Discover Top Benefits of Sourcing Encoder Manufacturer (2025)
Introduction: Navigating the Global Market for encoder manufacturer
Navigating the complexities of sourcing high-quality encoder manufacturers can be a daunting task for international B2B buyers, especially those operating in diverse markets like Africa, South America, the Middle East, and Europe. Encoders play a critical role in converting physical signals into electrical ones, essential for applications ranging from robotics to CNC machinery. This guide aims to demystify the encoder market by providing comprehensive insights into various encoder types, including incremental and absolute encoders, and their specific applications across industries.
Understanding the intricacies of encoder specifications, such as accuracy, resolution, and signal output types, is crucial for making informed purchasing decisions. Additionally, we will explore the essential criteria for vetting suppliers, including assessing quality certifications, lead times, and after-sales support. Cost considerations will also be addressed, enabling buyers to evaluate the total cost of ownership rather than just initial purchase prices.
By equipping B2B buyers with actionable knowledge on these critical aspects, this guide empowers them to navigate the global encoder market effectively. Whether you are in Australia, Thailand, or any other region, our insights will help you streamline your sourcing process, ensuring you choose the right encoder manufacturer that meets your operational needs and budget constraints.
Understanding encoder manufacturer Types and Variations
Type Name | Key Distinguishing Features | Primary B2B Applications | Brief Pros & Cons for Buyers |
---|---|---|---|
Incremental Encoder | Outputs pulses corresponding to movement; lacks position memory | CNC machinery, robotics, conveyor systems | Pros: Cost-effective, simple design. Cons: Requires homing after power loss. |
Absolute Encoder | Provides unique position value for every position | Robotics, aerospace, automotive applications | Pros: No need for reference points. Cons: Generally more expensive. |
Optical Encoder | Uses light to detect position; high precision | Industrial automation, medical devices | Pros: High accuracy and resolution. Cons: Sensitive to dust and dirt. |
Magnetic Encoder | Utilizes magnetic fields for position sensing | Automotive, consumer electronics, robotics | Pros: Robust against environmental conditions. Cons: Limited resolution compared to optical types. |
Capacitive Encoder | Measures changes in capacitance for position detection | Automation, textile machinery, positioning systems | Pros: Non-contact measurement, durable. Cons: Affected by environmental factors like humidity. |
What are the Characteristics of Incremental Encoders?
Incremental encoders are designed to generate a series of pulses as the shaft rotates, translating angular movement into digital signals. They are widely used in CNC machinery and robotics due to their simplicity and cost-effectiveness. However, they do not retain position information once power is lost, necessitating a homing process to establish a reference point. When purchasing, consider the required resolution and signal output type, as these factors impact overall performance in specific applications.
How Do Absolute Encoders Stand Out?
Absolute encoders offer a unique output for every position, allowing for precise measurement without the need for a reference point. This feature is particularly beneficial in applications like robotics and aerospace, where knowing the exact position is critical. While they tend to be more expensive than incremental types, their ability to maintain position information through power cycles can justify the investment. Buyers should assess the resolution and communication protocols to ensure compatibility with existing systems.
What Makes Optical Encoders a Preferred Choice?
Optical encoders utilize light to detect position changes and are known for their high precision and resolution. They are commonly employed in industrial automation and medical devices where accuracy is paramount. The main drawback is their sensitivity to dust and dirt, which can affect performance. When considering optical encoders, B2B buyers should evaluate environmental conditions and maintenance needs to ensure long-term reliability.
Why Choose Magnetic Encoders?
Magnetic encoders leverage magnetic fields to determine position, making them suitable for various applications, including automotive and consumer electronics. Their robustness against environmental factors like dust and moisture makes them a reliable choice for challenging conditions. However, they may offer lower resolution compared to optical encoders. Buyers should weigh the operational environment and required accuracy when selecting magnetic encoders.
What are the Advantages of Capacitive Encoders?
Capacitive encoders measure changes in capacitance to detect position, providing a non-contact solution that enhances durability. They are used in automation and textile machinery, where wear and tear can significantly impact performance. However, their sensitivity to environmental factors like humidity can be a concern. B2B purchasers should consider the specific application environment and ensure that capacitive encoders meet operational requirements for reliability and accuracy.
Related Video: What is Encoder?
Key Industrial Applications of encoder manufacturer
Industry/Sector | Specific Application of encoder manufacturer | Value/Benefit for the Business | Key Sourcing Considerations for this Application |
---|---|---|---|
Manufacturing | CNC Machining | Increases precision and efficiency in manufacturing processes. | Accuracy of measurement, compatibility with existing machinery, and maintenance support. |
Robotics | Robotic Arm Control | Enhances automation and productivity in assembly lines. | Type of encoder (incremental or absolute), environmental conditions, and integration capabilities. |
Automotive | Vehicle Positioning Systems | Improves safety and reliability in navigation systems. | Compliance with industry standards, durability, and response time. |
Packaging | Automated Packaging Systems | Streamlines operations and reduces labor costs. | Speed of operation, ease of installation, and adaptability to different packaging types. |
Renewable Energy | Wind Turbine Positioning | Maximizes energy capture and operational efficiency. | Tolerance to environmental factors, energy output monitoring, and maintenance needs. |
How is Encoder Technology Used in Manufacturing?
In the manufacturing sector, encoders are vital for CNC (Computer Numerical Control) machines, which require precise control of position and speed. By converting physical motion into electrical signals, encoders ensure that machines operate with high accuracy, reducing waste and improving product quality. Buyers from regions like Africa and South America should prioritize encoders that offer reliability and ease of integration with existing systems, while also considering local support for maintenance and repairs.
What Role Do Encoders Play in Robotics?
In robotics, encoders are used extensively for controlling robotic arms and other automated systems. They provide feedback on the position and speed of moving parts, allowing for precise manipulation of objects. This capability is crucial in industries where automation boosts productivity, such as assembly lines. International buyers must assess the encoder’s compatibility with various robotic systems and its ability to function in diverse environmental conditions, particularly in the Middle East where temperatures can be extreme.
How Are Encoders Applied in the Automotive Industry?
The automotive sector utilizes encoders in vehicle positioning systems, enhancing navigation and safety features. These systems rely on accurate data regarding the vehicle’s position to function effectively. For B2B buyers in Europe, it’s important to consider encoders that meet stringent automotive industry standards for durability and performance, as well as those that can provide real-time data processing for improved decision-making.
What Benefits Do Encoders Provide in Packaging Automation?
In packaging industries, encoders are crucial for automated systems that require precise control over packaging processes. They help in synchronizing the machinery involved in filling, sealing, and labeling products, leading to increased efficiency and reduced labor costs. Buyers should focus on encoders that offer high-speed performance and flexibility to adapt to various packaging formats, ensuring that their operations can scale as demand fluctuates.
How Do Encoders Enhance Renewable Energy Systems?
Encoders are also essential in renewable energy applications, particularly in wind turbines where they assist in optimizing blade positioning for maximum energy capture. By providing precise angular feedback, they help in adjusting the turbine’s orientation to the wind direction. Buyers from regions investing in renewable energy, such as Africa and South America, should consider encoders that can withstand harsh weather conditions and provide reliable performance over time, ensuring long-term operational efficiency.
3 Common User Pain Points for ‘encoder manufacturer’ & Their Solutions
Scenario 1: Ensuring Compatibility with Existing Systems
The Problem: B2B buyers often encounter compatibility issues when integrating new encoders into their existing machinery or systems. This can arise from varying output formats, signal types, or communication protocols that encoders utilize. For instance, a manufacturing company in South America may find that their new absolute encoder does not communicate effectively with their existing PLC system, leading to production delays and increased costs.
The Solution: To mitigate compatibility challenges, buyers should conduct thorough research before selecting an encoder. This involves understanding the specifications of both the new encoder and the existing systems. Buyers should request detailed technical documentation from the encoder manufacturer, including information about output types (e.g., TTL, HTL), communication protocols (e.g., CAN, RS-232), and power supply requirements. Additionally, engaging with the manufacturer’s technical support team can provide insights into compatibility and integration processes. Buyers should also consider modular encoder options that allow for easy upgrades or adjustments without overhauling the entire system.
Scenario 2: Managing Maintenance and Downtime Costs
The Problem: Maintenance and unexpected downtime are significant concerns for businesses relying on encoders for precision tasks, such as in automation or robotics. For example, a European company might face substantial losses due to the failure of a rotary encoder, which halts operations and requires immediate replacement. This situation is compounded by the lack of readily available spare parts, leading to prolonged downtime.
The Solution: To address maintenance issues, buyers should prioritize sourcing encoders from manufacturers that offer reliable support and robust warranties. Implementing a predictive maintenance strategy can also help mitigate downtime. This involves using software tools that monitor encoder performance and provide alerts for potential failures based on historical data. Establishing a partnership with the encoder manufacturer for regular maintenance checks and training on proper usage can significantly reduce unexpected failures. Additionally, buyers should maintain an inventory of critical spare parts to ensure quick replacements when needed, minimizing operational disruptions.
Scenario 3: Navigating Pricing and Quality Trade-offs
The Problem: International B2B buyers frequently struggle with balancing cost and quality when sourcing encoders. A buyer from Africa may be tempted to select a low-cost encoder to cut expenses, only to find that its performance is subpar, resulting in inaccuracies and inefficiencies in their processes. This trade-off can lead to higher long-term costs that outweigh initial savings.
The Solution: To navigate the pricing and quality dilemma, buyers should conduct a comprehensive cost-benefit analysis that considers not only the initial purchase price but also the encoder’s long-term performance, reliability, and support services. Engaging in discussions with multiple manufacturers can provide insights into the value offered at various price points. Buyers should seek reviews and testimonials from other users within their industry to gauge reliability and performance. Additionally, opting for manufacturers that provide transparent pricing structures and detailed specifications can help buyers make informed decisions. Investing in a slightly higher-priced encoder with a proven track record can ultimately lead to greater operational efficiency and reduced costs over time.
Strategic Material Selection Guide for encoder manufacturer
What Are the Key Materials Used in Encoder Manufacturing?
When selecting materials for encoder manufacturing, understanding the properties and applications of various materials is crucial for ensuring optimal performance and longevity. Here, we analyze four common materials used in encoders: aluminum, stainless steel, plastic, and glass. Each material has distinct characteristics that influence the encoder’s performance, durability, and suitability for specific applications.
How Does Aluminum Benefit Encoder Manufacturing?
Aluminum is widely used in encoder housings due to its lightweight nature and excellent corrosion resistance. With a temperature rating typically ranging from -40°C to 120°C, aluminum can withstand various operational environments.
Pros: Its lightweight nature reduces shipping costs, and its corrosion resistance makes it ideal for outdoor applications. Additionally, aluminum is relatively easy to machine, which simplifies manufacturing processes.
Cons: While aluminum is durable, it may not withstand extreme pressure as effectively as some other materials. It can also be more expensive than plastics, particularly for high-grade aluminum alloys.
Impact on Application: Aluminum encoders are suitable for environments where weight is a concern, such as in robotics and aerospace applications. However, they may not be the best choice for highly corrosive environments unless treated.
Considerations for International Buyers: Buyers from regions like Africa and the Middle East should ensure that aluminum encoders comply with local corrosion resistance standards, such as ASTM B117 for salt spray testing.
What Advantages Does Stainless Steel Offer for Encoders?
Stainless steel is another popular material choice for encoders, particularly in industrial applications. Known for its high strength and excellent corrosion resistance, stainless steel can operate effectively in harsh environments, with temperature ratings often exceeding 150°C.
Pros: The durability of stainless steel makes it suitable for heavy-duty applications, and its resistance to corrosion ensures longevity in challenging conditions.
Cons: The primary drawback is its higher cost compared to aluminum and plastic. Additionally, the manufacturing complexity increases due to the need for specialized machining equipment.
Impact on Application: Stainless steel encoders are ideal for applications involving exposure to chemicals or extreme temperatures, such as in food processing or oil and gas industries.
Considerations for International Buyers: Buyers in Europe should look for compliance with EU regulations regarding material safety, while those in South America may need to consider local standards for industrial equipment.
How Do Plastics Compare in Encoder Manufacturing?
Plastics, particularly engineering plastics like polycarbonate and nylon, are often used in encoder components due to their lightweight and cost-effective nature. They typically have temperature ratings up to 100°C.
Pros: Plastics are generally less expensive than metals and can be molded into complex shapes, allowing for innovative designs. Their lightweight nature also contributes to reduced shipping costs.
Cons: While plastics offer good resistance to moisture and some chemicals, they may not be suitable for high-temperature or high-pressure applications. They are also less durable than metals, which can lead to shorter lifespans.
Impact on Application: Plastic encoders are best for low-stress environments, such as consumer electronics or light industrial applications where weight and cost are primary concerns.
Considerations for International Buyers: Buyers should ensure that the plastics used comply with relevant safety standards, such as REACH in Europe, which regulates the use of chemicals.
What Role Does Glass Play in Encoder Manufacturing?
Glass is primarily used in optical encoders, where its clarity and precision are essential for accurate readings. Glass components can withstand high temperatures and offer excellent dimensional stability.
Pros: The transparency of glass allows for precise light transmission, which is critical for optical encoding. It is also resistant to temperature fluctuations.
Cons: Glass is fragile and can break easily, making it less suitable for rugged applications. Additionally, the manufacturing process can be more complex and costly.
Impact on Application: Glass is ideal for high-precision applications, such as in robotics and medical devices, where accuracy is paramount.
Considerations for International Buyers: Buyers should consider the fragility of glass in transportation and installation, particularly in regions with challenging logistics.
Summary Table of Material Selection for Encoder Manufacturing
Material | Typical Use Case for encoder manufacturer | Key Advantage | Key Disadvantage/Limitation | Relative Cost (Low/Med/High) |
---|---|---|---|---|
Aluminum | Lightweight encoders for robotics | Corrosion-resistant and easy to machine | Less effective under extreme pressure | Medium |
Stainless Steel | Heavy-duty industrial applications | High strength and excellent corrosion resistance | Higher cost and complex manufacturing | High |
Plastic | Consumer electronics and light industrial | Cost-effective and lightweight | Less durable and temperature-sensitive | Low |
Glass | High-precision optical encoders | Excellent clarity and precision | Fragile and higher manufacturing complexity | Medium |
This guide provides international B2B buyers with essential insights into material selection for encoders, helping them make informed decisions based on their specific application needs and regional standards.
In-depth Look: Manufacturing Processes and Quality Assurance for encoder manufacturer
What Are the Main Stages in the Manufacturing Process of Encoders?
Manufacturing encoders involves several critical stages, each crucial for ensuring the quality and functionality of the final product. The primary stages of the manufacturing process include:
-
Material Preparation
The initial step involves selecting high-quality raw materials, such as metals for housing and plastics for internal components. Suppliers should ensure materials meet specific industry standards to guarantee durability and performance. -
Forming
This stage encompasses various techniques such as machining, injection molding, and stamping. Precision machining is often employed to create intricate parts, while injection molding is used for mass-producing plastic components. The choice of technique depends on the encoder type—incremental or absolute—and its intended application. -
Assembly
During assembly, components such as sensors, code discs, and housing are brought together. This phase may involve automated assembly lines or manual assembly, depending on the complexity and volume of production. Ensuring that each component is aligned correctly is vital for the encoder’s accuracy. -
Finishing
The finishing stage includes surface treatments, such as anodizing or painting, to enhance corrosion resistance and aesthetic appeal. Additionally, any necessary calibration is performed to ensure that the encoder meets specified performance standards.
What Quality Control Practices Are Essential for Encoder Manufacturers?
Quality control (QC) is integral to the manufacturing process of encoders. The following practices are vital for maintaining high standards:
-
International Standards Compliance
Encoder manufacturers should adhere to international standards such as ISO 9001, which outlines the requirements for a quality management system. Compliance with these standards helps ensure consistent product quality and customer satisfaction. -
Industry-Specific Certifications
Depending on the application, encoders may require additional certifications. For example, products used in medical or aerospace applications might need to comply with CE or API standards, ensuring they meet specific safety and performance criteria. -
Quality Checkpoints
– Incoming Quality Control (IQC): This involves inspecting raw materials and components upon arrival at the manufacturing facility to ensure they meet specified standards.
– In-Process Quality Control (IPQC): Regular checks during the manufacturing process help identify issues early, reducing waste and ensuring compliance with quality standards.
– Final Quality Control (FQC): Before shipping, each encoder undergoes thorough testing to verify functionality, accuracy, and overall quality.
How Do Encoder Manufacturers Conduct Testing to Ensure Quality?
Testing is a critical component of the quality assurance process. Common testing methods for encoders include:
-
Functional Testing
This involves verifying that the encoder performs its intended functions, such as outputting accurate signals corresponding to its position or rotation. -
Environmental Testing
Encoders are tested for performance under various environmental conditions, including temperature extremes, humidity, and exposure to dust or moisture. This ensures reliability in diverse applications. -
Durability Testing
Manufacturers often conduct fatigue testing to evaluate how well encoders can withstand repeated use. This is especially important for encoders used in demanding industrial environments.
How Can B2B Buyers Verify the Quality Control Processes of Encoder Suppliers?
International B2B buyers must take proactive steps to verify the quality control processes of encoder manufacturers. Here are several strategies:
-
Supplier Audits
Conducting on-site audits of potential suppliers can provide insights into their manufacturing processes and quality control measures. This allows buyers to assess compliance with international standards and certifications. -
Requesting Quality Reports
Buyers should request detailed quality reports, including results from IQC, IPQC, and FQC stages. These reports can provide a clear picture of the supplier’s commitment to quality. -
Third-Party Inspections
Engaging third-party inspection services can help validate the supplier’s claims about their quality control processes. Independent inspectors can provide unbiased assessments of the manufacturing and testing procedures.
What Are the Quality Control Nuances for International Buyers from Africa, South America, the Middle East, and Europe?
For international buyers, particularly those from Africa, South America, the Middle East, and Europe, understanding the nuances of quality control is essential. Here are key considerations:
-
Cultural and Regulatory Differences
Buyers should be aware of cultural differences that may influence communication and business practices. Additionally, varying regulatory requirements across regions can impact product standards and certifications. -
Logistics and Supply Chain Considerations
Understanding the logistics of shipping products from manufacturers to their region is crucial. Buyers should inquire about the supplier’s ability to meet delivery timelines and handle customs processes efficiently. -
Post-Purchase Support
Quality assurance doesn’t end at delivery. Buyers should ensure that suppliers offer robust post-purchase support, including warranty and repair services. This is particularly important for encoders used in critical applications where downtime can be costly.
Conclusion
In conclusion, understanding the manufacturing processes and quality assurance practices is vital for international B2B buyers looking to procure encoders. By focusing on the main stages of manufacturing, adhering to international standards, and implementing thorough testing and verification methods, buyers can ensure they partner with reliable suppliers that meet their quality expectations. Engaging in proactive measures such as supplier audits and requesting detailed quality reports will further safeguard their investments in encoder technology.
Practical Sourcing Guide: A Step-by-Step Checklist for ‘encoder manufacturer’
Introduction
This practical sourcing guide is designed to assist international B2B buyers in procuring high-quality encoders from reliable manufacturers. Encoders are essential components used in various applications, including robotics and CNC machinery. A systematic approach to sourcing can ensure you find a manufacturer that meets your technical and business needs.
Step 1: Define Your Technical Specifications
Before reaching out to potential suppliers, it is crucial to clearly outline your technical requirements. This includes the type of encoder (incremental or absolute), resolution, output signal type (analog or digital), and environmental conditions (temperature and humidity levels).
- Why it matters: A precise specification helps manufacturers understand your needs and provides a basis for comparing offers from different suppliers.
- Tip: Consider involving your engineering team in this process to ensure all technical aspects are covered.
Step 2: Research Potential Manufacturers
Conduct thorough research to identify manufacturers specializing in encoder production. Look for companies with a solid reputation and extensive experience in the industry.
- Why it matters: Reliable manufacturers are more likely to deliver quality products and services, reducing the risk of operational disruptions.
- Tip: Utilize online directories, trade associations, and industry forums to compile a list of potential suppliers.
Step 3: Evaluate Supplier Capabilities
Before making a decision, assess the manufacturing capabilities of each supplier. Key aspects to consider include production capacity, technology used, and quality control processes.
- Why it matters: A supplier’s capacity and technology directly impact their ability to meet your volume and quality requirements.
- Tip: Request detailed information on their manufacturing processes and certifications (ISO, CE, etc.).
Step 4: Verify Supplier Certifications
Ensure that the manufacturers you consider have the necessary certifications to operate in your industry. This may include ISO certifications, compliance with safety standards, and environmental management certifications.
- Why it matters: Certifications provide assurance that the manufacturer adheres to industry standards and best practices, which can significantly reduce risks associated with product quality.
- Tip: Ask for copies of certifications and verify them with the issuing bodies.
Step 5: Request Samples and Conduct Testing
Once you narrow down your options, request samples of the encoders you are interested in. Conduct rigorous testing to ensure they meet your specifications and quality standards.
- Why it matters: Testing samples allows you to evaluate the performance and reliability of the encoders in your specific applications before making a bulk purchase.
- Tip: Develop a testing protocol that includes all critical performance parameters relevant to your application.
Step 6: Negotiate Terms and Conditions
After selecting a supplier, engage in negotiations regarding pricing, delivery schedules, payment terms, and warranties. Ensure that all terms are documented clearly in a contract.
- Why it matters: Clear agreements help prevent misunderstandings and disputes later in the procurement process.
- Tip: Be open to discussing terms that benefit both parties, fostering a long-term business relationship.
Step 7: Establish a Communication Plan
Once the procurement process is underway, establish a clear communication plan with the manufacturer. Regular updates and open lines of communication can help address any potential issues promptly.
- Why it matters: Effective communication is key to ensuring smooth collaboration and timely responses to any challenges that arise during production and delivery.
- Tip: Set regular check-ins and updates to stay informed about the manufacturing progress and any changes in timelines.
By following this checklist, B2B buyers from Africa, South America, the Middle East, and Europe can confidently navigate the sourcing process for encoders, ensuring they find the right manufacturer to meet their business needs.
Comprehensive Cost and Pricing Analysis for encoder manufacturer Sourcing
Understanding the cost structure and pricing strategies in the encoder manufacturing sector is crucial for international B2B buyers, particularly those from Africa, South America, the Middle East, and Europe. This analysis will explore the various cost components, price influencers, and practical tips for negotiating favorable terms.
What Are the Key Cost Components in Encoder Manufacturing?
The total cost of manufacturing encoders can be broken down into several key components:
-
Materials: The cost of raw materials such as metals, plastics, and electronic components forms the foundation of the encoder’s price. High-quality materials often lead to better performance and durability, impacting overall costs.
-
Labor: Labor costs vary significantly based on the region. Skilled labor is essential for precision engineering, especially in sectors requiring high accuracy, such as robotics and CNC machinery.
-
Manufacturing Overhead: This includes expenses related to facilities, utilities, equipment maintenance, and administrative costs. Overhead can be a significant portion of the total cost, particularly in countries with higher operational costs.
-
Tooling: Specialized tools and machinery for producing encoders can require substantial initial investment. This cost is often amortized over production runs, influencing pricing for bulk orders.
-
Quality Control (QC): Ensuring that encoders meet specified standards incurs costs related to testing and inspection processes. Rigorous QC practices are crucial in maintaining product reliability and performance.
-
Logistics: Shipping and transportation costs can vary depending on the distance, mode of transport, and Incoterms agreed upon. For international buyers, these costs can significantly affect the final purchase price.
-
Margin: Manufacturers typically add a profit margin to cover their risks and ensure business sustainability. This margin can vary based on competition, market demand, and the value added by the manufacturer.
How Do Price Influencers Affect Encoder Costs?
Several factors influence the pricing strategies of encoder manufacturers:
-
Volume/MOQ (Minimum Order Quantity): Larger orders often come with discounts due to economies of scale. Buyers should assess their needs to determine the most cost-effective order size.
-
Specifications and Customization: Custom encoders tailored to specific applications can incur higher costs due to unique design and manufacturing processes. Buyers should clearly define their requirements to avoid unnecessary expenses.
-
Materials and Quality Certifications: The choice of materials directly affects pricing. Additionally, products certified to international standards may command higher prices but offer assurance of quality and reliability.
-
Supplier Factors: The reputation, reliability, and production capabilities of the supplier can influence pricing. Established manufacturers may charge more due to their experience and quality assurance processes.
-
Incoterms: Understanding the delivery terms is essential. Terms like FOB (Free on Board) or CIF (Cost, Insurance, and Freight) can significantly impact the total cost, as they dictate who bears various costs during transportation.
What Are the Best Buyer Tips for Negotiating Encoder Prices?
-
Leverage Volume Discounts: When possible, consolidate orders to meet MOQ thresholds and negotiate better pricing.
-
Focus on Total Cost of Ownership (TCO): Evaluate not just the purchase price but also the long-term costs associated with maintenance, operation, and potential failures. A slightly higher initial investment may lead to lower overall costs.
-
Negotiate Payment Terms: Flexible payment options can ease cash flow constraints. Discussing terms upfront can lead to better financial arrangements.
-
Request Sample Products: Before committing to large orders, request samples to assess quality and performance. This step helps avoid costly mistakes.
-
Stay Informed About Market Trends: Understanding market dynamics, such as shifts in material costs or technological advancements, can empower buyers during negotiations.
Conclusion
Navigating the complexities of encoder sourcing requires a thorough understanding of the cost structure and pricing strategies employed by manufacturers. By considering the various cost components and price influencers, international B2B buyers can make informed decisions that optimize their procurement processes. Always remember to approach negotiations with a clear strategy focused on achieving the best overall value.
Alternatives Analysis: Comparing encoder manufacturer With Other Solutions
Understanding Alternatives for Encoder Solutions
In today’s rapidly evolving technology landscape, international B2B buyers must explore various solutions to meet their operational needs. While encoder manufacturers offer specialized devices for converting physical signals into electrical signals, several alternative technologies can provide similar functionalities. This section compares encoder manufacturers with two viable alternatives: Sensor Fusion Technology and Digital Signal Processing (DSP).
Comparison Table of Encoder Solutions
Comparison Aspect | Encoder Manufacturer | Sensor Fusion Technology | Digital Signal Processing (DSP) |
---|---|---|---|
Performance | High accuracy and reliability | Variable, depends on sensors | High processing speed and flexibility |
Cost | Moderate to high | Often lower due to common sensors | Varies widely based on implementation |
Ease of Implementation | Requires specific integration | Can be complex, requires calibration | Moderate, needs expertise for setup |
Maintenance | Regular calibration and checks | Depends on sensors used | Low, mostly software updates |
Best Use Case | Robotics, CNC machines | IoT applications, autonomous systems | Audio processing, signal analysis |
In-Depth Analysis of Alternatives
What is Sensor Fusion Technology and How Does It Compare?
Sensor fusion technology combines data from multiple sensors to achieve more accurate and comprehensive information about an environment. For instance, in robotics, it integrates readings from encoders, accelerometers, and gyroscopes to improve navigation and positioning.
Pros:
– Cost-effective: Utilizing existing sensors can reduce overall costs.
– Enhanced accuracy: Combining data can result in superior precision compared to single sensors.
Cons:
– Complexity: Implementing sensor fusion may require sophisticated algorithms and calibration, increasing the initial setup complexity.
– Dependency on multiple sensors: The performance is contingent on the reliability of each sensor involved.
How Does Digital Signal Processing (DSP) Serve as an Alternative?
Digital Signal Processing (DSP) refers to the manipulation of signals after they have been converted into a digital format. DSPs are widely used in various applications, including audio processing, telecommunications, and robotics.
Pros:
– Flexibility: DSP systems can be programmed to handle various types of signal processing tasks, making them versatile for different applications.
– Speed: High-speed processing capabilities allow for real-time data analysis and response.
Cons:
– Initial investment: Depending on the application, DSP systems can involve significant upfront costs.
– Expertise required: Implementation often necessitates specialized knowledge, which may not be readily available in all organizations.
Conclusion: Choosing the Right Solution for Your Needs
When selecting between an encoder manufacturer and alternative solutions such as sensor fusion technology or DSP, B2B buyers should consider their specific operational requirements, budget constraints, and available technical expertise. If high accuracy and reliability are paramount, traditional encoders may be the best choice. However, for organizations looking to leverage existing sensors and reduce costs, sensor fusion could provide a compelling alternative. Meanwhile, if versatility and speed are critical, DSP might be the ideal solution. Ultimately, the decision should align with the company’s long-term goals and operational framework, ensuring that the chosen technology integrates seamlessly into existing systems.
Essential Technical Properties and Trade Terminology for encoder manufacturer
What Are the Key Technical Properties of Encoders That B2B Buyers Should Consider?
When selecting encoders, international B2B buyers must understand several critical specifications that can impact performance, reliability, and compatibility with existing systems. Here are some essential technical properties:
-
Resolution
– Definition: Resolution refers to the smallest detectable change in position that an encoder can measure. It is typically expressed in pulses per revolution (PPR) for rotary encoders or in millimeters for linear encoders.
– B2B Importance: Higher resolution allows for more precise control in applications such as robotics and CNC machinery, leading to improved product quality and operational efficiency. -
Accuracy and Tolerance
– Definition: Accuracy indicates how close the encoder’s output is to the actual position, while tolerance refers to the allowable deviation from the specified accuracy.
– B2B Importance: Ensuring high accuracy and tight tolerances is crucial for applications that require precision, such as aerospace and medical devices. Buyers should evaluate these specifications to avoid costly errors in manufacturing processes. -
Signal Output Type
– Definition: Encoders can provide various types of signal outputs, including analog (e.g., sine/cosine) and digital (e.g., quadrature signals).
– B2B Importance: Understanding signal types is vital for compatibility with control systems. For instance, digital signals are often preferred for their noise resistance and ease of integration into modern systems. -
Operating Temperature Range
– Definition: This specification defines the temperature limits within which the encoder can operate effectively.
– B2B Importance: Buyers operating in extreme environments (e.g., industrial plants in tropical or arctic regions) must ensure that the encoders can withstand the specific temperature ranges to maintain performance and longevity. -
Power Supply Requirements
– Definition: This refers to the voltage and current specifications needed for the encoder to function, commonly ranging from 5V to 24V DC.
– B2B Importance: Understanding power supply requirements helps buyers ensure that their encoder selections are compatible with existing electrical systems, avoiding the need for additional power supply modifications. -
Durability and IP Rating
– Definition: The durability of an encoder often correlates with its Ingress Protection (IP) rating, which indicates the level of protection against dust and moisture.
– B2B Importance: For applications in harsh environments, such as outdoor or wet settings, a higher IP rating is essential to prevent failure and reduce maintenance costs.
What Are Common Trade Terms in the Encoder Manufacturing Industry?
Familiarity with industry terminology can help B2B buyers navigate the procurement process more effectively. Here are several common trade terms:
-
OEM (Original Equipment Manufacturer)
– Definition: An OEM is a company that produces parts or equipment that may be marketed by another manufacturer.
– Importance: Understanding OEM relationships can help buyers identify reliable suppliers who produce high-quality components tailored to specific applications. -
MOQ (Minimum Order Quantity)
– Definition: MOQ refers to the minimum number of units that a supplier is willing to sell in a single order.
– Importance: Knowing the MOQ is crucial for budgeting and inventory management, especially for smaller businesses that may not require large quantities. -
RFQ (Request for Quotation)
– Definition: An RFQ is a document sent by a buyer to suppliers requesting a quote for specific products or services.
– Importance: Submitting RFQs can help buyers compare pricing, lead times, and terms from multiple suppliers, facilitating more informed purchasing decisions. -
Incoterms (International Commercial Terms)
– Definition: Incoterms are a set of predefined international rules that define the responsibilities of buyers and sellers in the shipping process.
– Importance: Understanding Incoterms can help B2B buyers clarify shipping costs, risk transfer, and delivery obligations, reducing potential disputes in international transactions. -
Lead Time
– Definition: Lead time is the time it takes from placing an order until the product is delivered.
– Importance: Knowing lead times is essential for planning production schedules and ensuring timely project completion, especially in industries with tight deadlines.
By understanding these technical properties and trade terminologies, B2B buyers can make informed decisions, optimize their supply chain, and enhance operational efficiency when sourcing encoders for their applications.
Navigating Market Dynamics and Sourcing Trends in the encoder manufacturer Sector
What Are the Key Trends Influencing the Encoder Manufacturer Market?
The encoder manufacturer sector is experiencing significant transformation driven by technological advancements and shifting market demands. One of the foremost global drivers is the increasing automation across various industries, such as manufacturing, robotics, and automotive sectors. This trend is particularly pronounced in regions like Africa and South America, where industrialization is rapidly advancing. As businesses seek to enhance operational efficiency, the demand for high-precision encoders has surged, making it essential for international B2B buyers to understand the latest technologies, such as IoT-enabled encoders that facilitate real-time monitoring and control.
Emerging sourcing trends also play a crucial role in shaping the market dynamics. B2B buyers are increasingly prioritizing suppliers that offer customizable encoder solutions tailored to specific applications. Additionally, the rise of Industry 4.0 has led to a growing interest in smart encoders that integrate seamlessly with digital systems, providing better data analytics and performance tracking. Furthermore, sustainability considerations are influencing sourcing decisions, with buyers seeking partners committed to eco-friendly practices and materials.
In Europe and the Middle East, regulatory pressures are pushing manufacturers to adopt more stringent quality and safety standards, further complicating sourcing strategies. Buyers must navigate these regulations while ensuring they partner with reliable manufacturers who can meet compliance requirements. Overall, understanding these market dynamics is essential for international B2B buyers looking to make informed sourcing decisions in the encoder manufacturer sector.
How Important Is Sustainability and Ethical Sourcing in the Encoder Manufacturing Sector?
Sustainability and ethical sourcing have become paramount in the encoder manufacturing sector, reflecting a broader trend across industries. The environmental impact of production processes is under increasing scrutiny, with buyers keen to partner with manufacturers that prioritize green practices. This includes the use of recyclable materials and energy-efficient production methods, which can significantly reduce the carbon footprint associated with encoder manufacturing.
Ethical supply chains are equally important, as buyers are more aware of the social implications of their sourcing decisions. Manufacturers that adhere to fair labor practices and have transparent supply chains not only enhance their brand reputation but also attract conscientious buyers. Certifications such as ISO 14001 for environmental management and ISO 45001 for occupational health and safety are becoming essential credentials for suppliers aiming to demonstrate their commitment to sustainability.
Moreover, the demand for “green” materials in the production of encoders, such as biodegradable plastics or recycled metals, is on the rise. B2B buyers should actively seek suppliers that can provide these sustainable options to align with their corporate social responsibility (CSR) goals. By integrating sustainability into their sourcing strategies, international buyers can contribute to a healthier planet while also meeting the expectations of their stakeholders.
How Has the Encoder Manufacturing Sector Evolved Over Time?
The evolution of the encoder manufacturing sector has been marked by significant technological advancements and changing market demands. Initially, encoders were primarily mechanical devices used for simple position tracking. However, with the advent of digital technology in the late 20th century, encoders transformed into sophisticated electronic devices capable of high precision and speed.
As industries began to embrace automation, the demand for more advanced encoder solutions surged, leading to the development of various types, including incremental and absolute encoders. Over the years, manufacturers have integrated features such as increased durability, enhanced resolution, and improved signal processing capabilities, allowing encoders to be used in a wider range of applications.
Today, the focus has shifted towards smart encoders that can communicate with other devices within an IoT framework, enabling real-time data sharing and analytics. This evolution not only reflects technological progress but also highlights the increasing complexity of industrial systems, necessitating continuous innovation in encoder design and functionality. For B2B buyers, understanding this historical context is crucial for making informed purchasing decisions that align with current technological trends.
Frequently Asked Questions (FAQs) for B2B Buyers of encoder manufacturer
-
How do I choose the right encoder for my application?
Choosing the right encoder depends on several factors including the type of application, required precision, and environmental conditions. For applications requiring high accuracy, consider absolute encoders, which provide unique position values for each position. If your application involves continuous rotation, incremental encoders may be suitable. Additionally, assess the encoder’s output type (analog or digital), resolution, and compatibility with your existing systems. Always evaluate the working temperature range and environmental factors to ensure longevity and reliability. -
What are the key specifications to look for when sourcing encoders?
When sourcing encoders, key specifications include resolution, measurement accuracy, output type (incremental vs. absolute), and environmental ratings such as IP (Ingress Protection) level. Also, consider the encoder’s supply voltage requirements, maximum speed, and acceleration capabilities. Understanding your application’s specific needs, such as size constraints and installation conditions, will help in selecting the right encoder. Make sure to request detailed datasheets from manufacturers to compare specifications effectively. -
What customization options are available for encoders?
Many encoder manufacturers offer customization options such as different mounting configurations, shaft sizes, and output types tailored to specific applications. Customization can also extend to housing materials for harsh environments or specific connector types to meet your integration requirements. When engaging with manufacturers, clearly communicate your needs and ask about their capabilities for modifications. This can significantly enhance compatibility and performance in your specific operational context. -
What is the minimum order quantity (MOQ) for encoders?
Minimum order quantities (MOQ) can vary widely among encoder manufacturers, often ranging from a few pieces to several hundred units. MOQs may depend on the type of encoder, customization, and production capacity of the manufacturer. When sourcing, inquire about MOQs to ensure they align with your project requirements and budget. Some manufacturers may be open to smaller orders, especially for standard models, while custom orders might necessitate higher MOQs. -
What payment terms can I expect when purchasing encoders internationally?
Payment terms for international purchases of encoders typically vary by manufacturer and may include options like advance payment, letters of credit, or payment upon delivery. It is crucial to discuss and negotiate terms upfront to avoid misunderstandings. Additionally, consider payment methods that offer buyer protection, such as PayPal or escrow services, particularly for large transactions. Always clarify currency exchange rates and any potential fees associated with international transactions. -
How can I ensure quality assurance when sourcing encoders?
To ensure quality assurance when sourcing encoders, request detailed quality control (QC) protocols from manufacturers, including testing standards and certifications (e.g., ISO 9001). Inquire about the testing process for each batch and whether they offer warranty or return policies. If possible, arrange for third-party inspections or audits before finalizing orders. Building a strong relationship with suppliers can also facilitate better transparency regarding their production quality. -
What logistics considerations should I keep in mind when importing encoders?
When importing encoders, consider logistics aspects such as shipping methods, lead times, and customs regulations specific to your region. Evaluate the total landed cost, including freight, insurance, and import duties. Partnering with a reliable freight forwarder can streamline the shipping process and help navigate complex customs procedures. Additionally, ensure that the manufacturer provides necessary documentation for customs clearance to avoid delays.
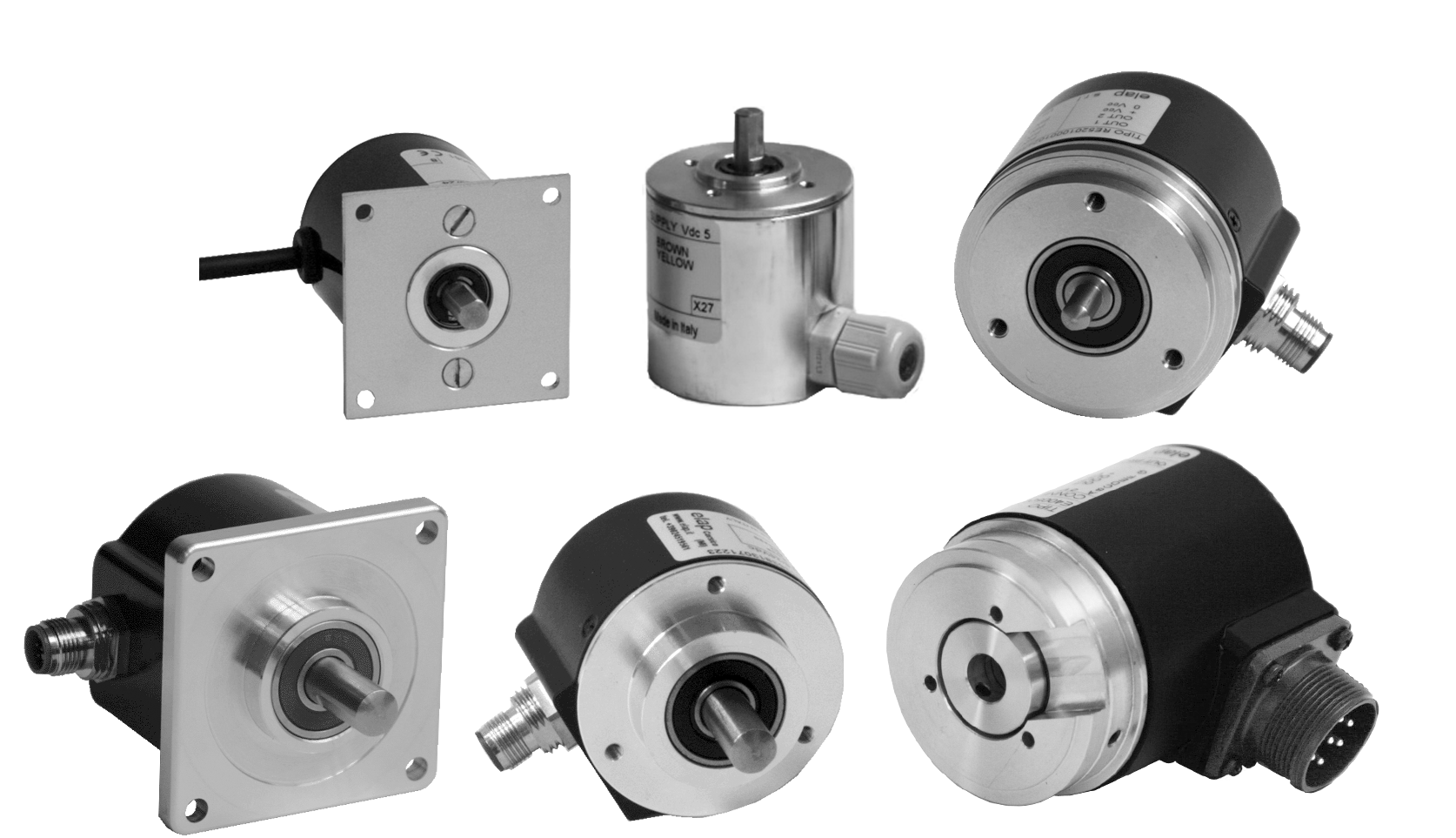
A stock image related to encoder manufacturer.
- How do I evaluate the reliability of an encoder manufacturer?
To evaluate the reliability of an encoder manufacturer, research their industry reputation, years of experience, and customer reviews. Look for manufacturers with certifications and compliance with international standards, as this indicates a commitment to quality. Engaging in direct communication can also provide insights into their customer service and responsiveness. Request references from previous clients, especially those in similar industries, to gauge their satisfaction with the products and support received.
Important Disclaimer & Terms of Use

A stock image related to encoder manufacturer.
⚠️ Important Disclaimer
The information provided in this guide, including content regarding manufacturers, technical specifications, and market analysis, is for informational and educational purposes only. It does not constitute professional procurement advice, financial advice, or legal advice.
While we have made every effort to ensure the accuracy and timeliness of the information, we are not responsible for any errors, omissions, or outdated information. Market conditions, company details, and technical standards are subject to change.
B2B buyers must conduct their own independent and thorough due diligence before making any purchasing decisions. This includes contacting suppliers directly, verifying certifications, requesting samples, and seeking professional consultation. The risk of relying on any information in this guide is borne solely by the reader.
Strategic Sourcing Conclusion and Outlook for encoder manufacturer
In today’s rapidly evolving industrial landscape, strategic sourcing has emerged as a critical component for businesses seeking to enhance operational efficiency and competitive advantage in encoder manufacturing. By aligning purchasing strategies with organizational goals, B2B buyers can secure high-quality encoders that meet their specific needs while optimizing costs. Key takeaways for international buyers include the importance of understanding different encoder types—incremental versus absolute—and their respective applications in various sectors such as robotics, CNC machinery, and motor control.
How can international B2B buyers leverage strategic sourcing in encoder procurement? By fostering relationships with reliable manufacturers and exploring options across diverse markets—particularly in Africa, South America, the Middle East, and Europe—buyers can gain access to innovative technologies and competitive pricing.
As the demand for precision and reliability in automation systems continues to rise, now is the time for businesses to refine their sourcing strategies. Embrace the opportunity to evaluate potential suppliers, assess their capabilities, and invest in partnerships that will drive long-term success. Take the next step in enhancing your encoder procurement process and position your organization for future growth.