Unlock Quality: The Ultimate Guide to Table Legs Custom (2025)
Introduction: Navigating the Global Market for table legs custom
In the dynamic world of custom table legs, international B2B buyers face the pressing challenge of sourcing high-quality products that align with specific design and functional requirements. Whether you’re looking for robust legs for commercial dining tables or elegant options for bespoke office furniture, understanding the nuances of the global market is essential. This guide serves as a comprehensive resource, delving into various types of table legs, their applications across different industries, and the critical factors to consider when vetting suppliers.
International buyers, particularly from regions such as Africa, South America, the Middle East, and Europe—including countries like Mexico and Turkey—must navigate diverse manufacturing standards, cultural preferences, and logistical considerations. This guide empowers you to make informed purchasing decisions by providing insights into cost structures, material choices, and trends influencing the custom furniture market.
With actionable strategies and expert advice, you will learn how to identify reliable suppliers, evaluate product quality, and negotiate favorable terms. By the end of this guide, you will be equipped to enhance your sourcing process, ensuring that your selections not only meet aesthetic and functional needs but also contribute to your overall business success in the competitive landscape of custom furniture manufacturing.
Understanding table legs custom Types and Variations
Type Name | Key Distinguishing Features | Primary B2B Applications | Brief Pros & Cons for Buyers |
---|---|---|---|
Metal Table Legs | Durable, modern aesthetics, customizable finishes | Restaurants, offices, outdoor spaces | Pros: High durability, modern look; Cons: Can be heavy and expensive. |
Wooden Table Legs | Classic appeal, various wood types, easy to customize | Furniture manufacturers, bespoke projects | Pros: Warm aesthetics, easy to work with; Cons: Susceptible to moisture and damage. |
Adjustable Table Legs | Height flexibility, often foldable, versatile | Conference tables, multi-purpose furniture | Pros: Space-saving, versatile for different uses; Cons: May lack stability under heavy loads. |
Trestle Table Legs | Supportive design, often made of wood or metal | Banquet tables, rustic furniture | Pros: Strong support, aesthetic appeal; Cons: Limited adjustability, heavier design. |
Cylindrical Table Legs | Sleek, modern shape, often made from metal or plastic | Contemporary offices, retail displays | Pros: Unique look, space-efficient; Cons: May lack stability compared to traditional designs. |
What Are the Key Characteristics of Metal Table Legs for B2B Buyers?
Metal table legs are known for their durability and modern aesthetics. They can be customized with various finishes, making them suitable for different design themes. These legs are ideal for high-traffic environments such as restaurants and outdoor spaces, where resilience is crucial. When considering metal table legs, buyers should evaluate the weight and cost, as these legs can be heavier and more expensive than alternatives, which may impact shipping and assembly.
How Do Wooden Table Legs Stand Out in Customization?
Wooden table legs offer a classic appeal and come in various types of wood, allowing for extensive customization in terms of finish and style. They are particularly popular among furniture manufacturers and in bespoke projects where unique designs are paramount. Buyers should consider the wood’s susceptibility to moisture and damage, which may require additional maintenance or protective finishes, particularly in humid climates.
Why Choose Adjustable Table Legs for Versatile B2B Applications?
Adjustable table legs provide height flexibility, making them ideal for conference tables and multi-purpose furniture. Their foldable nature allows for easy storage and transport, which is beneficial for businesses that frequently change their layouts. However, buyers should assess their stability, as adjustable legs may not support heavy loads as effectively as fixed designs.
What Advantages Do Trestle Table Legs Offer in B2B Settings?
Trestle table legs are characterized by their supportive design, making them an excellent choice for banquet tables and rustic furniture. They offer strong support and an aesthetically pleasing appearance, which is appealing for events and dining settings. However, their heavier design may limit portability, and their lack of adjustability can be a drawback for businesses that require flexible setups.
How Do Cylindrical Table Legs Enhance Modern B2B Designs?
Cylindrical table legs are known for their sleek, modern shape and are often made from materials like metal or plastic. They are suitable for contemporary offices and retail displays where space efficiency and aesthetics are crucial. While they provide a unique look, buyers should be cautious about their stability compared to more traditional leg designs, especially in high-use environments.
Key Industrial Applications of table legs custom
Industry/Sector | Specific Application of table legs custom | Value/Benefit for the Business | Key Sourcing Considerations for this Application |
---|---|---|---|
Furniture Manufacturing | Custom dining table legs | Enhances product differentiation and brand identity | Material quality, design specifications, and manufacturing lead times |
Hospitality | Custom table legs for restaurants and cafes | Improves aesthetics and functionality in dining spaces | Durability, ease of maintenance, and compliance with safety standards |
Office Furniture | Adjustable table legs for workstations | Supports ergonomic designs, improving employee productivity | Adjustability features, load capacity, and compatibility with existing furniture |
Retail Display | Custom table legs for retail fixtures | Attracts customers and enhances product presentation | Customization options, stability, and ease of assembly |
Event Management | Lightweight, portable table legs | Facilitates easy setup and breakdown for events | Weight, portability, and strength to withstand various setups |
How Are Custom Table Legs Used in Furniture Manufacturing?
In the furniture manufacturing sector, custom dining table legs play a crucial role in product differentiation. Manufacturers can create unique designs that align with their brand identity, appealing to specific consumer preferences. Buyers in this industry should prioritize material quality and design specifications to ensure that the final product meets both aesthetic and functional requirements. Additionally, understanding manufacturing lead times is essential for effective inventory management and timely delivery.
What Benefits Do Custom Table Legs Offer to the Hospitality Industry?
In hospitality, particularly in restaurants and cafes, custom table legs are vital for enhancing the aesthetics and functionality of dining spaces. These legs can be designed to match the overall decor, creating a cohesive atmosphere that attracts customers. For B2B buyers in this sector, durability and ease of maintenance are key considerations, as tables endure frequent use. Compliance with safety standards is also critical to prevent accidents and ensure customer satisfaction.
How Do Adjustable Table Legs Improve Office Furniture?
Adjustable table legs are increasingly popular in the office furniture sector, particularly for workstations. They support ergonomic designs that cater to the diverse needs of employees, thereby enhancing productivity and comfort. Buyers should focus on features such as adjustability, load capacity, and compatibility with existing furniture when sourcing these components. Additionally, ensuring that the legs comply with workplace safety regulations can mitigate potential liabilities.
Why Are Custom Table Legs Important for Retail Displays?
Custom table legs are essential in retail display applications, as they significantly impact product presentation and customer attraction. Retailers can design legs that complement their branding and enhance the visual appeal of their merchandise. For international B2B buyers, customization options, stability, and ease of assembly are crucial sourcing considerations. These factors ensure that the displays are not only attractive but also functional and reliable in high-traffic environments.
How Do Lightweight Table Legs Benefit Event Management?
In event management, lightweight and portable table legs are invaluable for facilitating easy setup and breakdown at various venues. These legs allow event planners to create versatile layouts quickly, adapting to different types of events. Buyers should consider the weight, portability, and strength of the table legs to ensure they can withstand various setups and conditions. Additionally, understanding the logistics of transport and storage can further streamline event operations.
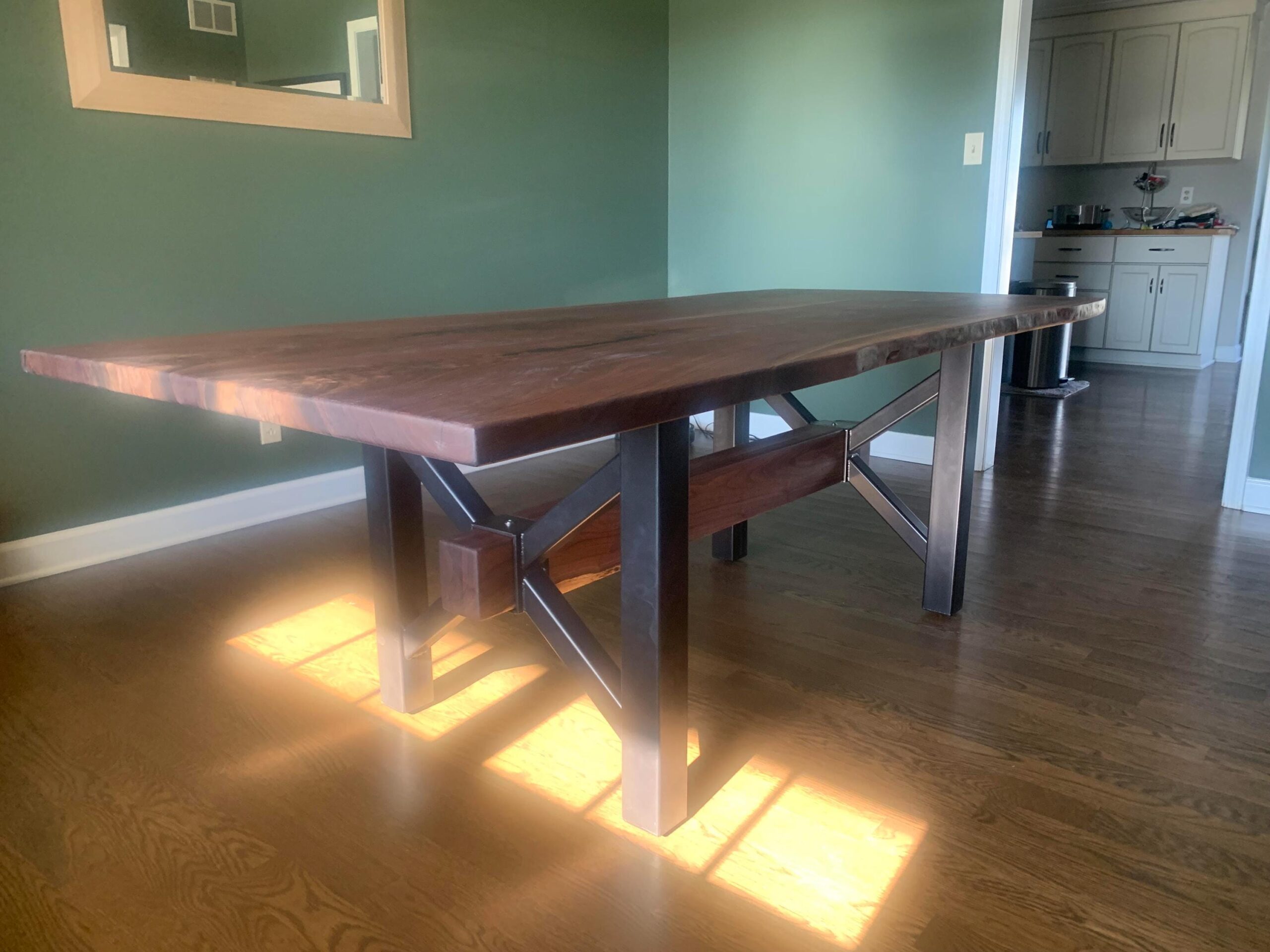
A stock image related to table legs custom.
Related Video: How To Make An Industrial Black Pipe Bar Height Table
3 Common User Pain Points for ‘table legs custom’ & Their Solutions
Scenario 1: Sourcing Quality Materials for Custom Table Legs
The Problem: One of the biggest challenges faced by B2B buyers, especially in regions like Africa and South America, is ensuring the quality of materials used in custom table legs. Poor-quality materials can lead to structural instability, compromising the product’s lifespan and affecting customer satisfaction. Buyers may struggle with finding reliable suppliers who offer durable materials that meet their specifications, especially when dealing with international sourcing and shipping logistics.
The Solution: To address this issue, B2B buyers should establish clear criteria for material selection before initiating the sourcing process. This includes specifying the type of wood, metal, or composite materials desired, along with any necessary certifications (e.g., FSC for wood). Engaging in direct communication with suppliers about their sourcing practices and material origins can also foster transparency. Additionally, utilizing platforms that allow for sample orders can help assess the quality before committing to larger purchases. Partnering with suppliers who provide detailed material specifications and test results can further ensure the durability and reliability of the table legs.
Scenario 2: Customization Limitations and Design Constraints
The Problem: Many B2B buyers encounter limitations in customization options when sourcing table legs. This is particularly prevalent in the Middle East and Europe, where unique designs are crucial for catering to diverse customer preferences. Buyers often find that suppliers offer a limited range of styles, colors, and sizes, which can hinder their ability to create distinctive products that stand out in a competitive market.
The Solution: To overcome customization challenges, buyers should prioritize working with suppliers who specialize in bespoke solutions. Establishing a collaborative relationship with these suppliers can lead to more flexibility in design choices. When approaching a supplier, it’s beneficial to present detailed design specifications, including sketches or CAD files, to convey the desired outcome clearly. Buyers can also ask about the supplier’s design capabilities and whether they have experience with similar projects. Additionally, leveraging technology such as 3D modeling can help visualize the final product, ensuring alignment between the buyer’s expectations and the supplier’s output.
Scenario 3: Navigating International Shipping and Customs Regulations
The Problem: International B2B buyers often face hurdles related to shipping logistics and customs regulations when importing custom table legs. This can be particularly challenging for buyers in Africa and South America, where shipping delays and unexpected tariffs can significantly impact project timelines and budgets. Buyers may find themselves unprepared for the complexities involved in ensuring compliance with local regulations, leading to potential fines or shipment rejections.
The Solution: To effectively navigate these shipping challenges, buyers should conduct thorough research on the customs regulations of their respective countries before placing orders. Engaging a freight forwarder or logistics expert familiar with international shipping can provide valuable insights into the best practices for importing custom products. Buyers should also communicate with suppliers about their shipping methods and timelines, ensuring that both parties agree on delivery expectations. Additionally, obtaining comprehensive shipping documentation and ensuring that all required duties and taxes are accounted for can streamline the process. By proactively addressing these logistics concerns, buyers can minimize delays and ensure a smoother import experience for their custom table legs.
Strategic Material Selection Guide for table legs custom
When selecting materials for custom table legs, international B2B buyers must consider various factors, including the properties of the materials, their suitability for specific applications, and compliance with regional standards. Here, we analyze four common materials—wood, metal, plastic, and composite materials—highlighting their advantages and limitations in the context of custom table legs.
What Are the Key Properties of Wood for Custom Table Legs?
Wood is a traditional choice for table legs, known for its aesthetic appeal and versatility. Key properties include its natural strength and lightweight nature, making it easy to handle and install. However, wood is susceptible to temperature and humidity changes, which can lead to warping and cracking.
Pros & Cons: While wood offers excellent durability and a classic look, it can be more expensive than other materials, especially when sourced from sustainable forests. Manufacturing complexity can vary based on the type of wood and finishing processes. For applications requiring stability, wood may not be the best choice in humid climates typical in parts of Africa and South America.
Impact on Application: Wood is generally compatible with most table surfaces but may not be ideal for environments exposed to moisture or extreme temperatures. Buyers should consider local wood types that are resistant to these conditions.
How Does Metal Compare for Custom Table Legs?
Metal, particularly steel and aluminum, is renowned for its strength and durability. Key properties include high corrosion resistance (especially in stainless steel) and the ability to withstand significant weight and pressure.
Pros & Cons: Metal legs are highly durable and can support heavier tables, making them suitable for commercial applications. However, they can be more expensive than wood and may require complex manufacturing processes, including welding and finishing. Additionally, metal can be prone to scratching and denting, which may affect the aesthetic over time.
Impact on Application: Metal is a great choice for industrial or modern-style tables, but buyers must consider local standards for metal quality and corrosion resistance, particularly in humid regions like the Middle East.
What Are the Advantages of Plastic for Custom Table Legs?
Plastic is increasingly popular for custom table legs due to its lightweight nature and versatility. Key properties include resistance to moisture and chemicals, making it suitable for various environments.
Pros & Cons: The primary advantage of plastic is its low cost and ease of manufacturing. However, it may not provide the same level of durability as wood or metal, particularly under heavy loads. Additionally, plastic can become discolored over time and may not have the same aesthetic appeal as natural materials.
Impact on Application: Plastic is well-suited for casual or outdoor furniture but may not meet the aesthetic expectations for high-end applications. Buyers should ensure that the plastic used complies with local environmental regulations.
Why Choose Composite Materials for Custom Table Legs?
Composite materials, which combine different materials to enhance performance, are gaining traction in the furniture industry. Key properties include improved strength-to-weight ratios and resistance to environmental factors.
Pros & Cons: Composites can offer the best of both worlds—durability and aesthetic appeal—while often being lighter than solid wood or metal. However, they can be more expensive and may require specialized manufacturing processes.
Impact on Application: Composites are suitable for both indoor and outdoor applications, but buyers should verify that the composites used meet international quality standards, especially in regions with strict regulations like Europe.
Summary Table of Material Selection for Custom Table Legs
Material | Typical Use Case for table legs custom | Key Advantage | Key Disadvantage/Limitation | Relative Cost (Low/Med/High) |
---|---|---|---|---|
Wood | Residential and decorative tables | Aesthetic appeal and versatility | Susceptible to warping and humidity | Medium |
Metal | Industrial and commercial tables | High strength and durability | Higher cost and manufacturing complexity | High |
Plastic | Casual and outdoor furniture | Lightweight and moisture-resistant | Lower durability and aesthetic appeal | Low |
Composite | Versatile indoor/outdoor applications | Enhanced strength and aesthetics | Higher cost and specialized manufacturing | High |
This analysis provides a comprehensive overview of material options for custom table legs, enabling international B2B buyers to make informed decisions based on their specific needs and regional considerations.
In-depth Look: Manufacturing Processes and Quality Assurance for table legs custom
What Are the Main Stages in the Manufacturing Process for Custom Table Legs?
The manufacturing of custom table legs involves several key stages, each critical for ensuring quality and functionality. Understanding these stages allows B2B buyers to make informed decisions when selecting suppliers.
-
Material Preparation
– The process begins with the selection of appropriate materials, such as wood, metal, or plastic. Buyers should consider the properties of each material, such as strength, weight, and aesthetic appeal.
– Raw materials are inspected for defects and sorted according to specifications. This initial quality check is crucial for preventing issues down the line. -
Forming
– This stage involves shaping the materials into the desired leg designs. Techniques can vary widely, including CNC machining for metal legs or steam bending for wooden legs.
– Customization options such as size, shape, and finish can be incorporated during this phase. Advanced techniques like 3D printing are increasingly being adopted for unique designs. -
Assembly
– After forming, components are assembled. For metal legs, welding or bolting might be utilized, while wooden legs could be joined using dowels or screws.
– Precision in assembly is essential to ensure stability and durability. Buyers should inquire about the methods used to guarantee that the final product meets specified tolerances. -
Finishing
– This final stage enhances the appearance and durability of the table legs. Finishing techniques may include sanding, painting, staining, or applying protective coatings.
– The choice of finish can impact both aesthetics and the lifespan of the product. B2B buyers should discuss finishing options with suppliers to align with their branding and usage requirements.
How Is Quality Assurance Managed in Custom Table Leg Manufacturing?
Quality assurance (QA) is a critical component of the manufacturing process, ensuring that the final product meets international standards and customer expectations. Here’s an overview of how QA is typically managed.
What International Standards Should B2B Buyers Be Aware Of?
B2B buyers should familiarize themselves with relevant international quality standards that can impact their sourcing decisions. Key standards include:
- ISO 9001: This standard focuses on quality management systems and is widely adopted across industries. It ensures that suppliers have processes in place to consistently deliver quality products.
- CE Marking: Particularly relevant in Europe, CE marking indicates that a product meets EU safety, health, and environmental protection standards.
- API Standards: For metal components, API standards may be applicable, ensuring that products meet specific performance requirements.
What Are the Key Quality Control Checkpoints?
Quality control (QC) checkpoints are crucial for maintaining product quality throughout the manufacturing process. Common checkpoints include:
- Incoming Quality Control (IQC): This involves inspecting raw materials upon arrival to ensure they meet specified criteria.
- In-Process Quality Control (IPQC): During manufacturing, ongoing checks are performed to monitor adherence to quality standards. This may include dimensional checks and visual inspections.
- Final Quality Control (FQC): Once the products are completed, a thorough inspection is carried out to verify that they meet all specifications and standards before shipment.
What Testing Methods Are Commonly Used in Quality Assurance?
Various testing methods are employed to assess the quality and performance of custom table legs:
- Dimensional Testing: Ensures that the product meets specified measurements and tolerances.
- Load Testing: This is particularly important for table legs to ensure they can support the intended weight without failure.
- Finish Testing: Evaluates the durability of paints or coatings, often through scratch tests or adhesion tests.
How Can B2B Buyers Verify Supplier Quality Control?
Verifying a supplier’s quality control processes is crucial for mitigating risks in international sourcing. Here are effective methods B2B buyers can use:
-
Supplier Audits
– Conducting regular audits of suppliers can provide insights into their quality management systems and manufacturing processes. Buyers should look for certifications like ISO 9001 during these audits. -
Reviewing Quality Reports
– Requesting detailed quality reports from suppliers can help buyers understand the frequency and results of quality checks conducted throughout production. -
Third-Party Inspections
– Engaging third-party inspection services can offer an unbiased assessment of product quality before shipment. This is particularly valuable for international transactions, where buyers may not have direct oversight.
What Are the Quality Control Nuances for International B2B Buyers?
B2B buyers from Africa, South America, the Middle East, and Europe should be aware of several nuances in quality control when sourcing custom table legs:
- Cultural Differences: Different regions may have varying approaches to quality assurance. Understanding these differences can help buyers set realistic expectations and foster better supplier relationships.
- Regulatory Compliance: Buyers must ensure that the products comply with local regulations in their markets, which may differ significantly from those in the supplier’s country.
- Language Barriers: Clear communication is essential for quality assurance. Buyers should ensure that technical specifications and quality expectations are accurately conveyed and understood.
Conclusion: Prioritizing Manufacturing and Quality Assurance in Custom Table Legs
For international B2B buyers, a comprehensive understanding of the manufacturing processes and quality assurance measures is vital when sourcing custom table legs. By focusing on material selection, production techniques, and robust quality control practices, buyers can ensure they partner with reliable suppliers that meet their specific needs. By leveraging international standards and verification methods, businesses can mitigate risks and enhance product satisfaction, leading to long-term success in their ventures.
Practical Sourcing Guide: A Step-by-Step Checklist for ‘table legs custom’
This sourcing guide aims to equip international B2B buyers with a systematic approach to procuring custom table legs. Understanding the unique requirements of your market and ensuring a reliable supply chain can lead to significant cost savings and enhanced product quality. The following checklist outlines the essential steps to ensure a successful sourcing process.
Step 1: Define Your Technical Specifications
Begin by clearly outlining the technical specifications of the custom table legs you require. This includes dimensions, materials, load-bearing capacity, and design features. Having a detailed specification is crucial as it sets the foundation for supplier engagement and ensures that the final product meets your quality standards.
- Material Considerations: Specify whether you prefer wood, metal, or composite materials.
- Design Elements: Consider if you need any unique features, such as adjustable height or specific finishes.
Step 2: Research and Identify Potential Suppliers
Conduct thorough research to identify potential suppliers that specialize in custom table legs. Look for companies with a strong reputation in the market and a proven track record of delivering quality products.
- Utilize B2B Platforms: Leverage platforms like Alibaba, ThomasNet, or local trade directories relevant to your region.
- Industry Recommendations: Seek referrals from industry contacts or trade associations to find reputable suppliers.
Step 3: Evaluate Supplier Capabilities
Before committing, it’s crucial to vet suppliers thoroughly. Assess their production capabilities, including technology, workforce expertise, and quality control processes.
- Request Documentation: Ask for certifications, factory audits, and compliance with international standards.
- Capacity Analysis: Ensure they can meet your order volume and timeline without compromising quality.
Step 4: Request Samples for Quality Assessment
Always request samples of custom table legs before placing a bulk order. This step is essential to evaluate the quality, craftsmanship, and adherence to your specifications.
- Check for Consistency: Ensure that the samples reflect the quality you expect for your final order.
- Functional Testing: If applicable, test the samples for load-bearing capacity and durability.
Step 5: Negotiate Terms and Pricing
Once you have shortlisted suppliers, initiate negotiations on pricing, payment terms, and delivery schedules. This step is vital to establish a mutually beneficial relationship.
- Consider Total Cost of Ownership: Factor in shipping, customs duties, and potential tariffs in your negotiations.
- Flexible Payment Terms: Discuss options like letters of credit or payment upon delivery to manage cash flow effectively.
Step 6: Establish a Clear Contract
Draft a clear and comprehensive contract that outlines all agreed-upon terms, including delivery timelines, quality standards, and penalties for non-compliance. A well-structured contract protects both parties and minimizes potential disputes.
- Include Clauses: Ensure there are clauses for quality assurance and recourse in case of disputes.
- Confidentiality Agreements: If necessary, include non-disclosure agreements to protect proprietary designs.
Step 7: Monitor Production and Quality Control
Once production begins, maintain regular communication with your supplier. Implement quality control measures to ensure the final products meet your specifications.
- Regular Updates: Schedule periodic updates and site visits if possible.
- Final Inspection: Plan for a final quality inspection before shipment to catch any issues early.
By following this structured approach, B2B buyers from Africa, South America, the Middle East, and Europe can effectively navigate the complexities of sourcing custom table legs, ensuring quality and reliability in their supply chain.
Comprehensive Cost and Pricing Analysis for table legs custom Sourcing
What Are the Key Cost Components in Custom Table Legs Sourcing?
When sourcing custom table legs, understanding the cost structure is crucial for effective budgeting and negotiation. The primary cost components include:
-
Materials: The choice of material significantly impacts the overall cost. Common materials such as wood, metal, and plastic each have different price points based on quality and market availability. For instance, hardwoods like oak or walnut will typically cost more than softwoods or manufactured materials.
-
Labor: Labor costs vary by region and depend on the complexity of the design. Skilled craftsmanship will command higher wages, especially if the production is in areas with higher living costs.
-
Manufacturing Overhead: This includes costs related to utilities, rent, equipment maintenance, and salaries of non-direct labor. Depending on the supplier’s operational efficiency, this can vary widely.
-
Tooling: Initial setup costs for molds and specific tooling can be significant, particularly for custom designs. These costs can often be amortized over larger production runs, making them less impactful for higher volume orders.
-
Quality Control (QC): Implementing rigorous QC processes ensures product reliability but adds to the overall cost. It’s essential for maintaining standards, particularly for international shipments where compliance may be scrutinized.
-
Logistics: Shipping costs, including freight, insurance, and handling, are vital considerations, particularly for international buyers. Incoterms will influence who bears these costs.
-
Margin: Suppliers will typically include a margin to cover risks and ensure profitability. This can vary based on market competition and perceived value of the product.
How Do Price Influencers Affect Custom Table Legs?
Several factors can influence the pricing of custom table legs, which international B2B buyers should be aware of:
-
Volume/MOQ: Minimum Order Quantities (MOQs) can significantly affect pricing. Larger orders usually lead to lower per-unit costs, but this requires careful demand forecasting.
-
Specifications and Customization: More complex designs or specific requirements can drive up costs due to additional labor and material needs. Clear communication about specifications can help manage expectations and costs.
-
Material Choices: As previously mentioned, different materials come with varying costs. Opting for more sustainable or premium materials may increase expenses but can also enhance product appeal.
-
Quality and Certifications: Certifications for sustainability or safety can also affect pricing. Suppliers with recognized certifications may charge a premium, but this can also provide a competitive advantage in certain markets.
-
Supplier Factors: The supplier’s reputation, location, and production capabilities can influence pricing. Established suppliers might charge more for their reliability and service.
-
Incoterms: Understanding Incoterms is essential for international transactions. They define responsibilities regarding shipping, insurance, and tariffs, which can affect the total landed cost of products.
What Are Some Effective Buyer Tips for Cost-Efficiency in Custom Table Legs?
To ensure cost-effective sourcing of custom table legs, international buyers should consider the following strategies:
-
Negotiation Skills: Strong negotiation can lead to better pricing, especially for bulk orders. Always be prepared to discuss terms and explore discounts for larger volumes.
-
Total Cost of Ownership (TCO): Look beyond the initial purchase price. Consider maintenance, replacement, and logistics costs to get a true picture of what the investment will entail over time.
-
Understand Pricing Nuances: Be aware of the pricing landscape in different regions. For example, suppliers in Turkey might offer competitive pricing due to lower labor costs, while European suppliers may provide superior quality and faster shipping.
-
Market Research: Conduct thorough research on potential suppliers. Understanding their production capabilities, lead times, and quality assurance processes can help mitigate risks and control costs.
-
Build Long-term Relationships: Establishing long-term partnerships with suppliers can lead to better pricing and priority service. Loyalty can often translate into cost savings over time.
Disclaimer on Indicative Prices
Please note that the prices associated with custom table legs can vary widely based on the factors discussed above. It is advisable to conduct specific inquiries to obtain accurate quotes tailored to your requirements.
Alternatives Analysis: Comparing table legs custom With Other Solutions
Understanding Alternative Solutions for Custom Table Legs
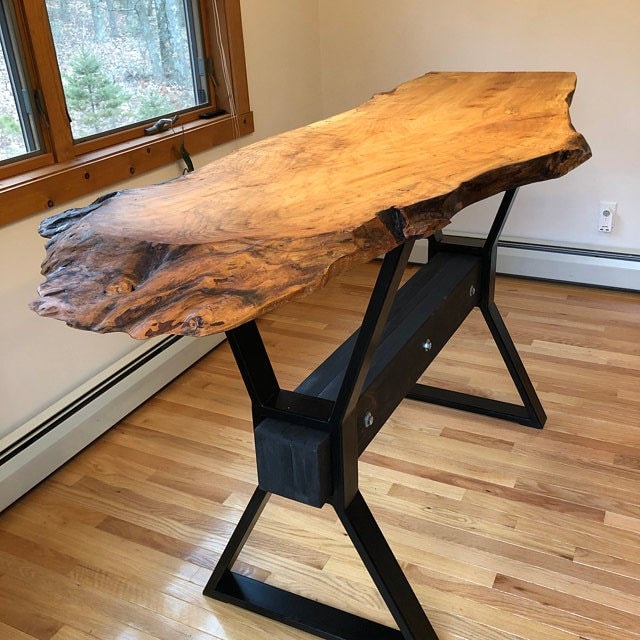
A stock image related to table legs custom.
In the realm of furniture design and manufacturing, the need for customized solutions is paramount, especially for B2B buyers who require flexibility in their projects. Custom table legs offer a unique opportunity for businesses to differentiate their products, but it’s important to evaluate other viable solutions that can meet similar needs. In this section, we will compare custom table legs with pre-manufactured table legs and adjustable table legs, providing insights that will aid international buyers in making informed decisions.
Comparison Table
Comparison Aspect | Table Legs Custom | Pre-Manufactured Table Legs | Adjustable Table Legs |
---|---|---|---|
Performance | High durability and tailored aesthetics | Standardized design; may lack uniqueness | Versatile; can adapt to different heights |
Cost | Generally higher due to bespoke design | Lower cost due to mass production | Mid-range; varies by complexity |
Ease of Implementation | Requires collaboration with manufacturers | Quick and straightforward | Moderate; requires assembly |
Maintenance | Often lower maintenance if well-designed | Variable; depends on material quality | Regular checks needed for adjustability |
Best Use Case | Unique projects requiring specific design elements | High-volume orders needing consistency | Spaces needing flexibility and height adjustments |
What Are the Pros and Cons of Pre-Manufactured Table Legs?
Pre-manufactured table legs are a cost-effective solution for businesses that prioritize budget over customization. These legs are mass-produced, which allows for lower prices and quicker delivery times. However, the trade-off is that they lack the unique design elements that can set a brand apart. For B2B buyers in regions like Africa or South America, where budget constraints may be tighter, pre-manufactured options can provide a practical solution. On the downside, businesses may find that these legs do not always meet specific aesthetic or functional requirements, potentially limiting design creativity.
How Do Adjustable Table Legs Offer Flexibility?
Adjustable table legs provide an innovative alternative, especially for businesses that require versatility in their furniture designs. These legs can be modified to different heights, making them ideal for multi-functional spaces, such as conference rooms or dining areas. The flexibility of adjustable legs can enhance usability and comfort, which is particularly appealing in the Middle Eastern and European markets, where diverse consumer needs are prevalent. However, they may require more regular maintenance to ensure that the adjustment mechanisms function properly, which could be a consideration for B2B buyers evaluating long-term usability.
Making an Informed Decision: Which Solution Is Right for You?
When choosing between custom table legs and alternative solutions, B2B buyers should carefully assess their specific needs, budget constraints, and desired outcomes. Custom table legs excel in providing unique designs tailored to a brand’s identity, making them an excellent choice for businesses focused on differentiation. In contrast, pre-manufactured legs can offer significant cost savings and expedited delivery, appealing to those prioritizing efficiency. Adjustable legs present a middle ground, providing flexibility that can cater to various functionalities.
Ultimately, the right choice depends on the buyer’s specific project requirements, market demands, and long-term goals. By analyzing these alternatives, international B2B buyers can strategically position themselves in the competitive furniture market.
Essential Technical Properties and Trade Terminology for table legs custom
What Are the Key Technical Properties of Custom Table Legs?
When sourcing custom table legs, understanding the technical properties is vital for ensuring quality, durability, and compatibility with your specific requirements. Here are some essential specifications to consider:
1. Material Grade: Why Does It Matter?
The material grade refers to the quality of the material used to manufacture the table legs. Common materials include wood, metal (like steel or aluminum), and plastic. Each material has unique characteristics, such as weight capacity, aesthetic appeal, and resistance to environmental factors. For instance, stainless steel is favored for its strength and corrosion resistance, making it ideal for outdoor furniture. Selecting the appropriate material grade is crucial for meeting industry standards and ensuring longevity.
2. Tolerance: How Does Precision Impact Quality?
Tolerance indicates the acceptable variation in the dimensions of the table legs. It is typically expressed as a range (e.g., ±0.5 mm). High tolerance standards are essential for parts that must fit together perfectly, especially in modular or customizable furniture designs. Inaccurate tolerances can lead to assembly issues, compromising the overall stability and functionality of the table. Understanding tolerance specifications helps buyers ensure that the products meet their design expectations and operational needs.
3. Load Capacity: What Should You Consider for Stability?
Load capacity defines the maximum weight a table leg can support without compromising its structural integrity. This specification is particularly important for buyers in industries such as hospitality or manufacturing, where heavy loads are common. Knowing the load capacity helps in selecting the right table legs for various applications, ensuring that they can withstand intended usage without failure.
4. Finish: How Does Surface Treatment Affect Aesthetics and Durability?
The finish of custom table legs refers to the surface treatment applied to enhance appearance and resistance to wear. Common finishes include powder coating, lacquer, or varnish for wood. A well-chosen finish not only improves aesthetic appeal but also protects against scratches, moisture, and UV damage. For international buyers, understanding finish options can significantly influence product longevity and maintenance requirements.
What Are Common Trade Terms Related to Custom Table Legs?
Familiarizing yourself with industry jargon is essential for effective communication and negotiation. Here are some common trade terms you should know:
1. OEM (Original Equipment Manufacturer): What Is Its Role?
OEM refers to companies that manufacture products that are sold under another brand’s name. In the context of custom table legs, working with an OEM can provide you with tailored solutions that align with your brand’s specifications. This relationship allows for greater customization and often results in lower production costs, making it an attractive option for B2B buyers.
2. MOQ (Minimum Order Quantity): How Does It Affect Your Purchase?
MOQ is the smallest quantity of a product that a supplier is willing to sell. Understanding the MOQ is critical for budgeting and inventory management. Suppliers may impose MOQs to ensure efficiency in production and shipping. Buyers should negotiate these terms to align with their project scales, especially if they are testing new designs or entering new markets.
3. RFQ (Request for Quotation): Why Is It Important?
An RFQ is a document that solicits price proposals from suppliers. It is an essential tool for buyers looking to compare costs and capabilities among different manufacturers. Providing detailed specifications in an RFQ can lead to more accurate quotes, enabling better decision-making based on price and quality comparisons.
4. Incoterms (International Commercial Terms): How Do They Simplify Trade?
Incoterms are standardized international trade terms that define the responsibilities of buyers and sellers in the shipping process. They clarify who is responsible for shipping costs, insurance, and risk during transit. Familiarity with Incoterms helps buyers understand their obligations and mitigate risks related to international shipping, which is particularly relevant for buyers from diverse regions like Africa, South America, the Middle East, and Europe.
By comprehensively understanding these technical properties and trade terms, B2B buyers can make informed decisions that enhance their procurement processes for custom table legs.
Navigating Market Dynamics and Sourcing Trends in the table legs custom Sector
What Are the Key Market Dynamics and Trends Affecting Custom Table Legs?
The custom table legs sector is witnessing significant transformations driven by globalization, technological advancements, and shifting consumer preferences. International B2B buyers, especially from regions like Africa, South America, the Middle East, and Europe, should be aware of the following key trends.
Firstly, the rise of e-commerce platforms has revolutionized sourcing, enabling buyers to access a wider range of suppliers and manufacturers globally. This shift has facilitated competitive pricing and enhanced product variety, making it easier for businesses to find custom solutions that meet specific design and functional requirements. Additionally, the increasing demand for personalization in furniture design has led manufacturers to adopt flexible production methods, such as CNC machining and 3D printing, allowing for more tailored offerings.
Moreover, sustainability is becoming a crucial consideration in the sourcing process. Buyers are increasingly looking for suppliers that prioritize eco-friendly materials and practices, which not only align with global sustainability goals but also appeal to environmentally conscious consumers. As a result, there is a growing emphasis on local sourcing to reduce carbon footprints and support regional economies.
In summary, international B2B buyers should focus on leveraging technology for efficient sourcing while being mindful of sustainability trends to stay competitive in the custom table legs market.
How Is Sustainability Shaping Sourcing Decisions in the Custom Table Legs Sector?
Sustainability and ethical sourcing are no longer optional but essential components of successful B2B strategies in the custom table legs market. The environmental impact of manufacturing processes and materials used in furniture production is under scrutiny, prompting buyers to seek out suppliers committed to sustainability.
The importance of ethical supply chains cannot be overstated. Buyers are increasingly inclined to partner with manufacturers that demonstrate transparency in their sourcing practices, ensuring that materials are sourced responsibly and labor practices are fair. This commitment not only enhances brand reputation but also fosters trust among consumers who are more likely to support businesses that align with their values.
In terms of materials, the demand for ‘green’ certifications, such as FSC (Forest Stewardship Council) for wood products or certifications for recycled materials, is on the rise. Buyers should prioritize suppliers who offer certified sustainable options, as these products often come with a lower environmental impact and appeal to a growing segment of eco-conscious consumers. Additionally, incorporating recyclable and biodegradable materials into custom table legs can further bolster a company’s sustainability credentials.
By embracing sustainability, B2B buyers can not only meet regulatory requirements but also differentiate their offerings in a competitive marketplace.
What Is the Historical Context of Custom Table Legs in the B2B Sector?
The evolution of custom table legs has been shaped by various cultural, economic, and technological influences over the years. Historically, table legs were predominantly crafted from solid wood, reflecting the craftsmanship of local artisans. This artisanal approach allowed for unique designs but often resulted in longer lead times and limited customization options.
With the industrial revolution, mass production techniques emerged, allowing for greater consistency and lower costs. However, this shift also led to a decline in bespoke furniture, as standardized products became the norm. In recent years, there has been a resurgence in demand for custom solutions, driven by changing consumer preferences for unique and personalized designs.
Today’s manufacturers leverage advanced technologies like CAD (Computer-Aided Design) and CNC (Computer Numerical Control) machining to produce custom table legs with precision and speed. This blend of traditional craftsmanship and modern technology enables B2B buyers to access a wide range of options while maintaining high quality and design integrity. As the market continues to evolve, understanding this historical context can help buyers make informed decisions about their sourcing strategies.
Frequently Asked Questions (FAQs) for B2B Buyers of table legs custom
-
How do I determine the right specifications for custom table legs?
To determine the right specifications for custom table legs, start by assessing the intended use of the table—consider factors like weight capacity, height, and design aesthetics. Collaborate with your design team to establish the dimensions and materials that align with your brand’s vision. Additionally, research industry standards to ensure compliance and durability. Engaging with potential suppliers early in the design process can provide insights into feasible options and help refine your requirements. -
What is the best material for custom table legs in different markets?
The best material for custom table legs often depends on regional preferences and market trends. In Europe, metal and hardwood are popular for their durability and aesthetic appeal. In Africa and South America, locally sourced materials like bamboo or reclaimed wood are gaining traction due to sustainability concerns. In the Middle East, luxurious materials like marble or high-quality metals are favored. Understanding your target market’s preferences can guide material selection for optimal customer satisfaction. -
What are the typical minimum order quantities (MOQs) for custom table legs?
Minimum order quantities (MOQs) for custom table legs can vary significantly based on the supplier and production capabilities. Generally, MOQs can range from 50 to 500 units. Smaller suppliers may offer lower MOQs, while larger manufacturers might require higher quantities to justify production costs. Always clarify MOQs with potential suppliers early in negotiations to ensure that your order aligns with your business needs and cash flow. -
How can I vet suppliers for custom table legs effectively?
To vet suppliers for custom table legs, start by checking their credentials, including industry certifications and production capabilities. Request references from previous clients and review their portfolio to gauge the quality of their work. Conduct site visits or virtual tours to assess their manufacturing processes and quality control measures. Additionally, engaging in a small trial order can help evaluate their reliability and responsiveness before committing to larger orders. -
What payment terms should I negotiate when sourcing custom table legs?
When sourcing custom table legs, it’s essential to negotiate favorable payment terms to manage cash flow effectively. Common terms include a deposit (often 30% upfront) with the balance due upon delivery or before shipping. Consider discussing alternative options like letter of credit or escrow services for larger orders to mitigate risk. Ensure that the payment terms are clearly outlined in the contract to avoid misunderstandings later in the transaction. -
What quality assurance measures should I expect from suppliers of custom table legs?
Reputable suppliers should implement comprehensive quality assurance (QA) measures throughout the production process. Expect them to conduct inspections at various stages, including raw material sourcing, in-process checks, and final product assessments. Ask about their QA certifications, such as ISO standards, and request samples to assess craftsmanship. Establishing clear quality expectations upfront can help ensure that the final products meet your standards and reduce the risk of defects. -
How do I manage logistics and shipping for custom table legs internationally?
Managing logistics for international shipping of custom table legs requires careful planning. Start by selecting a reliable freight forwarder experienced in your target markets. Ensure that you understand the customs regulations and import duties for each region, particularly in Africa, South America, the Middle East, and Europe. Consider using Incoterms to clarify responsibilities for shipping and insurance. Additionally, factor in lead times for production and shipping to avoid delays in delivery. -
What are the common challenges faced when sourcing custom table legs internationally?
Common challenges when sourcing custom table legs internationally include language barriers, cultural differences, and varying quality standards. Time zone differences can also complicate communication. To mitigate these challenges, establish clear communication channels and consider hiring a local representative familiar with the market. Additionally, invest time in building relationships with suppliers to foster trust and ensure smoother transactions. Understanding local customs and business practices can significantly enhance your sourcing experience.
Important Disclaimer & Terms of Use
⚠️ Important Disclaimer
The information provided in this guide, including content regarding manufacturers, technical specifications, and market analysis, is for informational and educational purposes only. It does not constitute professional procurement advice, financial advice, or legal advice.
While we have made every effort to ensure the accuracy and timeliness of the information, we are not responsible for any errors, omissions, or outdated information. Market conditions, company details, and technical standards are subject to change.
B2B buyers must conduct their own independent and thorough due diligence before making any purchasing decisions. This includes contacting suppliers directly, verifying certifications, requesting samples, and seeking professional consultation. The risk of relying on any information in this guide is borne solely by the reader.
Strategic Sourcing Conclusion and Outlook for table legs custom
In today’s competitive marketplace, the strategic sourcing of custom table legs is crucial for international B2B buyers looking to enhance product offerings and optimize supply chains. By focusing on quality, sustainability, and local sourcing where feasible, businesses can not only improve their product aesthetics but also reduce costs and lead times.
What are the Key Takeaways for B2B Buyers?
Investing in reliable suppliers with proven track records in design and manufacturing can significantly elevate your product’s market appeal. Moreover, understanding regional preferences—whether in Africa, South America, the Middle East, or Europe—can guide your sourcing decisions and ensure that your products resonate with local markets.
How Can Strategic Sourcing Enhance Competitive Advantage?
Strategic sourcing is not merely a procurement process; it is a vital component of your overall business strategy. By leveraging data analytics, businesses can identify trends, predict market shifts, and make informed decisions that align with customer demands. This proactive approach positions companies to adapt quickly and effectively.
What Should International B2B Buyers Do Next?
As you look toward the future, consider diversifying your supplier base and exploring emerging markets for table leg production. Engaging with suppliers who prioritize innovation and sustainability will set your business apart. Embrace the opportunity to collaborate with manufacturers that align with your brand values and operational goals. Your next steps in strategic sourcing can pave the way for sustained growth and success in the custom furniture market.