Cut Costs with Prefab House China: The Complete Buying Guide (2025)
Introduction: Navigating the Global Market for prefab house china
The global market for prefab houses from China presents a compelling opportunity for international B2B buyers looking to streamline construction processes while ensuring cost-effectiveness and quality. However, navigating this complex landscape can be challenging due to varying regulations, quality standards, and supplier reliability. This guide aims to address these challenges by providing a comprehensive overview of prefab houses in China, focusing on key aspects such as types, applications, supplier vetting, and cost considerations.
International buyers, particularly from regions like Africa, South America, the Middle East, and Europe, including countries such as Saudi Arabia and Argentina, will find this guide invaluable. It empowers decision-makers with actionable insights on sourcing high-quality prefab housing solutions that meet their specific needs. By understanding the different types of prefab houses—ranging from modular units to panelized systems—and their applications across various sectors, buyers can make informed choices that align with their project requirements.
Moreover, the guide emphasizes the importance of rigorous supplier vetting processes, ensuring that buyers can identify reputable manufacturers and avoid potential pitfalls. With detailed cost analysis and comparisons, this resource equips B2B buyers with the knowledge necessary to negotiate effectively and optimize their procurement strategies. As you embark on your journey to source prefab houses from China, this guide will serve as your trusted companion, enabling you to navigate the global market with confidence.
Understanding prefab house china Types and Variations
Type Name | Key Distinguishing Features | Primary B2B Applications | Brief Pros & Cons for Buyers |
---|---|---|---|
Container Homes | Built from shipping containers, modular design | Affordable housing, temporary sites | Pros: Cost-effective, quick to assemble. Cons: Limited space, insulation issues. |
Modular Homes | Prefabricated sections assembled on-site | Residential buildings, hotels | Pros: Customizable, energy-efficient. Cons: Higher initial costs, zoning restrictions. |
Panelized Homes | Flat panels shipped and assembled on-site | Single-family homes, commercial buildings | Pros: Quick construction, less waste. Cons: Requires skilled labor for assembly. |
Steel Frame Houses | Strong steel structure, resistant to weather | Industrial sites, disaster recovery | Pros: Durable, low maintenance. Cons: Higher costs, thermal conductivity issues. |
Eco-Friendly Prefabs | Sustainable materials, energy-efficient designs | Green housing projects, eco-villages | Pros: Lower environmental impact, energy savings. Cons: May have higher upfront costs, limited designs. |
What are the Key Characteristics of Container Homes?
Container homes are constructed using repurposed shipping containers, offering a unique modular design that promotes quick assembly. They are particularly suitable for affordable housing projects and temporary sites, making them a popular choice in developing regions. B2B buyers should consider the cost-effectiveness and speed of construction, but also be aware of potential challenges such as limited interior space and insulation issues, which may affect livability in extreme climates.
How Do Modular Homes Differ from Traditional Homes?
Modular homes consist of prefabricated sections that are manufactured off-site and assembled on-site. This type of prefab home is highly customizable, allowing businesses to tailor designs to specific needs, making them ideal for residential developments and hotels. While modular homes can be energy-efficient and reduce construction time, B2B buyers should be prepared for higher initial costs and potential zoning restrictions that could complicate project timelines.
What are the Advantages of Panelized Homes?
Panelized homes are constructed from flat panels that are shipped to the site for assembly. This method allows for quick construction and minimizes waste, making it an attractive option for single-family homes and commercial buildings. B2B purchasers should note that while panelized homes can be built swiftly, they require skilled labor for proper assembly, which may impact project costs and timelines.
Why Choose Steel Frame Houses for Industrial Applications?
Steel frame houses utilize a robust steel structure, providing excellent durability and weather resistance. They are particularly well-suited for industrial applications and disaster recovery efforts due to their strength and low maintenance requirements. However, B2B buyers should consider the higher costs associated with steel construction, as well as thermal conductivity issues that may necessitate additional insulation.
What Makes Eco-Friendly Prefabs a Smart Investment?
Eco-friendly prefabs are designed with sustainable materials and energy-efficient features, catering to the growing demand for environmentally responsible housing solutions. These homes are ideal for green housing projects and eco-villages, appealing to socially conscious buyers. While they offer long-term energy savings and a lower environmental impact, B2B buyers may face higher upfront costs and a limited selection of designs, which could affect project feasibility.
Related Video: 30 days finished 300sqm Luxury prefab homes made from Light gauge Steel framing Villa made in China,
Key Industrial Applications of prefab house china
Industry/Sector | Specific Application of prefab house china | Value/Benefit for the Business | Key Sourcing Considerations for this Application |
---|---|---|---|
Construction & Real Estate | Temporary housing for construction workers | Reduces project delays and enhances worker safety | Compliance with local building codes and regulations |
Disaster Relief | Emergency shelters in disaster zones | Quick deployment and cost-effective solutions | Durability against local climate conditions |
Hospitality | Modular hotels and resorts | Rapid construction and flexibility in design | Aesthetic appeal and adherence to brand standards |
Education | Classrooms and dormitories | Fast setup to accommodate growing student populations | Customization for local educational needs |
Healthcare | Mobile clinics and healthcare facilities | Immediate response to healthcare demands | Compliance with health regulations and standards |
How is Prefab House China Used in Construction & Real Estate?
In the construction and real estate sector, prefab houses from China are often utilized as temporary housing for construction workers. This application addresses the challenge of providing safe and comfortable living conditions for workers on-site, thereby minimizing project delays due to worker absenteeism or safety concerns. For international buyers, especially in regions like Africa and the Middle East, it’s essential to ensure that the prefab structures comply with local building codes and regulations to avoid legal issues.
What Role Do Prefab Houses Play in Disaster Relief?
Prefab houses are critical in disaster relief efforts, serving as emergency shelters in areas affected by natural disasters. These structures can be rapidly deployed, providing immediate housing solutions for displaced populations. The key benefit for businesses involved in humanitarian efforts is the cost-effectiveness and speed of deployment. Buyers must consider the durability of materials against local climate conditions to ensure the shelters can withstand environmental challenges.

A stock image related to prefab house china.
How Can Prefab Houses Enhance Hospitality Ventures?
In the hospitality sector, prefab houses are increasingly being used to create modular hotels and resorts. This application allows for rapid construction and the flexibility to design unique accommodations that can be tailored to various landscapes. For international buyers, particularly in South America and Europe, it’s crucial to focus on the aesthetic appeal of these structures, ensuring they align with brand standards and customer expectations to attract guests.
Why Are Prefab Houses Valuable in Education?
Prefab houses are utilized in educational settings for constructing classrooms and dormitories, especially in regions facing rapid population growth. These structures can be set up quickly to accommodate more students, addressing urgent educational needs. Buyers should prioritize customization options to meet local educational requirements, ensuring that the prefab solutions are conducive to effective learning environments.
How Are Prefab Houses Beneficial in Healthcare?
In healthcare, prefab houses are employed to create mobile clinics and healthcare facilities, especially in remote or underserved areas. This application allows for an immediate response to healthcare demands, providing essential services where they are most needed. For international B2B buyers, compliance with health regulations and standards is paramount to ensure the safety and efficacy of healthcare delivery in these structures.
Related Video: INDUSTRY SHIFTING prefab house! FIRST LOOK at this MUST SEE modular home!
3 Common User Pain Points for ‘prefab house china’ & Their Solutions
Scenario 1: Sourcing Quality Materials for Prefab Houses from China
The Problem: One of the most pressing challenges for B2B buyers looking to import prefab houses from China is ensuring the quality of materials used in construction. Many international buyers report issues with substandard materials that do not meet local building codes or sustainability standards. This not only affects the safety and durability of the structures but can also lead to costly delays and legal complications in the buyer’s home country.
The Solution: To mitigate this risk, it is crucial for buyers to conduct thorough due diligence when selecting suppliers. Start by verifying certifications and compliance with international standards such as ISO and local building regulations. Request samples of materials and, if possible, conduct on-site inspections or hire third-party quality assurance firms to evaluate the manufacturing process. Establishing a direct line of communication with the manufacturers can also facilitate better understanding and transparency regarding material sourcing and quality control practices. Additionally, consider partnering with local agents who have experience in the Chinese market to navigate potential pitfalls effectively.
Scenario 2: Navigating Import Regulations for Prefab Houses
The Problem: Another significant challenge faced by international buyers is navigating the complex landscape of import regulations and tariffs associated with prefab houses. Each country has specific requirements that can include customs documentation, health and safety standards, and environmental regulations. Failing to comply can lead to delays, additional costs, or even confiscation of goods.
The Solution: To streamline the import process, buyers should engage with a knowledgeable customs broker who specializes in construction materials or prefab housing. This expert can help clarify the necessary documentation and compliance requirements. Furthermore, it’s beneficial to familiarize yourself with your country’s import regulations before placing orders. Prepare a comprehensive checklist of required documents such as import permits, certificates of origin, and packing lists. Establishing a timeline that accounts for potential delays at customs will also help in planning projects more effectively.
Scenario 3: Understanding Customization Options for Prefab Houses
The Problem: Many B2B buyers enter the market with a vision of customized prefab houses, only to find that communication barriers and cultural differences can lead to misunderstandings regarding design specifications. This often results in prototypes that do not align with the buyer’s expectations, leading to frustration and wasted resources.
The Solution: To ensure that customization needs are met accurately, it is crucial to engage in detailed discussions with manufacturers at the outset. Utilize visual aids such as 3D models or CAD drawings to convey your design specifications clearly. Additionally, establish a feedback loop where both parties can review and refine designs throughout the development process. Consider employing bilingual staff or hiring interpreters during negotiations to bridge any communication gaps. Finally, stipulate clear terms in contracts regarding changes and approvals to avoid potential disputes later in the project.
Strategic Material Selection Guide for prefab house china
When selecting materials for prefab houses from China, international B2B buyers must consider various factors including performance, durability, cost, and compliance with regional standards. Below, we analyze four common materials used in prefab construction, focusing on their properties, advantages and disadvantages, and implications for buyers from Africa, South America, the Middle East, and Europe.
What Are the Key Properties of Steel in Prefab House Construction?
Steel is a prevalent choice for prefab houses due to its high strength-to-weight ratio, making it suitable for various structural applications. Key properties include:
- Temperature/Pressure Rating: Steel can withstand high temperatures and pressures, making it ideal for regions with extreme weather conditions.
- Corrosion Resistance: Galvanized or coated steel offers enhanced resistance to corrosion, prolonging the lifespan of the structure.
Pros: Steel is durable, recyclable, and allows for rapid construction. It is also fire-resistant and can be prefabricated off-site for quick assembly.
Cons: The initial cost can be high, and it may require additional insulation to meet energy efficiency standards, particularly in colder climates.
Impact on Application: Steel is compatible with various media and is particularly effective in seismic zones due to its ductility.
Considerations for International Buyers: Buyers must ensure compliance with local building codes and standards such as ASTM in the U.S. or EN standards in Europe. In regions like Saudi Arabia, consideration for corrosion resistance in coastal areas is crucial.
How Does Concrete Perform as a Material for Prefab Houses?
Concrete is another widely used material in prefab construction, known for its compressive strength and durability.
- Temperature/Pressure Rating: Concrete can withstand significant pressure and is effective in thermal mass applications, helping to regulate indoor temperatures.
- Corrosion Resistance: While inherently durable, concrete can be susceptible to cracking and requires proper curing and reinforcement.
Pros: Concrete is fire-resistant, low-maintenance, and offers excellent sound insulation. It is also readily available and cost-effective in many regions.
Cons: The weight of concrete can complicate transportation and assembly, and it requires a longer curing time compared to other materials.
Impact on Application: Concrete is ideal for load-bearing walls and foundations, particularly in areas with high wind or seismic activity.
Considerations for International Buyers: Compliance with local standards such as DIN in Germany or JIS in Japan is essential. Buyers in South America may find concrete to be a cost-effective option due to local availability.
What Are the Benefits of Using Wood in Prefab House Construction?
Wood is a traditional material that is gaining popularity in modern prefab construction due to its aesthetic appeal and sustainability.
- Temperature/Pressure Rating: Wood has a lower thermal conductivity, providing good insulation properties. However, it is less effective under high pressure compared to steel or concrete.
- Corrosion Resistance: Treated wood can resist moisture and pests, but untreated wood is vulnerable to rot and insect damage.
Pros: Wood is lightweight, easy to work with, and offers excellent thermal insulation. It is also a renewable resource, appealing to environmentally conscious buyers.
Cons: Wood can be more susceptible to fire and requires regular maintenance to ensure longevity.
Impact on Application: Wood is well-suited for residential applications and can be used in aesthetic features such as beams and cladding.
Considerations for International Buyers: Buyers should be aware of local regulations regarding fire safety and sustainability certifications. In Europe, for instance, adherence to the EU Timber Regulation is crucial.
What Role Does Composite Material Play in Prefab Houses?
Composite materials, often a blend of wood fibers and plastics, are becoming increasingly popular in prefab construction.
- Temperature/Pressure Rating: Composites can withstand a range of temperatures and pressures, making them versatile for various applications.
- Corrosion Resistance: They are generally resistant to moisture, rot, and pests, making them suitable for humid climates.
Pros: Composites are low-maintenance, durable, and can be designed to mimic the appearance of wood without the drawbacks.
Cons: The initial cost can be higher than traditional materials, and the long-term environmental impact of plastics is a concern.
Impact on Application: Composites are ideal for decking, siding, and other exterior applications where moisture resistance is critical.
Considerations for International Buyers: Compliance with environmental regulations is essential, particularly in regions with strict sustainability standards. Buyers in the Middle East should consider the heat resistance of composites in their selections.
Summary Table of Material Selection for Prefab Houses
Material | Typical Use Case for prefab house china | Key Advantage | Key Disadvantage/Limitation | Relative Cost (Low/Med/High) |
---|---|---|---|---|
Steel | Structural framework | High strength and durability | High initial cost | High |
Concrete | Foundations and load-bearing walls | Fire-resistant and low-maintenance | Heavy and requires curing | Medium |
Wood | Residential interiors and exteriors | Aesthetic appeal and sustainability | Susceptible to fire and pests | Medium |
Composite | Decking and siding | Moisture-resistant and low-maintenance | Higher initial cost and environmental concerns | High |
This strategic material selection guide provides international B2B buyers with essential insights to make informed decisions when sourcing prefab houses from China. By understanding the properties, advantages, and limitations of each material, buyers can align their choices with regional requirements and standards.
In-depth Look: Manufacturing Processes and Quality Assurance for prefab house china
What Are the Main Stages of Manufacturing Prefab Houses in China?
Manufacturing prefab houses in China involves a series of well-defined stages, each critical to ensuring the final product meets international quality standards. Understanding these stages will help international B2B buyers make informed decisions when sourcing prefab houses.
-
Material Preparation
The first stage involves selecting and preparing the raw materials. Common materials include steel, concrete, wood, and insulation. Quality control begins here, with suppliers typically adhering to international standards for material properties (e.g., ASTM, ISO). Buyers should verify the material specifications through certifications and supplier documentation. -
Forming
In this stage, raw materials are shaped into components through various techniques such as cutting, welding, and molding. Advanced machinery like CNC machines and laser cutters enhance precision and efficiency. Buyers should inquire about the technology used and whether the facility employs skilled labor to ensure quality output. -
Assembly
Once components are formed, they are assembled into modules. This process can occur in a factory setting or on-site, depending on project requirements. The assembly line often follows lean manufacturing principles to minimize waste and maximize productivity. B2B buyers should assess the assembly process’s efficiency and the workforce’s expertise. -
Finishing
The final stage involves surface treatment, painting, and installation of fixtures. Quality checks are performed to ensure that finishes meet aesthetic and durability standards. Buyers should ask for samples of finishes and inspect them for consistency and quality.
How Is Quality Assurance Implemented in Prefab House Manufacturing?
Quality assurance (QA) is paramount in the prefab housing sector, particularly for international buyers who must meet specific regulations and standards.
-
International Standards Compliance
Manufacturers typically adhere to international standards such as ISO 9001, which outlines requirements for a quality management system. Additionally, industry-specific standards like CE marking for European markets and API standards for certain materials may apply. Buyers should ensure that suppliers can provide documentation demonstrating compliance with these standards. -
Quality Control Checkpoints
Quality control is integrated at various checkpoints throughout the manufacturing process:
– Incoming Quality Control (IQC): Inspects raw materials upon arrival to ensure they meet specified standards.
– In-Process Quality Control (IPQC): Monitors production processes to catch defects early. This includes regular inspections during forming and assembly stages.
– Final Quality Control (FQC): Conducts comprehensive tests on finished products, including structural integrity assessments and safety checks. -
Testing Methods
Common testing methods include non-destructive testing (NDT) for structural components, thermal performance tests for insulation, and moisture resistance tests. B2B buyers should inquire about the specific tests performed and request test reports.
How Can International B2B Buyers Verify Supplier Quality Control?
Verifying a supplier’s quality control measures is essential for international B2B buyers to ensure product reliability.
-
Supplier Audits
Conducting on-site audits allows buyers to evaluate the manufacturing processes, equipment, and workforce. During an audit, buyers can review quality control documentation, inspect the production line, and assess compliance with international standards. -
Quality Reports and Certifications
Buyers should request quality reports that detail inspection results and certifications from recognized bodies. This documentation provides insight into the supplier’s commitment to quality and adherence to standards. -
Third-Party Inspections
Engaging third-party inspection services can provide an unbiased assessment of the manufacturing process and product quality. These services can perform random inspections at various stages of production, offering an additional layer of assurance.
What Are the Nuances of Quality Control and Certification for B2B Buyers from Different Regions?
Understanding regional nuances in quality control and certification can help buyers navigate the complexities of international procurement.
-
Africa and South America
Buyers from these regions should be aware of local regulations and standards that may differ from international norms. Establishing clear communication with suppliers about compliance with both local and international standards is crucial. -
Middle East
The Middle Eastern market often requires compliance with specific building codes and standards, such as the Gulf Cooperation Council (GCC) regulations. Buyers should verify that suppliers are familiar with these requirements and can provide relevant certifications. -
Europe
European buyers must ensure that products meet stringent EU regulations, including CE marking. Suppliers should be able to provide detailed documentation demonstrating compliance with these regulations. Regular updates on changes in standards are also vital for maintaining compliance.
Conclusion
International B2B buyers sourcing prefab houses from China must have a thorough understanding of the manufacturing processes and quality assurance practices in place. By focusing on material preparation, forming, assembly, and finishing, alongside a robust quality control framework, buyers can ensure they receive high-quality products that meet their specific needs. Additionally, verifying supplier practices through audits, reports, and third-party inspections will help mitigate risks and build successful partnerships.
Practical Sourcing Guide: A Step-by-Step Checklist for ‘prefab house china’
In the quest for sourcing prefab houses from China, a structured approach is essential for international B2B buyers. This guide outlines a step-by-step checklist to help you navigate the complexities of procurement effectively.
Step 1: Define Your Technical Specifications
Establishing clear technical specifications is the foundation of any successful procurement process. This includes details like dimensions, materials, design preferences, and compliance with local building codes. By having precise specifications, you can communicate effectively with suppliers and ensure that the final product meets your requirements.
- Consider the climate and environmental factors in your location when defining materials.
- Include any specific features such as energy efficiency or modularity.
Step 2: Conduct Market Research on Suppliers
Before engaging with suppliers, it’s vital to research the market landscape. Identify key players in the prefab house industry in China, looking for those who have experience in international shipping and compliance with foreign standards.
- Use platforms like Alibaba or Global Sources to find suppliers and read reviews.
- Look for suppliers that have successfully exported to your region or country.
Step 3: Evaluate Potential Suppliers
Before committing, it’s crucial to vet suppliers thoroughly. Request company profiles, case studies, and references from buyers in a similar industry or region. Don’t just rely on their website; a deeper investigation can reveal their reliability and product quality.
- Check for certifications such as ISO or CE that validate their manufacturing processes.
- Request samples of materials or products to assess quality firsthand.
Step 4: Negotiate Terms and Pricing
Negotiation is a critical step in the sourcing process. Ensure that you discuss not only the price but also payment terms, lead times, and shipping logistics. A well-negotiated contract can save costs and prevent misunderstandings later.
- Be clear about your budget constraints and payment methods (e.g., letter of credit, advance payment).
- Consider including clauses for penalties in case of delays or quality issues.
Step 5: Verify Compliance with Local Regulations
Understanding and adhering to local regulations is paramount when importing prefab houses. Ensure that the supplier can provide documentation proving compliance with safety and building codes in your region.
- Consult with local authorities or a legal expert to understand import regulations.
- Request documentation from your supplier that demonstrates their adherence to these standards.
Step 6: Plan for Logistics and Shipping
Logistics can be a daunting task when dealing with international shipments. Work with suppliers to determine the best shipping methods, delivery timelines, and costs involved.
- Evaluate whether you will handle shipping logistics or if the supplier will provide this service.
- Consider using freight forwarders to simplify the process and mitigate risks.
Step 7: Establish a Quality Control Process
Finally, implement a quality control process to ensure that the prefab houses meet your specifications upon arrival. This can involve inspections at the factory, during shipping, or upon delivery.
- Define quality benchmarks and establish criteria for acceptance.
- Consider hiring third-party inspection services to provide an unbiased evaluation.
By following this checklist, international B2B buyers from regions such as Africa, South America, the Middle East, and Europe can streamline their procurement process and ensure a successful sourcing experience from China.
Comprehensive Cost and Pricing Analysis for prefab house china Sourcing
When sourcing prefab houses from China, international B2B buyers must navigate a complex cost structure and pricing landscape. Understanding the various cost components and price influencers is essential for making informed purchasing decisions that align with budgetary constraints and project specifications.
What are the Key Cost Components in Prefab House Sourcing?
-
Materials: The choice of materials significantly impacts the overall cost. Common materials include steel, wood, and insulation, each varying in price based on quality and sourcing location. Buyers should assess the cost implications of using sustainable or locally sourced materials, which might offer long-term benefits despite higher upfront costs.
-
Labor: Labor costs in China are generally lower than in many Western countries, but they can vary by region and the complexity of the prefab designs. Skilled labor for assembly and installation may incur additional charges, so it is vital to factor this into the overall budget.
-
Manufacturing Overhead: This includes costs related to factory operations, such as utilities, maintenance, and administrative expenses. Understanding the overhead structure of your chosen supplier can provide insights into their pricing strategies.
-
Tooling: For customized prefab designs, tooling costs can be significant. This refers to the expenses involved in creating molds and other tools specific to the order. Buyers should inquire about these costs upfront, especially for unique specifications.
-
Quality Control (QC): Ensuring product quality is crucial, particularly for international shipments. QC processes can add to the cost but are essential for reducing the risk of defects and ensuring compliance with international standards.
-
Logistics: Shipping costs can vary dramatically based on the destination and the Incoterms agreed upon. It is vital to consider freight charges, insurance, and potential customs duties when calculating logistics expenses.
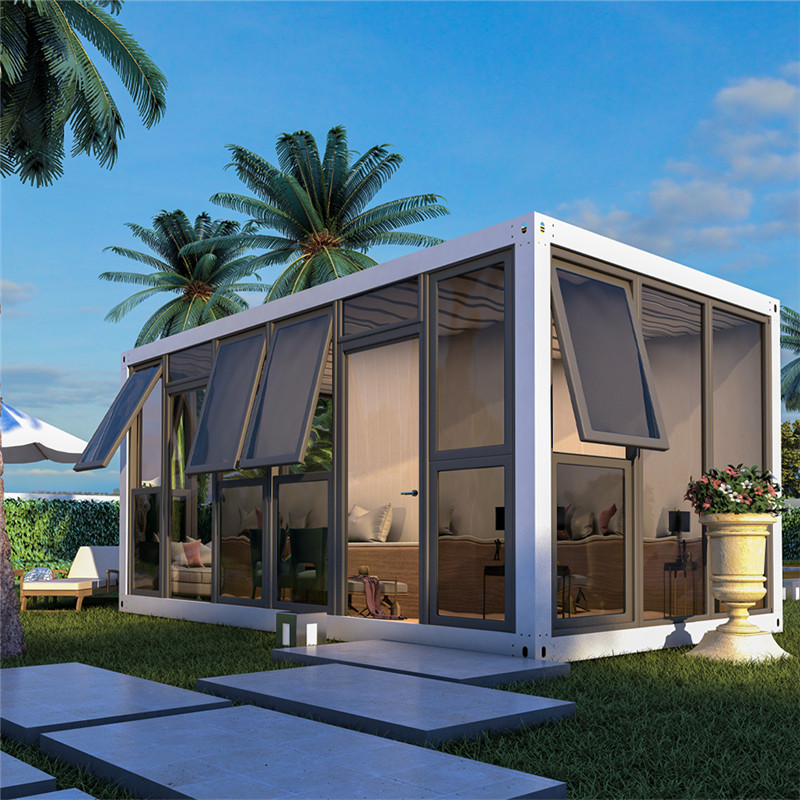
A stock image related to prefab house china.
- Margin: Suppliers will include a profit margin in their pricing. Understanding typical margins in the prefab housing sector can help buyers gauge whether a supplier’s pricing is competitive.
How Do Price Influencers Affect Prefab House Costs?
-
Volume and Minimum Order Quantity (MOQ): Larger orders typically lead to lower per-unit costs. Buyers should negotiate MOQs that align with their project needs while maximizing cost efficiency.
-
Specifications and Customization: Custom designs can significantly increase costs. Buyers should balance the desire for unique features with budgetary constraints, considering whether standardized options could suffice.
-
Materials and Quality Certifications: Higher-quality materials and certifications can elevate costs. However, investing in quality may lead to lower maintenance and operational costs in the long run.
-
Supplier Factors: The supplier’s reputation, reliability, and production capabilities can influence pricing. Researching and comparing multiple suppliers can yield better options.
-
Incoterms: The choice of Incoterms (e.g., FOB, CIF) affects who bears the shipping costs and risks. Selecting the right terms can lead to significant savings.
What Tips Can Help International B2B Buyers Optimize Costs?
-
Negotiate Effectively: Engage in open negotiations with suppliers regarding pricing, payment terms, and delivery schedules. Building a strong relationship can lead to better deals.
-
Consider Total Cost of Ownership (TCO): Evaluate the long-term costs associated with the prefab house, including maintenance, energy efficiency, and potential resale value. This holistic view can guide more sustainable purchasing decisions.
-
Understand Pricing Nuances: Be aware of seasonal fluctuations in pricing and demand, particularly during peak construction seasons. Timing your orders can lead to better pricing.
-
Conduct Thorough Supplier Research: Vet suppliers carefully to ensure they meet quality standards and have a track record of reliability. This due diligence can prevent costly mistakes.
Disclaimer on Pricing
Prices for prefab houses can fluctuate based on market conditions, currency exchange rates, and changes in material costs. It is advisable for buyers to seek multiple quotes and conduct regular market assessments to ensure competitive pricing.
By understanding the cost components and price influencers, as well as employing effective negotiation strategies, international B2B buyers can make well-informed decisions when sourcing prefab houses from China.
Alternatives Analysis: Comparing prefab house china With Other Solutions
When exploring options for housing solutions, international B2B buyers, especially those from Africa, South America, the Middle East, and Europe, must weigh various alternatives against prefab houses from China. These alternatives can offer unique advantages and disadvantages based on specific project requirements, budget constraints, and regional considerations.
Comparison Aspect | Prefab House China | Modular Construction | Traditional Brick and Mortar |
---|---|---|---|
Performance | Quick assembly and energy-efficient | High durability and customization | Strong structural integrity but longer build time |
Cost | Generally lower cost due to mass production | Moderate to high, depending on design | Higher costs due to labor and material expenses |
Ease of Implementation | Fast setup with minimal site work | Requires skilled labor for installation | Lengthy process requiring extensive site preparation |
Maintenance | Low maintenance; durable materials | Moderate maintenance; depends on materials | High maintenance; susceptible to wear and weather |
Best Use Case | Ideal for rapid deployment in urban areas | Suitable for bespoke projects and complex designs | Best for long-term investments and permanent structures |
What Are the Advantages and Disadvantages of Modular Construction Compared to Prefab Houses from China?
Modular construction is a method where buildings are created in sections (modules) in a factory setting before being transported to the site for assembly.
Pros:
– Customization: Modular construction offers significant flexibility in design, allowing buyers to tailor homes to specific needs.
– Quality Control: Factory settings ensure better quality control and less waste.
Cons:
– Cost Variability: Depending on the level of customization, costs can escalate quickly.
– Longer Timeframes: While faster than traditional builds, the modular process can still take longer than prefab houses.
How Does Traditional Brick and Mortar Construction Compare to Prefab House China?
Traditional brick and mortar construction involves building homes using concrete, bricks, and mortar, often resulting in sturdy and long-lasting structures.
Pros:
– Durability: These buildings generally have superior longevity and resistance to natural disasters.
– Aesthetic Appeal: They can offer more traditional and appealing designs that fit well in established neighborhoods.
Cons:
– Higher Costs: The labor-intensive process and material costs often lead to higher overall expenses.
– Time-Consuming: Construction can take much longer, delaying project completion and occupancy.
How Can International B2B Buyers Choose the Right Housing Solution for Their Needs?
When selecting the appropriate housing solution, buyers should consider various factors such as budget, project timelines, and desired levels of customization. Prefab houses from China are particularly advantageous for projects requiring rapid deployment and cost efficiency, making them ideal for urban developments or temporary housing solutions. On the other hand, modular construction may be more suitable for clients looking for customized designs, while traditional brick and mortar should be favored for long-term investments where durability and aesthetic value are paramount.
In conclusion, the choice of housing solution should align with the specific project goals, financial capabilities, and regional requirements, ensuring that international B2B buyers make informed decisions that best serve their business objectives.
Essential Technical Properties and Trade Terminology for prefab house china
When considering the purchase of prefab houses from China, understanding the essential technical properties and trade terminology is crucial for international B2B buyers. This section will delve into key specifications and common jargon that will aid in making informed decisions.
What Are the Key Technical Properties of Prefab Houses from China?
1. Material Grade
The material grade refers to the quality of the materials used in the construction of prefab houses, such as steel, wood, and insulation. Higher-grade materials often result in improved durability, energy efficiency, and resistance to environmental factors. For buyers in regions like Africa and the Middle East, where climate conditions vary significantly, choosing the right material grade can enhance the lifespan and performance of the structure.
2. Tolerance Levels
Tolerance levels indicate the allowable deviation in dimensions during manufacturing. In prefab construction, precise tolerances are essential to ensure that components fit together correctly, maintaining structural integrity. A tight tolerance can reduce the risk of costly on-site adjustments, making it a key consideration for B2B buyers focused on efficiency and cost management.
3. Thermal Insulation Properties
Thermal insulation properties are critical for energy efficiency and comfort within prefab houses. Insulation materials are rated based on their R-value, which measures resistance to heat flow. Higher R-values translate to better energy efficiency, which is particularly important for buyers in Europe and North America, where energy costs can significantly impact operational expenses.
4. Load-Bearing Capacity
Load-bearing capacity defines how much weight a structure can support without compromising safety. This property is vital for buyers looking to install heavy equipment or furniture in their prefab homes. Understanding the load-bearing specifications ensures compliance with local building codes and safety regulations, thus preventing potential liabilities.
5. Fire Resistance Rating
The fire resistance rating of materials used in prefab houses indicates how well they can withstand fire exposure. This is especially relevant for buyers in regions with stringent fire safety regulations, such as parts of Europe and North America. Choosing materials with higher fire resistance ratings can enhance safety and reduce insurance costs.
What Are Common Trade Terms Used in the Prefab Housing Industry?
1. OEM (Original Equipment Manufacturer)
OEM refers to a company that produces parts or equipment that may be marketed by another manufacturer. In the context of prefab housing, buyers may engage with OEMs to procure specific components that meet their unique project requirements, ensuring quality and compatibility.
2. MOQ (Minimum Order Quantity)
MOQ is the smallest quantity of a product that a supplier is willing to sell. Understanding MOQ is essential for B2B buyers to assess whether they can meet the supplier’s requirements without overcommitting resources. For buyers in South America and Africa, negotiating MOQs can lead to cost savings.
3. RFQ (Request for Quotation)
An RFQ is a document that buyers send to suppliers to solicit price quotes for specific products or services. By issuing an RFQ, buyers can compare pricing and services across multiple suppliers, ensuring they make competitive purchasing decisions.
4. Incoterms (International Commercial Terms)
Incoterms are a set of internationally recognized rules that define the responsibilities of buyers and sellers for the delivery of goods under sales contracts. Familiarity with these terms is crucial for international transactions, as they clarify who is responsible for shipping, insurance, and tariffs, reducing the risk of misunderstandings.
5. Lead Time
Lead time refers to the time it takes from placing an order to receiving the product. For international buyers, understanding lead times is vital for project planning and scheduling. Longer lead times may necessitate early ordering to avoid delays in construction timelines.
By grasping these technical properties and industry terms, international B2B buyers can navigate the complexities of purchasing prefab houses from China with greater confidence and strategic insight.
Navigating Market Dynamics and Sourcing Trends in the prefab house china Sector
What Are the Current Trends Driving the Prefab House Market in China?
The prefab house sector in China is experiencing rapid growth, driven by several global factors. First, the increasing demand for affordable housing solutions, particularly in urban areas across Africa, South America, the Middle East, and Europe, is pushing the market. Economic constraints and the need for efficient housing solutions during population booms make prefabricated homes an attractive option. Moreover, the COVID-19 pandemic highlighted the necessity for faster construction methods, making prefab housing a preferred choice for many governments and private developers.
Technological advancements are also reshaping the landscape. Innovations in Building Information Modeling (BIM) and modular construction techniques enable more precise design and planning, reducing waste and time. Additionally, the integration of smart home technology into prefab designs is appealing to tech-savvy buyers, enhancing comfort and efficiency. B2B buyers should be mindful of these trends, as they indicate a shift towards more technologically advanced and sustainable living solutions.
Emerging sourcing trends include a focus on local materials to reduce transportation costs and environmental impact. International buyers are increasingly looking for suppliers who can offer customization options that cater to specific regional needs, ensuring that the prefab structures meet local building codes and cultural preferences. These dynamics present a lucrative opportunity for B2B buyers to engage with Chinese manufacturers who are adapting to these global demands.
How Is Sustainability Influencing Sourcing Decisions in the Prefab House Sector?
Sustainability is becoming a cornerstone of the prefab house market in China, influencing both sourcing decisions and construction practices. The environmental impact of traditional construction methods has led to a growing emphasis on eco-friendly materials and practices. B2B buyers are now prioritizing suppliers who utilize sustainable resources, such as recycled steel, bamboo, and low-impact concrete, which help reduce the carbon footprint of construction projects.
Ethical sourcing is another critical consideration. Buyers are increasingly seeking transparency in their supply chains, ensuring that materials are sourced responsibly without harming local communities or ecosystems. Certifications such as LEED (Leadership in Energy and Environmental Design) and BREEAM (Building Research Establishment Environmental Assessment Method) are becoming essential indicators of a supplier’s commitment to sustainability.
Furthermore, the demand for green certifications is reshaping the market. Companies that can demonstrate compliance with international environmental standards are more likely to attract international buyers. For instance, prefab houses that incorporate energy-efficient designs and renewable energy sources, such as solar panels, not only appeal to environmentally conscious buyers but also help reduce long-term operational costs. This trend is particularly relevant for B2B buyers from regions like Europe and the Middle East, where sustainability is increasingly mandated by regulatory frameworks.
What Is the Historical Context of Prefab Housing in China?
The history of prefab housing in China dates back to the 1950s when the government initiated mass housing projects to address post-war housing shortages. Initially, these homes were constructed using basic materials and methods, aimed at providing rapid shelter solutions. Over the decades, the sector has evolved significantly, with advancements in manufacturing technology leading to improved quality and design flexibility.
The economic reforms of the 1980s spurred a construction boom, prompting the introduction of more sophisticated prefab techniques. Today, China stands as a global leader in prefab housing, with an industry that not only meets domestic needs but also exports to various international markets. This evolution reflects the increasing recognition of prefab housing as a viable solution to urbanization challenges, making it a critical focus for international B2B buyers seeking innovative and efficient building options.
Frequently Asked Questions (FAQs) for B2B Buyers of prefab house china
-
How do I choose the right prefab house supplier in China?
Choosing the right prefab house supplier involves thorough research and vetting. Start by checking the supplier’s credentials, such as certifications (ISO, CE) and experience in the industry. Look for reviews and testimonials from previous clients. Attend trade shows or exhibitions to meet suppliers in person and assess their products. Additionally, ask for references and follow up to ensure the supplier can deliver quality and meet deadlines. Establishing a clear line of communication can also help gauge their responsiveness and professionalism. -
What are the key benefits of sourcing prefab houses from China?
Sourcing prefab houses from China offers several advantages, including competitive pricing due to lower manufacturing costs, a wide variety of designs and materials, and advanced construction technology. Chinese manufacturers often have the capability for bulk production, allowing for faster delivery times. Moreover, many suppliers offer customizable solutions tailored to specific needs, which can be particularly beneficial for international buyers looking to adapt designs to local regulations or preferences. -
What is the minimum order quantity (MOQ) for prefab houses from China?
The minimum order quantity (MOQ) for prefab houses can vary significantly between suppliers. Generally, MOQs can range from a single unit for smaller suppliers to several units for larger manufacturers. It’s essential to clarify the MOQ during initial discussions with potential suppliers. If your project requires fewer units, consider negotiating or exploring suppliers that specialize in smaller orders or are open to custom arrangements. -
What payment terms should I expect when sourcing prefab houses from China?
Payment terms when sourcing prefab houses from China can vary widely. Common terms include a 30% deposit upon order confirmation and the remaining 70% before shipment. Some suppliers may offer more flexible terms, such as letter of credit or payment upon delivery. Always ensure that payment terms are clearly defined in the contract to avoid misunderstandings. It is advisable to use secure payment methods to protect your investment. -
How can I ensure quality assurance for my prefab house order?
To ensure quality assurance for your prefab house order, request samples or visit the manufacturing facility if possible. Establish a clear quality control process, including inspections at various stages of production. Many suppliers offer third-party inspection services, which can be beneficial for international buyers. Additionally, include quality standards in your contract, specifying acceptable tolerances and materials used, to hold suppliers accountable. -
What logistics considerations should I keep in mind when importing prefab houses?
Logistics for importing prefab houses include shipping methods, customs clearance, and transportation from the port to the final destination. Choose between sea freight or air freight based on your budget and urgency. Ensure all necessary documentation, such as bills of lading and import permits, are in order to avoid delays at customs. Collaborating with a logistics partner experienced in international shipping can streamline the process and help navigate potential challenges. -
Can I customize the design of prefab houses sourced from China?
Yes, most Chinese prefab house manufacturers offer customization options to accommodate specific design preferences, size requirements, and material choices. It is advisable to discuss your design ideas during the initial negotiation phase to understand the supplier’s capabilities. Providing detailed specifications, including architectural drawings, can facilitate the customization process. Be mindful of any additional costs that may arise from custom requests.
- What are the common challenges faced when sourcing prefab houses from China?
Common challenges when sourcing prefab houses from China include language barriers, cultural differences, and varying quality standards. Time zone differences can complicate communication, so establishing clear and frequent updates is essential. Additionally, navigating customs regulations in your country can present hurdles. To mitigate these challenges, consider hiring a local agent or consultant who understands both the Chinese market and your local regulations to assist with the sourcing process.
Important Disclaimer & Terms of Use
⚠️ Important Disclaimer
The information provided in this guide, including content regarding manufacturers, technical specifications, and market analysis, is for informational and educational purposes only. It does not constitute professional procurement advice, financial advice, or legal advice.
While we have made every effort to ensure the accuracy and timeliness of the information, we are not responsible for any errors, omissions, or outdated information. Market conditions, company details, and technical standards are subject to change.
B2B buyers must conduct their own independent and thorough due diligence before making any purchasing decisions. This includes contacting suppliers directly, verifying certifications, requesting samples, and seeking professional consultation. The risk of relying on any information in this guide is borne solely by the reader.
Strategic Sourcing Conclusion and Outlook for prefab house china
As the global demand for prefab houses continues to rise, international B2B buyers from regions such as Africa, South America, the Middle East, and Europe must prioritize strategic sourcing to capitalize on this trend. Understanding the landscape of suppliers in China is essential, as it allows buyers to access innovative designs, cost-effective solutions, and efficient production capabilities. The ability to establish strong relationships with reputable manufacturers can lead to improved supply chain resilience and enhanced project delivery timelines.
In conclusion, strategic sourcing in the prefab housing sector not only provides cost advantages but also opens avenues for sustainable building practices that are increasingly sought after in today’s market. Buyers are encouraged to leverage digital platforms and industry networks to identify and engage with potential suppliers, ensuring they make informed decisions that align with their project goals and regional regulations.
Looking ahead, as the prefab housing industry evolves, staying informed about market trends and emerging technologies will be crucial. International B2B buyers should actively seek partnerships that foster innovation and adaptability, paving the way for successful ventures in the global prefab housing arena. Embrace the opportunity—strategically source your next project from China and lead the way in sustainable construction.