The Ultimate Guide to Brake Caliper Manufacturer (2025)
Introduction: Navigating the Global Market for brake caliper manufacturer
Navigating the complex landscape of sourcing brake calipers can be a daunting challenge for international B2B buyers, particularly those operating in diverse regions like Africa, South America, the Middle East, and Europe. With the growing demand for high-quality automotive components, understanding the nuances of the brake caliper manufacturing market is essential. This guide aims to equip you with the necessary insights to make informed purchasing decisions, ensuring that you not only find reliable suppliers but also secure the best value for your investment.
In this comprehensive resource, we will explore various types of brake calipers, their applications across different automotive sectors, and the critical factors to consider when vetting suppliers. Additionally, we will delve into pricing structures and the implications of cost on your overall procurement strategy. By understanding these elements, you will be better positioned to navigate the global market effectively.
Whether you’re a procurement manager in Turkey seeking to enhance your supply chain or a business owner in Vietnam looking to expand your product offerings, this guide serves as a valuable tool. It empowers you to identify quality manufacturers, assess market trends, and establish long-term partnerships that can elevate your business. Prepare to unlock the potential of the brake caliper market and drive your operations toward success.
Understanding brake caliper manufacturer Types and Variations
Type Name | Key Distinguishing Features | Primary B2B Applications | Brief Pros & Cons for Buyers |
---|---|---|---|
Floating Calipers | Single or dual pistons, moves with rotor | Passenger vehicles, light trucks | Pros: Cost-effective, lightweight. Cons: Less braking force compared to fixed calipers. |
Fixed Calipers | Multiple pistons, stationary design | High-performance vehicles, racing | Pros: Superior braking performance, even pressure distribution. Cons: Typically more expensive. |
Piston Calipers | Features one or more pistons for hydraulic action | Commercial vehicles, heavy machinery | Pros: High durability, reliable under heavy loads. Cons: Bulkier, can be more complex to install. |
Electromechanical Calipers | Integrates electronic control systems | Electric vehicles, advanced braking systems | Pros: Enhanced precision, adaptability. Cons: Higher maintenance, requires specialized knowledge. |
Brembo Calipers | High-performance brand, renowned for quality | Motorsports, luxury vehicles | Pros: Exceptional performance, brand reputation. Cons: Premium pricing, may not be necessary for all applications. |
What are Floating Calipers and Their B2B Relevance?
Floating calipers are designed with a single or dual piston that moves with the brake rotor. They are commonly found in passenger vehicles and light trucks, making them a popular choice for fleet managers and automotive suppliers. When considering floating calipers, B2B buyers should evaluate their cost-effectiveness and lightweight design, which can lower overall vehicle weight and improve fuel efficiency. However, it’s essential to note that while they are economical, they may not provide the same braking force as fixed calipers, which could be a consideration for performance-oriented applications.
How Do Fixed Calipers Differ from Other Types?
Fixed calipers are characterized by their stationary design, housing multiple pistons that apply even pressure to the brake pads. They are often used in high-performance vehicles and racing applications, making them ideal for B2B buyers in the automotive performance sector. The primary advantage of fixed calipers is their superior braking performance and consistent pressure distribution, which enhances stopping power. However, they typically come at a higher price point, so buyers should assess whether the investment aligns with their performance needs.
What Are Piston Calipers and Their Key Considerations?
Piston calipers utilize one or more pistons to create hydraulic pressure for braking. They are widely used in commercial vehicles and heavy machinery due to their robustness and reliability under high loads. B2B buyers should consider the durability and performance of piston calipers, especially in demanding environments. While they offer excellent performance, their bulkier design may complicate installation and maintenance, necessitating skilled technicians for service.
What Advantages Do Electromechanical Calipers Offer?
Electromechanical calipers incorporate electronic control systems, making them suitable for electric vehicles and advanced braking systems. These calipers provide enhanced precision and adaptability, which can be a significant selling point for B2B buyers looking for cutting-edge technology. However, the complexity of these systems may lead to higher maintenance requirements and necessitate specialized knowledge for installation and repairs. Buyers should weigh these factors against the potential benefits of improved performance and efficiency.
Why Choose Brembo Calipers for High-Performance Applications?
Brembo calipers are synonymous with high-performance braking solutions and are favored in motorsports and luxury vehicle markets. Their exceptional performance and brand reputation make them a compelling choice for B2B buyers focused on quality. However, the premium pricing of Brembo products may not be justifiable for all applications, particularly for those with standard performance requirements. Buyers should evaluate their specific needs and budget constraints before opting for this high-end solution.
Related Video: How to Replace a Brake Caliper
Key Industrial Applications of brake caliper manufacturer
Industry/Sector | Specific Application of brake caliper manufacturer | Value/Benefit for the Business | Key Sourcing Considerations for this Application |
---|---|---|---|
Automotive Manufacturing | Production of passenger and commercial vehicle brake systems | Enhanced safety and performance, compliance with regulations | Quality certifications, material specifications, lead times |
Public Transport | Brake systems for buses and trains | Increased reliability and safety for mass transit systems | Durability, maintenance support, local regulations |
Construction Equipment | Brake calipers for heavy machinery | Improved operational efficiency and safety in construction | Heavy-duty specifications, compatibility with existing systems |
Aerospace | Aircraft brake calipers | Strict adherence to safety standards, weight reduction | Certifications (FAA/EASA), material properties, lead times |
Industrial Machinery | Brake systems for manufacturing equipment | Enhanced productivity and worker safety | Customization options, integration capabilities, reliability |
How is Brake Caliper Manufacturing Applied in Automotive Manufacturing?
In the automotive manufacturing sector, brake calipers are critical components in the brake systems of both passenger and commercial vehicles. They serve to clamp the brake pads against the rotors, providing the necessary stopping power. For international B2B buyers, especially in regions like Africa and South America, sourcing high-quality calipers is essential for ensuring vehicle safety and regulatory compliance. Manufacturers must prioritize suppliers that offer certified products with a track record of reliability, as well as competitive lead times to meet production schedules.
What Role Do Brake Calipers Play in Public Transport Systems?
Brake calipers are vital for the safety and reliability of public transport vehicles, such as buses and trains. These systems require robust braking solutions that can endure heavy usage while providing consistent performance. For buyers in the Middle East and Europe, selecting a brake caliper manufacturer that understands local safety standards and regulations is crucial. Furthermore, suppliers should offer comprehensive maintenance support and warranties to ensure long-term operational efficiency.
How Are Brake Calipers Utilized in Construction Equipment?
In the construction industry, brake calipers are used in heavy machinery such as excavators, bulldozers, and cranes. These applications demand high-performance braking systems that can withstand extreme conditions and heavy loads. International B2B buyers must seek manufacturers that specialize in heavy-duty specifications and can provide products that integrate seamlessly with existing machinery. Additionally, understanding the local market’s needs and compliance requirements is critical for successful procurement.
What Are the Requirements for Aerospace Brake Caliper Manufacturing?
The aerospace sector has stringent requirements for brake calipers due to the critical nature of aircraft safety. These components must meet rigorous safety standards and be lightweight to enhance fuel efficiency. Buyers from Europe and the Middle East should prioritize manufacturers with FAA or EASA certifications and a proven history in aerospace applications. Material properties, such as corrosion resistance and thermal stability, are also essential considerations for ensuring optimal performance in flight.
How Do Brake Calipers Enhance Industrial Machinery Operations?
In industrial machinery, brake calipers are integral to ensuring safety and productivity. They are used in various manufacturing equipment, where precise braking is necessary to prevent accidents and maintain operational flow. For B2B buyers in South America and Africa, sourcing brake systems that offer customization options to fit specific machinery needs is vital. Reliability and integration capabilities with existing systems are also key factors that can significantly impact operational efficiency and worker safety.
Related Video: Valvoline Brake Cleaner Instructional Video
3 Common User Pain Points for ‘brake caliper manufacturer’ & Their Solutions
Scenario 1: Difficulty in Ensuring Quality Standards in Brake Calipers
The Problem: Many B2B buyers, especially in regions like Africa and South America, face the challenge of sourcing high-quality brake calipers that meet international safety standards. Inconsistent product quality can lead to safety issues, increased warranty claims, and damage to the buyer’s reputation. Buyers often find it difficult to evaluate suppliers’ quality assurance processes, leading to uncertainty about the reliability of the components they purchase.
The Solution: To mitigate quality concerns, buyers should conduct thorough due diligence when selecting brake caliper manufacturers. This involves reviewing the manufacturer’s certifications, such as ISO 9001, and asking for samples of previous work. Engaging in direct conversations with the manufacturer about their quality control processes can provide additional assurance. It may also be beneficial to conduct factory audits or work with third-party quality assurance companies that can assess the manufacturing processes and product quality. Establishing a long-term partnership with a manufacturer that demonstrates consistent quality can greatly enhance reliability in the supply chain.
Scenario 2: Challenges in Customizing Brake Calipers to Specific Needs
The Problem: Another significant pain point for B2B buyers is the need for custom brake calipers tailored to specific vehicle models or unique applications. Many manufacturers offer only standard products, which may not meet the precise requirements of the buyer’s clients. This can lead to issues with vehicle performance and safety, ultimately affecting customer satisfaction and loyalty.
The Solution: To overcome customization challenges, buyers should clearly define their specifications and communicate these to potential manufacturers early in the sourcing process. This includes providing detailed drawings, performance requirements, and material specifications. It can be advantageous to work with manufacturers that specialize in custom solutions and have a track record of successful projects. Buyers should also ask about the manufacturer’s design capabilities and whether they utilize advanced engineering software for prototyping. Collaborating closely during the design phase can ensure that the final product meets all necessary specifications and performance standards.
Scenario 3: Navigating Import Regulations and Logistics for Brake Caliper Supply
The Problem: International B2B buyers often encounter complex import regulations and logistical challenges when sourcing brake calipers from overseas manufacturers. These challenges can lead to delays in delivery, unexpected tariffs, and complications with customs clearance, all of which can disrupt operations and increase costs.
The Solution: To navigate these logistical hurdles effectively, buyers should familiarize themselves with the import regulations in their respective countries. Consulting with local import/export experts or customs brokers can provide valuable insights into the necessary documentation and compliance requirements. Additionally, establishing a relationship with manufacturers who have experience in international shipping can simplify the process. Buyers should also consider using suppliers who offer comprehensive logistics solutions, including shipping and customs management, to streamline the supply chain. Developing a robust logistics plan that includes clear timelines and contingency strategies can help mitigate risks associated with international sourcing.
Strategic Material Selection Guide for brake caliper manufacturer
When selecting materials for brake calipers, manufacturers must consider various factors that impact performance, durability, and cost. This section will analyze four common materials used in brake caliper manufacturing: aluminum, cast iron, carbon composite, and stainless steel. Each material has distinct properties, advantages, and limitations that can significantly influence the final product’s effectiveness and marketability.
What Are the Key Properties of Aluminum for Brake Calipers?
Aluminum is a lightweight material known for its excellent strength-to-weight ratio. It typically has a temperature rating of up to 200°C and offers good corrosion resistance, making it suitable for various environments. Its ability to dissipate heat effectively helps maintain braking performance under high-stress conditions.
Pros and Cons:
The primary advantage of aluminum is its lightweight nature, which contributes to improved vehicle fuel efficiency. However, it can be more expensive than traditional materials like cast iron, and its manufacturing complexity can increase costs. Additionally, while aluminum is durable, it may not withstand extreme conditions as well as some heavier materials.
Impact on Application:
Aluminum calipers are particularly effective in high-performance vehicles where weight reduction is crucial. However, they may not be suitable for heavy-duty applications where extreme durability is required.
Considerations for International Buyers:
Buyers from regions like Europe and the Middle East should ensure compliance with standards such as ASTM and DIN. The preference for lightweight materials in European markets may favor aluminum, while cost-sensitive markets in Africa and South America might lean towards more economical options.
How Does Cast Iron Perform as a Brake Caliper Material?
Cast iron is a traditional choice for brake calipers, known for its excellent wear resistance and ability to withstand high temperatures (up to 400°C). It also exhibits good thermal conductivity, which helps in heat dissipation during braking.
Pros and Cons:
The primary advantage of cast iron is its durability and low cost, making it a popular choice for mass-produced vehicles. However, its weight can negatively impact fuel efficiency and performance. Additionally, cast iron is prone to corrosion if not properly treated, which can limit its lifespan.
Impact on Application:
Cast iron calipers are typically used in standard vehicles and heavy-duty applications, where durability and cost-effectiveness are prioritized over weight.
Considerations for International Buyers:
For buyers in South America and Africa, the cost-effectiveness of cast iron may be appealing. However, they should be aware of corrosion resistance standards, especially in humid climates. Compliance with local regulations regarding emissions and vehicle safety is also essential.
What Are the Benefits of Carbon Composite Brake Calipers?
Carbon composite materials are increasingly popular in high-performance brake calipers due to their exceptional strength and lightweight characteristics. They can withstand temperatures exceeding 600°C and have excellent corrosion resistance.
Pros and Cons:
The key advantage of carbon composites is their ability to provide superior performance while significantly reducing weight. However, the manufacturing process is complex and costly, making them less suitable for budget-sensitive applications.
Impact on Application:
These materials are ideal for racing and high-performance vehicles, where every gram counts and performance is paramount.
Considerations for International Buyers:
Buyers in Europe, particularly in the automotive racing sector, may find carbon composites appealing. However, the higher costs may deter buyers in developing regions like Africa and South America, where budget constraints are more prevalent.
How Does Stainless Steel Compare for Brake Caliper Manufacturing?
Stainless steel is known for its high corrosion resistance and durability, with temperature ratings reaching up to 300°C. It combines strength with a relatively low weight compared to cast iron.
Pros and Cons:
The main advantage of stainless steel is its resistance to rust and corrosion, making it suitable for various climates. However, it is generally more expensive than cast iron and can be heavier than aluminum.
Impact on Application:
Stainless steel calipers are well-suited for vehicles operating in harsh environments, such as coastal areas with high humidity.
Considerations for International Buyers:
International buyers should consider the climate and environmental conditions when selecting stainless steel. Compliance with international standards for corrosion resistance is also crucial, especially for buyers in the Middle East and Europe.
Summary Table of Material Selection for Brake Calipers
Material | Typical Use Case for brake caliper manufacturer | Key Advantage | Key Disadvantage/Limitation | Relative Cost (Low/Med/High) |
---|---|---|---|---|
Aluminum | High-performance vehicles | Lightweight and fuel-efficient | Higher cost and manufacturing complexity | High |
Cast Iron | Standard and heavy-duty vehicles | Durable and cost-effective | Heavy and prone to corrosion | Low |
Carbon Composite | Racing and high-performance applications | Superior performance and lightweight | High manufacturing cost | High |
Stainless Steel | Vehicles in harsh environments | Excellent corrosion resistance | More expensive and heavier than aluminum | Medium |
This strategic guide provides international B2B buyers with essential insights into material selection for brake calipers, helping them make informed decisions based on performance needs, cost considerations, and regional compliance standards.
In-depth Look: Manufacturing Processes and Quality Assurance for brake caliper manufacturer
What Are the Main Stages in the Manufacturing Process of Brake Calipers?
The manufacturing of brake calipers involves several critical stages, each designed to ensure the final product meets the stringent demands of performance and safety. For B2B buyers, understanding these stages can help in assessing the capabilities of potential suppliers.
-
Material Preparation: The process begins with the selection of high-quality materials, typically aluminum or cast iron, chosen for their strength and weight properties. Materials must be inspected for defects and conform to international standards, ensuring they can withstand high pressure and temperature variations.
-
Forming: In this stage, the raw materials undergo shaping through processes like die casting or machining. Die casting allows for intricate designs while maintaining dimensional accuracy. Machining further refines the caliper, ensuring precise fit and function. This stage is crucial for achieving the correct geometry, which directly affects brake performance.
-
Assembly: Once the individual components are formed, they are assembled into the caliper unit. This includes the integration of pistons, seals, and other critical parts. Automated assembly lines are common, enhancing efficiency and reducing human error. However, manual assembly may be employed for more complex designs, ensuring careful attention to detail.
-
Finishing: The final stage involves surface treatments such as anodizing or powder coating, which improve corrosion resistance and aesthetic appeal. Quality checks are performed at this stage to ensure that the calipers meet all specifications before they move to the testing phase.
How Is Quality Assurance Integrated into Brake Caliper Manufacturing?
Quality assurance (QA) is an integral part of the manufacturing process, ensuring that the brake calipers produced are safe and reliable. For international B2B buyers, understanding QA measures helps in evaluating potential suppliers.
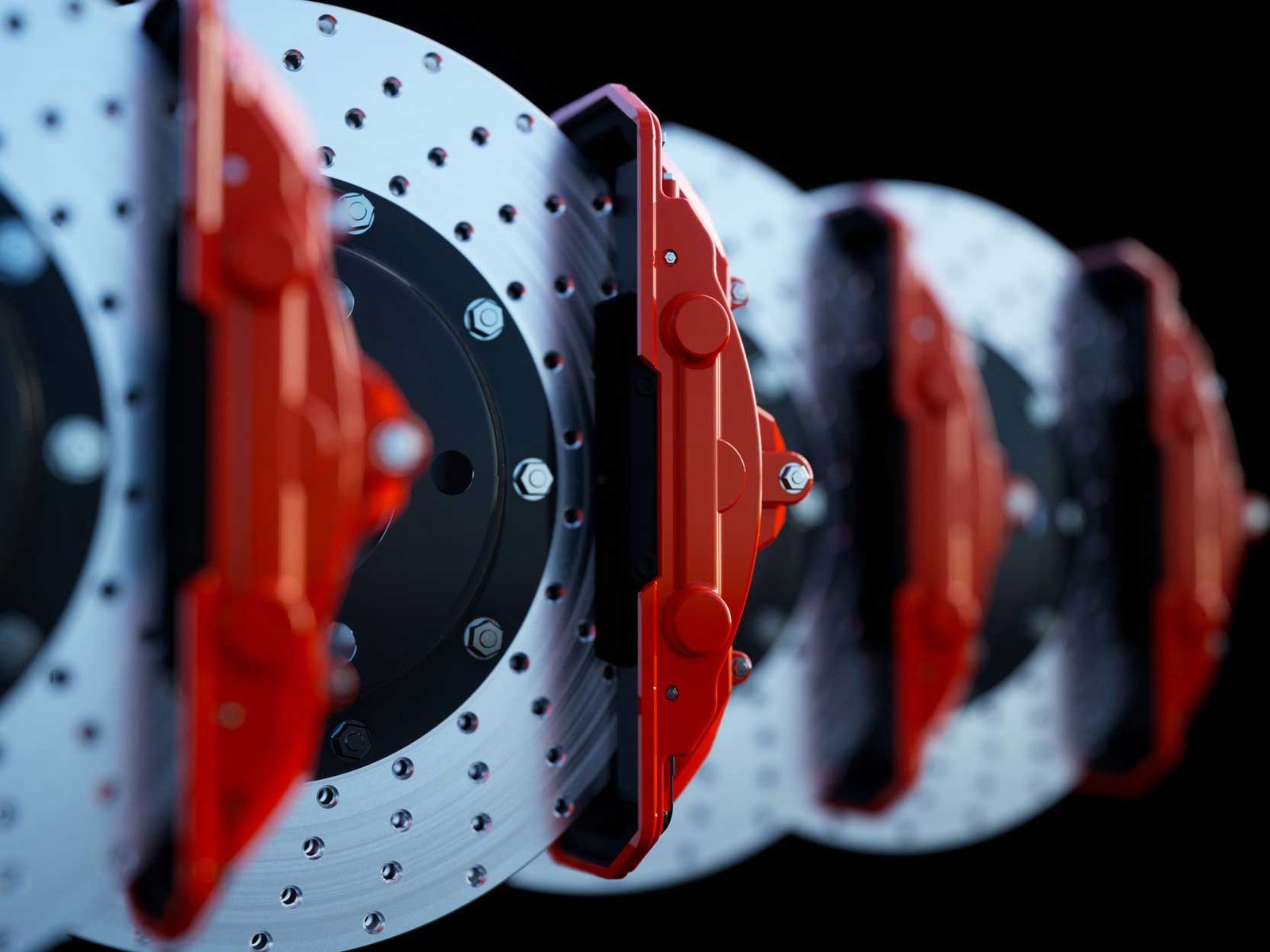
A stock image related to brake caliper manufacturer.
-
International Standards: Many manufacturers adhere to ISO 9001, a global standard for quality management systems. Compliance with this standard indicates a commitment to quality processes and customer satisfaction. Additionally, industry-specific certifications such as CE marking for European markets and API standards for certain applications are critical for ensuring that the products meet regulatory requirements.
-
Quality Control Checkpoints:
– Incoming Quality Control (IQC): This stage involves inspecting raw materials upon arrival at the manufacturing facility. Ensuring that materials meet predetermined specifications is essential to avoid defects in the final product.
– In-Process Quality Control (IPQC): Throughout the manufacturing stages, IPQC checks are conducted to monitor processes and ensure that any deviations from quality standards are addressed immediately.
– Final Quality Control (FQC): After finishing, FQC involves comprehensive testing of the finished calipers. This may include dimensional checks, functional tests, and performance evaluations to ensure that the product meets all specifications.
What Common Testing Methods Are Used for Brake Calipers?
Testing methods are vital for ensuring the performance and safety of brake calipers. B2B buyers should inquire about the specific testing protocols used by potential suppliers.
-
Hydraulic Pressure Testing: This method simulates real-world conditions to check for leaks and structural integrity under pressure. Calipers are subjected to high-pressure conditions to ensure they can withstand operational demands.
-
Thermal Cycling Tests: These tests assess how calipers perform under extreme temperature fluctuations, simulating conditions they might encounter in actual use. The ability to maintain performance without warping or degradation is crucial.
-
Dimensional and Visual Inspections: These checks ensure that all components meet precise specifications. Visual inspections help identify any surface defects or irregularities that could affect performance.
How Can B2B Buyers Verify Supplier Quality Control?
Ensuring that a brake caliper manufacturer meets quality standards is essential for B2B buyers. Here are actionable steps to verify supplier quality control:
-
Conduct Supplier Audits: Regular audits of potential suppliers can reveal their manufacturing practices, quality control measures, and adherence to international standards. It is advisable to have a checklist based on ISO certifications and specific industry requirements.
-
Request Quality Reports: Suppliers should provide documentation detailing their quality control processes, including results from recent tests and inspections. This transparency can help buyers assess reliability.
-
Utilize Third-Party Inspection Services: Engaging third-party inspection agencies can offer an unbiased evaluation of the manufacturer’s quality assurance processes. These agencies can conduct audits and testing on behalf of the buyer, ensuring compliance with international standards.
What Are the Nuances of Quality Certification for International B2B Buyers?
For B2B buyers, particularly those from Africa, South America, the Middle East, and Europe, understanding the nuances of quality certification is crucial for making informed purchasing decisions.
-
Regional Compliance: Different regions may have specific regulatory requirements. For instance, CE marking is mandatory for products sold in Europe, while certain certifications may be needed for markets in Africa or South America. Buyers should ensure that their suppliers have the relevant certifications for their target markets.
-
Understanding Certification Validity: Certifications can expire or be subject to renewal. Buyers should verify that the suppliers’ certifications are current and relevant. This includes checking the scope of certification to ensure it covers the specific products being purchased.
-
Cultural and Communication Considerations: Engaging with suppliers from different regions may present language and cultural barriers. Buyers should ensure clear communication regarding quality expectations and requirements, possibly utilizing local intermediaries who understand regional practices.
Conclusion
In summary, the manufacturing processes and quality assurance measures for brake calipers are multifaceted and critical for ensuring safety and performance. For international B2B buyers, especially those from diverse regions, understanding these processes not only aids in supplier selection but also enhances confidence in the products being procured. By focusing on material preparation, forming, assembly, and finishing, alongside stringent quality control measures and relevant certifications, buyers can make informed decisions that support their operational needs.
Practical Sourcing Guide: A Step-by-Step Checklist for ‘brake caliper manufacturer’
Introduction
Sourcing brake calipers for your business involves careful consideration and strategic planning. This guide provides a step-by-step checklist to help international B2B buyers, particularly from Africa, South America, the Middle East, and Europe, navigate the complexities of procurement. By following these actionable steps, you can ensure you select the right manufacturer that meets your quality, compliance, and operational needs.
Step 1: Define Your Technical Specifications
Before engaging with potential suppliers, clearly outline the technical specifications of the brake calipers you require. This includes details such as material composition, size, weight, and performance standards.
- Why it’s important: Precise specifications help prevent misunderstandings and ensure that the products meet your operational requirements.
- What to look for: Consider industry standards such as ISO certifications or specific automotive regulations that may apply in your region.
Step 2: Conduct Market Research on Manufacturers
Research potential brake caliper manufacturers that have a strong reputation in the industry. Look for companies that specialize in the type of calipers you need and have a history of successful exports to your region.
- Why it’s important: Understanding the market landscape helps you identify reliable suppliers and avoid those with poor track records.
- What to look for: Check online reviews, industry publications, and trade shows for insights into manufacturers’ reputations and capabilities.
Step 3: Verify Supplier Certifications
Ensure that the manufacturers you are considering hold relevant certifications, such as ISO/TS 16949 for automotive suppliers.
- Why it’s important: Certifications indicate that a manufacturer adheres to international quality management systems, which can significantly reduce risks associated with product defects.
- What to look for: Request copies of certifications and check their validity with issuing bodies.
Step 4: Request Samples and Conduct Quality Checks
Before finalizing a supplier, request samples of their brake calipers to evaluate quality firsthand.
- Why it’s important: Sampling allows you to assess the product’s quality and compatibility with your existing systems before placing a large order.
- What to look for: Pay attention to materials used, finishing, and overall craftsmanship. Conduct testing where possible to ensure performance standards are met.
Step 5: Assess Production Capabilities and Lead Times
Inquire about the manufacturer’s production capacity and lead times for orders.
- Why it’s important: Understanding their ability to meet your demand and delivery schedules is crucial for maintaining your supply chain.
- What to look for: Confirm their production capabilities, including maximum order quantities and typical turnaround times for large orders.
Step 6: Evaluate Communication and Support Services
Assess the level of communication and support you can expect from potential suppliers.
- Why it’s important: Effective communication is vital for resolving issues that may arise during production or delivery.
- What to look for: Ensure that the supplier has a dedicated support team and is responsive to inquiries. Look for multilingual support, especially if you are dealing with suppliers in non-English speaking regions.
Step 7: Negotiate Terms and Conditions
Once you’ve shortlisted potential manufacturers, begin negotiating terms and conditions, including pricing, payment terms, and warranties.
- Why it’s important: Clear agreements help prevent disputes and ensure that both parties understand their responsibilities.
- What to look for: Be sure to discuss terms related to quality assurance, return policies, and after-sales support.
By following this checklist, international B2B buyers can make informed decisions when sourcing brake calipers, ultimately leading to a more efficient and cost-effective procurement process.
Comprehensive Cost and Pricing Analysis for brake caliper manufacturer Sourcing
What Are the Key Cost Components in Brake Caliper Manufacturing?
Understanding the cost structure of brake caliper manufacturing is crucial for international B2B buyers aiming to make informed sourcing decisions. The primary cost components include:
-
Materials: The choice of materials significantly impacts costs. High-quality alloys, rubber seals, and other components can vary widely in price depending on the supplier and source. Buyers should assess the quality versus cost trade-offs.
-
Labor: Labor costs vary by region and are influenced by local wage standards and workforce skill levels. Manufacturers in countries with lower labor costs may offer competitive pricing, but it’s essential to evaluate the skill and expertise of the labor force.
-
Manufacturing Overhead: This includes costs related to utilities, facility maintenance, and administrative expenses. Manufacturers with efficient operations can offer better pricing, so it’s beneficial to inquire about their overhead management strategies.
-
Tooling: The initial investment in tooling can be significant, especially for custom designs. Buyers should understand how tooling costs are amortized over production runs, which can affect pricing for smaller orders.
-
Quality Control (QC): Robust QC processes ensure product reliability but can also add to costs. Buyers should inquire about the supplier’s QC protocols and certifications, as these can influence both price and product quality.
-
Logistics: Shipping costs can vary depending on the distance, mode of transport, and Incoterms used. Understanding these logistics costs is essential for calculating the total cost of ownership.
-
Margin: Manufacturers typically include a profit margin in their pricing. Understanding the market and negotiating margins can lead to better pricing outcomes.
How Do Volume and Customization Affect Brake Caliper Pricing?
Volume and Minimum Order Quantity (MOQ) play a significant role in pricing. Generally, higher order volumes lead to lower per-unit costs due to economies of scale. Conversely, smaller orders may incur higher prices due to the fixed costs associated with production setup.
Customization also influences price. Custom designs or specifications require additional tooling and labor, which can increase costs. Buyers should clearly communicate their needs and explore whether batch production for customized items might reduce overall costs.
What Quality Certifications Should Buyers Consider When Sourcing Brake Calipers?
Quality certifications are critical when sourcing brake calipers. Look for suppliers with ISO 9001 or IATF 16949 certifications, as these indicate adherence to international quality management standards. Certifications can add to the cost but often lead to better quality assurance and reliability, which can save costs in the long run due to reduced failures and warranty claims.
What Negotiation Strategies Can Help Buyers Achieve Cost Efficiency?
Effective negotiation is key to achieving cost efficiency. Here are some strategies:
-
Research the Market: Understanding the pricing landscape helps buyers negotiate effectively. Gather quotes from multiple suppliers to establish a baseline.
-
Leverage Volume Discounts: If possible, consolidate orders to negotiate better pricing based on higher volumes.
-
Discuss Payment Terms: Offering favorable payment terms can sometimes lead to discounts. Discussing options like early payment or bulk payment can be beneficial.
-
Build Relationships: Establishing long-term relationships with suppliers can lead to better pricing and terms over time.
What Is the Total Cost of Ownership for Brake Calipers?
When evaluating the pricing of brake calipers, consider the Total Cost of Ownership (TCO), which encompasses not just the purchase price but also logistics, maintenance, and potential replacement costs. By factoring in these elements, international B2B buyers can make better-informed decisions that align with their long-term financial goals.
What Should International Buyers Know About Pricing Nuances?
International buyers must navigate various pricing nuances, including currency fluctuations, import duties, and local taxes, which can significantly affect the final cost. It is advisable to account for these factors in your budgeting and pricing discussions with suppliers.
Disclaimer on Indicative Prices
While this analysis provides a comprehensive overview of cost components and pricing influences, actual prices can vary based on specific supplier agreements, market conditions, and individual buyer needs. Always request detailed quotes and conduct thorough due diligence before making purchasing decisions.
Alternatives Analysis: Comparing brake caliper manufacturer With Other Solutions
When considering brake caliper solutions, it is essential to evaluate various alternatives that may better suit specific operational needs or financial constraints. This section compares traditional brake caliper manufacturers with two viable alternatives: Aftermarket Brake Calipers and Brake-by-Wire Systems. Each option presents unique advantages and challenges, and understanding these can empower international B2B buyers to make informed decisions.
Comparison Aspect | Brake Caliper Manufacturer | Aftermarket Brake Calipers | Brake-by-Wire Systems |
---|---|---|---|
Performance | High durability and reliability, engineered for specific vehicle models | Varies widely; can enhance performance but may not match OEM standards | Offers precise control and can improve overall vehicle performance |
Cost | Higher initial investment due to quality and brand reputation | Generally lower cost, but quality varies; potential for hidden costs | Higher upfront cost; reduced maintenance costs over time |
Ease of Implementation | Straightforward installation for OEM applications | May require modifications; installation can be complex | Requires specialized knowledge and technology integration |
Maintenance | Typically low maintenance if OEM standards are followed | May require more frequent checks; quality varies by brand | Lower maintenance needs due to fewer mechanical parts |
Best Use Case | Ideal for manufacturers seeking quality assurance and reliability | Suitable for cost-conscious buyers or performance enthusiasts | Best for advanced vehicle designs prioritizing efficiency and performance |
What Are the Advantages and Disadvantages of Aftermarket Brake Calipers?
Aftermarket brake calipers are often a cost-effective solution for buyers looking to save on expenses. They provide an opportunity for customization and may enhance performance in specific contexts, particularly for racing or modified vehicles. However, the quality of aftermarket products can vary significantly. Buyers must conduct thorough research to ensure they are purchasing from reputable manufacturers. Additionally, since these calipers may not be designed for specific vehicle models, installation could require additional modifications, which can increase total costs.
How Do Brake-by-Wire Systems Compare to Traditional Brake Calipers?
Brake-by-wire systems represent a cutting-edge alternative to traditional mechanical brake systems. These systems utilize electronic controls to engage braking, offering superior precision and responsiveness. They can improve vehicle performance and reduce weight, making them appealing for modern automotive applications. However, the initial investment can be substantial, and implementation may require specialized knowledge and technology integration. Furthermore, as a relatively new technology, long-term reliability and maintenance practices are still being established, which could pose risks for conservative buyers.
Conclusion: How Should B2B Buyers Choose the Right Brake Solution?
In deciding between brake caliper manufacturers and their alternatives, B2B buyers should consider their specific operational needs, budget constraints, and the intended application of the vehicle. For companies prioritizing reliability and performance, investing in a reputable brake caliper manufacturer may be the best choice. Conversely, those looking for cost-effective solutions or innovations might find value in aftermarket options or the latest brake-by-wire technologies. Conducting a thorough analysis of each option’s advantages and drawbacks will ensure that buyers select the most appropriate solution for their unique requirements.
Essential Technical Properties and Trade Terminology for brake caliper manufacturer
What Are the Key Technical Properties of Brake Calipers?
When sourcing brake calipers, understanding the essential technical properties is crucial for ensuring product quality and performance. Here are several critical specifications that international B2B buyers should consider:
1. Material Grade
Brake calipers are commonly manufactured from materials such as aluminum, cast iron, or composite materials. The choice of material significantly impacts weight, durability, and thermal performance. For instance, aluminum calipers offer a lightweight solution that enhances vehicle performance, while cast iron provides better wear resistance. Buyers should assess the material grade to ensure it meets their specific application requirements and performance standards.
2. Tolerance
Tolerance refers to the permissible limit of variation in a physical dimension, which is vital for the proper functioning of brake calipers. High precision in manufacturing tolerances ensures that parts fit together seamlessly, reducing the risk of mechanical failure. In the B2B context, specifying the required tolerance levels can help prevent costly reworks and ensure compatibility with existing systems.
3. Weight Specifications
The weight of a brake caliper can influence the overall weight distribution of a vehicle, affecting handling and fuel efficiency. Buyers should consider weight specifications to ensure that the calipers align with their vehicle’s design and performance goals. Lighter calipers can enhance performance, particularly in high-performance or racing applications.
4. Corrosion Resistance
Given that brake calipers are often exposed to harsh environmental conditions, corrosion resistance is a crucial property. Manufacturers may apply various coatings or treatments to enhance corrosion resistance. Buyers should inquire about the specific treatments used, especially if the calipers will be used in regions with high humidity or salt exposure, such as coastal areas.
5. Thermal Conductivity
Brake calipers undergo significant heat during operation, making thermal conductivity an important property. Effective heat dissipation helps maintain braking performance and prevents brake fade. When sourcing calipers, buyers should evaluate the thermal properties to ensure they can withstand the demands of their specific applications.
What Are Common Trade Terms Related to Brake Caliper Manufacturing?
Familiarity with industry terminology is essential for effective communication and negotiation in B2B transactions. Here are some common trade terms that buyers should understand:
1. OEM (Original Equipment Manufacturer)
OEM refers to companies that produce parts or equipment that may be marketed by another manufacturer. In the context of brake calipers, sourcing from OEMs can ensure compatibility and reliability, as these products are designed to meet original specifications. Buyers should prioritize OEM parts for new vehicle builds or replacements.
2. MOQ (Minimum Order Quantity)
MOQ is the smallest quantity of a product that a supplier is willing to sell. Understanding the MOQ is vital for budgeting and inventory management. Buyers should negotiate the MOQ based on their needs, particularly if they are entering new markets or require smaller batches for testing purposes.
3. RFQ (Request for Quotation)
An RFQ is a document used to invite suppliers to bid on providing specific products or services. When sourcing brake calipers, submitting an RFQ can help buyers receive competitive pricing and terms from multiple manufacturers. It’s a strategic tool for ensuring that the procurement process is efficient and cost-effective.
4. Incoterms (International Commercial Terms)
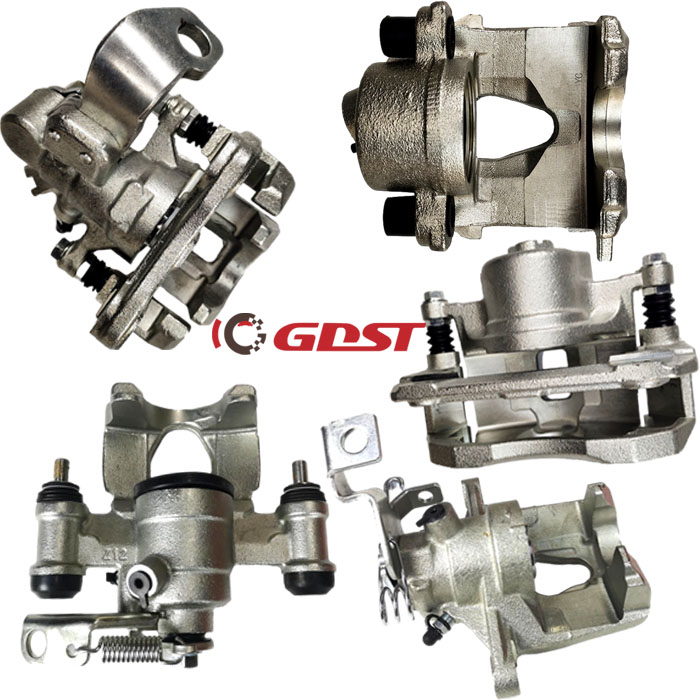
A stock image related to brake caliper manufacturer.
Incoterms are a set of international rules that define the responsibilities of buyers and sellers regarding the transportation and delivery of goods. Familiarity with Incoterms is essential for international trade, as they clarify who bears the risk and cost at each stage of the shipping process. Buyers should ensure they understand the applicable Incoterms when negotiating contracts with manufacturers.
5. Lead Time
Lead time refers to the time it takes from placing an order to receiving the product. Understanding lead times is crucial for inventory planning and ensuring timely delivery of brake calipers, especially in industries with strict deadlines. Buyers should inquire about lead times during negotiations to align their production schedules accordingly.
By grasping these essential technical properties and trade terms, international B2B buyers can make informed decisions when sourcing brake calipers, ultimately leading to enhanced performance and reliability in their applications.
Navigating Market Dynamics and Sourcing Trends in the brake caliper manufacturer Sector
What Are the Key Market Dynamics and Trends in the Brake Caliper Manufacturing Sector?
The brake caliper manufacturing sector is currently experiencing significant transformation driven by globalization, technological advancement, and evolving consumer preferences. The increasing demand for electric vehicles (EVs) is one of the primary global drivers influencing this market. As automakers shift towards EV production, the need for lightweight and high-performance brake calipers has intensified. This shift is particularly relevant for international buyers from regions like Africa and South America, where the automotive industry is rapidly developing.
Emerging technologies, such as 3D printing and automation, are reshaping the sourcing landscape. These advancements enable manufacturers to produce brake calipers with greater precision and lower costs, making it an attractive option for B2B buyers looking for competitive pricing and quality assurance. Additionally, the rise of digital platforms for procurement is streamlining sourcing processes, allowing buyers from Turkey and Vietnam to efficiently connect with global suppliers.
Market dynamics are also influenced by geopolitical factors, such as trade policies and tariffs. Buyers must stay informed about these changes to mitigate risks associated with sourcing. For example, fluctuations in raw material prices due to trade tensions can directly impact production costs. Understanding regional market conditions and establishing strong relationships with suppliers are crucial for effective sourcing strategies.
How Can Sustainability and Ethical Sourcing Impact B2B Decisions in Brake Caliper Manufacturing?
As the global focus on sustainability intensifies, ethical sourcing has become paramount for B2B buyers in the brake caliper manufacturing sector. The environmental impact of manufacturing processes and material sourcing has led to increased scrutiny from consumers and regulatory bodies alike. Buyers are encouraged to prioritize suppliers who adhere to sustainable practices, which can enhance brand reputation and customer loyalty.
One significant aspect of sustainability is the use of eco-friendly materials. Buyers should look for brake calipers made from recycled metals or sourced from suppliers with green certifications. Such materials not only reduce the environmental footprint but also often comply with international standards, making them more acceptable in various markets, including Europe and the Middle East.
Furthermore, ethical supply chains are becoming a competitive differentiator. B2B buyers must consider the labor practices and sourcing policies of their suppliers. Ensuring that suppliers operate in compliance with labor laws and environmental regulations can mitigate risks associated with reputational damage and potential legal issues. Emphasizing sustainability and ethical sourcing can lead to long-term partnerships and greater market access.
What Is the Evolution of Brake Caliper Manufacturing?
The brake caliper manufacturing sector has evolved significantly over the decades, transitioning from simple mechanical designs to sophisticated, high-performance components. Initially, brake calipers were primarily made from cast iron, focusing on durability and cost. However, with advancements in materials science and engineering, manufacturers began to utilize aluminum alloys and composites, which offer lighter weight and improved performance.
The evolution has been further accelerated by the integration of technology, such as computer-aided design (CAD) and finite element analysis (FEA), enabling manufacturers to optimize designs for strength and efficiency. As a result, today’s brake calipers are not only more efficient but also play a crucial role in enhancing vehicle safety and performance. For international B2B buyers, understanding this historical context is vital for making informed sourcing decisions, as it highlights the importance of innovation and quality in the selection of suppliers.
Frequently Asked Questions (FAQs) for B2B Buyers of brake caliper manufacturer
-
How do I choose the right brake caliper manufacturer for my business needs?
Choosing the right brake caliper manufacturer involves evaluating several key factors. First, assess the manufacturer’s industry experience and reputation. Look for reviews or testimonials from other B2B buyers in your region. Additionally, consider the manufacturer’s production capacity and technology. Are they capable of meeting your volume requirements? Finally, inquire about their compliance with international quality standards, such as ISO certification, which can assure product reliability and safety. -
What customization options are available when sourcing brake calipers?
Many brake caliper manufacturers offer customization options to meet specific requirements. These may include variations in materials, colors, and finishes, as well as modifications in design to fit unique vehicle models. Discuss your needs with potential suppliers to understand their capabilities. Ensure that they can provide prototypes for testing before placing a bulk order. Customization can enhance compatibility and performance, ultimately leading to greater customer satisfaction in your target market. -
What is the typical minimum order quantity (MOQ) for brake caliper manufacturers?
The MOQ for brake calipers can vary significantly depending on the manufacturer and the specific product line. Generally, established manufacturers may have a MOQ ranging from 100 to 1,000 units. However, some may accommodate lower quantities for special orders or new buyers. Always clarify the MOQ during initial discussions, as this can impact your purchasing strategy and inventory management. Consider negotiating terms if your business requires smaller batches, especially for niche markets. -
What payment terms should I expect when dealing with brake caliper manufacturers?
Payment terms can differ widely among manufacturers and depend on factors such as order size and buyer reputation. Common terms include upfront deposits (often 30-50%) with the balance due upon shipment or delivery. Some manufacturers may offer credit terms for established clients. Always clarify payment conditions before finalizing agreements and ensure they align with your cash flow requirements. Additionally, inquire about accepted payment methods, such as letters of credit, wire transfers, or PayPal, to ensure a smooth transaction process. -
How can I ensure quality assurance when sourcing brake calipers?
To ensure quality assurance, it’s crucial to partner with manufacturers who adhere to rigorous quality control processes. Request information about their quality management systems and certifications. Conducting factory audits can also provide insights into their operational standards. Additionally, consider implementing a third-party quality inspection service before shipment to verify that the products meet your specifications and international safety standards. This proactive approach can prevent costly defects and enhance customer trust. -
What logistics considerations should I keep in mind when importing brake calipers?
When importing brake calipers, logistics is a critical factor. Evaluate shipping options based on cost, speed, and reliability. Consider using freight forwarders who specialize in automotive parts to navigate customs regulations effectively. Also, factor in the lead times for production and shipping to avoid delays in your supply chain. Ensure that your supplier provides adequate documentation for customs clearance. Understanding the logistics landscape will help you manage inventory levels and maintain timely delivery to your customers. -
What are the common challenges in international trade for brake caliper procurement?
International trade can present various challenges, including fluctuating tariffs, customs delays, and regulatory compliance. Buyers must stay informed about trade agreements that may affect import duties in their respective regions. Language barriers and cultural differences can also complicate negotiations. To mitigate these risks, consider working with local agents or consultants who understand the regional market dynamics. Building strong relationships with manufacturers can also facilitate smoother communication and collaboration throughout the procurement process. -
How do I handle disputes or issues with my brake caliper supplier?
In the event of disputes or issues with your brake caliper supplier, it’s essential to approach the situation professionally and constructively. Start by documenting all communications and agreements to have a clear record. Initiate a dialogue with the supplier to discuss the issue openly and seek a resolution. If necessary, refer to your contract terms regarding dispute resolution mechanisms. In extreme cases, consider mediation or arbitration services to resolve conflicts amicably without damaging the business relationship.
Important Disclaimer & Terms of Use
⚠️ Important Disclaimer
The information provided in this guide, including content regarding manufacturers, technical specifications, and market analysis, is for informational and educational purposes only. It does not constitute professional procurement advice, financial advice, or legal advice.
While we have made every effort to ensure the accuracy and timeliness of the information, we are not responsible for any errors, omissions, or outdated information. Market conditions, company details, and technical standards are subject to change.
B2B buyers must conduct their own independent and thorough due diligence before making any purchasing decisions. This includes contacting suppliers directly, verifying certifications, requesting samples, and seeking professional consultation. The risk of relying on any information in this guide is borne solely by the reader.
Strategic Sourcing Conclusion and Outlook for brake caliper manufacturer
In the rapidly evolving landscape of brake caliper manufacturing, strategic sourcing emerges as a pivotal element for international B2B buyers. By adopting a comprehensive sourcing strategy, companies from Africa, South America, the Middle East, and Europe can ensure access to high-quality products while optimizing costs. Key takeaways include the importance of evaluating suppliers based on quality certifications, production capabilities, and reliability. Furthermore, fostering long-term relationships with manufacturers can lead to enhanced negotiation power and better terms.
How can B2B buyers leverage technology in strategic sourcing? Utilizing advanced technologies such as AI and data analytics can streamline the sourcing process, allowing for smarter decision-making and improved supplier selection. Additionally, engaging with local suppliers can mitigate supply chain risks and promote regional economic growth.
Looking ahead, the brake caliper manufacturing sector is poised for innovation, driven by sustainability and technological advancements. International B2B buyers should remain proactive in exploring new sourcing opportunities and partnerships that align with their strategic goals. Embrace the potential of strategic sourcing to enhance your supply chain resilience and drive competitive advantage in a global market.