Discover Top Cutting Machine Manufacturers: Save Costs Today (2025)
Introduction: Navigating the Global Market for cutting machine manufacturer
In the dynamic landscape of manufacturing, sourcing reliable cutting machine manufacturers can pose significant challenges for B2B buyers, particularly those from regions such as Africa, South America, the Middle East, and Europe, including countries like Poland and Colombia. The complexities of identifying quality suppliers, understanding diverse machine applications, and evaluating costs often lead to uncertainty in purchasing decisions. This comprehensive guide is designed to empower international buyers by providing insights into various types of cutting machines, their applications across different industries, and essential criteria for vetting suppliers.
By delving into critical aspects such as market trends, supplier reliability, and technological advancements, this guide equips businesses with the knowledge necessary to make informed purchasing decisions. Whether you are looking to invest in CNC cutting machines for precision manufacturing or laser cutters for intricate designs, understanding the nuances of each option will help streamline your procurement process.
Additionally, this guide addresses cost considerations and potential ROI, enabling buyers to align their investments with their operational goals. With a focus on actionable insights, our aim is to facilitate a smooth sourcing experience, ultimately leading to enhanced productivity and competitiveness in the global market.
Understanding cutting machine manufacturer Types and Variations
Type Name | Key Distinguishing Features | Primary B2B Applications | Brief Pros & Cons for Buyers |
---|---|---|---|
Laser Cutting Machines | High precision, versatile materials, minimal waste | Aerospace, automotive, electronics | Pros: Exceptional accuracy; Cons: Higher initial investment. |
Plasma Cutting Machines | Uses ionized gas for cutting, effective on thick metals | Metal fabrication, shipbuilding | Pros: Fast cutting speed; Cons: Limited to conductive materials. |
Waterjet Cutting Machines | Employs high-pressure water jets, suitable for various materials | Stone, glass, and composite industries | Pros: No heat-affected zones; Cons: Slower than laser/plasma. |
CNC Cutting Machines | Computer-controlled for automated precision | Manufacturing, furniture production | Pros: High repeatability; Cons: Requires skilled operators. |
Band Saw Machines | Continuous blade for cutting, ideal for bulk materials | Woodworking, metal cutting | Pros: Cost-effective for bulk; Cons: Limited to specific shapes. |
What Are Laser Cutting Machines and Their Applications?
Laser cutting machines are known for their exceptional precision and versatility, making them ideal for a variety of materials, including metals, plastics, and wood. They are particularly favored in industries such as aerospace, automotive, and electronics where high accuracy is critical. When considering a laser cutting machine, B2B buyers should evaluate the machine’s wattage, cutting speed, and the types of materials it can process. The initial investment can be substantial, but the long-term savings on material waste and labor can justify the cost.
How Do Plasma Cutting Machines Work and Where Are They Used?
Plasma cutting machines utilize an ionized gas to create a high-temperature plasma arc that effectively cuts through thick metals. They are widely used in metal fabrication and shipbuilding industries due to their fast cutting speeds and ability to handle heavy-duty materials. Buyers should consider the thickness of materials they will be working with and the machine’s duty cycle. While plasma cutting machines are faster than many alternatives, they are limited to conductive materials, which may affect their versatility in certain applications.
What Are the Benefits of Waterjet Cutting Machines?
Waterjet cutting machines are unique in that they use high-pressure water jets to cut a wide range of materials, including metals, glass, and stone. This method is particularly advantageous because it does not create heat-affected zones, preserving the integrity of the material. Waterjet machines are ideal for industries like stone fabrication and aerospace. B2B buyers should assess the machine’s cutting speed and the thickness of materials it can handle. While slower than laser or plasma options, the ability to cut diverse materials makes waterjet technology a valuable investment.
Why Choose CNC Cutting Machines for Precision Tasks?
CNC (Computer Numerical Control) cutting machines are designed for automated precision, making them a staple in manufacturing and furniture production. These machines can produce high repeatability and accuracy, which are essential for large-scale production runs. When purchasing CNC machines, buyers should consider the software compatibility, ease of programming, and the range of materials that can be processed. While they require skilled operators for setup and maintenance, their efficiency and consistency can significantly boost production capabilities.
What Are Band Saw Machines and Their Key Features?
Band saw machines utilize a continuous blade to make cuts, making them particularly effective for bulk materials in woodworking and metal cutting applications. They are often more cost-effective than other cutting machines for large volumes. B2B buyers should consider the blade size, cutting capacity, and ease of blade replacement when evaluating band saw machines. While they are excellent for straight cuts, their limitations in cutting complex shapes may require additional machinery, impacting overall operational efficiency.
Related Video: 2024 Best Laser Cutting Machine for Fabric, Textile and Garment
Key Industrial Applications of cutting machine manufacturer
Industry/Sector | Specific Application of Cutting Machine Manufacturer | Value/Benefit for the Business | Key Sourcing Considerations for this Application |
---|---|---|---|
Automotive Manufacturing | Precision cutting of metal parts and components | Enhances accuracy, reduces waste, and improves production efficiency | Supplier reliability, machine adaptability to various materials, and after-sales support |
Textile and Apparel | Fabric cutting for garment production | Increases throughput, minimizes fabric waste, and ensures consistent quality | Technology integration with design software, cutting speed, and blade longevity |
Aerospace | Cutting of composite materials for aircraft parts | Ensures high precision for safety-critical components and reduces lead times | Compliance with industry standards, material compatibility, and precision capabilities |
Construction and Fabrication | Structural steel cutting for frameworks | Improves project timelines, enhances safety, and reduces material costs | Equipment size and portability, cutting speed, and service availability |
Electronics and Electrical Goods | PCB (Printed Circuit Board) cutting | Increases production efficiency and ensures high precision for complex designs | Scalability, integration with existing manufacturing processes, and support for diverse PCB materials |
How Cutting Machines Enhance Automotive Manufacturing
In the automotive industry, cutting machines are essential for the precision cutting of metal parts and components. They solve the challenges of maintaining high accuracy while reducing material waste during production. For international buyers, especially those in regions like South America and Europe, sourcing cutting machines that can adapt to various materials and provide reliable after-sales support is crucial. This ensures that production lines remain efficient and responsive to market demands.
What Role Do Cutting Machines Play in Textile and Apparel Production?
In the textile and apparel sector, cutting machines are utilized for fabric cutting, which is a critical step in garment production. These machines not only increase throughput but also minimize fabric waste, ensuring that businesses maximize their resources. B2B buyers in Africa and the Middle East should consider sourcing machines that integrate seamlessly with design software for enhanced efficiency. Additionally, factors like cutting speed and blade longevity are vital for maintaining production quality.
How Are Cutting Machines Used in Aerospace Applications?
In aerospace manufacturing, cutting machines play a pivotal role in cutting composite materials used for aircraft parts. The precision offered by these machines is paramount, as safety-critical components require exact specifications. Buyers in Europe, particularly in countries with stringent regulatory standards, must ensure that the machines they source comply with industry regulations and are compatible with the materials used. This not only enhances production efficiency but also significantly reduces lead times.
What Are the Benefits of Cutting Machines in Construction and Fabrication?
In the construction and fabrication industry, cutting machines are employed for structural steel cutting, which is essential for creating frameworks. These machines help improve project timelines and enhance safety while simultaneously reducing material costs. Buyers from regions such as Africa and South America should prioritize equipment that offers portability and high cutting speeds. Ensuring access to service and maintenance support is also critical to avoid project delays.
How Do Cutting Machines Improve Electronics Manufacturing?
In the electronics sector, cutting machines are vital for the precise cutting of printed circuit boards (PCBs). These machines enhance production efficiency and ensure high precision, which is necessary for complex electronic designs. International B2B buyers should focus on sourcing scalable machines that can integrate with their existing manufacturing processes. Additionally, support for diverse PCB materials is essential to accommodate the evolving needs of electronic manufacturing.
Related Video: Metal laser cutting machine LS7 | BLM GROUP
3 Common User Pain Points for ‘cutting machine manufacturer’ & Their Solutions
Scenario 1: Difficulty in Customizing Cutting Machines for Unique Applications
The Problem: Many B2B buyers encounter challenges when seeking cutting machines that can be tailored to their specific production needs. For instance, a manufacturer in Africa may require a cutting machine capable of processing a variety of materials, such as textiles and plastics, but struggles to find a supplier that offers customizable options. This lack of adaptability can lead to inefficiencies in production, increased costs, and the inability to meet client specifications, ultimately impacting the buyer’s bottom line.
The Solution: To address this issue, buyers should prioritize manufacturers that specialize in custom solutions. When sourcing cutting machines, it’s crucial to engage with suppliers early in the process to discuss specific requirements and explore the range of customization options available. Buyers should request detailed product specifications, including the machine’s adaptability to different materials and cutting techniques. Additionally, consider suppliers that offer prototyping services, allowing for real-world testing before a full-scale purchase. This proactive approach not only ensures that the cutting machine will meet unique production needs but also fosters a collaborative relationship with the manufacturer.
Scenario 2: High Operational Costs Due to Inefficient Machinery
The Problem: Operational efficiency is paramount for B2B buyers, yet many face the challenge of high operational costs stemming from outdated or inefficient cutting machines. For example, a company in South America may find that their existing machines consume excessive energy and require frequent maintenance, leading to increased operational expenses and downtime. These factors can severely hinder profitability and competitiveness in a fast-paced market.
The Solution: Buyers should consider investing in modern, energy-efficient cutting machines that not only reduce operational costs but also enhance productivity. When evaluating potential suppliers, request information on energy consumption ratings and total cost of ownership (TCO) for their machines. Look for manufacturers that provide detailed case studies or testimonials demonstrating the efficiency and reliability of their equipment. Additionally, implementing a preventive maintenance schedule with the chosen supplier can help ensure that machines operate at peak performance, reducing unexpected costs and prolonging equipment lifespan.
Scenario 3: Inadequate After-Sales Support and Training
The Problem: After purchasing a cutting machine, many B2B buyers experience frustration due to inadequate after-sales support and insufficient training. This can lead to underutilization of the equipment, as operators may not be fully aware of its capabilities or best practices. For instance, a buyer in Europe might invest in a high-end cutting machine but struggle to achieve optimal results due to a lack of guidance from the manufacturer.
The Solution: To mitigate this pain point, buyers should thoroughly assess the after-sales support and training services offered by potential manufacturers before making a purchase. Inquire about the availability of operator training sessions, technical support, and maintenance services. A reputable manufacturer will provide comprehensive training programs that cover machine operation, troubleshooting, and maintenance procedures. Additionally, consider suppliers that offer online resources, such as video tutorials and user manuals, to facilitate ongoing learning. Establishing a strong support system can empower operators to maximize the machine’s potential, ensuring a successful return on investment and enhanced productivity.
Strategic Material Selection Guide for cutting machine manufacturer
When selecting materials for cutting machines, international B2B buyers must consider several factors, including performance characteristics, cost implications, and regional compliance standards. Here, we analyze four common materials used in cutting machine manufacturing: Steel, Aluminum, Composite Materials, and Carbide.
What are the Key Properties of Steel in Cutting Machines?
Steel is a widely used material in cutting machines due to its excellent strength and durability. Key properties include high tensile strength, good wear resistance, and the ability to withstand high temperatures and pressures. Steel can be alloyed with other elements to enhance its properties, such as chromium for corrosion resistance or carbon for increased hardness.
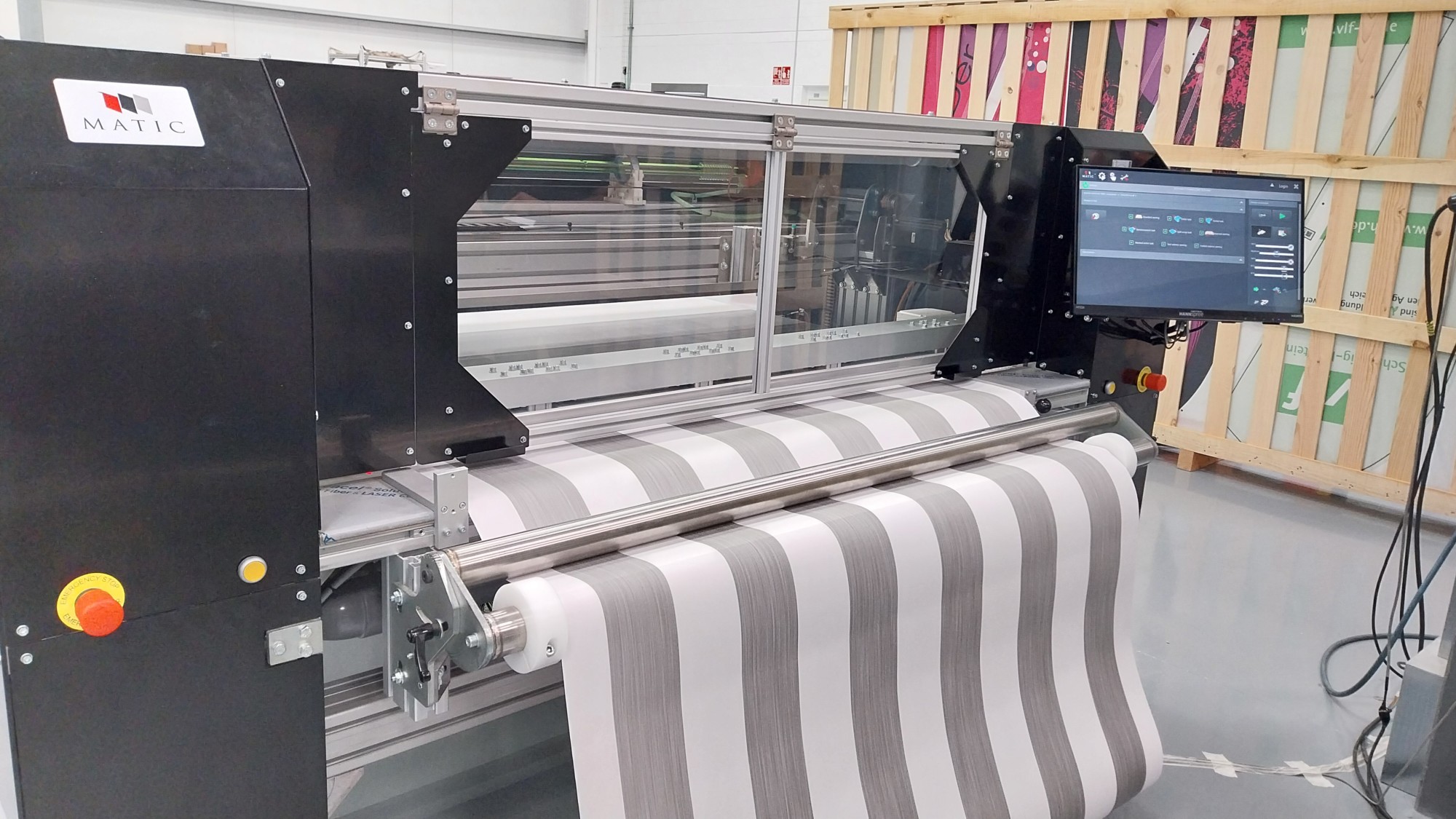
A stock image related to cutting machine manufacturer.
Pros and Cons: The primary advantage of steel is its durability, making it suitable for heavy-duty applications. However, it can be heavy and may require more energy to operate, which could increase operational costs. Additionally, the manufacturing complexity can vary based on the type of steel used, impacting production timelines.
Impact on Application: Steel is compatible with various media, including metals and plastics, making it versatile for different cutting applications. However, its weight may affect the mobility of the cutting machine.
Considerations for International Buyers: Buyers from regions like Africa and South America should ensure compliance with local and international standards (e.g., ASTM, DIN) when sourcing steel. Understanding the specific grades of steel available in the local market is also crucial for ensuring quality.
How Does Aluminum Benefit Cutting Machine Manufacturing?
Aluminum is another popular choice for cutting machine components. It is lightweight, corrosion-resistant, and has good thermal conductivity. These properties make aluminum an attractive option for applications requiring precision and efficiency.
Pros and Cons: The key advantage of aluminum is its lightweight nature, which enhances machine maneuverability and reduces energy consumption. However, aluminum is generally less durable than steel and may not be suitable for high-stress applications, leading to potential wear over time.
Impact on Application: Aluminum is particularly effective in applications involving softer materials, where its properties can be fully utilized without excessive wear. However, its reduced strength can limit its use in heavy-duty cutting scenarios.
Considerations for International Buyers: Buyers in Europe and the Middle East should consider the availability of specific aluminum alloys that meet local standards. Familiarity with regional preferences for lightweight materials can also influence purchasing decisions.
What Role Do Composite Materials Play in Cutting Machines?
Composite materials, which often combine polymers with reinforcing fibers, are increasingly used in cutting machines. Their lightweight and high-strength characteristics make them suitable for advanced applications.
Pros and Cons: The primary advantage of composites is their exceptional strength-to-weight ratio, allowing for more efficient machine designs. However, they can be more expensive to manufacture and may require specialized processing techniques.
Impact on Application: Composites are ideal for specialized cutting applications, particularly in industries like aerospace and automotive, where weight savings are critical. However, their compatibility with certain cutting media may vary, necessitating careful selection.
Considerations for International Buyers: Buyers from regions like South America and Africa should assess the availability of composite materials and their compliance with international standards. Understanding local manufacturing capabilities for composites is also essential for successful integration.
How Does Carbide Compare in Cutting Machine Applications?
Carbide, particularly tungsten carbide, is renowned for its hardness and wear resistance, making it a top choice for cutting tools and inserts.
Pros and Cons: The key advantage of carbide is its exceptional durability, allowing for longer tool life and reduced downtime. However, it is more brittle than other materials, which can lead to chipping or breaking under certain conditions.
Impact on Application: Carbide is particularly effective for cutting hard materials, such as metals and ceramics, making it invaluable in precision machining applications. However, its brittleness may limit its use in high-impact scenarios.
Considerations for International Buyers: Buyers in Europe and the Middle East should be aware of the specific grades of carbide available and their compliance with relevant standards. Understanding the supply chain for carbide components is also critical for ensuring timely delivery.
Summary Table of Material Selection for Cutting Machines
Material | Typical Use Case for cutting machine manufacturer | Key Advantage | Key Disadvantage/Limitation | Relative Cost (Low/Med/High) |
---|---|---|---|---|
Steel | Heavy-duty cutting applications | High durability and strength | Heavier, higher energy consumption | Medium |
Aluminum | Precision cutting for softer materials | Lightweight, corrosion-resistant | Less durable than steel | Medium |
Composite | Advanced applications (e.g., aerospace) | Exceptional strength-to-weight ratio | Higher manufacturing costs | High |
Carbide | Cutting hard materials (e.g., metals, ceramics) | Exceptional hardness and wear resistance | Brittle, prone to chipping | High |
This material selection guide provides actionable insights for international B2B buyers, enabling them to make informed decisions based on performance, cost, and compliance considerations.
In-depth Look: Manufacturing Processes and Quality Assurance for cutting machine manufacturer
What Are the Main Stages in the Manufacturing Process of Cutting Machines?
When it comes to manufacturing cutting machines, understanding the main stages of the production process is crucial for international B2B buyers. The manufacturing process typically includes four main stages: material preparation, forming, assembly, and finishing.
-
Material Preparation: This initial phase involves selecting the right materials, which could include high-strength steel, aluminum, or specialized alloys. The materials are then cut to size, inspected for defects, and treated to enhance durability. For B2B buyers, it’s essential to verify that suppliers source high-quality materials to ensure the performance and longevity of the cutting machines.
-
Forming: In this stage, the prepared materials are shaped into components through various methods such as stamping, laser cutting, or CNC machining. Each method has its benefits; for instance, CNC machining offers precision, while laser cutting can handle complex shapes. Buyers should inquire about the technologies used by manufacturers and their capabilities to ensure they meet specific project requirements.
-
Assembly: The assembly stage is where individual components come together to form the cutting machine. This process can be manual or automated, depending on the manufacturer’s scale and capabilities. Effective assembly requires skilled labor and adherence to strict protocols to ensure all parts fit and function correctly. Buyers should look for manufacturers that provide detailed assembly documentation and quality checks.
-
Finishing: The final stage involves applying surface treatments, such as painting, anodizing, or plating, to protect the machine from corrosion and wear. This not only enhances the aesthetic appeal but also increases the machine’s lifespan. International buyers should confirm that the finishing processes comply with regional environmental regulations and standards.
How Do Quality Assurance Practices Impact Cutting Machine Manufacturing?
Quality assurance (QA) is integral to the manufacturing process, ensuring that cutting machines meet the highest standards of performance and safety. For B2B buyers, understanding QA practices can help in selecting reliable suppliers.
-
International Standards: Many cutting machine manufacturers adhere to international standards such as ISO 9001, which focuses on quality management systems. Compliance with these standards indicates a commitment to quality and continuous improvement. Additionally, industry-specific certifications such as CE for Europe or API for oil and gas applications can further assure buyers of a product’s reliability.
-
Quality Control Checkpoints:
– Incoming Quality Control (IQC): This checkpoint occurs at the beginning of the manufacturing process, where materials are inspected upon arrival. It ensures that only high-quality materials are used in production.
– In-Process Quality Control (IPQC): During the manufacturing process, ongoing inspections are conducted to identify any defects or deviations from standards. This proactive approach minimizes errors and waste.
– Final Quality Control (FQC): Once assembly is complete, the finished product undergoes a thorough inspection to ensure it meets all specifications before shipping. This stage often includes performance testing and validation. -
Common Testing Methods: Manufacturers often employ various testing methods, including functional tests, endurance tests, and safety checks. These tests help verify that the cutting machines perform as expected under real-world conditions. Buyers should ask about the specific testing procedures a manufacturer uses and request documentation of test results.
How Can B2B Buyers Verify Supplier Quality Control Processes?
For international B2B buyers, verifying the quality control processes of suppliers is critical to ensuring they receive reliable cutting machines. Here are some actionable insights:
-
Conducting Audits: Regular audits of potential suppliers can provide insight into their manufacturing processes and quality control practices. Buyers should consider both on-site audits and remote assessments, especially when dealing with suppliers in regions like Africa or South America, where travel might be challenging.
-
Requesting Quality Assurance Reports: Suppliers should be willing to provide detailed quality assurance reports that outline their processes, standards, and test results. These documents can reveal a lot about the manufacturer’s commitment to quality.
-
Third-Party Inspections: Engaging third-party inspection services can offer an unbiased evaluation of a manufacturer’s quality control practices. These services can conduct inspections at various stages of production and ensure compliance with international standards.
What Are the Quality Control Nuances for International B2B Buyers?
International B2B buyers, especially from regions like Europe, Africa, and the Middle East, must be aware of several nuances in quality control:
-
Regional Standards: Different regions may have varying standards and regulations. For example, European buyers often require CE marking, while Middle Eastern markets might focus on GCC standards. Buyers should ensure that their suppliers are knowledgeable about and compliant with the standards applicable to their target markets.
-
Cultural and Language Barriers: Communication can pose challenges when dealing with suppliers from different cultural backgrounds. Buyers should ensure clear communication regarding quality expectations and standards. Utilizing local representatives or translators can help bridge these gaps.
-
Logistics and Supply Chain Considerations: The supply chain can significantly impact quality assurance. Delays or mishandling during transportation can compromise the integrity of cutting machines. Buyers should establish clear logistics protocols with suppliers to ensure that products arrive in optimal condition.
Conclusion: Ensuring Quality in Cutting Machine Manufacturing
For international B2B buyers, understanding the manufacturing processes and quality assurance practices of cutting machine manufacturers is vital. By focusing on the main stages of production, verifying quality control measures, and being aware of regional nuances, buyers can make informed decisions that lead to successful procurement and long-term partnerships. Investing time in due diligence will pay off, ensuring that the cutting machines meet operational needs and industry standards.
Practical Sourcing Guide: A Step-by-Step Checklist for ‘cutting machine manufacturer’
Introduction
When sourcing a cutting machine manufacturer, it is essential for B2B buyers to approach the process methodically. This checklist serves as a practical guide to help you navigate the complexities of selecting a reliable supplier. By following these steps, you can ensure that your investment meets your operational needs and quality standards.
Step 1: Define Your Technical Specifications
Understanding your specific requirements is the first step in sourcing the right cutting machine. Consider factors such as the type of materials to be cut, the dimensions, and the desired precision. Defining these specifications helps narrow down potential suppliers that can meet your needs effectively.
- Material Types: Identify whether you need the machine for metal, plastic, or textiles.
- Cutting Techniques: Determine if you require laser, waterjet, or mechanical cutting processes.
Step 2: Research Potential Suppliers
Conduct thorough research to identify manufacturers with a solid reputation in the industry. Utilize online resources, industry forums, and trade shows to gather information about potential suppliers. This step is crucial in finding manufacturers that align with your technical and business requirements.
- Industry Experience: Look for suppliers with a proven track record in your specific market.
- Customer Reviews: Check for testimonials and ratings from other businesses that have used their services.
Step 3: Evaluate Supplier Certifications
Certifications can serve as a mark of quality and compliance. Verify that potential suppliers hold relevant industry certifications, such as ISO 9001, which ensures a quality management system is in place. This step is vital to ensure you are partnering with a manufacturer committed to maintaining high standards.
- Compliance with Standards: Ensure that the manufacturer meets international safety and operational standards.
- Sustainability Certifications: Consider suppliers that have eco-friendly practices if sustainability is a priority for your business.
Step 4: Request Detailed Quotes
Once you have shortlisted suppliers, request detailed quotations that outline pricing, delivery timelines, and warranty terms. This step allows you to compare offers comprehensively and understand the total cost of ownership, including maintenance and operational expenses.
- Breakdown of Costs: Ensure quotes include all potential costs, such as shipping and installation.
- Warranty and Support: Inquire about the warranty period and post-purchase support available.
Step 5: Visit the Manufacturing Facility
If possible, arrange a visit to the manufacturing facility. Observing the production processes firsthand can provide valuable insights into the supplier’s capabilities and quality control measures. This step is particularly important for high-value investments.
- Quality Control Procedures: Look for evidence of rigorous quality checks during production.
- Equipment and Technology: Assess whether the supplier uses modern technology and equipment that meets your standards.
Step 6: Check References and Past Projects
Before making a final decision, reach out to existing clients of the supplier to gather feedback on their experiences. This step can reveal important information about the reliability and service quality of the manufacturer.
- Client Satisfaction: Ask about the supplier’s responsiveness and problem-solving capabilities.
- Project Relevance: Inquire whether the supplier has worked on projects similar to yours.
Step 7: Negotiate Terms and Finalize the Contract
Once you have selected a supplier, engage in negotiations to finalize terms that work for both parties. Pay attention to payment terms, delivery schedules, and any contingencies in case of delays or issues. This step ensures that you have a clear understanding of the agreement and protects your interests.
- Clear Communication: Ensure all terms are clearly outlined to avoid misunderstandings later.
- Legal Review: Consider having a legal professional review the contract before signing.
By following this checklist, international B2B buyers from regions like Africa, South America, the Middle East, and Europe can make informed decisions when sourcing cutting machine manufacturers, ultimately leading to successful partnerships and enhanced operational efficiency.
Comprehensive Cost and Pricing Analysis for cutting machine manufacturer Sourcing
What Are the Key Cost Components in Cutting Machine Manufacturing?
When sourcing cutting machines, understanding the cost structure is crucial for B2B buyers, particularly in regions such as Africa, South America, the Middle East, and Europe. The primary cost components include:
-
Materials: The type and quality of materials used (e.g., steel, aluminum, composites) significantly influence the cost. High-grade materials often lead to higher durability and efficiency but can raise upfront costs.
-
Labor: Labor costs can vary dramatically depending on the region of manufacture. Countries with lower labor costs may provide cheaper options but could compromise quality if not managed properly.
-
Manufacturing Overhead: This includes all indirect costs related to production, such as utilities, rent, and salaries of non-production staff. Efficient manufacturing processes can help minimize these costs.
-
Tooling: Specialized tools and equipment necessary for production contribute to the initial investment. The complexity of the cutting machines often dictates the tooling expenses.
-
Quality Control (QC): Implementing a robust QC system ensures product reliability, which can add to costs but is essential for maintaining brand reputation.
-
Logistics: Shipping and handling costs can vary based on distance and method of transport. Incoterms play a crucial role in determining who bears these costs.
-
Margin: Manufacturers typically include a profit margin in their pricing. Understanding the market standard for margins can help buyers gauge whether they are receiving a fair price.
How Do Price Influencers Affect Cutting Machine Costs?
Several factors can influence the pricing of cutting machines, including:
-
Volume/MOQ: Minimum Order Quantities (MOQ) can affect pricing. Larger orders often receive volume discounts, making it essential for buyers to assess their needs accurately.
-
Specifications and Customization: Custom-built machines tailored to specific applications can incur higher costs. Buyers should clearly define their specifications to avoid unexpected expenses.
-
Materials: The choice of materials not only impacts durability but also price. Buyers should weigh the long-term benefits of higher-quality materials against initial costs.
-
Quality Certifications: Machines that meet international quality standards (ISO, CE marking) may be priced higher due to additional testing and compliance costs, but they often ensure better performance and reliability.
-
Supplier Factors: Supplier reputation, experience, and relationship history can influence pricing. Long-term partnerships may yield better prices and service agreements.
-
Incoterms: Understanding different shipping terms can significantly affect total costs. Choosing the right Incoterm can optimize logistics and cost management.
What Negotiation Strategies Can Help B2B Buyers?
For international B2B buyers, especially in diverse markets such as Africa and South America, effective negotiation strategies are essential:
-
Research the Market: Conduct thorough market research to understand typical pricing and cost structures in your region. This knowledge can empower you during negotiations.
-
Leverage Volume: If possible, consolidate orders to negotiate better pricing. Suppliers are often more willing to offer discounts for larger quantities.
-
Discuss Payment Terms: Flexible payment terms can reduce immediate cash flow pressures, making it easier to finalize deals.
-
Consider Total Cost of Ownership (TCO): Evaluate not just the purchase price but also long-term costs associated with maintenance, operation, and energy consumption.
-
Build Relationships: Establishing strong relationships with suppliers can lead to better pricing, service, and support.
Why Is It Important to Understand Pricing Nuances?
For buyers in Africa, South America, the Middle East, and Europe, being aware of pricing nuances is crucial. Exchange rates, local tariffs, and import duties can affect overall costs. Always seek clarity on these factors before finalizing a purchase. Additionally, be prepared for potential fluctuations in prices due to market demand or raw material availability.
Disclaimer on Indicative Prices
While the information provided offers a comprehensive overview of potential costs and pricing structures, actual prices may vary based on specific requirements, supplier negotiations, and current market conditions. Always request formal quotes from manufacturers to ensure accurate budgeting and planning.
Alternatives Analysis: Comparing cutting machine manufacturer With Other Solutions
When considering the acquisition of a cutting machine, it’s essential to evaluate alternatives that may fulfill similar needs while potentially offering different benefits or drawbacks. This analysis will compare traditional cutting machine manufacturers with two viable alternatives: CNC laser cutting systems and waterjet cutting technologies. Understanding these options helps international B2B buyers, particularly from Africa, South America, the Middle East, and Europe, make informed decisions based on performance, cost, and implementation ease.
Comparison Aspect | Cutting Machine Manufacturer | CNC Laser Cutting Systems | Waterjet Cutting Technologies |
---|---|---|---|
Performance | High precision for thick materials | Excellent precision for thin to medium thickness | Versatile for various materials |
Cost | Generally high initial investment | Moderate, with potential for lower operating costs | High initial cost, but low maintenance |
Ease of Implementation | Requires skilled operators | User-friendly software; training needed | Complex setup; skilled operators necessary |
Maintenance | Routine maintenance required | Lower maintenance; occasional part replacements | Regular maintenance for pumps and nozzles |
Best Use Case | Heavy-duty industrial applications | Prototyping and intricate designs | Cutting thick or complex materials |
What Are the Benefits and Drawbacks of CNC Laser Cutting Systems?
CNC laser cutting systems utilize focused laser beams to cut materials, providing high precision and speed. One of the main advantages of this technology is its ability to handle intricate designs with minimal waste. It’s particularly effective for materials like acrylic and thin metals, making it an excellent choice for prototyping or projects requiring detailed work. However, while the initial investment may be moderate, the need for skilled operators and potential training can be a hurdle for companies lacking experience in this area.
How Do Waterjet Cutting Technologies Compare?
Waterjet cutting technologies use high-pressure water jets, often combined with abrasives, to cut through various materials, including metals, glass, and stone. The primary advantage of waterjet cutting is its versatility and ability to cut thick materials without affecting their structural integrity. However, this technology typically involves a higher initial investment and requires regular maintenance of pumps and nozzles. Additionally, the complexity of setup and the necessity for skilled operators can present challenges for companies considering this option.
How Should B2B Buyers Choose the Right Solution?
When selecting the appropriate cutting solution, B2B buyers should assess their specific operational needs, production volume, and budget constraints. If precision and intricate designs are paramount, CNC laser cutting may be the preferred option. Conversely, for heavy-duty applications or cutting through various materials, traditional cutting machines or waterjet technologies could be more suitable. Evaluating the long-term costs associated with maintenance and operator training will also help determine the best fit for your organization. Ultimately, a thorough understanding of each technology’s strengths and weaknesses will empower buyers to make informed decisions aligned with their production goals.
Essential Technical Properties and Trade Terminology for cutting machine manufacturer
What Are the Key Technical Properties of Cutting Machines?
When evaluating cutting machines, international B2B buyers should focus on several critical specifications that directly impact performance and cost-effectiveness. Understanding these properties ensures that you select a machine that meets your operational needs.
1. Material Grade
The material grade of the cutting machine components, particularly the blades and frame, is crucial for durability and cutting efficiency. High-grade materials, such as hardened steel or carbide, provide better wear resistance and longer service life. For buyers in sectors like manufacturing and construction, investing in machines with superior material grades can reduce long-term costs associated with replacements and maintenance.
2. Tolerance
Tolerance refers to the allowable deviation from a specified dimension in the cutting process. High precision is vital in industries that require exact measurements, such as aerospace and automotive. Machines with tighter tolerances ensure higher quality products, reducing waste and rework, which is especially important for B2B buyers aiming to maintain competitive advantage.
3. Cutting Speed
Cutting speed is the rate at which a cutting machine can operate. This specification affects productivity and efficiency, making it critical for industries with high-volume demands. Buyers should assess their production needs and choose machines that offer the required cutting speed without sacrificing quality.
4. Power Consumption
The power consumption of a cutting machine affects operational costs. Machines that are energy-efficient can lead to significant savings in electricity bills over time. As sustainability becomes a priority for many businesses, selecting machines with lower power consumption can also enhance your company’s green credentials.
5. Ease of Maintenance
Machines designed with ease of maintenance in mind can significantly reduce downtime. Features such as accessible parts for lubrication and cleaning should be prioritized. Buyers should inquire about the maintenance requirements and schedules to ensure minimal disruption in operations.
What Are Common Trade Terms in the Cutting Machine Industry?
Understanding industry jargon is essential for effective communication in B2B transactions. Here are some key terms that buyers should familiarize themselves with:
1. OEM (Original Equipment Manufacturer)
An OEM is a company that produces parts or equipment that may be marketed by another manufacturer. For buyers, understanding whether they are dealing with an OEM can impact the quality and warranty of the machines. It’s crucial to ensure that the OEM has a good reputation for reliability and support.
2. MOQ (Minimum Order Quantity)
MOQ refers to the smallest quantity of a product that a supplier is willing to sell. This term is significant for B2B buyers as it affects inventory management and cash flow. Knowing the MOQ can help you plan your purchases strategically, especially when dealing with international suppliers.
3. RFQ (Request for Quotation)
An RFQ is a document sent to suppliers requesting pricing and other details for specific products. It’s a critical tool for buyers to compare prices and terms. Providing detailed specifications in the RFQ can lead to more accurate quotes and better negotiation outcomes.
4. Incoterms
Incoterms are international commercial terms that define the responsibilities of buyers and sellers in the shipping process. Familiarity with these terms is vital to understanding shipping costs, risks, and responsibilities. Buyers should ensure clarity on which Incoterms apply to their transactions to avoid disputes.
5. Lead Time
Lead time is the amount of time between placing an order and receiving the product. For B2B buyers, understanding lead times is crucial for planning production schedules. A shorter lead time can enhance responsiveness to market demands, making it an important factor in supplier selection.
By grasping these essential technical properties and trade terminologies, B2B buyers can make informed decisions when procuring cutting machines, ultimately leading to improved operational efficiency and profitability.
Navigating Market Dynamics and Sourcing Trends in the cutting machine manufacturer Sector
What Are the Key Market Dynamics and Trends in the Cutting Machine Manufacturing Sector?
The cutting machine manufacturing sector is experiencing a dynamic shift driven by technological advancements and global market demands. Key factors influencing this market include automation, digitalization, and the increasing need for precision engineering. As industries across Africa, South America, the Middle East, and Europe (notably Poland and Colombia) seek to enhance productivity, manufacturers are prioritizing innovations such as CNC (Computer Numerical Control) cutting machines. These machines not only improve operational efficiency but also offer enhanced accuracy and reduced waste, making them appealing to international B2B buyers.
Moreover, the integration of Industry 4.0 technologies—like IoT (Internet of Things) and AI (Artificial Intelligence)—is revolutionizing sourcing strategies. Buyers are increasingly looking for suppliers that can provide smart, connected machines capable of real-time data analytics for predictive maintenance and operational optimization. The demand for customization is also rising, prompting manufacturers to offer flexible solutions tailored to specific industry needs, such as textiles, automotive, and metal fabrication.
Furthermore, the shift towards e-commerce platforms for B2B transactions is significant. Buyers are now leveraging online marketplaces to source cutting machines, enabling them to compare prices, features, and supplier ratings effortlessly. This trend emphasizes the importance of digital presence for manufacturers looking to attract international clients.
How Important Is Sustainability and Ethical Sourcing in the Cutting Machine Manufacturing Sector?
Sustainability and ethical sourcing are increasingly critical considerations for B2B buyers in the cutting machine manufacturing sector. The environmental impact of manufacturing processes has come under scrutiny, leading companies to adopt greener practices. This shift not only addresses regulatory compliance but also enhances brand reputation and customer loyalty.
B2B buyers are now prioritizing suppliers who demonstrate a commitment to sustainability through certifications such as ISO 14001 (Environmental Management) and adherence to eco-friendly manufacturing processes. The use of recyclable materials and energy-efficient production methods is becoming a standard expectation. For instance, sourcing cutting machines made from sustainable materials can significantly reduce the carbon footprint associated with production and end-of-life disposal.
Moreover, ethical supply chains are essential for maintaining transparency and accountability. Buyers are increasingly conducting due diligence to ensure that their suppliers uphold fair labor practices and contribute positively to local communities. This focus on ethical sourcing not only mitigates risks but also aligns with the growing consumer preference for brands that prioritize social responsibility.
What Is the Historical Evolution of Cutting Machine Manufacturing?
The evolution of cutting machine manufacturing can be traced back to the industrial revolution when mechanization began to transform production processes. Early cutting machines were manually operated, limiting precision and scalability. The introduction of electric power in the early 20th century marked a significant advancement, allowing for the development of more complex and efficient machines.
In the latter half of the 20th century, the advent of CNC technology revolutionized the sector. This innovation enabled automated, precise cutting processes that significantly increased production rates and reduced human error. Today, cutting machines continue to evolve, incorporating advanced technologies like robotics and AI, which further enhance capabilities and efficiency. As a result, the cutting machine manufacturing sector is not only more efficient but also more responsive to the intricate demands of modern industries globally.
Frequently Asked Questions (FAQs) for B2B Buyers of cutting machine manufacturer
-
How do I choose the right cutting machine for my business needs?
Selecting the right cutting machine involves assessing your specific application requirements, such as the materials you will be cutting, the thickness of these materials, and the desired precision. Evaluate the machine’s features, including cutting speed, blade type, and automation capabilities. Additionally, consider the machine’s compatibility with your existing processes and whether it can be easily integrated into your workflow. Consulting with manufacturers and seeking demonstrations can also provide valuable insights into which machine will best meet your operational needs. -
What factors should I consider when sourcing a cutting machine manufacturer internationally?
When sourcing a cutting machine manufacturer, consider their reputation, manufacturing capabilities, and experience in your specific industry. Research their certifications and compliance with international quality standards. Assess their ability to provide after-sales support and training for your staff. Additionally, consider logistical factors such as shipping times, costs, and any customs regulations that may apply to your region, particularly if you are importing from Africa, South America, the Middle East, or Europe. -
What is the minimum order quantity (MOQ) for cutting machines from manufacturers?
Minimum order quantities can vary significantly between manufacturers and depend on the type of cutting machine and customization options. Some manufacturers may offer flexible MOQs for standard models, while custom machines may require larger orders to justify production costs. It’s essential to communicate your specific needs with potential suppliers and negotiate terms that align with your purchasing capabilities. Additionally, inquire about options for trial purchases or demo units to mitigate risk before committing to larger orders. -
What customization options are typically available for cutting machines?
Many cutting machine manufacturers offer a range of customization options, including size, cutting capacity, software integration, and specialized blades or tools tailored to specific materials. You may also have the option to modify features such as automation levels, safety mechanisms, and user interfaces. Discussing your specific requirements with manufacturers can lead to tailored solutions that enhance productivity and efficiency in your operations. -
What payment terms are commonly accepted when purchasing cutting machines?
Payment terms can vary widely among manufacturers but typically include options such as upfront payment, installments, or financing arrangements. It’s advisable to clarify these terms early in negotiations to ensure they align with your budget and cash flow management strategies. Some manufacturers may also offer trade credit or discounts for early payments. Always review the contract details carefully to understand any potential fees or penalties associated with late payments. -
How can I ensure quality assurance when buying cutting machines?
To ensure quality assurance, request detailed specifications and certifications from manufacturers, such as ISO 9001 or CE marking. Inquire about their quality control processes and whether they conduct regular testing on their machines. If possible, arrange for factory visits or third-party inspections to verify manufacturing practices. Additionally, reviewing customer testimonials and case studies can provide insights into the reliability and performance of the machines you are considering. -
What logistics considerations should I keep in mind when importing cutting machines?
Logistics play a crucial role in the successful importation of cutting machines. Consider factors such as shipping methods, costs, and estimated delivery times. Ensure you understand the customs requirements for your country, including tariffs and import duties. Collaborating with a logistics partner who has experience in handling industrial equipment can streamline the process. Additionally, account for any potential delays and plan your inventory accordingly to avoid disruptions in your operations. -
What support should I expect from cutting machine manufacturers post-purchase?
After purchasing a cutting machine, manufacturers should provide ongoing support, including installation assistance, operator training, and maintenance services. Inquire about warranty coverage and what it entails, as well as the availability of spare parts. A reliable manufacturer will also have a customer support team to assist with troubleshooting and technical issues. Building a strong relationship with your supplier can enhance the support you receive and ensure your machinery operates optimally.
Important Disclaimer & Terms of Use
⚠️ Important Disclaimer
The information provided in this guide, including content regarding manufacturers, technical specifications, and market analysis, is for informational and educational purposes only. It does not constitute professional procurement advice, financial advice, or legal advice.
While we have made every effort to ensure the accuracy and timeliness of the information, we are not responsible for any errors, omissions, or outdated information. Market conditions, company details, and technical standards are subject to change.
B2B buyers must conduct their own independent and thorough due diligence before making any purchasing decisions. This includes contacting suppliers directly, verifying certifications, requesting samples, and seeking professional consultation. The risk of relying on any information in this guide is borne solely by the reader.
Strategic Sourcing Conclusion and Outlook for cutting machine manufacturer
In the rapidly evolving landscape of cutting machine manufacturing, strategic sourcing emerges as a pivotal component for international B2B buyers. By understanding and leveraging global supply chains, businesses in Africa, South America, the Middle East, and Europe can enhance their procurement strategies, ensuring access to high-quality machinery at competitive prices.
What are the key benefits of strategic sourcing for cutting machine manufacturers? First, it fosters long-term partnerships with suppliers, leading to improved product innovation and reliability. Additionally, it allows buyers to navigate fluctuating market conditions more effectively, mitigating risks associated with supply disruptions.
As we look to the future, the emphasis on sustainability and technological integration will shape the sourcing strategies of cutting machine manufacturers. Buyers should actively seek suppliers who prioritize eco-friendly practices and innovation, aligning with global trends toward sustainability.
To capitalize on these opportunities, international B2B buyers are encouraged to engage in thorough market research and establish strong relationships with manufacturers that demonstrate a commitment to quality and innovation. By doing so, businesses can position themselves for success in a competitive marketplace, ensuring they remain at the forefront of the cutting machine industry.