The Ultimate Guide to Mechanical Keyboard Custom (2025)
Introduction: Navigating the Global Market for mechanical keyboard custom
In an increasingly digital world, the demand for high-quality, customizable mechanical keyboards has surged, presenting a unique challenge for international B2B buyers seeking reliable sourcing options. Whether you’re looking to enhance employee productivity in an office setting or cater to niche gaming markets, understanding the intricacies of the mechanical keyboard custom market is essential. This guide will help you navigate the complexities of sourcing, from identifying different types of keyboards to exploring their diverse applications across various industries.
As we delve into the various aspects of mechanical keyboards, this guide will cover critical topics such as supplier vetting processes, cost considerations, and the latest trends shaping the market. For buyers in regions like Africa, South America, the Middle East, and Europe, including the UK and UAE, having a comprehensive understanding of these factors is key to making informed purchasing decisions.
By equipping you with actionable insights and practical strategies, this guide empowers you to approach the global market with confidence. Whether you are a procurement manager looking to streamline your supply chain or a business owner aiming to enhance your product offerings, our expert analysis will provide the tools necessary to succeed in the competitive landscape of mechanical keyboard custom products.
Understanding mechanical keyboard custom Types and Variations
Type Name | Key Distinguishing Features | Primary B2B Applications | Brief Pros & Cons for Buyers |
---|---|---|---|
Tenkeyless (TKL) | Compact design without numeric keypad | Gaming, office use | Pros: Space-efficient; Cons: Lacks number pad |
Full-Size | Includes all keys, including the number pad | Data entry, accounting | Pros: Complete functionality; Cons: Bulky |
60% Layout | Minimalist design, omits function and arrow keys | Programming, casual gaming | Pros: Highly portable; Cons: Limited key access |
Hot-Swappable | Switches can be changed without soldering | Customization, prototyping | Pros: Versatile; Cons: Potential durability issues |
RGB Backlit | Customizable lighting effects | Design, creative industries | Pros: Aesthetic appeal; Cons: May distract users |
What are the Characteristics of Tenkeyless (TKL) Mechanical Keyboards?
Tenkeyless (TKL) mechanical keyboards are designed without the numeric keypad, making them more compact and easier to transport. This feature is particularly beneficial for businesses in sectors like gaming and general office environments where desk space is at a premium. B2B buyers should consider TKL keyboards for employees who need mobility and quick access to frequently used keys without the bulk of a full-sized keyboard. However, the absence of a number pad may hinder tasks that require extensive data entry.
Why Choose Full-Size Mechanical Keyboards for Data Entry?
Full-size mechanical keyboards include all keys, providing a comprehensive typing experience. They are ideal for businesses focused on data entry, accounting, or any task requiring frequent use of the numeric keypad. The main purchasing consideration for B2B buyers is the balance between functionality and space. While full-size keyboards offer complete functionality, they can be bulky, which may not suit all office environments. Ensuring that the keyboard layout fits the workspace is essential for optimizing productivity.
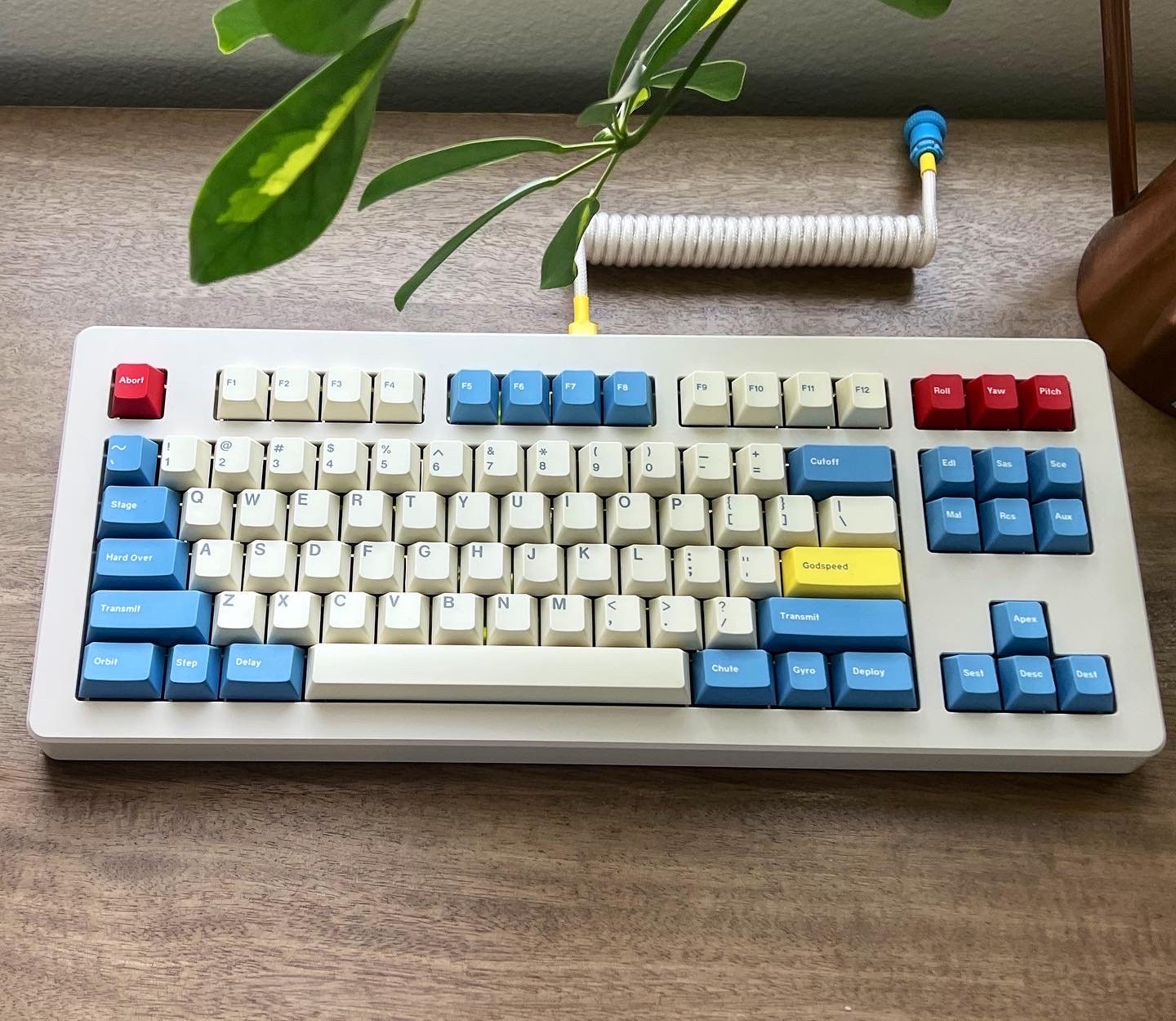
A stock image related to mechanical keyboard custom.
How Do 60% Layout Keyboards Benefit Programming and Gaming?
The 60% layout mechanical keyboard is a minimalist option that omits function and arrow keys, focusing on the essential alphanumeric keys. This compact design is particularly appealing to programmers and casual gamers who value portability and desk organization. B2B buyers should assess whether the limited key options align with their team’s needs, as some users may find the lack of dedicated keys for certain functions inconvenient. However, the lightweight design can facilitate easier transport for remote workers.
What Advantages Do Hot-Swappable Keyboards Offer for Customization?
Hot-swappable mechanical keyboards allow users to change switches without soldering, making them a versatile choice for businesses focused on customization and prototyping. This feature enables companies to adapt keyboards to different user preferences or ergonomic needs easily. B2B buyers should consider the potential for enhanced employee satisfaction through personalized setups. However, it’s important to evaluate the quality of the switches and the keyboard’s overall durability, as frequent changes can lead to wear and tear.
Why Invest in RGB Backlit Keyboards for Creative Industries?
RGB backlit mechanical keyboards are favored in design and creative industries for their customizable lighting effects, which can enhance the workspace’s aesthetic. These keyboards not only provide visual appeal but can also improve user experience by allowing users to assign specific colors to different keys for easier navigation. B2B buyers should weigh the aesthetic benefits against the potential for distraction, as bright lights may not be suitable for all work environments. Ensuring that the lighting features align with the company culture and employee preferences is crucial for maximizing their value.
Related Video: How to customize MX Mechanical Keyboard using Logi Options+
Key Industrial Applications of mechanical keyboard custom
Industry/Sector | Specific Application of mechanical keyboard custom | Value/Benefit for the Business | Key Sourcing Considerations for this Application |
---|---|---|---|
Gaming | Custom keyboards for esports teams and gaming cafes | Enhanced performance and user experience | Durability, switch types, and customization options |
IT and Software Development | Ergonomic keyboards for software developers | Improved productivity and reduced strain | Key layout flexibility, tactile feedback, and programmable keys |
Education | Custom keyboards for educational institutions | Tailored solutions for different learning environments | Compatibility with educational software and durability for frequent use |
Creative Design | Keyboards designed for graphic designers and artists | Precision control and enhanced creative workflow | Aesthetic customization, key feel, and macro programming capabilities |
Telecommunications | Specialized keyboards for call centers | Increased efficiency and comfort during long shifts | Noise level, key travel distance, and ergonomic design |
How Are Mechanical Keyboards Custom Used in the Gaming Industry?
In the gaming sector, custom mechanical keyboards are integral for esports teams and gaming cafes. These keyboards provide enhanced performance through tailored switch types that cater to gaming styles, offering rapid response times and durability. For B2B buyers, sourcing considerations include ensuring the keyboards can withstand extensive use, feature customizable key layouts, and have a variety of switch options to suit different gaming preferences. This customization leads to improved user experience and can significantly impact gaming performance.
What Is the Role of Custom Mechanical Keyboards in IT and Software Development?
In IT and software development, ergonomic custom mechanical keyboards are essential for improving developer productivity and reducing physical strain during long coding sessions. These keyboards can be tailored to specific coding languages or software environments, with programmable keys that enhance workflow efficiency. International buyers must consider key layout flexibility, tactile feedback preferences, and the availability of features that support extensive programming tasks. Investing in high-quality custom keyboards can lead to better focus and output from development teams.
How Do Educational Institutions Benefit from Custom Mechanical Keyboards?
Educational institutions leverage custom mechanical keyboards to create tailored learning environments that cater to various student needs. For example, keyboards can be designed with specific layouts for different subjects, enhancing the learning experience. Buyers from educational sectors should prioritize compatibility with educational software, durability for high-traffic environments, and ease of cleaning. Custom keyboards can significantly improve engagement and accessibility in classrooms, making them a valuable investment for educational organizations.
Why Are Custom Mechanical Keyboards Important for Creative Design Professionals?
For graphic designers and artists, custom mechanical keyboards are vital tools that enhance precision and streamline creative workflows. These keyboards can be customized with specific key functions, allowing for quick access to design software commands, which can significantly enhance productivity. B2B buyers in creative industries should consider aesthetic customization options, key feel preferences, and the availability of macro programming capabilities. A well-designed keyboard can facilitate creativity and improve the overall design process.
How Do Call Centers Utilize Specialized Mechanical Keyboards?
In the telecommunications industry, particularly in call centers, specialized mechanical keyboards are designed to improve efficiency and comfort during long shifts. These keyboards often feature quiet switches and ergonomic designs that reduce fatigue. Buyers must consider factors such as noise levels, key travel distance, and overall ergonomic design to ensure employee comfort and productivity. Implementing custom keyboards can lead to better performance and employee satisfaction in high-pressure environments.
Related Video: My Favorite Mechanical Keyboard: A DIY 3D Printed and Handwired Custom
3 Common User Pain Points for ‘mechanical keyboard custom’ & Their Solutions
Scenario 1: Difficulty in Customization and Personalization
The Problem:
B2B buyers often face challenges when trying to meet the unique preferences of their teams or clients with mechanical keyboards. For example, a tech company in Europe may want to provide its developers with keyboards that not only enhance productivity but also reflect personal style and comfort. However, the multitude of options—from switch types to keycap materials—can lead to confusion and misalignment with user needs. This can result in investment in products that don’t satisfy the end-users, ultimately affecting productivity and employee satisfaction.
The Solution:
To effectively customize mechanical keyboards, B2B buyers should begin by conducting a thorough needs assessment involving the end-users. Surveys or focus groups can help gather insights on preferred switch types (e.g., tactile, linear, or clicky), keycap designs, and ergonomic considerations. Once the preferences are established, sourcing from reputable suppliers who specialize in custom mechanical keyboards becomes crucial. Buyers should also consider offering a range of options that allow employees to personalize their keyboards. This could include modular designs where users can swap out switches or keycaps easily. By prioritizing user input during the selection process, companies can invest in keyboards that enhance both functionality and employee satisfaction.
Scenario 2: Managing Supply Chain and Lead Time Challenges
The Problem:
For B2B buyers, especially in regions such as Africa and South America, sourcing custom mechanical keyboards can pose significant supply chain challenges. Delays in lead times can disrupt project timelines, particularly if the keyboards are intended for specific client deliveries or employee onboarding. Additionally, fluctuating shipping costs and import regulations can complicate the procurement process, leading to unexpected budget overruns.
The Solution:
To mitigate supply chain risks, B2B buyers should establish relationships with multiple suppliers across different regions. This diversification can provide backup options in case of delays or issues with a primary vendor. Implementing just-in-time (JIT) inventory practices can also help maintain optimal stock levels without overcommitting resources. Furthermore, buyers should negotiate clear lead times and penalties for delays in their contracts to hold suppliers accountable. Regularly monitoring shipping regulations and costs can also help anticipate potential barriers, allowing buyers to adjust their procurement strategies proactively. By enhancing supply chain resilience, companies can ensure timely delivery of custom mechanical keyboards to meet their operational needs.
Scenario 3: Understanding Technical Specifications and Compatibility
The Problem:
B2B buyers often struggle with the technical specifications of mechanical keyboards, particularly when integrating them with existing systems or ensuring compatibility with various software applications. For instance, a company in the Middle East may want to implement custom keyboards for a gaming setup but lacks the technical knowledge to determine whether the chosen keyboards will work seamlessly with their current hardware and software. This lack of understanding can lead to poor purchasing decisions, resulting in wasted resources and operational inefficiencies.
The Solution:
To address this knowledge gap, B2B buyers should invest in training sessions or workshops that focus on the technical aspects of mechanical keyboards. Engaging with suppliers who provide detailed product specifications and compatibility guides can also be beneficial. Additionally, creating a checklist of required specifications based on existing systems will help buyers make informed decisions. Buyers should prioritize suppliers that offer trial periods or demo units, allowing them to test compatibility before committing to bulk orders. By enhancing their technical knowledge and ensuring compatibility, B2B buyers can make strategic purchasing decisions that support their business objectives and improve overall productivity.
Strategic Material Selection Guide for mechanical keyboard custom
When selecting materials for custom mechanical keyboards, international B2B buyers must consider various factors that influence performance, durability, and cost. This guide analyzes several common materials used in mechanical keyboards, focusing on their properties, advantages, disadvantages, and specific considerations for buyers in Africa, South America, the Middle East, and Europe.
What Are the Key Properties of ABS Plastic in Mechanical Keyboards?
Acrylonitrile Butadiene Styrene (ABS) plastic is a popular choice for keycaps and housing in mechanical keyboards. It boasts excellent impact resistance and is relatively lightweight. ABS can withstand moderate temperatures and pressures, making it suitable for typical user environments. However, it is prone to wear over time, especially with heavy usage.
Pros & Cons:
ABS offers a good balance between cost and performance, making it an attractive option for manufacturers. Its low cost allows for competitive pricing in the market. However, its susceptibility to scratching and yellowing can detract from the aesthetic appeal over time, which may be a concern for buyers focused on product longevity.
Impact on Application:
ABS is compatible with various printing techniques, allowing for custom designs and branding. However, it may not be suitable for high-temperature environments, which could limit its application in specialized sectors.
Considerations for International Buyers:
Buyers should ensure compliance with international standards such as ASTM D638 for tensile properties. In regions like Europe, adherence to REACH regulations regarding chemical safety is crucial.
How Does PBT Plastic Compare for Mechanical Keyboards?
Polybutylene Terephthalate (PBT) plastic is another material frequently used for keycaps. It is known for its superior durability and resistance to wear, heat, and chemicals compared to ABS. PBT maintains its color and texture over time, making it a preferred choice for high-end mechanical keyboards.
Pros & Cons:
While PBT is more expensive than ABS, its long lifespan and resistance to fading justify the higher cost for many manufacturers. The trade-off is that PBT can be more challenging to mold, increasing manufacturing complexity and lead times.
Impact on Application:
PBT’s thermal stability makes it suitable for environments that experience higher temperatures. Its chemical resistance also allows for use in industrial settings where exposure to solvents is common.
Considerations for International Buyers:
Buyers should verify that PBT materials meet the relevant ISO standards. In the Middle East and Africa, understanding local regulations regarding plastic use can be critical for compliance.
What Are the Benefits of Using Aluminum in Mechanical Keyboards?
Aluminum is increasingly popular for custom mechanical keyboard housings due to its strength and lightweight properties. It offers excellent thermal conductivity and a premium feel, making it attractive for high-end products.
Pros & Cons:
The main advantage of aluminum is its durability and aesthetic appeal. However, it is more costly than plastic options and requires specialized manufacturing processes, which can increase overall production costs.
Impact on Application:
Aluminum’s robust nature makes it suitable for gaming and professional environments where durability is paramount. Its ability to dissipate heat effectively can enhance performance in high-intensity scenarios.
Considerations for International Buyers:
Buyers should be aware of the varying standards for aluminum quality, such as ASTM B221 for extruded aluminum. Custom regulations in Europe may also dictate specific alloy compositions.
Why Choose Steel for Mechanical Keyboard Components?
Steel is often used for structural components in mechanical keyboards, such as backplates. Its high tensile strength and resistance to deformation make it ideal for ensuring stability and longevity.
Pros & Cons:
Steel provides exceptional durability and can withstand significant wear and tear. However, it is heavier and more expensive than other materials, which may not suit all applications.
Impact on Application:
The weight of steel can enhance the keyboard’s stability, making it less prone to movement during intense use. However, its weight may be a drawback for portable designs.
Considerations for International Buyers:
Buyers should ensure compliance with international steel standards, such as ASTM A36. In regions like South America, understanding local sourcing and environmental regulations is essential.
Summary Table of Material Selection for Mechanical Keyboards
Material | Typical Use Case for mechanical keyboard custom | Key Advantage | Key Disadvantage/Limitation | Relative Cost (Low/Med/High) |
---|---|---|---|---|
ABS Plastic | Keycaps and housing | Lightweight and cost-effective | Prone to wear and yellowing | Low |
PBT Plastic | High-end keycaps | Durable and heat-resistant | Higher manufacturing complexity | Med |
Aluminum | Housings and structural components | Premium feel and durability | Higher cost and manufacturing complexity | High |
Steel | Backplates and structural components | Exceptional strength and stability | Heavier and more expensive | High |
This strategic material selection guide provides international B2B buyers with the insights needed to make informed decisions when sourcing materials for custom mechanical keyboards. Understanding the properties, advantages, and compliance requirements of each material can help ensure that the final product meets both performance and market expectations.
In-depth Look: Manufacturing Processes and Quality Assurance for mechanical keyboard custom
What Are the Main Stages of Manufacturing Mechanical Keyboards?
The manufacturing process for custom mechanical keyboards involves several key stages, each critical to ensuring the final product meets quality and performance standards. These stages include material preparation, forming, assembly, and finishing.
How Is Material Prepared for Mechanical Keyboards?
Material preparation is the initial step where raw materials are sourced and processed. For mechanical keyboards, this typically involves selecting high-quality plastics for the casing and durable metals for the switches. Suppliers often use ABS or PBT plastic, with PBT being favored for its durability and resistance to wear. The selected materials undergo rigorous testing for compliance with international safety standards, ensuring they are free from harmful substances like lead and phthalates.
What Forming Techniques Are Used in Mechanical Keyboard Manufacturing?
Once materials are prepared, forming techniques come into play. Injection molding is a primary method for shaping the keyboard casing and keycaps. This process involves melting plastic pellets and injecting the molten material into molds, where it cools and solidifies into the desired shapes. For the key switches, manufacturers may use metal stamping and machining to create precision components that ensure reliable performance.
How Is Assembly Conducted for Custom Mechanical Keyboards?
The assembly stage combines all the individual components into a functional product. Workers or automated systems place the switches on the PCB (Printed Circuit Board) and secure them using soldering techniques. Additionally, quality assurance teams monitor this stage closely to ensure alignment and functionality.
What Finishing Processes Enhance Mechanical Keyboards?
Finishing processes enhance both aesthetics and durability. This stage may include surface treatments like painting, coating, or applying decals to the keyboard. Manufacturers often implement UV coating for a glossy finish that increases scratch resistance. Final inspections during this phase ensure that the product meets visual and functional quality standards before shipping.
How Do Quality Control Measures Ensure Mechanical Keyboards Meet Standards?
Quality control (QC) is paramount in mechanical keyboard production, ensuring that each unit meets established specifications and customer expectations. Manufacturers often adhere to international standards, such as ISO 9001, which focuses on maintaining effective quality management systems.
What Are the Key Quality Control Checkpoints in the Manufacturing Process?
Quality control checkpoints typically include:
- Incoming Quality Control (IQC): Inspecting raw materials for defects before they enter the production process.
- In-Process Quality Control (IPQC): Continuous monitoring during the manufacturing stages to detect issues early.
- Final Quality Control (FQC): Comprehensive testing of the finished product to ensure functionality and compliance with specifications.
What International Standards Are Relevant for Mechanical Keyboard Manufacturing?
International standards play a crucial role in ensuring the quality and safety of mechanical keyboards. In addition to ISO 9001, manufacturers may also comply with industry-specific standards, such as:
- CE Marking: Indicates conformity with health, safety, and environmental protection standards for products sold within the European Economic Area.
- RoHS Compliance: Restricts the use of specific hazardous materials in electrical and electronic equipment.
- UL Certification: Demonstrates that products meet specific safety standards set by Underwriters Laboratories.
How Can B2B Buyers Verify Supplier Quality Control Processes?
B2B buyers looking to ensure quality in their supply chain should employ several strategies to verify supplier QC processes:
- Supplier Audits: Conducting on-site audits allows buyers to assess the manufacturing environment, processes, and adherence to quality standards.
- Requesting QC Reports: Suppliers should provide detailed QC reports that outline testing methods, results, and any corrective actions taken for non-conforming products.
- Third-Party Inspections: Engaging independent inspection firms can provide unbiased evaluations of the supplier’s quality processes and product quality.
What Are the Common Testing Methods for Mechanical Keyboards?
Testing methods for mechanical keyboards can vary but typically include:
- Functional Testing: Ensures all keys register correctly and that the keyboard functions as intended.
- Durability Testing: Simulates prolonged use to assess the lifespan of switches and other components.
- Environmental Testing: Evaluates how the keyboard performs under various conditions, such as extreme temperatures or humidity.
What Quality Control Nuances Should International Buyers Be Aware Of?
International B2B buyers, especially from Africa, South America, the Middle East, and Europe, should be aware of specific QC nuances:
- Cultural Differences in Quality Expectations: Understanding regional variations in quality standards and consumer expectations can guide negotiations and product specifications.
- Regulatory Compliance: Buyers must ensure that products meet local regulations, which may differ significantly from those in the supplier’s country.
- Language Barriers: Effective communication regarding quality standards and specifications is vital. Buyers should consider working with suppliers who can provide documentation in their preferred language.
How Can B2B Buyers Leverage Quality Assurance for Competitive Advantage?
Investing time and resources into understanding and verifying the manufacturing and quality assurance processes can provide B2B buyers with a competitive edge. By ensuring that suppliers adhere to strict quality standards, buyers can reduce the risk of product failures, enhance customer satisfaction, and ultimately improve their market reputation. This diligence not only fosters strong supplier relationships but also positions buyers as informed and responsible stakeholders in the global supply chain.
By focusing on the intricacies of manufacturing and quality assurance, international B2B buyers can make informed decisions that align with their operational goals and market demands.
Practical Sourcing Guide: A Step-by-Step Checklist for ‘mechanical keyboard custom’
This sourcing guide is designed to assist international B2B buyers in procuring custom mechanical keyboards effectively. By following this step-by-step checklist, you can streamline your sourcing process, ensuring that you select the right supplier and product that meets your specific needs.
Step 1: Define Your Technical Specifications
Before initiating the sourcing process, it’s vital to clearly define your technical specifications. This includes determining the type of switches, keycap materials, and layout options that suit your target market. By establishing these parameters, you can communicate your requirements effectively to potential suppliers and avoid misunderstandings later in the process.
- Switch Types: Decide between tactile, linear, or clicky switches based on user preferences.
- Keycap Material: Choose between ABS or PBT materials for durability and feel.
Step 2: Research Potential Suppliers
Conduct thorough research to identify potential suppliers that specialize in custom mechanical keyboards. Utilize online platforms, trade shows, and industry networks to gather a list of candidates. This step is essential for ensuring that you partner with suppliers who have the necessary expertise and capabilities.
- Directories and Platforms: Explore B2B marketplaces like Alibaba, Global Sources, and industry-specific directories.
- Trade Shows: Attend relevant trade shows in your region to meet suppliers face-to-face.
Step 3: Evaluate Supplier Capabilities
Before committing to any supplier, assess their production capabilities and experience in manufacturing custom mechanical keyboards. Request detailed company profiles, including case studies and references from previous clients. This evaluation helps ensure that the supplier can meet your quality and delivery expectations.
- Production Capacity: Inquire about their ability to handle your order size and deadlines.
- Quality Assurance Processes: Understand their quality control measures to ensure product reliability.
Step 4: Request Samples for Quality Assessment
Always request samples of the custom mechanical keyboards before placing a bulk order. This allows you to evaluate the quality of materials, craftsmanship, and overall functionality. Testing samples can help you make informed decisions and mitigate risks associated with poor quality.
- Testing Criteria: Assess switch responsiveness, keycap durability, and overall aesthetics.
- User Feedback: Gather feedback from potential users to gauge satisfaction with the samples.
Step 5: Verify Supplier Certifications and Compliance
Ensure that the suppliers you are considering have the necessary certifications and comply with relevant industry standards. This is particularly important for international buyers, as compliance with regional regulations can affect marketability.
- ISO Certifications: Look for ISO 9001 or other relevant certifications indicating quality management systems.
- Safety Standards: Verify compliance with electronic product safety standards applicable in your region.
Step 6: Negotiate Terms and Conditions
Once you have identified a suitable supplier, engage in negotiations to finalize terms and conditions. This includes pricing, payment terms, lead times, and after-sales support. Clear agreements can prevent misunderstandings and ensure a smooth procurement process.
- Payment Terms: Discuss whether payments will be made upfront, upon delivery, or through other arrangements.
- Lead Times: Confirm production and shipping timelines to align with your inventory needs.
Step 7: Establish a Communication Plan
After selecting a supplier, establish a clear communication plan to facilitate ongoing interactions. Regular updates on production status, shipping timelines, and any potential issues are crucial for maintaining a strong supplier relationship.
- Preferred Channels: Determine the best communication methods (email, phone, etc.) and frequency of updates.
- Point of Contact: Designate a primary contact person for streamlined communication.
By following this practical sourcing guide, B2B buyers can effectively navigate the complexities of procuring custom mechanical keyboards, ensuring a successful partnership with suppliers and satisfying end-user needs.
Comprehensive Cost and Pricing Analysis for mechanical keyboard custom Sourcing
What Are the Key Cost Components in Custom Mechanical Keyboard Sourcing?
When sourcing custom mechanical keyboards, understanding the cost structure is crucial for B2B buyers. The primary cost components include:
-
Materials: The choice of materials significantly impacts the overall cost. High-quality switches, keycaps, and circuit boards can drive up expenses, while budget-friendly alternatives may reduce costs but affect performance and durability.
-
Labor: Labor costs vary by region. For instance, manufacturers in Asia may offer lower labor costs compared to those in Europe or North America. However, it’s essential to consider the skill level and experience of the workforce, as these factors influence product quality.
-
Manufacturing Overhead: This includes costs associated with factory operations, utilities, and administrative expenses. Efficient manufacturing processes can help reduce overhead costs, which is beneficial for buyers looking for competitive pricing.
-
Tooling: Custom tooling is necessary for unique designs and specifications. The initial investment in tooling can be significant, but it’s often amortized over larger production runs, making it a critical factor for buyers to assess.
-
Quality Control (QC): Ensuring product quality is non-negotiable, particularly for international buyers. QC processes and certifications can add to the cost, but they also safeguard against defects and enhance customer satisfaction.
-
Logistics: Shipping costs depend on distance, weight, and the chosen shipping method. International logistics can be complex, and buyers should account for potential tariffs and duties when calculating total costs.
-
Margin: Suppliers typically add a profit margin to cover their operational costs and risks. Understanding industry-standard margins can help buyers gauge whether they are receiving a fair price.
How Do Price Influencers Affect Custom Mechanical Keyboard Sourcing?
Several factors influence the pricing of custom mechanical keyboards:
-
Volume/MOQ: Minimum order quantities (MOQ) can significantly affect pricing. Larger orders often yield lower per-unit costs, making it advantageous for buyers planning for long-term needs.
-
Specifications and Customization: The complexity of the design and the level of customization required will directly impact pricing. Unique features or custom branding can increase costs, so it’s essential to prioritize must-have specifications.
-
Material Quality and Certifications: Higher-quality materials and compliance with international standards (like ISO certifications) can elevate costs but also enhance product longevity and reliability.
-
Supplier Factors: The reputation and reliability of the supplier play a crucial role. Established suppliers with a track record of quality may charge more, but the investment often pays off through better service and fewer defects.
-
Incoterms: Understanding Incoterms is vital for managing logistics costs and responsibilities. Different terms dictate who bears the cost of shipping, insurance, and customs duties, influencing the total cost of ownership.
What Are Effective Buyer Tips for Sourcing Custom Mechanical Keyboards?
For international B2B buyers, particularly those from Africa, South America, the Middle East, and Europe, navigating the complexities of custom mechanical keyboard sourcing requires strategic thinking:
-
Negotiate Wisely: Always negotiate pricing, especially when dealing with larger volumes. Suppliers may be willing to offer discounts for bulk orders or long-term contracts.
-
Focus on Cost-Efficiency: Evaluate the total cost of ownership rather than just the initial purchase price. Consider factors such as durability, warranty, and potential repair costs to make informed decisions.
-
Understand Pricing Nuances: Be aware that pricing can fluctuate based on market demand, currency exchange rates, and geopolitical factors. Staying informed about these changes can provide leverage during negotiations.
-
Prioritize Reliable Suppliers: Conduct thorough research to identify reputable suppliers with proven track records. Request samples and references to ensure they meet your quality standards.
-
Leverage Technology: Use digital tools and platforms to streamline the sourcing process. Online marketplaces can provide insights into pricing trends and supplier performance.
Disclaimer on Indicative Prices
Prices for custom mechanical keyboards can vary significantly based on the aforementioned factors. The figures provided in market analyses should be regarded as indicative and are subject to change based on market conditions and individual supplier negotiations. Always conduct thorough due diligence to obtain the most accurate and relevant pricing information for your specific needs.
Alternatives Analysis: Comparing mechanical keyboard custom With Other Solutions
Understanding Alternatives in Mechanical Keyboards
When considering mechanical keyboards, particularly custom options, it is essential for B2B buyers to evaluate alternative solutions that may meet their operational needs. Custom mechanical keyboards offer unique advantages, but alternatives such as membrane keyboards and hybrid keyboards can also serve specific functions and user preferences. This analysis will help international buyers from regions like Africa, South America, the Middle East, and Europe make informed decisions based on performance, cost, and other relevant factors.
Comparison Table of Mechanical Keyboard Custom and Alternatives
Comparison Aspect | Mechanical Keyboard Custom | Membrane Keyboard | Hybrid Keyboard |
---|---|---|---|
Performance | High tactile feedback and responsiveness | Moderate performance, less tactile | Good balance of performance and comfort |
Cost | Higher initial investment, long-term value | Lower initial cost, shorter lifespan | Moderate cost, good durability |
Ease of Implementation | Requires customization and setup | Plug-and-play, no setup needed | Simple setup, some customization options |
Maintenance | Low maintenance, durable components | Higher frequency of replacement | Moderate maintenance, durable yet replaceable |
Best Use Case | Gaming, programming, and professional typing | General office use, casual typing | Versatile use, suitable for both casual and gaming |
Detailed Breakdown of Alternatives
What Are the Pros and Cons of Membrane Keyboards?
Membrane keyboards are often seen as the budget-friendly option in the keyboard market. They are typically less expensive and provide a straightforward plug-and-play experience, making them ideal for general office environments. However, their performance lags behind mechanical options; the lack of tactile feedback can lead to typing fatigue over long periods. Additionally, membrane keyboards tend to have a shorter lifespan compared to mechanical keyboards, which could result in higher replacement costs over time.
How Do Hybrid Keyboards Compare to Mechanical Keyboards?
Hybrid keyboards combine features of both mechanical and membrane designs, offering a compromise between the two. They often provide a better tactile experience than traditional membrane keyboards while remaining more affordable than fully mechanical options. This makes them suitable for diverse applications, from casual typing to gaming. However, they may not deliver the same level of durability or performance as fully mechanical keyboards, which could be a downside for users who prioritize heavy usage or gaming.
Making the Right Choice for Your Needs
Choosing the right keyboard solution ultimately depends on your organization’s specific needs and use cases. For businesses that prioritize performance, custom mechanical keyboards are the clear choice, especially for tasks requiring precision and responsiveness. However, if budget constraints or simpler usage scenarios are prevalent, membrane or hybrid keyboards may provide sufficient functionality without the higher costs associated with mechanical keyboards. By carefully evaluating the performance, cost, and maintenance of each option, international B2B buyers can align their keyboard choices with their operational goals and user preferences.
Essential Technical Properties and Trade Terminology for mechanical keyboard custom
What Are the Key Technical Properties of Custom Mechanical Keyboards?
When engaging with suppliers of custom mechanical keyboards, understanding the technical properties is crucial for making informed purchasing decisions. Here are some essential specifications to consider:
1. Material Grade: What Are the Best Materials for Durability and Performance?
The materials used in mechanical keyboards significantly affect their durability and performance. Common materials include ABS (Acrylonitrile Butadiene Styrene) and PBT (Polybutylene Terephthalate) for keycaps, with PBT generally offering better durability and a premium feel. The choice of material can impact not only the lifespan of the keyboard but also its tactile feedback and overall user experience. For B2B buyers, specifying the desired material grade can ensure product longevity and user satisfaction.
2. Switch Type: How Do Different Switches Affect User Experience?
Mechanical switches are the heart of the keyboard, influencing tactile feedback, actuation force, and noise level. Common types include Cherry MX, Gateron, and Kailh switches, each offering varying characteristics. Understanding the differences can help buyers select keyboards that meet specific needs, whether for gaming, typing, or specialized applications. Customization options for switch type can also be a selling point when targeting niche markets.
3. Tolerance: Why Is Precision Important in Mechanical Keyboards?
Tolerance refers to the allowable deviation in dimensions during manufacturing. High precision in tolerances ensures that the keycaps fit snugly onto the switches, enhancing the overall feel and performance of the keyboard. For B2B buyers, a focus on manufacturers that can meet strict tolerance standards can reduce issues related to assembly and functionality, thus minimizing returns and enhancing customer satisfaction.
4. Backlighting: What Are the Advantages of Customizable Lighting Options?
Backlighting options, including RGB and single-color LEDs, provide aesthetic appeal and functional advantages, such as visibility in low-light environments. Customizable lighting can be a significant selling point, particularly for gamers and professionals who work in dimly lit settings. When negotiating with suppliers, inquire about the flexibility of backlighting options to cater to your target market’s preferences.
5. Key Rollover and Anti-Ghosting: What Do These Features Mean for Performance?
Key rollover refers to the number of keys that can be pressed simultaneously without failure, while anti-ghosting prevents incorrect key presses during rapid input. These features are particularly important for gamers and high-speed typists. Understanding the specifications around key rollover and anti-ghosting can help buyers select keyboards that enhance performance and reliability, ensuring customer satisfaction.
What Are the Common Trade Terms in the Custom Mechanical Keyboard Industry?
Familiarizing yourself with industry jargon can facilitate smoother communication with suppliers. Here are some critical terms to know:
1. OEM (Original Equipment Manufacturer): What Role Does an OEM Play?
An OEM is a company that produces parts or equipment that may be marketed by another manufacturer. In the context of mechanical keyboards, working with an OEM can allow for customization and branding opportunities. B2B buyers should consider OEM partnerships to leverage their expertise in design and manufacturing.
2. MOQ (Minimum Order Quantity): How Does MOQ Affect Your Purchasing Strategy?
MOQ refers to the smallest quantity of a product that a supplier is willing to sell. Understanding MOQs is vital for budget management and inventory planning. Buyers should negotiate MOQs based on their market demand to avoid overstocking or stockouts.
3. RFQ (Request for Quotation): Why Is RFQ Important in the Sourcing Process?
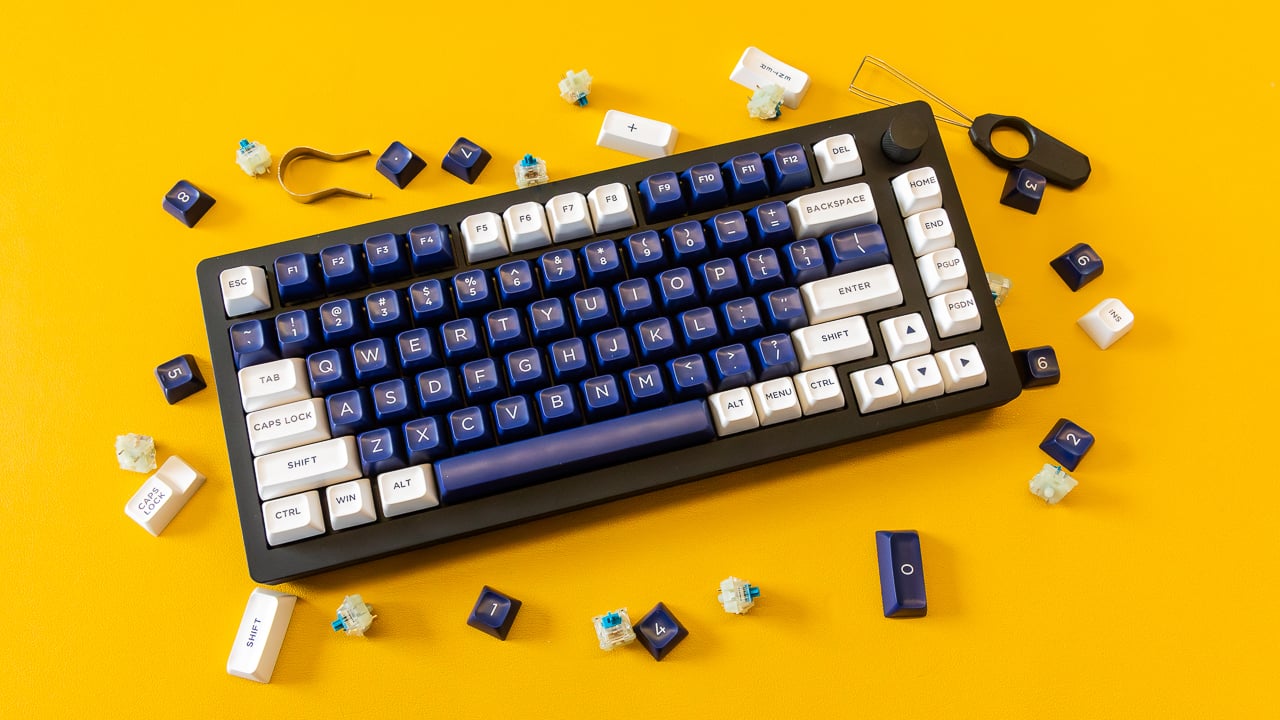
A stock image related to mechanical keyboard custom.
An RFQ is a document issued by a buyer to solicit price quotes from suppliers. It is essential for comparing costs and understanding the market rate for custom mechanical keyboards. A well-structured RFQ can lead to better pricing and terms, making it a crucial step in the procurement process.
4. Incoterms: What Are They and Why Do They Matter?
Incoterms, or International Commercial Terms, define the responsibilities of buyers and sellers in international trade. Understanding these terms can help mitigate risks related to shipping, insurance, and delivery. Buyers should ensure clarity on Incoterms when negotiating contracts with suppliers to avoid unexpected costs.
By grasping these essential technical properties and trade terms, B2B buyers can navigate the landscape of custom mechanical keyboards more effectively, ensuring they make informed decisions that align with their business needs.
Navigating Market Dynamics and Sourcing Trends in the mechanical keyboard custom Sector
What Are the Current Market Dynamics and Key Trends in the Mechanical Keyboard Custom Sector?
The mechanical keyboard custom sector is experiencing significant growth fueled by several global drivers. The increasing demand for personalized and high-performance peripherals in gaming and professional environments has led to a surge in custom keyboard offerings. Key trends include the rise of modular designs, which allow users to easily swap out components like switches and keycaps, enhancing personalization and user experience. Additionally, the adoption of smart technology in keyboards, such as programmable keys and integrated software, is becoming more prevalent, making them attractive to tech-savvy consumers.
For international B2B buyers, particularly from Africa, South America, the Middle East, and Europe, understanding regional preferences and market dynamics is crucial. In Europe, for instance, there is a growing trend towards premium products, while in Africa and South America, affordability and availability are key drivers. The Middle Eastern market is leaning towards luxury and bespoke designs, influenced by a culture of exclusivity. Buyers should also keep an eye on emerging markets that are adopting e-commerce platforms, making it easier to source custom mechanical keyboards directly from manufacturers.
How Does Sustainability Impact Sourcing in the Mechanical Keyboard Custom Sector?
Sustainability and ethical sourcing are becoming increasingly important in the mechanical keyboard custom sector. Environmental concerns related to electronic waste and the sourcing of materials are prompting buyers to consider the sustainability of their suppliers. Ethical supply chains not only enhance a brand’s reputation but also align with the growing consumer demand for environmentally friendly products.
B2B buyers should prioritize suppliers who utilize eco-friendly materials, such as recycled plastics and sustainably sourced woods. Certifications like ISO 14001 or the Forest Stewardship Council (FSC) are indicators of a supplier’s commitment to sustainability. Additionally, engaging with manufacturers who have transparent supply chains can provide assurance that labor practices are ethical. As global regulations tighten around environmental impact, sourcing from sustainable suppliers can also mitigate future compliance risks.
What Is the Evolution of the Mechanical Keyboard Custom Sector?
The mechanical keyboard custom sector has evolved significantly over the last few decades. Initially, mechanical keyboards were primarily utilized in professional settings due to their durability and tactile feedback. However, the late 2000s saw a resurgence in popularity among gamers and tech enthusiasts, leading to a wave of customization options.
This evolution has been driven by advancements in technology and a shift in consumer preferences towards personalized experiences. Today, the market is characterized by a vibrant community of enthusiasts who share designs, modify keyboards, and contribute to a robust ecosystem of aftermarket parts. For B2B buyers, this evolution presents opportunities to tap into a diverse range of products that cater to various customer needs, from budget-friendly options to high-end custom builds. Understanding this history can help buyers appreciate current trends and forecast future developments in the sector.
Frequently Asked Questions (FAQs) for B2B Buyers of mechanical keyboard custom
-
How do I select the right custom mechanical keyboard supplier for my business?
To select the right supplier, begin by assessing their credibility through online reviews and industry certifications. Request samples to evaluate product quality, and inquire about their experience with international shipping, particularly to your region (Africa, South America, the Middle East, or Europe). Additionally, establish clear communication to ensure they understand your customization needs and timelines. A reliable supplier should also have a transparent process for handling any potential issues that may arise during production or delivery. -
What are the key customization options available for mechanical keyboards?
Customization options for mechanical keyboards include switch types (e.g., tactile, linear, or clicky), keycap materials (like ABS or PBT), and backlighting features (RGB or single color). You can also choose layouts (ANSI or ISO), sizes (full-size, tenkeyless, or compact), and additional features such as programmable keys or detachable cables. Discuss these options with your supplier to create a product that meets your specific requirements and branding. -
What is the typical minimum order quantity (MOQ) for custom mechanical keyboards?
The MOQ for custom mechanical keyboards can vary significantly among suppliers, often ranging from 50 to 500 units. Factors influencing MOQ include the complexity of the customization, material costs, and production capabilities. When negotiating with suppliers, clarify their MOQ policies and explore options for lower quantities if you are just starting or testing the market, as some may be flexible based on your business relationship. -
What payment terms should I expect when sourcing custom mechanical keyboards internationally?
Payment terms for international B2B transactions typically include options like upfront deposits (commonly 30-50%), with the balance due before shipment. Some suppliers may offer net payment terms, allowing you to pay within a specified period after delivery. It’s crucial to discuss these terms upfront, considering factors like currency fluctuations and transaction fees, especially when dealing with suppliers in different regions. -
How can I ensure quality assurance (QA) for my custom mechanical keyboards?
To ensure quality assurance, request detailed specifications and quality control processes from your supplier. Conduct inspections during production and before shipment, utilizing third-party QA services if necessary. Establish clear criteria for product quality and functionality, and consider implementing a trial run with a smaller batch before committing to larger orders. This approach helps identify any potential issues early on, ensuring the final product meets your standards. -
What logistics considerations should I keep in mind when importing mechanical keyboards?
When importing mechanical keyboards, consider shipping methods, lead times, and customs regulations specific to your country. Opt for freight forwarders experienced in handling electronics to navigate import duties and tariffs effectively. Additionally, evaluate shipping insurance options to mitigate risks of loss or damage during transit. Understanding these logistics can streamline your supply chain and reduce unexpected costs. -
How do I handle potential disputes with my mechanical keyboard supplier?
To handle disputes effectively, maintain clear communication and documentation throughout the sourcing process. Establish a contract that outlines terms, conditions, and responsibilities, including a dispute resolution clause. If issues arise, address them promptly through direct dialogue, and consider mediation if necessary. Building a strong relationship with your supplier can also facilitate smoother resolutions in case of disagreements. -
What trends should I be aware of in the custom mechanical keyboard market?
Stay informed about trends such as the growing demand for ergonomic designs, wireless technology, and customizable RGB lighting. The rise of gaming and remote work has increased interest in high-performance keyboards, leading to innovations in materials and switch technology. Additionally, eco-friendly manufacturing practices are becoming more important, as buyers increasingly prefer sustainable options. Monitoring these trends can help you align your product offerings with market demands and stay competitive.
Important Disclaimer & Terms of Use
⚠️ Important Disclaimer
The information provided in this guide, including content regarding manufacturers, technical specifications, and market analysis, is for informational and educational purposes only. It does not constitute professional procurement advice, financial advice, or legal advice.
While we have made every effort to ensure the accuracy and timeliness of the information, we are not responsible for any errors, omissions, or outdated information. Market conditions, company details, and technical standards are subject to change.
B2B buyers must conduct their own independent and thorough due diligence before making any purchasing decisions. This includes contacting suppliers directly, verifying certifications, requesting samples, and seeking professional consultation. The risk of relying on any information in this guide is borne solely by the reader.
Strategic Sourcing Conclusion and Outlook for mechanical keyboard custom
In the evolving landscape of custom mechanical keyboards, strategic sourcing emerges as a vital component for international B2B buyers. By understanding market trends, assessing supplier capabilities, and prioritizing quality and reliability, businesses can significantly enhance their procurement processes. Engaging with suppliers from diverse regions, particularly in Africa, South America, the Middle East, and Europe, provides an opportunity to tap into unique designs and innovations that cater to varying consumer preferences.
How can B2B buyers leverage strategic sourcing for competitive advantage? The answer lies in building strong supplier relationships and conducting thorough due diligence. This approach not only minimizes risks but also fosters collaboration that can lead to customized solutions tailored to specific business needs. As the demand for personalized mechanical keyboards continues to grow, aligning sourcing strategies with market insights will be crucial for maintaining a competitive edge.
Looking ahead, the mechanical keyboard market presents exciting opportunities for growth and innovation. B2B buyers are encouraged to stay informed about emerging trends, invest in supplier partnerships, and adapt their sourcing strategies to meet evolving consumer demands. Now is the time to act—unlock the potential of your business through strategic sourcing of custom mechanical keyboards.