The Ultimate Guide to Medicine Cabinet Manufacturer (2025)
Introduction: Navigating the Global Market for medicine cabinet manufacturer
Navigating the global market for a medicine cabinet manufacturer presents a unique challenge for international B2B buyers, particularly when sourcing high-quality products that meet diverse regional standards and regulations. As the demand for innovative storage solutions in healthcare and residential settings rises, understanding the various types of medicine cabinets, their applications, and the nuances of supplier vetting becomes imperative. This comprehensive guide will delve into the essential factors that influence purchasing decisions, including material quality, design specifications, compliance with international safety standards, and cost considerations.
This resource is designed to empower B2B buyers from Africa, South America, the Middle East, and Europe—including countries like the UK and Poland—by providing actionable insights and practical strategies for informed procurement. From evaluating supplier reliability to understanding the logistics of international shipping, this guide aims to simplify the complexities of sourcing. By the end of this guide, readers will be equipped with the knowledge needed to make strategic purchasing decisions that not only enhance their product offerings but also meet the specific needs of their markets. With the right information at hand, navigating the global landscape of medicine cabinet manufacturing can transform from a daunting task into an opportunity for growth and innovation.
Understanding medicine cabinet manufacturer Types and Variations
Type Name | Key Distinguishing Features | Primary B2B Applications | Brief Pros & Cons for Buyers |
---|---|---|---|
Wall-Mounted Cabinets | Space-saving, installed directly on walls, often with mirrors | Hospitals, clinics, pharmacies | Pros: Space-efficient, customizable; Cons: Limited storage for larger items. |
Freestanding Cabinets | Stand-alone units, often larger, with multiple compartments | Medical offices, outpatient facilities | Pros: Ample storage, easy access; Cons: Requires more floor space, less flexible. |
Mobile Cabinets | On wheels for easy transport, designed for mobility | Emergency rooms, home healthcare, mobile clinics | Pros: Highly versatile, easy to relocate; Cons: Stability can be an issue on uneven surfaces. |
Specialty Cabinets | Designed for specific uses (e.g., narcotics, surgical tools) | Specialty clinics, surgical centers | Pros: Enhanced security and organization; Cons: Higher cost, may not be suitable for general use. |
Custom Cabinets | Tailored to specific needs and specifications | Large healthcare systems, private practices | Pros: Perfect fit for unique spaces; Cons: Longer lead times, potentially higher costs. |
What are the Characteristics of Wall-Mounted Cabinets?
Wall-mounted medicine cabinets are designed to maximize space efficiency, making them ideal for smaller facilities or rooms. They often feature mirrors and can be customized with various finishes to match the décor. B2B buyers should consider the weight capacity and installation requirements, as these cabinets must be securely mounted to support the items stored within.
How do Freestanding Cabinets Serve Medical Facilities?
Freestanding cabinets are larger units that provide extensive storage options, often featuring multiple drawers and shelves. They are suitable for medical offices and outpatient facilities where ample storage is necessary. Buyers should evaluate the cabinet’s material durability and ease of cleaning, as these factors impact long-term usability in clinical environments.
What are the Advantages of Mobile Cabinets?
Mobile medicine cabinets are designed for mobility, equipped with wheels for easy transport. They are particularly useful in settings like emergency rooms or home healthcare services where quick access to supplies is critical. Buyers should assess the stability of these cabinets, especially on uneven surfaces, to ensure safety during use.
Why Choose Specialty Cabinets for Specific Needs?
Specialty cabinets cater to specific storage requirements, such as narcotics or surgical instruments, and are often equipped with enhanced security features. These cabinets are essential for specialty clinics and surgical centers that need to comply with strict regulations. B2B buyers must consider compliance with local regulations and the cabinet’s locking mechanisms to ensure safety and security.
What are the Benefits of Custom Cabinets for Healthcare Providers?
Custom medicine cabinets are tailored to meet the unique needs of healthcare providers, allowing for an exact fit in designated spaces. These cabinets can be designed with specific features to enhance functionality. Buyers should be prepared for longer lead times and higher costs, but the investment often results in improved efficiency and organization in the healthcare setting.
Related Video: 5 AWESOME MEDICINE MAKING MACHINERY IN PHARMACEUTICAL INDUSTRY
Key Industrial Applications of medicine cabinet manufacturer
Industry/Sector | Specific Application of Medicine Cabinet Manufacturer | Value/Benefit for the Business | Key Sourcing Considerations for this Application |
---|---|---|---|
Healthcare Facilities | Storage for Medical Supplies and Medications | Ensures organized storage and quick access to essential items, enhancing workflow efficiency. | Compliance with health regulations, durability, and ease of cleaning. |
Pharmaceuticals | Secure Storage for Controlled Substances | Prevents unauthorized access and ensures compliance with legal requirements. | Security features, fire resistance, and lock mechanisms. |
Home Healthcare | Personal Medication Management Systems | Supports patient adherence to medication schedules, improving health outcomes. | Customization options and portability for home use. |
Hospitality | Guestroom Medicine Cabinets | Provides convenience for guests, enhancing their experience and satisfaction. | Aesthetic design, durability, and integration with room décor. |
Educational Institutions | First Aid and Health Supplies Storage | Facilitates quick access to first aid materials, promoting safety and preparedness. | Compliance with safety regulations and capacity for diverse supplies. |
How Are Medicine Cabinets Utilized in Healthcare Facilities?
In healthcare facilities, medicine cabinets serve a critical role in the organized storage of medical supplies and medications. They ensure that essential items are readily accessible, which significantly enhances workflow efficiency and reduces the likelihood of errors during medication administration. For international B2B buyers in regions such as Africa and Europe, it is essential to source cabinets that comply with local health regulations, are durable, and easy to clean, as these features directly impact operational efficiency and patient safety.
What Is the Role of Medicine Cabinets in Pharmaceuticals?
In the pharmaceutical sector, secure storage for controlled substances is paramount. Medicine cabinets designed for this purpose prevent unauthorized access and help maintain compliance with stringent legal requirements. Buyers from South America and the Middle East should prioritize cabinets that feature robust security systems, such as advanced locking mechanisms and fire resistance, to protect valuable inventory while adhering to local regulations regarding the storage of sensitive materials.
How Do Home Healthcare Solutions Benefit from Medicine Cabinets?
For home healthcare providers, personal medication management systems are increasingly important. Medicine cabinets tailored for this application support patient adherence to medication schedules, which can lead to improved health outcomes. B2B buyers, particularly in Europe, should look for customizable solutions that are portable and user-friendly, as these features can significantly enhance the patient experience and facilitate better health management in home settings.
What Advantages Do Hospitality Medicine Cabinets Offer?
In the hospitality industry, guestroom medicine cabinets not only provide convenience for guests but also enhance their overall experience. A well-designed cabinet can leave a positive impression and contribute to customer satisfaction. Buyers from Africa and South America should consider sourcing cabinets that are aesthetically pleasing, durable, and capable of integrating seamlessly with room décor, as these factors can influence guest perceptions and retention.
Why Are Medicine Cabinets Important in Educational Institutions?
Educational institutions benefit from medicine cabinets that facilitate the storage of first aid and health supplies. Quick access to these materials promotes safety and preparedness among students and staff alike. For international buyers, particularly in Europe, it is crucial to ensure that the cabinets comply with safety regulations and are capable of accommodating a diverse range of supplies, thereby enhancing the institution’s readiness for emergencies.
Related Video: LABORATORY APPARATUS AND THEIR USES
3 Common User Pain Points for ‘medicine cabinet manufacturer’ & Their Solutions
Scenario 1: Overcoming Supply Chain Disruptions in Medicine Cabinet Manufacturing
The Problem: In today’s global market, B2B buyers often face significant challenges due to supply chain disruptions. For instance, a healthcare facility in South Africa may struggle to procure high-quality medicine cabinets from manufacturers in Europe due to delays caused by shipping issues, customs regulations, or material shortages. These interruptions not only affect timelines but can also lead to increased costs and compromised patient safety if critical supplies are unavailable. Buyers often feel the pressure to find alternative solutions quickly to avoid operational downtime.
The Solution: To mitigate supply chain disruptions, B2B buyers should consider establishing relationships with multiple suppliers across different regions. Diversifying the supplier base allows for flexibility and reduces dependency on a single source. Additionally, buyers should invest in robust logistics planning and inventory management systems that can forecast demand and adjust orders accordingly. Utilizing technologies such as blockchain can enhance transparency and traceability in the supply chain, ensuring timely deliveries and quality assurance. Engaging with local manufacturers can also be a viable strategy, as they may offer shorter lead times and easier communication.
Scenario 2: Ensuring Compliance with Regional Regulations for Medicine Cabinets
The Problem: Compliance with local health and safety regulations can be a daunting task for B2B buyers, especially in diverse regions like Europe and the Middle East. For example, a hospital in Poland might need to ensure that the medicine cabinets meet stringent European Union standards for materials used, fire safety, and accessibility. Failure to comply can result in hefty fines, legal issues, and the potential for product recalls, which can disrupt services and harm the institution’s reputation.
The Solution: To navigate regulatory compliance effectively, B2B buyers should engage with manufacturers who possess a thorough understanding of local laws and standards. Before making a purchase, buyers should request documentation that verifies compliance, such as certifications and test reports. Establishing a partnership with a manufacturer that has a proven track record of adhering to regulatory requirements can provide peace of mind. Additionally, buyers should stay updated on changes in regulations by participating in industry associations and forums, which can offer insights into upcoming compliance challenges and best practices.
Scenario 3: Customization Challenges in Medicine Cabinet Design and Functionality
The Problem: Many healthcare facilities have unique requirements for their medicine cabinets, whether due to space constraints, specific storage needs, or aesthetic preferences. A buyer from a clinic in the Middle East may find that standard designs do not meet their operational needs, leading to frustration and wasted resources. The inability to customize products can result in inefficient storage solutions and inadequate patient care.
The Solution: B2B buyers should prioritize manufacturers that offer customizable medicine cabinet solutions. Before engaging with a supplier, it’s crucial to clearly outline the specific requirements, such as dimensions, materials, and additional features like locking mechanisms or ventilation systems. Buyers should also inquire about the manufacturer’s design capabilities and whether they can provide prototypes or mock-ups for approval. Collaborating closely with manufacturers during the design phase can lead to innovative solutions that meet unique needs while maintaining functionality and compliance. Furthermore, consider leveraging 3D modeling technologies that allow buyers to visualize the product before production, ensuring that the final design meets all operational expectations.
Strategic Material Selection Guide for medicine cabinet manufacturer
When selecting materials for medicine cabinets, manufacturers must consider various factors that affect product performance, durability, and compliance with international standards. Below, we analyze four common materials used in medicine cabinet manufacturing, focusing on their key properties, advantages, disadvantages, and considerations for international B2B buyers, particularly from Africa, South America, the Middle East, and Europe.
What Are the Key Properties of Steel for Medicine Cabinets?
Steel is a popular choice for medicine cabinets due to its strength and durability. It typically offers excellent corrosion resistance, especially when treated with coatings like galvanization or powder coating. Steel can withstand high temperatures and pressures, making it suitable for various environments.
Pros & Cons:
The primary advantage of steel is its strength, which ensures longevity and resistance to impact. However, it can be heavier than other materials, potentially complicating installation and transportation. Additionally, while steel is cost-effective, high-quality stainless steel can be more expensive.
Impact on Application:
Steel cabinets are ideal for environments that require robust storage solutions, such as hospitals and clinics. Their corrosion resistance makes them suitable for storing medical supplies that may be sensitive to moisture.
Considerations for International Buyers:
Buyers should ensure compliance with international standards such as ASTM and DIN. In regions like Europe, buyers may prefer stainless steel for its aesthetic appeal and hygiene properties, while in Africa and South America, cost-effectiveness may be more critical.
How Does Plastic Compare as a Material for Medicine Cabinets?
Plastic, particularly high-density polyethylene (HDPE) and polyvinyl chloride (PVC), is increasingly used in medicine cabinets due to its lightweight nature and resistance to moisture and chemicals.
Pros & Cons:
The key advantage of plastic is its lightweight and easy-to-manufacture properties, which can reduce shipping costs. However, plastic may not offer the same level of durability as metal options and can be prone to scratching and UV degradation over time.
Impact on Application:
Plastic cabinets are suitable for environments where moisture resistance is crucial, such as in coastal regions or humid climates. They are often used in home settings or smaller clinics where the risk of heavy use is lower.
Considerations for International Buyers:
Buyers should consider the specific regulations regarding plastic materials in their regions. For instance, compliance with environmental regulations is more stringent in Europe, where recyclability and sustainability are increasingly prioritized.
What Are the Advantages of Glass in Medicine Cabinet Manufacturing?
Glass is often utilized in medicine cabinets for its aesthetic appeal and ease of cleaning. Tempered glass is commonly used for safety, providing a robust option that can withstand impacts.
Pros & Cons:
The primary advantage of glass is its visual appeal, allowing for a modern and clean look. However, it is more fragile than other materials and can pose safety risks if not properly handled. The cost of glass cabinets can also be higher due to the manufacturing process.
Impact on Application:
Glass cabinets are often found in settings where aesthetics are important, such as upscale clinics or private practices. They are ideal for displaying medications or medical supplies while maintaining a clean appearance.
Considerations for International Buyers:
International buyers should be aware of safety standards related to glass use in medical environments. Compliance with standards such as JIS in Japan or EN in Europe can affect product design and marketability.
Why is Wood Still a Viable Option for Medicine Cabinets?
Wood, particularly hardwoods like oak or maple, is still a viable option for medicine cabinets, especially in home settings. It provides a warm aesthetic and can be treated for moisture resistance.
Pros & Cons:
Wood’s primary advantage is its aesthetic appeal and versatility in design. However, it can be susceptible to warping and damage from moisture, making it less suitable for high-humidity environments. Additionally, wood cabinets can be more expensive due to the cost of raw materials and craftsmanship.
Impact on Application:
Wood cabinets are often used in residential settings or in environments where aesthetics are prioritized over durability. They can be customized to fit various design themes.
Considerations for International Buyers:
Buyers should consider the availability of sustainable wood sources and compliance with international regulations regarding wood treatment and pest control, especially in regions like Africa and South America.
Summary Table of Material Selection for Medicine Cabinets
Material | Typical Use Case for medicine cabinet manufacturer | Key Advantage | Key Disadvantage/Limitation | Relative Cost (Low/Med/High) |
---|---|---|---|---|
Steel | Hospitals, clinics | High durability | Heavier, potential rust | Medium |
Plastic | Home settings, small clinics | Lightweight, moisture-resistant | Less durable, UV degradation | Low |
Glass | Upscale clinics, private practices | Aesthetic appeal | Fragile, higher cost | High |
Wood | Residential settings | Warm aesthetic, customizable | Susceptible to moisture damage | Medium |
In conclusion, selecting the right material for medicine cabinets involves balancing durability, aesthetics, cost, and compliance with international standards. By understanding the properties and implications of each material, international B2B buyers can make informed decisions that align with their specific market needs.
In-depth Look: Manufacturing Processes and Quality Assurance for medicine cabinet manufacturer
What Are the Main Stages in the Manufacturing Process of Medicine Cabinets?
The manufacturing of medicine cabinets involves several critical stages that ensure both functionality and quality. The primary stages include material preparation, forming, assembly, and finishing. Understanding these stages helps B2B buyers evaluate suppliers effectively.
-
Material Preparation
The first stage involves sourcing and preparing raw materials, which typically include metals, glass, and various types of plastics. Materials are assessed for quality to ensure they meet the necessary standards. For instance, stainless steel is often preferred for its durability and resistance to corrosion. Buyers should inquire about the sourcing practices of suppliers to ensure materials are ethically sourced and comply with international standards. -
Forming
During the forming stage, raw materials are shaped into components of the medicine cabinet. This can involve processes like stamping, bending, and cutting for metal parts, or molding for plastic components. Advanced techniques, such as laser cutting or CNC machining, are often employed to enhance precision. B2B buyers should look for suppliers who utilize state-of-the-art machinery to ensure consistency and accuracy in the components produced. -
Assembly
In the assembly phase, individual components are brought together to form the final product. This may include fitting shelves, attaching doors, and integrating any electronic features, such as lighting or smart technology. Quality control during assembly is vital; thus, suppliers should have well-defined assembly procedures that minimize errors. Buyers can request detailed assembly process documentation to understand how quality is maintained. -
Finishing
The finishing stage involves applying coatings, such as paint or powder coating, to enhance aesthetics and protect against wear and tear. Techniques like electroplating may also be used for metal components to provide an additional layer of protection. Buyers should consider the environmental impact of finishing processes and ask suppliers about their sustainability practices.
How Is Quality Assurance Implemented in Medicine Cabinet Manufacturing?
Quality assurance (QA) is a crucial aspect of the manufacturing process, particularly in industries that require high standards, such as healthcare. For medicine cabinet manufacturers, implementing robust QA practices can ensure product reliability and safety.
-
What Are the Relevant International Standards?
International standards, such as ISO 9001, provide a framework for quality management systems. Compliance with ISO 9001 ensures that a manufacturer has consistent processes in place to enhance customer satisfaction. Additionally, industry-specific standards like CE marking (required in Europe) or API standards (for products that may involve pharmaceuticals) must be adhered to. B2B buyers should verify that suppliers have the necessary certifications and are compliant with local regulations. -
What Are the Key Quality Control Checkpoints?
Quality control involves several checkpoints throughout the manufacturing process:
– Incoming Quality Control (IQC): This step involves inspecting raw materials upon receipt to ensure they meet specified requirements.
– In-Process Quality Control (IPQC): During manufacturing, random samples are taken to assess the quality of components as they are being produced.
– Final Quality Control (FQC): After assembly, the finished product undergoes thorough testing to confirm it meets all design specifications and safety standards. -
What Common Testing Methods Are Used?
Testing methods can vary but typically include visual inspections, functional testing, and stress testing. For instance, cabinets may be subjected to weight tests to ensure they can support the intended load without failure. B2B buyers should inquire about the specific testing protocols employed by suppliers to gauge product reliability.
How Can B2B Buyers Verify Supplier Quality Control?
For international B2B buyers, particularly those from Africa, South America, the Middle East, and Europe, verifying supplier quality control is essential for ensuring product integrity.
-
What Role Do Audits Play in Supplier Verification?
Conducting regular audits of suppliers can provide insights into their manufacturing processes and quality control systems. Buyers should consider scheduling on-site audits or requesting third-party audit reports to evaluate compliance with international standards and the effectiveness of quality assurance practices. -
How Can Buyers Utilize Quality Reports?
Suppliers should provide comprehensive quality reports that outline testing results, compliance with standards, and any corrective actions taken for non-conformance. Buyers should review these reports to assess the supplier’s commitment to quality. Clear documentation is essential for transparency and accountability. -
What Are the Benefits of Third-Party Inspections?
Engaging third-party inspection agencies can further validate the quality of products before they are shipped. These inspections can be particularly beneficial for international transactions where buyers may have limited ability to oversee the manufacturing process. Third-party inspectors can verify that the medicine cabinets meet all specified standards and regulations.
What Nuances Should International Buyers Consider Regarding Quality Control?
International B2B buyers must navigate several nuances related to quality control that may vary by region.
-
Understanding Regional Standards and Regulations
Different regions may have specific regulations that affect product standards. For example, the European Union has stringent CE marking requirements, whereas other regions may have different compliance criteria. Buyers should familiarize themselves with these regulations and ensure that their suppliers are compliant. -
Cultural and Communication Considerations
Effective communication is crucial when dealing with international suppliers. Language barriers and cultural differences can impact the clarity of quality expectations. Buyers should establish clear lines of communication and consider using local intermediaries who understand regional practices. -
Logistics and Supply Chain Management
The logistics of transporting medicine cabinets internationally can also affect quality. Buyers should consider how products are packaged and transported to minimize damage during transit. Understanding the supplier’s logistics strategy can provide insights into how they manage quality throughout the supply chain.
By understanding these manufacturing processes and quality assurance practices, international B2B buyers can make informed decisions when selecting medicine cabinet manufacturers, ensuring they partner with reliable suppliers that meet their quality expectations.
Practical Sourcing Guide: A Step-by-Step Checklist for ‘medicine cabinet manufacturer’
The following practical sourcing guide offers a step-by-step checklist for international B2B buyers seeking to procure medicine cabinets from manufacturers. This guide is designed to streamline your purchasing process, ensuring that you select the right supplier who meets your specific needs, particularly for those operating in Africa, South America, the Middle East, and Europe.
Step 1: Define Your Technical Specifications
Establish clear product requirements before beginning your search. Consider the materials, dimensions, design features, and compliance with local regulations. This step is crucial to ensure that the medicine cabinets meet your operational needs and safety standards.
- Materials: Identify whether you need stainless steel, wood, or a combination, depending on durability and aesthetic preferences.
- Size and Capacity: Specify the dimensions and storage capacity required for your intended use.
Step 2: Conduct Market Research
Investigate the market landscape to identify potential suppliers. Understanding the competitive landscape will help you locate manufacturers that specialize in medicine cabinets and have a good reputation.
- Local vs. International Suppliers: Consider both local manufacturers for quicker logistics and international suppliers who may offer unique designs or pricing advantages.
- Industry Trends: Stay informed about trends in materials and design that may influence your purchasing decisions.
Step 3: Evaluate Potential Suppliers
Thoroughly vet potential suppliers to ensure they align with your standards. Look beyond their website and assess their credibility through various means.
- Request Documentation: Ask for company profiles, certifications, and case studies.
- Seek References: Contact other businesses in your industry or region to gather insights on their experiences with the supplier.
Step 4: Verify Supplier Certifications
Ensure that your selected suppliers meet industry standards and certifications. This is particularly important for products that must comply with health and safety regulations.
- Quality Certifications: Look for ISO certifications or similar that indicate adherence to quality management systems.
- Compliance with Local Regulations: Verify that the products meet the specific standards set by health authorities in your region.
Step 5: Request Samples
Before placing a large order, request samples of the medicine cabinets. This step allows you to assess the quality and suitability of the product firsthand.
- Quality Assessment: Evaluate the craftsmanship, materials, and overall functionality.
- Fit for Purpose: Test how well the cabinets meet your specified requirements in a practical environment.
Step 6: Negotiate Terms and Conditions
Once you’ve chosen a supplier, negotiate favorable terms and conditions. This includes pricing, payment terms, delivery schedules, and warranties.
- Pricing Flexibility: Discuss bulk purchase discounts or long-term partnership incentives.
- Delivery and Lead Times: Establish clear timelines for delivery to avoid disruptions in your operations.
Step 7: Monitor Supplier Performance
After procurement, continuously monitor your supplier’s performance. This ensures that they maintain quality and service standards over time.
- Quality Control: Implement regular checks on the products received.
- Feedback Loop: Establish a feedback mechanism for ongoing communication regarding performance issues or improvements.
This structured approach will help international B2B buyers navigate the procurement process for medicine cabinets effectively, ensuring that they partner with the right manufacturers for their specific needs.
Comprehensive Cost and Pricing Analysis for medicine cabinet manufacturer Sourcing
What are the Key Cost Components in Sourcing Medicine Cabinets?
When sourcing medicine cabinets, understanding the cost structure is crucial for international B2B buyers. The primary components that contribute to the overall cost include:
-
Materials: The choice of materials significantly impacts the price. Common materials include stainless steel, wood, and glass. Premium materials increase durability and aesthetic appeal but also raise costs.
-
Labor: Labor costs vary by region and are influenced by local wage standards and skill levels. In countries with higher labor costs, manufacturers may pass these expenses onto buyers.
-
Manufacturing Overhead: This includes costs associated with factory operations, such as utilities, rent, and equipment depreciation. Efficient manufacturing processes can help mitigate these overhead costs.
-
Tooling: Tooling costs arise from the need for specialized equipment to produce custom designs. Buyers should consider whether they need standard products or custom solutions, as custom tooling can increase initial costs.
-
Quality Control (QC): Ensuring product quality is essential, particularly in the healthcare sector. Comprehensive QC processes can add to costs but are vital for compliance with health regulations.
-
Logistics: Transportation and shipping fees also play a significant role in the total cost. Factors such as distance, shipping method, and freight forwarding services must be evaluated.
-
Margin: Manufacturers typically add a profit margin to cover their costs and ensure viability. Understanding typical margins in the industry can help buyers negotiate better prices.
How Do Pricing Influencers Affect Medicine Cabinet Costs?
Several factors influence pricing beyond the basic cost structure:
-
Volume and Minimum Order Quantity (MOQ): Higher order volumes often lead to lower per-unit costs. Buyers should negotiate MOQs to optimize their purchasing strategy.
-
Specifications and Customization: Customized cabinets tailored to specific needs can incur higher costs. Buyers should weigh the benefits of customization against budget constraints.
-
Materials and Certifications: Products made from certified materials (e.g., environmentally friendly or health-compliant) may come at a premium. Buyers should consider the importance of these certifications in their purchasing decisions.
-
Supplier Factors: The reputation, reliability, and experience of the supplier can impact pricing. Established suppliers may charge more due to their proven track record.
-
Incoterms: Understanding Incoterms (International Commercial Terms) is essential for international transactions. These terms define the responsibilities of buyers and sellers regarding shipping, insurance, and tariffs, influencing the overall cost.
What Tips Can Help International B2B Buyers Negotiate Better Prices?
For buyers in Africa, South America, the Middle East, and Europe, negotiating costs effectively requires strategic approaches:
-
Conduct Thorough Research: Understanding market prices and supplier offerings helps buyers negotiate effectively. Use industry benchmarks to assess whether a quote is reasonable.
-
Focus on Total Cost of Ownership (TCO): Consider not just the purchase price but also the long-term costs associated with maintenance, shipping, and potential repairs. A lower upfront cost may not always lead to overall savings.
-
Negotiate Terms: Engage in discussions about payment terms, delivery schedules, and warranties. Flexible terms can enhance value without significantly impacting price.
-
Leverage Relationships: Building strong relationships with suppliers can lead to better pricing and terms. Long-term partnerships often yield better deals and reliability in supply.
-
Be Aware of Pricing Nuances: International buyers should be mindful of currency fluctuations, tariffs, and local taxes that can affect the final price. Understanding these nuances can help in budgeting and financial planning.
Disclaimer on Indicative Prices
It is important to note that the prices for medicine cabinets can vary widely based on the aforementioned factors. This analysis provides a framework for understanding costs but should not be seen as a definitive pricing guide. Buyers are encouraged to conduct due diligence and obtain multiple quotes to ensure competitive pricing.
Alternatives Analysis: Comparing medicine cabinet manufacturer With Other Solutions
Exploring Alternatives to Medicine Cabinet Manufacturing
When considering the procurement of medicine cabinets, B2B buyers have a variety of alternatives that may fulfill their storage and organizational needs. Understanding these alternatives is crucial for making an informed decision that aligns with operational requirements, budget constraints, and long-term sustainability. Below, we compare the traditional medicine cabinet manufacturing approach with two viable alternatives: modular storage systems and digital health solutions.
Comparison Aspect | Medicine Cabinet Manufacturer | Modular Storage Systems | Digital Health Solutions |
---|---|---|---|
Performance | High durability; traditional design | Flexible design; customizable | Enhanced data management; remote access |
Cost | Moderate to high production costs | Variable based on size and materials | Subscription-based; can scale |
Ease of Implementation | Requires installation; may need professional help | Easy to assemble; DIY options available | Requires IT infrastructure; training necessary |
Maintenance | Low; generally durable | Moderate; depends on material | High; ongoing software updates and support |
Best Use Case | Healthcare facilities needing secure storage | Clinics or pharmacies with space constraints | Telehealth providers needing patient data management |
What Are the Advantages and Disadvantages of Modular Storage Systems?
Modular storage systems provide a flexible alternative to traditional medicine cabinets. These systems can be tailored to fit specific space requirements and can easily adapt to changing needs. The ease of assembly makes them attractive for organizations looking to minimize downtime during implementation. However, while they offer versatility, their performance in terms of security and durability may not match that of traditional medicine cabinets, particularly in high-stakes environments like hospitals.
How Do Digital Health Solutions Compare?
Digital health solutions represent a modern approach to managing medical supplies and patient information. These systems often integrate with electronic health records (EHRs) and offer remote access to data, enhancing operational efficiency. However, they require significant investment in IT infrastructure and ongoing training for staff, making them a less attractive option for some organizations. Additionally, the costs can vary widely based on the scale of implementation, which may deter smaller facilities.
Conclusion: How Should B2B Buyers Choose the Right Solution?
Selecting the right solution for your storage needs hinges on multiple factors, including budget, space availability, and operational objectives. Medicine cabinets remain a staple for secure and durable storage, particularly in environments where safety is paramount. Conversely, modular systems may be ideal for organizations with limited space or those seeking flexibility. For businesses looking to modernize their operations, digital health solutions offer advanced capabilities but require careful consideration of the associated costs and training needs. Ultimately, a thorough assessment of your specific requirements will guide you in choosing the most effective solution.
Essential Technical Properties and Trade Terminology for medicine cabinet manufacturer
What Are the Essential Technical Properties for Medicine Cabinets?
Understanding the key technical properties of medicine cabinets is crucial for international B2B buyers seeking to make informed purchasing decisions. Here are some critical specifications to consider:
1. Material Grade
The material used in medicine cabinets often dictates durability, aesthetics, and maintenance. Common materials include stainless steel, aluminum, and high-grade plastics. Stainless steel, for example, is favored for its corrosion resistance and strength, making it suitable for high-moisture environments like bathrooms. Understanding material grade helps buyers select products that meet specific environmental and usage conditions.
2. Tolerance Levels
Tolerance refers to the allowable deviation from specified dimensions in the manufacturing process. In medicine cabinets, maintaining tight tolerances is essential for ensuring that doors align properly and that the cabinet fits securely in its designated space. High tolerance levels reduce the risk of misalignment and operational issues, which can lead to increased maintenance costs.
3. Load Capacity
Load capacity indicates the maximum weight that a medicine cabinet can safely hold. This is particularly important for cabinets designed to store heavy items such as large medicine bottles or medical supplies. Buyers should consider the intended use and choose cabinets that provide adequate support to prevent damage and ensure safety.
4. Finish Type
The finish of a medicine cabinet affects both its appearance and durability. Common finishes include powder coating, anodizing, and polished surfaces. A high-quality finish not only enhances the cabinet’s aesthetic appeal but also provides protection against scratches, tarnishing, and moisture. Buyers should evaluate the finish options based on their target market and desired look.
5. Dimensions and Configuration
Standard dimensions for medicine cabinets often range from small, compact units to larger, multi-shelf designs. Buyers must consider the space available in their target locations and the specific configuration that will best meet customer needs. Customization options can also be a selling point for manufacturers looking to differentiate their products in a competitive market.
What Are Common Trade Terms in the Medicine Cabinet Manufacturing Industry?
Familiarizing yourself with industry jargon can streamline communication and negotiations. Here are some essential trade terms for buyers in the medicine cabinet manufacturing sector:
1. OEM (Original Equipment Manufacturer)
An OEM is a company that produces parts or products that are used in another company’s end product. For medicine cabinet manufacturers, working with OEMs can provide access to specialized components, enhancing product quality and reducing production costs. Understanding OEM relationships can help buyers identify reliable suppliers for their needs.
2. MOQ (Minimum Order Quantity)
MOQ refers to the minimum number of units a supplier is willing to produce or sell. This is a critical factor for B2B buyers as it impacts inventory management and cash flow. Knowing the MOQ can help buyers negotiate better pricing and avoid overstocking.
3. RFQ (Request for Quotation)
An RFQ is a formal document used to request pricing and terms from suppliers. It is essential for buyers to articulate their requirements clearly in an RFQ to receive accurate and competitive quotes. This process helps ensure that all potential suppliers are evaluated on a level playing field.
4. Incoterms (International Commercial Terms)
Incoterms define the responsibilities of buyers and sellers in international trade. They clarify aspects such as shipping costs, risk, and insurance. Familiarity with Incoterms is vital for B2B buyers to understand their obligations and mitigate risks during the import/export process.
5. Lead Time
Lead time is the duration from placing an order to receiving the product. Understanding lead times is crucial for effective inventory planning and meeting customer demands. Buyers should communicate their timeline needs with manufacturers to ensure timely delivery.
By grasping these essential technical properties and trade terms, international B2B buyers can make more informed decisions when sourcing medicine cabinets, ultimately leading to better product quality and customer satisfaction.
Navigating Market Dynamics and Sourcing Trends in the medicine cabinet manufacturer Sector
What are the Current Market Dynamics and Sourcing Trends in the Medicine Cabinet Manufacturer Sector?
The medicine cabinet manufacturing sector is experiencing transformative changes driven by technological advancements, evolving consumer preferences, and global supply chain dynamics. Key drivers include the increasing demand for personalized healthcare solutions and the integration of smart technology into traditional products. For international B2B buyers, particularly from Africa, South America, the Middle East, and Europe, understanding these trends is crucial for strategic sourcing decisions.
One significant trend is the rise of digital platforms that facilitate sourcing and procurement. Companies are leveraging e-commerce solutions to streamline operations and reduce lead times. Additionally, the adoption of advanced manufacturing technologies, such as automation and robotics, is enhancing production efficiency while minimizing costs. Buyers from regions like Europe and the Middle East are particularly focused on these technologies, as they seek suppliers that can provide competitive pricing and quick turnaround times.
Another emerging trend is the shift towards modular and customizable medicine cabinets that meet specific healthcare requirements. This flexibility allows manufacturers to cater to diverse market needs, enhancing their appeal in different regions. B2B buyers should consider suppliers that offer innovative designs and can adapt to local regulations and preferences.
How is Sustainability Shaping Sourcing Decisions in the Medicine Cabinet Manufacturing Sector?
Sustainability and ethical sourcing are becoming increasingly vital in the medicine cabinet manufacturing sector. The environmental impact of manufacturing processes is under scrutiny, prompting companies to adopt greener practices. For B2B buyers, the importance of sourcing from manufacturers that prioritize sustainable materials and processes cannot be overstated.
Buyers should look for suppliers who utilize certified sustainable materials, such as recycled plastics and eco-friendly finishes. Certifications like Forest Stewardship Council (FSC) for wood products or ISO 14001 for environmental management systems can serve as indicators of a manufacturer‘s commitment to sustainability. Furthermore, ethical supply chains that ensure fair labor practices are gaining traction, particularly among European buyers who are increasingly aligning their sourcing strategies with corporate social responsibility (CSR) goals.
Investing in sustainable sourcing not only enhances brand reputation but also attracts environmentally-conscious consumers. As regulatory pressures around environmental standards tighten globally, manufacturers who prioritize sustainability will likely gain a competitive edge in the market.
What is the Historical Context of the Medicine Cabinet Manufacturing Sector?
The medicine cabinet manufacturing sector has evolved significantly over the past few decades. Initially, medicine cabinets were simple storage solutions for medical supplies, primarily used in healthcare facilities. However, as the focus on healthcare quality and patient safety increased, the design and functionality of medicine cabinets advanced.
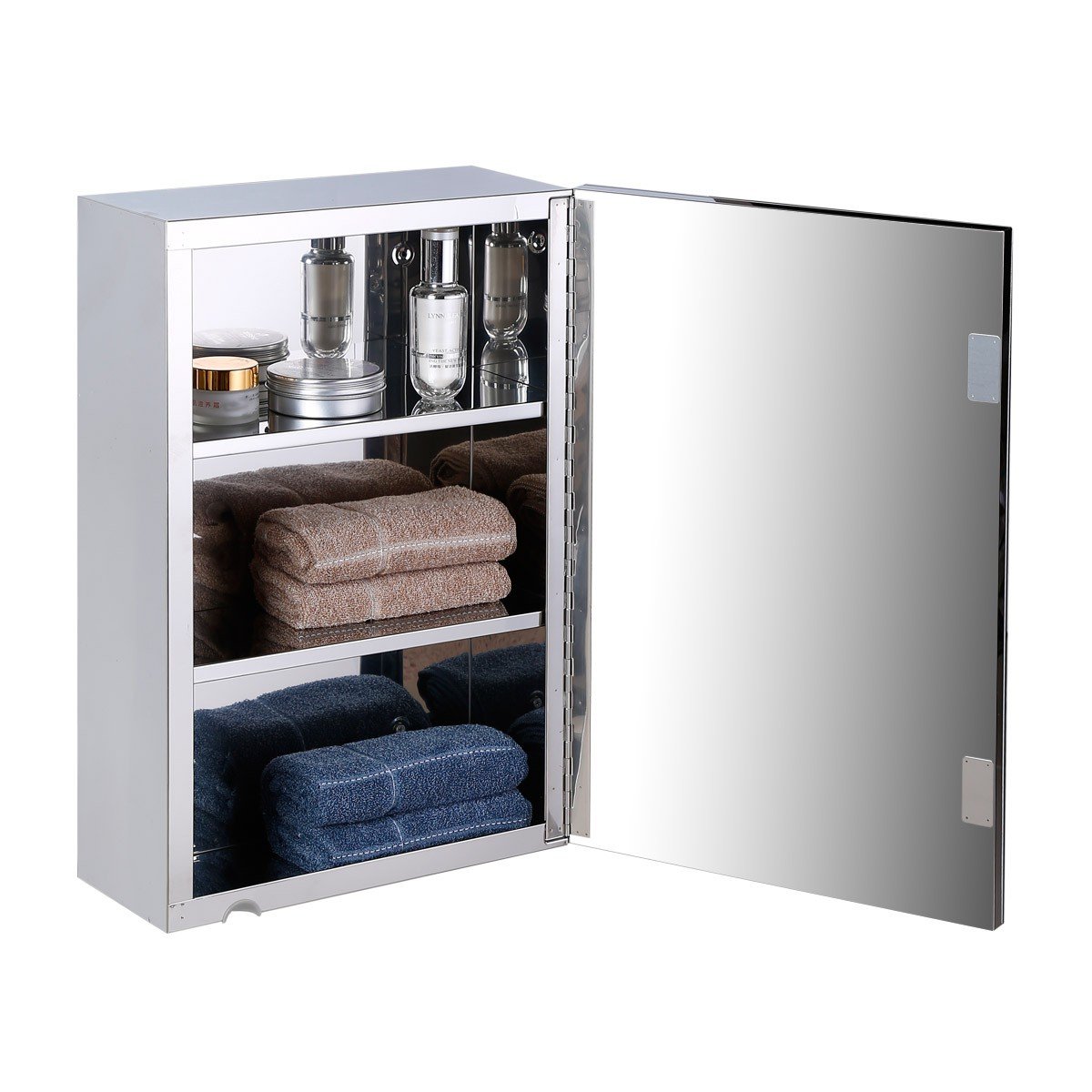
A stock image related to medicine cabinet manufacturer.
The introduction of smart technology has further revolutionized the sector, allowing for features such as integrated lighting, digital health monitoring, and secure storage for medications. This evolution reflects a broader trend in the healthcare industry towards innovation and technology integration, catering to the modern consumer’s needs.
Understanding this historical context is essential for B2B buyers, as it highlights the importance of innovation in sourcing decisions. Suppliers that have adapted to these changes by incorporating technology and sustainable practices into their offerings will be better positioned to meet the demands of today’s market.
Frequently Asked Questions (FAQs) for B2B Buyers of medicine cabinet manufacturer
-
How do I select the right medicine cabinet manufacturer for my business needs?
Choosing the right medicine cabinet manufacturer involves evaluating several key factors. Start by assessing the manufacturer’s experience and reputation in the industry, particularly in your target market regions like Africa, South America, the Middle East, and Europe. Look for certifications that ensure product quality and safety standards compliance. Additionally, consider their production capabilities, including the ability to customize products based on your specifications and the flexibility in meeting your order volumes. -
What customization options are available when sourcing medicine cabinets?
Most reputable medicine cabinet manufacturers offer a range of customization options to meet diverse client needs. You can typically request changes in size, material, color, and design features. It’s essential to discuss your specific requirements upfront and inquire about the manufacturer’s design capabilities. Some manufacturers may also provide prototype samples to ensure the final product aligns with your vision before mass production begins. -
What are the minimum order quantities (MOQs) for medicine cabinets from manufacturers?
Minimum order quantities can vary significantly between manufacturers. Generally, MOQs may range from a few dozen to several hundred units, depending on the product type and customization level. When negotiating with suppliers, clarify their MOQ policies to ensure they align with your purchasing capabilities. If your order volume is lower, consider discussing potential flexibility or alternative solutions that could accommodate your needs. -
What payment terms should I expect when working with international medicine cabinet suppliers?
Payment terms can differ widely based on the manufacturer’s policies and the nature of the transaction. Common terms may include upfront deposits ranging from 30% to 50% of the total order value, with the balance due before shipment. Additionally, inquire about options for letters of credit or payment through escrow services for added security. Understanding these terms upfront will help you manage cash flow and ensure a smooth transaction process. -
How can I ensure quality assurance when sourcing medicine cabinets internationally?
To ensure quality assurance, request detailed information about the manufacturer’s quality control processes. Look for certifications like ISO 9001, which indicate adherence to international quality standards. Additionally, consider arranging third-party inspections during production or before shipment to verify that the products meet your specifications. Establishing clear quality benchmarks in your contract can also help in maintaining product consistency. -
What logistics considerations should I keep in mind when importing medicine cabinets?
Logistics plays a crucial role in international sourcing. Be aware of shipping methods, estimated delivery times, and customs regulations specific to your region. Work closely with your supplier to understand their shipping practices and choose a reliable freight forwarder familiar with medical product imports. Also, factor in potential tariffs and duties, as these can significantly affect your total landed cost. -
What are the common challenges faced when sourcing medicine cabinets internationally?
Common challenges include language barriers, cultural differences, and varying regulatory standards across countries. Additionally, managing lead times and ensuring timely delivery can be complicated by global logistics issues. To mitigate these risks, develop clear communication channels with your supplier, conduct thorough due diligence, and consider working with local agents who understand the market dynamics and regulations. -
How do I verify the credibility of a medicine cabinet manufacturer?
Verifying a manufacturer’s credibility involves several steps. Begin by researching their business history, customer reviews, and industry presence. Request references from past clients and check for any certifications or memberships in industry associations. Additionally, consider visiting their manufacturing facility if feasible, or utilizing online platforms that provide insights into supplier ratings and performance metrics to ensure they meet your standards.
Important Disclaimer & Terms of Use
⚠️ Important Disclaimer
The information provided in this guide, including content regarding manufacturers, technical specifications, and market analysis, is for informational and educational purposes only. It does not constitute professional procurement advice, financial advice, or legal advice.
While we have made every effort to ensure the accuracy and timeliness of the information, we are not responsible for any errors, omissions, or outdated information. Market conditions, company details, and technical standards are subject to change.
B2B buyers must conduct their own independent and thorough due diligence before making any purchasing decisions. This includes contacting suppliers directly, verifying certifications, requesting samples, and seeking professional consultation. The risk of relying on any information in this guide is borne solely by the reader.
Strategic Sourcing Conclusion and Outlook for medicine cabinet manufacturer
What Are the Key Takeaways for B2B Buyers in the Medicine Cabinet Manufacturing Sector?
In the competitive landscape of medicine cabinet manufacturing, strategic sourcing emerges as a vital component for international B2B buyers. By focusing on supplier relationships, understanding regional market dynamics, and leveraging data analytics, companies can significantly enhance their procurement processes. Buyers should prioritize manufacturers with robust quality control measures, sustainable practices, and innovative product designs to meet diverse consumer needs across Africa, South America, the Middle East, and Europe.
How Can Strategic Sourcing Drive Competitive Advantage?
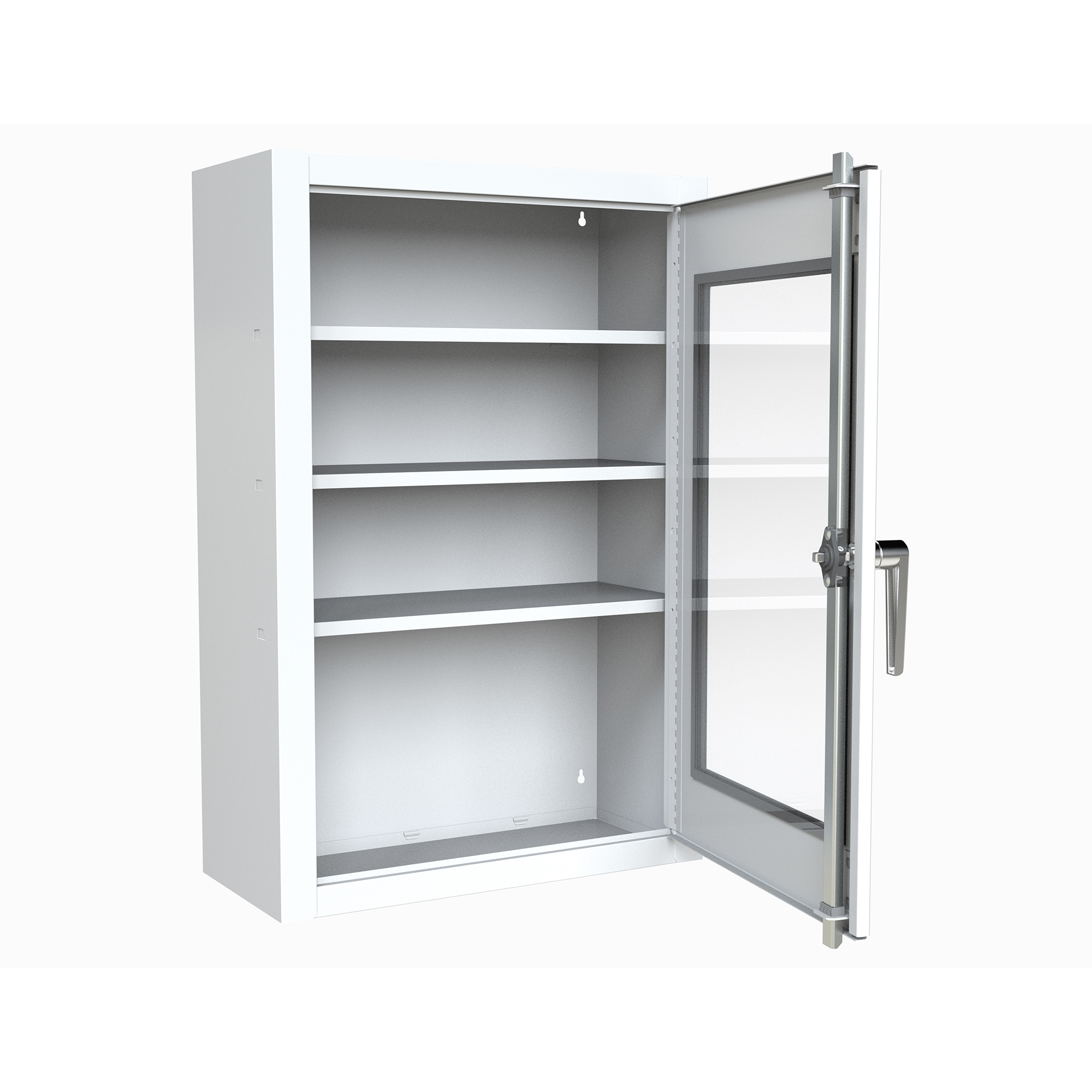
A stock image related to medicine cabinet manufacturer.
The value of strategic sourcing cannot be overstated; it streamlines operations, reduces costs, and fosters long-term partnerships that can lead to exclusive market advantages. By integrating technology and AI-driven insights into sourcing strategies, buyers can enhance decision-making and responsiveness to market changes, ensuring alignment with evolving consumer expectations.
What Is the Future Outlook for International B2B Buyers?
Looking ahead, international B2B buyers should remain agile and proactive in their sourcing strategies. As trends in sustainability and smart technologies continue to shape the medicine cabinet market, leveraging these insights will be crucial for securing a competitive edge. Engage with suppliers who demonstrate innovation and adaptability, and consider investing in collaborative platforms to enhance communication and streamline logistics. By doing so, you will position your business not only to meet current demands but also to thrive in the evolving marketplace.