The Ultimate Guide to Table Tennis Table Manufacturer (2025)
Introduction: Navigating the Global Market for table tennis table manufacturer
In the rapidly evolving landscape of global trade, sourcing high-quality table tennis tables presents a unique challenge for international B2B buyers, especially those from regions such as Africa, South America, the Middle East, and Europe. As demand for recreational sports equipment surges, it becomes essential for buyers to navigate the complexities of selecting the right table tennis table manufacturer. This guide aims to streamline the procurement process by providing actionable insights into various types of tables, their applications, and the critical factors to consider when vetting suppliers.
Understanding the nuances of table tennis tables—from construction materials to design specifications—can significantly impact purchasing decisions. This comprehensive guide will delve into essential topics such as manufacturing standards, pricing strategies, and supplier reliability, empowering buyers to make informed choices that align with their business objectives.
For B2B buyers in countries like Vietnam and Colombia, where the sports equipment market is burgeoning, this resource serves as a crucial tool in ensuring that they not only meet the expectations of their clientele but also enhance their competitive edge. By the end of this guide, you will be equipped with the knowledge to confidently engage with manufacturers, negotiate better terms, and ultimately, procure the best table tennis tables for your specific needs.
Understanding table tennis table manufacturer Types and Variations
Type Name | Key Distinguishing Features | Primary B2B Applications | Brief Pros & Cons for Buyers |
---|---|---|---|
Indoor Table Tennis Tables | Made from high-quality plywood or MDF, often with a smooth finish for enhanced gameplay. | Schools, gyms, and recreational centers | Pros: Excellent bounce and durability. Cons: Not suitable for outdoor use. |
Outdoor Table Tennis Tables | Constructed from weather-resistant materials like aluminum composite, designed for outdoor conditions. | Parks, resorts, and outdoor sports facilities | Pros: Durable against elements. Cons: Heavier and may require more maintenance. |
Competition-Grade Tables | Built to international standards, featuring adjustable legs and high-quality surfaces for professional play. | Tournaments, clubs, and training centers | Pros: Superior performance and stability. Cons: Higher cost and specific maintenance needs. |
Foldable Table Tennis Tables | Designed for easy storage and transportation, often featuring a compact folding mechanism. | Home use, temporary setups, and events | Pros: Space-saving and portable. Cons: May compromise on stability compared to fixed tables. |
Customizable Tables | Allows buyers to select materials, colors, and sizes tailored to specific needs. | Corporate events, branding opportunities | Pros: Unique branding options. Cons: Longer lead times and potential higher costs. |
What Are the Key Characteristics of Indoor Table Tennis Tables?
Indoor table tennis tables are typically made from high-quality materials like plywood or MDF, ensuring a smooth surface for optimal gameplay. They are designed for use in controlled environments, such as schools and gyms. When considering an indoor table, buyers should evaluate factors like surface quality, thickness, and the overall durability of the frame, as these affect the table’s playability and longevity.
How Do Outdoor Table Tennis Tables Differ from Indoor Models?
Outdoor table tennis tables are constructed from weather-resistant materials, such as aluminum composite, making them ideal for parks and outdoor recreational facilities. Their design focuses on durability against the elements, and they often feature a heavier build to withstand wind. Buyers should consider the table’s weight, material quality, and maintenance requirements when selecting an outdoor model.
What Makes Competition-Grade Tables Essential for Professional Use?
Competition-grade tables are built to meet international standards and are often used in tournaments and training centers. They feature adjustable legs, high-quality surfaces, and a stable construction that ensures consistent performance. B2B buyers should prioritize specifications like bounce quality and surface smoothness, as these can significantly impact competitive play.
Why Choose Foldable Table Tennis Tables for Versatile Use?
Foldable table tennis tables are designed for easy storage and portability, making them suitable for home use or temporary setups at events. While they save space, buyers should be mindful of their stability and durability compared to traditional fixed tables. Assessing the folding mechanism and overall weight is crucial for ensuring ease of use and transportation.
What Are the Benefits of Customizable Table Tennis Tables?
Customizable tables allow buyers to select specific materials, colors, and sizes to meet unique needs, making them popular for corporate events and branding opportunities. While they provide a distinctive look, buyers should be aware of potential longer lead times and higher costs associated with customization. Evaluating the supplier’s capabilities in customization can enhance the purchasing experience.
Related Video: Understanding Spin | Killerspin Table Tennis Lessons
Key Industrial Applications of table tennis table manufacturer
Industry/Sector | Specific Application of Table Tennis Table Manufacturer | Value/Benefit for the Business | Key Sourcing Considerations for this Application |
---|---|---|---|
Educational Institutions | Table tennis tables for schools and universities | Enhances student engagement and physical fitness | Durability, safety standards, and customization options |
Corporate Wellness Programs | Table tennis tables in office recreational areas | Boosts employee morale and promotes teamwork | Space requirements, table size, and assembly options |
Sports Clubs and Associations | Professional-grade tables for training and tournaments | Supports competitive play and skill development | Quality materials, international shipping logistics |
Community Recreation Centers | Public access tables for recreational use | Encourages community interaction and healthy activities | Weather resistance, maintenance needs, and cost-effectiveness |
Hospitality Sector | Tables for hotels and resorts’ leisure facilities | Attracts guests and enhances the overall experience | Aesthetic appeal, brand alignment, and warranty terms |
How Are Table Tennis Tables Used in Educational Institutions?
In educational settings, table tennis tables are essential for promoting physical activity and fostering social interaction among students. They serve as a valuable tool for physical education programs, helping to develop coordination and sportsmanship. International buyers, particularly from Africa and South America, should ensure that the tables meet local safety standards and are robust enough to withstand heavy use. Customization options may also be important to fit specific space requirements in schools.
What Role Do Table Tennis Tables Play in Corporate Wellness Programs?
Table tennis tables in corporate environments are increasingly popular as part of wellness initiatives. They provide employees with a fun way to relieve stress and engage in physical activity during breaks. For buyers in the Middle East and Europe, sourcing tables that are both aesthetically pleasing and durable is crucial, as they need to blend seamlessly into office decor while withstanding frequent use. Considerations such as size and assembly ease are also key to ensuring they fit within the available office space.
Why Are Professional-Grade Tables Important for Sports Clubs?
For sports clubs and associations, investing in professional-grade table tennis tables is vital for training athletes and hosting tournaments. These tables enhance the competitive experience, providing players with high-quality equipment that meets international standards. Buyers from regions like Europe and South America should prioritize sourcing tables made from premium materials that offer durability and consistent playing surfaces, while also considering logistics for international shipping.
How Do Community Recreation Centers Benefit from Table Tennis Tables?
Community recreation centers utilize table tennis tables to foster social interaction and promote healthy activities among residents. These tables are often accessible to the public, encouraging participation in recreational sports. Buyers from Africa and South America should focus on sourcing weather-resistant tables that require minimal maintenance, ensuring they remain functional in various environments and can withstand outdoor conditions.
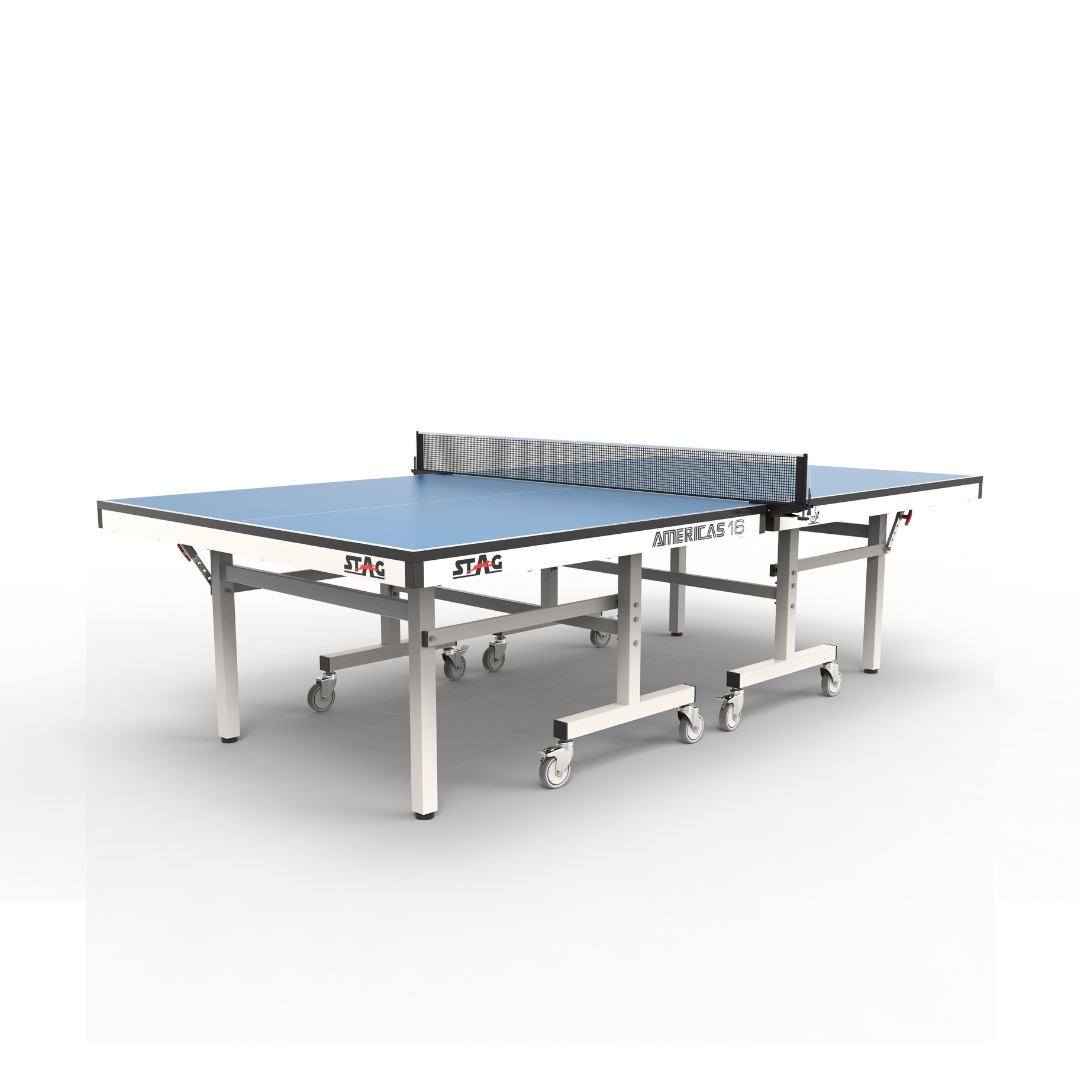
A stock image related to table tennis table manufacturer.
What Are the Advantages of Table Tennis Tables in the Hospitality Sector?
In the hospitality sector, table tennis tables can significantly enhance guest experiences at hotels and resorts. They attract visitors by offering engaging recreational activities, which can lead to longer stays and positive reviews. For international buyers, particularly from Europe and the Middle East, the focus should be on sourcing aesthetically appealing tables that align with the hotel’s branding while also considering warranty terms and customer support for maintenance needs.
Related Video: Sources and Uses Table
3 Common User Pain Points for ‘table tennis table manufacturer’ & Their Solutions
Scenario 1: Difficulty in Sourcing Quality Table Tennis Tables for Commercial Use
The Problem:
B2B buyers, particularly those in the hospitality or sports sectors in regions like Africa and South America, often face challenges when sourcing quality table tennis tables. Many manufacturers provide subpar products that do not withstand heavy usage or varying climatic conditions, leading to dissatisfaction among customers and potential loss of business. Buyers may also struggle with the lack of reliable suppliers who can provide consistent quality and timely delivery, resulting in operational delays.
The Solution:
To mitigate these issues, buyers should conduct thorough research on manufacturers’ reputations and product durability. Look for manufacturers that provide detailed specifications and testing results for their tables. Consider establishing direct communication channels with potential suppliers to discuss your specific needs and inquire about their quality assurance processes. Additionally, requesting samples or visiting production facilities can help ensure the tables meet your standards before committing to a large order. Leveraging platforms like Alibaba or regional trade fairs can also introduce you to reliable manufacturers with proven track records in quality.
Scenario 2: Complex Import Regulations and Shipping Logistics
The Problem:
Navigating the complex landscape of import regulations can be a significant pain point for B2B buyers in the Middle East and Europe. Buyers may encounter unexpected customs fees, import duties, and lengthy shipping times, which can disrupt their supply chains. Furthermore, understanding the documentation and compliance requirements for importing table tennis tables can be overwhelming, particularly for first-time importers.
The Solution:
To overcome these challenges, it is crucial for buyers to partner with logistics experts who specialize in international shipping. These professionals can provide invaluable guidance on the documentation required for customs clearance, such as commercial invoices, packing lists, and import permits. Additionally, establishing a relationship with a freight forwarder can help streamline the shipping process and reduce costs through bulk shipping or consolidated freight options. Buyers should also stay updated on local import regulations by consulting with trade associations or government trade departments, ensuring compliance and avoiding potential penalties.
Scenario 3: Inadequate After-Sales Support and Warranty Issues
The Problem:
After-sales support is a significant concern for B2B buyers in the table tennis industry, particularly when it comes to warranty claims and maintenance services. Buyers may find themselves stranded with defective products or insufficient guidance on repairs, leading to extended downtime and frustration. This is especially critical for businesses that rely on table tennis tables for revenue-generating activities, such as sports clubs or hotels.
The Solution:
To ensure satisfactory after-sales support, buyers should prioritize manufacturers that offer comprehensive warranties and responsive customer service. Before making a purchase, inquire about the specifics of the warranty, including coverage duration and the process for claiming repairs or replacements. Establishing a clear line of communication with the manufacturer’s support team can also facilitate quicker resolution of any issues. Additionally, consider opting for manufacturers that provide maintenance services or training for your staff on table upkeep. This proactive approach can help reduce long-term costs and improve the lifespan of your investment in table tennis tables.
Strategic Material Selection Guide for table tennis table manufacturer
What Are the Key Materials for Table Tennis Table Manufacturing?
When selecting materials for manufacturing table tennis tables, several factors come into play, including performance, durability, cost, and compliance with international standards. Below are four common materials used in the industry, analyzed from a B2B perspective.
How Does Wood Perform as a Material for Table Tennis Tables?
Key Properties: Wood is known for its excellent playability, providing a natural feel and sound during gameplay. It typically has good temperature resistance, though it can warp under extreme moisture or heat.
Pros & Cons: The primary advantage of wood is its superior performance characteristics, which enhance the playing experience. However, wood can be more expensive and may require more complex manufacturing processes, including cutting, sanding, and finishing. Additionally, it can be less durable than synthetic materials, particularly in outdoor settings.
Impact on Application: Wood tables are generally preferred for indoor use and are often used in professional settings. They may not withstand harsh weather conditions, making them unsuitable for outdoor applications.
Considerations for International Buyers: Buyers from regions like Africa, South America, and the Middle East should consider local climate conditions that could affect wood durability. Compliance with standards such as ASTM for indoor use is crucial.
What Advantages Does Aluminum Offer for Table Tennis Tables?
Key Properties: Aluminum is lightweight, corrosion-resistant, and has a high strength-to-weight ratio. It performs well under varying temperatures and is less likely to warp compared to wood.
Pros & Cons: The key advantage of aluminum is its durability and low maintenance requirements, making it suitable for outdoor tables. However, it may not provide the same level of playability as wood, which can be a disadvantage for competitive players. The manufacturing process for aluminum can also be complex and costly.
Impact on Application: Aluminum tables are ideal for outdoor use and can withstand various weather conditions. They are often used in recreational settings, schools, and community centers.
Considerations for International Buyers: Buyers should ensure that aluminum tables comply with local standards and regulations, particularly in regions with high humidity or extreme temperatures.
How Does MDF Compare as a Material for Table Tennis Tables?
Key Properties: Medium-density fiberboard (MDF) offers a smooth playing surface and is relatively inexpensive compared to solid wood. It has moderate resistance to moisture but can be susceptible to warping if not properly sealed.
Pros & Cons: MDF is cost-effective and easy to manufacture, making it a popular choice for budget-friendly tables. However, it is less durable than wood or aluminum and may not withstand heavy use or outdoor conditions.
Impact on Application: MDF tables are typically used for recreational play and are not recommended for professional settings. They are suitable for indoor use but should be kept away from moisture.
Considerations for International Buyers: Compliance with safety standards such as JIS in Japan or DIN in Europe is essential for MDF products. Buyers should also consider the availability of MDF in their local markets.
What Role Does Plastic Play in Table Tennis Table Manufacturing?
Key Properties: Plastic tables are lightweight, highly durable, and resistant to weather conditions. They are easy to clean and maintain, making them suitable for various environments.
Pros & Cons: The primary advantage of plastic is its durability and low cost. However, plastic tables may not provide the same quality of play as wood or MDF, which can deter serious players.
Impact on Application: Plastic tables are often used in casual settings, such as parks, schools, and recreational centers. They are perfect for outdoor use due to their weather resistance.
Considerations for International Buyers: Buyers should check for compliance with local safety and environmental regulations, especially in regions with strict manufacturing standards.
Summary Table of Material Selection for Table Tennis Tables
Material | Typical Use Case for table tennis table manufacturer | Key Advantage | Key Disadvantage/Limitation | Relative Cost (Low/Med/High) |
---|---|---|---|---|
Wood | Indoor professional tables | Superior playability | Expensive, less durable outdoors | High |
Aluminum | Outdoor recreational tables | Lightweight, corrosion-resistant | Less playability than wood | Medium |
MDF | Budget-friendly indoor tables | Cost-effective, easy to manufacture | Less durable, moisture-sensitive | Low |
Plastic | Casual outdoor tables | Durable, low maintenance | Poor playability for serious players | Low |
This guide provides international B2B buyers with essential insights into material selection for table tennis tables, ensuring informed decisions that align with their specific needs and market conditions.
In-depth Look: Manufacturing Processes and Quality Assurance for table tennis table manufacturer
What are the Key Manufacturing Processes for Table Tennis Tables?
The manufacturing of table tennis tables involves several critical stages, each essential for producing high-quality products that meet international standards. Understanding these stages can help B2B buyers make informed decisions when selecting suppliers.
1. Material Preparation: What Materials are Used in Table Tennis Table Manufacturing?
The first step in the manufacturing process is material preparation. Common materials include:
- Wood: High-density fiberboard (HDF) is often used for the playing surface due to its consistent bounce and durability.
- Metal: Steel is commonly used for the table’s frame and legs, providing stability and support.
- Plastic: Used for components such as the net and clips.
Buyers should verify the quality and sourcing of these materials, as they significantly impact the table’s performance and longevity.
2. Forming: How are Table Tennis Tables Shaped and Sized?
After material preparation, the next stage is forming. This involves:
- Cutting: The wood panels are cut to the standard dimensions of 2.74m x 1.525m for the playing surface.
- Shaping: The edges of the table may be rounded or beveled to enhance aesthetics and safety.
- Coating: The wood is often treated with a primer and finished with a high-quality paint or varnish to protect against moisture and wear.
B2B buyers should inquire about the machinery and techniques used in this stage, as modern CNC machines ensure precision and consistency.
3. Assembly: What are the Steps in Assembling a Table Tennis Table?
The assembly stage includes several steps:
- Joining: Components such as the playing surface, frame, and legs are joined using screws, brackets, or welding, depending on the material.
- Net Assembly: The net system is installed, ensuring it is taut and meets official regulations.
Quality control at this stage is crucial; any misalignment can affect gameplay. Buyers should look for manufacturers that employ skilled labor and adhere to strict assembly guidelines.
4. Finishing: How is the Final Touch Applied to Table Tennis Tables?
Finishing involves applying the final touches to the table:
- Surface Treatment: The playing surface is sanded and treated to provide the right level of grip and smoothness.
- Quality Check: Each table undergoes a thorough inspection to ensure it meets aesthetic and functional standards.
Buyers should ask for samples or demonstrations of finished products to assess quality firsthand.
What Quality Assurance Practices Should B2B Buyers Expect?
Quality assurance (QA) is a critical aspect of manufacturing, ensuring that the final products meet specific standards and customer expectations. Here’s what to look for:
1. International Standards: How Do ISO Certifications Impact Quality?
Manufacturers should adhere to international quality management standards, such as ISO 9001. This certification indicates that a company has established a quality management system (QMS) that meets customer and regulatory requirements. Buyers should request proof of certifications to verify compliance.
2. Industry-Specific Standards: What Certifications are Relevant for Table Tennis Tables?
In addition to ISO certifications, certain industry-specific standards are applicable:
- CE Marking: Required for products sold in the European Economic Area, indicating compliance with health, safety, and environmental protection standards.
- API Certification: Relevant for products that may be used in more industrial applications or settings.
Understanding these certifications helps buyers ensure that products are safe and reliable.
3. Quality Control Checkpoints: What Are the Key Stages of Quality Control?
Quality control (QC) checkpoints are integral throughout the manufacturing process:
- Incoming Quality Control (IQC): Materials are inspected upon arrival to ensure they meet specifications.
- In-Process Quality Control (IPQC): Ongoing inspections during production to catch defects early.
- Final Quality Control (FQC): Comprehensive testing of the finished product before shipment.
Buyers should inquire about the frequency and methods of these inspections to gauge the manufacturer’s commitment to quality.
What Common Testing Methods are Used in Table Tennis Table Manufacturing?
Manufacturers should employ a variety of testing methods to ensure product quality:
- Bounce Tests: Assess the consistency and quality of the playing surface.
- Durability Tests: Simulate wear and tear to evaluate the longevity of materials and construction.
- Safety Tests: Ensure that the table meets safety standards, including stability and structural integrity.
B2B buyers should request test reports or certifications from third-party laboratories to validate these assessments.
How Can B2B Buyers Verify Supplier Quality Assurance?
When sourcing table tennis tables, buyers can take several steps to verify the quality assurance practices of suppliers:
1. Conducting Audits: What Should Be Included in a Supplier Audit?
Auditing potential suppliers can provide insights into their manufacturing processes and quality assurance systems. Key areas to assess include:
- Facility Inspection: Evaluate the manufacturing environment for cleanliness and organization.
- Process Evaluation: Review production workflows and quality control practices.
- Documentation Review: Check for compliance with international standards and internal QA protocols.
2. Requesting Reports: What Documentation is Essential for B2B Buyers?
Buyers should request comprehensive reports on:
- Quality Control Procedures: Documentation outlining the QC process and checkpoints.
- Test Results: Evidence of testing methods and outcomes for product performance.
- Certifications: Copies of relevant certifications to validate compliance with industry standards.
3. Engaging Third-Party Inspectors: How Can Third-Party Services Enhance Quality Assurance?
Hiring third-party inspection services can provide an unbiased assessment of a supplier’s quality assurance processes. These inspectors can conduct thorough evaluations and offer detailed reports, giving buyers confidence in their purchasing decisions.
Conclusion: How to Ensure Quality in Your Table Tennis Table Procurement
For B2B buyers in Africa, South America, the Middle East, and Europe, understanding the manufacturing processes and quality assurance practices of table tennis table manufacturers is crucial. By focusing on material quality, manufacturing techniques, and robust QC measures, buyers can ensure they partner with reliable suppliers who deliver high-quality products that meet international standards.
Practical Sourcing Guide: A Step-by-Step Checklist for ‘table tennis table manufacturer’
In this practical sourcing guide, B2B buyers seeking to procure table tennis tables from manufacturers will find a step-by-step checklist designed to streamline the process. This guide aims to equip buyers with essential actions to ensure quality, compliance, and cost-effectiveness while facilitating successful partnerships with manufacturers.
Step 1: Define Your Technical Specifications
Establishing clear technical specifications is crucial for ensuring that the table tennis tables meet your quality and performance expectations. Outline parameters such as materials (e.g., plywood or MDF), dimensions (regulatory sizes), and features (foldability, weather resistance). This clarity helps streamline communication with potential suppliers and prevents misunderstandings later in the process.
Step 2: Research Potential Suppliers
Conduct thorough research to identify potential manufacturers. Utilize online directories, trade shows, and industry forums to compile a list of suppliers specializing in table tennis tables. Pay attention to their experience in the industry, geographical location, and production capabilities to ensure they align with your sourcing needs.
Step 3: Evaluate Supplier Certifications and Compliance
Before moving forward, verify that potential suppliers hold the necessary certifications. Look for compliance with international standards such as ISO 9001 for quality management and EN 14468 for sports equipment safety. This step is vital in ensuring that the products are safe and reliable, which is especially important for sports equipment used by various demographics.
Step 4: Request Samples and Prototypes
Requesting samples or prototypes allows you to assess the quality and craftsmanship of the tables firsthand. This step is essential for evaluating the materials used, finish quality, and overall design. Ensure that the sample matches your defined specifications to avoid potential discrepancies in the final order.
Step 5: Assess Production Capacity and Lead Times
Understanding a supplier’s production capacity and lead times is critical for planning your inventory and sales strategy. Inquire about their manufacturing processes and their ability to scale production to meet your demand. Additionally, confirm their typical lead times to ensure timely delivery, especially if you have specific deadlines or seasonal demands.
Step 6: Negotiate Pricing and Terms
Once you’ve shortlisted potential suppliers, initiate negotiations on pricing, payment terms, and delivery conditions. It’s essential to achieve a balance between cost and quality; therefore, consider requesting bulk order discounts or flexible payment options. Be clear about your expectations regarding warranties, returns, and after-sales support to avoid future complications.
Step 7: Establish Communication Channels
Effective communication is the backbone of a successful supplier relationship. Establish clear channels for ongoing dialogue, including regular updates on production status and responsiveness to inquiries. This proactive approach fosters trust and can lead to better collaboration, ensuring that any issues are addressed promptly.
By following this checklist, B2B buyers can navigate the procurement process for table tennis tables more effectively, leading to informed decisions and successful partnerships with manufacturers.
Comprehensive Cost and Pricing Analysis for table tennis table manufacturer Sourcing
What Are the Key Cost Components for Sourcing Table Tennis Tables?
When sourcing table tennis tables, understanding the cost structure is crucial for international B2B buyers. The primary cost components include:
-
Materials: The choice of materials significantly impacts the cost. High-quality wood or composite materials may increase initial expenses but can enhance durability and performance, providing better value in the long run.
-
Labor: Labor costs can vary widely depending on the manufacturing location. Countries with lower labor costs, such as Vietnam or Colombia, can offer competitive pricing, but this may come with trade-offs in quality and consistency.
-
Manufacturing Overhead: This includes costs associated with factory operations, such as utilities, equipment maintenance, and facility management. Efficient manufacturing processes can reduce these overheads, impacting the overall price.
-
Tooling: Initial setup costs for molds and machinery can be substantial, especially for custom designs. Buyers should inquire about tooling costs and whether they are included in the overall price or charged separately.
-
Quality Control (QC): Implementing robust QC processes is essential to ensure that products meet specified standards. While this may add to costs, it can prevent costly returns and dissatisfaction later.
-
Logistics: Shipping costs, tariffs, and handling fees play a significant role in the total cost. Buyers should consider the distance from the manufacturer and the chosen shipping method, as these factors can vary greatly.
-
Margin: Manufacturers will typically add a profit margin to their costs. Understanding the typical margins in the industry can help buyers gauge whether a quoted price is reasonable.
How Do Price Influencers Affect Table Tennis Table Costs?
Several factors influence pricing beyond the basic cost components:
-
Volume/MOQ (Minimum Order Quantity): Bulk orders often lead to lower per-unit costs. Buyers should evaluate their purchasing needs to leverage volume discounts effectively.
-
Specifications and Customization: Custom designs or additional features can increase costs. Buyers need to balance the desire for customization with budget constraints.
-
Materials and Quality Certifications: Higher-quality materials and certifications (e.g., ITTF approval for competitive play) can elevate prices. Buyers should assess the necessity of these features based on their target market.
-
Supplier Factors: The reputation, reliability, and production capabilities of the supplier can influence pricing. Established suppliers may charge more but can offer better quality assurance.
-
Incoterms: The chosen Incoterms (International Commercial Terms) dictate who is responsible for shipping costs and risks. This affects overall pricing and should be clearly understood during negotiations.
What Are Effective Buyer Tips for Negotiating Table Tennis Table Prices?
For international B2B buyers, particularly those from Africa, South America, the Middle East, and Europe, here are some actionable tips:
-
Negotiate Effectively: Always negotiate pricing based on detailed cost breakdowns. Understanding the components can provide leverage in discussions.
-
Focus on Cost-Efficiency: Assess the Total Cost of Ownership (TCO) rather than just the initial purchase price. Consider factors such as durability, maintenance, and potential resale value.
-
Understand Pricing Nuances: Prices can fluctuate based on economic conditions, material availability, and exchange rates. Staying informed about market trends can aid in making timely purchasing decisions.
-
Establish Clear Communication: Ensure that all terms, including delivery schedules and quality expectations, are clearly communicated to avoid misunderstandings that could lead to additional costs.
-
Seek Multiple Quotes: Always obtain quotes from several suppliers. This not only provides a range of pricing options but also helps in understanding the market standard.
Disclaimer on Indicative Prices
Prices for table tennis tables can vary significantly based on the aforementioned factors. The information provided here serves as a general guide. Buyers should conduct thorough market research and supplier evaluations to obtain accurate pricing tailored to their specific needs.
Alternatives Analysis: Comparing table tennis table manufacturer With Other Solutions
When evaluating options for sourcing table tennis tables, international B2B buyers, especially from regions like Africa, South America, the Middle East, and Europe, should consider a range of alternatives to traditional table tennis table manufacturers. Understanding these alternatives can help buyers make informed decisions based on their specific needs, budget, and operational constraints.
Comparison Table of Alternatives
Comparison Aspect | Table Tennis Table Manufacturer | Modular Table Solutions | Custom DIY Table Solutions |
---|---|---|---|
Performance | High-quality, durable tables | Versatile, adaptable | Variable, depends on materials used |
Cost | Moderate to high | Moderate | Low to moderate |
Ease of Implementation | Easy, with delivery options | Requires assembly | Requires technical skills |
Maintenance | Low, with warranty options | Moderate, depends on materials | High, variable upkeep |
Best Use Case | Professional tournaments | Schools, community centers | Hobbyists, custom settings |
What Are the Benefits and Drawbacks of Modular Table Solutions?
Modular table solutions offer flexibility and adaptability, making them a great choice for buyers in dynamic environments like schools or community centers. They can be easily reconfigured or expanded based on space requirements. However, they typically require assembly, which may necessitate additional time and effort. Maintenance is moderate, as the durability of components can vary based on the materials used.
How Do Custom DIY Table Solutions Compare?
For buyers with a limited budget or specific design needs, custom DIY table solutions present a viable alternative. These tables can be tailored to specific dimensions or styles, making them ideal for hobbyists or niche settings. However, the performance can vary greatly based on the materials and craftsmanship involved, and they may require significant upkeep over time. Additionally, creating a DIY table demands technical skills, which may not be feasible for all buyers.
Conclusion: How Should B2B Buyers Choose the Right Solution?
Choosing the right solution for sourcing table tennis tables depends on a variety of factors, including budget, performance requirements, and intended use. Buyers in Africa, South America, the Middle East, and Europe should carefully assess their unique needs—such as whether they require high durability for professional use or cost-effective options for recreational purposes. By evaluating the performance, cost, ease of implementation, and maintenance of each alternative, B2B buyers can make an informed choice that aligns with their operational goals.
Essential Technical Properties and Trade Terminology for table tennis table manufacturer
What Are the Essential Technical Properties for Table Tennis Tables?
When sourcing table tennis tables, understanding the technical specifications is crucial for making informed purchasing decisions. Here are some essential properties to consider:
1. Material Grade: Why Is It Important?
The material used in table tennis tables significantly affects their durability and performance. Common materials include high-density fiberboard (HDF) and plywood, which are preferred for their balance of weight and resilience. HDF typically offers a smoother playing surface, making it essential for competitive play. Buyers should seek tables constructed from at least 19mm thick HDF for optimal performance.
2. Surface Finish: How Does It Affect Playability?
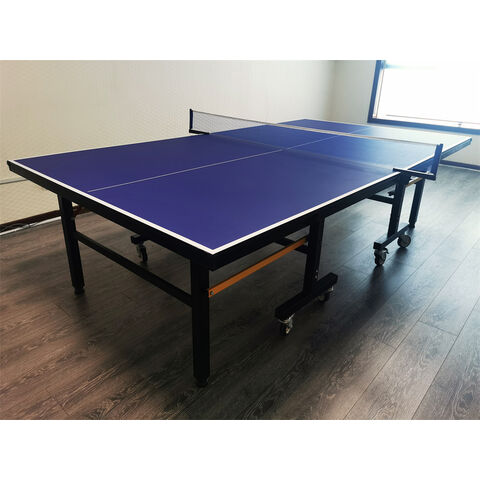
A stock image related to table tennis table manufacturer.
The surface finish impacts how the ball interacts with the table. A quality finish, such as a melamine or lacquer coating, enhances the table’s resistance to scratches and moisture, extending its lifespan. For international buyers, especially in humid climates, selecting a table with a robust finish is vital to ensure consistent performance over time.
3. Tolerance Levels: What Should You Look For?
Tolerance refers to the allowable deviation from specified dimensions, which is crucial for ensuring a level playing surface. A tolerance of ±1mm is recommended for competition-grade tables. This precision is essential for maintaining fairness and consistency in gameplay, making it a critical consideration for B2B buyers who prioritize competitive standards.
4. Frame Construction: Why Is It a Key Factor?
The frame’s construction material and design contribute to the overall stability and longevity of the table. Steel frames are commonly used for their strength and durability, while folding mechanisms should be robust and easy to operate. Buyers should assess the weight capacity of the frame to ensure it can withstand rigorous use, especially in commercial settings.
5. Weight and Portability: How Do They Impact Usage?
The weight of the table influences its portability and stability. Heavier tables are generally more stable but can be less portable, while lighter tables offer easier mobility but may sacrifice stability. For commercial buyers in regions like Africa and South America, where transport can be challenging, understanding the trade-offs between weight and usability is essential.
What Trade Terms Should B2B Buyers Be Familiar With?
Understanding trade terminology is equally important for navigating the procurement process. Here are several key terms you should know:
1. OEM (Original Equipment Manufacturer): What Does It Mean?
OEM refers to a company that produces parts or equipment that may be marketed by another manufacturer. For B2B buyers, partnering with an OEM can lead to cost savings and customization options, allowing for tailored solutions that meet specific market demands.
2. MOQ (Minimum Order Quantity): Why Is It Relevant?
MOQ is the smallest quantity of a product that a supplier is willing to sell. Understanding MOQ is crucial for budgeting and inventory management. For international buyers, especially in Europe, negotiating lower MOQs can help mitigate risks associated with overstocking.
3. RFQ (Request for Quotation): How Is It Used?
An RFQ is a document sent to suppliers to request pricing information for specific products. Utilizing RFQs helps buyers compare offers from multiple manufacturers, ensuring they secure the best deal. This practice is particularly beneficial for B2B buyers in competitive markets.
4. Incoterms: What Are They and Why Do They Matter?
Incoterms are international commercial terms that define the responsibilities of buyers and sellers in shipping agreements. Familiarity with these terms is essential for international transactions, as they clarify who bears the costs and risks associated with transporting goods. Understanding Incoterms can prevent costly misunderstandings in the supply chain.
5. Lead Time: What Should Buyers Expect?
Lead time refers to the time it takes from placing an order to receiving the product. Knowing the lead time is crucial for inventory planning and ensuring timely availability for customers. For international buyers, understanding lead times can help manage expectations and improve supply chain efficiency.
By grasping these technical properties and trade terms, B2B buyers can make more informed decisions when sourcing table tennis tables, ensuring they meet their specific needs and market conditions.
Navigating Market Dynamics and Sourcing Trends in the table tennis table manufacturer Sector
What Are the Current Market Dynamics and Sourcing Trends in the Table Tennis Table Manufacturing Sector?
The global table tennis table manufacturing sector is experiencing significant growth, driven by increasing interest in sports and recreational activities, particularly in developing regions such as Africa, South America, and the Middle East. The rise in sporting events and an emphasis on fitness have catalyzed demand for quality table tennis tables. In addition, the influence of major international events, such as the Olympics and World Championships, has spurred interest in table tennis as a competitive sport.
Emerging B2B technologies are reshaping sourcing trends in this sector. Innovations such as 3D printing and advanced materials are enabling manufacturers to offer customized solutions, enhancing product differentiation. Furthermore, the integration of digital supply chain management tools is allowing manufacturers to streamline operations, reduce lead times, and improve inventory management. International buyers are increasingly seeking suppliers who can provide real-time data and transparency throughout the supply chain, which is crucial for maintaining competitiveness in today’s fast-paced market.
For buyers from regions like Europe and Latin America, understanding local market dynamics is essential. For instance, European buyers are focusing on high-quality, durable products that meet strict safety standards, while South American buyers may prioritize cost-effectiveness and accessibility. Therefore, international B2B buyers should conduct thorough market research to identify the specific needs and preferences of their target regions.
How Is Sustainability Influencing Sourcing Decisions in the Table Tennis Table Manufacturing Industry?
Sustainability is becoming a pivotal concern for international B2B buyers in the table tennis table manufacturing sector. The environmental impact of manufacturing processes, from sourcing raw materials to production and distribution, is under scrutiny. Buyers are increasingly looking for manufacturers who prioritize sustainable practices, such as using eco-friendly materials and reducing waste throughout the supply chain.
Ethical sourcing is equally important. Buyers are encouraged to assess the supply chains of potential manufacturers for compliance with ethical labor practices and environmental regulations. Certifications such as Forest Stewardship Council (FSC) for wood sourcing and ISO 14001 for environmental management systems are becoming vital indicators of a supplier’s commitment to sustainability.
Moreover, many manufacturers are investing in ‘green’ materials and technologies, which not only appeal to eco-conscious consumers but can also enhance brand reputation. For instance, the use of recycled materials in production processes is gaining traction. Buyers should prioritize partnerships with manufacturers that demonstrate a commitment to sustainability, as this can provide a competitive edge in markets increasingly driven by consumer awareness and environmental responsibility.
What Is the Historical Context of the Table Tennis Table Manufacturing Sector?
The history of table tennis table manufacturing can be traced back to the late 19th century when the sport began to gain popularity in England. Originally crafted from simple materials, these tables evolved significantly with advancements in technology and materials science. The introduction of specialized plywood and high-density fiberboard in the mid-20th century revolutionized the industry, allowing for enhanced durability and performance.
As the sport grew globally, particularly in Asia and Europe, the demand for quality tables surged, leading to the establishment of dedicated manufacturers. The late 20th and early 21st centuries saw a focus on innovation, with manufacturers developing tables that are not only functional but also aesthetically appealing, catering to both recreational and competitive markets. This evolution reflects broader trends in consumer preferences and technological advancements, which continue to shape the sector today.
In conclusion, international B2B buyers in the table tennis table manufacturing sector must navigate a complex landscape characterized by evolving market dynamics, sustainability imperatives, and a rich historical context that informs current trends. Understanding these factors is essential for making informed sourcing decisions and establishing successful partnerships in this competitive industry.
Frequently Asked Questions (FAQs) for B2B Buyers of table tennis table manufacturer
-
How do I choose the right table tennis table manufacturer for my business needs?
Selecting the ideal table tennis table manufacturer involves assessing their product range, quality, and certifications. Look for manufacturers with experience in the industry and positive reviews from other B2B clients. Request samples to evaluate materials and craftsmanship. Additionally, consider their ability to customize tables to suit your brand or specific requirements. Finally, ensure they can meet your delivery timelines and have a solid after-sales support system in place. -
What are the typical minimum order quantities (MOQs) when sourcing table tennis tables?
Minimum order quantities can vary widely among table tennis table manufacturers. Typically, MOQs range from 50 to 200 units, depending on the manufacturer and customization options. Some manufacturers may offer lower MOQs for standard models but might require higher quantities for customized designs. It’s crucial to communicate your needs clearly and negotiate terms that align with your budget and inventory capacity. -
What payment terms should I expect when working with a table tennis table manufacturer?
Payment terms often vary, but many manufacturers will require a deposit (usually 30-50%) upfront before production begins, with the balance due upon completion or before shipment. Some may offer flexible payment options such as letters of credit or installment plans, especially for larger orders. Ensure to clarify these terms during negotiations to avoid any surprises and establish a mutually beneficial agreement. -
How can I ensure the quality of table tennis tables before making a bulk purchase?
To ensure quality, request certifications and compliance documents from the manufacturer that demonstrate adherence to international standards. Conduct a factory visit if possible, or arrange for a third-party quality inspection service to evaluate product quality before shipment. Additionally, consider starting with a smaller order or a sample batch to assess quality firsthand before committing to larger quantities. -
What customization options are typically available for table tennis tables?
Many manufacturers offer customization options such as color, size, branding, and additional features like foldability or specialized surfaces. Discuss your specific needs with the manufacturer, as some may have limitations on what can be customized based on their production capabilities. Be clear about your requirements early in the process to ensure the final product aligns with your brand vision.
- What logistics considerations should I keep in mind when sourcing table tennis tables internationally?
Logistics play a critical role in international sourcing. Consider shipping methods, costs, and estimated delivery times. Ensure the manufacturer has experience with international shipping and can provide proper documentation for customs clearance. It’s also wise to discuss insurance options for your shipment to mitigate risks during transit. Finally, factor in potential tariffs or duties that may apply upon importation to your country.
-
How do I vet a table tennis table manufacturer for reliability and reputation?
Vetting a manufacturer involves checking their business credentials, such as years in operation, industry certifications, and customer reviews. Utilize online platforms, trade shows, and industry contacts to gather information. Request references from previous clients to understand their experiences. Additionally, consider reviewing their production processes and quality control measures to ensure they align with your standards. -
What are the common challenges faced when sourcing table tennis tables, and how can I overcome them?
Common challenges include communication barriers, quality discrepancies, and delayed shipments. To overcome these, establish clear communication channels and use professional translation services if necessary. Set realistic timelines and maintain regular contact with the manufacturer throughout the production process. Utilizing third-party inspections can help mitigate quality issues, ensuring that products meet your expectations before shipment.
Important Disclaimer & Terms of Use
⚠️ Important Disclaimer
The information provided in this guide, including content regarding manufacturers, technical specifications, and market analysis, is for informational and educational purposes only. It does not constitute professional procurement advice, financial advice, or legal advice.
While we have made every effort to ensure the accuracy and timeliness of the information, we are not responsible for any errors, omissions, or outdated information. Market conditions, company details, and technical standards are subject to change.
B2B buyers must conduct their own independent and thorough due diligence before making any purchasing decisions. This includes contacting suppliers directly, verifying certifications, requesting samples, and seeking professional consultation. The risk of relying on any information in this guide is borne solely by the reader.
Strategic Sourcing Conclusion and Outlook for table tennis table manufacturer
The landscape of strategic sourcing for table tennis table manufacturers is evolving, particularly for international B2B buyers in Africa, South America, the Middle East, and Europe. Understanding the nuances of sourcing—such as identifying reliable suppliers, negotiating favorable terms, and ensuring quality standards—can significantly impact your business’s success. By leveraging strategic sourcing, buyers can not only optimize costs but also enhance product quality and delivery times, ultimately leading to improved customer satisfaction.
As global markets become increasingly interconnected, the importance of strategic sourcing cannot be overstated. It allows businesses to tap into diverse supplier networks, mitigate risks associated with supply chain disruptions, and adapt to changing market demands. For buyers from regions like Vietnam and Colombia, embracing these strategies can open doors to innovative products and competitive pricing, fostering growth in local markets.
Looking ahead, international B2B buyers should prioritize establishing strong relationships with manufacturers that align with their strategic goals. By doing so, they can position themselves for success in an ever-competitive landscape. Now is the time to evaluate your sourcing strategies and seek out partnerships that will drive your business forward.