Discover Top Benefits of Enameled Wire Suppliers (2025)
Introduction: Navigating the Global Market for enameled wire supplier
In an increasingly interconnected world, sourcing high-quality enameled wire can be a daunting task for international B2B buyers, especially those operating in diverse markets such as Africa, South America, the Middle East, and Europe. The challenge lies not only in identifying reliable enameled wire suppliers but also in understanding the various types, applications, and compliance standards that govern this essential component used in electric motors, transformers, and other electrical equipment. This guide is designed to empower you with the knowledge and insights necessary to navigate the global market effectively.
Throughout this comprehensive resource, we will delve into the different types of enameled wire, explore their applications across industries, and provide actionable strategies for vetting potential suppliers. Additionally, we will address cost considerations and factors that influence pricing, ensuring you are well-equipped to make informed purchasing decisions. By highlighting best practices and key market trends, this guide aims to enhance your sourcing strategy, mitigate risks, and ultimately foster successful partnerships with enameled wire suppliers.
Whether you are based in Mexico, the UK, or elsewhere, understanding the nuances of the enameled wire market will significantly impact your procurement processes and operational efficiency. Equip yourself with the tools to thrive in this competitive landscape and drive your business forward.
Understanding enameled wire supplier Types and Variations
Type Name | Key Distinguishing Features | Primary B2B Applications | Brief Pros & Cons for Buyers |
---|---|---|---|
Magnet Wire Suppliers | High copper content, insulated with enamel | Electric motors, transformers | Pros: High conductivity; Cons: Higher cost due to copper prices. |
Heating Wire Suppliers | Specialized for high-temperature applications | Industrial heaters, furnaces | Pros: Durable under heat; Cons: Limited flexibility in design. |
Coated Wire Suppliers | Various coatings (polyester, polyurethane) | Automotive, aerospace | Pros: Customizable; Cons: Coating may affect conductivity. |
Flat Wire Suppliers | Flat cross-section, often used in tight spaces | Medical devices, compact electronics | Pros: Space-saving design; Cons: More complex manufacturing. |
Multi-strand Wire Suppliers | Composed of several thin strands for flexibility | Robotics, flexible connections | Pros: High flexibility; Cons: Lower tensile strength compared to solid wire. |
What Are the Key Characteristics of Magnet Wire Suppliers?
Magnet wire suppliers specialize in providing high-purity copper wire coated with enamel insulation, designed for use in electric motors and transformers. These wires are known for their excellent conductivity and thermal resistance, making them ideal for applications requiring efficient energy transfer. When purchasing magnet wire, B2B buyers should consider wire gauge, insulation type, and temperature rating to ensure compatibility with their specific applications.
How Do Heating Wire Suppliers Stand Out?
Heating wire suppliers offer products engineered to withstand high temperatures, making them suitable for industrial heaters and furnaces. These wires are often constructed from materials that can endure prolonged exposure to heat without degrading. Buyers should evaluate the wire’s temperature rating, resistance, and compatibility with heating elements to ensure optimal performance in their heating applications.
What Are the Advantages of Coated Wire Suppliers?
Coated wire suppliers provide a variety of insulated wires, including those with polyester or polyurethane coatings. These wires are commonly used in automotive and aerospace industries due to their customizable properties, which can enhance performance and longevity. When sourcing coated wires, buyers should assess the coating material, thickness, and intended application to ensure that the wire meets specific requirements.
Why Choose Flat Wire Suppliers?
Flat wire suppliers deliver wires with a flat cross-section, ideal for applications where space constraints are critical, such as in medical devices and compact electronics. The unique shape allows for better packing density and improved thermal management. B2B buyers must consider the specific dimensions and material properties when selecting flat wires to ensure they meet the design criteria of their products.
What Are the Benefits of Multi-strand Wire Suppliers?
Multi-strand wire suppliers focus on wires made from multiple thin strands, providing enhanced flexibility for applications in robotics and flexible connections. This type of wire is particularly useful in environments that require movement or bending. Buyers should weigh the benefits of flexibility against the potential trade-off in tensile strength when selecting multi-strand wires for their projects.
Related Video: Enameled CopeprWinding Wire Production process–ZhengZhou LP Industry Co,.LTD
Key Industrial Applications of enameled wire supplier
Industry/Sector | Specific Application of Enameled Wire Supplier | Value/Benefit for the Business | Key Sourcing Considerations for this Application |
---|---|---|---|
Electrical Equipment | Windings in motors and transformers | Enhanced efficiency and performance of electrical devices | Ensure compatibility with voltage and temperature ratings |
Automotive | Wiring in electric vehicles and hybrid systems | Improved energy efficiency and reduced weight | Look for suppliers with automotive-grade certifications |
Consumer Electronics | Coils in inductors and speakers | Superior sound quality and reliable performance | Assess the wire’s insulation properties and durability |
Industrial Machinery | Magnet wire in heavy machinery | Increased durability and reduced downtime | Verify compliance with industry-specific standards |
Renewable Energy | Solar panel wiring | Optimized energy transfer and system reliability | Consider local sourcing options for reduced shipping costs |
How is Enameled Wire Used in Electrical Equipment?
In the electrical equipment sector, enameled wire is crucial for windings in motors and transformers. It provides electrical insulation while maintaining a compact design, which enhances the efficiency and performance of devices. International buyers from regions such as Africa and South America should ensure that the wire meets specific voltage and temperature ratings to suit their operational conditions. Sourcing from suppliers who understand local regulations can also facilitate smoother import processes.
What Role Does Enameled Wire Play in the Automotive Industry?
Enameled wire is extensively used in electric vehicles (EVs) and hybrid systems for wiring applications. This wire type is favored for its lightweight properties and improved energy efficiency, which are critical for battery performance and overall vehicle range. Buyers in the automotive sector, particularly from Europe and the Middle East, should prioritize suppliers that offer automotive-grade certifications to ensure compliance with safety and quality standards.
How is Enameled Wire Applied in Consumer Electronics?
In consumer electronics, enameled wire is primarily utilized in coils for inductors and speakers. Its ability to deliver superior sound quality and reliable performance makes it essential for high-fidelity audio devices. B2B buyers in this sector should evaluate the wire’s insulation properties and durability, particularly when sourcing from international suppliers, to ensure compatibility with various electronic applications.
What is the Importance of Enameled Wire in Industrial Machinery?
Within industrial machinery, enameled wire is used in magnet wire applications. Its robustness contributes to increased durability, which is vital for minimizing downtime in manufacturing processes. Buyers should verify that their suppliers comply with industry-specific standards, especially in regions like South America, where machinery performance can be affected by environmental factors.
How Does Enameled Wire Benefit Renewable Energy Solutions?
Enameled wire is integral to solar panel wiring, optimizing energy transfer and ensuring system reliability. The growing demand for renewable energy solutions in Europe and Africa highlights the need for high-quality wiring materials. Buyers should consider local sourcing options to reduce shipping costs and ensure timely delivery, which can be critical for project timelines in the rapidly evolving renewable energy sector.
Related Video: What is Magnet Wire? Explore Enameled Copper Wire Uses & Benefits
3 Common User Pain Points for ‘enameled wire supplier’ & Their Solutions
Scenario 1: Difficulty in Assessing Quality Standards of Enameled Wire
The Problem: B2B buyers, particularly in regions like Africa and South America, often encounter challenges in assessing the quality standards of enameled wire from suppliers. This issue is exacerbated by varying international standards, leading to uncertainty about whether the wire will meet the necessary performance requirements for specific applications, such as motors or transformers. Buyers may worry about the durability and reliability of the wire, fearing that subpar quality could result in costly failures down the line.
The Solution: To overcome this challenge, buyers should prioritize sourcing suppliers who can provide comprehensive quality certifications, such as ISO 9001 or UL certification. When evaluating potential suppliers, request detailed product specifications, including the type of enamel used, wire gauge, thermal ratings, and resistance values. Conducting due diligence, such as visiting manufacturing facilities or requesting samples for testing, can also help ensure that the wire meets the required standards. Additionally, leveraging third-party testing services can provide an unbiased assessment of product quality, allowing buyers to make informed decisions.
Scenario 2: Navigating Complex Import Regulations for Enameled Wire
The Problem: International buyers, especially from the Middle East and Europe, often face a labyrinth of import regulations when sourcing enameled wire. This complexity can lead to unexpected delays, increased costs, and even penalties if regulations are not adhered to. For instance, buyers may struggle with tariffs, customs clearance processes, or specific import permits required for electrical components, which can disrupt supply chains and lead to project delays.
The Solution: To navigate these complexities effectively, buyers should engage with a customs broker or trade compliance expert familiar with their specific region’s import regulations. Before placing an order, research the applicable tariffs and necessary documentation required for importing enameled wire. Maintaining open communication with the supplier regarding shipping terms and documentation can also mitigate risks. Additionally, establishing a relationship with local trade authorities can provide insight into any upcoming changes in regulations, allowing buyers to adapt their sourcing strategies proactively.
Scenario 3: Limited Availability of Custom Specifications for Enameled Wire
The Problem: Many B2B buyers require enameled wire with custom specifications tailored to their unique applications. However, they often find that suppliers have a limited range of standard products, which may not meet the specific needs of their projects. This limitation can hinder innovation, as companies may be forced to compromise on product performance or invest in costly modifications later in the production process.
The Solution: To address this pain point, buyers should proactively communicate their specific requirements to potential suppliers. This includes detailing the desired wire diameter, enamel type, insulation properties, and any particular thermal or electrical characteristics. Engaging suppliers early in the design process can lead to collaborative solutions, where suppliers can offer tailored options or even develop custom products. Additionally, buyers can explore partnerships with manufacturers that specialize in custom wire production, ensuring a broader selection of materials that align with their project specifications. By leveraging these relationships, buyers can foster innovation and enhance the performance of their end products.
Strategic Material Selection Guide for enameled wire supplier
What Are the Key Materials for Enameled Wire Suppliers?
When selecting materials for enameled wire, international B2B buyers must consider various factors that affect performance, cost, and compliance with regional standards. Below, we analyze four common materials used in the production of enameled wire, focusing on their properties, advantages, disadvantages, and implications for buyers from Africa, South America, the Middle East, and Europe.
1. Copper: The Traditional Choice for Enameled Wire
Key Properties: Copper is known for its excellent electrical conductivity, thermal conductivity, and ductility. It typically has a temperature rating of up to 200°C, making it suitable for a wide range of applications.
Pros & Cons: The primary advantage of copper is its superior conductivity, which enhances the efficiency of electrical systems. However, it is susceptible to corrosion, particularly in humid environments, which can lead to degradation over time. Additionally, copper is more expensive than some alternatives, which can impact overall project budgets.
Impact on Application: Copper enameled wire is ideal for applications requiring high electrical performance, such as transformers and motors. However, its corrosion sensitivity means that it may not be suitable for outdoor applications without protective coatings.
Considerations for International Buyers: Buyers should ensure compliance with international standards such as ASTM B3 and B8 for copper wire. In regions like Europe and the Middle East, the demand for high-quality copper wire is driven by stringent electrical safety regulations.
2. Aluminum: A Lightweight Alternative
Key Properties: Aluminum offers good electrical conductivity (about 60% that of copper) and is significantly lighter, making it easier to handle and install. It has a temperature rating of around 150°C.
Pros & Cons: The lightweight nature of aluminum reduces shipping costs and makes it easier to work with in large installations. However, its lower conductivity means that larger gauge wires are required for the same electrical performance, which can offset some of the weight advantages. Aluminum is also more prone to oxidation, which can affect performance if not properly coated.
Impact on Application: Aluminum enameled wire is commonly used in overhead power lines and applications where weight is a critical factor. However, its lower conductivity can limit its use in high-performance electrical applications.
Considerations for International Buyers: Buyers in regions with stringent environmental regulations should ensure that aluminum wire meets the relevant standards, such as IEC 60228. Additionally, the cost-effectiveness of aluminum may be appealing in developing markets in Africa and South America.
3. Nickel-Plated Copper: Enhanced Corrosion Resistance
Key Properties: Nickel-plated copper combines the excellent conductivity of copper with a nickel coating that enhances corrosion resistance. It typically maintains a temperature rating similar to that of copper.
Pros & Cons: The primary advantage of nickel-plated copper is its resistance to oxidation and corrosion, making it suitable for harsh environments. However, it is generally more expensive than standard copper wire due to the additional plating process.
Impact on Application: This material is particularly useful in applications exposed to moisture or harsh chemicals, such as industrial motors and marine environments. The enhanced durability can lead to lower maintenance costs over time.
Considerations for International Buyers: Buyers should verify that nickel-plated copper meets standards like ASTM B-488 for plating thickness. Compliance with local regulations regarding electrical safety and environmental impact is crucial, especially in Europe and the Middle East.
4. Silver-Plated Copper: Premium Performance
Key Properties: Silver-plated copper offers the highest electrical conductivity among common enameled wire materials, with a temperature rating similar to copper.
Pros & Cons: The exceptional conductivity of silver makes it ideal for high-frequency applications, such as RF and microwave systems. However, the high cost of silver can be a significant drawback, making it less accessible for budget-conscious projects.
Impact on Application: Silver-plated copper is often used in specialized applications where performance is critical, such as aerospace and telecommunications. The premium cost is justified by the performance benefits in these sectors.
Considerations for International Buyers: Buyers should be aware of the fluctuating market prices for silver and ensure compliance with relevant standards such as ASTM B-486. In regions like Europe, the demand for high-performance materials in technology sectors is growing.
Summary Table of Material Selection for Enameled Wire
Material | Typical Use Case for enameled wire supplier | Key Advantage | Key Disadvantage/Limitation | Relative Cost (Low/Med/High) |
---|---|---|---|---|
Copper | Transformers, motors | Superior electrical conductivity | Corrosion susceptibility | High |
Aluminum | Overhead power lines | Lightweight and cost-effective | Lower conductivity | Medium |
Nickel-Plated Copper | Industrial motors, marine environments | Enhanced corrosion resistance | Higher cost due to plating | High |
Silver-Plated Copper | RF and microwave systems | Highest electrical conductivity | Very high cost | High |
This strategic material selection guide provides international B2B buyers with essential insights into the properties, advantages, and considerations of various materials used in enameled wire. By understanding these factors, buyers can make informed decisions that align with their project requirements and regional standards.
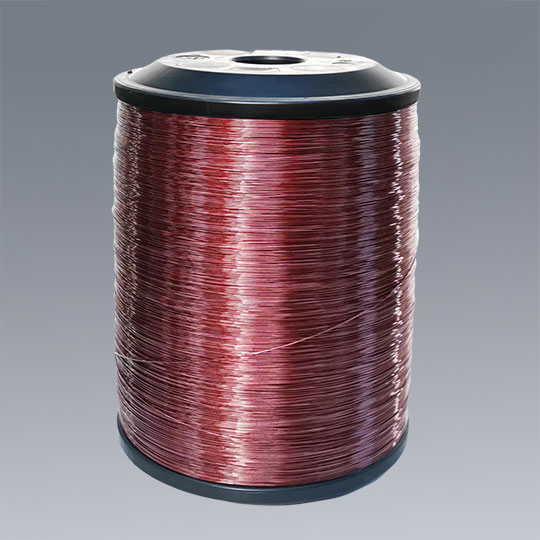
A stock image related to enameled wire supplier.
In-depth Look: Manufacturing Processes and Quality Assurance for enameled wire supplier
What Are the Key Manufacturing Processes for Enameled Wire?
The manufacturing of enameled wire involves several critical stages that ensure the final product meets the high standards required by various industries. The main stages include material preparation, forming, assembly, and finishing. Each stage employs specific techniques that contribute to the wire’s quality and performance.
How is Material Prepared for Enameled Wire Production?
The first step in the manufacturing process is the selection and preparation of the base metal, typically copper or aluminum. The metal is drawn into wire of the desired diameter through a series of dies, ensuring uniformity and consistency. This process often involves annealing, which softens the metal to improve its ductility.
Once the wire is drawn to size, it undergoes surface cleaning to remove any oxides or impurities. This is critical, as any contaminants can affect the adhesion of the enamel insulation later in the process. Typical cleaning methods include acid pickling and electrochemical cleaning, which enhance the wire’s surface quality.
What Techniques Are Used in Forming Enameled Wire?
After preparation, the wire enters the forming stage, where it is coated with an insulating enamel. This is achieved through various methods, including:
- Single-Coat and Multi-Coat Applications: Depending on the application, the wire can be coated with one or more layers of enamel. Multi-coat systems provide additional insulation and thermal resistance.
- Electrostatic Coating: This technique uses an electric charge to ensure an even application of the enamel, which is crucial for maintaining the integrity of the insulation.
- Thermal Curing: Following coating, the wire is heated in an oven to cure the enamel, allowing it to bond effectively to the wire surface.
The choice of technique depends on the desired properties of the final product, such as thermal resistance, flexibility, and electrical conductivity.
How is Assembly Conducted in Enameled Wire Manufacturing?
The assembly stage may involve additional processes such as twisting or bundling wires together, depending on the specific application. For example, in applications requiring higher conductivity, multiple strands of enameled wire may be twisted together to create a composite wire.
Quality control checks are integrated throughout the assembly process. These checks ensure that the wire meets dimensional and aesthetic specifications, which are essential for its performance in end-use applications.
What Finishing Techniques Are Commonly Applied?
Finishing involves final treatments that enhance the wire’s properties. Common techniques include:
- Surface Treatment: This may involve additional coatings to improve corrosion resistance or enhance electrical properties.
- Packaging: Proper packaging is crucial for protecting the wire during transport and storage. It often includes spool winding and moisture-proof wrapping.
What Quality Assurance Standards Should B2B Buyers Consider?
Quality assurance is vital in the production of enameled wire, especially for B2B buyers operating in international markets. Several international and industry-specific standards govern quality assurance practices.
Which International Standards Are Relevant for Enameled Wire?
ISO 9001 is the most recognized quality management standard globally. It outlines criteria for a quality management system, emphasizing a process-oriented approach and customer satisfaction. Adherence to ISO 9001 indicates that a supplier follows standardized procedures to ensure product quality.
Additional standards relevant to specific applications may include:
- CE Marking: Particularly important in Europe, this indicates compliance with health, safety, and environmental protection standards.
- API Standards: For wires used in the oil and gas industry, adherence to American Petroleum Institute (API) standards is critical.
How Are Quality Control Checkpoints Structured?
Quality control in enameled wire manufacturing is structured around several key checkpoints:
-
Incoming Quality Control (IQC): This initial checkpoint verifies the quality of raw materials before they enter the production process. Suppliers must provide material certification to validate compliance with specifications.
-
In-Process Quality Control (IPQC): During the manufacturing process, various tests are conducted to monitor the quality of the wire, including diameter measurements, enamel adhesion tests, and electrical resistance tests.
-
Final Quality Control (FQC): At the end of the production line, the finished enameled wire undergoes comprehensive testing to ensure it meets all specified standards. This may include mechanical testing, thermal cycling tests, and insulation resistance tests.
What Common Testing Methods Are Employed?
Several testing methods are employed to verify the quality of enameled wire:
- Electrical Testing: Measures the insulation resistance and conductivity of the wire.
- Mechanical Testing: Assesses the tensile strength and elongation of the wire.
- Thermal Testing: Evaluates the wire’s performance under high temperatures, ensuring it meets application-specific requirements.
How Can B2B Buyers Verify Supplier Quality Control Processes?
For international B2B buyers, verifying a supplier‘s quality control processes is crucial to ensure product reliability. Here are several strategies:
-
Supplier Audits: Conducting on-site audits allows buyers to directly assess the manufacturing processes and quality control measures in place.
-
Requesting Quality Reports: Suppliers should provide documentation of their quality control processes, including test results and compliance certifications.
-
Third-Party Inspections: Engaging third-party inspection agencies can provide an unbiased assessment of a supplier’s quality assurance practices.
What Nuances Should International Buyers Be Aware Of?
When sourcing enameled wire from suppliers in different regions, it’s essential to consider regional compliance and certification nuances. For example, CE marking is mandatory for products sold in the European Union, while other regions may have different regulatory requirements.
Understanding these regional differences can help B2B buyers avoid compliance issues and ensure the products meet local market standards. Additionally, establishing clear communication with suppliers about quality expectations and compliance requirements can foster stronger partnerships and enhance supply chain reliability.
By understanding the manufacturing processes and quality assurance practices associated with enameled wire, B2B buyers can make informed decisions and select suppliers that meet their specific needs and industry standards.
Practical Sourcing Guide: A Step-by-Step Checklist for ‘enameled wire supplier’
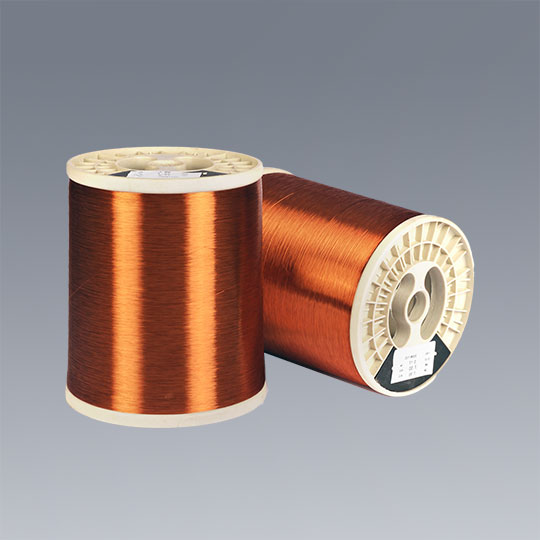
A stock image related to enameled wire supplier.
In the competitive landscape of international sourcing, procuring enameled wire from reliable suppliers is crucial for the success of your business. This checklist serves as a practical guide for B2B buyers, particularly those operating in Africa, South America, the Middle East, and Europe, to streamline the sourcing process effectively.
Step 1: Define Your Technical Specifications
Establishing clear technical specifications is vital for ensuring that the enameled wire meets your operational needs. Consider factors such as wire gauge, insulation type, and thermal resistance. A well-defined specification helps in communicating your requirements effectively to potential suppliers.
Step 2: Conduct Market Research for Enameled Wire Suppliers
Before reaching out to suppliers, perform thorough market research to identify potential candidates. Utilize industry reports, trade shows, and online platforms to gather information on suppliers’ capabilities, market reputation, and product offerings. This step will help you narrow down your options and focus on suppliers that align with your needs.
Step 3: Evaluate Supplier Certifications and Compliance
✅ Verify Supplier Certifications
Ensure that the suppliers you are considering possess relevant certifications, such as ISO 9001 for quality management or UL certification for safety standards. Compliance with international quality standards not only assures product reliability but also minimizes risks associated with non-compliance.
Step 4: Request Samples for Testing
Requesting samples from shortlisted suppliers is a critical step in the sourcing process. Testing samples allows you to assess the quality and performance of the enameled wire under actual operating conditions. Pay attention to factors like coating uniformity and adhesion strength, which are crucial for long-term performance.
Step 5: Assess Supplier Financial Stability
How to Evaluate Supplier Financial Stability?
Review the financial health of potential suppliers by examining their credit ratings and financial statements. A financially stable supplier is less likely to face disruptions that could affect your supply chain. Consider using third-party credit assessment services for a comprehensive analysis.
Step 6: Negotiate Terms and Conditions
Once you have identified a preferred supplier, engage in negotiations to establish favorable terms and conditions. Discuss pricing, payment terms, lead times, and warranty policies. Clear agreements help prevent misunderstandings and ensure a smooth procurement process.
Step 7: Establish a Communication Plan
Effective communication is essential for successful collaboration with your supplier. Develop a communication plan that outlines how often you will check in, what information will be shared, and who the primary contacts will be. This proactive approach can help address issues promptly and maintain a strong working relationship.
By following this checklist, B2B buyers can make informed decisions when sourcing enameled wire suppliers, ensuring product quality and reliability while fostering strong supplier partnerships.
Comprehensive Cost and Pricing Analysis for enameled wire supplier Sourcing
When sourcing enameled wire suppliers, understanding the comprehensive cost structure is essential for making informed purchasing decisions. This analysis dives into the various cost components, price influencers, and actionable tips specifically tailored for international B2B buyers from Africa, South America, the Middle East, and Europe, including regions such as Mexico and the UK.
What Are the Key Cost Components in Enameled Wire Sourcing?
-
Materials: The primary cost driver is the raw materials used in manufacturing enameled wire, which typically include copper or aluminum. The market prices for these metals can fluctuate based on global demand and supply dynamics. Buyers should monitor commodity prices and consider long-term contracts to lock in favorable rates.
-
Labor: Labor costs vary significantly by region, impacting the overall pricing. For instance, suppliers in Europe may have higher labor costs compared to those in parts of Africa or South America. Understanding local wage standards can help buyers gauge the labor component of the pricing structure.
-
Manufacturing Overhead: This encompasses the indirect costs associated with production, including utilities, maintenance, and factory management. Efficient operations can lower overhead, which may be reflected in pricing.
-
Tooling: Custom tooling for specific wire specifications can incur additional costs. Buyers requiring unique dimensions or coatings should expect higher initial tooling expenses, which can be amortized over larger orders.
-
Quality Control (QC): Investment in quality assurance processes ensures that the enameled wire meets industry standards. Suppliers that prioritize QC may charge a premium, but this can lead to lower defect rates and better overall product quality.
-
Logistics: Transportation costs are pivotal, especially for international shipments. Factors such as distance, mode of transport, and shipping terms (Incoterms) can significantly affect pricing. Understanding these elements helps in calculating the total landed cost.
-
Margin: Supplier profit margins will vary based on market competition and the supplier’s positioning. It’s crucial to evaluate if the price reflects the quality and service level offered.
How Do Price Influencers Impact Enameled Wire Sourcing?
-
Volume and Minimum Order Quantity (MOQ): Larger orders often attract discounts, which can significantly reduce the per-unit cost. Buyers should negotiate MOQs that align with their needs while benefiting from bulk pricing.
-
Specifications and Customization: Customized enameled wire (e.g., specific gauge, insulation type) can lead to higher costs. Buyers should clearly define their requirements to avoid unexpected price increases.
-
Materials and Quality Certifications: Suppliers offering higher-grade materials or certifications (like ISO) may charge more, but this can be justified through enhanced reliability and performance.
-
Supplier Factors: The supplier’s reputation, location, and production capabilities can influence pricing. Established suppliers with a track record of quality may command higher prices, but they also reduce risk.
-
Incoterms: The choice of Incoterms (e.g., FOB, CIF) affects cost structure and risk. Buyers should understand the implications of these terms on pricing and liability.
What Are the Best Negotiation Tips for International B2B Buyers?
-
Research and Benchmarking: Conduct market research to understand typical pricing structures and benchmarks. This knowledge empowers buyers during negotiations.
-
Focus on Total Cost of Ownership (TCO): Rather than just the purchase price, consider the TCO, which includes logistics, maintenance, and potential scrap costs. This holistic view can justify a higher upfront investment for better quality products.
-
Leverage Relationships: Building long-term relationships with suppliers can lead to better pricing and terms over time. Loyalty can be a powerful negotiation tool.
-
Be Clear on Requirements: Clearly communicating specifications and expectations can prevent misunderstandings that lead to unexpected costs.
-
Consider Payment Terms: Flexible payment terms can be a bargaining chip. Offering to pay upfront may yield discounts, while extended payment options can help manage cash flow.
Conclusion
In the competitive landscape of enameled wire sourcing, understanding the cost structure and price influencers allows international buyers to make strategic decisions. By applying these insights and negotiation strategies, businesses can optimize their sourcing efforts, ensuring they obtain quality products at the best possible price. Always remember that prices are indicative and can fluctuate based on market conditions, so continuous market monitoring is advisable.
Alternatives Analysis: Comparing enameled wire supplier With Other Solutions
The decision-making process for international B2B buyers often involves evaluating various solutions to determine the best fit for their operational needs. In the context of enameled wire suppliers, it is essential to explore alternative options that may deliver similar benefits or solve comparable challenges. This analysis will compare enameled wire suppliers with alternative technologies such as insulated wire, bare wire, and specialty wire coatings.
Comparison Aspect | Enameled Wire Supplier | Insulated Wire | Bare Wire | Specialty Wire Coatings |
---|---|---|---|---|
Performance | High thermal resistance and electrical efficiency | Good insulation but can be bulky | High conductivity but low insulation | Enhanced durability and corrosion resistance |
Cost | Moderate to high | Low to moderate | Low | High |
Ease of Implementation | Requires specialized handling | Simple to install | Easy to handle | Requires expertise in application |
Maintenance | Low maintenance needs | Moderate maintenance | Low maintenance | Variable based on coating type |
Best Use Case | Motors, transformers, and coils | General electrical wiring | High current applications | Harsh environments or specialized applications |
What are the Pros and Cons of Insulated Wire as an Alternative?
Insulated wire serves as a straightforward alternative to enameled wire, primarily used in general electrical wiring applications. The key advantage of insulated wire is its ease of installation and flexibility. It provides adequate electrical insulation, making it suitable for a wide range of applications. However, it may lack the thermal resistance and compactness that enameled wire offers, making it less efficient in high-performance settings such as motors and transformers.
How Does Bare Wire Compare to Enameled Wire?
Bare wire is known for its excellent conductivity and is often used in high-current applications. The primary benefit of bare wire is its low cost, which makes it attractive for bulk applications. However, it lacks insulation, requiring additional protective measures to prevent short circuits and ensure safety. This can lead to increased installation complexity and long-term maintenance costs, especially in environments susceptible to corrosion or physical damage.
What Advantages Do Specialty Wire Coatings Offer?
Specialty wire coatings provide a unique alternative by enhancing the durability and corrosion resistance of standard wire types. These coatings can be tailored to specific applications, making them suitable for harsh environments. However, the cost of specialty wire coatings can be significantly higher than that of enameled wire, and the application process may require specialized expertise. This can limit their use to particular industries where durability is paramount, such as aerospace or marine sectors.
How Should B2B Buyers Choose the Right Solution?
When selecting the appropriate solution, B2B buyers should consider their specific operational needs and constraints. Factors such as performance requirements, budget limitations, and the environment in which the wire will be used are crucial in making an informed decision. While enameled wire offers excellent performance for high-temperature and high-efficiency applications, alternatives like insulated wire, bare wire, and specialty coatings can provide cost-effective solutions depending on the specific use case. Assessing these alternatives against the operational context will help buyers make the best choice for their projects.
Essential Technical Properties and Trade Terminology for enameled wire supplier
What Are the Essential Technical Properties of Enameled Wire?
When sourcing enameled wire, it is crucial for B2B buyers to understand the key technical properties that define the quality and suitability of the wire for specific applications. Here are some critical specifications to consider:
-
Material Grade
– Enameled wire is typically made from copper or aluminum. The material grade influences its conductivity, tensile strength, and overall performance. High-grade materials ensure better electrical properties and durability, which are vital for applications in motors and transformers. -
Wire Gauge
– Wire gauge indicates the thickness of the wire. This measurement affects both the current-carrying capacity and the flexibility of the wire. A lower gauge number signifies a thicker wire, which can handle higher current loads, making it essential for high-power applications. -
Insulation Thickness
– The insulation thickness around the wire plays a significant role in its resistance to electrical leakage and heat dissipation. A thicker insulation layer provides better protection against short circuits and improves the wire’s longevity, especially in high-temperature environments. -
Thermal Class
– This specification refers to the maximum operating temperature that the wire can withstand without degrading. Common thermal classes include 130°C (Class B), 155°C (Class F), and 180°C (Class H). Choosing the right thermal class is crucial for applications involving high heat. -
Tolerance
– Tolerance defines the allowable deviation in wire dimensions from the specified measurements. It is essential for ensuring compatibility with other components in electrical systems. Tight tolerances are particularly important in precision applications, where even minor variations can affect performance. -
Coating Type
– Enameled wires can have different types of coatings, such as polyurethane, polyester, or polyamide. Each coating type offers unique properties, such as chemical resistance and flexibility. Understanding the coating type helps buyers select the right wire for their specific environmental conditions.
What Are Common Trade Terms Used in Enameled Wire Procurement?
Understanding industry jargon is equally important for effective communication and negotiation in the B2B landscape. Here are some common trade terms that buyers should be familiar with:
-
OEM (Original Equipment Manufacturer)
– This term refers to companies that produce parts or equipment that may be marketed by another manufacturer. Knowing whether a supplier operates as an OEM helps buyers assess the reliability and quality of the wire being sourced. -
MOQ (Minimum Order Quantity)
– MOQ indicates the smallest amount of product that a supplier is willing to sell. Understanding MOQ is crucial for buyers to manage inventory and cash flow effectively, especially when evaluating suppliers from different regions. -
RFQ (Request for Quotation)
– An RFQ is a formal process where buyers request quotes from suppliers for specific products. Providing detailed specifications in an RFQ allows suppliers to offer accurate pricing and terms, facilitating better decision-making. -
Incoterms (International Commercial Terms)
– These are standardized trade terms that define the responsibilities of buyers and sellers in international transactions. Familiarity with Incoterms, such as FOB (Free on Board) or CIF (Cost, Insurance, and Freight), helps buyers understand shipping costs and risks associated with their orders. -
Lead Time
– Lead time refers to the time taken from placing an order to receiving the product. Understanding lead times is essential for planning and inventory management, especially in industries where timely delivery is critical. -
Certification Standards
– Various certification standards, such as ISO 9001 or RoHS compliance, indicate the quality and safety of the enameled wire. Buyers should ensure that their suppliers meet relevant certification requirements to guarantee product reliability and compliance with industry regulations.
By understanding these technical properties and trade terms, B2B buyers can make informed decisions when sourcing enameled wire, ultimately enhancing the efficiency and effectiveness of their procurement processes.
Navigating Market Dynamics and Sourcing Trends in the enameled wire supplier Sector
What Are the Key Market Dynamics and Sourcing Trends for Enameled Wire Suppliers?
The global enameled wire market is experiencing significant growth driven by the expansion of industries such as automotive, electronics, and renewable energy. As international B2B buyers from regions like Africa, South America, the Middle East, and Europe look to source enameled wire, they should be aware of several key trends shaping the market landscape.
Firstly, technological advancements are enhancing production processes. Suppliers are increasingly adopting automation and smart manufacturing technologies, which improve efficiency and reduce costs. This trend is particularly relevant for buyers seeking cost-effective solutions without compromising quality. Furthermore, the demand for high-performance enameled wires is rising, driven by the need for lightweight and durable materials in electric vehicles and renewable energy applications.
Secondly, the focus on local sourcing is gaining traction. International buyers are encouraged to explore regional suppliers to mitigate risks associated with global supply chain disruptions. This shift not only supports local economies but also reduces shipping costs and lead times. Additionally, sustainability is becoming a critical factor in sourcing decisions, with buyers increasingly prioritizing suppliers who demonstrate environmentally responsible practices.
How Is Sustainability Influencing the Enameled Wire Supplier Sector?
Sustainability and ethical sourcing are paramount in today’s B2B landscape, particularly for enameled wire suppliers. The environmental impact of manufacturing processes, including waste generation and energy consumption, is under scrutiny. Buyers are now more inclined to partner with suppliers who implement eco-friendly practices, such as utilizing recycled materials and reducing carbon footprints.
Ethical supply chains are crucial for fostering trust and transparency. Suppliers who are certified with ‘green’ credentials, such as ISO 14001 for environmental management or certifications related to responsible sourcing, can provide buyers with assurance regarding their commitment to sustainability. This is especially important for companies in Europe and North America, where regulatory frameworks are increasingly stringent.
Moreover, the demand for environmentally friendly materials is driving innovation in the sector. Suppliers are developing bio-based or low-emission enamels, which can significantly lower the environmental impact of enameled wires. By prioritizing sustainability in their sourcing strategies, buyers can align with global initiatives aimed at reducing environmental harm while enhancing their brand image.
What Is the Historical Context of Enameled Wire Development?
The evolution of the enameled wire sector dates back to the early 20th century, when the need for insulated wiring solutions became apparent with the rise of electrical applications. Initially, enameled wires were primarily used in electric motors and transformers. Over the decades, advancements in materials science led to the development of more efficient and heat-resistant enamel coatings, enhancing the performance of these wires.
As industries expanded and diversified, the applications for enameled wires grew to include telecommunications, consumer electronics, and renewable energy sectors. Today, these wires are indispensable in various electrical devices, playing a crucial role in energy efficiency and performance. Understanding this historical context can help international B2B buyers appreciate the technological progress that has shaped the current market dynamics and sourcing opportunities.
In conclusion, navigating the enameled wire supplier sector requires an awareness of market dynamics, sustainability trends, and historical context. By leveraging these insights, international B2B buyers can make informed sourcing decisions that align with their operational goals and values.
Frequently Asked Questions (FAQs) for B2B Buyers of enameled wire supplier
-
How can I ensure the quality of enameled wire before purchasing?
To guarantee the quality of enameled wire, request samples from potential suppliers and conduct tests for durability, insulation resistance, and thermal stability. Look for suppliers who provide certification for their products, such as ISO or ASTM standards. Additionally, consider conducting a factory audit to assess their production processes and quality control measures. Engaging third-party inspection services can also help verify the quality before bulk purchases. -
What are the key factors to consider when choosing an enameled wire supplier?
When selecting an enameled wire supplier, evaluate their industry experience, reputation, and product range. Assess their ability to meet specific customization requirements, such as wire gauge and coating types. Investigate their compliance with international standards and certifications. Additionally, consider their logistical capabilities, including shipping options and delivery timelines, to ensure they align with your business needs. -
What are the typical minimum order quantities (MOQs) for enameled wire?
Minimum order quantities for enameled wire can vary significantly by supplier and the specific type of wire. Generally, MOQs range from 100 kg to several tons. Suppliers may offer lower MOQs for standard products but require higher quantities for customized orders. It’s advisable to discuss your requirements directly with potential suppliers to find a mutually beneficial arrangement. -
What payment terms should I negotiate with my enameled wire supplier?
Negotiating payment terms is crucial for managing cash flow. Common terms include partial upfront payments (e.g., 30%) with the balance due upon delivery or after inspection. Consider negotiating payment through letters of credit or escrow services to ensure security for both parties. Always clarify the currency used, as international transactions can involve currency fluctuations. -
How can I customize enameled wire to fit my specific application?
Customization of enameled wire is typically available, including variations in wire gauge, insulation materials, and thermal ratings. Communicate your specific needs to the supplier, providing detailed specifications and application requirements. Many suppliers can offer tailored solutions, but be prepared to meet higher MOQs and longer lead times for customized products. -
What logistics considerations should I keep in mind when sourcing enameled wire internationally?
When sourcing enameled wire internationally, consider shipping methods, costs, and delivery timelines. Be aware of customs regulations in your country and the supplier’s country, as these can impact delivery schedules. It’s also essential to verify insurance coverage for goods in transit. Working with a logistics partner experienced in international shipping can help streamline the process. -
What are the common quality assurance practices for enameled wire suppliers?
Reputable enameled wire suppliers implement various quality assurance practices, including raw material inspections, in-process quality checks, and final product testing. Look for suppliers that adhere to recognized quality management systems, such as ISO 9001. Request documentation of their quality control procedures and any relevant testing results to ensure compliance with your standards. -
How do I handle disputes with my enameled wire supplier?
To effectively handle disputes, establish clear communication channels and document all agreements and transactions. If issues arise, address them promptly and professionally, aiming for a resolution through dialogue. If necessary, refer to the terms outlined in your contract regarding dispute resolution mechanisms, such as mediation or arbitration. Engaging a legal expert familiar with international trade laws can also be beneficial if disputes escalate.
Important Disclaimer & Terms of Use
⚠️ Important Disclaimer
The information provided in this guide, including content regarding manufacturers, technical specifications, and market analysis, is for informational and educational purposes only. It does not constitute professional procurement advice, financial advice, or legal advice.
While we have made every effort to ensure the accuracy and timeliness of the information, we are not responsible for any errors, omissions, or outdated information. Market conditions, company details, and technical standards are subject to change.
B2B buyers must conduct their own independent and thorough due diligence before making any purchasing decisions. This includes contacting suppliers directly, verifying certifications, requesting samples, and seeking professional consultation. The risk of relying on any information in this guide is borne solely by the reader.
Strategic Sourcing Conclusion and Outlook for enameled wire supplier
In the evolving landscape of international trade, strategic sourcing of enameled wire is crucial for businesses seeking to enhance their supply chain efficiency and product quality. By prioritizing relationships with reliable suppliers across regions such as Africa, South America, the Middle East, and Europe, companies can leverage competitive pricing, access advanced technologies, and ensure compliance with local regulations.
What Are the Key Benefits of Strategic Sourcing for Enameled Wire?
The key takeaways for B2B buyers include the importance of conducting thorough market research to identify reputable suppliers, understanding the nuances of international logistics, and fostering long-term partnerships that can adapt to changing market conditions. Strategic sourcing not only mitigates risks but also enables businesses to innovate and respond swiftly to customer demands.
How Can International Buyers Prepare for Future Challenges in Sourcing?
As we look to the future, buyers should remain agile and proactive in their sourcing strategies. Embracing digital tools for supplier evaluation and performance monitoring will enhance decision-making capabilities. By investing in these strategies, international B2B buyers can position themselves for success in a competitive marketplace.
Engage with your suppliers today to explore how strategic sourcing can drive value and growth for your business in the global economy.