Find the Best Wire Harness Supplier: Your Ultimate Guide (2025)
Introduction: Navigating the Global Market for wire harness supplier
Navigating the complexities of sourcing wire harness suppliers can be a daunting task for international B2B buyers, especially in diverse regions like Africa, South America, the Middle East, and Europe. With an ever-expanding global market, understanding the nuances of different wire harness applications—from automotive to industrial machinery—becomes crucial. This guide serves as a comprehensive resource to help you make informed decisions when selecting wire harness suppliers. We will explore various types of wire harnesses, their specific applications, and the vital factors to consider during the supplier vetting process.
One of the key challenges buyers face is ensuring the reliability and quality of wire harness products while managing costs effectively. This guide addresses these challenges by offering insights into supplier qualifications, certifications, and best practices for negotiating pricing and terms. Additionally, we will delve into payment options that facilitate smoother transactions, particularly for cross-border dealings.
By equipping international buyers with actionable insights and strategies, this guide aims to empower you to navigate the global wire harness market confidently. Whether you are located in bustling urban centers or emerging markets, understanding these dynamics will enhance your procurement strategies and ultimately lead to successful sourcing outcomes.
Understanding wire harness supplier Types and Variations
Type Name | Key Distinguishing Features | Primary B2B Applications | Brief Pros & Cons for Buyers |
---|---|---|---|
Custom Wire Harness Suppliers | Tailored designs, specific requirements, high flexibility | Aerospace, automotive, medical devices | Pros: Precisely meets unique needs; Cons: Higher costs and longer lead times. |
Standard Wire Harness Suppliers | Pre-manufactured designs, lower customization | Consumer electronics, appliances | Pros: Cost-effective, quicker delivery; Cons: Limited adaptability to specific needs. |
Industrial Wire Harness Suppliers | Robust construction, often designed for harsh environments | Machinery, industrial automation | Pros: High durability, suited for heavy-duty applications; Cons: May require specialized knowledge for integration. |
Automotive Wire Harness Suppliers | Specialized for automotive applications, compliance with industry standards | Vehicle manufacturing, aftermarket parts | Pros: Expertise in automotive standards; Cons: Regulatory compliance can increase costs. |
Military Wire Harness Suppliers | Designed to meet stringent military specifications, high reliability | Defense systems, military vehicles | Pros: High reliability and performance; Cons: Often expensive due to compliance and testing. |
What are the Characteristics of Custom Wire Harness Suppliers?
Custom wire harness suppliers focus on creating tailored solutions to meet specific customer requirements. These suppliers work closely with clients to design harnesses that fit unique applications, which is especially vital in sectors like aerospace and medical devices. Buyers should consider the complexity of their requirements and whether the added expense of a custom solution aligns with their budget and timeline.
How Do Standard Wire Harness Suppliers Operate?
Standard wire harness suppliers provide pre-manufactured harnesses that are widely used across various industries. Their offerings are generally more cost-effective and available for quicker delivery compared to custom options. However, these harnesses might not meet specific needs, making it essential for buyers to evaluate whether their applications can conform to existing designs or if customization is necessary.
What Makes Industrial Wire Harness Suppliers Unique?
Industrial wire harness suppliers specialize in creating durable products designed to withstand harsh environmental conditions. These harnesses are typically used in machinery and industrial automation, where reliability is paramount. Buyers should assess their operational environments and consider the longevity and robustness of the harnesses to ensure they meet the demands of their applications.
Why Choose Automotive Wire Harness Suppliers?
Automotive wire harness suppliers are experts in manufacturing harnesses that comply with automotive standards and regulations. They cater to both vehicle manufacturers and aftermarket suppliers, providing solutions that ensure safety and efficiency. Buyers need to consider the regulatory landscape and whether their suppliers can meet the necessary compliance requirements while delivering quality products.
What are the Benefits of Working with Military Wire Harness Suppliers?
Military wire harness suppliers offer products designed to meet rigorous military specifications, emphasizing reliability and performance in critical applications. These suppliers often provide harnesses for defense systems and military vehicles, which require extensive testing and compliance with strict standards. Buyers should weigh the benefits of high reliability against the potential costs, as these harnesses tend to be more expensive due to the stringent requirements involved.
Related Video: Automobile Harness and Wire Repair, How to Solder and protect wires
Key Industrial Applications of wire harness supplier
Industry/Sector | Specific Application of wire harness supplier | Value/Benefit for the Business | Key Sourcing Considerations for this Application |
---|---|---|---|
Automotive | Electrical systems in vehicles | Enhanced safety and reliability of vehicle systems | Compliance with regional safety standards; customization options |
Aerospace | Wiring for avionics and communication systems | Improved performance and reduced weight | Certification requirements; resistance to extreme environmental conditions |
Industrial Automation | Control systems for machinery and robotics | Increased efficiency and productivity | Compatibility with existing systems; scalability for future needs |
Renewable Energy | Connections in solar panels and wind turbines | Enhanced energy efficiency and reliability | Durability in harsh environments; support for international standards |
Consumer Electronics | Internal wiring for devices like appliances and gadgets | Improved functionality and user experience | Quality assurance; adherence to global safety regulations |
How is Wire Harness Used in the Automotive Sector?
In the automotive industry, wire harness suppliers provide critical electrical systems that connect various components such as sensors, lights, and control units. These harnesses enhance the safety and reliability of vehicles by ensuring that all electrical systems operate seamlessly. Buyers in this sector should consider compliance with regional safety standards and the ability to customize harnesses to fit specific vehicle models. Additionally, suppliers should be evaluated based on their capacity to deliver high-quality products that can withstand the rigors of automotive use.
What Role Does Wire Harness Play in Aerospace Applications?
In aerospace, wire harness suppliers are essential for wiring avionics and communication systems within aircraft. These harnesses are designed to be lightweight yet durable, contributing to the overall performance of the aircraft while ensuring safety and reliability during flight. International buyers must focus on certification requirements from aviation authorities and the supplier’s ability to withstand extreme environmental conditions, such as high altitudes and fluctuating temperatures.
How Does Wire Harness Contribute to Industrial Automation?
In the realm of industrial automation, wire harnesses are integral to control systems used in machinery and robotics. They facilitate the efficient transfer of electrical signals, which is crucial for operational productivity. Buyers seeking wire harnesses for industrial applications should prioritize compatibility with existing systems and the scalability of the harnesses to accommodate future technological advancements. The ability to customize harnesses for specific machinery can also provide a competitive edge.
Why is Wire Harness Important in Renewable Energy?
Wire harness suppliers play a vital role in renewable energy sectors, particularly in the wiring of solar panels and wind turbines. These harnesses enhance energy efficiency and reliability, essential for maximizing output in renewable energy systems. Buyers must ensure that the harnesses are durable enough to withstand harsh environmental conditions, such as extreme temperatures and moisture. Additionally, suppliers should demonstrate compliance with international standards to facilitate global operations.
What is the Significance of Wire Harness in Consumer Electronics?
In consumer electronics, wire harnesses are used for internal wiring in devices such as appliances, smartphones, and computers. These harnesses improve the functionality and user experience by ensuring reliable connections between components. Buyers in this sector should focus on quality assurance processes to minimize defects and ensure adherence to global safety regulations. Selecting suppliers with a proven track record in the electronics market can significantly impact product performance and customer satisfaction.
Related Video: Fully automated cable harness production in the automotive industry (EN)
3 Common User Pain Points for ‘wire harness supplier’ & Their Solutions
Scenario 1: Navigating Supply Chain Disruptions in Wire Harness Procurement
The Problem: In the current global market, supply chain disruptions have become a significant challenge for B2B buyers sourcing wire harnesses. Buyers from regions like Africa and South America may face delays due to geopolitical issues, transportation hurdles, or shortages of raw materials. These disruptions can result in production downtime and missed deadlines, severely impacting a company’s operational efficiency and customer satisfaction.
The Solution: To mitigate supply chain risks, it is crucial for buyers to develop relationships with multiple suppliers across different regions. This diversification can provide alternative sourcing options during disruptions. Additionally, implementing just-in-time inventory strategies can reduce the need for large stockpiles, which can be costly and space-consuming. Buyers should also consider leveraging technology, such as supply chain management software, to enhance visibility and real-time tracking of orders. This proactive approach will allow buyers to anticipate potential delays and communicate effectively with stakeholders.
Scenario 2: Ensuring Quality and Compliance with Wire Harness Standards
The Problem: Ensuring that wire harnesses meet specific industry standards and compliance requirements is a critical concern for B2B buyers, particularly in the automotive and aerospace sectors. Non-compliance can lead to costly recalls, reputational damage, and even legal issues. Buyers in Europe may face stringent regulations that require rigorous testing and certification of components.
The Solution: To address quality and compliance issues, buyers should prioritize sourcing from suppliers who provide comprehensive documentation and proof of compliance with relevant standards. This includes certifications such as ISO 9001 or specific automotive standards like IATF 16949. Conducting regular audits and assessments of suppliers can also help ensure adherence to quality standards. Buyers should establish clear specifications and expectations upfront, including detailed requirements for materials, testing, and quality assurance processes. Collaborating closely with suppliers during the design phase can also help ensure that the final product meets all necessary regulations.
Scenario 3: Managing Customization Needs for Diverse Applications
The Problem: B2B buyers often require customized wire harnesses tailored to specific applications, which can pose challenges in terms of design, lead times, and costs. Buyers from various industries, such as renewable energy or medical devices, may struggle to find suppliers that can meet their unique specifications without compromising on quality or increasing costs.
The Solution: To effectively manage customization requirements, buyers should engage in early and open communication with potential suppliers about their specific needs. Providing detailed technical specifications and expected performance criteria can facilitate the design process. Additionally, leveraging prototyping services offered by suppliers can help buyers evaluate designs before full-scale production, reducing the risk of costly modifications later. Buyers should also consider suppliers with flexible manufacturing capabilities that can adapt to changing requirements and volumes. Establishing long-term partnerships with these suppliers can lead to improved collaboration and innovation, ultimately resulting in more effective customized solutions.
Strategic Material Selection Guide for wire harness supplier
When selecting materials for wire harnesses, international B2B buyers must consider various factors that influence performance, durability, and compliance with regional standards. Below, we analyze four common materials used in wire harness manufacturing, focusing on their properties, advantages, disadvantages, and specific considerations for buyers from Africa, South America, the Middle East, and Europe.
What Are the Key Properties of Copper in Wire Harnesses?
Copper is the most widely used material in wire harnesses due to its excellent electrical conductivity. It typically has a temperature rating of up to 200°C and can withstand significant mechanical stress. Copper also exhibits good corrosion resistance, especially when coated with tin or nickel.
Pros and Cons of Copper:
– Pros: High conductivity, excellent thermal properties, and good ductility make copper a preferred choice for high-performance applications.
– Cons: Copper is relatively expensive compared to alternatives like aluminum and can be prone to corrosion in harsh environments without proper coatings.
Impact on Application:
Copper is suitable for applications requiring high current loads, such as automotive and aerospace industries. However, in humid or corrosive environments, additional protective measures are necessary.
Considerations for International Buyers:
Buyers should ensure compliance with international standards such as ASTM B170 for copper wire and consider local regulations regarding material sourcing and environmental impact.
How Does Aluminum Compare as a Material for Wire Harnesses?
Aluminum is often chosen as a lightweight alternative to copper, offering a good balance between conductivity and weight. It has a lower temperature rating than copper, generally around 150°C, and is less resistant to mechanical stress.
Pros and Cons of Aluminum:
– Pros: Lightweight, cost-effective, and resistant to corrosion, making it suitable for various outdoor applications.
– Cons: Lower conductivity than copper, which may require larger wire sizes to achieve the same performance.
Impact on Application:
Aluminum is ideal for applications where weight reduction is critical, such as in automotive and aerospace sectors. However, it may not be suitable for high-current applications without careful design considerations.
Considerations for International Buyers:
Buyers should be aware of standards like ASTM B231 for aluminum conductors and ensure that their suppliers can meet local quality certifications.
What Role Does PVC Play in Wire Harness Manufacturing?
Polyvinyl Chloride (PVC) is a common insulation material used in wire harnesses. It has a temperature rating of about 70°C and is known for its excellent chemical resistance and flexibility.
Pros and Cons of PVC:
– Pros: Cost-effective, easy to process, and provides good insulation properties.
– Cons: Limited temperature tolerance and can emit toxic fumes when burned.
Impact on Application:
PVC is suitable for general-purpose wire harnesses in automotive and consumer electronics. However, in high-temperature environments, alternative materials may be necessary.
Considerations for International Buyers:
Buyers should consider compliance with regulations such as RoHS and REACH, which govern the use of hazardous substances in electrical components.
Why Is Thermoplastic Elastomer (TPE) Gaining Popularity in Wire Harnesses?
Thermoplastic elastomers (TPE) are increasingly used for insulation and jacketing in wire harnesses due to their flexibility and durability. They can withstand temperatures up to 125°C and offer excellent resistance to oils and chemicals.
Pros and Cons of TPE:
– Pros: Excellent flexibility, good mechanical strength, and resistance to environmental stress.
– Cons: Generally more expensive than PVC and may have limited compatibility with certain solvents.
Impact on Application:
TPE is ideal for applications in harsh environments, such as industrial machinery and automotive applications, where flexibility and durability are critical.
Considerations for International Buyers:
Buyers should verify that TPE materials meet relevant standards, such as ISO 9001 for quality management systems, and ensure that suppliers can provide necessary certifications.
Summary Table of Material Selection for Wire Harness Suppliers
Material | Typical Use Case for wire harness supplier | Key Advantage | Key Disadvantage/Limitation | Relative Cost (Low/Med/High) |
---|---|---|---|---|
Copper | High-performance electrical applications | Excellent conductivity | Expensive and prone to corrosion | High |
Aluminum | Lightweight applications in automotive | Cost-effective and lightweight | Lower conductivity | Medium |
PVC | General-purpose wire insulation | Cost-effective and flexible | Limited temperature tolerance | Low |
Thermoplastic Elastomer (TPE) | Harsh environment applications | Excellent flexibility and durability | Higher cost than PVC | Medium |
This strategic material selection guide provides valuable insights for international B2B buyers, helping them make informed decisions based on performance requirements, cost considerations, and compliance with regional standards.
In-depth Look: Manufacturing Processes and Quality Assurance for wire harness supplier
What Are the Key Stages in the Manufacturing Process of Wire Harnesses?
The manufacturing process of wire harnesses involves several critical stages that ensure the final product meets the required specifications and quality standards. These stages typically include:
-
Material Preparation
The first step involves sourcing and preparing the raw materials, which include wires, connectors, terminals, and insulation materials. High-quality materials are essential, as they directly affect the performance and reliability of the wire harness. B2B buyers should inquire about the supplier’s material sourcing practices and certifications to ensure compliance with international standards. -
Forming
In this stage, the wires are cut to specified lengths and stripped of insulation at the ends. Advanced machinery is often used to perform these tasks with precision. The forming process may also include bending and shaping wires to fit into the designated assembly layouts. Buyers should look for suppliers that utilize automated forming processes to minimize human error and enhance consistency. -
Assembly
The assembly stage involves connecting the wires to terminals and connectors according to the design specifications. This can include crimping, soldering, or using heat-shrink tubing to secure connections. Employing skilled technicians and automated systems in this stage can greatly improve the quality and reliability of the wire harness. Buyers should ask potential suppliers about their assembly techniques and whether they use specialized equipment for intricate designs. -
Finishing
The final stage of manufacturing wire harnesses includes testing and packaging. This may involve applying protective coatings, labeling, and organizing harnesses for shipment. Effective finishing processes not only enhance the product’s durability but also ensure that it is ready for immediate use upon delivery. Buyers should ensure that the supplier has robust packaging practices to prevent damage during transportation.
How Is Quality Assurance Implemented in Wire Harness Manufacturing?
Quality assurance (QA) is a critical aspect of wire harness manufacturing, ensuring that products meet both international and industry-specific standards.
-
What Are the Relevant International Quality Standards?
Many wire harness suppliers adhere to international quality standards such as ISO 9001, which outlines requirements for a quality management system (QMS). Compliance with these standards indicates that the supplier has established processes to consistently provide products that meet customer and regulatory requirements. Additionally, industry-specific certifications such as CE for European markets and API for oil and gas applications further validate a supplier’s commitment to quality. -
What Are the Quality Control Checkpoints?
Quality control (QC) processes typically include several checkpoints throughout the manufacturing process:
– Incoming Quality Control (IQC): This involves inspecting raw materials upon arrival to ensure they meet specified standards.
– In-Process Quality Control (IPQC): Continuous monitoring during the manufacturing process helps identify defects early.
– Final Quality Control (FQC): A thorough inspection of the finished product is conducted before shipment, ensuring it meets all specifications. -
What Common Testing Methods Are Used?
Various testing methods are employed to verify the integrity and performance of wire harnesses, including:
– Continuity Testing: Ensures that electrical connections are intact.
– Insulation Resistance Testing: Confirms that insulation materials effectively prevent electrical leakage.
– Environmental Testing: Assesses performance under different conditions, such as temperature and humidity.
How Can B2B Buyers Verify Supplier Quality Control?
For B2B buyers, particularly those from diverse regions such as Africa, South America, the Middle East, and Europe, verifying a supplier’s quality control processes is essential. Here are some effective strategies:
-
Conduct Supplier Audits
Regular audits of potential suppliers can provide insights into their manufacturing processes and quality assurance practices. Buyers should consider onsite visits to assess the facilities, equipment, and workflow. -
Request Quality Assurance Reports
Suppliers should provide detailed QA reports that outline their processes, standards compliance, and testing results. These documents can help buyers evaluate the supplier’s commitment to quality. -
Engage Third-Party Inspection Services
Utilizing third-party inspection services can offer an unbiased assessment of a supplier’s quality control. This is particularly beneficial for international buyers who may face challenges in verifying supplier practices from afar.
What Are the Quality Control Nuances for International B2B Buyers?
Navigating quality control as an international buyer involves understanding specific nuances:
-
Cultural Differences in Quality Standards
Different regions may have varying expectations regarding quality standards. Buyers should familiarize themselves with local regulations and industry standards to ensure compliance. -
Communication Challenges
Language barriers and time zone differences can complicate communication with suppliers. Establishing clear lines of communication and utilizing technology for real-time updates can mitigate these issues. -
Understanding Certification Requirements
Buyers must ensure that the wire harnesses meet the certification requirements of their specific market. This may involve verifying that suppliers have the necessary certifications for their products, which can vary by region.
Conclusion
For international B2B buyers, particularly from Africa, South America, the Middle East, and Europe, understanding the manufacturing processes and quality assurance practices of wire harness suppliers is crucial. By focusing on the key stages of production, relevant quality standards, and effective verification strategies, buyers can make informed decisions that enhance their supply chain reliability and product quality.
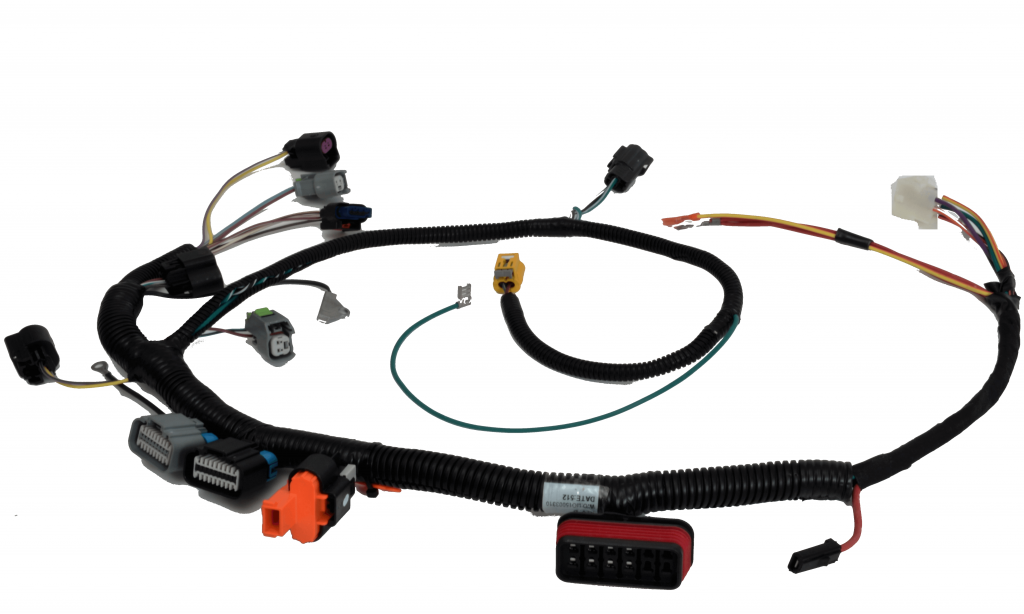
A stock image related to wire harness supplier.
Practical Sourcing Guide: A Step-by-Step Checklist for ‘wire harness supplier’
In the competitive landscape of sourcing wire harness suppliers, particularly for international B2B buyers from regions like Africa, South America, the Middle East, and Europe, having a structured approach is essential. This checklist provides a systematic way to evaluate and select the best suppliers for your needs.
Step 1: Define Your Technical Specifications
Clearly articulate your technical requirements, including the type of wire harness, materials, and compliance standards. This step is crucial as it ensures that potential suppliers can meet your specific needs and avoid costly revisions later. Consider factors such as:
– Voltage and current ratings: Ensure compatibility with your applications.
– Environmental conditions: Specify requirements for temperature, moisture, and chemical exposure.
Step 2: Research and Shortlist Suppliers
Conduct thorough research to identify potential suppliers. Utilize industry directories, trade shows, and online platforms to create a shortlist. This step is essential to widen your options and discover suppliers who specialize in your required products. Pay attention to:
– Supplier experience: Look for companies with a proven track record in manufacturing wire harnesses.
– Industry reputation: Seek reviews and ratings from other B2B buyers.
Step 3: Evaluate Supplier Capabilities
Before committing, it’s crucial to vet suppliers thoroughly. Request company profiles, case studies, and references from buyers in a similar industry or region. Don’t just rely on their website. Focus on:
– Production capacity: Ensure the supplier can meet your order volumes.
– Technological capabilities: Assess their equipment and production techniques to ensure they align with modern standards.
Step 4: Verify Certifications and Compliance
Confirm that the suppliers hold relevant certifications, such as ISO 9001 or UL listings. This step helps mitigate risks associated with quality and safety. Compliance with industry standards is vital to ensure that products meet regulatory requirements. Look for:
– Quality assurance processes: Inquire about their quality control measures and testing procedures.
– Environmental compliance: Ensure adherence to regulations like RoHS or REACH.
Step 5: Request Samples and Prototypes
Before making a large order, request samples or prototypes of the wire harnesses. This step allows you to evaluate the quality of the materials and workmanship firsthand. Pay attention to:
– Fit and functionality: Ensure the sample meets your technical specifications.
– Aesthetic and durability aspects: Assess the overall finish and robustness of the harness.
Step 6: Assess Pricing and Payment Terms
Evaluate the pricing structure and payment terms offered by each supplier. This step is critical to ensure you remain within budget while obtaining the best value. Consider:
– Total cost of ownership: Factor in shipping, tariffs, and potential hidden costs.
– Payment flexibility: Look for favorable terms that can help manage cash flow effectively.
Step 7: Establish Communication and Support Channels
Strong communication is vital for successful supplier relationships. Ensure that the supplier has efficient support systems in place. This step enhances collaboration and problem-solving capabilities. Focus on:
– Responsiveness: Gauge how quickly they respond to inquiries and issues.
– Language and cultural understanding: Consider whether they can effectively communicate with your team.
By following this checklist, B2B buyers can strategically approach the sourcing of wire harness suppliers, ensuring they make informed decisions that align with their operational needs and business goals.
Comprehensive Cost and Pricing Analysis for wire harness supplier Sourcing
What Are the Key Cost Components in Wire Harness Supplier Pricing?
When sourcing wire harnesses, understanding the cost structure is crucial for international B2B buyers. The primary cost components include:
-
Materials: The choice of materials, such as copper, aluminum, or specialized insulation, significantly affects pricing. High-quality materials tend to be more expensive but can enhance the durability and performance of the wire harness.
-
Labor: Labor costs vary depending on the supplier’s location. For instance, suppliers in regions with lower labor costs may offer more competitive pricing. However, it’s essential to consider the skill level and training of the workforce, which can impact the overall quality of the product.
-
Manufacturing Overhead: This includes costs associated with factory operations, such as utilities, rent, and administrative expenses. Suppliers with efficient processes may pass savings on to buyers.
-
Tooling: Custom tooling for specific wire harness designs can add to the initial costs. Buyers should inquire whether tooling costs are amortized over a larger production volume to reduce per-unit pricing.
-
Quality Control (QC): Investing in quality assurance processes can lead to higher upfront costs but may save money in the long run by reducing defects and warranty claims.
-
Logistics: Shipping costs can vary widely based on distance, mode of transport, and Incoterms agreed upon. International buyers should factor in these costs when calculating total expenses.
-
Margin: The supplier’s profit margin can also influence pricing. A transparent discussion about margins can lead to more favorable terms for both parties.
How Do Price Influencers Affect Wire Harness Costs?
Several factors influence the pricing of wire harnesses, including:
-
Volume/MOQ (Minimum Order Quantity): Larger orders often lead to lower unit costs due to economies of scale. Buyers should negotiate MOQs that align with their demand to optimize costs.
-
Specifications and Customization: Custom designs or specific technical specifications can increase costs. It’s vital for buyers to clearly communicate their requirements to avoid unexpected expenses.
-
Materials and Quality Certifications: High-quality materials and certifications (e.g., ISO, UL) can enhance the product’s reliability but also raise prices. Buyers should assess the necessity of such certifications based on their market needs.
-
Supplier Factors: The supplier’s reputation, experience, and location can affect pricing. Established suppliers may charge more due to their reliability and quality history.
-
Incoterms: The agreed terms of delivery can significantly influence final costs. Buyers should be clear about responsibilities for shipping, insurance, and customs duties to avoid hidden costs.
What Tips Can Help Buyers Negotiate Better Prices?
For international B2B buyers, particularly those from Africa, South America, the Middle East, and Europe, the following tips can enhance negotiation outcomes:
-
Understand Total Cost of Ownership (TCO): Beyond the initial purchase price, consider long-term costs such as maintenance, warranty, and potential downtime. A higher upfront cost may be justified by lower TCO.
-
Leverage Relationships: Building strong relationships with suppliers can lead to better pricing and terms. Regular communication can foster trust and open doors for negotiation on future orders.
-
Be Transparent About Needs: Clearly articulating your specifications and expectations can help suppliers provide accurate quotes, reducing the likelihood of unexpected costs down the line.
-
Explore Multiple Suppliers: Engaging with multiple suppliers can provide competitive quotes and leverage for negotiation. It’s essential to evaluate not just prices but also quality and service levels.
-
Consider Payment Terms: Negotiating favorable payment terms can alleviate cash flow pressures. Options such as payment upon delivery or extended payment schedules can be beneficial.
Conclusion
Understanding the cost structure and pricing influencers in wire harness sourcing is essential for international B2B buyers. By being informed and strategic in negotiations, buyers can achieve more favorable pricing, ensuring that their sourcing decisions align with their operational and financial objectives. Always remember that indicative prices can vary based on market conditions and supplier-specific factors.
Alternatives Analysis: Comparing wire harness supplier With Other Solutions
When considering the procurement of a wire harness supplier, international B2B buyers, particularly those from Africa, South America, the Middle East, and Europe, should be aware of viable alternative solutions. This analysis compares wire harness suppliers with two prominent alternatives: custom cable assembly and printed circuit boards (PCBs). Each option presents unique advantages and drawbacks that can influence a buyer’s decision based on their specific operational needs and market conditions.
Comparison Table
Comparison Aspect | Wire Harness Supplier | Custom Cable Assembly | Printed Circuit Boards (PCBs) |
---|---|---|---|
Performance | High reliability; customizable | Good for specific applications; less flexible | High integration of components; compact design |
Cost | Moderate to high; depends on complexity | Generally lower; cost-effective for bulk | High initial setup cost; economical at scale |
Ease of Implementation | Requires technical expertise for design | Easier for specific applications; quick turnaround | Complex design process; longer lead times |
Maintenance | Moderate; subject to wear and tear | Low; easy to replace components | Moderate; requires skilled technicians for repairs |
Best Use Case | Automotive, aerospace, industrial machinery | Electronics, consumer goods | High-tech devices, compact applications |
What Are the Pros and Cons of Custom Cable Assembly?
Custom cable assembly serves as a flexible alternative to wire harness suppliers, particularly advantageous for projects requiring specific lengths, connectors, or shielding. The primary benefit lies in its cost-effectiveness for bulk orders, which can significantly reduce per-unit costs. Additionally, custom assemblies are typically easier to implement, making them suitable for companies with limited technical resources. However, they may not provide the same level of reliability and durability as a wire harness, especially in demanding environments, which can be a critical consideration for industries like automotive or aerospace.
How Do Printed Circuit Boards (PCBs) Compare?
Printed Circuit Boards (PCBs) offer a compact and efficient solution for integrating multiple electronic components into a single unit. This method is ideal for high-tech applications where space is at a premium and performance is paramount. The main advantage of PCBs is their ability to support complex circuitry within a small footprint, making them suitable for sophisticated devices. However, the initial setup costs can be high, and the design process is more complex compared to wire harnesses. Additionally, repair and maintenance require skilled technicians, which can increase operational costs for businesses lacking in-house expertise.
How Can B2B Buyers Choose the Right Solution?
When selecting the right solution for their needs, B2B buyers should evaluate their specific requirements, including performance expectations, budget constraints, and the technical capabilities of their workforce. If reliability and customization are paramount, a wire harness supplier may be the best choice. Conversely, for projects with a focus on cost efficiency and less demanding environments, custom cable assembly might be more suitable. For high-tech applications where space and integration are crucial, PCBs could be the optimal solution. Ultimately, understanding the unique advantages and limitations of each alternative will empower international buyers to make informed purchasing decisions that align with their operational goals.
Essential Technical Properties and Trade Terminology for wire harness supplier
What Are the Essential Technical Properties of Wire Harnesses?
Understanding the technical properties of wire harnesses is crucial for international B2B buyers looking to source reliable and high-quality components. Here are some key specifications to consider:
1. Material Grade: Why Is It Important?
The material used in wire harnesses typically includes copper or aluminum conductors, with insulation made from PVC, XLPE, or other materials. The choice of material affects conductivity, durability, and resistance to environmental factors. High-grade materials ensure better performance and longevity, which is vital for applications in automotive, aerospace, and industrial sectors.
2. Tolerance Levels: How Do They Impact Quality?
Tolerance refers to the acceptable limits of variation in the dimensions of wire harness components. In B2B contexts, precise tolerances are essential to ensure compatibility with other components. For instance, a tolerance of ±0.01 mm in connector dimensions may be critical for ensuring secure connections in high-speed applications, thereby preventing failures and costly downtimes.
3. Temperature Rating: Why Is It a Key Specification?
Wire harnesses must withstand various temperature ranges depending on their application. A temperature rating indicates the maximum and minimum operating temperatures of the harness. For example, automotive wire harnesses may need to function effectively in environments ranging from -40°C to 125°C. Choosing the right temperature rating can prevent insulation breakdown and ensure reliable operation in extreme conditions.
4. Voltage Rating: What Does It Signify?
The voltage rating denotes the maximum voltage the wire harness can handle safely. It is critical for preventing electrical failures and ensuring safety. For example, a wire harness rated for 600V is suitable for many industrial applications, while higher ratings are necessary for specialized equipment. Understanding voltage ratings helps buyers select appropriate products for their specific needs.
5. Shielding and Insulation: How Do They Affect Performance?
Shielding helps protect wire harnesses from electromagnetic interference (EMI), which can disrupt signal integrity. Insulation materials also play a role in preventing short circuits and protecting against environmental hazards. Buyers should consider harnesses with proper shielding and insulation ratings to ensure optimal performance, especially in sensitive electronic applications.
What Are Common Trade Terminology and Jargon Used in Wire Harness Sourcing?
Familiarity with industry-specific terms can streamline the purchasing process for B2B buyers. Here are some essential terms:
1. What Is OEM (Original Equipment Manufacturer)?
An OEM is a company that produces parts or equipment that may be marketed by another manufacturer. In the wire harness industry, purchasing from an OEM ensures that you are getting components that meet specific quality standards and compatibility requirements.
2. What Does MOQ (Minimum Order Quantity) Mean?
MOQ refers to the smallest quantity of a product that a supplier is willing to sell. Understanding MOQ is crucial for budgeting and inventory management. For instance, a wire harness supplier may have an MOQ of 500 units, which can impact your purchasing strategy.
3. What Is RFQ (Request for Quotation)?
An RFQ is a document sent by a buyer to suppliers to request pricing and other details for specific products or services. This process is essential for comparing costs and terms among different suppliers, ensuring that buyers make informed decisions.
4. How Do Incoterms Affect International Shipping?
Incoterms (International Commercial Terms) define the responsibilities of buyers and sellers in international transactions. They clarify who is responsible for shipping, insurance, and tariffs. Understanding these terms can help avoid disputes and ensure smooth logistics. For example, ‘FOB’ (Free On Board) indicates that the seller covers costs until the goods are loaded onto a shipping vessel.
5. What Is Lead Time and Why Is It Important?
Lead time refers to the time taken from placing an order to its delivery. It is a critical factor for B2B buyers, particularly in industries with tight schedules. Knowing the lead time helps in planning inventory and production schedules effectively.
By grasping these technical properties and trade terms, international B2B buyers can make more informed decisions when sourcing wire harnesses, ensuring that they select the right products for their applications.
Navigating Market Dynamics and Sourcing Trends in the wire harness supplier Sector
What Are the Current Trends and Dynamics in the Wire Harness Supplier Market?
The wire harness supplier market is experiencing significant transformation driven by various global factors. Rapid technological advancements, particularly in the automotive and electronics sectors, are pushing demand for high-quality, reliable wire harnesses. International B2B buyers, especially those from Africa, South America, the Middle East, and Europe, should focus on several emerging trends:
-
Increased Automation: Automation in manufacturing processes enhances efficiency and reduces production costs. Suppliers leveraging robotics and AI-driven technologies can provide faster turnaround times and improved product quality, which is critical for international buyers looking for competitive pricing and reliability.
-
Customization and Flexibility: As industries move towards more specialized applications, customization becomes essential. Suppliers are increasingly offering tailored solutions that meet specific client needs, enabling businesses to integrate wire harnesses seamlessly into their systems.
-
Digital Transformation: The rise of digital platforms for sourcing and procurement is reshaping the buying experience. B2B buyers can benefit from online marketplaces and digital catalogs that provide comprehensive product specifications, pricing, and supplier ratings, making it easier to compare options and make informed decisions.
-
Emerging Markets: Regions such as Africa and South America are becoming focal points for investment in manufacturing and technology. As these markets grow, they present new opportunities for wire harness suppliers to establish partnerships and expand their reach.
-
Regulatory Compliance: Understanding and adhering to local and international regulations regarding product standards and safety is crucial. Buyers must ensure that their suppliers are compliant with relevant certifications to avoid legal complications and enhance product credibility.
How Important Is Sustainability and Ethical Sourcing in the Wire Harness Sector?
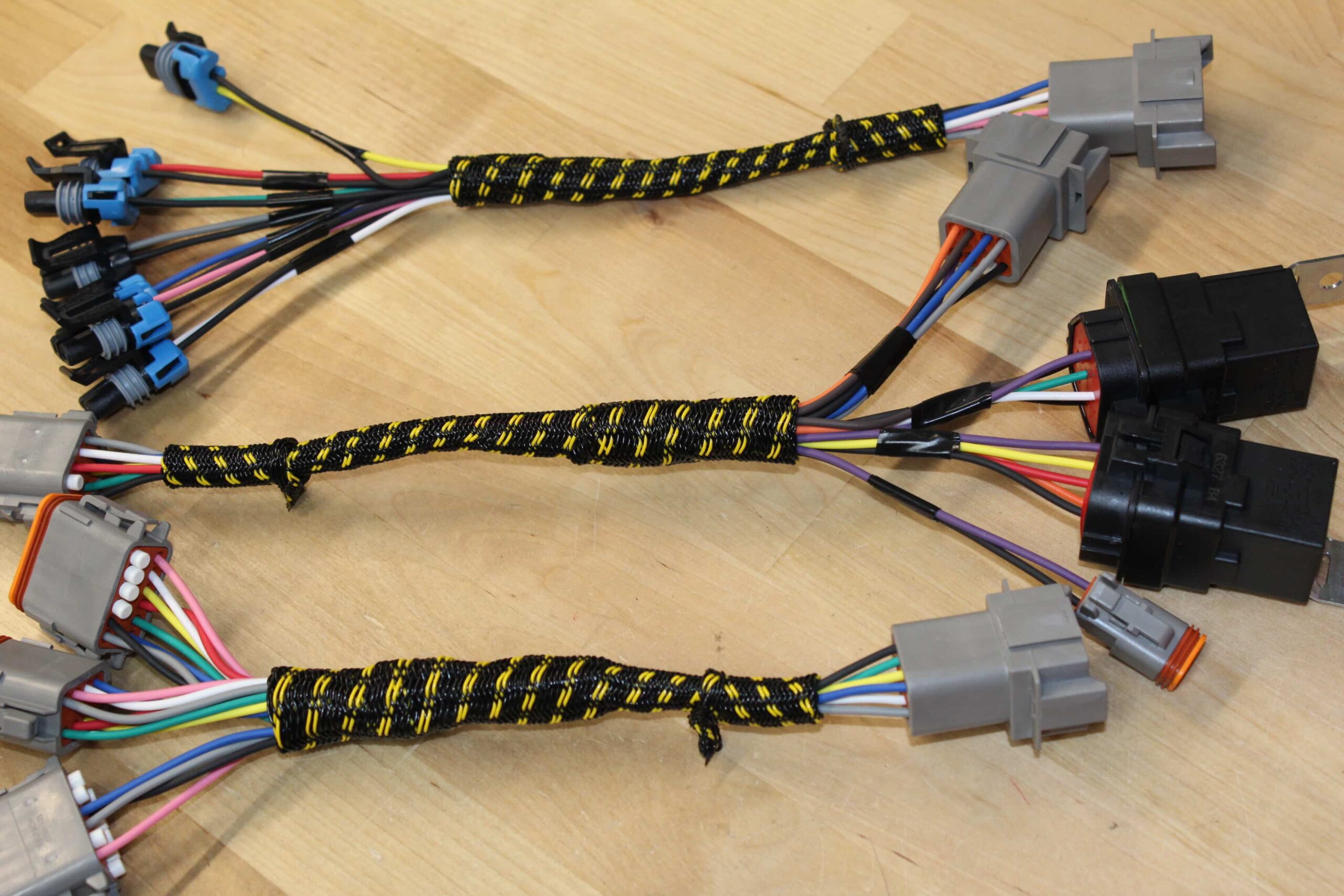
A stock image related to wire harness supplier.
Sustainability and ethical sourcing are becoming non-negotiable factors for international B2B buyers in the wire harness sector. The environmental impact of manufacturing processes, especially concerning waste and resource consumption, is under scrutiny. Buyers should consider the following aspects:
-
Environmental Responsibility: Suppliers that prioritize eco-friendly practices, such as using recyclable materials and reducing energy consumption, can help buyers meet their sustainability goals. This is particularly important as consumers increasingly demand greener products.
-
Ethical Supply Chains: Transparency in the supply chain is critical. Buyers should partner with suppliers who can demonstrate responsible sourcing of materials, fair labor practices, and adherence to human rights standards. This not only mitigates risks but also enhances brand reputation.
-
Green Certifications: Many suppliers are obtaining certifications that demonstrate their commitment to sustainability, such as ISO 14001 for environmental management. Buyers should look for these certifications as indicators of a supplier’s dedication to sustainable practices.
-
Life Cycle Assessments: Conducting life cycle assessments (LCAs) allows businesses to evaluate the environmental impact of their products from production to disposal. By choosing suppliers that provide LCAs, buyers can make informed decisions that align with their sustainability objectives.
What Is the Brief Evolution of the Wire Harness Supplier Market?
The wire harness supplier market has evolved significantly over the decades, adapting to technological advancements and changing consumer demands. Initially dominated by simple electrical connections, the industry has transitioned towards sophisticated, multi-functional wire harnesses that cater to the complexities of modern electronic systems. The automotive sector has been a primary driver of this evolution, pushing for innovations such as lightweight materials and integrated systems to enhance vehicle performance and safety.
In recent years, the advent of electric vehicles (EVs) has further transformed the market, as manufacturers seek wire harness solutions that support advanced connectivity and energy efficiency. This ongoing evolution underscores the importance for B2B buyers to stay informed about the latest technological developments and sourcing trends to maintain a competitive edge in their respective industries.
Frequently Asked Questions (FAQs) for B2B Buyers of wire harness supplier
-
How do I choose the right wire harness supplier for my business needs?
Selecting the right wire harness supplier involves several key considerations. First, assess their industry experience and expertise, particularly in your specific sector (automotive, aerospace, etc.). Evaluate their production capabilities, including technology and equipment used. Request samples to check quality and compliance with industry standards. Additionally, review customer testimonials and their responsiveness to inquiries. Finally, consider their geographical location and logistics capabilities to ensure timely delivery and communication. -
What are the common customization options available for wire harnesses?
Most wire harness suppliers offer a range of customization options to meet specific requirements. This can include variations in wire gauge, insulation type, and connector styles. Suppliers may also provide options for different lengths and configurations to fit unique applications. Discussing your project specifications upfront is crucial to ensure that the supplier can meet your needs effectively. Furthermore, inquire about their design capabilities, as some suppliers can assist with engineering and prototyping. -
What is the minimum order quantity (MOQ) for wire harnesses?
The MOQ for wire harnesses can vary significantly among suppliers, often ranging from a few hundred to several thousand units. This depends on factors such as the complexity of the harness, manufacturing processes, and material costs. When sourcing suppliers, it’s essential to confirm their MOQ policies, as lower MOQs may be available for custom orders or prototyping runs. Understanding these requirements can help you plan your inventory and budgeting accordingly. -
What payment terms should I expect when sourcing from international wire harness suppliers?
Payment terms can vary widely depending on the supplier and the nature of the transaction. Common options include advance payment, partial upfront payment with the balance upon delivery, or payment through letters of credit. It’s crucial to negotiate terms that are mutually beneficial and to ensure they align with your cash flow needs. Additionally, consider payment methods that offer protection, such as PayPal or escrow services, especially for larger transactions. -
How can I ensure quality assurance for my wire harness orders?
Quality assurance (QA) is critical in wire harness manufacturing. Start by requesting documentation of the supplier’s QA processes, including certifications like ISO 9001. Ask about their testing protocols, which should cover electrical testing, insulation resistance, and mechanical strain. Arrange for third-party inspections if necessary, especially for large orders. Establish clear communication regarding quality expectations and standards before production begins to minimize issues later. -
What logistics considerations should I keep in mind when sourcing wire harnesses internationally?
When sourcing wire harnesses from international suppliers, logistics plays a crucial role. Assess shipping options based on cost, speed, and reliability. Familiarize yourself with customs regulations in both the supplier’s and your own country to avoid delays. Consider the implications of tariffs and duties on your total cost. Finally, establish clear timelines with the supplier for production and shipping to ensure that your supply chain remains uninterrupted. -
How do I handle potential language and cultural barriers when sourcing wire harnesses?
Language and cultural barriers can pose challenges in international sourcing. To mitigate these issues, consider working with suppliers who have experience dealing with international clients and offer bilingual support. Utilize clear, concise communication and confirm understanding by summarizing key points in writing. Establishing a good relationship with the supplier can also facilitate smoother interactions, so take the time to understand their cultural practices and business etiquette. -
What are the key certifications to look for in a wire harness supplier?
When evaluating wire harness suppliers, certain certifications can indicate their commitment to quality and compliance. Look for ISO 9001 certification, which demonstrates adherence to quality management systems. For automotive applications, IATF 16949 certification is crucial. Additionally, UL certification can indicate compliance with safety standards. Ensure that the supplier can provide documentation for these certifications to verify their credibility and commitment to quality manufacturing practices.
Important Disclaimer & Terms of Use
⚠️ Important Disclaimer
The information provided in this guide, including content regarding manufacturers, technical specifications, and market analysis, is for informational and educational purposes only. It does not constitute professional procurement advice, financial advice, or legal advice.
While we have made every effort to ensure the accuracy and timeliness of the information, we are not responsible for any errors, omissions, or outdated information. Market conditions, company details, and technical standards are subject to change.
B2B buyers must conduct their own independent and thorough due diligence before making any purchasing decisions. This includes contacting suppliers directly, verifying certifications, requesting samples, and seeking professional consultation. The risk of relying on any information in this guide is borne solely by the reader.
Strategic Sourcing Conclusion and Outlook for wire harness supplier
In the dynamic landscape of global supply chains, strategic sourcing for wire harness suppliers has emerged as a critical component for businesses aiming to enhance operational efficiency and reduce costs. By focusing on reliable supplier partnerships, companies can ensure the consistent quality and timely delivery of wire harnesses, which are essential for various applications across industries, from automotive to electronics.
How Can International Buyers Leverage Strategic Sourcing?
For international B2B buyers, particularly in regions such as Africa, South America, the Middle East, and Europe, it is vital to evaluate suppliers based on their manufacturing capabilities, compliance with international standards, and responsiveness to market needs. Establishing long-term relationships with suppliers not only fosters innovation but also mitigates risks associated with supply chain disruptions.
What is the Future Outlook for Wire Harness Suppliers?
As the demand for advanced wire harness solutions grows, particularly in sectors like electric vehicles and renewable energy, the outlook remains positive. Buyers should remain proactive in their sourcing strategies, leveraging technology and data analytics to make informed decisions. Engaging with suppliers who prioritize sustainability and technological advancements will be crucial for maintaining competitive advantage.
In conclusion, strategic sourcing is not just a procurement function; it is a pathway to building resilient supply chains. International B2B buyers are encouraged to take decisive actions today by reassessing their sourcing strategies to align with future market trends and demands. The time to invest in strong supplier relationships is now, ensuring a sustainable and innovative business landscape for the years to come.