Introduction: Navigating the Global Market for knitting machine manufacturer
In today’s competitive landscape, sourcing high-quality knitting machines can pose significant challenges for international B2B buyers, especially those operating in diverse markets across Africa, South America, the Middle East, and Europe. Buyers must navigate a complex web of suppliers, varying technologies, and regional compliance standards to ensure they invest in machinery that enhances productivity and meets specific manufacturing needs. This guide serves as a comprehensive resource for understanding the global market for knitting machine manufacturers, addressing everything from types of knitting machines and their applications to effective supplier vetting processes and cost considerations.
By exploring the intricacies of knitting technology, this guide empowers B2B buyers to make informed purchasing decisions that align with their operational goals. We delve into the different types of knitting machines available, including flat, circular, and warp knitting machines, and their respective applications in fashion, textiles, and industrial sectors. Furthermore, we provide actionable insights on evaluating suppliers, understanding pricing structures, and recognizing the importance of after-sales support and maintenance.
Whether you are a manufacturer in Brazil seeking to enhance your production capabilities or a textile company in Vietnam looking to upgrade your machinery, this guide is designed to equip you with the knowledge and tools necessary for successful sourcing in the global knitting machine market.
Understanding knitting machine manufacturer Types and Variations
Type Name | Key Distinguishing Features | Primary B2B Applications | Brief Pros & Cons for Buyers |
---|---|---|---|
Flat Knitting Machines | Produce flat fabric, ideal for garments like sweaters | Fashion, sportswear, home textiles | Pros: Versatile, good for detailed patterns. Cons: Slower production rates. |
Circular Knitting Machines | Create tubular fabric, suitable for seamless products | Hosiery, t-shirts, activewear | Pros: High-speed production, less fabric waste. Cons: Limited to tubular designs. |
Warp Knitting Machines | Use warp yarns, great for complex textiles | Industrial textiles, upholstery | Pros: Strong, stretchable fabrics. Cons: Higher initial investment. |
Computerized Knitting Machines | Automated control for precision knitting | High-end fashion, technical textiles | Pros: High accuracy, customizable designs. Cons: Requires technical expertise. |
Specialty Knitting Machines | Designed for specific applications (e.g., lace, ribbing) | Niche markets, specialty textiles | Pros: Tailored for unique products. Cons: Limited versatility, higher costs. |
What Are the Key Characteristics of Flat Knitting Machines?
Flat knitting machines are designed to produce flat fabric, making them ideal for crafting garments such as sweaters and cardigans. These machines can create intricate designs and patterns, offering versatility in fabric thickness and texture. For B2B buyers, the primary consideration is the machine’s ability to handle various yarn types and its production speed, which may be slower compared to other types but compensates with high-quality outputs.
How Do Circular Knitting Machines Benefit B2B Buyers?
Circular knitting machines are engineered to produce seamless tubular fabric, making them perfect for applications like hosiery and t-shirts. Their high-speed capabilities significantly reduce production time and material waste, making them cost-effective for large-scale production. Buyers should consider the machine’s capacity and the types of fabrics it can produce, as these factors impact overall efficiency and product quality.
What Advantages Do Warp Knitting Machines Offer?
Warp knitting machines utilize warp yarns to create complex textiles, which are particularly strong and stretchable. They are commonly used in industrial textiles and upholstery. For B2B buyers, the initial investment may be higher, but the durability and versatility of the fabrics produced can lead to long-term savings. Buyers should evaluate the machine’s adaptability to different yarns and the range of products it can create.
Why Invest in Computerized Knitting Machines?
Computerized knitting machines offer automated control, enhancing precision in the knitting process. They are ideal for high-end fashion and technical textiles, enabling the creation of customized designs with high accuracy. While these machines require a higher level of technical expertise to operate, the benefits of increased efficiency and reduced error rates make them a worthwhile investment for B2B buyers looking to innovate in their product offerings.
What Are the Considerations for Specialty Knitting Machines?
Specialty knitting machines are tailored for specific applications such as lace or ribbing, making them suitable for niche markets. While they provide exceptional quality and detail in their output, their limited versatility and higher costs can be drawbacks for some buyers. When considering these machines, B2B buyers should assess their target market demands and the potential return on investment based on the unique products they aim to create.
Related Video: POWER FLAT KNITTING MACHINE (V -BED)Computerized Flat Knitting Machine
Key Industrial Applications of knitting machine manufacturer
Industry/Sector | Specific Application of knitting machine manufacturer | Value/Benefit for the Business | Key Sourcing Considerations for this Application |
---|---|---|---|
Textile Manufacturing | Production of knitted fabrics and garments | Enhances production efficiency and product quality | Machine durability, production speed, and maintenance support |
Fashion Industry | Customizable knitwear design | Offers flexibility in design and rapid prototyping | Technology for design integration and sample production speed |
Sportswear and Activewear | High-performance knitted sports fabrics | Improves comfort and performance of athletic wear | Material compatibility, moisture-wicking properties, and elasticity |
Medical Textiles | Manufacturing of knitted medical garments | Provides comfort and functionality in healthcare | Compliance with medical standards and fabric safety certifications |
Home Textiles | Production of knitted home furnishings | Enhances aesthetic appeal and durability of products | Customization options and colorfastness of the fabrics |
What are the Key Applications of Knitting Machines in Textile Manufacturing?
In the textile manufacturing sector, knitting machines are pivotal for producing a wide array of knitted fabrics and garments. These machines allow manufacturers to create intricate patterns and textures, which are essential for meeting diverse market demands. By investing in advanced knitting technology, businesses can significantly enhance production efficiency and ensure high-quality output. International buyers should prioritize sourcing machines that offer durability and require minimal maintenance to reduce operational downtime.
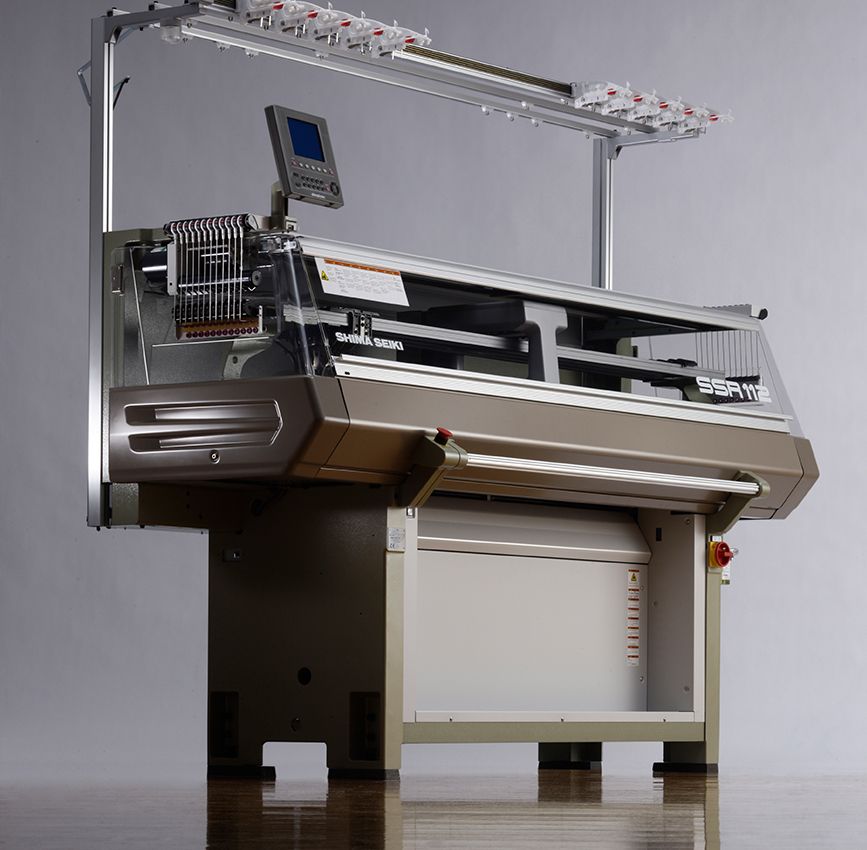
A stock image related to knitting machine manufacturer.
How Do Knitting Machines Support the Fashion Industry?
The fashion industry benefits greatly from the versatility of knitting machines, which enable the creation of customizable knitwear designs. Designers can quickly prototype various styles, ensuring that their collections remain trendy and appealing. This rapid design capability allows brands to respond swiftly to market trends, ultimately leading to increased sales. Buyers should look for knitting machines that integrate seamlessly with design software, facilitating a smooth workflow from concept to production.
What are the Advantages of Knitting Machines in Sportswear Production?
In the sportswear and activewear industry, knitting machines play a crucial role in producing high-performance fabrics that enhance the comfort and performance of athletic clothing. These machines can create specialized fabrics that are breathable, moisture-wicking, and elastic, catering to the specific needs of athletes. For international buyers, sourcing machines that can handle a variety of materials while ensuring consistent quality is essential for maintaining a competitive edge in the market.
How are Knitting Machines Used in Medical Textiles?
Knitting machines are increasingly utilized in the production of medical textiles, including garments that provide comfort and support to patients. These machines allow for the creation of fabrics that meet strict medical standards, ensuring safety and functionality. Buyers in this sector must consider compliance with healthcare regulations and the need for fabric safety certifications when sourcing knitting machines.
What Role do Knitting Machines Play in Home Textile Production?
In the home textiles sector, knitting machines are essential for producing a range of knitted products, such as blankets, cushions, and upholstery fabrics. These machines provide manufacturers with the ability to create durable and aesthetically pleasing items that enhance home décor. When sourcing knitting machines for home textiles, buyers should prioritize customization options and the colorfastness of the fabrics to ensure long-lasting quality and appeal.
Related Video: Circular Knitting Process ।। Types of Circular knitting Machine and Uses
3 Common User Pain Points for ‘knitting machine manufacturer’ & Their Solutions
Scenario 1: Navigating Complex Specifications for Knitting Machines
The Problem: B2B buyers often face challenges in understanding the intricate specifications and capabilities of various knitting machines. This lack of clarity can lead to purchasing equipment that does not meet their production needs, resulting in wasted investment and operational delays. For example, a textile manufacturer in Brazil may require a machine that can handle multiple yarn types and gauge settings, but without clear guidance, they may end up with a machine designed for a different application.
The Solution: To overcome this challenge, buyers should engage directly with manufacturers to discuss their specific production requirements. It is essential to prepare a detailed list of needs, including yarn types, desired production speed, and the complexity of patterns. Additionally, requesting samples of knitted fabrics produced on different machines can provide invaluable insights into their performance. Buyers should also consider utilizing online resources and forums dedicated to the knitting industry to gather feedback from other users regarding the machines they are considering. By leveraging this information, buyers can make informed decisions that align with their production goals.
Scenario 2: Managing Downtime Due to Equipment Failures
The Problem: Unexpected machine breakdowns can lead to significant downtime in production, causing delays in fulfilling orders and impacting overall profitability. For instance, a knitting company in South Africa may experience frequent failures due to inadequate maintenance schedules or lack of spare parts availability. This situation not only disrupts operations but can also damage customer relationships if orders are not met on time.
The Solution: To mitigate this issue, B2B buyers should prioritize preventive maintenance plans when purchasing knitting machines. This includes negotiating service agreements that cover regular maintenance checks and ensuring a robust supply chain for spare parts. Buyers can also invest in training for their staff on basic troubleshooting and maintenance practices to reduce reliance on external technicians. Establishing a relationship with the manufacturer for direct access to support and technical assistance can also help in quickly addressing issues as they arise. By implementing these strategies, buyers can significantly reduce downtime and maintain smooth production flows.
Scenario 3: Ensuring Compliance with International Standards
The Problem: B2B buyers often struggle with ensuring that their knitting machines comply with international quality and safety standards, especially when importing from manufacturers in different regions. For example, a textile manufacturer in the Middle East may find that a machine meets local standards but does not align with EU regulations, creating complications for exporting their products.
The Solution: To navigate compliance issues, buyers should conduct thorough research on the relevant regulations for their target markets before making a purchase. This includes understanding the certifications required for machinery in both local and international contexts. Engaging with third-party consultants who specialize in compliance can also provide guidance on necessary modifications or certifications needed for the machines. Additionally, buyers should request documentation from manufacturers that demonstrate compliance with international standards. By proactively addressing these compliance concerns, buyers can ensure that their operations remain within legal frameworks and avoid costly penalties or delays in market entry.
Strategic Material Selection Guide for knitting machine manufacturer
What Are the Key Materials Used in Knitting Machine Manufacturing?
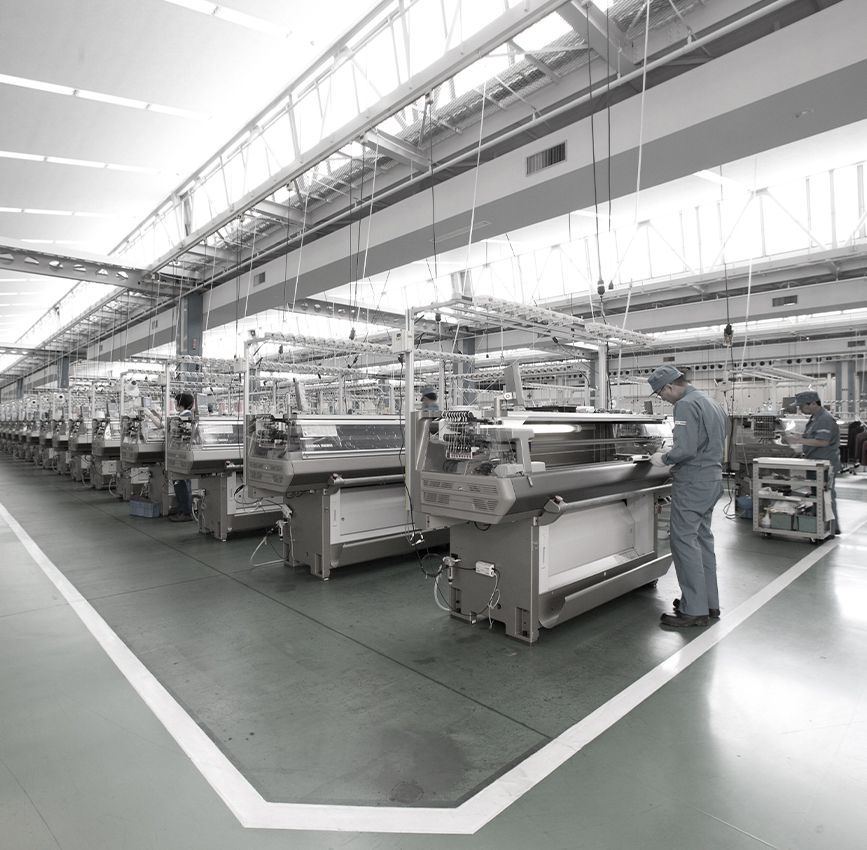
A stock image related to knitting machine manufacturer.
When selecting materials for knitting machines, manufacturers must consider several factors that affect performance, durability, and cost. Here, we analyze four common materials used in the manufacturing of knitting machines, focusing on their properties, advantages, disadvantages, and implications for international B2B buyers.
How Does Steel Impact Knitting Machine Performance?
Steel is a widely used material in knitting machines due to its excellent strength and durability. It typically offers high tensile strength, making it suitable for components that experience significant stress. Steel’s corrosion resistance can vary depending on the type (e.g., stainless steel vs. carbon steel), which is crucial for machines operating in humid or corrosive environments.
Pros: Steel components are known for their longevity and ability to withstand high operational pressures, making them ideal for heavy-duty applications. They are also relatively cost-effective compared to high-performance alloys.
Cons: The primary drawback is that steel can be heavy, which may affect the overall weight of the knitting machine. Additionally, it may require more complex manufacturing processes, such as machining or heat treatment, which can increase production time and costs.
Considerations for Buyers: International buyers should ensure compliance with local standards, such as ASTM for the U.S. or DIN for Europe. Buyers in humid regions should prioritize stainless steel to avoid corrosion issues.
What Role Does Aluminum Play in Knitting Machines?
Aluminum is another popular material, particularly for parts that require a lightweight yet strong structure. It has a good strength-to-weight ratio and excellent corrosion resistance, making it suitable for various components in knitting machines.
Pros: The lightweight nature of aluminum allows for easier handling and installation, which can reduce labor costs. Its resistance to corrosion also means less maintenance is required over time.
Cons: Aluminum tends to be more expensive than steel, and while it is strong, it may not be suitable for high-stress applications where steel would be more appropriate. Additionally, it can be less durable under extreme conditions.
Considerations for Buyers: Buyers from regions with high temperatures should consider aluminum’s performance under heat. Compliance with international standards is essential, especially for parts that may be exposed to varying environmental conditions.
How Does Plastic Influence Knitting Machine Design?
Plastic materials, such as polycarbonate and nylon, are increasingly used in knitting machines for components like gears and housings. They offer good resistance to wear and can be manufactured in various colors and shapes.
Pros: Plastics are lightweight and can be molded into complex shapes, allowing for innovative designs. They are also resistant to corrosion and can be cost-effective for mass production.
Cons: The main limitation of plastics is their lower strength compared to metals, which may not make them suitable for all applications. They can also degrade over time when exposed to UV light or extreme temperatures.
Considerations for Buyers: Buyers should ensure that the chosen plastic meets relevant standards for mechanical properties, especially in high-stress applications. Understanding the environmental impact of plastics is also increasingly important for buyers in Europe and other regions focused on sustainability.
What Are the Benefits of Composite Materials in Knitting Machines?
Composite materials, combining fibers and resins, are gaining traction in knitting machine manufacturing. They offer unique properties that can enhance performance.
Pros: Composites are lightweight yet strong, providing excellent fatigue resistance. They can be engineered to meet specific performance criteria, making them versatile for various applications.
Cons: The primary drawback is the higher cost of composite materials compared to metals and plastics. Additionally, manufacturing processes can be more complex, requiring specialized equipment and expertise.
Considerations for Buyers: International buyers should consider the availability of composite materials in their regions and their compliance with local regulations. Understanding the lifecycle and recyclability of composites is also critical for environmentally conscious buyers.
Summary Table of Material Selection for Knitting Machines
Material | Typical Use Case for knitting machine manufacturer | Key Advantage | Key Disadvantage/Limitation | Relative Cost (Low/Med/High) |
---|---|---|---|---|
Steel | Structural components, frames | High strength and durability | Heavy weight, complex manufacturing | Medium |
Aluminum | Lightweight parts, casings | Lightweight, corrosion-resistant | Higher cost, less durable under stress | High |
Plastic | Gears, housings | Lightweight, moldable | Lower strength, UV degradation | Low |
Composite | Specialized components | Lightweight, customizable | Higher cost, complex manufacturing | High |
This strategic material selection guide provides a comprehensive overview for international B2B buyers, enabling informed decisions that align with their operational needs and regional standards.
In-depth Look: Manufacturing Processes and Quality Assurance for knitting machine manufacturer
What Are the Main Stages of Manufacturing Knitting Machines?
Manufacturing knitting machines involves several crucial stages that ensure the production of high-quality and reliable equipment. Understanding these stages is vital for international B2B buyers, especially those from regions like Africa, South America, the Middle East, and Europe, as it informs purchasing decisions and supplier evaluations.
Material Preparation: How Are Raw Materials Selected and Processed?
The first step in the manufacturing process is material preparation. Knitting machines typically require high-quality metals, plastics, and electronic components. Suppliers should provide certifications for these materials, ensuring they meet international standards for durability and performance. Key processes in material preparation include:
- Material Sourcing: Manufacturers often work with multiple suppliers to ensure the quality and availability of raw materials. B2B buyers should inquire about the sourcing strategy and supplier relationships.
- Material Inspection: Incoming materials undergo rigorous inspections (Incoming Quality Control, IQC) to verify compliance with specifications. Buyers should request documentation of these inspections to ensure quality assurance.
Forming: What Techniques Are Used to Shape Components?
The forming stage involves converting raw materials into parts through various techniques. Common methods include:
- Machining: Precision machining is used to shape metal parts, ensuring they meet exact specifications. This process is critical for components that require high precision, such as needle beds and cam systems.
- Injection Molding: For plastic components, injection molding is a common method. This technique is efficient and allows for complex shapes, which are essential in modern knitting machines.
B2B buyers should assess the capabilities of manufacturers regarding forming techniques, ensuring they can meet specific design requirements.
Assembly: How Are Knitting Machines Assembled and Tested?
After forming, the assembly process begins. This stage is vital for ensuring that all components fit and function together seamlessly. Key aspects include:
- Modular Assembly Lines: Many manufacturers use modular assembly lines, allowing for flexibility and efficiency. This approach can reduce lead times, which is crucial for B2B buyers looking to meet production schedules.
- Initial Testing: During assembly, initial functionality tests are performed to catch any defects early. This includes checking electronic components and mechanical functions.
B2B buyers should inquire about the assembly process and the testing methods employed to ensure that machines meet performance standards.
Finishing: What Quality Control Measures Are Implemented?
The finishing stage involves final touches, including painting, coating, and additional testing. This stage is essential for the aesthetic and functional quality of the machines. Key activities include:
- Surface Treatment: Components may undergo surface treatment to enhance durability and resistance to wear.
- Final Quality Checks: Before shipping, final quality checks (Final Quality Control, FQC) ensure that the machines meet all specifications. Buyers should request information on these checks.
What International Standards and Quality Assurance Practices Are Relevant?
Quality assurance is a critical component of knitting machine manufacturing. International standards provide a framework for ensuring product quality and safety. Here are some essential standards and practices:
Which International Standards Should B2B Buyers Be Aware Of?
-
ISO 9001: This standard focuses on quality management systems and is crucial for manufacturers. It ensures that companies consistently meet customer requirements and enhance satisfaction. Buyers should look for ISO 9001 certification as a mark of quality.
-
CE Marking: For buyers in Europe, CE marking indicates compliance with EU safety and environmental regulations. It is essential for ensuring that products can be legally sold within the EU.
-
API Standards: If the knitting machines are used in specialized applications (e.g., industrial textiles), adherence to API standards may also be relevant.
What Are the Key Quality Control Checkpoints in Manufacturing?
Quality control checkpoints are integral to the manufacturing process. B2B buyers should be familiar with the following checkpoints:
- Incoming Quality Control (IQC): Inspects raw materials before production to ensure they meet specifications.
- In-Process Quality Control (IPQC): Monitors production processes to catch defects early. This includes testing during the forming and assembly stages.
- Final Quality Control (FQC): Conducts final inspections and tests before shipment to ensure that the finished product meets all requirements.
How Can B2B Buyers Verify Supplier Quality Control Practices?
Verifying supplier quality control practices is crucial for international B2B buyers. Here are actionable steps to ensure that potential suppliers maintain high standards:
What Are the Best Practices for Conducting Supplier Audits?
-
On-Site Audits: Conducting on-site audits allows buyers to evaluate the manufacturing processes and quality control measures firsthand. This assessment should include reviewing documentation and observing operations.
-
Requesting Quality Reports: Suppliers should provide detailed quality reports, including data on inspections and tests conducted throughout the manufacturing process.
-
Engaging Third-Party Inspectors: Utilizing third-party inspection services can provide an unbiased assessment of a supplier’s quality control practices. This step is particularly beneficial for buyers in regions with less established manufacturing standards.
What Nuances Should International Buyers Consider?
B2B buyers from Africa, South America, the Middle East, and Europe should be aware of regional differences in manufacturing practices and standards. Factors such as local regulations, cultural attitudes towards quality, and the availability of skilled labor can impact the manufacturing and quality assurance processes. Understanding these nuances can help buyers make informed decisions and establish strong partnerships with suppliers.
Conclusion: Ensuring Quality in Knitting Machine Procurement
Understanding the manufacturing processes and quality assurance practices of knitting machine manufacturers is vital for B2B buyers. By focusing on material preparation, forming, assembly, and finishing stages, along with adhering to international standards, buyers can ensure they procure reliable and high-quality equipment. Verifying supplier practices through audits and reports adds another layer of assurance, fostering successful international business relationships.
Practical Sourcing Guide: A Step-by-Step Checklist for ‘knitting machine manufacturer’
This sourcing guide provides a practical checklist for international B2B buyers looking to procure knitting machines from manufacturers. The steps outlined below will help you navigate the complex landscape of supplier selection, ensuring you make informed decisions that align with your business needs.
Step 1: Define Your Technical Specifications
Before initiating the sourcing process, clearly outline your technical requirements. This includes the types of knitting machines you need, their production capacity, and any specific features such as automation or compatibility with different yarn types.
– Considerations: Determine if you require specialized machines for specific fabrics or if standard options will suffice.
Step 2: Conduct Market Research
Understanding the market landscape is critical. Investigate various manufacturers, their product offerings, and geographical locations to identify potential suppliers that meet your needs.
– Action Items: Utilize industry reports, trade publications, and online platforms to gather insights about the latest trends and innovations in knitting machines.
Step 3: Evaluate Potential Suppliers
Before committing, it’s crucial to vet suppliers thoroughly. Request company profiles, product catalogs, and references from buyers in similar industries or regions.
– Assessment Criteria: Look for suppliers with a solid track record of reliability and quality. Don’t hesitate to ask for case studies showcasing their previous work.
Step 4: Verify Certifications and Compliance
Ensure that potential manufacturers adhere to industry standards and possess relevant certifications. This is particularly important for buyers in regions with stringent regulations.
– Key Certifications: Look for ISO certifications, CE marking, or any local compliance documents that demonstrate the manufacturer’s commitment to quality and safety.
Step 5: Request Samples and Demonstrations
Once you have shortlisted potential suppliers, request samples of their machines or demonstrations of their capabilities. This firsthand experience will allow you to assess the quality and functionality of the machines.
– What to Observe: Pay attention to the machine’s ease of use, maintenance requirements, and overall build quality during demonstrations.
Step 6: Understand Pricing and Payment Terms
Discuss pricing structures and payment terms with potential suppliers. A transparent pricing model helps avoid unexpected costs later in the procurement process.
– Considerations: Inquire about bulk purchase discounts, warranty terms, and after-sales support, as these can significantly impact your overall investment.
Step 7: Evaluate After-Sales Support and Warranty
After-sales support is critical for ensuring the longevity and efficiency of your knitting machines. Confirm what kind of support the manufacturer offers post-purchase.
– Support Aspects: Check for available training, maintenance services, and the length and terms of the warranty provided.
By following this step-by-step checklist, international B2B buyers can effectively navigate the sourcing process for knitting machines, ensuring they select the right manufacturers that align with their operational needs and strategic goals.
Comprehensive Cost and Pricing Analysis for knitting machine manufacturer Sourcing
What Are the Key Cost Components in Knitting Machine Manufacturing?
When sourcing knitting machines, understanding the comprehensive cost structure is essential for international B2B buyers. The primary cost components include:
-
Materials: This is often the largest portion of the cost. High-quality components such as steel, electronics, and specialized yarns can significantly affect the final price. Buyers should consider the trade-offs between quality and cost, especially when sourcing from different regions.
-
Labor: Labor costs vary widely across regions. Countries with lower labor costs, such as some in South America or Africa, may offer competitive pricing but could lack skilled labor. Conversely, European manufacturers might have higher labor costs but provide superior craftsmanship and expertise.
-
Manufacturing Overhead: This includes costs related to utilities, maintenance, and factory operation. Efficient manufacturing processes can reduce overhead, impacting overall pricing. International buyers should inquire about the manufacturer’s operational efficiency.
-
Tooling: Custom tooling for knitting machines can be a significant upfront investment. Buyers should assess whether the tooling costs are included in the quoted price and what implications this has for customization.
-
Quality Control (QC): Ensuring that machines meet quality standards involves additional costs. Manufacturers with robust QC processes may charge more, but this can lead to lower defect rates and better long-term performance.
-
Logistics: Shipping costs can vary greatly depending on the origin and destination of the machines. Understanding Incoterms is critical for determining who bears the logistics costs and responsibilities.
-
Margin: Manufacturers will typically add a profit margin to cover their costs and risks. This margin can fluctuate based on competition, demand, and the buyer’s negotiation leverage.
How Do Price Influencers Impact Knitting Machine Costs?
Several factors can influence the pricing of knitting machines:
-
Volume/MOQ: Manufacturers often offer better pricing for larger orders. Buyers should assess their needs carefully to leverage economies of scale.
-
Specifications and Customization: Custom features may drive up costs. Buyers need to balance their specific requirements with budget constraints.
-
Materials and Quality Certifications: The choice of materials and the presence of quality certifications (such as ISO) can impact price. Machines built with premium materials or those that meet rigorous quality standards may come at a higher cost but offer better durability and performance.
-
Supplier Factors: The manufacturer’s reputation and location can also influence pricing. Established manufacturers with a proven track record may charge more but provide reliability.
-
Incoterms: Understanding the terms of shipping and responsibility (e.g., FOB, CIF) is crucial. These terms affect the total cost of ownership and can introduce additional costs if not properly understood.
What Buyer Tips Can Enhance Cost-Efficiency in Sourcing Knitting Machines?
-
Negotiation Strategies: Buyers should approach negotiations with a clear understanding of their budget and the manufacturer’s cost structure. Being informed about market prices can empower buyers during discussions.
-
Assessing Total Cost of Ownership (TCO): Beyond the initial purchase price, buyers should consider maintenance, operational costs, and potential downtime. A lower upfront cost may lead to higher long-term expenses if the machine is less reliable.
-
Pricing Nuances for International Buyers: Buyers from Africa, South America, the Middle East, and Europe should be aware of currency fluctuations, import tariffs, and local market conditions that can affect pricing. Engaging with local experts or consultants can provide insights into these factors.
-
Supplier Relationships: Building long-term relationships with suppliers can result in better pricing and terms over time. Regular communication and feedback can enhance collaboration and lead to improved service and support.
-
Market Research: Conducting thorough market research can uncover competitive offers and help buyers identify the best suppliers that align with their quality and pricing expectations.
Disclaimer on Indicative Prices
Prices for knitting machines can vary significantly based on the factors discussed above. Buyers should seek multiple quotations and consider the total cost of ownership when evaluating offers.
Alternatives Analysis: Comparing knitting machine manufacturer With Other Solutions
When considering the procurement of knitting machinery, it is crucial for B2B buyers to evaluate not only traditional knitting machine manufacturers but also alternative solutions that may offer distinct advantages. Understanding these alternatives can help businesses in Africa, South America, the Middle East, and Europe make informed decisions that align with their operational goals and budget constraints.
Comparison Aspect | Knitting Machine Manufacturer | Alternative 1: Hand Knitting | Alternative 2: 3D Knitting Technology |
---|---|---|---|
Performance | High-speed production, consistent quality | Low-speed, variable quality | High-speed, intricate designs |
Cost | High initial investment, potential long-term savings | Low initial cost, but labor-intensive | Moderate cost, reduces material waste |
Ease of Implementation | Requires training and setup | Minimal setup, easily accessible | Requires technical expertise and setup |
Maintenance | Regular maintenance needed, spare parts availability | Minimal maintenance | Requires specialized service |
Best Use Case | Large-scale production, uniform products | Small-scale, artisanal production | Complex, customized designs |
What Are the Advantages and Disadvantages of Hand Knitting?
Pros:
Hand knitting is an alternative that requires minimal initial investment and can be executed using basic tools. This method is particularly beneficial for small businesses or artisans who wish to create unique, customized products. Furthermore, it allows for flexibility in design and can adapt to changing consumer demands quickly.
Cons:
However, hand knitting is labor-intensive and can result in inconsistent product quality and slower production rates. This makes it less suitable for businesses that require mass production or have high output demands. Additionally, the reliance on skilled labor can pose challenges in scalability.
How Does 3D Knitting Technology Compare to Traditional Machines?
Pros:
3D knitting technology represents a modern approach to textile manufacturing, enabling the production of intricate designs with minimal material waste. This method not only enhances design capabilities but also offers a faster production cycle compared to traditional methods. It is particularly useful for creating customized products on demand, which can cater to niche markets.
Cons:
On the downside, the initial investment in 3D knitting technology can be significant, and it requires a level of technical expertise that may not be readily available in all regions. Maintenance and repair of advanced machinery can also necessitate specialized training and support, which could lead to additional costs.
How Can B2B Buyers Choose the Right Solution for Their Needs?
When selecting the right solution, B2B buyers should assess their specific operational needs, production volume, and budget. For businesses focused on large-scale production, investing in a knitting machine manufacturer may be the best approach due to its high performance and long-term savings. Conversely, smaller enterprises or those looking to produce unique, artisanal products may find hand knitting to be a more viable option. Lastly, companies aiming for innovation and customization may benefit from adopting 3D knitting technology, despite the higher initial investment.
Ultimately, the decision should align with the company’s strategic goals, market demand, and resource availability, ensuring that the chosen method enhances efficiency and profitability.
Essential Technical Properties and Trade Terminology for knitting machine manufacturer
What Are the Key Technical Properties of Knitting Machines?
When considering a knitting machine for your business, understanding the essential technical properties is crucial. Here are some critical specifications that international B2B buyers should prioritize:
-
Material Grade
The material grade of a knitting machine refers to the quality of materials used in its construction, such as stainless steel or high-grade aluminum. Higher quality materials enhance durability and reduce maintenance costs. This is particularly important for buyers in regions like Africa and South America, where environmental factors may lead to increased wear and tear. -
Tolerance Levels
Tolerance levels indicate the precision with which machine components are manufactured. A tighter tolerance often results in better product quality and consistency in the finished knitwear. For B2B buyers, particularly in Europe, understanding tolerance levels can mean the difference between satisfactory and exceptional product output. -
Production Speed
Production speed, measured in stitches per minute (SPM), is a vital property for any knitting machine. Faster machines can significantly boost productivity, allowing businesses to meet demand more efficiently. Buyers should evaluate their production needs to ensure they select a machine that aligns with their operational goals. -
Needle Gauge
The needle gauge refers to the thickness of the needles used in the machine. This specification affects the type of yarn that can be used and the fineness of the knitted fabric. Different regions may have varying preferences for fabric weight, making it essential for buyers to choose a gauge that meets their market demands. -
Motor Power
The motor power of a knitting machine impacts its performance and efficiency. A more powerful motor can handle thicker yarns and more complex patterns without sacrificing speed. Buyers should consider their product line and select a machine with adequate motor power to avoid operational bottlenecks. -
User Interface Technology
Modern knitting machines come equipped with user-friendly interfaces and programmable settings. This technology simplifies operation and allows for quick adjustments to patterns and settings. For international buyers, particularly those in the Middle East, investing in advanced user interfaces can reduce training time and improve operational efficiency.
What Are Common Trade Terminologies in the Knitting Machine Industry?
Understanding industry jargon is essential for effective communication and negotiation. Here are several key terms that B2B buyers should be familiar with:
-
OEM (Original Equipment Manufacturer)
An OEM is a company that produces parts or equipment that may be marketed by another manufacturer. When sourcing knitting machines, buyers might deal directly with OEMs to ensure they receive quality equipment tailored to their specifications. -
MOQ (Minimum Order Quantity)
MOQ refers to the smallest quantity of a product that a supplier is willing to sell. Knowing the MOQ is vital for budgeting and inventory management. For buyers from regions with limited resources, like certain areas in Africa, understanding MOQs can help in planning purchases effectively. -
RFQ (Request for Quotation)
An RFQ is a document that a buyer sends to suppliers to solicit price quotes for specific products. This process is essential for comparing costs and negotiating terms. International buyers should provide detailed specifications in their RFQs to ensure accurate quotes. -
Incoterms (International Commercial Terms)
Incoterms are a set of rules that define the responsibilities of buyers and sellers in international transactions. Understanding these terms helps buyers clarify shipping responsibilities, insurance, and risk during transit. For businesses in South America and Europe, familiarity with Incoterms can streamline logistics and reduce costs. -
Lead Time
Lead time is the amount of time it takes from placing an order until it is delivered. Understanding lead times is critical for supply chain management, especially for businesses in fast-paced markets. Buyers should factor lead times into their production schedules to avoid delays. -
Warranty Period
The warranty period refers to the duration during which a manufacturer will repair or replace defective parts. This is a crucial consideration for buyers, as it can impact long-term operational costs. Ensuring a favorable warranty can safeguard against unexpected expenses and downtime.
By grasping these technical properties and trade terms, B2B buyers can make informed decisions and foster successful partnerships in the knitting machine industry.
Navigating Market Dynamics and Sourcing Trends in the knitting machine manufacturer Sector
What Are the Current Market Dynamics and Key Trends in the Knitting Machine Manufacturer Sector?
The global knitting machine manufacturer sector is experiencing significant transformation driven by technological advancements and changing consumer demands. Key trends include the increasing adoption of automation and smart technology, which enhance efficiency and reduce labor costs. As international B2B buyers, particularly from regions like Africa, South America, the Middle East, and Europe, seek to optimize their production processes, the integration of Internet of Things (IoT) capabilities in knitting machines is becoming essential. This allows manufacturers to monitor machine performance in real-time, predict maintenance needs, and improve overall operational efficiency.
Another notable trend is the shift towards customization and rapid prototyping. Manufacturers are responding to the demand for personalized products by investing in machines that can produce small batches with diverse designs quickly. This flexibility is crucial for buyers aiming to cater to niche markets or respond swiftly to fashion trends, particularly in regions with growing textile industries, such as Brazil and Vietnam.
Moreover, sustainability is becoming a pivotal factor influencing purchasing decisions. Buyers are increasingly aware of the environmental impacts of textile production, prompting a shift towards sourcing from manufacturers who prioritize eco-friendly practices and materials. This trend is not only about compliance but also about enhancing brand value in an increasingly eco-conscious market.
How Is Sustainability and Ethical Sourcing Reshaping the Knitting Machine Manufacturing Landscape?
Sustainability and ethical sourcing are no longer optional considerations for knitting machine manufacturers; they are imperative for long-term viability. Environmental impacts associated with textile production, such as water consumption, chemical use, and waste generation, are prompting buyers to seek partners who demonstrate a commitment to sustainable practices.
International B2B buyers should prioritize manufacturers that utilize eco-friendly materials and processes. This includes sourcing machines that can work with recycled fibers or organic yarns, which significantly reduce the ecological footprint. Additionally, obtaining certifications such as Global Organic Textile Standard (GOTS) or OEKO-TEX can provide assurance of a manufacturer’s commitment to sustainable practices, giving buyers confidence in their sourcing decisions.
Moreover, ethical supply chains are essential for fostering trust and transparency. Buyers are encouraged to engage with manufacturers who maintain fair labor practices and ensure safe working conditions. By aligning with ethical partners, companies can enhance their brand reputation while contributing positively to the communities they operate in, particularly in developing regions.
What Is the Brief Evolution and History of Knitting Machine Manufacturing?
The knitting machine manufacturing sector has evolved significantly since its inception in the late 18th century with the introduction of the first mechanical knitting machines. Initially, these machines were hand-operated and limited in scope. The 20th century saw the advent of fully automated knitting machines, revolutionizing textile production by increasing speed and efficiency.
As globalization took hold, the industry began to shift towards mass production, catering to the booming demand for affordable textiles. However, in recent years, the focus has shifted again, with technological advancements leading to the development of computerized and smart knitting machines. These innovations allow for greater precision, customization, and efficiency, aligning with the current market trends of sustainability and ethical sourcing. For international B2B buyers, understanding this evolution is crucial in making informed decisions about machine investments that can meet contemporary market demands.
Frequently Asked Questions (FAQs) for B2B Buyers of knitting machine manufacturer
-
How do I choose the right knitting machine manufacturer for my business?
Selecting the right knitting machine manufacturer involves evaluating several factors. Start by assessing the manufacturer’s experience and reputation in the industry. Look for customer testimonials and case studies that demonstrate their capability to deliver high-quality machines. Additionally, consider their technological innovations and the range of machines they offer. For international buyers, ensure that the manufacturer can provide support and service in your region, which can significantly impact your operational efficiency. -
What are the key features to look for in a knitting machine?
When sourcing a knitting machine, prioritize features that align with your production needs. Look for machines that offer versatility in fabric types and patterns, ease of operation, and efficiency in production speed. Advanced features like computerized controls and automation can enhance productivity and reduce labor costs. Additionally, consider the machine’s energy consumption and maintenance requirements, as these factors can impact long-term operational costs.
-
What is the typical minimum order quantity (MOQ) for knitting machines?
The minimum order quantity (MOQ) for knitting machines varies by manufacturer and the complexity of the machine. Generally, MOQs can range from a single unit to several dozen machines. For smaller businesses or those just starting, it’s advisable to communicate directly with the manufacturer to negotiate terms that suit your needs. Some manufacturers may offer flexibility on MOQs for first-time buyers or when combined with additional equipment orders. -
How can I ensure quality assurance when purchasing knitting machines?
To guarantee quality assurance, request detailed documentation from the manufacturer regarding their quality control processes. This should include certifications such as ISO 9001, which signifies adherence to international quality management standards. Additionally, consider visiting the manufacturer’s facility or requesting samples of their machines. Establishing a clear communication channel for ongoing support and feedback will also enhance the quality assurance process. -
What payment terms should I expect when sourcing knitting machines internationally?
Payment terms for international purchases of knitting machines often include options like upfront deposits, letters of credit, or staggered payments based on milestones. It’s crucial to discuss these terms upfront and ensure they are documented in the contract. Be aware of the implications of currency exchange rates and potential additional fees when dealing with international transactions. Using secure payment methods can also mitigate risks. -
What logistical considerations should I be aware of when importing knitting machines?
Importing knitting machines involves several logistical considerations, including shipping methods, customs duties, and delivery timelines. Choose a reliable freight forwarder experienced in handling heavy machinery to ensure smooth transport. Be aware of import regulations in your country, as these can affect delivery schedules and costs. Additionally, consider the machine’s installation requirements and whether the manufacturer offers support for setup in your facility. -
How can I customize knitting machines to fit my production needs?
Many manufacturers offer customization options for knitting machines to meet specific production requirements. When discussing your needs, clearly outline the types of fabrics, patterns, and production volumes you aim to achieve. Collaborate with the manufacturer’s engineering team to explore potential modifications or enhancements. Customization may involve changes in machine size, features, or software, which can significantly improve your production efficiency. -
What are the best practices for maintaining knitting machines after purchase?
Regular maintenance is crucial for the longevity and performance of knitting machines. Establish a maintenance schedule based on the manufacturer’s recommendations, which typically includes routine cleaning, lubrication, and inspection of parts. Train your staff on proper operating procedures to minimize wear and tear. Additionally, keep a record of maintenance activities and any issues that arise, as this information can be invaluable for troubleshooting and warranty claims.
Important Disclaimer & Terms of Use
⚠️ Important Disclaimer
The information provided in this guide, including content regarding manufacturers, technical specifications, and market analysis, is for informational and educational purposes only. It does not constitute professional procurement advice, financial advice, or legal advice.
While we have made every effort to ensure the accuracy and timeliness of the information, we are not responsible for any errors, omissions, or outdated information. Market conditions, company details, and technical standards are subject to change.
B2B buyers must conduct their own independent and thorough due diligence before making any purchasing decisions. This includes contacting suppliers directly, verifying certifications, requesting samples, and seeking professional consultation. The risk of relying on any information in this guide is borne solely by the reader.
Strategic Sourcing Conclusion and Outlook for knitting machine manufacturer
How Can Strategic Sourcing Enhance Your Competitive Edge in the Knitting Machine Market?
As we conclude our exploration of strategic sourcing in the knitting machine manufacturing sector, it’s essential to highlight the key takeaways that can significantly influence international B2B buyers. First and foremost, strategic sourcing is not merely a procurement process; it is a comprehensive strategy that aligns your purchasing decisions with your business objectives, ensuring cost efficiency while enhancing product quality. By leveraging local suppliers from regions like Africa and South America, buyers can gain access to innovative technologies and sustainable materials that meet growing market demands.
Furthermore, understanding regional market dynamics in the Middle East and Europe can provide valuable insights into supplier capabilities and pricing strategies. Establishing strong relationships with manufacturers not only fosters trust but also facilitates more favorable terms and conditions, ultimately leading to better supply chain resilience.
What’s Next for International B2B Buyers in the Knitting Machine Industry?
Looking ahead, international B2B buyers must remain proactive in their sourcing strategies. By embracing digital transformation and utilizing data analytics, companies can refine their decision-making processes and respond more effectively to market changes. As the knitting machine industry continues to evolve, now is the time to invest in strategic partnerships that will drive innovation and growth. Take action today—evaluate your sourcing strategies and position your business for success in this dynamic marketplace.