Cut Costs with Quality: Spare Parts China Guide (2025)
Introduction: Navigating the Global Market for spare parts china
Navigating the intricate landscape of sourcing spare parts from China can be a daunting task for international B2B buyers, particularly those from regions such as Africa, South America, the Middle East, and Europe. As businesses strive to maintain operational efficiency, the need for reliable and quality spare parts becomes paramount. This guide aims to address the critical challenges of sourcing spare parts from China by providing detailed insights into the types of parts available, their applications across various industries, and effective strategies for supplier vetting.
Understanding the dynamics of the Chinese market is essential for making informed purchasing decisions. This guide will cover essential aspects such as pricing structures, shipping logistics, and quality assurance practices, which are vital for minimizing risks and maximizing value. Whether you are in Egypt looking for automotive components or in Mexico seeking industrial machinery parts, this comprehensive resource will empower you with the knowledge necessary to navigate the complexities of international procurement.
By equipping B2B buyers with actionable insights and strategies, this guide aims to facilitate smoother transactions and foster long-term partnerships with Chinese suppliers. As you delve deeper into this guide, you’ll discover how to leverage the opportunities presented by China‘s robust manufacturing sector while mitigating potential pitfalls, ultimately enhancing your operational capabilities and competitive edge in the global market.
Understanding spare parts china Types and Variations
Type Name | Key Distinguishing Features | Primary B2B Applications | Brief Pros & Cons for Buyers |
---|---|---|---|
OEM Spare Parts | Manufactured by original equipment manufacturers | Automotive, machinery, electronics | Pros: High compatibility, quality assurance. Cons: Higher cost, limited availability. |
Aftermarket Spare Parts | Third-party parts designed to replace OEM components | Automotive, home appliances, machinery | Pros: Often cheaper, wider availability. Cons: Variable quality, potential compatibility issues. |
Custom Spare Parts | Tailored components designed to meet specific requirements | Aerospace, industrial equipment | Pros: Exact fit for unique needs, enhanced performance. Cons: Longer lead times, higher costs. |
Re-manufactured Parts | Refurbished parts that restore functionality to used components | Automotive, industrial machinery | Pros: Cost-effective, environmentally friendly. Cons: May not have the same lifespan as new parts. |
Generic Spare Parts | Non-branded parts that serve as alternatives to name brands | Various industries | Pros: Cost savings, wide range of applications. Cons: Quality can be inconsistent, lack of support. |
What Are OEM Spare Parts and Their Key Characteristics?
OEM (Original Equipment Manufacturer) spare parts are produced by the same company that manufactured the original components of the equipment. These parts are designed to meet the exact specifications and standards set by the original manufacturer, ensuring high compatibility and reliability. B2B buyers in sectors like automotive, machinery, and electronics often prefer OEM parts for their quality assurance and warranty coverage. However, these benefits come at a higher price point and may have limited availability, making them a significant investment.
How Do Aftermarket Spare Parts Differ from OEM Options?
Aftermarket spare parts are produced by third-party manufacturers and aim to replace OEM components. They are often more affordable and widely available, catering to industries such as automotive and home appliances. While they can provide cost savings, buyers must be cautious about the variable quality and potential compatibility issues that can arise. It is crucial for B2B buyers to verify the reliability of the aftermarket supplier to ensure that the parts will perform adequately in their applications.
What Makes Custom Spare Parts a Valuable Investment?
Custom spare parts are specifically designed to meet unique requirements, making them ideal for specialized applications in industries like aerospace and industrial equipment. These parts offer enhanced performance and a perfect fit, ensuring that machinery operates at optimal levels. However, B2B buyers should consider the longer lead times and potentially higher costs associated with custom manufacturing. The investment may be worthwhile for businesses with specific operational needs that cannot be met by standard parts.
What Are the Advantages of Re-manufactured Parts?
Re-manufactured parts involve refurbishing used components to restore their functionality. This option is particularly appealing in the automotive and industrial machinery sectors, where cost-effectiveness and environmental sustainability are priorities. While re-manufactured parts can save money and reduce waste, buyers should be aware that they may not have the same lifespan as new components. Thorough evaluation of the re-manufacturing process and supplier reputation is essential to ensure reliability.
Are Generic Spare Parts a Practical Choice for B2B Buyers?
Generic spare parts are non-branded alternatives that can serve a variety of applications across different industries. They often come at a lower price point, making them attractive for budget-conscious buyers. However, the quality of generic parts can vary significantly, and there may be a lack of support or warranty. B2B buyers should conduct careful research and potentially test these parts in less critical applications before fully integrating them into their operations.
Related Video: Functions and Classification of Spare Parts Management
Key Industrial Applications of spare parts china
Industry/Sector | Specific Application of spare parts china | Value/Benefit for the Business | Key Sourcing Considerations for this Application |
---|---|---|---|
Manufacturing | Machinery components | Enhanced operational efficiency through reliable parts | Quality certifications, supplier reliability, and lead times |
Automotive | Replacement parts for vehicles | Cost-effective repairs and maintenance | OEM standards, warranty terms, and shipping logistics |
Agriculture | Equipment spare parts | Improved productivity and reduced downtime | Compatibility with existing machinery, local regulations, and pricing |
Oil & Gas | Drilling equipment components | Increased safety and operational uptime | Compliance with industry standards, material specifications, and sourcing transparency |
Construction | Heavy machinery spare parts | Extended lifespan of equipment and reduced capital costs | Supplier certifications, after-sales support, and custom solutions |
How Are Spare Parts from China Used in Manufacturing?
In the manufacturing sector, spare parts from China are crucial for maintaining machinery and production lines. They help mitigate downtime, which can be costly for businesses. International buyers, particularly from Africa and South America, often seek high-quality components that meet specific operational standards. Sourcing considerations include assessing the supplier’s quality certifications and ensuring timely delivery to avoid disruptions in production.
What Are the Benefits of Using Automotive Spare Parts from China?
Automotive spare parts sourced from China are essential for the maintenance and repair of vehicles. They provide a cost-effective solution for businesses looking to minimize operational expenses. Buyers from the Middle East and Europe should ensure that these parts meet OEM standards to guarantee compatibility and performance. Key factors to consider include warranty terms and the supplier’s reliability in meeting shipping deadlines, which can significantly impact service delivery.
How Do Agriculture Spare Parts Enhance Productivity?
In the agricultural sector, spare parts from China play a vital role in keeping farming equipment operational. By ensuring that machinery is well-maintained, farmers can significantly reduce downtime and improve overall productivity. Buyers from regions like Africa should focus on compatibility with existing equipment and compliance with local regulations when sourcing these parts. Pricing is also a crucial consideration, as it directly impacts the overall cost of farming operations.
What Is the Importance of Spare Parts in the Oil & Gas Industry?
The oil and gas industry relies heavily on spare parts from China for drilling equipment and other critical components. These parts are essential for maintaining safety standards and operational efficiency. International buyers must prioritize compliance with industry regulations and material specifications when sourcing. Transparency in the sourcing process is vital, as it builds trust and ensures that the parts meet the rigorous demands of the industry.
How Do Spare Parts Impact Construction Equipment Longevity?
In construction, spare parts sourced from China are vital for the maintenance of heavy machinery. They help extend the lifespan of equipment, thereby reducing the need for costly replacements. Buyers, especially from Europe and South America, should consider supplier certifications and the level of after-sales support available. Custom solutions may also be necessary to meet specific project requirements, making it essential to engage with suppliers who can offer tailored services.
Related Video: Industrial Control Panel Basics
3 Common User Pain Points for ‘spare parts china’ & Their Solutions
Scenario 1: Navigating Quality Control Issues with Spare Parts from China
The Problem: A B2B buyer in South America is sourcing spare parts for machinery but frequently encounters issues with inconsistent quality. Parts arrive that do not meet specifications, leading to costly delays and production downtime. The buyer feels frustrated, as they have invested time and resources into building relationships with suppliers, only to face quality-related setbacks.
The Solution: To mitigate quality control issues, it is crucial to establish a robust vetting process for suppliers. Begin by conducting thorough due diligence, which includes requesting product samples and inspecting them for compliance with international standards. Utilize third-party inspection services based in China that specialize in quality assurance. These services can perform pre-shipment inspections to verify that the parts meet agreed specifications. Additionally, consider implementing a quality agreement that outlines specific metrics for quality and performance. This proactive approach helps ensure that the buyer receives reliable parts and can significantly reduce the risk of operational disruptions.
Scenario 2: Overcoming Language and Cultural Barriers in Communication
The Problem: An international buyer from Egypt is struggling to communicate effectively with a supplier in China. Misunderstandings arise due to language barriers and differing business practices, leading to incorrect orders and frustration on both sides. This scenario often results in wasted time and resources as the buyer attempts to clarify issues and re-order parts.
The Solution: To bridge the communication gap, it is advisable for buyers to engage a local intermediary or hire bilingual staff who are familiar with both cultures. This approach facilitates clearer communication and helps navigate cultural nuances that may affect negotiations and order processes. Additionally, leveraging technology such as translation software can enhance communication. When placing orders, always confirm specifications in writing and request visual confirmations, such as photos or diagrams, to ensure both parties have a mutual understanding. This strategy not only enhances order accuracy but also builds stronger relationships with suppliers, creating a more efficient procurement process.
Scenario 3: Managing Lead Times and Delivery Delays
The Problem: A buyer in Europe is facing chronic delays in receiving spare parts from Chinese suppliers, which is impacting their ability to meet customer demands. Despite placing orders well in advance, they find themselves constantly reacting to late deliveries, which erodes their reputation and increases operational costs.
The Solution: To address lead time challenges, it is essential to implement a more strategic sourcing plan. Start by analyzing past order histories to identify patterns in delivery times from various suppliers. Once you have this data, engage with multiple suppliers to compare their lead times and reliability. Incorporating a just-in-time inventory strategy can also be beneficial, where orders are placed only as needed, reducing the risk of overstock and associated costs. Establish clear communication protocols with suppliers regarding delivery expectations and timelines, and consider using logistics partners that specialize in international shipping to streamline the process. By proactively managing supplier relationships and logistics, buyers can significantly improve their delivery performance and maintain customer satisfaction.
Strategic Material Selection Guide for spare parts china
When selecting materials for spare parts sourced from China, international B2B buyers must consider various factors that influence product performance and compliance with regional standards. This guide analyzes common materials used in spare parts manufacturing, focusing on their properties, advantages, disadvantages, and specific considerations for buyers from Africa, South America, the Middle East, and Europe.
What Are the Key Properties of Aluminum in Spare Parts?
Aluminum is a lightweight metal known for its excellent corrosion resistance and good thermal conductivity. It typically performs well under moderate temperature and pressure conditions, making it suitable for various applications. Its low density contributes to reduced shipping costs, which is a significant advantage for international buyers.
Pros:
– Lightweight and easy to machine.
– High corrosion resistance, ideal for humid environments.
– Cost-effective for mass production.
Cons:
– Lower strength compared to steel, which may limit its use in high-stress applications.
– Susceptible to wear in abrasive environments.
Impact on Application:
Aluminum is compatible with a range of media, including water and many chemicals, but may not be suitable for high-temperature steam applications.
Considerations for International Buyers:
Buyers should ensure compliance with international standards such as ASTM and DIN. In regions like Europe, there is a strong preference for aluminum alloys that meet specific strength requirements.
How Does Steel Compare as a Material for Spare Parts?
Steel is renowned for its high strength and durability, making it a popular choice for heavy-duty applications. It offers excellent temperature and pressure ratings, making it suitable for demanding environments.
Pros:
– Exceptional strength and toughness.
– Versatile; can be alloyed for enhanced properties.
– Cost-effective for large-scale applications.
Cons:
– Prone to corrosion without protective coatings.
– Heavier than alternative materials, which can increase shipping costs.
Impact on Application:
Steel is suitable for high-pressure and high-temperature applications, but its susceptibility to rust necessitates protective measures in corrosive environments.
Considerations for International Buyers:
Buyers should be aware of the specific grades of steel required for their applications and ensure they meet local standards. For example, compliance with JIS standards is crucial for Japanese markets.
What Are the Advantages of Using Plastics in Spare Parts?
Plastics, particularly engineering plastics, are increasingly used in spare parts due to their lightweight nature and resistance to corrosion. They can be molded into complex shapes, offering design flexibility.
Pros:
– Lightweight, which reduces shipping costs.
– Excellent resistance to chemicals and corrosion.
– Can be produced in various colors and finishes.
Cons:
– Generally lower strength compared to metals.
– Temperature sensitivity may limit their use in high-heat applications.
Impact on Application:
Plastics are suitable for non-structural components and applications where weight savings are critical. However, their performance can degrade under extreme temperatures.
Considerations for International Buyers:
Buyers should verify that the plastics used comply with relevant regulations, especially in food and medical applications. Standards like FDA compliance are essential in regions such as North America and Europe.
Why Choose Composites for Spare Parts Applications?
Composite materials, such as carbon fiber reinforced polymers, offer a unique combination of strength and lightweight properties. They are increasingly popular in high-performance applications.
Pros:
– High strength-to-weight ratio.
– Excellent fatigue resistance.
– Tailorable properties for specific applications.
Cons:
– Higher manufacturing complexity and costs.
– Limited recyclability compared to metals.
Impact on Application:
Composites are ideal for aerospace and automotive applications where performance is critical. However, they may not be suitable for applications involving high temperatures or harsh chemical environments.
Considerations for International Buyers:
Buyers should ensure that composite materials meet specific industry standards and certifications, particularly in aerospace and automotive sectors.
Summary Table of Material Selection for Spare Parts
Material | Typical Use Case for spare parts china | Key Advantage | Key Disadvantage/Limitation | Relative Cost (Low/Med/High) |
---|---|---|---|---|
Aluminum | Automotive components, housing parts | Lightweight, corrosion-resistant | Lower strength than steel | Medium |
Steel | Structural components, machinery parts | High strength and durability | Prone to corrosion | Low |
Plastics | Non-structural components, housings | Lightweight, chemical resistance | Lower strength, temperature sensitive | Low |
Composites | Aerospace, high-performance parts | High strength-to-weight ratio | High cost, manufacturing complexity | High |
This strategic material selection guide provides valuable insights for international B2B buyers, enabling informed decisions when sourcing spare parts from China. Understanding the properties, advantages, and limitations of each material will help buyers select the most suitable options for their specific applications.
In-depth Look: Manufacturing Processes and Quality Assurance for spare parts china
What Are the Typical Manufacturing Processes for Spare Parts in China?
When sourcing spare parts from China, understanding the manufacturing processes is crucial for B2B buyers. The manufacturing of spare parts typically involves several key stages, which include material preparation, forming, assembly, and finishing. Each of these stages employs various techniques and technologies that impact the final product’s quality and performance.
How Is Material Prepared in the Manufacturing Process?
The first step in the manufacturing process is material preparation. This involves selecting the appropriate raw materials, which can vary from metals to plastics, depending on the specific requirements of the spare part. The materials are then subjected to processes such as cutting, machining, and surface treatment to ensure they meet the specifications required for the subsequent manufacturing stages.
For example, metals may undergo processes like casting or forging, while plastics might be injection molded. Quality control at this stage is essential to eliminate defects that could lead to failures in later stages. Buyers should inquire about the suppliers’ material sourcing practices to ensure they meet international standards.
What Techniques Are Used in Forming Spare Parts?
Once the materials are prepared, the forming stage begins. This involves shaping the materials into the desired form through various techniques, including:
- Casting: Molten metal is poured into a mold to create complex shapes.
- Machining: Materials are cut and shaped using tools and equipment like lathes and mills.
- Forging: Metal is shaped through compressive forces, often resulting in stronger parts.
- Injection Molding: This technique is primarily used for plastics, where molten plastic is injected into a mold.
Each of these techniques has its advantages and is chosen based on the part’s complexity, volume, and material properties. Understanding these techniques can help buyers assess the capabilities of potential suppliers in China.
How Does Assembly Fit into the Spare Parts Manufacturing Process?
After forming, the next stage is assembly, where various components are brought together to create the final product. This process can involve manual labor or automated systems, depending on the complexity and volume of the parts being produced.
Quality assurance during assembly is critical, as improper assembly can lead to product failures. B2B buyers should inquire about the assembly processes used by suppliers, including the types of tools and machinery involved, and whether they employ automated assembly lines to improve precision and efficiency.
What Finishing Processes Are Commonly Used?
The final stage in manufacturing spare parts is finishing, which enhances the product’s appearance and performance. Common finishing processes include:
- Surface Treatment: Techniques like anodizing, painting, or plating to improve corrosion resistance and aesthetic appeal.
- Quality Inspection: Final checks are performed to ensure that the product meets all specifications and standards.
Finishing is a vital step that can significantly affect the durability and functionality of spare parts. Buyers should understand the finishing processes employed by suppliers and their impact on the final product.
What Quality Assurance Measures Are Implemented in Spare Parts Manufacturing?
Quality assurance (QA) is an integral aspect of the manufacturing process for spare parts in China. International standards such as ISO 9001, as well as industry-specific certifications like CE for Europe and API for the oil and gas sector, guide the quality management systems of manufacturers.
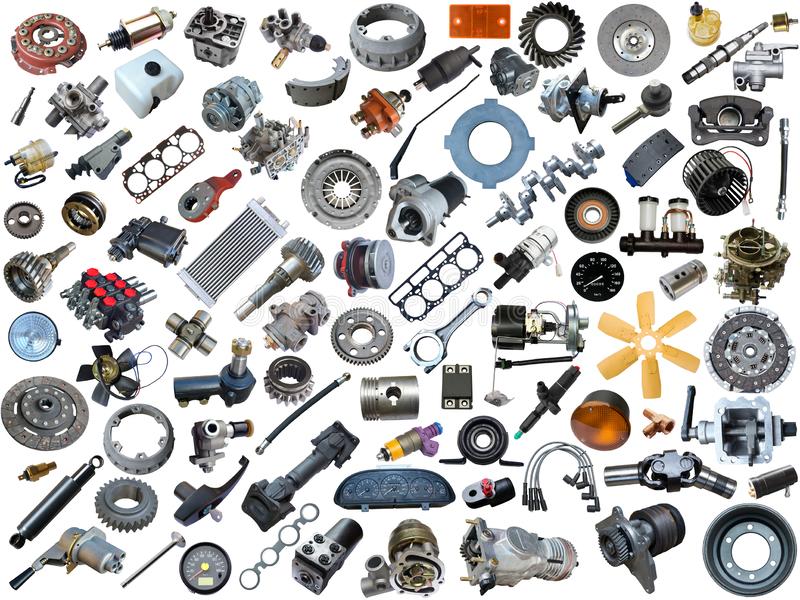
A stock image related to spare parts china.
Which International Standards Should Buyers Be Aware Of?
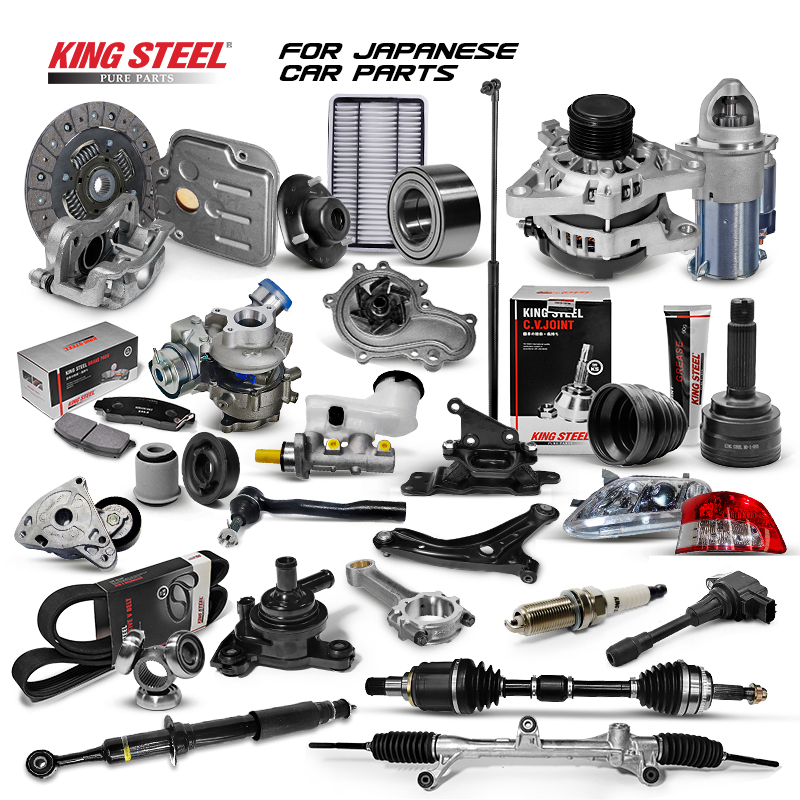
A stock image related to spare parts china.
Understanding the relevant international standards is essential for B2B buyers. ISO 9001 outlines the requirements for a quality management system and is recognized globally. Compliance with this standard indicates that a manufacturer has a robust quality management process in place.
In addition to ISO standards, industry-specific certifications may be required. For instance, CE marking is crucial for products sold in the European market, ensuring they meet safety and environmental requirements. Buyers should verify that suppliers hold the necessary certifications relevant to their industry.
What Are the Key Quality Control Checkpoints?
Quality control (QC) is typically organized into several checkpoints throughout the manufacturing process:
- Incoming Quality Control (IQC): Inspects raw materials before they enter the production line.
- In-Process Quality Control (IPQC): Monitors the manufacturing process to ensure that the parts are being produced according to specifications.
- Final Quality Control (FQC): Conducts final inspections and tests on the completed parts before shipment.
These checkpoints help to identify and rectify issues at various stages of production, reducing the likelihood of defective products reaching the buyer.
How Can B2B Buyers Verify Supplier Quality Control?
To ensure that suppliers maintain high-quality standards, B2B buyers can implement several verification strategies:
- Audits: Conducting on-site audits of suppliers can provide insights into their manufacturing processes and quality management systems.
- Quality Reports: Requesting regular quality reports can help buyers monitor the supplier’s performance over time.
- Third-Party Inspections: Engaging third-party inspection agencies can provide an unbiased assessment of the supplier’s quality control practices.
Buyers from regions such as Africa, South America, the Middle East, and Europe should be particularly diligent in verifying quality control measures, as these can vary significantly between suppliers.
What Common Testing Methods Are Used in Quality Assurance?
Quality assurance in spare parts manufacturing also involves various testing methods to ensure that products meet the required specifications. Common testing methods include:
- Dimensional Inspection: Verifying that the dimensions of the parts conform to specified tolerances.
- Functional Testing: Assessing whether the spare parts perform their intended functions under operational conditions.
- Material Testing: Conducting tests like tensile strength and hardness to evaluate the material properties.
Understanding these testing methods can help buyers ascertain the reliability and performance of the spare parts they are sourcing.
Conclusion: Navigating Manufacturing and Quality Assurance in China
For international B2B buyers, particularly from Africa, South America, the Middle East, and Europe, comprehending the manufacturing processes and quality assurance measures for spare parts in China is essential. By focusing on material preparation, forming, assembly, and finishing, alongside rigorous quality control practices, buyers can make informed decisions and minimize risks associated with sourcing spare parts from this dynamic market.
Practical Sourcing Guide: A Step-by-Step Checklist for ‘spare parts china’
To successfully procure spare parts from China, it’s essential to follow a structured approach that minimizes risks and maximizes quality. This checklist provides actionable insights for international B2B buyers, particularly from Africa, South America, the Middle East, and Europe.
Step 1: Define Your Technical Specifications
Clearly outline the specifications for the spare parts you need. This includes dimensions, materials, tolerances, and any certifications required. A well-defined specification not only helps you communicate effectively with suppliers but also ensures that you receive products that meet your operational needs.
- Consider functional requirements: Understand how the spare parts will be used within your operations.
- Document everything: Create a detailed technical document that can be shared with potential suppliers.
Step 2: Research and Shortlist Suppliers
Conduct thorough research to identify potential suppliers in China. Use platforms like Alibaba, Global Sources, and industry-specific directories. Shortlist suppliers based on their product offerings, reputation, and experience in your industry.
- Check reviews and ratings: Look for feedback from other international buyers to gauge reliability.
- Evaluate company history: Consider the length of time they have been in business and their track record with international clients.
Step 3: ✅ Verify Supplier Certifications
Before engaging further, ensure that suppliers possess the necessary certifications relevant to your industry. Certifications such as ISO, CE, or specific industry standards are critical indicators of quality and reliability.
- Request documentation: Ask suppliers for copies of their certifications and ensure they are up to date.
- Cross-check with certifying bodies: Validate the authenticity of the certifications directly through the certifying organizations.
Step 4: Request Samples for Evaluation
Always request samples before placing a bulk order. This allows you to assess the quality and suitability of the spare parts against your specifications.
- Set clear evaluation criteria: Determine what aspects of the sample are most important (e.g., fit, finish, functionality).
- Consider lead times: Understand the time it will take to receive samples and factor this into your procurement timeline.
Step 5: Negotiate Terms and Pricing
Engage in discussions with shortlisted suppliers to negotiate pricing, payment terms, and delivery schedules. Be prepared to discuss minimum order quantities and potential discounts for bulk orders.
- Ask about payment methods: Secure options that protect your interests, such as letters of credit or escrow services.
- Clarify delivery terms: Ensure you understand shipping responsibilities and timelines, especially for international transactions.
Step 6: Conduct a Factory Audit (if possible)
If feasible, conduct a factory audit to inspect the supplier’s operations. This step is crucial for large orders or long-term partnerships, as it provides insights into the supplier’s capabilities and quality control processes.
- Look for quality management practices: Assess how the supplier ensures product quality throughout production.
- Evaluate working conditions: Ensure that the supplier adheres to ethical labor practices.
Step 7: Establish a Communication Plan
Effective communication is vital throughout the sourcing process. Establish a clear plan for how you will communicate with your supplier, including frequency and preferred channels.
- Designate a point of contact: Ensure that there is a dedicated person on both sides to facilitate smooth interactions.
- Use technology: Consider using project management tools for tracking progress and addressing any issues promptly.
By following this practical sourcing guide, you can enhance your procurement process for spare parts from China, ensuring quality, reliability, and value for your business.
Comprehensive Cost and Pricing Analysis for spare parts china Sourcing
When considering sourcing spare parts from China, international B2B buyers need to understand the comprehensive cost structure and pricing strategies involved. This knowledge is essential for making informed purchasing decisions and optimizing the supply chain.
What Are the Key Cost Components in Sourcing Spare Parts from China?
-
Materials: The cost of raw materials can significantly impact the overall price. Buyers should evaluate the types of materials required for their specific spare parts, as prices can vary widely based on quality, availability, and market fluctuations.
-
Labor: Labor costs in China have been rising, though they remain competitive compared to many other countries. Understanding the labor intensity of the manufacturing process for the spare parts can help buyers gauge potential costs.
-
Manufacturing Overhead: This includes costs associated with factory operations, utilities, equipment depreciation, and administrative expenses. Buyers should inquire about these costs during negotiations to ensure transparency.
-
Tooling: Custom tooling can be a significant upfront investment, particularly for specialized parts. Buyers should assess whether the tooling costs are included in the quoted price or if they will be charged separately.
-
Quality Control (QC): Implementing quality control measures can add to the costs but is crucial for ensuring the reliability of the spare parts. Buyers should consider incorporating QC costs into their budgeting to avoid potential issues.
-
Logistics: Shipping costs can vary based on the mode of transport (air, sea, or land) and the distance from the manufacturing facility to the buyer’s location. Understanding the logistics involved is vital for accurate cost estimation.
-
Margin: Suppliers typically add a profit margin to their costs. This margin can vary based on the supplier’s reputation, the complexity of the parts, and the relationship established with the buyer.
How Do Price Influencers Affect the Cost of Spare Parts?
-
Volume and Minimum Order Quantity (MOQ): Higher order volumes often lead to lower per-unit costs due to economies of scale. Understanding the MOQ set by suppliers can help buyers negotiate better pricing.
-
Specifications and Customization: Customized parts may incur additional costs due to the complexity of design and manufacturing processes. Buyers should balance the need for customization with budget constraints.
-
Quality and Certifications: Parts that meet international quality standards and certifications may come at a premium. Buyers should weigh the importance of quality against potential savings.
-
Supplier Factors: Different suppliers may offer varying levels of service, quality, and pricing. Establishing relationships with reputable suppliers can lead to better pricing and reliability.
-
Incoterms: The terms of shipping and delivery (Incoterms) can significantly impact costs. Understanding terms such as FOB (Free on Board) or CIF (Cost, Insurance, and Freight) can help buyers manage their total costs effectively.
What Are Some Effective Buyer Tips for Cost-Efficiency?
-
Negotiation Strategies: Engage in negotiations with suppliers to secure better pricing, especially for larger orders. Building a strong relationship can lead to favorable terms and discounts.
-
Total Cost of Ownership (TCO): Consider not just the purchase price but all associated costs, including logistics, duties, and potential downtime if parts fail. A lower initial price may not always equate to better value.
-
Pricing Nuances for International Buyers: Be aware of currency fluctuations and their impact on pricing. Also, familiarize yourself with the local regulations and tariffs that may apply to imports.
-
Research and Comparison: Conduct thorough research on multiple suppliers and compare their offerings, prices, and service levels. This diligence can help identify the best value options.
-
Seek Expert Advice: Leveraging local experts or consultants familiar with the Chinese market can provide valuable insights and potentially save costs in the long run.
Disclaimer on Indicative Prices
Prices for spare parts can fluctuate based on numerous factors, including market conditions, material costs, and geopolitical influences. Therefore, it is essential for buyers to obtain updated quotes and conduct due diligence to ensure they are making informed purchasing decisions.
Alternatives Analysis: Comparing spare parts china With Other Solutions
Understanding Alternative Solutions for Spare Parts Procurement
When sourcing spare parts, particularly for machinery and equipment, international B2B buyers often explore various procurement options. While “Spare Parts China” has become a popular choice due to its cost-effectiveness and vast selection, it is essential to evaluate alternative solutions that may better suit specific operational needs. This section delves into viable alternatives, assessing their performance, cost, ease of implementation, maintenance requirements, and ideal use cases.
Comparison Table of Spare Parts Solutions
Comparison Aspect | Spare Parts China | Local Suppliers | OEM (Original Equipment Manufacturer) Parts |
---|---|---|---|
Performance | High variety, variable quality | Generally high quality | Guaranteed compatibility and quality |
Cost | Low to moderate | Moderate to high | High |
Ease of Implementation | Moderate (language, logistics) | Easy (local knowledge) | Moderate (depends on contract) |
Maintenance | Variable, depends on part quality | Consistent, known vendors | High reliability with warranties |
Best Use Case | Cost-sensitive projects requiring bulk parts | Urgent needs and specialized service | Critical components requiring precision |
What Are the Advantages and Disadvantages of Sourcing from Local Suppliers?
Local suppliers often provide high-quality spare parts that are readily available, reducing lead times significantly. This is crucial for businesses that rely on quick turnarounds. Additionally, local suppliers have a better understanding of regional market demands, which can lead to more tailored solutions and services. However, the cost can be higher compared to sourcing from China, and the variety might be limited depending on the specific local market.
How Do OEM Parts Compare in Terms of Quality and Reliability?
OEM parts are designed and manufactured by the original equipment manufacturers, ensuring that they meet the exact specifications of the machinery. This guarantees compatibility and high quality, making them the preferred choice for critical components where reliability is paramount. However, they come at a premium price point, and obtaining these parts may involve longer procurement processes due to contractual obligations and distribution channels.
Conclusion: How to Choose the Right Spare Parts Solution
Selecting the right spare parts solution depends on several factors, including budget constraints, urgency, and the critical nature of the equipment involved. For cost-sensitive projects, “Spare Parts China” might offer the best value, but for urgent needs or specialized service, local suppliers can provide quicker and more reliable options. On the other hand, if quality and compatibility are non-negotiable, investing in OEM parts is the best strategy. B2B buyers should assess their operational priorities and align their procurement strategy accordingly to ensure optimal performance and minimal downtime.
Essential Technical Properties and Trade Terminology for spare parts china
What Are the Key Technical Properties of Spare Parts from China?
Understanding the technical properties of spare parts is crucial for international B2B buyers, especially when sourcing from China. Here are some essential specifications to consider:
1. Material Grade: What Should You Know?
Material grade refers to the specific composition and quality of the material used in manufacturing spare parts. Common materials include metals (like steel and aluminum), plastics, and composites. The grade affects durability, corrosion resistance, and overall performance. For instance, using a higher-grade steel can significantly enhance the lifespan of machinery components, which is vital for industries like manufacturing and automotive.
2. Tolerance: Why Is It Important?
Tolerance is the permissible limit or limits of variation in a physical dimension. In spare parts, tight tolerances are essential to ensure that components fit and function as intended. For example, an engine part with a tolerance of ±0.01 mm will fit perfectly, reducing the risk of failure. Buyers should request detailed tolerance specifications to avoid costly replacements or repairs.
3. Surface Finish: How Does It Affect Performance?
Surface finish refers to the texture and quality of the surface of a part. It can influence not only aesthetics but also functionality, such as friction, wear resistance, and corrosion resistance. A smoother surface finish can reduce friction in moving parts, thereby extending the lifespan of machinery. Understanding the required surface finish is crucial for applications in sectors like aerospace and automotive.
4. Heat Treatment: What Is Its Role?
Heat treatment processes, such as annealing or quenching, are applied to enhance the mechanical properties of materials. These processes can improve hardness, strength, and resistance to wear. For B2B buyers, understanding whether heat treatment is necessary for specific parts can prevent premature failure and ensure reliability in demanding applications.
5. Certification Standards: Which Ones Matter?
Certification standards such as ISO, ASTM, or DIN are essential in ensuring that spare parts meet specific quality and safety requirements. These certifications can serve as a benchmark for quality assurance, giving buyers confidence in the products they source. When dealing with suppliers, always inquire about their certification status to ensure compliance with international standards.
What Are Common Trade Terms You Should Know in the Spare Parts Industry?
Familiarity with industry jargon can significantly streamline communication and negotiation processes. Here are some commonly used terms:
1. OEM (Original Equipment Manufacturer): What Does It Mean?
OEM refers to companies that produce parts or equipment that may be marketed by another manufacturer. In the spare parts industry, OEM parts are often preferred due to their quality and compatibility with original machinery. Understanding the difference between OEM and aftermarket parts can help buyers make informed decisions regarding reliability and performance.
2. MOQ (Minimum Order Quantity): Why Is It Important?
MOQ is the smallest quantity of a product that a supplier is willing to sell. This term is particularly relevant for international buyers as it can affect the overall cost of procurement. Buyers should negotiate MOQs that align with their needs to avoid excess inventory or increased costs.
3. RFQ (Request for Quotation): How Should You Use It?
An RFQ is a document used by buyers to solicit price quotes from suppliers for specific products or services. It should include detailed specifications, quantities, and delivery timelines. A well-crafted RFQ can lead to competitive pricing and better supplier relationships.
4. Incoterms: What Are They and Why Do They Matter?
Incoterms (International Commercial Terms) are a set of rules that define the responsibilities of buyers and sellers in international transactions. They clarify who is responsible for shipping, insurance, and tariffs. Understanding Incoterms is vital for international B2B buyers to avoid misunderstandings and ensure smooth transactions.
5. Lead Time: How Does It Impact Your Supply Chain?
Lead time is the time it takes from placing an order to receiving the goods. This period can vary based on factors like manufacturing complexity and shipping logistics. Buyers should account for lead time in their planning to avoid disruptions in their supply chains.
By understanding these technical properties and trade terms, international B2B buyers can make more informed decisions when sourcing spare parts from China, ultimately leading to better procurement strategies and enhanced operational efficiency.
Navigating Market Dynamics and Sourcing Trends in the spare parts china Sector
What Are the Key Market Dynamics Influencing Spare Parts Sourcing from China?
The spare parts sector in China has experienced substantial growth, driven by factors such as globalization, technological advancements, and increasing demand for efficient supply chains. For international B2B buyers, especially those from Africa, South America, the Middle East, and Europe, understanding these market dynamics is crucial. The adoption of Industry 4.0 technologies, including IoT and AI, is transforming manufacturing processes, enhancing quality control, and streamlining logistics. This evolution allows suppliers to respond rapidly to market demands, thus reducing lead times.
Emerging trends such as e-commerce platforms and digital marketplaces are revolutionizing how spare parts are sourced. These platforms provide buyers with access to a wide array of products and suppliers, facilitating competitive pricing and better inventory management. Additionally, the rise of cross-border trade agreements has lowered tariffs and increased the flow of goods, making it easier for buyers to import spare parts from China. However, international buyers must also be aware of geopolitical tensions and their potential impacts on trade regulations and supply chain stability.
How Important Is Sustainability and Ethical Sourcing in the Spare Parts Sector?
Sustainability and ethical sourcing are becoming increasingly vital in the spare parts industry, particularly for B2B buyers who prioritize corporate responsibility. The environmental impact of manufacturing processes, including waste generation and resource depletion, is under scrutiny. Buyers are encouraged to seek suppliers who adhere to sustainable practices and can provide documentation of their environmental impact.
One way to ensure sustainability is by choosing suppliers that offer ‘green’ certifications and materials. These certifications, such as ISO 14001 for environmental management or the Forest Stewardship Council (FSC) for materials, indicate a commitment to reducing environmental footprints. Moreover, ethical sourcing practices, including fair labor conditions and transparent supply chains, are essential for building long-term relationships with suppliers. Buyers should assess potential partners not only on price and quality but also on their sustainability credentials.
What Is the Historical Context of the Spare Parts Market in China?
The evolution of the spare parts market in China can be traced back to the late 20th century when the country embraced economic reforms and opened its markets to foreign investment. Initially focused on low-cost manufacturing, the sector has matured significantly, shifting towards high-quality production and innovation. Over the past two decades, China has established itself as a global manufacturing hub, leveraging its vast labor force and advanced technologies.
As a result, the landscape for international B2B buyers has transformed, with Chinese suppliers now offering a diverse range of products that meet global quality standards. This historical context highlights the importance of understanding not only the current trends but also the foundational changes that have shaped the spare parts sector, enabling buyers to make informed sourcing decisions that align with their business strategies.
Frequently Asked Questions (FAQs) for B2B Buyers of spare parts china
-
How do I evaluate suppliers when sourcing spare parts from China?
Evaluating suppliers in China requires a comprehensive approach. Start by checking their business licenses and certifications to ensure legitimacy. Request references from past clients to gauge reliability and quality. Utilize platforms like Alibaba and Global Sources to read reviews and ratings. Additionally, consider conducting an on-site audit or hiring a third-party inspection service to verify the manufacturing processes and facilities. This thorough vetting process minimizes the risk of fraud and ensures you partner with trustworthy suppliers. -
What are the typical minimum order quantities (MOQs) for spare parts in China?
Minimum order quantities (MOQs) for spare parts can vary significantly based on the supplier and type of part. Generally, MOQs can range from 50 to several thousand units. Custom parts often have higher MOQs due to setup costs. When negotiating, clarify MOQs upfront and explore flexibility based on your needs. Some suppliers may accommodate smaller orders for a premium, while others may offer discounts for larger quantities, so it’s essential to communicate your requirements clearly. -
What payment terms should I expect when sourcing spare parts from China?
Payment terms when sourcing spare parts from China typically include options like T/T (telegraphic transfer), PayPal, and L/C (letter of credit). Standard practices often require a deposit (usually 30%) upfront, with the balance paid before shipment. Ensure to discuss and negotiate terms that align with your cash flow and risk management strategies. Additionally, consider using escrow services for larger orders to safeguard your funds until the parts meet your quality expectations. -
How can I ensure quality assurance when purchasing spare parts from China?
Implementing a robust quality assurance (QA) process is crucial when sourcing from China. Start by specifying quality standards in your purchase agreement. Request samples before placing a large order to evaluate the parts firsthand. Consider third-party inspection services to conduct quality checks during production and prior to shipment. Establish clear communication channels with your supplier to address any quality issues promptly, ensuring that the final product meets your specifications. -
What logistics considerations should I keep in mind when importing spare parts from China?
Logistics play a vital role in the successful importation of spare parts. Understand the shipping options available, such as air freight for speed or sea freight for cost-effectiveness. Factor in lead times, customs clearance, and potential delays. Collaborate with freight forwarders who specialize in international shipping to navigate regulations and documentation requirements. Also, consider warehousing options in your target market to facilitate quicker distribution upon arrival. -
What are the common challenges faced by international buyers when sourcing spare parts from China?
International buyers often encounter challenges such as language barriers, cultural differences, and varying quality standards. Additionally, navigating regulatory compliance and customs procedures can be complex. To mitigate these issues, invest time in building relationships with suppliers, utilize professional translation services, and familiarize yourself with local regulations. Establishing clear contracts and expectations can also help prevent misunderstandings and ensure smoother transactions. -
How can I customize spare parts to meet my specific requirements from Chinese suppliers?
Customizing spare parts involves clear communication of your specifications to the supplier. Provide detailed drawings, material specifications, and performance criteria to avoid ambiguity. Discuss the design process and timelines, ensuring the supplier understands your needs. Be prepared for potential additional costs and longer lead times associated with custom orders. Engaging in regular updates and feedback during the development phase can help ensure the final product aligns with your expectations. -
What are the best practices for maintaining long-term relationships with Chinese suppliers?
Building long-term relationships with suppliers in China hinges on effective communication and mutual trust. Regularly engage with your suppliers through meetings and updates to foster transparency. Consider placing consistent orders to establish reliability and predictability. Address issues collaboratively and provide constructive feedback to enhance product quality and service. Additionally, recognizing and rewarding good performance can strengthen your partnership and encourage suppliers to prioritize your needs.
Important Disclaimer & Terms of Use
⚠️ Important Disclaimer
The information provided in this guide, including content regarding manufacturers, technical specifications, and market analysis, is for informational and educational purposes only. It does not constitute professional procurement advice, financial advice, or legal advice.
While we have made every effort to ensure the accuracy and timeliness of the information, we are not responsible for any errors, omissions, or outdated information. Market conditions, company details, and technical standards are subject to change.
B2B buyers must conduct their own independent and thorough due diligence before making any purchasing decisions. This includes contacting suppliers directly, verifying certifications, requesting samples, and seeking professional consultation. The risk of relying on any information in this guide is borne solely by the reader.
Strategic Sourcing Conclusion and Outlook for spare parts china
What Are the Key Takeaways for B2B Buyers in Spare Parts Sourcing?
In conclusion, strategic sourcing from China for spare parts presents a wealth of opportunities for international B2B buyers, particularly from Africa, South America, the Middle East, and Europe. The ability to access a wide range of high-quality components at competitive prices can significantly enhance operational efficiency and profitability. Buyers should prioritize establishing strong relationships with reliable suppliers, leveraging technology for supply chain transparency, and ensuring compliance with international standards to mitigate risks.
How Can International Buyers Prepare for Future Sourcing Trends?
Looking ahead, the landscape of global sourcing is rapidly evolving. Buyers must stay agile and informed about emerging trends, such as sustainability in manufacturing and advancements in logistics technology. Engaging in continuous market analysis and adapting sourcing strategies will be crucial to maintaining a competitive edge.
What Steps Should You Take Next?
International B2B buyers are encouraged to take proactive steps in their sourcing strategy by exploring partnerships with verified suppliers in China. By fostering collaboration and open communication, businesses can secure a reliable supply chain that not only meets current demands but also anticipates future challenges. The future of spare parts sourcing is bright, and with the right approach, your business can thrive in this dynamic market.