Discover Cost-Saving Strategies for Machine Tools China (2025)
Introduction: Navigating the Global Market for machine tools china
In an increasingly competitive global landscape, sourcing high-quality machine tools from China poses unique challenges for international B2B buyers. Whether you are in Africa, South America, the Middle East, or Europe, navigating the complexities of supplier selection, cost management, and quality assurance can be daunting. This comprehensive guide aims to simplify the process of sourcing machine tools from China, providing you with actionable insights to make informed purchasing decisions.
From a detailed analysis of various types of machine tools—such as CNC machines, lathes, and milling machines—to their diverse applications across industries, this guide covers it all. We delve into the critical aspects of supplier vetting, ensuring you know how to assess reliability and compliance. Additionally, we address cost considerations, including import duties and shipping fees, to help you budget effectively for your procurement needs.
By arming yourself with the information in this guide, you will be better equipped to navigate the global market for machine tools from China, ultimately enhancing your operational efficiency and competitiveness. This resource is particularly tailored for B2B buyers in regions like Argentina and Indonesia, ensuring that your specific needs and challenges are met with expert insights and practical solutions.
Understanding machine tools china Types and Variations
Type Name | Key Distinguishing Features | Primary B2B Applications | Brief Pros & Cons for Buyers |
---|---|---|---|
CNC Machines | Computer-controlled for precision and automation | Aerospace, automotive, electronics | Pros: High precision, repeatability. Cons: Higher initial cost, requires skilled operators. |
Lathes | Rotating workpiece with cutting tools for shaping | Metal fabrication, woodwork | Pros: Versatile for various materials. Cons: Limited to cylindrical shapes. |
Milling Machines | Uses rotary cutters to remove material from a workpiece | Engineering, mold making | Pros: Ideal for complex shapes, high productivity. Cons: Maintenance can be intensive. |
Grinding Machines | Abrasive wheels for finishing and surface improvement | Tool manufacturing, automotive | Pros: Excellent surface finish, precise dimensions. Cons: Slower process, potential for heat damage. |
Laser Cutting Machines | Uses focused laser beams for cutting materials | Sign making, metal fabrication | Pros: High accuracy, ability to cut intricate designs. Cons: Equipment can be costly, requires safety precautions. |
What are CNC Machines and Their B2B Applications?
CNC (Computer Numerical Control) machines are highly sophisticated tools that automate machining processes through computer programming. They are distinguished by their ability to perform complex cuts and shapes with high precision. B2B buyers in sectors such as aerospace and automotive benefit from CNC machines due to their ability to produce consistent and repeatable parts. When considering a CNC machine, buyers should evaluate initial costs against long-term productivity gains and the need for skilled personnel to operate and maintain these machines.
How Do Lathes Fit into the Manufacturing Process?
Lathes are traditional machine tools that rotate a workpiece against a stationary cutting tool. They are widely used for shaping materials into cylindrical forms and are essential in metal fabrication and woodworking. The versatility of lathes makes them suitable for a range of applications, from creating simple parts to complex geometries. Buyers should consider the type of materials they will be working with and the specific shapes needed when investing in a lathe, as they are limited to rotational symmetry.
What Makes Milling Machines Essential for Complex Shapes?
Milling machines utilize rotating cutters to remove material from a workpiece, allowing for the creation of intricate shapes and designs. They are particularly useful in engineering and mold-making industries. The ability to work on multiple axes enhances their versatility. However, potential buyers should be aware of maintenance requirements and operational costs, as milling machines can be more complex to service compared to simpler machine tools.
Why Choose Grinding Machines for Surface Finishing?
Grinding machines are specialized tools that use abrasive wheels to achieve a high-quality surface finish on various materials. They are crucial in tool manufacturing and automotive applications, where precise dimensions and smooth finishes are essential. While grinding machines provide excellent results, they operate at slower speeds compared to other machining processes, which may affect production timelines. Buyers should assess their finishing needs and production speed requirements when considering grinding machines.
What are the Advantages of Laser Cutting Machines?
Laser cutting machines employ focused laser beams to cut materials with remarkable precision, making them ideal for intricate designs in industries such as sign making and metal fabrication. The ability to cut through various materials, including metals, plastics, and wood, adds to their versatility. However, buyers should factor in the high initial investment and ongoing operational costs, as well as the need for safety measures when operating laser cutting equipment.
Related Video: China‘s Machine Tools 50 Years Behind West; A 1.4 Billion Nation Bested by 200-Person Japanese Shops
Key Industrial Applications of machine tools china
Industry/Sector | Specific Application of machine tools china | Value/Benefit for the Business | Key Sourcing Considerations for this Application |
---|---|---|---|
Aerospace | Precision machining for aircraft components | High accuracy and reduced waste, ensuring safety and reliability in aerospace products | Certifications (e.g., AS9100), supplier reliability, and advanced technology capabilities |
Automotive | CNC machining for engine parts | Enhanced production efficiency and precision, leading to improved vehicle performance | Cost competitiveness, quality control measures, and delivery timelines |
Construction | Fabrication of structural steel components | Strength and durability of structures, contributing to safety and longevity | Compliance with local regulations, material specifications, and customization options |
Electronics | Production of circuit boards and enclosures | Faster production cycles and higher precision, reducing time-to-market for electronic devices | Technological compatibility, scalability, and after-sales support |
Medical Devices | Manufacturing of surgical instruments | Ensures high standards of hygiene and precision, critical for patient safety | Quality certifications (ISO 13485), material sourcing, and customization capabilities |
How Are Machine Tools from China Used in Aerospace?
In the aerospace industry, machine tools from China are utilized for precision machining of aircraft components, such as turbine blades and structural parts. These tools help manufacturers achieve the high accuracy required to meet stringent safety standards. International buyers must prioritize suppliers with certifications like AS9100, ensuring compliance with industry standards. Additionally, advanced technology capabilities are crucial for producing lightweight yet durable materials, which are essential for modern aircraft.
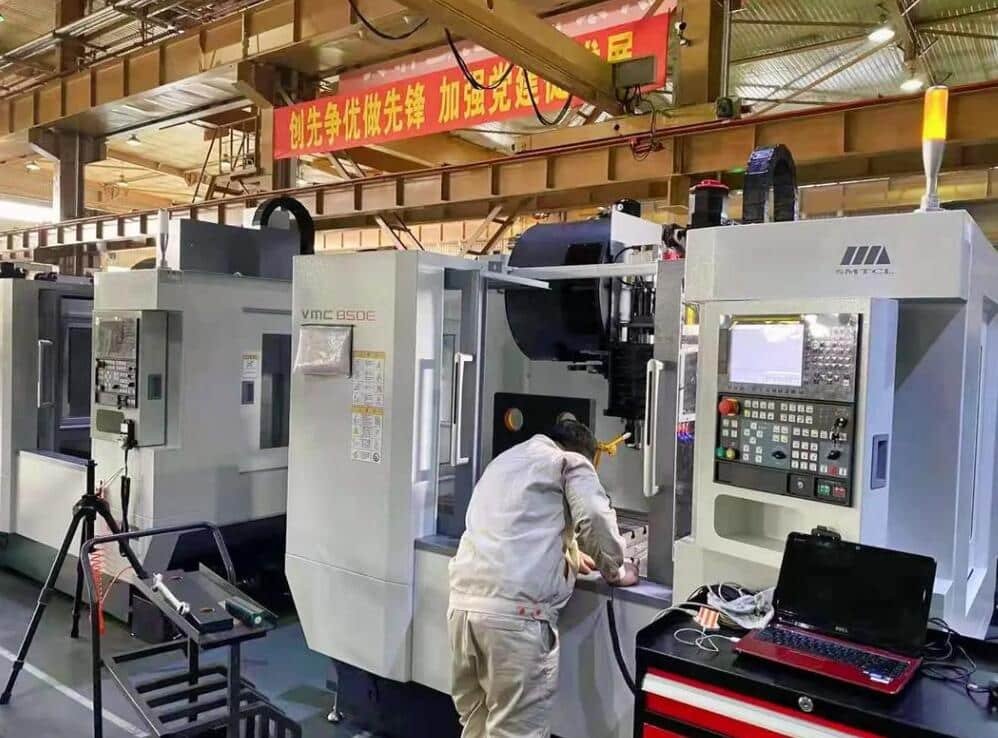
A stock image related to machine tools china.
What Role Do Machine Tools Play in the Automotive Sector?
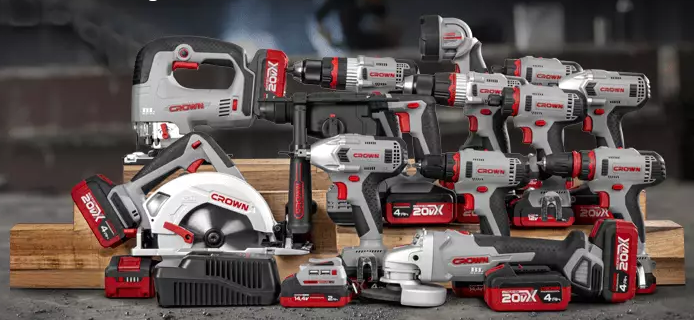
A stock image related to machine tools china.
The automotive sector leverages CNC machining technology from China for the production of engine parts, transmission systems, and chassis components. These machine tools enhance production efficiency and precision, which directly impacts vehicle performance and reliability. When sourcing, international buyers should focus on cost competitiveness and the supplier’s quality control measures to ensure consistent output. Delivery timelines are also critical, as the automotive industry often operates on tight schedules.
How Are Machine Tools Applied in Construction?
In construction, machine tools are essential for fabricating structural steel components, such as beams and columns. These tools ensure the strength and durability of structures, which is paramount for safety and longevity. For buyers in regions like Africa and South America, compliance with local regulations and material specifications is vital. Furthermore, the ability to customize solutions to fit specific project requirements can be a significant advantage when sourcing from Chinese manufacturers.
Why Are Machine Tools Important for Electronics Manufacturing?
Machine tools from China are crucial in the electronics sector, particularly for producing circuit boards and enclosures. The precision offered by these tools allows for faster production cycles, which is essential for reducing time-to-market for electronic devices. Buyers should consider technological compatibility with existing systems and the scalability of the supplier’s operations. Additionally, robust after-sales support can greatly enhance the overall value of the partnership.
How Do Machine Tools Contribute to Medical Device Production?
In the medical device industry, machine tools from China are used to manufacture surgical instruments and diagnostic equipment. The high standards of hygiene and precision required in this sector are critical for patient safety. International buyers must ensure that suppliers hold quality certifications like ISO 13485 and can source appropriate materials. Customization capabilities are also important, as medical devices often require specific designs to meet regulatory standards.
Related Video: The Q5 CNC punching machine with forming and bending capabilities
3 Common User Pain Points for ‘machine tools china’ & Their Solutions
Scenario 1: Navigating Quality Assurance in Machine Tools from China
The Problem: One of the most pressing challenges for B2B buyers sourcing machine tools from China is the inconsistency in quality. Many companies have encountered issues where the machinery does not meet the specifications promised by suppliers. This can lead to significant operational disruptions, delays in production, and financial losses. Buyers may feel overwhelmed by the vast array of options available, making it difficult to ascertain which suppliers can deliver reliable, high-quality products.
The Solution: To navigate this challenge, B2B buyers should implement a robust vendor evaluation process. Start by conducting thorough research on potential suppliers, focusing on their certifications and previous customer reviews. Engaging third-party inspection services before shipment can also ensure the products meet your quality standards. Additionally, consider establishing a trial order for critical equipment to assess performance in your specific context. Collaborating with local agents or consultants in China can provide valuable insights into reliable suppliers and help mitigate risks associated with quality discrepancies.
Scenario 2: Overcoming Language Barriers and Communication Issues
The Problem: Language barriers can create significant communication challenges for international buyers dealing with Chinese manufacturers. Misunderstandings regarding specifications, delivery schedules, and payment terms can lead to frustration and costly errors. Many buyers report feeling isolated when trying to resolve issues, as they struggle to communicate effectively with suppliers.
The Solution: To overcome these communication hurdles, buyers should consider hiring a bilingual procurement specialist or using translation services to facilitate discussions with suppliers. Clearly documented specifications and expectations in both languages can minimize misunderstandings. Utilizing visual aids, such as diagrams and videos, can also enhance clarity. Moreover, establishing regular check-ins via video calls can foster a stronger relationship and ensure that both parties remain aligned throughout the purchasing process. Building a rapport with the supplier can lead to better cooperation and smoother transactions.
Scenario 3: Managing Logistics and Supply Chain Complexity
The Problem: International logistics can be a daunting task, particularly when sourcing machine tools from China. Buyers often face delays due to customs clearance, transportation issues, or inadequate supply chain management. Such disruptions can halt production lines, leading to lost revenue and strained customer relationships. The complexity of coordinating shipments across borders can leave buyers feeling anxious and uncertain.
The Solution: To effectively manage logistics, buyers should partner with experienced freight forwarders who specialize in international shipments from China. These professionals can navigate customs regulations, optimize shipping routes, and provide real-time tracking updates. It is also beneficial to utilize supply chain management software that offers insights into shipping timelines and potential delays. By maintaining open lines of communication with suppliers regarding inventory levels and production schedules, buyers can better anticipate needs and avoid last-minute rush orders. Implementing a flexible inventory strategy, such as just-in-time delivery, can also mitigate the risks associated with supply chain disruptions.
Strategic Material Selection Guide for machine tools china
What Are the Key Materials Used in Machine Tools from China?
When selecting materials for machine tools, international B2B buyers must consider various factors that affect performance, durability, and cost. Here, we analyze four common materials used in machine tools manufactured in China: steel, aluminum, cast iron, and composite materials. Each material has unique properties, advantages, and limitations that can significantly impact the performance of machine tools in various applications.
How Does Steel Perform as a Material for Machine Tools?
Steel is one of the most widely used materials in machine tool manufacturing due to its excellent mechanical properties. It offers high tensile strength, durability, and resistance to wear and deformation under high pressure and temperature.
Pros: Steel’s high strength-to-weight ratio makes it suitable for heavy-duty applications. It is also relatively cost-effective and can be easily machined to precise tolerances.
Cons: However, steel can be prone to corrosion if not properly treated, which may require additional coatings or treatments, increasing manufacturing complexity.
Impact on Application: Steel is compatible with various media, including oils and coolants, making it a versatile choice for machining operations.
Considerations for International Buyers: Buyers from regions like Africa and South America should ensure compliance with international standards such as ASTM and DIN for quality assurance.
What Are the Advantages of Aluminum in Machine Tool Applications?
Aluminum is gaining popularity in machine tool applications due to its lightweight nature and excellent corrosion resistance. Its thermal conductivity makes it ideal for applications requiring efficient heat dissipation.
Pros: The lightweight property of aluminum allows for faster machining speeds and reduced energy consumption during operation.
Cons: On the downside, aluminum is less rigid than steel, which may limit its use in high-stress applications.
Impact on Application: Aluminum’s compatibility with various cutting fluids enhances its usability in machining operations, particularly in aerospace and automotive industries.
Considerations for International Buyers: Buyers should look for aluminum grades that meet international standards, ensuring consistent quality and performance.
Why Is Cast Iron a Preferred Choice for Machine Tool Bases?
Cast iron is often used for machine tool bases due to its excellent damping properties, which reduce vibrations during operation. This material is known for its rigidity and stability.
Pros: Cast iron can absorb vibrations effectively, leading to improved machining precision and surface finish.
Cons: However, cast iron is heavy and can be brittle, making it less suitable for portable applications.
Impact on Application: The material’s ability to withstand high temperatures and pressures makes it ideal for heavy machining operations.
Considerations for International Buyers: Compliance with standards such as JIS (Japanese Industrial Standards) is crucial for ensuring quality and performance in international markets.
How Do Composite Materials Enhance Machine Tool Performance?
Composite materials, often a combination of polymers and reinforcing fibers, are increasingly used in specialized machine tools. They offer unique properties such as lightweight and high strength.
Pros: The primary advantage of composites is their ability to reduce weight while maintaining strength, which is beneficial in applications where weight is a critical factor.
Cons: However, composites can be more expensive to manufacture and may require specialized machining processes.
Impact on Application: Composites are particularly useful in aerospace and automotive applications, where weight savings can lead to significant performance improvements.
Considerations for International Buyers: Buyers must consider the specific material certifications and standards applicable in their regions, as composite materials can vary widely in quality and performance.
Summary Table of Material Selection for Machine Tools
Material | Typical Use Case for machine tools china | Key Advantage | Key Disadvantage/Limitation | Relative Cost (Low/Med/High) |
---|---|---|---|---|
Steel | Heavy-duty machining | High strength and durability | Prone to corrosion | Medium |
Aluminum | Aerospace and automotive applications | Lightweight and corrosion-resistant | Less rigidity than steel | Medium |
Cast Iron | Machine tool bases | Excellent vibration damping | Heavy and brittle | Medium |
Composite | Specialized applications | Lightweight with high strength | Higher manufacturing cost | High |
By understanding the properties, advantages, and limitations of these materials, international B2B buyers can make informed decisions that align with their specific operational needs and compliance requirements.
In-depth Look: Manufacturing Processes and Quality Assurance for machine tools china
What Are the Main Stages of Manufacturing Machine Tools in China?
The manufacturing of machine tools in China follows a structured process that ensures precision and quality. This process typically involves four main stages: material preparation, forming, assembly, and finishing.
-
Material Preparation
– The initial step involves selecting high-quality raw materials, usually steel or other alloys, that meet industry specifications. Suppliers often conduct rigorous inspections of these materials to ensure they are free from defects.
– Materials are then cut, shaped, and treated to enhance their properties, such as hardness and durability. Common techniques include heat treatment and surface hardening. -
Forming
– This stage involves shaping the prepared materials into specific components using various methods like casting, forging, and machining. CNC (Computer Numerical Control) machining is particularly prominent, offering high precision and efficiency.
– Advanced techniques such as laser cutting and water jet cutting may also be employed to achieve intricate designs and tight tolerances. -
Assembly
– Once components are formed, they are assembled into the final machine tool. This step requires skilled labor and meticulous attention to detail, as the accuracy of assembly directly affects the tool’s performance.
– Automated assembly lines are increasingly utilized to enhance speed and reduce human error, while manual assembly is reserved for complex components. -
Finishing
– The finishing stage includes processes such as grinding, polishing, and coating to ensure the machine tools meet aesthetic and functional standards. This is crucial for achieving the desired surface finish and protecting against corrosion.
– Quality checks are performed throughout this stage to ensure compliance with specifications.
How Is Quality Assurance Implemented in Machine Tool Manufacturing?
Quality assurance (QA) is a critical component of the manufacturing process for machine tools in China, ensuring that products meet international standards and customer expectations. The following outlines key aspects of QA:
-
International and Industry-Specific Standards
– Manufacturers often adhere to international standards such as ISO 9001, which focuses on quality management systems. Compliance with these standards demonstrates a commitment to quality and continuous improvement.
– Additionally, industry-specific certifications like CE (Conformité Européenne) for European markets and API (American Petroleum Institute) for oil and gas applications may be relevant depending on the machine tool’s intended use. -
Quality Control Checkpoints
– Quality control (QC) is integrated at various stages of production:- Incoming Quality Control (IQC): Raw materials are inspected upon arrival to ensure they meet specifications.
- In-Process Quality Control (IPQC): Ongoing inspections during manufacturing help identify and correct issues in real time.
- Final Quality Control (FQC): Completed products undergo thorough testing to verify functionality, accuracy, and compliance with standards.
-
Common Testing Methods
– Various testing methods are employed to validate the performance and durability of machine tools. These include:- Dimensional Inspection: Ensures parts meet specified dimensions using tools like calipers and coordinate measuring machines (CMM).
- Functional Testing: Assesses the operational performance of the machine tools under simulated conditions.
- Stress Testing: Evaluates the tools’ endurance under extreme conditions to identify potential failure points.
How Can B2B Buyers Verify Supplier Quality Control?
For international B2B buyers, particularly from Africa, South America, the Middle East, and Europe, verifying a supplier’s quality control processes is essential to ensure product reliability. Here are actionable strategies:
-
Conduct Supplier Audits
– Regular audits can help buyers assess a supplier’s quality control systems and manufacturing processes. This may involve visiting the manufacturing facility to review compliance with industry standards and quality practices. -
Request Quality Assurance Documentation
– Buyers should request and review documents such as ISO certification, quality control reports, and test results. These documents provide insight into the supplier’s commitment to quality. -
Engage Third-Party Inspection Services
– Utilizing third-party inspection services can provide an unbiased evaluation of the supplier’s quality control measures. These services can conduct inspections at various stages of production, ensuring adherence to agreed specifications. -
Understand Certification Nuances for Different Markets
– Different regions may have specific requirements for certifications and quality standards. Buyers should familiarize themselves with these nuances to ensure compliance with local regulations and market expectations.
What Are the Challenges and Considerations for International Buyers?
International buyers should be aware of several challenges when sourcing machine tools from China:
-
Cultural and Communication Barriers
– Language differences and cultural misunderstandings can lead to misinterpretations of quality requirements. Establishing clear communication channels and using professional translation services can mitigate these issues. -
Regulatory Compliance
– Different countries have varying regulations regarding machine tool imports. Buyers must ensure that the products comply with local laws to avoid legal complications. -
Supply Chain Reliability
– Global supply chains can be vulnerable to disruptions. Buyers should assess the supplier’s logistics capabilities and consider diversifying their sourcing strategy to minimize risks. -
Market Adaptation
– Understanding local market needs and adapting products accordingly is crucial. Buyers should collaborate with suppliers to ensure that machine tools are tailored to meet specific regional demands.
Conclusion
For international B2B buyers, particularly those from Africa, South America, the Middle East, and Europe, understanding the manufacturing processes and quality assurance mechanisms of machine tools in China is vital. By focusing on the main stages of production, quality control standards, and verification strategies, buyers can make informed decisions that enhance their operational efficiency and product reliability.
Practical Sourcing Guide: A Step-by-Step Checklist for ‘machine tools china’
To successfully procure machine tools from China, international B2B buyers need a structured approach. This checklist will guide you through the essential steps to ensure you choose the right supplier and products for your operational needs.
Step 1: Define Your Technical Specifications
Before you start sourcing, it’s vital to clearly outline your technical requirements. This includes the type of machine tools needed, specifications such as size, capacity, and material compatibility.
– Why It Matters: A precise definition helps you communicate effectively with suppliers and ensures you receive products that meet your operational standards.
– What to Consider: Include details on power requirements, operational speed, and any special features necessary for your production processes.
Step 2: Research Potential Suppliers
Start by compiling a list of potential machine tool manufacturers in China. Utilize platforms like Alibaba, Made-in-China, or industry-specific directories.
– Why It Matters: Thorough research helps you identify credible suppliers and reduces the risk of engaging with unreliable companies.
– What to Look For: Focus on suppliers with a strong track record, positive reviews, and relevant industry experience.
Step 3: Verify Supplier Certifications
It’s crucial to check if the suppliers hold necessary certifications such as ISO 9001 or CE marking. These certifications indicate adherence to international quality standards.
– Why It Matters: Verified certifications ensure that the products you receive meet safety and quality benchmarks, which is particularly important in industrial applications.
– Action Items: Request copies of certifications and verify them with the issuing bodies if possible.
Step 4: Request Samples
Before placing a large order, request samples of the machine tools. This allows you to assess the quality and suitability of the products firsthand.
– Why It Matters: Evaluating samples helps prevent costly mistakes and ensures the products meet your specifications.
– What to Assess: Check for build quality, finish, and functionality of the machine tools during sample evaluation.
Step 5: Negotiate Terms and Pricing
Once you are satisfied with the supplier and samples, engage in negotiations regarding pricing, payment terms, and delivery schedules.
– Why It Matters: Effective negotiation can lead to better pricing and favorable terms that can significantly impact your bottom line.
– Key Considerations: Discuss bulk order discounts, payment methods (e.g., Letter of Credit), and warranty terms.
Step 6: Conduct Factory Visits or Virtual Inspections
If feasible, visit the supplier’s factory or arrange for a virtual inspection to evaluate production capabilities and quality control processes.
– Why It Matters: A factory visit provides insight into the supplier’s operations and quality assurance practices, helping you gauge reliability.
– What to Observe: Look for cleanliness, organization, and adherence to production standards during the inspection.
Step 7: Establish a Clear Contract
Finalize the procurement process with a detailed contract outlining all agreed-upon terms, specifications, delivery timelines, and penalties for non-compliance.
– Why It Matters: A clear contract protects both parties and sets expectations, reducing the risk of misunderstandings.
– What to Include: Include clauses on warranties, post-sale support, and procedures for handling defects or delays.
By following these steps, B2B buyers from Africa, South America, the Middle East, and Europe can effectively navigate the complexities of sourcing machine tools from China, ensuring they make informed decisions that support their operational goals.
Comprehensive Cost and Pricing Analysis for machine tools china Sourcing
When sourcing machine tools from China, understanding the comprehensive cost structure and pricing dynamics is essential for international B2B buyers. This section delves into the critical cost components, price influencers, and actionable buyer tips tailored specifically for stakeholders from Africa, South America, the Middle East, and Europe.
What Are the Key Cost Components in Machine Tools Sourcing from China?
-
Materials: The cost of raw materials is a significant factor in the overall price of machine tools. Prices can fluctuate based on global supply and demand, trade tariffs, and the quality of materials sourced. Buyers should consider sourcing from suppliers that offer transparent pricing on raw materials to better forecast costs.
-
Labor: Labor costs in China can vary widely depending on the region and the complexity of the manufacturing process. While China’s labor costs are generally lower than in Europe and the Americas, the rising wages in recent years can impact pricing. It’s crucial to assess the skill level of the labor force when evaluating suppliers.
-
Manufacturing Overhead: This includes costs associated with factory operations, such as utilities, rent, and administrative expenses. A supplier with efficient operations can offer more competitive pricing. Buyers should inquire about the factory’s operational efficiency and capacity utilization.
-
Tooling: Custom tooling can significantly influence the cost. If a buyer requires specific designs or features, the tooling cost should be factored into the total price. Discussing tooling requirements early in negotiations can help in managing these costs.
-
Quality Control (QC): Implementing effective quality control measures can add to the manufacturing costs but is crucial for ensuring product reliability. Buyers should consider the costs associated with quality certifications and compliance to international standards, which can affect pricing.
-
Logistics: Shipping costs from China can vary based on the chosen Incoterms, shipping methods, and the distance to the destination. Understanding the logistics and potential delays is vital for accurate cost estimation.
-
Margin: Suppliers will add a profit margin to cover their costs and ensure profitability. This margin can vary based on the supplier’s market position and the competitiveness of their pricing.
How Do Price Influencers Affect Machine Tool Costs?
-
Volume and Minimum Order Quantity (MOQ): Larger orders often attract better pricing due to economies of scale. Buyers should negotiate MOQs to achieve more favorable terms, especially if they can commit to future orders.
-
Specifications and Customization: Custom machine tools tailored to specific needs can drive up costs. Clearly defining specifications upfront can help suppliers provide accurate quotes.
-
Material Quality and Certifications: Higher quality materials and certifications (e.g., ISO) can increase costs but may lead to better performance and lower maintenance in the long run. It’s essential to evaluate the trade-off between cost and quality.
-
Supplier Factors: Supplier reputation, experience, and location can influence pricing. Established suppliers may charge more due to their track record of reliability, while newer entrants may offer lower prices to gain market share.
-
Incoterms: The choice of Incoterms can significantly impact total costs. For instance, choosing FOB (Free On Board) might shift more responsibility (and cost) to the buyer, affecting overall pricing calculations.
What Tips Can Help Buyers Navigate Machine Tool Pricing in China?
-
Negotiate Wisely: Build relationships with suppliers and be prepared to negotiate on price, MOQ, and payment terms. A collaborative approach can lead to better pricing and terms.
-
Focus on Total Cost of Ownership (TCO): Instead of just evaluating upfront costs, consider the TCO, which includes maintenance, operation, and potential downtime. This holistic view can guide better purchasing decisions.
-
Understand Pricing Nuances: Stay informed about market trends, currency fluctuations, and trade policies that may affect pricing. For instance, tariffs on imported goods can significantly alter costs for buyers in regions like Europe and the Middle East.
-
Seek Multiple Quotes: Always obtain multiple quotes from different suppliers to ensure competitive pricing and terms. This practice can also provide insights into industry pricing standards.
-
Be Mindful of Currency Risks: International transactions may involve currency conversion, which can impact final costs. Consider locking in exchange rates or using hedging strategies to mitigate risks.
Disclaimer on Indicative Prices
Please note that the prices indicated in this analysis are subject to change based on market conditions, supplier negotiations, and specific buyer requirements. Always consult with suppliers for the most accurate and up-to-date pricing information.
Alternatives Analysis: Comparing machine tools china With Other Solutions
When considering the procurement of machine tools, international B2B buyers often face the challenge of selecting the most suitable solution from a range of options. This section analyzes ‘Machine Tools China’ in comparison to two viable alternatives: European CNC Machines and South American Local Fabrication. By understanding the strengths and weaknesses of each option, buyers can make informed decisions that align with their operational needs and budgetary constraints.
Comparison Aspect | Machine Tools China | European CNC Machines | South American Local Fabrication |
---|---|---|---|
Performance | High precision, varied types | Industry-leading precision | Adequate for basic tasks |
Cost | Generally lower cost | Higher cost, but robust | Moderate cost, variable quality |
Ease of Implementation | Quick setup, user-friendly | May require advanced training | Quick adaptation, local support |
Maintenance | Often requires external support | Comprehensive warranties | Generally lower maintenance needs |
Best Use Case | Mass production, competitive pricing | High-precision, complex machining | Small-scale production, repairs |
What are the Pros and Cons of Machine Tools from China?
Machine tools from China are known for their competitive pricing and broad range of options. They are particularly effective for mass production scenarios where cost efficiency is critical. However, buyers should be aware that these tools may sometimes require additional support for maintenance and might not match the precision levels of more advanced European counterparts. Overall, they are best suited for businesses focusing on bulk production without the highest precision requirements.
How do European CNC Machines Compare?
European CNC machines are renowned for their performance and precision, making them ideal for intricate and high-stakes manufacturing operations. While they typically come with a higher upfront cost, they also offer robust warranties and excellent support networks, which can be invaluable for companies needing consistent reliability. The downside is that they may require specialized training for staff, which could add to the overall implementation time and cost.
What are the Benefits of South American Local Fabrication?
Local fabrication in South America offers a unique advantage in terms of adaptability and maintenance. These tools are often easier to implement due to local support and familiarity with the technology. The costs are moderate, appealing to businesses that need quick turnaround times for repairs or small-scale production. However, the performance may vary significantly, and buyers should carefully assess the quality of local manufacturers to ensure they meet their operational standards.
How Can B2B Buyers Choose the Right Solution?
When selecting the right machine tool solution, B2B buyers should assess their specific operational needs, budget constraints, and the required precision for their manufacturing processes. For mass production with cost efficiency, ‘Machine Tools China’ may be the most viable option. If precision and reliability are paramount, investing in European CNC machines could provide long-term value despite the higher initial costs. Conversely, for businesses looking for flexibility and local support, South American local fabrication may offer the best balance of cost and performance. Ultimately, understanding the trade-offs between these options will empower buyers to make decisions that enhance their operational efficiency and competitiveness.
Essential Technical Properties and Trade Terminology for machine tools china
What Are the Essential Technical Properties of Machine Tools from China?
When considering machine tools from China, international B2B buyers need to understand several critical technical properties that impact performance, longevity, and overall value. Here are some key specifications to keep in mind:
-
Material Grade
– The material used in machine tools significantly affects their durability and performance. Common materials include high-carbon steel, alloy steel, and cast iron. Buyers should assess the material grade to ensure it meets their operational needs, especially for high-stress applications. -
Tolerance
– Tolerance refers to the allowable deviation from a specified dimension. In precision machining, tight tolerances (e.g., ±0.01 mm) are crucial for ensuring that parts fit together correctly. For international buyers, understanding tolerance levels is essential, as it directly influences product quality and compatibility with existing systems. -
Hardness
– Hardness is a measure of a material’s resistance to deformation and wear. It is typically measured on scales like Rockwell or Brinell. Higher hardness levels often correlate with better wear resistance, making tools last longer. Buyers should verify hardness ratings to ensure they can withstand the intended applications. -
Power Consumption
– The efficiency of machine tools can be quantified by their power consumption, measured in kilowatts (kW). Lower power consumption not only reduces operational costs but also aligns with sustainability goals. Buyers should inquire about energy efficiency ratings to optimize total cost of ownership. -
Spindle Speed
– Spindle speed, measured in revolutions per minute (RPM), determines how quickly a machine can operate. High spindle speeds are crucial for processes like drilling and milling. Buyers should consider their specific machining requirements to select tools with appropriate spindle speed capabilities.
What Are Common Trade Terms in the Machine Tool Industry?
Understanding trade terminology is vital for effective communication and negotiation with suppliers. Here are some common terms that international B2B buyers should know:
-
OEM (Original Equipment Manufacturer)
– OEM refers to companies that produce parts or equipment that may be marketed by another manufacturer. Understanding OEM relationships can help buyers identify reliable suppliers who produce high-quality components that meet industry standards. -
MOQ (Minimum Order Quantity)
– MOQ is the smallest number of units a supplier is willing to sell. It is crucial for buyers to understand MOQ requirements, as they affect inventory management and cash flow. Negotiating lower MOQs can be beneficial for startups or small businesses. -
RFQ (Request for Quotation)
– An RFQ is a document issued by a buyer to solicit price quotes from suppliers for specific products or services. This term is essential in procurement processes, as it helps buyers compare prices and terms from different vendors effectively. -
Incoterms (International Commercial Terms)
– Incoterms are a series of pre-defined commercial terms published by the International Chamber of Commerce. They clarify the responsibilities of buyers and sellers in international transactions, such as who is responsible for shipping costs and insurance. Familiarity with Incoterms can prevent misunderstandings in cross-border trade. -
Lead Time
– Lead time refers to the period between placing an order and receiving the goods. For machine tools, lead time can vary significantly based on manufacturing capabilities and logistics. Buyers should factor in lead times when planning production schedules to avoid delays.
By understanding these technical properties and trade terms, international buyers can make informed purchasing decisions when sourcing machine tools from China, ensuring they meet their operational requirements and business goals.
Navigating Market Dynamics and Sourcing Trends in the machine tools china Sector
What Are the Current Market Dynamics and Key Trends in the Machine Tools China Sector?
The machine tools sector in China is experiencing robust growth, driven by several global factors including the rise of automation and Industry 4.0. As international B2B buyers from regions such as Africa, South America, the Middle East, and Europe seek to enhance their manufacturing capabilities, understanding these market dynamics becomes crucial. The increasing demand for precision engineering, coupled with technological advancements, has positioned China as a global leader in machine tool manufacturing.
Emerging trends such as digitalization and the integration of Artificial Intelligence (AI) into machine tools are reshaping sourcing strategies. Buyers are now prioritizing suppliers who can offer smart, connected machines that enhance productivity and reduce downtime. Moreover, the shift towards additive manufacturing (3D printing) is creating new avenues for sourcing innovative machinery that can produce complex parts efficiently. This is particularly relevant for buyers in sectors like aerospace, automotive, and medical devices.
Additionally, geopolitical factors, such as trade agreements and tariffs, significantly influence sourcing decisions. For instance, buyers in Europe and the Middle East need to navigate the complexities of trade regulations that may impact import costs and timelines. Understanding these dynamics will help buyers make informed decisions when selecting machine tool suppliers in China, ensuring they not only meet their operational needs but also align with their strategic business objectives.
How Important Are Sustainability and Ethical Sourcing in the Machine Tools Sector?
Sustainability is becoming a pivotal consideration for B2B buyers in the machine tools sector. The environmental impact of manufacturing processes and the urgency of addressing climate change are leading companies to prioritize ethical sourcing practices. Buyers are increasingly looking for suppliers who demonstrate a commitment to sustainability through eco-friendly production methods and materials.
In the context of machine tools from China, this involves sourcing machinery that adheres to international environmental standards and certifications. Buyers should look for suppliers that offer ‘green’ certifications, such as ISO 14001, which indicates that the manufacturer adheres to environmentally responsible practices. Furthermore, selecting machine tools that utilize recyclable materials or energy-efficient technologies can significantly reduce the environmental footprint of operations.
Ethical supply chains are also crucial, as buyers are becoming more aware of labor practices and the socio-economic implications of their sourcing choices. Engaging with suppliers who uphold fair labor standards and contribute positively to their communities not only enhances brand reputation but also aligns with the values of increasingly conscientious consumers. This shift towards sustainability and ethical sourcing represents both a challenge and an opportunity for international B2B buyers in the machine tools sector.
What Is the Brief Evolution and History of the Machine Tools Sector in China?
The evolution of the machine tools sector in China can be traced back to the early 20th century when the country began developing its industrial capabilities. Initially, machine tools were primarily imported, but as China’s manufacturing sector expanded, local production started to gain momentum. By the late 20th century, China emerged as a major player in machine tool manufacturing, driven by government initiatives aimed at enhancing industrial competitiveness.
In recent decades, the sector has evolved significantly, characterized by rapid technological advancements and increased investment in research and development. The shift towards automation and digital manufacturing has further propelled China’s position as a leader in the global machine tools market. Today, Chinese manufacturers are not only meeting domestic demand but are also exporting advanced machine tools worldwide, making it essential for international B2B buyers to engage with this dynamic sector.
Understanding the historical context of China’s machine tools industry provides valuable insights into its current capabilities and future potential, allowing buyers to make informed decisions that align with their operational and strategic goals.
Frequently Asked Questions (FAQs) for B2B Buyers of machine tools china
-
How do I evaluate the quality of machine tools from China?
To assess the quality of machine tools from China, start by reviewing the supplier’s certifications, such as ISO 9001 or CE marks, which indicate adherence to international quality standards. Request samples or conduct trials of the machinery to verify performance and durability. It is also beneficial to look for customer testimonials and reviews, as well as to visit the manufacturing facility if possible. Engaging third-party inspection services can provide an unbiased evaluation before making large purchases. -
What are the most reliable suppliers of machine tools in China?
Reliable suppliers can be identified through platforms such as Alibaba, Made-in-China, or Global Sources. Look for suppliers with a strong track record, positive customer reviews, and extensive experience in the industry. It’s advisable to verify their business licenses and request references from other international buyers. Attending trade fairs such as the China International Machine Tool Show (CIMT) can also help in meeting reputable suppliers face-to-face. -
What is the typical lead time for machine tools orders from China?
The lead time for machine tool orders can vary based on factors like order size, customization, and supplier workload. Generally, expect a lead time of 30 to 90 days from the order confirmation date. Custom-made machines may require longer lead times. Always confirm the estimated delivery time with the supplier and consider potential delays due to customs or shipping issues. -
How can I negotiate better payment terms with Chinese suppliers?
Negotiating payment terms can be approached by establishing a relationship built on trust and transparency. Start by proposing a flexible payment plan that includes a small deposit (usually 30%) upfront and the remaining balance upon delivery or inspection of the goods. Offering to pay through secure methods, such as letters of credit, can also make suppliers more amenable to favorable terms. Be prepared to compromise and explore options like staggered payments based on production milestones. -
What are the minimum order quantities (MOQs) for machine tools from China?
Minimum order quantities vary widely by supplier and product type. For standard machine tools, MOQs may range from 1 to 10 units, while customized machines often have higher MOQs due to the setup costs involved. Always discuss MOQs upfront to avoid misunderstandings, and inquire if the supplier offers flexible terms for smaller orders, especially for first-time buyers. -
How do I ensure my machine tool meets specific industry standards?
To ensure compliance with industry standards, communicate your requirements clearly to the supplier during the negotiation phase. Request that the machine tools come with appropriate certifications and documentation, such as CE, ISO, or other relevant local standards. Conduct thorough testing upon receipt and consider third-party audits to validate that the machinery adheres to the specified standards before putting it into operation. -
What logistics options are available for shipping machine tools from China?
Shipping options for machine tools from China include air freight, sea freight, and rail transport. Sea freight is often the most economical for large shipments, though it takes longer. Air freight is faster but more expensive, suitable for urgent orders. Work with logistics companies experienced in international shipping to navigate customs regulations and ensure timely delivery. Consider insurance for high-value equipment to mitigate risks during transit. -
How can I manage potential risks when sourcing machine tools from China?
Managing risks involves thorough due diligence on suppliers, including background checks, financial stability assessments, and quality control processes. Establish clear contracts detailing specifications, delivery timelines, and penalties for non-compliance. Use escrow services for payments to protect your investment until goods are received as agreed. Additionally, consider starting with smaller orders to evaluate supplier reliability before committing to larger investments.
Important Disclaimer & Terms of Use
⚠️ Important Disclaimer
The information provided in this guide, including content regarding manufacturers, technical specifications, and market analysis, is for informational and educational purposes only. It does not constitute professional procurement advice, financial advice, or legal advice.
While we have made every effort to ensure the accuracy and timeliness of the information, we are not responsible for any errors, omissions, or outdated information. Market conditions, company details, and technical standards are subject to change.
B2B buyers must conduct their own independent and thorough due diligence before making any purchasing decisions. This includes contacting suppliers directly, verifying certifications, requesting samples, and seeking professional consultation. The risk of relying on any information in this guide is borne solely by the reader.
Strategic Sourcing Conclusion and Outlook for machine tools china
As international B2B buyers navigate the competitive landscape of machine tools from China, strategic sourcing remains a crucial element for success. By leveraging China’s advanced manufacturing capabilities, buyers can access high-quality machine tools that enhance production efficiency and reduce operational costs. Key takeaways include the importance of understanding supplier capabilities, the need for rigorous quality control processes, and the benefits of establishing long-term partnerships with reliable manufacturers.
What should international buyers consider for future sourcing from China? The evolving landscape of machine tool technology, coupled with shifting global trade dynamics, presents both challenges and opportunities. Buyers from Africa, South America, the Middle East, and Europe must stay informed about market trends and technological advancements to make informed purchasing decisions.
To capitalize on these opportunities, it is essential to engage in proactive communication with suppliers and to conduct thorough market research. By doing so, buyers can ensure they are not only meeting their immediate needs but also positioning themselves strategically for future growth. As we look ahead, embracing innovation and fostering collaboration will be key to unlocking the full potential of machine tools sourced from China.