Cut Costs with the Best Tool Kit Manufacturer Guide (2025)
Introduction: Navigating the Global Market for tool kit manufacturer
Navigating the global market for tool kit manufacturers presents a unique set of challenges for international B2B buyers, particularly those sourcing from diverse regions such as Africa, South America, the Middle East, and Europe. The complexity of identifying reliable suppliers, ensuring product quality, and managing logistics can often feel overwhelming. This guide is designed to streamline your procurement process by providing comprehensive insights into the types of tool kits available, their various applications across industries, and effective supplier vetting strategies.
Throughout this guide, we will explore essential factors to consider when selecting a tool kit manufacturer, including cost analysis, quality assurance measures, and compliance with international standards. Each section aims to empower you with actionable strategies, helping you make informed purchasing decisions that align with your operational needs and budget constraints.
By addressing critical questions such as “How do I assess the quality of tool kits?” and “What are the best practices for negotiating with manufacturers?”, this resource serves as a valuable tool for enhancing your procurement efforts. Whether you are looking to source specialized tool kits for construction, automotive, or industrial applications, this guide is tailored to equip you with the knowledge necessary to navigate the complexities of the global market successfully.
Understanding tool kit manufacturer Types and Variations
Type Name | Key Distinguishing Features | Primary B2B Applications | Brief Pros & Cons for Buyers |
---|---|---|---|
OEM Tool Kit Manufacturers | Customization options, specialized designs | Automotive, electronics, heavy machinery | Pros: Tailored solutions, high-quality standards. Cons: Longer lead times, potentially higher costs. |
Aftermarket Tool Kit Manufacturers | Cost-effective alternatives, wide availability | Repair services, DIY markets | Pros: Lower prices, extensive product range. Cons: Variable quality, less customization. |
Industrial Tool Kit Manufacturers | Heavy-duty materials, comprehensive sets | Manufacturing, construction | Pros: Durability, high performance. Cons: Higher initial investment, bulk purchasing required. |
Specialized Tool Kit Manufacturers | Niche products for specific trades | Aviation, medical, telecommunications | Pros: Precision engineering, tailored for specific tasks. Cons: Limited availability, higher costs. |
Consumer Tool Kit Manufacturers | Basic tools, user-friendly designs | Retail, home improvement | Pros: Affordable, widely accessible. Cons: Less durable, not suitable for professional use. |
What Are OEM Tool Kit Manufacturers and Their B2B Relevance?
OEM (Original Equipment Manufacturer) tool kit manufacturers focus on producing customized tool kits tailored to the specific needs of their clients. These manufacturers often work closely with businesses in sectors like automotive and electronics, providing specialized designs that meet rigorous industry standards. B2B buyers should consider OEM options when seeking high-quality tools that can enhance their production processes, although they should be prepared for potentially longer lead times and higher costs associated with customization.
How Do Aftermarket Tool Kit Manufacturers Serve B2B Buyers?
Aftermarket tool kit manufacturers provide cost-effective alternatives to OEM products, often featuring a wide range of tools that cater to repair services and DIY markets. These manufacturers focus on delivering affordable solutions without compromising functionality. B2B buyers, especially in regions with budget constraints, can benefit from these options. However, they should be aware of the variability in quality, which can affect performance and longevity.
What Are the Characteristics of Industrial Tool Kit Manufacturers?
Industrial tool kit manufacturers specialize in producing heavy-duty tools designed to withstand the rigors of manufacturing and construction environments. Their products typically include comprehensive sets that support various industrial applications. For B2B buyers, the durability and high performance of these tools can lead to increased efficiency and reduced downtime. However, the initial investment may be higher, and bulk purchasing may be required, which could be a consideration for smaller businesses.
How Do Specialized Tool Kit Manufacturers Cater to Niche Markets?
Specialized tool kit manufacturers focus on creating products for specific trades, such as aviation, medical, or telecommunications. These manufacturers offer precision-engineered tools that are tailored for niche applications, ensuring that they meet the exacting standards of their respective industries. B2B buyers in these fields should consider these manufacturers for their unique requirements, though they may face limited availability and higher costs compared to more generalized options.
What Should Buyers Know About Consumer Tool Kit Manufacturers?
Consumer tool kit manufacturers produce basic tool kits that are user-friendly and widely accessible, often targeted toward retail and home improvement markets. These products are typically affordable and cater to individuals rather than professionals. B2B buyers in industries that rely on budget-conscious solutions may find value in these kits. However, they should note that consumer-grade tools may lack the durability required for professional use, making them unsuitable for demanding applications.
Related Video: TOP 5 POWER TOOL BRANDS IN THE WORLD! (best of the best)
Key Industrial Applications of tool kit manufacturer
Industry/Sector | Specific Application of Tool Kit Manufacturer | Value/Benefit for the Business | Key Sourcing Considerations for this Application |
---|---|---|---|
Automotive | Maintenance and Repair Tool Kits | Enhanced efficiency in vehicle servicing and reduced downtime. | Quality standards, compatibility with various vehicle models. |
Construction | Construction Tool Kits for Site Projects | Streamlined operations and improved project timelines. | Durability, compliance with safety regulations, and local availability. |
Electronics Manufacturing | Precision Tool Kits for Assembly and Repair | Increased accuracy and reduced errors in electronic assembly. | Precision requirements, certifications for electronic components. |
Aerospace | Specialized Tool Kits for Aircraft Maintenance | Improved safety and compliance with stringent aviation standards. | Certification for aerospace use, lightweight materials, and portability. |
Oil and Gas | Tool Kits for Field Operations and Maintenance | Enhanced operational efficiency and reduced maintenance costs. | Resistance to harsh environments, local sourcing, and certification. |
How Are Tool Kits Used in the Automotive Industry?
In the automotive sector, tool kits are essential for maintenance and repair activities. They typically include wrenches, screwdrivers, and diagnostic tools designed for specific vehicle models. By providing mechanics with the right tools, these kits help reduce vehicle downtime, thus enhancing service efficiency. For international buyers, especially in regions like Africa and South America, sourcing high-quality tool kits that meet local automotive standards is crucial to ensure compatibility with a diverse range of vehicles.
What Role Do Tool Kits Play in Construction Projects?
Construction tool kits are vital for various site projects, encompassing hand tools and power tools tailored for building and infrastructure work. These kits streamline operations by ensuring that workers have the necessary tools at their fingertips, thereby improving productivity and project timelines. For buyers in the Middle East and Europe, it is important to consider the durability and compliance of tool kits with local safety regulations, as these factors significantly impact worker safety and project success.
Why Are Precision Tool Kits Important in Electronics Manufacturing?
In electronics manufacturing, precision tool kits are crucial for assembly and repair tasks. These kits often include specialized tools designed to handle delicate components with accuracy, minimizing the risk of damage. For businesses in Europe and South America, ensuring that these tools meet rigorous quality standards and certifications is essential for maintaining production efficiency and product quality. Buyers must also consider the specific requirements of their manufacturing processes when sourcing these tool kits.
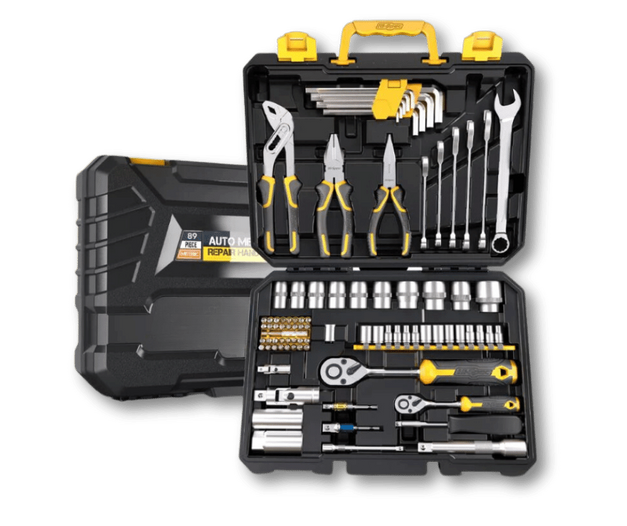
A stock image related to tool kit manufacturer.
How Do Specialized Tool Kits Benefit the Aerospace Sector?
The aerospace industry requires specialized tool kits tailored for aircraft maintenance. These kits must comply with strict aviation safety standards and include lightweight, durable tools that facilitate easy handling in confined spaces. For B2B buyers in Africa and the Middle East, sourcing such specialized tool kits requires a focus on certification for aerospace use, ensuring that all tools meet regulatory requirements. This not only enhances safety but also ensures compliance with international aviation standards.
What Are the Key Considerations for Tool Kits in Oil and Gas Operations?
In the oil and gas sector, tool kits are essential for field operations and maintenance activities. These kits often include tools designed to withstand harsh environmental conditions, ensuring reliability and efficiency in critical operations. Buyers from regions like Africa and South America must prioritize sourcing tools that are resistant to corrosion and extreme temperatures. Additionally, understanding local sourcing options and obtaining necessary certifications can significantly impact operational efficiency and cost-effectiveness in this challenging industry.
Related Video: CLEVER things to do with an Oscillating Multi-Tool!
3 Common User Pain Points for ‘tool kit manufacturer’ & Their Solutions
Scenario 1: Sourcing Quality Tool Kits for Diverse Needs
The Problem: B2B buyers often struggle to find tool kit manufacturers that offer a diverse range of high-quality tools tailored to specific industry needs. In regions such as Africa and South America, where local suppliers may have limited options, buyers may face difficulty ensuring that the tool kits they purchase meet both international standards and local regulatory requirements. This can lead to project delays, increased costs, and dissatisfaction among end-users who depend on reliable tools for their operations.
The Solution: To effectively source quality tool kits, buyers should begin by conducting thorough research on manufacturers with a proven track record of delivering diverse and compliant products. Utilizing platforms such as Alibaba or Global Sources can help identify manufacturers based on reviews and product offerings. Additionally, establishing direct communication with manufacturers to discuss specific requirements, certifications, and customization options is crucial. Buyers should also consider visiting trade shows or industry exhibitions where manufacturers showcase their products, allowing for firsthand evaluation of quality and suitability. Forming partnerships with manufacturers that have local representation can further ensure that products meet regional needs, enhancing reliability and trust.
Scenario 2: Ensuring Timely Delivery of Tool Kits
The Problem: One significant pain point for B2B buyers is the uncertainty surrounding delivery times when ordering tool kits from international manufacturers. Buyers in regions like the Middle East and Europe may experience delays due to logistics challenges, customs clearance, or unexpected demand fluctuations. Such delays can disrupt project timelines, increase operational costs, and affect client satisfaction.
The Solution: To mitigate delivery issues, B2B buyers should prioritize manufacturers that offer transparent shipping policies and real-time tracking capabilities. When negotiating contracts, it is essential to discuss lead times and set clear expectations regarding delivery schedules. Implementing a buffer period in project timelines can also provide a cushion against potential delays. Additionally, diversifying suppliers by establishing relationships with multiple manufacturers can reduce reliance on a single source and improve supply chain resilience. Buyers should consider local manufacturers or those with regional warehouses to facilitate quicker delivery times and minimize logistical hurdles.
Scenario 3: Customizing Tool Kits for Specific Applications
The Problem: Many B2B buyers face challenges in obtaining tool kits that are customized for specific applications or industries. For example, a construction company in Europe may require specialized tools that are not readily available in standard kits. This lack of customization can lead to inefficiencies, as teams may need to purchase additional tools separately, increasing overall costs and complicating inventory management.
The Solution: To address customization needs, buyers should engage manufacturers that specialize in bespoke tool kit solutions. Communicating specific requirements early in the procurement process is vital. Buyers should prepare a detailed list of necessary tools, including specifications and quantities, to facilitate discussions with manufacturers. Furthermore, requesting prototypes or samples before placing large orders can help ensure that the customized kits meet the intended needs. Establishing long-term partnerships with manufacturers that are willing to adapt their offerings based on buyer feedback can lead to more tailored solutions over time, ultimately enhancing operational efficiency and cost-effectiveness.
Strategic Material Selection Guide for tool kit manufacturer
When selecting materials for tool kit manufacturing, international B2B buyers must consider various factors that influence product performance, durability, and compliance with regional standards. Below is an analysis of four commonly used materials in tool kit manufacturing, focusing on their properties, advantages, disadvantages, and specific considerations for buyers from Africa, South America, the Middle East, and Europe.
What Are the Key Properties of Steel in Tool Kit Manufacturing?
Steel is one of the most widely used materials in tool kit manufacturing due to its strength and versatility. Key properties include high tensile strength, excellent hardness, and good temperature resistance, making it suitable for various applications. Steel can withstand high pressures and extreme temperatures, which is critical for tools that require durability under stress.
Pros & Cons:
The primary advantage of steel is its durability and resistance to deformation, which enhances the longevity of tools. However, it is susceptible to corrosion if not properly treated or coated. Additionally, manufacturing processes for steel tools can be complex and costly, especially when high-grade alloys are used.
Impact on Application:
Steel is compatible with a wide range of media, including oils and fuels, but its susceptibility to rust can limit its use in humid or corrosive environments.
Considerations for International Buyers:
Buyers must ensure compliance with international standards such as ASTM and DIN, especially when sourcing steel from different regions. Understanding local regulations regarding material quality and safety is crucial, particularly in markets like Europe and the Middle East.
How Does Aluminum Compare as a Material for Tool Kits?
Aluminum is another popular choice for tool kits, known for its lightweight properties and resistance to corrosion. It has a lower density than steel, making it easier to handle and transport.
Pros & Cons:
The key advantage of aluminum is its excellent corrosion resistance, which makes it ideal for tools used in outdoor or marine environments. However, it is not as strong as steel and can deform under high pressure, which may limit its application for heavy-duty tools.
Impact on Application:
Aluminum tools are particularly suitable for applications involving non-ferrous materials, as they do not cause contamination. However, they may not be the best choice for high-stress applications.
Considerations for International Buyers:
Buyers should be aware of the differing grades of aluminum and their respective standards (e.g., JIS in Japan). Additionally, understanding local preferences for lightweight tools can help in making informed purchasing decisions.
What Are the Benefits of Using Plastic in Tool Kit Manufacturing?
Plastic materials, particularly high-density polyethylene (HDPE) and polycarbonate, are increasingly used in tool kits for their versatility and cost-effectiveness. They are lightweight and resistant to chemicals, making them suitable for various applications.
Pros & Cons:
The primary advantage of plastic is its resistance to corrosion and chemicals, which is beneficial for tools exposed to harsh environments. However, plastics generally have lower strength compared to metals, which may limit their use in heavy-duty applications.
Impact on Application:
Plastic tools are ideal for use in environments where metal tools may corrode or react with chemicals. They are also safer to use in electrical applications due to their insulating properties.
Considerations for International Buyers:
Buyers should check for compliance with local safety standards and regulations regarding plastic materials, especially in Europe, where stringent regulations may apply.
Why Is Composite Material Gaining Popularity in Tool Kit Manufacturing?
Composite materials, which combine two or more different materials, are gaining traction in tool kit manufacturing due to their unique properties. They can offer the strength of metals while maintaining the lightweight characteristics of plastics.
Pros & Cons:
The key advantage of composite materials is their high strength-to-weight ratio, making them suitable for a wide range of applications. However, they can be more expensive to manufacture and may require specialized processing techniques.
Impact on Application:
Composites are particularly effective in applications requiring high strength and low weight, such as aerospace tools or specialized automotive tools.
Considerations for International Buyers:
Buyers should be aware of the specific manufacturing standards for composite materials, which can vary significantly by region. Understanding the lifecycle and recyclability of composites is also crucial for sustainability-focused buyers.
Summary Table of Material Selection for Tool Kit Manufacturers
Material | Typical Use Case for tool kit manufacturer | Key Advantage | Key Disadvantage/Limitation | Relative Cost (Low/Med/High) |
---|---|---|---|---|
Steel | Heavy-duty tools, wrenches, sockets | High durability and strength | Susceptible to corrosion | Medium |
Aluminum | Lightweight tools, portable kits | Excellent corrosion resistance | Lower strength than steel | Medium |
Plastic | Chemical handling tools, safety equipment | Corrosion and chemical resistance | Lower strength for heavy-duty use | Low |
Composite | Specialized tools, aerospace applications | High strength-to-weight ratio | Higher manufacturing costs | High |
This strategic material selection guide equips international B2B buyers with the insights necessary to make informed decisions when sourcing materials for tool kit manufacturing, ensuring compliance and suitability for diverse applications across different regions.
In-depth Look: Manufacturing Processes and Quality Assurance for tool kit manufacturer
What Are the Main Stages of Manufacturing Tool Kits?
The manufacturing process for tool kits involves several critical stages, each designed to ensure that the final product meets quality standards and fulfills customer requirements. Understanding these stages is essential for international B2B buyers to make informed decisions.
1. Material Preparation
The first step in the manufacturing process is material preparation. This stage involves sourcing high-quality raw materials, which can include metals, plastics, and composites. It is crucial for buyers to verify the quality of these materials, as they directly influence the durability and performance of the tool kits. Suppliers should provide certificates of compliance to ensure that materials meet relevant industry standards.
2. Forming
Once the materials are prepared, they undergo forming processes. This can include machining, stamping, or injection molding, depending on the design requirements of the tool kit. Advanced techniques such as computer numerical control (CNC) machining are often employed to achieve precision. Buyers should inquire about the technology used in forming, as this can affect lead times and production costs.
3. Assembly
The assembly stage is where individual components come together to create the final tool kit. This process may involve manual labor or automated systems, depending on the scale of production. For B2B buyers, understanding the assembly techniques used—such as robotic assembly or hand assembly—can provide insights into the supplier’s capabilities and production flexibility.
4. Finishing
Finishing processes, such as surface treatment, coating, and packaging, enhance the aesthetic and functional properties of the tool kits. Treatments like powder coating or anodizing can improve corrosion resistance and durability. Buyers should assess the finishing processes to ensure they align with their expectations for product longevity and appearance.
How Is Quality Assurance Implemented in Tool Kit Manufacturing?
Quality assurance (QA) is a fundamental aspect of tool kit manufacturing that ensures products meet specified standards before reaching the market. For international buyers, understanding the QA process is crucial for minimizing risks associated with product quality.
Relevant International Standards for Tool Kit Manufacturing
International standards such as ISO 9001 play a vital role in quality assurance. ISO 9001 outlines criteria for a quality management system (QMS) and focuses on consistent quality in production. Additionally, industry-specific standards, such as CE marking for the European market or API standards for oilfield tools, are essential for compliance. Buyers should verify that their suppliers adhere to these standards as part of their due diligence.
What Are the Key Quality Control Checkpoints?
Quality control (QC) involves several checkpoints throughout the manufacturing process:
-
Incoming Quality Control (IQC): This initial stage assesses the quality of raw materials before production begins. Suppliers should maintain detailed records of material inspections and tests.
-
In-Process Quality Control (IPQC): During manufacturing, continuous monitoring is conducted to ensure that processes remain within specified limits. This may involve statistical process control (SPC) techniques.
-
Final Quality Control (FQC): Before the tool kits are packaged and shipped, a comprehensive inspection is carried out to check for defects and ensure compliance with specifications.
B2B buyers should request documentation of these QC processes to ensure that suppliers maintain rigorous quality standards.
What Common Testing Methods Are Used in Tool Kit Quality Assurance?
Testing methods play a crucial role in validating the quality and performance of tool kits. Common methods include:
-
Functional Testing: This assesses whether the tool kits operate as intended under normal conditions.
-
Durability Testing: Evaluating how well the tool kits withstand wear and tear over time.
-
Safety Testing: Ensuring compliance with safety standards relevant to the intended use of the tools.
Buyers should inquire about the specific testing methods employed by suppliers and request test reports as part of their quality assurance process.
How Can B2B Buyers Verify Supplier Quality Control?
Verifying a supplier’s quality control processes is essential for mitigating risks associated with poor product quality. Here are some effective strategies for international buyers:
-
Conduct Audits: Regular audits of potential suppliers can provide insights into their manufacturing processes and quality control practices. This can be done through on-site visits or third-party audits.
-
Request Quality Reports: Suppliers should be willing to provide detailed quality assurance reports, including results from IQC, IPQC, and FQC processes.
-
Engage Third-Party Inspectors: Utilizing third-party inspection services can provide an unbiased assessment of product quality before shipment, ensuring that the tool kits meet the buyer’s specifications.
What Are the Quality Control and Certification Nuances for International Buyers?
International B2B buyers need to be aware of specific nuances related to quality control and certifications in their respective regions:
-
Regional Compliance: Different regions may have varying compliance requirements. For instance, products sold in the European market must adhere to CE marking regulations, while those in the Middle East may require compliance with local standards.
-
Documentation and Certification: Buyers should ensure that suppliers provide all necessary documentation and certifications, including material test certificates and compliance statements. This is particularly important for buyers from Africa and South America, where regulatory environments may differ significantly.
-
Cultural Considerations: Understanding cultural nuances related to quality expectations can help buyers communicate effectively with suppliers. Building strong relationships with suppliers can also lead to better quality assurance practices.
Conclusion
In summary, the manufacturing processes and quality assurance protocols for tool kit manufacturers are intricate and essential for delivering high-quality products. International B2B buyers, especially from Africa, South America, the Middle East, and Europe, should take proactive steps to understand these processes, verify supplier credentials, and ensure compliance with relevant standards. By doing so, they can mitigate risks and foster successful partnerships with reliable tool kit manufacturers.
Practical Sourcing Guide: A Step-by-Step Checklist for ‘tool kit manufacturer’
The purpose of this sourcing guide is to provide international B2B buyers with a structured checklist to effectively procure tool kits from manufacturers. This step-by-step approach will ensure that buyers can make informed decisions, minimizing risks and optimizing their procurement process.
Step 1: Define Your Technical Specifications
Before starting your search for a tool kit manufacturer, it’s essential to clearly outline your technical specifications. This includes determining the types of tools required, material preferences, and any specific features that your tool kits must have. Defining these parameters helps streamline your search and ensures that potential suppliers can meet your exact needs.
- Considerations: Think about the intended use of the tool kits and the environment they will be used in. For example, are they for industrial use, DIY projects, or educational purposes?
Step 2: Research Potential Manufacturers
Once you have your specifications, begin researching potential manufacturers. Look for companies that specialize in tool kit production and have a strong reputation in the industry. Utilize online directories, trade shows, and industry publications to compile a list of candidates.
- Where to Search: Platforms like Alibaba, Global Sources, and industry-specific exhibitions can provide valuable insights into manufacturers’ capabilities.
Step 3: Evaluate Supplier Credentials
Before moving forward, it’s crucial to vet potential suppliers thoroughly. Request documentation such as company profiles, relevant certifications, and quality control procedures. This step helps ensure that the suppliers adhere to international standards and regulations.
- Key Certifications: Look for ISO certifications, compliance with safety standards, and any industry-specific qualifications that may apply to your tool kits.
Step 4: Request Samples and Prototypes
To assess the quality of the tool kits, request samples or prototypes from your shortlisted manufacturers. This allows you to evaluate the craftsmanship, durability, and overall functionality of the products before making a larger investment.
- What to Look For: Pay attention to material quality, ergonomic design, and how well the tools perform under simulated conditions.
Step 5: Analyze Pricing and Payment Terms
Pricing is a critical factor in procurement. Analyze the quotes provided by each manufacturer and compare them against your budget and the quality of the samples received. Additionally, review payment terms and conditions to ensure they align with your financial capabilities.
- Considerations: Look for transparency in pricing, including hidden costs such as shipping and customs duties, which can affect your overall expenditure.
Step 6: Negotiate Terms and Conditions
Once you’ve selected a manufacturer, engage in negotiations to finalize the terms of your agreement. This includes discussing lead times, minimum order quantities, warranties, and after-sales support. Clear communication at this stage can prevent misunderstandings later on.
- Negotiation Tips: Be prepared to walk away if terms are not favorable; this can often lead to better offers from the supplier.
Step 7: Establish a Communication Plan
Finally, set up a communication plan with your chosen supplier. Establish regular check-ins to discuss production timelines, quality assurance, and any potential issues that may arise. Effective communication is key to a successful long-term partnership.
- Best Practices: Utilize project management tools to keep track of milestones and ensure that both parties are aligned throughout the production process.
By following this structured checklist, international B2B buyers can navigate the complexities of sourcing tool kits from manufacturers with confidence, ensuring that they make informed decisions that meet their business needs.
Comprehensive Cost and Pricing Analysis for tool kit manufacturer Sourcing
What Are the Key Cost Components in Tool Kit Manufacturing?
Understanding the cost structure of tool kit manufacturing is critical for international B2B buyers seeking to optimize their sourcing strategy. The primary cost components include:
-
Materials: Raw materials, such as metals, plastics, and composites, significantly impact the overall cost. Prices can fluctuate based on global supply chain dynamics and local market conditions, making it essential to establish reliable suppliers.
-
Labor: Labor costs vary widely across regions. For instance, countries in Africa may offer lower labor costs compared to Europe or North America. However, the skill level and availability of labor can affect product quality and production efficiency.
-
Manufacturing Overhead: This encompasses expenses related to facilities, utilities, and equipment maintenance. Overhead can vary based on the manufacturer’s location and operational efficiency.
-
Tooling: The initial setup and tooling costs are crucial for custom tool kit production. High-quality tooling can lead to better precision and reduced defect rates, justifying higher initial investments.
-
Quality Control (QC): Implementing stringent quality control measures ensures product reliability. The costs associated with QC processes can vary based on the complexity of the tool kits being manufactured.
-
Logistics: Transportation and warehousing costs are critical, especially for international shipments. Factors such as distance, shipping method, and the chosen Incoterms can significantly influence these costs.
-
Margin: Manufacturers typically add a markup to cover operational costs and profit margins. This varies by supplier and can be influenced by competitive market dynamics.
How Do Price Influencers Affect Tool Kit Sourcing?
Several factors can influence the pricing of tool kits:
-
Volume/MOQ (Minimum Order Quantity): Larger orders often result in lower per-unit costs due to economies of scale. Buyers should assess their purchasing strategies to leverage bulk discounts.
-
Specifications and Customization: Custom-designed tool kits may incur additional charges for design and production adjustments. Buyers should clearly communicate their requirements to avoid unexpected costs.
-
Materials and Quality Certifications: Higher-quality materials and certifications (e.g., ISO, CE) can increase costs but may be necessary for compliance and market acceptance in certain regions.
-
Supplier Factors: The reputation and reliability of suppliers can impact pricing. Established suppliers may charge a premium for their experience and quality assurance practices.
-
Incoterms: Understanding the implications of different Incoterms is essential. For example, choosing DDP (Delivered Duty Paid) may simplify logistics but could lead to higher upfront costs.
What Tips Can Help B2B Buyers Optimize Their Sourcing Costs?
International B2B buyers can adopt several strategies to ensure cost-efficiency in sourcing tool kits:
-
Negotiate Wisely: Engage suppliers in discussions about pricing, especially if you can commit to larger volumes or longer-term contracts. Building a relationship can also lead to better pricing and terms.
-
Consider Total Cost of Ownership (TCO): Evaluate the complete cost associated with sourcing tool kits, including shipping, duties, and potential delays. A lower purchase price may not always equate to a lower TCO.
-
Understand Pricing Nuances for International Markets: Familiarize yourself with regional pricing trends, currency fluctuations, and local economic conditions in your target markets. This knowledge can help in negotiating better deals.
-
Benchmark Against Competitors: Research competitors’ pricing and sourcing strategies to ensure you are not overpaying. This can provide leverage in negotiations and help identify market trends.
Disclaimer on Indicative Prices
Pricing for tool kits can vary significantly based on the aforementioned factors. It is advisable for buyers to conduct thorough market research and obtain multiple quotes from suppliers to establish a fair price range. Always consider the unique requirements of your business and the specific market conditions in your region.
Alternatives Analysis: Comparing tool kit manufacturer With Other Solutions
Understanding Alternatives to Tool Kit Manufacturers
In the fast-evolving landscape of industrial solutions, B2B buyers often face the challenge of selecting the most effective tools for their operational needs. While tool kit manufacturers provide a robust solution for various applications, exploring alternative methods and technologies can lead to enhanced efficiency and cost-effectiveness. This section evaluates two primary alternatives: Modular Tool Systems and Automated Tool Management Solutions.
Comparison Table
Comparison Aspect | Tool Kit Manufacturer | Modular Tool Systems | Automated Tool Management Solutions |
---|---|---|---|
Performance | High-quality tools designed for specific tasks. | Versatile and customizable; can adapt to various tasks. | Streamlined operations through automation; reduces human error. |
Cost | Varies by brand and complexity; initial investment can be high. | Generally lower initial costs; ongoing costs depend on customization. | Higher upfront investment; long-term savings through efficiency. |
Ease of Implementation | Requires training for effective use. | Easy to assemble and modify; minimal training required. | Complex setup; requires significant training and integration. |
Maintenance | Regular maintenance needed to ensure longevity. | Low maintenance; parts can be easily replaced. | Minimal maintenance post-installation; relies on software updates. |
Best Use Case | Ideal for traditional, hands-on work environments. | Best for diverse applications requiring flexibility. | Suitable for large-scale operations needing efficiency and tracking. |
What Are the Advantages and Disadvantages of Modular Tool Systems?
Modular Tool Systems offer a flexible alternative to traditional tool kits. They allow users to customize their tool setups based on specific project needs, enabling a more tailored approach. This adaptability often results in lower initial costs compared to comprehensive tool kits. However, the trade-off can be a lack of specialized tools that might be necessary for certain tasks, which could lead to inefficiencies if specific needs are not anticipated. Additionally, while assembly is straightforward, users may still require a basic understanding of tool compatibility.
How Do Automated Tool Management Solutions Enhance Operational Efficiency?
Automated Tool Management Solutions represent a significant leap in efficiency for B2B buyers, particularly in large-scale operations. These systems facilitate tracking, inventory management, and tool usage analytics, drastically reducing the likelihood of human error. Although they involve a higher initial investment and can be complex to implement, the long-term savings and operational improvements often justify the costs. The major downside is the need for thorough training and integration with existing processes, which can be resource-intensive.
Conclusion: How to Choose the Right Solution for Your Needs
When selecting between a tool kit manufacturer and its alternatives, B2B buyers should carefully assess their specific operational needs and project requirements. Consider factors such as performance expectations, budget constraints, and ease of implementation. For companies operating in diverse environments, modular systems may offer the necessary flexibility. Conversely, firms focused on efficiency and error reduction may find automated solutions to be a worthwhile investment. Ultimately, the right choice hinges on aligning the solution with your business’s unique operational context and long-term goals.
Essential Technical Properties and Trade Terminology for tool kit manufacturer
What Are the Essential Technical Properties for Tool Kit Manufacturing?
Understanding the technical specifications of tool kits is crucial for B2B buyers, especially when sourcing products that meet specific operational needs. Here are some key properties to consider:
1. Material Grade: Why Does It Matter?
The material grade of components used in tool kits (such as steel, aluminum, or plastic) directly affects their durability and performance. High-grade materials like chrome vanadium steel provide enhanced strength and corrosion resistance, making them ideal for professional applications. Buyers should prioritize suppliers who specify material grades, ensuring that the tools can withstand rigorous use without failure.
2. Tolerance Levels: How Do They Impact Performance?
Tolerance refers to the permissible limit of variation in a physical dimension, crucial for ensuring that tools fit together correctly. In tool kit manufacturing, tight tolerances are essential for precision instruments, such as wrenches and screwdrivers. A lack of attention to tolerance can lead to poor performance or even tool failure. Buyers should inquire about tolerance specifications to ensure the tools will meet their quality standards.
3. Finish Type: What Should You Look For?
The finish type of tools affects not only aesthetics but also functionality and longevity. Common finishes include polished, matte, and coated (e.g., black oxide or chrome plating). Each finish offers different benefits, such as reduced friction or enhanced corrosion resistance. Understanding these finishes can help buyers select the right tools for their specific environments, whether they are for automotive, industrial, or home use.
4. Weight and Ergonomics: Why Are They Important?
The weight of tools can impact user fatigue during prolonged use, while ergonomic designs can enhance comfort and efficiency. Tool kits designed with ergonomics in mind often feature soft grips and balanced weights, minimizing strain on the user. Buyers should consider these factors, especially for tools intended for professional use where comfort and usability can significantly affect productivity.
5. Certification Standards: What Should You Verify?
Certification standards, such as ISO or ANSI, indicate that products meet specific quality and safety criteria. Tools that bear these certifications are more likely to perform reliably and safely. B2B buyers should always verify the certifications of tools they are considering, as this can be a crucial factor in compliance with local regulations or industry standards.
What Are Common Trade Terms in Tool Kit Manufacturing?
Familiarizing oneself with industry jargon is essential for effective communication and negotiation. Here are some common terms that B2B buyers should know:
1. OEM (Original Equipment Manufacturer): What Does It Signify?
OEM refers to a company that produces parts or equipment that may be marketed by another manufacturer. In tool kit manufacturing, working with OEMs can offer customization options and potentially lower costs for bulk purchases. Buyers often seek OEM partnerships to ensure that they receive tailored solutions that meet their specific needs.
2. MOQ (Minimum Order Quantity): Why Is It Relevant?
MOQ indicates the smallest number of units a supplier is willing to sell. Understanding MOQ is crucial for buyers, as it affects inventory management and cost efficiency. For companies operating in regions like Africa or South America, where market demand can fluctuate, negotiating MOQs can lead to significant savings and more flexible purchasing options.
3. RFQ (Request for Quotation): How to Use It Effectively?
An RFQ is a document sent to suppliers requesting pricing and terms for specific products. Crafting a clear and detailed RFQ helps suppliers understand the buyer’s requirements, leading to more accurate quotes. B2B buyers should include specifications, quantities, and timelines in their RFQs to streamline the procurement process.
4. Incoterms: What Are They and Why Do They Matter?
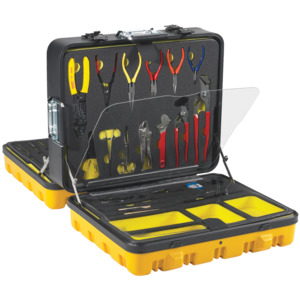
A stock image related to tool kit manufacturer.
Incoterms (International Commercial Terms) define the responsibilities of buyers and sellers in international trade. They clarify who is responsible for shipping, insurance, and tariffs, reducing the risk of misunderstandings. Buyers should familiarize themselves with relevant Incoterms to ensure smooth transactions and avoid unexpected costs.
By understanding these technical properties and trade terms, international B2B buyers can make informed decisions when sourcing tool kits, ultimately enhancing their operational efficiency and product quality.
Navigating Market Dynamics and Sourcing Trends in the tool kit manufacturer Sector
What Are the Key Market Dynamics and Trends Influencing Tool Kit Manufacturers?
The global tool kit manufacturing sector is witnessing significant transformation driven by several key factors. One of the foremost drivers is the increasing demand for customization among B2B buyers. Companies are looking for tailored solutions that meet specific project needs, which is prompting manufacturers to innovate and diversify their product offerings. Additionally, the rise of e-commerce platforms is reshaping how international buyers, especially from Africa, South America, the Middle East, and Europe, source tools. With the ability to compare prices and product specifications online, buyers are empowered to make informed decisions quickly.
Moreover, the integration of advanced technologies, such as IoT and AI, is becoming prevalent in the tool kit sector. These technologies enhance product functionality and improve supply chain efficiency, which is crucial for international buyers seeking reliability and responsiveness in sourcing. Sustainability is another emerging trend, with an increasing emphasis on eco-friendly materials and processes. Buyers are more inclined to partner with manufacturers who demonstrate a commitment to reducing their environmental footprint.
How Is Sustainability Influencing Sourcing Decisions in the Tool Kit Manufacturing Sector?
Sustainability and ethical sourcing are critical considerations for B2B buyers in the tool kit manufacturing industry. The environmental impact of manufacturing processes is under scrutiny, compelling companies to adopt greener practices. This shift is not only driven by regulatory pressures but also by consumer demand for sustainable products. International buyers are increasingly evaluating suppliers based on their sustainability credentials, including the use of recycled materials and energy-efficient manufacturing techniques.
Ethical supply chains are essential for maintaining brand integrity and meeting corporate social responsibility (CSR) goals. Buyers from diverse regions, including Africa and Europe, are prioritizing partnerships with manufacturers that uphold fair labor practices and transparency in their operations. Certifications such as ISO 14001 for environmental management and Fair Trade can significantly enhance a manufacturer’s appeal to conscientious buyers.
Furthermore, the adoption of sustainable materials, such as biodegradable plastics and responsibly sourced metals, is becoming a competitive differentiator. Buyers are encouraged to seek out manufacturers who are not only compliant with local regulations but also proactive in their sustainability initiatives.
How Has the Tool Kit Manufacturing Sector Evolved Over Time?
The evolution of the tool kit manufacturing sector can be traced back to the Industrial Revolution, where mechanization began to transform production methods. Initially, tools were handcrafted, but the advent of mass production techniques in the late 19th and early 20th centuries enabled manufacturers to produce high-quality tools at scale. Over the decades, technological advancements have continuously reshaped the industry, with the introduction of precision engineering and automation enhancing product quality and reducing lead times.
In recent years, the focus has shifted towards digitalization and sustainability, reflecting broader market trends. Manufacturers are increasingly leveraging data analytics to optimize production processes and improve customer engagement. This evolution underscores the importance of adaptability in the tool kit sector, particularly for international B2B buyers seeking reliable and innovative partners. Understanding these historical shifts allows buyers to make more informed decisions when selecting suppliers and navigating the complexities of the global market.
Frequently Asked Questions (FAQs) for B2B Buyers of tool kit manufacturer
-
How do I choose the right tool kit manufacturer for my business needs?
Selecting the right tool kit manufacturer involves several key considerations. First, assess the manufacturer’s experience and expertise in producing the specific type of tools you need. Look for certifications and quality standards that align with your industry requirements. Additionally, evaluate their ability to customize products based on your specifications and their track record in meeting deadlines. Finally, consider their geographical location and logistics capabilities, especially if you are sourcing from regions like Africa or South America, which can impact shipping times and costs. -
What are the advantages of sourcing tool kits from manufacturers in Africa?
Sourcing tool kits from African manufacturers can provide several advantages. Local production can lead to lower shipping costs and shorter lead times, which is beneficial for businesses needing quick turnaround. Additionally, many African manufacturers are increasingly adopting modern manufacturing technologies and practices, ensuring competitive quality. Supporting local businesses can also enhance your brand’s reputation as a socially responsible company, fostering goodwill in international markets. -
What customization options should I consider when ordering tool kits?
When ordering tool kits, consider customization options such as branding, packaging, and specific tool configurations. Determine whether you need specific tools tailored to your industry or unique branding elements that reflect your company’s identity. Additionally, inquire about custom packaging solutions that can enhance product presentation and protect the tools during transport. Discussing these options early in the negotiation process can help streamline production and ensure that the final product meets your expectations. -
What is the typical minimum order quantity (MOQ) for tool kit manufacturers?
Minimum order quantities (MOQ) can vary significantly among tool kit manufacturers, depending on factors like the type of tools, materials used, and production capabilities. Generally, MOQs can range from a few dozen to several hundred units. It’s essential to communicate your needs clearly with potential suppliers, as some manufacturers may offer flexibility in MOQs for first-time buyers or bulk orders. Understanding MOQs will help you manage inventory levels and cash flow effectively. -
What payment terms should I negotiate with a tool kit manufacturer?
Negotiating payment terms is critical to managing cash flow in your purchasing process. Common terms include upfront payments, deposits, and net payment periods (e.g., 30, 60, or 90 days). Consider discussing payment methods, such as wire transfers or letters of credit, which can provide security for both parties. It’s advisable to establish clear terms in the purchase agreement to avoid misunderstandings and ensure timely payments, particularly in international transactions where exchange rates and banking fees may apply. -
How can I ensure quality assurance when sourcing tool kits internationally?
To ensure quality assurance when sourcing tool kits internationally, conduct thorough due diligence on potential manufacturers. Request samples to evaluate the quality of their products and visit their production facilities if possible. Implement a quality control process that includes regular inspections during production and before shipment. Additionally, consider working with third-party inspection services that can provide unbiased assessments of product quality and compliance with your specifications. -
What logistics considerations should I keep in mind when sourcing tool kits?
When sourcing tool kits, logistics play a crucial role in the supply chain. Evaluate shipping options, including air freight for expedited delivery or sea freight for cost-effective bulk shipments. Understand the customs regulations and import duties in your country, as they can impact overall costs. Collaborate with logistics partners who have experience in international shipping to ensure timely deliveries and proper handling of your products, especially when dealing with long distances from regions like the Middle East or South America. -
How do I build a long-term relationship with my tool kit manufacturer?
Building a long-term relationship with your tool kit manufacturer involves consistent communication and trust. Start by setting clear expectations for quality, delivery times, and pricing. Regularly engage with your supplier to provide feedback and discuss any challenges that arise. Consider collaborative projects or joint ventures to strengthen the partnership. By investing time and effort into nurturing this relationship, you can secure better terms, preferential treatment, and enhanced support as your business grows.
Important Disclaimer & Terms of Use
⚠️ Important Disclaimer
The information provided in this guide, including content regarding manufacturers, technical specifications, and market analysis, is for informational and educational purposes only. It does not constitute professional procurement advice, financial advice, or legal advice.
While we have made every effort to ensure the accuracy and timeliness of the information, we are not responsible for any errors, omissions, or outdated information. Market conditions, company details, and technical standards are subject to change.
B2B buyers must conduct their own independent and thorough due diligence before making any purchasing decisions. This includes contacting suppliers directly, verifying certifications, requesting samples, and seeking professional consultation. The risk of relying on any information in this guide is borne solely by the reader.
Strategic Sourcing Conclusion and Outlook for tool kit manufacturer
In the evolving landscape of tool kit manufacturing, international B2B buyers must recognize the importance of strategic sourcing as a pivotal component of their operational success. By leveraging data-driven insights and fostering relationships with reliable suppliers, companies can not only enhance product quality but also achieve cost efficiencies that directly impact their bottom line. For buyers from Africa, South America, the Middle East, and Europe, the ability to source strategically can facilitate entry into new markets and drive competitive advantage.
What are the key takeaways for effective strategic sourcing in tool kit manufacturing? First, understanding regional supply chain dynamics is crucial. Buyers should engage with local suppliers who are attuned to market needs while ensuring compliance with international standards. Second, adopting a flexible sourcing strategy that embraces technological advancements can streamline procurement processes and mitigate risks associated with market fluctuations.
Looking ahead, the future of tool kit manufacturing will be shaped by innovation and sustainability. Buyers are encouraged to prioritize partnerships with manufacturers committed to eco-friendly practices and cutting-edge technologies. By doing so, they position themselves not only as leaders in their respective markets but also as responsible contributors to a sustainable future. Embrace the opportunity to optimize your sourcing strategy and unlock new possibilities in the global tool kit market.