Discover Top Strainer Manufacturers: The Ultimate Buying Guide (2025)
Introduction: Navigating the Global Market for strainer manufacturer
Navigating the global market for strainer manufacturers can be a daunting task, particularly for international B2B buyers seeking reliable suppliers. With the increasing complexity of sourcing quality strainers that meet specific industry standards, it is crucial to have a comprehensive understanding of the market landscape. This guide serves as an invaluable resource, offering insights into various types of strainers, their applications across different sectors, and the nuances of supplier vetting.
By exploring factors such as material quality, design specifications, and compliance with international regulations, buyers will gain the tools necessary to make informed purchasing decisions. Furthermore, the guide provides practical strategies for assessing supplier reliability and evaluating costs, allowing buyers from regions like Africa, South America, the Middle East, and Europe—including countries like Mexico and Vietnam—to optimize their procurement processes.
Ultimately, this guide aims to empower B2B buyers to navigate the strainer manufacturing landscape confidently, ensuring they can secure the best products tailored to their operational needs. Whether you’re looking to enhance efficiency in manufacturing, improve water treatment processes, or ensure compliance in food and beverage production, understanding the strainer market is essential for successful operations.
Understanding strainer manufacturer Types and Variations
Type Name | Key Distinguishing Features | Primary B2B Applications | Brief Pros & Cons for Buyers |
---|---|---|---|
Y-Strainers | Compact design, typically installed in horizontal pipelines | Water treatment, HVAC, chemical processing | Pros: Space-efficient, easy to clean. Cons: Limited to low-pressure applications. |
Basket Strainers | Larger capacity, removable basket for easy cleaning | Oil & gas, petrochemical industries | Pros: High dirt-holding capacity. Cons: Requires more space and maintenance. |
T-Strainers | T-shaped configuration, ideal for low-flow applications | Food processing, pharmaceuticals | Pros: Effective for low flow rates. Cons: Not suitable for high-pressure systems. |
Duplex Strainers | Two parallel strainers for continuous operation | Marine applications, power plants | Pros: Minimal downtime during maintenance. Cons: Higher initial cost. |
Permanent Strainers | Fixed mesh or perforated plate, designed for specific applications | Mining, wastewater treatment | Pros: Low maintenance, durable. Cons: Limited cleaning options, may clog over time. |
What Are Y-Strainers and Their B2B Relevance?
Y-strainers are compact devices often used in horizontal pipelines to filter out debris from liquids. Their design allows for easy cleaning, making them suitable for applications in water treatment, HVAC systems, and chemical processing. When purchasing Y-strainers, buyers should consider the size, mesh type, and pressure ratings to ensure compatibility with their systems. Their space-efficient design is a significant advantage, although they are limited to low-pressure applications.
How Do Basket Strainers Benefit Industrial Applications?
Basket strainers feature a larger capacity and are designed with a removable basket for straightforward cleaning. Commonly found in the oil and gas sector, as well as petrochemical industries, these strainers are ideal for processes requiring higher dirt-holding capacities. B2B buyers should evaluate the installation space and maintenance requirements, as basket strainers demand more room and regular upkeep compared to other types. Their ability to handle larger volumes of debris makes them a preferred choice for many industrial applications.
What Makes T-Strainers Ideal for Specific Industries?
T-strainers are characterized by their T-shaped configuration and are particularly effective in low-flow applications. They are commonly used in food processing and pharmaceutical industries, where maintaining product purity is crucial. Buyers should pay attention to the flow rate and pressure compatibility when selecting T-strainers. While they are effective in their niche, their performance diminishes under high-pressure conditions, making it essential for B2B purchasers to assess their specific operational needs.
Why Choose Duplex Strainers for Continuous Operations?
Duplex strainers consist of two parallel strainers, allowing for uninterrupted operation during maintenance. They are widely utilized in marine applications and power plants, where continuous flow is critical. B2B buyers should consider the higher initial investment against the long-term benefits of reduced downtime. While duplex strainers may come at a premium, their efficiency in maintaining operational continuity makes them a valuable asset in demanding environments.
What Are the Advantages of Permanent Strainers in Industrial Settings?
Permanent strainers are designed with fixed mesh or perforated plates tailored for specific applications, often seen in mining and wastewater treatment. Their low maintenance requirements and durable construction are significant advantages for businesses looking for long-lasting solutions. However, buyers must be aware that these strainers can become clogged over time and may have limited options for cleaning. Thus, understanding the operational environment and potential debris types is crucial for effective purchasing decisions.
Related Video: Brass Y Strainer
Key Industrial Applications of strainer manufacturer
Industry/Sector | Specific Application of strainer manufacturer | Value/Benefit for the Business | Key Sourcing Considerations for this Application |
---|---|---|---|
Oil & Gas | Filtration in pipeline systems to remove debris and contaminants | Enhances equipment longevity and operational efficiency | Consider the strainer material compatibility with various fluids and the size of particulates to be filtered. |
Water Treatment | Removal of sediment and debris in water purification systems | Improves water quality and reduces maintenance costs | Assess the strainer’s flow rate and pressure drop characteristics for optimal performance. |
Food and Beverage | Filtration in processing lines to ensure product purity | Ensures compliance with health regulations and quality standards | Evaluate hygiene certifications and materials used to avoid contamination. |
Chemical Manufacturing | Protection of pumps and valves from solid particles | Minimizes downtime and repair costs | Focus on strainers that can handle corrosive materials and varying temperatures. |
HVAC Systems | Filtration of air and fluid systems to maintain efficiency | Enhances system performance and energy efficiency | Investigate the strainer size and maintenance requirements for ease of use. |
How Are Strainers Used in the Oil & Gas Industry?
In the oil and gas sector, strainers are critical for filtering out debris and contaminants from pipeline systems. They prevent particles from damaging pumps, valves, and other equipment, which can lead to costly repairs and downtime. International buyers, especially from regions like Africa and the Middle East, should ensure that the strainers are compatible with various fluid types and can handle specific particulate sizes relevant to their operations.
What Role Do Strainers Play in Water Treatment?
Strainers are essential in water treatment facilities, where they remove sediment and debris to ensure the purification of water. This process significantly improves water quality and reduces the frequency of maintenance interventions. B2B buyers from South America and Europe must consider the strainer’s flow rate and pressure drop to maintain optimal system performance, especially in high-demand situations.
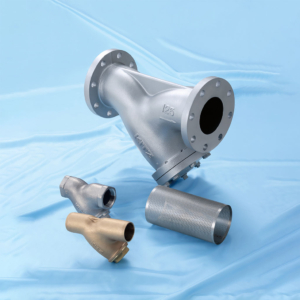
A stock image related to strainer manufacturer.
Why Are Strainers Important in the Food and Beverage Sector?
In the food and beverage industry, strainers are vital for maintaining product purity during processing. They help ensure compliance with health regulations and quality standards by filtering out contaminants. Buyers in this sector should prioritize strainers with appropriate hygiene certifications and materials that prevent contamination, particularly when sourcing from international manufacturers.
How Do Strainers Benefit Chemical Manufacturing?
Strainers in chemical manufacturing protect critical components like pumps and valves from solid particles, which can lead to operational inefficiencies. By minimizing downtime and repair costs, they contribute to overall productivity. Buyers should focus on strainers that can withstand corrosive materials and varying temperatures, ensuring they meet the specific requirements of their chemical processes.
How Do Strainers Enhance HVAC System Performance?
In HVAC systems, strainers filter both air and fluid, ensuring that systems operate efficiently. This filtration process not only improves performance but also enhances energy efficiency, leading to cost savings. Buyers should investigate the size and maintenance requirements of strainers to ensure easy integration and upkeep within their HVAC systems, particularly in international markets where service availability may vary.
Related Video: Basket Strainer Explained
3 Common User Pain Points for ‘strainer manufacturer’ & Their Solutions
Scenario 1: Inconsistent Strainer Performance Leading to System Downtime
The Problem: B2B buyers often face issues with strainers that do not perform consistently, leading to unexpected system downtime. This inconsistency can stem from a variety of factors, including inadequate filtration capabilities, poor material selection, or incorrect sizing. For manufacturers in sectors such as oil and gas, water treatment, and food processing, these disruptions can result in costly halts in production, damaged equipment, and even safety risks for employees.
The Solution: To mitigate these risks, it’s essential to conduct a thorough needs assessment before selecting a strainer manufacturer. Start by evaluating the specific requirements of your application, including flow rates, pressure drops, and the type of contaminants that need to be filtered. Collaborate closely with potential manufacturers to ensure they provide strainers made from appropriate materials for your environment, whether that’s corrosion-resistant stainless steel or durable plastic. Request performance data and case studies that demonstrate the strainer’s reliability in conditions similar to yours. Moreover, consider implementing a regular maintenance schedule and establish a relationship with the manufacturer for ongoing support and troubleshooting.
Scenario 2: Difficulty in Sourcing the Right Strainer Size and Type
The Problem: Many B2B buyers struggle to identify the correct size and type of strainer for their systems, which can lead to inefficiencies and increased operational costs. Choosing a strainer that is either too small or too large can affect fluid dynamics, leading to inadequate filtration or excessive pressure drops, both of which compromise system efficiency.
The Solution: To address sizing issues, buyers should utilize detailed technical specifications and consult with engineers during the selection process. Start by gathering essential data, such as pipeline dimensions, flow rates, and fluid characteristics. Engage with strainer manufacturers who offer customized solutions and can assist in the engineering process. Consider utilizing software tools or online calculators provided by manufacturers to help determine the optimal strainer size based on your specific application parameters. Additionally, request prototype testing or pilot installations to validate your choice before making a bulk purchase.
Scenario 3: Lack of After-Sales Support and Technical Assistance
The Problem: After purchasing strainers, many B2B buyers find themselves lacking adequate after-sales support and technical assistance. This can be particularly challenging when issues arise during installation or operation, leading to frustration and wasted resources. Buyers may feel abandoned by manufacturers who do not provide sufficient guidance, leaving them to troubleshoot problems on their own.
The Solution: When evaluating strainer manufacturers, prioritize those who offer robust after-sales support and technical resources. Look for manufacturers that provide comprehensive installation manuals, troubleshooting guides, and access to a dedicated customer service team. It can be beneficial to establish a partnership with a manufacturer that offers training sessions for your maintenance staff, ensuring they are well-equipped to handle any issues that may arise. Additionally, inquire about warranty options and service agreements that include periodic check-ups or on-site support. Building a long-term relationship with a responsive manufacturer can significantly enhance operational efficiency and minimize downtime.
By addressing these common pain points with tailored solutions, international B2B buyers can enhance their procurement processes, ensuring they select the right strainers for their unique applications and receive the necessary support to maintain optimal performance.
Strategic Material Selection Guide for strainer manufacturer
When selecting materials for strainers, manufacturers must consider various factors that influence performance, durability, and cost. This guide analyzes four common materials used in strainer manufacturing, providing insights that are particularly relevant for international B2B buyers from Africa, South America, the Middle East, and Europe.
What Are the Key Properties of Stainless Steel in Strainer Manufacturing?
Stainless steel is a popular choice for strainer manufacturers due to its excellent corrosion resistance and high-temperature tolerance. Typically, grades like 304 and 316 are used, with 316 offering superior resistance to chlorides and acidic environments. The pressure rating of stainless steel strainers can reach up to 1500 psi, making them suitable for high-pressure applications.
Pros: Stainless steel is durable and can withstand harsh environments, making it ideal for industries such as oil and gas, food processing, and pharmaceuticals. Its aesthetic appeal also allows for use in visible applications.
Cons: The primary drawback is its cost, which can be significantly higher than other materials. Additionally, stainless steel can be challenging to machine, leading to increased manufacturing complexity.
Impact on Application: Stainless steel strainers are compatible with a wide range of media, including water, oil, and chemicals, making them versatile across various sectors.
Considerations for International Buyers: Buyers should ensure compliance with international standards such as ASTM A240 for stainless steel. In regions like Europe, adherence to EN standards is crucial, while buyers in Africa and South America should verify local regulations regarding material certifications.
How Does Carbon Steel Compare for Strainer Applications?
Carbon steel is another common material used in strainer manufacturing, known for its strength and affordability. It typically has a lower corrosion resistance compared to stainless steel, but its properties can be enhanced through coatings or galvanization.
Pros: The primary advantage of carbon steel is its cost-effectiveness, making it suitable for large-scale applications where budget constraints are a concern. It also has a high strength-to-weight ratio.
Cons: The main limitation is its susceptibility to corrosion, which can lead to premature failure in harsh environments. This necessitates additional protective measures, increasing overall costs.
Impact on Application: Carbon steel strainers are best suited for applications involving non-corrosive media, such as water or certain oils, but should be avoided in acidic or saline environments.
Considerations for International Buyers: Buyers should consider compliance with ASTM A106 for carbon steel pipes and fittings. In regions like the Middle East, where high temperatures are common, ensuring proper coating is essential to prevent rust.
What Are the Advantages of Plastic Strainers in B2B Applications?
Plastic materials, such as PVC and polypropylene, are increasingly used in strainer manufacturing, particularly in applications involving corrosive chemicals. These materials offer excellent chemical resistance and are lightweight.
Pros: The main advantage of plastic strainers is their resistance to corrosion and lower weight, which simplifies installation and reduces shipping costs. They are also cost-effective for low-pressure applications.
Cons: However, plastic strainers typically have lower temperature and pressure ratings compared to metal options, limiting their use in high-stress environments.
Impact on Application: Plastic strainers are ideal for applications involving aggressive chemicals, such as in wastewater treatment or chemical processing.
Considerations for International Buyers: Buyers should verify compliance with standards like ASTM D1784 for PVC materials. In Europe, adherence to REACH regulations is vital for chemical safety.
How Does Bronze Perform as a Material for Strainers?
Bronze, particularly when alloyed with tin, is another material used in strainer manufacturing. It offers good corrosion resistance and is often used in marine applications due to its ability to withstand saltwater.
Pros: Bronze strainers are durable and have excellent resistance to corrosion, especially in marine environments. They also have good machinability.
Cons: The primary disadvantage is the higher cost compared to carbon steel and plastic. Additionally, bronze can be prone to dezincification, which can affect performance.
Impact on Application: Bronze strainers are suitable for applications involving seawater or other corrosive environments, making them ideal for marine and coastal industries.
Considerations for International Buyers: Buyers should ensure compliance with ASTM B584 for bronze alloys. In regions like South America, understanding local sourcing and availability is crucial for timely procurement.
Summary Table of Material Selection for Strainer Manufacturers
Material | Typical Use Case for strainer manufacturer | Key Advantage | Key Disadvantage/Limitation | Relative Cost (Low/Med/High) |
---|---|---|---|---|
Stainless Steel | Oil and gas, food processing, pharmaceuticals | Excellent corrosion resistance | Higher cost, complex machining | High |
Carbon Steel | Water and oil applications | Cost-effective, strong | Susceptible to corrosion | Medium |
Plastic | Chemical processing, wastewater treatment | Lightweight, corrosion-resistant | Lower temperature/pressure ratings | Low |
Bronze | Marine applications | Good corrosion resistance | Higher cost, prone to dezincification | Medium |
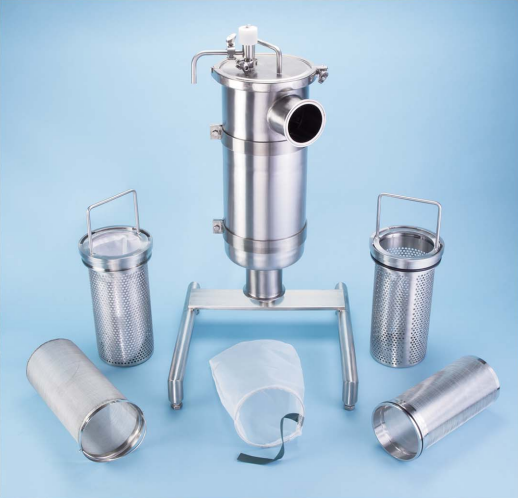
A stock image related to strainer manufacturer.
This guide provides essential insights into material selection for strainers, enabling international B2B buyers to make informed decisions that align with their specific operational needs and regulatory requirements.
In-depth Look: Manufacturing Processes and Quality Assurance for strainer manufacturer
What Are the Key Stages of Manufacturing for Strainers?
The manufacturing process for strainers involves several critical stages that ensure the final product meets industry standards and customer expectations. Understanding these stages is essential for international B2B buyers looking to source high-quality strainers.
1. Material Preparation
The first step in the manufacturing process is material preparation. Strainers are typically made from materials such as stainless steel, carbon steel, and other alloys. The selection of the right material is crucial as it affects the strainer’s durability and resistance to corrosion.
- Material Selection: Buyers should ensure that the supplier uses high-grade materials that comply with international standards. For example, stainless steel grades like 304 or 316 are commonly used for their corrosion resistance.
- Cutting and Shaping: Materials are cut to size using techniques such as laser cutting or water jet cutting. This precision is vital for the next stages of manufacturing.
2. Forming Techniques
Once the materials are prepared, they undergo various forming processes to create the desired shapes.
- Bending and Forming: Techniques like hydraulic bending or stamping are used to form the body of the strainer. This process must ensure that the dimensions are accurate to prevent any operational issues later.
- Welding: For welded strainers, processes such as TIG (Tungsten Inert Gas) welding are employed to join components. The quality of welding is critical, as it affects the structural integrity of the strainer.
3. Assembly of Components
After forming, the next stage is the assembly of various components.
- Component Integration: Strainers typically consist of multiple parts, including the body, filter mesh, and end connections. Each component must be fitted accurately to ensure optimal performance.
- Sealing and Gasketing: Proper sealing techniques are used to prevent leaks. Gaskets made from materials compatible with the fluid being filtered are selected to ensure a tight seal.
4. Finishing Processes
The finishing stage enhances both the aesthetics and functionality of the strainer.
- Surface Treatment: Techniques such as sandblasting, polishing, and coating (e.g., epoxy coating) are applied to improve corrosion resistance and appearance.
- Quality Checks: Before proceeding to quality assurance, strainers undergo initial quality checks to identify any defects resulting from the manufacturing process.
How Is Quality Assurance Implemented in Strainer Manufacturing?
Quality assurance (QA) is a critical aspect of strainer manufacturing, ensuring that products meet both international and industry-specific standards. This is particularly important for B2B buyers from diverse regions, including Africa, South America, the Middle East, and Europe.
Relevant International Standards for Quality Assurance
- ISO 9001: This international standard outlines the criteria for a quality management system. Manufacturers who comply with ISO 9001 demonstrate their commitment to quality and customer satisfaction.
- Industry-Specific Standards: Strainer manufacturers may also comply with standards such as CE marking for products sold in Europe or API (American Petroleum Institute) standards for those used in the oil and gas sector. Buyers should verify compliance with these standards to ensure product reliability.
What Are the Key Quality Control Checkpoints?
Quality control (QC) is integrated throughout the manufacturing process with specific checkpoints to ensure compliance with standards and specifications.
1. Incoming Quality Control (IQC)
- Material Inspection: Incoming materials are inspected for quality and compliance with specifications before they are used in production. This includes checking for the correct material grades and dimensions.
- Supplier Verification: B2B buyers should ensure that suppliers conduct robust IQC processes, as poor-quality materials can lead to product failures.
2. In-Process Quality Control (IPQC)
- Ongoing Inspections: Throughout the manufacturing process, periodic inspections are conducted to monitor for defects or deviations from specifications. This might include dimensional checks and visual inspections.
- Process Control: Utilizing statistical process control (SPC) can help manufacturers maintain quality standards by monitoring production processes in real-time.
3. Final Quality Control (FQC)
- End-of-Line Testing: Once the strainers are assembled, they undergo final inspections, which may include pressure testing, flow testing, and dimensional verification.
- Documentation: Proper documentation of FQC results is essential. B2B buyers should request these reports for verification.
How Can B2B Buyers Verify Supplier Quality Control Practices?
For international B2B buyers, verifying a supplier’s quality control practices is crucial to ensure they are receiving high-quality products.
1. Conducting Audits
- Supplier Audits: Regular audits of potential suppliers can provide insights into their manufacturing processes and quality control systems. Buyers should look for suppliers with a track record of compliance with international standards.
2. Requesting Quality Reports
- Documentation Review: Buyers should request access to quality assurance reports, including IQC, IPQC, and FQC results. This documentation can offer transparency into the supplier’s quality practices.
3. Engaging Third-Party Inspectors
- Independent Inspections: Engaging third-party inspection services can provide an unbiased assessment of the supplier’s quality control processes. This is particularly beneficial for buyers from regions with stringent regulatory requirements.
What Nuances Should International Buyers Be Aware Of?
When sourcing strainers, international buyers must navigate various nuances related to quality control and certifications.
- Regional Compliance: Different regions may have specific compliance requirements. For example, products exported to Europe must meet CE marking requirements, while those in the Middle East may need to comply with local standards.
- Cultural Considerations: Understanding cultural differences in business practices and communication can facilitate smoother negotiations and stronger supplier relationships.
By comprehensively understanding the manufacturing processes and quality assurance mechanisms, international B2B buyers can make informed decisions and ensure they are sourcing high-quality strainers that meet their operational needs.
Practical Sourcing Guide: A Step-by-Step Checklist for ‘strainer manufacturer’
This guide provides a structured approach for B2B buyers looking to source strainer manufacturers. By following these steps, you can ensure that you select the right supplier to meet your operational needs while minimizing risks and maximizing value.
Step 1: Define Your Technical Specifications
Understanding your specific requirements is essential before reaching out to manufacturers. Clearly outline the types of strainers you need, such as basket strainers, Y-strainers, or duplex strainers, along with material specifications (e.g., stainless steel, carbon steel) and dimensions. This clarity will help potential suppliers provide accurate quotes and ensure that the products meet your operational standards.
Step 2: Research Potential Suppliers
Conduct thorough research to identify reputable strainer manufacturers. Utilize online platforms, industry forums, and trade associations to compile a list of candidates. Pay attention to suppliers that have a strong presence in your target markets, such as Africa, South America, the Middle East, and Europe, as they may have tailored solutions for your specific region.
Step 3: Evaluate Supplier Certifications and Compliance
✅ Verify Supplier Certifications
Ensure that the manufacturers you consider have relevant industry certifications, such as ISO 9001 for quality management systems. These certifications indicate a commitment to quality and compliance with industry standards. Additionally, check for any local compliance certifications that may be necessary for your region.
Step 4: Request Samples and Product Specifications
Before making a final decision, request product samples and detailed specifications from shortlisted suppliers. This will allow you to assess the quality of their strainers firsthand. Look for detailed documentation that includes material properties, performance metrics, and installation guidelines to ensure they meet your needs.
Step 5: Assess Manufacturing Capabilities
What Are the Manufacturer’s Production Capabilities?
Understanding a supplier’s manufacturing capabilities is crucial. Evaluate their production capacity, technology, and quality control processes. A manufacturer with advanced machinery and rigorous quality checks is more likely to deliver consistent products that meet your specifications.
Step 6: Review Pricing and Payment Terms
Once you have narrowed down your options, request quotes from multiple suppliers. Compare not only the pricing but also the payment terms, including any discounts for bulk orders or early payments. This will help you determine the overall cost-effectiveness of each option and ensure that you stay within budget.
Step 7: Check References and Customer Feedback
Before finalizing your decision, reach out to previous clients or read customer reviews regarding the suppliers you are considering. This feedback can provide insights into the manufacturer’s reliability, customer service, and post-sale support. Look for testimonials from companies within your industry or region for more relevant feedback.
By following this checklist, you can streamline your sourcing process for strainer manufacturers and make informed decisions that align with your business goals.
Comprehensive Cost and Pricing Analysis for strainer manufacturer Sourcing
What Are the Key Cost Components in Strainer Manufacturing?
Understanding the cost structure of strainer manufacturing is essential for international B2B buyers. The main cost components include:
-
Materials: The choice of materials significantly influences the overall cost. Common materials used in strainers include stainless steel, plastic, and bronze. Each material has its own cost implications based on market demand and availability.
-
Labor: Labor costs vary based on the region and the skill level of workers. Countries with lower labor costs, such as those in parts of Africa and South America, can offer competitive pricing but may have varying levels of expertise.
-
Manufacturing Overhead: This includes costs associated with running the manufacturing facility, such as utilities, equipment maintenance, and administrative expenses. Efficient overhead management can help lower prices.
-
Tooling: Tooling costs relate to the equipment and machinery required to manufacture strainers. Custom tooling can increase initial costs but may yield savings in the long run through increased production efficiency.
-
Quality Control (QC): Investing in quality control processes ensures that the strainers meet industry standards, which can prevent costly returns and replacements. However, rigorous QC measures can also add to the manufacturing cost.
-
Logistics: Shipping and handling costs are crucial, especially for international buyers. Factors such as distance, shipping mode, and customs duties can significantly affect total logistics costs.
-
Margin: The supplier’s profit margin is another factor influencing pricing. Understanding how margins are set can provide insights into potential negotiation points.
How Do Price Influencers Impact Strainer Sourcing?
Several factors can influence the final pricing of strainers:
-
Volume and Minimum Order Quantity (MOQ): Larger orders typically result in lower per-unit costs due to economies of scale. Buyers should consider their needs carefully to negotiate favorable terms.
-
Specifications and Customization: Customized strainers tailored to specific applications can lead to higher costs. Buyers should be clear about their requirements to avoid unexpected expenses.
-
Material Quality and Certifications: Strainers that meet specific industry certifications (e.g., ISO, CE) often come at a premium. Buyers should assess whether the certification is necessary for their application.
-
Supplier Factors: The reliability and reputation of the supplier can affect pricing. Established suppliers may charge more for their proven quality and service.
-
Incoterms: Understanding Incoterms (International Commercial Terms) is essential for determining who bears the shipping costs and risks. This can have a significant impact on the total landed cost of the product.
What Buyer Tips Can Help Optimize Strainer Sourcing Costs?
B2B buyers can utilize several strategies to enhance their sourcing process:
-
Negotiation Strategies: Be prepared to negotiate on price, especially if ordering in bulk. Understanding the supplier’s cost structure can provide leverage during discussions.
-
Focus on Total Cost of Ownership (TCO): Instead of just looking at the initial purchase price, consider the total cost of ownership, which includes maintenance, operational costs, and potential downtime.
-
Understand Pricing Nuances for International Buyers: Currency fluctuations, import tariffs, and local taxes can all impact the final cost. Buyers from Africa, South America, the Middle East, and Europe should be aware of these factors when budgeting.
-
Evaluate Multiple Suppliers: Conducting a comparative analysis of different suppliers can reveal better pricing options. This also allows buyers to assess the quality and reliability of various manufacturers.
- Stay Informed About Market Trends: Keeping abreast of material costs and supply chain developments can help buyers make informed decisions and time their purchases effectively.
Disclaimer on Indicative Prices
Pricing for strainers can vary widely based on the aforementioned factors. It is advisable for buyers to obtain detailed quotes from multiple suppliers to ascertain accurate and relevant pricing for their specific requirements.
Alternatives Analysis: Comparing strainer manufacturer With Other Solutions
Understanding Alternative Solutions to Strainer Manufacturing
In the industrial sector, strainer manufacturers play a crucial role in ensuring the efficiency and longevity of various systems by filtering out unwanted particles. However, buyers should consider alternative solutions that may better fit their operational needs, budget constraints, or specific applications. This section provides a comparative analysis of strainer manufacturers against other viable solutions, helping international B2B buyers make informed decisions.
Comparison Table of Strainer Manufacturer and Alternatives
Comparison Aspect | Strainer Manufacturer | Alternative 1: Filtration Systems | Alternative 2: Cyclone Separators |
---|---|---|---|
Performance | High efficiency in removing particulates | Varies by filter type; generally effective | Good for larger particles; less effective for fine particulates |
Cost | Moderate to high initial investment | Varies widely; can be cost-effective | Generally lower cost with lower maintenance |
Ease of Implementation | Requires specialized installation | Usually straightforward; can be DIY | Simple installation; minimal training needed |
Maintenance | Regular cleaning and replacement needed | Filter replacement needed; maintenance varies | Low maintenance; periodic cleaning required |
Best Use Case | Ideal for liquid applications with small particles | Versatile; suitable for gases and liquids | Best for bulk material separation in heavy industries |
Detailed Breakdown of Alternatives
What are Filtration Systems and How Do They Compare?
Filtration systems encompass a broad range of technologies designed to remove contaminants from liquids and gases. They can include cartridge filters, bag filters, and membrane filters, among others. The performance of these systems can vary significantly based on the type of filter used. While they are typically more versatile than strainers, they can also be more expensive over time due to the need for regular filter replacements. Filtration systems are particularly well-suited for applications requiring high levels of purity, such as pharmaceuticals or food and beverage processing.
How Effective are Cyclone Separators in Industrial Applications?
Cyclone separators offer a different approach to particulate removal, utilizing centrifugal force to separate particles from the gas or liquid stream. They are particularly effective for larger particles and bulk materials, making them a common choice in industries such as mining and agriculture. Their lower initial cost and minimal maintenance requirements are appealing, but they are less effective for fine particulates compared to strainers. Cyclone separators are best utilized in scenarios where the primary concern is the removal of larger debris, rather than achieving high levels of filtration.
How to Choose the Right Solution for Your Needs?
When deciding between a strainer manufacturer and alternative solutions, international B2B buyers should carefully assess their specific operational requirements, including the nature of the materials being processed, budget constraints, and maintenance capabilities. Consideration of factors such as performance efficiency, cost-effectiveness, and ease of implementation will be crucial. Additionally, analyzing the long-term implications of maintenance and operational downtime will help in selecting the most suitable solution. Ultimately, the right choice will align with both immediate needs and future growth objectives.
Essential Technical Properties and Trade Terminology for strainer manufacturer
What Are the Essential Technical Properties of Strainers?
When sourcing strainers, understanding the technical properties is crucial for ensuring product performance and reliability in various industrial applications. Below are key specifications that international B2B buyers should consider:
-
Material Grade
The material used in strainers significantly affects their durability and corrosion resistance. Common materials include stainless steel (e.g., 304, 316 grades) and carbon steel. For buyers in sectors such as oil and gas or water treatment, selecting the appropriate material grade is essential to withstand harsh environments and prevent premature failure. -
Filtration Rating
This specification indicates the size of particles that the strainer can effectively filter out. Ratings can range from microns to millimeters, depending on the application. Knowing the filtration requirements helps buyers select a strainer that meets their operational needs without compromising flow rates or efficiency. -
Pressure Drop
Pressure drop refers to the loss of pressure as fluid passes through the strainer. A low pressure drop is preferable, as it ensures efficient operation and minimizes energy costs. Buyers should assess the pressure drop specifications to ensure that the strainer will not hinder system performance. -
Tolerance Levels
Tolerances indicate the acceptable limits of deviation from specified dimensions. Strainers with tight tolerances ensure proper fit and function within piping systems. This is especially critical for OEMs (Original Equipment Manufacturers) who require precise components for their machinery. -
Connection Type
Strainers can feature various connection types, including threaded, flanged, or welded. The choice of connection type should align with existing piping systems to facilitate installation and maintenance. Buyers must consider compatibility to avoid costly modifications. -
Temperature Rating
This specification indicates the maximum and minimum temperatures that a strainer can withstand. Different industries have varying temperature requirements, and understanding these ratings is vital for operational safety and efficiency.
What Are Common Trade Terms Used in the Strainer Manufacturing Industry?
Familiarity with industry jargon can streamline communication and negotiation processes. Below are common terms that B2B buyers should know:
-
OEM (Original Equipment Manufacturer)
An OEM refers to a company that produces components that are used in another company’s products. Buyers should consider sourcing strainers from reputable OEMs to ensure quality and compatibility with their systems. -
MOQ (Minimum Order Quantity)
MOQ is the smallest number of units a supplier is willing to sell. Understanding MOQ is critical for buyers, particularly for small or medium-sized enterprises that may have limited budgets and storage capacity. -
RFQ (Request for Quotation)
An RFQ is a document sent to suppliers to request pricing and terms for specific products. International buyers can utilize RFQs to obtain competitive pricing and ensure they are making informed purchasing decisions. -
Incoterms (International Commercial Terms)
These are standardized terms that define the responsibilities of buyers and sellers in international transactions. Familiarity with Incoterms helps buyers understand shipping costs, risk transfer, and customs responsibilities, facilitating smoother import processes. -
Lead Time
This term refers to the time it takes for a supplier to fulfill an order, from the moment it is placed until it is delivered. Knowing the lead time is essential for buyers to plan their inventory and production schedules effectively. -
Certification Standards
Certifications such as ISO (International Organization for Standardization) or API (American Petroleum Institute) indicate that a product meets specific quality and safety standards. Buyers should look for these certifications to ensure that the strainers comply with industry regulations and best practices.
By grasping these technical properties and trade terms, B2B buyers can make more informed purchasing decisions, ultimately enhancing operational efficiency and reducing costs.
Navigating Market Dynamics and Sourcing Trends in the strainer manufacturer Sector
What Are the Current Market Dynamics and Sourcing Trends in the Strainer Manufacturer Sector?
The strainer manufacturing sector is experiencing significant growth driven by various global factors, including increased industrialization, a focus on water and wastewater management, and stringent regulations regarding fluid management. The rise in infrastructure projects across Africa, South America, and the Middle East is creating a surge in demand for strainers in industries such as oil and gas, pharmaceuticals, and food processing. Additionally, technological advancements such as automation and the Internet of Things (IoT) are reshaping sourcing strategies, enabling manufacturers to improve efficiency and reduce operational costs.
Emerging B2B tech trends like predictive analytics and data-driven decision-making are also influencing how international buyers approach sourcing. For instance, companies are leveraging analytics to forecast demand, manage inventory, and optimize supply chains. In regions like Europe, the emphasis on digital transformation is pushing strainer manufacturers to adopt smart manufacturing practices, which not only enhance product quality but also offer real-time monitoring capabilities.
International B2B buyers should also be aware of the increasing competition among manufacturers. This has led to a trend where suppliers are offering customized solutions to meet specific industry needs, enhancing their value proposition. Thus, establishing strong relationships with manufacturers who prioritize innovation and customer-centricity is essential for buyers looking to secure a competitive edge.
How Does Sustainability and Ethical Sourcing Impact the Strainer Manufacturer Sector?
Sustainability is becoming a pivotal concern in the strainer manufacturing industry, with international buyers increasingly prioritizing environmentally-friendly practices. The environmental impact of manufacturing processes, including energy consumption and waste generation, has led to a demand for sustainable materials and practices. Strainer manufacturers are now focusing on eco-friendly materials, such as recycled metals and biodegradable components, to minimize their carbon footprint.
Moreover, ethical sourcing is essential for building a responsible supply chain. Buyers should seek manufacturers who adhere to ethical labor practices and sustainability certifications, such as ISO 14001 for environmental management and ISO 45001 for occupational health and safety. These certifications not only reflect a commitment to sustainable practices but also enhance brand reputation in an increasingly eco-conscious market.
By choosing suppliers with a strong sustainability ethos, international B2B buyers can contribute to a circular economy while ensuring compliance with international regulations and standards. This strategic approach not only mitigates risk but also aligns with the growing consumer demand for environmentally responsible products.
What Is the Brief Evolution of the Strainer Manufacturing Sector?
The evolution of the strainer manufacturing sector can be traced back to the industrial revolution when the need for efficient filtration systems became apparent. Initially, strainers were simple mesh devices used to prevent debris from entering pipelines and machinery. Over the years, advancements in materials science and engineering have led to the development of more sophisticated strainers, including self-cleaning and automated systems.
In recent decades, the focus has shifted towards enhancing the functionality and efficiency of strainers, with innovations such as multi-barrier systems and smart strainers equipped with sensors for real-time monitoring. This evolution reflects the sector’s response to growing industrial demands and the need for higher operational efficiency, thereby setting the stage for future advancements in filtration technology. International B2B buyers should be aware of these historical trends as they seek suppliers who are not only established but also innovative and adaptable to changing market needs.
Frequently Asked Questions (FAQs) for B2B Buyers of strainer manufacturer
- How do I solve the issue of finding a reliable strainer manufacturer?
To find a reliable strainer manufacturer, start by researching industry certifications and standards such as ISO or ASTM. Utilize platforms like Alibaba or ThomasNet to compare suppliers and read reviews from other buyers. Engage in direct communication to assess responsiveness and willingness to provide documentation, such as quality assurance certificates. Consider visiting trade shows or exhibitions relevant to your industry for face-to-face interactions. Finally, request samples to evaluate product quality before placing larger orders.
-
What is the best type of strainer for industrial applications?
The best type of strainer for industrial applications depends on the specific fluid and the contaminants you need to filter. Basket strainers are ideal for high flow rates and larger debris, while Y-strainers are compact and suitable for smaller spaces. If dealing with corrosive materials, consider stainless steel or plastic options. Always assess the operating pressure and temperature limits to ensure compatibility with your system. Consulting with the manufacturer can provide tailored recommendations based on your operational needs. -
How can I customize my strainer order to meet specific requirements?
Most reputable strainer manufacturers offer customization options to meet specific requirements. When reaching out to suppliers, clearly outline your needs regarding size, materials, and filtration specifications. Ask about available custom features such as pressure ratings, connection types, or even branding options. Ensure that the manufacturer provides a detailed proposal that includes timelines, costs, and any necessary prototypes. Building a strong relationship with your supplier can facilitate more effective customization processes. -
What is the minimum order quantity (MOQ) for strainer purchases?
The minimum order quantity (MOQ) for strainers varies by manufacturer and the type of strainer being ordered. Generally, MOQs can range from 10 to several hundred units, especially for customized products. It is crucial to discuss MOQs upfront during negotiations to avoid misunderstandings. If you are a smaller buyer, consider consolidating orders with other businesses to meet MOQ requirements, or look for manufacturers that cater specifically to smaller orders. -
What payment terms should I expect when sourcing strainers internationally?
Payment terms for international transactions typically include options like advance payment, letter of credit, or installment payments. Many manufacturers require a deposit (usually 30-50%) before production, with the balance due upon shipment or delivery. Always negotiate terms that protect your interests, such as escrow services or payment upon receipt of goods. Review the supplier’s reputation and financial stability to mitigate risks associated with upfront payments. -
How do I ensure quality assurance when sourcing strainers?
To ensure quality assurance when sourcing strainers, first verify the manufacturer’s certifications and quality control processes. Request detailed information about their testing procedures, including the standards they adhere to. Establish a clear quality assurance agreement that outlines acceptable tolerances and inspection protocols. Consider arranging for third-party inspections before shipment to validate product quality. Building a long-term partnership with the manufacturer can also enhance accountability for product standards. -
What logistics considerations should I keep in mind when importing strainers?
When importing strainers, consider logistics factors such as shipping methods, lead times, and customs regulations. Select a reliable freight forwarder who understands the intricacies of international shipping, including tariffs and duties. Ensure that the manufacturer provides all necessary documentation, including invoices and certificates of origin, to facilitate smooth customs clearance. Additionally, account for potential delays in shipping and customs processing in your project timelines to avoid disruptions. -
How can I evaluate and vet potential strainer suppliers effectively?
To evaluate and vet potential strainer suppliers, start by checking their industry experience and client testimonials. Request references and case studies to understand their performance and reliability. Conduct a factory audit, if possible, to inspect their production capabilities and quality control measures firsthand. Review their response time and customer service during initial communications, as this can be indicative of their overall business practices. Utilizing platforms that aggregate supplier ratings can also provide valuable insights into their reputation in the market.
Important Disclaimer & Terms of Use
⚠️ Important Disclaimer
The information provided in this guide, including content regarding manufacturers, technical specifications, and market analysis, is for informational and educational purposes only. It does not constitute professional procurement advice, financial advice, or legal advice.
While we have made every effort to ensure the accuracy and timeliness of the information, we are not responsible for any errors, omissions, or outdated information. Market conditions, company details, and technical standards are subject to change.
B2B buyers must conduct their own independent and thorough due diligence before making any purchasing decisions. This includes contacting suppliers directly, verifying certifications, requesting samples, and seeking professional consultation. The risk of relying on any information in this guide is borne solely by the reader.
Strategic Sourcing Conclusion and Outlook for strainer manufacturer
As the global marketplace continues to evolve, the importance of strategic sourcing for strainer manufacturers cannot be overstated. By leveraging a comprehensive sourcing strategy, international B2B buyers from regions such as Africa, South America, the Middle East, and Europe can enhance supply chain resilience and optimize cost efficiencies. Key takeaways include the necessity of evaluating supplier capabilities, understanding regional market trends, and maintaining open communication channels to ensure alignment on quality and delivery expectations.
How can strategic sourcing improve supply chain resilience for international buyers?
Strategic sourcing not only mitigates risks associated with fluctuating market conditions but also fosters long-term partnerships that contribute to innovation and sustainability. By aligning sourcing decisions with broader business objectives, buyers can drive significant value across their operations.
Looking ahead, the landscape for strainer manufacturers is poised for growth, driven by advancements in technology and increased demand for filtration solutions. International B2B buyers are encouraged to proactively seek out reliable suppliers who demonstrate a commitment to quality and sustainability. Engage with potential partners today to harness the benefits of strategic sourcing and position your business for success in the global marketplace.