The Ultimate Guide to Ultrasonic Sensor Manufacturer (2025)
Introduction: Navigating the Global Market for ultrasonic sensor manufacturer
In today’s rapidly evolving industrial landscape, sourcing the right ultrasonic sensor manufacturer can be a daunting task for international B2B buyers. With the increasing demand for precision in applications ranging from automotive to manufacturing, the challenge lies in identifying a reliable supplier that meets both quality standards and budget constraints. This comprehensive guide is designed to equip businesses from Africa, South America, the Middle East, and Europe—particularly Germany and Mexico—with the insights needed to navigate the complexities of the global ultrasonic sensor market.
The guide covers a broad spectrum of essential topics, including the different types of ultrasonic sensors available, their diverse applications across various industries, and best practices for supplier vetting. Additionally, we delve into cost considerations and potential pitfalls to avoid when selecting a manufacturer. By understanding these key areas, B2B buyers can make informed decisions that align with their operational needs and strategic goals.
Whether you are looking to enhance product efficiency, improve safety measures, or reduce operational costs, this guide serves as a valuable resource. With actionable insights and data-driven recommendations, it empowers businesses to confidently engage with ultrasonic sensor manufacturers, ensuring that they select partners who can deliver innovation and reliability in an increasingly competitive marketplace.
Understanding ultrasonic sensor manufacturer Types and Variations
Type Name | Key Distinguishing Features | Primary B2B Applications | Brief Pros & Cons for Buyers |
---|---|---|---|
Contact Ultrasonic Sensors | Direct contact with the object; high precision in measurement | Level measurement in tanks and silos | Pros: High accuracy; Cons: Limited range |
Non-Contact Ultrasonic Sensors | Uses sound waves to detect objects without physical contact | Distance measurement in automotive applications | Pros: Versatile; Cons: Environmental sensitivity |
Ultrasonic Proximity Sensors | Detects presence or absence of objects within a specific range | Robotics and automation systems | Pros: Quick response; Cons: Limited detection range |
Ultrasonic Flow Meters | Measures the flow rate of liquids and gases | Water treatment and industrial processes | Pros: High reliability; Cons: Installation complexity |
Ultrasonic Thickness Gauges | Measures material thickness using ultrasonic waves | Quality control in manufacturing | Pros: Non-destructive; Cons: Requires calibration |
What Are the Characteristics of Contact Ultrasonic Sensors?
Contact ultrasonic sensors are designed to measure the distance or level of materials by directly interacting with them. These sensors are characterized by their high precision and reliability, making them suitable for applications in industries like manufacturing and food processing where accurate level measurement in tanks and silos is critical. When considering a purchase, buyers should evaluate the sensor’s calibration requirements and compatibility with their specific materials.
How Do Non-Contact Ultrasonic Sensors Work?
Non-contact ultrasonic sensors operate by emitting sound waves and measuring the time it takes for the echo to return after hitting an object. This type of sensor is particularly useful in automotive applications for distance measurement and obstacle detection. B2B buyers should consider environmental factors such as temperature and humidity, which can impact sensor performance, as well as the sensor’s range and detection capabilities.
What Are Ultrasonic Proximity Sensors and Their Uses?
Ultrasonic proximity sensors are specialized devices that detect the presence or absence of objects within a defined range, making them ideal for robotics and automation systems. These sensors provide a quick response time, which is essential in high-speed manufacturing environments. Buyers should assess the sensor’s detection range and the types of materials it can effectively sense, as these factors will influence its suitability for specific applications.
Why Choose Ultrasonic Flow Meters for Your Business?
Ultrasonic flow meters measure the flow rate of liquids and gases by analyzing the time it takes for ultrasonic signals to travel between sensors. They are widely used in water treatment facilities and various industrial processes due to their high reliability and accuracy. B2B buyers must consider installation complexity and the need for regular maintenance, as these factors can affect operational efficiency and costs.
What Should You Know About Ultrasonic Thickness Gauges?
Ultrasonic thickness gauges utilize ultrasonic waves to measure the thickness of materials without causing any damage, making them invaluable in quality control processes across industries like manufacturing and construction. These gauges are non-destructive and provide precise measurements, but they require calibration to ensure accuracy. Buyers should evaluate the gauge’s range and the types of materials it can measure, as these will determine its effectiveness for their specific needs.
Related Video: Ultrasonic sensor working principle | How does HC-SR04 Work
Key Industrial Applications of ultrasonic sensor manufacturer
Industry/Sector | Specific Application of Ultrasonic Sensor Manufacturer | Value/Benefit for the Business | Key Sourcing Considerations for this Application |
---|---|---|---|
Manufacturing | Automated Quality Control Systems | Enhances product consistency and reduces waste | Ensure compatibility with existing machinery and standards |
Logistics and Supply Chain | Inventory Management Systems | Improves accuracy in stock levels and reduces costs | Evaluate sensor range and integration with software systems |
Agriculture | Livestock Monitoring | Increases animal welfare and optimizes feeding practices | Consider environmental conditions and sensor durability |
Oil and Gas | Leak Detection Systems | Prevents environmental hazards and reduces downtime | Look for sensors with high sensitivity and reliability |
Construction | Distance Measurement for Site Planning | Enhances project efficiency and resource allocation | Assess measurement range and calibration capabilities |
How Are Ultrasonic Sensors Used in Manufacturing Quality Control Systems?
Ultrasonic sensors play a pivotal role in automated quality control systems within the manufacturing sector. These sensors can detect imperfections in materials and products during the production process. By implementing ultrasonic technology, manufacturers can enhance product consistency and significantly reduce waste caused by defects. For international buyers, it is crucial to ensure that the sensors are compatible with existing machinery and adhere to industry standards, particularly when sourcing from different regions.
What Are the Benefits of Ultrasonic Sensors in Logistics and Supply Chain Management?
In logistics and supply chain management, ultrasonic sensors are utilized for inventory management systems to enhance accuracy in stock levels. These sensors can measure the distance to stock items, enabling real-time monitoring and reducing the risk of overstock or stockouts. This efficiency translates to lower operational costs and improved service levels. Buyers should evaluate the sensor’s range and its integration capabilities with existing software systems to ensure seamless operations.
How Do Ultrasonic Sensors Contribute to Livestock Monitoring in Agriculture?
In the agricultural sector, ultrasonic sensors are instrumental in livestock monitoring, allowing farmers to keep track of animal health and behavior. This technology can optimize feeding practices and improve overall animal welfare. For buyers in regions like Africa and South America, it is essential to consider the environmental conditions where the sensors will be deployed, ensuring they are durable and can withstand various weather conditions.
Why Are Ultrasonic Sensors Critical for Leak Detection in Oil and Gas?
Ultrasonic sensors are vital for leak detection systems in the oil and gas industry. These sensors can detect leaks before they escalate into significant environmental hazards, thereby reducing downtime and potential fines. For international buyers, sourcing sensors with high sensitivity and reliability is paramount to ensure compliance with safety regulations and to protect the environment.
How Do Ultrasonic Sensors Improve Distance Measurement in Construction?
In the construction industry, ultrasonic sensors are employed for precise distance measurement, aiding in site planning and resource allocation. This technology enhances project efficiency by providing accurate data that informs decision-making processes. Buyers should assess the measurement range and calibration capabilities of these sensors to ensure they meet the specific requirements of their construction projects, particularly in diverse geographical settings across Europe and the Middle East.
Related Video: What is a Sensor? Different Types of Sensors, Applications
3 Common User Pain Points for ‘ultrasonic sensor manufacturer’ & Their Solutions
Scenario 1: Inconsistent Sensor Performance Across Environments
The Problem: One of the significant challenges that B2B buyers face when sourcing ultrasonic sensors is their inconsistent performance in varying environmental conditions. For example, a manufacturer in South America may find that the sensors function well in controlled indoor settings but falter in outdoor applications due to interference from temperature fluctuations, humidity, or dust. This can lead to incorrect readings, resulting in costly operational inefficiencies and potential safety hazards.
The Solution: To overcome this issue, buyers should prioritize sourcing ultrasonic sensors that are specifically designed for diverse environmental conditions. When engaging with manufacturers, inquire about their products’ performance metrics in various settings. Request data sheets that detail the sensors’ operating temperature ranges, humidity tolerances, and any certifications for environmental resilience. Additionally, consider conducting field tests in your specific operational environment before committing to a large order. Collaborating with manufacturers who offer customization options can also help tailor sensors to meet your unique environmental challenges, ensuring reliable performance across different scenarios.
Scenario 2: Lack of Integration with Existing Systems
The Problem: Many international buyers struggle with integrating new ultrasonic sensors into their existing automated systems. For instance, a European company may want to implement ultrasonic sensors for inventory management but find that their current software does not support data inputs from the new sensors, leading to silos of information and inefficiencies in data handling. This integration gap can slow down operations and hinder decision-making processes.
The Solution: To effectively integrate ultrasonic sensors, buyers should conduct a thorough assessment of their current systems and identify compatibility requirements before purchasing. Engage with manufacturers early in the sourcing process to discuss integration capabilities and the availability of APIs or software development kits (SDKs) that facilitate seamless data exchange. Additionally, seek manufacturers that provide robust technical support and training services to assist with integration. Establishing a collaborative relationship with the sensor manufacturer can also lead to tailored solutions that ensure a smoother transition and optimal functionality within your existing infrastructure.
Scenario 3: Unclear Return on Investment (ROI) Metrics
The Problem: B2B buyers often face challenges in justifying the investment in ultrasonic sensors due to unclear ROI metrics. For example, a Middle Eastern firm considering ultrasonic sensors for monitoring material levels may struggle to quantify the potential savings and productivity improvements, making it difficult to secure budget approval. This lack of clarity can result in missed opportunities for enhanced operational efficiency.
The Solution: To address this pain point, it’s essential for buyers to work closely with ultrasonic sensor manufacturers who can provide comprehensive case studies and data showcasing the ROI from similar implementations. Buyers should ask for examples where ultrasonic sensors have led to measurable improvements in operational efficiency, safety, or cost savings. Additionally, consider conducting a pilot project to gather empirical data on the sensors’ performance and its impact on your operations. This approach not only allows for a better understanding of the sensors’ value but also provides tangible evidence to support future investments in technology. Engaging in discussions about potential cost savings and productivity gains during the negotiation phase can also facilitate a clearer picture of the ROI, helping to justify the expenditure.
Strategic Material Selection Guide for ultrasonic sensor manufacturer
When selecting materials for ultrasonic sensors, it’s essential to consider the specific application requirements, environmental conditions, and regulatory standards that may vary across different regions, especially for international B2B buyers from Africa, South America, the Middle East, and Europe. Here, we analyze four common materials used in the manufacturing of ultrasonic sensors, focusing on their properties, advantages, disadvantages, and implications for buyers.
What Are the Key Properties of Polycarbonate in Ultrasonic Sensors?
Polycarbonate is a popular choice for ultrasonic sensor housings due to its excellent impact resistance and transparency. It typically withstands temperatures ranging from -40°C to 120°C and offers good dimensional stability under varying conditions. Its inherent resistance to UV light makes it suitable for outdoor applications.
Pros: The durability of polycarbonate ensures longevity in harsh environments, while its lightweight nature reduces shipping costs. Additionally, it can be easily molded into complex shapes, enhancing manufacturing flexibility.
Cons: While polycarbonate is resistant to many chemicals, it can be susceptible to certain solvents, which may limit its use in specific applications. Moreover, it can be more expensive than other plastics.
Impact on Application: Polycarbonate is well-suited for applications requiring transparency and impact resistance, such as in automotive or industrial settings.
Considerations for International Buyers: Buyers should ensure compliance with standards such as ASTM D256 for impact resistance and consider local regulations regarding material safety and environmental impact.
How Does Stainless Steel Perform in Ultrasonic Sensor Manufacturing?
Stainless steel is frequently used in ultrasonic sensors due to its exceptional corrosion resistance and mechanical strength. It can endure high temperatures and pressures, making it ideal for industrial applications. Common grades include 304 and 316, with the latter offering superior resistance to chlorides.
Pros: The durability of stainless steel enhances the lifespan of sensors, especially in corrosive environments. Its robustness also means that it can withstand mechanical stress without deforming.
Cons: Stainless steel is heavier than plastic alternatives, which may increase shipping costs. Additionally, its higher manufacturing complexity can lead to increased production costs.
Impact on Application: Stainless steel is ideal for applications in chemical processing and marine environments, where exposure to harsh conditions is common.
Considerations for International Buyers: Buyers should verify compliance with standards like ASTM A240 for stainless steel and consider certifications for food-grade applications if relevant.
What Are the Benefits of Using Epoxy Resins in Ultrasonic Sensors?
Epoxy resins are used in ultrasonic sensors primarily for encapsulation and potting applications. They provide excellent adhesion, chemical resistance, and electrical insulation properties, making them suitable for various environments.
Pros: Epoxy resins are highly durable and can protect sensitive components from moisture and contaminants. They also offer good thermal stability, which is beneficial in high-temperature applications.
Cons: The curing process can be time-consuming, potentially extending lead times. Additionally, once cured, epoxy resins can be difficult to remove, complicating repairs or modifications.
Impact on Application: Epoxy resins are particularly effective in applications where moisture and chemical exposure are concerns, such as in outdoor sensors.
Considerations for International Buyers: Buyers should ensure that the epoxy used complies with relevant chemical safety standards and consider the environmental impact of the materials.
Why Choose PEEK for High-Performance Ultrasonic Sensors?
Polyether ether ketone (PEEK) is a high-performance thermoplastic known for its excellent mechanical and thermal properties. It can operate at temperatures up to 260°C and exhibits outstanding chemical resistance.
Pros: PEEK’s strength and thermal stability make it suitable for demanding applications, including aerospace and medical devices. Its lightweight nature also contributes to reduced shipping costs.
Cons: PEEK is one of the most expensive thermoplastics, which may deter cost-sensitive buyers. Its processing requires specialized equipment, increasing manufacturing complexity.
Impact on Application: PEEK is ideal for high-temperature applications where mechanical performance is critical.
Considerations for International Buyers: Buyers should be aware of the high cost and ensure that PEEK components meet international standards such as ISO 9001 for quality management.
Summary Table of Material Selection for Ultrasonic Sensors
Material | Typical Use Case for ultrasonic sensor manufacturer | Key Advantage | Key Disadvantage/Limitation | Relative Cost (Low/Med/High) |
---|---|---|---|---|
Polycarbonate | Automotive and industrial sensors | Lightweight and impact-resistant | Susceptible to certain solvents | Medium |
Stainless Steel | Chemical processing and marine applications | Excellent corrosion resistance | Higher manufacturing costs | High |
Epoxy Resins | Outdoor sensors requiring moisture protection | Durable and moisture-resistant | Time-consuming curing process | Medium |
PEEK | Aerospace and medical devices | High thermal and mechanical strength | High cost and complex processing | High |
This guide provides actionable insights for international B2B buyers, helping them make informed decisions about material selection based on performance, cost, and compliance with regional standards.
In-depth Look: Manufacturing Processes and Quality Assurance for ultrasonic sensor manufacturer
What Are the Key Stages in the Manufacturing Process of Ultrasonic Sensors?
Manufacturing ultrasonic sensors involves several critical stages that ensure the final product meets both performance standards and customer expectations. Understanding these stages is essential for international B2B buyers to evaluate the capabilities and reliability of potential suppliers.
-
Material Preparation
The first step in the manufacturing process involves sourcing and preparing raw materials. High-quality piezoelectric materials, such as lead zirconate titanate (PZT), are typically used for their exceptional ultrasonic properties. Suppliers must ensure that the materials meet international standards and specifications to prevent defects during production. B2B buyers should inquire about the supplier’s sourcing practices and whether they utilize certified materials. -
Forming
The forming stage includes shaping the piezoelectric elements and other components. This can be done through processes like injection molding or CNC machining. The precision in forming is crucial, as any discrepancies can lead to performance issues. Buyers should assess the technology and machinery used by suppliers to ensure they are equipped for high-precision manufacturing. -
Assembly
During assembly, the formed components are put together to create the ultrasonic sensor. This step often includes soldering, bonding, and the integration of electronic components. Automated assembly lines are increasingly being adopted to enhance efficiency and reduce human error. Buyers should consider the supplier’s assembly capabilities, especially if they require customized sensors. -
Finishing
The finishing stage involves applying protective coatings, ensuring proper sealing, and conducting final adjustments to the sensor’s performance. This step is vital for ensuring the durability of the sensor in various environments. B2B buyers should ask about the finishing techniques used and the environmental tests conducted to verify the sensor’s resilience.
How is Quality Assurance Implemented in Ultrasonic Sensor Manufacturing?
Quality assurance (QA) is integral to the manufacturing process of ultrasonic sensors, ensuring that products meet both regulatory and customer standards. International B2B buyers should be aware of the various QA practices and standards that reputable manufacturers follow.
-
What International Standards Should B2B Buyers Consider?
Most ultrasonic sensor manufacturers adhere to international quality management standards, such as ISO 9001. This standard outlines requirements for quality management systems, ensuring consistent quality and continuous improvement. Additionally, industry-specific certifications like CE marking for European markets and API standards for oil and gas applications may also apply. Buyers should verify that their suppliers possess the necessary certifications relevant to their industries. -
What Are the Key Quality Control Checkpoints?
Quality control (QC) is typically divided into several checkpoints throughout the manufacturing process:
– Incoming Quality Control (IQC): This stage checks the quality of raw materials upon arrival to ensure they meet specified standards.
– In-Process Quality Control (IPQC): Conducted during the manufacturing process, this checkpoint monitors ongoing production to catch defects early.
– Final Quality Control (FQC): This final check ensures that the finished product meets all specifications before shipment. B2B buyers should inquire about the frequency and rigor of these QC checkpoints. -
What Common Testing Methods Are Used?
Various testing methods are employed to validate the performance and reliability of ultrasonic sensors. These may include:
– Functional Testing: Ensures the sensor operates as intended under specified conditions.
– Environmental Testing: Assesses the sensor’s performance under extreme temperatures, humidity, and other environmental factors.
– Calibration: Ensures accuracy in measurements, which is crucial for applications requiring precise data. Buyers should request documentation of testing methodologies and results.
How Can B2B Buyers Verify Supplier Quality Control?
Verifying a supplier’s quality control processes is essential for B2B buyers to ensure they are partnering with reliable manufacturers. Here are some actionable steps buyers can take:
-
Conduct Supplier Audits
Performing on-site audits allows buyers to assess the manufacturing processes, quality control measures, and overall facility conditions. An audit can reveal a lot about a supplier’s commitment to quality and compliance with international standards. -
Request Quality Reports and Certifications
Buyers should ask suppliers for their quality assurance documentation, including quality control reports and certifications. These documents provide insight into the supplier’s adherence to industry standards and their quality management practices. -
Engage Third-Party Inspection Services
Utilizing third-party inspection services can offer an unbiased evaluation of the supplier’s quality control processes. These services can conduct inspections at various stages of the manufacturing process, providing additional assurance of product quality.
What Are the Quality Control Nuances for International B2B Buyers?
International B2B buyers, particularly from regions such as Africa, South America, the Middle East, and Europe, should be aware of specific nuances in quality control that may affect their procurement processes:
-
Understanding Regional Standards
Different regions may have varying compliance requirements and quality standards. For instance, European buyers must comply with CE marking regulations, while buyers in the Middle East may need to consider local regulatory bodies. Understanding these requirements can help buyers make informed decisions about potential suppliers. -
Language and Communication Barriers
Language differences can lead to misunderstandings regarding quality specifications and requirements. Buyers should ensure that communication with suppliers is clear and that all technical documents are available in a language both parties understand. -
Cultural Considerations in Quality Assurance
Cultural attitudes toward quality and compliance may differ across regions. Buyers should take the time to understand a supplier’s cultural approach to quality assurance and how it might impact their manufacturing processes.
In summary, a comprehensive understanding of the manufacturing processes and quality assurance practices in ultrasonic sensor manufacturing is vital for B2B buyers. By focusing on material preparation, forming, assembly, finishing, and rigorous QC measures, buyers can ensure they select the right suppliers that meet their quality standards and operational needs.
Practical Sourcing Guide: A Step-by-Step Checklist for ‘ultrasonic sensor manufacturer’
In the competitive landscape of international sourcing, particularly for ultrasonic sensors, a structured approach is essential for B2B buyers. This guide provides a step-by-step checklist to ensure you make informed decisions when selecting a manufacturer. By following these actionable insights, you can streamline your procurement process and enhance your supply chain efficiency.
Step 1: Define Your Technical Specifications
Before initiating the sourcing process, clearly outline the technical specifications required for the ultrasonic sensors. Consider parameters such as operating range, frequency, and environmental resistance. This clarity not only helps in communicating your needs effectively to potential suppliers but also aids in evaluating their capabilities against your requirements.
Step 2: Conduct Market Research for Suppliers
Understanding the market landscape is critical. Research potential suppliers from different regions, focusing on their reputation, product offerings, and market presence. Utilize platforms like industry directories, trade shows, and online forums to gather information and identify manufacturers with a strong track record in producing high-quality ultrasonic sensors.
Step 3: Evaluate Potential Suppliers
Before committing to any supplier, conduct a thorough evaluation. Request comprehensive company profiles, case studies, and references from previous clients, especially those in industries similar to yours. Look for testimonials that highlight the supplier’s reliability, product quality, and customer service, ensuring they align with your expectations.
Step 4: Verify Supplier Certifications and Compliance
Ensure that the suppliers you are considering possess relevant certifications, such as ISO 9001 for quality management systems or CE marking for compliance with European standards. This verification is crucial as it signifies adherence to industry standards and can help mitigate risks associated with quality and safety.
Step 5: Assess Manufacturing Capabilities and Technology
Investigate the manufacturing processes and technologies employed by potential suppliers. A manufacturer that utilizes advanced technologies and maintains high production standards will likely offer superior products. Consider visiting the facility if possible, or request virtual tours to gain a better understanding of their operational capabilities.
Step 6: Request Samples for Testing
Before making a bulk purchase, request samples of the ultrasonic sensors. Testing these samples against your specifications will provide valuable insights into their performance and reliability. This step can also help you identify any potential issues early on, allowing for adjustments in your final order.
Step 7: Negotiate Terms and Conditions
Once you have identified a suitable supplier, focus on negotiating favorable terms and conditions. Discuss pricing, payment terms, lead times, and warranties. Clear communication at this stage is vital to establish a mutually beneficial relationship and to ensure that both parties have aligned expectations.
By following this structured checklist, international B2B buyers can effectively navigate the sourcing process for ultrasonic sensors, ensuring they select a manufacturer that meets their specific needs while minimizing risks associated with procurement.
Comprehensive Cost and Pricing Analysis for ultrasonic sensor manufacturer Sourcing
What Are the Key Cost Components in Sourcing Ultrasonic Sensors?
When sourcing ultrasonic sensors, international B2B buyers must understand the multifaceted cost structure involved in production. The primary cost components include:
-
Materials: The choice of materials significantly impacts the overall cost. High-quality sensors often utilize advanced materials that enhance durability and performance, which can lead to higher prices.
-
Labor: Labor costs vary by region. Countries with lower labor costs may offer competitive pricing, but this can affect the quality and reliability of the product.
-
Manufacturing Overhead: This includes all indirect costs associated with production, such as utilities, facility maintenance, and administrative expenses. Efficient manufacturing processes can help minimize overhead.
-
Tooling: Tooling costs are critical, especially for custom ultrasonic sensors. The initial investment in molds and dies can be substantial, but it is often amortized over large production runs.
-
Quality Control (QC): Robust QC processes ensure that sensors meet required specifications and certifications. While this adds to the cost, it is essential for maintaining product reliability and brand reputation.
-
Logistics: Shipping and handling fees can vary widely based on the origin and destination of the products. Understanding Incoterms can help buyers assess total logistics costs.
-
Margin: Manufacturers typically add a profit margin to cover their operational risks and ensure sustainability. This margin can fluctuate based on market conditions and competition.
How Do Price Influencers Affect Ultrasonic Sensor Sourcing?
Several factors can influence the pricing of ultrasonic sensors, which buyers should consider when evaluating suppliers:
-
Volume and Minimum Order Quantity (MOQ): Bulk orders often qualify for discounts. Understanding a supplier’s MOQ can help buyers negotiate better pricing.
-
Specifications and Customization: Tailored sensors may incur additional costs due to specialized materials or design requirements. Clearly defined specifications can streamline the production process and reduce costs.
-
Materials and Quality Certifications: Sensors made from premium materials or those that meet specific industry certifications may command higher prices. Buyers should balance quality needs with budget constraints.
-
Supplier Factors: The reputation, reliability, and location of the supplier can affect pricing. Established suppliers may offer better warranty terms and support, justifying a higher price.
-
Incoterms: Familiarity with Incoterms can help buyers understand their responsibilities regarding shipping and delivery, which directly impacts overall cost.
What Negotiation Strategies Can Optimize Costs for International Buyers?
For international B2B buyers, particularly from Africa, South America, the Middle East, and Europe, effective negotiation strategies can lead to significant cost savings:
-
Leverage Volume Discounts: When possible, consolidate orders to meet MOQs and negotiate volume discounts, which can substantially lower the unit price.
-
Discuss Payment Terms: Flexible payment terms can ease cash flow pressures. Propose options such as staggered payments or longer payment periods to improve your financial flexibility.
-
Evaluate Total Cost of Ownership (TCO): Consider not just the purchase price but also the long-term costs associated with maintenance, downtime, and efficiency. A lower initial cost might lead to higher operational costs.
-
Research Market Trends: Stay informed about market fluctuations and supplier capacity. Understanding the competitive landscape allows for more informed negotiations.
What Pricing Nuances Should International Buyers Be Aware Of?
International buyers need to be aware of specific pricing nuances that can affect their sourcing decisions:
-
Currency Fluctuations: Exchange rate volatility can significantly impact the final cost. Consider hedging options to mitigate risks.
-
Import Duties and Taxes: Understanding local regulations regarding import tariffs can prevent unexpected costs. Engage with customs experts to ensure compliance and budget accurately.
-
Cultural Differences in Negotiation: Different regions have distinct negotiation styles. Being aware of these cultural nuances can lead to more effective communication and better deals.
Disclaimer on Indicative Prices
Prices for ultrasonic sensors can vary widely based on the factors mentioned above. This analysis provides a framework for understanding potential costs but should not be interpreted as definitive pricing. Buyers are encouraged to conduct thorough market research and supplier evaluations to obtain accurate quotes tailored to their specific needs.
Alternatives Analysis: Comparing ultrasonic sensor manufacturer With Other Solutions
In the competitive landscape of industrial automation and sensing technologies, B2B buyers must evaluate various solutions to meet their operational needs. Ultrasonic sensors are widely utilized for distance measurement and object detection, but several alternative technologies also serve similar purposes. This section examines how ultrasonic sensor manufacturers stack up against other viable solutions, enabling informed decision-making for international buyers.
Comparison Table of Ultrasonic Sensors and Alternatives
Comparison Aspect | Ultrasonic Sensor Manufacturer | Laser Sensor Technology | Infrared Sensor Technology |
---|---|---|---|
Performance | High accuracy in various conditions, suitable for long-range detection | Extremely precise with minimal deviation, ideal for short distances | Good performance in clear conditions but affected by environmental factors |
Cost | Moderate initial investment with low operational costs | Higher initial cost, but long lifespan reduces total cost | Lower initial cost but may require frequent replacements |
Ease of Implementation | Generally user-friendly with standard mounting options | Requires precise alignment and calibration | Simple installation but may need adjustments for optimal performance |
Maintenance | Low maintenance needs; periodic checks recommended | Low maintenance, but calibration needed | Moderate maintenance; lens cleaning may be necessary |
Best Use Case | Ideal for liquid level measurement and object detection in diverse environments | Best for high-precision applications like robotics and manufacturing | Suitable for short-range applications like presence detection in controlled environments |
What Are the Pros and Cons of Laser Sensor Technology?
Laser sensors utilize focused light to measure distances with remarkable accuracy. One of the key advantages of laser sensors is their ability to function effectively in a variety of industrial settings, providing pinpoint precision even over longer ranges. However, the cost of laser sensors can be significantly higher than that of ultrasonic sensors, which may deter budget-conscious buyers. Additionally, the need for precise alignment during installation can complicate implementation, particularly in environments where space is limited.
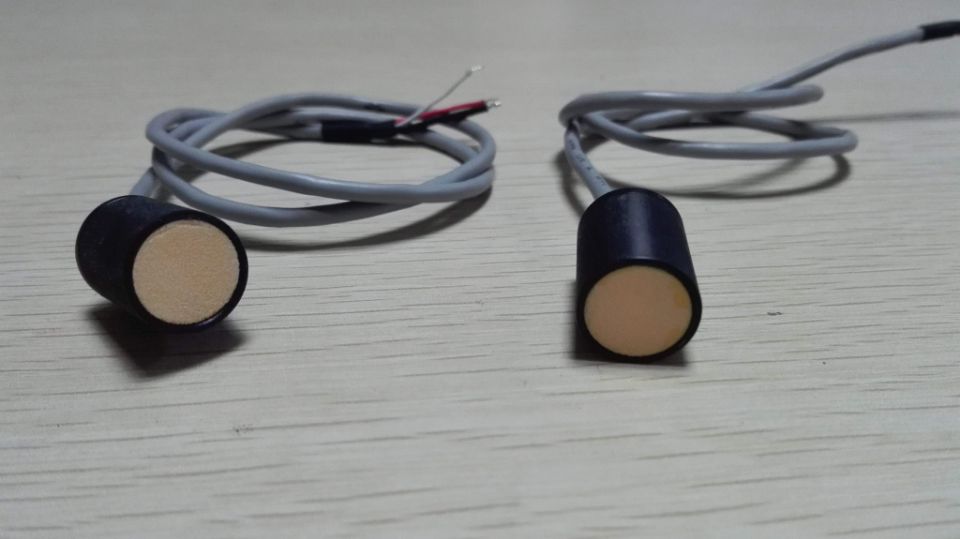
A stock image related to ultrasonic sensor manufacturer.
How Does Infrared Sensor Technology Compare?
Infrared sensors detect objects by measuring the heat emitted from them or by using reflected infrared light. They are generally less expensive than both ultrasonic and laser sensors, making them attractive for low-budget projects. However, their performance can be influenced by environmental factors such as dust, fog, or temperature variations, which may lead to inconsistent readings. Infrared sensors are best suited for applications in controlled environments where these variables can be minimized.
Conclusion: Which Solution Is Right for Your Business Needs?
When selecting a sensing technology, B2B buyers must consider specific operational requirements, including the intended application, environmental conditions, and budget constraints. Ultrasonic sensors offer a versatile solution with low maintenance and operational costs, making them suitable for a wide range of industries. However, if precision is paramount, investing in laser sensors may be justified despite the higher initial costs. For simpler applications with budget limitations, infrared sensors can provide adequate functionality. Ultimately, understanding the strengths and weaknesses of each technology will empower buyers to make an informed decision that aligns with their business objectives.
Essential Technical Properties and Trade Terminology for ultrasonic sensor manufacturer
What Are the Key Technical Properties of Ultrasonic Sensors?
When selecting ultrasonic sensors, B2B buyers should be well-versed in the critical technical properties that influence performance and suitability for their applications. Here are some essential specifications to consider:
1. Operating Frequency
Operating frequency is a crucial parameter for ultrasonic sensors, typically ranging from 20 kHz to 1 MHz. Higher frequencies provide better resolution and accuracy, making them ideal for detecting small objects or measuring short distances. In contrast, lower frequencies can penetrate through obstacles better, suitable for longer-range applications. Understanding the frequency needs of your specific application can significantly impact sensor effectiveness.
2. Detection Range
The detection range defines how far an ultrasonic sensor can effectively measure distances. Most sensors operate within a range of a few centimeters to several meters. For B2B buyers, it is vital to match the sensor’s range to the operational requirements of the intended application, whether in industrial automation, robotics, or liquid level measurement.
3. Beam Angle
The beam angle of an ultrasonic sensor affects the area it can cover. A narrow beam angle (e.g., 5°) allows for precise measurements of small targets, while a wider beam angle (e.g., 30°) is better for detecting larger objects or for use in applications requiring broader coverage. This property is essential for ensuring accurate detection without unwanted interference from surrounding objects.
4. Material Composition
The material composition of ultrasonic sensors can influence durability and performance in various environments. Common materials include plastics and metals, each offering different resistance to environmental factors such as humidity, temperature, and chemical exposure. Understanding material grades helps buyers select sensors that can withstand specific conditions, particularly in harsh industrial settings.
5. Tolerance Levels
Tolerance refers to the permissible limit of variation in the dimensions of the sensor. For precision applications, tighter tolerances are essential to ensure consistent performance. Buyers should consider the manufacturing standards and certifications of suppliers to guarantee that the ultrasonic sensors meet necessary tolerance requirements for their applications.
What Common Trade Terms Should B2B Buyers Know?
Navigating the world of ultrasonic sensors also involves understanding industry-specific terminology. Here are some common terms that B2B buyers should be familiar with:
1. OEM (Original Equipment Manufacturer)
An OEM is a company that produces parts or equipment that may be marketed by another manufacturer. In the context of ultrasonic sensors, buyers often source from OEMs who specialize in manufacturing these components for integration into larger systems. Understanding OEM relationships can help buyers ensure they are procuring high-quality sensors that meet their specifications.
2. MOQ (Minimum Order Quantity)
MOQ refers to the smallest number of units a supplier is willing to sell. This term is crucial for B2B buyers, as it affects inventory management and budgeting. Understanding the MOQ helps in planning purchases, especially for smaller companies or those just starting to implement ultrasonic sensors in their operations.
3. RFQ (Request for Quotation)
An RFQ is a document sent to suppliers to request a price quote for specific products or services. For ultrasonic sensor purchases, a well-structured RFQ can help buyers obtain competitive pricing and terms from multiple manufacturers, facilitating better negotiation and procurement strategies.
4. Incoterms
Incoterms are internationally recognized rules that define the responsibilities of buyers and sellers in the shipping process. Familiarity with these terms is vital for B2B buyers, as they clarify who bears the costs and risks associated with the transportation of ultrasonic sensors. Key Incoterms include FOB (Free On Board) and CIF (Cost, Insurance, and Freight), which can significantly impact total cost and logistics planning.
5. Lead Time
Lead time refers to the time it takes from placing an order until the goods are delivered. Understanding lead times is essential for B2B buyers to manage their supply chains effectively, especially when planning production schedules or inventory levels. Being aware of potential delays can help in making informed decisions regarding sensor procurement.
By grasping these technical properties and trade terms, international B2B buyers can make more informed purchasing decisions when sourcing ultrasonic sensors, ensuring they select the right products for their specific applications.
Navigating Market Dynamics and Sourcing Trends in the ultrasonic sensor manufacturer Sector
What Are the Key Market Dynamics and Sourcing Trends in the Ultrasonic Sensor Sector?
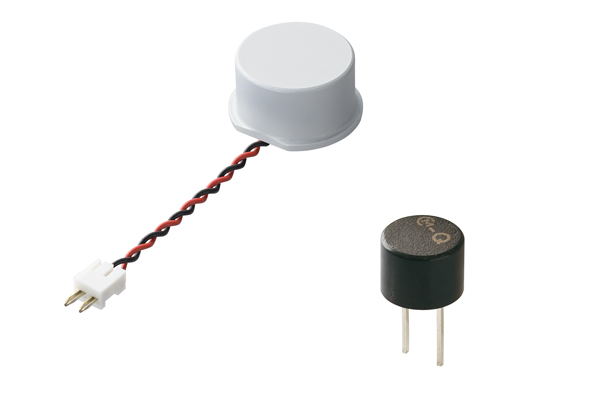
A stock image related to ultrasonic sensor manufacturer.
The ultrasonic sensor market is experiencing significant growth, driven by advancements in technology and the increasing adoption of automation across various industries. Factors such as the rising demand for automation in manufacturing, coupled with the growing emphasis on IoT applications, are propelling the market forward. International B2B buyers, especially from Africa, South America, the Middle East, and Europe, should note that industries such as automotive, healthcare, and smart home technology are leading the charge in integrating ultrasonic sensors.
Emerging trends include the adoption of miniaturized sensors, which are crucial for applications requiring space efficiency and high performance. Additionally, the increasing demand for wireless sensors is reshaping sourcing strategies, as companies seek to reduce installation costs and improve flexibility. Buyers should also consider the integration of AI and machine learning with ultrasonic technology, which enhances data processing and accuracy.
International buyers must navigate varying regional regulations and standards. In Europe, for example, stringent environmental regulations drive the demand for compliant and innovative sensor technologies. Buyers in Africa and South America may find opportunities in less saturated markets where the adoption of ultrasonic technology is still in its infancy. Understanding these market dynamics is essential for making informed sourcing decisions that align with both current trends and future opportunities.
How Important Is Sustainability and Ethical Sourcing in the Ultrasonic Sensor Industry?
Sustainability has become a critical focus in the ultrasonic sensor manufacturing sector, with increasing pressure on suppliers to adopt environmentally friendly practices. The environmental impact of ultrasonic sensors, particularly in terms of raw material sourcing and production processes, is under scrutiny. Buyers should prioritize manufacturers who demonstrate commitment to sustainability through certifications such as ISO 14001 or the use of recycled materials in their products.
Ethical sourcing practices are equally vital, as they ensure the integrity of the supply chain. Buyers should inquire about the sourcing of raw materials, ensuring that they are obtained from suppliers who adhere to ethical labor practices and environmental stewardship. This not only mitigates risks associated with supply chain disruptions but also enhances brand reputation and customer loyalty.
Moreover, the demand for “green” technologies is reshaping product development. Manufacturers are increasingly focusing on creating energy-efficient ultrasonic sensors that minimize power consumption and carbon footprint. By choosing suppliers who align with these sustainability goals, international buyers can contribute to a more sustainable future while also meeting the growing consumer demand for eco-friendly products.
What Is the Evolution of the Ultrasonic Sensor Manufacturing Sector?
The ultrasonic sensor manufacturing sector has evolved significantly over the past few decades. Initially, these sensors were primarily utilized in industrial applications, such as distance measurement and material handling. However, as technology advanced, their applications expanded into consumer electronics, automotive safety systems, and medical devices, reflecting a broader trend toward automation and smart technology integration.
The introduction of digital signal processing (DSP) in the 1990s marked a turning point, allowing for enhanced accuracy and reliability in sensor performance. As industries began to embrace Industry 4.0 concepts, ultrasonic sensors found new roles in smart factories, contributing to real-time data collection and process optimization.
Today, the sector continues to innovate, with a strong focus on wireless technology and IoT integration. This evolution not only highlights the versatility of ultrasonic sensors but also underscores the importance of staying abreast of technological advancements and market changes for international B2B buyers looking to invest in this dynamic industry.
Frequently Asked Questions (FAQs) for B2B Buyers of ultrasonic sensor manufacturer
-
How do I choose the right ultrasonic sensor manufacturer for my needs?
Selecting the right ultrasonic sensor manufacturer involves several key steps. Start by assessing your specific application requirements, such as measurement range, accuracy, and environmental conditions. Research potential manufacturers’ industry experience, customer reviews, and case studies to gauge reliability. For international buyers, consider logistics and shipping capabilities, ensuring they can deliver to your region efficiently. Engaging in direct communication with manufacturers to discuss customization options and technical support can also provide insights into their capabilities. -
What are the key features to look for in ultrasonic sensors?
When sourcing ultrasonic sensors, prioritize features like frequency range, beam angle, and response time. Sensors with a higher frequency can offer better resolution, while wider beam angles improve coverage. Consider durability and environmental ratings, especially for applications in harsh conditions. Furthermore, check for integration capabilities with existing systems and protocols, which can streamline installation and ensure compatibility with your operational needs. -
What are the minimum order quantities (MOQ) for ultrasonic sensors?
Minimum order quantities can vary significantly between manufacturers. Typically, MOQs for ultrasonic sensors range from 100 to 1,000 units, depending on the manufacturer’s production capacity and the complexity of the sensor. For international buyers, it’s advisable to inquire about flexible MOQ options, especially if you’re testing a new application or entering a new market. Some manufacturers may offer sample orders, which allow you to evaluate quality before committing to larger purchases. -
How do payment terms work with international ultrasonic sensor manufacturers?
Payment terms can differ based on the manufacturer and the buyer’s location. Common arrangements include upfront payments, partial deposits, or payment upon delivery. For international transactions, consider using secure payment methods such as letters of credit or escrow services to mitigate risks. It’s essential to discuss payment terms upfront to avoid misunderstandings and ensure alignment with your cash flow management. -
What customization options are available for ultrasonic sensors?
Many ultrasonic sensor manufacturers offer customization to meet specific application needs. Customization can include altering sensor dimensions, frequency settings, or output signals. Some manufacturers may also provide tailored firmware or software solutions for integration with your existing systems. When discussing customization, ensure that you clearly communicate your requirements and timelines to avoid delays in production. -
What quality assurance processes should I expect from ultrasonic sensor manufacturers?
Reputable ultrasonic sensor manufacturers implement rigorous quality assurance processes, including material inspections, in-process testing, and final product evaluations. Look for certifications such as ISO 9001 or industry-specific standards that indicate adherence to quality practices. Additionally, inquire about warranty policies and post-sales support, as these can provide further assurance of product reliability and manufacturer accountability. -
How can I effectively vet ultrasonic sensor suppliers from different regions?
When vetting suppliers, start with online research to assess their reputation and product offerings. Request references and case studies from previous clients to understand their experience. For international suppliers, verify their export capabilities and compliance with regional regulations. Visiting manufacturing facilities or attending trade shows can also provide valuable insights into their operations and product quality. -
What are the logistics considerations when sourcing ultrasonic sensors internationally?
Logistics play a crucial role in international sourcing. Consider factors such as shipping times, customs regulations, and potential tariffs that may impact your overall costs. Collaborate with manufacturers to understand their shipping options and choose the most efficient method based on your timeline. Ensure that you have a clear plan for handling import duties and local delivery to avoid delays in receiving your ultrasonic sensors.
Important Disclaimer & Terms of Use
⚠️ Important Disclaimer
The information provided in this guide, including content regarding manufacturers, technical specifications, and market analysis, is for informational and educational purposes only. It does not constitute professional procurement advice, financial advice, or legal advice.
While we have made every effort to ensure the accuracy and timeliness of the information, we are not responsible for any errors, omissions, or outdated information. Market conditions, company details, and technical standards are subject to change.
B2B buyers must conduct their own independent and thorough due diligence before making any purchasing decisions. This includes contacting suppliers directly, verifying certifications, requesting samples, and seeking professional consultation. The risk of relying on any information in this guide is borne solely by the reader.
Strategic Sourcing Conclusion and Outlook for ultrasonic sensor manufacturer
In navigating the complexities of sourcing ultrasonic sensors, international B2B buyers, particularly from Africa, South America, the Middle East, and Europe, should prioritize strategic sourcing as a critical component of their procurement strategy. By understanding the nuances of supplier capabilities, regional market dynamics, and technological advancements, buyers can make informed decisions that enhance operational efficiency and product quality.
What are the key benefits of strategic sourcing for ultrasonic sensors? Engaging with manufacturers who prioritize innovation and customer-centric solutions not only ensures access to high-quality products but also fosters long-term partnerships that can adapt to evolving market needs. By leveraging data-driven insights and aligning with suppliers that demonstrate sustainability and reliability, businesses can mitigate risks and capitalize on competitive advantages.
Looking ahead, the demand for ultrasonic sensors is set to grow significantly, driven by advancements in automation and smart technology. Now is the time for international B2B buyers to explore new partnerships and invest in strategic sourcing initiatives that will position them favorably in their respective markets. Embrace this opportunity to enhance your supply chain resilience and drive your business forward by collaborating with leading ultrasonic sensor manufacturers.