Discover Top Benefits from a Transducer Manufacturer (2025)
Introduction: Navigating the Global Market for transducer manufacturer
In today’s rapidly evolving industrial landscape, sourcing reliable transducer manufacturers can be a daunting challenge for international B2B buyers. Transducers play a crucial role in converting physical quantities into electrical signals, essential for a wide range of applications from automation to environmental monitoring. However, navigating the complexities of different transducer types, their applications, and the myriad of suppliers can overwhelm even the most experienced procurement professionals. This comprehensive guide aims to demystify the global market for transducer manufacturers, providing insights into various types of transducers, their operational principles, and critical applications across industries.
Buyers will learn how to effectively vet suppliers, compare costs, and ensure quality while considering specific regional factors that may influence their purchasing decisions. With a focus on the unique needs of businesses in Africa, South America, the Middle East, and Europe—including key markets such as France and Thailand—this guide empowers B2B buyers to make informed decisions. By equipping readers with actionable strategies and knowledge, we aim to streamline the sourcing process, ultimately facilitating successful partnerships with transducer manufacturers that meet their operational demands.
Understanding transducer manufacturer Types and Variations
Type Name | Key Distinguishing Features | Primary B2B Applications | Brief Pros & Cons for Buyers |
---|---|---|---|
Active Transducers | No external power required; direct conversion of energy | Temperature measurement, pressure sensing | Pros: Lower operational costs; simpler installation. Cons: Limited to specific applications. |
Passive Transducers | Requires external power; measures physical changes | Flow measurement, strain gauge applications | Pros: Versatile; can measure a wide range of variables. Cons: Higher energy costs; more complex setup. |
Digital Transducers | Converts signals to digital format for easy integration | Automation systems, IoT applications | Pros: High accuracy; easy integration with digital systems. Cons: May require specific interfaces. |
Analog Transducers | Provides continuous output signal proportional to input | Industrial automation, environmental monitoring | Pros: Simplicity in design; direct measurement. Cons: Susceptible to noise; limited data processing. |
Specialized Transducers | Designed for specific applications (e.g., piezoelectric) | Aerospace, medical devices, automotive testing | Pros: Tailored performance; high precision. Cons: Higher costs; limited availability. |
What Are Active Transducers and Their B2B Relevance?
Active transducers are devices that convert physical quantities into electrical signals without needing external power. They are particularly suitable for applications like temperature measurement and pressure sensing. B2B buyers should consider the simplicity of installation and lower operational costs associated with these devices. However, their application scope is limited, making them ideal for specific scenarios rather than general use.
How Do Passive Transducers Differ in Application?
Passive transducers require an external power source to function and are adept at measuring changes in physical quantities such as flow or strain. They are versatile and can be used in various applications across industries. Buyers should weigh the benefits of their broad applicability against the potential for higher energy costs and a more complex installation process.
What Advantages Do Digital Transducers Offer to Businesses?
Digital transducers provide a significant advantage by converting analog signals into digital formats, facilitating easy integration with automation systems and IoT applications. Their high accuracy and compatibility with modern technology make them appealing for industries looking to enhance their digital infrastructure. However, buyers should be aware of the potential need for specific interfaces, which may add to the overall cost.
Why Choose Analog Transducers for Industrial Automation?
Analog transducers generate continuous output signals that are directly proportional to the measured input. They are commonly used in industrial automation and environmental monitoring due to their straightforward design. While they offer ease of use, buyers must consider their susceptibility to noise and the limitations in data processing capabilities when making purchasing decisions.
What Makes Specialized Transducers Unique?
Specialized transducers are designed for specific applications, such as piezoelectric transducers in aerospace or medical devices. These devices offer tailored performance and high precision, making them invaluable in niche markets. However, buyers should be prepared for potentially higher costs and limited availability, which can affect procurement strategies.
Related Video: Pressure Sensor, Transducer, and Transmitter Explained | Application of Each
Key Industrial Applications of transducer manufacturer
Industry/Sector | Specific Application of transducer manufacturer | Value/Benefit for the Business | Key Sourcing Considerations for this Application |
---|---|---|---|
Manufacturing | Pressure measurement in hydraulic systems | Enhanced safety and efficiency in production processes | Accuracy, durability, and compatibility with existing systems |
Energy | Temperature monitoring in power generation | Improved operational efficiency and reduced downtime | High-temperature tolerance and reliability under extreme conditions |
Automotive | Displacement measurement in vehicle assembly lines | Increased precision in manufacturing and quality control | Calibration accuracy and integration with automation systems |
Healthcare | Monitoring patient vitals using bio-transducers | Real-time data collection for improved patient outcomes | Biocompatibility and adherence to regulatory standards |
Agriculture | Soil moisture level sensing for irrigation systems | Optimized water usage and increased crop yield | Environmental resilience and adaptability to various soil types |
How Are Transducers Used in the Manufacturing Industry?
In the manufacturing sector, transducers play a vital role in pressure measurement within hydraulic systems. By converting physical pressure into electrical signals, these devices enable real-time monitoring and control of hydraulic pressure, which is crucial for ensuring safety and operational efficiency. For international buyers, particularly in regions like Africa and South America, sourcing high-quality pressure transducers that offer durability and accuracy is essential. The ability to withstand harsh environments while maintaining precision can significantly enhance production processes.
What is the Role of Transducers in the Energy Sector?
In the energy industry, transducers are extensively used for temperature monitoring in power generation facilities. By converting temperature readings into electrical signals, these transducers help operators maintain optimal operating conditions, thereby improving overall efficiency and reducing downtime. For buyers in Europe and the Middle East, it is imperative to consider transducers that can withstand high temperatures and operate reliably under extreme conditions. This ensures compliance with safety regulations and enhances the longevity of equipment.
How Do Transducers Improve Automotive Manufacturing?
Transducers are crucial in the automotive industry, particularly for displacement measurement in vehicle assembly lines. They provide precise measurements of component positioning, which is essential for maintaining high standards of quality control during manufacturing. International buyers, especially from regions like Europe and Thailand, should prioritize sourcing transducers that offer calibration accuracy and seamless integration with automation systems. This can lead to significant improvements in production efficiency and product quality.
What Are the Applications of Transducers in Healthcare?
In healthcare, bio-transducers are used for monitoring patient vitals, converting physiological signals into electrical outputs for real-time data collection. This application is vital for improving patient outcomes through timely interventions. Buyers from diverse regions must ensure that the transducers meet biocompatibility standards and comply with regulatory requirements, which is crucial for patient safety and device efficacy.
How Can Transducers Benefit Agricultural Practices?
In agriculture, transducers are employed to sense soil moisture levels in irrigation systems, allowing for optimized water usage. This technology helps farmers increase crop yield while conserving resources. For international buyers, particularly in regions facing water scarcity, sourcing resilient transducers that can adapt to various soil types is critical. Such devices not only enhance agricultural productivity but also contribute to sustainable farming practices.
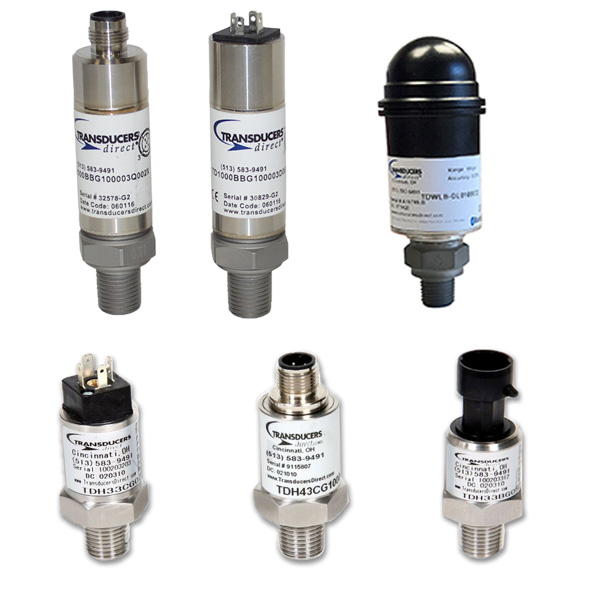
A stock image related to transducer manufacturer.
3 Common User Pain Points for ‘transducer manufacturer’ & Their Solutions
Scenario 1: Difficulty in Selecting the Right Type of Transducer for Specific Applications
The Problem: Many B2B buyers, particularly in sectors like manufacturing and energy, often struggle with selecting the appropriate type of transducer for their specific applications. With various types available—such as temperature, pressure, and displacement transducers—making the right choice can be overwhelming. This confusion is compounded by the lack of detailed application insights provided by manufacturers, leading to misapplication, increased costs, and operational inefficiencies.
The Solution: To effectively navigate this challenge, buyers should start by clearly defining their application requirements, including the physical quantities to be measured, environmental conditions, and desired accuracy levels. It’s crucial to engage directly with transducer manufacturers to seek tailored recommendations based on these criteria. When sourcing, look for manufacturers that provide comprehensive product catalogs with specifications, application notes, and case studies. Additionally, consider requesting samples or conducting pilot tests to validate the performance of the transducers in real-world conditions before making a bulk purchase. This proactive approach can significantly reduce the risk of poor selection and enhance operational efficiency.
Scenario 2: Overcoming Calibration and Maintenance Challenges
The Problem: Another common pain point for B2B buyers is the ongoing calibration and maintenance of transducers. Many organizations find that their transducers drift over time, leading to inaccurate readings that can compromise process integrity and safety. This issue is particularly prevalent in industries like oil and gas, where precise measurements are critical. Buyers often face the dilemma of either investing in costly calibration services or risking operational disruptions due to erroneous data.
The Solution: To address this issue, buyers should prioritize transducers that offer built-in self-diagnostics and calibration features. When evaluating manufacturers, inquire about their calibration protocols and the frequency of maintenance required for their devices. Establish a routine maintenance schedule and utilize software tools that can integrate with your existing systems to monitor transducer performance in real-time. Moreover, consider partnering with manufacturers that provide training on best practices for transducer maintenance and calibration. This not only empowers your team but also ensures that the transducers remain accurate and reliable over their lifespan, ultimately saving costs and enhancing safety.
Scenario 3: Navigating Supply Chain Delays and Quality Assurance
The Problem: Supply chain disruptions have become increasingly common, affecting the timely delivery of transducers and components. Buyers from regions such as Africa and South America may experience longer lead times, which can stall projects and impact operational timelines. Additionally, concerns regarding the quality of transducers—especially when sourced from multiple suppliers—can lead to inconsistencies in performance and reliability.
The Solution: To mitigate supply chain risks, it is advisable for buyers to establish relationships with multiple transducer manufacturers and distributors. This diversification can help ensure a steady supply of quality products even if one supplier faces delays. When selecting manufacturers, prioritize those with a proven track record of quality assurance, including certifications like ISO 9001. Implement a robust supplier evaluation process that considers lead times, quality control measures, and customer service responsiveness. Additionally, consider investing in local suppliers or regional manufacturers to reduce lead times and support local economies. By adopting these strategies, buyers can secure a reliable supply chain while maintaining high-quality standards for their transducer needs.
Strategic Material Selection Guide for transducer manufacturer
What Are the Common Materials Used in Transducer Manufacturing?
When selecting materials for transducer manufacturing, it is essential to consider key properties such as temperature and pressure ratings, corrosion resistance, and compatibility with specific media. Here, we analyze four common materials: stainless steel, ceramics, polymers, and piezoelectric materials, focusing on their properties, advantages, disadvantages, and implications for international B2B buyers.
How Does Stainless Steel Perform as a Material for Transducers?
Key Properties: Stainless steel is known for its excellent corrosion resistance and high strength, making it suitable for harsh environments. It typically withstands temperatures up to 800°C and pressures of several hundred bar, depending on the specific grade.
Pros & Cons: The durability of stainless steel is a significant advantage, as it can endure extreme conditions without degrading. However, it can be more expensive than other materials and may require complex manufacturing processes, such as machining and welding.
Impact on Application: Stainless steel is compatible with various media, including corrosive fluids, making it ideal for pressure and temperature transducers in industries like oil and gas, food processing, and pharmaceuticals.
Considerations for International Buyers: Buyers from Africa, South America, the Middle East, and Europe should ensure compliance with international standards such as ASTM and DIN for material specifications. Additionally, local sourcing may reduce costs and lead times.
What Are the Benefits of Using Ceramics in Transducer Design?
Key Properties: Ceramics exhibit high thermal stability and excellent electrical insulation properties. They can operate at temperatures exceeding 1000°C and are chemically inert, making them suitable for aggressive environments.
Pros & Cons: The primary advantage of ceramics is their ability to maintain performance in extreme conditions. However, they can be brittle, which poses challenges during manufacturing and handling. Additionally, the cost of high-performance ceramics can be relatively high.
Impact on Application: Ceramics are often used in high-temperature applications, such as thermocouples and piezoelectric sensors, where precision and stability are critical.
Considerations for International Buyers: Buyers should consider the availability of ceramic components in their regions and ensure that they meet relevant industry standards. Understanding the local market’s preferences for ceramic materials can also influence procurement decisions.
How Do Polymers Compare as a Material for Transducers?
Key Properties: Polymers offer flexibility, lightweight characteristics, and good resistance to chemical corrosion. They typically operate effectively at lower temperatures, usually below 100°C, and can handle moderate pressures.
Pros & Cons: The affordability and ease of manufacturing polymers make them attractive for mass production. However, their lower thermal and mechanical stability compared to metals and ceramics may limit their application in high-stress environments.
Impact on Application: Polymers are commonly used in applications where weight savings and cost efficiency are crucial, such as in consumer electronics and automotive sensors.
Considerations for International Buyers: Buyers should be aware of the specific polymer grades suitable for their applications and ensure compliance with local regulations regarding material safety and environmental impact.
Why Are Piezoelectric Materials Essential in Transducer Manufacturing?
Key Properties: Piezoelectric materials, such as quartz and certain ceramics, convert mechanical stress into electrical signals. They can operate effectively in a wide temperature range, depending on the specific material used.
Pros & Cons: The primary advantage of piezoelectric materials is their sensitivity and response time, making them ideal for dynamic measurements. However, they can be sensitive to temperature variations and may require careful handling during manufacturing.
Impact on Application: These materials are widely used in applications such as accelerometers and pressure sensors, where rapid response to changes is critical.
Considerations for International Buyers: Buyers should evaluate the sourcing of piezoelectric materials, as availability may vary by region. Additionally, understanding the specific performance characteristics required for their applications is crucial for selecting the right material.
Summary Table of Material Selection for Transducer Manufacturing
Material | Typical Use Case for transducer manufacturer | Key Advantage | Key Disadvantage/Limitation | Relative Cost (Low/Med/High) |
---|---|---|---|---|
Stainless Steel | Pressure and temperature transducers | Excellent corrosion resistance and durability | Higher cost and complex manufacturing | High |
Ceramics | High-temperature sensors | High thermal stability and insulation | Brittle and expensive | High |
Polymers | Consumer electronics and automotive sensors | Cost-effective and lightweight | Lower thermal/mechanical stability | Low |
Piezoelectric Materials | Accelerometers and pressure sensors | High sensitivity and fast response | Sensitive to temperature variations | Medium |
This strategic material selection guide provides B2B buyers with crucial insights into the properties, advantages, and limitations of various materials used in transducer manufacturing. Understanding these factors will aid in making informed decisions tailored to specific applications and regional requirements.
In-depth Look: Manufacturing Processes and Quality Assurance for transducer manufacturer
What Are the Main Stages of the Manufacturing Process for Transducers?
The manufacturing process of transducers involves several critical stages that ensure the final product meets the required specifications and performance standards. Understanding these stages is essential for B2B buyers looking to source high-quality transducers.
1. Material Preparation
The first step in transducer manufacturing is material preparation, which includes selecting the appropriate raw materials based on the type of transducer being produced. Common materials include ceramics, metals, and polymers. Each material has unique properties that impact the transducer’s performance, such as sensitivity and temperature range.
During this stage, materials undergo inspections to ensure they meet quality standards. Suppliers should provide Material Safety Data Sheets (MSDS) and certificates of compliance to assure buyers of the material’s quality and safety.
2. Forming Techniques Used in Transducer Production
Once the materials are prepared, they undergo various forming techniques to create the desired shapes and structures. Common methods include:
- Molding: Used for polymer-based transducers, this technique allows for complex shapes and can be done through injection or compression molding.
- Machining: Involves cutting materials into precise dimensions. This is vital for metal transducers where high precision is required.
- Laminating: Often used in piezoelectric transducers, where layers of materials are bonded to enhance performance.
Each technique has its advantages and impacts the transducer’s functionality, so it’s important for buyers to understand the processes their suppliers employ.
3. Assembly Process for Transducers
After forming, the next stage is assembly, where various components are brought together. This can involve:
- Wiring and Soldering: Connecting electrical components is crucial, especially for active transducers that require precise electrical pathways.
- Calibration: Ensuring that the transducer measures accurately is done at this stage. Calibration should be performed using standardized equipment and procedures.
Buyers should inquire about the assembly processes used by suppliers, as these can significantly influence the reliability and accuracy of the final product.
4. Finishing Touches in Transducer Manufacturing
The finishing stage includes surface treatments and protective coatings to enhance durability and performance. Techniques such as anodizing, plating, or applying protective films are common. This not only improves the aesthetic quality but also protects against environmental factors that could affect performance.
How Is Quality Assurance Implemented in Transducer Manufacturing?
Quality assurance (QA) is a critical component of the transducer manufacturing process. It ensures that the products meet both international standards and customer expectations.
What Are Relevant International Standards for Transducer Quality?
B2B buyers should be familiar with several international quality standards that transducer manufacturers often adhere to, such as:
- ISO 9001: This standard outlines the criteria for a quality management system, ensuring consistent quality in products and services.
- CE Marking: Indicates conformity with health, safety, and environmental protection standards for products sold within the European Economic Area.
- API Standards: Particularly relevant for transducers used in oil and gas applications, these standards ensure reliability and safety in extreme conditions.
These certifications provide a benchmark for quality, helping buyers assess potential suppliers.
What Are the Key Quality Control Checkpoints in Transducer Manufacturing?
Quality control (QC) checkpoints are essential for maintaining product integrity. Key checkpoints include:
- Incoming Quality Control (IQC): Involves inspecting raw materials before production begins. This step ensures that only materials meeting specified standards are used.
- In-Process Quality Control (IPQC): Continuous monitoring during production helps identify and rectify issues early in the process, reducing waste and rework.
- Final Quality Control (FQC): The final inspection before products are shipped. This includes performance testing to confirm that transducers operate within specified parameters.
B2B buyers should ask suppliers about their QC processes and how they ensure compliance with these checkpoints.
What Common Testing Methods Are Used to Ensure Transducer Quality?
Testing is a crucial aspect of quality assurance for transducers. Common methods include:
- Functional Testing: Ensures that the transducer operates as intended under various conditions.
- Environmental Testing: Checks performance under extreme temperatures, humidity, and pressure.
- Electromagnetic Compatibility Testing: Assesses how well the transducer can operate in the presence of electromagnetic interference.
Understanding these testing methods helps buyers evaluate the reliability of the transducers they are considering.
How Can B2B Buyers Verify Supplier Quality Control?
B2B buyers must take proactive steps to verify the quality control practices of their suppliers. Here are some effective strategies:
- Audits: Conducting on-site audits provides insight into the manufacturing processes and QC practices. Buyers can observe operations firsthand and ensure compliance with standards.
- Quality Reports: Requesting detailed reports on quality metrics, including defect rates and testing outcomes, can help buyers make informed decisions.
- Third-Party Inspections: Engaging independent inspectors can provide unbiased assessments of a supplier’s manufacturing and quality assurance processes.
What Are the Quality Control and Certification Nuances for International Buyers?
For international buyers, understanding the nuances of quality control and certification is essential. Different regions may have varying requirements, which can impact sourcing decisions.
- Regional Standards: Buyers in Africa and South America may need to familiarize themselves with local standards that could affect product acceptance.
- Customs Regulations: Compliance with import regulations in different countries is crucial. Buyers should ensure that their suppliers can provide the necessary documentation for customs clearance.
By being aware of these factors, B2B buyers can better navigate the complexities of international sourcing for transducers.
Practical Sourcing Guide: A Step-by-Step Checklist for ‘transducer manufacturer’
In the competitive landscape of international B2B procurement, sourcing transducer manufacturers requires a strategic approach. This guide outlines a step-by-step checklist designed to assist buyers, particularly from Africa, South America, the Middle East, and Europe, in making informed decisions. Each step emphasizes critical considerations to ensure a successful procurement process.
Step 1: Define Your Technical Specifications
Before initiating your search for transducer manufacturers, clearly outline your technical requirements. This includes the type of transducer needed (e.g., temperature, pressure, or displacement), the measurement range, and any specific industry standards that must be met. A well-defined specification helps in filtering potential suppliers who can meet your precise needs, saving time and resources.
Step 2: Research Potential Suppliers
Conduct thorough research to identify suitable transducer manufacturers. Utilize industry directories, trade shows, and online platforms to compile a list of potential suppliers. Focus on companies with a proven track record in your industry and region. Analyzing their product offerings and market presence will provide insights into their capabilities and reliability.
Step 3: Evaluate Supplier Certifications and Compliance
Verify that the manufacturers you are considering hold relevant certifications (e.g., ISO 9001, CE marking). These certifications indicate adherence to quality management systems and regulatory compliance, which is critical for ensuring the reliability of transducers in your applications. Ensure that the suppliers comply with both local and international standards pertinent to your industry.
Step 4: Request Samples and Prototypes
Before finalizing a supplier, request samples or prototypes of the transducers you intend to procure. Testing these samples in your operational environment will help you assess their performance and compatibility with your systems. This step is crucial in identifying any potential issues early in the procurement process, reducing the risk of costly mistakes.
Step 5: Inquire About Lead Times and Production Capacity
Understanding the supplier’s lead times and production capacity is essential for planning your procurement timeline. Inquire about their manufacturing processes, order fulfillment capabilities, and how they manage large or customized orders. Suppliers who can demonstrate flexibility and efficiency in their production processes are more likely to meet your demands promptly.
Step 6: Assess After-Sales Support and Warranty Terms
Evaluate the after-sales support offered by the manufacturer, including warranty terms and technical assistance. Reliable support can significantly impact your operational efficiency, especially if issues arise post-purchase. Ensure the manufacturer provides adequate training, documentation, and access to customer service to address any concerns swiftly.
Step 7: Review Pricing and Payment Terms
Finally, compare the pricing structures and payment terms of different suppliers. While cost is a crucial factor, it should not compromise quality or service. Look for transparent pricing models and favorable payment options that align with your budget and cash flow requirements. Negotiating terms can lead to better overall value and strengthen supplier relationships.
By following this checklist, B2B buyers can effectively navigate the complexities of sourcing transducer manufacturers. Each step is designed to help ensure that the selected supplier not only meets technical and operational requirements but also contributes to the overall success of your business.
Comprehensive Cost and Pricing Analysis for transducer manufacturer Sourcing
What Are the Key Cost Components in Transducer Manufacturing?
Understanding the cost structure of transducer manufacturing is vital for B2B buyers aiming to optimize their sourcing strategy. The primary cost components include:
-
Materials: The choice of materials significantly influences the overall cost. For instance, high-quality metals or specialized polymers used in transducers can raise expenses. Always assess the material specifications to ensure they meet your application needs without unnecessary costs.
-
Labor: Skilled labor is essential for the precision required in manufacturing transducers. Labor costs can vary significantly based on geographic location and the complexity of the production process.
-
Manufacturing Overhead: This includes costs associated with factory operations, such as utilities, rent, and equipment maintenance. High overheads can drive up the price, particularly in regions with elevated operational costs.
-
Tooling: Investment in tooling is necessary for producing custom transducer designs. While initial tooling costs can be high, they may reduce per-unit costs for larger orders.
-
Quality Control (QC): Implementing rigorous QC processes ensures that the transducers meet performance standards. However, this adds to the overall cost. Buyers should inquire about QC practices to gauge potential impacts on pricing.
-
Logistics: Transportation and shipping costs are vital, especially for international buyers. The choice of shipping method and distance from the manufacturing site can significantly affect the total cost.
-
Margin: Manufacturers typically include a profit margin in their pricing, which can vary based on market competition and the perceived value of their products.
How Do Price Influencers Affect Transducer Sourcing?
When sourcing transducers, several factors can influence pricing:
-
Volume/MOQ (Minimum Order Quantity): Larger orders often lead to lower per-unit costs due to economies of scale. Buyers should consider their demand forecasts to negotiate better pricing.
-
Specifications and Customization: Custom designs or specific performance criteria can increase costs. Clearly defining your requirements can help avoid unnecessary expenses.
-
Material Quality and Certifications: Higher quality materials or certifications (e.g., ISO standards) may lead to increased costs. Assess the necessity of these features based on your application requirements.
-
Supplier Factors: The supplier’s reputation, location, and production capacity can influence pricing. Established suppliers may charge a premium for reliability and quality assurance.
-
Incoterms: Understanding shipping terms (e.g., FOB, CIF) is crucial for international buyers. These terms dictate who is responsible for shipping costs and risks, impacting the overall price.
What Are the Best Buyer Tips for Cost-Efficient Transducer Sourcing?
B2B buyers, particularly from Africa, South America, the Middle East, and Europe, should consider these strategies for effective sourcing:
-
Negotiate Terms: Don’t hesitate to negotiate prices and terms with suppliers. Building a relationship can lead to better deals in future transactions.
-
Evaluate Total Cost of Ownership (TCO): Beyond initial purchase price, consider maintenance, operational efficiency, and potential downtime costs. A cheaper transducer may lead to higher TCO if it requires frequent replacements or repairs.
-
Understand Pricing Nuances for International Buyers: Currency fluctuations, import duties, and local taxes can affect the final cost. Always factor these into your budget when sourcing internationally.
-
Research and Compare Suppliers: Conduct thorough research to compare various suppliers and their offerings. Look for reviews, case studies, or testimonials that can provide insight into their reliability and service quality.
-
Leverage Local Regulations: Familiarize yourself with local regulations regarding imports and product certifications. Compliance can save costs related to fines or delays.
Conclusion
In summary, a comprehensive understanding of cost components, price influencers, and strategic sourcing tips can significantly enhance the purchasing experience for international B2B buyers of transducers. Always approach negotiations and supplier evaluations with a keen eye on both immediate costs and long-term value. Remember, prices can vary widely based on numerous factors, and it’s crucial to maintain flexibility and adapt your strategy as needed.
Alternatives Analysis: Comparing transducer manufacturer With Other Solutions
Introduction: Understanding Alternatives in Transducer Solutions
When considering transducer solutions, international B2B buyers must evaluate various alternatives that meet their specific operational needs. Transducers are essential for converting physical quantities into electrical signals, but other technologies may offer similar functionalities with distinct advantages. By analyzing alternatives, buyers can make informed decisions that align with their requirements for performance, cost, and ease of implementation.
Comparison Table of Transducer Manufacturer and Alternative Solutions
Comparison Aspect | Transducer Manufacturer | Alternative 1: Sensors | Alternative 2: Data Acquisition Systems |
---|---|---|---|
Performance | High accuracy and reliability in measurements | Varies; typically good but can lack precision | Very high performance, especially for complex data |
Cost | Moderate to high, depending on type | Generally lower cost | Higher initial investment but cost-effective over time |
Ease of Implementation | Requires technical expertise for setup | Easier to implement, often plug-and-play | Complex setup requiring trained personnel |
Maintenance | Regular calibration needed | Low maintenance, often self-calibrating | Moderate maintenance, dependent on system complexity |
Best Use Case | Industrial automation, precise measurement needs | General monitoring, home automation | Large-scale data collection and analysis |
In-Depth Analysis of Alternatives
How Do Sensors Compare to Transducer Manufacturers?
Sensors are devices that detect physical phenomena and convert them into signals. While they can serve similar purposes as transducers, their performance varies significantly depending on the type and application. Sensors are generally more cost-effective and easier to implement, making them suitable for applications like home automation or simple monitoring tasks. However, their accuracy may not match that of specialized transducers, especially in industrial settings where precision is critical. Buyers seeking low-cost solutions for non-critical applications may find sensors a practical alternative.
What Are the Benefits of Data Acquisition Systems Over Transducer Manufacturers?
Data acquisition systems (DAQ) represent a more sophisticated alternative that integrates multiple sensors and transducers to collect and analyze data from various sources. They offer exceptional performance and are ideal for applications requiring detailed analysis and real-time data processing. However, DAQ systems typically come with a higher initial cost and a complex setup process that may necessitate trained personnel. For organizations that need to monitor multiple variables and perform extensive data analysis, DAQ systems can be more beneficial in the long run despite the upfront investment.
Conclusion: How to Choose the Right Solution for Your Needs
Selecting the right solution among transducer manufacturers and their alternatives depends on the specific requirements of your operations. Consider the performance needs, budget constraints, and ease of implementation when making your choice. If precision is paramount, investing in a reputable transducer manufacturer may be the best option. Conversely, for less critical applications, sensors or data acquisition systems can provide adequate functionality at a lower cost. By carefully analyzing these alternatives, B2B buyers can optimize their investment and ensure they meet their operational goals efficiently.
Essential Technical Properties and Trade Terminology for transducer manufacturer
What Are the Essential Technical Properties for Transducer Manufacturers?
When sourcing transducers, understanding their critical specifications is vital for ensuring compatibility and performance in your applications. Here are several key technical properties to consider:
1. Material Grade: Why Is It Crucial for Transducer Durability?
The material used in transducer manufacturing directly impacts its durability and performance. Common materials include stainless steel, aluminum, and various polymers. The choice of material affects factors such as thermal stability, corrosion resistance, and mechanical strength. For international buyers, especially in industries like oil and gas, automotive, or medical, selecting the appropriate material grade can significantly influence the lifespan and reliability of the transducer in harsh environments.
2. Operating Temperature Range: How Does It Affect Functionality?
Every transducer has a specified operating temperature range, which defines the extremes of environmental conditions it can withstand while maintaining accuracy. This property is especially important for applications in industries such as aerospace or manufacturing, where equipment may be exposed to extreme temperatures. Understanding this specification helps buyers ensure that the transducers will function correctly under their specific operational conditions.
3. Tolerance: What Role Does Precision Play in Measurements?
Tolerance refers to the acceptable deviation from a specified measurement. In transducers, tighter tolerances result in higher accuracy and reliability in measurements. For B2B buyers, especially those in precision-dependent sectors like pharmaceuticals or automotive, selecting transducers with appropriate tolerances is critical for maintaining quality control and compliance with industry standards.
4. Sensitivity: Why Is This Parameter Important?
Sensitivity measures how responsive a transducer is to changes in the input physical quantity. High sensitivity is essential for applications requiring precise measurements, such as pressure sensors in hydraulic systems or temperature sensors in process control. Buyers should evaluate the sensitivity specifications to ensure that the transducer meets their measurement needs effectively.
5. Response Time: How Does It Impact Performance?
Response time refers to the time taken by a transducer to respond to a change in the measured variable. For applications that require real-time monitoring, such as in automated manufacturing systems, a short response time is crucial. Understanding this parameter helps buyers select transducers that can deliver timely data, enhancing operational efficiency.
What Trade Terminology Should B2B Buyers Understand When Purchasing Transducers?
Navigating the procurement process for transducers involves familiarizing yourself with industry-specific terminology. Here are some essential terms:
1. OEM (Original Equipment Manufacturer): What Does This Mean for Your Supply Chain?
OEM refers to a company that produces parts or equipment that may be marketed by another manufacturer. In the context of transducers, an OEM may supply transducers that are integrated into larger systems or products. Understanding OEM relationships can help buyers streamline their supply chain and ensure compatibility with existing equipment.
2. MOQ (Minimum Order Quantity): How Does It Affect Procurement Decisions?
MOQ denotes the smallest number of units that a supplier is willing to sell. This term is critical for international buyers as it impacts inventory management and cash flow. Buyers should assess their needs against the MOQ requirements to avoid overcommitting or understocking.
3. RFQ (Request for Quotation): Why Is It Important in the Buying Process?
An RFQ is a document that solicits price proposals from suppliers. It is essential for comparing costs and ensuring you get the best value for your investment. Issuing an RFQ helps buyers clarify specifications and negotiate terms effectively with potential suppliers.
4. Incoterms (International Commercial Terms): How Do They Affect Shipping and Delivery?
Incoterms are a set of international trade terms that define the responsibilities of buyers and sellers in shipping agreements. Familiarity with Incoterms helps buyers understand their obligations concerning shipping costs, insurance, and risk during transit, which is crucial for international transactions.
5. Lead Time: Why Is It Critical for Project Planning?
Lead time refers to the time taken from placing an order to the delivery of goods. Understanding lead times is vital for project planning, especially for industries with strict deadlines. Buyers should discuss lead times with suppliers to ensure that transducers arrive in time for their operational needs.
By understanding these technical properties and trade terminologies, B2B buyers can make informed purchasing decisions that align with their operational requirements and industry standards.
Navigating Market Dynamics and Sourcing Trends in the transducer manufacturer Sector
What Are the Current Market Dynamics and Key Trends in the Transducer Manufacturing Sector?
The transducer manufacturing sector is experiencing significant growth, driven by various global factors. A key driver is the increasing demand for automation and control systems across industries such as manufacturing, automotive, and healthcare. For international B2B buyers, particularly from Africa, South America, the Middle East, and Europe, understanding the technological advancements in transducers is vital. Emerging trends include the integration of IoT (Internet of Things) technology, which enhances data collection and real-time monitoring capabilities. Additionally, there is a growing preference for smart transducers, which can perform advanced functions like self-calibration and predictive maintenance.
Another notable trend is the shift towards miniaturization and precision engineering in transducer design. This trend is particularly relevant for industries requiring compact and highly accurate measurement tools, such as medical devices and aerospace applications. Furthermore, sustainability is becoming a crucial factor in transducer sourcing, with manufacturers increasingly focusing on energy-efficient designs and materials that minimize environmental impact. Buyers are encouraged to seek suppliers that not only meet performance specifications but also align with these emerging trends to ensure long-term competitiveness.
How Does Sustainability Impact Sourcing in the Transducer Manufacturing Sector?
Sustainability is reshaping the landscape of B2B sourcing, particularly in the transducer manufacturing sector. The environmental impact of manufacturing processes has led to increased scrutiny from consumers and regulatory bodies alike. B2B buyers are now prioritizing suppliers that demonstrate a commitment to ethical sourcing and sustainability. This includes choosing manufacturers that utilize ‘green’ materials, such as recyclable components and low-impact manufacturing processes.
Moreover, obtaining certifications like ISO 14001 (Environmental Management) or adhering to RoHS (Restriction of Hazardous Substances) standards can significantly enhance a supplier’s appeal. These certifications not only indicate compliance with environmental regulations but also reflect a manufacturer’s dedication to reducing their carbon footprint. Buyers are encouraged to engage with suppliers who actively promote transparency in their supply chains, ensuring that their sourcing practices align with global sustainability goals. This not only mitigates environmental risks but also enhances brand reputation and customer loyalty.
What Is the Evolution of the Transducer Manufacturing Industry and Its Relevance to B2B Buyers?
The transducer manufacturing industry has evolved significantly over the past few decades, transitioning from simple mechanical devices to complex electronic systems. Early transducers were primarily mechanical and lacked the precision required for modern applications. The introduction of electronic transducers, particularly in the 20th century, revolutionized measurement and control processes across various industries. This evolution has enabled the development of highly sophisticated devices that offer greater accuracy and reliability.
For B2B buyers, understanding this evolution is crucial for making informed purchasing decisions. The current landscape features advanced transducer technologies such as MEMS (Micro-Electro-Mechanical Systems), which provide enhanced performance in compact designs. As industries continue to demand higher efficiency and smarter solutions, buyers must keep abreast of technological advancements and select suppliers who are at the forefront of innovation. Engaging with manufacturers that have a proven track record in adapting to these changes can significantly impact operational efficiency and product quality.
Frequently Asked Questions (FAQs) for B2B Buyers of transducer manufacturer
-
How do I select the right transducer manufacturer for my business needs?
Choosing the right transducer manufacturer involves evaluating several key factors. Start by assessing their expertise in your specific industry and the types of transducers you require, such as temperature, pressure, or displacement transducers. Check their certifications and compliance with international standards to ensure quality. Additionally, consider their production capacity, lead times, and ability to provide customization options. Engaging with existing customers through testimonials or case studies can provide valuable insights into their reliability and service quality. -
What are the most common types of transducers used in industrial applications?
In industrial settings, the most common types of transducers include temperature transducers (like thermocouples), pressure transducers (such as piezoresistive sensors), and flow transducers. Each type serves a specific function: temperature transducers measure thermal energy, pressure transducers monitor fluid pressures, and flow transducers track the flow rate of liquids or gases. Identifying the right type for your application is crucial, as it impacts the accuracy and efficiency of your measurement systems. -
What customization options should I look for in a transducer manufacturer?
When sourcing a transducer manufacturer, inquire about their customization capabilities. Key customization options may include specific measurement ranges, output signal types (e.g., analog or digital), housing materials, and connector types. Additionally, consider whether they can accommodate unique calibration requirements or integrate advanced features like wireless communication. A manufacturer that offers tailored solutions can significantly enhance the performance and reliability of your applications. -
What is the minimum order quantity (MOQ) for transducers from manufacturers?
Minimum order quantities (MOQ) can vary widely among transducer manufacturers, often depending on the complexity of the product and the manufacturer’s production capabilities. Some manufacturers may have MOQs as low as 10 units for standard products, while custom solutions might require larger orders. It’s advisable to discuss MOQs directly with potential suppliers to understand their policies and negotiate terms that align with your purchasing strategy. -
What payment terms should I expect when sourcing transducers internationally?
Payment terms can differ significantly among transducer manufacturers, especially in international trade. Common arrangements include upfront deposits (typically 30-50%), with the balance due upon delivery or after inspection. Some manufacturers may offer letters of credit or payment through platforms like PayPal for additional security. It’s essential to clarify these terms before finalizing your order to avoid misunderstandings and ensure smooth transactions. -
How can I ensure quality assurance (QA) when sourcing transducers?
To ensure quality assurance when sourcing transducers, request detailed information about the manufacturer’s QA processes. Look for certifications such as ISO 9001, which indicates a commitment to quality management. Inquire about their testing procedures, including calibration and performance verification, to ensure that their products meet your specifications. Additionally, consider requesting samples or conducting a factory audit to verify their quality control measures firsthand. -
What logistics considerations should I keep in mind when importing transducers?
When importing transducers, consider logistics aspects such as shipping methods, delivery times, and customs regulations. Evaluate the manufacturer’s shipping options, including air or sea freight, and their ability to handle international logistics. Ensure that they provide clear documentation for customs clearance, including invoices and certificates of origin. Additionally, factor in potential delays due to customs procedures in your delivery timeline to avoid disruptions in your supply chain. -
What are the key market trends affecting the transducer industry globally?
The transducer industry is currently influenced by several key trends, including the increasing demand for automation in manufacturing, the rise of IoT (Internet of Things) applications, and advancements in sensor technology. Manufacturers are focusing on developing more compact and efficient transducers that can integrate with digital systems. Additionally, sustainability concerns are driving innovation toward environmentally friendly materials and energy-efficient designs. Staying abreast of these trends can help B2B buyers make informed decisions and capitalize on emerging opportunities.
Important Disclaimer & Terms of Use
⚠️ Important Disclaimer
The information provided in this guide, including content regarding manufacturers, technical specifications, and market analysis, is for informational and educational purposes only. It does not constitute professional procurement advice, financial advice, or legal advice.
While we have made every effort to ensure the accuracy and timeliness of the information, we are not responsible for any errors, omissions, or outdated information. Market conditions, company details, and technical standards are subject to change.
B2B buyers must conduct their own independent and thorough due diligence before making any purchasing decisions. This includes contacting suppliers directly, verifying certifications, requesting samples, and seeking professional consultation. The risk of relying on any information in this guide is borne solely by the reader.
Strategic Sourcing Conclusion and Outlook for transducer manufacturer
In today’s rapidly evolving industrial landscape, the importance of strategic sourcing for transducer manufacturers cannot be overstated. By prioritizing the procurement of high-quality transducers, international B2B buyers can significantly enhance their operational efficiency and product reliability. Understanding the various types of transducers—active, passive, analog, and digital—enables buyers to select the right components tailored to their specific applications, whether it be in manufacturing, healthcare, or environmental monitoring.
Moreover, the geographic diversity of suppliers from Africa, South America, the Middle East, and Europe presents unique opportunities for collaboration and innovation. As global supply chains become increasingly interconnected, leveraging regional strengths can lead to cost savings and improved service delivery.
Looking ahead, international buyers should not only focus on immediate sourcing needs but also consider long-term partnerships with transducer manufacturers. Engaging with suppliers who prioritize sustainability and technological advancements will be crucial in staying competitive. By fostering these relationships, businesses can ensure they are at the forefront of industry trends and are well-equipped to meet future demands. Take the next step in your sourcing strategy—explore partnerships that align with your operational goals and drive value in your supply chain.