Discover Top Mini Excavator Manufacturers: The Ultimate Guide (2025)
Introduction: Navigating the Global Market for mini excavator manufacturer
In the competitive landscape of construction and excavation equipment, sourcing a reliable mini excavator manufacturer can pose significant challenges for international B2B buyers. The complexities of navigating global markets, particularly for those in Africa, South America, the Middle East, and Europe, can hinder the procurement process, leading to costly mistakes. This guide aims to demystify the intricacies of selecting the right mini excavator manufacturer by providing valuable insights into the various types of mini excavators available, their diverse applications, and the critical factors to consider when vetting suppliers.
Understanding the market landscape is essential for making informed purchasing decisions. This comprehensive resource will delve into the technical specifications of mini excavators, explore their uses in different industries such as construction, landscaping, and agriculture, and highlight the importance of assessing manufacturer credentials. Additionally, we will discuss pricing structures, cost-saving strategies, and tips for negotiating favorable terms with suppliers.
By equipping international B2B buyers with actionable insights and practical knowledge, this guide empowers decision-makers to navigate the global market effectively. Whether you’re a procurement officer in the UAE seeking robust machinery for urban development or an entrepreneur in Italy looking to expand your equipment fleet, the information within these pages will help you make strategic choices that align with your business objectives.
Understanding mini excavator manufacturer Types and Variations
Type Name | Key Distinguishing Features | Primary B2B Applications | Brief Pros & Cons for Buyers |
---|---|---|---|
Standard Mini Excavators | Compact size, versatile attachments | Landscaping, construction, utility work | Pros: High versatility; Cons: Limited power compared to larger models |
Zero Tail Swing Excavators | Designed for tight spaces with minimal overhang | Urban construction, demolition | Pros: Excellent maneuverability; Cons: Slightly less stability in rough terrain |
Long Reach Mini Excavators | Extended arm for deeper digging | Excavation, trenching, deep foundation work | Pros: Greater reach; Cons: Reduced lifting capacity |
Electric Mini Excavators | Eco-friendly, lower noise levels | Indoor projects, urban areas | Pros: Sustainable; Cons: Limited battery life and power compared to diesel |
Hydraulic Mini Excavators | Enhanced power and efficiency through hydraulic systems | Heavy-duty tasks, industrial applications | Pros: High lifting capacity; Cons: Requires more maintenance |
What are the Characteristics of Standard Mini Excavators?
Standard mini excavators are characterized by their compact size, which allows for versatility in various attachments. They typically range from 1 to 6 tons and can easily maneuver in tight spaces. These machines are suitable for a range of applications, including landscaping, construction, and utility work. When purchasing, B2B buyers should consider factors such as the attachment options available, operating weight, and ease of transport to ensure they meet specific project needs.
How Do Zero Tail Swing Excavators Enhance Urban Operations?
Zero tail swing excavators are specifically designed to operate in confined spaces without the risk of overhang. This feature makes them ideal for urban construction and demolition projects where space is a premium. They offer excellent maneuverability and can work closely to existing structures. B2B buyers should assess the machine’s stability and reach, as well as the types of attachments that can be utilized, to maximize efficiency in urban environments.
When Should You Choose Long Reach Mini Excavators?
Long reach mini excavators are equipped with extended arms that enable deeper digging capabilities. They are particularly useful in excavation, trenching, and deep foundation work where standard excavators may struggle. B2B buyers should consider the machine’s reach and lifting capacity, as well as the type of projects they will undertake, to determine if this type of excavator fits their operational requirements.
What Benefits Do Electric Mini Excavators Offer for Urban Projects?
Electric mini excavators are becoming increasingly popular due to their eco-friendly design and lower noise levels, making them suitable for indoor projects and urban areas. These machines help reduce carbon footprints and comply with stricter environmental regulations. However, B2B buyers must evaluate battery life and power limitations, ensuring that the electric excavator can meet the demands of their specific applications.
Why Consider Hydraulic Mini Excavators for Heavy-Duty Tasks?
Hydraulic mini excavators leverage hydraulic systems to provide enhanced power and efficiency, making them ideal for heavy-duty tasks and industrial applications. These machines typically offer high lifting capacities and can handle tough working conditions. When considering a hydraulic mini excavator, B2B buyers should pay attention to maintenance requirements and the availability of parts, as these factors can impact long-term operational costs.
Related Video: BUYING AND UPGRADING A CHINESE MINI EXCAVATOR
Key Industrial Applications of mini excavator manufacturer
Industry/Sector | Specific Application of mini excavator manufacturer | Value/Benefit for the Business | Key Sourcing Considerations for this Application |
---|---|---|---|
Construction | Site preparation and foundation digging | Efficiently clears land and prepares sites, reducing project time | Load capacity, hydraulic power, and attachment options |
Landscaping and Gardening | Soil excavation and planting | Enhances landscaping projects, allowing for precise planting | Size and maneuverability, especially in urban settings |
Utilities and Infrastructure | Trenching for utility lines | Facilitates quick installation and repairs of utilities | Compatibility with existing infrastructure and ease of transport |
Agriculture | Land clearing and soil leveling | Increases arable land and improves crop yield potential | Durability in rugged terrains and fuel efficiency |
Mining and Quarrying | Material handling and site development | Streamlines operations and enhances productivity | Reliability, maintenance support, and spare parts availability |
How Are Mini Excavators Used in Construction Projects?
In the construction sector, mini excavators are vital for site preparation and foundation digging. These compact machines are designed to maneuver in tight spaces while providing the power needed for excavation tasks. By utilizing mini excavators, construction companies can significantly reduce the time required for land clearing and foundation work, leading to faster project completion. International buyers should focus on the machine’s load capacity and hydraulic power to ensure it meets specific project demands.
What Role Do Mini Excavators Play in Landscaping and Gardening?
In landscaping and gardening, mini excavators are employed for soil excavation and planting. Their ability to navigate through narrow pathways makes them ideal for residential and commercial landscaping projects. They enhance the precision of planting and allow for the efficient removal of unwanted soil and debris. Buyers in this sector, particularly from regions like Europe and South America, should prioritize the size and maneuverability of the mini excavator to adapt to various landscaping environments.
How Are Mini Excavators Essential for Utilities and Infrastructure?
In the utilities and infrastructure sector, mini excavators are crucial for trenching utility lines. Their compact size allows them to access areas that larger machinery cannot, facilitating the installation and repair of essential utilities such as water, gas, and electricity. This capability not only speeds up the process but also minimizes disruption to surrounding areas. For international buyers, it is essential to consider the compatibility of the mini excavator with existing infrastructure and its ease of transport to remote locations.
How Do Mini Excavators Benefit Agricultural Operations?
In agriculture, mini excavators are used for land clearing and soil leveling, which are critical for preparing fields for planting. They enable farmers to increase the amount of arable land and improve the efficiency of soil management, ultimately enhancing crop yield potential. Buyers from Africa and South America, where agricultural expansion is vital, should look for machines that offer durability in rugged terrains and fuel efficiency to maximize operational costs.
What Advantages Do Mini Excavators Provide in Mining and Quarrying?
In the mining and quarrying industries, mini excavators are utilized for material handling and site development. Their versatility allows for the efficient movement of materials and the preparation of sites for further development. This enhances productivity and streamlines operations, which is essential in competitive markets. Buyers should prioritize the reliability of the machinery, availability of maintenance support, and access to spare parts, especially in remote mining locations.
Related Video: FF Industrial FF18R Mini Excavator Review & Maintenance Tips!
3 Common User Pain Points for ‘mini excavator manufacturer’ & Their Solutions
Scenario 1: Difficulty in Sourcing Reliable Mini Excavators
The Problem:
B2B buyers often face the challenge of sourcing mini excavators that meet their specific operational needs, especially in diverse markets like Africa and South America. Factors such as varying terrain, different project requirements, and local regulations can complicate the decision-making process. Moreover, the risk of encountering unreliable manufacturers or subpar products can lead to costly project delays and operational inefficiencies.
The Solution:
To overcome these sourcing challenges, B2B buyers should conduct thorough market research to identify reputable mini excavator manufacturers with a proven track record. Utilizing online platforms and trade shows can provide valuable insights into manufacturer reliability and product quality. Additionally, buyers should prioritize manufacturers that offer customizable options tailored to local conditions and specific project requirements. Establishing relationships with local distributors can also facilitate smoother transactions and provide post-purchase support. Finally, reviewing case studies or testimonials from similar industries can help in making informed decisions.
Scenario 2: Managing Maintenance and Downtime of Mini Excavators
The Problem:
A common pain point for B2B buyers is managing the maintenance and potential downtime of mini excavators. In regions such as the Middle East and Europe, where projects often operate under tight deadlines, any equipment failure can halt operations, leading to significant financial losses. Buyers may struggle with understanding maintenance schedules and the availability of spare parts, which can exacerbate the situation.
The Solution:
To mitigate downtime, buyers should prioritize selecting manufacturers that provide comprehensive maintenance plans and readily available spare parts. Inquire about the manufacturer’s support services, including training for on-site technicians to handle basic repairs and maintenance. Establishing a proactive maintenance schedule based on the equipment’s usage can help prevent unexpected breakdowns. Furthermore, engaging with the manufacturer for regular updates on best practices for maintenance can enhance the lifespan and reliability of the mini excavators.
Scenario 3: Understanding Compliance and Regulatory Requirements
The Problem:
Navigating compliance and regulatory requirements when purchasing mini excavators can be daunting, particularly for international buyers. Regulations can vary significantly across countries in Africa, South America, the Middle East, and Europe, leading to confusion and potential legal issues if the equipment does not meet local standards. This lack of clarity can result in delays in project initiation and additional costs for modifications or fines.
The Solution:
B2B buyers should proactively seek out manufacturers who are well-versed in the regulatory landscape of their target markets. Engage with local industry associations or regulatory bodies to gain insights into the necessary compliance standards. When evaluating manufacturers, ask for documentation demonstrating that their mini excavators meet local certifications and safety standards. Building a relationship with a manufacturer that provides compliance guidance can be invaluable. Additionally, consider collaborating with local experts or consultants who specialize in equipment compliance to ensure all regulatory requirements are met before making a purchase.
Strategic Material Selection Guide for mini excavator manufacturer
When selecting materials for manufacturing mini excavators, it is essential to consider various factors that influence performance, durability, and cost-effectiveness. Below, we analyze four common materials used in mini excavator manufacturing, focusing on their properties, advantages, disadvantages, and implications for international B2B buyers.
What Are the Key Properties of Steel in Mini Excavator Manufacturing?
Steel is a widely used material in the construction of mini excavators due to its excellent strength-to-weight ratio and versatility. It can withstand high temperatures and pressures, making it suitable for various components, including frames and arm assemblies. Steel also exhibits good corrosion resistance when treated with protective coatings.
Pros and Cons:
– Pros: High durability, excellent tensile strength, and cost-effective for mass production.
– Cons: Can be heavy, which may affect the overall weight of the excavator; requires proper treatment to prevent rust.
Impact on Application:
Steel’s compatibility with hydraulic systems and its ability to endure heavy loads make it ideal for mini excavators operating in demanding environments.
Considerations for International Buyers:
Buyers from regions such as the Middle East and Africa should ensure compliance with local standards like ASTM and JIS. Additionally, the choice of steel grade can impact the longevity of the equipment in harsh climates.
How Does Aluminum Benefit Mini Excavator Manufacturers?
Aluminum is increasingly being used in mini excavator manufacturing due to its lightweight nature and resistance to corrosion. This material is particularly advantageous for components that benefit from reduced weight, such as booms and arms.
Pros and Cons:
– Pros: Lightweight, excellent corrosion resistance, and good thermal conductivity.
– Cons: Generally more expensive than steel and has lower tensile strength, which may limit its use in high-stress components.
Impact on Application:
Aluminum’s lightweight properties allow for better fuel efficiency and maneuverability, making it suitable for urban construction sites where space is limited.
Considerations for International Buyers:
In Europe, where sustainability is a priority, aluminum can align with eco-friendly initiatives. Buyers should also verify compliance with European standards for aluminum alloys.
What Role Does High-Strength Composite Material Play in Mini Excavators?
High-strength composites, such as carbon fiber and fiberglass, are becoming popular in mini excavator manufacturing due to their exceptional strength-to-weight ratio and resistance to corrosion and fatigue.
Pros and Cons:
– Pros: Extremely lightweight, high strength, and excellent resistance to environmental factors.
– Cons: Higher manufacturing complexity and costs, which may not be justifiable for all components.
Impact on Application:
Composites are ideal for specialized applications, such as reducing the weight of attachments, which can enhance the performance of mini excavators in sensitive operations.
Considerations for International Buyers:
Buyers from South America and Europe should consider the availability of composite materials and their compliance with local manufacturing standards. The higher cost may require justification in terms of performance gains.
Why Is Cast Iron a Viable Option for Mini Excavator Components?
Cast iron is another material option for mini excavators, particularly for components that require high wear resistance, such as buckets and gears. Its ability to absorb vibrations makes it suitable for heavy-duty applications.
Pros and Cons:
– Pros: Excellent wear resistance, good machinability, and ability to withstand high temperatures.
– Cons: Heavier than steel and can be brittle, leading to potential fractures under extreme stress.
Impact on Application:
Cast iron is particularly effective for components that experience high wear and tear, ensuring longevity and reliability in demanding conditions.
Considerations for International Buyers:
Buyers should ensure that cast iron components meet local standards, especially in regions like Africa and the Middle East, where operational conditions can be extreme.
Summary Table of Material Selection for Mini Excavator Manufacturing
Material | Typical Use Case for mini excavator manufacturer | Key Advantage | Key Disadvantage/Limitation | Relative Cost (Low/Med/High) |
---|---|---|---|---|
Steel | Frames, arm assemblies | High durability and cost-effective | Heavy and requires rust treatment | Medium |
Aluminum | Booms, arms | Lightweight and corrosion-resistant | Higher cost and lower tensile strength | High |
High-Strength Composite | Specialized attachments | Extremely lightweight and strong | Complex manufacturing and higher cost | High |
Cast Iron | Buckets, gears | Excellent wear resistance | Heavy and brittle under stress | Medium |
This strategic material selection guide provides valuable insights for international B2B buyers looking to optimize their mini excavator manufacturing processes while ensuring compliance with regional standards and preferences.
In-depth Look: Manufacturing Processes and Quality Assurance for mini excavator manufacturer
What Are the Key Stages in the Manufacturing Process of Mini Excavators?
Understanding the manufacturing process of mini excavators is crucial for international B2B buyers, especially those looking to invest in durable, high-quality machinery. The manufacturing process typically consists of several key stages: material preparation, forming, assembly, and finishing.
1. Material Preparation: What Materials Are Used in Mini Excavator Manufacturing?
The first step in manufacturing mini excavators involves selecting and preparing materials. Common materials include high-strength steel for the frame, hydraulic components made from durable alloys, and rubber for tracks. The quality of these materials directly affects the machine’s durability and performance. Suppliers often conduct pre-manufacturing checks to ensure that materials meet specified standards, such as tensile strength and corrosion resistance.
2. Forming: How Are Mini Excavator Components Shaped?
In the forming stage, various techniques such as cutting, bending, and welding are employed to shape the components. Advanced methods like CNC machining are increasingly used to ensure precision. For instance, the chassis and boom are often fabricated through laser cutting, which allows for intricate designs and reduces waste. Buyers should inquire about the forming technologies used by suppliers, as modern techniques can significantly enhance the quality and longevity of the equipment.
3. Assembly: What Does the Assembly Process Entail?
The assembly stage is where all the prepared components come together. This process typically involves multiple checkpoints to ensure that each part fits correctly and functions as intended. For example, the hydraulic system is meticulously installed to ensure optimal performance. Skilled technicians often conduct this assembly, and the use of jigs and fixtures helps maintain alignment and precision. Buyers should assess the workforce skill levels and assembly practices to gauge the potential quality of the final product.
4. Finishing: How Is the Final Product Prepared for Market?
The finishing stage includes painting, coating, and additional treatments that protect the excavator from environmental factors. Techniques such as powder coating not only improve aesthetics but also enhance durability against rust and wear. Buyers should ask potential suppliers about their finishing processes, as these can significantly influence the machine’s lifespan and maintenance needs.
What Quality Assurance Standards Should B2B Buyers Look For?
Quality assurance is a critical aspect of the manufacturing process for mini excavators. International standards such as ISO 9001 provide a framework for quality management systems that manufacturers should adhere to. Additionally, industry-specific certifications such as CE marking in Europe and API standards for hydraulic components are also essential indicators of quality.
How Are Quality Control Checkpoints Implemented?
Quality control (QC) is integrated at various stages of the manufacturing process, often categorized into three main checkpoints:
-
Incoming Quality Control (IQC): This initial stage involves inspecting raw materials as they arrive at the manufacturing facility. Buyers should ensure that suppliers have stringent IQC measures in place to catch defects early in the process.
-
In-Process Quality Control (IPQC): During assembly, continuous monitoring is essential. This may include checks on weld integrity, hydraulic pressure tests, and operational trials of components. Suppliers should provide documentation of these checks to assure buyers of their commitment to quality.
-
Final Quality Control (FQC): Before shipment, a comprehensive final inspection is conducted. This includes functional testing, safety checks, and aesthetic evaluations. Buyers should request FQC reports to verify that the final product meets all necessary specifications.
What Testing Methods Are Commonly Used in Mini Excavator Manufacturing?
Various testing methods are employed to ensure that mini excavators meet performance and safety standards. These include:
-
Hydraulic Testing: This assesses the performance of hydraulic systems under simulated operational conditions.
-
Load Testing: Mini excavators are subjected to various load conditions to ensure stability and performance under stress.
-
Vibration and Noise Testing: These tests evaluate the machine’s operational sound levels and vibrations, which are critical for user comfort and machine longevity.
How Can B2B Buyers Verify Supplier Quality Control?
For international buyers, verifying a supplier’s quality control processes is essential to ensure that the machinery will meet their operational needs. Here are several methods to consider:
-
Supplier Audits: Conducting on-site audits allows buyers to assess the manufacturing processes and quality control systems firsthand. This can also provide insight into the supplier’s commitment to quality and continuous improvement.
-
Requesting Quality Reports: Buyers should request detailed quality assurance reports that outline the procedures followed during manufacturing and testing. This documentation can serve as a record of compliance with international standards.
-
Third-Party Inspections: Engaging third-party inspection services can provide an unbiased assessment of the manufacturing quality. These organizations can conduct random checks at various stages of the production process.
What Are the QC and Certification Nuances for International Buyers?
Navigating the landscape of quality control and certification can be challenging for international B2B buyers. Each region may have specific requirements that need to be addressed. For example, buyers in Europe must ensure that their suppliers comply with CE regulations, while those in the Middle East might need to consider local standards and certifications.
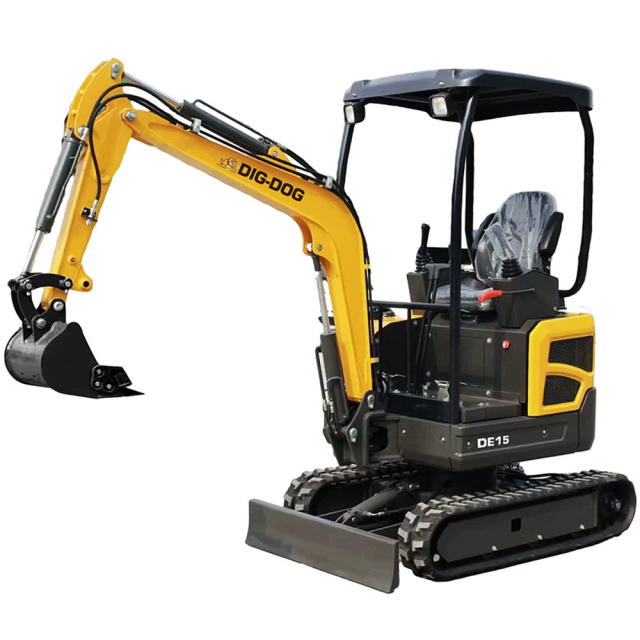
A stock image related to mini excavator manufacturer.
Furthermore, understanding the nuances of warranty terms and after-sales support is vital. Buyers should seek clarity on the terms associated with QC certifications and how they relate to product warranties. This can help avoid potential disputes regarding product performance and service expectations.
Conclusion: What Should B2B Buyers Keep in Mind?
In summary, a thorough understanding of the manufacturing processes and quality assurance standards for mini excavators is essential for international buyers. By focusing on material selection, forming techniques, assembly practices, and finishing methods, buyers can make informed decisions. Additionally, verifying QC processes through audits, reports, and third-party inspections will ensure that the purchased machinery meets their operational needs and standards. By keeping these insights in mind, B2B buyers can navigate the complexities of the mini excavator market effectively.
Practical Sourcing Guide: A Step-by-Step Checklist for ‘mini excavator manufacturer’
In the dynamic world of construction and heavy machinery, sourcing a reliable mini excavator manufacturer is a critical task for international B2B buyers. This guide offers a clear checklist to help you navigate the procurement process effectively, ensuring that you choose a supplier that meets your operational needs and standards.
Step 1: Define Your Technical Specifications
Establishing clear technical specifications is the foundation of a successful sourcing process. Outline the size, weight, digging depth, and additional features you require. This clarity will help you communicate effectively with potential manufacturers and ensure that the excavators meet your operational requirements.
Step 2: Conduct Market Research
Before reaching out to suppliers, perform thorough market research. Identify the leading mini excavator manufacturers in your target regions—Africa, South America, the Middle East, and Europe. Analyze their product offerings, market reputation, and customer reviews to create a shortlist of potential suppliers that align with your needs.
Step 3: Evaluate Potential Suppliers
Before committing, it’s crucial to vet suppliers thoroughly. Request company profiles, case studies, and references from buyers in a similar industry or region. Focus on the following:
– Experience: Look for manufacturers with a proven track record in producing mini excavators.
– Portfolio: Review their past projects to gauge the quality and diversity of their products.
Step 4: Verify Supplier Certifications
Ensuring that your chosen supplier holds relevant certifications is vital for quality assurance and compliance. Check for industry certifications such as ISO 9001 for quality management systems or CE marking for compliance with European standards. These certifications indicate that the manufacturer adheres to recognized quality and safety standards.
Step 5: Request Sample Products
Before making a large order, it’s prudent to request sample products or arrange a factory visit. This allows you to assess the build quality, performance, and suitability of the mini excavators firsthand. Look for:
– Durability: Test the materials used and the overall construction of the mini excavator.
– Operational Efficiency: Evaluate how the machine performs under simulated working conditions.
Step 6: Negotiate Terms and Conditions
Once you’ve identified a suitable supplier, engage in negotiations regarding pricing, payment terms, delivery schedules, and warranty provisions. Ensure that both parties have a clear understanding of the expectations and obligations. Look for flexibility in payment terms, particularly if you are a new buyer or purchasing in bulk.
Step 7: Establish a Communication Plan
Effective communication is crucial throughout the sourcing process. Set up a communication plan that outlines how often you will check in with the supplier and through which channels (email, video calls, etc.). Clear communication can help resolve issues quickly and foster a strong working relationship.
By following this checklist, B2B buyers can streamline their sourcing process for mini excavators, ensuring they select a manufacturer that not only meets their technical requirements but also aligns with their business goals.
Comprehensive Cost and Pricing Analysis for mini excavator manufacturer Sourcing
What Are the Key Cost Components in Mini Excavator Manufacturing?
When sourcing mini excavators, understanding the cost structure is paramount for B2B buyers. The primary cost components include:
-
Materials: The choice of materials significantly impacts the overall cost. High-quality steel and specialized alloys used in the manufacturing of mini excavators are essential for durability but can raise expenses. Buyers should evaluate the trade-off between cost and quality.
-
Labor: Labor costs vary greatly depending on the region of manufacturing. Countries with lower labor costs, such as some in South America and Africa, may offer competitive pricing. However, this can come at the expense of craftsmanship and quality assurance.
-
Manufacturing Overhead: This includes costs related to factory operation, utilities, and administrative expenses. Efficient production facilities can lead to lower overheads, thus providing better pricing for buyers.
-
Tooling: The investment in tooling for mini excavator production can be substantial. Custom tooling for specialized models can elevate costs, so buyers should inquire about the tooling requirements for their specific needs.
-
Quality Control (QC): Robust QC processes ensure that the mini excavators meet safety and performance standards. While this adds to the cost, it is essential for minimizing post-purchase issues and enhancing reliability.
-
Logistics: Shipping and transportation costs can be significant, especially for international buyers. Factors such as distance, shipping methods, and customs duties can influence the total logistics expenditure.
-
Margin: Manufacturers typically include a profit margin in their pricing. Understanding the margin expectations of different suppliers can help buyers negotiate better terms.
How Do Price Influencers Affect Mini Excavator Sourcing?
Several factors can influence the pricing of mini excavators, which buyers should consider when negotiating:
-
Volume and Minimum Order Quantity (MOQ): Ordering in bulk can lead to discounts. Buyers should assess their needs and potential future requirements to leverage better pricing.
-
Specifications and Customization: Customized mini excavators tailored to specific tasks may incur additional costs. Buyers should clearly define their requirements to avoid unexpected charges.
-
Material Quality and Certifications: Higher-quality materials and certifications (such as ISO) can increase costs but are essential for ensuring safety and compliance with local regulations.
-
Supplier Factors: The reputation and reliability of the manufacturer can impact pricing. Established manufacturers with a strong track record may charge more due to their perceived value.
-
Incoterms: Understanding the terms of delivery (Incoterms) is crucial for international transactions. The choice of Incoterms can affect shipping costs and responsibilities, influencing the overall pricing.
What Are the Best Practices for Negotiating Mini Excavator Prices?
International B2B buyers can adopt several strategies to ensure cost-efficiency when sourcing mini excavators:
-
Conduct Comprehensive Research: Understand the market pricing and gather quotes from multiple suppliers. This will provide leverage during negotiations.
-
Focus on Total Cost of Ownership (TCO): Evaluate not just the purchase price but also maintenance, operational costs, and resale value. A lower initial price might lead to higher long-term costs.
-
Negotiate Payment Terms: Discussing flexible payment terms can ease cash flow constraints. Buyers should consider options like staggered payments or discounts for upfront payments.
-
Assess Local and Regional Suppliers: Buyers from Africa, South America, the Middle East, and Europe should explore local manufacturers to reduce shipping costs and lead times.
-
Be Aware of Pricing Nuances: International buyers should consider currency fluctuations and geopolitical factors that may affect pricing. Being informed can aid in making timely purchasing decisions.
Conclusion
Understanding the comprehensive cost structure and pricing dynamics of mini excavator manufacturing is essential for international B2B buyers. By focusing on key cost components, price influencers, and negotiation strategies, buyers can make informed decisions that align with their operational needs and budget constraints. Always remember to verify indicative prices with suppliers, as they can vary based on market conditions and individual specifications.
Alternatives Analysis: Comparing mini excavator manufacturer With Other Solutions
In the competitive landscape of construction and excavation, it’s essential for B2B buyers to explore various equipment solutions. While mini excavators are a popular choice for their versatility and efficiency, there are alternative methods and technologies that may better suit specific project needs, particularly for international buyers from regions such as Africa, South America, the Middle East, and Europe. This section will compare mini excavators against two viable alternatives: backhoe loaders and compact track loaders.
Comparison Table of Mini Excavator Manufacturer and Alternatives
Comparison Aspect | Mini Excavator Manufacturer | Backhoe Loader | Compact Track Loader |
---|---|---|---|
Performance | High digging depth, precise control | Versatile for digging and loading | Excellent traction, stable on uneven terrain |
Cost | Moderate initial investment | Higher upfront cost due to dual functionality | Generally higher due to specialized tracks |
Ease of Implementation | Easy to transport and maneuver | Requires more space for operation | Compact size, easy to transport |
Maintenance | Low maintenance with regular service | Moderate maintenance needs due to complexity | Higher maintenance due to track wear |
Best Use Case | Tight spaces, precision work | General construction, landscaping | Grading, site preparation, and heavy lifting |
What Are the Advantages and Disadvantages of Backhoe Loaders?
Backhoe loaders combine the functionalities of a loader and an excavator, making them incredibly versatile. They are well-suited for general construction tasks, landscaping, and digging. However, their higher initial cost can be a drawback for budget-conscious buyers. Additionally, they require more space to operate effectively compared to mini excavators. While backhoe loaders can handle a variety of tasks, their efficiency in tight spaces is not as strong as that of mini excavators.
How Do Compact Track Loaders Compare in Terms of Functionality?
Compact track loaders are designed for stability and traction, making them ideal for uneven or soft ground. They excel in grading and site preparation, especially in environments where mini excavators might struggle. However, the cost of compact track loaders can be higher due to their specialized tracks, and they often require more maintenance. The ability to tackle heavy lifting tasks is a significant advantage, but buyers must weigh this against the potential for increased operational costs.
Conclusion: How Should B2B Buyers Choose the Right Solution?
Choosing the right equipment depends on the specific needs of your project, budget constraints, and the working environment. For projects requiring precision in tight spaces, a mini excavator may be the best choice. If versatility across different tasks is paramount, a backhoe loader could be more suitable despite its higher cost. For stability on uneven terrains and heavy lifting, a compact track loader might be ideal, though it comes with increased maintenance requirements. By analyzing these aspects and considering the unique demands of their projects, B2B buyers can make informed decisions that align with their operational goals.
Essential Technical Properties and Trade Terminology for mini excavator manufacturer
What Are the Key Technical Specifications for Mini Excavators?
Understanding the technical specifications of mini excavators is crucial for B2B buyers looking to make informed purchasing decisions. Here are some essential properties to consider:
-
Operating Weight
Operating weight refers to the total weight of the mini excavator, including fluids and standard equipment. This is vital for determining the machine’s stability and suitability for different job sites. For instance, lighter models may be ideal for residential projects, while heavier models are suited for construction sites with demanding tasks. -
Digging Depth
This specification indicates how deep the excavator can dig. Digging depth is essential for projects requiring foundation work or utility installation. Buyers should assess their project requirements to ensure the mini excavator can meet the necessary digging specifications. -
Hydraulic Flow Rate
The hydraulic flow rate measures the volume of hydraulic fluid that can be moved through the system per minute, often expressed in liters per minute (LPM). This property impacts the performance of attachments such as augers and grapples. A higher flow rate allows for more efficient operation and greater versatility in attachment options. -
Engine Power
Measured in horsepower (HP) or kilowatts (kW), engine power is crucial for assessing the machine’s performance capabilities. More powerful engines can handle tougher jobs and operate more efficiently, making it a key consideration for buyers planning to use the excavator in demanding environments. -
Boom and Arm Reach
The reach of the boom and arm determines the excavator’s ability to access hard-to-reach areas. Buyers should evaluate the reach specifications to ensure that the excavator can perform the tasks required in their specific projects. -
Tread Width and Ground Pressure
Tread width affects the mini excavator’s stability and its ability to traverse various terrains. Ground pressure is the weight distribution of the excavator on the ground, which is especially important in soft or unstable soils. Understanding these parameters helps buyers select machines that will not damage delicate surfaces or become stuck in challenging conditions.
What Are Common Trade Terms Used in the Mini Excavator Industry?
Familiarity with industry jargon is essential for effective communication and negotiation in B2B transactions. Here are several key terms you should know:
-
OEM (Original Equipment Manufacturer)
This term refers to companies that produce parts and equipment that may be marketed by another manufacturer. Understanding OEM relationships is vital for buyers seeking quality assurance and compatibility with existing machinery. -
MOQ (Minimum Order Quantity)
MOQ represents the smallest quantity of a product that a supplier is willing to sell. This term is significant for budget-conscious buyers as it influences total costs and inventory management. Negotiating MOQs can lead to better pricing or terms. -
RFQ (Request for Quotation)
An RFQ is a document sent to suppliers requesting detailed pricing and terms for specific products. For buyers, using an RFQ helps ensure that they receive competitive bids and allows for a straightforward comparison of offers. -
Incoterms (International Commercial Terms)
These standardized terms define the responsibilities of buyers and sellers in international trade, covering aspects like shipping, insurance, and tariffs. Familiarity with Incoterms can help buyers avoid unexpected costs and clarify shipping responsibilities. -
Lead Time
Lead time is the duration between placing an order and receiving the goods. Understanding lead times is crucial for project planning, especially in sectors with strict timelines. Buyers should inquire about lead times to ensure timely delivery and project continuity. -
Warranty Period
The warranty period indicates the duration for which the manufacturer guarantees the performance of the mini excavator. This term is essential for risk management, as it affects maintenance costs and long-term investment value.
By grasping these essential technical properties and trade terms, international B2B buyers can make more informed decisions, ensuring that they select the right mini excavator for their specific needs while navigating the complexities of global trade effectively.
Navigating Market Dynamics and Sourcing Trends in the mini excavator manufacturer Sector
What Are the Key Market Dynamics and Sourcing Trends in the Mini Excavator Manufacturing Sector?
The global mini excavator market is experiencing significant growth driven by urbanization, infrastructure development, and advancements in construction technology. International B2B buyers, particularly in regions like Africa, South America, the Middle East, and Europe, are capitalizing on these trends to enhance their procurement strategies. The increasing demand for compact machinery that can operate in confined spaces is pushing manufacturers to innovate. Notably, the integration of telematics and IoT technologies is revolutionizing equipment management, enabling real-time monitoring and predictive maintenance.
In the Middle East and North Africa, government initiatives aimed at diversifying economies and boosting construction activities are propelling the demand for mini excavators. Similarly, in Europe, a surge in urban infrastructure projects is fueling growth. Buyers should be aware of regional dynamics; for instance, in Italy, there is a strong focus on energy efficiency and lightweight machinery, while in the UAE, the emphasis is on high-tech solutions that improve productivity and reduce downtime.
Emerging trends also include the rise of digital platforms for sourcing, allowing buyers to compare manufacturers and products easily. Additionally, the push for more sustainable manufacturing practices is leading to a growing number of suppliers adopting environmentally friendly technologies. This shift not only meets regulatory requirements but also enhances brand reputation, making it a critical consideration for international buyers.
How Can Sustainability and Ethical Sourcing Impact Your B2B Procurement Strategy?
Sustainability has become a key focus in the mini excavator manufacturing sector, as companies increasingly recognize their environmental impact. For international buyers, particularly those in Africa and South America, understanding the importance of ethical sourcing is crucial. This involves selecting suppliers that prioritize sustainable practices, such as reducing carbon footprints and minimizing waste.
Buyers should look for manufacturers that have obtained ‘green’ certifications, like ISO 14001, which demonstrates a commitment to environmental management. Additionally, sourcing materials that are recycled or sustainably harvested can significantly reduce the overall environmental impact of mini excavators.
Moreover, ethical supply chains contribute to a positive brand image and can enhance customer loyalty. As regulations around environmental compliance become stricter, aligning procurement strategies with sustainability goals will not only ensure compliance but also open up new business opportunities. Buyers should proactively engage with suppliers to understand their sustainability initiatives and incorporate these practices into their sourcing decisions.
What Is the Historical Context Behind the Mini Excavator Manufacturing Sector?
The mini excavator manufacturing sector has evolved significantly since its inception in the late 20th century. Originally designed for small-scale landscaping and gardening tasks, these machines have transformed into versatile tools capable of handling a variety of construction and demolition projects. The introduction of hydraulic technology in the 1980s allowed for greater efficiency and power in compact machinery, paving the way for the modern mini excavators we see today.
Over the years, the sector has witnessed technological advancements, such as enhanced fuel efficiency, improved ergonomics, and the integration of smart technology. These developments have allowed mini excavators to become indispensable in urban construction projects, facilitating quicker and more efficient operations. Understanding this evolution provides B2B buyers with insight into the capabilities and innovations available, enabling them to make informed decisions when sourcing mini excavators tailored to their specific needs.
Frequently Asked Questions (FAQs) for B2B Buyers of mini excavator manufacturer
-
How do I determine the right mini excavator for my project needs?
To select the appropriate mini excavator, assess your project requirements, including the type of terrain, the weight of materials to be moved, and the size of the work area. Consider factors such as digging depth, reach, and attachment compatibility. Additionally, consult with manufacturers to understand their product specifications and gain insights into which models are best suited for specific applications. Engaging with local dealers can also provide valuable regional insights based on common use cases. -
What are the key features to look for in a mini excavator?
When evaluating mini excavators, prioritize features such as engine power, hydraulic performance, operating weight, and cab comfort. Look for models that offer versatility with various attachments, as well as those with advanced safety features like ROPS and FOPS. Fuel efficiency and ease of maintenance should also be significant considerations, as they directly impact operational costs and uptime. Reading user reviews and expert opinions can further guide your decision. -
What is the typical lead time for ordering a mini excavator from a manufacturer?
Lead times can vary widely based on the manufacturer, model, and customization requirements. Typically, you can expect delivery within 4 to 12 weeks after placing an order. For highly customized models, this timeline may extend. It’s advisable to confirm lead times during the negotiation phase and factor in potential delays due to shipping or production schedules, especially when sourcing from international manufacturers. -
How can I vet a mini excavator manufacturer for quality and reliability?
To vet a mini excavator manufacturer, start by researching their industry reputation through customer testimonials, reviews, and case studies. Check for certifications and compliance with international quality standards, such as ISO certifications. Engaging in discussions with other buyers in your region can provide insights into the manufacturer’s after-sales support and service quality. Additionally, visiting the manufacturer’s facilities, if possible, can provide a firsthand look at their production processes and quality control measures. -
What customization options are available when ordering a mini excavator?
Customization options can include specific attachments (like buckets, grapples, and augers), paint colors, cab configurations, and additional features like enhanced hydraulic systems or improved seating. Some manufacturers offer tailored solutions for unique project requirements. It’s essential to discuss your specific needs with the manufacturer to explore available options and understand the associated costs and lead times for customizations. -
What are the minimum order quantities (MOQ) for mini excavators?
Minimum order quantities for mini excavators can vary by manufacturer and region. Some manufacturers may allow single-unit purchases, while others might have MOQs of two or more units, especially for bulk orders. It’s essential to inquire about MOQs during the initial discussions to align with your budget and project needs. In some cases, manufacturers may offer flexible options for first-time buyers or smaller enterprises. -
What payment terms should I expect when purchasing a mini excavator?
Payment terms can vary significantly between manufacturers. Generally, expect to pay a deposit (often 20-30%) upon order confirmation, with the balance due before shipping or upon delivery. Some manufacturers may offer financing options or extended payment plans for larger purchases. Ensure you clarify these terms upfront and consider negotiating to find a payment schedule that aligns with your cash flow needs. -
How does logistics work for shipping mini excavators internationally?
Shipping logistics for mini excavators typically involve coordinating with freight forwarders experienced in heavy equipment transport. Factors to consider include shipping methods (container vs. roll-on/roll-off), customs clearance, and import duties applicable in your country. It’s advisable to discuss shipping logistics with your manufacturer and freight forwarder to understand all associated costs and timelines. Proper planning can help mitigate delays and ensure that your equipment arrives safely and on schedule.
Important Disclaimer & Terms of Use
⚠️ Important Disclaimer
The information provided in this guide, including content regarding manufacturers, technical specifications, and market analysis, is for informational and educational purposes only. It does not constitute professional procurement advice, financial advice, or legal advice.
While we have made every effort to ensure the accuracy and timeliness of the information, we are not responsible for any errors, omissions, or outdated information. Market conditions, company details, and technical standards are subject to change.
B2B buyers must conduct their own independent and thorough due diligence before making any purchasing decisions. This includes contacting suppliers directly, verifying certifications, requesting samples, and seeking professional consultation. The risk of relying on any information in this guide is borne solely by the reader.
Strategic Sourcing Conclusion and Outlook for mini excavator manufacturer
What are the key takeaways for B2B buyers in mini excavator sourcing?
In conclusion, strategic sourcing is pivotal for international B2B buyers looking to procure mini excavators. By understanding market dynamics and supplier capabilities, buyers can significantly reduce costs while ensuring high-quality equipment tailored to their specific needs. Key takeaways include the importance of evaluating suppliers based on their technological innovation, production capacity, and compliance with international standards. Additionally, fostering strong relationships with manufacturers can lead to better service and support, especially in regions like Africa and South America where local expertise may be limited.
How can B2B buyers prepare for future sourcing opportunities?
Looking ahead, the landscape for mini excavator manufacturing is poised for growth, driven by advancements in technology and increasing demand in emerging markets. Buyers are encouraged to stay informed about trends such as sustainability and automation in construction equipment. Engaging with manufacturers who prioritize these aspects will not only enhance operational efficiency but also align with global sustainability goals.
What is the next step for B2B buyers in the mini excavator market?
As you embark on your sourcing journey, consider leveraging platforms that connect you with reputable manufacturers across Europe, the Middle East, and beyond. By taking proactive steps now, you can ensure your business remains competitive and equipped with the best machinery for future projects. Embrace the opportunity to optimize your procurement strategy today!