Discover Top Benefits of Choosing a Tape Measure Supplier (2025)
Introduction: Navigating the Global Market for tape measure supplier
In today’s competitive landscape, sourcing a reliable tape measure supplier can pose significant challenges for international B2B buyers, especially in diverse markets such as Africa, South America, the Middle East, and Europe. With various applications ranging from construction to manufacturing and DIY projects, the need for precision tools like tape measures is paramount. This guide aims to streamline your sourcing process by providing a comprehensive overview of the types of tape measures available, their specific applications, and critical factors to consider when vetting suppliers.
Navigating the global market for tape measure suppliers requires a strategic approach. In this guide, you will find actionable insights on supplier selection criteria, cost considerations, and the importance of quality assurance. Understanding these elements can empower businesses to make informed purchasing decisions that align with their operational needs and budget constraints.
For B2B buyers from regions like Vietnam or the UK, the nuances of international trade, cultural differences, and varying standards can complicate sourcing efforts. This guide addresses these complexities, offering valuable tips on negotiating with suppliers, understanding shipping logistics, and ensuring compliance with local regulations. By leveraging the insights provided, you can enhance your procurement strategy, minimize risks, and ultimately ensure that your projects are equipped with the right tools for success.
Understanding tape measure supplier Types and Variations
Type Name | Key Distinguishing Features | Primary B2B Applications | Brief Pros & Cons for Buyers |
---|---|---|---|
Mechanical Tape Measure | Rigid metal or plastic, manual retractable mechanism | Construction, woodworking, engineering | Pros: Durable, accurate. Cons: Limited flexibility. |
Electronic Tape Measure | Digital display, laser measuring capabilities | Surveying, interior design, construction | Pros: High precision, easy to read. Cons: Battery dependency. |
Folding Tape Measure | Compact, flexible, often made of cloth or plastic | Tailoring, crafts, general measurements | Pros: Portable, versatile. Cons: Less durable. |
Surveyor’s Tape Measure | Long, often fiberglass, designed for distance measurement | Land surveying, civil engineering | Pros: High length accuracy, robust. Cons: Bulky, requires more handling. |
Specialty Tape Measure | Customized features (e.g., magnetic tips, dual-sided) | Niche industries (e.g., HVAC, plumbing) | Pros: Tailored functionality. Cons: Higher cost, limited availability. |
What are the Key Characteristics of Mechanical Tape Measures?
Mechanical tape measures are among the most traditional types, featuring a rigid metal or plastic body with a manual retractable mechanism. They are commonly used in construction, woodworking, and engineering applications where durability and accuracy are paramount. When purchasing, B2B buyers should consider the tape’s length, width, and measurement units (imperial or metric). Mechanical tape measures are generally robust but may lack the flexibility that some projects require.
How Do Electronic Tape Measures Enhance Measurement Accuracy?
Electronic tape measures incorporate digital displays and often feature laser measuring capabilities. These tools are essential in fields such as surveying, interior design, and construction, where precision is critical. Buyers should evaluate battery life, measurement range, and additional features like memory functions or Bluetooth connectivity. While electronic tape measures offer high precision and ease of reading, they also come with the drawback of being dependent on battery power.
What Makes Folding Tape Measures Ideal for Portability?
Folding tape measures are characterized by their compact design, typically made from cloth or flexible plastic. They are widely used in tailoring, crafts, and general measurements due to their lightweight and portable nature. B2B buyers should look for features such as tape length and markings clarity. Although these measures are versatile and easy to carry, they may not be as durable as their rigid counterparts, making them less suitable for heavy-duty applications.
Why Are Surveyor’s Tape Measures Essential in Civil Engineering?
Surveyor’s tape measures are designed for long-distance measurements, often made from fiberglass to withstand outdoor conditions. They are crucial in land surveying and civil engineering, where accuracy over long distances is required. Buyers should consider the tape’s length, ease of handling, and durability when selecting a surveyor’s tape. While they provide high accuracy, these measures can be bulky and require more effort to handle, which may not be ideal for all users.
What Benefits Do Specialty Tape Measures Offer to Niche Industries?
Specialty tape measures come with customized features tailored to specific industries, such as magnetic tips for HVAC work or dual-sided measurements for plumbing. They serve niche markets where standard options may not suffice. When considering a purchase, B2B buyers should assess the unique features and their applicability to their specific needs. Although specialty tape measures can enhance functionality, they often come at a higher cost and may be less readily available than standard options.
Related Video: How to read a tape measure : Tips for reading a tape faster
Key Industrial Applications of tape measure supplier
Industry/Sector | Specific Application of tape measure supplier | Value/Benefit for the Business | Key Sourcing Considerations for this Application |
---|---|---|---|
Construction | Site Measurement for Project Planning | Ensures accurate material estimation and reduces waste | Durability, length options, and ease of use in various conditions |
Manufacturing | Quality Control Measurements | Maintains product standards and minimizes defects | Precision, calibration options, and compliance with industry standards |
Interior Design and Architecture | Space Planning and Layout Design | Enhances design accuracy and client satisfaction | Versatility, measurement range, and ergonomic design |
Landscaping and Agriculture | Plant and Feature Spacing | Optimizes land use and improves aesthetic appeal | Weather resistance, length, and visibility of markings |
Retail and Inventory Management | Stockroom and Display Setup | Improves efficiency in layout and inventory control | Compactness, ease of storage, and measurement precision |
How is Tape Measure Used in Construction for Project Planning?
In the construction industry, tape measures are essential for site measurement and project planning. They enable precise calculations for material estimation, ensuring that builders order the correct quantities, thereby minimizing waste and reducing costs. International buyers should consider sourcing heavy-duty tape measures that can withstand harsh conditions and have clear markings for easy readability. Additionally, tape measures that are longer than standard lengths are often beneficial for large construction sites.
What Role Does Tape Measure Play in Manufacturing for Quality Control?
In manufacturing, tape measures are critical for quality control measurements. They help ensure that products meet specified dimensions, which is vital for maintaining standards and minimizing defects. Buyers in this sector should prioritize tape measures with high precision and calibration options to guarantee accuracy. Compliance with industry standards is also crucial, making it important to source from suppliers that provide certification for their measuring tools.
How Do Interior Designers and Architects Utilize Tape Measures for Space Planning?
Interior designers and architects rely on tape measures for space planning and layout design. Accurate measurements are essential to create functional and aesthetically pleasing environments. For B2B buyers in this field, sourcing versatile tape measures that offer a range of lengths and ergonomic designs can enhance usability during projects. Additionally, tape measures with features like locking mechanisms can improve measurement accuracy, which is critical in design applications.
Why is Tape Measure Important in Landscaping and Agriculture for Plant Spacing?
In landscaping and agriculture, tape measures are used to determine the optimal spacing for plants and features. This practice maximizes land use and enhances visual appeal. Buyers in these sectors should look for tape measures that are weather-resistant and designed for outdoor use. Visibility of markings is also a key consideration, as clear readings can significantly improve the efficiency of planting layouts.
How Does Tape Measure Improve Efficiency in Retail and Inventory Management?
In retail and inventory management, tape measures assist in stockroom organization and display setup. They help ensure that products are arranged efficiently, which can enhance customer experience and streamline inventory control. For international B2B buyers, compact tape measures that are easy to store yet provide accurate measurements are essential. Additionally, sourcing options that include features for quick measurement retrieval can further improve operational efficiency.
Related Video: How to Use a Tape Measure
3 Common User Pain Points for ‘tape measure supplier’ & Their Solutions
Scenario 1: Inconsistent Measurement Accuracy Leads to Cost Overruns
The Problem: B2B buyers often face challenges with the accuracy of tape measures supplied by manufacturers. Inconsistent measurement can lead to errors in construction or manufacturing processes, causing significant cost overruns. For example, a contractor in South America may rely on a batch of tape measures that provide varying measurements, leading to materials being cut incorrectly. This not only wastes resources but also affects project timelines and profitability.
The Solution: To mitigate this issue, B2B buyers should prioritize sourcing tape measures from suppliers who provide quality assurance certifications and conduct regular calibration checks. When evaluating potential suppliers, ask for documentation that verifies their products meet industry standards, such as ISO 9001. Additionally, consider suppliers who offer a return policy or warranty on their products, ensuring you can replace any defective items. Investing in digital tape measures that provide electronic readouts can also enhance accuracy, reducing human error in measurement. Finally, establish a routine for quality checks on incoming supplies to catch any discrepancies early in the project lifecycle.
Scenario 2: Limited Availability of Custom Tape Measures
The Problem: Many businesses require custom tape measures to suit specific applications, such as those used in industrial environments or specialized construction projects. However, B2B buyers from regions like Africa and the Middle East often find that suppliers have limited options for customization. This lack of availability can hinder operational efficiency and lead to reliance on generic solutions that may not meet specific needs.
The Solution: To address this challenge, B2B buyers should proactively seek suppliers who specialize in custom solutions. During the supplier selection process, inquire about their ability to accommodate bespoke requirements, such as length, markings, and material specifications. Engaging with manufacturers directly can facilitate customization options. Establishing a long-term partnership with a supplier who understands your business needs can also lead to better options and pricing. Additionally, consider leveraging online platforms that connect buyers with manufacturers specializing in custom tape measures, ensuring you find the right fit for your operational requirements.
Scenario 3: Poor Durability and Reliability of Tape Measures
The Problem: Durability is a critical concern for B2B buyers, especially in demanding environments where tape measures are exposed to harsh conditions. For instance, a construction firm in Europe may experience frequent tape measure failures due to wear and tear, leading to operational delays and increased replacement costs. This problem is exacerbated when suppliers do not disclose the materials used or the expected lifespan of their products.
The Solution: To ensure you are sourcing durable tape measures, conduct thorough research on suppliers’ materials and manufacturing processes. Look for tape measures made from high-quality materials like stainless steel or reinforced plastics that can withstand tough conditions. When evaluating potential suppliers, request samples to test the durability of their products in real-world scenarios before committing to a large order. Additionally, consider investing in tape measures with features such as weather resistance or shock absorption to extend their lifespan. Engaging with suppliers who provide detailed product specifications and user reviews can help you make informed purchasing decisions that minimize the risk of product failure.
Strategic Material Selection Guide for tape measure supplier
When selecting materials for tape measures, understanding the properties, advantages, and limitations of each option is crucial for international B2B buyers. This guide analyzes common materials used in tape measure manufacturing, offering insights tailored to buyers from Africa, South America, the Middle East, and Europe.
What Are the Key Properties of Steel in Tape Measures?
Steel is one of the most commonly used materials for tape measures, particularly for those requiring durability and precision. Its high tensile strength allows it to withstand considerable stress without deformation. Steel tape measures can typically handle a temperature range of -40°C to 85°C, making them suitable for various environments. Additionally, they exhibit good corrosion resistance, especially when coated.
Pros & Cons: The primary advantage of steel is its durability, which ensures a long lifespan even under heavy use. However, steel tape measures can be heavier than alternatives, which may not be ideal for all applications. The manufacturing complexity can also increase costs, particularly if specialized coatings are required.
Impact on Application: Steel tape measures are particularly compatible with construction and engineering applications, where precision and durability are paramount. Buyers should ensure compliance with international standards such as ASTM and DIN, which govern the quality and safety of steel products.
How Does Fiberglass Compare for Tape Measure Applications?
Fiberglass is another popular material for tape measures, especially in applications requiring flexibility and resistance to environmental factors. Fiberglass tape measures can withstand a temperature range of -20°C to 60°C and are resistant to moisture and chemicals, making them ideal for outdoor and industrial use.
Pros & Cons: The flexibility of fiberglass allows for easier handling and storage, and it is generally lighter than steel. However, fiberglass is less durable than steel and can be prone to wear and tear over time. The manufacturing process for fiberglass can also be more complex, potentially leading to higher costs.
Impact on Application: Fiberglass tape measures are suitable for landscaping, plumbing, and electrical applications where flexibility is advantageous. International buyers should be aware of the specific standards applicable to fiberglass products in their regions, such as JIS in Japan or EN standards in Europe.
What Advantages Does Plastic Offer for Tape Measures?
Plastic is often used for tape measures designed for light-duty applications. It is lightweight and can be manufactured in various colors and designs. Plastic tape measures typically have a temperature rating of -10°C to 50°C and are resistant to moisture.
Pros & Cons: The primary advantage of plastic is its low cost, making it an attractive option for budget-conscious buyers. However, plastic tape measures are not as durable as steel or fiberglass and may not perform well under heavy stress or extreme conditions.
Impact on Application: Plastic tape measures are best suited for home use, DIY projects, or light construction tasks. Buyers should consider the implications of using plastic in environments where durability is critical and ensure compliance with relevant safety standards.
How Do Composite Materials Enhance Tape Measure Performance?
Composite materials, which combine various elements like fiberglass and plastic, offer a balance of strength, flexibility, and lightweight properties. They can typically handle temperatures ranging from -30°C to 70°C and provide excellent resistance to environmental factors.
Pros & Cons: The key advantage of composite materials is their versatility, making them suitable for a wide range of applications. However, they can be more expensive than standard materials like plastic and may require more complex manufacturing processes.
Impact on Application: Composite tape measures are ideal for specialized industries such as aerospace and automotive, where precision and performance are crucial. International buyers should verify compliance with industry-specific standards to ensure product reliability.
Summary Table of Material Selection for Tape Measure Suppliers
Material | Typical Use Case for tape measure supplier | Key Advantage | Key Disadvantage/Limitation | Relative Cost (Low/Med/High) |
---|---|---|---|---|
Steel | Construction, engineering | High durability and precision | Heavier, higher manufacturing costs | Medium |
Fiberglass | Landscaping, plumbing, electrical | Lightweight and flexible | Less durable, prone to wear | Medium |
Plastic | Home use, DIY projects | Low cost and easy to handle | Not durable under stress | Low |
Composite | Aerospace, automotive | Versatile with balanced properties | Higher cost, complex manufacturing | High |
This comprehensive overview equips B2B buyers with the necessary insights to make informed decisions regarding material selection for tape measures, ensuring compatibility with their specific applications and compliance with regional standards.
In-depth Look: Manufacturing Processes and Quality Assurance for tape measure supplier
What Are the Key Manufacturing Stages for Tape Measure Suppliers?
The manufacturing process for tape measures involves several critical stages that ensure both functionality and durability. Understanding these stages can empower B2B buyers to make informed decisions when selecting suppliers.
1. Material Preparation: What Materials Are Used in Tape Measure Production?
The first step in manufacturing tape measures is the selection and preparation of materials. Common materials include:
- Base Material: Typically, tape measures are made from high-grade steel or fiberglass for flexibility and durability. Steel provides strength, while fiberglass is lightweight and resistant to stretching.
- Case Materials: The outer casing is often constructed from durable plastic or metal, providing protection and enhancing grip.
- Printing Inks: High-quality inks that resist fading are used for the measurement markings to ensure clarity over time.
Buyers should inquire about the source and quality of these materials, as they significantly affect the tape measure’s lifespan and accuracy.
2. How Are Tape Measures Formed and Assembled?
After material preparation, the next stage is forming the tape and assembling the components. This process includes:
- Metal Strip Formation: For steel tape measures, a metal strip is cut to the desired length, then coated to prevent rust. Fiberglass tapes are extruded into flat forms.
- Marking and Calibration: Measurement markings are printed on the tape using methods like screen printing or laser etching, ensuring precision.
- Casing Assembly: The formed tape is then coiled and placed into its casing. The casing is designed to allow easy retraction and locking of the tape.
Understanding the manufacturing techniques used, such as whether they employ automated machinery or manual labor, can provide insights into the supplier’s capability and consistency.
3. What Finishing Processes Are Essential for Quality?
Finishing processes enhance the durability and aesthetic appeal of tape measures. Key techniques include:
- Coating: A protective coating may be applied to steel tapes to prevent corrosion and enhance durability.
- Quality Control Inspection: Final inspection is crucial to ensure that every tape measure meets quality standards before packaging.
B2B buyers should look for suppliers that emphasize these finishing processes, as they directly impact the performance and longevity of the product.
How is Quality Assurance Implemented in Tape Measure Manufacturing?
Quality assurance (QA) is a critical component in the manufacturing process. It ensures that the final product meets international standards and customer expectations.
1. What International Standards Should Buyers Be Aware Of?
Tape measure suppliers often adhere to various international standards to ensure quality. Some key standards include:
- ISO 9001: This standard focuses on quality management systems, ensuring that suppliers maintain consistent quality in their processes.
- CE Marking: In Europe, CE marking indicates that the product meets safety and environmental protection standards.
- API Standards: For specific industrial applications, adherence to API standards may be relevant.
B2B buyers should request documentation of these certifications to validate the supplier’s compliance.
2. What Are the QC Checkpoints in Tape Measure Manufacturing?
Quality control is implemented at various checkpoints throughout the manufacturing process. These typically include:
- Incoming Quality Control (IQC): This involves inspecting raw materials upon arrival to ensure they meet specifications before production begins.
- In-Process Quality Control (IPQC): During manufacturing, periodic checks are performed to monitor processes and detect any deviations.
- Final Quality Control (FQC): This final inspection assesses the finished products for accuracy, durability, and overall quality before shipping.
Understanding these checkpoints allows buyers to gauge the thoroughness of a supplier’s QA process.
3. What Common Testing Methods Are Used for Tape Measures?
To ensure accuracy and reliability, various testing methods are employed, including:
- Length Measurement Tests: These tests verify that the tape measures are accurate to their stated lengths.
- Durability Tests: Tape measures undergo stress tests to evaluate their resistance to wear and tear.
- Environmental Tests: Assessments may be conducted to see how tape measures withstand different environmental conditions, such as humidity and temperature changes.
Buyers should inquire about the specific tests conducted and their results to ensure product reliability.
How Can B2B Buyers Verify Supplier Quality Control?
Verifying a supplier’s quality control processes is essential for B2B buyers, especially when sourcing internationally. Here are actionable steps:
1. What Should Buyers Look for in Supplier Audits and Reports?
Requesting audits and quality reports can provide insights into a supplier’s quality management practices. Look for:
- Regular Audits: Suppliers should undergo regular internal and external audits to ensure compliance with international standards.
- Corrective Action Reports: These documents outline how suppliers address any quality issues, showcasing their commitment to continuous improvement.
2. How Can Third-Party Inspections Enhance Buyer Confidence?
Engaging third-party inspection services can provide an unbiased assessment of the supplier’s quality control processes. These inspections can include:
- Pre-shipment Inspections: Before products are shipped, third-party inspectors can verify that they meet quality standards.
- Random Sampling: Inspectors can randomly select products from batches to ensure consistent quality across shipments.
Third-party verification helps build trust and mitigates risks associated with international procurement.
What Quality Control Nuances Should International Buyers Consider?
When sourcing tape measures from suppliers in Africa, South America, the Middle East, and Europe, several nuances come into play:
- Cultural Differences: Understanding the cultural context of suppliers can impact negotiations and expectations around quality.
- Regulatory Compliance: Different regions may have specific regulations regarding product safety and quality. Buyers should familiarize themselves with these regulations to ensure compliance.
- Communication Barriers: Language differences can lead to misunderstandings regarding quality expectations. Clear, concise communication is essential.
By considering these factors, international buyers can navigate the complexities of sourcing tape measures effectively and ensure they receive high-quality products that meet their needs.
Practical Sourcing Guide: A Step-by-Step Checklist for ‘tape measure supplier’
The purpose of this guide is to provide international B2B buyers with a comprehensive checklist for sourcing tape measure suppliers. By following these steps, buyers can ensure that they choose reliable, high-quality suppliers that meet their specific needs, particularly in diverse markets such as Africa, South America, the Middle East, and Europe.
Step 1: Define Your Technical Specifications
Before starting your search, clearly outline the technical specifications for the tape measures you require. This includes the length, units of measurement (metric vs. imperial), material (plastic, steel, etc.), and any special features such as magnetic ends or shock resistance. Having detailed specifications helps you communicate effectively with potential suppliers and ensures you receive products that meet your exact needs.
Step 2: Research Potential Suppliers
Conduct thorough research to identify potential suppliers. Utilize online platforms such as Alibaba, Global Sources, or trade directories specific to your region. Pay attention to suppliers’ profiles, product offerings, and customer reviews. This initial research phase is critical to building a shortlist of credible suppliers.
Step 3: Verify Supplier Certifications
Ensure that the suppliers you are considering have the necessary certifications and compliance with international standards. Look for ISO certifications, CE markings, or specific industry-related certifications. These credentials not only indicate quality assurance but also demonstrate the supplier’s commitment to meeting regulatory requirements in your target market.
Step 4: Request Samples for Evaluation
Before making a bulk purchase, request samples of the tape measures from your shortlisted suppliers. Testing the samples allows you to evaluate the quality, durability, and functionality firsthand. This step is essential to ensure that the products meet your standards and that the supplier can deliver what they promise.
Step 5: Assess Supplier Production Capabilities
Investigate the production capabilities of your potential suppliers. Consider factors such as their manufacturing processes, capacity to handle large orders, and lead times. This assessment is vital to ensure that the supplier can meet your demand, especially if you have specific deadlines for project completion.
Step 6: Negotiate Terms and Pricing
Once you have narrowed down your options, initiate negotiations regarding pricing, payment terms, and delivery schedules. Be clear about your budget and requirements, and don’t hesitate to negotiate for better terms. Good negotiation can lead to cost savings and a stronger supplier relationship.
Step 7: Establish Clear Communication Channels
Effective communication is key to a successful supplier relationship. Establish clear channels of communication and define points of contact on both sides. This clarity can help prevent misunderstandings and ensure that any issues are resolved promptly, enhancing collaboration throughout the sourcing process.
By following this practical sourcing checklist, B2B buyers can make informed decisions when selecting tape measure suppliers, ultimately leading to successful partnerships and high-quality products.
Comprehensive Cost and Pricing Analysis for tape measure supplier Sourcing
What Are the Key Cost Components in Sourcing Tape Measures?
When sourcing tape measures, understanding the cost structure is essential for international B2B buyers. The primary cost components include materials, labor, manufacturing overhead, tooling, quality control (QC), logistics, and profit margins.
-
Materials: The choice of materials significantly impacts the overall cost. High-quality steel or fiberglass, which are commonly used in tape measures, can be more expensive but offer better durability and precision. Buyers should evaluate the material specifications to balance quality and cost.
-
Labor: Labor costs vary significantly by region. For example, sourcing from countries with lower labor costs may initially seem appealing; however, this could compromise quality. Understanding the labor market in the supplier’s location is crucial for making informed decisions.
-
Manufacturing Overhead: This includes expenses related to utilities, rent, and equipment maintenance. A supplier’s overhead can vary based on their operational efficiency and location, influencing the final price of the tape measures.
-
Tooling: Custom tooling for specific tape measures can incur substantial upfront costs. Buyers should consider whether the investment in custom tooling is justified by the expected volume and pricing structure.
-
Quality Control (QC): Effective QC processes ensure that products meet required specifications, which may add to the cost but are vital for maintaining product integrity. Buyers should inquire about the QC measures implemented by suppliers.
-
Logistics: Transportation costs can fluctuate based on shipping methods and distances. International buyers must factor in these logistics costs, including customs duties and taxes, to understand the total expenditure.
-
Margin: Suppliers typically build a profit margin into their pricing. Understanding the industry standards for margins can help buyers negotiate better deals.
How Do Price Influencers Affect Tape Measure Costs?
Several factors influence the pricing of tape measures, which buyers need to consider for effective sourcing.
-
Volume and Minimum Order Quantity (MOQ): Purchasing in bulk often leads to discounted rates. Buyers should negotiate MOQs with suppliers to secure the best price while ensuring they can manage inventory effectively.
-
Specifications and Customization: Custom features, such as branding or unique measurement increments, can increase costs. Buyers should assess whether these customizations are necessary or if standard options suffice.
-
Material Quality and Certifications: Higher quality materials and necessary certifications (e.g., ISO standards) can raise costs but are essential for certain industries. Buyers should weigh the importance of these factors against their budget constraints.
-
Supplier Factors: The supplier’s reputation, reliability, and location can significantly affect pricing. Established suppliers may charge more due to their proven track record, while newer suppliers might offer lower prices to attract business.
-
Incoterms: Understanding Incoterms is crucial for clarifying shipping responsibilities and costs. Buyers should negotiate terms that minimize their total cost while ensuring timely delivery.
What Are Effective Buyer Tips for Cost-Efficiency?
To maximize cost-efficiency when sourcing tape measures, international buyers can adopt several strategies:
-
Negotiate: Always negotiate prices and terms. Suppliers often have flexibility, especially for larger orders. Establishing a long-term relationship can also lead to better terms over time.
-
Evaluate Total Cost of Ownership (TCO): Instead of focusing solely on the purchase price, consider the TCO, which includes shipping, handling, and potential warranty costs. This holistic view helps in making more informed sourcing decisions.
-
Understand Pricing Nuances for International Markets: Different regions have varying expectations regarding pricing and quality. Buyers from Africa, South America, the Middle East, and Europe should research local market dynamics and cultural nuances that may affect negotiations.
-
Request Samples: Before committing to a large order, request samples to evaluate quality and functionality. This step can help avoid costly mistakes and ensure satisfaction with the final product.
Disclaimer on Indicative Prices
Prices for tape measures can fluctuate based on market conditions, material availability, and supplier pricing strategies. It is advisable for buyers to conduct thorough market research and obtain multiple quotes to ensure they secure the best possible deal.
Alternatives Analysis: Comparing tape measure supplier With Other Solutions
Understanding the Need for Alternative Solutions in Measuring Tools
When sourcing measuring tools for construction, manufacturing, or design, international B2B buyers often face the dilemma of choosing between traditional options like tape measures and emerging alternatives. Understanding the strengths and weaknesses of different solutions is crucial for making informed purchasing decisions that align with operational needs and budget constraints. This section compares tape measure suppliers with two viable alternatives: digital measuring tools and laser distance measurers.
Comparison Table of Tape Measure Supplier and Alternatives
Comparison Aspect | Tape Measure Supplier | Digital Measuring Tools | Laser Distance Measurers |
---|---|---|---|
Performance | Reliable for basic measurements; manual accuracy required | Offers real-time data; may require calibration | High precision; can measure long distances quickly |
Cost | Generally low-cost and widely available | Moderate cost; varies by features | Higher initial investment, but may save time |
Ease of Implementation | Simple to use; no setup required | Requires understanding of digital interfaces | Can be intuitive but may need training for optimal use |
Maintenance | Minimal maintenance needed | Requires software updates | Regular calibration needed for accuracy |
Best Use Case | Ideal for small-scale projects or manual tasks | Best for projects needing speed and accuracy | Suitable for large-scale projects with complex measurements |
What Are the Pros and Cons of Digital Measuring Tools?
Digital measuring tools leverage technology to provide quick and accurate measurements. They often come equipped with features like memory storage, data transfer capabilities, and user-friendly interfaces. The primary advantage is their ability to minimize human error and offer precise readings, making them ideal for projects that require high accuracy. However, they may require a learning curve for those unfamiliar with digital technology and could be more expensive than traditional tape measures.
How Do Laser Distance Measurers Compare to Tape Measures?
Laser distance measurers are designed for speed and precision, particularly in larger spaces where traditional tape measures may fall short. They can provide measurements over long distances and often include features such as area and volume calculations. The main advantage is their ability to deliver accurate results quickly, which can significantly enhance productivity on job sites. On the downside, they typically come with a higher price tag and require regular calibration to maintain accuracy.
How Should B2B Buyers Decide Between These Measuring Solutions?
Selecting the right measuring tool depends on several factors, including the specific requirements of your projects, budget constraints, and the level of accuracy needed. For smaller tasks or straightforward measurements, a tape measure supplier may suffice due to its low cost and ease of use. Conversely, for larger projects that demand rapid and accurate measurements, investing in digital measuring tools or laser distance measurers could lead to better efficiency and reduced labor costs in the long run. Ultimately, understanding the unique advantages and limitations of each solution will empower B2B buyers to make choices that enhance operational performance while aligning with financial goals.
Essential Technical Properties and Trade Terminology for tape measure supplier
What Are the Key Technical Properties of Tape Measures That B2B Buyers Should Consider?
When sourcing tape measures, understanding the technical properties is crucial for making informed purchasing decisions. Here are some essential specifications to consider:
1. Material Grade
Tape measures are typically constructed from a variety of materials, including steel, fiberglass, and plastic. Steel tape measures are known for their durability and resistance to wear, making them suitable for heavy-duty applications. Fiberglass options are often more flexible and resistant to environmental conditions, such as moisture and temperature fluctuations. Understanding the material grade helps buyers select a tape measure that meets their specific industry requirements.
2. Length and Width Specifications
Tape measures come in various lengths, commonly ranging from 3 to 100 meters, and widths that affect their usability and accuracy. Longer tape measures are ideal for large-scale projects, while shorter ones are more portable. The width of the tape can influence its rigidity and ease of use, particularly in construction settings. B2B buyers should evaluate the intended application to select the appropriate length and width.
3. Tolerance and Accuracy Levels
Tolerance refers to the permissible limits of variation in a measurement. High-quality tape measures typically offer a tolerance of ±1 mm or better. This accuracy is vital in precision-dependent industries like construction and manufacturing. Buyers should prioritize tape measures that meet their accuracy standards to ensure the reliability of their measurements.
4. Locking Mechanism
A reliable locking mechanism is essential for maintaining measurement accuracy while in use. Common types include thumb locks and auto-lock systems. A robust locking mechanism enhances usability, especially in dynamic environments where measurements need to be held in place temporarily. Buyers should assess the effectiveness of the locking system to avoid potential measurement errors.
5. Blade Coating
The blade coating can significantly affect the durability and visibility of the tape measure. Common coatings include nylon, which provides resistance to wear and tear, and a bright color finish for improved visibility in low-light conditions. Selecting a tape measure with the right blade coating can enhance its lifespan and functionality in various working conditions.
What Common Trade Terms Should International B2B Buyers of Tape Measures Know?
Familiarity with industry terminology can streamline the purchasing process and facilitate smoother transactions. Here are some key trade terms:
1. OEM (Original Equipment Manufacturer)
OEM refers to companies that produce products for other brands to sell under their name. For B2B buyers, partnering with OEMs can provide access to high-quality tape measures tailored to specific requirements, often at a lower cost than purchasing branded items.
2. MOQ (Minimum Order Quantity)
MOQ indicates the smallest number of units a supplier is willing to sell. Understanding the MOQ is crucial for buyers to manage inventory and budget effectively. Negotiating MOQs can also lead to more favorable pricing structures for larger orders.
3. RFQ (Request for Quotation)
An RFQ is a formal request sent to suppliers to obtain pricing and terms for specific products. B2B buyers should prepare detailed RFQs to ensure they receive accurate and comparable quotations, which can aid in decision-making and negotiation processes.
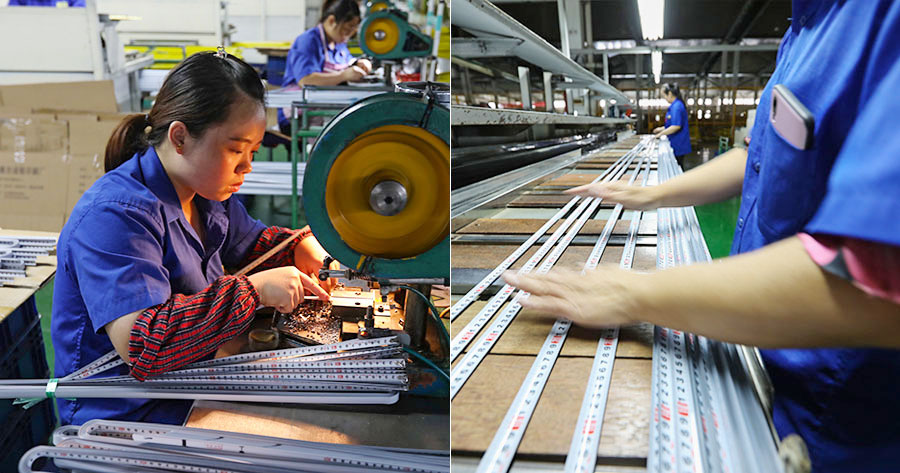
A stock image related to tape measure supplier.
4. Incoterms (International Commercial Terms)
Incoterms are standardized trade terms that define the responsibilities of buyers and sellers in international transactions. Familiarity with these terms, such as FOB (Free On Board) and CIF (Cost, Insurance, and Freight), helps buyers understand shipping costs, risks, and delivery responsibilities.
5. Lead Time
Lead time refers to the time taken from placing an order to receiving the product. Understanding lead times is essential for B2B buyers to plan their projects and inventory levels effectively. Suppliers who can provide shorter lead times may offer a competitive advantage.
6. Warranty and Service Terms
Warranty terms outline the conditions under which a product can be repaired or replaced. Knowing the warranty details helps buyers assess the long-term value of their purchase and the level of support they can expect from the supplier.
By grasping these technical properties and trade terms, international B2B buyers can make more informed decisions when sourcing tape measures, ultimately enhancing their operational efficiency and project outcomes.
Navigating Market Dynamics and Sourcing Trends in the tape measure supplier Sector
What Are the Key Market Dynamics and Sourcing Trends in the Tape Measure Supplier Sector?
The global tape measure supplier market is influenced by several key drivers, including technological advancements, increasing demand for precision tools, and the rise of e-commerce platforms. In recent years, the integration of digital technologies such as laser measuring tools and smart tape measures has gained traction, appealing particularly to tech-savvy consumers and professionals in construction and engineering sectors. This trend is mirrored in international markets, including Africa, South America, the Middle East, and Europe, where buyers are increasingly seeking innovative measuring solutions that enhance accuracy and efficiency.
Emerging sourcing trends also highlight the shift towards direct procurement through online platforms. B2B buyers are leveraging digital marketplaces to streamline their sourcing processes, comparing suppliers and products in real-time. This evolution is particularly significant for international buyers from regions like Africa and South America, where traditional supply chains may have limitations. Additionally, the growing importance of local suppliers in Europe and the Middle East emphasizes the need for B2B buyers to evaluate not only product quality but also lead times and shipping costs associated with international sourcing.
Furthermore, the market is witnessing a push towards customization and personalization in product offerings. Suppliers are responding to this demand by providing tailored solutions that cater to specific industry requirements, whether in construction, woodworking, or DIY projects. This trend allows B2B buyers to differentiate themselves in their respective markets, ensuring they have the right tools for their unique applications.
How Is Sustainability Influencing Sourcing Decisions in the Tape Measure Supplier Sector?
Sustainability is becoming a cornerstone of sourcing strategies for B2B buyers in the tape measure sector. With heightened awareness of environmental impact, buyers are increasingly prioritizing suppliers that adopt sustainable practices. This includes the use of recyclable materials in tape measure production, which can significantly reduce waste and carbon footprints. For international buyers, especially those in Europe and the Middle East, compliance with stringent environmental regulations is crucial and can affect supplier selection.
Ethical sourcing also plays a vital role in decision-making. Buyers are more inclined to partner with suppliers who demonstrate transparency in their supply chains and adhere to fair labor practices. Certifications such as ISO 14001 for environmental management and Fair Trade can serve as indicators of a supplier’s commitment to sustainability and ethical standards. By choosing suppliers with these credentials, B2B buyers not only enhance their brand reputation but also align with the growing consumer demand for responsible products.
Moreover, the shift towards eco-friendly materials, such as bioplastics and sustainably sourced wood for tape measure cases, is gaining momentum. B2B buyers should actively seek suppliers that invest in green technologies and materials, ensuring their products meet both performance and environmental standards.
How Has the Tape Measure Supplier Sector Evolved Over Time?
The evolution of the tape measure supplier sector reflects broader technological advancements and shifts in consumer preferences. Originally, tape measures were simple mechanical devices, often made from metal or fabric. However, as industries evolved, so did the need for more precise and durable measuring tools. The introduction of fiberglass and plastic tape measures in the mid-20th century marked a significant turning point, offering enhanced flexibility and durability.
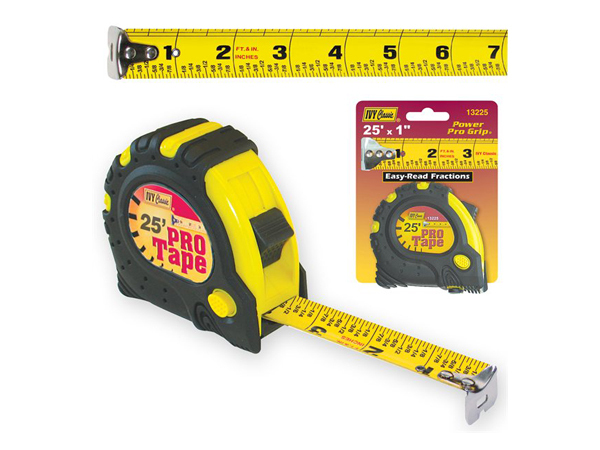
A stock image related to tape measure supplier.
In recent decades, the integration of digital technology has transformed the market further. Smart tape measures equipped with Bluetooth connectivity and mobile app integrations now allow users to store measurements digitally, share data instantly, and even calculate areas and volumes. This evolution signifies a transition towards multifunctional tools that cater to the needs of modern professionals across various sectors.
As the sector continues to innovate, B2B buyers must remain vigilant in monitoring these changes, ensuring they are equipped with the latest tools that offer both reliability and advanced features for their specific needs.
Frequently Asked Questions (FAQs) for B2B Buyers of tape measure supplier
-
How do I choose the right tape measure supplier for my business needs?
Choosing the right tape measure supplier involves assessing several critical factors. First, identify your specific requirements, such as measurement range, precision, and durability. Research potential suppliers by checking their reputation, customer reviews, and industry experience. Additionally, request samples to evaluate the quality of their products. Consider suppliers who offer customization options to meet your unique specifications. Lastly, ensure they have reliable logistics capabilities to facilitate timely delivery to your location in Africa, South America, the Middle East, or Europe. -
What are the typical minimum order quantities (MOQ) for tape measures?
Minimum order quantities (MOQ) for tape measures can vary widely depending on the supplier and product specifications. Generally, MOQs can range from 100 to 1,000 units for standard models. However, some suppliers may offer lower MOQs for specific products or customization requests. It is advisable to communicate directly with potential suppliers to understand their MOQ policies and negotiate terms that align with your business volume and budget constraints. -
What payment terms should I expect when sourcing tape measures internationally?
Payment terms for international sourcing can vary significantly based on the supplier’s policies and your negotiation. Common terms include upfront payments (30-50%), letters of credit, or payment upon delivery. Some suppliers may offer net terms (e.g., 30 or 60 days) for established relationships. Always clarify payment methods accepted (e.g., bank transfer, PayPal) and ensure that the terms are documented in your contract to avoid misunderstandings and protect your investment. -
How can I verify the quality assurance processes of a tape measure supplier?
To verify a supplier’s quality assurance processes, request their quality control certifications, such as ISO 9001. Inquire about their manufacturing processes and standards, including how they conduct product testing for accuracy and durability. Additionally, consider visiting their facilities if feasible or ask for third-party inspection reports. Establishing clear communication about quality expectations upfront can help ensure that you receive products that meet your standards. -
What customization options are available when ordering tape measures?
Many suppliers offer customization options for tape measures, which can include branding (logo printing), color variations, length specifications, and additional features such as magnetic tips or ergonomic designs. When discussing customization, clearly outline your needs and verify any additional costs or changes to lead times. Customization can significantly enhance your product’s appeal in the market, making it essential to choose a supplier who can accommodate your specific requirements. -
What logistics considerations should I keep in mind when sourcing tape measures?
Logistics play a crucial role in international sourcing. Assess the supplier’s shipping options, including freight methods (air, sea, or land) and estimated delivery times. It is essential to understand the costs associated with shipping, customs duties, and import regulations specific to your country. Partnering with a supplier experienced in international shipping can streamline the process and minimize delays. Additionally, consider working with a freight forwarder to manage logistics efficiently. -
How do I handle disputes with a tape measure supplier?
Dispute resolution should be addressed in your contract with the supplier. Establish clear communication channels and maintain records of all interactions. In the event of a dispute, attempt to resolve it amicably through negotiation first. If unresolved, consider mediation or arbitration as stipulated in your agreement. Always ensure that your contract includes a clause outlining the governing law and jurisdiction to facilitate legal proceedings if necessary. -
What are the key factors to consider for sustainable sourcing of tape measures?
When focusing on sustainable sourcing, evaluate suppliers based on their environmental policies, material sourcing, and manufacturing processes. Look for certifications such as FSC (Forest Stewardship Council) for wood-based products or compliance with REACH regulations for chemical safety. Engage suppliers who prioritize eco-friendly materials and practices, as this not only supports corporate social responsibility but can also enhance your brand image in increasingly environmentally-conscious markets.
Important Disclaimer & Terms of Use
⚠️ Important Disclaimer
The information provided in this guide, including content regarding manufacturers, technical specifications, and market analysis, is for informational and educational purposes only. It does not constitute professional procurement advice, financial advice, or legal advice.
While we have made every effort to ensure the accuracy and timeliness of the information, we are not responsible for any errors, omissions, or outdated information. Market conditions, company details, and technical standards are subject to change.
B2B buyers must conduct their own independent and thorough due diligence before making any purchasing decisions. This includes contacting suppliers directly, verifying certifications, requesting samples, and seeking professional consultation. The risk of relying on any information in this guide is borne solely by the reader.
Strategic Sourcing Conclusion and Outlook for tape measure supplier
In today’s competitive landscape, strategic sourcing is essential for B2B buyers seeking reliable tape measure suppliers. By prioritizing quality, cost-effectiveness, and supplier reliability, businesses can enhance operational efficiency and improve project outcomes. It is crucial to conduct thorough research and leverage supplier partnerships that align with your specific requirements, especially for international buyers from regions like Africa, South America, the Middle East, and Europe.
What should B2B buyers prioritize when sourcing tape measures? Focus on suppliers who demonstrate a commitment to innovation and sustainability. This not only helps in meeting current demands but also positions your business favorably for future growth. Additionally, understanding local regulations and market dynamics can provide a competitive edge.
Looking ahead, the demand for high-quality tape measures is expected to grow, driven by advancements in construction, manufacturing, and DIY sectors. B2B buyers are encouraged to embrace a proactive sourcing strategy that includes regular assessments of supplier performance and market trends. By doing so, you will not only secure the best products but also build long-lasting partnerships that contribute to your organization’s success. Engage with suppliers today to position your business for a prosperous tomorrow.