Discover Top Laser Cutter Manufacturers: A Complete Guide (2025)
Introduction: Navigating the Global Market for laser cutter manufacturer
In today’s competitive landscape, sourcing the right laser cutter manufacturer can be a daunting task for international B2B buyers. With numerous options available across continents, including Africa, South America, the Middle East, and Europe, companies must navigate a complex array of features, applications, and pricing models. This guide aims to demystify the global market for laser cutting machines, providing insights that empower buyers to make informed purchasing decisions.
Throughout this comprehensive resource, we will explore various types of laser cutters, from CO2 to fiber laser technologies, and their specific applications in industries such as automotive, textiles, and electronics. Understanding the nuances of each type will help buyers identify the best fit for their operational needs. Additionally, we will delve into the critical aspects of supplier vetting, including quality assurance, certifications, and after-sales support, ensuring that buyers choose reliable partners.
Moreover, we will provide a detailed analysis of cost factors, highlighting not just the initial investment but also long-term operational expenses, maintenance, and potential return on investment. By equipping B2B buyers with this knowledge, our guide serves as a crucial tool for making strategic procurement decisions that align with business goals and market demands. Whether you are a manufacturer in South Africa or a distributor in Vietnam, this guide will help you navigate the complexities of sourcing laser cutting solutions effectively.
Understanding laser cutter manufacturer Types and Variations
Type Name | Key Distinguishing Features | Primary B2B Applications | Brief Pros & Cons for Buyers |
---|---|---|---|
CO2 Laser Cutters | Uses a CO2 gas laser, ideal for non-metal materials | Woodworking, textiles, acrylic cutting | Pros: Versatile, cost-effective. Cons: Limited metal cutting capability. |
Fiber Laser Cutters | Utilizes a fiber optic laser, excellent for metals | Automotive, aerospace, and metal fabrication | Pros: High speed, low maintenance. Cons: Higher initial investment. |
Crystal Laser Cutters | Employs solid-state laser technology, suitable for precision work | Medical device manufacturing, electronics | Pros: High precision, compact design. Cons: More complex operation. |
UV Laser Cutters | Uses ultraviolet light for cutting and engraving | Electronics, plastics, and glass | Pros: Fine detail, minimal heat-affected zone. Cons: Slower cutting speed. |
Multi-Technology Laser Systems | Combines various laser technologies for versatile applications | Prototyping, custom manufacturing | Pros: Highly adaptable, multi-functional. Cons: Potentially higher operational costs. |
What Are CO2 Laser Cutters and Their Applications?
CO2 laser cutters are one of the most common types used in various industries, particularly for non-metal materials like wood, textiles, and acrylics. These machines are known for their versatility and cost-effectiveness, making them ideal for small to medium-sized enterprises. When considering a CO2 laser cutter, buyers should evaluate the machine’s power rating and bed size to ensure it meets their production needs. Additionally, assess the availability of replacement parts and support services, especially if sourcing from international manufacturers.
How Do Fiber Laser Cutters Stand Out?
Fiber laser cutters are recognized for their efficiency in cutting metals, including stainless steel, aluminum, and brass. They utilize a solid-state laser that offers high speed and low maintenance, making them suitable for high-volume production environments such as automotive and aerospace industries. Buyers should consider the power output, as higher wattage allows for thicker material cutting. Furthermore, it’s crucial to investigate the manufacturer’s reputation for service and support, as these factors can significantly impact operational uptime.
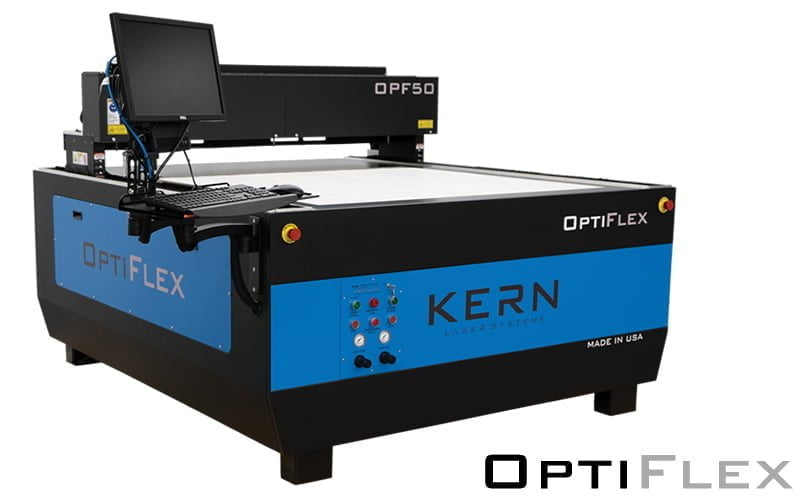
A stock image related to laser cutter manufacturer.
What Are the Key Features of Crystal Laser Cutters?
Crystal laser cutters utilize solid-state lasers to achieve high precision in cutting and engraving applications. These machines are often favored in sectors like medical device manufacturing and electronics due to their ability to perform intricate cuts with minimal kerf. When purchasing a crystal laser cutter, B2B buyers should focus on the machine’s compatibility with various materials and its operational complexity, as these factors can affect training requirements and production efficiency. Understanding the manufacturer’s technology and support can also provide an advantage in maximizing the cutter’s capabilities.
Why Choose UV Laser Cutters for Your Business?
UV laser cutters employ ultraviolet light to achieve fine detail in cutting and engraving, making them particularly effective for sensitive materials such as plastics and glass. They generate minimal heat, which reduces the risk of warping or damaging the material. Buyers should evaluate the machine’s speed and precision, as well as its ability to handle the specific materials needed for their applications. Additionally, consider the availability of technical support and training, especially if your team is new to this technology.
What Are the Benefits of Multi-Technology Laser Systems?
Multi-technology laser systems integrate various laser technologies, providing businesses with a versatile tool for diverse applications, including prototyping and custom manufacturing. These systems can handle multiple materials and processes, from cutting to engraving. When considering this type of system, B2B buyers should assess the overall cost of ownership, including maintenance and operational expenses. It’s also essential to examine the manufacturer’s expertise in providing comprehensive support and training, as this can enhance the return on investment and efficiency in production.
Related Video: How to Laser Engrave Anything with the xTool D1 Laser Cutter/Engraver
Key Industrial Applications of laser cutter manufacturer
Industry/Sector | Specific Application of Laser Cutter Manufacturer | Value/Benefit for the Business | Key Sourcing Considerations for this Application |
---|---|---|---|
Automotive Manufacturing | Precision cutting of metal components | Increases production efficiency and reduces waste | Evaluate machine speed, precision, and compatibility with materials. |
Aerospace | Cutting of composite materials and metals | Enhances structural integrity and reduces weight | Look for certifications, material handling capabilities, and after-sales support. |
Electronics | PCB and electronic housing fabrication | Improves product reliability and reduces lead times | Ensure compatibility with various materials and precision cutting capabilities. |
Fashion and Textiles | Custom designs and patterns in fabrics | Offers unique designs and reduces inventory costs | Assess customization options and material versatility. |
Construction and Architecture | Cutting of signage and structural components | Streamlines project timelines and enhances aesthetics | Consider cutting size capabilities and software integration for design. |
How is Laser Cutting Used in Automotive Manufacturing?
In the automotive industry, laser cutters are essential for the precision cutting of metal components such as chassis parts and engine components. These machines significantly enhance production efficiency by allowing for intricate designs and reducing material waste. Buyers from regions like Africa and South America should focus on sourcing laser cutters that offer high-speed operation and compatibility with various metals, ensuring they meet local manufacturing standards and regulations.
What Role Does Laser Cutting Play in Aerospace Applications?
Aerospace manufacturers utilize laser cutting to process composite materials and metals, crucial for producing lightweight yet durable aircraft components. This technology not only improves structural integrity but also enables manufacturers to meet stringent weight requirements. International buyers, especially from the Middle East and Europe, should prioritize suppliers that provide robust certifications and after-sales service, ensuring compliance with aerospace industry standards.
How is Laser Cutting Transforming the Electronics Sector?
In the electronics sector, laser cutting is used for the fabrication of printed circuit boards (PCBs) and electronic housings. This application enhances product reliability and reduces lead times, which is vital in a fast-paced market. B2B buyers, particularly from emerging markets, should ensure that the laser cutter can handle a variety of materials and offers precise cutting capabilities to maintain high-quality standards.
What Benefits Does Laser Cutting Offer to Fashion and Textiles?
In the fashion and textiles industry, laser cutters allow for the creation of custom designs and intricate patterns in fabrics. This capability not only fosters unique product offerings but also helps in managing inventory costs by enabling on-demand production. Buyers from diverse regions should evaluate the customization options available and the machine’s ability to work with various fabric types to ensure flexibility in design.
How Can Laser Cutting Enhance Construction and Architecture Projects?
Laser cutting is increasingly used in construction and architecture for crafting signage and structural components. This technology streamlines project timelines and enhances the aesthetic appeal of buildings and installations. Buyers in this sector should consider the cutting size capabilities of the laser cutters and their integration with design software to ensure a seamless workflow from design to production.
Related Video: Industrial Applications for Laser Technology
3 Common User Pain Points for ‘laser cutter manufacturer’ & Their Solutions
Scenario 1: Navigating Complex Specifications for Laser Cutters
The Problem:
B2B buyers often face the daunting task of selecting a laser cutter that meets their specific operational needs. This challenge is exacerbated when manufacturers provide overly technical specifications that can be difficult to interpret. For instance, a company in South Africa may require a laser cutter that can handle both metal and wood, but they struggle to understand which model is best suited for diverse materials, power levels, and cutting speeds. This lack of clarity can lead to costly purchasing mistakes or equipment that underperforms.
The Solution:
To effectively navigate the complexities of laser cutter specifications, buyers should start with a detailed needs assessment. Collaborate with stakeholders from various departments—production, engineering, and maintenance—to gather comprehensive requirements. Once these needs are clearly defined, engage directly with manufacturers or distributors to ask specific questions about how their equipment can meet those requirements. For example, inquire about the cutter’s versatility in handling different materials and its operational efficiency in your specific industry context. Additionally, seeking demonstrations or trial periods can provide valuable hands-on experience, ensuring that the chosen machine aligns with your operational expectations.
Scenario 2: Managing Maintenance and Downtime Issues
The Problem:
One of the most pressing pain points for international B2B buyers is the potential for equipment downtime due to inadequate maintenance support. A manufacturer in Europe may invest heavily in a high-end laser cutter, but without a reliable maintenance plan, they risk unexpected breakdowns that can halt production and lead to significant financial losses. This is particularly critical for businesses that rely on just-in-time manufacturing processes, where every minute of downtime can translate to lost revenue.
The Solution:
To mitigate maintenance-related issues, buyers should prioritize manufacturers that offer comprehensive support packages. Before making a purchase, inquire about the availability of local service technicians, response times for emergency repairs, and the accessibility of replacement parts. Establishing a proactive maintenance schedule in collaboration with the manufacturer can also help identify potential issues before they escalate. Furthermore, consider implementing a remote monitoring system, if available, that allows for real-time diagnostics and alerts for maintenance needs, which can significantly reduce the risk of unplanned downtime.
Scenario 3: Understanding Total Cost of Ownership (TCO) for Laser Cutters
The Problem:
Many B2B buyers underestimate the Total Cost of Ownership (TCO) associated with laser cutters, focusing only on the initial purchase price. For instance, a business in South America might find a laser cutter that fits their budget, only to later discover that energy costs, consumables, and maintenance significantly increase operational expenses. This oversight can lead to budget overruns and impact overall profitability.
The Solution:
To gain a clear understanding of TCO, buyers should conduct a thorough cost analysis that extends beyond the initial investment. Request detailed operational cost estimates from manufacturers, including energy consumption, maintenance needs, and the lifespan of consumables such as lenses and nozzles. Additionally, consider the potential for automation and efficiency gains that could offset some of these costs. Engaging with industry peers to gather insights on their experiences can also provide valuable context regarding long-term expenses. By adopting a holistic view of costs, buyers can make more informed decisions that align with their financial goals and operational capacities.
Strategic Material Selection Guide for laser cutter manufacturer
When selecting materials for laser cutting applications, understanding the properties, advantages, and limitations of each material is crucial for international B2B buyers. This guide will analyze four common materials used in laser cutting: acrylic, stainless steel, aluminum, and wood. Each material has unique characteristics that influence performance and suitability for various applications, particularly in diverse markets such as Africa, South America, the Middle East, and Europe.
What Are the Key Properties of Acrylic in Laser Cutting?
Acrylic, also known as PMMA (polymethyl methacrylate), is a popular choice for laser cutting due to its optical clarity and versatility. It has a low melting point, making it easy to cut and engrave with lasers. Acrylic is also resistant to UV light and weathering, which enhances its durability in outdoor applications.
Pros & Cons: The main advantages of acrylic include its lightweight nature and aesthetic appeal, making it suitable for signage and displays. However, it can be prone to scratching and may not withstand high temperatures, limiting its use in high-heat environments.
Impact on Application: Acrylic is widely used in signage, displays, and protective barriers. Its compatibility with various colors and finishes allows for creative applications.
Considerations for International Buyers: Buyers should consider local regulations regarding plastic materials, as some regions may have restrictions on certain types of plastics. Compliance with standards such as ASTM D4802 is essential for ensuring quality.
How Does Stainless Steel Perform in Laser Cutting Applications?
Stainless steel is renowned for its strength, durability, and corrosion resistance, making it a preferred material for industrial applications. It can withstand high temperatures and is less likely to warp during the cutting process, which is crucial for precision work.
Pros & Cons: The key advantage of stainless steel is its longevity and resistance to rust, making it ideal for outdoor and marine applications. However, it is more challenging to cut than softer metals and may require higher power settings, increasing operational costs.
Impact on Application: Stainless steel is commonly used in manufacturing components for the automotive and aerospace industries, as well as in kitchenware and medical equipment.
Considerations for International Buyers: Buyers should ensure compliance with international standards such as ASTM A240 and DIN 1.4301, which govern the quality of stainless steel. Understanding local market preferences for specific grades of stainless steel can also influence purchasing decisions.
What Are the Advantages of Using Aluminum in Laser Cutting?
Aluminum is lightweight and has excellent thermal conductivity, making it a versatile choice for laser cutting. It is available in various alloys, each with distinct properties that can be tailored to specific applications.
Pros & Cons: The main advantage of aluminum is its ability to be easily machined and formed, which is beneficial for intricate designs. However, its softness can lead to issues with edge quality, requiring post-processing to achieve a smooth finish.
Impact on Application: Aluminum is frequently used in the automotive and aerospace industries, as well as in consumer electronics and packaging.
Considerations for International Buyers: Buyers should be aware of the differences in aluminum grades and their compliance with standards such as JIS H 4040. Furthermore, understanding the local supply chain for aluminum can help reduce lead times.
Why Is Wood a Preferred Material for Laser Cutting?
Wood is a traditional material that offers a unique aesthetic and is widely used in various applications, from furniture to decorative items. The natural variations in wood grain can enhance the final product’s appearance.
Pros & Cons: The advantages of wood include its availability and ease of cutting, making it a cost-effective option. However, wood can be susceptible to warping and moisture damage, which may affect the quality of the final product.
Impact on Application: Wood is commonly used for crafting, signage, and interior design elements, with compatibility for various finishes and treatments.
Considerations for International Buyers: Buyers should consider the sustainability of wood sources and compliance with regulations such as the Forest Stewardship Council (FSC) certification. Different regions may have preferences for specific wood types, influencing purchasing decisions.
Summary Table of Material Selection for Laser Cutting
Material | Typical Use Case for laser cutter manufacturer | Key Advantage | Key Disadvantage/Limitation | Relative Cost (Low/Med/High) |
---|---|---|---|---|
Acrylic | Signage and displays | Lightweight and versatile | Prone to scratching | Medium |
Stainless Steel | Automotive and aerospace components | High strength and corrosion resistance | Difficult to cut, higher costs | High |
Aluminum | Automotive and consumer electronics | Easy to machine and form | Softness can affect edge quality | Medium |
Wood | Furniture and decorative items | Aesthetic appeal and availability | Susceptible to warping and moisture | Low |
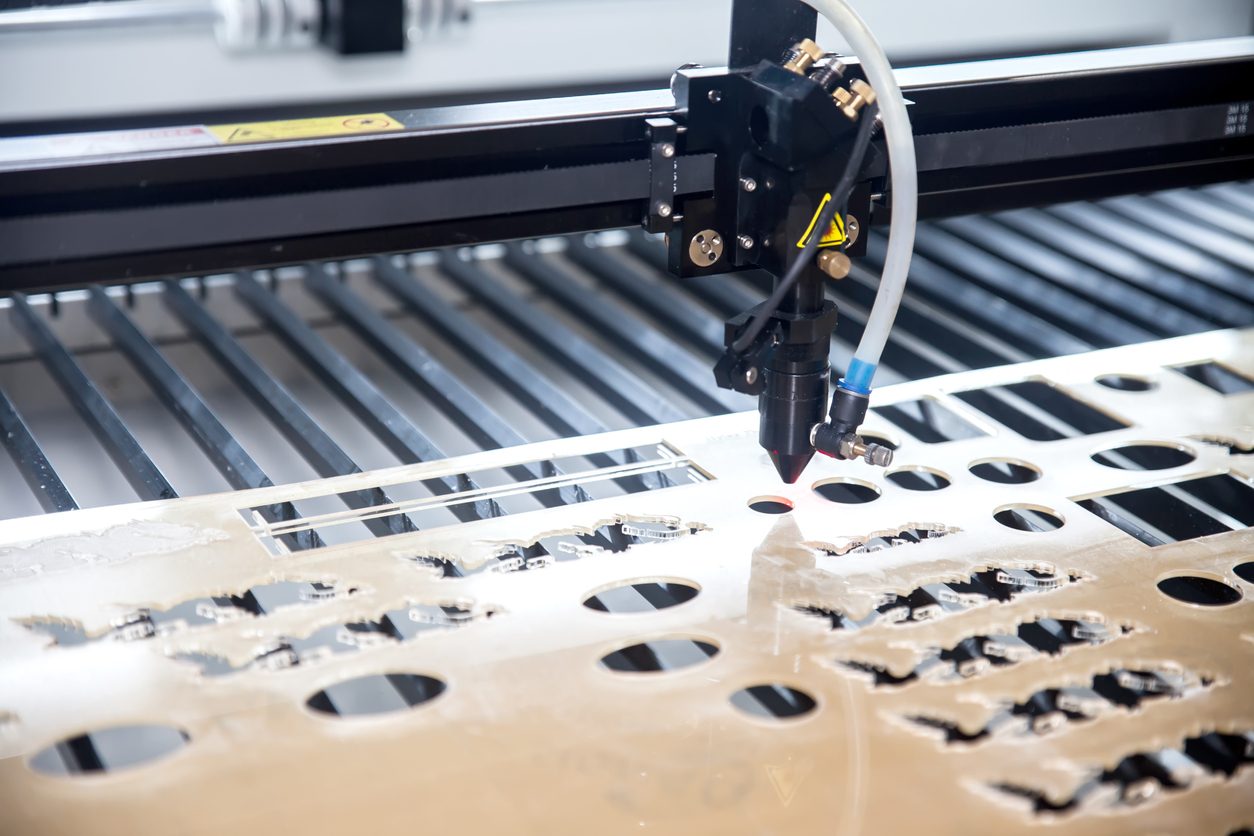
A stock image related to laser cutter manufacturer.
This strategic material selection guide provides essential insights for international B2B buyers, enabling informed decisions based on the properties and applications of each material in laser cutting. Understanding these factors can significantly enhance the efficiency and effectiveness of purchasing strategies in diverse markets.
In-depth Look: Manufacturing Processes and Quality Assurance for laser cutter manufacturer
What Are the Main Stages of Manufacturing Laser Cutters?
The manufacturing of laser cutters involves several critical stages that ensure the product meets the rigorous demands of the market. Understanding these stages can help B2B buyers make informed decisions when selecting a manufacturer.
Material Preparation
The first stage in the manufacturing process is material preparation. This involves selecting high-quality raw materials, such as metals (steel, aluminum) and composites that can withstand high temperatures and are suitable for laser cutting. Buyers should look for manufacturers that source materials compliant with international standards, as this can impact durability and performance.
Forming Techniques
Once the materials are prepared, the next step is forming. This can include processes such as laser cutting, bending, and machining. Manufacturers often employ advanced CNC (Computer Numerical Control) technology to enhance precision. B2B buyers should inquire about the specific forming techniques used, as this can greatly influence the accuracy and efficiency of the laser cutter.
Assembly Process
The assembly stage is where all components come together. This includes integrating the laser source, optics, and control systems. Effective assembly is crucial for ensuring that the machine operates correctly and efficiently. Buyers should assess whether manufacturers utilize automated assembly processes, as these can improve consistency and reduce human error.
Finishing Touches
Finally, the finishing stage involves surface treatments, painting, and quality inspections. This stage not only enhances aesthetics but also protects the machine from environmental factors. Buyers should verify if the manufacturer employs environmentally friendly finishing techniques, which can be a selling point in many markets.
How Do Quality Assurance Protocols Ensure Product Reliability?
Quality assurance (QA) is a vital component in the manufacturing process, particularly for complex machinery like laser cutters. Implementing robust QA protocols helps ensure that the final product meets both performance and safety standards.
What Are the Key International Standards for Quality Assurance?
Many manufacturers adhere to international standards such as ISO 9001, which outlines criteria for quality management systems. Additionally, industry-specific certifications like CE (Conformité Européenne) for European markets and API (American Petroleum Institute) for oil and gas applications can signify a manufacturer’s commitment to quality and safety. Buyers should prioritize manufacturers with these certifications to ensure compliance with global standards.
How Are Quality Checkpoints Implemented During Manufacturing?
Quality checkpoints are integrated throughout the manufacturing process, typically categorized as Incoming Quality Control (IQC), In-Process Quality Control (IPQC), and Final Quality Control (FQC).
- IQC: This phase involves inspecting raw materials before they enter production. Effective IQC helps prevent defects caused by subpar materials.
- IPQC: During the assembly and forming stages, IPQC ensures that each step meets specified quality criteria. This often includes real-time monitoring and adjustments.
- FQC: The final inspection phase verifies that the finished product meets all specifications before shipping. This may involve functional tests and performance assessments.
What Common Testing Methods Are Used in Laser Cutter Manufacturing?
Various testing methods are employed to ensure the reliability and performance of laser cutters:
- Performance Testing: Assessing cutting speed, accuracy, and quality of the cut.
- Durability Testing: Simulating prolonged use to evaluate wear and tear.
- Safety Testing: Ensuring compliance with safety regulations, particularly in high-power laser applications.
B2B buyers should inquire about the specific testing methods utilized by manufacturers, as these can significantly impact the longevity and safety of the equipment.
How Can B2B Buyers Verify Supplier Quality Control Processes?
Verification of a supplier‘s quality control processes is crucial for B2B buyers, especially when sourcing internationally. Here are some actionable steps:
Conducting Audits
Buyers can conduct onsite audits to assess a manufacturer’s quality control processes. This allows for direct observation of manufacturing practices and adherence to QA protocols.
Requesting Quality Reports
Manufacturers should provide detailed quality reports that outline their QA processes, testing methods, and results. These reports can give insight into the manufacturer’s commitment to quality.
Utilizing Third-Party Inspections
Engaging third-party inspection services can offer an unbiased evaluation of the manufacturer’s quality control practices. This is particularly beneficial for international buyers who may not have the resources to conduct audits themselves.
What Are the Quality Control Nuances for International Buyers?
International buyers, particularly those from regions like Africa, South America, the Middle East, and Europe, face unique challenges in quality control. Understanding these nuances can help in making informed purchasing decisions.
Navigating Different Regulatory Environments
Each region has its own regulatory standards, which can affect the quality assurance process. For example, European buyers must ensure that products comply with CE marking, while buyers in Africa and South America may face different local regulations. Buyers should familiarize themselves with these requirements to avoid compliance issues.
Language and Communication Barriers
Language differences can create misunderstandings in quality specifications and requirements. It is advisable for buyers to work with manufacturers who have multilingual support or local representatives to facilitate clear communication.
Cultural Differences in Business Practices
Cultural differences can influence manufacturing practices and quality perceptions. Buyers should approach negotiations with an understanding of these differences to foster strong partnerships with suppliers.
Conclusion
By understanding the manufacturing processes and quality assurance protocols of laser cutter manufacturers, B2B buyers can make more informed decisions. Prioritizing manufacturers with robust QA systems, international certifications, and transparent practices will enhance the likelihood of acquiring high-quality equipment that meets specific business needs.
Practical Sourcing Guide: A Step-by-Step Checklist for ‘laser cutter manufacturer’
In the competitive landscape of industrial manufacturing, sourcing a reliable laser cutter manufacturer is crucial for businesses aiming to enhance their operational efficiency and product quality. This practical sourcing guide serves as a checklist to help international B2B buyers, particularly from Africa, South America, the Middle East, and Europe, navigate the procurement process effectively.
Step 1: Define Your Technical Specifications
Establishing clear technical specifications is foundational to your sourcing process. Identify the specific requirements for your laser cutting needs, including material types, thicknesses, cutting speed, and precision levels. This clarity will enable you to communicate effectively with potential suppliers and ensure they can meet your operational demands.
Step 2: Conduct Market Research
Understanding the market landscape is essential for making informed decisions. Research various laser cutter manufacturers and their product offerings. Look for industry reports, reviews, and case studies to gauge the reputation and reliability of different suppliers. This step helps you identify leading manufacturers and emerging players that may offer competitive advantages.
Step 3: Evaluate Supplier Certifications
Before engaging with a supplier, verify their certifications and compliance with international standards. Look for ISO certifications and other relevant industry-specific qualifications. Certifications indicate that the manufacturer adheres to quality management systems and meets safety and performance standards, which is particularly important for buyers from diverse regulatory environments.
Step 4: Request Samples and Product Demonstrations
To ensure the manufacturer’s equipment meets your needs, request samples or demonstrations of their laser cutting technology. This allows you to assess the machine’s performance, quality of cuts, and ease of operation. Pay attention to how the equipment handles different materials and thicknesses, as well as any software features that may enhance usability.
Step 5: Assess After-Sales Support and Service
A strong after-sales support system can significantly impact your long-term satisfaction with a laser cutter. Inquire about the manufacturer’s warranty policies, technical support availability, and training programs for your staff. Reliable support can minimize downtime and ensure your operations run smoothly, especially in regions where local service may be limited.
Step 6: Compare Pricing and Payment Terms
Cost is always a critical factor in procurement decisions. Compare pricing structures from different manufacturers while considering the total cost of ownership, which includes maintenance and operational costs. Additionally, negotiate payment terms that align with your budget and cash flow needs, ensuring that the terms are favorable and transparent.
Step 7: Check References and Customer Feedback
Before finalizing your decision, seek references from other businesses that have purchased from the manufacturers you are considering. Customer feedback can provide insights into the reliability of the equipment and the manufacturer’s customer service. Engaging with other buyers, especially those in similar industries or regions, can also help you understand potential challenges and benefits.
By following this step-by-step checklist, international B2B buyers can make well-informed decisions when sourcing laser cutter manufacturers, ultimately leading to successful partnerships and enhanced operational capabilities.
Comprehensive Cost and Pricing Analysis for laser cutter manufacturer Sourcing
What Are the Key Cost Components in Laser Cutter Manufacturing?
Understanding the cost structure of laser cutter manufacturing is crucial for international B2B buyers. The primary components include:
-
Materials: The choice of materials significantly impacts pricing. High-quality steel and aluminum are commonly used, but options may vary based on specifications and desired durability.
-
Labor: Labor costs can fluctuate based on the region of manufacturing. Countries with lower labor costs, such as those in South America or parts of Africa, may offer competitive pricing, but it’s essential to assess the skill level of the workforce.
-
Manufacturing Overhead: This includes costs associated with utilities, facility maintenance, and administrative expenses. In regions with high operational costs, such as Europe, this can influence the final price.
-
Tooling: The investment in tooling and machinery is a significant upfront cost that can affect overall pricing. Custom tooling for specific projects may further increase expenses.
-
Quality Control (QC): Rigorous QC processes ensure product reliability and safety. Manufacturers with higher QC standards may charge a premium, but this investment often pays off in terms of reduced failure rates.
-
Logistics: Shipping costs can vary dramatically depending on the distance, mode of transport, and freight terms. Incoterms play a vital role in determining who bears these costs.
-
Margin: Manufacturers typically include a margin that reflects their operational risk and market conditions. Understanding this can aid in negotiating better terms.
How Do Price Influencers Affect Laser Cutter Costs?
Several factors influence pricing in laser cutter manufacturing, which buyers should consider:
-
Volume and Minimum Order Quantity (MOQ): Larger orders often lead to better pricing due to economies of scale. Buyers should negotiate MOQs to optimize costs.
-
Specifications and Customization: Custom features or specific requirements can increase costs. Providing clear specifications can help manufacturers offer accurate quotes.
-
Material Quality and Certifications: Higher quality materials or certifications (like ISO) can increase costs but also enhance product performance and reliability. Buyers should weigh the benefits against the additional expenses.
-
Supplier Factors: The reputation and experience of the supplier can influence pricing. Established manufacturers may charge more due to their proven track record, while newer suppliers might offer competitive rates to build their portfolio.
-
Incoterms: These terms define the responsibilities of buyers and sellers in shipping. Understanding which terms apply can help manage logistics costs effectively.
What Tips Can International Buyers Use to Negotiate Better Prices?
Negotiating effectively can lead to significant savings. Here are actionable tips for international buyers from Africa, South America, the Middle East, and Europe:
-
Conduct Market Research: Understand the prevailing market rates for laser cutters in your region. This information can provide leverage during negotiations.
-
Evaluate Total Cost of Ownership (TCO): Consider not just the purchase price but also maintenance, operation, and potential downtime costs. A lower initial price may not always equate to better value.
-
Be Open to Multiple Suppliers: Engaging with various manufacturers can foster competition, leading to better pricing and terms. It can also reduce risk if one supplier cannot meet your needs.
-
Negotiate Terms and Conditions: Discuss payment terms, warranties, and support services. Favorable terms can offset higher initial costs and contribute to overall savings.
-
Leverage Long-Term Relationships: Building a strong relationship with suppliers can lead to better pricing over time. Consider negotiating long-term contracts for consistent supply and potential discounts.
Disclaimer on Indicative Prices
Prices for laser cutters can vary significantly based on the factors mentioned above. This analysis provides a general framework, but buyers should obtain specific quotes from manufacturers to understand the pricing landscape accurately. Always consider regional variations and market dynamics when making purchasing decisions.
Alternatives Analysis: Comparing laser cutter manufacturer With Other Solutions
When considering the acquisition of a laser cutter, it’s essential for B2B buyers to explore various alternatives that may fulfill their operational needs. Each solution presents unique advantages and challenges, which can significantly influence the decision-making process. This analysis compares the traditional laser cutter with two viable alternatives: plasma cutting and waterjet cutting.
Comparison Aspect | Laser Cutter Manufacturer | Plasma Cutting | Waterjet Cutting |
---|---|---|---|
Performance | High precision and speed | Good for thicker materials but less precision | Excellent for intricate designs, no heat distortion |
Cost | Higher initial investment | Generally lower cost | Moderate to high cost |
Ease of Implementation | Requires skilled operators | Easier to set up and operate | More complex setup needed |
Maintenance | Moderate upkeep required | Low maintenance costs | Higher maintenance due to pumps and components |
Best Use Case | Thin to medium materials | Heavy-duty industrial applications | Delicate materials and complex shapes |
What Are the Advantages and Disadvantages of Plasma Cutting?
Plasma cutting is a popular alternative to laser cutting, particularly in industrial settings where speed and cost are critical. This method utilizes a high-velocity jet of ionized gas to cut through metals, making it particularly effective for thicker materials. One of the key advantages of plasma cutting is its lower initial cost compared to laser cutting, which can be appealing for budget-conscious buyers. However, it tends to sacrifice precision for speed and may not be suitable for intricate designs or thinner materials, which can lead to a rougher edge finish.
How Does Waterjet Cutting Compare to Laser Cutting?
Waterjet cutting employs a high-pressure stream of water, often mixed with abrasives, to cut through a variety of materials. This method is particularly advantageous for applications that require intricate shapes or where heat distortion must be minimized, as it does not generate heat during the cutting process. Although waterjet cutting can handle a wide range of materials, including metal, glass, and stone, it typically comes with a moderate to high cost and a more complex setup, which may require additional operator training. Maintenance can also be higher due to the pumps and other components involved.
Which Solution Is Right for Your Business Needs?
When evaluating the best solution for your cutting needs, consider your specific requirements, such as the types of materials you work with, production volume, and budget constraints. Laser cutters are ideal for precision and speed with thinner materials, while plasma cutters may serve better in heavy-duty applications. Waterjet cutters are excellent for intricate designs and materials sensitive to heat. By carefully assessing these factors, B2B buyers can make informed decisions that align with their operational goals and financial considerations. Ultimately, the right choice will depend on striking a balance between cost, performance, and the specific needs of your manufacturing processes.
Essential Technical Properties and Trade Terminology for laser cutter manufacturer
What Are the Key Technical Properties of Laser Cutters?
Understanding the essential technical properties of laser cutters is crucial for B2B buyers, especially when evaluating different manufacturers. Here are some critical specifications to consider:
1. Material Compatibility
Laser cutters can work with various materials, including metals (like steel and aluminum), plastics, wood, and textiles. Each machine has specific capabilities regarding the types of materials it can cut and the thickness it can handle. Knowing the material compatibility helps buyers select machines that meet their production needs without compromising quality.
2. Laser Power Output
Measured in watts, the laser power output determines the cutting speed and the thickness of the material that can be effectively processed. Higher wattage is generally suitable for thicker materials and faster cutting speeds. B2B buyers should assess their production requirements to choose a laser cutter with an appropriate power output that aligns with their operational efficiency goals.
3. Cutting Speed
Cutting speed, usually expressed in millimeters per minute (mm/min), indicates how quickly the laser cutter can process materials. This specification directly impacts productivity; faster cutting speeds enable higher throughput. Buyers should evaluate their production timelines and select a laser cutter that offers optimal cutting speeds for their operations.
4. Precision and Tolerance
Tolerance refers to the allowable deviation from a specified measurement, which is critical in industries requiring high accuracy. Laser cutters are known for their precision, with tolerances often in the range of ±0.01 mm. For B2B buyers, understanding the precision capabilities of a laser cutter is essential, particularly for applications in electronics or aerospace where minute measurements are critical.
5. Cooling System
The cooling system is vital for maintaining the performance and longevity of the laser cutter. Common types include water cooling and air cooling systems. A reliable cooling system prevents overheating, ensuring consistent performance and reducing maintenance costs. Buyers should consider the cooling requirements of their operations when selecting a machine.
What Common Trade Terms Should Buyers Know?
Navigating the terminology used in the laser cutting industry can be daunting. Here are some common trade terms that B2B buyers should be familiar with:
1. OEM (Original Equipment Manufacturer)
An OEM produces parts or equipment that may be marketed by another manufacturer. When purchasing a laser cutter, knowing whether you are dealing with an OEM can affect warranty, support, and parts availability. Buyers should ensure that they are sourcing from reputable OEMs for reliability.
2. MOQ (Minimum Order Quantity)
MOQ refers to the smallest number of units a supplier is willing to sell. Understanding MOQ is crucial for budget planning and inventory management. B2B buyers should negotiate MOQs to align with their production needs without overcommitting to inventory that may not be used.
3. RFQ (Request for Quotation)
An RFQ is a document sent to suppliers to solicit price quotes for specified goods or services. B2B buyers should prepare detailed RFQs that outline their exact requirements to receive accurate and comparable quotes from different manufacturers.
4. Incoterms (International Commercial Terms)
Incoterms define the responsibilities of buyers and sellers in international trade, including shipping, insurance, and tariffs. Familiarity with Incoterms helps B2B buyers understand their obligations and costs associated with the purchase, ensuring smoother transactions.
5. Lead Time
Lead time is the duration between placing an order and receiving the product. For laser cutters, lead times can vary significantly based on customization and availability. Buyers should factor in lead times when planning production schedules to avoid delays.
Understanding these technical properties and trade terminologies empowers B2B buyers to make informed decisions, ensuring they choose the right laser cutter manufacturer to meet their specific needs in various markets, including Africa, South America, the Middle East, and Europe.
Navigating Market Dynamics and Sourcing Trends in the laser cutter manufacturer Sector
What Are the Current Market Dynamics Affecting Laser Cutter Manufacturers?
The laser cutter manufacturing sector is experiencing significant transformation driven by technological advancements and changing market demands. Key global drivers include the rise of automation and Industry 4.0, which emphasize precision and efficiency in production processes. B2B buyers from Africa, South America, the Middle East, and Europe are increasingly seeking laser cutters that integrate smart technology, such as IoT capabilities for real-time monitoring and predictive maintenance. This shift not only enhances operational efficiency but also reduces downtime, a critical factor for manufacturers in competitive markets.
Emerging trends in sourcing practices highlight the importance of flexibility and adaptability. Buyers are gravitating toward manufacturers that offer customized solutions tailored to specific industry needs. Additionally, the demand for faster lead times and just-in-time delivery is reshaping supply chain dynamics, encouraging manufacturers to optimize their operations and logistics. For international buyers, particularly in regions like South Africa and Vietnam, understanding local market nuances and establishing strong supplier relationships can yield significant advantages in terms of cost efficiency and product availability.
How Important Is Sustainability and Ethical Sourcing in the Laser Cutter Industry?
Sustainability and ethical sourcing are becoming paramount in the laser cutter manufacturing sector. As global awareness of environmental issues rises, buyers are increasingly scrutinizing the environmental impact of their suppliers. Laser cutter manufacturers are adopting sustainable practices by utilizing energy-efficient technologies and sourcing materials from responsible suppliers. This shift not only meets regulatory requirements but also aligns with the values of environmentally-conscious businesses.
The importance of ethical supply chains cannot be overstated. Buyers are looking for manufacturers that prioritize transparency and sustainability in their operations. Certifications such as ISO 14001 for environmental management and adherence to the UN Sustainable Development Goals are becoming essential criteria for procurement decisions. Furthermore, utilizing green materials and technologies, such as recycled components and eco-friendly packaging, can enhance a company’s reputation and appeal to a broader customer base, particularly in European markets where sustainability is often a purchasing criterion.
What Is the Evolution of the Laser Cutter Manufacturing Sector?
The laser cutter manufacturing sector has evolved significantly since its inception in the late 1960s. Initially developed for industrial applications, laser cutting technology has seen rapid advancements in precision, speed, and versatility. The introduction of fiber lasers in the 2000s marked a turning point, offering enhanced performance and cost-effectiveness compared to traditional CO2 lasers.
This evolution has made laser cutting accessible to a wider range of industries, including automotive, aerospace, and textiles, fostering innovation and new applications. For B2B buyers, understanding this historical context is crucial in recognizing the capabilities and potential of modern laser cutting solutions, enabling informed decisions in sourcing and investment. As the sector continues to innovate, staying abreast of technological trends will be essential for buyers aiming to maintain a competitive edge in their respective markets.
Frequently Asked Questions (FAQs) for B2B Buyers of laser cutter manufacturer
-
How do I choose the right laser cutter manufacturer for my business needs?
Choosing the right laser cutter manufacturer involves assessing several key factors. Start by evaluating the manufacturer’s experience and reputation in the industry. Look for customer reviews and case studies that demonstrate their capability in delivering high-quality products. Additionally, consider their technological advancements, support services, and customization options to ensure they can meet your specific requirements. It is also wise to request samples or demonstrations to gauge performance before making a commitment. -
What types of laser cutters are best for small to medium-sized businesses?
For small to medium-sized businesses, CO2 laser cutters are often the best choice due to their versatility and cost-effectiveness. They are ideal for cutting materials like wood, acrylic, and fabric. Fiber laser cutters are also gaining popularity, particularly for metal processing, as they offer precision and speed. When selecting a model, consider the materials you will be working with, the required cutting thickness, and whether you need additional features such as engraving capabilities. -
What should I consider regarding minimum order quantities (MOQ) when sourcing laser cutters?
When sourcing laser cutters, it’s essential to inquire about the manufacturer’s minimum order quantities (MOQ). Many manufacturers have MOQs that can vary significantly based on the product type and customization options. If you are a smaller business or a startup, look for manufacturers willing to accommodate lower MOQs or flexible ordering arrangements. This approach can help you manage costs and reduce excess inventory while still obtaining high-quality machinery. -
How can I ensure quality assurance (QA) when purchasing laser cutters internationally?
To ensure quality assurance when purchasing laser cutters internationally, request documentation of the manufacturer’s quality control processes. Look for certifications such as ISO 9001, which indicates adherence to international quality standards. Additionally, consider visiting the manufacturing facility if possible, or utilizing third-party inspection services to verify product quality before shipment. Establishing a clear communication channel with the manufacturer can also help address any concerns regarding quality. -
What payment terms should I negotiate with laser cutter manufacturers?
Negotiating payment terms with laser cutter manufacturers is crucial for managing cash flow. Common terms include a deposit upon order confirmation, followed by the balance before shipment. Explore options for letters of credit or payment through escrow services to enhance security. Additionally, inquire about discounts for early payment or bulk orders. Clear and mutually agreed-upon payment terms can build trust and ensure a smoother transaction process. -
What logistics considerations should I be aware of when importing laser cutters?
When importing laser cutters, logistics play a vital role in ensuring timely delivery and cost management. Consider the shipping methods available (air freight vs. sea freight) based on your urgency and budget. Familiarize yourself with customs regulations in your country to avoid unexpected delays or fees. Additionally, engage a reliable freight forwarder who can handle all aspects of logistics, including documentation and delivery to your facility. -
How can I assess the technical support offered by laser cutter manufacturers?
Assessing technical support from laser cutter manufacturers is essential for long-term operational success. Inquire about their support services, including installation, training, and ongoing maintenance. Check if they offer remote assistance or on-site support for troubleshooting issues. A manufacturer with a robust support system can help minimize downtime and ensure that your equipment operates efficiently. Look for reviews or testimonials from other customers regarding their experiences with the manufacturer’s support team. -
What are the common challenges faced when sourcing laser cutters internationally, and how can I overcome them?
Common challenges when sourcing laser cutters internationally include language barriers, cultural differences, and varying quality standards. To overcome these, work with local intermediaries who understand both the market and the manufacturer. Conduct thorough research to understand the supplier’s background and reputation. Establish clear communication and expectations from the outset to minimize misunderstandings. Additionally, consider starting with smaller orders to test the relationship before committing to larger purchases.
Important Disclaimer & Terms of Use
⚠️ Important Disclaimer
The information provided in this guide, including content regarding manufacturers, technical specifications, and market analysis, is for informational and educational purposes only. It does not constitute professional procurement advice, financial advice, or legal advice.
While we have made every effort to ensure the accuracy and timeliness of the information, we are not responsible for any errors, omissions, or outdated information. Market conditions, company details, and technical standards are subject to change.
B2B buyers must conduct their own independent and thorough due diligence before making any purchasing decisions. This includes contacting suppliers directly, verifying certifications, requesting samples, and seeking professional consultation. The risk of relying on any information in this guide is borne solely by the reader.
Strategic Sourcing Conclusion and Outlook for laser cutter manufacturer
In conclusion, the strategic sourcing of laser cutters has become an essential component for B2B buyers looking to enhance operational efficiency and competitiveness across various sectors. By understanding the nuances of the laser cutting market, including technological advancements and supplier capabilities, international buyers from regions such as Africa, South America, the Middle East, and Europe can make informed purchasing decisions.
What are the key factors to consider when sourcing laser cutters? Buyers should focus on supplier reliability, after-sales support, and the adaptability of the equipment to local manufacturing needs. Furthermore, leveraging regional trade agreements can facilitate smoother transactions and lower tariffs, enhancing overall cost-effectiveness.
As we look to the future, the demand for laser cutting technology is poised for growth, driven by innovations in automation and materials. B2B buyers are encouraged to engage with manufacturers who not only meet current specifications but also demonstrate a commitment to future advancements. By prioritizing strategic sourcing, companies can position themselves to capitalize on emerging opportunities in the global market.
Now is the time to act; evaluate your sourcing strategies and align them with leading laser cutter manufacturers to ensure your business remains competitive in an evolving landscape.