Improve Quality: The Ultimate Marine Plywood Manufacturer Guide (2025)
Introduction: Navigating the Global Market for marine plywood manufacturer
In the quest for high-quality marine plywood manufacturers, international B2B buyers often face significant challenges, including fluctuating material costs, varying quality standards, and the complexities of cross-border logistics. Sourcing marine plywood that meets specific project requirements while ensuring durability and compliance with international standards can be daunting. This comprehensive guide addresses these challenges head-on, equipping buyers with essential knowledge to navigate the global market effectively.
Throughout this guide, we will explore a variety of marine plywood types, detailing their specific applications in industries such as construction, shipping, and furniture manufacturing. We will also delve into the intricacies of supplier vetting processes, enabling buyers to identify reliable manufacturers who can deliver quality products consistently. Additionally, we will provide insights into cost considerations and best practices for negotiating favorable terms with suppliers.
For B2B buyers from Africa, South America, the Middle East, and Europe—especially in markets like Spain and the UK—this guide serves as a vital resource for making informed purchasing decisions. By understanding the nuances of the marine plywood market, buyers can streamline their sourcing strategies, reduce risks associated with procurement, and ultimately enhance their project outcomes. With the right knowledge at their fingertips, international buyers can confidently engage with suppliers and secure the best materials for their specific needs.
Understanding marine plywood manufacturer Types and Variations
Type Name | Key Distinguishing Features | Primary B2B Applications | Brief Pros & Cons for Buyers |
---|---|---|---|
Tropical Marine Plywood | Made from hardwood species, high durability, and water resistance | Shipbuilding, docks, and marine structures | Pros: Excellent strength and durability; Cons: Higher cost due to sourcing. |
Film-Faced Marine Plywood | Coated with a phenolic film for enhanced waterproofing and surface finish | Concrete formwork, architectural applications | Pros: Smooth finish; Cons: Limited resistance to impact. |
Softwood Marine Plywood | Constructed from softwood species, lighter weight, and cost-effective | Boat interiors, furniture, and cabinetry | Pros: Cost-effective and lightweight; Cons: Less durable compared to hardwood variants. |
Structural Marine Plywood | Engineered for high load-bearing capacity and structural integrity | Bridges, floors, and heavy-duty applications | Pros: High strength; Cons: Requires careful handling and installation. |
Bamboo Marine Plywood | Eco-friendly alternative, made from bamboo, offers flexibility and strength | Sustainable building projects, interior design | Pros: Sustainable and lightweight; Cons: Availability can be limited. |
What are the Characteristics of Tropical Marine Plywood?
Tropical marine plywood is crafted from hardwood species such as Meranti or Okoume, which offer exceptional durability and resistance to water. This type is particularly suitable for applications in shipbuilding, docks, and other marine structures where exposure to harsh environments is common. When purchasing, B2B buyers should consider the sourcing of the wood, as sustainably sourced materials can enhance brand reputation and compliance with environmental regulations. Although the upfront cost may be higher, the long-term benefits in durability often justify the investment.
How Does Film-Faced Marine Plywood Stand Out?
Film-faced marine plywood is coated with a phenolic film that provides an additional layer of waterproofing and a smooth surface finish, making it ideal for concrete formwork and architectural applications. The film enhances durability against moisture while allowing for easy cleaning and maintenance. B2B buyers should evaluate the thickness of the film and the plywood’s overall quality, as these factors affect performance and lifespan. While it offers a superior finish, buyers should be aware that it may not withstand heavy impacts as well as other types.
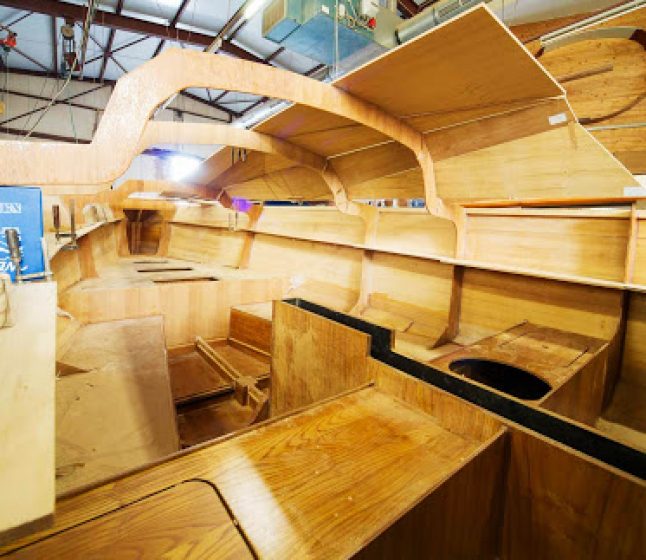
A stock image related to marine plywood manufacturer.
Why Choose Softwood Marine Plywood?
Softwood marine plywood is made from lighter wood species and is often more cost-effective than its hardwood counterparts. This variation is suitable for applications like boat interiors, furniture, and cabinetry where weight is a consideration. For B2B buyers, the affordability of softwood marine plywood can be attractive, especially for large-scale projects. However, it is essential to note that this type may not provide the same level of durability as hardwood options, making it less suitable for high-stress environments.
What is the Importance of Structural Marine Plywood?
Structural marine plywood is engineered for high load-bearing capacity, making it ideal for applications such as bridges, floors, and other heavy-duty structures. This type is designed to withstand significant stress and environmental challenges. Buyers should prioritize quality certifications and the plywood’s structural rating when making purchasing decisions, as these factors impact safety and performance. While it offers exceptional strength, buyers must also consider the handling and installation requirements, as improper treatment can lead to damage.
How Does Bamboo Marine Plywood Contribute to Sustainability?
Bamboo marine plywood is an eco-friendly alternative that utilizes rapidly renewable bamboo, offering both flexibility and strength. It is particularly appealing for sustainable building projects and interior design applications. B2B buyers focused on sustainability should consider the sourcing and production processes to ensure they align with environmental standards. While bamboo plywood is lightweight and sustainable, its availability can sometimes be limited, which may affect project timelines and costs.
Related Video: Manufacturing plywood boards: then and now
Key Industrial Applications of marine plywood manufacturer
Industry/Sector | Specific Application of Marine Plywood Manufacturer | Value/Benefit for the Business | Key Sourcing Considerations for this Application |
---|---|---|---|
Shipbuilding | Hull construction and interior structures | Provides durability and water resistance, essential for longevity and safety at sea. | Certifications for marine-grade quality, compliance with international standards. |
Construction | Waterfront structures such as docks and piers | Enhances structural integrity and withstands harsh marine conditions. | Availability of custom sizes and thicknesses to meet project specifications. |
Furniture Manufacturing | Production of marine-grade furniture for outdoor use | Ensures longevity and resistance to moisture, suitable for marine environments. | Sourcing from manufacturers with a track record in high-quality finishes and treatments. |
Transportation | Boat and yacht interiors | Offers lightweight yet strong solutions for enhancing vessel aesthetics and functionality. | Need for eco-friendly sourcing options and compliance with safety regulations. |
Recreational Vehicle (RV) Manufacturing | Construction of RV exteriors and interiors | Provides lightweight, durable materials that can withstand varying weather conditions. | Importance of consistent supply chains and bulk purchasing options for cost efficiency. |
How is Marine Plywood Used in Shipbuilding and What Problems Does it Solve?
In the shipbuilding industry, marine plywood is essential for constructing hulls and interior structures of boats and ships. Its water-resistant properties ensure that vessels remain safe and durable over time, addressing the critical challenge of material degradation in marine environments. International B2B buyers must prioritize sourcing marine plywood that meets stringent certifications and international quality standards to ensure compliance and safety.
What are the Applications of Marine Plywood in Construction?
Marine plywood is widely used in the construction of waterfront structures like docks and piers. Its robust design allows it to withstand harsh marine conditions, providing the necessary structural integrity for long-lasting installations. Buyers in Africa, South America, the Middle East, and Europe should focus on sourcing custom sizes and thicknesses that align with specific project requirements, ensuring optimal performance and durability.
How is Marine Plywood Beneficial for Furniture Manufacturing?
In the furniture manufacturing sector, marine plywood is utilized to create outdoor furniture that can endure exposure to moisture and varying weather conditions. This application enhances the longevity of products, making them suitable for marine environments. B2B buyers should seek manufacturers who specialize in high-quality finishes and treatments to ensure that the furniture not only meets functional requirements but also aesthetic standards.
What Role Does Marine Plywood Play in Transportation?
Marine plywood is critical in the transportation industry, particularly for the interiors of boats and yachts. Its lightweight yet strong properties allow for innovative design solutions that enhance both the aesthetics and functionality of vessels. Buyers should consider eco-friendly sourcing options and ensure that materials comply with safety regulations, which is increasingly important in global markets.
How is Marine Plywood Used in Recreational Vehicle Manufacturing?
In the recreational vehicle (RV) manufacturing sector, marine plywood is used for both exteriors and interiors due to its durability and lightweight characteristics. This application addresses the challenges of varying weather conditions that RVs face during their use. B2B buyers should focus on establishing reliable supply chains and consider bulk purchasing options to maximize cost efficiency while ensuring consistent quality.
Related Video: Marine Plywood vs. Cheaper Options
3 Common User Pain Points for ‘marine plywood manufacturer’ & Their Solutions
Scenario 1: Difficulty in Assessing Quality of Marine Plywood
The Problem:
International B2B buyers often face challenges in assessing the quality of marine plywood before making a purchase. This difficulty can stem from a lack of standardized grading systems across different manufacturers, leading to confusion and potential dissatisfaction with the product. Buyers may receive products that do not meet their specifications, resulting in costly project delays or failures. This issue is especially pronounced in regions like Africa and South America, where local suppliers might not have the same quality assurance processes as those in Europe or the Middle East.
The Solution:
To effectively assess the quality of marine plywood, buyers should establish a clear set of criteria based on international standards such as BS 1088 (British Standard for marine plywood) or the equivalent standards in their region. This includes checking for certifications, grade markings, and specifications related to water resistance, durability, and the type of adhesive used. Engaging with manufacturers who provide transparent product information, including technical datasheets and third-party quality assessments, can significantly mitigate quality risks. Additionally, considering sample orders or visiting the manufacturing facility can provide firsthand insight into the production process and material quality.
Scenario 2: Challenges in Sourcing Reliable Suppliers
The Problem:
Sourcing reliable marine plywood manufacturers can be a daunting task, particularly for B2B buyers operating in emerging markets. Issues such as inconsistent supply chains, fluctuating prices, and lack of communication can hinder timely project execution. This is particularly critical for industries such as boat building or construction in the Middle East and parts of Europe, where project timelines are often strict and depend heavily on the availability of quality materials.
The Solution:
To overcome sourcing challenges, buyers should leverage technology and online platforms that specialize in connecting businesses with verified suppliers. Utilizing B2B marketplaces and industry-specific trade shows can facilitate direct communication with potential suppliers, allowing buyers to establish relationships and negotiate terms. Additionally, conducting due diligence by checking references, reviewing past client testimonials, and assessing the supplier’s financial stability can help ensure reliability. Establishing long-term partnerships with manufacturers who demonstrate consistent quality and supply can also lead to better pricing and priority service in times of high demand.
Scenario 3: Navigating Compliance and Regulatory Issues
The Problem:
Compliance with international regulations and local laws regarding the use of marine plywood can pose significant challenges for B2B buyers. Regulations may vary widely between regions, particularly in Europe, Africa, and South America, where environmental standards and trade restrictions can affect the importation and use of certain types of plywood. Failing to adhere to these regulations can result in fines, project delays, or even legal repercussions, which can have lasting impacts on a company’s reputation and bottom line.
The Solution:
To navigate compliance and regulatory issues effectively, buyers should stay informed about the specific regulations that apply in their target markets. This includes understanding import tariffs, environmental regulations concerning the sourcing of timber, and any standards specific to marine applications. Collaborating with local experts or consultants who specialize in regulatory compliance can provide valuable insights. Furthermore, working with manufacturers that are well-versed in international trade and compliance can streamline the procurement process. Buyers should also ensure that their suppliers are compliant with certifications such as FSC (Forest Stewardship Council) or PEFC (Programme for the Endorsement of Forest Certification) to assure that the materials are sourced sustainably and legally.
Strategic Material Selection Guide for marine plywood manufacturer
When selecting materials for marine plywood manufacturing, international B2B buyers must consider a range of factors including performance properties, cost, and compliance with regional standards. Below, we analyze four common materials used in marine plywood production, highlighting their key properties, advantages, disadvantages, and specific considerations for buyers from Africa, South America, the Middle East, and Europe.
What Are the Key Properties of Phenolic Resin Bonded Plywood?
Phenolic resin bonded plywood is a popular choice in marine applications due to its excellent water resistance and durability. This material can withstand extreme temperatures and pressures, making it suitable for various marine environments. Its corrosion resistance is particularly beneficial for applications exposed to saltwater, which is common in coastal regions.
Pros & Cons:
The primary advantage of phenolic resin bonded plywood is its long lifespan, which can exceed 20 years with proper maintenance. However, the manufacturing complexity can lead to higher costs, making it less suitable for budget-sensitive projects. Additionally, its weight may be a concern for certain applications where lighter materials are preferred.
Impact on Application:
This type of plywood is ideal for boat hulls, docks, and other structures requiring high durability and moisture resistance. Its compatibility with harsh marine conditions makes it a preferred choice for many manufacturers.
How Does Marine Grade Plywood Compare to Other Materials?
Marine grade plywood is constructed from high-quality veneers and bonded with waterproof adhesive, ensuring it can withstand moisture and prevent delamination. This material typically has a temperature rating suitable for moderate marine environments.
Pros & Cons:
The key advantage of marine grade plywood is its balance between performance and cost. It provides good durability at a relatively lower price compared to phenolic resin bonded plywood. However, it may not perform as well in extreme conditions or prolonged exposure to seawater, which could limit its applications.
Impact on Application:
Marine grade plywood is often used in the construction of small boats, furniture, and cabinetry in marine settings. Its versatility makes it a common choice for various marine applications, but buyers should assess their specific environmental conditions to ensure suitability.
What Are the Benefits of Using Okoume Plywood in Marine Applications?
Okoume plywood, sourced from the Okoume tree, is known for its lightweight and strong properties. It has a natural resistance to moisture and is often treated to enhance its durability against marine conditions.
Pros & Cons:
The primary advantage of Okoume plywood is its lightweight nature, which is crucial for applications where weight reduction is essential, such as in boat construction. However, it may not be as durable as other materials like phenolic resin bonded plywood, leading to a shorter lifespan in harsh environments.
Impact on Application:
Okoume plywood is suitable for the construction of lightweight boats and interior fittings. Its aesthetic appeal and ease of handling make it popular among manufacturers, but buyers should consider its longevity in saltwater applications.
Why Choose Marine Birch Plywood for High-Performance Needs?
Marine birch plywood is known for its high strength-to-weight ratio and excellent surface finish, making it a premium choice for high-performance marine applications. It is resistant to moisture and has good temperature stability.
Pros & Cons:
The key advantage of marine birch plywood is its superior strength and durability, making it ideal for demanding applications. However, the cost can be significantly higher than other options, which may deter budget-conscious buyers.
Impact on Application:
This material is often used in high-end boat interiors and structural components where performance is critical. Buyers should be aware of the need for compliance with international standards, especially when exporting products.
Summary Table of Material Selection for Marine Plywood Manufacturing
Material | Typical Use Case for marine plywood manufacturer | Key Advantage | Key Disadvantage/Limitation | Relative Cost (Low/Med/High) |
---|---|---|---|---|
Phenolic Resin Bonded Plywood | Boat hulls, docks, marine structures | Excellent water resistance and durability | Higher cost and manufacturing complexity | High |
Marine Grade Plywood | Small boats, furniture, cabinetry | Good balance of performance and cost | Limited performance in extreme conditions | Medium |
Okoume Plywood | Lightweight boats, interior fittings | Lightweight and easy to handle | Shorter lifespan in harsh environments | Medium |
Marine Birch Plywood | High-end boat interiors, structural components | Superior strength and durability | Higher cost compared to alternatives | High |
This guide provides international B2B buyers with a strategic approach to selecting the right materials for marine plywood manufacturing, ensuring compliance with regional standards and suitability for specific applications.
In-depth Look: Manufacturing Processes and Quality Assurance for marine plywood manufacturer
What Are the Main Stages in the Manufacturing Process of Marine Plywood?
Marine plywood is specifically engineered to withstand the harsh conditions of marine environments, making its manufacturing process critical for quality. The production of marine plywood involves several key stages:
-
Material Preparation: The first step involves selecting high-quality logs, typically hardwood species such as Meranti, Okoume, or Douglas Fir. These logs are debarked and cut into veneers, which are then dried to a specific moisture content to prevent warping and ensure optimal bonding during assembly.
-
Forming: In this stage, the dried veneers are laid out in a cross-laminated manner. This technique enhances the strength and stability of the plywood. The orientation of the grain in each layer is crucial; typically, the grain of adjacent layers runs perpendicular to one another, providing added strength.
-
Assembly: The veneers are glued together using waterproof adhesives, which are essential for marine applications. Hot pressing is often employed, where heat and pressure are applied to ensure a strong bond between layers. The pressing duration and conditions are meticulously controlled to achieve the desired thickness and density.
-
Finishing: After assembly, the marine plywood is trimmed and sanded to ensure smooth surfaces. A protective coating, such as marine-grade varnish or epoxy, is often applied to enhance water resistance and longevity. This finishing step is vital for aesthetic appeal and functional durability.
How is Quality Assurance Implemented in Marine Plywood Manufacturing?
Quality assurance (QA) in marine plywood manufacturing is paramount to ensure that the final product meets international standards and customer expectations. Here are the key components of a robust QA process:
-
International Standards Compliance: Many manufacturers adhere to international standards such as ISO 9001, which focuses on quality management systems. Additionally, industry-specific certifications such as CE marking (for European markets) and API standards (for oil and gas applications) are crucial.
-
Quality Control Checkpoints: The QA process incorporates multiple checkpoints:
– Incoming Quality Control (IQC): This initial stage verifies the quality of raw materials (veneer and adhesives) before they enter the production line. Suppliers must provide certificates of compliance to ensure materials meet specified standards.
– In-Process Quality Control (IPQC): During production, continuous monitoring is conducted. This includes checking adhesive application, pressing parameters, and veneer alignment.
– Final Quality Control (FQC): After the product is completed, a thorough inspection is conducted to ensure it meets the specified dimensions, weight, and surface finish. Any defects are identified and rectified at this stage. -
Common Testing Methods for Marine Plywood: Various tests are conducted to assess the quality of marine plywood, including:
– Moisture Content Testing: Ensures that the plywood maintains an optimal moisture level to prevent future warping.
– Bonding Strength Tests: Evaluates the strength of adhesive bonds under various conditions.
– Water Resistance Tests: Assesses the plywood’s ability to withstand prolonged exposure to water without delaminating.
How Can B2B Buyers Verify Supplier Quality Control Practices?
For international B2B buyers, particularly those from Africa, South America, the Middle East, and Europe, verifying a marine plywood manufacturer’s quality control practices is essential. Here are actionable strategies:
-
Supplier Audits: Conducting audits of potential suppliers allows buyers to assess their manufacturing processes, quality control measures, and compliance with international standards. This can be done through on-site visits or virtual inspections.
-
Reviewing Quality Assurance Reports: Requesting detailed QA reports from suppliers can provide insights into their quality management systems. These reports should include results from IQC, IPQC, and FQC, as well as any corrective actions taken for non-conformities.
-
Third-Party Inspections: Engaging third-party inspection services can offer an unbiased evaluation of the supplier’s quality control processes. These inspections can verify compliance with industry standards and provide certification that may be required for importation.
-
Understanding Certification Nuances: Different regions have varying certification requirements. For example, European buyers must be aware of CE marking regulations, while buyers in the Middle East may require compliance with local standards. Understanding these nuances is crucial for seamless procurement.
What Are the Challenges and Considerations for International B2B Buyers?
International B2B buyers face unique challenges when sourcing marine plywood, particularly in relation to quality assurance. Here are key considerations:
-
Cultural and Regulatory Differences: Buyers must navigate different regulatory environments and cultural practices that may affect quality expectations. This may require additional research and potentially adapting procurement strategies.
-
Supply Chain Transparency: Ensuring transparency in the supply chain is vital. Buyers should seek suppliers who are willing to share their sourcing practices and provide traceability for raw materials used in production.
-
Long-Term Relationships: Establishing long-term relationships with trusted suppliers can mitigate risks associated with quality inconsistency. Regular communication and collaboration can help ensure that quality standards are maintained over time.
-
Market Trends and Innovations: Keeping abreast of innovations in marine plywood manufacturing, such as advancements in adhesive technology or sustainable sourcing practices, can provide a competitive edge. Buyers should consider suppliers who invest in R&D to enhance product quality and sustainability.
In summary, understanding the manufacturing processes and quality assurance practices of marine plywood manufacturers is essential for B2B buyers looking to procure high-quality products. By focusing on rigorous quality control measures, international standards compliance, and proactive supplier verification, buyers can ensure that they receive reliable and durable marine plywood suited for their specific applications.
Practical Sourcing Guide: A Step-by-Step Checklist for ‘marine plywood manufacturer’
To ensure a successful procurement process for marine plywood, this practical sourcing guide provides a comprehensive checklist. By following these steps, international B2B buyers from regions such as Africa, South America, the Middle East, and Europe can effectively navigate their sourcing journey, ensuring quality and value from suppliers.
Step 1: Define Your Technical Specifications
Begin by outlining the specific requirements for your marine plywood. Consider factors such as thickness, grade, and treatment methods. Clear specifications will help you communicate effectively with potential suppliers and ensure that the products meet your operational needs.
- Key Considerations:
- What is the intended application of the marine plywood?
- Are there specific industry standards or certifications required in your region?
Step 2: Research Potential Suppliers
Conduct thorough research to identify credible marine plywood manufacturers. Utilize online resources, industry directories, and trade shows to compile a list of potential suppliers. This step is vital as it lays the foundation for your procurement process.
- Action Points:
- Look for manufacturers with a strong online presence and positive reviews.
- Focus on suppliers who specialize in marine-grade products.
Step 3: Evaluate Supplier Certifications
Once you have a shortlist, verify the certifications and standards of potential suppliers. Certifications such as ISO, CE marking, or specific marine standards demonstrate a commitment to quality and safety.
- Why It Matters:
- Certifications ensure that the products comply with international quality standards.
- They reduce the risk of acquiring subpar materials that could lead to project failures.
Step 4: Request Samples and Test Quality
Before finalizing any contracts, request samples from your top suppliers. Testing the quality of marine plywood through physical samples can provide insights into its performance under real-world conditions.
- Testing Criteria:
- Assess the plywood’s durability, water resistance, and finish.
- Check for any defects or inconsistencies in the material.
Step 5: Negotiate Terms and Conditions
Engage in negotiations with your selected suppliers to establish favorable terms. Discuss pricing, delivery schedules, and payment terms. A clear agreement protects both parties and helps avoid misunderstandings later on.
- Key Negotiation Points:
- What are the minimum order quantities?
- Are there any warranties or return policies in place?
Step 6: Establish Logistics and Shipping Arrangements
Plan the logistics of transporting the marine plywood to your location. Consider factors like shipping costs, lead times, and customs regulations that may affect delivery.
- Considerations:
- What are the shipping options available from the supplier’s location?
- Are there any additional fees that may arise during customs clearance?
Step 7: Monitor Supplier Performance Post-Purchase
After procurement, continuously monitor the performance of your chosen supplier. Gather feedback from your team regarding product quality and service delivery to assess whether the supplier meets your expectations over time.
- Feedback Mechanisms:
- Set up regular check-ins with your supplier.
- Encourage your team to report any issues promptly.
By following this structured checklist, B2B buyers can enhance their sourcing process for marine plywood, ensuring that they partner with reliable manufacturers who can meet their specific needs effectively.
Comprehensive Cost and Pricing Analysis for marine plywood manufacturer Sourcing
What Are the Key Cost Components in Marine Plywood Manufacturing?
When sourcing marine plywood, understanding the cost structure is crucial for international B2B buyers. The primary cost components include:
-
Materials: The quality of wood, adhesive, and finishes significantly influences the price. Marine-grade plywood often uses durable, water-resistant materials that can increase costs but provide better longevity.
-
Labor: Skilled labor is essential in the production of high-quality marine plywood. Labor costs can vary widely depending on the region, with higher wages in Europe compared to Africa or South America.
-
Manufacturing Overhead: This includes costs related to factory operations such as utilities, equipment maintenance, and administrative expenses. Efficient manufacturing processes can help mitigate these costs.
-
Tooling: The initial investment in machinery and tools can be substantial, but it can also enhance production efficiency. Manufacturers may pass these costs onto buyers, especially for customized orders.
-
Quality Control (QC): Rigorous QC processes ensure that the plywood meets international standards. While this adds to the cost, it is essential for maintaining product integrity and buyer satisfaction.
-
Logistics: Transportation costs, including shipping and customs duties, can significantly impact the overall price. Buyers need to account for these when evaluating suppliers, especially for international shipments.
-
Margin: Manufacturers typically include a profit margin, which can vary based on market conditions and competition.
How Do Pricing Influencers Affect Marine Plywood Costs?
Several factors can influence the pricing of marine plywood, making it essential for buyers to understand these nuances:
-
Volume/MOQ (Minimum Order Quantity): Larger orders often lead to lower per-unit costs. Buyers should negotiate for bulk pricing to maximize cost efficiency.
-
Specifications and Customization: Custom orders can increase costs due to the need for specialized materials or processes. Clearly defined specifications can help avoid unexpected expenses.
-
Material Quality and Certifications: Higher quality materials and certifications (e.g., FSC certification) can raise costs but may be necessary for certain projects, especially in regulated markets like Europe.
-
Supplier Factors: The reputation and reliability of suppliers can impact pricing. Established suppliers may charge more due to their proven track record and quality assurance.
-
Incoterms: Understanding shipping terms is critical. Terms like FOB (Free On Board) or CIF (Cost, Insurance, and Freight) can affect the total landed cost of the product.
What Are Effective Buyer Tips for Negotiating Marine Plywood Prices?
For international B2B buyers, especially from regions such as Africa, South America, the Middle East, and Europe, the following strategies can enhance negotiation outcomes:
-
Conduct a Total Cost of Ownership Analysis: Look beyond the initial purchase price. Evaluate logistics, potential delays, and quality issues that could incur additional costs down the line.
-
Leverage Competitive Bids: Engage multiple suppliers to create competitive tension. This can lead to better pricing and terms.
-
Understand Local Market Dynamics: Familiarize yourself with the local market conditions of the supplier’s country. Factors such as currency fluctuations and economic stability can influence pricing.
-
Be Prepared to Walk Away: Establish a clear budget and stick to it. If a supplier cannot meet your financial expectations, be ready to explore alternatives.
-
Build Long-term Relationships: Establishing a good rapport with suppliers can lead to better pricing and priority service in the future. Regular communication and feedback can enhance this partnership.
Disclaimer Regarding Indicative Prices
It is important to note that the prices discussed in this analysis are indicative and can vary based on market conditions, specific supplier negotiations, and changes in material costs. Buyers should conduct thorough research and due diligence to obtain accurate and current pricing information tailored to their specific needs.
Alternatives Analysis: Comparing marine plywood manufacturer With Other Solutions
Understanding the Importance of Exploring Alternatives
In the marine and construction industries, selecting the right materials is crucial for ensuring durability and functionality. While marine plywood is a well-known solution for projects requiring water resistance and structural integrity, several alternative materials and methods may also meet these needs. This analysis compares marine plywood manufacturers with other viable options to help international B2B buyers make informed decisions.
Comparison Aspect | Marine Plywood Manufacturer | Fiber-Reinforced Polymer (FRP) | Steel Marine Panels |
---|---|---|---|
Performance | Excellent water resistance and structural strength. | High tensile strength and corrosion resistance. | Very strong and durable, but heavier. |
Cost | Moderate to high, depending on quality. | High initial investment, but lower long-term costs. | Generally more expensive, especially with custom designs. |
Ease of Implementation | Requires skilled labor for installation. | Can be prefabricated, reducing on-site labor. | Heavy and may require specialized equipment for installation. |
Maintenance | Requires regular sealing and inspection. | Minimal maintenance needed; resistant to rot and corrosion. | Low maintenance, but may require periodic inspections for rust. |
Best Use Case | Ideal for boats and marine structures. | Best for high-performance applications, such as offshore structures. | Suitable for heavy-duty applications requiring superior strength. |
What Are the Advantages and Disadvantages of Fiber-Reinforced Polymer (FRP)?
Fiber-Reinforced Polymer (FRP) is a composite material that combines fibers, such as glass or carbon, with a resin. Its primary advantage lies in its exceptional strength-to-weight ratio and resistance to corrosion, making it suitable for marine applications. Additionally, FRP can be prefabricated, which streamlines installation and reduces labor costs on-site. However, the initial investment for FRP can be significantly higher than marine plywood, which may deter some buyers. Moreover, while it offers minimal maintenance, repair options can be limited compared to wood-based products.
How Do Steel Marine Panels Compare to Marine Plywood?
Steel marine panels are another alternative that offers considerable strength and durability. They are commonly used in shipbuilding and heavy-duty marine structures where superior load-bearing capacity is essential. The robustness of steel panels means they can withstand harsh marine conditions, but they are heavier than marine plywood, which may complicate transport and installation. Additionally, while steel is generally low-maintenance, it can be susceptible to rust, necessitating protective coatings and inspections. The cost of steel panels is typically higher, especially for custom designs, making them less accessible for smaller projects.
Conclusion: How to Choose the Right Solution for Your Needs?
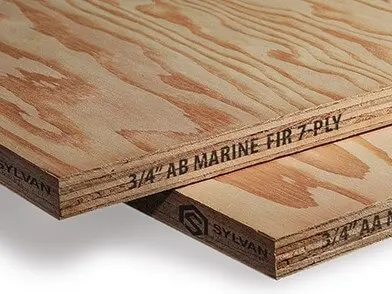
A stock image related to marine plywood manufacturer.
When deciding between marine plywood and its alternatives, B2B buyers should consider several factors, including the specific requirements of their projects, budget constraints, and long-term maintenance plans. Marine plywood is an excellent choice for many applications due to its balance of performance and cost. However, for projects that demand exceptional strength and durability, alternatives like FRP or steel panels may provide better long-term value despite their higher upfront costs. Ultimately, evaluating the unique demands of each project will guide buyers in selecting the most appropriate material or method for their needs.
Essential Technical Properties and Trade Terminology for marine plywood manufacturer
What Are the Key Technical Properties of Marine Plywood?
Understanding the technical properties of marine plywood is essential for international B2B buyers, especially those in Africa, South America, the Middle East, and Europe. Here are some critical specifications to consider:
1. Material Grade
Marine plywood is categorized into different grades based on quality. The most common grades are A, B, C, and D, with ‘A’ being the highest quality. This grading affects the plywood’s appearance, durability, and resistance to moisture. For B2B buyers, selecting the appropriate grade ensures that the plywood meets specific project requirements and longevity expectations.
2. Bonding Type
The bonding type refers to the adhesive used in the plywood. Marine plywood typically uses phenolic or waterproof adhesives that withstand water exposure. Understanding the bonding type is crucial for buyers since it determines the plywood’s water resistance and overall strength. This knowledge helps in selecting the right product for marine applications, reducing the risk of delamination and failure.
3. Thickness Tolerance
Thickness tolerance indicates the permissible variation in the plywood’s thickness. For marine applications, a consistent thickness is vital to ensure structural integrity and performance. Buyers should pay attention to the specified tolerance levels, as variations can impact the overall project quality and installation processes.
4. Moisture Content
The moisture content of marine plywood should ideally be between 8-12% for optimal performance. Higher moisture content can lead to warping, swelling, or even mold growth. B2B buyers must confirm the moisture content during procurement to ensure that the plywood is suitable for their specific environmental conditions.
5. Mechanical Properties
Mechanical properties such as tensile strength, bending strength, and modulus of elasticity are critical indicators of plywood performance under load. Buyers should assess these properties based on their project requirements, as they directly influence the plywood’s capacity to endure stresses and impacts.
What Are Common Trade Terms Related to Marine Plywood Manufacturing?
Navigating the marine plywood market requires familiarity with specific trade terminology. Here are some essential terms that B2B buyers should know:
1. OEM (Original Equipment Manufacturer)
OEM refers to companies that produce products that are marketed by another company under its own brand. For marine plywood buyers, understanding OEM relationships can help in sourcing high-quality products that meet specific standards while ensuring brand integrity.
2. MOQ (Minimum Order Quantity)
MOQ is the smallest quantity of a product that a supplier is willing to sell. It’s crucial for buyers to understand MOQs, as they can significantly affect procurement strategies and inventory management. Low MOQs can be beneficial for smaller projects, while larger orders may offer cost efficiencies.
3. RFQ (Request for Quotation)
An RFQ is a document that buyers send to suppliers to request pricing for specific products. For marine plywood procurement, issuing an RFQ allows buyers to compare prices, specifications, and lead times from multiple suppliers, facilitating informed decision-making.
4. Incoterms (International Commercial Terms)
Incoterms are standardized trade terms that define the responsibilities of buyers and sellers in international transactions. Familiarity with Incoterms such as FOB (Free on Board) or CIF (Cost, Insurance, and Freight) is essential for B2B buyers to understand shipping responsibilities and cost implications.
5. Certification Standards
Certification standards, such as BS 1088 or EN 636, validate the quality and suitability of marine plywood for specific applications. Buyers should look for these certifications to ensure compliance with international quality and safety standards, enhancing the credibility of their procurement choices.
By grasping these technical properties and trade terms, international B2B buyers can make more informed decisions when sourcing marine plywood, ultimately leading to successful project outcomes.
Navigating Market Dynamics and Sourcing Trends in the marine plywood manufacturer Sector
What Are the Key Market Dynamics Affecting Marine Plywood Manufacturers?
The marine plywood market has been experiencing significant growth driven by various global factors. Rising construction activities in developing regions, particularly in Africa and South America, are leading to increased demand for high-quality marine plywood. Additionally, the expansion of the maritime industry and recreational boating in Europe and the Middle East creates new opportunities for manufacturers. Digital transformation is also reshaping the sourcing landscape. Technologies such as AI and blockchain are being adopted to enhance transparency in the supply chain, improve inventory management, and streamline procurement processes. International B2B buyers should consider suppliers who leverage these technologies to optimize their operations.
Emerging trends indicate a growing preference for customized marine plywood solutions, tailored to specific project requirements. This trend is particularly relevant in regions like Spain and the UK, where architectural designs demand unique specifications. Furthermore, the shift towards sustainable building materials is influencing procurement decisions, as buyers increasingly seek eco-friendly options without compromising on quality. Understanding these dynamics is essential for international buyers to make informed decisions and remain competitive in their respective markets.
How Is Sustainability Shaping the Sourcing of Marine Plywood?
Sustainability is becoming a critical consideration in the marine plywood sector, impacting both production practices and supply chain dynamics. The environmental impact of deforestation and resource depletion has prompted a shift toward more responsible sourcing practices. International B2B buyers are now prioritizing suppliers who demonstrate a commitment to sustainability through certified practices, such as sourcing timber from responsibly managed forests. Certifications like FSC (Forest Stewardship Council) and PEFC (Programme for the Endorsement of Forest Certification) are increasingly recognized as benchmarks for ethical sourcing in marine plywood manufacturing.
Moreover, the importance of ethical supply chains cannot be overstated. Buyers are now scrutinizing their suppliers’ environmental policies and labor practices to ensure compliance with global standards. The push for ‘green’ materials is not just a trend; it is becoming a prerequisite for businesses aiming to enhance their brand reputation and meet regulatory requirements. As buyers from Africa, South America, the Middle East, and Europe look to source marine plywood, they should engage with manufacturers that prioritize sustainability and provide clear documentation of their environmental impact and sourcing practices.
How Has the Marine Plywood Industry Evolved Over Time?
The marine plywood industry has evolved significantly over the past few decades, adapting to changing consumer needs and technological advancements. Initially, marine plywood was primarily used for boat building, but its applications have expanded to include construction, furniture, and marine infrastructure. The introduction of advanced manufacturing techniques has improved the durability and water resistance of marine plywood, making it suitable for a broader range of applications.
Moreover, the globalization of trade has enabled manufacturers to source raw materials from different regions, creating a more competitive market landscape. As international B2B buyers navigate this sector, understanding its historical context can provide valuable insights into current market dynamics and future trends. This knowledge will empower buyers to make strategic sourcing decisions that align with their business goals.
Frequently Asked Questions (FAQs) for B2B Buyers of marine plywood manufacturer
-
How do I evaluate the quality of marine plywood from manufacturers?
When sourcing marine plywood, it’s essential to assess quality through several criteria. First, check for certifications such as BS 1088 or EN 636, which indicate compliance with international standards. Request samples to evaluate the plywood’s durability, water resistance, and finish. Additionally, inquire about the sourcing of raw materials and manufacturing processes. Establishing a relationship with the manufacturer can also provide insights into their quality control measures. -
What are the key specifications to consider when purchasing marine plywood?
Key specifications include thickness, grade, and type of adhesive used. Marine plywood typically ranges from 4mm to 25mm in thickness. Grades (such as A-B or B-B) determine the surface quality and internal voids. It’s crucial to understand the type of adhesive—phenolic or waterproof—used in the plywood, as this affects its resistance to moisture and durability. Always align these specifications with your project requirements. -
What is the minimum order quantity (MOQ) for marine plywood?
Minimum order quantities can vary significantly between manufacturers. Generally, MOQs for marine plywood range from 100 to 500 sheets, depending on the supplier’s capacity and your specific needs. Discussing your project size and future demand with the manufacturer can lead to more favorable terms. If your order falls below the MOQ, consider negotiating or collaborating with other buyers to meet the requirements. -
How can I ensure timely delivery when sourcing marine plywood internationally?
To ensure timely delivery, establish clear communication with your supplier regarding lead times and shipping methods. Confirm the manufacturer’s production capacity and their ability to meet deadlines. Utilizing Incoterms like FOB (Free on Board) or CIF (Cost, Insurance, and Freight) can clarify responsibilities for shipping. Additionally, consider working with logistics partners experienced in international shipping to mitigate delays. -
What payment terms should I negotiate with marine plywood manufacturers?
Payment terms can vary widely, but common practices include 30% upfront with the balance due upon delivery or after inspection. For larger orders, consider negotiating extended payment terms or letter of credit to reduce upfront costs. Always clarify the currency used for transactions and any potential fees associated with international payments. Establishing trust with the manufacturer can facilitate more favorable payment arrangements. -
How do I vet a marine plywood supplier before making a purchase?
Vetting suppliers involves researching their background, client testimonials, and industry reputation. Request references from previous customers and check for any certifications or memberships in trade organizations. Conducting a factory visit or using third-party inspection services can provide further assurance of their manufacturing capabilities. Online platforms and trade shows can also serve as valuable resources for supplier vetting. -
Can marine plywood be customized for specific projects?
Yes, many manufacturers offer customization options for marine plywood. Customization can include specific dimensions, thicknesses, and finishes tailored to your project requirements. Be prepared to discuss your needs in detail and understand the implications on pricing and lead times. Always request samples of customized products to ensure they meet your quality expectations before placing a larger order. -
What quality assurance processes should I expect from marine plywood manufacturers?
Reputable marine plywood manufacturers implement rigorous quality assurance processes. These typically include raw material inspections, in-process quality checks, and final product testing. Ask about their quality control certifications and specific testing methods, such as moisture resistance or adhesive bond strength. Establishing a clear quality assurance agreement in your contract can help ensure that you receive products that meet your specifications and standards.
Important Disclaimer & Terms of Use
⚠️ Important Disclaimer
The information provided in this guide, including content regarding manufacturers, technical specifications, and market analysis, is for informational and educational purposes only. It does not constitute professional procurement advice, financial advice, or legal advice.
While we have made every effort to ensure the accuracy and timeliness of the information, we are not responsible for any errors, omissions, or outdated information. Market conditions, company details, and technical standards are subject to change.
B2B buyers must conduct their own independent and thorough due diligence before making any purchasing decisions. This includes contacting suppliers directly, verifying certifications, requesting samples, and seeking professional consultation. The risk of relying on any information in this guide is borne solely by the reader.
Strategic Sourcing Conclusion and Outlook for marine plywood manufacturer
How Can Strategic Sourcing Enhance Your Marine Plywood Procurement?
In conclusion, the strategic sourcing of marine plywood is essential for international B2B buyers looking to optimize their procurement processes and enhance product quality. By focusing on supplier reliability, cost-effectiveness, and sustainability, companies in Africa, South America, the Middle East, and Europe can significantly improve their supply chain resilience. Key takeaways include the importance of establishing long-term relationships with reputable manufacturers, leveraging technology for better supply chain visibility, and prioritizing eco-friendly sourcing practices.
As the demand for marine plywood continues to rise due to global construction and marine industries’ growth, buyers must stay ahead by adopting innovative sourcing strategies. This proactive approach will not only ensure compliance with international standards but also position your business favorably in a competitive market.
What’s Next for International B2B Buyers in Marine Plywood?
Looking ahead, international buyers should engage in market research and remain adaptable to evolving industry trends. Collaborating with manufacturers that prioritize quality and sustainability will be crucial. Embrace strategic partnerships and stay informed about technological advancements in the sourcing process. By taking these steps, you can secure a reliable supply of marine plywood that meets your operational needs while contributing to a more sustainable future. Now is the time to act—evaluate your sourcing strategies and build a robust supply chain that can withstand the challenges of tomorrow.