel China | Aluminum Composite Panels (ACP) | Plywood |
---|---|---|---|
Performance | High strength-to-weight ratio; good insulation properties; resistant to corrosion. | Excellent durability; good fire resistance; lightweight. | Good structural strength; susceptible to moisture; limited insulation. |
Cost | Generally cost-effective; varies by supplier and specifications. | Moderate cost; often higher than composite panels but offers longevity. | Typically the least expensive option; cost-effective for many applications. |
Ease of Implementation | Requires specialized tools for cutting and installation. | Easy to handle; can be cut and installed with standard tools. | Simple to work with; readily available and easy to install. |
Maintenance | Low maintenance; easy to clean; resistant to fading and wear. | Low maintenance; resistant to weather and corrosion. | Requires regular maintenance; prone to warping or rotting if exposed to moisture. |
Best Use Case | Ideal for modern buildings, signage, and interior applications. | Best for facades, signage, and interior finishes where fire resistance is critical. | Suitable for furniture, cabinetry, and temporary structures. |
What are the Pros and Cons of Aluminum Composite Panels (ACP)?
Aluminum Composite Panels (ACP) present a robust alternative to composite panels from China. Their key advantage lies in their excellent durability and fire resistance, making them suitable for high-rise buildings and commercial applications. ACPs are lightweight and easy to handle, which simplifies installation. However, they can be more expensive than composite panels and may not offer the same insulation properties, depending on the core material used.
How Does Plywood Compare as an Alternative Material?
Plywood stands out as a traditional and cost-effective option. It is readily available and easy to work with, making it a popular choice for many construction projects. Its structural strength is commendable, especially for furniture and cabinetry. However, plywood has notable drawbacks, such as susceptibility to moisture damage and a need for regular maintenance to prevent warping and degradation. Additionally, it may not provide the same level of insulation as composite panels.
How Can B2B Buyers Choose the Right Solution for Their Needs?
When selecting between ‘Composite Panel China’ and its alternatives, B2B buyers should carefully assess their specific project requirements, including performance expectations, budget constraints, and installation capabilities. The intended application plays a crucial role; for instance, a project that prioritizes fire safety may lean towards ACP, while a cost-sensitive initiative might favor plywood. Ultimately, understanding the unique characteristics and advantages of each option will empower buyers to make informed decisions that align with their operational goals.
Essential Technical Properties and Trade Terminology for composite panel china
What Are the Key Technical Properties of Composite Panels from China?
When sourcing composite panels from China, understanding the technical properties is crucial for making informed purchasing decisions. Here are several key specifications to consider:
1. Material Grade: Why Is It Important?
Material grade refers to the quality and composition of the composite material used in the panel. Different grades may offer varying levels of strength, durability, and resistance to environmental factors. For B2B buyers, selecting the right material grade is essential to ensure that the panels meet specific application requirements, whether for construction, automotive, or aerospace industries.
2. Tolerance: How Does It Affect Manufacturing?
Tolerance indicates the allowable variation in dimensions during manufacturing. For composite panels, tight tolerances are critical to ensure that parts fit together correctly, reducing the need for adjustments during installation. In industries like aerospace and automotive, where precision is paramount, understanding tolerance levels can significantly impact project timelines and costs.
3. Weight-to-Strength Ratio: What Should You Look For?
The weight-to-strength ratio measures how much strength a material provides relative to its weight. Composite panels are often favored for their lightweight characteristics while maintaining high strength. This property is particularly beneficial in sectors such as transportation and construction, where reducing weight can lead to lower fuel consumption and easier handling.
4. Fire Resistance: Why Is It Essential?
Fire resistance is a critical property for composite panels, especially in construction and transportation applications. Panels that meet specific fire safety standards can prevent the spread of flames and reduce smoke emissions. Buyers should look for certifications that ensure the panels comply with international fire safety regulations, enhancing safety and compliance in their projects.
5. Thermal Conductivity: How Does It Impact Performance?
Thermal conductivity measures a material’s ability to conduct heat. Low thermal conductivity in composite panels can lead to better energy efficiency and temperature regulation in buildings and vehicles. For B2B buyers, understanding thermal properties can help in selecting panels that meet energy standards and improve overall system performance.
6. UV Resistance: Why Consider It?
UV resistance refers to a material’s ability to withstand degradation from ultraviolet light exposure. For outdoor applications, selecting composite panels with high UV resistance can prolong the lifespan of the product and maintain its aesthetic appearance. This property is particularly relevant for buyers in regions with high sun exposure, ensuring that the panels perform well over time.
What Trade Terminology Should B2B Buyers Understand?
Familiarity with industry jargon is essential for effective communication and negotiation in the procurement process. Here are some common terms relevant to composite panels:
1. OEM (Original Equipment Manufacturer): What Does It Mean?
OEM refers to companies that produce parts or equipment that may be marketed by another manufacturer. In the context of composite panels, understanding OEM relationships can help buyers identify reliable suppliers and assess the quality of the products being offered.
2. MOQ (Minimum Order Quantity): Why Is It Relevant?
MOQ denotes the smallest quantity of a product that a supplier is willing to sell. Knowing the MOQ is crucial for buyers to plan their inventory and budget accordingly. Suppliers in China may have different MOQs based on production capabilities, so negotiating these terms can lead to cost savings.
3. RFQ (Request for Quotation): How to Use It?
An RFQ is a document that solicits price quotes from suppliers for specific products or services. For B2B buyers, issuing an RFQ for composite panels can streamline the procurement process, enabling them to compare prices and terms from multiple suppliers effectively.
4. Incoterms: What Are They?
Incoterms (International Commercial Terms) are standardized trade terms that define the responsibilities of buyers and sellers in international transactions. Familiarity with Incoterms helps buyers understand shipping costs, risk transfer, and delivery responsibilities, which is critical for cost management and logistics planning.
5. Lead Time: Why Should You Consider It?
Lead time is the period between placing an order and receiving the goods. For composite panels, understanding lead times can help buyers plan projects effectively, ensuring that materials arrive when needed without causing delays.
By grasping these essential technical properties and trade terminologies, international B2B buyers can navigate the complexities of sourcing composite panels from China with greater confidence and efficiency.
Navigating Market Dynamics and Sourcing Trends in the composite panel china Sector
What are the Current Market Dynamics and Key Trends in the Composite Panel Sector in China?
The composite panel market in China is experiencing significant growth driven by various global factors. As industries increasingly seek lightweight yet durable materials, the demand for composite panels is surging across sectors such as construction, automotive, and aerospace. Key trends include the integration of advanced manufacturing technologies, such as automation and digitalization, which enhance production efficiency and product quality. Additionally, the rise of smart materials that incorporate sensors and IoT capabilities is reshaping applications, offering international B2B buyers innovative solutions that meet modern demands.
For international buyers, particularly from Africa, South America, the Middle East, and Europe, understanding the local market dynamics is crucial. China’s strategic initiatives, such as the Belt and Road Initiative (BRI), are opening up new avenues for trade and investment in composite materials. Buyers should be aware of regional preferences and regulatory standards, as they can influence sourcing decisions. Additionally, China’s focus on sustainable manufacturing practices is becoming increasingly relevant, prompting buyers to consider suppliers that adhere to environmental regulations and standards.
How Can International B2B Buyers Ensure Sustainability and Ethical Sourcing in Composite Panels?
Sustainability and ethical sourcing are becoming pivotal in the procurement of composite panels. The environmental impact of composite materials, particularly in terms of waste and recyclability, is a growing concern. International buyers must prioritize suppliers that implement sustainable practices, such as using recycled materials or bio-based resins in their production processes. Certifications like ISO 14001, which focuses on effective environmental management systems, and LEED (Leadership in Energy and Environmental Design) certifications can guide buyers in identifying responsible suppliers.
Moreover, ethical supply chains are essential to ensure that materials are sourced responsibly. Buyers should conduct due diligence to verify that suppliers maintain fair labor practices and do not engage in exploitative sourcing. This not only enhances brand reputation but also aligns with the increasing consumer demand for transparency and accountability in the supply chain. By choosing suppliers with ‘green’ certifications and a commitment to ethical practices, international buyers can contribute to a more sustainable future while meeting their business needs.
What is the Brief Evolution of Composite Materials and Their Relevance to B2B Buyers?
The evolution of composite materials dates back to ancient times, with early applications including reinforced wood and linen. However, the modern era of composites began in the early 20th century with the development of synthetic resins and glass fibers. The aerospace industry, particularly with the introduction of carbon fiber composites in the 1960s, significantly influenced the growth of this sector. Today, composites are integral in various industries, including construction, where they are utilized for panels that offer enhanced strength, durability, and aesthetic appeal.
For B2B buyers, understanding this historical context is vital as it highlights the ongoing innovations and improvements in composite technology. The advancements in manufacturing processes and material science not only enhance product performance but also create opportunities for cost-effective solutions. As the market continues to evolve, buyers must stay informed about emerging technologies and trends to leverage the full potential of composite panels in their respective industries.
Frequently Asked Questions (FAQs) for B2B Buyers of composite panel china
- How do I choose the right composite panel supplier in China?
Choosing the right supplier for composite panels in China involves thorough research and due diligence. Start by assessing the supplier’s industry experience, product quality, and certifications (such as ISO). Request samples to evaluate the material’s properties and durability. Additionally, consider the supplier’s communication responsiveness and willingness to accommodate your specific needs. Utilize platforms like Alibaba or trade shows to connect with reputable suppliers and read reviews from other international buyers to gauge reliability.
-
What are the most common applications for composite panels?
Composite panels are versatile and used across various industries, including construction, automotive, aerospace, and marine. They are ideal for building facades, interior partitions, signage, and furniture due to their lightweight and durable nature. In the automotive sector, they contribute to weight reduction while maintaining strength. Understanding your specific application will help you choose the right type of composite panel that meets your performance and aesthetic requirements. -
What is the minimum order quantity (MOQ) for composite panels from China?
Minimum order quantities (MOQs) for composite panels can vary significantly between suppliers and the type of panels being ordered. Generally, MOQs range from 100 to 1,000 square meters, but some suppliers may accommodate smaller orders for a higher price. It’s essential to discuss your needs upfront with the supplier to find a mutually agreeable MOQ that fits your project scale while ensuring cost-effectiveness. -
What payment terms are typical when sourcing composite panels from China?
When sourcing composite panels, common payment terms include a 30% deposit upfront and the remaining 70% before shipping. Some suppliers may offer more flexible terms based on your relationship and order size. Be cautious about using secure payment methods such as letters of credit or escrow services to protect your investment. Always clarify terms in the contract to prevent misunderstandings. -
How can I ensure quality assurance for composite panels sourced from China?
To ensure quality assurance, request certifications and test reports from the supplier, such as ASTM or ISO standards. Conduct factory audits, if possible, to assess manufacturing processes and quality control measures. Implement a third-party inspection before shipment to verify that the panels meet your specifications. Establish clear quality criteria in your purchase agreement to hold suppliers accountable. -
What logistics considerations should I keep in mind when importing composite panels from China?
When importing composite panels, consider shipping methods (sea freight is often more cost-effective for large orders), lead times, and customs clearance processes. Collaborate with a reliable freight forwarder who understands regulations for your destination country. Ensure that the shipping terms (Incoterms) are clearly defined, and anticipate potential delays or additional costs related to tariffs or inspections. -
Can I customize composite panels to suit my specific needs?
Yes, many suppliers in China offer customization options for composite panels, including size, color, texture, and specific material properties. Discuss your requirements with the supplier early in the negotiation process to understand the feasibility and any additional costs involved. Providing detailed specifications and design files will help ensure that the final product meets your expectations. -
What are the environmental considerations when sourcing composite panels?
When sourcing composite panels, consider the environmental impact of the materials and manufacturing processes. Look for suppliers that use eco-friendly resins and sustainable raw materials. Additionally, inquire about the recyclability of the panels and the supplier’s waste management practices. Choosing environmentally responsible suppliers can enhance your brand’s sustainability profile and comply with regulations in your target market.
Important Disclaimer & Terms of Use
⚠️ Important Disclaimer
The information provided in this guide, including content regarding manufacturers, technical specifications, and market analysis, is for informational and educational purposes only. It does not constitute professional procurement advice, financial advice, or legal advice.
While we have made every effort to ensure the accuracy and timeliness of the information, we are not responsible for any errors, omissions, or outdated information. Market conditions, company details, and technical standards are subject to change.
B2B buyers must conduct their own independent and thorough due diligence before making any purchasing decisions. This includes contacting suppliers directly, verifying certifications, requesting samples, and seeking professional consultation. The risk of relying on any information in this guide is borne solely by the reader.
Strategic Sourcing Conclusion and Outlook for composite panel china
In the evolving landscape of composite panels from China, strategic sourcing emerges as a crucial driver for international B2B buyers. Understanding the unique advantages of composite materials—such as their lightweight nature, superior strength, and resistance to environmental factors—can significantly enhance your procurement strategy. Buyers from Africa, South America, the Middle East, and Europe (including key markets like Germany and Spain) should prioritize partnerships with reputable manufacturers who adhere to international quality standards, ensuring reliability and performance.
As the demand for composite panels continues to rise across various sectors, leveraging competitive pricing and innovative manufacturing processes from Chinese suppliers can result in substantial cost savings and improved product offerings. Emphasizing long-term relationships with suppliers can also foster collaboration and innovation, leading to tailored solutions that meet specific market needs.
Looking ahead, the future of composite panels in global markets is promising. By staying informed about technological advancements and market trends, B2B buyers can position themselves advantageously. Engage with suppliers today to explore how composite materials can transform your projects and drive your business forward in this dynamic industry.