Discover Cost-Saving Strategies for Blade Custom Solutions (2025)
Introduction: Navigating the Global Market for blade custom
In today’s competitive landscape, international B2B buyers are increasingly challenged with sourcing custom blades that meet specific operational needs while ensuring quality, efficiency, and cost-effectiveness. The global market for custom blades is diverse, encompassing a range of applications from industrial manufacturing to specialized crafts. This guide is designed to navigate this complex terrain, offering in-depth insights into various types of custom blades, their applications, and the critical factors to consider when selecting suppliers.
As buyers from regions such as Africa, South America, the Middle East, and Europe—countries like Nigeria and France—embark on their procurement journeys, understanding the nuances of supplier vetting, pricing strategies, and market trends becomes essential. This comprehensive resource will empower you to make informed purchasing decisions, highlighting best practices in evaluating suppliers and assessing the total cost of ownership.
Moreover, we will delve into the importance of compliance with international standards and the potential for establishing long-term partnerships with manufacturers. By equipping you with actionable insights and strategic frameworks, this guide aims to streamline your sourcing process, mitigate risks, and ultimately enhance your competitive edge in the global market for custom blades. Embrace this opportunity to transform your procurement strategy and drive success in your operations.
Understanding blade custom Types and Variations
Type Name | Key Distinguishing Features | Primary B2B Applications | Brief Pros & Cons for Buyers |
---|---|---|---|
Fixed Blades | Sturdy, non-retractable design for durability | Industrial cutting, agriculture | Pros: High durability, low maintenance. Cons: Limited versatility, bulkier. |
Folding Blades | Compact, retractable design for portability | Outdoor activities, emergency kits | Pros: Space-saving, easy to carry. Cons: Less robust than fixed blades. |
Specialty Blades | Custom shapes and materials for specific tasks | Precision cutting, specialized industries | Pros: Tailored solutions, high efficiency. Cons: Higher cost, longer lead times. |
Multi-Functional Blades | Integrated tools for diverse applications | Construction, emergency services | Pros: Versatile, cost-effective. Cons: Can be complex, may compromise individual tool quality. |
Ceramic Blades | Non-metallic, corrosion-resistant materials | Food service, medical applications | Pros: Sharpness retention, lightweight. Cons: Brittle, requires careful handling. |
What Are the Characteristics of Fixed Blades and Their Suitability for B2B Buyers?
Fixed blades are characterized by their non-retractable design, which enhances durability and strength. These blades are typically used in heavy-duty applications such as industrial cutting and agricultural tasks. B2B buyers should consider fixed blades when seeking tools that require minimal maintenance and can withstand harsh working conditions. However, their bulkiness may limit their versatility in compact spaces.
How Do Folding Blades Offer Portability for B2B Applications?
Folding blades provide a compact, retractable design that makes them ideal for portability. This type of blade is commonly used in outdoor activities and emergency kits, allowing users to carry them easily without taking up much space. B2B buyers focused on convenience and ease of transport will find folding blades appealing. However, they may sacrifice some robustness compared to fixed blades, making them less suitable for heavy-duty applications.
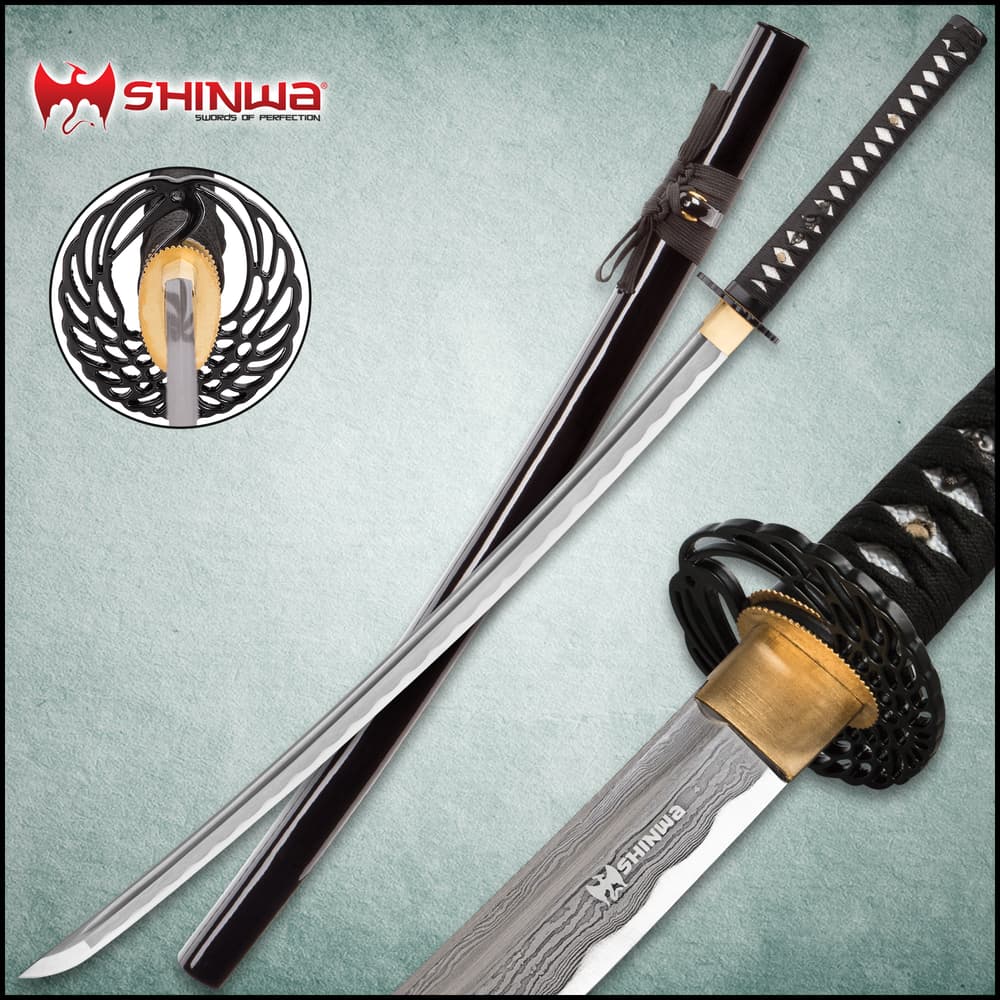
A stock image related to blade custom.
What Makes Specialty Blades a Valuable Investment for Specific Industries?
Specialty blades are designed with custom shapes and materials tailored to specific tasks, making them invaluable in precision cutting and specialized industries. B2B buyers in sectors such as manufacturing or design should consider investing in these blades for enhanced efficiency and effectiveness. While they offer tailored solutions, buyers must also be aware of potentially higher costs and longer lead times associated with custom orders.
Why Should B2B Buyers Consider Multi-Functional Blades for Diverse Applications?
Multi-functional blades integrate various tools into one design, making them suitable for a range of applications, including construction and emergency services. These blades are cost-effective for businesses looking to maximize utility without purchasing multiple separate tools. However, buyers should be cautious, as the complexity of these tools may compromise the quality of individual components, potentially affecting overall performance.
What Are the Advantages and Disadvantages of Using Ceramic Blades in B2B Settings?
Ceramic blades are known for their non-metallic, corrosion-resistant materials, making them particularly effective in food service and medical applications. Their ability to retain sharpness and lightweight nature are significant advantages for B2B buyers in these sectors. However, the brittleness of ceramic blades requires careful handling, which may not suit all operational environments. Buyers should weigh these factors when considering ceramic options for their business needs.
Related Video: Mortal Kombat X: All of Kitana’s Variations Explained
Key Industrial Applications of blade custom
Industry/Sector | Specific Application of blade custom | Value/Benefit for the Business | Key Sourcing Considerations for this Application |
---|---|---|---|
Aerospace | Custom turbine blades for jet engines | Enhanced performance and fuel efficiency | Compliance with stringent safety regulations |
Renewable Energy | Tailored wind turbine blades for specific wind conditions | Increased energy output and reduced maintenance costs | Material durability and environmental impact |
Manufacturing | Precision cutting blades for CNC machines | Improved production efficiency and reduced waste | Compatibility with existing machinery and processes |
Agriculture | Custom blades for harvesting equipment | Higher yield and reduced operational downtime | Adaptability to different crops and terrain |
Automotive | Specialized blades for electric vehicle battery cooling | Enhanced battery performance and longevity | Thermal management capabilities and cost efficiency |
How Are Custom Blades Used in the Aerospace Industry?
In the aerospace sector, custom turbine blades are critical for jet engines. These blades are engineered to withstand extreme temperatures and pressures, significantly impacting engine efficiency and performance. For international B2B buyers, particularly from regions like Africa and Europe, sourcing these components requires a keen understanding of compliance with international safety standards. Buyers must ensure that suppliers can provide documentation to verify that their blades meet stringent aerospace regulations.
What Role Do Custom Blades Play in Renewable Energy?
In the renewable energy sector, tailored wind turbine blades are designed to optimize performance based on specific wind conditions. This customization leads to increased energy output and reduced maintenance costs, making projects more economically viable. Buyers from South America and the Middle East should prioritize sourcing blades that are not only durable but also environmentally friendly, as sustainability is increasingly becoming a critical factor in project approval and financing.
How Are Precision Cutting Blades Used in Manufacturing?
Precision cutting blades are essential for CNC machines in the manufacturing industry. These custom blades enhance production efficiency by delivering cleaner cuts and reducing material waste. For B2B buyers, especially in European markets, it’s vital to consider compatibility with existing machinery and production processes. Suppliers should be able to demonstrate how their blades can integrate seamlessly into current operations, minimizing downtime during the transition.
Why Are Custom Blades Important in Agriculture?
In agriculture, custom blades for harvesting equipment can dramatically improve yield and reduce operational downtime. These blades are tailored to specific crops and terrain, ensuring optimal performance. Buyers from regions like Africa need to focus on sourcing blades that are adaptable to varying agricultural conditions, ensuring that the blades can withstand diverse climates and soil types, which is crucial for maximizing productivity.
How Do Specialized Blades Enhance Automotive Applications?
In the automotive sector, specialized blades are increasingly used for electric vehicle battery cooling systems. These custom blades enhance thermal management, which is vital for battery performance and longevity. B2B buyers, particularly in Europe where electric vehicle technology is rapidly advancing, should consider sourcing blades that not only offer efficiency but also align with cost-effective manufacturing practices. Understanding the thermal management capabilities of these blades can lead to better product performance and customer satisfaction.
Related Video: Uses and Gratifications Theory – UGT
3 Common User Pain Points for ‘blade custom’ & Their Solutions
Scenario 1: Difficulty in Sourcing Quality Blade Custom Providers
The Problem:
B2B buyers, particularly in emerging markets like Nigeria or Brazil, often struggle to find reliable suppliers for blade custom services. The challenges include a lack of local expertise, limited access to international suppliers, and the risk of receiving subpar products that don’t meet specific operational requirements. The pressure to ensure quality while managing costs can lead to frustration, especially when buyers are relying on these blades for critical applications in manufacturing or energy sectors.
The Solution:
To effectively source quality blade custom providers, buyers should start by conducting thorough market research to identify suppliers with proven track records in their industry. Utilizing platforms such as Alibaba or ThomasNet can help buyers find reputable manufacturers. It’s essential to request samples and detailed specifications before placing large orders to ensure that the blades meet the required standards. Additionally, forming partnerships with local distributors who have established relationships with international suppliers can ease the sourcing process and provide added assurance of quality. Engaging in industry-specific trade shows can also be beneficial for networking and discovering new suppliers that align with quality expectations.
Scenario 2: Miscommunication on Blade Specifications
The Problem:
Miscommunication regarding specifications is a common issue for B2B buyers when working with blade custom manufacturers. This often arises from language barriers or differences in technical jargon, leading to incorrect orders that can delay production and increase costs. For instance, a buyer in France may specify a certain material or tolerance, but if the manufacturer misinterprets these requirements, it could result in a product that is unsuitable for the intended application.
The Solution:
To mitigate miscommunication, buyers should invest time in creating detailed, clear specifications that include drawings, material data sheets, and application notes. Utilizing visual aids can significantly enhance understanding. It’s also advisable to have regular communication checkpoints throughout the design and manufacturing process. Engaging a bilingual project manager who can facilitate discussions between the buyer and the manufacturer can bridge any language gaps. Furthermore, establishing a standardized communication protocol can ensure that all parties are on the same page regarding the project’s progress and expectations.
Scenario 3: Managing Lead Times and Delivery Challenges
The Problem:
International B2B buyers frequently face challenges with lead times and delivery schedules when ordering blade custom products. This is particularly true for companies in the Middle East and Africa, where logistical issues and customs delays can disrupt supply chains. The inability to predict delivery times can hinder production schedules and impact overall operational efficiency, leading to lost revenue opportunities.
The Solution:
To better manage lead times, buyers should have open discussions with suppliers about realistic timelines and potential delays upfront. Implementing a just-in-time (JIT) inventory system can also help mitigate the impact of delays. Buyers should work closely with their logistics partners to understand the shipping routes and customs processes specific to their region, allowing them to anticipate and plan for potential bottlenecks. Additionally, establishing agreements with suppliers for expedited shipping options can provide a buffer against unexpected delays, ensuring that critical components arrive on time. Regularly reviewing and optimizing the supply chain process can also enhance responsiveness and efficiency, allowing buyers to adapt to any changes in demand or supply.
Strategic Material Selection Guide for blade custom
When selecting materials for custom blades, it is essential to consider various factors that influence performance, durability, and cost-effectiveness. Below, we analyze four common materials used in blade manufacturing, focusing on their properties, advantages, disadvantages, and specific considerations for international B2B buyers, particularly those from Africa, South America, the Middle East, and Europe.
What Are the Key Properties of Stainless Steel for Blade Customization?
Stainless Steel is a popular choice for blade manufacturing due to its excellent corrosion resistance and strength. It can withstand high temperatures and pressures, making it suitable for various applications, including food processing and chemical industries. The most common grades used are 304 and 316, with 316 offering better corrosion resistance, especially in marine environments.
Pros: Stainless steel blades are durable, easy to clean, and maintain sharpness over time. They are also relatively cost-effective compared to other high-performance materials.
Cons: The primary limitation is that stainless steel can be more challenging to machine than softer metals, which may increase manufacturing complexity and costs.
Impact on Application: Stainless steel is compatible with a wide range of media, including acidic and alkaline substances. However, it may not be suitable for highly abrasive materials, which can lead to quicker wear.
Considerations for International Buyers: Compliance with standards like ASTM A240 is crucial. Buyers should also consider local regulations regarding food safety and material certifications, especially in regions like Europe, where stringent standards apply.
How Does Carbon Steel Compare in Blade Customization?
Carbon Steel is known for its high strength and ability to maintain a sharp edge. It is often used in applications where cutting performance is critical, such as in industrial knives or surgical blades.
Pros: Carbon steel blades are typically less expensive than stainless steel and can be manufactured to very sharp edges, enhancing performance.
Cons: The major drawback is its susceptibility to corrosion, which requires regular maintenance and protective coatings. Additionally, it may not be suitable for humid or wet environments without proper treatment.
Impact on Application: Carbon steel is ideal for dry applications or where immediate corrosion resistance is not a priority. However, it is not recommended for use in environments with high moisture or chemical exposure.
Considerations for International Buyers: Buyers should be aware of the need for protective coatings and maintenance schedules. Compliance with standards such as ASTM A681 can also be necessary, particularly in regulated industries.
What Are the Advantages of High-Speed Steel in Blade Manufacturing?
High-Speed Steel (HSS) is designed for high-performance applications where durability and heat resistance are paramount. It is commonly used in cutting tools and blades that need to withstand high temperatures generated during operation.
Pros: HSS is incredibly tough and maintains its hardness even at elevated temperatures. This makes it suitable for high-speed applications.
Cons: The cost of HSS is generally higher than that of stainless or carbon steel, and it can be more challenging to manufacture due to its hardness.
Impact on Application: HSS is particularly effective in machining and cutting operations, where it can handle tough materials without losing its edge.
Considerations for International Buyers: Buyers should ensure that HSS complies with standards like ASTM A600. Additionally, sourcing from reputable suppliers is essential to guarantee quality and performance.
When Should Composite Materials Be Considered for Blade Customization?
Composite Materials, such as carbon fiber reinforced polymers, are increasingly being used in blade manufacturing due to their lightweight nature and high strength-to-weight ratio.
Pros: Composites can provide excellent performance in terms of weight reduction and corrosion resistance. They are also customizable in terms of shape and design.
Cons: The main limitation is the higher cost and complexity of manufacturing. Composites may also have lower impact resistance compared to metals.
Impact on Application: Composites are ideal for applications where weight is a critical factor, such as in aerospace or automotive industries. However, they may not be suitable for heavy-duty industrial applications.
Considerations for International Buyers: Buyers should verify compliance with relevant standards and certifications, particularly in industries with strict safety regulations. Understanding local market preferences for composite materials is also essential.
Summary Table of Material Selection for Blade Customization
Material | Typical Use Case for blade custom | Key Advantage | Key Disadvantage/Limitation | Relative Cost (Low/Med/High) |
---|---|---|---|---|
Stainless Steel | Food processing, chemical industries | Excellent corrosion resistance | More challenging to machine | Medium |
Carbon Steel | Industrial knives, surgical blades | Maintains sharp edges | Susceptible to corrosion | Low |
High-Speed Steel | Cutting tools, machining applications | Toughness and heat resistance | Higher cost, manufacturing complexity | High |
Composite Materials | Aerospace, automotive applications | Lightweight and customizable | Higher cost, lower impact resistance | High |
This guide provides a comprehensive overview of material options for custom blades, enabling international B2B buyers to make informed decisions based on performance requirements, application compatibility, and compliance considerations.
In-depth Look: Manufacturing Processes and Quality Assurance for blade custom
What Are the Main Stages of Manufacturing Blade Custom Products?
The manufacturing of custom blades is a multifaceted process that involves several critical stages to ensure the final product meets the specific needs of international B2B buyers. Here’s a detailed look at the main stages:
1. Material Preparation
The foundation of any high-quality blade begins with the selection of materials. Manufacturers typically use high-carbon steel, stainless steel, or specialized alloys, depending on the intended use of the blade. The material preparation stage involves:
- Material Selection: Evaluating the specific requirements such as hardness, corrosion resistance, and flexibility.
- Cutting and Shaping: Raw materials are cut into manageable sizes and shapes using techniques like laser cutting or water jet cutting, ensuring precision for subsequent processes.
2. Forming Techniques
Once the materials are prepared, the forming stage shapes the blade into its final design. Common techniques include:
- Forging: This process involves shaping metal using compressive forces, which enhances the material’s strength and durability.
- Casting: In scenarios where complex shapes are required, casting allows for the pouring of molten metal into molds.
Each technique has its advantages and is selected based on the required blade characteristics.
3. Assembly
For blades that require multiple components, the assembly stage is crucial. This may involve:
- Welding: Joining different parts of the blade, such as the handle and blade, using various welding techniques to ensure a robust connection.
- Mechanical Fastening: Using screws or rivets for blades that need to be disassembled or repaired easily.
4. Finishing
The finishing stage significantly impacts the blade’s performance and aesthetic appeal. Key processes include:
- Grinding and Polishing: Achieving the desired sharpness and surface finish through grinding, followed by polishing to enhance corrosion resistance and visual appeal.
- Coating: Applying protective coatings can increase durability and resistance to environmental factors.
How Is Quality Assurance Implemented in Blade Custom Manufacturing?
Quality assurance (QA) is paramount in the manufacturing process of custom blades, ensuring that the final products meet international standards and customer expectations. Here’s how QA is typically implemented:
Understanding International Standards for Quality Assurance
For B2B buyers, familiarity with quality standards is essential. The most relevant international standards include:
- ISO 9001: This standard focuses on quality management systems and is applicable across various industries, ensuring that manufacturers maintain consistent quality.
- CE Marking: Particularly significant for products sold within the European Economic Area, CE marking indicates compliance with health, safety, and environmental protection standards.
- API Standards: For blades used in the oil and gas industry, API standards ensure that products meet specific safety and operational criteria.
What Are the Key QC Checkpoints During the Manufacturing Process?
To maintain high-quality standards, manufacturers implement several Quality Control (QC) checkpoints throughout the manufacturing process:
1. Incoming Quality Control (IQC)
Before production begins, IQC is conducted to ensure that raw materials meet specified requirements. This includes:
- Material Inspection: Assessing the quality of incoming materials through documentation and physical inspection.
- Supplier Verification: Ensuring that suppliers comply with relevant standards and certifications.
2. In-Process Quality Control (IPQC)
During manufacturing, IPQC involves continuous monitoring of the production process. Key activities include:
- Process Monitoring: Checking parameters such as temperature and pressure during forging or casting.
- Dimensional Inspection: Ensuring that components meet design specifications using precision measuring tools.
3. Final Quality Control (FQC)
After the blades are manufactured, FQC is critical to verify that they meet all quality standards. This involves:
- Functional Testing: Assessing the performance of the blades in real-world conditions.
- Visual Inspection: Looking for any surface defects or inconsistencies.
How Can B2B Buyers Verify Supplier Quality Control Practices?
For international B2B buyers, especially those from regions like Africa, South America, the Middle East, and Europe, verifying a supplier’s quality control practices is essential. Here are actionable steps:
Conducting Supplier Audits
Regular audits can provide insight into a supplier’s manufacturing processes and adherence to quality standards. This includes:
- On-Site Visits: Observing production processes, QC checkpoints, and overall facility conditions.
- Documentation Review: Examining quality management documents, including ISO certifications and inspection reports.
Requesting Quality Control Reports
Buyers should request detailed QC reports that outline:
- Testing Methods: Information on the types of tests conducted and their results.
- Compliance Records: Documentation proving adherence to international standards.
Utilizing Third-Party Inspection Services
Engaging third-party inspection services can add an extra layer of assurance. These services can provide:
- Impartial Assessments: Independent verification of product quality and supplier processes.
- Expert Insights: Recommendations on potential improvements or compliance issues.
What Are the Quality Control and Certification Nuances for International B2B Buyers?
Navigating the landscape of quality control and certifications can be challenging for B2B buyers, particularly those from diverse regions. Here are some nuances to consider:
- Regional Regulations: Different regions may have specific quality requirements. For example, European standards may differ from those in Africa or South America.
- Certification Validity: Buyers should ensure that any certifications presented by suppliers are current and recognized in their respective markets.
- Cultural Considerations: Understanding the local manufacturing culture can provide insights into potential quality issues or strengths.
By focusing on these aspects of manufacturing processes and quality assurance, international B2B buyers can make informed decisions when sourcing custom blades, ensuring they receive high-quality products that meet their specific needs.
Practical Sourcing Guide: A Step-by-Step Checklist for ‘blade custom’
Introduction
Navigating the procurement of custom blades can be complex, particularly for international B2B buyers. This step-by-step checklist aims to provide a practical approach to sourcing custom blades, focusing on essential actions that ensure quality, compliance, and value. By following these steps, businesses in regions such as Africa, South America, the Middle East, and Europe can streamline their sourcing process and enhance their purchasing decisions.
Step 1: Define Your Technical Specifications
Clearly outlining your technical specifications is critical to finding the right custom blade supplier. Consider factors such as blade material, dimensions, intended use, and any industry standards that must be met. This clarity will not only help suppliers understand your needs but also enable you to compare offerings effectively.
- Material Requirements: Specify if you need stainless steel, carbon steel, or specialty materials.
- Dimensional Tolerances: Detail the required thickness, length, and any specific design features.
Step 2: Conduct Market Research for Suppliers
Before selecting a supplier, conduct thorough market research to identify potential candidates. Utilize online directories, industry trade shows, and professional networks to find suppliers with a strong reputation in custom blade manufacturing.
- Check Reviews and Ratings: Look for feedback from other businesses to gauge reliability and product quality.
- Identify Local vs. International Options: Consider the advantages of local suppliers, such as reduced shipping times and costs.
Step 3: Evaluate Potential Suppliers
Before committing, it’s crucial to vet suppliers thoroughly. Request company profiles, case studies, and references from buyers in a similar industry or region. Don’t just rely on their website.
- Request Product Samples: If feasible, ask for samples to evaluate quality firsthand.
- Assess Production Capabilities: Ensure the supplier can meet your volume and customization requirements.
Step 4: Verify Supplier Certifications and Compliance
Ensure that potential suppliers hold relevant certifications that meet international standards for safety and quality. This is particularly important in industries where compliance is critical, such as aerospace or medical.
- ISO Certifications: Check for ISO 9001 or other relevant quality management certifications.
- Regulatory Compliance: Verify adherence to local regulations in your target market.
Step 5: Negotiate Terms and Pricing
Once you have shortlisted suppliers, initiate discussions around pricing, payment terms, and delivery timelines. Be clear about your budget constraints and seek transparency in pricing to avoid hidden costs.
- Request a Detailed Quotation: Ensure the quotation includes all potential costs, such as shipping and taxes.
- Discuss Payment Methods: Determine acceptable payment methods and any required deposits.
Step 6: Establish Communication Channels
Effective communication is vital for successful sourcing. Establish clear channels for ongoing dialogue with your chosen supplier to address any issues that may arise.
- Designate a Point of Contact: Ensure there is a specific person responsible for communication on both sides.
- Set Regular Updates: Agree on a schedule for progress reports and updates during production.
Step 7: Plan for Quality Assurance and Feedback
Before finalizing your order, develop a plan for quality assurance and post-purchase feedback. This will help you evaluate the supplier’s performance and product quality over time.
- Implement Inspection Protocols: Define how and when products will be inspected upon arrival.
- Solicit Feedback from Users: Gather input from end-users to assess the performance of the blades in real-world applications.
By following this practical checklist, B2B buyers can effectively navigate the complexities of sourcing custom blades, ensuring they make informed decisions that align with their operational needs and business objectives.
Comprehensive Cost and Pricing Analysis for blade custom Sourcing
What Are the Key Cost Components in Blade Custom Sourcing?
Understanding the cost structure of blade custom sourcing is crucial for international B2B buyers looking to optimize their procurement processes. The primary cost components include:
-
Materials: The type of materials selected significantly impacts the overall cost. High-performance materials may command a premium, but they often result in longer-lasting products that can reduce overall maintenance costs.
-
Labor: Labor costs vary widely by region. Countries with lower wage structures may offer more competitive pricing, but it’s essential to consider the skill level and training of the workforce, which can affect product quality.
-
Manufacturing Overhead: This includes costs related to the factory’s operation, such as utilities, rent, and administrative expenses. Efficient manufacturing processes can lower overhead, enabling suppliers to offer better pricing.
-
Tooling: Custom tooling can be a significant upfront cost, especially for specialized blade designs. However, this investment is often justified by the precision and efficiency it brings to production.
-
Quality Control (QC): Robust QC processes ensure product reliability and adherence to specifications, but they also add to the overall cost. Buyers should assess the level of QC required for their specific applications.
-
Logistics: Shipping costs can vary greatly based on distance, mode of transportation, and urgency. Understanding the logistics involved is essential for accurate cost forecasting.
-
Margin: Suppliers typically mark up their costs to ensure profitability. This margin can be influenced by market demand, competition, and the supplier’s pricing strategy.
How Do Price Influencers Affect Blade Custom Sourcing Costs?
Several factors can influence pricing in blade custom sourcing, and understanding these can help buyers make informed decisions:
-
Volume/MOQ: Larger orders often lead to better pricing due to economies of scale. Buyers should negotiate minimum order quantities (MOQs) to leverage volume discounts.
-
Specifications and Customization: Custom designs and specifications can increase costs due to additional engineering and production complexities. Buyers should clarify their needs upfront to avoid unexpected expenses.
-
Materials: The choice of materials can significantly affect pricing. Buyers should evaluate the trade-offs between cost and performance to ensure they are making the best choice for their applications.
-
Quality and Certifications: Products that meet international standards or come with certifications may be priced higher. However, these certifications can also reduce long-term risks associated with product failures.
-
Supplier Factors: The supplier’s location, reputation, and production capacity can influence pricing. Buyers should conduct thorough due diligence to select reliable suppliers.
-
Incoterms: The chosen Incoterms (International Commercial Terms) can affect the total landed cost. Understanding these terms can help buyers avoid unexpected charges related to shipping and customs.
What Are the Best Buyer Tips for Cost-Efficiency in Blade Custom Sourcing?
B2B buyers can adopt several strategies to enhance cost-efficiency in blade custom sourcing:
-
Negotiation Strategies: Engage suppliers in open discussions about pricing and be prepared to negotiate terms. Establishing a partnership can lead to better pricing arrangements over time.
-
Total Cost of Ownership (TCO): Consider all costs associated with the product, including maintenance, logistics, and disposal, rather than just the upfront purchase price. This holistic view can reveal more cost-effective options.
-
Understanding Pricing Nuances: Buyers from diverse regions—such as Africa, South America, the Middle East, and Europe—should be aware of regional pricing strategies and market conditions. Tailoring your approach to local contexts can provide leverage in negotiations.
-
Leverage Technology: Utilize procurement tools and platforms that can help you analyze pricing trends and supplier performance. This data-driven approach can lead to better sourcing decisions.
Are There Any Price Disclaimer Considerations to Keep in Mind?
While the insights provided can guide buyers in their sourcing decisions, it’s essential to recognize that prices can vary widely based on market conditions, supplier capabilities, and specific project requirements. Therefore, it is advisable to obtain detailed quotes from multiple suppliers and to remain flexible in your sourcing strategy to adapt to changing circumstances.
Alternatives Analysis: Comparing blade custom With Other Solutions
When considering the implementation of ‘blade custom’, it is crucial to evaluate alternative solutions that may meet the same needs or challenges. Understanding the strengths and weaknesses of each option can help international B2B buyers from regions such as Africa, South America, the Middle East, and Europe make informed decisions. Below is a detailed comparison of ‘blade custom’ against two viable alternatives: 3D Printing and Traditional Manufacturing.
Comparison Aspect | Blade Custom | 3D Printing | Traditional Manufacturing |
---|---|---|---|
Performance | High precision, tailored designs | Moderate precision, limited material options | High volume, consistent quality |
Cost | Moderate initial investment, variable long-term costs | Lower initial costs, but material costs can add up | High initial investment, economies of scale reduce unit costs |
Ease of Implementation | Requires specialized skills | User-friendly software, but needs training | Complex setup, labor-intensive |
Maintenance | Low maintenance, but skilled technicians needed | Minimal maintenance, technology-dependent | High maintenance, often requires skilled labor |
Best Use Case | Custom, low-volume production | Prototyping and complex geometries | High-volume, standardized production |
What Are the Advantages and Disadvantages of 3D Printing Compared to Blade Custom?
3D Printing offers flexibility in design and rapid prototyping capabilities, making it ideal for businesses needing quick iterations. However, it typically has limitations in material choices and may not achieve the same level of precision as blade custom solutions. The initial investment is lower, which can be attractive for startups or smaller companies. Yet, as material costs accumulate, long-term expenditures can rise significantly.
How Does Traditional Manufacturing Compare to Blade Custom?
Traditional Manufacturing is well-suited for high-volume production, ensuring consistent quality and lower per-unit costs when scaled. This method is advantageous for established companies with a robust supply chain and the ability to handle complex setups. However, it often involves higher initial investments and can be less adaptable to changes in design or production processes. Additionally, the maintenance demands and reliance on skilled labor can be considerable drawbacks, especially in regions where skilled workers are scarce.
How Can B2B Buyers Choose the Right Solution for Their Needs?
Choosing the right solution depends on several factors, including budget, production volume, and the specific requirements of the project. For businesses that prioritize customization and precision in low-volume production, blade custom may be the best fit. Conversely, if rapid prototyping and flexibility are paramount, 3D printing could provide the necessary advantages. For companies focused on scaling production while maintaining cost-efficiency, traditional manufacturing may be the most suitable choice.
In conclusion, a thorough understanding of the alternatives to blade custom allows B2B buyers to align their production strategies with their operational goals. By considering performance, cost, ease of implementation, maintenance, and best use cases, decision-makers can make informed choices that drive efficiency and profitability in their operations.
Essential Technical Properties and Trade Terminology for blade custom
What Are the Essential Technical Properties for Custom Blades?
When sourcing custom blades, understanding the critical technical properties is vital for ensuring the product meets your specific operational needs. Here are several key specifications:
1. Material Grade: Why Is It Important?
The material grade of a blade significantly influences its durability, performance, and application suitability. Common materials include high-carbon steel, stainless steel, and specialized alloys. Each grade has its unique properties, such as resistance to corrosion, wear, and heat. For instance, stainless steel blades are ideal for food processing due to their hygienic properties, while high-carbon steel blades may be preferred in woodworking applications for their sharpness and edge retention.
2. Tolerance: How Does It Affect Performance?
Tolerance refers to the permissible limit of variation in a blade’s dimensions. It is critical in applications requiring precision, such as aerospace or medical devices. Tight tolerances ensure that blades fit seamlessly with other components, enhancing overall system reliability. Failure to meet specified tolerances can lead to operational inefficiencies or product failures, making it essential for B2B buyers to verify these specifications with suppliers.
3. Hardness: What Role Does It Play?
Hardness measures a material’s resistance to deformation and wear. It is typically assessed using the Rockwell or Brinell scales. A harder blade can maintain its cutting edge longer but may be more brittle, making it susceptible to chipping. Understanding the hardness level required for your application helps in selecting a blade that balances durability and performance.
4. Coating: How Can It Enhance Blade Performance?
Coatings, such as titanium nitride or Teflon, are applied to blades to enhance their properties, including wear resistance and reduced friction. These coatings can also provide additional benefits like corrosion resistance and improved cutting efficiency. Buyers should consider whether a coated blade is necessary for their specific operational conditions, particularly in harsh environments.
5. Edge Geometry: What Should You Consider?
The edge geometry of a blade impacts its cutting efficiency and application suitability. Common geometries include straight, serrated, and beveled edges. Each design serves different purposes: for example, serrated edges are ideal for cutting through tough materials, while straight edges provide cleaner cuts. Understanding the right edge geometry for your application can optimize performance and reduce operational costs.
What Trade Terminology Should B2B Buyers Understand for Blade Customization?
Familiarity with industry terminology can streamline communication and negotiation processes. Here are some essential terms:
1. OEM (Original Equipment Manufacturer): What Does It Mean?
OEM refers to companies that produce parts or equipment that may be marketed by another manufacturer. When discussing custom blades, understanding OEM relationships can help buyers ensure that they are sourcing quality products that meet industry standards.
2. MOQ (Minimum Order Quantity): Why Is It Relevant?
MOQ is the smallest quantity of a product that a supplier is willing to sell. Knowing the MOQ is crucial for budgeting and inventory management. For international buyers, especially those from Africa and South America, negotiating MOQs can lead to cost savings and more efficient supply chain management.
3. RFQ (Request for Quotation): How Should It Be Used?
An RFQ is a document sent to suppliers to solicit price quotes for specific products or services. It is an essential tool for B2B buyers to compare pricing, terms, and capabilities from different suppliers. A well-crafted RFQ can lead to more accurate responses and better negotiation outcomes.
4. Incoterms: What Are They and Why Do They Matter?
Incoterms are international commercial terms that define the responsibilities of buyers and sellers in global trade. They clarify who bears the risk and costs associated with shipping, insurance, and customs clearance. Understanding Incoterms is vital for B2B buyers to avoid unexpected charges and ensure smooth logistics.
5. Lead Time: How Does It Impact Your Supply Chain?
Lead time refers to the amount of time it takes from placing an order to receiving the product. It is a critical factor in supply chain management, as longer lead times can disrupt production schedules. B2B buyers should inquire about lead times during negotiations to align their purchasing strategy with operational needs.
By grasping these technical properties and trade terms, international B2B buyers can make more informed decisions when sourcing custom blades, ultimately leading to improved operational efficiency and cost-effectiveness.
Navigating Market Dynamics and Sourcing Trends in the blade custom Sector
What Are the Key Market Dynamics and Trends in the Blade Custom Sector?
The blade custom sector is experiencing a significant transformation driven by various global factors. The increasing demand for precision-engineered components in industries such as aerospace, automotive, and renewable energy is propelling market growth. International B2B buyers from Africa, South America, the Middle East, and Europe should be particularly aware of the rising technological advancements, including automation and digitalization, that are reshaping sourcing strategies. For instance, the integration of AI and IoT in manufacturing processes is enhancing efficiency and reducing lead times, which is crucial for buyers looking for reliable supply chains.
Moreover, customization is becoming a key trend, with buyers increasingly seeking tailored solutions that meet specific operational requirements. This trend is driven by the need for competitive differentiation in diverse markets. Additionally, sustainability is now a top priority, as more companies are adopting eco-friendly practices to meet regulatory requirements and consumer expectations. This shift is particularly relevant for buyers in regions such as Europe, where stringent environmental regulations are influencing sourcing decisions.
How Can Sustainability and Ethical Sourcing Impact the Blade Custom Sector?
Sustainability and ethical sourcing have emerged as critical considerations in the blade custom sector. The environmental impact of manufacturing processes has led to a growing emphasis on sustainable practices. International B2B buyers must evaluate suppliers based on their commitment to reducing carbon footprints and utilizing renewable resources. This involves sourcing materials that are certified as sustainable, which can enhance brand reputation and appeal to environmentally-conscious consumers.
Furthermore, ethical supply chains are gaining traction. Buyers should prioritize partnerships with suppliers who adhere to fair labor practices and transparent operations. Certifications such as ISO 14001 for environmental management and Fair Trade can serve as indicators of a supplier’s commitment to sustainability and ethical standards. By aligning with these principles, buyers not only contribute to global sustainability efforts but also mitigate risks associated with supply chain disruptions due to regulatory changes or reputational damage.
What Is the Historical Context of the Blade Custom Sector’s Development?
The blade custom sector has evolved significantly over the past few decades. Initially dominated by traditional manufacturing methods, the industry has gradually embraced technological advancements that have revolutionized production capabilities. The introduction of CNC (Computer Numerical Control) machines in the late 20th century marked a turning point, allowing for higher precision and the ability to produce complex designs.
In recent years, the industry has seen a shift towards more agile manufacturing practices, driven by the need for customization and shorter lead times. This evolution is essential for B2B buyers to understand, as it highlights the importance of choosing suppliers who are not only technologically adept but also capable of adapting to market demands. Understanding this historical context provides valuable insight into current trends and the future trajectory of the blade custom sector.
By staying informed about these market dynamics and sourcing trends, international B2B buyers can make strategic decisions that enhance their competitive edge while promoting sustainability and ethical practices.
Frequently Asked Questions (FAQs) for B2B Buyers of blade custom
-
How do I solve issues with blade custom quality control?
To address quality control issues in blade custom manufacturing, establish clear quality standards and specifications with your supplier from the outset. Implement regular quality assurance checks during production and conduct final inspections before shipment. Additionally, consider partnering with third-party inspection agencies that specialize in your industry to validate the quality of materials and craftsmanship. This proactive approach helps mitigate risks associated with defects and ensures that the blades meet your operational requirements. -
What is the best approach for sourcing blade custom suppliers internationally?
When sourcing blade custom suppliers internationally, start by conducting thorough market research to identify reputable manufacturers in your target regions, such as Africa, South America, the Middle East, and Europe. Utilize online platforms, trade shows, and industry networks to find potential suppliers. Evaluate their credentials, certifications, and past customer reviews. It’s also beneficial to request samples and visit production facilities if possible, to assess their capabilities and quality firsthand. -
What should I consider when negotiating payment terms for blade custom orders?
Negotiating payment terms for blade custom orders requires a balance between security and flexibility. Common terms include upfront deposits, milestone payments based on production stages, and net payment terms upon delivery. Assess the financial stability of your supplier and consider using secure payment methods such as letters of credit to mitigate risks. Additionally, clarify terms regarding any potential delays or quality issues to protect your investment. -
What are the typical minimum order quantities (MOQ) for blade custom production?
Minimum order quantities (MOQ) for blade custom production can vary widely based on the supplier, the complexity of the design, and the materials used. Generally, MOQs may range from a few dozen to several hundred units. When negotiating MOQs, consider your budget, storage capabilities, and demand forecasts. Some suppliers may be willing to accommodate lower MOQs for first-time buyers or offer flexible arrangements for repeat orders, so open communication is key. -
How can I ensure timely logistics and delivery for my blade custom orders?
To ensure timely logistics and delivery, work closely with your supplier to establish a clear production timeline and shipping schedule. Choose reliable logistics partners with experience in international shipping, especially if you are importing from regions like Africa or South America. Utilize tracking systems to monitor shipment progress and communicate proactively with your supplier about any potential delays. Additionally, consider customs regulations and clearance times in your planning to avoid unexpected hold-ups. -
What are the key factors to consider in blade custom design and customization?
When considering blade custom design and customization, focus on functionality, material selection, and intended application. Collaborate closely with your supplier to discuss specific design requirements, including dimensions, coatings, and durability needs. It’s crucial to provide detailed specifications and prototypes if possible. Consider engaging in a design review process to ensure that the final product aligns with your operational standards and performance expectations. -
How do I vet blade custom suppliers to ensure reliability and quality?
Vetting blade custom suppliers involves checking their industry experience, certifications, and references. Conduct background research on their business history and customer feedback, and request case studies or examples of previous work. Assess their production capabilities, technology used, and quality control processes. Engaging in an initial small-scale order can also serve as a practical trial to evaluate their reliability and quality before committing to larger orders. -
What are the common challenges faced in international trade for blade custom products?
Common challenges in international trade for blade custom products include navigating different regulatory environments, customs clearance issues, and varying quality standards. Additionally, fluctuations in exchange rates and shipping costs can impact overall expenses. To mitigate these challenges, stay informed about trade regulations in your target markets, work with experienced logistics providers, and consider purchasing insurance for shipments. Building strong relationships with suppliers and logistics partners can also enhance your ability to manage these challenges effectively.
Important Disclaimer & Terms of Use
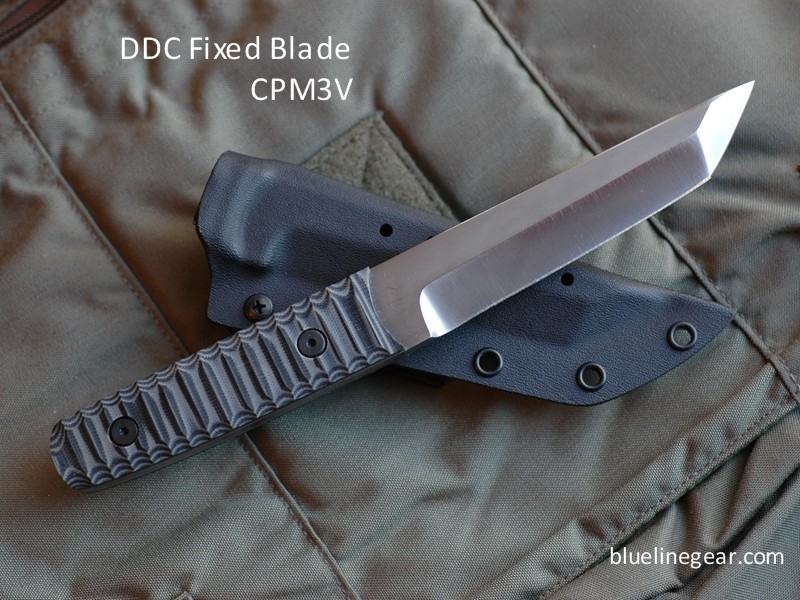
A stock image related to blade custom.
⚠️ Important Disclaimer
The information provided in this guide, including content regarding manufacturers, technical specifications, and market analysis, is for informational and educational purposes only. It does not constitute professional procurement advice, financial advice, or legal advice.
While we have made every effort to ensure the accuracy and timeliness of the information, we are not responsible for any errors, omissions, or outdated information. Market conditions, company details, and technical standards are subject to change.
B2B buyers must conduct their own independent and thorough due diligence before making any purchasing decisions. This includes contacting suppliers directly, verifying certifications, requesting samples, and seeking professional consultation. The risk of relying on any information in this guide is borne solely by the reader.
Strategic Sourcing Conclusion and Outlook for blade custom
In the evolving landscape of blade custom sourcing, businesses must prioritize strategic sourcing to enhance their competitive edge. Key takeaways highlight the importance of understanding regional market dynamics, particularly in Africa, South America, the Middle East, and Europe. By leveraging local suppliers and establishing robust relationships, international B2B buyers can mitigate risks and optimize supply chain efficiency.
How Can Strategic Sourcing Drive Value in Blade Custom Procurement?
Strategic sourcing not only reduces costs but also enables companies to access innovative solutions tailored to specific needs. Emphasizing quality and compliance with international standards ensures that buyers receive superior products that align with their operational requirements. As sustainability becomes increasingly critical, sourcing from environmentally responsible manufacturers can also enhance brand reputation and customer loyalty.
What Does the Future Hold for International B2B Buyers in Blade Custom?
Looking ahead, the demand for customized blades is expected to grow, driven by advancements in technology and manufacturing processes. Buyers are encouraged to stay informed about industry trends and emerging markets, particularly in regions like Nigeria and France, where opportunities abound. By adopting a proactive approach to sourcing and fostering collaborative partnerships, businesses can position themselves for success in the dynamic blade custom market. Engage with suppliers today to explore the possibilities of tailored solutions that meet your unique business needs.