Unlock Savings: The Complete Guide to Terrazzo Suppliers (2025)
Introduction: Navigating the Global Market for terrazzo supplier
Navigating the global market for terrazzo suppliers can be a daunting task for international B2B buyers, especially when seeking durable and aesthetically pleasing flooring solutions. With the rise in demand for high-quality terrazzo products across regions such as Africa, South America, the Middle East, and Europe, understanding the diverse options available is crucial. This comprehensive guide addresses key challenges in sourcing terrazzo suppliers, including identifying different types of terrazzo, evaluating their applications in various industries, and vetting suppliers based on quality and reliability.
Buyers will explore a variety of terrazzo types, such as epoxy terrazzo and traditional cement-based options, along with their unique characteristics and ideal usage scenarios. Additionally, this guide delves into critical factors influencing pricing and cost-effectiveness, ensuring that B2B buyers can make informed financial decisions. By highlighting essential supplier vetting criteria, including certifications and production capabilities, this resource empowers international buyers to select suppliers that align with their project requirements and sustainability goals.
Whether you are in the construction, hospitality, or healthcare sectors, this guide equips you with actionable insights to navigate the global terrazzo market confidently. By understanding the nuances of sourcing terrazzo products, you can enhance your purchasing decisions and ultimately contribute to the success of your projects.
Understanding terrazzo supplier Types and Variations
Type Name | Key Distinguishing Features | Primary B2B Applications | Brief Pros & Cons for Buyers |
---|---|---|---|
Traditional Terrazzo | Made from marble chips and cement, offering a classic aesthetic | Commercial spaces, retail, hotels | Pros: Durable, customizable designs. Cons: Heavier, longer installation time. |
Epoxy Terrazzo | Uses a two-part matrix for flexibility in design and color | Hospitals, laboratories, high-traffic areas | Pros: Quick installation, lightweight. Cons: Higher initial cost, requires skilled labor. |
Polymer Terrazzo | Incorporates polymers for enhanced durability and impact resistance | Industrial environments, warehouses | Pros: Highly resistant to chemicals and stains. Cons: Limited design options compared to traditional. |
Precast Terrazzo | Factory-made tiles that ensure uniform quality and finish | Malls, airports, large public spaces | Pros: Easy installation, consistent quality. Cons: Transportation costs, less flexibility in design on-site. |
Terrazzo Tiles | Available in various sizes and finishes, suitable for various applications | Residential, commercial, and outdoor areas | Pros: Versatile, easy to maintain. Cons: May require sealing, susceptible to cracking if not installed properly. |
What Are the Characteristics of Traditional Terrazzo Suppliers?
Traditional terrazzo suppliers focus on producing materials that combine marble chips with cement, resulting in a timeless aesthetic. Ideal for commercial spaces, retail environments, and hotels, this type of terrazzo is known for its durability and ability to be customized in various designs and colors. When purchasing, B2B buyers should consider the weight of traditional terrazzo, as it may require additional structural support and longer installation times, impacting project timelines and costs.
How Does Epoxy Terrazzo Differ from Other Types?
Epoxy terrazzo suppliers utilize a two-part matrix system, allowing for a high degree of flexibility in design and color. This type is particularly suitable for hospitals, laboratories, and areas with high foot traffic due to its quick installation and lightweight nature. However, buyers should be aware of the initial costs, which can be higher than traditional options, and the need for skilled labor for installation to ensure durability and aesthetic quality.
What Are the Benefits of Polymer Terrazzo for Industrial Applications?
Polymer terrazzo suppliers create flooring solutions that incorporate polymers, enhancing durability and impact resistance. This type is particularly beneficial in industrial environments and warehouses where chemical spills and heavy machinery are common. Buyers should consider the chemical resistance and stain-proof qualities of polymer terrazzo; however, they may find that design options are limited compared to traditional terrazzo.
Why Choose Precast Terrazzo for Large Projects?
Precast terrazzo suppliers produce tiles that are factory-made, ensuring consistent quality and finish across large installations. This type is ideal for malls, airports, and large public spaces, where uniformity is crucial. While precast terrazzo offers easy installation and consistent quality, buyers must factor in transportation costs and the potential for reduced flexibility in on-site design modifications.
How Do Terrazzo Tiles Meet Diverse B2B Needs?
Terrazzo tile suppliers offer a versatile product available in various sizes and finishes, catering to residential, commercial, and outdoor applications. Their ease of maintenance and aesthetic appeal make them a popular choice among buyers. However, B2B purchasers should note that while terrazzo tiles are generally durable, they may require sealing and could be susceptible to cracking if not installed correctly, which can affect long-term performance and maintenance costs.
Related Video: Webinar: General Overview on Terrazzo
Key Industrial Applications of terrazzo supplier
Industry/Sector | Specific Application of terrazzo supplier | Value/Benefit for the Business | Key Sourcing Considerations for this Application |
---|---|---|---|
Healthcare Facilities | Flooring in hospitals and clinics | Antimicrobial properties and easy maintenance | Compliance with health regulations and durability standards |
Retail Spaces | Showroom and store flooring | Aesthetic appeal and durability for high foot traffic | Customization options and resistance to wear and tear |
Educational Institutions | Classrooms and common areas | Safe, slip-resistant surfaces that enhance learning | Sustainability certifications and ease of installation |
Food Processing Plants | Flooring in food production areas | Hygiene compliance and resistance to chemicals | Resistance to stains and easy cleaning protocols |
Commercial Spaces | Lobbies and office buildings | Elegant design and low lifecycle costs | Availability of various colors and patterns for branding needs |
How is Terrazzo Used in Healthcare Facilities?
In healthcare settings, terrazzo is often chosen for its superior hygiene and antimicrobial properties, making it ideal for hospitals and clinics. The seamless finish of terrazzo flooring minimizes the risk of bacteria harboring in joints, which is crucial for maintaining a sterile environment. For international buyers, particularly from regions like Africa and the Middle East, it is essential to ensure that the terrazzo supplier complies with local health regulations and standards. Additionally, the flooring’s durability reduces long-term maintenance costs, an important consideration for budget-conscious healthcare providers.
What are the Benefits of Terrazzo in Retail Spaces?
Retail environments benefit significantly from terrazzo flooring due to its aesthetic versatility and durability. High foot traffic areas require materials that can withstand wear while maintaining an attractive appearance. Terrazzo allows for customization in color and design, which can enhance brand identity and customer experience. For buyers in South America and Europe, sourcing from suppliers who offer a range of designs and finishes is critical. This ensures that the chosen terrazzo complements the store’s branding and interior design effectively.
Why Choose Terrazzo for Educational Institutions?
Educational institutions, including schools and universities, often utilize terrazzo for its safety and slip-resistant properties. Classrooms and common areas require flooring that can handle heavy use while providing a safe environment for students. Terrazzo is not only durable but also contributes to a conducive learning atmosphere with its aesthetic appeal. Buyers from Europe, particularly in Spain, should consider suppliers that offer sustainable options, as many educational institutions are increasingly focused on environmentally friendly materials.
How Does Terrazzo Support Hygiene in Food Processing Plants?
In food processing plants, terrazzo flooring is highly valued for its hygiene compliance and resistance to chemicals. The seamless nature of terrazzo prevents food particles and bacteria from becoming trapped, facilitating easier cleaning and sanitation. International buyers, especially from regions with strict food safety regulations, must ensure that the terrazzo supplier provides products that meet local hygiene standards. Additionally, the flooring’s resistance to stains and spills is crucial for maintaining a clean production environment.
What Makes Terrazzo Ideal for Commercial Spaces?
For commercial spaces such as lobbies and office buildings, terrazzo flooring offers an elegant design that enhances the professional atmosphere. Its low lifecycle costs and maintenance requirements make it an economical choice for businesses. Buyers from Africa and Europe should look for suppliers who can provide a variety of colors and patterns, as this flexibility allows for branding opportunities and creative design solutions. Ensuring that the terrazzo can withstand high traffic without compromising its appearance is also vital for commercial applications.
Related Video: A close-up look at our terrazzo tile manufacturing process
3 Common User Pain Points for ‘terrazzo supplier’ & Their Solutions
Scenario 1: Sourcing Quality Terrazzo Products at Competitive Prices
The Problem:
B2B buyers often face the challenge of sourcing high-quality terrazzo products that meet their project specifications while remaining within budget. With numerous suppliers in the market, differentiating between quality offerings and subpar materials can be daunting. Buyers from regions such as Africa and South America may encounter additional hurdles, such as shipping delays, unexpected tariffs, and fluctuating currency values that can impact overall project costs.
The Solution:
To address these challenges, buyers should conduct thorough market research before selecting a terrazzo supplier. Start by identifying suppliers who specialize in the specific type of terrazzo you need, whether it’s epoxy-based or cementitious terrazzo. Utilize online platforms and industry forums to read reviews and gather insights from other buyers. It is also beneficial to request samples before making a bulk order to assess the quality firsthand.
Establishing a direct line of communication with potential suppliers can also mitigate risks. Discuss your project requirements in detail, including design preferences, application environments, and budget constraints. This will help suppliers understand your needs and provide tailored solutions. Additionally, inquire about their production capabilities, lead times, and logistics support to ensure a smooth procurement process.
Scenario 2: Managing Installation Challenges of Terrazzo Flooring
The Problem:
The installation of terrazzo flooring can be complex and requires skilled labor. Buyers often struggle with finding qualified installers who are familiar with the specific techniques needed for terrazzo application, especially in regions with less experience in this material. Poor installation can lead to long-term issues such as cracking, uneven surfaces, or inadequate bonding, resulting in costly repairs.
The Solution:
To overcome installation challenges, buyers should prioritize collaboration with suppliers who offer comprehensive support services. Choose a supplier that not only sells terrazzo products but also provides installation services or can recommend certified installers. Ask for references or case studies of previous projects to verify the installers’ expertise.
Furthermore, ensure that the supplier provides clear installation guidelines and training for local teams if you choose to manage the installation in-house. This could include detailed specifications regarding substrate preparation, mixing ratios, and curing times. Investing in proper training and support will enhance the likelihood of achieving a high-quality finish and reduce the risk of future maintenance issues.
Scenario 3: Addressing Long-Term Maintenance Concerns for Terrazzo Surfaces
The Problem:
Long-term maintenance of terrazzo surfaces can be a significant concern for B2B buyers, particularly in high-traffic areas or environments that require stringent hygiene standards, such as healthcare facilities. Buyers are often unsure about the best maintenance practices that will prolong the life of their terrazzo installations without damaging the surface.
The Solution:
To ensure the longevity of terrazzo flooring, buyers should engage with suppliers who offer clear maintenance recommendations and products specifically designed for terrazzo care. This includes regular cleaning schedules using neutral pH cleaners that do not contain acidic or abrasive substances, which can degrade the surface over time.
Additionally, consider implementing a sealing regimen as recommended by the supplier. A quality sealant can protect the terrazzo from staining and wear while enhancing its aesthetic appeal. It’s also advisable to schedule periodic professional maintenance to address any wear and tear that may accumulate over time.
To aid in maintaining the surfaces, suppliers may provide training or resources that outline best practices for cleaning and care. By establishing a solid maintenance plan, buyers can ensure that their terrazzo surfaces remain attractive and functional for years to come, ultimately protecting their investment.
Strategic Material Selection Guide for terrazzo supplier
What Are the Key Materials Used in Terrazzo Production?
When selecting materials for terrazzo, international B2B buyers must consider various options that influence performance, aesthetics, and compliance with local standards. Here, we analyze four common materials used in terrazzo production: marble chips, glass chips, epoxy resins, and cement.
How Do Marble Chips Affect Terrazzo Quality?
Key Properties: Marble chips are known for their aesthetic appeal and durability. They offer a wide range of colors and textures, contributing to the visual quality of the final product. However, they are sensitive to acidic cleaning agents, which can cause etching.
Pros & Cons: The primary advantage of marble chips is their natural beauty and the luxurious finish they provide. They are also relatively durable under normal conditions. However, they can be more expensive than other aggregates and may require more complex installation processes.
Impact on Application: Marble chips are suitable for high-end residential and commercial spaces where aesthetics are a priority. They are not recommended for environments that require heavy-duty flooring due to their susceptibility to scratching and staining.
Considerations for International Buyers: Buyers from regions like Africa and the Middle East should consider the availability of local marble sources to reduce costs. Compliance with standards such as ASTM C897 for aggregates is crucial for ensuring product quality.
What Role Do Glass Chips Play in Terrazzo?
Key Properties: Glass chips are manufactured from recycled glass, offering excellent color variety and a unique shine. They are highly resistant to staining and scratching, making them suitable for high-traffic areas.
Pros & Cons: The key advantage of glass chips is their sustainability and aesthetic appeal. They can also be easier to maintain compared to marble. However, their brittleness can lead to cracking under extreme pressure, and they may not be suitable for all applications.
Impact on Application: Glass chips are ideal for modern commercial spaces, such as retail stores and restaurants, where visual impact is essential. They are compatible with various media, including epoxy and cement-based systems.
Considerations for International Buyers: Buyers should check local regulations regarding the use of recycled materials. Compliance with environmental standards can enhance brand reputation in markets like Europe, where sustainability is valued.
How Do Epoxy Resins Enhance Terrazzo Performance?
Key Properties: Epoxy resins provide a strong bond and excellent chemical resistance. They are available in various formulations, allowing for flexibility in design and application.
Pros & Cons: The main advantage of epoxy is its durability and resistance to chemicals, making it suitable for industrial applications. However, the initial cost can be higher, and installation requires skilled labor.
Impact on Application: Epoxy terrazzo is ideal for environments such as hospitals and laboratories, where hygiene and durability are paramount. It can withstand heavy loads and is resistant to moisture.
Considerations for International Buyers: Buyers must ensure that the epoxy used complies with local standards, such as DIN EN 13813 in Europe. Understanding the curing time and environmental conditions for installation is also critical.
What Is the Importance of Cement in Terrazzo?
Key Properties: Cement serves as the primary binding agent in traditional terrazzo. It provides structural integrity and can be formulated to enhance strength and flexibility.
Pros & Cons: The advantage of cement-based terrazzo is its cost-effectiveness and ease of sourcing. However, it may require more maintenance and is less resistant to staining compared to epoxy systems.
Impact on Application: Cement terrazzo is suitable for general commercial applications but may not be ideal for high-moisture environments. It is often used in educational institutions and public buildings.
Considerations for International Buyers: Buyers should be aware of local standards like ASTM C150 for cement to ensure quality. Understanding the climatic conditions in regions like South America is essential for proper installation and longevity.
Summary Table of Terrazzo Materials
Material | Typical Use Case for terrazzo supplier | Key Advantage | Key Disadvantage/Limitation | Relative Cost (Low/Med/High) |
---|---|---|---|---|
Marble Chips | High-end residential/commercial spaces | Natural beauty and luxurious finish | Higher cost and complex installation | High |
Glass Chips | Modern commercial spaces | Sustainability and aesthetic appeal | Brittleness may lead to cracking | Medium |
Epoxy Resins | Hospitals and laboratories | Durability and chemical resistance | Higher initial cost and skilled labor needed | High |
Cement | Educational institutions and public buildings | Cost-effective and easy to source | Requires more maintenance and less stain resistance | Low |
This analysis provides actionable insights for international B2B buyers looking to source terrazzo materials, emphasizing the importance of material properties, application suitability, and compliance with local standards.
In-depth Look: Manufacturing Processes and Quality Assurance for terrazzo supplier
What are the Key Stages in the Manufacturing Process of Terrazzo?
The manufacturing process of terrazzo involves several crucial stages that ensure the final product’s quality and durability. Understanding these stages can help B2B buyers assess potential suppliers effectively.
1. Material Preparation
The first step in terrazzo manufacturing is the preparation of raw materials. This typically includes:
- Selection of Aggregates: High-quality aggregates such as marble chips, glass, or synthetic materials are selected based on the desired aesthetic and performance characteristics.
- Mixing with Bindings: The aggregates are mixed with a binding agent, usually cement or epoxy resin. The choice of binder affects the strength, durability, and appearance of the final product.
- Coloring Agents: If colored terrazzo is required, pigments are added during this phase to ensure uniformity.
2. Forming and Casting
Once the materials are prepared, they are cast into molds:
- Mold Design: Molds are designed to create specific shapes and sizes of terrazzo tiles or slabs. Custom molds can be created for unique projects.
- Pouring: The prepared mixture is poured into the molds, ensuring that it fills all voids and achieves the desired thickness.
- Vibration: To eliminate air bubbles and ensure a compact structure, the molds may be vibrated.
3. Curing
Curing is a critical process that allows the terrazzo to gain strength:
- Initial Curing: After pouring, the terrazzo is allowed to cure under controlled conditions, which can take several days. This is essential for hydration and strength development.
- Moisture Control: Maintaining optimal moisture levels during curing is vital to prevent cracking and ensure a strong bond between aggregates and the binder.
4. Finishing Processes
Finishing processes enhance the aesthetic appeal and functionality of terrazzo:
- Grinding and Polishing: Once cured, the surface is ground down to achieve a smooth finish. This process can be performed using various grits to achieve the desired gloss level.
- Sealing: A sealant may be applied to protect the surface from stains and enhance its durability.
- Quality Inspection: The finished products undergo thorough inspections to ensure they meet quality standards.
How is Quality Assurance Ensured in Terrazzo Manufacturing?
Quality assurance (QA) is a fundamental aspect of terrazzo production, ensuring that products meet international standards and customer expectations.
Relevant International Standards for Quality Control
B2B buyers should look for suppliers adhering to international quality standards, such as:
- ISO 9001: This standard specifies requirements for a quality management system (QMS) and is crucial for ensuring consistent product quality.
- CE Marking: Required in Europe, CE marking indicates that the product complies with EU safety, health, and environmental protection standards.
- API Standards: For specific applications, such as in chemical plants or medical facilities, API standards may apply to ensure safety and performance.
What are the Key Quality Control Checkpoints?
Quality control in terrazzo manufacturing typically includes several checkpoints throughout the production process:
- Incoming Quality Control (IQC): Raw materials are inspected upon arrival to ensure they meet specified standards. This includes checking aggregates for size, shape, and purity.
- In-Process Quality Control (IPQC): During production, random samples are taken to ensure that mixing, casting, and curing processes are performed correctly. Parameters such as moisture content and mix consistency are monitored.
- Final Quality Control (FQC): Finished products undergo a final inspection to check for defects, surface finish, and adherence to specifications. This may include dimensional checks and visual inspections.
What Testing Methods are Commonly Used in Terrazzo Quality Assurance?
Several testing methods are employed to evaluate the quality of terrazzo products:
- Compression Strength Tests: These tests measure the material’s ability to withstand loads, ensuring that it meets the required strength standards.
- Water Absorption Tests: This test assesses the porosity of the terrazzo, which affects its durability and stain resistance.
- Chemical Resistance Tests: For applications in sensitive environments, suppliers may perform tests to evaluate the material’s resistance to chemicals and staining agents.
How Can B2B Buyers Verify Supplier Quality Control?
Verification of a supplier’s quality control processes is essential for B2B buyers, especially when sourcing from international markets.
1. Conducting Supplier Audits
Regular audits of suppliers’ manufacturing facilities can provide insights into their quality control systems. Buyers should look for:
- Documentation of Processes: Ensure that suppliers maintain detailed records of their quality control processes and results.
- Compliance with Standards: Check if the supplier’s processes comply with relevant international and industry-specific standards.
2. Requesting Quality Control Reports
Suppliers should be able to provide documentation on their quality control measures, including:
- Test Results: Documentation of strength, durability, and other relevant tests performed on products.
- Certification: Evidence of compliance with quality standards, such as ISO certification.
3. Engaging Third-Party Inspectors
For added assurance, B2B buyers can engage third-party inspection services to evaluate the quality of products before shipment. This can help identify any potential issues that may arise during transportation or installation.
What Nuances Should International B2B Buyers Consider Regarding Quality Control?
When sourcing terrazzo products internationally, particularly from regions like Africa, South America, the Middle East, and Europe, buyers should consider several factors:
- Cultural and Regulatory Differences: Different regions may have varying standards for quality and safety. Understanding local regulations and certifications can help avoid compliance issues.
- Logistical Considerations: The transportation of terrazzo products requires careful handling to prevent damage. Buyers should ensure that suppliers are equipped to manage logistics effectively.
- After-Sales Support: Quality assurance does not end with delivery. Buyers should inquire about the supplier’s after-sales support, including warranties and maintenance recommendations.
By understanding the manufacturing processes and quality assurance protocols of terrazzo suppliers, international B2B buyers can make informed decisions, ensuring they source high-quality materials that meet their project requirements.
Practical Sourcing Guide: A Step-by-Step Checklist for ‘terrazzo supplier’
In the ever-evolving world of B2B procurement, selecting the right terrazzo supplier is crucial for achieving high-quality flooring solutions. This practical sourcing guide provides international buyers with a structured checklist to ensure a smooth and effective procurement process.
Step 1: Define Your Technical Specifications
Clearly outline your requirements for terrazzo products. This includes the types of terrazzo (e.g., epoxy or cement-based), colors, designs, and any specific performance characteristics needed, such as slip resistance or durability. Having a well-defined specification helps streamline the selection process and ensures that suppliers understand your needs.
Step 2: Research Potential Suppliers
Conduct thorough market research to identify potential terrazzo suppliers. Utilize online resources, industry directories, and trade shows to compile a list of reputable companies. Pay attention to suppliers with experience in your target regions, such as Africa, South America, the Middle East, or Europe, as they may better understand local regulations and market preferences.
Step 3: Evaluate Supplier Certifications
Verify that potential suppliers hold relevant certifications. Look for quality management certifications (e.g., ISO 9001) and compliance with local building codes. Certifications ensure that the supplier adheres to industry standards, which is essential for maintaining product quality and safety.
- Check for eco-friendly certifications if sustainability is a priority for your project.
Step 4: Request Samples and Product Specifications
Always ask for product samples before making a decision. This allows you to assess the quality, texture, and finish of the terrazzo. Additionally, request detailed product specifications, including information on material composition, installation guidelines, and maintenance requirements.
Step 5: Assess Supplier Experience and Reputation
Investigate the supplier’s history and reputation within the industry. Look for testimonials, case studies, and reviews from previous clients, especially those in similar sectors or regions. A supplier with a proven track record is more likely to deliver on promises and provide reliable support throughout the project.
Step 6: Inquire About Lead Times and Delivery Options
Discuss lead times and delivery logistics with potential suppliers. Understanding how long it will take for products to be manufactured and delivered is critical for project planning. Ensure that the supplier can meet your deadlines and has reliable logistics in place, especially if you are sourcing internationally.
- Ask about their ability to handle large orders and any potential delays in peak seasons.
Step 7: Negotiate Terms and Conditions
Engage in discussions about pricing, payment terms, and warranty policies. Transparent negotiation can help you secure favorable terms that align with your budget and project needs. Ensure that you understand the warranty coverage for the products and any after-sales support that the supplier offers.
By following these steps, B2B buyers can navigate the complexities of sourcing terrazzo suppliers with confidence, ultimately leading to successful procurement outcomes that meet their specific flooring needs.
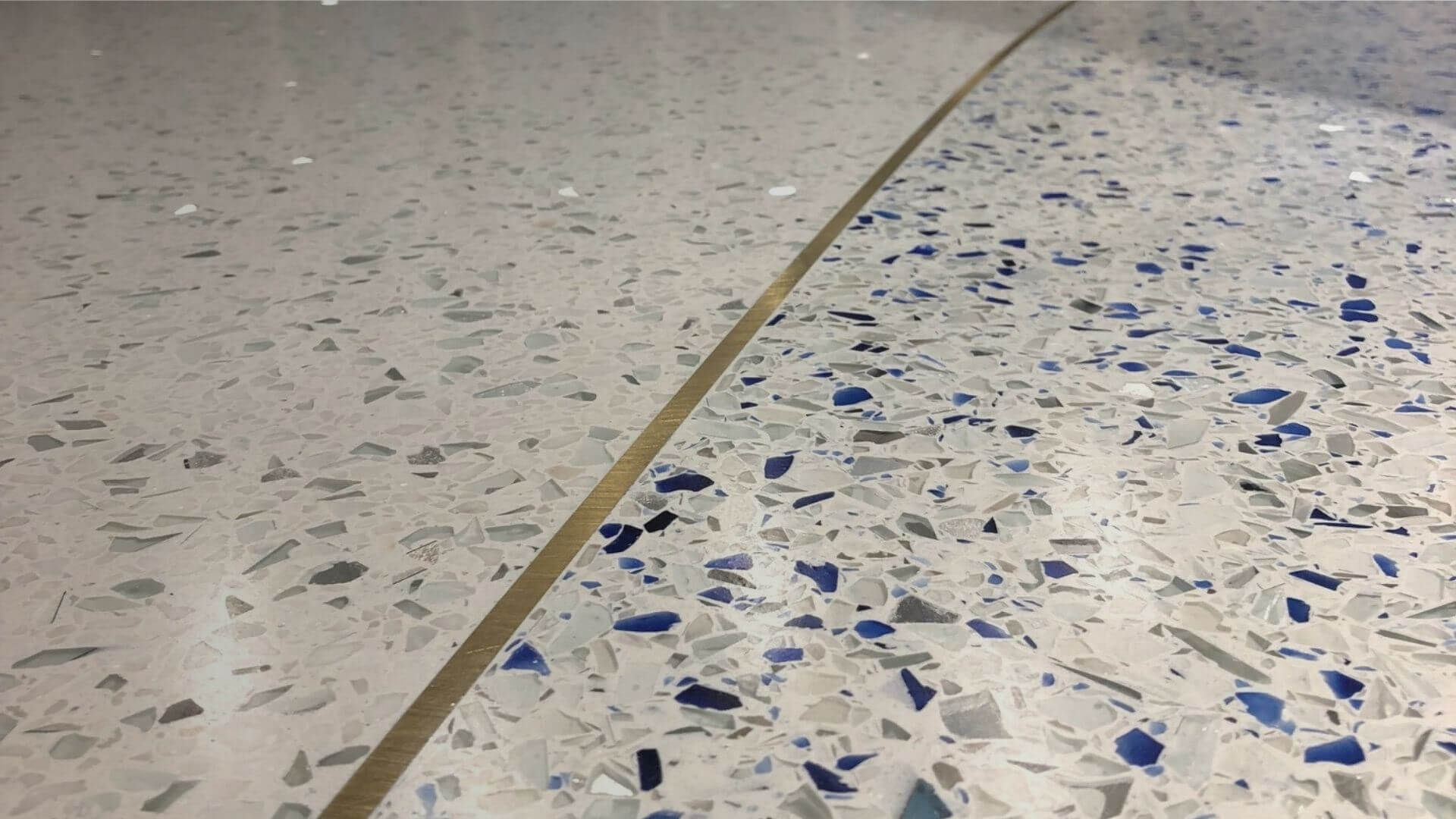
A stock image related to terrazzo supplier.
Comprehensive Cost and Pricing Analysis for terrazzo supplier Sourcing
When considering sourcing terrazzo products for your business, understanding the comprehensive cost structure and pricing dynamics is crucial. This analysis will help international B2B buyers, especially from Africa, South America, the Middle East, and Europe, navigate the complexities of terrazzo supplier sourcing effectively.
What Are the Key Cost Components in Terrazzo Supplier Pricing?
The cost structure of terrazzo products can be broken down into several critical components:
-
Materials: The primary cost driver for terrazzo is the raw materials, which include marble chips, cement, and pigments. The quality and source of these materials significantly influence the price. High-quality aggregates and specialized pigments will elevate costs but can also enhance the product’s aesthetic and durability.
-
Labor: Skilled labor is essential for both the manufacturing and installation of terrazzo. Labor costs can vary widely based on the region, with skilled artisans in Europe potentially commanding higher wages than those in other regions.
-
Manufacturing Overhead: This includes costs related to machinery, utilities, and factory maintenance. Suppliers with advanced production lines, such as those employing epoxy terrazzo systems, may have higher overhead but can offer superior products.
-
Tooling: The initial setup for producing terrazzo tiles and slabs requires significant investment in tooling. This cost is often amortized over the production volume, making it a crucial factor for suppliers.
-
Quality Control (QC): Implementing strict quality control measures ensures that the final product meets required standards. This can involve additional costs but is essential for maintaining customer satisfaction and compliance with international certifications.
-
Logistics: Transportation costs are influenced by the distance from the manufacturing site to the buyer, shipping methods, and tariffs. International buyers should account for these costs when evaluating supplier pricing.
-
Margin: Suppliers will typically include a profit margin, which can vary based on market competition, brand reputation, and the uniqueness of their products.
How Do Price Influencers Affect Terrazzo Sourcing?
Several factors can influence the final pricing of terrazzo products:
-
Volume/MOQ (Minimum Order Quantity): Larger orders often lead to volume discounts. Suppliers may offer more favorable pricing for bulk purchases, making it essential for buyers to consider their needs carefully.
-
Specifications and Customization: Custom designs or specific color requirements can increase costs due to additional labor and material needs. Buyers should clearly communicate their specifications to avoid unexpected costs.
-
Quality and Certifications: Products that meet international standards or come with certifications (e.g., eco-friendly materials) may command higher prices. However, these certifications often add value, especially in markets with stringent building codes.
-
Supplier Factors: The reputation and reliability of a supplier can impact pricing. Established suppliers may charge a premium for their proven quality and service.
-
Incoterms: Understanding the agreed terms of shipping can significantly affect pricing. Terms like FOB (Free on Board) or CIF (Cost, Insurance, and Freight) will determine which party bears the shipping costs and risks.
What Are the Best Practices for Negotiating Terrazzo Prices?
When negotiating with terrazzo suppliers, consider the following tips:
-
Research and Benchmark: Gather data on typical market prices for similar products to have a baseline for negotiations.
-
Discuss Total Cost of Ownership (TCO): Focus on the long-term value rather than just the initial price. Highlight aspects like durability, maintenance costs, and lifecycle benefits.
-
Leverage Relationships: Building strong relationships with suppliers can lead to better pricing and terms. Frequent communication and timely payments can foster goodwill.
-
Be Clear on Expectations: Specify your requirements upfront to avoid misunderstandings that could lead to cost overruns or quality issues.
Conclusion
Understanding the intricate cost structure and pricing dynamics of terrazzo sourcing is essential for international B2B buyers. By considering the various cost components and influencers, as well as employing effective negotiation strategies, buyers can make informed decisions that align with their business needs.
Disclaimer: Prices and costs mentioned herein are indicative and may vary based on supplier, location, and market conditions. Always consult with suppliers for the most accurate pricing information.
Alternatives Analysis: Comparing terrazzo supplier With Other Solutions
Introduction: Understanding Alternative Flooring Solutions
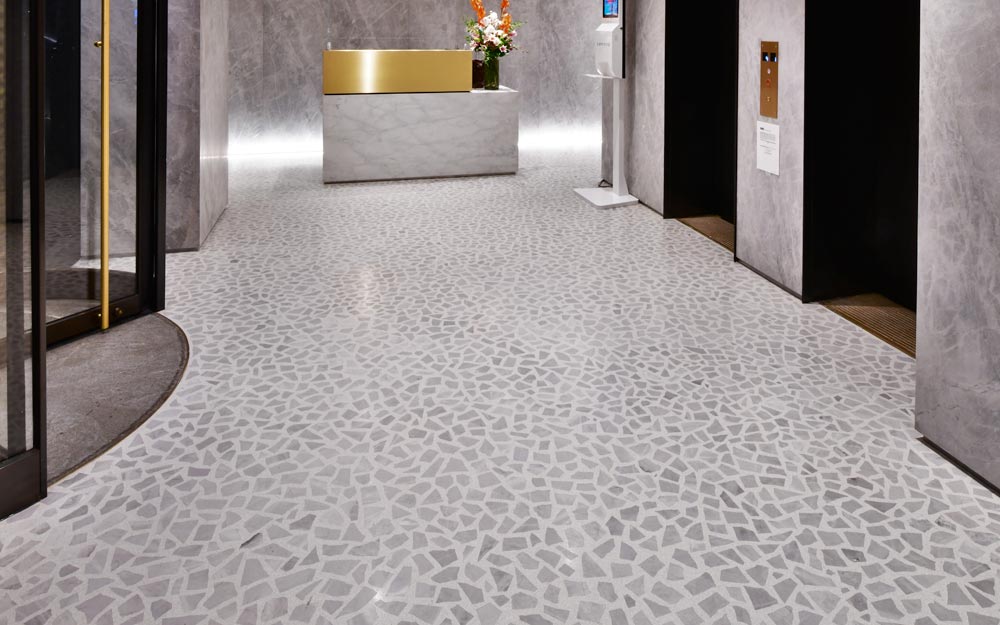
A stock image related to terrazzo supplier.
When considering flooring solutions for commercial or industrial spaces, it’s essential for B2B buyers to evaluate various options to ensure they select the best fit for their needs. Terrazzo flooring has gained popularity due to its aesthetic appeal and durability, but other alternatives exist that may cater to specific requirements or budgets. This analysis compares terrazzo suppliers with two viable alternatives: epoxy flooring and polished concrete.
Comparison Table of Flooring Solutions
Comparison Aspect | Terrazzo Supplier | Epoxy Flooring | Polished Concrete |
---|---|---|---|
Performance | High durability, aesthetic variety | Chemical resistance, customizable | Very durable, low maintenance |
Cost | Moderate to high initial investment | Moderate cost with lower maintenance | Generally lower upfront cost |
Ease of Implementation | Requires skilled installation | Relatively easy to install | Simple installation, can be DIY |
Maintenance | Low maintenance, easy cleaning | Low maintenance, requires occasional re-coating | Very low maintenance, easy to clean |
Best Use Case | High-traffic commercial spaces | Industrial settings, laboratories | Warehouses, retail spaces |
Detailed Breakdown of Alternatives
What are the advantages and disadvantages of epoxy flooring?
Epoxy Flooring is a versatile and durable flooring solution made from a mixture of resin and hardener. It is particularly advantageous in environments exposed to chemicals and heavy foot traffic, such as manufacturing facilities and laboratories. One of the key benefits of epoxy is its seamless application, which minimizes the risk of water penetration and allows for easier cleaning. However, while the initial cost is moderate, potential re-coating after several years can add to long-term expenses. Additionally, the aesthetic options, while customizable, may not offer the same design flexibility as terrazzo.
How does polished concrete compare to terrazzo flooring?
Polished Concrete is another strong contender for industrial and commercial flooring. It involves grinding down the surface of the concrete slab to a desired sheen. The main advantages include its affordability and the fact that it requires minimal maintenance. Polished concrete is resistant to stains and can be treated to enhance its appearance. However, it may lack the artistic variety and color options that terrazzo flooring offers, which can be a deciding factor for businesses looking to create a specific ambiance or design aesthetic. Moreover, polished concrete may not provide the same level of comfort underfoot as terrazzo.
Conclusion: How to Choose the Right Flooring Solution for Your Needs
Selecting the right flooring solution hinges on understanding the specific requirements of your business environment. For B2B buyers from Africa, South America, the Middle East, and Europe, factors such as budget, aesthetic preferences, maintenance capabilities, and the intended use of the space should guide the decision-making process. Terrazzo offers unparalleled beauty and durability, making it ideal for high-traffic areas, whereas epoxy flooring provides robust chemical resistance suitable for industrial applications. Polished concrete stands out for its cost-effectiveness and low maintenance, making it a practical choice for warehouses and retail spaces. Ultimately, assessing these alternatives against your unique business needs will lead to the best flooring investment.
Essential Technical Properties and Trade Terminology for terrazzo supplier
What Are the Essential Technical Properties of Terrazzo?
Understanding the technical specifications of terrazzo is crucial for B2B buyers. These properties influence the performance, durability, and aesthetic appeal of the flooring material. Here are some key specifications to consider:
-
Material Grade
Material grade refers to the quality of the aggregates used in terrazzo, which can include marble chips, glass, or quartz. Higher-grade materials not only enhance the visual appeal but also improve durability and resistance to wear. For buyers, investing in higher-grade materials can result in long-term savings due to reduced maintenance and replacement costs. -
Compressive Strength
This property indicates the ability of terrazzo to withstand axial loads. Typically measured in megapascals (MPa), a compressive strength of at least 25 MPa is recommended for commercial applications. Understanding compressive strength helps buyers ensure that the terrazzo can handle heavy foot traffic, making it ideal for retail and industrial settings. -
Water Absorption Rate
The water absorption rate is a measure of how much moisture the terrazzo can absorb, expressed as a percentage. A lower absorption rate signifies better resistance to staining and damage from moisture. For buyers in humid regions or those involved in food processing, selecting terrazzo with low water absorption is essential for hygiene and longevity. -
Slip Resistance
Slip resistance is critical for safety, particularly in commercial environments. This is typically measured using a coefficient of friction (COF). A COF of 0.60 or higher is generally recommended for wet areas. Buyers should prioritize slip-resistant terrazzo to minimize the risk of accidents and comply with safety regulations. -
Thermal Conductivity
Thermal conductivity measures how well the material conducts heat. Terrazzo with low thermal conductivity can help maintain comfortable floor temperatures, making it suitable for both heating and cooling applications. This is especially important for buyers in colder climates or those looking to enhance energy efficiency.
Which Trade Terminology Should B2B Buyers Know When Sourcing Terrazzo?
Familiarity with industry jargon can facilitate smoother negotiations and ensure clarity in transactions. Here are some essential trade terms relevant to terrazzo suppliers:
-
OEM (Original Equipment Manufacturer)
This term refers to companies that produce products that are then branded by another company. For terrazzo suppliers, understanding OEM relationships can help buyers negotiate better pricing and quality assurance for custom designs. -
MOQ (Minimum Order Quantity)
MOQ denotes the smallest quantity of a product that a supplier is willing to sell. Knowing the MOQ is crucial for budget planning and inventory management. B2B buyers should negotiate MOQs that align with their project needs to avoid excess costs. -
RFQ (Request for Quotation)
An RFQ is a formal document sent to suppliers requesting pricing and terms for specific products. For terrazzo buyers, submitting an RFQ allows for competitive bidding and helps ensure transparency in pricing. -
Incoterms (International Commercial Terms)
Incoterms are a set of predefined commercial terms published by the International Chamber of Commerce, used in international shipping. Understanding these terms helps buyers clarify responsibilities regarding shipping, insurance, and tariffs, thus avoiding unexpected costs. -
Lead Time
Lead time refers to the time it takes from placing an order to receiving the product. It is a critical factor for project planning, especially in construction and renovation projects. Buyers should communicate their timelines clearly to suppliers to ensure timely delivery. -
Installation Standards
These are guidelines and specifications that dictate how terrazzo should be installed to ensure its longevity and performance. Buyers should inquire about installation standards to avoid potential issues post-installation, ensuring that the product meets local building codes and safety regulations.
By understanding these technical properties and trade terms, B2B buyers can make informed decisions when sourcing terrazzo, ultimately leading to successful projects and satisfied clients.
Navigating Market Dynamics and Sourcing Trends in the terrazzo supplier Sector
What Are the Key Trends Shaping the Terrazzo Supplier Market?
The terrazzo supplier market is experiencing significant shifts driven by globalization, evolving consumer preferences, and technological advancements. International buyers, particularly from Africa, South America, the Middle East, and Europe, are increasingly drawn to terrazzo for its aesthetic appeal and durability. The demand for customized designs, colors, and patterns is on the rise, reflecting a broader trend toward personalization in the construction and interior design sectors.
Emerging technologies such as digital design software and automation in manufacturing are enhancing the efficiency and precision of terrazzo production. Buyers can now leverage these technologies to create bespoke flooring solutions that meet specific project requirements. Additionally, the integration of e-commerce platforms is revolutionizing how buyers source materials, allowing for streamlined procurement processes and greater access to global suppliers.
Market dynamics are also influenced by regional economic factors. In Europe, for example, there is a strong focus on high-quality materials that comply with stringent building regulations, while in Africa and South America, the emphasis may be on cost-effectiveness and availability. Understanding these regional nuances is crucial for international buyers looking to navigate the complexities of sourcing terrazzo products effectively.
How Is Sustainability Affecting Sourcing Decisions in the Terrazzo Sector?
Sustainability is becoming a non-negotiable factor in sourcing decisions for terrazzo suppliers. The environmental impact of sourcing materials and manufacturing processes is under increasing scrutiny from both consumers and regulatory bodies. Buyers are seeking suppliers who prioritize sustainable practices, such as using recycled materials and eco-friendly production methods.
Ethical sourcing is equally important, as international buyers are now more aware of the social implications of their purchasing decisions. Ensuring that suppliers adhere to fair labor practices and contribute positively to their communities can enhance brand reputation and foster long-term partnerships.
Certifications such as LEED (Leadership in Energy and Environmental Design) and other “green” certifications are becoming vital in the decision-making process. Buyers should look for suppliers that can demonstrate compliance with these standards, as it not only reflects commitment to sustainability but also adds value to the end product.
How Has the Terrazzo Industry Evolved Over Time?
The terrazzo industry has a rich history that dates back to ancient times, with origins in Italy where artisans used marble chips to create stunning floor designs. Over the centuries, terrazzo has evolved from a labor-intensive craft to a sophisticated manufacturing process that incorporates modern technology and innovative materials.
Today, terrazzo is not just a flooring option but a design statement that embodies versatility and sustainability. The introduction of epoxy terrazzo has revolutionized the market, offering a lighter and more flexible alternative that meets contemporary design demands while maintaining durability. This evolution has positioned terrazzo as a sought-after choice for commercial and residential spaces alike, appealing to a diverse range of international buyers.
As the market continues to grow, understanding these trends and historical contexts will empower B2B buyers to make informed sourcing decisions that align with their business goals and values.
Frequently Asked Questions (FAQs) for B2B Buyers of terrazzo supplier
-
How can I ensure the quality of terrazzo products from a supplier?
To ensure the quality of terrazzo products, request samples and certifications from potential suppliers. Look for industry certifications like ISO or local quality standards. Evaluate the supplier’s production process, including their raw materials and quality assurance measures. Conduct factory visits if possible, or use third-party inspection services to assess the manufacturing environment and product quality before making a bulk purchase. -
What is the best terrazzo material for high-traffic commercial spaces?
For high-traffic commercial spaces, epoxy terrazzo is often the best choice. It offers superior durability and resistance to wear, moisture, and stains compared to traditional cement-based terrazzo. Additionally, epoxy terrazzo can be customized with various colors and patterns, allowing for aesthetic flexibility while maintaining functionality. Ensure that the supplier provides specific information on the material’s lifecycle and maintenance requirements. -
What customization options should I consider when sourcing terrazzo?
When sourcing terrazzo, consider customization options such as color, aggregate size, and finish. Discuss the specific design requirements with your supplier to explore different blends of aggregates, which can include glass, marble, or recycled materials. Additionally, inquire about the ability to create unique patterns or logos, as these customizations can enhance the aesthetic appeal of your project while meeting your brand’s identity. -
What are the typical minimum order quantities (MOQ) for terrazzo suppliers?
Minimum order quantities (MOQ) can vary significantly among terrazzo suppliers. Generally, MOQs can range from 100 to 1,000 square meters, depending on the supplier’s production capabilities and the specific product line. It’s essential to clarify the MOQ before placing an order, as this can affect your project’s budget and timeline. Some suppliers may offer flexibility on MOQs for repeat customers or larger projects. -
What payment terms should I expect when dealing with terrazzo suppliers?
Payment terms for terrazzo suppliers typically include options like a deposit upfront (commonly 30-50%) and the balance upon delivery or before shipment. Some suppliers may offer credit terms for established customers. It’s crucial to discuss payment terms upfront and ensure they align with your cash flow needs. Always request a pro forma invoice detailing the terms before finalizing your order. -
How can I vet a terrazzo supplier for international trade?
Vetting a terrazzo supplier for international trade involves researching their reputation, certifications, and past projects. Utilize platforms like Alibaba or Global Sources for reviews and ratings. Request references from previous clients and verify their business licenses and certifications. Additionally, consider conducting a background check or using third-party verification services to assess the supplier’s financial stability and operational capacity. -
What logistics considerations should I keep in mind when importing terrazzo?
When importing terrazzo, consider logistics aspects such as shipping methods, customs clearance, and delivery timelines. Choose between sea or air freight based on your budget and urgency. Ensure that the supplier provides proper documentation for customs, including bills of lading and certificates of origin. Additionally, work with a reliable freight forwarder who can navigate customs regulations specific to your country and manage the import process smoothly. -
What quality assurance measures should I request from a terrazzo supplier?
Requesting quality assurance measures from a terrazzo supplier is crucial for ensuring product reliability. Ask for details on their quality control processes, including in-process inspections, final product testing, and adherence to international standards. Inquire about their return policy for defective products and whether they provide warranties for their materials. Establishing clear QA expectations upfront can help mitigate risks and ensure satisfaction with your purchase.
Important Disclaimer & Terms of Use
⚠️ Important Disclaimer
The information provided in this guide, including content regarding manufacturers, technical specifications, and market analysis, is for informational and educational purposes only. It does not constitute professional procurement advice, financial advice, or legal advice.
While we have made every effort to ensure the accuracy and timeliness of the information, we are not responsible for any errors, omissions, or outdated information. Market conditions, company details, and technical standards are subject to change.
B2B buyers must conduct their own independent and thorough due diligence before making any purchasing decisions. This includes contacting suppliers directly, verifying certifications, requesting samples, and seeking professional consultation. The risk of relying on any information in this guide is borne solely by the reader.
Strategic Sourcing Conclusion and Outlook for terrazzo supplier
In today’s competitive market, the strategic sourcing of terrazzo materials is not just a procurement activity; it is a vital component for ensuring quality, sustainability, and cost-effectiveness in construction projects. By understanding the unique characteristics of terrazzo, such as its durability, aesthetic versatility, and low maintenance requirements, international B2B buyers can make informed decisions that align with their project goals.
What are the key benefits of partnering with reputable terrazzo suppliers? Establishing relationships with suppliers who offer high-quality materials and reliable service can lead to enhanced project outcomes and reduced lifecycle costs. Moreover, suppliers that provide innovative options like epoxy terrazzo can help meet specific industry needs, such as hygiene standards in healthcare facilities.
As the demand for sustainable and visually appealing flooring solutions grows in regions like Africa, South America, the Middle East, and Europe, buyers are encouraged to explore new partnerships and technologies. By embracing strategic sourcing practices, businesses can not only improve their supply chain efficiency but also contribute to a more sustainable future.
Act now to leverage these insights and elevate your projects with quality terrazzo solutions that stand the test of time.