Discover Top Benefits of Choosing a PDU Manufacturer (2025)
Introduction: Navigating the Global Market for pdu manufacturer
Navigating the global market for PDU manufacturers poses unique challenges for international B2B buyers, particularly those in Africa, South America, the Middle East, and Europe. The need for reliable power distribution units (PDUs) is growing as businesses increasingly rely on technology and data centers. However, sourcing the right PDU can be daunting due to varying specifications, compliance requirements, and supplier reliability. This guide aims to demystify the complexities of selecting the ideal PDU, empowering buyers to make informed decisions.
Throughout this comprehensive resource, we will explore different types of PDUs, their applications across various industries, and essential criteria for vetting suppliers. Additionally, we will address cost considerations, helping buyers understand the financial implications of their choices. By providing actionable insights and practical strategies, this guide equips B2B buyers with the knowledge necessary to navigate their sourcing journeys effectively.
Whether you’re a decision-maker in a burgeoning tech company in South America or an operations manager in a data center in Germany, understanding the nuances of PDU procurement is vital. This guide not only highlights best practices but also offers a roadmap to sourcing high-quality products that meet your specific needs, ensuring that your business remains competitive in an increasingly interconnected market.
Understanding pdu manufacturer Types and Variations
Type Name | Key Distinguishing Features | Primary B2B Applications | Brief Pros & Cons for Buyers |
---|---|---|---|
Basic PDU | Simple design, passive power distribution | Small server rooms, offices | Pros: Cost-effective, easy to install. Cons: Limited monitoring capabilities. |
Metered PDU | Integrated power meters for load monitoring | Data centers, telecommunications | Pros: Real-time monitoring, helps prevent overloads. Cons: Higher initial cost. |
Smart PDU | Network-enabled for remote management and monitoring | Large enterprises, cloud services | Pros: Advanced features, energy efficiency. Cons: Complexity may require training. |
High-Density PDU | Compact design with numerous outlets for high power demands | Data centers, high-performance computing | Pros: Maximizes space, tailored for high loads. Cons: May require specialized installation. |
Vertical PDU | Designed to mount in server racks, saving floor space | Data centers, server farms | Pros: Space-saving, easy access to outlets. Cons: Limited to specific rack types. |
What are the Characteristics of Basic PDUs?
Basic PDUs are the most straightforward type of power distribution unit, providing passive power distribution without any monitoring or management features. They are typically utilized in small server rooms or office environments where the power needs are minimal and straightforward. Buyers should consider their budget and installation simplicity, as these units are generally cost-effective and require little technical know-how for setup. However, the lack of monitoring capabilities may lead to unexpected overloads if not managed properly.
How Do Metered PDUs Enhance Power Management?
Metered PDUs come equipped with integrated power meters that allow users to monitor the electrical load on each outlet in real-time. This feature is particularly beneficial in data centers and telecommunications environments where managing power consumption is critical. Buyers should evaluate their need for monitoring capabilities, as these units can help prevent overloads and improve energy efficiency. However, the initial investment is higher compared to basic PDUs, which may deter budget-conscious buyers.
Why Choose Smart PDUs for Advanced Management?
Smart PDUs offer advanced features such as network connectivity, enabling remote management and monitoring via web interfaces or mobile apps. These units are ideal for large enterprises and cloud service providers that need to manage multiple power distribution points efficiently. When considering a Smart PDU, buyers should assess their infrastructure’s readiness for advanced technology and the potential return on investment through improved energy management. The complexity of these systems may require additional training for staff, which is an important consideration.
What Makes High-Density PDUs Suitable for Data Centers?
High-Density PDUs are designed to accommodate the significant power demands of modern data centers and high-performance computing environments. They feature a compact design that maximizes the number of outlets within a limited space, making them suitable for facilities with high power requirements. Buyers should consider their specific power load needs and ensure that the PDU can handle their equipment’s demands. While they effectively utilize space, these units may require specialized installation, which could add to overall costs.
How Do Vertical PDUs Optimize Space in Server Racks?
Vertical PDUs are specifically designed to be mounted within server racks, helping to save valuable floor space while providing easy access to multiple outlets. This design is particularly advantageous in data centers and server farms where space is at a premium. Buyers should assess the compatibility of the vertical PDU with their existing rack systems and the overall layout of their facilities. Although these units provide excellent space-saving benefits, their functionality is limited to specific rack types, which may not suit all environments.
Related Video: Heat Pump Thermostat O, B, and C Terminal Variations Explained
Key Industrial Applications of pdu manufacturer
Industry/Sector | Specific Application of PDU Manufacturer | Value/Benefit for the Business | Key Sourcing Considerations for this Application |
---|---|---|---|
Data Centers | Power Distribution Units for server racks | Ensures reliable power supply and efficient energy use | Compatibility with existing infrastructure and power ratings |
Telecommunications | PDU for telecom equipment in remote locations | Optimizes uptime and reduces operational costs | Environmental resilience and remote management capabilities |
Manufacturing | PDU for industrial machinery and robotics | Enhances equipment performance and reduces downtime | Load capacity and safety certifications |
Renewable Energy | PDU for solar and wind energy systems | Maximizes energy output and operational efficiency | Adaptability to varying energy inputs and monitoring features |
Healthcare Facilities | PDU for medical equipment in hospitals | Guarantees uninterrupted power for critical devices | Compliance with medical standards and scalability options |
How is PDU Manufacturer Used in Data Centers?
In data centers, Power Distribution Units (PDUs) are essential for distributing electricity to server racks. They solve problems related to power management, such as load balancing and redundancy. International B2B buyers must consider compatibility with existing infrastructure, energy efficiency ratings, and the ability to monitor power consumption. For regions like Africa and South America, where power reliability can be an issue, selecting a PDU that offers robust surge protection and backup options is crucial.
What Role Does PDU Play in Telecommunications?
Telecommunications companies utilize PDUs to manage power supply for equipment located in remote sites, such as cell towers and data relay stations. These PDUs enhance uptime and minimize operational costs by providing reliable power and enabling remote monitoring. Buyers from the Middle East and Europe should prioritize environmental resilience, as equipment may face harsh conditions. Features like remote management and alert systems can significantly reduce maintenance efforts and response times.
How is PDU Beneficial for Manufacturing?
In manufacturing, PDUs are crucial for powering industrial machinery and robotics, ensuring optimal performance and minimizing downtime. They help manage the distribution of power to various machines, which can be critical in high-output environments. For buyers in Europe, particularly in Germany, sourcing PDUs with high load capacities and safety certifications is vital to meet stringent regulatory standards and operational efficiency.
What is the Importance of PDU in Renewable Energy Systems?
PDUs are integral to renewable energy systems, such as solar and wind farms, where they manage the distribution of generated power. They help maximize energy output and ensure that power is effectively routed to storage systems or the grid. Buyers from South America, where renewable energy projects are expanding, should look for PDUs that can adapt to varying energy inputs and offer monitoring features to optimize performance.
How is PDU Used in Healthcare Facilities?
In healthcare settings, PDUs are essential for ensuring that medical equipment receives uninterrupted power supply, particularly in critical care environments. They help mitigate the risks of power outages, which can have dire consequences for patient care. International buyers must consider compliance with medical standards and the scalability of PDUs to accommodate future growth or changes in equipment needs. Investing in PDUs with advanced monitoring capabilities can further enhance operational reliability in healthcare facilities.
Related Video: Types Of Flowmeters And Their Industrial Applications.
3 Common User Pain Points for ‘pdu manufacturer’ & Their Solutions
Scenario 1: Struggling with Power Distribution in Data Centers
The Problem: B2B buyers in Africa and South America often face the challenge of inadequate power distribution systems within their data centers. As businesses expand, the demand for efficient and reliable power becomes critical. Many buyers encounter issues such as overloaded circuits, insufficient power outlets, and a lack of monitoring capabilities. These problems can lead to unexpected downtime, which is particularly detrimental in regions where continuous operation is essential for competitiveness.
The Solution: To address these issues, buyers should consider investing in advanced Power Distribution Units (PDUs) that offer scalability and monitoring features. When sourcing PDUs, look for manufacturers that provide customizable solutions tailored to specific power requirements. Ensure that the selected PDU can handle the anticipated load and has features such as remote monitoring, which allows for real-time tracking of power usage and alerts for any anomalies. By implementing PDUs that support load balancing and offer redundancy, businesses can enhance their power distribution efficiency and minimize the risk of outages.
Scenario 2: Navigating Compliance and Regulatory Standards
The Problem: In the Middle East and Europe, compliance with local electrical standards and safety regulations is paramount. B2B buyers often find themselves overwhelmed by the varying requirements across different countries. This complexity can lead to costly delays in project timelines and even potential legal issues if the equipment does not meet necessary standards. Buyers may struggle to determine which PDU specifications align with their local regulations.
The Solution: To navigate compliance effectively, B2B buyers should prioritize working with PDU manufacturers that have a strong reputation for understanding regional regulations. Engage with suppliers that provide comprehensive documentation, including compliance certifications and safety standards relevant to your location. Buyers should also leverage the expertise of local consultants or electrical engineers who can guide them through the regulatory landscape. Additionally, selecting PDUs that are designed with safety features—such as overcurrent protection and short-circuit protection—can help ensure that installations meet compliance requirements while enhancing overall operational safety.
Scenario 3: Limited Knowledge About Smart PDU Features
The Problem: Many international B2B buyers from Europe and South America are unaware of the advanced features that modern PDUs offer, such as smart monitoring and energy management capabilities. This lack of knowledge can lead to inefficient power management, resulting in higher operational costs and wasted energy. Businesses may find themselves utilizing outdated systems that do not provide the insights needed for effective energy consumption management.
The Solution: Buyers should take the initiative to educate themselves about the benefits of smart PDUs. When evaluating options, look for manufacturers that provide PDUs equipped with intelligent monitoring features, such as energy usage analytics and predictive maintenance alerts. These features allow businesses to optimize power usage, identify inefficiencies, and implement energy-saving measures. Consider engaging in pilot programs to test smart PDUs in a controlled environment before full-scale deployment. This approach not only enhances understanding but also demonstrates the tangible benefits of smart technology in reducing operational costs and improving energy efficiency.
Strategic Material Selection Guide for pdu manufacturer
What Are the Key Materials Used in PDU Manufacturing?
When selecting materials for Power Distribution Units (PDUs), manufacturers must consider various factors such as performance, durability, and cost. Here, we analyze four common materials used in PDU manufacturing: aluminum, steel, plastic, and copper. Each material has unique properties and implications for international B2B buyers, particularly from Africa, South America, the Middle East, and Europe.
How Does Aluminum Perform in PDU Applications?
Aluminum is widely used in PDU manufacturing due to its excellent strength-to-weight ratio and corrosion resistance. It typically has a temperature rating of up to 150°C and can withstand moderate pressure.
Pros:
– Lightweight, making it easier to handle and install.
– Good thermal conductivity, which helps in heat dissipation.
– Corrosion-resistant, ensuring longevity in various environments.
Cons:
– More expensive than some alternatives like plastic.
– Can be less durable under extreme conditions compared to steel.
Impact on Application:
Aluminum is suitable for environments where weight is a concern, such as mobile or temporary installations. However, its cost may be a barrier for budget-conscious projects.
Considerations for International Buyers:
Buyers should ensure compliance with standards like ASTM B221 for aluminum extrusions. In regions like Europe, adherence to DIN standards is also essential.
What Are the Advantages of Steel in PDU Manufacturing?
Steel is another popular choice for PDUs, known for its exceptional strength and durability. It has a higher temperature rating, often exceeding 200°C, and offers excellent resistance to physical impacts.
Pros:
– Highly durable and impact-resistant.
– Cost-effective compared to aluminum.
– Can be treated to enhance corrosion resistance.
Cons:
– Heavier, which can complicate installation.
– Prone to rust if not properly coated or maintained.
Impact on Application:
Steel is ideal for permanent installations in industrial settings where robustness is critical. However, its weight may limit its use in portable applications.
Considerations for International Buyers:
Compliance with standards such as ASTM A36 or JIS G3101 is crucial, especially for buyers in regions like South America and the Middle East, where local regulations may vary.
Why Is Plastic Used in PDU Manufacturing?
Plastic materials, particularly high-density polyethylene (HDPE) and polycarbonate, are increasingly being used in PDU manufacturing due to their lightweight and insulating properties. They typically have a temperature rating of around 60-80°C.
Pros:
– Lightweight and easy to mold into complex shapes.
– Excellent electrical insulation properties.
– Generally lower cost than metals.
Cons:
– Less durable than metal options, especially in high-temperature environments.
– Limited resistance to UV light, which can degrade performance over time.
Impact on Application:
Plastic is suitable for non-critical applications where electrical insulation is paramount, such as in residential or light commercial settings. However, it may not be ideal for heavy-duty industrial environments.
Considerations for International Buyers:
Buyers should ensure compliance with standards like UL 94 for flammability and ASTM D638 for tensile strength. Understanding local regulations regarding plastic use is also essential.
What Role Does Copper Play in PDU Manufacturing?
Copper is primarily used for electrical connections within PDUs due to its excellent conductivity. It can handle high temperatures and has a temperature rating of up to 200°C.
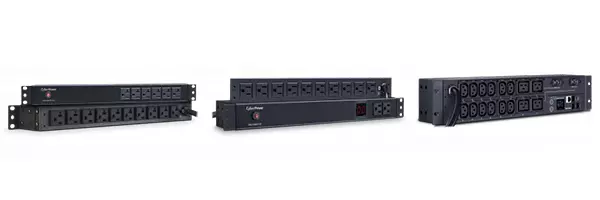
A stock image related to pdu manufacturer.
Pros:
– Superior electrical conductivity, reducing energy losses.
– Highly durable and resistant to corrosion.
– Easy to work with for electrical connections.
Cons:
– More expensive than aluminum and plastic.
– Heavier, which can complicate installation.
Impact on Application:
Copper is essential for high-performance applications requiring efficient power distribution, such as data centers. Its cost may be a limiting factor for budget-sensitive projects.
Considerations for International Buyers:
Compliance with standards such as ASTM B170 for copper and DIN EN 1977 is vital, especially for European buyers who prioritize regulatory adherence.
Summary Table of Material Properties for PDU Manufacturing
Material | Typical Use Case for PDU Manufacturer | Key Advantage | Key Disadvantage/Limitation | Relative Cost (Low/Med/High) |
---|---|---|---|---|
Aluminum | Lightweight PDUs for mobile applications | Excellent corrosion resistance | Higher cost than plastic | Medium |
Steel | Permanent installations in industrial settings | Highly durable and cost-effective | Heavier, complicating installation | Low |
Plastic | Non-critical applications requiring insulation | Lightweight and easy to mold | Less durable in high temperatures | Low |
Copper | High-performance electrical connections | Superior conductivity | More expensive than alternatives | High |
This analysis provides a comprehensive overview of the materials commonly used in PDU manufacturing, highlighting their properties and implications for international B2B buyers. Understanding these factors can help buyers make informed decisions that align with their specific operational needs and regional compliance requirements.
In-depth Look: Manufacturing Processes and Quality Assurance for pdu manufacturer
What Are the Main Stages of the Manufacturing Process for PDU Manufacturers?
The manufacturing of Power Distribution Units (PDUs) involves a multi-step process that ensures the final product meets the required specifications and industry standards. Here are the typical stages involved:
1. Material Preparation
The first stage in PDU manufacturing is the preparation of raw materials. This includes sourcing high-quality components such as circuit breakers, connectors, and enclosures. Suppliers often conduct a thorough vetting process to ensure the materials meet international standards such as ISO 9001. This is crucial for international buyers, particularly from regions like Africa and South America, where supply chain reliability can be a concern.
2. Forming and Fabrication
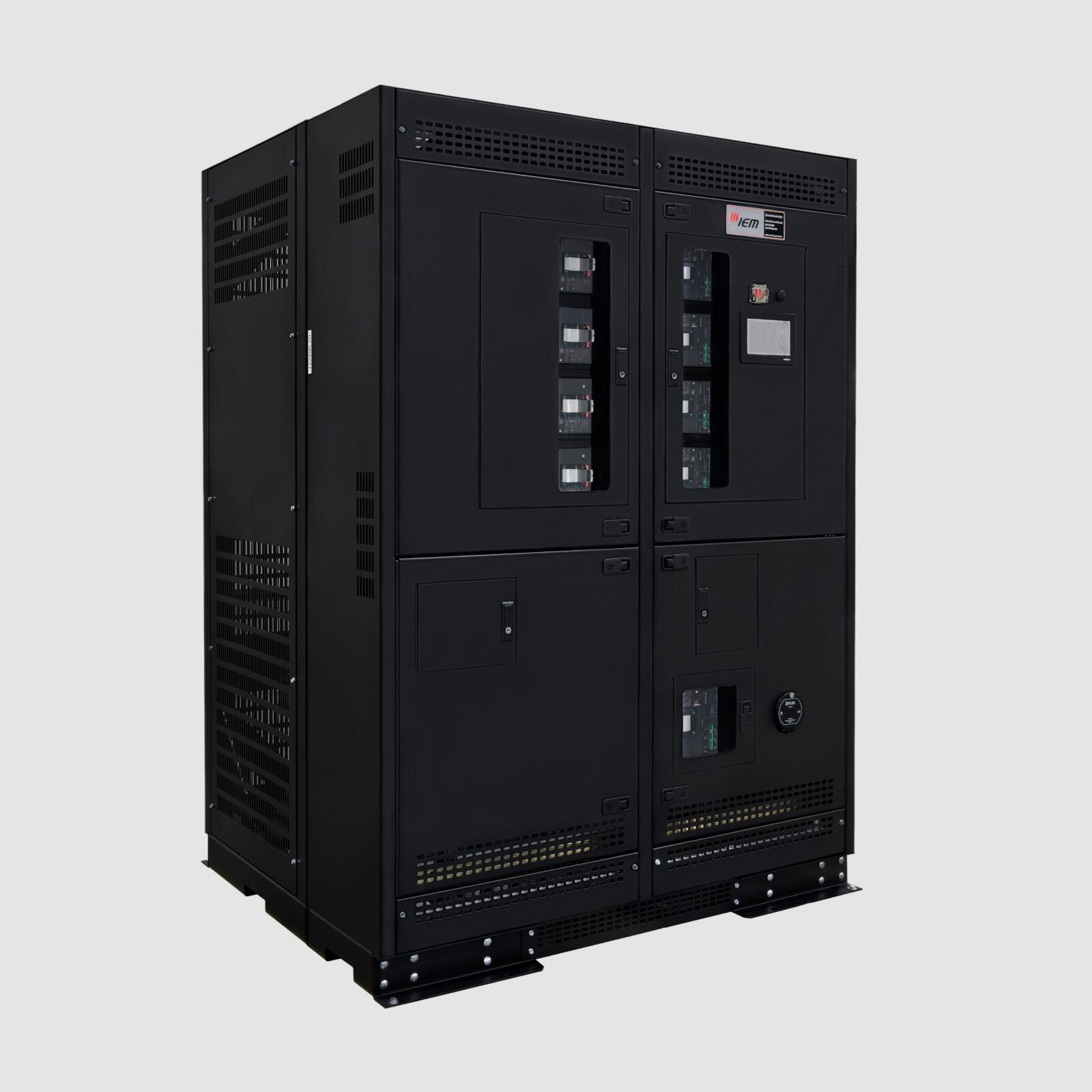
A stock image related to pdu manufacturer.
In this stage, raw materials are transformed into components through processes like cutting, bending, and machining. Advanced techniques such as laser cutting and CNC machining are commonly employed to achieve precision. This ensures that the parts fit together correctly during assembly, which is vital for the functionality and safety of the PDU.
3. Assembly
During assembly, various components are integrated to form the complete PDU. This stage often involves soldering, wiring, and fastening components together. Quality control checkpoints are critical here; manufacturers typically conduct In-Process Quality Control (IPQC) to ensure that each assembly meets specified tolerances and standards. For international buyers, understanding the assembly process can provide insights into the reliability and robustness of the final product.
4. Finishing
The final manufacturing stage involves finishing processes such as painting, labeling, and packaging. This not only enhances the aesthetic appeal of the PDU but also protects it from environmental factors. Manufacturers often use environmentally friendly coatings to comply with regulations in Europe and other regions.
How is Quality Assurance Implemented in PDU Manufacturing?
Quality assurance is a fundamental aspect of the manufacturing process for PDUs, ensuring that products are reliable and safe for use in various applications. Here’s how quality assurance is typically structured:
1. What International Standards Should B2B Buyers Look For?
International standards such as ISO 9001 are essential for ensuring that a manufacturer follows a quality management system. Additionally, industry-specific certifications like CE (Conformité Européenne) and API (American Petroleum Institute) may be relevant depending on the application of the PDU. For buyers from Europe, particularly countries like Spain and Germany, these certifications serve as a mark of quality and compliance with EU regulations.
2. What Are the Key Quality Control Checkpoints?
Quality control (QC) in PDU manufacturing typically involves several checkpoints, including:
- Incoming Quality Control (IQC): Assessing the quality of materials received from suppliers.
- In-Process Quality Control (IPQC): Monitoring the assembly process to catch defects early.
- Final Quality Control (FQC): Conducting thorough tests on finished products to ensure they meet specifications.
These checkpoints ensure that any issues are identified and rectified before the product reaches the customer.
What Common Testing Methods Are Used for PDUs?
Testing methods are crucial for verifying the functionality and safety of PDUs. Here are some common testing procedures:
- Electrical Testing: This includes measuring voltage, current, and resistance to ensure the PDU operates within specified limits.
- Thermal Testing: Assessing the heat dissipation capabilities of the PDU to prevent overheating during operation.
- Load Testing: Evaluating how the PDU performs under maximum load conditions.
These tests help ensure that the PDUs are safe for use in critical applications.
How Can B2B Buyers Verify Supplier Quality Control?
For international B2B buyers, especially in regions such as Africa and the Middle East, verifying the quality control processes of suppliers is vital. Here are several methods to consider:
- Supplier Audits: Conducting on-site audits of manufacturing facilities can provide insights into their quality management practices.
- Requesting Quality Reports: Buyers should ask for detailed quality control reports that outline testing results and compliance with relevant standards.
- Third-Party Inspections: Engaging third-party inspection services can offer an unbiased evaluation of the manufacturer’s processes and products.
What Are the Quality Control Nuances for International B2B Buyers?
International buyers must navigate various quality control nuances when sourcing PDUs. Here are some considerations:
- Understanding Regional Standards: Different regions may have specific standards that must be met. For instance, PDUs sold in Europe must comply with CE marking requirements, while those in the Middle East may need to meet local electrical safety standards.
- Cultural Considerations: Building relationships with suppliers may require an understanding of cultural norms and business practices in different regions.
- Language Barriers: Clear communication is essential; therefore, working with suppliers who can provide documentation in the buyer’s language can prevent misunderstandings.
Conclusion
The manufacturing processes and quality assurance practices for PDUs are critical for ensuring product reliability and safety. For international B2B buyers, particularly those from Africa, South America, the Middle East, and Europe, understanding these processes not only aids in making informed purchasing decisions but also fosters stronger relationships with suppliers. By focusing on quality assurance standards, testing methods, and supplier verification, buyers can secure high-quality PDUs that meet their operational needs.
Practical Sourcing Guide: A Step-by-Step Checklist for ‘pdu manufacturer’
Introduction
This sourcing guide is designed to assist international B2B buyers, particularly from regions such as Africa, South America, the Middle East, and Europe, in effectively procuring Power Distribution Units (PDUs) from manufacturers. Given the critical role PDUs play in ensuring reliable power distribution for electrical devices, following a structured checklist can streamline the selection process, mitigate risks, and ensure that your organization invests wisely.
Step 1: Define Your Technical Specifications
Before reaching out to manufacturers, it’s essential to clearly outline your technical requirements. Identify the power capacity, input and output configurations, and any specific features such as monitoring capabilities or remote management functionalities.
– Consider your application: Different environments (e.g., data centers vs. industrial settings) may necessitate distinct specifications.
– Future-proofing: Anticipate future needs by selecting PDUs that can accommodate potential growth in power requirements.
Step 2: Research Potential Manufacturers
Conduct thorough research to identify manufacturers that specialize in PDUs. Utilize industry directories, trade shows, and online platforms to compile a list of potential suppliers.
– Focus on reputation: Look for manufacturers with a strong reputation in the industry, as well as positive reviews and testimonials from previous clients.
– Regional considerations: Consider manufacturers that have experience in your specific region, as they may better understand local regulations and market conditions.
Step 3: Verify Supplier Certifications
Ensure that the manufacturers you are considering have the necessary certifications, such as ISO 9001 or IEC standards. This verification is crucial for ensuring quality and safety in manufacturing processes.
– Ask for documentation: Request copies of relevant certifications and compliance documents to confirm their validity.
– Quality assurance: Certified manufacturers are more likely to adhere to high-quality standards, reducing the risk of equipment failure.
Step 4: Evaluate Supplier Capabilities
Assess the manufacturing capabilities of potential suppliers to ensure they can meet your specific needs. This evaluation should include their production capacity, technology used, and design flexibility.
– Customization options: Determine if the manufacturer can accommodate custom designs that may be necessary for your application.
– Lead times: Inquire about production lead times to ensure they align with your project timelines.
Step 5: Request Samples and Technical Support
Before making a final decision, request samples of the PDUs you are considering. This will allow you to evaluate the quality and performance of the units firsthand.
– Technical support availability: Ensure that the manufacturer provides robust technical support and after-sales service, which is crucial for troubleshooting and maintenance.
– Installation guidance: Manufacturers that offer installation support or resources can help ensure a smooth setup process.
Step 6: Compare Pricing and Payment Terms
Collect pricing information from multiple manufacturers to evaluate cost-effectiveness. However, consider the total cost of ownership, not just the initial purchase price.
– Payment flexibility: Review the payment terms offered by each supplier, looking for options that align with your financial policies.
– Warranty and service agreements: Factor in warranties and service agreements as part of your overall cost evaluation.
Step 7: Conduct Site Visits if Possible
If feasible, arrange site visits to the manufacturing facilities of your shortlisted suppliers. This will provide insight into their operations, quality control measures, and overall professionalism.
– Inspect quality control processes: Observing their quality assurance practices can help you gauge their commitment to product excellence.
– Build relationships: Personal interactions can foster stronger partnerships and enhance communication throughout the procurement process.
By following this step-by-step checklist, B2B buyers can make informed decisions when sourcing PDUs from manufacturers, ultimately leading to improved operational efficiency and reliability in power distribution.
Comprehensive Cost and Pricing Analysis for pdu manufacturer Sourcing
What Are the Key Cost Components in PDU Manufacturing?
When sourcing Power Distribution Units (PDUs), understanding the cost structure is crucial for international B2B buyers. The primary cost components include:
-
Materials: The choice of materials significantly impacts the overall cost. High-quality components such as copper for wiring or specialized plastics for casing can increase material costs but enhance durability and performance.
-
Labor: Labor costs vary by region and can be influenced by local wage standards and skill levels. Skilled labor is often required for assembly and quality assurance, which can add to the total expense.
-
Manufacturing Overhead: This includes costs related to the production facility, utilities, and equipment maintenance. Efficient production processes can help minimize overhead costs.
-
Tooling: Initial tooling costs for custom designs can be substantial. However, these costs are amortized over the production run, making them less impactful for high-volume orders.
-
Quality Control (QC): Implementing stringent QC processes is essential to ensure product reliability. The costs associated with testing and certification can be significant but are necessary for compliance with industry standards.
-
Logistics: Shipping costs, including freight charges and customs duties, can vary widely based on the destination. Efficient logistics planning can help mitigate these costs.
-
Margin: Manufacturers typically add a profit margin to cover their expenses and provide a return on investment. This margin can be negotiated based on order size and relationship with the supplier.
How Do Price Influencers Affect PDU Sourcing?
Several factors can influence the pricing of PDUs:
-
Volume and Minimum Order Quantity (MOQ): Larger orders often lead to lower per-unit costs. Understanding the supplier’s MOQ can help buyers negotiate better pricing.
-
Specifications and Customization: Custom specifications can increase costs due to the need for specialized materials or processes. Buyers should clearly outline their needs to get accurate quotes.
-
Materials: The choice of materials not only affects the upfront cost but also the long-term reliability and maintenance costs of the PDU.
-
Quality and Certifications: Products that meet international standards or come with specific certifications may command higher prices. Buyers should weigh the benefits of these certifications against their budget.
-
Supplier Factors: The reputation and reliability of the supplier can impact pricing. Established suppliers may offer better quality but at a higher cost.
-
Incoterms: The terms of delivery can significantly affect pricing. Understanding who is responsible for shipping, insurance, and tariffs can help buyers calculate the total landed cost.
What Negotiation Tips Can Buyers Use for Cost Efficiency?
For international B2B buyers, particularly those from Africa, South America, the Middle East, and Europe, effective negotiation can lead to significant savings:
-
Understand Total Cost of Ownership (TCO): Consider not just the initial purchase price but also the long-term costs associated with maintenance, energy consumption, and potential downtime.
-
Leverage Volume Discounts: If planning multiple purchases, negotiate bulk pricing or long-term contracts to reduce costs.
-
Build Relationships: Establishing strong relationships with suppliers can lead to better pricing, improved service, and more favorable terms.
-
Request Multiple Quotes: Always obtain quotes from several manufacturers to compare prices and terms. This can provide leverage in negotiations.
-
Be Clear About Specifications: Providing detailed specifications can help avoid misunderstandings that may lead to increased costs.
Are There Pricing Nuances for International Buyers?
International buyers must navigate additional complexities in pricing:
-
Currency Fluctuations: Exchange rates can impact costs, so locking in prices at the time of order can mitigate risks.
-
Tariffs and Duties: Be aware of any import tariffs or duties that may apply when sourcing PDUs from different countries.
-
Shipping Times and Costs: Longer shipping times can lead to increased costs, so consider suppliers who can offer competitive shipping options.
Disclaimer on Indicative Prices
It’s important to note that the prices for PDUs can vary widely based on the aforementioned factors. Therefore, while indicative pricing can provide a baseline, actual costs may differ based on specific requirements and market conditions. Always conduct thorough market research and supplier negotiations to ensure the best possible pricing.
Alternatives Analysis: Comparing pdu manufacturer With Other Solutions
In the dynamic landscape of power distribution solutions, B2B buyers often face a myriad of options when selecting the right equipment for their operations. Understanding the alternatives to the traditional PDU (Power Distribution Unit) can provide valuable insights that enable informed decision-making. This section will explore two viable alternatives to PDUs, comparing them across various dimensions critical for international buyers, particularly in Africa, South America, the Middle East, and Europe.
Comparison Table of Power Distribution Solutions
Comparison Aspect | PDU Manufacturer | Alternative 1: Smart Power Strips | Alternative 2: Power Management Software |
---|---|---|---|
Performance | High efficiency; stable power | Moderate efficiency; limited load capacity | Variable; relies on existing hardware |
Cost | Medium to high initial cost | Low initial cost | Subscription or licensing fees |
Ease of Implementation | Moderate; requires installation | Easy; plug-and-play setup | Complex; needs integration with systems |
Maintenance | Requires periodic checks | Minimal maintenance | Requires updates and monitoring |
Best Use Case | Data centers and critical infrastructure | Home offices and small businesses | Large organizations needing detailed power analytics |
What Are the Benefits and Drawbacks of Smart Power Strips?
Smart power strips are an appealing alternative for businesses seeking cost-effective solutions. These devices allow users to plug multiple appliances into a single outlet, often featuring energy monitoring capabilities. Their low initial cost makes them accessible for small enterprises or remote workers. However, they typically offer moderate efficiency and limited load capacity, making them unsuitable for high-demand environments like data centers.
How Does Power Management Software Compare?
Power management software provides an innovative approach to energy distribution by monitoring and managing power usage across devices. This solution can be particularly beneficial for large organizations that require detailed analytics to optimize energy consumption. While it allows for significant flexibility and control, its complexity can pose challenges during implementation and integration with existing hardware. Additionally, it often incurs ongoing subscription or licensing fees, which can accumulate over time.
Conclusion: How Can B2B Buyers Choose the Right Power Distribution Solution?
When selecting a power distribution solution, B2B buyers must consider their specific operational needs, budget constraints, and the scale of their operations. For those managing critical infrastructure, investing in a PDU manufacturer may be necessary to ensure reliability and efficiency. Alternatively, small to medium-sized businesses may find smart power strips sufficient for their requirements. For larger enterprises, power management software could offer the detailed insights needed to enhance energy efficiency. Ultimately, the decision should align with both immediate operational demands and long-term energy management goals.
Essential Technical Properties and Trade Terminology for pdu manufacturer
What Are the Key Technical Properties of PDUs for B2B Buyers?
When selecting a Power Distribution Unit (PDU), international B2B buyers must consider various technical properties that directly impact performance, reliability, and suitability for specific applications. Here are some critical specifications to keep in mind:
-
Material Grade
The material used in PDUs is crucial for durability and thermal management. Common materials include aluminum and steel, which provide strength and conductivity. High-grade materials can withstand environmental stresses, making them ideal for data centers and industrial applications. For buyers in regions like Africa and South America, understanding local environmental conditions can guide material selection. -
Load Capacity
Load capacity, typically measured in kilowatts (kW), indicates how much power the PDU can distribute. It’s essential to match the PDU’s load capacity with the total power requirements of connected devices. Overloading a PDU can lead to failures and safety hazards, making this specification vital for decision-makers in sectors such as IT and telecommunications. -
Input Voltage and Frequency
Different regions operate on varying voltage and frequency standards (e.g., 220V/50Hz in Europe vs. 120V/60Hz in North America). Selecting a PDU compatible with local electrical standards is essential to ensure optimal performance and compliance with regulations. Buyers should consult local electrical codes and standards to avoid costly mistakes. -
Tolerance Levels
Tolerance levels refer to the allowable variation in the PDU’s specifications, such as voltage and current. Understanding these tolerances helps buyers assess the reliability and safety of the PDU in real-world applications. A tighter tolerance level often indicates a higher quality product, which is crucial for sensitive equipment in data centers. -
Cooling Features
PDUs equipped with advanced cooling features, such as temperature monitoring and fan integration, are essential for maintaining optimal operating conditions. These features help prevent overheating, particularly in high-density environments. Buyers should consider cooling capabilities, especially in warmer climates or high-traffic data centers. -
Smart Monitoring Capabilities
Modern PDUs often come with smart monitoring features that allow remote access to power usage data, alarms, and alerts. These capabilities enhance operational efficiency and provide insights into energy consumption, which can lead to cost savings. For businesses in Europe and the Middle East focusing on sustainability, these features align with energy management goals.
What Are Common Trade Terms Used in the PDU Manufacturing Industry?
Understanding industry jargon is vital for B2B buyers to navigate procurement processes effectively. Here are some common terms:
-
OEM (Original Equipment Manufacturer)
OEMs are companies that produce parts or equipment that may be marketed by another manufacturer. In the PDU industry, collaborating with OEMs can offer buyers customized solutions tailored to their specific needs. -
MOQ (Minimum Order Quantity)
MOQ refers to the smallest quantity of a product that a supplier is willing to sell. Knowing the MOQ helps buyers plan their budgets and inventory levels accordingly, especially when dealing with manufacturers in different regions. -
RFQ (Request for Quotation)
An RFQ is a document used to solicit price proposals from suppliers. For B2B buyers, submitting an RFQ can clarify pricing structures and lead times, facilitating better negotiation strategies. -
Incoterms (International Commercial Terms)
Incoterms define the responsibilities of buyers and sellers in international transactions, including shipping costs and risk management. Familiarity with these terms is crucial for buyers in Africa and South America, where logistics can be complex. -
Lead Time
Lead time is the amount of time it takes from placing an order to receiving the product. Understanding lead times helps businesses plan their operations and avoid disruptions, particularly in industries with tight deadlines. -
Certification Standards
Certification standards, such as CE, UL, or ISO, indicate that a product meets specific safety and quality requirements. Buyers should prioritize PDUs with relevant certifications to ensure compliance with local regulations and enhance product reliability.
By understanding these technical properties and trade terms, B2B buyers can make informed decisions when selecting PDUs, ensuring they meet their operational needs while also complying with regional standards.
Navigating Market Dynamics and Sourcing Trends in the pdu manufacturer Sector
What Are the Current Market Dynamics and Key Trends in the PDU Manufacturer Sector?
The global market for Power Distribution Units (PDUs) is witnessing significant growth, driven by the increasing demand for efficient power management solutions across various industries. As businesses expand and data centers proliferate, the need for reliable and scalable power distribution systems becomes paramount. For international B2B buyers, especially those in Africa, South America, the Middle East, and Europe (such as Spain and Germany), understanding these dynamics is critical for effective sourcing.
One of the key trends is the shift towards intelligent PDUs that incorporate monitoring and management capabilities. These devices allow users to track power consumption in real time, enabling better energy management and reducing operational costs. Additionally, the rise of the Internet of Things (IoT) is facilitating remote management and predictive maintenance, which are essential for minimizing downtime and enhancing operational efficiency.
Moreover, sustainability is gaining traction as businesses seek to reduce their carbon footprints. Buyers are increasingly looking for PDUs that are energy-efficient and made from sustainable materials. This trend aligns with global initiatives aimed at promoting renewable energy and reducing environmental impact.
How Is Sustainability and Ethical Sourcing Impacting the PDU Manufacturer Sector?
Sustainability and ethical sourcing are becoming central to procurement strategies in the PDU manufacturing sector. The environmental impact of manufacturing processes, including energy consumption and waste generation, has prompted buyers to consider the sustainability credentials of their suppliers. This shift is particularly relevant for international B2B buyers who are under pressure to meet regulatory requirements and consumer expectations for sustainable practices.
Buyers should prioritize manufacturers that hold recognized ‘green’ certifications, such as Energy Star or ISO 14001, which demonstrate a commitment to environmental management. Additionally, the use of recyclable materials in PDU production is becoming a standard expectation. By opting for suppliers that implement sustainable practices, companies can not only enhance their corporate social responsibility but also improve their brand reputation in increasingly eco-conscious markets.
Ethical supply chains are also crucial, as they ensure compliance with labor standards and fair trade practices. Buyers should investigate the sourcing of raw materials and the conditions under which products are manufactured. This diligence not only mitigates risks associated with unethical practices but also fosters long-term partnerships built on trust and shared values.
What Is the Brief Evolution of the PDU Sector?
The evolution of Power Distribution Units can be traced back to the early days of electricity distribution, where the need for safe and efficient power management solutions emerged. Initially, PDUs were simple devices designed to distribute power to various electrical components within a system. However, as technology advanced, the demand for more sophisticated systems grew.
In recent years, the integration of smart technologies has revolutionized the PDU landscape. Modern PDUs now feature advanced monitoring capabilities, allowing users to track and manage energy consumption more effectively. This evolution reflects broader trends in the B2B sector, where digital transformation is reshaping how businesses operate and manage resources.
As the market continues to evolve, international buyers must stay informed about these changes to make strategic purchasing decisions that align with their operational needs and sustainability goals.
Frequently Asked Questions (FAQs) for B2B Buyers of pdu manufacturer
-
How do I choose the right PDU manufacturer for my business needs?
When selecting a PDU manufacturer, consider factors such as product quality, compliance with international standards, and customer reviews. Look for manufacturers with a proven track record in your industry and those who offer customized solutions tailored to your specific requirements. Evaluate their ability to meet your volume needs and lead times, especially if you are sourcing from regions like Africa or South America where logistics can be challenging. -
What are the key features to look for in a PDU?
Key features to consider include the type of input and output connections, load capacity, monitoring capabilities, and protection features such as surge protection and overload alarms. Additionally, assess whether the PDU can be integrated into existing systems and if it supports remote management. This is crucial for businesses in the Middle East and Europe where efficient power management is vital for operations. -
What are the typical minimum order quantities (MOQ) for PDUs?
Minimum order quantities can vary significantly among manufacturers. Some may require orders of 100 units or more, while others might offer flexibility for smaller quantities. It’s essential to communicate your needs upfront and explore manufacturers that can accommodate your requirements, especially if you are a smaller business or a startup in regions like South America or Africa. -
How do I ensure the quality of PDUs from international suppliers?
To ensure quality, request certifications such as ISO 9001 and compliance with safety standards relevant to your market. Additionally, ask for product samples before committing to a larger order. Conducting factory audits or utilizing third-party inspection services can further validate the manufacturing processes and quality control measures in place, which is particularly important when sourcing from overseas. -
What payment terms should I expect when sourcing PDUs internationally?
Payment terms can vary widely depending on the manufacturer and the relationship established. Common arrangements include upfront payment, partial deposits, or payment upon delivery. It’s advisable to negotiate terms that balance risk and cash flow, especially when dealing with suppliers in different regions. Utilizing secure payment methods such as letters of credit can also mitigate financial risks. -
How can I efficiently manage logistics and shipping when importing PDUs?
Efficient logistics management involves selecting a reliable freight forwarder who understands the regulations and challenges of your destination country. Be aware of customs duties and ensure all shipping documentation is accurate to avoid delays. Consider using Incoterms to clarify responsibilities for shipping, delivery, and risk during transport, especially important for buyers in Africa and the Middle East. -
What customization options are available for PDUs?
Many manufacturers offer customization options such as specific configurations, colors, and additional features like remote monitoring or smart technology integration. Discuss your specific requirements with potential suppliers to understand the extent of customization they can provide. This is particularly beneficial for businesses in Europe seeking to align products with their branding or operational needs. -
What are common pitfalls to avoid when sourcing PDUs internationally?
Common pitfalls include failing to conduct thorough research on the manufacturer, not clarifying technical specifications, and neglecting to understand local regulations. Additionally, overlooking the importance of after-sales support and warranty terms can lead to complications. Always ensure clear communication regarding expectations and maintain a robust contract that outlines all aspects of the transaction to prevent misunderstandings.
Important Disclaimer & Terms of Use
⚠️ Important Disclaimer
The information provided in this guide, including content regarding manufacturers, technical specifications, and market analysis, is for informational and educational purposes only. It does not constitute professional procurement advice, financial advice, or legal advice.
While we have made every effort to ensure the accuracy and timeliness of the information, we are not responsible for any errors, omissions, or outdated information. Market conditions, company details, and technical standards are subject to change.
B2B buyers must conduct their own independent and thorough due diligence before making any purchasing decisions. This includes contacting suppliers directly, verifying certifications, requesting samples, and seeking professional consultation. The risk of relying on any information in this guide is borne solely by the reader.
Strategic Sourcing Conclusion and Outlook for pdu manufacturer
What Are the Key Takeaways for International B2B Buyers in PDU Manufacturing?
In the competitive landscape of PDU manufacturing, strategic sourcing emerges as a crucial element for international B2B buyers aiming to optimize operational efficiency and cost-effectiveness. By focusing on suppliers that offer innovative solutions tailored to specific industry needs, buyers can enhance their power distribution capabilities while ensuring reliability and scalability. It’s essential to evaluate vendors not just on price but also on their technological advancements, service support, and ability to adapt to evolving market demands.
How Can Strategic Sourcing Shape the Future of Your PDU Procurement?
As we look ahead, the role of smart PDUs with integrated monitoring and management capabilities will only grow in importance. Buyers from Africa, South America, the Middle East, and Europe, particularly in countries like Spain and Germany, should prioritize partnerships with manufacturers who emphasize sustainability and energy efficiency. This forward-thinking approach not only aligns with global trends but also positions businesses to leverage advancements in power management technology.
What Should International Buyers Do Next?
In conclusion, international B2B buyers are encouraged to adopt a proactive stance in their sourcing strategies. Engage with reputable PDU manufacturers who understand the unique challenges of your market and can provide customized solutions. Start exploring partnerships today to ensure your business is well-equipped for future challenges and opportunities in power distribution.