Discover Cost-Saving Tips from Top Storage Box Suppliers (2025)
Introduction: Navigating the Global Market for storage box supplier
Navigating the global market for storage box suppliers presents a significant challenge for international B2B buyers, particularly when it comes to sourcing durable and cost-effective solutions. With a diverse range of materials, sizes, and applications available, understanding how to select the right storage box can make a substantial difference in operational efficiency and cost management. This guide delves into the various types of storage boxes, their specific applications across different industries, and the essential criteria for vetting suppliers effectively.
In an increasingly interconnected world, the importance of reliable suppliers cannot be overstated. Buyers from Africa, South America, the Middle East, and Europe, including key markets like Germany and Italy, will find valuable insights on how to assess supplier credibility and negotiate favorable terms. This comprehensive resource covers everything from evaluating product quality and compliance with international standards to understanding regional shipping logistics and cost implications.
By providing actionable insights and practical tips, this guide empowers B2B buyers to make informed purchasing decisions that enhance their supply chain efficiency. Whether you are looking to streamline inventory management, reduce overhead costs, or ensure timely delivery, this guide will equip you with the knowledge to navigate the complexities of the global storage box supply market confidently.
Understanding storage box supplier Types and Variations
Type Name | Key Distinguishing Features | Primary B2B Applications | Brief Pros & Cons for Buyers |
---|---|---|---|
Plastic Storage Box Suppliers | Lightweight, waterproof, and stackable options | Warehousing, retail, and logistics | Pros: Cost-effective, durable. Cons: Less aesthetic appeal. |
Metal Storage Box Suppliers | Heavy-duty, secure, and fire-resistant | Manufacturing, construction, and military | Pros: High security, long-lasting. Cons: Heavier, higher cost. |
Wooden Storage Box Suppliers | Eco-friendly, customizable, and aesthetically pleasing | Furniture, crafts, and boutique retail | Pros: Attractive design, sustainable. Cons: Higher maintenance, variable durability. |
Corrugated Cardboard Suppliers | Lightweight, recyclable, and cost-efficient | Shipping, e-commerce, and temporary storage | Pros: Economical, easy to customize. Cons: Less durable, not waterproof. |
Specialty Storage Box Suppliers | Tailored solutions for specific industries | Pharmaceuticals, electronics, and art storage | Pros: Custom-fit for needs, unique designs. Cons: Potentially higher costs, longer lead times. |
What are the Characteristics of Plastic Storage Box Suppliers?
Plastic storage box suppliers offer products that are lightweight, waterproof, and often feature stackable designs, making them ideal for various applications in warehousing, retail, and logistics. Their affordability and durability make them a popular choice among businesses looking for practical storage solutions. When purchasing, buyers should consider the load capacity, UV resistance, and whether the boxes are made from recyclable materials, which can enhance sustainability efforts.
How Do Metal Storage Box Suppliers Stand Out?
Metal storage box suppliers provide heavy-duty options that are secure and fire-resistant, catering primarily to industries like manufacturing, construction, and military. These boxes are known for their long-lasting durability and high-security features, making them suitable for storing valuable equipment and sensitive materials. Buyers should evaluate the box’s weight, corrosion resistance, and security features, ensuring they meet industry standards and specific operational requirements.
What Makes Wooden Storage Box Suppliers Unique?
Wooden storage box suppliers focus on eco-friendly and customizable products that are aesthetically pleasing. These boxes are often used in furniture design, crafts, and boutique retail settings, appealing to businesses that prioritize sustainability and design. When considering a purchase, B2B buyers should assess the quality of the wood, the finish options available, and the potential for bespoke designs that can enhance branding and customer experience.
Why Choose Corrugated Cardboard Suppliers for Storage Needs?
Corrugated cardboard suppliers provide lightweight, recyclable, and cost-efficient storage solutions, making them ideal for shipping, e-commerce, and temporary storage. Their easy customization options allow businesses to create branded packaging solutions that are both functional and appealing. However, buyers must be aware of the limitations in durability and water resistance, making it crucial to assess the environmental conditions where the boxes will be used.
What Are the Benefits of Specialty Storage Box Suppliers?
Specialty storage box suppliers offer tailored solutions designed for specific industries, such as pharmaceuticals, electronics, and art storage. These providers focus on delivering unique designs and custom-fit products that cater to particular storage challenges. While the potential for higher costs and longer lead times exists, the benefits of precision and functionality often justify the investment. B2B buyers should carefully evaluate their specific needs and the supplier’s expertise in their industry to ensure a successful partnership.
Related Video: Warehouse Storage Solution | Racking | Types of Racking for Manual storage
Key Industrial Applications of storage box supplier
Industry/Sector | Specific Application of Storage Box Supplier | Value/Benefit for the Business | Key Sourcing Considerations for this Application |
---|---|---|---|
Retail and E-commerce | Organizing inventory and shipping supplies | Improves efficiency in stock management | Durability, size variety, and customization options |
Automotive Manufacturing | Storing parts and components during assembly | Reduces risk of damage and loss of inventory | Compliance with industry standards, material quality |
Food and Beverage | Packaging and transporting perishable goods | Ensures product safety and freshness | Temperature control features, food-grade materials |
Pharmaceuticals | Secure storage of medical supplies and equipment | Enhances safety and regulatory compliance | Security features, traceability, and sterilization options |
Construction and Engineering | Storing tools and materials on-site | Increases productivity and reduces downtime | Weather resistance, portability, and lockable features |
How Are Storage Boxes Used in Retail and E-commerce?
In the retail and e-commerce sector, storage box suppliers provide essential solutions for organizing inventory and shipping supplies. Businesses can streamline their operations by utilizing customized storage boxes that fit specific product dimensions. This organization not only enhances the efficiency of stock management but also reduces the time spent locating items. International buyers should consider sourcing durable boxes that can withstand the rigors of shipping and storage while offering a variety of sizes to accommodate diverse product ranges.
What Role Do Storage Boxes Play in Automotive Manufacturing?
In automotive manufacturing, storage boxes are crucial for storing parts and components during the assembly process. The use of robust storage solutions minimizes the risk of damage and loss of inventory, which can lead to costly production delays. Buyers in this sector should prioritize suppliers who comply with industry standards and provide high-quality materials that can withstand heavy use. Customizable options for labeling and organization can also enhance workflow efficiency on the assembly line.
Why Are Storage Boxes Important in the Food and Beverage Industry?
The food and beverage industry relies heavily on storage boxes for packaging and transporting perishable goods. These boxes must ensure product safety and freshness throughout the supply chain. International buyers should seek storage solutions that incorporate temperature control features and are made from food-grade materials. Additionally, sustainability is becoming increasingly important, so suppliers offering eco-friendly options can be a significant advantage in this sector.
How Do Storage Boxes Enhance Pharmaceutical Operations?
In the pharmaceutical sector, secure storage boxes are essential for the safe storage of medical supplies and equipment. These boxes help enhance safety and ensure compliance with stringent regulations governing the handling of pharmaceuticals. Buyers should focus on suppliers that provide storage solutions with advanced security features, traceability options, and sterilization capabilities to meet industry requirements effectively.
What Benefits Do Storage Boxes Provide in Construction and Engineering?
Storage boxes play a vital role in construction and engineering by providing a safe and organized way to store tools and materials on-site. This organization can significantly increase productivity and reduce downtime caused by misplaced tools. When sourcing storage solutions for this sector, international buyers should consider weather-resistant materials, portability, and lockable features to protect valuable equipment and materials from theft or damage.
Related Video: AS/RS Automated Storage and Retrieval Systems- Warehousing Technology
3 Common User Pain Points for ‘storage box supplier’ & Their Solutions
Scenario 1: Difficulty in Sourcing Quality Storage Boxes
The Problem:
B2B buyers, especially those operating in diverse regions like Africa and South America, often encounter challenges when trying to source high-quality storage boxes. They may struggle with suppliers that lack consistency in product quality, which can lead to inventory issues and affect overall operations. Additionally, language barriers, cultural differences, and varying standards can complicate communication and expectations, making it hard to ensure that the products meet the required specifications.
The Solution:
To address these sourcing challenges, B2B buyers should conduct thorough research on potential suppliers. Start by utilizing platforms like Alibaba or local trade directories to identify reputable storage box suppliers. Look for suppliers with certifications and positive reviews from other businesses. Once potential suppliers are shortlisted, request samples to evaluate quality firsthand. It’s crucial to establish clear communication channels, possibly using a bilingual intermediary if necessary, to ensure that specifications and quality standards are mutually understood. Furthermore, consider negotiating terms that allow for periodic quality assessments and open feedback loops throughout the ordering process.
Scenario 2: Inefficient Inventory Management with Storage Solutions
The Problem:
Many businesses face significant challenges in managing their inventory effectively, particularly when using storage boxes that do not align with their operational workflows. This can lead to wasted space, difficulty in locating items, and ultimately increased operational costs. For example, a supplier in the Middle East might find that their storage boxes are not stackable or modular, which can result in disorganization and inefficiency in warehouses or retail environments.
The Solution:
To optimize inventory management, B2B buyers should look for storage box solutions that offer modular designs and stackability. When selecting storage boxes, consider conducting a thorough analysis of your inventory needs, including dimensions, weight capacity, and accessibility requirements. Additionally, employing inventory management software can significantly streamline the process. Integrating barcodes or RFID tags with the storage boxes can enhance tracking and retrieval, making it easier to locate items quickly. Buyers should also engage with suppliers that provide customized storage solutions tailored to their specific inventory challenges, ensuring that the boxes contribute positively to their operational workflow.
Scenario 3: Navigating Import Regulations and Logistics Challenges
The Problem:
International B2B buyers often encounter logistical hurdles when importing storage boxes due to varying regulations across countries. This includes compliance with import duties, taxes, and customs regulations, which can delay shipments and increase costs unexpectedly. For instance, a company in Europe might face stringent environmental regulations regarding packaging materials, complicating their procurement process.
The Solution:
To mitigate these logistical challenges, B2B buyers should work closely with a logistics partner experienced in international shipping and customs clearance. Before finalizing orders, conduct a thorough review of the import regulations specific to both the supplier’s country and your own. This includes understanding any certifications or documentation required for the storage boxes. Buyers should also consider sourcing from local suppliers when possible, as this can simplify logistics and reduce import complexities. Additionally, maintaining open communication with suppliers regarding any potential changes in regulations or tariffs can provide advanced notice and allow for better planning. Regularly updating knowledge on trade agreements between countries can also help in identifying more favorable sourcing options.
Strategic Material Selection Guide for storage box supplier
When selecting materials for storage boxes, international B2B buyers must consider various factors that influence product performance, cost, and compliance with regional standards. Below, we analyze four common materials used in storage box manufacturing: plastic, metal, wood, and cardboard. Each material has unique properties, advantages, and limitations that can significantly affect the suitability of the final product for specific applications.
What Are the Key Properties of Plastic Storage Boxes?
Plastic is a versatile material widely used for storage boxes due to its lightweight nature and resistance to moisture. Key properties include excellent impact resistance and a temperature rating that can withstand a range of environmental conditions, making it suitable for both indoor and outdoor use. Additionally, plastics like polyethylene and polypropylene offer good chemical resistance, which is crucial when storing sensitive materials.
Pros & Cons:
The primary advantage of plastic storage boxes is their durability and low weight, which can reduce shipping costs. However, they may not be as strong as metal options and can degrade under UV exposure unless treated. Additionally, while the manufacturing process is generally straightforward, high-quality plastics can be more expensive.
Impact on Application:
Plastic storage boxes are ideal for storing chemicals, food products, and other sensitive items due to their moisture resistance. However, buyers should ensure that the specific type of plastic used complies with local regulations, particularly in the food and pharmaceutical sectors.
How Do Metal Storage Boxes Compare in Terms of Performance?
Metal storage boxes, often made from steel or aluminum, provide exceptional strength and durability. They can withstand high pressures and harsh environmental conditions, making them suitable for industrial applications. Metal also offers good fire resistance, which can be a critical factor in certain industries.
Pros & Cons:
The key advantage of metal storage boxes is their robustness and security, making them ideal for high-value items. However, they are heavier and typically more expensive than plastic options. Additionally, metal can be prone to corrosion if not properly treated, which can limit its use in humid environments.
Impact on Application:
Metal boxes are particularly effective for storing tools, machinery parts, and hazardous materials. Buyers in regions with high humidity, such as parts of Africa and South America, should consider corrosion-resistant coatings to enhance longevity.
What Advantages Do Wooden Storage Boxes Offer?
Wooden storage boxes are favored for their aesthetic appeal and strength. They provide good insulation and can be treated to resist moisture, making them suitable for various applications. Key properties include a moderate temperature rating and natural resistance to certain chemicals.
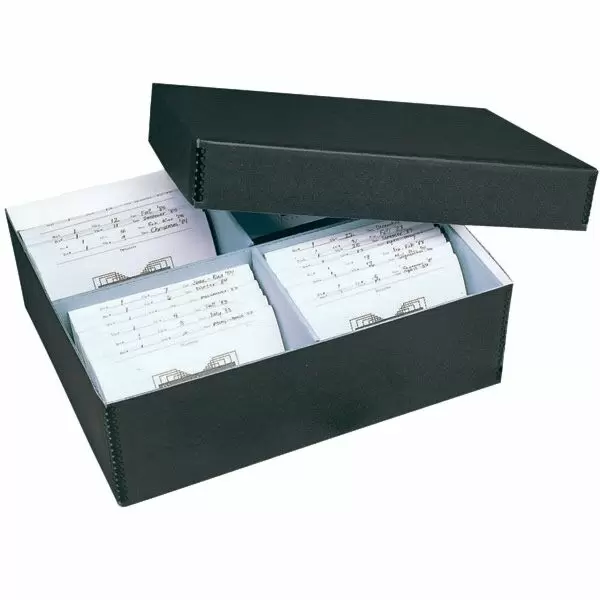
A stock image related to storage box supplier.
Pros & Cons:
The primary advantage of wooden boxes is their sustainability and ability to be customized. However, they can be susceptible to pests and moisture if not properly treated. Additionally, the manufacturing process can be more complex, leading to higher costs.
Impact on Application:
Wooden boxes are often used for storing decorative items, antiques, or food products, particularly in markets where natural materials are preferred. Buyers should ensure that the wood is sourced sustainably and meets local regulations regarding chemical treatments.
How Does Cardboard Compare for Storage Solutions?
Cardboard is a lightweight and cost-effective material widely used for temporary storage solutions. It is biodegradable and can be recycled, aligning with sustainability goals. Key properties include a moderate temperature rating and good compressive strength.
Pros & Cons:
The main advantage of cardboard is its low cost and ease of manufacturing. However, it is not suitable for long-term storage or in humid conditions, as it can easily degrade. Additionally, its strength is limited compared to other materials.
Impact on Application:
Cardboard boxes are ideal for shipping and storing non-sensitive items. Buyers should consider the local recycling infrastructure and regulations to ensure compliance with sustainability practices.
Summary Table of Material Selection for Storage Boxes
Material | Typical Use Case for storage box supplier | Key Advantage | Key Disadvantage/Limitation | Relative Cost (Low/Med/High) |
---|---|---|---|---|
Plastic | Storing chemicals and food products | Lightweight and moisture-resistant | May degrade under UV exposure | Medium |
Metal | Storing tools and hazardous materials | Exceptional strength and security | Heavier and prone to corrosion | High |
Wood | Storing decorative items and antiques | Aesthetic appeal and sustainability | Susceptible to pests and moisture | Medium |
Cardboard | Temporary storage and shipping | Low cost and recyclable | Not suitable for long-term use | Low |
In conclusion, the choice of material for storage boxes significantly impacts performance, cost, and compliance with regional standards. International B2B buyers must weigh these factors carefully to select the most suitable option for their specific needs.
In-depth Look: Manufacturing Processes and Quality Assurance for storage box supplier
What Are the Key Stages in the Manufacturing Process of Storage Boxes?
The manufacturing process for storage boxes typically involves several critical stages: material preparation, forming, assembly, and finishing. Each stage is designed to ensure that the final product meets both functional and aesthetic standards, catering to the diverse needs of B2B buyers.
-
Material Preparation: This initial stage involves selecting the right materials, which can include plastic, wood, metal, or cardboard, depending on the intended use of the storage box. Suppliers often use advanced software for material optimization, ensuring minimal waste and cost efficiency. For international buyers, it’s vital to understand the material sourcing practices of suppliers, as this can affect product quality and sustainability.
-
Forming: In this stage, materials are shaped into the desired box configuration. Techniques such as injection molding for plastics or die-cutting for cardboard are commonly used. Advanced technology, including CNC machines, may also be employed for precision manufacturing. Buyers should inquire about the specific techniques utilized, as this can impact lead times and production scalability.
-
Assembly: After forming, the components are assembled. This can involve manual labor or automated systems, depending on the complexity of the design. Quality during assembly is critical; therefore, suppliers often employ jigs and fixtures to ensure consistency. For B2B buyers, understanding the assembly process can provide insights into production efficiency and potential bottlenecks.
-
Finishing: The final stage includes surface treatment, labeling, and packaging. This is where aesthetics and brand presentation come into play. Techniques such as painting, varnishing, or laminating are used to enhance the visual appeal and durability of storage boxes. Buyers should consider how these finishing processes align with their branding needs.
How Is Quality Assurance Implemented in Storage Box Manufacturing?
Quality assurance (QA) is essential for ensuring that storage boxes meet international standards and customer expectations. Various methods and checkpoints are implemented throughout the manufacturing process to maintain high-quality standards.
-
International Standards Compliance: A significant aspect of quality assurance in manufacturing is adherence to international standards, such as ISO 9001, which provides a framework for quality management systems. Additionally, industry-specific certifications like CE (Conformité Européenne) for safety and performance or API (American Petroleum Institute) standards for boxes used in industrial applications are crucial. B2B buyers should verify that their suppliers hold relevant certifications, as this is indicative of a commitment to quality.
-
Quality Control Checkpoints: Effective quality control typically involves several checkpoints:
– Incoming Quality Control (IQC): This initial checkpoint assesses raw materials before production begins. Suppliers should conduct inspections to ensure materials meet specified standards.
– In-Process Quality Control (IPQC): During manufacturing, continuous monitoring is essential. This involves checking dimensions, weight, and other specifications to catch defects early.
– Final Quality Control (FQC): After production, a thorough inspection of the finished product is conducted. This may include functionality tests and visual inspections to ensure that storage boxes meet all requirements. -
Common Testing Methods: Various testing methods are employed to ensure quality, including mechanical testing for strength, thermal testing for heat resistance, and chemical testing for material safety. B2B buyers should request information on the specific tests conducted and the results, as this can affect product reliability.
How Can B2B Buyers Verify Supplier Quality Control Practices?
For international B2B buyers, especially those from Africa, South America, the Middle East, and Europe, verifying a supplier’s quality control processes is essential to mitigate risks and ensure product reliability.
-
Supplier Audits: Conducting regular audits of suppliers can provide valuable insights into their quality management systems. Buyers should establish audit protocols that assess compliance with international standards and the effectiveness of internal processes. This can include reviewing documentation, observing manufacturing practices, and interviewing personnel.
-
Quality Reports: Requesting detailed quality reports from suppliers can help buyers understand their quality control measures. These reports should outline inspection results, defect rates, and corrective actions taken for any identified issues. Buyers should look for transparency in these reports, as it reflects the supplier’s commitment to quality.
-
Third-Party Inspections: Engaging third-party inspection services can add an additional layer of assurance. Independent inspectors can provide unbiased evaluations of the manufacturing process and product quality. This is particularly beneficial for buyers who may not have the resources for in-house inspections.
What Are the Quality Control and Certification Nuances for International B2B Buyers?
Navigating quality control and certification nuances can be complex for international B2B buyers. Understanding regional regulations and standards is crucial for making informed purchasing decisions.
-
Regional Standards: Different regions may have specific quality standards that must be adhered to. For example, European buyers must consider EU regulations, while Middle Eastern buyers might need to comply with local standards. Buyers should familiarize themselves with these regulations to ensure supplier compliance.
-
Sustainability Certifications: Increasingly, buyers are prioritizing sustainability in their purchasing decisions. Suppliers that hold certifications like FSC (Forest Stewardship Council) for wood products or ISO 14001 for environmental management can provide assurance that they are committed to sustainable practices.
-
Cultural Considerations: When dealing with suppliers from different regions, cultural differences can impact communication and quality assurance practices. Buyers should be aware of these differences and adapt their approaches accordingly, fostering strong relationships that prioritize quality and reliability.
In conclusion, understanding the manufacturing processes and quality assurance measures in the storage box supply chain is essential for international B2B buyers. By leveraging this knowledge, buyers can make informed decisions, ensuring that they partner with suppliers who meet their quality expectations and operational needs.
Practical Sourcing Guide: A Step-by-Step Checklist for ‘storage box supplier’
Introduction
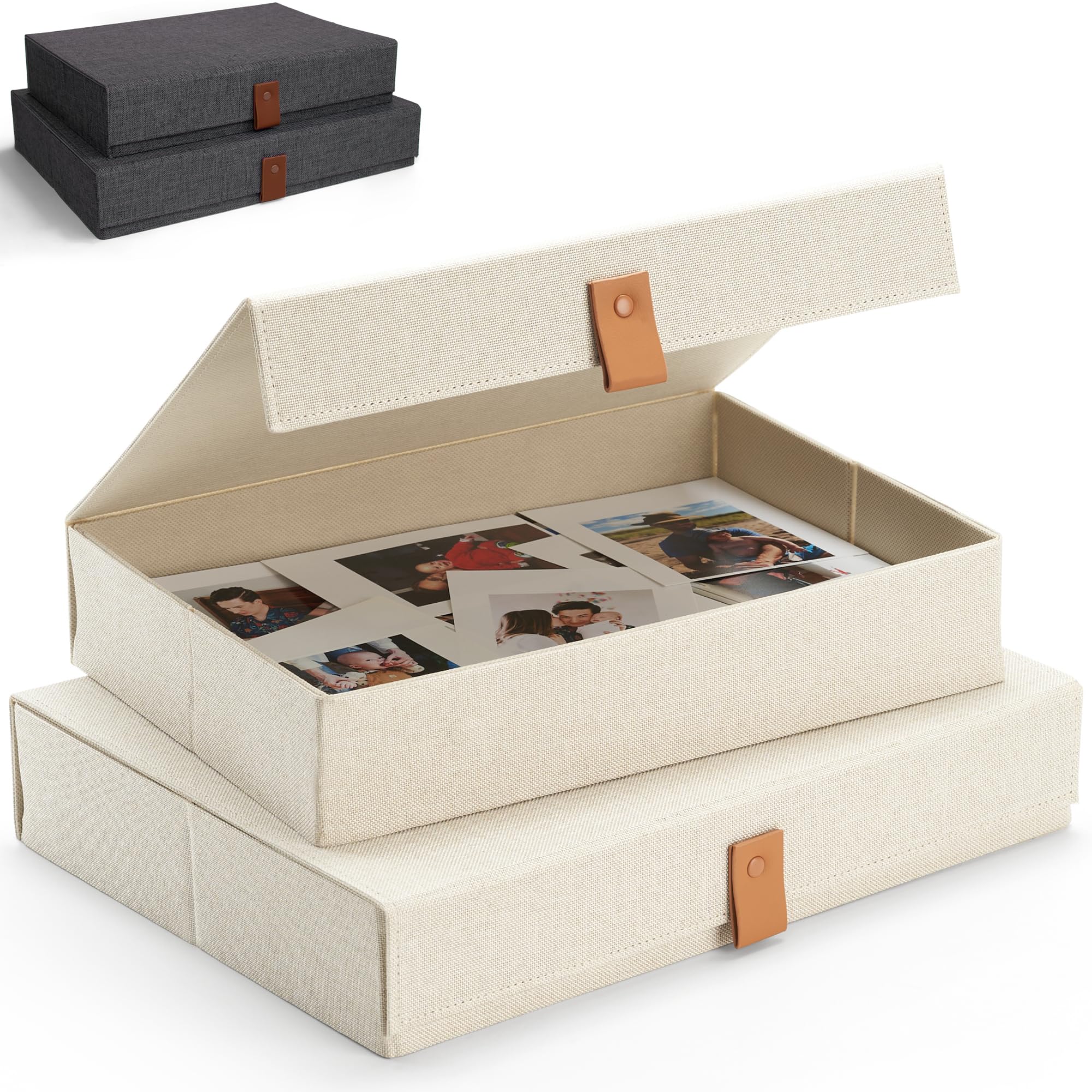
A stock image related to storage box supplier.
Navigating the procurement process for storage boxes requires a strategic approach, especially for international B2B buyers from diverse regions such as Africa, South America, the Middle East, and Europe. This guide outlines a step-by-step checklist to help you identify, evaluate, and select the right storage box suppliers to meet your business needs effectively. By following these steps, you can ensure that your sourcing process is efficient, cost-effective, and aligned with your operational requirements.
Step 1: Define Your Technical Specifications
Before you start searching for suppliers, it is essential to clarify your specific requirements for storage boxes. This includes dimensions, materials (such as plastic, wood, or metal), weight capacity, and any special features (like stackability or waterproofing).
- Consider the end use: Understand how the storage boxes will be utilized in your operations to avoid overpaying for unnecessary features.
- Document your needs: Create a detailed specification sheet that can be shared with potential suppliers for accurate quotations.
Step 2: Conduct Market Research
Understanding the market landscape is crucial for finding reliable suppliers. Research various manufacturers and distributors in your target regions, focusing on their reputation, product offerings, and customer reviews.
- Utilize online platforms: Websites like Alibaba, Global Sources, and industry-specific trade portals can provide insights into supplier credibility.
- Engage local trade associations: They can offer recommendations and insights into reputable suppliers operating within your region.
Step 3: Evaluate Potential Suppliers
Before committing, it’s crucial to vet suppliers thoroughly. Request company profiles, case studies, and references from buyers in a similar industry or region.
- Assess their experience: Look for suppliers with a proven track record in manufacturing storage boxes that meet your specific needs.
- Check for certifications: Ensure that suppliers adhere to relevant quality standards and certifications, which can vary by region.
Step 4: Request Samples
Once you have shortlisted potential suppliers, request samples of the storage boxes. Evaluating physical samples allows you to assess the quality, durability, and suitability of the products.
- Test for functionality: Ensure that the boxes meet your specifications in real-world scenarios.
- Inspect craftsmanship: Pay attention to details such as seams, finishes, and material quality to gauge overall manufacturing standards.
Step 5: Negotiate Terms and Conditions
Negotiating favorable terms is essential for a successful procurement process. Discuss pricing, payment terms, delivery schedules, and warranty options with your selected suppliers.
- Aim for bulk discounts: If you plan to order in large quantities, leverage this for better pricing.
- Clarify shipping arrangements: Ensure that shipping methods and costs are clearly outlined to avoid unexpected expenses.
Step 6: Establish a Communication Plan
Effective communication is key to a successful supplier relationship. Establish clear channels and protocols for ongoing communication to address any issues that may arise.
- Set regular check-ins: Schedule updates to discuss order status and any potential adjustments needed.
- Utilize technology: Consider using project management tools to facilitate transparency and collaboration.
Step 7: Monitor Supplier Performance
After finalizing your supplier, continue to monitor their performance against agreed-upon standards. This will help you ensure that they consistently meet your expectations and address any issues promptly.
- Solicit feedback from your team: Gather insights from those who interact with the supplier regularly.
- Review quality and delivery metrics: Regular assessments can help maintain a strong supplier relationship and inform future sourcing decisions.
By following this checklist, you can streamline your sourcing process for storage boxes and make informed decisions that align with your business objectives.
Comprehensive Cost and Pricing Analysis for storage box supplier Sourcing
What Are the Key Cost Components in Sourcing Storage Boxes?
When sourcing storage boxes, understanding the cost structure is crucial for international B2B buyers. The primary cost components include:
-
Materials: The choice of materials significantly influences the overall cost. Common materials include cardboard, plastic, and metal. Each has varying price points based on quality and durability. Sustainable materials may incur higher costs but can appeal to eco-conscious markets.
-
Labor: Labor costs can vary based on the supplier’s location and the complexity of the manufacturing process. Regions with lower labor costs may offer competitive pricing, but this can also affect quality and lead times.
-
Manufacturing Overhead: This includes expenses associated with utilities, facility maintenance, and administrative costs. Understanding a supplier’s overhead can help gauge their pricing strategy.
-
Tooling: Custom molds or tools needed for specific designs can add significant upfront costs. Buyers should inquire about tooling fees, especially when ordering custom sizes or shapes.
-
Quality Control (QC): Implementing rigorous QC processes ensures product reliability but adds to costs. Buyers should consider whether the supplier’s QC practices align with their quality standards.
-
Logistics: Transportation costs play a pivotal role in pricing. Factors such as shipping distance, mode of transport, and import/export regulations can affect the final cost significantly.
-
Margin: Finally, suppliers will include a profit margin in their pricing. Understanding the typical margins in the industry can help buyers negotiate better deals.
How Do Price Influencers Affect Storage Box Sourcing?
Several factors can influence the pricing of storage boxes, and recognizing these can lead to more informed purchasing decisions:
-
Volume/MOQ (Minimum Order Quantity): Bulk orders often lead to cost savings. Suppliers may offer discounts for larger quantities, making it essential to evaluate how MOQ affects overall pricing.
-
Specifications and Customization: Custom specifications can increase costs. Buyers should assess whether the added value of customization justifies the higher price tag.
-
Material Quality and Certifications: High-quality materials and certifications (e.g., ISO, FSC) may come at a premium. However, these can enhance brand reputation and customer satisfaction.
-
Supplier Factors: The supplier’s reputation, reliability, and operational efficiency can all influence pricing. Established suppliers might charge more but offer better service and consistency.
-
Incoterms: Understanding Incoterms (International Commercial Terms) is vital as they define the responsibilities of buyers and sellers regarding shipping costs and risks. Misunderstanding these can lead to unexpected expenses.
What Tips Can Help Buyers Negotiate Better Prices?
Effective negotiation is key to achieving favorable pricing in international B2B transactions. Here are actionable tips:
-
Conduct Thorough Market Research: Familiarize yourself with industry standards and competitor pricing to establish a baseline for negotiations.
-
Assess Total Cost of Ownership (TCO): Look beyond the purchase price. Consider logistics, maintenance, and potential waste when evaluating suppliers. A lower upfront cost might lead to higher TCO if quality is compromised.
-
Build Relationships with Suppliers: Establishing strong relationships can lead to better terms and pricing. Suppliers are often more willing to negotiate with buyers who demonstrate loyalty and long-term potential.
-
Be Clear About Requirements: Clear communication of your needs can prevent misunderstandings that might lead to added costs. Detailed specifications and expectations help streamline the sourcing process.
-
Leverage Multiple Quotes: Obtaining quotes from several suppliers can provide leverage in negotiations. It gives you options and the ability to negotiate based on competitive pricing.
Conclusion: Why Is It Important to Understand Pricing Nuances?
For international B2B buyers, particularly those from Africa, South America, the Middle East, and Europe, understanding the complexities of storage box pricing is essential. By analyzing cost components, recognizing price influencers, and employing effective negotiation strategies, buyers can make informed decisions that align with their operational needs and budgetary constraints. Always keep in mind that prices can vary significantly based on market conditions and supplier practices, so staying informed is key.
- Disclaimer: Prices mentioned are indicative and may vary based on market fluctuations, supplier negotiations, and specific order requirements.*
Alternatives Analysis: Comparing storage box supplier With Other Solutions
When considering the procurement of storage solutions, it’s essential for B2B buyers to evaluate not only the traditional storage box suppliers but also alternative methods and technologies. Each option has its unique strengths and weaknesses, which can significantly impact operational efficiency, cost-effectiveness, and overall productivity. Below is a detailed comparison of ‘storage box supplier’ against two viable alternatives: modular shelving systems and mobile storage units.
Comparison Table of Storage Solutions
Comparison Aspect | Storage Box Supplier | Modular Shelving Systems | Mobile Storage Units |
---|---|---|---|
Performance | High durability, stackable | Excellent space utilization | Flexible and scalable |
Cost | Moderate initial investment | Higher upfront cost | Variable cost based on usage |
Ease of Implementation | Simple setup | Requires assembly and planning | Quick setup, may require permits |
Maintenance | Low maintenance | Moderate (cleaning and upkeep) | Low to moderate, depends on usage |
Best Use Case | General storage needs | Efficient for bulk items | Temporary or project-based needs |
What Are the Advantages and Disadvantages of Modular Shelving Systems?
Modular shelving systems provide an excellent solution for businesses with significant storage requirements. These systems are designed to optimize space, allowing for vertical stacking and custom configurations. The primary advantage lies in their capacity to adapt to different product sizes and volumes, making them ideal for warehouses or retail environments.
However, the initial investment can be substantial, as the systems often require custom design and installation. Additionally, they may necessitate a more complex setup, which could lead to longer lead times before becoming operational. Maintenance is moderate, primarily involving cleaning and occasional adjustments.
How Do Mobile Storage Units Compare?
Mobile storage units offer flexibility that traditional storage solutions often lack. These units can be relocated based on changing needs, making them particularly useful for businesses engaged in temporary projects or those that frequently shift inventory. The ease of setup is a significant advantage, as many mobile units can be quickly deployed without extensive planning or assembly.
On the downside, the cost of mobile storage can vary significantly based on the duration of use and rental agreements. This variability can complicate budgeting for some businesses. Furthermore, while maintenance is generally low, it can increase if the units are frequently moved or if they encounter environmental challenges.
How Can B2B Buyers Choose the Right Storage Solution?
When selecting the appropriate storage solution, B2B buyers must consider their specific operational needs, budget constraints, and the nature of their inventory. If the primary goal is to maximize space efficiency and long-term storage, modular shelving may be the best choice. Conversely, for businesses that require flexibility and quick deployment, mobile storage units can offer a compelling alternative.
Ultimately, understanding the trade-offs between cost, performance, and maintenance is crucial in making an informed decision. Buyers should assess their unique requirements, including the type of products being stored and the anticipated duration of storage, to determine which solution aligns best with their operational strategy. By conducting a thorough analysis of these options, B2B buyers can ensure they invest in a solution that not only meets their current needs but also supports future growth.
Essential Technical Properties and Trade Terminology for storage box supplier
What Are the Key Technical Properties of Storage Boxes for B2B Buyers?
When sourcing storage boxes, understanding their technical properties is essential for making informed purchasing decisions. Here are some critical specifications that B2B buyers should consider:
1. Material Grade
The material from which storage boxes are made significantly affects durability and functionality. Common materials include high-density polyethylene (HDPE), polypropylene, and metal. Each material has unique properties—HDPE is resistant to impact and weather, while metal offers superior strength. For B2B buyers, choosing the right material grade ensures that the storage boxes meet specific storage needs and environmental conditions.
2. Load Capacity
Load capacity indicates how much weight a storage box can safely hold. This specification is vital for businesses that plan to store heavy items. Understanding load capacity helps avoid overloading and potential product failure, which could lead to financial loss and safety hazards. B2B buyers should always verify this property against their intended use to ensure optimal performance.
3. Tolerance Levels
Tolerance levels refer to the permissible limits of variation in the dimensions of storage boxes. For instance, if a box is designed to fit into a specific space, even minor deviations can lead to compatibility issues. Establishing clear tolerance levels is crucial for B2B buyers to ensure that the storage solutions fit seamlessly into their operations, particularly in sectors like logistics and manufacturing.
4. Weather Resistance
For businesses that operate in diverse climates, weather resistance is a significant consideration. Storage boxes may need to withstand moisture, UV radiation, or extreme temperatures. Evaluating weather resistance properties can help buyers choose products that will maintain their integrity over time, protecting stored items and reducing replacement costs.
5. Stackability
Stackability refers to the ability to safely stack storage boxes without compromising their structural integrity. This property is essential for maximizing space in warehouses or storage facilities. B2B buyers should assess stackability to optimize storage solutions and reduce logistical costs, especially in high-density environments.
What Trade Terminology Should B2B Buyers Understand When Sourcing Storage Boxes?
Familiarity with industry jargon can enhance communication and streamline procurement processes. Here are some common terms that are crucial for B2B buyers:
1. OEM (Original Equipment Manufacturer)
OEM refers to companies that produce components or products that are sold by another company under its brand name. For buyers, engaging with OEMs can ensure that they receive quality products tailored to their specifications, which is particularly important in customized storage solutions.
2. MOQ (Minimum Order Quantity)
MOQ indicates the smallest quantity of a product that a supplier is willing to sell. Understanding MOQ helps B2B buyers plan their inventory and budget effectively. Suppliers in different regions may have varying MOQs, so it’s essential to negotiate terms that align with your business needs.
3. RFQ (Request for Quotation)
An RFQ is a formal process where buyers request pricing and terms from suppliers for specific products or services. Utilizing RFQs helps buyers compare offers from multiple suppliers, ensuring they receive competitive pricing and favorable terms for storage boxes.
4. Incoterms (International Commercial Terms)
Incoterms are standardized trade terms that define the responsibilities of buyers and sellers in international transactions. Familiarity with Incoterms is crucial for B2B buyers to understand shipping responsibilities, insurance, and risk management, thereby facilitating smoother transactions across borders.
5. Lead Time
Lead time is the period between placing an order and receiving the product. Understanding lead times helps B2B buyers plan their inventory and operations more effectively, especially when dealing with suppliers in different regions.
6. Certification Standards
Certification standards, such as ISO or ASTM, indicate that products meet specific quality and safety benchmarks. For B2B buyers, sourcing storage boxes that comply with relevant certification standards ensures reliability and compliance with industry regulations, enhancing overall operational efficiency.
By grasping these technical properties and trade terminologies, B2B buyers can navigate the complexities of sourcing storage boxes more effectively, ensuring they make informed decisions that meet their business needs.
Navigating Market Dynamics and Sourcing Trends in the storage box supplier Sector
What Are the Current Market Dynamics and Key Trends in the Storage Box Supplier Sector?
The storage box supplier sector is experiencing notable shifts driven by globalization, e-commerce growth, and changing consumer preferences. International B2B buyers, particularly from Africa, South America, the Middle East, and Europe, must navigate these dynamics to make informed sourcing decisions. One significant trend is the increasing demand for customizable and multifunctional storage solutions. Businesses are looking for products that not only serve storage purposes but also enhance aesthetic appeal and usability.
Additionally, advancements in technology are reshaping the sourcing landscape. The rise of e-commerce platforms has facilitated direct connections between suppliers and buyers, reducing the reliance on traditional distribution channels. Buyers can now leverage data analytics to assess supplier performance and optimize inventory management. Furthermore, automation in manufacturing processes is leading to faster turnaround times and cost reductions, making it essential for B2B buyers to evaluate suppliers’ technological capabilities.
Another emerging trend is the focus on local sourcing, driven by supply chain disruptions caused by global events. Buyers are increasingly prioritizing suppliers that can provide reliable and consistent supply, even in times of crisis. This shift is particularly relevant for buyers in Europe, where proximity to suppliers can significantly reduce lead times and transportation costs. Understanding these market dynamics is crucial for making strategic sourcing decisions that align with business goals.
How Important Is Sustainability and Ethical Sourcing in the Storage Box Supplier Sector?
Sustainability has become a cornerstone of modern supply chain management, especially in the storage box supplier sector. International B2B buyers must consider the environmental impact of their sourcing decisions. The production of storage boxes often involves materials that can contribute to pollution and waste. As such, buyers should seek suppliers who prioritize eco-friendly materials and sustainable practices.
Ethical sourcing is equally important. Businesses are under increasing pressure from consumers and regulatory bodies to ensure that their supply chains are transparent and socially responsible. This means sourcing products that are manufactured under fair labor conditions and using materials that do not harm the environment. Certifications like FSC (Forest Stewardship Council) for wood products or GRS (Global Recycle Standard) for recycled materials can guide buyers toward responsible suppliers.
Investing in sustainable and ethical sourcing not only aligns with corporate social responsibility goals but also enhances brand reputation. Companies that demonstrate commitment to sustainability can attract more customers and build loyalty, particularly in regions where consumers are becoming increasingly eco-conscious. Thus, B2B buyers in Africa, South America, the Middle East, and Europe should prioritize suppliers who can demonstrate their commitment to sustainability and ethical practices.
What Is the Brief Evolution of the Storage Box Supplier Sector?
The storage box supplier sector has evolved significantly over the past few decades. Initially dominated by traditional manufacturers producing basic storage solutions, the industry has transformed with the advent of new materials and technologies. The introduction of plastics and advanced composites has allowed for greater design flexibility and durability, catering to a wider range of consumer needs.
In recent years, the market has witnessed a shift towards sustainability, driven by both consumer demand and regulatory pressures. Suppliers are increasingly adopting environmentally friendly materials and practices, responding to a growing market segment that prioritizes eco-conscious products. The rise of e-commerce has also revolutionized the way storage solutions are marketed and sold, enabling suppliers to reach a global audience more effectively.
This evolution underscores the importance for international B2B buyers to stay informed about market trends and supplier capabilities. By understanding the historical context, buyers can better appreciate the innovations and practices that define today’s storage box supplier landscape.
Frequently Asked Questions (FAQs) for B2B Buyers of storage box supplier
-
How do I choose the right storage box supplier for my business needs?
Choosing the right storage box supplier involves assessing several critical factors. Start by evaluating the supplier’s product range to ensure they offer the types and sizes of storage boxes that meet your specific requirements. Check for certifications and compliance with international quality standards, especially if you’re sourcing from regions like Europe or the Middle East. Additionally, consider their reputation in the market by reading reviews and testimonials. Engaging in direct communication can provide insights into their customer service, reliability, and responsiveness to inquiries. -
What are the key factors to consider when sourcing storage boxes internationally?
When sourcing storage boxes internationally, consider logistics, tariffs, and customs regulations specific to your region. Analyze shipping costs and lead times, as these can significantly impact your overall expenses and supply chain efficiency. It’s also crucial to understand the supplier’s minimum order quantities (MOQ) and payment terms to ensure they align with your business cash flow. Lastly, consider the potential for supply chain disruptions and how the supplier manages these risks, especially in regions with varying political and economic stability. -
What is the minimum order quantity (MOQ) for storage boxes from suppliers?
The minimum order quantity (MOQ) for storage boxes can vary widely among suppliers, often ranging from a few dozen to several thousand units. Factors affecting MOQ include the type of storage box, materials used, and the supplier’s production capabilities. It’s advisable to negotiate MOQs, especially if you are a smaller business or are testing new products. Some suppliers may offer flexibility on MOQs for first-time orders or long-term contracts, so engaging in open discussions can lead to mutually beneficial arrangements. -
What payment terms should I expect when sourcing storage boxes?
Payment terms when sourcing storage boxes can vary depending on the supplier and the nature of your agreement. Common terms include full payment upfront, a deposit with the balance upon delivery, or payment after receipt of goods. For international transactions, consider using secure payment methods such as letters of credit or escrow services to mitigate risks. Always clarify and document payment terms in your contracts to avoid misunderstandings. Understanding regional payment practices, especially in Africa or South America, can also help in negotiating favorable terms. -
How can I ensure the quality of storage boxes from my supplier?
To ensure quality, request samples from potential suppliers before placing larger orders. Evaluate the samples for durability, design, and usability. Additionally, inquire about the supplier’s quality assurance processes, including testing and inspection protocols. Consider visiting the supplier’s manufacturing facilities if possible or hiring third-party inspection services to verify compliance with quality standards. Building a strong relationship with your supplier can also facilitate better quality control and accountability. -
What customization options are available for storage boxes?
Many suppliers offer customization options, including sizes, colors, materials, and branding features. Discuss your specific needs with potential suppliers to see what they can accommodate. Customization can enhance your brand identity and better meet your storage requirements. Be mindful that custom orders may have longer lead times and higher costs, so plan accordingly. Always request prototypes or samples of customized products to ensure they meet your expectations before committing to larger orders. -
How do shipping and logistics affect my sourcing of storage boxes?
Shipping and logistics play a crucial role in the sourcing process, impacting costs, delivery times, and overall supply chain efficiency. Understand the shipping options available, including air freight and sea freight, and evaluate their respective costs and delivery timelines. Collaborate with your supplier to determine the best shipping method based on your urgency and budget. Additionally, stay informed about any changes in international shipping regulations or tariffs that could affect your sourcing strategy, particularly in regions like Africa and South America. -
What are the common challenges faced when sourcing storage boxes internationally?
Common challenges include language barriers, cultural differences, and varying business practices that may complicate communication and negotiations. Additionally, fluctuating exchange rates and geopolitical issues can affect pricing and delivery timelines. To mitigate these challenges, work with suppliers who have experience in international trade and understand the specific dynamics of your region. Establish clear communication protocols and consider using intermediaries or trade agents to facilitate smoother transactions and build trust with your suppliers.
Important Disclaimer & Terms of Use
⚠️ Important Disclaimer
The information provided in this guide, including content regarding manufacturers, technical specifications, and market analysis, is for informational and educational purposes only. It does not constitute professional procurement advice, financial advice, or legal advice.
While we have made every effort to ensure the accuracy and timeliness of the information, we are not responsible for any errors, omissions, or outdated information. Market conditions, company details, and technical standards are subject to change.
B2B buyers must conduct their own independent and thorough due diligence before making any purchasing decisions. This includes contacting suppliers directly, verifying certifications, requesting samples, and seeking professional consultation. The risk of relying on any information in this guide is borne solely by the reader.
Strategic Sourcing Conclusion and Outlook for storage box supplier
What Are the Key Takeaways for B2B Buyers in Strategic Sourcing?
In conclusion, strategic sourcing for storage box suppliers is crucial for international B2B buyers aiming to optimize their supply chains and enhance operational efficiency. By focusing on quality, sustainability, and supplier reliability, businesses can not only reduce costs but also improve their overall product offering. Buyers from regions such as Africa, South America, the Middle East, and Europe should prioritize establishing long-term partnerships with suppliers that align with their values and operational goals.
How Can International Buyers Enhance Their Sourcing Strategies?
As you navigate the evolving landscape of global trade, remain vigilant about market trends and regional demands. Leverage data analytics and market intelligence to make informed decisions that resonate with your target audience. Engaging with suppliers that demonstrate adaptability to changing market conditions will ensure you stay competitive in your sector.
What’s Next for B2B Buyers in the Storage Box Industry?
Looking ahead, consider how advancements in technology and sustainability practices can influence your sourcing strategies. Embrace innovation by exploring new materials and production methods that minimize environmental impact while meeting consumer expectations. By proactively adapting to these trends, you can position your business for success in an increasingly interconnected marketplace. Take the next step—evaluate your current suppliers and seek out those who can help you achieve your strategic sourcing goals.