Cut Costs with the Best Blood Pressure Cuff Manufacturer (2025)
Introduction: Navigating the Global Market for blood pressure cuff manufacturer
In the fast-evolving landscape of healthcare, sourcing reliable blood pressure cuffs presents a significant challenge for international B2B buyers. With a growing emphasis on patient comfort and accurate readings, manufacturers must navigate a complex market landscape that encompasses diverse product types, applications, and regulatory standards. This guide serves as a comprehensive resource, addressing the myriad factors involved in selecting the right blood pressure cuff manufacturer. From understanding the different types of cuffs available to evaluating supplier credentials and pricing structures, this guide is designed to empower decision-makers across Africa, South America, the Middle East, and Europe, including key markets like Kenya and France.
As you delve into this guide, you’ll discover actionable insights that will streamline your procurement process. Learn how to effectively vet suppliers to ensure compliance with international quality standards, and explore the latest innovations that enhance both functionality and user experience. Additionally, we will provide a detailed analysis of cost considerations, helping you to make informed purchasing decisions that align with your budgetary constraints. By the end of this guide, you will be equipped with the knowledge and tools necessary to navigate the global market for blood pressure cuff manufacturers confidently, enabling you to foster partnerships that enhance your healthcare offerings and ultimately improve patient outcomes.
Understanding blood pressure cuff manufacturer Types and Variations
Type Name | Key Distinguishing Features | Primary B2B Applications | Brief Pros & Cons for Buyers |
---|---|---|---|
Manual Blood Pressure Cuffs | Operated by hand; often less expensive | Clinics, small practices | Pros: Cost-effective; Cons: Requires skilled personnel for accurate readings. |
Digital Blood Pressure Cuffs | Automated readings; often portable | Home healthcare, telemedicine | Pros: Easy to use; Cons: Battery dependency can be a drawback. |
Pediatric Blood Pressure Cuffs | Smaller sizes for children; specialized design | Pediatric clinics, hospitals | Pros: Tailored for accuracy in children; Cons: Limited application for adults. |
Large Adult Blood Pressure Cuffs | Designed for larger arm sizes; adjustable | Hospitals, emergency services | Pros: Ensures accurate readings for larger patients; Cons: May be bulkier and harder to store. |
Ambulatory Blood Pressure Cuffs | Continuous monitoring; worn for 24 hours | Research, hypertension management | Pros: Provides comprehensive data; Cons: More expensive and complex to use. |
What Are the Key Characteristics of Manual Blood Pressure Cuffs?
Manual blood pressure cuffs, commonly known as sphygmomanometers, require a healthcare professional to operate. These cuffs are typically less expensive than their digital counterparts and are often used in clinics and small practices. When considering a manual cuff, B2B buyers should assess the skill level of their staff, as accurate readings depend on proper technique. These cuffs are generally reliable but may be less efficient in high-volume settings.
How Do Digital Blood Pressure Cuffs Enhance Efficiency?
Digital blood pressure cuffs are designed for ease of use, often featuring automatic inflation and deflation. This type is ideal for home healthcare and telemedicine applications, where patients may need to monitor their blood pressure independently. Buyers should consider the reliability of the device, battery life, and ease of reading the results. While these cuffs are user-friendly, they can be more expensive and reliant on battery power, which may not be suitable for all environments.
Why Are Pediatric Blood Pressure Cuffs Essential for Healthcare Providers?
Pediatric blood pressure cuffs are specifically designed for smaller arms, ensuring accurate readings for children. These cuffs are crucial in pediatric clinics and hospitals, where the need for precise measurements is paramount. B2B buyers should focus on the quality of materials and the cuff’s ability to provide consistent results. Although these cuffs serve a specific market, their necessity in specialized settings cannot be overstated.
What Should Buyers Know About Large Adult Blood Pressure Cuffs?
Large adult blood pressure cuffs accommodate patients with larger arm sizes, making them essential in hospitals and emergency services. These cuffs typically offer adjustable features to ensure a proper fit, which is vital for accurate readings. Buyers should evaluate the cuff’s design for comfort and ease of use, as well as its storage requirements. While they provide critical functionality, large cuffs can be bulkier and may require more space.
How Do Ambulatory Blood Pressure Cuffs Support Long-Term Monitoring?
Ambulatory blood pressure cuffs are designed for continuous monitoring over 24-hour periods, providing valuable data for research and hypertension management. These devices are particularly useful in clinical studies and for patients with chronic conditions. When purchasing ambulatory cuffs, B2B buyers should consider the complexity of operation and the associated costs. Despite their higher price point, the comprehensive data they provide can significantly enhance patient care and monitoring strategies.
Related Video: How to use blood pressure cuff correctly placement and size
Key Industrial Applications of blood pressure cuff manufacturer
Industry/Sector | Specific Application of Blood Pressure Cuff Manufacturer | Value/Benefit for the Business | Key Sourcing Considerations for this Application |
---|---|---|---|
Healthcare Facilities | Routine Patient Monitoring in Hospitals | Enhanced patient care and accurate health assessments | Compliance with medical regulations and standards |
Home Healthcare | At-home Blood Pressure Monitoring Devices | Improved patient adherence to treatment regimens | Product reliability and ease of use for non-professionals |
Fitness and Wellness | Blood Pressure Monitoring in Gyms | Personalized health tracking for clients | Compatibility with fitness devices and apps |
Research Institutions | Clinical Trials and Medical Research | High-quality data collection for studies | Customization options for specific research needs |
Emergency Services | Portable Blood Pressure Monitoring | Rapid assessment in critical situations | Durability and ease of transport in emergency scenarios |
How are Blood Pressure Cuffs Used in Healthcare Facilities?
In hospitals, blood pressure cuffs are essential tools for routine patient monitoring. They allow healthcare professionals to assess patient health accurately, which is vital for timely interventions. For B2B buyers in Africa and South America, sourcing cuffs that comply with local medical regulations is crucial. Additionally, ensuring that the cuffs are durable and easy to use can enhance patient care and workflow efficiency.
What is the Importance of Home Healthcare Monitoring?
Blood pressure cuffs designed for home healthcare are becoming increasingly popular as they empower patients to monitor their health independently. This application is particularly beneficial for managing chronic conditions such as hypertension. Buyers from the Middle East and Europe should prioritize cuffs that are user-friendly and provide consistent readings, as these factors significantly influence patient adherence to treatment plans. Reliability and accuracy are paramount to ensure that patients can manage their health effectively at home.
How is Blood Pressure Monitoring Integrated into Fitness and Wellness?
In the fitness sector, blood pressure cuffs are utilized to monitor clients’ cardiovascular health during workouts. Gyms and wellness centers can offer personalized health tracking, enhancing their service offerings and client satisfaction. B2B buyers in Europe should consider sourcing cuffs that integrate seamlessly with existing fitness technology, providing a comprehensive health overview. This integration can help fitness centers differentiate themselves in a competitive market.
Why are Blood Pressure Cuffs Critical in Research Institutions?
Research institutions rely on high-quality blood pressure cuffs for clinical trials and medical studies. Accurate data collection is essential for validating research outcomes, making the quality of the cuffs a priority. Buyers in South America and Africa should look for manufacturers that offer customization options to meet specific research requirements. This adaptability can significantly enhance the research process and ensure that studies yield reliable results.
What Role do Blood Pressure Cuffs Play in Emergency Services?
In emergency services, portable blood pressure cuffs are crucial for rapid assessments in critical situations. They need to be durable and easy to transport, allowing paramedics to make quick decisions that can save lives. For B2B buyers in the Middle East, sourcing high-quality, portable monitoring devices is essential. Ensuring that the cuffs are lightweight yet robust can facilitate effective emergency response, a critical factor in enhancing public health outcomes.
3 Common User Pain Points for ‘blood pressure cuff manufacturer’ & Their Solutions
Scenario 1: Inconsistent Quality Across Suppliers
The Problem:
B2B buyers often face challenges when sourcing blood pressure cuffs from multiple manufacturers. Inconsistent quality can lead to significant issues, including inaccurate readings, increased patient risk, and potential liability for healthcare providers. For instance, a hospital in Kenya may order cuffs from different suppliers to meet varying demand but discover that each batch has different calibration standards. This inconsistency not only affects the reliability of patient care but can also erode trust in the healthcare system.
The Solution:
To overcome this challenge, buyers should prioritize establishing long-term relationships with a select group of trusted manufacturers. Conduct thorough due diligence on potential suppliers, including their manufacturing processes, quality control measures, and certification standards (e.g., ISO 13485 for medical devices). Request samples and conduct independent testing to verify the accuracy and reliability of the cuffs before making large orders. Additionally, consider implementing a standardized quality assurance protocol within your procurement process to ensure all products meet specific clinical needs and regulatory requirements.
Scenario 2: Complex Regulatory Compliance Requirements
The Problem:
Navigating the complex landscape of regulatory compliance can be a daunting task for B2B buyers of medical devices, including blood pressure cuffs. Different regions, such as South America and Europe, have distinct regulations that manufacturers must adhere to, which can create confusion for buyers sourcing products across borders. For example, a company in Brazil may struggle to ensure that the cuffs they purchase comply with both ANVISA regulations and CE marking requirements, risking delays or even shipment rejections.
The Solution:
B2B buyers should invest time in understanding the regulatory frameworks governing medical devices in their respective regions. Partnering with manufacturers who have a proven track record of compliance can ease this burden. Buyers should also request documentation proving compliance with international standards and local regulations. Establishing a checklist for regulatory requirements can streamline the sourcing process, ensuring that all necessary certifications and documentation are acquired before purchase. Consulting with legal experts in medical device regulations can further enhance compliance efforts.
Scenario 3: Limited Customization Options for Diverse Needs
The Problem:
Healthcare providers often require blood pressure cuffs that cater to a diverse range of patients, including those with unique anatomical needs. A hospital in the Middle East may find that standard cuffs do not fit all patient sizes, leading to inaccurate measurements and suboptimal care. This lack of customization can frustrate healthcare professionals and diminish patient satisfaction, highlighting a critical pain point in sourcing.
The Solution:
To address the need for customization, B2B buyers should actively seek manufacturers that offer tailored solutions. When engaging with potential suppliers, inquire about their ability to provide a range of cuff sizes and styles, including pediatric, adult, and bariatric options. Furthermore, consider collaborating with manufacturers who are willing to engage in product development discussions, allowing for the design of specialized cuffs that meet specific clinical requirements. Establishing a feedback loop with healthcare professionals can also help inform manufacturers of emerging needs, ensuring the supply of cuffs that are both functional and comfortable for diverse patient populations.
Strategic Material Selection Guide for blood pressure cuff manufacturer
What Are the Key Materials Used in Blood Pressure Cuff Manufacturing?
When selecting materials for blood pressure cuffs, manufacturers must consider various factors that impact performance, durability, and compliance with international standards. Below are analyses of four common materials used in the production of blood pressure cuffs, focusing on their properties, advantages, disadvantages, and implications for international B2B buyers.
How Does PVC Perform as a Material for Blood Pressure Cuffs?
Polyvinyl Chloride (PVC) is a widely used material in blood pressure cuffs due to its cost-effectiveness and versatility. PVC exhibits good resistance to chemicals, making it suitable for various medical applications. Its temperature and pressure ratings are adequate for standard blood pressure measurements, ensuring reliable performance.
Pros: PVC is relatively inexpensive and easy to manufacture, which can lower production costs. Its durability and resistance to wear make it a suitable choice for cuffs that require frequent cleaning and sterilization.
Cons: However, PVC can be less flexible than other materials, which may affect comfort for the patient. Additionally, it is not biodegradable, raising environmental concerns.
Impact on Application: PVC cuffs are compatible with most standard blood pressure monitoring devices. However, buyers should ensure compliance with local regulations regarding the use of PVC in medical devices, particularly in regions with strict environmental laws.
What Advantages Does Nylon Offer for Blood Pressure Cuffs?
Nylon is another popular material for blood pressure cuffs, known for its strength and flexibility. This synthetic polymer can withstand higher pressures and temperatures than PVC, making it ideal for more demanding medical environments.
Pros: The high tensile strength of nylon provides excellent durability, and its flexibility enhances patient comfort during use. Nylon cuffs are also resistant to abrasion and tearing, which can be beneficial in high-volume clinical settings.
Cons: On the downside, nylon can be more expensive than PVC, which may impact cost-sensitive buyers. Additionally, nylon may require more complex manufacturing processes, potentially leading to longer lead times.
Impact on Application: Nylon is compatible with a wide range of blood pressure monitoring equipment. Buyers in regions like Europe and the Middle East should verify compliance with standards such as DIN and ISO, which may be more stringent than those in other areas.
Why Is Neoprene a Preferred Material for Blood Pressure Cuffs?
Neoprene is a synthetic rubber known for its excellent elasticity and resistance to temperature fluctuations. This material is often used in high-quality medical products, including blood pressure cuffs, due to its ability to provide a snug fit.
Pros: Neoprene cuffs offer superior comfort and flexibility, which can enhance patient experience. They are also resistant to moisture and chemicals, making them suitable for various medical environments.
Cons: The primary drawback of neoprene is its higher cost compared to PVC and nylon. Additionally, neoprene may not be as durable as nylon in high-stress applications.
Impact on Application: Neoprene cuffs are compatible with most blood pressure monitoring devices. However, buyers should consider the higher price point and ensure compliance with local medical device regulations, especially in regions with strict health standards.
What Role Does Cotton Play in Blood Pressure Cuff Manufacturing?
Cotton, often blended with synthetic materials, is used primarily for the inner lining of blood pressure cuffs. Its natural properties make it a comfortable choice for direct contact with the skin.
Pros: Cotton is breathable and hypoallergenic, reducing the risk of skin irritation for patients. It also provides a soft feel, enhancing overall comfort during use.
Cons: However, cotton is less durable than synthetic materials and may not withstand repeated sterilization processes. This can lead to increased replacement costs over time.
Impact on Application: Cotton-lined cuffs are suitable for use in environments where patient comfort is paramount. Buyers should ensure that the cotton used meets international standards for medical textiles, particularly in markets like Africa and South America where local sourcing may be a factor.
Summary Table of Material Selection for Blood Pressure Cuffs
Material | Typical Use Case for blood pressure cuff manufacturer | Key Advantage | Key Disadvantage/Limitation | Relative Cost (Low/Med/High) |
---|---|---|---|---|
PVC | Standard medical environments | Cost-effective and durable | Less flexible, environmental concerns | Low |
Nylon | High-pressure clinical settings | High durability and flexibility | More expensive, complex manufacturing | Medium |
Neoprene | High-quality medical applications | Superior comfort and elasticity | Higher cost, less durable under stress | High |
Cotton | Patient comfort applications | Breathable and hypoallergenic | Less durable, higher replacement costs | Medium |
This strategic material selection guide provides international B2B buyers with insights into the properties and implications of various materials used in blood pressure cuff manufacturing. By understanding these factors, buyers can make informed decisions that align with their operational needs and regulatory requirements.
In-depth Look: Manufacturing Processes and Quality Assurance for blood pressure cuff manufacturer
What Are the Main Stages of Manufacturing Blood Pressure Cuffs?
Manufacturing blood pressure cuffs involves several critical stages that ensure the product meets both functional and regulatory standards. The main stages of the manufacturing process include material preparation, forming, assembly, and finishing.
-
Material Preparation: The process begins with selecting appropriate materials, typically including durable, latex-free fabrics and medical-grade plastics. Manufacturers often source these materials from certified suppliers to ensure compliance with international standards. The preparation phase may involve cutting, dyeing, and treating materials to enhance performance characteristics such as durability and comfort.
-
Forming: Once the materials are prepared, they are shaped into the required form. Techniques such as die-cutting or thermoforming are commonly used to create the cuff’s structure. This stage is crucial as it directly impacts the cuff’s fit and functionality. Advanced manufacturers utilize computer-aided design (CAD) technology to optimize the shaping process and ensure precision.
-
Assembly: After forming, the components are assembled. This typically includes attaching the inflation bladder, tubing, and Velcro or snap fasteners. Automated assembly lines are often employed to enhance efficiency and ensure consistency. Skilled operators may perform quality checks during this stage to identify defects early in the process.
-
Finishing: The final stage involves applying any necessary coatings or treatments, such as antimicrobial finishes, and conducting final inspections. This phase ensures that the product not only meets aesthetic standards but also adheres to safety regulations.
How Is Quality Assurance Implemented in Blood Pressure Cuff Manufacturing?
Quality assurance (QA) is paramount in the manufacturing of medical devices, including blood pressure cuffs. Manufacturers typically implement a multi-faceted quality control (QC) system that adheres to both international and industry-specific standards.
-
International Standards: Compliance with ISO 9001 is essential for ensuring quality management systems are in place. ISO 13485, specifically for medical devices, is another critical standard that outlines the requirements for a comprehensive quality management system. Certifications under these standards reassure buyers of the manufacturer’s commitment to quality.
-
Industry-Specific Regulations: In Europe, products must meet CE marking requirements, which signify compliance with health, safety, and environmental protection standards. In the United States, the FDA regulates medical devices and requires manufacturers to follow Good Manufacturing Practices (GMP). Understanding these nuances is crucial for international buyers to ensure the products meet their regional regulations.
What Are the Key QC Checkpoints in Blood Pressure Cuff Production?
Quality control in the manufacturing of blood pressure cuffs involves several checkpoints throughout the production process, ensuring that every product meets the necessary specifications.
-
Incoming Quality Control (IQC): This initial checkpoint verifies the quality of raw materials upon arrival at the manufacturing facility. Materials are inspected for compliance with specified standards, and any non-conforming materials are rejected or returned.
-
In-Process Quality Control (IPQC): During the manufacturing process, regular inspections are performed at various stages. This includes checks during material forming, assembly, and finishing. Operators are trained to identify defects early, reducing waste and ensuring that only products meeting quality standards proceed to the next phase.
-
Final Quality Control (FQC): At the end of the production line, each blood pressure cuff undergoes a final inspection. This includes functionality tests, such as pressure calibration, and visual inspections for defects. Only products that pass these checks are packaged and shipped.
What Testing Methods Are Commonly Used in Blood Pressure Cuff Production?
To ensure the reliability and safety of blood pressure cuffs, manufacturers employ a variety of testing methods throughout the production process.
-
Performance Testing: This includes calibration tests to ensure that the cuffs provide accurate readings. Manufacturers may use pressure gauges to verify that the cuffs inflate and deflate within specified parameters.
-
Durability Testing: Cuffs undergo stress tests to evaluate their performance over time. This includes simulating repeated use to ensure the materials withstand wear and tear without compromising functionality.
-
Biocompatibility Testing: Given the medical nature of the product, materials must be tested for biocompatibility to ensure they do not cause adverse reactions when in contact with skin. This is particularly relevant for international buyers concerned about regulatory compliance in their respective regions.
How Can B2B Buyers Verify Supplier Quality Control Processes?
For international B2B buyers, particularly in regions like Africa, South America, the Middle East, and Europe, verifying a supplier’s quality control processes is crucial for ensuring product reliability.
-
Supplier Audits: Conducting on-site audits provides insights into the supplier’s manufacturing processes and quality control systems. This allows buyers to assess compliance with international standards and identify any potential risks.
-
Quality Assurance Reports: Requesting documentation such as quality assurance reports, test results, and compliance certificates can help buyers evaluate a supplier’s commitment to quality. These documents should detail the testing methods used and the outcomes of quality control inspections.
-
Third-Party Inspections: Engaging third-party inspection agencies can provide an unbiased assessment of a supplier’s quality control processes. These agencies often have expertise in medical device manufacturing and can identify areas for improvement.
What Are the Quality Control Nuances for International B2B Buyers?
B2B buyers from different regions must navigate various quality control nuances when sourcing blood pressure cuffs. Understanding these differences can help ensure compliance and mitigate risks.
-
Regulatory Requirements: Buyers in Europe must be familiar with CE marking and EU regulations, while those in the Middle East may need to adhere to local health authority guidelines. In Africa, where regulations can vary widely, understanding the local context is essential.
-
Cultural Considerations: Different regions may have varying expectations regarding quality and customer service. Building strong relationships with suppliers and understanding their practices can facilitate smoother transactions and better communication.
-
Logistical Challenges: Buyers should also consider the logistical aspects of importing medical devices, including customs regulations and import duties. Engaging with suppliers who have experience in international shipping can help streamline the process.
In conclusion, understanding the manufacturing processes and quality assurance measures in blood pressure cuff production is essential for international B2B buyers. By focusing on these aspects, buyers can make informed decisions, ensuring they procure high-quality medical devices that meet regulatory standards in their respective regions.
Practical Sourcing Guide: A Step-by-Step Checklist for ‘blood pressure cuff manufacturer’
Introduction
In the competitive landscape of medical device procurement, sourcing a reliable blood pressure cuff manufacturer is critical for ensuring quality and compliance. This checklist serves as a practical guide for international B2B buyers, particularly those in Africa, South America, the Middle East, and Europe. By following these steps, you can streamline your sourcing process and make informed decisions that align with your business needs.
Step 1: Define Your Technical Specifications
Before initiating contact with manufacturers, clearly outline the technical specifications required for your blood pressure cuffs. This includes dimensions, materials, measurement accuracy, and compliance with international standards such as ISO and CE marking. A well-defined specification will help you communicate effectively with potential suppliers and ensure that the products meet your quality expectations.
Step 2: Conduct Market Research
Understanding the market landscape is essential for informed sourcing. Research various manufacturers’ reputations, market share, and customer feedback. Utilize platforms like LinkedIn, industry forums, and trade shows to gather insights about potential suppliers. This will help you identify reputable manufacturers who have a proven track record in delivering quality products.
Step 3: Evaluate Potential Suppliers
Before committing to a supplier, conduct a thorough evaluation. Request detailed company profiles, case studies, and references from existing clients, particularly those in your industry. Look for evidence of successful partnerships and customer satisfaction, as this will provide insight into the supplier’s reliability and service quality.
Step 4: Verify Supplier Certifications
Ensure that your chosen manufacturers possess the necessary certifications and compliance with international standards. This includes quality management system certifications (like ISO 13485) and product-specific certifications (like FDA approval for certain markets). Verifying these credentials minimizes the risk of sourcing substandard products and ensures compliance with regulatory requirements.
Step 5: Request Samples for Testing
Before placing a bulk order, request samples of the blood pressure cuffs for testing. This step is crucial to evaluate the product’s quality, functionality, and user experience. Conduct thorough testing in your operational environment to ensure that the cuffs meet your specifications and performance expectations.
Step 6: Negotiate Terms and Conditions
Once you have selected a supplier, negotiate the terms and conditions of your procurement agreement. Discuss pricing, payment terms, delivery schedules, and warranty provisions. Clear and mutually agreed-upon terms will help prevent misunderstandings and ensure a smooth transaction process.
Step 7: Establish Communication Channels
Effective communication is key to successful sourcing. Establish clear channels of communication with your chosen manufacturer to facilitate ongoing dialogue regarding order status, product updates, and any potential issues that may arise. Regular communication helps build a strong partnership and ensures that both parties are aligned throughout the procurement process.
By following this checklist, international B2B buyers can navigate the complexities of sourcing blood pressure cuffs, ensuring they partner with manufacturers that meet their specific needs and standards.
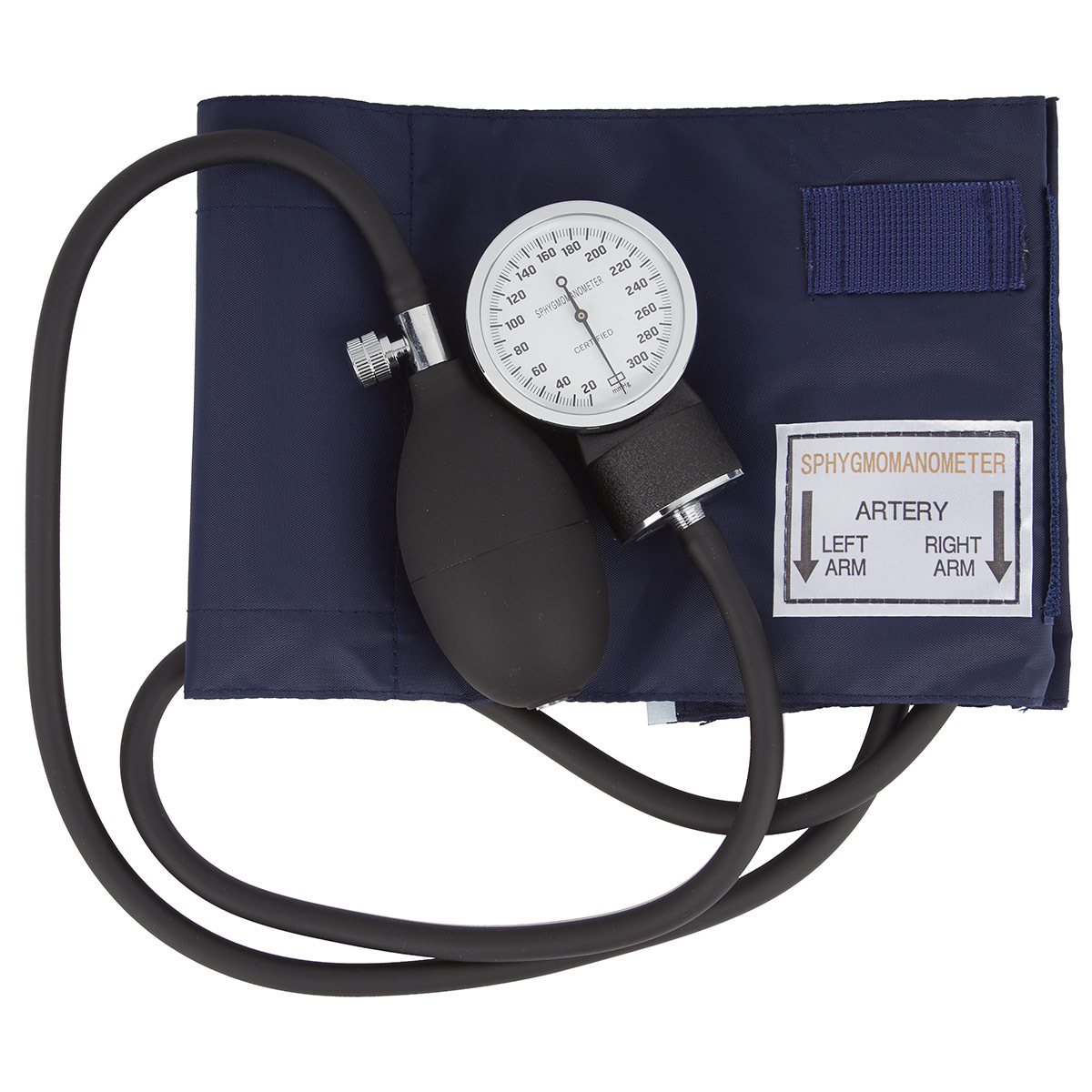
A stock image related to blood pressure cuff manufacturer.
Comprehensive Cost and Pricing Analysis for blood pressure cuff manufacturer Sourcing
What Are the Key Cost Components in Blood Pressure Cuff Manufacturing?
When sourcing blood pressure cuffs, understanding the cost structure is crucial for international B2B buyers. The primary cost components include:
-
Materials: The choice of materials significantly influences the cost. Common materials include PVC, nylon, and cotton for the cuff, as well as rubber for the inflation bulb. Sourcing high-quality materials may incur higher costs but can lead to better product performance and durability.
-
Labor: Labor costs can vary greatly depending on the manufacturing location. For instance, countries in South America and Africa may offer lower labor costs compared to Europe, but this can affect quality and lead times.
-
Manufacturing Overhead: This includes utilities, rent, and equipment depreciation. Manufacturers with advanced facilities may have higher overhead costs, but they often yield better quality control and efficiency.
-
Tooling: Custom tooling may be required for specific designs or sizes. These initial costs can be substantial, but they often lead to economies of scale in larger production runs.
-
Quality Control (QC): Ensuring compliance with international standards (such as ISO or CE marking) involves additional QC costs. However, rigorous testing can prevent costly recalls and enhance market reputation.
-
Logistics: Transportation and handling fees can add significantly to the total cost, especially for international shipments. It’s essential to consider both shipping costs and potential tariffs.
-
Margin: Manufacturers typically add a profit margin to cover their risks and ensure sustainability. Understanding the average margin in your target region can aid in negotiating prices.
How Do Price Influencers Affect Blood Pressure Cuff Sourcing?
Several factors can influence the pricing of blood pressure cuffs:
-
Volume/MOQ (Minimum Order Quantity): Larger orders often attract discounts. Buyers should assess their needs carefully to maximize savings while avoiding overstock.
-
Specifications and Customization: Customized cuffs tailored to specific medical requirements or branding can increase costs. Buyers should weigh the benefits of customization against the potential price increase.
-
Material Quality and Certifications: Higher quality materials and certifications can drive up costs but are often necessary for compliance with regulatory standards in various markets.
-
Supplier Factors: The reputation and reliability of the supplier can affect pricing. Established suppliers may charge a premium for their experience and proven track record.
-
Incoterms: The terms of trade can impact overall costs. Understanding whether the price includes shipping, insurance, and duties is vital for accurate budgeting.
What Buyer Tips Can Enhance Cost-Efficiency?
International B2B buyers should consider the following strategies to enhance cost-efficiency when sourcing blood pressure cuffs:
-
Negotiate Effectively: Leverage your purchasing power by negotiating terms based on volume and long-term contracts. Establishing a good relationship with suppliers can also lead to more favorable pricing.
-
Evaluate Total Cost of Ownership (TCO): Beyond the purchase price, consider maintenance, warranty, and potential replacement costs. A cheaper product may incur higher TCO if it requires more frequent replacements or repairs.
-
Understand Pricing Nuances for International Markets: Regional pricing strategies can vary. For instance, buyers in Kenya may face different import duties than those in France. Being aware of these nuances can prevent unexpected costs.
-
Conduct Market Research: Regularly assess the market for trends in pricing and material costs. This knowledge can empower buyers to make informed decisions and time their purchases effectively.
-
Consider Local Sourcing Options: Depending on the region, local suppliers may provide cost advantages and reduced shipping times. This can also aid in compliance with local regulations.
Conclusion
Navigating the cost structure and pricing landscape for blood pressure cuff manufacturing requires a strategic approach. By understanding the key cost components, price influencers, and implementing effective negotiation and sourcing strategies, international B2B buyers can optimize their procurement processes, particularly in diverse markets across Africa, South America, the Middle East, and Europe. Always remember that prices can fluctuate based on various factors, so it’s wise to seek updated quotes and conduct thorough due diligence before finalizing contracts.
Alternatives Analysis: Comparing blood pressure cuff manufacturer With Other Solutions
Understanding Alternatives to Blood Pressure Cuff Manufacturers
When it comes to measuring blood pressure, businesses have various options beyond traditional blood pressure cuffs. Understanding these alternatives is crucial for international B2B buyers, particularly in regions like Africa, South America, the Middle East, and Europe. This section provides a comparative analysis of blood pressure cuffs against alternative solutions, helping buyers make informed decisions based on performance, cost, ease of implementation, maintenance, and best use cases.
Comparison Aspect | Blood Pressure Cuff Manufacturer | Digital Blood Pressure Monitor | Wearable Blood Pressure Monitor |
---|---|---|---|
Performance | High accuracy with manual inflation | High accuracy with automatic inflation | Variable accuracy depending on model |
Cost | Moderate initial investment | Varies (generally lower) | Higher initial cost but may save on long-term monitoring |
Ease of Implementation | Requires trained personnel | Easy to use, minimal training needed | User-friendly, integration with mobile apps available |
Maintenance | Requires periodic calibration | Low maintenance | Requires regular charging and software updates |
Best Use Case | Clinical settings, hospital use | Home monitoring, outpatient settings | Continuous monitoring for chronic conditions |
What are the Advantages and Disadvantages of Digital Blood Pressure Monitors?
Digital blood pressure monitors offer a streamlined approach to measuring blood pressure. They are user-friendly, with many models allowing for automatic inflation and deflation, which reduces the risk of human error. The ease of use makes them suitable for outpatient settings and home monitoring, especially for patients managing hypertension. However, the cost can vary significantly, and some models may not provide the same level of accuracy as traditional cuffs, particularly in patients with arrhythmias.
How Do Wearable Blood Pressure Monitors Compare?
Wearable blood pressure monitors represent an innovative solution for continuous monitoring of blood pressure. These devices are often integrated with mobile applications, allowing users to track their blood pressure over time and share data with healthcare providers. They are particularly beneficial for patients with chronic conditions who need to monitor their blood pressure regularly. However, the initial investment can be higher, and the accuracy may vary significantly between models. Additionally, they require regular charging and updates, which can be a drawback for some users.
Conclusion: How to Choose the Right Blood Pressure Monitoring Solution?
Selecting the right blood pressure monitoring solution depends on various factors, including the specific needs of the healthcare facility, budget constraints, and the patient population being served. For clinical environments where precision is paramount, traditional blood pressure cuffs may remain the gold standard. In contrast, digital monitors may be more suitable for home use due to their ease of use and lower cost. Wearable technology offers advanced monitoring capabilities for patients requiring ongoing management. By carefully assessing these alternatives based on performance, cost, and application, B2B buyers can make strategic choices that align with their operational goals and enhance patient care.
Essential Technical Properties and Trade Terminology for blood pressure cuff manufacturer
What Are the Essential Technical Properties of Blood Pressure Cuffs?
When sourcing blood pressure cuffs, understanding the critical technical properties can significantly impact quality, performance, and patient safety. Here are key specifications to consider:
1. Material Grade
Blood pressure cuffs are typically made from materials like nylon, polyester, or rubber. The material grade affects durability, flexibility, and comfort for the patient. High-quality materials ensure that the cuff can withstand repeated use and cleaning, making it essential for manufacturers to source durable and safe materials compliant with international health standards.
2. Cuff Size and Range
Cuff size is crucial for accurate blood pressure readings. They come in various sizes (small, medium, large) to accommodate different arm circumferences. Proper sizing ensures that the cuff fits snugly without being too tight, which can lead to inaccurate readings. Manufacturers should provide a range of sizes to cater to diverse populations, especially in regions with varying body types.
3. Tolerance Levels
Tolerance refers to the acceptable deviation in measurements during manufacturing. For blood pressure cuffs, maintaining strict tolerance levels ensures consistency in pressure application, which is vital for accurate readings. Buyers should inquire about the manufacturer’s quality control processes to ensure that the cuffs meet these tolerance standards.
4. Pressure Calibration
Calibration is essential for ensuring that the cuff accurately reflects the blood pressure. Manufacturers should provide information on how their cuffs are calibrated and whether they adhere to recognized standards, such as those set by the American National Standards Institute (ANSI). Proper calibration minimizes discrepancies in readings, which can affect patient diagnosis and treatment.
5. Latex-Free Options
Many users may have latex allergies, making it essential for manufacturers to offer latex-free cuffs. This specification not only broadens the potential market but also aligns with health regulations in various regions. Buyers should confirm the availability of latex-free options to ensure patient safety.
What Trade Terminology Should International B2B Buyers Know?
Understanding industry jargon is vital for effective communication and negotiation in the procurement process. Here are common trade terms relevant to blood pressure cuff manufacturing:
1. OEM (Original Equipment Manufacturer)
OEM refers to a company that produces parts or equipment that may be marketed by another manufacturer. For blood pressure cuffs, an OEM might create the cuffs for a brand that sells them under its name. Understanding OEM relationships can help buyers assess quality and reliability.
2. MOQ (Minimum Order Quantity)
MOQ is the smallest number of units a supplier is willing to sell. This term is particularly important for international buyers as it affects inventory management and cash flow. Knowing the MOQ helps in planning purchases and understanding the financial commitment involved in sourcing products.
3. RFQ (Request for Quotation)
An RFQ is a document sent to suppliers asking for price quotes for specific products. For blood pressure cuffs, sending an RFQ allows buyers to compare prices, terms, and conditions across different manufacturers, enabling informed decision-making.
4. Incoterms (International Commercial Terms)
Incoterms define the responsibilities of buyers and sellers regarding shipping, insurance, and tariffs. Familiarity with these terms is crucial for international transactions to avoid misunderstandings and ensure compliance with trade regulations. For instance, understanding terms like FOB (Free on Board) or CIF (Cost, Insurance, and Freight) can influence shipping costs and logistics.
5. Lead Time
Lead time refers to the time taken from placing an order to receiving the goods. For medical supplies like blood pressure cuffs, knowing the lead time is critical for inventory management and ensuring timely availability in healthcare settings. Buyers should discuss lead times with manufacturers to align with their operational needs.
Conclusion
In summary, grasping the essential technical properties and trade terminology related to blood pressure cuffs is crucial for international B2B buyers. By understanding these specifications and terms, decision-makers can make informed purchasing choices that enhance patient care and optimize operational efficiency.
Navigating Market Dynamics and Sourcing Trends in the blood pressure cuff manufacturer Sector
What Are the Current Market Dynamics in the Blood Pressure Cuff Manufacturer Sector?
The blood pressure cuff manufacturing sector is experiencing significant transformation driven by technological advancements, evolving regulatory landscapes, and heightened global health awareness. One of the primary global drivers is the increasing prevalence of hypertension, which has led to a surge in demand for accurate and reliable blood pressure monitoring devices. Additionally, the COVID-19 pandemic has accelerated the adoption of telehealth services, prompting manufacturers to innovate and develop smart blood pressure cuffs that can integrate with mobile applications for remote patient monitoring.
International B2B buyers, particularly from regions like Africa, South America, the Middle East, and Europe, must stay attuned to emerging sourcing trends such as the shift towards digital procurement platforms. These platforms enhance transparency and efficiency, enabling buyers to connect directly with manufacturers. Moreover, the trend of regional sourcing is gaining momentum, as companies look to minimize supply chain disruptions by partnering with local or regional manufacturers. This is particularly relevant for buyers in Africa and South America, where local production capabilities are expanding.
Furthermore, there is a noticeable shift towards customizable solutions. B2B buyers are increasingly seeking manufacturers that can provide tailored products to meet specific health needs, thereby enhancing patient outcomes. As a result, understanding the unique health challenges within different regions will be crucial for international buyers to make informed sourcing decisions.
How Is Sustainability Shaping the Blood Pressure Cuff Manufacturing Landscape?
Sustainability and ethical sourcing have become paramount concerns for B2B buyers in the blood pressure cuff manufacturing sector. Environmental impacts associated with manufacturing processes, such as waste generation and carbon emissions, are under scrutiny. Buyers are increasingly demanding transparency in the supply chain to ensure that manufacturers adhere to sustainable practices.
The importance of ethical supply chains cannot be overstated. Buyers from Europe, for instance, are often bound by stringent regulations regarding sustainable sourcing, which necessitate the use of ‘green’ materials and certifications. Manufacturers that utilize eco-friendly materials, such as biodegradable or recyclable components, not only reduce their environmental footprint but also appeal to ethically conscious buyers.
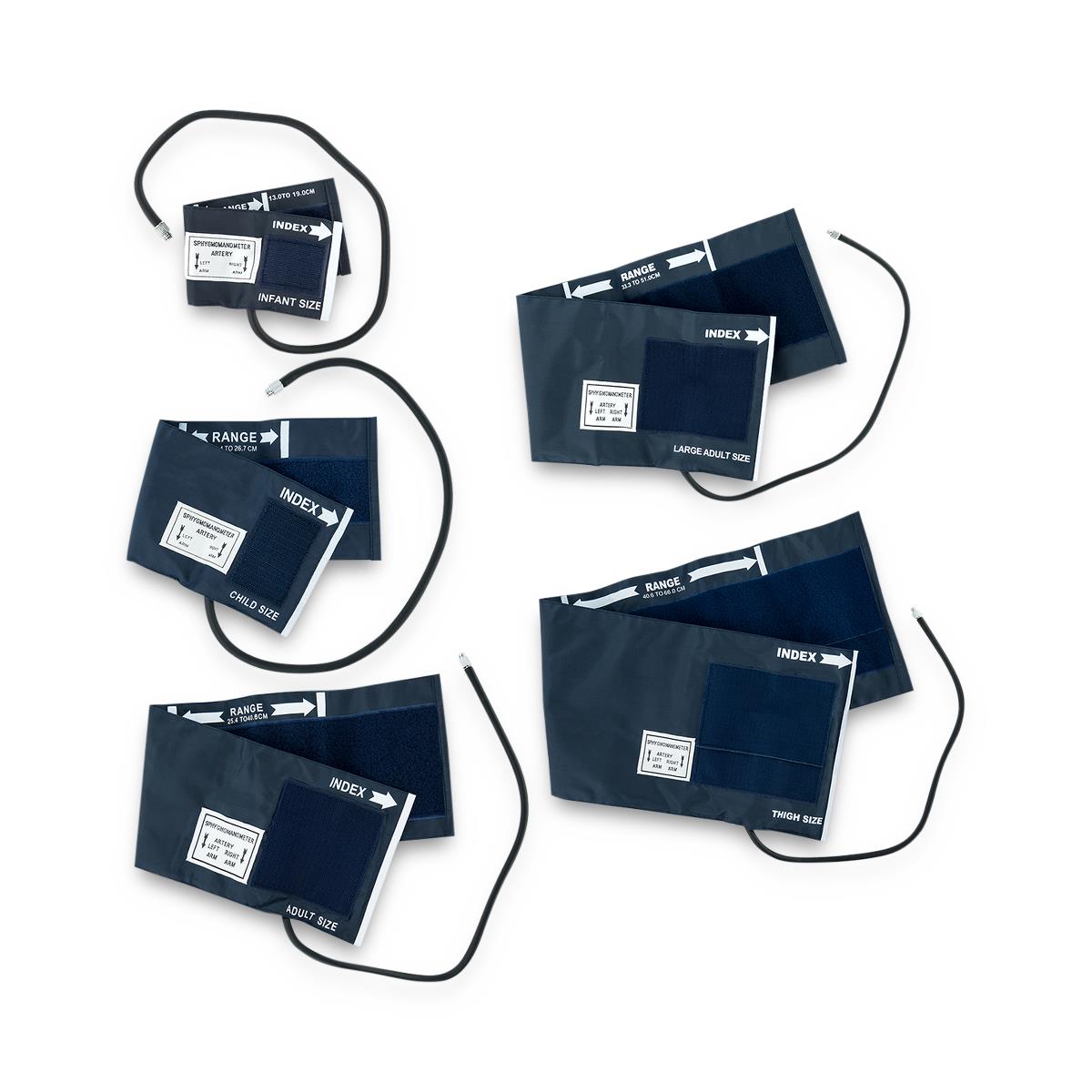
A stock image related to blood pressure cuff manufacturer.
Certifications such as ISO 14001, which focuses on effective environmental management systems, and the Global Organic Textile Standard (GOTS) for organic materials are gaining traction. Buyers should prioritize manufacturers with these certifications, as they demonstrate a commitment to sustainability. Additionally, engaging with suppliers who actively participate in corporate social responsibility initiatives can enhance brand reputation and customer loyalty.
How Has the Blood Pressure Cuff Manufacturer Sector Evolved Over Time?
The blood pressure cuff manufacturing sector has evolved significantly over the past few decades. Initially dominated by traditional manual devices, the sector has embraced technological advancements, leading to the development of automatic and digital cuffs. This evolution has been propelled by the need for greater accuracy and ease of use, particularly in home healthcare settings.
In the early 2000s, the introduction of wireless technology marked a pivotal shift. This innovation allowed for real-time data transmission to healthcare providers, facilitating better patient management. As awareness of hypertension’s global impact grew, manufacturers began to focus on creating user-friendly products that cater to a broader demographic, including elderly patients and those in remote areas.
Today, the integration of artificial intelligence and machine learning in blood pressure monitoring devices is setting new benchmarks for accuracy and functionality. For international B2B buyers, understanding this evolution is essential for identifying reliable partners who can meet current and future market demands. By aligning with manufacturers that are at the forefront of these advancements, buyers can ensure they are sourcing high-quality, innovative products that enhance healthcare delivery.
Frequently Asked Questions (FAQs) for B2B Buyers of blood pressure cuff manufacturer
-
How do I choose the right blood pressure cuff manufacturer for my business needs?
Selecting the right blood pressure cuff manufacturer involves assessing their product quality, compliance with medical standards, and manufacturing capabilities. Look for manufacturers with ISO certification and experience in producing medical devices. Additionally, evaluate their ability to customize products to meet your specifications and their history of timely delivery. Engaging with references or existing clients can provide insights into their reliability and service quality. -
What are the key factors to consider when sourcing blood pressure cuffs internationally?
When sourcing blood pressure cuffs internationally, consider factors such as regulatory compliance, quality assurance processes, and the manufacturer’s reputation. Investigate the manufacturer’s certifications, such as CE marking for Europe or FDA approval for the U.S. market. Understand the import/export regulations in your country, including tariffs and taxes, to ensure a smooth transaction. Lastly, consider logistics and shipping times, especially if you are sourcing from regions with longer delivery periods. -
What is the minimum order quantity (MOQ) for blood pressure cuffs from manufacturers?
The minimum order quantity (MOQ) for blood pressure cuffs can vary significantly among manufacturers, ranging from a few hundred to several thousand units. This often depends on the manufacturer’s production capabilities and the complexity of the product. When negotiating with suppliers, inquire about their flexibility regarding MOQs, especially if you are a smaller business or testing a new product line. Some manufacturers may offer lower MOQs for first-time buyers or trial orders. -
How can I ensure the quality of blood pressure cuffs before purchasing?
To ensure the quality of blood pressure cuffs, request samples before placing a bulk order. Evaluate the materials, design, and functionality of the cuffs. Additionally, inquire about the manufacturer’s quality control processes, including testing and compliance with international medical standards. Certifications such as ISO 13485 can indicate a commitment to quality management systems in the medical device sector. Consider conducting an on-site audit if feasible, or hiring a third-party inspection service for added assurance. -
What payment terms should I expect when dealing with blood pressure cuff manufacturers?
Payment terms can vary widely, but most manufacturers require a deposit (typically 30-50%) upfront with the balance due before shipping. Some manufacturers may offer net terms (e.g., 30 or 60 days) for established clients. It’s advisable to negotiate terms that align with your cash flow and business needs. Always use secure payment methods, and consider establishing an escrow service for larger transactions to mitigate risks. -
What customization options are available for blood pressure cuffs?
Many blood pressure cuff manufacturers offer customization options, including size, color, material, and branding. You can request specific features, such as adjustable cuffs for different arm sizes or unique designs for marketing purposes. Discuss your customization needs early in the negotiation process to ensure the manufacturer can meet your requirements. Also, inquire about lead times for custom orders, as these may differ from standard product offerings. -
How do I assess the reliability of a blood pressure cuff supplier?
Assessing a supplier’s reliability involves researching their business history, customer reviews, and industry reputation. Check for certifications and compliance with relevant standards, as these indicate a commitment to quality and safety. Engage in direct conversations with the manufacturer to evaluate their communication skills and responsiveness. Additionally, consider requesting references from other B2B clients to gain insights into their experience and satisfaction with the supplier’s service and product quality. -
What logistics considerations should I keep in mind when importing blood pressure cuffs?
Logistics play a crucial role in the importation of blood pressure cuffs. Be aware of shipping options, costs, and estimated delivery times, which can vary based on the manufacturer’s location and your destination. Understand the customs clearance process in your country, including any required documentation and duties. Collaborating with a freight forwarder can help streamline the logistics process and ensure compliance with international shipping regulations, thereby reducing potential delays.
Important Disclaimer & Terms of Use
⚠️ Important Disclaimer
The information provided in this guide, including content regarding manufacturers, technical specifications, and market analysis, is for informational and educational purposes only. It does not constitute professional procurement advice, financial advice, or legal advice.
While we have made every effort to ensure the accuracy and timeliness of the information, we are not responsible for any errors, omissions, or outdated information. Market conditions, company details, and technical standards are subject to change.
B2B buyers must conduct their own independent and thorough due diligence before making any purchasing decisions. This includes contacting suppliers directly, verifying certifications, requesting samples, and seeking professional consultation. The risk of relying on any information in this guide is borne solely by the reader.
Strategic Sourcing Conclusion and Outlook for blood pressure cuff manufacturer
As the global healthcare landscape continues to evolve, the strategic sourcing of blood pressure cuffs presents significant opportunities for international B2B buyers, particularly in regions like Africa, South America, the Middle East, and Europe. Engaging with reliable manufacturers ensures access to high-quality products that meet regulatory standards while also accommodating local market needs. Key takeaways include the importance of evaluating supplier capabilities, understanding the nuances of regional compliance, and leveraging technological advancements in manufacturing processes.
How can international buyers effectively optimize their sourcing strategies? By fostering strong relationships with manufacturers, buyers can negotiate favorable terms, ensure timely deliveries, and remain agile in response to market changes. Additionally, investing in partnerships that prioritize sustainability and innovation will not only enhance product offerings but also align with global health initiatives.
Looking ahead, the demand for reliable blood pressure monitoring solutions is expected to rise, driven by an increasing focus on preventive healthcare. International buyers are encouraged to take proactive steps in their sourcing strategies, exploring new partnerships that offer advanced technology and support. By doing so, they will position themselves as leaders in the healthcare market, equipped to meet the growing demands of their regions.