Discover Top Benefits of City BU Manufacturer Sourcing (2025)
Introduction: Navigating the Global Market for city bu manufacturer
In an increasingly competitive global marketplace, sourcing the right city bus manufacturer can be a daunting challenge for international B2B buyers. As urbanization accelerates across regions like Africa, South America, the Middle East, and Europe, the demand for efficient, reliable, and environmentally friendly public transportation solutions has never been greater. This guide aims to equip you with the essential knowledge needed to navigate this complex landscape, ensuring you make informed purchasing decisions that align with your operational goals and budgetary constraints.
Throughout this comprehensive resource, we will delve into various aspects of city bus manufacturing, including types of buses available, their applications in urban environments, and the latest technological advancements driving innovation. We will also provide practical insights on supplier vetting processes, helping you identify trustworthy manufacturers that meet international quality standards. Additionally, our guide will cover cost considerations, enabling you to evaluate pricing structures and negotiate favorable terms.
By the end of this guide, you will be well-prepared to tackle the challenges of sourcing city buses, armed with actionable insights tailored specifically for your market. Whether you are based in Germany, Argentina, or any other region, our focus on diverse international contexts ensures that you can confidently engage with suppliers and make strategic decisions that enhance your transportation infrastructure.
Understanding city bu manufacturer Types and Variations
Type Name | Key Distinguishing Features | Primary B2B Applications | Brief Pros & Cons for Buyers |
---|---|---|---|
Standard City Buses | Designed for urban transport; typically low-floor. | Public transportation, city tours. | Pros: Cost-effective, widely available. Cons: May lack luxury features. |
Electric City Buses | Environmentally friendly; powered by electric batteries. | Eco-friendly public transport solutions. | Pros: Lower operating costs, reduced emissions. Cons: Higher initial investment. |
Luxury City Buses | High-end amenities; spacious interiors; advanced tech. | Corporate shuttles, tourist services. | Pros: Enhanced passenger comfort, branding opportunities. Cons: Higher maintenance costs. |
Articulated Buses | Longer buses with flexible joints; higher capacity. | High-density routes, major urban corridors. | Pros: Efficient for crowded routes. Cons: Requires more road space. |
Mini City Buses | Smaller size; ideal for narrow streets and low demand. | Shuttle services, small urban areas. | Pros: Maneuverable, lower purchase price. Cons: Limited capacity and range. |
What Are the Characteristics of Standard City Buses for B2B Buyers?
Standard city buses are the backbone of urban transportation systems. They are designed to accommodate a large number of passengers and are typically low-floor for easy access. These buses are ideal for public transportation agencies looking to provide reliable service at a lower cost. When considering a purchase, B2B buyers should assess the total cost of ownership, including maintenance and operational efficiency, to ensure they meet the demands of their urban environments.
How Do Electric City Buses Benefit Urban Transport Systems?
Electric city buses are becoming increasingly popular due to their sustainability and lower operational costs. These vehicles are powered by electric batteries, offering a quieter and cleaner alternative to traditional diesel buses. B2B buyers in regions with stringent environmental regulations or those seeking to enhance their corporate social responsibility profiles may find electric buses particularly appealing. However, the higher upfront costs and the need for charging infrastructure should be carefully evaluated during the purchasing process.
What Should B2B Buyers Know About Luxury City Buses?
Luxury city buses cater to a niche market, offering high-end amenities such as comfortable seating, air conditioning, and advanced technology. They are often used for corporate shuttles and tourist services, providing a premium experience for passengers. Buyers should consider the target demographic and the potential for increased revenue through premium pricing. While the initial investment is higher, the added value of enhanced branding and customer satisfaction can justify the costs.
Why Are Articulated Buses Ideal for High-Density Routes?
Articulated buses are designed for high-capacity transport, making them suitable for busy urban corridors and high-density routes. Their flexible design allows for easier navigation in congested areas while providing more space for passengers. B2B buyers should consider the operational requirements, such as road space and turning radii, when selecting articulated buses. Although they are efficient for crowded routes, they may require additional training for drivers and more stringent road management.
What Are the Advantages of Mini City Buses for Urban Areas?
Mini city buses are compact vehicles designed for narrow streets and lower passenger demand. They are particularly useful in smaller urban areas or as shuttle services in larger facilities. B2B buyers looking for cost-effective solutions with lower purchase prices may find mini buses appealing. However, it is essential to keep in mind their limited capacity and range, which may not meet the needs of larger urban populations. Understanding local transport demands is crucial for making an informed purchase decision.
Related Video: Heat Pump Thermostat O, B, and C Terminal Variations Explained
Key Industrial Applications of city bu manufacturer
Industry/Sector | Specific Application of city bu manufacturer | Value/Benefit for the Business | Key Sourcing Considerations for this Application |
---|---|---|---|
Transportation & Logistics | Urban Bus Fleets | Enhanced public transport efficiency | Compliance with local regulations and sustainability standards |
Tourism & Hospitality | Sightseeing Buses | Increased tourist engagement and revenue | Customization options for branding and comfort features |
Construction & Infrastructure | Worker Transport Solutions | Improved workforce mobility and productivity | Durability and maintenance support for harsh environments |
Education | School Bus Services | Safe and reliable student transport | Safety certifications and adherence to educational transport laws |
Events & Entertainment | Shuttle Services for Events | Streamlined guest transport and experience | Flexibility in scheduling and capacity management |
How is ‘city bu manufacturer’ utilized in the Transportation & Logistics sector?
In the Transportation & Logistics sector, city bus manufacturers provide urban bus fleets that enhance public transport efficiency. These buses are designed to navigate dense urban environments, reducing traffic congestion and lowering emissions. For international B2B buyers, particularly in Africa and South America, it is crucial to consider compliance with local regulations on emissions and passenger safety. Additionally, sourcing partners should ensure the buses meet sustainability standards to align with global environmental goals.
What role does ‘city bu manufacturer’ play in Tourism & Hospitality?
In the Tourism & Hospitality industry, city bus manufacturers supply sightseeing buses that cater to tourists exploring urban areas. These buses not only provide comfortable transportation but also enhance the overall tourist experience by offering guided tours and information. For buyers in Europe and the Middle East, customization options for branding and comfort features are essential, as they seek to create a unique experience that reflects local culture and hospitality standards.
How does ‘city bu manufacturer’ support Construction & Infrastructure projects?
City bus manufacturers contribute to Construction & Infrastructure projects by offering worker transport solutions. These buses facilitate efficient movement of labor forces to and from job sites, which is particularly important in remote or developing regions. For international buyers, especially in Africa and South America, the durability of buses and ongoing maintenance support are critical considerations, ensuring reliability in various environmental conditions and enhancing overall productivity.
In what ways are ‘city bu manufacturer’ products utilized in Education?
In the Education sector, city bus manufacturers provide school bus services that ensure safe and reliable transport for students. These buses are designed with safety features to comply with educational transport laws, making them an essential investment for schools and educational institutions. Buyers from Europe and the Middle East must prioritize safety certifications and the ability to customize buses to meet specific needs, such as accessibility for students with disabilities.
How do ‘city bu manufacturer’ solutions enhance Events & Entertainment experiences?
City bus manufacturers also play a significant role in the Events & Entertainment industry by providing shuttle services for events. These buses streamline guest transport, enhancing the overall experience for attendees. For B2B buyers in this sector, flexibility in scheduling and capacity management is vital, as event demands can vary widely. Ensuring that the buses can accommodate fluctuating guest numbers while maintaining comfort and efficiency is a key consideration when sourcing from city bus manufacturers.
Related Video: FANUC Industrial Robots | AUDI Case Study
3 Common User Pain Points for ‘city bu manufacturer’ & Their Solutions
Scenario 1: Navigating Quality Assurance Challenges in City Bus Manufacturing
The Problem:
International B2B buyers often face the daunting task of ensuring the quality of city buses manufactured abroad. This challenge is particularly pronounced for buyers from regions like Africa and South America, where local standards may differ significantly from those in Europe or the Middle East. Factors such as inadequate supplier transparency, varying manufacturing standards, and potential language barriers can lead to misunderstandings about product specifications and quality expectations. As a result, buyers may find themselves dealing with buses that do not meet operational requirements, resulting in increased maintenance costs and safety concerns.
The Solution:
To effectively navigate quality assurance challenges, buyers should implement a robust vendor evaluation process prior to engagement. This includes conducting thorough due diligence, such as site visits to manufacturing facilities and requesting third-party quality certifications. Utilizing standardized quality metrics—such as ISO certifications or adherence to local safety regulations—can provide reassurance regarding product quality. Additionally, establishing clear communication channels and utilizing multilingual support can help clarify specifications and expectations. Buyers should also consider pilot testing a limited batch of buses before committing to large-scale purchases, allowing for real-world evaluation and feedback.
Scenario 2: Managing Supply Chain Disruptions in City Bus Manufacturing
The Problem:
Supply chain disruptions are a significant concern for B2B buyers in the city bus manufacturing sector. Buyers from Europe and the Middle East, for instance, may experience delays due to geopolitical tensions or transportation bottlenecks that hinder timely deliveries. Such disruptions can lead to project delays, increased costs, and the inability to meet public transportation demands, ultimately impacting service reliability and customer satisfaction.
The Solution:
To manage potential supply chain disruptions, B2B buyers should adopt a diversified sourcing strategy. This involves engaging multiple suppliers across different regions to mitigate risks associated with reliance on a single manufacturer. Additionally, maintaining open lines of communication with suppliers can facilitate proactive updates regarding potential delays or issues. Buyers should also consider implementing just-in-time inventory practices to better align with supply chain timelines and demand forecasts. Leveraging technology, such as supply chain management software, can provide real-time insights into the logistics process, enabling buyers to make informed decisions and adjustments swiftly.
Scenario 3: Addressing Customization Needs in City Bus Design
The Problem:
B2B buyers often encounter difficulties in sourcing city buses that meet specific local requirements and preferences. For instance, buyers in urban areas of Africa may seek buses designed for rugged terrains or equipped with specific passenger amenities that are not standard in many European models. This mismatch can lead to dissatisfaction and inadequate service delivery, hindering the effectiveness of public transportation systems.
The Solution:
To address customization needs, buyers should engage in collaborative design discussions with manufacturers during the procurement process. Clearly articulating local requirements and involving stakeholders—such as municipal authorities and potential passengers—in the design phase can ensure that the final product meets diverse needs. Additionally, buyers can request modular designs that allow for easy upgrades and modifications based on evolving needs or technological advancements. Utilizing platforms that facilitate direct communication with manufacturers can foster a more personalized approach to bus design, ensuring that the end product is tailored to the specific operational context of the buyer.
Strategic Material Selection Guide for city bu manufacturer
When selecting materials for city bus manufacturing, international B2B buyers must consider a range of factors that influence both the performance and cost-effectiveness of the final product. Below, we analyze four common materials used in city bus manufacturing: steel, aluminum, fiberglass, and composite materials. Each material has unique properties, advantages, and limitations that can significantly impact the manufacturing process and the end product’s suitability for various markets.
What Are the Key Properties of Steel in City Bus Manufacturing?
Steel is a traditional choice for city bus frames due to its high strength and durability. Key properties include excellent tensile strength, high impact resistance, and good weldability, making it suitable for heavy-duty applications. Steel can withstand significant pressure and temperature variations, which is crucial for city buses operating in diverse climates.
Pros & Cons: The primary advantage of steel is its durability, which translates to a longer lifespan for the bus. However, it is relatively heavy, which can affect fuel efficiency. Additionally, steel is prone to corrosion if not properly treated, necessitating additional maintenance costs.
Impact on Application: Steel is compatible with various media, including fuel and hydraulic fluids, making it versatile for different bus systems. However, its weight may limit the design options for certain bus models.
Considerations for International Buyers: Buyers from regions like Europe, where stringent environmental regulations exist, must ensure that the steel used complies with standards such as DIN. In contrast, buyers in Africa may prioritize cost-effectiveness and durability over weight considerations.
How Does Aluminum Compare as a Material for City Buses?
Aluminum is increasingly popular in city bus manufacturing due to its lightweight nature and resistance to corrosion. Key properties include a lower density than steel, which contributes to improved fuel efficiency, and excellent thermal conductivity.
Pros & Cons: The primary advantage of aluminum is its weight, which allows for better fuel economy and handling. However, it is generally more expensive than steel, and its lower strength means that it may require additional reinforcements in certain applications.
Impact on Application: Aluminum is particularly suitable for electric buses, where weight reduction can significantly enhance performance. Its corrosion resistance makes it ideal for humid or coastal environments.
Considerations for International Buyers: Buyers from South America and the Middle East may find aluminum appealing due to its resistance to corrosion in humid climates. However, they must also consider the higher initial costs and ensure compliance with regional standards like ASTM.
What Role Do Fiberglass Materials Play in City Bus Manufacturing?
Fiberglass is a composite material known for its lightweight and high strength-to-weight ratio. Key properties include excellent corrosion resistance and the ability to mold into complex shapes, which is beneficial for aerodynamic designs.
Pros & Cons: Fiberglass offers significant advantages in terms of design flexibility and weight reduction. However, it can be more expensive to produce and may not have the same impact resistance as metals, making it less suitable for heavy-duty applications.
Impact on Application: Fiberglass is ideal for body panels and interior components, where aesthetics and weight are critical. It is compatible with various media but may require specific treatments for fuel exposure.
Considerations for International Buyers: Buyers in Europe may appreciate the design flexibility of fiberglass, while those in Africa may need to weigh the cost against the benefits. Understanding local regulations regarding composite materials is essential.
How Do Composite Materials Enhance City Bus Design and Performance?
Composite materials, often a combination of fibers and resins, provide an excellent balance of weight, strength, and durability. Key properties include high resistance to environmental degradation and the ability to tailor material properties for specific applications.
Pros & Cons: The primary advantage of composites is their lightweight nature and high strength, which can lead to improved fuel efficiency and performance. However, they can be complex to manufacture, leading to higher production costs.
Impact on Application: Composites are suitable for various applications, including structural components and aesthetic finishes. Their compatibility with different media is generally good, but buyers should verify specific requirements.
Considerations for International Buyers: Buyers from regions with advanced manufacturing capabilities, such as Germany, may find composites appealing for their innovative designs. However, understanding the local market’s acceptance and regulatory environment for composite materials is crucial.
Summary Table of Material Selection for City Bus Manufacturing
Material | Typical Use Case for city bu manufacturer | Key Advantage | Key Disadvantage/Limitation | Relative Cost (Low/Med/High) |
---|---|---|---|---|
Steel | Frame and structural components | High durability and strength | Heavy and prone to corrosion | Medium |
Aluminum | Body panels and structural elements | Lightweight and corrosion-resistant | Higher cost and lower strength | High |
Fiberglass | Body panels and interior components | Design flexibility and lightweight | More expensive and lower impact resistance | Medium |
Composite | Structural components and aesthetics | High strength-to-weight ratio | Complex manufacturing and higher costs | High |
In conclusion, selecting the right material for city bus manufacturing requires careful consideration of the specific needs of the application, regional market conditions, and compliance with local standards. By evaluating the properties, advantages, and limitations of each material, international B2B buyers can make informed decisions that align with their operational goals and market demands.
In-depth Look: Manufacturing Processes and Quality Assurance for city bu manufacturer
What Are the Main Stages of Manufacturing for City BU Products?
The manufacturing process for City BU products involves several critical stages that ensure the final product meets the necessary quality and performance standards. These stages typically include:
-
Material Preparation: This initial phase involves sourcing high-quality raw materials suitable for the specific product requirements. Suppliers should be evaluated based on their material certifications and compliance with international standards. For instance, metals might need to meet ASTM specifications, while plastics could require compliance with ISO standards.
-
Forming: This stage employs various techniques such as casting, forging, and machining to shape the materials into the desired form. For City BU manufacturers, precision is crucial, and advanced technologies like CNC machining are often utilized to achieve high tolerances.
-
Assembly: In this phase, the formed components are assembled into the final product. This can involve manual labor or automated processes, depending on the complexity of the product. Attention to detail during assembly is essential to ensure that all components fit together correctly and function as intended.
-
Finishing: The final touches often include processes like painting, coating, or polishing. This not only enhances the product’s aesthetic appeal but also provides protection against environmental factors. Quality in finishing can significantly affect the longevity and performance of the products.
How Is Quality Assurance Implemented in City BU Manufacturing?
Quality assurance (QA) is a fundamental component of the manufacturing process, ensuring that products meet established standards and customer expectations. For City BU manufacturers, this involves adherence to both international and industry-specific standards.
What International Standards Should B2B Buyers Look For?
One of the most recognized international quality standards is ISO 9001, which outlines a framework for quality management systems. Compliance with ISO 9001 indicates that a manufacturer has a systematic approach to managing quality, ensuring continuous improvement and customer satisfaction.
In addition to ISO standards, industry-specific certifications may also be relevant. For example:
- CE Marking: Essential for products sold in the European Economic Area, indicating compliance with health, safety, and environmental protection standards.
- API Standards: Relevant for manufacturers producing equipment for the oil and gas industry, ensuring products meet specific performance requirements.
What Are the Key Quality Control Checkpoints in City BU Manufacturing?
Quality control (QC) is implemented at various checkpoints throughout the manufacturing process. This typically includes:
-
Incoming Quality Control (IQC): Before production begins, raw materials are inspected to ensure they meet the specified standards. This can involve checking material certificates and conducting physical inspections.
-
In-Process Quality Control (IPQC): During the manufacturing process, ongoing inspections are performed to monitor quality. This includes checking dimensions, tolerances, and any potential defects that could arise during forming and assembly.
-
Final Quality Control (FQC): Once manufacturing is complete, a final inspection is conducted to ensure the product meets all specifications before it is shipped to customers. This often includes performance testing and compliance checks against relevant standards.
What Common Testing Methods Are Used in Quality Assurance?
City BU manufacturers employ various testing methods to validate product quality:
- Dimensional Inspection: Using tools like calipers and micrometers to ensure that the product meets specified dimensions.
- Functional Testing: Assessing whether the product performs as intended under various conditions.
- Non-destructive Testing (NDT): Techniques such as ultrasonic testing or X-ray inspection are used to detect internal defects without damaging the product.
How Can B2B Buyers Verify Supplier Quality Control Practices?
For international B2B buyers, especially those from Africa, South America, the Middle East, and Europe, verifying a supplier’s quality control practices is crucial. Here are actionable steps:
-
Supplier Audits: Conducting audits helps assess the manufacturer’s quality management systems and processes. This can be done by the buyer’s team or through third-party auditing firms.
-
Request Quality Reports: Buyers should ask for quality assurance documentation, including inspection reports and certificates of compliance with relevant standards. This transparency helps build trust.
-
Third-Party Inspections: Engaging independent inspection agencies can provide an unbiased evaluation of the manufacturing process and product quality. This is particularly beneficial for buyers unfamiliar with the supplier’s local standards.
What Are the Quality Control and Certification Nuances for International Buyers?
International B2B buyers must be aware of specific nuances when it comes to quality control and certifications. Different regions may have varying standards and practices, which can affect product compliance and acceptance in the target market.
-
Regulatory Compliance: Buyers should ensure that products meet the regulatory requirements of their home country. For instance, products imported into the EU must comply with CE marking regulations, while those entering the Middle Eastern markets may need to adhere to specific local certifications.
-
Cultural Considerations: Understanding the local manufacturing culture can also impact quality. In some regions, informal practices may prevail, which can lead to inconsistencies in quality assurance. Engaging with local experts can help navigate these challenges.
Conclusion: Why Quality Assurance Is Essential for B2B Buyers
For international B2B buyers, especially those from diverse regions like Africa, South America, the Middle East, and Europe, understanding the manufacturing processes and quality assurance measures of City BU manufacturers is crucial. By focusing on the stages of production, relevant certifications, and effective QC practices, buyers can make informed decisions that ensure product quality and reliability. These insights not only enhance the procurement process but also foster long-term partnerships with manufacturers committed to excellence.
Practical Sourcing Guide: A Step-by-Step Checklist for ‘city bu manufacturer’
The purpose of this guide is to provide international B2B buyers with a structured checklist to effectively source city bus manufacturers. By following these steps, you can ensure that you select a reliable supplier that meets your specific needs while navigating the complexities of global procurement.
Step 1: Define Your Technical Specifications
Before initiating the sourcing process, it’s essential to have a clear understanding of the technical specifications required for your city buses. This includes size, capacity, fuel type, and environmental standards that comply with local regulations. Clearly defined specifications will not only streamline the selection process but also help in comparing different suppliers effectively.
Step 2: Research Potential Suppliers
Conduct thorough research to identify reputable city bus manufacturers. Utilize online platforms, trade fairs, and industry reports to gather a list of potential suppliers. Pay attention to their market presence in regions like Africa, South America, the Middle East, and Europe, as this can indicate their experience with diverse customer needs and compliance with local standards.
Step 3: Evaluate Supplier Certifications and Compliance
✅ Verify Supplier Certifications
Ensure that the manufacturers you are considering hold relevant industry certifications, such as ISO 9001 for quality management and environmental certifications like ISO 14001. These certifications demonstrate a commitment to quality and sustainability, which is crucial for long-term partnerships. Additionally, check for compliance with local and international safety standards specific to city buses.
Step 4: Request and Review Proposals
Once you have shortlisted potential suppliers, request detailed proposals. These should include pricing, delivery timelines, warranty terms, and after-sales support. A comprehensive proposal allows you to assess the overall value offered by each supplier and compare them against your budget and requirements.
Step 5: Conduct Factory Visits or Virtual Tours
If possible, arrange for factory visits to see the manufacturing processes firsthand. This step helps in assessing the production capabilities, quality control measures, and working conditions. If travel is not feasible, request virtual tours or video demonstrations to gain insights into the supplier’s operational standards.
Step 6: Check References and Past Performance
Reach out to previous clients of the manufacturers you are considering. Asking about their experience with the supplier can provide valuable insights into reliability, product quality, and customer service. Look for references from similar regions or industries to ensure that the supplier can meet your specific needs.
Step 7: Negotiate Terms and Finalize Contracts
Once you have selected a supplier, negotiate the terms of the agreement carefully. Ensure that all aspects, including pricing, delivery schedules, and warranty conditions, are clearly outlined in the contract. This step is crucial for protecting your interests and ensuring that both parties have aligned expectations.
By following this checklist, B2B buyers can navigate the sourcing process more effectively, ensuring that they choose a city bus manufacturer that aligns with their operational needs and strategic goals.
Comprehensive Cost and Pricing Analysis for city bu manufacturer Sourcing
What Are the Key Cost Components in City Bus Manufacturing?
When sourcing city buses, understanding the cost structure is essential for international B2B buyers. The primary cost components include:
-
Materials: The choice of materials significantly influences the overall cost. High-quality steel, aluminum, and composite materials can enhance durability but may increase the initial price. Buyers should consider the long-term benefits of investing in superior materials that offer better performance and lower maintenance costs.
-
Labor: Labor costs vary widely depending on the region of production. Countries with lower wage standards may offer competitive pricing, but it’s crucial to evaluate the skill level and productivity of the workforce. Higher labor costs in regions like Europe may be offset by superior craftsmanship and technology.
-
Manufacturing Overhead: This includes expenses related to facility maintenance, utilities, and administrative costs. Efficient manufacturing processes can help reduce overhead, making it a vital consideration when comparing suppliers.
-
Tooling: The initial investment in tooling can be substantial, especially for custom designs. Buyers should inquire about tooling costs when requesting quotes, as these can significantly affect the unit price, especially in low-volume orders.
-
Quality Control (QC): Implementing stringent QC measures ensures that the buses meet safety and performance standards. While this may increase costs, it ultimately contributes to better product reliability and customer satisfaction.
-
Logistics: Transportation and handling of the buses from the manufacturer to the buyer’s location can add to the total cost. Buyers should consider the logistics capabilities of suppliers, including shipping methods, delivery times, and any potential tariffs or duties.
-
Margin: Suppliers typically include a profit margin in their pricing. Understanding the expected margin in the industry can help buyers negotiate better deals.
How Do Price Influencers Impact City Bus Sourcing?
Several factors can influence the pricing of city buses:
-
Volume/MOQ (Minimum Order Quantity): Larger orders often lead to lower per-unit costs due to economies of scale. Buyers should assess their needs and consider consolidating orders to achieve better pricing.
-
Specifications and Customization: Customizing buses to meet specific requirements can increase costs. Buyers should balance their customization needs against budget constraints and explore if certain features can be standardized.
-
Materials and Quality Certifications: The type of materials and certifications (such as ISO) demanded by buyers can impact pricing. Higher quality and certified materials typically come at a premium but ensure compliance with international standards.
-
Supplier Factors: The reputation and reliability of the supplier play a critical role in pricing. Established manufacturers may charge more due to their experience and quality assurance practices.
-
Incoterms: Understanding the terms of delivery is crucial. Incoterms define the responsibilities of buyers and sellers, impacting the overall pricing structure, including shipping costs and risk management.
What Are the Best Buyer Tips for Cost Efficiency in City Bus Sourcing?
International B2B buyers should adopt several strategies to enhance cost efficiency:
-
Negotiate Wisely: Leverage your purchasing power when negotiating prices. Building a long-term relationship with suppliers can yield better terms and discounts.
-
Evaluate Total Cost of Ownership (TCO): Consider not just the purchase price but also maintenance, fuel efficiency, and lifespan. A lower initial cost may lead to higher expenses in the long run.
-
Understand Pricing Nuances: Be aware of the regional differences in pricing, especially between markets like Africa, South America, the Middle East, and Europe. Tailoring your approach based on local economic conditions can yield better results.
-
Request Detailed Quotes: Always ask for itemized quotes that break down costs. This transparency allows for better comparison between suppliers and helps identify areas for negotiation.
Disclaimer on Indicative Prices
Prices in the city bus manufacturing industry can fluctuate based on market conditions, material costs, and regional economic factors. Buyers should conduct thorough market research and consult multiple suppliers to obtain accurate pricing tailored to their specific needs.
Alternatives Analysis: Comparing city bu manufacturer With Other Solutions
Understanding the Importance of Alternatives in B2B Purchasing Decisions
In the fast-evolving landscape of B2B solutions, it is crucial for international buyers to evaluate various options before making a purchasing decision. The ‘city bu manufacturer’ offers specific advantages, but understanding how it compares with alternative solutions can help businesses identify the most effective technology or method that aligns with their unique requirements. This analysis will focus on comparing the ‘city bu manufacturer’ with two viable alternatives: Smart City Solutions and Traditional Urban Planning Approaches.
Comparison Table of City Bu Manufacturer and Alternatives
Comparison Aspect | City Bu Manufacturer | Smart City Solutions | Traditional Urban Planning Approaches |
---|---|---|---|
Performance | High | Very High | Moderate |
Cost | Medium | High | Low |
Ease of Implementation | Moderate | Complex | Easy |
Maintenance | Low | High | Low |
Best Use Case | Urban areas needing efficient transport | Cities looking for integrated tech solutions | Communities needing basic infrastructure |
What Are the Pros and Cons of Smart City Solutions?
Smart City Solutions leverage advanced technologies like IoT, big data, and AI to optimize urban services. The performance of smart city initiatives is generally very high, as they can enhance efficiency across multiple sectors, including transportation, energy, and waste management. However, the cost of implementing these solutions is typically higher due to the sophisticated technology involved. Additionally, the complexity of integrating various systems can pose challenges during implementation. Maintenance can also be demanding, requiring specialized personnel to manage the advanced technologies.
How Do Traditional Urban Planning Approaches Compare?
Traditional Urban Planning Approaches focus on foundational infrastructure development, such as roads, utilities, and public spaces. These methods are often less expensive and easier to implement, making them suitable for communities with limited budgets or resources. However, their performance can be moderate compared to more advanced technologies, as they may not incorporate the latest innovations. Maintenance requirements tend to be lower, but these approaches may lack the flexibility and adaptability seen in more modern solutions.
How Can B2B Buyers Choose the Right Solution for Their Needs?
When evaluating the best solution for urban development, B2B buyers should consider their specific context and objectives. Factors such as budget constraints, desired performance levels, and the complexity of implementation play a significant role in decision-making. For urban areas that require efficient transport solutions, the ‘city bu manufacturer’ may provide a balanced approach in terms of performance and cost. Conversely, cities aiming for a comprehensive, tech-integrated future might find that Smart City Solutions offer the most long-term benefits despite higher initial costs. Ultimately, the choice should align with the strategic goals of the organization and the needs of the community it serves.
Essential Technical Properties and Trade Terminology for city bu manufacturer
What Are the Essential Technical Properties for City Bus Manufacturing?
When engaging with city bus manufacturers, understanding the key technical properties is crucial for making informed procurement decisions. Here are several critical specifications:
1. Material Grade
The material grade refers to the type of materials used in the bus construction, which can range from steel to aluminum and composites. High-grade materials ensure durability, resistance to corrosion, and safety under various weather conditions. For B2B buyers, selecting the appropriate material grade impacts not only the bus’s lifespan but also maintenance costs over time.
2. Tolerance Levels
Tolerance levels denote the permissible limits of variation in dimensions and physical properties. These specifications are vital for ensuring parts fit together correctly during assembly, affecting performance and safety. For buyers, understanding tolerance levels helps in assessing the quality of manufacturing and the potential for future repairs or modifications.
3. Weight Capacity
Weight capacity is the maximum load a bus can safely carry, including passengers and cargo. This specification is particularly important for cities with high passenger volumes. Buyers should evaluate weight capacity to ensure compliance with local regulations and operational efficiency, which can affect fuel consumption and overall performance.
4. Fuel Efficiency Standards
Fuel efficiency standards outline the expected miles per gallon (MPG) or liters per 100 kilometers. Given the rising fuel costs and environmental regulations, understanding these standards is essential for buyers seeking to minimize operational costs and meet sustainability goals. Manufacturers that prioritize fuel efficiency can offer significant long-term savings.
5. Safety Ratings
Safety ratings are assessments from recognized organizations that evaluate the bus’s crashworthiness and safety features. For B2B buyers, this is a non-negotiable aspect that influences public trust and compliance with local safety regulations. Ensuring that the buses meet or exceed safety standards is vital for minimizing liability and ensuring passenger safety.
What Trade Terminology Should International Buyers Know?
Familiarity with industry terminology can streamline the procurement process and enhance communication with manufacturers. Here are several common terms that buyers should understand:
1. OEM (Original Equipment Manufacturer)
OEM refers to a company that produces parts or equipment that may be marketed by another manufacturer. Understanding OEM relationships is crucial for buyers, as it can affect the availability of parts, warranty coverage, and overall product quality.
2. MOQ (Minimum Order Quantity)
MOQ indicates the smallest quantity of a product that a supplier is willing to sell. This term is significant for buyers who need to balance inventory costs with supplier requirements. Knowing the MOQ can help in negotiating terms and assessing whether a supplier can meet specific needs without overcommitting resources.
3. RFQ (Request for Quotation)
An RFQ is a document sent to suppliers to solicit price quotes for specific products or services. This process allows buyers to compare prices and terms from different manufacturers. For international buyers, crafting a clear RFQ can lead to better negotiations and more favorable contract terms.
4. Incoterms (International Commercial Terms)
Incoterms are a set of predefined commercial terms published by the International Chamber of Commerce. They define the responsibilities of buyers and sellers in international transactions, covering aspects like shipping, insurance, and tariffs. Familiarity with Incoterms is essential for avoiding misunderstandings in international logistics and ensuring smooth delivery processes.
5. Lead Time
Lead time refers to the amount of time it takes from placing an order to receiving the product. Understanding lead times is crucial for inventory management and project planning. Buyers should consider lead times in their decision-making process to align procurement with operational needs.
In conclusion, a solid grasp of both technical properties and trade terminology is essential for international B2B buyers in the city bus manufacturing sector. By leveraging this knowledge, buyers can make informed decisions that align with their operational goals and budget constraints.
Navigating Market Dynamics and Sourcing Trends in the city bu manufacturer Sector
What Are the Global Drivers and Key Trends in the City Bus Manufacturer Sector?
The city bus manufacturing sector is currently influenced by a confluence of global drivers and emerging trends that B2B buyers must navigate. Urbanization is one of the most significant factors, with cities across Africa, South America, the Middle East, and Europe experiencing rapid growth. This surge in urban populations is leading to increased demand for efficient public transportation solutions, including city buses that can accommodate larger passenger volumes while minimizing environmental impact.
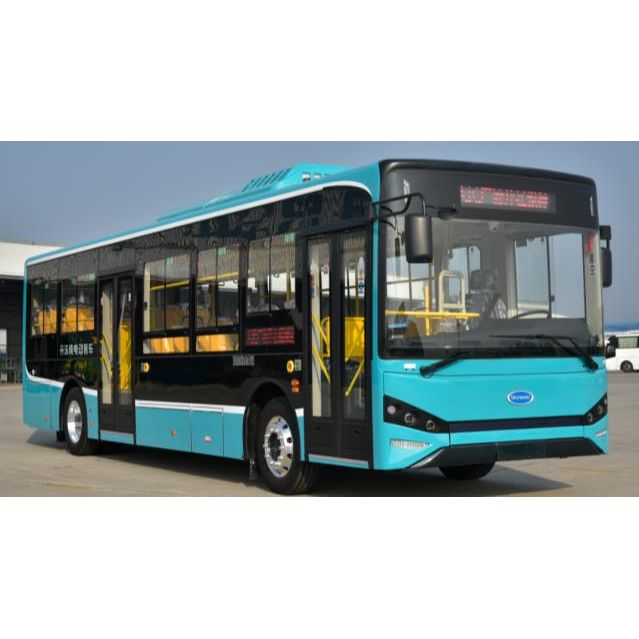
A stock image related to city bu manufacturer.
Technological advancements, particularly in electric and hybrid bus manufacturing, are reshaping the landscape. The transition to electric buses is being driven by both government regulations aimed at reducing emissions and the rising demand for sustainable transport options. Additionally, connected technologies, such as IoT and smart city integrations, are becoming integral in enhancing operational efficiencies, improving passenger experiences, and optimizing maintenance schedules.
International B2B buyers should also pay attention to sourcing trends, which include a shift towards local suppliers to mitigate risks associated with global supply chains. This trend is particularly relevant in regions like Europe and South America, where sourcing locally can enhance responsiveness and reduce lead times. Moreover, the rise of digital platforms for procurement and sourcing is streamlining the purchasing process, enabling buyers to access a wider range of products and services efficiently.
How Is Sustainability and Ethical Sourcing Shaping the City Bus Manufacturing Industry?
Sustainability and ethical sourcing have become paramount in the city bus manufacturing sector, reflecting growing environmental concerns and the demand for responsible business practices. The environmental impact of traditional diesel buses is significant, prompting a shift towards greener alternatives, such as electric and hydrogen fuel cell buses. These technologies not only reduce greenhouse gas emissions but also align with global initiatives aimed at combating climate change.
B2B buyers must prioritize suppliers who adhere to sustainable practices and possess certifications such as ISO 14001 for environmental management and LEED for green building standards. These certifications are indicators of a manufacturer’s commitment to sustainability, ensuring that their products are produced with minimal environmental impact. Furthermore, using recycled materials and sustainable components in the manufacturing process can enhance the overall appeal of the product to eco-conscious consumers and municipalities.
Ethical supply chains are equally critical, as buyers increasingly seek transparency in sourcing practices. This involves verifying that materials are sourced responsibly and that labor practices within the supply chain are fair. Buyers can leverage tools and certifications that track the ethical sourcing of materials, which can significantly influence purchasing decisions and brand reputation.
What Is the Evolution of the City Bus Manufacturing Sector?
The city bus manufacturing sector has evolved significantly over the past few decades. Initially dominated by diesel-powered buses, the industry has seen a paradigm shift towards more sustainable options, driven by both technological advancements and regulatory pressures. The introduction of electric buses in the early 2000s marked a crucial turning point, as manufacturers began to explore alternative fuels and energy-efficient technologies.
As urban areas expanded, so did the need for larger and more efficient public transport systems. This led to innovations in bus design, including low-floor buses for improved accessibility and articulated buses for higher capacity. The integration of smart technologies in buses has also gained traction, enabling features such as real-time tracking and passenger information systems that enhance the user experience.
In summary, the city bus manufacturing sector is at a pivotal juncture, shaped by urbanization, technological advancements, sustainability imperatives, and evolving consumer expectations. International B2B buyers must remain agile and informed about these trends to make strategic sourcing decisions that align with their operational goals and sustainability commitments.
Frequently Asked Questions (FAQs) for B2B Buyers of city bu manufacturer
-
How do I solve issues related to supplier reliability when sourcing a city bus manufacturer?
To ensure supplier reliability, conduct thorough due diligence on potential manufacturers. Start by checking their reputation through industry reviews and testimonials from previous clients. Engage in direct communication to assess their responsiveness and willingness to meet your requirements. Request references and verify their production capacity and quality control processes. Additionally, consider visiting their facilities or utilizing third-party inspection services to observe their operations firsthand, which can significantly mitigate risks associated with supplier reliability. -
What are the best practices for negotiating payment terms with city bus manufacturers?
When negotiating payment terms, aim for a balance that safeguards both parties. Typically, a 30-70 split, where 30% is paid upfront and the remaining 70% upon delivery, is common. Be transparent about your financial capabilities and negotiate flexible terms that align with your cash flow cycles. Explore options for letter of credit or escrow services for added security. Moreover, clearly outline penalties for late payments and incentives for early settlements to encourage timely transactions and strengthen supplier relationships. -
How can I ensure quality assurance when sourcing city buses from international manufacturers?
Implement a robust quality assurance (QA) framework that includes pre-production samples and regular inspections throughout the manufacturing process. Establish clear quality standards and specifications in your contract, and consider using third-party QA services to conduct checks at various stages. Additionally, request certifications such as ISO 9001, which can provide assurance of the manufacturer’s commitment to quality. Building a strong communication channel with the manufacturer will also help address any issues promptly and ensure adherence to your quality expectations. -
What is the typical minimum order quantity (MOQ) for city buses from manufacturers?
Minimum order quantities (MOQs) for city buses can vary widely among manufacturers, typically ranging from 5 to 50 units. Factors influencing MOQs include the manufacturer’s production capacity, customization options, and your negotiation skills. If you’re a smaller buyer, consider grouping orders with other companies or exploring manufacturers that specialize in lower MOQs. Always discuss your needs upfront to find a mutually beneficial arrangement that allows you to test the market without significant upfront investment. -
How do I assess the customization options available for city buses?
When evaluating customization options, inquire about the manufacturer’s capabilities in terms of design, features, and technology. Discuss your specific requirements, such as passenger capacity, accessibility features, and environmental standards. Request examples of past custom projects to gauge their expertise. Additionally, clarify lead times for custom orders and any extra costs associated with modifications. A manufacturer with a flexible approach to customization can significantly enhance your product offering and align with local market needs. -
What logistics considerations should I keep in mind when importing city buses?
Logistics is crucial when importing city buses, so consider shipping methods, costs, and timelines. Engage with a reliable freight forwarder who understands the complexities of international shipping, including customs regulations and documentation. Assess the total landed cost, which includes shipping, tariffs, and insurance. Plan for potential delays by allowing buffer time in your supply chain. Additionally, familiarize yourself with the import regulations in your country to ensure compliance and smooth delivery.
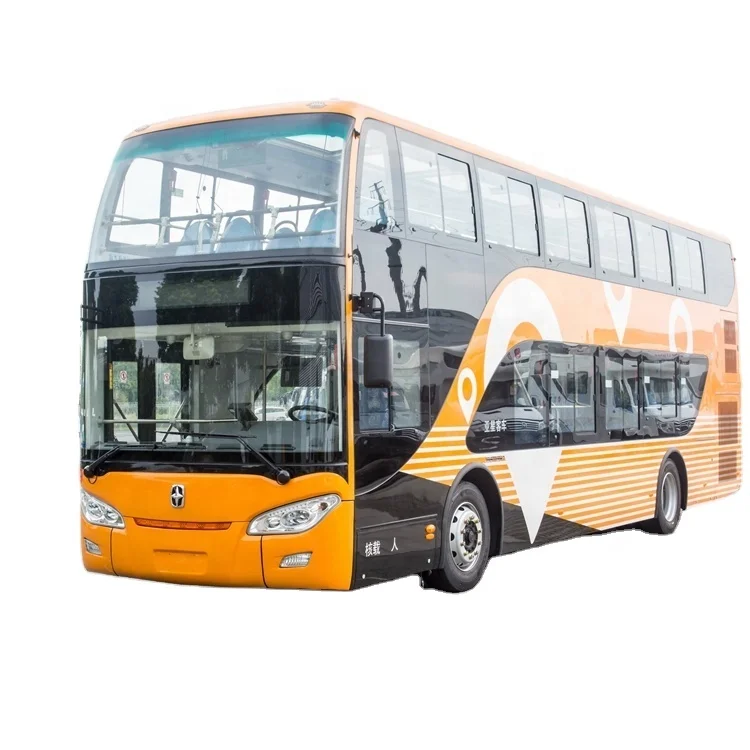
A stock image related to city bu manufacturer.
-
How do I vet potential city bus manufacturers for sustainability practices?
To vet manufacturers for sustainability practices, request information about their environmental policies and certifications, such as ISO 14001. Inquire about their production processes, waste management, and energy efficiency measures. Engage in discussions about their sourcing of materials, particularly if they prioritize eco-friendly options. Consider conducting site visits to observe their operations firsthand. A manufacturer committed to sustainability not only aligns with global trends but can also enhance your brand’s reputation in increasingly eco-conscious markets. -
What are the common challenges faced by B2B buyers when sourcing city buses internationally?
B2B buyers often encounter challenges such as language barriers, differing regulations, and cultural differences when sourcing city buses internationally. To mitigate these issues, consider working with local intermediaries who understand the regional market dynamics. Establish clear communication channels and set expectations early in the relationship. Additionally, stay informed about international trade agreements that may affect tariffs and duties. Developing a comprehensive understanding of these challenges will enable you to navigate the complexities of international sourcing more effectively.
Important Disclaimer & Terms of Use
⚠️ Important Disclaimer
The information provided in this guide, including content regarding manufacturers, technical specifications, and market analysis, is for informational and educational purposes only. It does not constitute professional procurement advice, financial advice, or legal advice.
While we have made every effort to ensure the accuracy and timeliness of the information, we are not responsible for any errors, omissions, or outdated information. Market conditions, company details, and technical standards are subject to change.
B2B buyers must conduct their own independent and thorough due diligence before making any purchasing decisions. This includes contacting suppliers directly, verifying certifications, requesting samples, and seeking professional consultation. The risk of relying on any information in this guide is borne solely by the reader.
Strategic Sourcing Conclusion and Outlook for city bu manufacturer
In today’s competitive landscape, strategic sourcing stands as a pivotal approach for international B2B buyers, especially those operating in diverse markets across Africa, South America, the Middle East, and Europe. By leveraging robust supplier networks and understanding regional market dynamics, businesses can optimize their procurement processes, reduce costs, and enhance product quality.
How Can Strategic Sourcing Enhance Your Competitive Edge?
The key takeaways for B2B buyers include the importance of developing strong relationships with local and global suppliers, conducting thorough market research to identify the best sourcing options, and embracing technology to streamline procurement. Additionally, understanding the cultural nuances and regulatory environments in different regions can significantly impact sourcing decisions and outcomes.
What Does the Future Hold for City BU Manufacturers?
Looking ahead, the emphasis on sustainable practices and ethical sourcing will continue to shape the city BU manufacturing sector. B2B buyers should prepare to adapt to these trends by prioritizing suppliers who demonstrate environmental responsibility and social accountability.
As you navigate this evolving landscape, consider implementing a strategic sourcing framework tailored to your specific market needs. Collaborate with trusted partners and remain vigilant in your sourcing efforts to ensure long-term success in your operations. Embrace the opportunities that lie ahead and position your business for growth in the global marketplace.