Discover Top CNC Machine China Suppliers: Save Costs (2025)
Introduction: Navigating the Global Market for cnc machine china
When it comes to sourcing CNC machines from China, international B2B buyers face a myriad of challenges, including quality assurance, supplier reliability, and navigating complex logistics. Understanding how to effectively source CNC machines from China is crucial for manufacturers and businesses looking to optimize their production processes. This guide offers a comprehensive overview tailored specifically for B2B buyers from regions such as Africa, South America, the Middle East, and Europe, including countries like Spain and Argentina.
Throughout this guide, you will explore various types of CNC machines available in the Chinese market, their diverse applications across industries, and essential strategies for supplier vetting. We will also delve into cost considerations, providing insights on pricing structures and potential hidden costs that may arise during the procurement process. By offering actionable insights and practical recommendations, this guide empowers international buyers to make informed purchasing decisions that align with their operational needs and budget constraints.
Whether you are looking to enhance your manufacturing capabilities or seeking to establish long-term partnerships with reliable suppliers, understanding the intricacies of sourcing CNC machines from China is paramount. This guide aims to equip you with the knowledge and tools necessary to navigate the global market effectively, ensuring that your investment yields maximum returns and contributes to your business’s growth and success.
Understanding cnc machine china Types and Variations
Type Name | Key Distinguishing Features | Primary B2B Applications | Brief Pros & Cons for Buyers |
---|---|---|---|
CNC Milling Machine | Utilizes rotary cutters for material removal | Aerospace, automotive, mold making | Pros: High precision; Cons: Higher initial cost |
CNC Lathe Machine | Rotates workpiece against stationary cutting tool | Metalworking, woodworking | Pros: Efficient for round shapes; Cons: Limited to cylindrical parts |
CNC Plasma Cutter | Uses plasma to cut through metal sheets | Construction, fabrication | Pros: Fast cutting speed; Cons: Limited to conductive materials |
CNC Router | Uses a rotating bit to carve materials | Sign making, woodworking | Pros: Versatile for various materials; Cons: Less precision than milling |
CNC Laser Cutter | Employs laser technology for cutting and engraving | Electronics, jewelry, textiles | Pros: High precision and clean cuts; Cons: Expensive maintenance |
What are the Characteristics and Suitability of CNC Milling Machines?
CNC milling machines are characterized by their ability to utilize rotary cutters for precise material removal, making them ideal for intricate designs and complex geometries. They are suitable for industries such as aerospace and automotive, where precision is paramount. When considering a CNC milling machine, B2B buyers should evaluate the machine’s speed, rigidity, and the range of materials it can handle, as these factors significantly affect production efficiency and output quality.
How Do CNC Lathe Machines Work and What are Their Key Applications?
CNC lathe machines are designed to rotate the workpiece while the cutting tool remains stationary, allowing for the efficient machining of cylindrical parts. These machines are widely used in metalworking and woodworking industries. B2B buyers should consider the machine’s capacity in terms of diameter and length of the workpiece, as well as the types of materials it can effectively process. Additionally, understanding the machine’s tooling options can enhance versatility and productivity.
What Advantages Do CNC Plasma Cutters Offer for B2B Buyers?
CNC plasma cutters are known for their high-speed cutting capabilities, utilizing plasma technology to slice through metal sheets. They are particularly advantageous in construction and fabrication sectors. B2B buyers should weigh the benefits of fast processing times against the limitations of working only with conductive materials. Furthermore, considering the machine’s operational costs, including consumables and power usage, can help buyers make informed purchasing decisions.
Why Choose a CNC Router for Diverse Material Applications?
CNC routers are versatile machines that can carve, engrave, and cut a variety of materials, including wood, plastics, and composites. They are commonly used in sign making and woodworking industries. B2B buyers should assess the router’s spindle speed and cutting area, as these factors influence the types of projects that can be undertaken. Additionally, understanding the software compatibility and ease of use can enhance operational efficiency and workflow.
What are the Benefits and Considerations for CNC Laser Cutters?
CNC laser cutters utilize advanced laser technology to achieve high precision and clean cuts, making them suitable for applications in electronics, jewelry, and textiles. B2B buyers should consider the initial investment and maintenance costs, as these machines can be more expensive than other types. It’s also essential to evaluate the machine’s cutting speed, thickness capabilities, and the types of materials it can process, ensuring it aligns with specific production needs.
Key Industrial Applications of cnc machine china
Industry/Sector | Specific Application of CNC Machine China | Value/Benefit for the Business | Key Sourcing Considerations for this Application |
---|---|---|---|
Aerospace | Precision Component Manufacturing | Enhanced accuracy and reduced waste | Certifications (e.g., ISO 9001), lead times |
Automotive | Tooling and Parts Production | Improved production efficiency and lower costs | Material compatibility, after-sales support |
Electronics | PCB and Enclosure Fabrication | High-quality finishes and complex designs | Technology specifications, rapid prototyping options |
Medical Devices | Custom Implant and Instrument Production | Tailored solutions for unique medical needs | Regulatory compliance (FDA, CE), quality assurance |
Furniture Manufacturing | Custom Design and Mass Production of Furniture Pieces | Increased design flexibility and market responsiveness | Material sourcing, delivery timelines |
How is CNC Machine China Used in Aerospace Manufacturing?
CNC machines are essential in the aerospace industry for manufacturing precision components such as turbine blades and fuselage parts. These machines solve the problem of achieving the high tolerances required for safety and performance. International buyers must consider certifications like ISO 9001 when sourcing CNC machines for aerospace applications, as these ensure compliance with stringent industry standards. Additionally, lead times for delivery can significantly impact production schedules, making timely sourcing crucial.
What Role Does CNC Machine China Play in Automotive Production?
In the automotive sector, CNC machines are predominantly used for tooling and parts production, including engine components and chassis parts. The primary benefits include enhanced production efficiency and reduced costs through automation and precision machining. Buyers from regions like South America and Africa should focus on material compatibility and after-sales support when sourcing CNC machines, as these factors can significantly affect maintenance and operational efficiency.
How is CNC Machine China Transforming Electronics Manufacturing?
CNC machines are widely utilized in the electronics industry for fabricating printed circuit boards (PCBs) and enclosures. They enable the production of high-quality finishes and complex designs, which are vital in a competitive market. International B2B buyers should prioritize technology specifications and rapid prototyping options when sourcing these machines, as advancements in technology can lead to significant improvements in product development cycles.
What Are the Applications of CNC Machine China in Medical Device Production?
In the medical sector, CNC machines are used to produce custom implants and surgical instruments tailored to specific patient needs. This application addresses the challenge of meeting unique medical requirements while maintaining high standards of safety and quality. Buyers must ensure that the CNC machines comply with regulatory standards such as FDA and CE certifications, as well as establish robust quality assurance processes to mitigate risks associated with medical manufacturing.
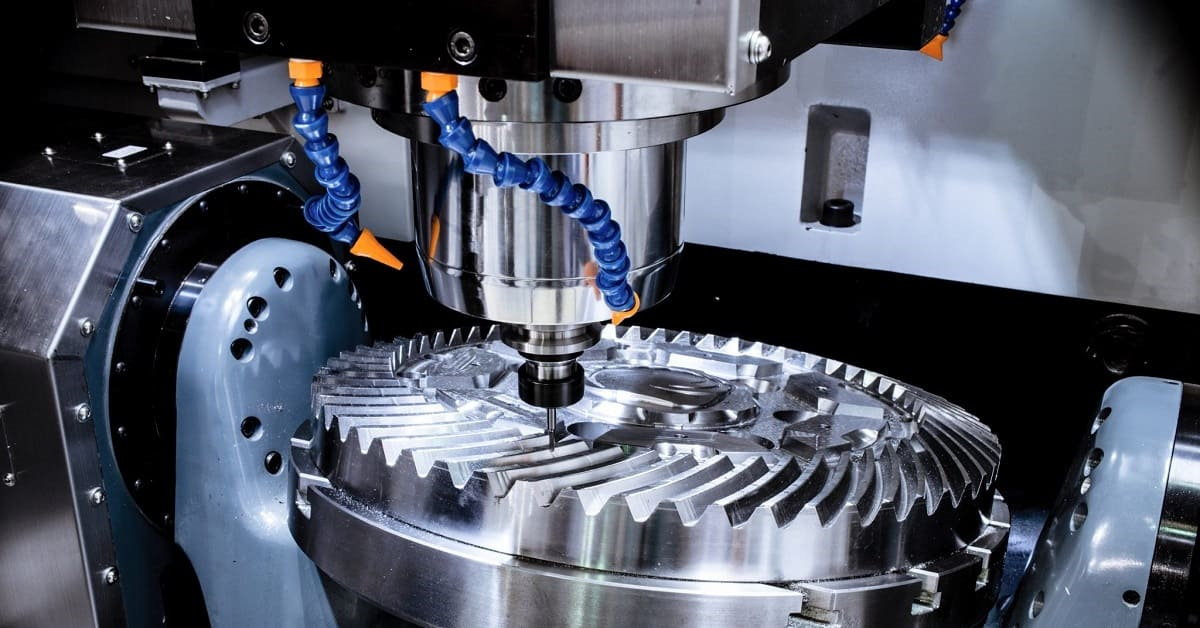
A stock image related to cnc machine china.
How Does CNC Machine China Enhance Furniture Manufacturing?
CNC machines are revolutionizing furniture manufacturing by allowing for the custom design and mass production of furniture pieces. This capability increases design flexibility and responsiveness to market trends, enabling manufacturers to meet consumer demands effectively. When sourcing CNC machines for this sector, international buyers should consider material sourcing and delivery timelines, as these factors play a crucial role in maintaining production schedules and meeting customer expectations.
Related Video: China Linear ATC CNC Wood Router with Saw Cutting Operational video
3 Common User Pain Points for ‘cnc machine china’ & Their Solutions
Scenario 1: Navigating Quality Assurance Challenges with CNC Machines from China
The Problem:
International B2B buyers often face significant uncertainty regarding the quality of CNC machines sourced from China. This concern is particularly acute for companies in Africa and South America, where local standards may differ vastly from those in China. Buyers may receive machines that do not meet their specifications or have inconsistent performance, leading to production delays, increased costs, and potential damage to their reputation.
The Solution:
To mitigate quality assurance challenges, buyers should implement a multi-step sourcing strategy. First, conduct thorough due diligence on potential suppliers by checking certifications such as ISO 9001 and reviewing client testimonials. It’s advisable to request sample parts produced by the CNC machines to evaluate their precision and reliability firsthand. Additionally, engage third-party inspection services to verify the machine’s quality before shipment. Establishing a clear set of specifications and quality standards in a contract can also protect buyers from subpar products. Lastly, consider building relationships with suppliers who have a track record of exporting to your region, as they are more likely to understand your specific needs and standards.
Scenario 2: Understanding Technical Support and Maintenance Requirements
The Problem:
A common pain point for B2B buyers is the lack of accessible technical support and maintenance for CNC machines purchased from China. Buyers in the Middle East and Europe may find that after the initial purchase, the supplier is less responsive, leaving them without crucial support for installation, programming, or troubleshooting. This can lead to extended downtimes and lost revenue.
The Solution:
To ensure adequate technical support, buyers should prioritize suppliers that offer comprehensive after-sales services. Before finalizing a purchase, inquire about the availability of local service centers or technical representatives in your region. It’s also beneficial to negotiate a maintenance contract that includes regular check-ups and prompt support response times. Additionally, consider investing in training for your staff, either through the supplier or a third-party provider, to empower them to handle minor issues independently. Documenting common troubleshooting steps and maintaining a good line of communication with the supplier can also enhance your ability to resolve issues quickly.
Scenario 3: Managing Import and Compliance Challenges with CNC Machinery
The Problem:
Importing CNC machines from China can be fraught with regulatory and compliance hurdles, particularly for businesses in Europe and Africa. Buyers may struggle with customs regulations, tariffs, and the need for specific documentation, which can lead to delays in receiving their machines and unexpected costs. This complexity can be especially daunting for companies lacking experience in international trade.
The Solution:
To navigate these import challenges effectively, buyers should engage with a logistics partner who specializes in international shipping and customs clearance. This partner can provide guidance on the necessary documentation, such as import licenses and compliance certificates, tailored to the buyer’s specific country regulations. It’s also wise to familiarize oneself with local laws regarding the import of machinery, including any tariffs that may apply. Buyers should consider including a clause in their contracts with suppliers that holds them accountable for any compliance-related issues that arise. Finally, establishing a buffer in the project timeline for potential delays can help mitigate the impact on production schedules.
Strategic Material Selection Guide for cnc machine china
When selecting materials for CNC machining in China, international B2B buyers must consider various factors to ensure optimal performance and compliance with industry standards. Below, we analyze four common materials used in CNC machining, focusing on their properties, advantages, disadvantages, and specific considerations for buyers from Africa, South America, the Middle East, and Europe.
What Are the Key Properties of Aluminum in CNC Machining?
Aluminum is a highly versatile material known for its lightweight and excellent corrosion resistance. It typically has a temperature rating of up to 600°F and can withstand moderate pressures. Its thermal conductivity is also noteworthy, making it suitable for applications requiring heat dissipation.
Pros & Cons:
The primary advantage of aluminum is its ease of machining, which translates to lower manufacturing complexity and costs. However, it may not be suitable for high-stress applications due to its relatively lower strength compared to other metals.
Impact on Application:
Aluminum is compatible with various media, including water and oils, making it ideal for automotive and aerospace applications.
Considerations for International Buyers:
Buyers should ensure compliance with standards such as ASTM B221 and DIN 1725. Additionally, understanding local sourcing options in countries like Spain or Argentina can help mitigate shipping costs and lead times.
How Does Stainless Steel Perform in CNC Machining Applications?
Stainless steel is renowned for its exceptional corrosion resistance and high strength. It can withstand temperatures up to 1,500°F and is suitable for high-pressure applications, making it a preferred choice in industries such as food processing and pharmaceuticals.
Pros & Cons:
While stainless steel offers superior durability and longevity, it comes at a higher cost and involves more complex machining processes due to its toughness.
Impact on Application:
This material is compatible with a wide range of media, including acids and bases, which makes it suitable for chemical processing applications.
Considerations for International Buyers:
Buyers from regions with stringent regulations, such as the EU, should ensure compliance with standards like ASTM A276 and JIS G4303. Understanding local market conditions can also help in negotiating better prices.
What Are the Benefits of Using Plastics in CNC Machining?
Plastics, such as polycarbonate and nylon, are increasingly popular in CNC machining due to their lightweight and excellent chemical resistance. They can typically operate at temperatures up to 250°F and are suitable for low-pressure applications.
Pros & Cons:
The main advantage of plastics is their low cost and ease of machining, which can significantly reduce production times. However, they may not be suitable for high-stress applications due to lower mechanical strength.
Impact on Application:
Plastics are compatible with various media, including water and some chemicals, making them suitable for consumer products and electronic housings.
Considerations for International Buyers:
Buyers should consider the specific grades of plastics that comply with local regulations, such as REACH in Europe or similar standards in South America.
Why Choose Titanium for CNC Machining?
Titanium is known for its high strength-to-weight ratio and excellent corrosion resistance, making it ideal for aerospace and medical applications. It can withstand temperatures up to 1,800°F and is suitable for high-pressure environments.
Pros & Cons:
The key advantage of titanium is its durability and performance in extreme conditions. However, it is one of the more expensive materials and requires specialized machining techniques.
Impact on Application:
Titanium is compatible with aggressive media, including saltwater and acids, making it ideal for marine and chemical applications.
Considerations for International Buyers:
International buyers should be aware of the high costs associated with titanium and ensure compliance with standards such as ASTM F136. Understanding the supply chain for titanium in regions like the Middle East can also provide cost advantages.
Summary Table of Material Selection for CNC Machining in China
Material | Typical Use Case for cnc machine china | Key Advantage | Key Disadvantage/Limitation | Relative Cost (Low/Med/High) |
---|---|---|---|---|
Aluminum | Automotive and aerospace components | Lightweight and easy to machine | Lower strength for high-stress use | Low |
Stainless Steel | Food processing and pharmaceuticals | Excellent corrosion resistance | Higher cost and complex machining | High |
Plastics | Consumer products and electronic housings | Low cost and quick production | Lower mechanical strength | Low |
Titanium | Aerospace and medical applications | High strength and corrosion resistance | High cost and specialized machining | High |
By understanding these materials and their implications, international B2B buyers can make informed decisions that align with their specific needs and regional standards.
In-depth Look: Manufacturing Processes and Quality Assurance for cnc machine china
What Are the Main Stages of CNC Machine Manufacturing in China?
The manufacturing of CNC machines in China involves a systematic approach, typically broken down into four main stages: material preparation, forming, assembly, and finishing. Each stage is critical to ensuring that the final product meets both performance expectations and quality standards.
1. Material Preparation
The first step in the manufacturing process involves selecting high-quality raw materials, often including various grades of steel, aluminum, and plastic. Suppliers should provide certifications that demonstrate the material’s compliance with international standards. For B2B buyers, ensuring that materials are sourced from reputable suppliers is crucial. Buyers may request material certifications and test results to confirm the quality before proceeding.
2. Forming Techniques Used in CNC Machine Manufacturing
Once the materials are prepared, the forming stage begins. This can include several key techniques such as:
- CNC Machining: This is the core process where computer-controlled machines cut, shape, and mold the material into precise components.
- Casting and Forging: These methods are often used for creating complex shapes that are difficult to achieve through machining alone.
- Laser Cutting and Water Jet Cutting: These modern techniques provide high precision and are commonly used for intricate designs.
Understanding these techniques allows buyers to assess whether the manufacturing processes align with their specific requirements.
3. Assembly Processes for CNC Machines
After forming, the next stage is assembly, where the individual components are brought together. This process may include:
- Sub-assembly: Components are first assembled into smaller units before being integrated into the final machine.
- Integration of Electronics: Given the advanced technology in CNC machines, integrating control systems and software is crucial for functionality.
For international buyers, especially those in regions like Africa and South America, understanding the assembly process is essential to ensure that the final product meets their operational standards.
4. Finishing Techniques and Their Importance
Finishing processes are the final step in manufacturing and involve polishing, coating, and sometimes painting the CNC machine. These processes not only enhance aesthetics but also protect against corrosion and wear. Buyers should inquire about the types of finishes used and their durability, particularly for machines that will operate in harsh environments.
How Is Quality Assurance Implemented in CNC Machine Manufacturing?
Quality assurance (QA) is a critical component of the manufacturing process, ensuring that products meet both international and industry-specific standards.
What International Standards Should B2B Buyers Consider?
International standards such as ISO 9001 are fundamental in ensuring consistent quality management practices. Additionally, certifications like CE (European Conformity) and API (American Petroleum Institute) may be relevant depending on the specific application of the CNC machines.
What Are the Key QC Checkpoints in the Manufacturing Process?
Quality control (QC) is typically structured around several key checkpoints:
- Incoming Quality Control (IQC): This stage involves inspecting raw materials upon arrival to ensure they meet specified standards before manufacturing begins.
- In-Process Quality Control (IPQC): During manufacturing, processes are continuously monitored to catch defects early.
- Final Quality Control (FQC): This final inspection checks the finished product against quality benchmarks and specifications.
B2B buyers should ask suppliers about their QC procedures to understand how quality is maintained throughout the production process.
Which Testing Methods Are Commonly Used for CNC Machines?
Several testing methods are employed to ensure that CNC machines operate effectively and safely:
- Dimensional Inspection: Measuring critical dimensions to ensure they meet specifications.
- Functional Testing: Assessing the machine’s performance under operating conditions.
- Durability Testing: Simulating extended use to gauge wear and tear.
Buyers can request detailed reports on these tests to verify compliance with quality standards.
How Can B2B Buyers Verify Supplier Quality Control?
To ensure that a supplier adheres to quality standards, B2B buyers can take several steps:
- Conduct Audits: Regular audits of the manufacturing facility can provide insights into production practices and quality management.
- Request Quality Reports: Suppliers should be able to provide documentation of their QC processes and results.
- Third-Party Inspections: Engaging independent inspectors can offer an unbiased assessment of the manufacturer’s quality assurance practices.
For buyers from Africa, South America, the Middle East, and Europe, understanding these verification methods is vital for mitigating risks associated with international procurement.
What Are the Nuances of Quality Control for International B2B Buyers?
When sourcing CNC machines from China, international buyers must be aware of specific nuances in quality control practices. Different regions may have varying expectations and regulations, which can affect compliance and quality assurance:
- Cultural Differences: Understanding the local manufacturing culture can aid in establishing effective communication and quality expectations.
- Regulatory Compliance: Buyers must ensure that the machines meet the regulatory requirements of their home countries, which may differ from those in China.
- Language Barriers: Clear communication is essential. B2B buyers should consider working with translators or local representatives to ensure that specifications and quality standards are understood.
By being informed about these aspects, B2B buyers can make more confident decisions when sourcing CNC machines from China, leading to better outcomes in terms of quality and performance.
Practical Sourcing Guide: A Step-by-Step Checklist for ‘cnc machine china’
In today’s competitive manufacturing landscape, sourcing CNC machines from China can be a strategic advantage for international B2B buyers. This guide provides a step-by-step checklist to ensure a smooth and effective procurement process, tailored specifically for buyers from Africa, South America, the Middle East, and Europe.
Step 1: Define Your Technical Specifications
Before reaching out to suppliers, clearly outline your technical requirements. This includes machine size, precision level, and the materials you intend to work with. Precise specifications will help you communicate effectively with potential suppliers and ensure you receive machines that meet your operational needs.
- Considerations: Determine if you need a CNC milling machine, lathe, or router. Specify any additional features, such as automation capabilities or software compatibility.
Step 2: Conduct Market Research
Research the CNC machine market in China to understand pricing, available technologies, and leading manufacturers. This will provide you with a benchmark for evaluating supplier quotes and capabilities.
- Strategies: Utilize online resources, industry reports, and trade publications. Attend virtual trade shows and forums to gather insights from other buyers and industry experts.
Step 3: Evaluate Potential Suppliers
Once you have a list of potential suppliers, conduct thorough evaluations. Request company profiles, product catalogs, and references from other businesses that have purchased CNC machines from them.
- Key Actions: Look for suppliers with a proven track record in your specific industry. Assess their experience with international shipments and after-sales support.
Step 4: Verify Supplier Certifications
Ensure that the suppliers hold relevant certifications, such as ISO 9001 or CE marking. These certifications indicate that the supplier adheres to international quality standards.
- Importance: Valid certifications assure you of the machine’s quality and reliability, reducing the risk of operational issues down the line.
Step 5: Request Samples or Demonstrations
Before making a final decision, request samples of the machines or arrange for a demonstration. This hands-on experience is invaluable in assessing the machine’s performance and suitability for your needs.
- Tips: If possible, visit the factory or arrange a virtual tour to see the manufacturing process and quality control measures in place.
Step 6: Negotiate Terms and Conditions
Engage in negotiations regarding pricing, payment terms, and delivery schedules. Ensure that all agreements are documented to avoid misunderstandings later.
- Focus Areas: Discuss warranty terms, technical support availability, and potential penalties for late delivery.
Step 7: Plan for Logistics and Customs
Finally, consider the logistics of transporting the CNC machine from China to your location. Research import regulations and customs duties applicable in your country to avoid unexpected costs.
- Logistics Considerations: Work with a freight forwarder experienced in international shipments to navigate the complexities of customs clearance and ensure timely delivery.
By following these steps, B2B buyers can confidently source CNC machines from China, ensuring they make informed decisions that align with their business objectives.
Comprehensive Cost and Pricing Analysis for cnc machine china Sourcing
When considering sourcing CNC machines from China, understanding the comprehensive cost structure and pricing analysis is crucial for international B2B buyers. This guide will delve into the various cost components, price influencers, and actionable buyer tips to help you make informed purchasing decisions.
What Are the Key Cost Components of CNC Machines from China?
-
Materials
The raw materials used in the production of CNC machines significantly impact the overall cost. Common materials include steel, aluminum, and specialized alloys. Fluctuations in global commodity prices can lead to variations in the cost of these materials, which buyers should monitor closely. -
Labor
Labor costs in China are generally lower than in many Western countries; however, the quality of craftsmanship can vary. Skilled labor for CNC machining is essential, and while basic labor costs may be low, investing in skilled workers can enhance the quality of the final product. -
Manufacturing Overhead
This includes all indirect costs associated with production, such as factory utilities, maintenance, and administrative expenses. Understanding the manufacturer’s overhead can provide insight into their pricing strategy. -
Tooling
Tooling costs refer to the expenses incurred for the equipment and tools necessary to produce CNC machines. Custom tooling can significantly increase upfront costs but may lead to better efficiency and lower per-unit costs in the long run. -
Quality Control (QC)
Implementing stringent QC processes is essential to ensure the machines meet international standards. Additional costs may arise from testing and certification processes, which are particularly important for buyers from regions with strict compliance regulations. -
Logistics
Shipping costs can vary based on the shipping method, distance, and current freight rates. Buyers should consider the total logistics cost, including duties and tariffs, when evaluating the overall expense of sourcing from China. -
Margin
Suppliers typically build a margin into their pricing to cover their risks and ensure profitability. Understanding the margin expectations of your supplier can provide leverage during negotiations.
How Do Price Influencers Affect CNC Machine Costs?
-
Volume/MOQ (Minimum Order Quantity)
Ordering in larger volumes can lead to significant discounts. Buyers should assess their needs and consider future demand to negotiate better pricing. -
Specifications and Customization
Customized machines will generally cost more than standard models. Be clear about your specifications to avoid unnecessary costs and ensure the supplier can meet your requirements. -
Materials
The choice of materials not only affects the initial cost but also the durability and maintenance of the CNC machine. Opting for higher-quality materials may increase upfront expenses but can lead to lower Total Cost of Ownership (TCO). -
Quality and Certifications
Machines certified to international standards (ISO, CE, etc.) may come at a premium but offer assurance of quality and reliability, which is crucial for long-term operations. -
Supplier Factors
The supplier’s reputation, experience, and production capabilities can influence pricing. Established suppliers may charge higher prices due to their reliability and service quality. -
Incoterms
Understanding Incoterms (International Commercial Terms) is vital. They dictate the responsibilities of buyers and sellers regarding shipping costs, insurance, and risk. Choosing the right Incoterm can help minimize costs and clarify obligations.
What Are the Best Buyer Tips for Cost-Efficiency?
-
Negotiate: Always negotiate prices and terms with suppliers. Understanding the cost components can provide leverage during discussions.
-
Evaluate Total Cost of Ownership: Look beyond the initial purchase price. Consider maintenance, operational costs, and potential downtime when assessing the value of a CNC machine.
-
Be Informed About Pricing Nuances: Familiarize yourself with the pricing structures common in China. This can help you identify reasonable offers and avoid scams.
-
Conduct Thorough Research: Understand the market trends, supplier capabilities, and regional price variations. This knowledge can empower you to make better decisions.
-
Build Relationships: Establishing long-term relationships with suppliers can lead to better pricing, priority service, and improved product offerings over time.
Conclusion
Sourcing CNC machines from China requires careful consideration of various cost components and pricing influencers. By leveraging the insights provided in this analysis, international B2B buyers from Africa, South America, the Middle East, and Europe can make informed decisions that optimize their sourcing strategies. Remember that while prices may vary, understanding the underlying factors can lead to more favorable outcomes. Always keep in mind that the prices mentioned are indicative and can fluctuate based on market conditions and supplier negotiations.
Alternatives Analysis: Comparing cnc machine china With Other Solutions
Understanding the Importance of Evaluating Alternatives
When considering the acquisition of CNC machines from China, it is essential for international B2B buyers to evaluate various alternatives to ensure they choose the best solution for their operational needs. Factors such as performance, cost, ease of implementation, maintenance requirements, and specific use cases can significantly influence the decision-making process. This analysis will compare CNC machines from China with two viable alternatives: European CNC machines and manual machining methods.
Comparison Table of CNC Machine Solutions
Comparison Aspect | Cnc Machine China | European CNC Machines | Manual Machining Methods |
---|---|---|---|
Performance | High precision; suitable for mass production | Superior precision; ideal for intricate designs | Lower precision; limited production capacity |
Cost | Generally lower initial investment | Higher initial investment; better long-term ROI | Low initial cost, but higher labor costs |
Ease of Implementation | Moderate; requires setup and training | Moderate; often includes support and training | Easy to implement; requires skilled labor |
Maintenance | Requires regular maintenance; parts may be less accessible | Higher reliability; readily available parts and support | High maintenance; skilled labor needed for repairs |
Best Use Case | High-volume production; standard parts | Custom parts; high-precision industries | Prototyping; low-volume production |
Detailed Breakdown of Alternatives
What are the advantages and disadvantages of European CNC Machines?
European CNC machines are renowned for their superior precision and reliability. These machines are often equipped with advanced technology and are designed for high-performance applications, making them suitable for industries requiring intricate designs, such as aerospace and automotive. However, the initial investment can be significantly higher compared to Chinese counterparts, which may deter smaller businesses. Despite the higher upfront costs, many buyers find that the long-term return on investment (ROI) justifies the expense due to lower maintenance costs and reduced downtime.
Why might businesses consider manual machining methods?
Manual machining methods represent a traditional approach that can be advantageous for certain scenarios, particularly in low-volume production or prototyping. The initial investment is typically lower, making it an attractive option for startups or companies with limited budgets. However, the reliance on skilled labor can lead to higher ongoing operational costs, and the precision achieved may not meet the standards required for more complex projects. Additionally, manual methods can be time-consuming, which may not align with the fast-paced demands of today’s manufacturing environments.
How to Choose the Right Solution for Your Business Needs
When evaluating CNC machines from China against other alternatives, B2B buyers should consider their specific operational needs, budget constraints, and long-term strategic goals. It is crucial to assess not only the initial costs but also the potential for ROI, maintenance requirements, and the skill level of the workforce. Conducting a thorough analysis of each option’s performance and suitability for your production goals will help ensure that your final choice aligns with your business objectives and enhances operational efficiency. By making an informed decision, buyers can optimize their manufacturing processes and maintain a competitive edge in their respective markets.
Essential Technical Properties and Trade Terminology for cnc machine china
When considering the procurement of CNC machines from China, understanding the essential technical properties and industry terminology can significantly enhance the decision-making process for international B2B buyers. This knowledge not only aids in evaluating machine specifications but also facilitates smoother negotiations and transactions.
What Are the Key Technical Properties of CNC Machines?
-
Material Grade
– Definition: The quality of materials used in the construction of CNC machines, often denoted by specific grades (e.g., stainless steel, cast iron).
– Importance: Material grade affects durability, machine performance, and maintenance. Higher-grade materials typically lead to longer machine lifespans and reduced operational costs, which is crucial for businesses in competitive markets. -
Tolerance
– Definition: The permissible limit of variation in a physical dimension, typically measured in millimeters or microns.
– Importance: Tolerance levels determine the precision of the parts produced by the CNC machine. For industries such as aerospace and automotive, where precision is critical, understanding tolerance is essential for ensuring product quality and compliance with industry standards. -
Spindle Speed
– Definition: The speed at which the spindle rotates, usually measured in revolutions per minute (RPM).
– Importance: Spindle speed influences the cutting capabilities of the CNC machine. A higher spindle speed allows for faster machining, which can enhance productivity, making it a key consideration for buyers aiming to optimize their manufacturing processes. -
Axis Configuration
– Definition: The number and arrangement of axes on the CNC machine (e.g., 3-axis, 5-axis).
– Importance: The configuration dictates the complexity of shapes that the machine can create. A 5-axis machine, for instance, can perform more intricate tasks than a 3-axis machine, providing greater flexibility for diverse applications. -
Control System
– Definition: The software and hardware that control the CNC machine’s operations, such as Fanuc, Siemens, or proprietary systems.
– Importance: The choice of control system impacts ease of use, programming capabilities, and integration with other machinery. Familiarity with various systems can help buyers select machines that align with their operational expertise and existing technology.
Which Trade Terms Should International Buyers Understand?
-
OEM (Original Equipment Manufacturer)
– Definition: A company that produces parts or equipment that may be marketed by another manufacturer.
– Importance: Understanding OEM relationships can help buyers identify reputable suppliers and assess the quality of parts provided. Engaging with established OEMs often leads to higher-quality products. -
MOQ (Minimum Order Quantity)
– Definition: The smallest quantity of a product that a supplier is willing to sell.
– Importance: Knowing the MOQ is vital for budget planning and inventory management. Buyers from Africa or South America, for example, should ensure that the MOQ aligns with their production needs to avoid excess inventory costs. -
RFQ (Request for Quotation)
– Definition: A document sent to suppliers requesting a quote for specific goods or services.
– Importance: An RFQ helps buyers gather pricing information and compare offers. This is particularly useful for international buyers to ensure they receive competitive pricing and favorable terms. -
Incoterms (International Commercial Terms)
– Definition: A set of rules that define the responsibilities of buyers and sellers in international trade.
– Importance: Familiarity with Incoterms such as FOB (Free on Board) or CIF (Cost, Insurance, and Freight) helps buyers understand shipping costs and responsibilities, which is essential for budgeting and risk management in international transactions. -
Lead Time
– Definition: The time taken from placing an order to receiving the goods.
– Importance: Understanding lead times is crucial for project planning and inventory control. Buyers need to account for manufacturing, shipping, and customs clearance times to avoid production delays.
By equipping themselves with this knowledge of technical properties and trade terminology, B2B buyers can enhance their procurement strategies, leading to more informed decisions and successful partnerships with CNC machine manufacturers in China.
Navigating Market Dynamics and Sourcing Trends in the cnc machine china Sector
What Are the Key Market Trends Influencing CNC Machine Sourcing from China?
The CNC machine sector in China has been experiencing significant growth driven by global demand for precision engineering and automation. As industries in Africa, South America, the Middle East, and Europe increasingly adopt advanced manufacturing technologies, the market dynamics are shifting towards more sophisticated and innovative solutions. Key trends include the rise of Industry 4.0, where the integration of IoT and AI is revolutionizing production efficiency. Additionally, the adoption of advanced materials and processes is becoming prevalent, allowing for lightweight yet durable components in various applications, from automotive to aerospace.
International B2B buyers are also witnessing a surge in customization capabilities offered by Chinese manufacturers. This shift allows for tailored solutions that meet specific regional needs, especially in emerging markets. Furthermore, the COVID-19 pandemic has accelerated digital transformation in the sourcing process, leading to an increased reliance on e-commerce platforms for procurement. This trend is particularly relevant for buyers from regions like Spain and Argentina, where traditional sourcing methods are being supplemented by online marketplaces, facilitating easier access to suppliers and competitive pricing.
How Are Sustainability and Ethical Sourcing Shaping the CNC Machine Sector?
Sustainability is becoming a crucial factor for B2B buyers in the CNC machine sector, especially those looking to maintain a competitive edge in their respective markets. The environmental impact of manufacturing processes has led to a growing emphasis on ethical sourcing and sustainable practices. Buyers are increasingly demanding transparency in supply chains, prompting manufacturers to adopt environmentally friendly practices. This includes the use of renewable energy sources, waste reduction initiatives, and the implementation of circular economy principles.
Furthermore, certifications such as ISO 14001 for environmental management and adherence to global sustainability standards are becoming prerequisites for suppliers. B2B buyers should prioritize sourcing from manufacturers who demonstrate a commitment to sustainability, as this not only enhances brand reputation but also aligns with the growing consumer demand for environmentally responsible products. Engaging with suppliers who utilize green materials and processes can lead to long-term cost savings and improved operational efficiencies.
What Is the Historical Context of CNC Machine Manufacturing in China?
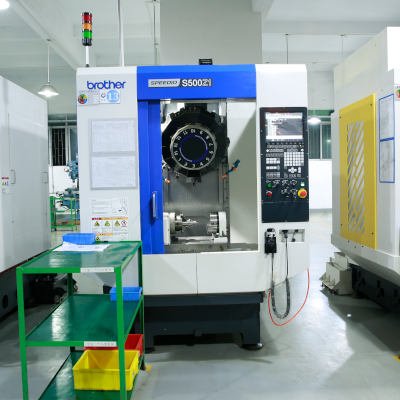
A stock image related to cnc machine china.
The evolution of CNC machine manufacturing in China can be traced back to the late 20th century when the country began to industrialize rapidly. Initially, the focus was on basic manufacturing capabilities, but significant investments in technology and workforce training have transformed China into a global leader in CNC machine production. By the early 2000s, advancements in computer technology and automation propelled Chinese manufacturers to adopt more sophisticated CNC technologies, enabling them to produce high-precision machines at competitive prices.
As a result, China has become a preferred sourcing destination for international buyers seeking cost-effective and reliable CNC solutions. Understanding this historical context can provide valuable insights into the current market dynamics and the competitive advantages that Chinese manufacturers offer, making it easier for B2B buyers from Africa, South America, the Middle East, and Europe to navigate their sourcing strategies effectively.
Frequently Asked Questions (FAQs) for B2B Buyers of cnc machine china
-
How do I choose the right CNC machine supplier in China?
Choosing the right CNC machine supplier in China involves thorough research and vetting. Start by identifying suppliers with a solid reputation and track record in the industry. Utilize platforms like Alibaba or Made-in-China to view supplier ratings and customer reviews. Request certifications (ISO, CE) to ensure quality compliance. Additionally, consider visiting the factory, if feasible, to assess production capabilities and quality control processes. Engaging with local trade associations can also provide valuable insights and recommendations. -
What are the common payment terms for purchasing CNC machines from China?
Payment terms can vary significantly between suppliers, but common practices include a 30% deposit with the order and the remaining 70% before shipment. Some suppliers may offer letter of credit (L/C) options, which can provide added security for large transactions. Be sure to clarify the terms in your contract, including any penalties for late payments or non-compliance. Using escrow services or trade assurance programs can also mitigate risks associated with international payments. -
What is the minimum order quantity (MOQ) for CNC machines in China?
The minimum order quantity (MOQ) for CNC machines typically ranges from one unit to several units, depending on the supplier and the machine type. Customization may require higher MOQs, as suppliers often prefer to produce in larger batches to optimize production costs. When sourcing, discuss your specific needs with suppliers to understand their MOQ policies and explore options for smaller orders if necessary. Negotiating with multiple suppliers can also help you find more favorable terms. -
How can I ensure quality assurance when sourcing CNC machines from China?
To ensure quality assurance when sourcing CNC machines, it is crucial to establish clear specifications and quality standards before placing an order. Request samples or prototypes to evaluate performance and quality. Implementing a third-party inspection service can help monitor production quality and verify compliance with your specifications. Additionally, maintain open communication with the supplier throughout the manufacturing process to address any concerns promptly. -
What are the typical shipping options for CNC machines from China?
Shipping options for CNC machines from China include sea freight, air freight, and express courier services. Sea freight is the most cost-effective method for large shipments but may take longer (typically 20-40 days). Air freight is faster but can be significantly more expensive, making it suitable for urgent orders. Evaluate your budget, time constraints, and shipment size to determine the most appropriate shipping method. Working with a freight forwarder can also streamline the logistics process and ensure compliance with international shipping regulations. -
What are the benefits of customizing CNC machines sourced from China?
Customizing CNC machines can provide significant advantages, including enhanced efficiency tailored to specific production needs and improved operational performance. Suppliers in China are often flexible in accommodating specific design changes, features, or functionalities. Customization can also lead to competitive differentiation in your market. However, it’s essential to communicate your requirements clearly and understand the implications of longer lead times and potential increases in cost. -
How do I navigate import regulations when buying CNC machines from China?
Navigating import regulations requires a clear understanding of both your country’s import laws and those of China. Begin by checking the tariff classifications and any duties applicable to CNC machines. Ensure compliance with safety and environmental standards in your country. Consulting with a customs broker can facilitate the import process and help manage documentation requirements, such as commercial invoices, packing lists, and certificates of origin. Staying informed about trade agreements between countries can also provide potential benefits. -
What should I consider regarding after-sales support for CNC machines sourced from China?
When sourcing CNC machines, consider the after-sales support offered by the supplier, which is critical for long-term operational success. Inquire about warranty terms, availability of spare parts, and technical support services. A reliable supplier should provide comprehensive training for your staff and have a responsive customer service team to address any issues that arise. Establishing a solid relationship with the supplier can also facilitate better support and faster resolution of any concerns in the future.
Important Disclaimer & Terms of Use
⚠️ Important Disclaimer
The information provided in this guide, including content regarding manufacturers, technical specifications, and market analysis, is for informational and educational purposes only. It does not constitute professional procurement advice, financial advice, or legal advice.
While we have made every effort to ensure the accuracy and timeliness of the information, we are not responsible for any errors, omissions, or outdated information. Market conditions, company details, and technical standards are subject to change.
B2B buyers must conduct their own independent and thorough due diligence before making any purchasing decisions. This includes contacting suppliers directly, verifying certifications, requesting samples, and seeking professional consultation. The risk of relying on any information in this guide is borne solely by the reader.
Strategic Sourcing Conclusion and Outlook for cnc machine china
As international B2B buyers navigate the complexities of sourcing CNC machines from China, strategic sourcing emerges as a critical approach to ensure both quality and cost-effectiveness. By understanding the nuances of the Chinese manufacturing landscape, buyers from Africa, South America, the Middle East, and Europe can leverage competitive pricing while maintaining high standards. Key takeaways include the importance of establishing robust supplier relationships, conducting thorough due diligence, and utilizing local market insights to enhance negotiation strategies.
How can buyers maximize their sourcing efforts in China?
To maximize sourcing efforts, buyers should consider employing local agents who understand regional dynamics and can facilitate smoother transactions. Additionally, integrating technology for real-time communication and tracking can significantly improve supply chain efficiency. With the increasing global demand for CNC machines, aligning sourcing strategies with market trends will be essential for staying ahead of competitors.
Looking ahead, the landscape of CNC machine procurement in China is set to evolve, driven by advancements in technology and shifts in global trade policies. International B2B buyers are encouraged to remain agile and proactive, ensuring they capitalize on emerging opportunities. By prioritizing strategic sourcing, businesses can not only enhance their operational capabilities but also forge lasting partnerships that drive growth in an increasingly interconnected market.